Расчет мебели Одной из самых важных операций при изготовлении мебели является её расчёт или деталировка. Иными словами. необходимо высчитать размер каждой детали будущего изделия. Это самый сложный и ответственный момент. Прежде чем начинать расчёт необходимо сделать проект мебели, определиться из какого материала будет будущая мебель и только после этого начинать считать. С чего начинать? У каждого свой подход. Давайте постараемся разобраться, как посчитать размер мебельных деталей. Возьмём чертёж шкафа и внимательно посмотрим на него. Как мы видим, шкаф состоит из нескольких деталей — крыша, дно, перегородка, полки. Прошу заметить, что первый размер деталей всегда даётся по структуре. Это значит, что если вы хотите, чтоб боковины имели вертикальную структуру, то записывая размер деталей, первой пишите высоту, а второй ширину детали. Более подробно читайте здесь — как правильно записать деталировку деталей. Заметим, что боковины шкафа и перегородка располагаются между крышей и дном, в других изделиях может быть и по-другому. Например. крыша накладывается на боковины, а дно располагается между ними. Итак начинаем считать размеры для деталей нашего шкафа. Допустим, что мы его будем изготавливать из ЛДСП толщиной 16 мм, а размеры шкафа будут такие: высота — 2400 мм, ширина — 1200 мм, глубина 600 мм. Крыша и дно имеют размер по ширине 1200 мм в готовом виде. Это значит, что в месте с наклеенной кромкой длина деталей будет 1200 мм. Соответственно 1200 минус две толщины кромки (с одной стороны и с другой стороны детали) и будет чистый размер длины крыши и дна. Теперь ширина деталей. Мы знаем, что глубина шкафа 600 мм. Если это глубина вместе с фасадами, то ширина деталей будет 600 минус толщина фасадов — допустим, что они из такого же материала ( ДСП 16 мм), значит 600 — 16 и минус толщина кромки, которой будет закромкована передняя часть крыши и дна. Это при условии, что фасады будут ложиться на крышу и дно, но бывает, что фасады располагаются между крышей и дном. При расчете высоты боковин шкафа следует не забывать учитывать высоту ножек, чтоб шкаф не получился выше запланированного. Например в нашем случае высота шкафа 2400 мм, высота ножек допустим будет 50 мм. Следовательно высота боковин 2400-50-32=2318 мм. где 50 мм — высота ножек, а 32 мм — толщина крыши и дна. Ширина боковин будет такая же как и у дна — 584 мм. Не забываем записывать размеры деталей правильно — 2318*584 мм. Первым размером пишем высоту, а вторым ширину. На данном примере можно заметить, что перегородка является такой же как и боковины, следовательно, её размер будет аналогичен — 2318*584 мм. Как нам теперь посчитать размер полок? Всё очень просто — от ширины шкафа ( длины дна ) отнимаем толщину двух боковин и одной пере городки 1200-48=1152 мм. И делим этот размер на два потому, что в нашем примере перегородка располагается точно посередине, получается 576 мм это ширина полок. Глубина полок обычно на 5 мм меньше ширины перегородки и составляет 579 мм. Для чего это делается? Бывают погрешности в размерах при распиле деталей и если полка окажется немного большего размера, то она будет выступать. Вследствие чего будет нарушен эстетический вид изделия. Ещё одним не маловажным фактором является то, что на слегка «утопленной» полке снижается вероятность подорвать кромку во время использования изделием. Когда кладём вещи или протираем пыль, можно нечаянно зацепить уголок кромки и подорвать её. Итак размер полок 576*579 мм. Ну вот пожалуй и всё. Осталось правильно записать размеры деталей и отметить, какие стороны следует кромковать. Ах, да! Ещё же для нашего шкафа следует посчитать размеры фасадов. |
ДВП-Древесноволокнистая плита 1,70*2,75 мм толщина 2,8 мм
Звоните нам по телефону +77003177073 +77005199909
Или пишите в Whatsapp
Из-за изменения курса, цена может незначительно отличаться от заявленной на сайте. Цену просьба уточнять у менеджера.
Древесноволокнистые плиты
Богатый ассортимент стройматериалов от ведущих производителей из стран СНГ и Европы предлагает компания «SERILIK-M CONSTRUCTION». Мы гарантируем высокое качество продукции, оптимальные цены и кратчайшие сроки поставки.
Преимущества плит ДВП:
Экологическая чистота и безопасность.
Высокая прочность.
Долговечность.
Легкость обработки.
Используются при производстве корпусной мебели, в строительстве, для потолочного перекрытия.
ДВП плиты от «SERILIK-M CONSTRUCTION»
Гарантированно высокого качества.
На продукцию имеется сертификаты.
Демократичной стоимости.
Выгодное предложение
Компания «SERILIK-M CONSTRUCTION» наладила прямые поставки от производителей строительных материалов.
Мы гарантируем доступные цены.
Внедрили гибкую систему скидок.
Реализуем товары оптом и в розницу.
Гарантируем 100% комплектность поставок.
Поддерживаем постоянный запас товаров на складе.
Готовы в кратчайшие сроки поставить даже очень крупные партии.
Компания «SERILIK-M CONSTRUCTION» – гарантия отличного качества и демократичных цен.
ДВП, Древесно волокнистая плита ― конструктивный материал, изготовляемый измельчением и расщеплением древесины в волокнистую массу, отливкой из нее плит их прессованием и сушкой.
Размер: 2750мм*1700мм
Толщина: 2,5 мм.
Страна Производитель: РОССИЯ.
Идеально подходит для корпусной мебели. Стройки. Для потолочного перекрытие.
У нас всегда доступные цены, всегда можно торговаться, индивидуальные скидки. Наши контакты: 8701 964 0007, 8 (727) 225 95 56, (57)
ДВП — продукт широкого применения
Предприятия концерна «Беллесбумпром» ежегодно выпускают порядка 140 млн условных квадратных метров древесно-волокнистых плит (ДВП). Более 70% этой продукции поставляется на экспорт.
В составе концерна производство ДВП различных видов осуществляют 6 предприятий. В 2018 году они произвели без малого 140 млн усл. кв. м ДВП, что на 16,2% больше, чем в 2017 году, на экспорт поставлено более 70% — 99 млн усл. кв. м. География поставок охватила 32страны. Около 47% экспортных продаж приходятся на рынки стран дальнего зарубежья, в основном Европейского союза. При этом, ДВП экспортируется и в более отдаленные регионы, например, в Иран и Канаду.
Многие, невареное, когда слышат про ДВП, представляют себе тонкий и гибкий серо-коричневый лист. Однако современные древесно-волокнистые плиты имеют достаточно широкий ассортимент, разнообразные технические и внешние характеристики.
ДВП – это листовой строительный или отделочный материал. Толщина листа может быть от 2-3 мм до 12-15 мм, некоторые виды могут быть и до 40 мм. Плиты используется в строительстве, в отделке, при изготовлении мебели и ламината.
Предприятия концерна выпускают 9 групп древесно-волокнистых плит: они разные по плотности изготовления и отделке, толщине, области применения. Плиты, выпускаемые концерном, имеют широкое применение. Их используют в строительстве, отделке помещений, в том числе их изоляции и утепления, а также в производстве мебели, дверей и напольных ламинированных покрытий.
Листовые ДВП отличаются высокой плотностью и прочностью, имеют относительно невысокую цену. Тонкие листы отлично гнутся, что позволяет их применять для обшивки криволинейных поверхностей. Используется ДВП в строительстве, в качестве обшивки при каркасном домостроении, для выравнивания пола, стен.
ДВП малой плотности используется в качестве звукоизоляционного материала. Хаотичное расположение волокон древесины способствует тому, что звуки «вязнут» в материале. Это самый недорогой и удобный в монтаже тип звукоизоляционных материалов.
Некоторые виды древесно-волокнистых плит могут использоваться как отделочные материалы — для отделки стен в помещениях нормальной влажности. Для этих целей применяют ДВП, одна из сторон листа которой покрашена, покрыта декоративной пленкой, заламинирована.
Еще одна область применения ДВП — производство мебели. Тонкие используют как вспомогательный материал — делают заднюю стенку корпусной мебели, подшивают днище в креслах и стульях, днища в ящиках и т.п.
Новое поколение древесно-волокнистых плит, такие как МДФ и ХДФ уже используются для изготовления фасадов корпусной мебели, межкомнатных дверей и напольных ламинированных покрытий соответственно.
Мебель из плит МДФ выглядит, практически, как мебель из массива древесины, она также привлекательна и долговечна. По цене она стоит посередине между мебелью из массива и ДСП. Причем если мебель из ДСП имеет линейное строение, из размолотых древесных волокон формуют изогнутые, плавные, скругленные формы. Все это позволяет создать большее видовое разнообразие. Используя ту же технологию, делают стеновые панели МДФ. Это не только ровные гладкие листы, но и с рисунком разного вида/типа.
Исходным сырьем для производства ДВП являются щепа и опилки. Высушенный материал, дробится в специальных машинах (дефибраторах и рафинаторах) на мельчайшие частицы — волокна. Степень помола может быть от грубой до мельчайшей. Далее процесс отличается для разных способов производства.
Есть два способа производства ДВП — мокрое и сухое прессование. «Мокрый» метод более экологичен. При мокром прессовании используется меньшее количество связующих (иногда, вообще без синтетических добавок), но материал получается более дорогим, так как процесс более энергоемкий.
При мокром прессовании некоторые сорта ДВП могут быть сделаны без добавления постороннего связующего. Под давлением и при высокой температуре, из древесных волокон выделяется лигнин (вещество, характеризующее одеревеневшие стенки растительных клеток). Он является натуральным связующим. Лигнин в значительных количествах содержится в древесине хвойных пород. Но не для всех сортов ДВП природного связующего достаточно. В этом случае добавляется от 4 до 7% синтетического связующего.
При сухом прессовании, обычно в массу добавляют синтетические смолы, которые связывают волокна. Именно этот метод позволяет получить ДВП большой толщины — до 12-15 мм, некоторые завод могут выпускать питы толщиной до 40 мм. На уплотнение и прессование сухой массы уходит намного меньше времени – 3-5 минут в зависимости от класса и толщины. Производительность пресса возрастает в разы. К тому же в сухую массу кладут меньшее количество добавок — они не вымываются водой. Все это ведет к снижению стоимости материала. Но дешевые связующие содержат формальдегид, а его содержание необходимо контролировать, так как в больших количествах он вреден для здоровья.
Для производства мебели и отделочных работ в помещениях, должен использоваться материал с классом эмиссии формальдегида Е0,5 или Е1. Это, как правило, ДВП мокрого прессования. Отличить ДВП, сделанное мокрым способом, можно по отпечатку сетки на тыльной стороне листа.
Производство МДФ, ХДФ
Производство ИДВП
youtube.com/embed/N5TiRbGaOjw» frameborder=»0″ allowfullscreen=»allowfullscreen» allow=»accelerometer; autoplay; encrypted-media; gyroscope; picture-in-picture»/>
Pinepanels Легкий ДВП средней плотности, толщина: от 2,5 мм до 35 мм, для мебели,
О компании
Год основания 1996
Юридический статус компании с ограниченной ответственностью (Ltd./Pvt.Ltd.)
Характер бизнеса Производитель
Количество сотрудников от 11 до 25 человек
Годовой оборот50–100 крор
Участник IndiaMART с января 2006 г.
GST07AAACE7115P1ZF
Код импорта и экспорта (IEC) 02960 *****
Eximcorp India Pvt. Ltd. — это деревообрабатывающая компания, стремящаяся предоставлять конкурентоспособные решения, разработанные вместе со своими клиентами и потребителями в Индии. Его сила заключается в оценке, разработке и предоставлении клиентам надежных решений, ориентированных на обслуживание и производительность.Гарантировать, что наши клиенты получают лучшую цену на рынке; мы постоянно улучшаем качество и ассортимент продукции, чтобы соответствовать постоянно растущим требованиям к производительности по доступным ценам для потребителей без ущерба для нашей политики устойчивого развития.
Отнюдь не являясь традиционным дистрибьютором, мы являемся компанией, специализирующейся на передовых технологиях и инновациях, чтобы предоставлять нашим клиентам новаторские решения, наилучшим образом соответствующие их конкретным потребностям Панели: березовая фанера, МДФ высокой плотности, OSB, соответствие требованиям CARB. МДФ (древесноволокнистая плита средней плотности) и другие древесные композиты, пиломатериалы: сушеные и отшлифованные в печи.
Благодаря стратегии постоянных инноваций компания предоставляет клиентам экологически чистые продукты с высокой добавленной стоимостью из источников, сертифицированных в цепочке поставок.
Eximcorp демонстрирует уникальные изделия из древесины всемирно известных компаний в Тихоокеанском регионе, Европе и Америке, соответствующие большинству международных стандартов и нормативов, таких как California ARB, European RoHS, JAS и Закон Лейси США.
Экологически чистые изделия из древесины — единственное, что нужно для выживания. Внесите вклад в охрану окружающей среды, сказав «НЕТ» изделиям из древесины, полученным из неустойчивого лесного хозяйства.
Видео компании
Как применять ДВП в мебельных изделиях
ДВП, также обычно называемое ДВП высокой плотности (HDF) , является отличным выбором материала для изготовления широкого спектра изделий. Он чем-то похож на ДВП средней плотности (МДФ) и ДСП, но по своей конструкции делает его на более плотным и прочным, чем другие материалы. Он сделан из взорванных древесных волокон, которые сильно сжимаются под действием тепла и давления во влажном процессе, а , в отличие от массивной древесины, очень однородный, без зерен.
Tablex, экологически чистый древесноволокнистый картон от Betanzos HB, входит в число лучших древесноволокнистых плит высокой плотности , используемых в производстве мебельных изделий.
Почему ДВП отлично подходит для изготовления мебели?
До того, как ДВП применялось в других областях, таких как панели , напольные покрытия, украшения, строительство и упаковка, , среди прочего, ДВП долгое время использовался для разработки широкого спектра мебельной продукции.Его универсальность, физическая и механическая стойкость, а также хорошая реакция на влажность. делают его отличным выбором материала для различных типов мебельной продукции, включая интерьеры диванов , днища ящиков, конструкции основания кроватей, спинки мебели, комоды ящиков, офисные столы и многое другое. .
имеют одинаковую толщину, плотность и внешний вид. В процессе строительства могут быть добавлены некоторые материалы для улучшения определенных свойств древесноволокнистого картона, таких как устойчивость к влаге и истиранию, , а также для повышения его прочности и долговечности.Кроме того, древесноволокнистые плиты HDF можно легко резать, фрезеровать, формировать и сверлить с помощью стандартных рабочих инструментов, что позволяет плотникам легко использовать их в производстве мебели .
Плита ХДФ может быть надежно приклеена или закреплена гвоздями, шурупами или скобами. — еще одна причина, по которой с ней легко работать во многих мебельных конструкциях. ДВП высокой плотности также можно ламинировать с различными накладками, такими как бумажные накладки, ламинированная бумага, керамика, пластик, шпон и винил , чтобы придать им особый желаемый вид мебели. Например, древесный шпон можно приклеить к плите HDF, чтобы придать ей вид твердой древесины.
Основные преимущества ДВП по сравнению с мебельной продукцией:
- Устойчивость к погодным условиям — Древесноволокнистая плита высокой плотности отлично переносит или противостоит влаге, истиранию, температуре, пятнам и выцветанию.
- Простота работы — Плиты HDF упрощают работу как плотникам, так и мастерам-мастерам. Доски можно легко разрезать, формировать, фрезеровать и просверливать с помощью стандартных рабочих инструментов.Их также можно легко закрепить шурупами, скобами или гвоздями.
- Отделки по индивидуальному заказу — ДВП можно ламинировать с различными покрытиями для достижения определенной желаемой отделки мебели, например, из массива дерева.
- Прочность и долговечность — ДВП из-за своей высокой плотности обеспечивает большую прочность мебельной продукции и, следовательно, гарантирует им более длительный срок службы по сравнению с другими материалами, такими как древесно-стружечные плиты, которые могут легко расколоться или потрескаться.
Руководство по физическому применению древесноволокнистых плит в мебельной продукции
При использовании плит HDF в производстве мебели существует ключевых рекомендаций , которых человек должен придерживаться для достижения успешных результатов.Сюда входят:
Что делать во время резки ДВП?
Для резки древесноволокнистых плит высокой плотности рекомендуется торцовочная пила , потому что она больше подходит для выполнения прямых пропилов. Циркуль или копировальную пилу можно использовать при резке криволинейных, неровных или по внутренним краям. Электропила может применяться, когда требуется скорость и обширная резка.
Для создания рисунков и узоров на доске, чтобы придать мебели уникальную отделку или внешний вид, рекомендуется использовать инструмент для надрезания.Помните, что дизайн перфорированного ДВП или перфорированного картона Tablex легко доступен, поэтому нет необходимости делать ненужные перфорации в вашем дизайне. Круглые отверстия могут быть созданы с помощью спирального сверла или скобы и сверла, а неровные края могут быть сглажены мелкозернистой наждачной бумагой. Hardboard также отлично подходит для лазерной / плазменной резки с числовым программным управлением.
Кондиционирование панелей ДВП
Перед нанесением древесноволокнистые панели должны быть хорошо кондиционированы в течение не менее 48 часов перед нанесением , поставив их по отдельности на длинный край.Это позволяет им, как и в случае с любыми деревянными панелями, уравновеситься с существующими условиями в помещении перед нанесением.
Обрамление и крепление плит ХДФ при строительстве
ПлитыHDF следует прикреплять только к прямым элементам каркаса, которые имеют адекватные свойства удерживания гвоздей. Для плит толщиной менее 3/16 дюйма необходима твердая подложка.
Прикрепление гвоздями и шурупами к картону
При забивании гвоздями в первую очередь следует закрепить центр доски, а остальную часть доски следует закрепить, двигаясь от центра к краям. Прибивание гвоздями должно производиться перпендикулярно поверхности и на расстоянии 8 дюймов друг от друга на промежуточных опорах, но 4 дюйма по краям. Рекомендуются гвозди с кольцевым стержнем, и они должны быть достаточно длинными, чтобы проникать в основание гвоздя не менее чем на дюйма.
Головки гвоздей можно скрыть, погрузив их под поверхность доски и заполнив отверстия для гвоздей подходящим материалом перед грунтованием. Не рекомендуется забивать доски толщиной менее 3/16 дюйма.
При привинчивании досок необходимо предварительное просверливание.
- Использование клея — Клеи можно использовать, когда требуется скорость в конструкции мебели или когда плиты HDF имеют толщину менее 3/16 дюйма. Однако при использовании клеевого средства многие экологические характеристики борта теряются.
- Отделка — Поверхность мебельного изделия должна быть чистой и сухой при подготовке к отделке.
Первый слой следует наносить очень аккуратно, и он должен быть совместим с последующими верхними покрытиями.Здесь важны инструкции производителя.
ДВП высокой плотности — один из лучших материалов для изготовления мебели. Их преимущества огромны, и поставщики плит высокой плотности или поставщики древесноволокнистых плит высокой плотности могут обозначить для вас еще больше преимуществ плит HDF для вашего конкретного применения.
Если вы профессиональный покупатель (торговец древесиной, импортер или дистрибьютор) , заинтересованный в получении дополнительной информации о ДВП и возможностях, обратитесь в нашу международную группу продаж . Betanzos HB — производитель из Испании. Мы производим продукцию в соответствии с высокими стандартами ЕС в отношении качества и юридической безопасности , а также , который также защищен стабильным обменным курсом евро.
Влияние типа панели и толщины панели на моментное сопротивление винтовых угловых соединений и жесткость четырехэлементных шкафов :: БиоРесурсы
Юксель, М.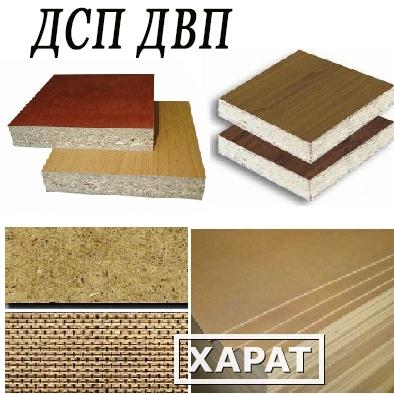
Abstract
Целью данного исследования было изучить влияние типа панели и толщины панели на моментное сопротивление угловых соединений L-типа и характеристики прогиба четырехэлементных шкафов. Для создания четырехэлементных шкафов были использованы три различных панели на основе древесины, а именно ДСП (ДСП), ДВП средней плотности (МДФ) и фанера окумэ ( Aucoumea klaineana ) (PW) с двумя разными уровнями толщины. Все угловые соединения и корпуса были собраны саморезами 4 x 50 мм без клея.Шкафы с четырьмя элементами были испытаны под статической нагрузкой, поддерживая их в трех точках. Кроме того, были испытаны моментные сопротивления однотипных шарнирных угловых соединений L-типа при статических сжимающих и растягивающих нагрузках. Результаты испытаний показали, что самые высокие значения жесткости наблюдались при толщине слоя 15 мм. Это показало, что фанеру толщиной 15 мм можно использовать вместо фанеры толщиной 18 мм. Шкафы из ПБ и МДФ толщиной 16 мм показали более высокие значения жесткости, чем шкафы из МДФ, ПВ и ПБ толщиной 18 мм. Результаты испытаний также показали, что панели толщиной 15 мм и 16 мм могут иметь почти такую же жесткость, как панели толщиной 18 мм.
Скачать PDF
Полная статья
Влияние типа панели и толщины панели на моментное сопротивление винтовых угловых соединений и жесткость четырехэлементных шкафов
Мехмет Юксель, a, * Надир Йилдирим, b Али Касал, a Юсуф Зия Эрдил, a и Сельчук Демирджи c
Целью данного исследования было изучить влияние типа панели и толщины панели на моментное сопротивление угловых соединений L-типа и характеристики прогиба четырехэлементных шкафов. Для создания четырехэлементных шкафов были использованы три различных панели на основе древесины, а именно ДСП (ДСП), ДВП средней плотности (МДФ) и фанера окумэ ( Aucoumea klaineana ) (PW) с двумя разными уровнями толщины. Все угловые соединения и корпуса были собраны саморезами 4 x 50 мм без клея. Шкафы с четырьмя элементами были испытаны под статической нагрузкой, поддерживая их в трех точках. Кроме того, были испытаны моментные сопротивления однотипных шарнирных угловых соединений L-типа при статических сжимающих и растягивающих нагрузках.Результаты испытаний показали, что самые высокие значения жесткости наблюдались при толщине слоя 15 мм. Это показало, что фанеру толщиной 15 мм можно использовать вместо фанеры толщиной 18 мм. Шкафы из ПБ и МДФ толщиной 16 мм показали более высокие значения жесткости, чем шкафы из МДФ, ПВ и ПБ толщиной 18 мм. Результаты испытаний также показали, что панели толщиной 15 мм и 16 мм могут иметь почти такую же жесткость, как панели толщиной 18 мм.
Ключевые слова: ДВП средней плотности; ДСП; Жесткость; Четырехсторонние шкафы; Угловые соединения L-образные
Контактная информация: a: Кафедра деревообрабатывающей промышленности, технологический факультет, Университет Мугла Сытки Кочман, Мугла, 48000, Турция; b: Университет штата Мэн, Ороно, ME 04469, США; c: Школа профессионального обучения Эге, Программа мебели и декора, Университет Эге, 35100, Борнова / Измир, Турция; * Автор для переписки: myuksel @ mu.edu.tr
ВВЕДЕНИЕ
Корпусная мебель — одна из важнейших категорий производимой и используемой сегодня мебели. Он широко используется в домах, офисах и промышленных зданиях для складских целей. Из-за увеличения затрат на ответственность, связанных с производством корпусной мебели с плохой конструкцией, использование рациональных методов проектирования корпусной мебели станет первоочередной задачей, особенно в мебельной промышленности корпусного типа, где каждому покупателю продаются большие партии мебели одного и того же дизайна. .
В отличие от жесткой рамной конструкции, прочность и жесткость которой определяется жесткостью на изгиб балок и колонн, прочность и жесткость панельной конструкции почти полностью зависит от жесткости ее пластин на кручение (Eckelman 1967).
В настоящее время соединения без клея являются обычным явлением в мебельном строительстве, поскольку их использование позволяет транспортировать мебель в разобранном состоянии и собирать на месте, и такой подход значительно снижает транспортные расходы.Несмотря на их широкое использование, были проведены ограниченные исследования прочности и жесткости винтовых соединений.
Винты используются в производстве мебели в течение двух-трех столетий, в основном для усиления других конструкций или для крепления таких деталей, как клеевые блоки. Их также можно использовать в качестве основных соединителей. Их способность противостоять вытягиванию и боковым нагрузкам делает винты отличными крепежными элементами для мебели. Они по-прежнему широко используются для крепления фурнитуры к мебели, но они также широко используются вместо других крепежных элементов, таких как дюбели и гвозди, для образования структурных несущих соединений.
Винтовые зажимы широко используются для изготовления угловых стыков мебельных шкафов с клеем и без него. Рациональная конструкция корпусной мебели, изготовленной с помощью шурупов, требует информации о ее жесткости в древесно-стружечных плитах (PB) и древесноволокнистых плитах средней плотности (MDF).
Котас (1957, 1958a, b) провел первые известные исследования структурных характеристик корпусной мебели; результаты его исследований позже были включены в небольшое руководство по проектированию. Лин и Экельман (1987) провели исследование, чтобы определить влияние жесткости суставов на жесткость корпуса; они указали, что соединения действительно оказывают значительное влияние на жесткость, и производители могут захотеть использовать соединения, обеспечивающие наибольшую жесткость в их конструкциях.Kasal et al. (2008) изучал влияние размера винта на несущую способность и жесткость пятисторонних мебельных ящиков, изготовленных из МДФ и ПБ. Пятисторонние корпуса были протестированы при статической нагрузке путем опоры в трех точках, и было обнаружено, что корпуса из МДФ обладают значительно большей несущей способностью, чем корпуса из полибутилена, но значимость жесткости корпусов из МДФ по сравнению с корпусами из полибутилена зависит от диаметра винта. Жесткость угловых соединений влияет на прочность корпусной мебели. Прогиб корпусной мебели, содержащей полки, можно уменьшить, увеличив жесткость угловых соединений (Cai and Wang, 1993).
До 90% (или более) всей мебели, производимой в Европе, изготовлено из древесных плит, особенно с использованием ДСП и МДФ (BioMatNet 2003). Стало очевидно, что моментное сопротивление стыков зависит от материала панели, типа клея и стыков (Tankut and Tankut 2009). Образцы с кромочной полосой, которая используется для покрытия открытых сторон материалов, дали более высокое диагональное растяжение и прочность на сжатие, чем контрольные образцы. Угловые соединения LamMDF (ламинированная древесноволокнистая плита) были прочнее, чем угловые соединения LamPB (ламинированная древесно-стружечная плита).Что касается типа кромочной ленты, кромочная облицовка меламинового типа дает больше прочности на диагональное растяжение и сжатие, чем другие. Наименьшая прочность на растяжение и сжатие была получена у кромкооблицовочного материала из ПВХ (Tankut and Tankut 2010).
Это предварительное исследование было направлено на определение влияния типа панели и толщины панели на моментное сопротивление угловых соединений L-типа и жесткость четырехэлементных шкафов путем сохранения всех других факторов (размер винта, тип винта и т. Д.) Постоянными.
ЭКСПЕРИМЕНТАЛЬНАЯ ИНФОРМАЦИЯ
В этом исследовании использовались три разных типа панелей (PB, MDF, PW) и две разные толщины панелей (от 18 мм до 16 мм для PB и MDF, от 18 мм до 15 мм для PW). Это наиболее часто используемые типы панелей и толщины панелей в мебельной промышленности (BioMatNet 2003).
Было по 5 повторов. Соответственно, в общей сложности было изготовлено 60 образцов угловых соединений L-типа (30 на сжатие, 30 на растяжение) и 30 четырехэлементных шкафов для испытаний на сопротивление статическому моменту и жесткость.Всего в этом исследовании было подготовлено и протестировано 90 образцов.
Таблица 1. Экспериментальный план исследования
Подготовка и построение образцов
Угловые соединения L-образного типа
У каждого экземпляра было по две части, названные лицом и прикладом. Размеры лицевого элемента составляли 320 200 мм для всей толщины панели, а размеры стыкового элемента составляли 320 182 мм для панелей толщиной 18 мм, 320 x 184 мм для панелей толщиной 16 мм и 320 x 185 мм для PW толщиной 15 мм. панель (рис.1). Члены были соединены друг с другом 3 винтами. Стальные шурупы для дерева с крестообразным шлицем 4 x 50 мм и углом резьбы 40 ± 3 градуса были использованы для создания угловых соединений четырехэлементных шкафов в соответствии с тем, что обычно используется в мебельной промышленности. Диаметр корня, внешний диаметр и резьба на шаг составляли 2,4 ± 0,25, 4,0 ± 0,3 и 1,8 мм для винтов соответственно.
Винты забивались по центру толщины стыкового элемента, в котором были просверлены пилотные отверстия. На рисунке 1 показано типичное размещение винтов в угловых соединениях L-типа, использованных в данном исследовании.Диаметр пилотных отверстий составлял примерно 80% диаметра основания шурупов, а глубина пилотных отверстий была равна примерно 75% глубины проникновения шурупов (Eckelman 2003). Образцы угловых соединений L-типа перед испытанием хранили в камере кондиционирования при 20 ºC ± 2 и 65 ± 3% относительной влажности, чтобы избежать колебаний содержания влаги.
Рис. 1. Общая конфигурация образца углового соединения L-типа и типичное расположение винтов (размеры в мм)
Шкафы четырехкомпонентные
Общая конфигурация четырехкомпонентных шкафов, использованных в данном исследовании, показана на рис.2. Четырехэлементные шкафы были изготовлены из панелей PB и MDF толщиной 16 мм и 18 мм и панелей PW толщиной 15 мм и 18 мм. okoume ( Aucoumea klaineana ). Четырехсторонний шкаф состоит из верхней, нижней и боковых панелей из того же материала. Четырехэлементные шкафы были сконструированы путем сборки боковых панелей на верхнюю и нижнюю панели. В конструкции испытательных шкафов используются полноразмерные листы 3660 x 1830 мм из ПБ и МДФ толщиной 18 мм, полноразмерные листы 2800 x 2100 мм из ПБ толщиной 16 мм, полноразмерные листы 2440 x 2100 мм из МДФ толщиной 16 мм, 2200 Полноразмерные листы толщиной 1700 мм PW толщиной 16 и 18 мм были разрезаны на верхнюю, нижнюю и боковые панели; затем эти панели были рассчитаны на окончательные ширину и длину элемента. Окончательные размеры каждого четырехстороннего ящика были основаны на обычно используемых размерах навесного шкафа: высота 650 мм, глубина 320 мм, ширина 650 мм. Все процедуры сборки и сборки были такими же, как и при сборке угловых соединений L-типа, чтобы обеспечить разумное сравнение.
Аналогичным образом, четырехэлементные шкафы хранились в камере кондиционирования при 20 ºC ± 2 и относительной влажности 65 ± 3% перед испытанием, чтобы также избежать колебаний содержания влаги.
Фиг.2. Общая конфигурация и диаграмма деформации четырехэлементного шкафа, поддерживаемого в трех точках при статическом испытании (размеры в мм)
Методы испытаний и нагружения
Физические и механические свойства PB, MDF и PW были испытаны в соответствии с процедурами, описанными в ASTM D 4442 (2003) и ASTM D 1037 (2001). Кроме того, сила фиксации болтов панелей PB, MDF и PW с краев и лицевых сторон была определена в соответствии с процедурами, установленными Erdil et al. (2002). Диаметр и глубина проникновения пилотных отверстий были такими же, как при сборке углового соединения L-типа и четырехэлементных шкафов, чтобы обеспечить разумное сравнение. Все испытания на крепление винта проводились на универсальной испытательной машине с усилием 50 кН. Скорость нагружения 2 мм / мин. Предельные нагрузки были приняты как прочность удержания материалов винтами.
Испытания на сопротивление моменту
Все испытания проводились на универсальной испытательной машине мощностью 50 кН при скорости нагружения 6 мм / мин (рис.3). В установке для испытания на растяжение нижняя часть каждой из двух опор шарниров была помещена на ролики так, чтобы два соединительных элемента могли свободно перемещаться наружу и оставаться свободными от ограничений при нагрузке на шарнир. Нагрузка продолжалась до тех пор, пока в образцах не произошло разрушение или полное разделение. Значения предельной приложенной нагрузки, F , измеренные в Н, были преобразованы в соответствующие значения моментного сопротивления с помощью выражений M c = L c x F и M t = L t x F / 2, для сжатия и растяжения соответственно. M c и M t , измеренные в Нм, представляют собой моментные сопротивления для образцов, подвергнутых нагрузкам сжатия и растяжения, соответственно. Моментные рычаги ( L c , L t ) были рассчитаны как 0,129 м (панель толщиной 18 мм), 0,130 м (панель толщиной 16 мм) и 0,131 м (панель толщиной 15 мм) и использовались в качестве постоянное значение, соответственно, для нагрузки сжатия и растяжения.
Рис.3. Диаграмма, показывающая формы нагружения образцов, подвергнутых сжатию (а) и растяжению (б). Буква «R» обозначает силу реакции (размеры в мм).
Статические испытания четырехэлементных шкафов
Четырехэлементные шкафы были испытаны при статических нагрузках, и были составлены диаграммы сила-прогиб для оценки жесткости четырехэлементных шкафов. На рис. 2 показаны условия нагрузки и поддержки четырехэлементных шкафов.
Все испытания проводились на универсальной испытательной машине с усилием 50 кН при скорости нагружения 6 мм / мин. Нагрузка прикладывалась со свободного угла. Сам четырехсторонний шкаф был закреплен на этом основном каркасе с помощью трех опор. Эти опоры были собраны на столе с помощью гаек и болтов. Сначала были протестированы некоторые случаи для определения предельных разрушающих нагрузок. Значения силы и прогиба в случаях регистрировались до 70% — 80% этих предельных разрушающих нагрузок. В ходе статических испытаний были зафиксированы виды отказов и прогибы в вертикальном ( Y ) направлении. Значения жесткости были рассчитаны в Н / мм путем нескольких измерений нагрузки vs. отклонение в упругом, очевидно линейном диапазоне, а затем сопоставление их с линией регрессии методом наименьших квадратов.
Статистический анализ данных
Несмотря на то, что в исследовании использовались три различных типа панелей, в анализе было описано шесть уровней для одного фактора (типа панели), чтобы практически сопоставить влияние толщины с фактором типа панели; , то есть вместо двух факторов (тип панели и толщина панели) использовалась односторонняя процедура ANOVA. Основная причина, побудившая использовать этот подход, заключалась в том, что толщина панелей PW отличалась от других. Подводя итог, процедуры односторонней ANOVA общей линейной модели были выполнены для отдельных данных для моментных сопротивлений угловых соединений L-типа при нагрузках сжатия и растяжения и значений жесткости четырехэлементных шкафов, чтобы проанализировать влияние типа панели на моментное сопротивление. угловых соединений L-образного типа и значений жесткости четырехчленных шкафов.
ANOVA показали, что моментные сопротивления угловых соединений L-типа и жесткость четырехкомпонентных шкафов статистически различались на уровне значимости 5% (таблица 2).
Процедура множественных сравнений с наименьшей значимой разницей (LSD) на уровне значимости 5% была проведена для определения средних разностей моментных сопротивлений угловых соединений и значений жесткости четырехэлементных шкафов, испытанных с учетом результатов дисперсионного анализа, упомянутых выше.
Таблица 2. Результаты дисперсионного анализа для моментных сопротивлений при нагрузках на сжатие и растяжение, а также значения жесткости
РЕЗУЛЬТАТЫ И ОБСУЖДЕНИЕ
Физико-механические свойства материалов, использованных в испытаниях, приведены в таблице 3 . Модуль сдвига панелей МДФ показал более высокие значения, чем у панелей PW и PB. На жесткость четырехкомпонентных шкафов влиял модуль сдвига панелей. Наивысшие значения модуля сдвига наблюдались для МДФ 18 мм, а самые низкие значения были получены для 18 мм ПБ. За исключением панелей МДФ для значений модуля сдвига, было определено, что менее толстые панели давали более высокую жесткость, чем панели с более толстыми панелями, с точки зрения как модуля сдвига, так и значений прочности IB (внутреннего связывания).
Для панелей МДФ, 18-миллиметровые панели в среднем примерно на 8% больше, чем 16-миллиметровые. В аналогичном исследовании сопротивления изгибающему моменту угловых соединений было показано, что значения модуля упругости и модуля жесткости МДФ выше, чем у ПБ (Maleki et al. 2012), как и ожидалось.
Таблица 3. Физические и механические свойства панелей, использованных в исследовании
Сила удержания винтов (от края и торца) из PB, MDF и PW, использованных в испытаниях, представлена в Таблице 4.16 мм PB и 15 мм PW дали более высокую прочность удержания винта от края, чем 18 мм PB и PW, соответственно. Для панелей МДФ различия в силе удержания шурупов на кромках панелей 16 мм и 18 мм не были значительными. Можно ясно видеть, что согласно результатам, было обнаружено, что сила удерживания панелей винтами от края и прочность панелей IB значительно больше влияют на жесткость четырехэлементных шкафов, чем на модуль сдвига панелей. Таким образом, можно утверждать, что жесткость четырехэлементных шкафов больше зависела от жесткости соединения, чем от свойств отдельных панелей, таких как MOE и модуль сдвига.Согласно результатам, приведенным в таблице 3, 15-миллиметровые панели PW показали на 34% более высокую прочность IB, чем 18-миллиметровые панели PW, и, согласно таблице 4, панели 15 мм PW показали на 20% большую прочность удержания винтов от края, чем панели. панелей PW 18 мм.
Логично предположить, что сила удержания винта от края и прочность панелей IB отражают жесткость соединений. Сила удержания винтами 18 мм панелей МДФ и PW с лицевой стороны показала более высокие значения, чем 16 мм МДФ и 15 мм PW, соответственно.Напротив, для панелей PB 16 мм панели давали более высокую прочность крепления винтами с лицевой стороны, чем панели 18 мм. Vassiliou (2005) аналогичным образом обнаружил, что MDF имеет более высокую прочность крепления винтов, чем PB. Они сравнили различные типы винтов и определили, что МДФ обеспечивает на 40% большую прочность крепления винтов, чем ПБ, для винтов того же типа.
Таблица 4. Прочность удерживания винтов панелей, используемых при изготовлении образцов
* Значения в скобках являются коэффициентами вариации (COV)
Установлено, что режимы разрушения угловых соединений L-типа аналогичны.Все совместные отказы произошли между 60 и 90 секундами. Угловые соединения L-типа открывались медленно, а не внезапно. Разрушение соединений, изготовленных из PB, MDF и PW, началось с вдавливания головок винтов в торцевой элемент с последующим отрывом винтов от стыковых элементов вместе с некоторым материалом сердечника вместе с расщеплением кромок вокруг винтов. Образцы PB показали большее количество материала сердечника, прикрепленного к винтам, чем образцы MDF и PW. Раскол вокруг винтов у образцов МДФ был больше, чем у ПБ.
При испытаниях на жесткость к корпусам прикладывались статические нагрузки до 70–80% предельных разрушающих нагрузок; следовательно, ожидаемые типичные прогибы в отдельных панелях и целых корпусах произошли.
Таблица 5. Среднее моментное сопротивление угловых соединений L-типа и жесткость четырехэлементных шкафов
Критическое значение LSD для растяжения = 7,849 Нм, для сжатия = 8,826, для жесткости = 41,21 Н / мм , HG: однородная группа
Средние значения моментного сопротивления угловых соединений L-типа и значения жесткости четырехэлементных шкафов и их коэффициенты вариации приведены в таблице 5.Результаты испытаний показали, что на моментное сопротивление угловых соединений L-типа и значения жесткости четырехэлементных шкафов существенно влияли тип панели и ее толщина. В целом, угловые соединения L-образного типа и четырехэлементные шкафы, изготовленные из 15 мм PW, показали самые высокие показатели.
Значительную разницу между PW 15 мм и 18 мм можно объяснить разницей в толщине. Также можно предположить, что 15 мм PW имеет более высокое качество изготовления, где 15 мм PW в основном демонстрируют более высокие механические свойства (MOE, MOR и IB), чем 18 мм PW.Образцы, изготовленные из МДФ, показали более высокие значения, чем образцы, изготовленные из ПБ, для двух уровней толщины. Эти различия в значениях моментного сопротивления и жесткости можно объяснить различиями в плотности и механических свойствах, таких как прочность на изгиб ( MOR ), прочность внутренней связи ( IB ), модуль сдвига ( G ) и прочность крепления винта панели. Фактом является то, что большинство прочностных свойств, особенно крепление винтов, у PW выше, чем у MDF, аналогично плотность и большинство прочностных свойств MDF выше, чем у PB.
Моментное сопротивление угловых соединений L-типа
Таблица 5 дает сравнительные ранжированные средние значения моментного сопротивления угловых соединений L-типа при растяжении и сжатии с учетом влияния взаимодействия типа панели и толщины панели. Наибольшие моментные сопротивления были получены у образцов 15 мм PW, 16 мм MDF, 18 мм PW и 18 мм MDF при растягивающих нагрузках. Однако различия моментных сопротивлений между образцами, построенными из упомянутых панелей, не были статистически значимыми.Наименьшие моментные сопротивления были получены у образцов из ПБ толщиной 18 мм. При сжимающих нагрузках наибольшие моментные сопротивления наблюдались у образцов PW 18 мм. Наименьшие значения моментного сопротивления были получены для образцов из полибутилена толщиной 18 мм как при растягивающих, так и при сжимающих нагрузках.
Группировка данных для соединений, подвергшихся испытанию на растягивающую нагрузку, дала среднее моментное сопротивление 81,42 Нм, в то время как группировка данных для соединений, испытанных при сжимающей нагрузке, дала среднее значение предельного моментного сопротивления, равное 73.70 Нм.
Жесткость четырехэлементных шкафов
Таблица 5 показывает ранжированные средние сравнения значений жесткости четырехэлементных шкафов, испытанных в отношении взаимодействия типа материала и толщины. Результаты показали, что самые высокие значения жесткости были получены в четырехэлементных шкафах PW толщиной 15 мм — 196,6 Н / мм, что на 52,4% выше, чем у следующего по величине материала по жесткости — МДФ 16 мм. Предполагается, что при изготовлении корпусов произошли некоторые отличия по жесткости соединений.Наименьшие значения жесткости были получены в четырехсекционных шкафах из ПБ 18 мм.
Согласно результатам испытаний, четырехэлементные шкафы толщиной 15 или 16 мм показали значительно более высокие значения жесткости по сравнению с панелями толщиной 18 мм. Значения жесткости четырехэлементных шкафов PB 16 мм были выше, чем четырехэлементных шкафов PW 18 мм. Лучший материал — PW, оптимальная толщина — 15 мм. Как и следовало ожидать, значения модуля жесткости отдельных панелей и полных четырехэлементных шкафов сильно взаимосвязаны.
В целом было обнаружено, что толщина в большей степени влияет на жесткость четырехэлементных шкафов. При увеличении толщины панелей жесткость четырехэлементных шкафов значительно уменьшилась.
ВЫВОДЫ
В этом исследовательском исследовании было исследовано влияние типа панели и толщины панели на моментное сопротивление угловых соединений L-типа и значения жесткости четырехэлементных шкафов, предполагая, что все угловые соединения L-типа и четырехэлементные шкафы были собраны и изготовлены. однородно.
Результаты показали, что четырехэлементные шкафы, изготовленные из панелей толщиной 15 мм или 16 мм, имеют более высокие значения моментного сопротивления и жесткости, чем панели толщиной 18 мм. Кроме того, было определено, что среди материалов PW дает более высокие характеристики, чем MDF и PB, как и ожидалось. Поэтому при производстве корпусов можно рекомендовать 15 мм PW в качестве типа панели вместо 18 мм и МДФ, ПБ. Однако производственные затраты и непокрытые поверхности PW — это проблемы, которые необходимо преодолеть, чтобы использовать их в мебельной промышленности.
Наконец, можно сделать вывод, что механические свойства конструкции углового соединения четырехэлементных шкафов с винтами сильно зависят от типа и толщины панели, если другие факторы (размер винта, типы винтов, центры винтов, и т. Д. .) Остаются постоянными. . Это исследование предоставляет ключевую информацию о том, как на угловые соединения корпусной мебели и свойства жесткости влияли тип и толщина панели. Дальнейшая работа будет включать изучение потенциальных решений для использования четырехсторонних шкафов PW в мебельной промышленности.
ССЫЛКИ
Американское общество испытаний и материалов (ASTM). (2001). «Стандартные методы испытаний для оценки свойств древесных волокон и древесно-стружечных панелей», ASTM D1037-99.
Американское общество испытаний и материалов (ASTM). (2003). «Стандартные методы испытаний для прямого измерения содержания влаги в древесине и древесных материалах», ASTM D4442-92.
BioMatNet (2003). «Композитные панели с высокой добавленной стоимостью за счет переработки отходов лигноцеллюлозных материалов», проект QLK5-1999-01221.Заключительный отчет. Европейская комиссия. Брюссель.
Цай Л. и Ван Ф. (1993). «Влияние жесткости углового соединения на прогиб корпусной мебели», Holz als Roh- und Werkstoff 51, 406-408.
Экельман, К. А. (1967). «Мебельная механика: анализ панельной корпусной и корпусной мебели», Purdue Univ. Agri. Expt. Sta. Прог. Репт. №: 274, West Lafayette, Ind.
Экельман, К. А. (2003). «Учебное пособие по проектированию изделий и прочному проектированию мебели», Purdue Univ., Вест-Лафайет, Индиана, .
Erdil, Y.Z., Zhang, J., and Eckelman, C.A. (2002). «Удерживающая способность шурупов для фанеры и ориентированно-стружечной плиты», Forest Prod. J. 52 (6), 55-62.
Kasal, A., Zhang, J., Yuksel, M., and Erdil, Y.Z. (2008). «Влияние размеров шурупов на несущую способность и жесткость пятисторонней мебели, изготовленной из ДСП и ДВП средней плотности», Forest Product Journal 58 (10), 25-32.
Котас, Т.(1957). «Теоретический и экспериментальный анализ конструкции шкафа», Совет по развитию мебели, Res. Репт. №: 6, Лондон .
Котас, Т. (1958a). «Жесткость корпусной мебели», Презем. Drzenwy. №: 10 и 11: стр. 10–14, 15–18, Варшава.
Котас, Т. (1958b). Руководство по дизайну корпусной мебели , Pergamon Press, Нью-Йорк.
Лин, С. К., и Экельман, К. А. (1987). «Жесткость мебельных корпусов с различными конструкциями шарниров», Forest Product Journal 37 (1), 23-27.
Maleki, S., Haftkhani AR, Dalvand M., Faezipour M. и Tajvidi M. 2012. «Сопротивление изгибающему моменту угловых соединений, построенных с помощью шлицевого соединения, при диагональном растяжении и сжатии», Journal of Forestry Research 23 (3), 481-490
Танкут, А. Н., Танкут, Н. (2009). «Исследования влияния типов крепежа, клея и композитных материалов на прочность угловых соединений в конструкции корпусной мебели», Материалы и конструкция 30, 4175-4182.
Танкут, А. Н., Танкут, Н. 2010. «Оценка влияния типа и толщины кромочной ленты на прочность угловых соединений в корпусной мебели», Материалы и конструкция 31, 2956-2963.
Статья подана: 4 апреля 2014 г .; Рецензирование завершено: 18 июня 2014 г .; Доработанная версия получена и принята: 20 августа 2014 г .; Опубликовано: 2 сентября 2014 г.
Использование деревянных композитных панелей в качестве основы для производства шкафов
Опубликовано февр.2017 | Id: NREM-5045
К Салим Хизироглу
Панели на древесной основе состоят из древесины или другого лигноцеллюлозного материала в разложенном состоянии. на мелкие элементы, а затем воссоздан для создания новых продуктов с использованием различных связующих под давлением и теплом. Производство древесных композитов, таких как ДСП и ДВП. постоянно растет в США.С. за последние 25 лет. Оба панельных продукта широко используются в качестве сырья в мебельной и корпусной промышленности. Этот информационный бюллетень суммирует основные этапы производства, свойства двух типов панелей, и их важность в производстве мебели и корпусов в качестве основы для тонких накладок.
ДСП
ДСП — один из наиболее часто используемых панелей в мебели и корпусах. производство, стеллажи и применение в строительстве, например, напольное покрытие, ламинат, вагонка.Основное сырье ДСП низкое качественные бревна и отходы производства изделий из дерева. Быстрорастущие виды, такие как осина и другие твердые или мягкие породы дерева, может использоваться в виде цельного дерева колотая композиция как сырье для производства ДСП. В большинстве случаев фишки измельчаются в частицы с помощью молотковой дробилки, дискового рафинера или измельчителя перед композицию (частицы, используемые для изготовления картона) сушат примерно до 3-5 процентное содержание влаги.Высушенный материал классифицируется по заданному размеры, такие как мелкие и крупные частицы, на ситах с разным размером ячеек. На рисунке 1 показано грохочение стружки перед измельчением частиц. Затем материал смешивают с карбамидоформальдегидом, которая является наиболее часто используемой внутренней смолой. Также добавляются воск и катализатор. в композицию во время процесса смешивания, чтобы улучшить стабильность размеров картон и обеспечить быстрое отверждение смолы в прессе.Смола и содержание парафина в конечном продукте колеблется от 5 до 9 процентов и от 0,4 до 1 процента, соответственно. После смешивания следует линия формования, на которой формируется композиция. в трехслойный рыхлый мат. На лицевые слои укладывается мелкий материал, а на лицевые слои — крупный. частицы составляют основной слой мата. На рисунках 2 и 3 показаны схемы трехслойный мат и непрессованная панель на формовочной станции.Многооткрывные прессы бывают также широко используется в производстве ДСП. Маты сжимаются от 600 до 740 фунтов на квадратный дюйм (фунтов на квадратный дюйм) давления при температуре от 350 до 380 ° F для От 4 до 6 минут в зависимости от типа отделки, толщины панели и других производств. переменные. Вырезание больших панелей на требуемый размер и шлифовка для получения равномерная толщина — это два последних этапа типичного производства древесно-стружечных плит.На рисунках 4, 5 и 6 показана общая технологическая схема производства древесностружечных плит. многократное раскрытие пресса и кондиционирование панелей после пресса соответственно.
Панели ДСП производятся различных размеров и уровней плотности. предоставление возможности конструировать конечные продукты с определенной необходимой панелью.Объем ДСП обычно выражается в квадратных футах поверхности для 0,75-дюймового толстая панель. Типичным условным обозначением является MSF (миллион квадратных футов) 0,75 дюйма, что означает до 1000 квадратных футов плиты толщиной 0,75 дюйма (M = 1000). На все панели можно ссылаться таким образом, умножив фактическую толщину на коэффициент преобразования.
Плотность панели — одно из важнейших свойств ДСП; это влияет как физические, так и механические свойства конечного продукта.Прочность на изгиб, внутренняя прочность сцепления, удерживающая сила винта и стабильность размеров значительно зависит от плотности доски. В таблице 1 показаны некоторые свойства коммерчески производство панелей ДСП и древесноволокнистых плит средней плотности (МДФ) как функция плотности доски. Как правило, фунт кубический фут используется в качестве меры плотности панелей. в отрасли. Например, если кусок ДСП имеет размер 8 на 15 дюймов 0.75 дюймов и весит 2,5 фунта, его плотность будет:
2,5 ÷ [(8 x 15 x 0,75) ÷ 1728] = 48 фунтов / фут3
(0,76 г / см3)
Рисунок 1 .Скрининг чипа. (Кортси Джорджия-Пасифик Корп.)
Рисунок 2. Схема трехслойного мата из ДСП.
Рисунок 3 . Коврик из непрессованного ДСП. (Кортси Джорджия-Пасифик Корп.)
Рисунок 4. Блок-схема типичного производства ДСП.
Рисунок 5. Пресс для ДСП с несколькими отверстиями. (Кортси Джорджия-Пасифик Корп.)
Рисунок 6 .Панельное кондиционирование.
Таблица 1 . Избранные свойства ДСП и МДФ. (Адаптировано из Composite Panel Association)
Тип и плотность панели | MOE (фунт / кв. Дюйм) | MOR (фунт / кв. Дюйм) | IB (фунт / кв. Дюйм) | Удерживающая поверхность винта (фунты) | Кромка крепления винта (фунты) |
---|---|---|---|---|---|
PB 50 фунтов / фут3 | 350 000 | 2,400 | 145 | 420 | 350 |
PB 40-50 фунтов / фут3 | 275 000 | 1 900 | 57 | 220 | 200 |
PB 40 фунтов / фут3 | 110 000 | 600 | 30 | 100 | НЕТ |
МДФ 50 фунтов / фут3 | 450 000 | 4 000 | 120 | 350 | 300 |
МДФ 40-50 фунтов / фут3 | 350 000 | 3 000 | 80 | 300 | 220 |
МДФ 40 фунтов / фут3 | 200 000 | 1,800 | 40 | 50 | 150 |
ДВП
ДВП изготавливается из рафинированного или частично рафинированного древесного волокна.Главным Процесс производства древесноволокнистых плит относительно аналогичен производству древесно-стружечных плит. Разница в том, что в качестве необработанного материала используются волокна — самый мелкий элемент древесины. материал при производстве ДВП, а не частиц. Чипы конвертируются к волокнам с использованием различных технологий и оборудования, такого как рафинеры с одним или двумя дисками, дефибраторы, рафинеры под давлением и атмосферные рафинеры.Фишки обработаны термически в одном из вышеуказанных единиц оборудования во время процесса дефибрации, где химический раствор попадает в древесину. После того, как волокно произведено и смешано со смолой следующий шаг — прессование мата, аналогичного мату из ДСП линия прессования, как показано на рисунке 7. Однако линия непрерывного прессования (процесс Mende) который производит панели с 0.Толщина от 125 до 0,150 дюйма очень распространена в ДВП. производство. Панели, изготовленные с использованием процесса Mende, широко используются в дверной обшивке. изготовление. Рисунок 8 — иллюстрация процесса Менде.
ДВП, как и ДСП, также можно классифицировать по плотности. Средняя плотность ДВП со средней плотностью от 0.От 70 г / см3 (44 фунт / фут3) до 0,80 г / см3 (50 фунтов / фут3) обычно используется в качестве основного промышленного сырья в прямой конкуренции с ДСП. МДФ отличается от других изделий из ДВП уникальным сочетанием. с умеренным профилем общей плотности и содержанием смолы, что обеспечивает отличное профилирование характеристики. Благодаря очень гладкой поверхности МДФ является превосходным субстратом для тонкие покрытия, такие как ультратонкая пропитанная меламином бумага, пленки, а также для прямого отделочные приложения.
Рисунок 7 . Мат из ДВП без прессования. (Courtsey Dominanee Industries, Pan Pacific Products)
Рисунок 8 .Схема непрерывного (Менде) процесса.
Панельные материалы в производстве корпусов
Как ДСП, так и МДФ являются основными панельными продуктами, широко используемыми в виде ламинированных панели в производстве корпусов, в том числе кухонных шкафов, офисной мебели, шкафы для спален, развлекательные центры и шкафы для хранения вещей.Ламинирование субстрата включает два процесса: самоклейку и склеивание. Шпон и высокого давления ламинаты (HPL), такие как Formica, являются примерами клеевых ламинатов, используемых в течение многих лет. в мебельной промышленности. HPL состоит из печатной бумаги, пропитанной термореактивную смолу, а затем прессуют под давлением от 1000 до 1400 фунтов на квадратный дюйм. Высокая долговечность и стойкость к истиранию HPL являются важными характеристиками таких накладок.Высококачественный шпон — это ламинированный продукт премиум-класса как для ДСП, так и для МДФ. Однако ее основным недостатком является высокая стоимость по сравнению с бумагой, пропитанной смолой. Тонкие бумаги, пропитанные меламиновой смолой, используются для покрытия поверхности панели применение тепла и давления в типичном процессе наплавки. Температура пресса и давление может варьироваться от 270 до 360 ° F и от 145 до 360 фунтов на квадратный дюйм в зависимости от наложения технические характеристики.
Панели ДСП с даже мелкими частицами, нанесенными на поверхностные слои, имеют относительно шероховатая поверхность по сравнению с МДФ. Поэтому ДСП — это более Подходящая основа для толстых покрытий, таких как шпон или ламинат высокого давления. В противном случае будут видны неровности основы, что в конечном итоге может уменьшить качество продукции.МДФ — идеальный панельный материал для тонких перекрытий, таких как как алюминиевая фольга, рисовая бумага или даже прямое нанесение тонкого слоя отделки на поверхность. Превосходные поверхностные характеристики МДФ делают его лучшей подложкой. для изготовления корпусов. На рисунках 9A и 9B показано сравнение шероховатости поверхности. профили из МДФ и ДСП, полученные с помощью профилометра игольчатого типа. Цифры 10 и 11 также представлены процесс наложения и различные панели с наложением соответственно.Такие панели широко используются в производстве корпусов.
Рисунок 9A . Типичный профиль шероховатости ДСП.
Рисунок 9B .Типичный профиль шероховатости МДФ.
Рисунок 10 . Процесс наложения.
Рисунок 11 .Накладные панельные изделия для изготовления корпусов.
Процесс ламинирования
Cauls, плоские металлические пластины с очень гладкой поверхностью или рельефными рисунками волокон древесины, используются для типичного процесса ламинирования.Качество тюля, чистота и температура являются ключевыми факторами, влияющими на качество ламинирования. Параметры пресса для ламинирования отображены в Таблице 2. Тканевая бумага с напечатанным рисунком текстуры древесины. примерно 20-30 г / м2 обычно используется в качестве верхнего слоя. Эти документы либо пропитанные смолой, либо ламинированные горячекатаные накладки. Иногда смоление бывает используется для улучшения качества поверхности панелей перед ламинированием.Смола панель предполагает пропускание панели под высоким давлением между двумя нагретыми и полированными. стальные ролики. Этот процесс приводит к тому, что смола становится жидкой, и пленка каландрируется. под действием стальных роликов и давления. Фольга — еще один пример оверлеи тяжелее тонкой бумаги (от 50 до 130 г / м2). Их обычно пропитывают с меламиновыми термореактивными смолами или без обработки для специальных применений.Фольги требуют клея для ламинирования и в промышленности обычно называются меламиновой бумагой.
Декоративный тяжелый винил, который может быть жестким или полужестким, также используется в качестве накладки. фильм. Он изготовлен из поливинилхлорида (ПВХ) и имеет толщину от 0,002 до 0,004 дюйма. Часто на нем предварительно тиснено разное тиснение и всегда требуется клей для приклеивания к основанию.Двухслойные сэндвич-пленки и оберточные пленки также обычно используются в качестве декоративного винила для облицовки панелей ДСП и МДФ.
Таблица 2 . Параметры ламинирования.
Ламинирующий материал | Температура (° F) | Давление (фунт / кв. Дюйм) | Время (сек) |
---|---|---|---|
Полиэстер | 280-330 | 175-200 | 50-200 |
Бумага высокой плотности | 290-300 | 170-200 | 200–250 |
Меламиновая бумага | 300-320 | 300-340 | 40-70 |
Заключение
Деревянные композитные панели с покрытием занимают большую долю рынка в деревообрабатывающей промышленности, и они играют важную роль в производстве мебели и корпусов.Далее подробно информацию об изготовлении композитных панелей и способах их наложения можно найти в следующей литературе.
Ассоциация производителей кухонных шкафов. 1899 Престон Уайт Доктор Рестон, Вирджиния 20191. www.kcma.org.
Ассоциация ламинирующих материалов.116 Лоуренс. Сент-Хиллсдейл, штат Нью-Джерси, 07642. www.lma.org.
Мэлони, Т. 1993. Современное производство древесностружечных плит и волокна сухим способом. Миллер Freeman Inc. Сан-Франциско.
Национальная ассоциация древесностружечных плит (NPA).1992. От начала до конца ДСП. 18928 Премьер Корт, Гейтерсбург, Мэриленд 20879.
Сучсленд, О. 1992. Практика производства древесноволокнистых плит. Справочник лесной службы Министерства сельского хозяйства США Справочник по сельскому хозяйству № 640. Вашингтон.
Ассоциация производителей изделий из дерева.175 State Rd.E. Вестминистер, Массачусетс 01473.
Салим Хизироглу
Доцент кафедры лесного хозяйства
Была ли эта информация полезной?
ДА НЕТМебель из шпона: все ли плохо?
Вы слышали кое-что о шпоне в нашей недавней публикации о типах древесины, но мы хотим копнуть глубже и рассказать вам, что это такое на самом деле.И это включает в себя развенчание главного мифа о шпоне: не все предметы мебели, в которых используется винир, низкого качества.
Но мы забегаем вперед. Продолжайте читать, чтобы узнать больше о шпоне (и ознакомьтесь с нашей подборкой великолепной деревянной мебели здесь).
Шпон — это кусок настоящего дерева, разрезанный на тонкий лист. Затем эти листы можно наносить на внешнюю поверхность другой цельной древесины, фанеры или МДФ (называемой подложкой). Это способ сократить стоимость мебели, поскольку вы можете просто взять тонкий слой более дорогой древесины и приклеить его к чему-то менее дорогому.Это делается путем нанесения тонкого слоя клея на основу, помещения фанеры на клей и давления с помощью пресса, пока клей не высохнет.
Высококачественный винир против низкокачественного
Шпонированная мебель может быть высокого качества, если основная древесина твердая — достаточно взглянуть на предметы 50-х и 60-х годов, которые до сих пор остаются сильными. Шпон также часто является единственным вариантом для некоторых прекрасных элементов мебели, таких как изогнутые ящики, подбор для создания уникального рисунка или использование дорогих экзотических пород дерева.Вы только посмотрите на этот красивый шпонированный комод от Skram.
Но и шпонированная мебель может быть некачественной. И, к сожалению, в наши дни гораздо больше шансов встретить плохо сделанный шпон. Самый верный показатель — цена: недорогие шпонированные предметы будут стоить около 1000 долларов, а качественная мебель — около 3000 долларов (или намного больше). Но помимо цены бывает сложно сказать, что вы покупаете в магазине. Вся фанерованная мебель в новом состоянии выглядит великолепно, вне зависимости от ее качества.
Как отличить
Качество шпона зависит от трех факторов: толщины шпона, адгезии шпона и основы, к которой он прикреплен. К сожалению, при покупке мебели трудно определить толщину и методы склеивания. Поэтому вместо того, чтобы пытаться использовать эти указатели в качестве рекомендаций по покупкам, используйте информацию как предостережение о возможных проблемах с недорогой шпонированной мебелью. К счастью, узнать, из чего сделан субстрат, относительно легко, и вы должны использовать эту информацию, чтобы найти более качественную шпонированную мебель.
- Толщина
- Чем толще облицовка, тем лучше — ремонт будет легче, так как вы можете слегка отшлифовать зазубрины, не обнажая находящийся под ними материал.
- Более тонкие виниры также подвержены сколам.
- Стандартная толщина шпона в США составляет 1/42 дюйма (0,6 мм или 0,024 дюйма), поэтому выбирайте виниры такого размера или толще.
- Международные стандарты намного меньше: 0,5 мм (0,0197 дюйма), что означает, что большая часть импортной мебели будет иметь более тонкий шпон, который более склонен к сколам и труднее ремонтируется.
- Адгезия
- Для прикрепления фанеры к основному куску дерева необходим клей.
- Виниры приклеиваются к более дешевому продукту (обычно фанере или МДФ) с помощью клея, а затем спрессовываются до высыхания.
- Существует несколько различных типов клеев, которые можно успешно использовать, но избегайте использования древесного шпона, приклеиваемого контактным цементом. Для приклеивания шпона следует использовать столярный клей или смолу.
- Клей должен быть распределен равномерно и иметь соответствующую влажность, чтобы не вызывать расширение шпона или основы.
- Плохое приклеивание клея может быть связано с проблемами с клеевой смесью, нанесением клея, временем высыхания или временем прессования.
- Плохая адгезия способствует отслаиванию и ослаблению шпона (небольшие микротрещины и выступы, возникающие при усадке и разбухании древесины).
- Подложка
- Основа — это то, к чему приклеивается шпон — это может быть просто менее дорогой массив дерева, но, скорее, это фанера или МДФ.
- Различия в содержании влаги в основе и облицовке могут вызвать так называемые проблемы с проверкой. Из-за содержания влаги древесина сжимается или разбухает, и если основание и шпон изменится по-другому, вы получите трещины и отслаивание.
- Как шпон, так и основание необходимо правильно высушить и поддерживать влажность на протяжении всего этапа прессования.
- Все детали должны храниться в экологически безопасных условиях до, во время и после нанесения шпона
- Мы говорили это раньше и скажем еще раз: избегайте MDF.
Плюсы шпонированной мебели
- Это экономичное решение для дорогих или экзотических пород дерева, таких как орех или зебрано.
- Вы можете создавать красивые рисунки с текстурой дерева, так как тонкие кусочки шпона можно легко разместить.
- Позволяет производителям создавать более сложные стили, например, с изогнутыми фасадами ящиков.
Минусы шпонированной мебели
- Большая часть фанеры на сегодняшнем рынке имеет низкое качество, он легко скалывается или имеет широкие микротрещины.
- Поскольку шпон стоит меньше, он часто является признаком того, что производитель мог урезать углы другими способами, например, используя МДФ или плохие столярные изделия.
- Повреждения трудно отремонтировать, так как древесина под ними другого сорта — любая морилка не будет выглядеть одинаково.
Как покупать шпонированную мебель
Хотя большая часть фанерованной мебели имеет низкое качество, это может быть отличным вариантом, если вы хотите, чтобы мебель была сделана из дорогих пород дерева или чего-то с изогнутым дизайном.Мебель, облицованная фанерным шпоном, может работать лучше, чем мебель из цельного дерева, в местах с очень влажными или сверхсухими условиями окружающей среды. Вот что нужно искать:
- Избегайте недорогой мебели из шпона, поскольку она, скорее всего, плохо сделана и подвержена сколам и трещинам.
- Избегайте любой фанерованной мебели из МДФ.
- Ищите фанеру толщиной не менее 1/42 дюйма или 0,6 мм.
- Осмотрите детали выставочного зала на предмет наличия сколов — это может быть видно на дверцах и ящиках.
Нравится то, что вы читаете? Посетите thestatedhome.com, чтобы сделать покупки из нашей коллекции мебели, произведенной в Америке.
Преимущества и недостатки мебели из МДФ
Мебель из массива дерева обычно считается красивой, вневременной и высококачественной. Будь то дуб, сосна или клен, есть множество вариантов использования дерева для мебели.
Для сравнения, МДФ (древесноволокнистая плита средней плотности) изготавливается из переработанных материалов таймера и волокон, смешанных с клеем на основе смолы и очень плотно спрессованных.
Обычно МДФ рассматривается как более дешевая альтернатива массивной древесине и часто считается более низким по качеству. Однако в последние годы наблюдается быстрое возрождение плоской мебели, производимой из МДФ. Это в значительной степени связано с более низкими материальными затратами, но также и с тем, что его легко хранить и компактно.
Итак, с преимуществами и недостатками как для массивной древесины, так и для МДФ, какой вариант лучше?
Содержание
В чем преимущества МДФ?
- Стоимость
Основным ингредиентом МДФ являются опилки и мелкая стружка других пиломатериалов.Все это собранные отходы процесса механической обработки, поэтому стоимость материала намного ниже, чем у фанеры и массивной древесины.
- Разнообразие размеров
Листы МДФ доступны в готовом виде в более чем 100 различных толщинах, от 2 мм до 60 мм. Широкий диапазон доступных опций позволяет очень легко получить толщину «дерева», необходимую для конкретного применения.Изображение предоставлено London Graphics с https: // www.londongraphics.co.uk
- Гладкая поверхность и разрезы
МДФ в процессе производства прессуется чрезвычайно компактно с большими стальными пластинами, что делает весь лист чрезвычайно плоским и гладким. Это делает МДФ идеальным вариантом для покраски, ламинирования или крепления шпона. После обрезки листов края остаются гладкими, тогда как у массивной древесины или фанеры края могут расколоться или иметь пустоты из-за естественных сучков и текстуры древесины.
- Сплошной материал
МДФ не имеет направленной текстуры, как фанера и массив дерева, что делает его идеальным для резки сложных деталей или лепки; другие материалы могут расколоться или разрез будет не таким гладким.
- Меньше проблем с короблением
В отличие от массивной древесины, МДФ останется прочным в помещениях с высокой влажностью и влажностью. Это связано с тем, что МДФ может постоянно сжиматься и расширяться, при этом различные части волокон не взаимодействуют друг с другом.
В чем недостатки МДФ?
- Уродливое сырье
Массив дерева славится своей поразительной природной красотой. МДФ — не самый привлекательный натуральный цвет, и ему не хватает характерных черт массивной древесины и фанеры.
- Ограничения по отделке
Если вы хотите подобрать существующую мебель с помощью морилки, лучше не использовать МДФ. МДФ впитает всю жидкость и не даст желаемого цветового эффекта. Лучше всего использовать этот материал, если планируется его покрасить.Изображение предоставлено Bunnings Warehouse через https://www.bunnings.com.au/
- МДФ впитывает воду
МДФ быстро впитывает воду из-за очень тонких волокон внутри плиты, которые могут вызвать разбухание МДФ и постепенную потерю своих структурных свойств.Изображение предоставлено DIY Exchange через https://diy.stackexchange.com/
- Слабый материал
МДФ не имеет направленной текстуры, которая придает массивной древесине и фанере прочность и структурную целостность. Несмотря на то, что многие стеллажи и шкафы переделаны из МДФ, они требуют прочного деревянного каркаса для поддержки или должны быть закреплены таким образом, чтобы он не провисал со временем.
- Трещины и расколы
При вкручивании МДФ необходимо соблюдать особую осторожность, так как он может треснуть или расколоться по волокнам.Перед ввинчиванием в МДФ необходимы направляющие отверстия, чтобы освободить место для шурупа и снизить вероятность раскола материала — хотя важно отметить, что МДФ все равно может расколоться, даже если вы используете обычный шуруп. Поскольку обычные шурупы конической формы по дереву будут раскалывать МДФ, необходим шуруп с прямым хвостовиком.Изображение предоставлено Celo Fixings через https://www.celofixings.com/
- Слабое крепление
Из-за очень тонких волокон получить надежное крепление при вкручивании в МДФ может быть очень сложно.Со временем винты могут начать раскачиваться, так как тонкие волокна вокруг винтовых креплений ослабнут. Это чаще встречается с петлями, которые крепятся к дверцам шкафов из МДФ.
- Содержит ЛОС
Клей, скрепляющий все волокна вместе, содержит формальдегид. При резке, шлифовке или механической обработке он выбрасывает много пыли, которая может вызвать раздражение легких и глаз. Долгосрочные эффекты могут включать рак легких, носа и горла.
Каковы преимущества массива дерева?
- Естественная красота
Одной из главных причин, по которой массивная древесина является таким популярным выбором для многих, является тот факт, что массивная древесина выглядит красиво.Натуральное зерно в куске дерева может показать характер, глубину цвета и полную уникальность, которую невозможно получить от искусственной древесины.Обеденный стол из натурального дуба крупным планом с прозрачным матовым лаком, зерно и рамка
- Долговечность на всю жизнь
Массив дерева — чрезвычайно прочный материал, который может служить долгое время благодаря своей прочности и прочности натурального волокна и волокон. Он не отслаивается и не трескается, как конструкционная древесина (МДФ, фанера и шпон), что в большинстве случаев приводит к необходимости замены стола.Массив дерева все еще можно поцарапать или повредить, но в большинстве случаев его можно легко восстановить. Большая часть мебели из массива дерева остается в домах гораздо дольше, что делает ее долгосрочным вложением.Изображение по зерну и кадру через Grainandframe.com
- Timeless
Цвет и внешний вид качественной мебели из натурального массива могут оставаться стильной на долгие годы. Массив дерева — чрезвычайно универсальный материал, поэтому его используют как в традиционных, так и в современных домах.Существует так много разных видов массивной древесины и видов отделки, которые можно применить к ним, чтобы они соответствовали определенному стилю интерьера. Если стиль или интерьер изменится, в большинстве случаев стол из цельного дерева можно отремонтировать по своему вкусу.
- Без агрессивных химических компонентов
Так как твердая древесина является натуральным материалом, она не содержит летучих органических соединений и химикатов, которые могут быть опасными для здоровья. Это поможет избежать потенциальной аллергии или реакции на пыль или частицы.
Какие недостатки у цельного дерева?
- Дорогой
Массив дерева дороже искусственных материалов, что во многом связано с длительными процессами подготовки древесины к использованию для изготовления мебели.Один из самых длительных этапов процесса — сушка древесины в сушильном шкафу и воздухом. Сушка древесины на воздухе иногда может длиться годами, в зависимости от толщины древесины. После этого древесина большинства мебельных сортов сушится в печи в течение 2-4 недель, на что может потребоваться много энергии. Твердая древесина — это медленнорастущее дерево, которое увеличивает цену по сравнению с быстрорастущей сосной.
- Стабильность
Дерево — это натуральный материал, поэтому он реагирует на изменения в окружающей среде. Когда окружающий воздух влажный, твердая древесина впитывает воду и начинает набухать, а когда влажность низкая и воздух сухой, твердая древесина теряет влагу и дает усадку.В крайних случаях это может привести к деформации древесины при высокой влажности или расколу и растрескиванию при слишком высокой влажности. Вот почему так важно контролировать влажность и избегать резкого повышения или понижения влажности, если в вашем доме цельная древесина.
Рекомендации по использованию МДФ
У каждого материала есть свои сильные и слабые стороны, поэтому трудно сказать, лучше ли один из них. В конце концов, важно использовать различные материалы для разных сценариев вашего дома.Мы рекомендуем использовать МДФ для следующей домашней мебели:
Окрашенные шкафы по зерну и каркасу через granandframe.com
- Мебель
МДФ — отличный материал для кухонных шкафов или других складских помещений в доме. Когда несколько досок надежно соединены вместе, они могут иметь улучшенную структурную целостность. Тем не менее, мы не рекомендуем использовать их для тяжелых предметов хранения, таких как скамейки, так как они с большей вероятностью сломаются.
- Стеллажи
Из МДФ можно сделать хорошие полки — фактически, из него можно сделать фантастические плавающие полки в нишах. Очень важно, чтобы любые полки из МДФ имели основу из массива дерева, чтобы они не провисали посередине.
- Декоративная или детализированная лепнина
МДФ идеально подходит для плинтусов, наличников и других декоративных элементов в вашем доме. У них гладкая, ровная и однородная поверхность, которая отлично смотрится после окрашивания.
Рекомендации по использованию массива дерева
Массив дерева — отличный выбор для мебели, несмотря на то, что он дороже других материалов. Мы считаем, что цельная древесина стоит вложенных средств, особенно для предметов мебели, которые являются несущими или выставленными на обозрение. Прочность и долговечность не имеют себе равных по сравнению с МДФ. На самом деле, естественная красота цельного дерева делает его стоящим, особенно если это предмет мебели, который всегда выставлен на обозрение.
Изображение по зерну и кадру через GrainandFrame.com
- Несущая способность
Благодаря твердому, прочному и износостойкому естественному состоянию массивная древесина отлично подходит для изготовления несущих предметов мебели. Так что это идеальный материал для скамей, стеллажей, шкафов и комодов.
- На выставке
Благодаря естественной красоте массива дерева, он лучше всего подходит для центральных мест или участков, которые всегда присутствуют в ваших домах.Например, такие предметы, как журнальные столики, обеденные столы, письменные столы или другая мебель, которые, по вашему мнению, должны выглядеть великолепно.
Хотя МДФ, производимый сегодня, имеет тенденцию быть намного прочнее, чем было много лет назад, его прочность по-прежнему несравнима с твердой древесиной. Натуральная текстура массивной древесины — это то, что дает высокий уровень прочности конструкции, которого не хватает МДФ. Мы не рекомендуем использовать МДФ для тяжелых предметов, так как со временем они могут прогнуться, потрескаться или сломаться. Шпонированные или ламинированные изделия из МДФ часто склонны к образованию сколов по краям со временем и часто не подлежат повторной полировке.
Несмотря на то, что древесина часто намного дороже, она прослужит намного дольше, чем МДФ, и иногда может оказаться вложением всей жизни в семейный дом. В большинстве случаев массивную древесину можно легко отполировать или отремонтировать, если она поцарапана или повреждена, однако важно обеспечить постоянный уровень влажности и избегать попадания прямых солнечных лучей, так как это может навсегда повредить мебель из цельной древесины.
Одна из вещей, которые нам больше всего нравятся в массиве дерева, — это естественная красота каждого изделия.Узоры текстуры всегда разные, поэтому вы гарантированно получите что-то совершенно уникальное, созданное специально для вас.
Если вы решили, что у вас стол из цельного дерева, вам может быть интересно наше руководство по теме «Сосна против дуба».
Как выбрать размер и толщину фанеры
Этот пост является частью Руководства Plyco по фанере.
Недооцененный и часто недооцениваемый аспект, когда дело доходит до выбора материалов для предстоящего проекта, — это покупка фанеры правильной толщины и размера листа.Правильный размер фанеры — необходимость, но бывает сложно учесть все цифры, если вы не опытный ветеран. Очевидно, вы хотите купить достаточно фанеры, чтобы у вас не закончилось ее производство до того, как вы дойдете до завершения, но вам также необходимо правильно определить свойства и размеры фанеры.
Редко бывает так просто, как выбрать случайное число или решить, хотите ли вы, чтобы что-то было толстым или тонким. Для некоторых областей применения выбор правильной толщины поможет вашему конечному продукту собираться более плавно и может избавить вас от некоторых потенциальных проблем в будущем.Никто не будет счастлив, когда на полпути к созданию чего-то вы поймете, что приобретенная вами фанерная плита слишком тонкая и недостаточно прочная, чтобы держать форму, или когда вы покупаете кучу фанерных панелей, чтобы понять, что они слишком толстые, и надеваете их. не подходит!
Чтобы помочь вам избежать этих потенциальных ловушек, мы рассмотрим, как выбрать правильную толщину фанеры для вашего следующего проекта. Наши специалисты по фанере в магазинах всегда рады помочь покупателям выбрать фанеру, соответствующую их потребностям, но иметь под рукой как можно больше знаний перед тем, как приступить к проекту, — отличная идея для планирования на будущее.
Подготовка к проекту
Первое, что вам нужно иметь в виду, когда речь идет о толщине фанеры, это то, что почти всегда будет небольшая разница. Производители всегда будут пытаться точно определить толщину, но из-за особенностей производства фанеры это не всегда возможно. Процесс шлифования обычно влияет на толщину, поскольку он не является полностью точным, и, как и любое деревянное изделие, он будет поглощать и терять влагу, что может повлиять на размер изделия.Однако, несмотря на эти различия, есть шаги, которые вы можете предпринять, чтобы заранее спланировать свои действия. Замерить фактическую толщину листа штангенциркулем — отличная идея. Также рекомендуется сделать пробные надрезы, если это возможно, чтобы узнать, будет ли ваша фанера плотно прилегать к ней или нет.
Важно предпринять эти профилактические меры, чтобы убедиться, что время строительства не подошло и вы не обнаружите, что ваши фанерные листы не собираются его резать, но не менее важно знать, на какую толщину вы должны смотреть. для определенных приложений.
Шкафы и мебель
Гардероб, созданный из фанеры Plyco’s Black Birch Film Face Plywood от BM Hall Kitchens
Шкафы и мебель обычно имеют наибольшую свободу действий при выборе толщины. Эти проекты обычно хранятся в безопасных местах внутри и не подвергаются слишком большому количеству опасностей. Мы обнаружили, что шкафы чаще всего изготавливаются из фанеры толщиной 12 мм. Требуемая толщина может варьироваться в зависимости от размера вашего шкафа, так как чем длиннее полки, тем толще вам понадобится фанера, поскольку она гарантирует, что лист не провиснет под давлением.То же самое касается и самостоятельных полок!
Мебель из фанеры
Когда дело доходит до мебели, вы обнаружите, что фанерный лист толщиной от 18 до 24 мм идеально подходит для сборки столов, в то время как в наборе чертежей будет использоваться комбинация фанеры 6 мм и фанеры 12 мм. Толщина других предметов мебели в основном определяется индивидуально. Если вы хотите создать что-то, что должно быть прочным и выдерживать изрядный вес, например, этот сервант от австралийского дизайнера мебели Мэтта Блатта, вам подойдет более толстый лист фанеры.С другой стороны, декоративные элементы, на которые не будет давить вес, обычно подходят для нижней части шкалы толщины.
Стены из фанеры
Если вы хотите немного приключений и поставить несколько фанерных стен, вы должны стремиться к фанере как минимум толщиной 12 мм, поскольку это стандартное требование.