Наша компания производит и поставляет ППУ скорлупы для теплоизоляции трубопроводов водоснабжения и отопления диаметром от 15 до 1220 мм. Изделия изготавливаются трех видов: без покрытия, с покрытием из фольги или стеклопластика. Скорлупа представляет собой полые полуцилиндры или сегменты длиной 1 м. В зависимости от диаметра трубы изделие будет состоять из одной, двух, трех или четырех частей. Каждый сегмент имеет выборку в четверть размера по периметру. Такая конструктивная особенность помогает избегать образования щелей и зазоров при проведении работ. Теплоизоляция трубопроводов – способы монтажаМонтаж теплоизоляции может производиться тремя способами:
Физико-механические свойства
Заключение: продукт соответствует требованиям ТУ 2293-002-42836534-2000 Примечание:
Последовательность работСкорлупы ППУ предназначены для теплоизоляции трубопроводов тепловых сетей и систем горячего водоснабжения (как в надземной, так и в подземной прокладке) Стоит отметить, что сам монтаж не представляет собой абсолютно никаких трудностей.
Уточняйте наличие готовых теплоизоляционных скорлуп и плит ППУ и их цену у менеджеров по телефонам в Москве: |
Теплоизоляция трубопроводов.
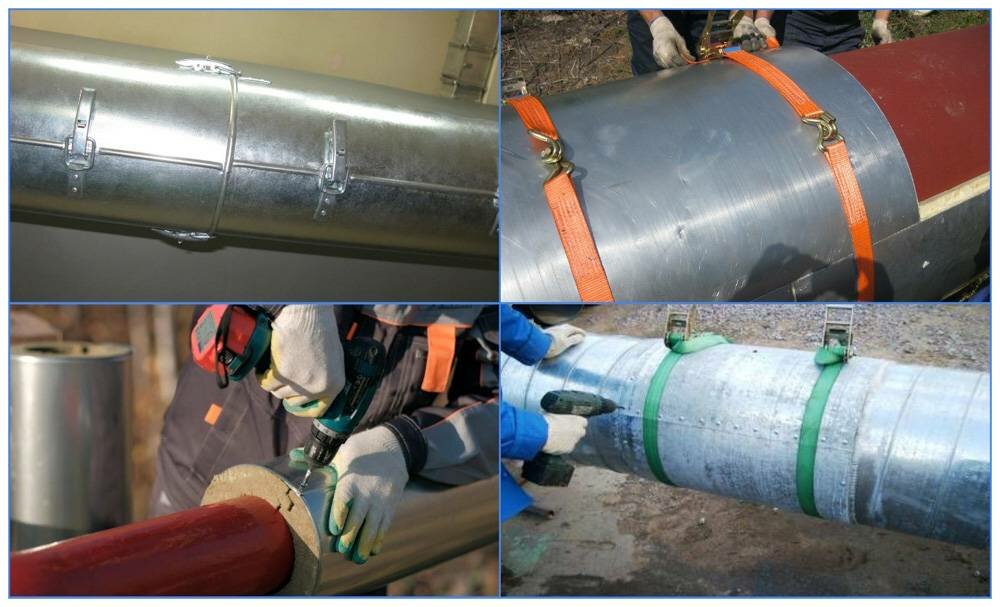
альбом технических решений
Утепление трубопроводов различного назначения (канализационных, водных, для отопления) — важное условие нормального функционирования как частного дома, так и многоэтажных зданий, строений общественного типа. В качестве утеплителя для труб сегодня наибольшей популярностью пользуются скорлупы из пенополистирола.
Многие не понимают, зачем нужно утеплять, например, трубы для горячей воды, ведь энергоноситель в них и так горячий и сам прогревает конструкцию, поэтому замерзнуть он не сможет даже в самые суровые морозы. Теплоизолирующий материал способствует снижению теплопотерь при прохождении энергоносителя от источника выработки тепловой энергии до потребителя. К тому же, и это весьма важно в наше время, когда стоимость газа и электричества вырастает каждые полгода, теплоизоляция труб поможет значительно сэкономить на счетах за отопление.
Утеплитель такого типа получил свое название — «скорлупа», за особенность внешнего вида и применения. Выглядит продукция как трубка, из пенополистирола.
Она может быть разрезана на 2, 3 или 4 части. Для надежности стыковки на краях разрезов имеются пазы. Сам цилиндр просто надевается на трубу (не важно, какую именно) — вот и весь процесс работы.
Таким образом применение скорлупы являет собой предельно простую технологию, которую можно использовать и самостоятельно. «Скорлупа» из пенополистирола для утепление трубопроводов имеет ряд преимуществ перед своими аналогами.
ПРЕИМУЩЕСТВА
Теплоизоляция
Влагостойкость
Легкость монтажа
Малый вес
Не поддерживает горение
Экологически безопасен
Экономическая выгода
НАША ПРОДУКЦИЯ
ЗАДАЙТЕ ВОПРОС
* — обязательное заполнение
Нажимая кнопку «Отправить» Вы даете согласие на обработку своих персональных данных.
Скорлупа ППУ — Изоляция
Скорлупа ППУ
Теплоизоляция трубопроводов скорлупами ппу
Скорлупа ппу является одним из самых популярных теплоизоляционных материалов для трубопроводов. Сама скорлупа представляет собой полые полуцилиндры, которые прикрепляются на трубопровод снаружи.
Скорлупы изготавливаются для каждого диаметра трубопровода и имеют различную толщину. В представленной таблице отображены наиболее популярные диаметры скорлуп.
Таблица 1 — Стандартные размеры скорлуп из пенополиуретана
Внешний диаметр трубопровода, мм |
Толщина стенки теплоизоляции, мм |
Длина изделия, мм |
25 | 20 | 1000 |
32 | 30 | 1000 |
42 | 30 | 1000 |
57 | 30 | 1000 |
76 | 30 | 1000 |
89 | 30 | 1000 |
108 | 30 | 1000 |
114 | 30 | 1000 |
133 | 30 | 1000 |
159 | 30 | |
219 | 30 | 1000 |
273 | 50 | 1000 |
325 | 50 | 1000 |
377 | 50 | 1000 |
426 | 50 | 1000 |
530 | 50 | 1000 |
630 | 50 | 1000 |
720 | 50 | 1000 |
820 | 50 | 1000 |
1020 | 60 | 1000 |
1220 | 60 | 1000 |

Кроме стандартных толщин и диаметров мы можем изготовить скорлупы на заказ с требуемыми параметрами и геометрией(например с желобом под информационный канал или трубу-спутник).
Скорлупы изготавливаются как без покрытия, так и с покрытием какого-либо материала. Скорлупы без покрытия чаще всего используются в помещениях, или в случае, когда трубопровод дополнительно будет покрываться защитным материалом. Скорлупы с покрытиями, а это, как правило, фольга или стеклопластиковая ткань, применяют на открытом воздухе. Пенополиуретан в таких скорлупах закрыт от солнечного света, что увеличивает срок его эксплуатации. К тому же, такая скорлупа более устойчива к механическим воздействиям.
Преимущества скорлупы ппу
Пенополиуретан является самым эффективным теплоизоляционным материалом. А выполненные из жесткого ппу скорлупы для трубопровода лучший на сегодняшний день способ утеплить трубопровод.
1. Минимальная теплопроводность
Пенополиуретан обладает самым малым коэффициентом теплопроводности – 0,021 Вт/м К. Теплоизоляция из пенополиуретана в несколько раз превосходит традиционные материалы для изоляции труб(мин. вата, пенопласт, Rockwell, и прочие). Многократные испытания показывают, что применение пенополиуретана при изоляции трубопроводов – экономически выгодное и быстро окупаемое мероприятие.
2. Долговечность
Срок эксплуатации пенополиуретанового покрытия без защиты от УФ-лучей составляет 10-15 лет. Если солнечный свет отсутствует (например, в помещении), или ппу закрыт(скорлупы с покрытием), то срок увеличивается в 2 раза. Такими показателями не обладает ни один материал, применяемый при утеплении трубопроводов. Пенополиуретан обладает великолепной морозостойкостью – до 1000 циклов замораживания / размораживания с сохранением эксплуатационных свойств. Такая теплоизоляция экономически выгодна так как не требует никаких ремонтных работ в ходе эксплуатации.
3. Защита от влаги
Жесткий пенополиуретан, из которого производятся скорлупы, имеет закрытопористую структуру. Благодаря этому, скорлупы не только держат тепло, но и не допускают проникновению влаги. Правильно смонтированные скорлупы являются еще и защитой от внешней коррозии трубы.
4. Биологическая стойкость
Пенополиуретан – материал органического происхождения, но может быть эксплуатироваться в непосредственной близости с грунтом, растительностью без опасности возникновения грибков, плесени и т.п. Кроме того скорлупы из ппу, абсолютно не подвержены действиям мелких грызунов, бактерии.
5. Широкий температурный диапазон
Пенополиуретановые скорлупы могут выдерживать температурный режим от -180 до +200 град с сохранением свойств и структуры. Это позволяет применять такую теплоизоляцию в различных отраслях промышленности и хозяйства.
6. Безопасность
Пенополиуретан давно применяется по всему миру как материал безопасный и экологически чистый. Он не выделяет вредных веществ и запаха. Поэтому он безопасен как для окружающей среды так и для живых организмов. Пенополиуретаны относятся к классу горючести Г2, Г3 или Г4, в зависимости от материала, используемого при производстве. Соответственно, скорлупы имеют свойства от «самозатухающих» до «трудногорючих».
7. Минимальные затраты на монтаж
Монтировать скорлупы достаточно легко, и не вызывает больших трудозатрат. Бригаде из 2х рабочих за рабочую смену удается провести изоляцию до 200 метров трубопровода.
Наша ценовая политика достаточно гибкая и зависит от особенностей именно Вашей заявки(общий объем, желаемые сроки поставки и многое другое). Поэтому нам важно услышать Ваши пожелания прежде чем назвать стоимость заказа. Отправляйте Ваши заявки на [email protected], [email protected].
Утепление трубопроводов полуцилиндрами (скорлупами) из пенополиуретана (ППУ)
Эффективная изоляция труб отопления достигается путем применения пенополиуретановых полуцилиндров (скорлуп) Данный метод применим для утепления труб самых разнообразных видов. ООО «Химэкселен» производит полуцилиндры из пенополиуретана с различным покрывным слоем. В качестве покрывного слоя используется рубероид, пергамин, фольгопергамин. Также возможно изготовление пенополиуретановых полуцилиндров без покрытия.
Теплоизоляция трубопроводов данным способом эффективна и выгодна за счет высоких технических характеристик полуцилиндров. Пенополиуретановые полуцилиндры рассчитаны на эксплуатацию в широком диапазоне температур: -150…+120 °С. Коэффициент теплопроводности – низкий, за счет чего достигается повышенная теплоизоляция для труб (трубная изоляция). Изготавливаемые нами полуцилиндры из пенополиуретана – прочны и надежны. Они способны выдержать напряжение до 350 кПа.
Мы изготавливаем следующие виды диаметров: 57, 76 , 89, 108, 133, 159, 219, 273, 325, 530 мм. Длина пенополиуретановых полуцилиндров фиксированная – 1000 мм. Есть возможность изготовления полуцилиндров из ППУ любой необходимой вам плотности. По желанию Заказчика мы можем выполнить монтаж полуцилиндров.
Заказать полуцилиндры можно по телефонам: +38 (050) 428-51-24, +38 (050) 428-51-25, +38 (096) 25-88-495, +38(068)634-24-81.
Сборка скорлупы — утепление для труб
Диаметр пенополиуретановых полуцилиндров (скорлуп) для изолируемого трубопровода от 18 до 1020мм. Длина – 1000мм.
Технические характеристики пенополиуретановых скорлупДиапазон рабочих температур | от -150 до +120 °С |
Кажущаяся плотность | 50-55 кг/м 3 |
Коэффициент теплопроводности | не более 0,028 Вт/мк |
Водопоглощение | не более 4% |
Объемная доля закрытых пор | не менее 94% |
Разрушающее напряжение | не менее 350 кПа |
Имеем возможность производить полуцилиндры (скорлупы) из ППУ необходимой для Вас плотности.
Диапазон рабочих температур
основное предназначение и преимущества использования
Одним из наиболее эффективных на сегодняшний день методов теплоизоляции для труб можно назвать скорлупы ППУ (пенополиуретановые цилиндры).
Их используют, прежде всего, для эффективной и быстрой теплоизоляции смонтированных трубопроводов, диаметр которых составляет 15 — 1420 мм, при этом расчетные параметры теплоносителя находятся в пределах +120°С. Осуществляется монтаж на месте проведения работ и характеризуется высокой производительностью и низкой трудоемкостью.
Стоит отметить, что теплоизоляционные пенополиуретановые скорлупы нашли свое применение также в изоляции канализационных систем, водоводов и нефтепроводов.
Преимущества соединений труб ППУ при помощи скорлуп
ППУ изоляция труб с использованием скорлуп имеет ряд неоспоримых достоинств:
— возможно проводить демонтаж в любое время года.
— процесс монтажа изоляции никоим образом не зависит от погодных условий.
— такой вид изоляции труб использовать можно не один раз.
— в случае аварийной ситуации всегда есть возможность быстрого доступа к повреждённому участку, что подтверждает высокую производительность такого способа изоляции.
— снижение в 5-6 раз времени монтажа изоляции трубопроводов
— невысокая трудоёмкость при монтаже
Соединение труб ППУ при помощи клея
Полуцилиндры соединять между собой можно при помощи специального полиуретанового клея — Випол ПК-200. Изначально его наносят на одну из поверхностей, которую впоследствии обрабатывают распыляемой водой. Таким образом, монтаж ППУ скорлуп осуществляется в течение суток с технологической фиксацией при помощи бандажей. Соединение получается не разъемное и полностью бесшовное. При этом, расход клея не превышает 300 г/м кв.
Отметим, что осуществить быстрый монтаж крепления ППУ скорлуп на трубе можно также при помощи вязальной проволоки, металлических лент, пластиковых стяжек.
Соединение труб при помощи муфт
Соединить между собой трубы ППУ можно также при помощи специальных муфт. В данном случае они будут выполнять роль опалубки. На месте монтажа свободное пространство, которое осталось между поверхностью муфты и стальной трубы, заполняют специальной полимерной субстанцией¸ которая состоит из вспенивающих элементов, полиэфиров, стабилизирующей добавки эмульгаторов, катализаторов и изоционата. Сварные поверхности труб заливают именно таким составом для их дальнейшей герметизации. При этом полученный слой пенополиуретана одетая муфта будет надежно предохранять от разрушения.
Важно отметить, что при заливке нужно соблюдать все условия, необходимые для отвердения синтетической массы. Это позволит проявиться свойствам адгезии оболочки. В противном случае, ни о каком качественном сцеплении нельзя будет и говорить, поскольку внутри теплоизоляционного слоя стальная труба будет свободно двигаться, что повлечет скапливание влаги в образовавшемся зазоре. Таким образом, процессы коррозии стальной трубы будут неизбежны.
Сделайте заказ или задайте интересующий вас вопрос
*Все поля обязательны к заполнению!
Задача теплоизоляции наружного трубопровода | Группа компаний «Экстрол»
При высокой насыщенности современного коттеджа разнообразными коммуникациями возникает необходимость уберечь их от замерзания. Наиболее удобным и практичным выбором станут теплоизоляционные скорлупы из экструзионного пенополистирола.
Тёплая оболочка
Как известно, экструзионный пенополистирол имеет закрыто-пористую структуру. Водопоглощение материала настолько мало, что его можно охарактеризовать как поверхностное. Поэтому монтаж и хранение теплоизоляции подобного типа можно производить при любой погоде. Если же произвести теплоизоляцию стальных труб грамотно, то вероятность попадания влаги внутрь теплоизоляции после монтажа полностью исключается. А значит, трубам не страшна проблема внешней коррозии.
Материал великолепно противостоит негативному воздействию агрессивной среды и природных факторов. Его не употребляют в пищу грызуны, на его поверхности не образуется плесень и грибок, а значит, изделия не требуют дополнительной химической защиты. Укладывать их можно прямо в грунт даже в местах буйной растительности.
При этом для экструзионного полистирола характерен высокий показатель безопасности — это экологически чистый, абсолютно безвредный материал. Его можно без опаски брать в руки и работать с ним без дополнительных мер предосторожности. Этим экструзионный пенополистирол выгодно отличается от стеклонаполненных минераловатных изоляторов, теплоизоляция которыми должна проводиться как минимум в перчатках, избегая контакта с кожей.
Полуцилиндры и сегменты имеют небольшой вес, что упрощает его монтаж и транспортировку — в обычном легковом автомобиле можно без проблем перевезти необходимое количество сегментов (это актуально для тех, кто предпочитает решать строительные задачи самостоятельно).
Скорлупа легко режется и обрабатывается обычным строительным инструментом. Простая для понимания схема соединений и доступные способы монтажа обеспечивают высокую скорость работ.
Пара работников без специальных навыков могут за смену изолировать от 150 до 300 метров трубопровода. При этом не составит проблему и монтаж скорлуп на трубы водоснабжения или канализации своими руками — с этим может справиться любой человек, мало-мальски знакомый со строительными процессами. При необходимости ремонта изолированного участка трубы скорлупа аккуратно и легко снимается, а по завершении работ устанавливается на свое место. Благодаря этому существенно увеличивается скорость и экономичность эксплуатационного процесса.
Преимущества экструзионного пенополистирола в виде полуцилиндров и сегментов для теплоизоляции труб:
Возможность круглогодичного монтажа.
Возможность многоразового использования.
Простота демонтажа и быстрый доступ к повреждённым участкам трубы.
Большой срок эксплуатации (до 50 лет).
Снижение расходов на строительство, эксплуатацию и ремонт.
Высокая производительность монтажных работ.
Экологичность и абсолютная безвредность для человека и окружающей среды.
Высокая химическая и биологическая стойкость.
Отвечает всем мировым стандартам прочности и надёжности.
Таким образом, достоинств у экструзионного пенополистирола достаточно. Именно эти преимущества и позволяют заявить об эффективности и экономической целесообразности данного типа трубной теплоизоляции.
Монтаж трубной теплоизоляции
Специалисты утверждают, что теплоизоляция труб должна выполняться ещё на этапе создания системы коммуникаций — это самый простой и наиболее удобный вариант. Чрезвычайные меры, вызванные внезапными повреждениями трубопроводов, обходятся на порядок дороже. Кроме того, проведение запоздалых «раскопок» после окончания работ по благоустройству участка становится очень проблематичным и затратным мероприятием.
Коммуникации необходимо проводить так, чтобы к ним при необходимости можно было подобраться, ничего не нарушив. Баню и гостевой домик многие планируют «обводнить» и отопить сразу. При этом не стоит исключать из плана и летнюю кухню. Её, при желании, станет возможно использовать и при лёгких минусовых температурах за окном, которые случаются в межсезонье. Не нужно будет опасаться, что уже подключенная вода порвёт трубы. Причём протянуть туда можно не только холодную воду, но и горячую.
Особых дополнительных затрат на это не потребуется, зато как порадует результат такой предусмотрительности в прохладную погоду! При этом канализацию туда вести не обязательно — стоки не такие уж объёмные и не особо «вредные». Сток из раковины можно запустить в дренажный колодец.
Помимо всего прочего, на участке стоит предусмотреть и другие точки водоразбора — на полив, помывку машины, для бассейна. В дом ведь с ведром не набегаешься, а временный вариант в виде поливочного шланга, как правило, превращается в постоянный мешающийся под ногами «ландшафтный объект».
Форма скорлуп обеспечивает удобство и простоту монтажа утеплителя на поверхности трубы вне зависимости от того, как она расположена. Различия могут заключаться во внутреннем диаметре полуцилиндров (для разных труб требуется скорлупа разного размера) и в толщине материала (чем толще, тем эффективнее и надёжнее изоляция). Кроме того, существуют не только стандартные прямые сегменты, но и скорлупа для утепления поворотов и колен трубопроводов.
Скорлупы ППУ используются для обеспечения тепловой изоляции труб
различного назначения, диаметров и способов прокладки. Производство скорлупы
ППУ, как производственный и технологический процесс, основывается на
использовании стальных пресс-форм и качество изготовленной скорлупы ППУ
зависит от их качества и количества. Даже самыми малопроизводительными
заливочными машинами ППУ можно залить скорлупы ППУ в течение не более 25
секунд, в то время как выдержка пенополиуретана в пресс-форме составляет 7-20
минут. Если более детально останавливаться на области применения скорлупы, то стоит отметить, что скорлупа для труб из пенополиуретана широко используется для замены старой изношенной стекловатной теплоизоляции или заделки стыков ППУ трубопроводов. Применение скорлупы теплоизоляционной снижает тепловые потери на трубопроводе и является наряду с этим также надежным, долговечным, недорогим и эффективным теплоизоляционным материалом. Скорлупа ППУ легко и быстро монтируется, легко поддается формованию (распиливанию для подгонки теплоизоляции по трубе) при монтаже, может использоваться многократно и изготавливается с разной толщиной, в основном составляющей 35 — 60 мм. Скорлупа из пенополиуретана, защищенная армафолом или стальной фольгой, при соблюдении правил монтажа и проведении работ по гидроизоляции стыков крепления скорлуп между собой, устойчива к воздействию внешних факторов, влияющих на трубопровод. Скорлупы ППУ изготавливаются в виде цилиндров и полуцилиндров скорлуп
длиной, как правило, один метр. Широкий спектр изоляционных покрытий скорлуп ППУ (скорлупа фольгированная с покрытием фольгой или армафолом, скорлупы теплоизоляционные с покрытием из стеклоткани и скорлупы из пенополиуретана с защитным оцинкованным кожухом) позволяет эффективно применять скорлупы из пенополиуретана в разных монтажных и эксплуатационных условиях пролегания теплоизолированного трубопровода. |
Изоцианат, ПОЛИЭФИЛЬНЫЙ ПОЛИОЛ продуктов от китайских производителей — ZIBO GUIDE NEW MATERIALS TECHNOLOGY CO., LTD.
{{if (item.springSalesTagInfo && item.springSalesTagInfo.showSpringSalesTag) {}} {{}}} {{if (item.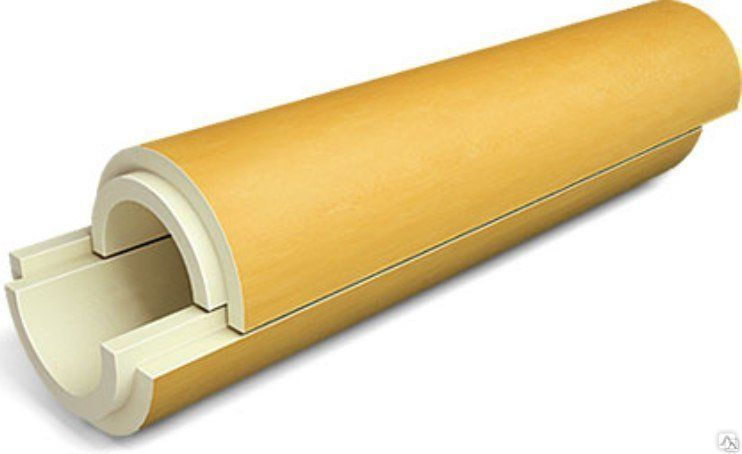
{{-meiAward.prodAwardDateAndName}}
{{})}} {{}}} {{if (item.springSalesTagInfo.showSpecialDiscountTag) {}} Специальная скидка {{}}} {{if (item.springSalesTagInfo.showFreeSampleTag) {}} Бесплатный образец {{}}} {{if (item.springSalesTagInfo.showRapidDispatchTag) {}} Rapid Dispatch (Быстрая отправка) {{}}} {{if (item.springSalesTagInfo.showSoldThousandTag) {}} Продано 10000+Горячие и актуальные товары
{{}}} {{if (item.springSalesTagInfo.showInstantOrderTag) {}} Мгновенный заказСлужба поддержки онлайн-заказов
{{}}} {{if (item.springSalesTagInfo.showReliableSupplierTag) {}} Надежный поставщик {{}}} {{if (item.springSalesTagInfo.showExpoTag) {}} Интернет-выставка {{}}}{{if (item.mainProps) {}} {{util.each (Object.keys (item.mainProps), function (prop, i) {}}
Aegion в соответствии с графиком проекта Shell по нанесению и нанесению покрытия на трубы
Aegion Corporation (Aegion или компания) объявила, что по графику начинается покрытие труб и нанесение инновационного изоляционного материала для труб для использования в проекте Shell Appomattox. Поставщик изоляционного материала для проекта, Materia, Inc., также идет по графику в отношении проекта. Shell Offshore, Inc., стопроцентная дочерняя компания Royal Dutch Shell plc, выбрала дочернюю компанию Aegion, Bayou Companies, LLC, для обеспечения покрытия и изоляции труб для проекта Appomattox, расположенного в глубоких водах Мексиканского залива.
Aegion сотрудничает с Materia в поставке подводной системы изоляции Proxima (R) HTI-1400 компании Materia для этого проекта. Недавно разработанная система термореактивных сшитых углеводородных полимеров обеспечивает прочный тепловой барьер между выкидными линиями и морской водой.Система изоляции представляет собой стабильное несжимаемое твердое вещество в глубоководных средах с глубиной воды более 10 000 футов. Компания Materia недавно завершила первый этап необходимого расширения своего предприятия в Хантсвилле, штат Техас, для производства нового теплоизоляционного материала, и продолжает процесс ввода в эксплуатацию. . Ожидается, что вторая фаза расширения состоится во втором и третьем кварталах 2016 года, что соответствует графику полномасштабного производства этой осенью.
Современный завод по нанесению изоляционного покрытия, спроектированный для проекта Appomattox, в настоящее время строится в районе Байу, Нью-Иберия, штат Луизиана, где Bayou будет обеспечивать антикоррозийное покрытие труб и вспомогательные услуги.Bayou Wasco Insulation, LLC (Bayou Wasco), совместное предприятие Aegion и малайзийской компании Wasco Energy, Ltd, является лидером в производстве запатентованных изоляционных покрытий и идеально подходит для обслуживания рынка глубоководных трубопроводов в Мексиканском заливе. В сотрудничестве с Materia и Shell компания Bayou Wasco разработала собственный процесс нанесения изоляционного покрытия на трубы ACS TM HT-200. В настоящее время Bayou получает специализированное оборудование для нанесения изоляции, так как строительство нового объекта будет завершено этим летом.Bayou планирует начать производство изоляционных материалов в 4К16.
Чарльз Р. Гордон, президент и главный исполнительный директор Aegion, сказал: «Наше сотрудничество с Materia демонстрирует нашу приверженность работе с клиентами для предоставления покрытий, изоляции, логистики и сборных решений мирового класса. Новый запатентованный процесс применения изоляции труб позволит безопасно и эффективно транспортировать сырую нефть с глубоководных месторождений в Мексиканском заливе.Мы гордимся своей способностью оказывать поддержку Shell масштабным проектам и по-прежнему привержены обеспечению высококачественной защиты трубопроводов от коррозии, обеспечению потока и другим услугам для их трубопроводных активов в регионе побережья Мексиканского залива ».
Нитин Апте, президент и главный исполнительный директор Materia, прокомментировал: «Теплоизоляция Materia обеспечивает простое и экономичное решение проблем глубоководной добычи нефти и газа. Выбор Bayou, Bayou Wasco и Materia для обеспечения системы изоляции для подводной рабочей среды нефтяного месторождения Appomattox подтверждает опыт Bayou Wasco в области изоляции и новейшие технологии материаловедения Materia, которые обеспечивают инновационное и надежное технологическое решение для трубопроводов. обеспечение потока.”
Нефтяные запасы Shell Appomattox расположены примерно в 80 милях от побережья Луизианы на глубине около 7200 футов. Ожидается, что проект по нанесению покрытия и изоляции труб, включающий более 200 миль производственных и передающих трубопроводов, будет завершено через 12 — 18 месяцев после начала нанесения покрытия на трубы и изоляции.
Отредактировано из источника Стефани Рокер
Прочтите статью на сайте: https: // www.worldpipelines.com/project-news/12042016/aegion-on-schedule-for-shells-pipe-coating-and-application-project/
Изоляция, применяемая в полевых условиях
Изоляция, применяемая в полевых условиях
Компания
Urecon Ltd. (ранее Polybrand Inc.) — самый диверсифицированный дистрибьютор, производитель и трансформатор жесткой изоляции на востоке Канады.Наш современный завод площадью 2110 м 2 (22 750 футов 2 ) , расположенный в Риго, Qubec, полностью оборудован для производства и преобразования различных жестких изоляционных материалов в соответствии с сегодняшними промышленными требованиями. Наши основные производственные линии включают: Тример и пенополистирол, Elliott Elfoam и Pittsburgh Corning Foamglas Insulation.
Urecon Ltd. также может поставлять вспомогательные материалы, такие как оболочки, покрытия, герметики, клеи, ленты и т. Д. Продукты Trymer, Elfoam, Styrofoam и Foamglas представляют собой жесткие изоляционные материалы с различными свойствами, выбор материалов зависит от типа проекта. .Урекон также производит полуоболочки из пенополиуретана с гладкой внешней обшивкой. Для получения дополнительной информации см. Спецификацию полуоболочек U.I.P.®.
Продукты
Продукты Trymer, Elfoam, Styrofoam и Foamglas — это жесткие изоляционные материалы с различными свойствами, выбор материалов зависит от типа проекта.
Изоляционные материалыPolybrand хорошо подходят для надземных или подземных проектов в пищевой промышленности, нефтеперерабатывающих заводах, институциональных, морских, коммерческих и промышленных применениях в горячих или холодных условиях.
После выбора типа изоляции Polybrand Inc. может изготовить изоляцию любой формы в соответствии с вашими индивидуальными требованиями. К ним относятся:
Секции изоляции для труб:
- стандартные полуоболочки до 0,91 м (3 фута) длиной
- полуоболочки корабельные
- пазовидные полуоболочки
- Многослойная стыковая кромка
Изоляционные листы и блоки:
- прецизионная резка
- листов шириной до 1.22 м (4 фута)
- длина листа до 3,04 м (10 футов)
- толщина листа от 13 мм (½ дюйма) и более
- резка по индивидуальному заказу в соответствии с вашими потребностями
Изготовление нестандартных форм и форм по специальному заказу.
Свяжитесь с Polybrand для получения полных спецификаций продукта и рекомендаций, соответствующих вашим потребностям.
Траймер Изоляция
Пенополиизоциануратная изоляция Trymer®с закрытыми ячейками производится ITW Insulation Systems и обеспечивает отличное сопротивление теплопередаче.Низкая теплопроводность означает, что для удовлетворения ваших требований к теплоизоляции требуется меньше изоляции Trymer®. Это означает значительную экономию времени и материалов на установку.
Этому изоляционному материалу можно придать различную форму, чтобы удовлетворить практически любое применение изоляции. Он доступен с различной плотностью и прочностью на сжатие для различных областей применения, в том числе:
- изоляция труб и резервуаров;
- основных материалов для конструкционных панелей.
Trymer имеет диапазон рабочих температур от -183C (-297F) до 149C (300F) .
Физические свойства полиизоциануратной пены марки TRYMER
Протестировано при 23C (75F) | ASTM Метод | Тример 1600 | Тример 1800 | Тример 2000 | Тример 3000 | Тример 4000 | Тример 6000 |
Плотность кг / м 3 (фунт / фут 3 ) | Д 1622 | 26.4 (1,65) | 29 (1,8) | 32,8 (2,05) | 48 (3,0) | 64 (4,0) | 96 (6,0) |
k-фактор Вт / мСт (БТЕ / час 2 F ) 180 дней при 75 ° F среднее значение | С 518 | 0.027 (0,19) | 0,027 (0,19) | 0,027 (0,19) | 0,027 (0,19) | 0,027 (0,19) | 0,029 (0,20) |
R-Value м 2 C / W (Hrft 2 F / BTU) 180 дней при 75F среднее | С 518 | 0.93 (5,3) | 0,93 (5,3) | 0,93 (5,3) | 0,93 (5,3) | 0,93 (5,3) | 0,88 (5,0) |
Прочность на сжатие кПа (psi) параллельно | Д 1621 | 117 (17) | 131 (19) | 165 (24) | 350 (50) | 550 (80) | 970 (140) |
Elfoam Insulation
Полиизоциануратная изоляция Elfoam P200 с закрытыми порами, жесткая вспененная изоляция подходит для различных применений теплоизоляции.
Наиболее гибкая и менее хрупкая изоляция из полиизоциануратных плит, Elfoam особенно подходит для применений, связанных с отрезными листами, такими как:
- Многослойный сердечник резервуара из стеклопластика, верхняя часть, нижняя часть и изоляция стен
- изоляционный материал сердцевины для ламинированных архитектурных и холодильных сэндвич-панелей
- изоляция для рефрижераторных морских контейнеров, таких как грузовики, прицепы и железнодорожные вагоны
- Основной материал для коммерческих и промышленных дверей
Изоляция марки Elfoam P200 имеет диапазон рабочих температур от -46C (-50F) от до 121C (250F) .
Физические свойства Изоляция ELFOAM P200 *
Протестировано при 23C (75F) | ASTM Метод | Elfoam |
Плотность кг / м 3 (фунт / фут 3 ) | Д 1622 | 31,9 (2,0) |
коэффициент k Вт / м • ° C (БТЕ • дюйм./ час • фут 2 ° F ) 10 дней при 158 ° F среднее | С 518 | 0,027 (0,185) |
Значение R м 2 • ° C / Вт (час • фут 2 • ° F / БТЕ) 180 дней при 75 ° F в среднем | С 518 | 0,96 (5,4) |
Прочность на сжатие кПа (psi) параллельно | Д 1621 | 172 (25) |
Изоляция из пенополистирола
ИзоляцияDow Plastic Styrofoam PIB * изготавливается из жесткого пенопласта с закрытыми порами и однородной микропористой структурой без пустот.Эта плотная, компактная структура обеспечивает отличную устойчивость к воде, водяному пару и циклическому замораживанию-оттаиванию во влажном состоянии.
В результате изоляция из пенополистирола сохраняет практически все свое первоначальное значение R в течение многих лет даже в условиях высокой влажности, когда пористые изоляционные материалы подвержены поглощению влаги и в конечном итоге теряют эффективность изоляции. Изоляция марки пенополистирола устойчива к кислотам, щелочам, рассолам и спирту. Эта жесткая пена не имеет пищевой ценности для привлечения или поддержания жизни растений или животных.
На протяжении многих лет изоляция из пенополистирола была признана за ее способность сводить к минимуму приток тепла и предотвращать конденсацию на поверхности.
Утеплитель марки пенополистиролподходит для:
- крышки клапанов / фитингов
- покрытие трубы
- оборудование отстает и др.
Пенополистирол имеет диапазон рабочих температур от -183C (-297F) до 74C (165F) .
Изоляция маркииз пенополистирола может быть произведена компанией Polybrand с высокой точностью в соответствии с вашими требованиями к широкому спектру трубопроводов и фитингов.
Физические свойства Утеплитель марки пенополистирол
Протестировано при 23C (75F) | ASTM Метод | Пенополистирол |
Плотность кг / м 3 (фунт / фут 3 ) | Д 1622 | 26 (1.6) |
k-фактор Вт / м • ° C (БТЕ • дюйм / час • фут 2 ° F ) 10 дней при 158 ° F, среднее 5 лет при 75 ° F, среднее | С 518 | 0,036 (0,25) 0,041 (0,28) |
Значение R м 2 • ° C / Вт (час • фут 2 • ° F / БТЕ) 180 дней при 75 ° F в среднем | С 518 | 0.70 (4,0) |
Прочность на сжатие кПа (psi) параллельно | Д 1621 | 138 (20) |
Изоляция из пеностекла
Изоляция Pittsburgh Corning Foamglas — это легкий, жесткий изоляционный материал, состоящий из миллионов полностью герметичных стеклянных ячеек, каждая из которых представляет собой изолирующее пространство. Эта цельностеклянная структура с закрытыми ячейками обеспечивает сочетание физических свойств, соответствующих требованиям промышленной изоляции.
Изоляция марки Foamglasустойчива к воде как в жидкой, так и в паровой форме, не вызывает коррозии, негорючие / не впитывает горючие жидкости, устойчива к большинству промышленных реагентов, стабильна по размерам, имеет превосходную прочность на сжатие.
Изоляция марки Foamglasподходит для широкого спектра услуг, проверенные области применения включают:
- криогенные трубопроводы, резервуары, сосуды и др.
- Трубопроводы и оборудование для средних и высоких температур
- системы теплоносителя
- Системы переработки углеводородов и серы
- подземные трубопроводы пара и охлажденной воды
- негорючая изоляция для морских платформ
Изоляция марки Foamglas имеет диапазон рабочих температур от -268C (-450F) до 482С (900F) .
Изоляция из пеностеклапроизводится компанией Pittsburgh Corning в виде блоков, а затем собирается, нарезается, сужается или иным образом трансформируется в соответствии с требованиями Polybrand.
Для изоляции Foamglas доступен выбор материалов внешней оболочки, включая Pittwrap. (для подземных применений), алюминия или других материалов оболочки для наземных применений.
Физические свойства Пеностекло утеплитель марки
Протестировано при 23C (75F) | ASTM Метод | Пеностекло |
Плотность кг / м 3 (фунт / фут 3 ) | С 303 | 120 (7.5) |
k-фактор Вт / м • ° C (БТЕ • дюйм / час • фут 2 ° F ) 180 дней при 75 ° F среднее значение | С 518 | 0,042 (0,29) |
Значение R м 2 • ° C / Вт (час • фут 2 • ° F / БТЕ) 180 дней при 75 ° F в среднем | С 518 | 0,60 (3,4) |
Прочность на сжатие кПа (psi) параллельно | С 165 | 620 (90) |
Типичные приложения
Утеплитель со скосом по периметру система производства Полибренд из пенопласта Trymer для масла большого диаметра передающий трубопровод. | Установка Pittwrap
обшивка поверх утеплителя Foamglas | |
Изоляция из пеноматериала марки Trymer, используемая для изоляции трубопровод в системе защиты от замерзания. | ||
Изоляция из пенополистирола марки используется для изоляции сосуда. |
Заявка на патент США на опору для трубопроводов и процесс установки такой опоры Заявка на патент (Заявка № 20020060274 от 23 мая 2002 г.)
ОБЛАСТЬ ИЗОБРЕТЕНИЯ& lsqb; 0001 & rsqb; Настоящее изобретение относится к опоре для трубопроводов для холодных жидкостей с кареткой, состоящей из двух или более чем двух частей, которая окружает изолирующую оболочку, окружающую трубопровод, при этом каретка содержит части каретки, соединенные друг с другом на соединительных фланцах.Кроме того, настоящее изобретение относится к способу установки или поддержки такой опоры.
ПРЕДПОСЫЛКИ ИЗОБРЕТЕНИЯ& lsqb; 0002 & rsqb; Такая поддержка показана, например, в Arbeitsblatt Q 03 Arbeitsgemeinschaft Industriebau e.V. (AGI) и будет кратко объяснено ниже на основе фиг. 15. Каретка 61, также называемая стальным башмаком, состоит из двух частей. Одна часть каретки имеет опору 62, на которой расположена полукруглая оболочка 63. Эта полукруглая оболочка 63, установленная через изоляцию, привинчена в точках соединения ко второй полукруглой оболочке 64, которая образует вторую часть каретки.Таким образом получают нижнюю часть каретки и верхнюю часть каретки, которые прикреплены друг к другу болтами в плоскости, проходящей под углом к вертикали. В результате трубопровод находится в плотном контакте в нижней части оболочки и уже закреплен должным образом.
& lsqb; 0003 & rsqb; Трубопроводы для холодных жидкостей, которые, как правило, определяются как жидкости с температурой ниже 11 ° C, снабжены изоляцией, которая включает изоляционный слой, непосредственно окружающий трубопровод, и внешний пароизоляционный слой.На практике внешняя пароизоляция иногда повреждается, поэтому влага проникает в изоляционный слой. В этом случае этот слой необходимо заменить. Для этого также необходимо снять каретку с трубопровода. Сама каретка также подвержена коррозионным воздействиям, поэтому время от времени ее необходимо снимать. Наконец, также необходимо время от времени проверять сам трубопровод на предмет трещин или коррозии на трубопроводе, особенно в сварных швах, для чего необходимо снова удалить изоляцию и вместе с ней каретку.Согласно уровню техники, для этой цели трубопровод должен быть поднят, чтобы вынуть его из нижней части корпуса, либо нижняя часть каретки и изоляция должны быть полностью разрушены. Подъем трубопровода не может рассматриваться в случае трубопроводов для очень холодных жидкостей, которые имеют температуру -164 ° C, например, в случае сжиженного природного газа (метана), из-за хрупкого охрупчивания стальной трубы. что происходит при этих низких температурах. Таким образом, трубопровод должен быть выведен из эксплуатации во время процедур технического обслуживания и осмотра, что связано со значительными затратами из-за простоев.Во время переустановки кареток предшествующего уровня техники трубопровод, уже снабженный новыми изолирующими кожухами согласно уровню техники, должен быть снова поднят, чтобы поместить его в нижнюю часть каретки. Как было сказано, этого нельзя делать во время работы трубопровода.
& lsqb; 0004 & rsqb; Другой тип опоры для труб используется в трубопроводах с малым диаметром трубы для холодных жидкостей. Эти опоры для труб, которые также называют трубными зажимами, показаны, например, e.g., в Каталоге LISEGA 1994 Rohrschellen Rohrlager & lsqb; 1994 LISEGA Трубные хомуты и опоры для труб — Тр. ред. & rsqb ;. Эти опоры для труб содержат две части каретки, которые соединены друг с другом на соединительных фланцах и между которыми трубопровод крепится непосредственно с помощью болтов без использования изоляции. Один из соединительных фланцев расположен, если смотреть со стороны опорной плиты, на которой трубопровод поддерживается вертикально по направлению к центральной оси трубопровода, точно под трубопроводом.Хомуты для труб образуют здесь тепловой мост, потому что они закрепляются непосредственно на трубопроводах без использования изоляции. Эти хомуты известны давно. Однако они не подходят для использования в качестве опор типа, упомянутого во введении.
& lsqb; 0005 & rsqb; Кроме того, тележки для поддержки трубопроводов, которые содержат множество частей тележки, известны из DE-GM 1 984 394, DE 299 13 157 Ul, DE-AS 2 053 949 и US Pat.№ 4858861, в котором части каретки могут быть соединены друг с другом с помощью соединительного фланца, который расположен точно под трубопроводом. В этом отношении эти каретки соответствуют опорам для труб, показанным в каталоге LISEGA 1994 Rohrschellen Rohrlager.
СУЩНОСТЬ ИЗОБРЕТЕНИЯ И ОБЪЕКТЫ ИЗОБРЕТЕНИЯ& lsqb; 0006 & rsqb; Исходя из этого, основная цель настоящего изобретения состоит в том, чтобы улучшить опору типа, упомянутого во введении, так, чтобы ее можно было снимать и поддерживать в упрощенном виде даже во время работы трубопровода.Кроме того, другой основной задачей настоящего изобретения является создание способа поддержки или установки таких опор.
& lsqb; 0007 & rsqb; Для достижения этой цели опора в соответствии с настоящим изобретением отличается тем, что, если смотреть со стороны опорной плиты, на которой трубопровод поддерживается вертикально по отношению к центральной оси трубопровода, один из соединительных фланцев расположен точно под трубопроводом и что детали каретки имеют направляющие для приема направляющих инструментов для поддержки каретки.
& lsqb; 0008 & rsqb; Способ согласно настоящему изобретению отличается тем, что части тележки смещены вбок рядом с трубопроводами, а затем перемещаются к трубопроводу с помощью направляющих инструментов и, наконец, соединяются друг с другом.
& lsqb; 0009 & rsqb; Осуществление процесса согласно настоящему изобретению становится возможным только благодаря конструкции опоры согласно настоящему изобретению. Детали тележки могут быть подведены к трубопроводу сбоку, т.е.е., в плоскости опорной плиты и соединены, здесь специально прикручены друг к другу. В результате предотвращается любое изменение положения центральной оси трубопровода, особенно подъем трубопровода. Таким образом, тележку можно поддерживать и снимать во время работы даже в случае трубопроводов, по которым проходят очень холодные жидкости. Опоры согласно настоящему изобретению также могут поддерживаться способом согласно настоящему изобретению даже в случае трубопроводов, примыкающих друг к другу в близко расположенных местах друг за другом во множестве рядов.Кроме того, направляющие инструменты гарантируют, что предотвращается заклинивание деталей каретки во время опоры и, как следствие, повреждение пароизоляции изоляции во время опоры.
& lsqb; 0010 & rsqb; В одном варианте в соединительных фланцах в качестве направляющих предусмотрены направляющие отверстия, особенно отдельные. Например, в этой простой конструкции болты можно использовать в качестве направляющих инструментов. В этом случае направляющие отверстия должны быть направлены на цилиндр болта, а не на резьбу.Таким образом, желаемые направляющие свойства могут быть легко достигнуты путем подходящего согласования посадки между направляющим отверстием и цилиндром затвора.
& lsqb; 0011 & rsqb; Рекомендуется предусмотреть временную опору для трубопровода во время опоры и снятия опоры в соответствии с настоящим изобретением. Эта временная опора содержит, согласно конкретному примерному варианту осуществления, виселицу, поддерживаемую над трубопроводом, которая имеет петлю слева и справа от опоры для временного приема трубопровода.
& lsqb; 0012 & rsqb; Настоящее изобретение будет более подробно объяснено ниже на основе примерных вариантов осуществления, показанных на чертежах.
& lsqb; 0013 & rsqb; Различные особенности новизны, которые характеризуют изобретение, конкретно указаны в формуле изобретения, прилагаемой к этому раскрытию и составляющей его часть. Для лучшего понимания изобретения, его эксплуатационных преимуществ и конкретных целей, достигаемых при его использовании, сделана ссылка на прилагаемые чертежи и описательный материал, в котором проиллюстрированы предпочтительные варианты осуществления изобретения.
КРАТКОЕ ОПИСАНИЕ ЧЕРТЕЖЕЙ& lsqb; 0014 & rsqb; На чертежах:
& lsqb; 0015 & rsqb; ИНЖИР. 1 — вертикальный разрез в плоскости B-B по фиг. 2, показывающий опору с признаками настоящего изобретения;
& lsqb; 0016 & rsqb; ИНЖИР. 2 — вид в разрезе опоры согласно фиг. 1 в самолете А-А,
& lsqb; 0017 & rsqb; ИНЖИР. 3 — подробный вид частично поддерживаемой опоры согласно фиг.1 в разрезе в плоскости А-А;
& lsqb; 0018 & rsqb; ИНЖИР. 4A — схематический вид в перспективе, показывающий этап {обведен кружком (1)} процесса поддержки опоры согласно фиг. 1;
& lsqb; 0019 & rsqb; ИНЖИР. 4B — схематический вид в перспективе, показывающий этап (кружок над (2)} процесса поддержки опоры согласно фиг. 1;
& lsqb; 0020 & rsqb; ИНЖИР. 4C — схематический вид в перспективе, показывающий этап (кружок над (3)} процесса поддержки опоры согласно фиг.1;
& lsqb; 0021 & rsqb; ИНЖИР. 5 — вид в разрезе, взятом по плоскости, аналогичной плоскости A-A на фиг. 1, показывающий другой примерный вариант осуществления опоры с признаками настоящего изобретения;
& lsqb; 0022 & rsqb; ИНЖИР. 6 — деталь опоры согласно фиг. 5 в частично поддерживаемом состоянии;
& lsqb; 0023 & rsqb; ИНЖИР. 7A — схематический вид в перспективе, показывающий этап процесса установки опоры согласно фиг.5;
& lsqb; 0024 & rsqb; ИНЖИР. 7B — схематический вид в перспективе, показывающий еще один этап процесса установки опоры согласно фиг. 5;
& lsqb; 0025 & rsqb; ИНЖИР. 7C — схематический вид в перспективе, показывающий еще один этап процесса установки опоры согласно фиг. 5;
& lsqb; 0026 & rsqb; ИНЖИР. 8А — вид с торца, показывающий первый примерный вариант изолирующей оболочки для опоры согласно настоящему изобретению;
& lsqb; 0027 & rsqb; ИНЖИР.8В — вид сбоку в разрезе, показывающий первый примерный вариант изолирующей оболочки для опоры согласно настоящему изобретению;
& lsqb; 0028 & rsqb; ИНЖИР. 9А — вид в перспективе, показывающий один из трех примерных вариантов изолирующей оболочки для опоры;
& lsqb; 0029 & rsqb; ИНЖИР. 9В — вид в перспективе, показывающий второй из трех примерных вариантов осуществления изолирующей оболочки для опоры;
& lsqb; 0030 & rsqb; ИНЖИР. 9С — вид в перспективе, показывающий третий из трех примерных вариантов осуществления изолирующей оболочки для опоры;
& lsqb; 0031 & rsqb; ИНЖИР.9D — схематический вид, показывающий соединение изоляционных кожухов для варианта осуществления по фиг. 9B;
& lsqb; 0032 & rsqb; ИНЖИР. 9E — схематический вид, показывающий соединение изоляционных кожухов для варианта осуществления, показанного на фиг. 9B;
& lsqb; 0033 & rsqb; ИНЖИР. 10 — вид в перспективе, показывающий один из примерных вариантов осуществления согласно фиг. 9 для изоляционной оболочки для опоры согласно настоящему изобретению;
& lsqb; 0034 & rsqb; ИНЖИР.11А — вид в перспективе изолирующей оболочки согласно фиг. 10 с пароизоляцией;
& lsqb; 0035 & rsqb; ИНЖИР. 11В — схематический вид сбоку в разрезе пароизоляции в положении во время сборки;
& lsqb; 0036 & rsqb; ИНЖИР. 11С — схематический вид сбоку в разрезе пароизоляции в положении после сборки;
& lsqb; 0037 & rsqb; ИНЖИР. 12 — вид в перспективе изоляционной оболочки по фиг. 10 с пароизоляцией и накладкой;
& lsqb; 0038 & rsqb; ИНЖИР.13 — вид в продольном разрезе другого примерного варианта осуществления опоры с признаками настоящего изобретения;
& lsqb; 0039 & rsqb; ИНЖИР. 14 — вид в разрезе опоры согласно фиг. 13 в самолетах A-A и B-B; и
& lsqb; 0040 & rsqb; ИНЖИР. 15 — вид в перспективе вспомогательного устройства для установки и снятия опоры.
ОПИСАНИЕ ПРЕДПОЧТИТЕЛЬНЫХ ВАРИАНТОВ ОСУЩЕСТВЛЕНИЯ& lsqb; 0041 & rsqb; В частности, со ссылкой на чертежи, настоящее изобретение относится, в частности, к опоре трубопроводов 20, особенно большого диаметра, для холодных жидкостей.Под холодными жидкостями здесь понимаются все жидкости с температурой ниже 11 ° C. Настоящее изобретение также включает, в частности, трубопроводы 20 для очень холодных жидкостей, например сжиженного природного газа (сжиженный природный газ, СПГ), сжиженного метана или сжиженного этана. , которые имеют температуру от -164 ° C (сжиженный природный газ) до -104 ° C (сжиженный этан). Также может использоваться для трубопроводов жидкого азота. Трубопроводы 20 снабжены изоляцией 21, которая образована двумя изоляционными слоями 22 и 23 в примерном варианте осуществления согласно фиг.1. Внешний изоляционный слой 22 и внутренний изоляционный слой 23 дополнительно снабжены пароизоляцией 24, предотвращающей проникновение влаги в изоляцию. Влага в изоляции ухудшает изоляционный эффект и приводит к коррозии трубопровода 20. Защитная оболочка 25, состоящая, например, из стальной пластины, также часто предусмотрена на пароизоляции 24 снаружи.
& lsqb; 0042 & rsqb; Трубопроводы поддерживаются в равномерно расположенных местах на опорной плите 26, в основном на верхней стороне держателя 27, несущего множество трубопроводов 20, расположенных один за другим или рядом друг с другом.Для этой цели используются опоры в соответствии с настоящим изобретением: опоры имеют изоляционную оболочку 28, изготовленную из твердого изоляционного материала, которая окружает трубопровод 20 и расположена между прилегающей изоляцией 21. Изолирующие оболочки 28 достаточно жесткие, чтобы выдерживать трубопровод 20 вместе с окружающей его изоляцией 21. Каждая изолирующая оболочка 28 кольцеобразно окружена кареткой 29. Каретка 29 имеет опору 30, с помощью которой она поддерживается на опорной плите 26.
& lsqb; 0043 & rsqb; Тележка 29 состоит из двух частей. Он состоит из двух частей 31, 32 каретки. Плоскость разделения каретки 29, в которой расположены точки соединения частей 31, 32 каретки, расположена под прямым углом к держателю 27. Таким образом, каретка имеет две симметричные каретки. детали 31,32, которые могут даже иметь идентичный дизайн. Таким образом, для каждого диаметра трубы или диаметра изоляции требуется только один тип каретки. Детали 31, 32 каретки имеют идентичную конструкцию и расположены зеркально перевернутыми друг относительно друга.Кроме того, части 31, 32 каретки выполнены в виде полукорпуса и окружают вместе трубопровод 20 и изолирующую оболочку 28 по кругу. Части 31, 32 каретки соединены, а именно привинчены друг к другу на верхних соединительных фланцах 33 и нижних соединительных фланцах 34. Плоскость разделения 35, которая в этом случае расположена точно вертикально (плоскость BB на фиг. 2 и 5), определяется соединительными фланцами 33, 34. Это удлинение рекомендуется в случае горизонтально расположенной опорной плиты 26, как в случае показанных примерных вариантов осуществления.Вообще говоря, плоскость разделения 35 всегда должна располагаться под прямым углом к плоскости опорной плиты 26. В результате нижние соединительные фланцы 34 всегда располагаются под трубопроводом, если смотреть в направлении опорной плиты 26. Другими словами, соединительные фланцы 34 расположены в зоне кратчайшего расстояния между трубопроводом 20 или изоляционной оболочкой 28 и опорной плитой 26.
& lsqb; 0044 & rsqb; Верхние соединительные фланцы 33 и нижние соединительные фланцы 34 имеют направляющие, которые являются направляющими отверстиями 36 в показанном примерном варианте осуществления.Направляющий инструмент 37 вставлен в направляющие отверстия 36. Этот инструмент 37 имеет в данном случае болт 38, цилиндр которого вставлен в направляющие отверстия 36. Резьба болта 38 может быть навинчена на гайку 40 с промежуточным положением распорная втулка 39. Распорная втулка 39 используется для обеспечения того, чтобы направляющие отверстия 36 были направлены на цилиндр болта 38, а не на резьбу болта. Как видно из фиг. 1, 4 и 6, два направляющих отверстия 36 связаны с каждым соединительным фланцем 33, 34, так что также предусмотрены четыре направляющих инструмента 37.
& lsqb; 0045 & rsqb; Как видно из фиг. 4 и 6, при установке опоры соблюдают следующую процедуру. Изолирующая оболочка 28, которая в данном случае образована двумя изолирующими полуоболочками 41 и 42, сначала помещается на трубопровод 20. Затем изоляционная оболочка 28 покрывается собственной пароизоляцией 43, а пароизоляция 43 закрывается. приваривается к области 44 перекрытия и затем загибается (фиг. 11). Затем пароизоляция 43 покрывается защитной рубашкой 45, состоящей из тонкой стальной пластины, которая действует как механическая защита.Как можно определить из фиг. 12, эта защитная оболочка 45 выполнена несколько уже, чем пароизоляция 43 и изоляционные оболочки 41, 42. Пароизоляция 24 примыкающей изоляции 21 трубопровода 20 размещается, а именно приклеивается или приваривается позже к выступающей части трубопровода. пароизоляция 43.
& lsqb; 0046 & rsqb; Детали 31, 32 каретки затем помещаются на опорную плиту 26 слева и справа рядом с трубопроводом 20 и сбоку сдвигаются вместе примерно в положение, показанное на фиг.3 и 6 (см. Также фиг. 4 и 7, в центре). Затем направляющие инструменты 37 вставляются в направляющие отверстия 36, и части 31, 32 каретки постепенно сводятся вместе, пока они не достигнут своего конечного положения (фиг. 4 и 6, внизу), путем попеременного завинчивания инструментов. Наконец, части 31, 32 каретки также скреплены вместе с помощью трех болтов 46 каждый на соединительный фланец 33, 34. Соединительные фланцы 33, 34 имеют для этой цели по три отверстия 47 каждое.
& lsqb; 0047 & rsqb; Подставка разбирается в обратном порядке.Все части можно снять без повреждений, чтобы их можно было повторно использовать для повторной поддержки. Таким образом, можно, в частности, удалить каретку, которая могла быть корродирована, ее можно подвергнуть пескоструйной очистке, снабдить защитой от коррозии и впоследствии снова поддержать описанным выше способом. Однако новый монтаж опор также может быть выполнен просто описанным выше способом.
& lsqb; 0048 & rsqb; Вспомогательная опора, более подробно показанная на фиг.15 показана временная опора трубопровода 20 во время монтажа и демонтажа. ИНЖИР. 15 по-прежнему показана вспомогательная опора с опорой в соответствии с уровнем техники, которая должна быть заменена опорой в соответствии с настоящим изобретением для временной опоры трубопровода 20 во время монтажа и демонтажа.
& lsqb; 0049 & rsqb; Вспомогательная опора имеет вспомогательную раму 48, которая размещается над трубопроводом 20 на держателе 27 трубопровода, а именно опорную плиту 26.Вспомогательная рама 48 теперь перемыкает через трубопровод 20. На вспомогательной раме 48 расположена виселица 49, которая расположена в продольном направлении трубопровода 20 и выступает над вспомогательной рамой 48 с обеих сторон. По две петли для переноски 50 каждая. , в котором подвешен трубопровод 20, закреплены на двух концах вспомогательной рамы и на виселице 49. Несущая петля 50 может состоять из троса или цепи, что, однако, рекомендуется только в том случае, если она размещается непосредственно на сам трубопровод 20. Если несущая петля 50 проложена поверх изоляции 21 трубопровода 20, рекомендуется использовать широкий пояс в качестве несущей петли 50.
& lsqb; 0050 & rsqb; Опора согласно уровню техники, показанная на фиг. 15, теперь удаляется путем разрезания и удаления каретки 29. Изолирующие оболочки впоследствии также разрушаются в области опоры и утилизируются. После этого могут быть выполнены необходимые в этой области процедуры технического обслуживания и осмотра. Наконец, новая опора согласно настоящему изобретению устанавливается вышеописанным способом, и вспомогательная рама 48 удаляется.
& lsqb; 0051 & rsqb; Фиг. 2-4, а также фиг. 5-7 показаны два примерных варианта выполнения кареток 29, но эти каретки 29 идентичны друг другу в своих основных моментах. Только ножки 30 выполнены иначе. Ножки по существу имеют L-образную конструкцию с вертикальными перемычками 52 и горизонтальными основаниями 53 в примерном варианте осуществления согласно фиг. 2-4A, B и C. Опоры 30 в примерном варианте осуществления согласно фиг. 5-7 имеют U-образную конструкцию, так что они образуют коробчатый профиль вместе с нижней частью корпуса частей 31, 32 каретки.Следовательно, есть две вертикальные перемычки 54, расположенные на расстоянии друг от друга на дне 55.
& lsqb; 0052 & rsqb; Другой аспект, который до сих пор не упоминался, следует принимать во внимание в связи с опорой изолирующей оболочки 28. В этой связи сделана ссылка на фиг. 8A и B. Как только изолирующая оболочка 28, а именно изолирующие полуоболочки 41, 42, будет помещена на трубопровод 20, влага может проникнуть в зазор между изолирующей оболочкой 28 и трубопроводом 20 и сконденсироваться там.Чтобы этого не произошло, уплотнение 57, состоящее из постоянно эластичного герметизирующего компаунда, предусмотрено, по крайней мере, на внешних краевых участках, то есть на переднем и заднем торцевых концах зазора, если смотреть в осевом направлении трубопровода 20. Такое Между изолирующими полуоболочками 41, 42 также предусмотрено уплотнение 57, так что они полностью герметичны. Постоянно эластичный герметизирующий состав может быть удален для снятия изоляционных полуоболочек 41, 42 из-за его постоянной эластичности, так что сами изолирующие полуоболочки 41, 42 остаются неповрежденными и могут использоваться повторно.Фиг. 9A, B, C, D и E также показаны различные примерные варианты осуществления, а именно геометрические конфигурации изоляционных полуоболочек 41, 42. Примерный вариант осуществления, показанный на фиг. 9A, который также более подробно показан на фиг. 10 — цилиндрическая рубашка, вырезанная в центральной продольной плоскости. Примерный вариант осуществления, показанный на фиг. 9B, который также показан на фиг. 8A и 8B, является ступенчатой, и ступенчатый выступ 58 также предусмотрен на передних сторонах. Примерный вариант осуществления, показанный на фиг. На фиг.9С показано расположение в виде шпунта и паза, а на передних сторонах также имеется ступенчатый выступ 58.Однако общим для всех примерных вариантов осуществления является то, что изолирующие оболочки 41, 42 имеют одинаковую конструкцию, так что они могут быть соединены вместе простым вращением друг относительно друга.
& lsqb; 0053 & rsqb; Особенность также показана на фиг. 13 и 14. Расстояние между трубопроводом 20 и держателем 27 трубопровода или его опорной плитой 26 на некоторых установках настолько мало, что соответствует толщине изоляции 21. Иногда это расстояние даже меньше. Чтобы, тем не менее, можно было разместить опору в соответствии с настоящим изобретением, изолирующая оболочка 28 сплющена, т.е.g., путем фрезерования ее нижней части, обращенной к держателю 27 трубопровода. В результате в изоляционной оболочке 28 образуется выемка 59, в которую помещается основание 30 каретки 29. Изоляция 21 в этой области ослабляется, что сознательно принято. Это может быть принято в свете значительно улучшенной возможности обслуживания тележки 29.
& lsqb; 0054 & rsqb; В показанных выше примерных вариантах осуществления изолирующие полуоболочки 41, 42 устанавливаются отдельно перед установкой держателя 29 на трубопроводе 20.Однако также возможно плотно расположить изолирующие полуоболочки 41, 42 на частях 31, 32 каретки. Рекомендуется, чтобы изолирующие оболочки 41, 42 были прикреплены к частям 31, 32 каретки с помощью постоянно эластичного уплотнения. состав, чтобы туда не могла проникнуть влага. Затем таким же образом наносится герметик между соединительными фланцами 33, 34. Затем пароизоляция 24 изоляции 21 должна быть помещена непосредственно на части 31, 32 каретки. Очевидно, что это труднее, так что следовательно, предпочтительным является способ поддержки, показанный на чертежах.
& lsqb; 0055 & rsqb; Хотя были показаны и подробно описаны конкретные варианты осуществления изобретения, чтобы проиллюстрировать применение принципов изобретения, следует понимать, что изобретение может быть реализовано иным образом, не отступая от таких принципов.
ПРИЛОЖЕНИЕ Список справочных номеров& lsqb; 0056 & rsqb; 20 Трубопровод
& lsqb; 0057 & rsqb; 21 Изоляция
& lsqb; 0058 & rsqb; 22 Изоляционный слой
& lsqb; 0059 & rsqb; 23 Изоляционный слой
& lsqb; 0060 & rsqb; 24 Пароизоляция
& lsqb; 0061 & rsqb; 25 Куртка защитная
& lsqb; 0062 & rsqb; 26 Опорная плита
& lsqb; 0063 & rsqb; 27 Трубопроводовоз
& lsqb; 0064 & rsqb; 28 Изоляционная оболочка
& lsqb; 0065 & rsqb; 29 вагон
& lsqb; 0066 & rsqb; 30 футов
& lsqb; 0067 & rsqb; 31 Деталь каретки
& lsqb; 0068 & rsqb; 32 Каретка часть
& lsqb; 0069 & rsqb; 33 Присоединительный фланец
& lsqb; 0070 & rsqb; 34 Присоединительный фланец
& lsqb; 0071 & rsqb; 35 Самолет дивизии
& lsqb; 0072 & rsqb; 36 Направляющее отверстие
& lsqb; 0073 & rsqb; 37 Направляющий инструмент
& lsqb; 0074 & rsqb; 38 Болт
& lsqb; 0075 & rsqb; 39 Распорная втулка
& lsqb; 0076 & rsqb; 40 Гайка
& lsqb; 0077 & rsqb; 41 Изоляционная полуоболочка
& lsqb; 0078 & rsqb; 42 Изоляционная полуоболочка
& lsqb; 0079 & rsqb; 43 Пароизоляция
& lsqb; 0080 & rsqb; 44 Площадь перекрытия
& lsqb; 0081 & rsqb; 45 Куртка защитная
& lsqb; 0082 & rsqb; 46 Болт соединение
& lsqb; 0083 & rsqb; 47 отверстие
& lsqb; 0084 & rsqb; 48 Вспомогательная рама
& lsqb; 0085 & rsqb; 49 Виселица
& lsqb; 0086 & rsqb; 50 Петля для переноски
& lsqb; 0087 & rsqb; 51 Datum level
& lsqb; 0088 & rsqb; 52 Интернет
& lsqb; 0089 & rsqb; 53 Низ
& lsqb; 0090 & rsqb; 54 Интернет
& lsqb; 0091 & rsqb; 55 Низ
& lsqb; 0092 & rsqb; 56 Разрыв
& lsqb; 0093 & rsqb; 57 Уплотнение
& lsqb; 0094 & rsqb; 58 Проекция
& lsqb; 0095 & rsqb; 59 выемка
& lsqb; 0096 & rsqb; 60 Центральная ось трубопровода
& lsqb; 0097 & rsqb; 61 вагон
& lsqb; 0098 & rsqb; 62 фут
& lsqb; 0099 & rsqb; 63 Ракушка
& lsqb; 0100 & rsqb; 64 Ракушка
Ячеистые изоляционные материалы для трубопроводов, транспортирующих сжиженный природный газ
Более детальная разработка проектов оборудования для сжиженного природного газа (СПГ) и, среди прочего, трубопроводов для его транспортировки необходима в связи с расширением производства СПГ в России и ростом газового бизнеса.Конструкция трубопровода определяется типом используемой изоляции. Практически все существующие формы низкотемпературной изоляции для оборудования СПГ описаны в технической литературе. Технические требования к производству, эксплуатации и стоимости изоляционного материала, которые несовместимы друг с другом, тем не менее, очень затрудняют определение приоритета одной формы над другими. Широкое распространение получили и считаются наиболее перспективными следующие ячеистые материалы: пенопласты, пеностекло и пенопласты, имеющие структуру с закрытыми порами; это уменьшает миграцию водяного пара во внутренние пространства изолируемых изделий.Пеностекло и пенопласт отличаются жесткой структурой; это упрощает создание пароизоляции и установку куртки. Невоспламеняемость на воздухе — важнейшее требование к изоляционным материалам. По химическому составу пеностекло — негорючий материал. Многие виды синтетических поролоновых каучуков и пенопластов становятся огнестойкими благодаря введению специальных добавок. Представляет интерес сравнение характеристик различных форм ячеистых материалов для изоляции трубопроводов СПГ.Конструкция изолированного трубопровода СПГ схематически показана на рис. 1. Трубопровод изолирован тремя слоями ячеистой изоляции (пеностекло или пенопласт). Во время производства изоляция формируется в оболочки и собирается путем закрепления сегментов оболочки на трубопроводе или на предыдущих слоях изоляции. Оболочки имеют допуск (на рисунке не показан), который компенсирует усадку изоляции при замерзании. Трубопровод имеет термоусадочные стыки, а также продольную и поперечную пароизоляцию.Последние необходимы для предотвращения миграции влаги через продольные грани оболочек. В нижней части рубашки имеется переливное отверстие для очень влажного атмосферного воздуха. В таблице 1 представлены характеристики различных форм ячеистых материалов применительно к рассматриваемой конструкции трубопровода. Также для сравнения показаны характеристики синтетического каучука Armaflex, производимого компанией Armstrong Co. [1], изоляционная технология которого несколько отличается от показанной на рисунке.Материал Kingspan Niflam является продуктом компании Kingspan Industrial Insulation Ltd. (Великобритания) и по химическому составу представляет собой полиизоцианурат, обладающий основными свойствами пенополиуретанов, но обладающий меньшей горючестью. Материал Kingspan Niflam использовался в ряде крупномасштабных проектов по изоляции оборудования и трубопроводов СПГ. Требования к процедуре изоляции и конструкции изоляции с использованием жестких пенопластов в качестве основного изоляционного материала следующие:
Новый метод усиления поврежденного трубопровода при высоких температурах с использованием неорганического изоляционного материала и композитного пластика, армированного углеродным волокном
Материалы (Базель) ).2019 ноя; 12 (21): 3484.
Цзы-Сянь Ян
2 Кафедра инженерии материалов и минеральных ресурсов, Национальный технологический университет Тайбэя, 1, сек. 3, Chung-Hsiao E. Rd., Тайбэй 10608, Тайвань
2 Кафедра инженерии материалов и минеральных ресурсов, Национальный технологический университет Тайбэя, 1, сек. 3, Chung-Hsiao E. Rd., Taipei 10608, Taiwan
Поступила в редакцию 5 октября 2019 г .; Принято 21 октября 2019 г.
Лицензиат MDPI, Базель, Швейцария.Эта статья представляет собой статью в открытом доступе, распространяемую в соответствии с условиями лицензии Creative Commons Attribution (CC BY) (http://creativecommons.org/licenses/by/4.0/). Эта статья цитировалась другими статьями в PMC. .Abstract
В данной статье был предложен метод усиления поврежденного трубопровода из жаропрочной стали с использованием неорганического изоляционного материала, который был ограничен композитными материалами из углепластика (углепластика). Два неорганических изоляционных материала состояли из магниево-фосфатного цемента (MPC), смешанного с порошками перлита и вермикулита соответственно.Обсуждалось влияние композитов изоляционных материалов с различным соотношением порошка перлита или вермикулита с точки зрения прочности на сжатие и коэффициентов теплопроводности неорганических изоляционных материалов. Также были исследованы изоляционные материалы, заключенные в полимерные оболочки, армированные углеродным волокном, для улучшения механических свойств. По результатам экспериментов, главный вывод работы заключался в том, что неорганические изоляционные материалы, добавленные к перлитовому порошку, обладали большей изоляционной способностью, чем добавленные вермикулитовые материалы, при той же прочности на сжатие.Разные соотношения цилиндров из перлитного неорганического изоляционного материала с размерами ϕ 10 см × 20 см были ограничены одним и двумя слоями композитного материала CFRP. Прочность на сжатие образцов увеличилась на 258–927% после использования однослойного композитного материала из углепластика и увеличилась на 480–1541% после нанесения двухслойного композитного материала из углепластика. Была предложена модель прогнозирования максимальной прочности изоляционных материалов, ограниченных углепластиком, и было обнаружено, что предложенная модель точно предсказывала максимальную прочность цилиндра из неорганического изоляционного материала.Наконец, было проведено контрольное испытание метода упрочнения поврежденного высокотемпературного трубопровода, чтобы доказать, что предложенный метод упрочнения осуществим.
Ключевые слова: перлит, вермикулит, изоляционный материал, углепластик, метод упрочнения
1. Введение
Нефтехимическая промышленность развивалась на протяжении многих десятилетий. Трубопроводы на нефтехимических заводах работают в высокотемпературных средах и представляют опасность, поскольку их износ приводит к уменьшению толщины трубопроводов.Повреждения трубопровода, используемого при высокой температуре, снижают его устойчивость к высоким внутренним давлениям и вызывают заметные аварии, такие как взрыв или серьезное разрушение. В настоящее время существует множество новых материалов и инновационных методов для улучшения коррозионной стойкости и улучшения теплоизоляционных работ для трубопроводов, таких как трубопровод с покрытием из минеральной ваты и нанесение покрытия на поверхность трубопровода распылением. Минеральная вата — это теплоизолятор, широко используемый в промышленности. Однако проникновение воды в систему изоляции через границу раздела между металлом и минеральной ватой неизбежно, поскольку эти стыки невозможно сделать водонепроницаемыми с помощью клея или герметиков.Когда вода проникает через систему и минеральная вата не может препятствовать проникновению воды между поверхностью раздела, может возникнуть щелевая и точечная коррозия внутренней поверхности металлического трубопровода [1].
Существующие методы упрочнения для нанесения теплоизоляционного материала на поверхность трубопровода все еще имеют проблемы, которые необходимо преодолеть, особенно когда корродированный трубопровод устанавливается в высокотемпературной среде. В целом изоляционные материалы для работ по теплоизоляции трубопроводов имеют в основном пористую морфологию, потому что пористые материалы обладают превосходными теплоизоляционными свойствами.Пористые материалы, используемые в качестве теплоизоляционного барьера на поверхности конструкции трубопровода, не могут одновременно усиливать его усиление. Однако, учитывая его легкую конструкцию, в трубопроводе используется чрезмерно тяжелый пористый материал, который не может выдерживать высокое внутреннее давление из-за корродированного трубопровода с меньшей прочностью. В частности, после того, как корродированный трубопровод, используемый в высокотемпературной среде, привел к состоянию повреждения, сильная коррозия снизила способность трубопровода к работе, что привело к аварийной аварии.Таким образом, инженерия теплоизоляционного слоя трубопровода сначала оборачивает защитным слоем поверхность неиспользуемого трубопровода, прежде чем помещать его в высокотемпературную среду. Трубопровод был покрыт водонепроницаемым материалом в качестве первого шага защитной конструкции, а затем покрыты пористые материалы в качестве теплоизоляционного слоя для теплового барьера.
В этом исследовании был предложен метод усиления трубопровода из жаропрочной стали с использованием неорганических изоляционных материалов, заключенных в композитные материалы из армированных углеродным волокном пластиков (углепластик).В последнее время цена на углеродное волокно намного ниже, чем в последние два десятилетия; поэтому углеродное волокно широко использовалось в спортивных товарах, автомобилестроении, авиакосмической промышленности и гражданском строительстве. Композитный материал из углепластика отличается стойкостью к кислотам и щелочам, антикоррозийной защитой и высоким удельным весом [2]. Композитный материал из углепластика может значительно повысить прочность трубопровода на сжатие и предотвратить утечку материала внутри трубопровода.
В этом исследовании собрана литература, связанная с коэффициентом теплопроводности и влиянием различных добавок на бетон в условиях высоких температур.Кроме того, бетонные цилиндры, ограниченные композитным материалом CFRP, были исследованы следующим образом. Вермикулит и вспученный перлит в качестве заполнителей помещали в легкий бетон, торкретбетон и глиняный стеновой кирпич, и было обнаружено, что теплопроводность снижалась с увеличением содержания вспученного перлита. Более того, увеличение содержания вспученного перлита также уменьшило модуль упругости и прочность на сжатие, тогда как модуль упругости упал более резко, чем уменьшение прочности на сжатие [3,4,5,6,7,8].Порошок минеральной ваты, печной шлак и летучая зола использовались для замены частичного содержания цемента, затем обсуждались текучесть, прочность на сжатие и некоторые механические свойства композитов [9]. Тем временем пенополистирол использовался для замены природных заполнителей в бетоне, и обсуждалась теплопроводность [10]. Различные типы легких мелких заполнителей, микрополых стеклянных сфер, волокна каннабиса, горных пород и пальмового масла вспенены в виде заполнителей бетона в ходе эксперимента по изучению влияния различного содержания воды и заполнителей на свойства теплопроводности [11,12 , 13,14].Гарсия и др. стремится исследовать, как нановолокна влияют на динамические характеристики и сопротивление расслаиванию композитов из армированного стекловолокном полимера (GFRP). Эксперименты и численное моделирование с использованием анализа методом конечных элементов (МКЭ) используются для оценки собственных частот, коэффициента демпфирования и межслойной прочности в композитах из стеклопластика [15,16].
Большинство уравнений для прогнозирования максимальной прочности бетонного цилиндра, ограниченного композитными материалами из стеклопластика, основаны на экспериментальных результатах и подгонке эмпирической кривой [17,18,19,20].Более того, Li et al. В принята теория огибающей разрушения Мора-Колумба, чтобы предложить максимальную прочность основной модели для бетонного цилиндра, ограниченного композитным материалом CFRP. Деформация при максимальной прочности была получена из регрессионного анализа экспериментальных результатов. Полиномиальное уравнение второго порядка использовалось для представления кривой напряжения-деформации конститутивной модели [21].
Были испытаны прочность ограниченного бетона FRP при нормальных и высокотемпературных условиях эксплуатации.Результаты показали, что прочность сильно снижается при высокой температуре, и композитный материал FRP не может противостоять высокотемпературной среде [22]. Mattos et al. изучили применимость композитов GFRP для ремонта ржавых металлических трубопроводов при температуре около 60–90 ° C. Потеря 70% внутреннего поперечного сечения трубопровода была отремонтирована композитным материалом GFRP. Было обнаружено, что давление повреждения результатов испытаний и аналитических результатов близко друг к другу [23].
2.Предлагаемый метод упрочнения
Иллюстрация предлагаемого метода упрочнения трубопровода из жаропрочной стали показана на рис. Два сборных изоляционных материала C-типа были помещены на верхнюю и нижнюю части или на левую и правую части трубопровода. показаны процедуры упрочняющего метода для аварийного обслуживания поврежденного трубопровода в высокотемпературном состоянии. Сначала внешняя поверхность высокотемпературного трубопровода была покрыта двумя сборными изоляционными материалами С-образной формы, а затем сборные изоляционные материалы С-образной формы были обернуты однослойной оболочкой из композитного материала углепластика.Наконец, для прикрепления оболочки из углеродного волокна использовалась эпоксидная смола, чтобы избежать неожиданного проскальзывания границы раздела между углеродным волокном и слоем изоляционного материала.
Предлагаемый способ упрочнения трубы из жаропрочной стали. ( a ) Боковое сечение; ( b ) Продольный разрез.
Технологическая схема метода восстановления высокотемпературного бывшего трубопровода. ( a ) Сборный C-образный изоляционный материал; ( b ) Трубопровод был покрыт двумя С-образными сборными изоляционными материалами; ( c ) С-образный изоляционный материал был обернут оболочкой из армированного углеродным волокном пластика (CFRP); ( d ) Эпоксидную смолу использовали в качестве клея для крепления оболочки из углепластика.
Тип эпоксидной смолы оказал значительное влияние на характеристики образцов в отношении их устойчивости к коррозии. Сборный неорганический изоляционный материал C-типа и композитный материал CFRP с эпоксидной смолой могут обеспечить отличную теплоизоляцию и водостойкость против коррозии внутреннего трубопровода. Обычно температура стеклования эпоксидной смолы составляет около 120 ° C. Однако эпоксидная смола, используемая в композитном материале из углепластика, разлагается в высокотемпературной среде, потому что высокотемпературные термические условия могут нарушить ее прочность сцепления на границе раздела углепластика и трубопровода.Чтобы уменьшить влияние тепловых условий на композитный материал из углепластика, в этом исследовании основное внимание уделялось влиянию различных добавок с магниево-фосфатным цементом (MPC) на его коэффициент теплопроводности и прочность на сжатие трубопроводов, используемых в высокотехнологичных трубопроводах. температура окружающей среды.
3. Изоляционные материалы и свойства
3.1. Материалы
Порошки перлита и вермикулита в качестве добавок для теплоизоляции были примешаны к MPC.Компонент ПДК в основном состоял из оксида магния, а компонент цемента — в основном из диоксида кремния. Особенностью МПК является быстрое затвердевание. До начального затвердевания MPC оставался только рабочий период 10-15 минут, и прочность образца увеличивалась за счет высокой ранней прочности в течение периода начального отверждения. Образец с порошком перлита и вермикулита 0, 5, 10, 15, 20 и 25 мас.% Для испытаний на прочность при сжатии и теплопроводность твердых тел.Описание различных условий образцов показано на. Для каждого дополнительного соотношения добавки было изготовлено по три образца. В общей сложности 33 образца, в том числе 3 эталона, были протестированы для испытания на сжатие и испытания на теплопроводность соответственно.
Таблица 1
Обозначение образца с различными дополнительными количествами порошков.
Название | Процент дополнительного порошка (%) |
---|---|
C | 0 |
PC | 5; 10; 15; 20; 25 |
PT | 5; 10; 15; 20; 25 |
T | 0 |
VC | 5; 10; 15; 20; 25 |
VT | 5; 10; 15; 20; 25 |
Механические свойства материала листа из углеродного волокна и эпоксидной смолы показаны на рис.Эпоксидный полимер на углеродном волокне использовался в двух случаях. Первый предназначался для перемалывания сборной оболочки из эластичного углепластика, а второй — для приклеивания внахлест сборной оболочки из углеродного волокна к С-образному теплоизоляционному слою.
Таблица 2
Свойства материала листа углеродного волокна и эпоксидной смолы.
Лист из углеродного волокна | Спецификация материалов | FAW 300 (г / м 2 ) | |
Модуль Юнга, E cf | 250 (ГПа) | ||
Предел прочности при растяжении | 4.9 (ГПа) | ||
Толщина | 0,16 (мм / слой) | ||
Предельная деформация | 0,02 | ||
Эпоксидная смола | Вязкость (25 ° C) | 56 1823 6 (сП) Модуль Юнга | 3,5 ГПа |
Прочность на разрыв | 52,2 (МПа) | ||
Прочность сцепления при растяжении | 10,5 МПа |
3.2. Испытания на прочность при сжатии и теплопроводность
Испытания на прочность на сжатие образца с размерами стандартных кубических образцов 5 мм × 5 мм × 5 мм, проведенные в соответствии с ASTM C109 / C M109-02 [24].Эта программа испытаний была проведена на универсальной испытательной машине мощностью 100 тс в лаборатории материалов Департамента гражданского строительства Национального технологического университета Тайбэя. На рисунке представлена иллюстративная фотография испытания на сжатие кубического образца.
Иллюстрированная фотография испытания на сжатие кубического образца.
Для твердой теплопроводности материала был принят закон Фурье, согласно которому тепловой поток пропорционален градиенту температуры, как показано в уравнении (1).
куда,
dQdt: Тепловой поток (Единица: Вт)
A: Тепловой поток через площадь поперечного сечения (Единица: м 2 )
k: Коэффициент теплопроводности (Единица: Вт / ( м ° C))
∇T: Температурный градиент вдоль направления теплового потока (Единица: ° C / м)
Образец для испытаний на теплопроводность представляет собой цилиндрический корпус диаметром 5,6 см и длиной 6 см для испытание на коэффициент теплопроводности в соответствии со спецификациями ASTM E1225-13 [25].Электрическая штанга в качестве источника нагрева обеспечивала тепловой источник образца над медным блоком, как показано на рисунке а. Термопаста была наклеена на верхнюю и нижнюю стороны образца, контактное термическое сопротивление на границе раздела медного блока. Были построены три контактных отверстия с интервалом расстояния от источника тепла 1 см, 3 см и 5 см соответственно, как показано на b. Измерение температуры проводилось термопарой Т-типа. Этот тест предполагался как только одно измерение теплового потока, и теплопроводность материала была рассчитана в соответствии с уравнением (1).
Иллюстрация теста на теплопроводность (SUS304, Xiwnag Jiazu LTD., Гаосюн, Тайвань). ( a ) Установка для испытания теплопроводности; ( b ) Образец для испытания на теплопроводность.
4. Результаты испытаний изоляционных материалов
4.1. Результаты испытаний на сжатие
Образец для испытания на сжатие был изготовлен из MPC, смешанного с перлитом или вермикулитом, и сформирован в виде испытательного блока размером 5 см × 5 см × 5 см. Отношение воды к ПДК было 0.22, а прочность на сжатие проверяли на универсальной испытательной машине через 3 дня. Прочность на сжатие образцов с разным количеством смешанных ПДК перлита и вермикулита представлена на рис. Прочность на сжатие образцов уменьшалась по мере увеличения содержания порошка перлита или вермикулита, независимо от того, какая добавка порошка перлита или вермикулита, смешанного с ПДК. Уменьшение прочности на сжатие было более очевидным при увеличении добавки перлита, чем при увеличении добавки вермикулита, смешанного с ПДК.Чтобы увеличить массовую долю порошков перлита и вермикулита с 0% до 25%, добавленных в бетонный блок, можно снизить прочность на сжатие, как показано на. Хотя порошок перлита имеет слабую прочность на сжатие, следующее испытание на теплопроводность показало, что он обладает хорошей теплоизоляцией благодаря своей пористой структуре.
Диаграмма зависимости между прочностью на сжатие и содержанием перлита или вермикулита (по весу в процентах) в смеси с магниево-фосфатным цементом (ПДК).
Таблица 3
Средняя 3-дневная прочность на сжатие классифицированных образцов.
Образец | Средняя прочность на сжатие (МПа) | Образец | Средняя прочность на сжатие (МПа) | |||||||||||||||||||||||||||||||||||||||||||||||||||||||||||||||||||||||||||||||||||||||||||||||||||||||||||||||||||||||||||||||||||||||||||||||||||||||||||||||||||||||||||||||||||||||||||||||||||||||||||||||||||||||||||||||||||||||||
---|---|---|---|---|---|---|---|---|---|---|---|---|---|---|---|---|---|---|---|---|---|---|---|---|---|---|---|---|---|---|---|---|---|---|---|---|---|---|---|---|---|---|---|---|---|---|---|---|---|---|---|---|---|---|---|---|---|---|---|---|---|---|---|---|---|---|---|---|---|---|---|---|---|---|---|---|---|---|---|---|---|---|---|---|---|---|---|---|---|---|---|---|---|---|---|---|---|---|---|---|---|---|---|---|---|---|---|---|---|---|---|---|---|---|---|---|---|---|---|---|---|---|---|---|---|---|---|---|---|---|---|---|---|---|---|---|---|---|---|---|---|---|---|---|---|---|---|---|---|---|---|---|---|---|---|---|---|---|---|---|---|---|---|---|---|---|---|---|---|---|---|---|---|---|---|---|---|---|---|---|---|---|---|---|---|---|---|---|---|---|---|---|---|---|---|---|---|---|---|---|---|---|---|---|---|---|---|---|---|---|---|---|---|---|---|---|---|---|---|---|---|---|---|---|---|---|---|---|---|---|---|---|---|---|---|---|
C0 | 35.60 | 56 — 0 ПКVC05 | 21,67 | |||||||||||||||||||||||||||||||||||||||||||||||||||||||||||||||||||||||||||||||||||||||||||||||||||||||||||||||||||||||||||||||||||||||||||||||||||||||||||||||||||||||||||||||||||||||||||||||||||||||||||||||||||||||||||||||||||||||||
PC10 | 7,85 | VC10 | 14.38 | |||||||||||||||||||||||||||||||||||||||||||||||||||||||||||||||||||||||||||||||||||||||||||||||||||||||||||||||||||||||||||||||||||||||||||||||||||||||||||||||||||||||||||||||||||||||||||||||||||||||||||||||||||||||||||||||||||||||||
PC15 | 3,81 | VC15 | 9,02 | |||||||||||||||||||||||||||||||||||||||||||||||||||||||||||||||||||||||||||||||||||||||||||||||||||||||||||||||||||||||||||||||||||||||||||||||||||||||||||||||||||||||||||||||||||||||||||||||||||||||||||||||||||||||||||||||||||||||||
PC20 | 2,39 | VC20 | 5,2 | |||||||||||||||||||||||||||||||||||||||||||||||||||||||||||||||||||||||||||||||||||||||||||||||||||||||||||||||||||||||||||||||||||||||||||||||||||||||||||||||||||||||||||||||||||||||||||||||||||||||||||||||||||||||||||||||||||||||||
5,2 | ||||||||||||||||||||||||||||||||||||||||||||||||||||||||||||||||||||||||||||||||||||||||||||||||||||||||||||||||||||||||||||||||||||||||||||||||||||||||||||||||||||||||||||||||||||||||||||||||||||||||||||||||||||||||||||||||||||||||||||
PC1001 9103 | 9 Результаты испытаний на теплопроводность
Образец | Средний коэффициент теплопроводности (Вт / (м ° C)) | Образец | Средний коэффициент теплопроводности (Вт / (м ° C)) | ||||||||||||||||||||||||||||||||||||||||||||||||||||||||||||||||||||||||||||||||||||||||||||||||||||||||||||||||||||||||||||||||||||||||||||||||||||||||||||||||||||||||||||||||||||||||||||||||||||||||||||||||
---|---|---|---|---|---|---|---|---|---|---|---|---|---|---|---|---|---|---|---|---|---|---|---|---|---|---|---|---|---|---|---|---|---|---|---|---|---|---|---|---|---|---|---|---|---|---|---|---|---|---|---|---|---|---|---|---|---|---|---|---|---|---|---|---|---|---|---|---|---|---|---|---|---|---|---|---|---|---|---|---|---|---|---|---|---|---|---|---|---|---|---|---|---|---|---|---|---|---|---|---|---|---|---|---|---|---|---|---|---|---|---|---|---|---|---|---|---|---|---|---|---|---|---|---|---|---|---|---|---|---|---|---|---|---|---|---|---|---|---|---|---|---|---|---|---|---|---|---|---|---|---|---|---|---|---|---|---|---|---|---|---|---|---|---|---|---|---|---|---|---|---|---|---|---|---|---|---|---|---|---|---|---|---|---|---|---|---|---|---|---|---|---|---|---|---|---|---|---|---|---|---|---|---|---|---|---|---|---|---|---|---|
— | — | ||||||||||||||||||||||||||||||||||||||||||||||||||||||||||||||||||||||||||||||||||||||||||||||||||||||||||||||||||||||||||||||||||||||||||||||||||||||||||||||||||||||||||||||||||||||||||||||||||||||||||||||||||
PT05 | 0,411 | VT05 | 0,422 | ||||||||||||||||||||||||||||||||||||||||||||||||||||||||||||||||||||||||||||||||||||||||||||||||||||||||||||||||||||||||||||||||||||||||||||||||||||||||||||||||||||||||||||||||||||||||||||||||||||||||||||||||
PT10 | 0,374 | VT10 | 0,412 | 6 VT10 | 0,412 | 6346 | VT15 | 0,393 | |||||||||||||||||||||||||||||||||||||||||||||||||||||||||||||||||||||||||||||||||||||||||||||||||||||||||||||||||||||||||||||||||||||||||||||||||||||||||||||||||||||||||||||||||||||||||||||||||||||||||||
PT20 | 0,322 | VT20 | 0,365 | ||||||||||||||||||||||||||||||||||||||||||||||||||||||||||||||||||||||||||||||||||||||||||||||||||||||||||||||||||||||||||||||||||||||||||||||||||||||||||||||||||||||||||||||||||||||||||||||||||||||||||||||||
PT25 | 0,295 | VT25 | различные и различные эффекты, | 0,344 | в образцах, связанных с их прочностью на сжатие и коэффициентом теплопроводности. Wongkeo et al. [27] использовали зольный остаток для замены цемента в бетоне с весовым соотношением 0%, 10%, 20% и 30%.При замене на 10% прочность на сжатие составляла 10,1 МПа. Эксперимент был основан на прочности на сжатие 10 МПа в качестве критерия и с помощью метода интерполяции были получены оптимальные количества добавок перлита и вермикулита 8% и 13%, см. Результаты показали, что прочность на сжатие образца, смешанного с порошком вермикулита, была выше, чем у образца, смешанного с порошком перлита. Напротив, добавка порошка вермикулита в образец не усиливала его теплоизоляционный эффект.Скорость потока суспензии при добавлении порошка перлита была выше, чем при добавлении порошка вермикулита. Поэтому для смешивания с MPC был выбран порошок перлита из-за хорошей теплоизоляции и обрабатываемости. После проведения испытания на теплопроводность и испытания на прочность на сжатие теплоизоляционного слоя, основанного на различных параметрах состава порошков перлита и вермикулита, прочность на сжатие порошка перлита, смешанного с цилиндрическим образцом MPC, ограниченным композитным материалом CFRP, будет обсуждаться в следующий раздел. 5. Испытание на сжатие конфайнмента из углепластикаОбзор более ранней литературы показал, что существующие основные модели замкнутого бетона были предложены для обеспечения высокой прочности. Однако пористый изоляционный материал является материалом с низкой прочностью, и в нескольких исследованиях изучались испытания на одноосное сжатие низкопрочного материала, такого как пористый изоляционный раствор, заключенный в оболочку из углепластика. В этом исследовании был предложен новый метод усиления высокотемпературного трубопровода, заключающийся в нанесении на него двух сборных неорганических изоляционных слоев С-образной формы.Затем обернули сборную оболочку из углепластика, чтобы ограничить неорганические изоляционные слои. 5.1. Подготовка образцов и экспериментальная установкаТонкий слой эпоксидной грунтовки, нанесенный на поверхность цилиндра для раствора. После того как грунтовочная эпоксидная смола на поверхности раствора была отверждена, лист из углеродного волокна был намотан на поверхность цилиндров изоляционного материала. На каждый слой листа из углеродного волокна наносили эпоксидную смолу с помощью малярной кисти, чтобы глубоко погрузить углеродное волокно.Излишки эпоксидной смолы для каждого слоя выдавливались с помощью плоского пластикового скребка. Как видно на фиг., Если прочность на сжатие образца с изоляционным материалом достигает 10 МПа, содержание изоляционного материала, смешанного с перлитом, составляет около 8%. Соответствующие соотношения перлита составляли 8%, 15%, 20% и 25%, а размер составлял ϕ10 см × 20 см. Каждый из цилиндров изоляционного материала был обернут дополнительным однослойным и двухслойным композитным материалом CFRP. Для каждого экспериментального параметра добавки перлита были изготовлены три цилиндра изоляционного материала.Три цилиндра без углепластика использовались в качестве эталона (эталона). Всего было протестировано 36 цилиндров из изоляционного материала; регулируемыми параметрами цилиндров являются соотношение перлита и количество слоев углепластика, как показано на. Обозначения образца показали следующее. Первая буква «P» обозначает перлит, следующее число обозначает процентное соотношение перлита; вторая буква «C» обозначала изоляцию из углепластика, а следующее число означало количество слоев композитного материала из углепластика. Таблица 5Расчетные параметры и обозначения образцов 36 бетонных цилиндров.
Эта программа испытаний была проведена на универсальной испытательной машине 100 тс в лаборатории материалов Департамента гражданского строительства Национального технологического университета Тайбэя.Экспериментальное оборудование включало датчик веса, линейный трансформатор смещения напряжения, аналого-цифровой преобразователь с усилителем сигнала и персональный компьютер, показанные на рис. Чтобы гарантировать, что одноосное усилие прикладывается равномерно к верхней и нижней поверхностям цилиндра из раствора, две поверхности образца были покрыты гипсовой пастой по горизонтали. Скорость нагружения актуатора составляла 1 мм / сек, и процесс нагружения прекращался, когда осевая нагрузка начинала уменьшаться. Иллюстрированная фотография испытания на сжатие цилиндрического образца. 5.2. Результаты испытаний на сжатиеТри тензодатчика были установлены сверху, посередине и снизу каждого цилиндра из изоляционного материала, обернутого композитным материалом CFRP; и были измерены поперечные деформации цилиндра изоляционного материала. Поскольку деформация цилиндра изоляционного материала была неоднородной, измеренные деформации показали изменчивость. — кривые деформирования образцов P08C1, когда напряжение достигает 16 МПа, жесткость начинает уменьшаться.Когда напряжение достигает предела прочности, образец при разрушении издавал громкий взрывной звук. Фотографии отказов образца P08C1 показаны на рис. Иллюстрированная фотография испытания на сжатие цилиндрических образцов P08C1. Фотографии отказов образцов P08C1. Прочность на сжатие образца с прикрепленными изоляционными материалами после нанесения укрепляющего слоя, восстановленного углепластиком, показана на. Прочность на сжатие образцов P08, P15, P20 и P25 была увеличена на 258–927% после удержания однослойным композитным материалом CFRP, а у образцов P08, P15, P20 и P25 увеличилась на 480%. –1541% после ограничения двухслойным композитным материалом CFRP.Результаты показали, что прочность на сжатие образца с изоляционными материалами, ограниченными композитными материалами из углепластика, может эффективно увеличиваться. Таблица 6Прочность изоляционных материалов на сжатие после нанесения углепластиком.
5.3. Предлагаемая формула максимального напряженияФормула максимального напряжения изоляционного материала, ограниченного углепластиком, была принята в соответствии с основной моделью, предложенной Ли и др.[19]. Основную физическую модель ограниченной прочности образца с изоляционными материалами (fcc ‘) можно выразить следующим образом: fcc’ = fco ‘+ fl’tan2 (450 + ϕ2) (единица измерения: МПа) (2) куда fl ‘= kc2 × n × t × Ecf × εcfD (единица измерения: МПа) (3) В уравнении (2) fco’ — прочность неизолированного изоляционного материала, fl ‘- эффективное поперечное ограниченное напряжение Углепластик, а ϕ — угол внутреннего трения изоляционного материала.В уравнении (3) kc — коэффициент формы сечения, n — количество слоев углепластика, t — толщина углепластика на слой, Ecf — модуль упругости углепластика, εcf — предельное значение. деформация углепластика, измеренная с помощью тензодатчика в испытании на сжатие (εcf = 1%, полученное в результате испытания на сжатие), и D — диаметр цилиндра. В уравнении (2) угол внутреннего трения зависит от прочности изоляционного материала, и он может быть выражен как линейная зависимость прочности изоляционного материала, как показано в уравнении (4), где a и b — коэффициенты, которые должны быть определяется регрессионным анализом. ϕ = a0 + 10 (fco’b) ≤450 (Единица: степень) (4) Из регрессионного анализа это исследование получило a = 16 и b = 7. Экспериментальные и предложенные теоретические значения прочности на сжатие изоляционного материала показаны на; а квадрат коэффициента корреляции (R2) равен 0,987. Как показано в, средняя абсолютная ошибка прочности на сжатие между экспериментальными данными и предложенной теоретической формулой составляет 3,33%. Предлагаемая формула может точно предсказать прочность на сжатие образца с ограниченным изоляционным материалом. Диаграмма взаимосвязи экспериментальной и предполагаемой теоретической силы. Таблица 7Анализ ошибок прочности на сжатие между экспериментом и предложенной формулой.
6.2. Результаты экспериментов и наблюденияЭксперимент был направлен на понимание влияния различных дополнительных соотношений перлита на теплоизоляцию. Для фиксированной толщины 25 мм были запланированы три различных соотношения перлита С-образных сборных изоляционных материалов, а именно образцы P08-25, P15-25 и P25-25. Образец P25-25 был выбран для первого эксперимента, образец P25-25 имел содержание 25% перлита с C-образным сборным изоляционным материалом толщиной 25 мм.Когда стальная труба нагревается до 200 ℃ в течение 17 часов, а система отопления остается в устойчивом состоянии; температура поверхности углепластика составляет около 85 ℃. Разница температур между стальной трубой и поверхностью из углепластика составляет 115 ℃ из-за изоляционного эффекта С-образного изоляционного материала. С-образный изоляционный материал был удален после охлаждения стальной трубы до комнатной температуры; На образце P25-25 из-за термического воздействия наблюдалось небольшое количество микротрещин. Однако композитный материал CFRP не был поврежден; наблюдаемое изображение образца P25-25, как показано на рисунке, хотя текстура излома возникает только с небольшими микротрещинами после теплового эксперимента.Как видно на a – c, образцы P08-25 и P15-25, экспериментальные результаты были аналогичны результатам образца P25-25, за исключением температур на поверхности углепластика. Приведенные температуры образцов с различным соотношением перлита показаны на рис. Как видно из экспериментальных результатов более высокого значения пониженной температуры, высокая температура с использованием трубопроводов уменьшала термическое повреждение при более высоком содержании перлита в С-образных изоляционных материалах и, следовательно, имела более сильную армирующую способность. В С-образных изоляционных материалах после нагрева было обнаружено несколько микротрещин. ( a ) Образец P08-25; ( b ) Образец P15-25; ( c ) Образец P25-25; ( d ) Образец П25-35. Таблица 9Измеренные температуры и обозначения образцов с различным соотношением перлита.
Были исследованы сборные С-образные изоляционные материалы трех различных толщин. образцы П25-15, П25-25 и П25-35, для фиксированного перлитного соотношения.Когда стальную трубу нагревали до 200 ℃ в течение 17 часов, температура поверхности углепластика составляла около 104 ° C и 75 ° C для образцов GP25-P15 и GP25-35 соответственно. Точно так же в образцах P25-15 и GP25-35 было обнаружено несколько микротрещин из-за термического повреждения, экспериментальные результаты были аналогичны результатам образца P25-25 после термической атаки, за исключением температур на поверхности углепластика, показанных на CD. Измеренные температуры образцов разной толщины представлены на рис.Как видно из экспериментальных результатов, толщина С-образных изоляционных материалов увеличивала пониженную температуру изоляционных материалов. Таблица 10Измеренные температуры углепластика образцов разной толщины.
7.ВыводыПо результатам исследования можно сделать следующие выводы:
БлагодарностиАвторы хотели бы поблагодарить Кайла Ходоуани за исправление английского текста этой рукописи. Вклад авторовКонцептуализация, Y.-F.L .; курирование данных, T.-H.T .; формальный анализ, T.-H.T .; расследование, T.-H.Y. и T.-H.T .; методология, Ю.-Ф.Л. и T.-H.Y .; администрация проекта, Ю.-Ф.Л .; надзор, Ю.-Ф.Л .; письменность — черновик, Т.-Х.Й. и T.-H.T .; написание — просмотр и редактирование, Ю.-Ф.Л. ФинансированиеЭто исследование финансировалось Министерством науки и технологий правительства Тайваня по контракту №MOST-105-2221-E-027-025 и «Исследовательский центр энергосбережения для нового поколения жилого, коммерческого и промышленного секторов» Министерства образования Тайваня. Конфликт интересовАвторы заявляют об отсутствии конфликта интересов. Список литературы1. Эльчалакани М. Восстановление корродированной стали CHS при комбинированном изгибе и опоре с использованием углепластика. J. Constr. Steel Res. 2016; 125: 26–42. DOI: 10.1016 / j.jcsr.2016.06.008. [CrossRef] [Google Scholar] 2.Вуттон И., Спейнхур Л., Яздани Н. Коррозия стальной арматуры в бетонных цилиндрах, армированных углеродным волокном и полимером. J. Compos. Констр. 2003. 7: 339–347. DOI: 10.1061 / (ASCE) 1090-0268 (2003) 7: 4 (339). [CrossRef] [Google Scholar] 3. Сенгуль О., Азизи С., Караосманоглу Ф., Тасдемир М.А. Влияние вспученного перлита на механические свойства и теплопроводность легкого бетона. Энергетика. 2011. 43: 671–676. DOI: 10.1016 / j.enbuild.2010.11.008. [CrossRef] [Google Scholar] 4. Лю В.В., Апель Д. Б., Биндиганавиле В. С. Тепловые свойства легкого сухого торкретбетона, содержащего вспученный перлитный заполнитель. Джем. Concr. Compos. 2014; 53: 44–51. DOI: 10.1016 / j.cemconcomp.2014.06.003. [CrossRef] [Google Scholar] 5. Джедиди М., Бенджедду О., Суси К. Влияние дозировки вспученного перлитного заполнителя на свойства легкого бетона. Jordan J. Civil Eng. 2015; 159: 1–14. DOI: 10.14525 / jjce.9.3.3071. [CrossRef] [Google Scholar] 6. Рамезанианпур А.А., Карейн С.М.М., Восуги П., Пильвар А., Исапур С., Муди Ф. Влияние обожженного перлитового порошка как SCM на прочность и проницаемость бетона. Констр. Строить. Матер. 2014; 66: 222–228. DOI: 10.1016 / j.conbuildmat.2014.05.086. [CrossRef] [Google Scholar] 7. Topçu İ.B., Işıkdağ B. Производство глиняных кирпичей с высокой теплопроводностью, содержащих перлит. Строить. Environ. 2007. 42: 3540–3546. DOI: 10.1016 / j.buildenv.2006.10.016. [CrossRef] [Google Scholar] 8. Türkmen I., Kantarcı A. Влияние вспученного перлитового заполнителя и различных условий отверждения на физико-механические свойства самоуплотняющегося бетона.Строить. Environ. 2007. 42: 2378–2383. DOI: 10.1016 / j.buildenv.2006.06.002. [CrossRef] [Google Scholar] 9. Абиди С., Наит-Али Б., Джолифф Ю., Фавотто С. Влияние перлита, вермикулита и цемента на теплопроводность гипсового композитного материала: экспериментальные и численные подходы. Compos. Часть B англ. 2015; 68: 392–400. DOI: 10.1016 / j.compositesb.2014.07.030. [CrossRef] [Google Scholar] 10. Демирбога Р., Кан А. Теплопроводность и усадочные свойства бетонов из модифицированных отходов полистирольного заполнителя.Констр. Строить. Матер. 2012; 35: 730–734. DOI: 10.1016 / j.conbuildmat.2012.04.105. [CrossRef] [Google Scholar] 11. Хан М.И. Факторы, влияющие на тепловые свойства бетона и применимость его прогнозных моделей. Строить. Environ. 2002. 37: 607–614. DOI: 10.1016 / S0360-1323 (01) 00061-0. [CrossRef] [Google Scholar] 12. Юн Т.С., Чон Й.Дж., Хан Т.-С., Юм К.-С. Оценка теплопроводности теплоизоляционных бетонов. Энергетика. 2013; 61: 125–132. DOI: 10.1016 / j.enbuild.2013.01.043. [CrossRef] [Google Scholar] 13.Лю М.Ю.Дж., Аленгарам Ю.Дж., Джумаат М.З., Мо К.Х. Оценка теплопроводности, механических и транспортных свойств легковесного пеногеополимерного бетона. Энергетика. 2014; 72: 238–245. DOI: 10.1016 / j.enbuild.2013.12.029. [CrossRef] [Google Scholar] 14. Колле Ф., Прето С. Теплопроводность конопляных бетонов: в зависимости от состава, плотности и содержания воды. Констр. Строить. Матер. 2014; 65: 612–619. DOI: 10.1016 / j.conbuildmat.2014.05.039. [CrossRef] [Google Scholar] 15. Гарсия К., Трендафилова И., Цукчелли А. Влияние нановолокон поликапролактона на динамическое и ударное поведение полимерных композитов, армированных стекловолокном. J. Compos. Sci. 2018; 2: 43. DOI: 10.3390 / jcs2030043. [CrossRef] [Google Scholar] 16. Гарсия К., Трендафилова И., Цукчелли А., Контрерас Дж. Влияние нейлоновых нановолокон на динамическое поведение и сопротивление расслаиванию композитов из стеклопластика. Веб-конференция MATEC. 2018; 148: 14001. DOI: 10.1051 / matecconf / 201814814001. [CrossRef] [Google Scholar] 17. Тэн Дж., Цзян Т., Лам Л., Луо Ю. Уточнение ориентированной на расчет модели напряжения-деформации для бетона с ограниченным стеклопластиком. J. Compos. Констр. 2009. 13: 269–278. DOI: 10.1061 / (ASCE) CC.1943-5614.0000012. [CrossRef] [Google Scholar] 18. Сеффо М., Хамчо М. Прочность бетонного цилиндра, заключенного в энергетические процедуры из композитных материалов (углепластик). 2012; 19: 276–285. DOI: 10.1016 / j.egypro.2012.05.207. [CrossRef] [Google Scholar] 19. Русакис Т.К., Ракицис Т.Д., Карабинис А.И. Расчетно-ориентированная модель прочности для бетонных элементов из стеклопластика.J. Compos. Констр. 2012; 16: 615–625. DOI: 10.1061 / (ASCE) CC.1943-5614.0000295. [CrossRef] [Google Scholar] 20. Nisticò N., Pallini F., Rousakis T., Wu Y.-F., Karabinis A. Прогнозирование максимальной прочности и предельной деформации для ограниченных квадратных и круглых бетонных секций из FRP. Compos. Часть B англ. 2014; 67: 543–554. DOI: 10.1016 / j.compositesb.2014.07.026. [CrossRef] [Google Scholar] 21. Ли Я.-Ф., Лин Ч.-Т., Сун Я.-Й. Базовая модель для бетона, армированного углеродным волокном пластика. Мех. Матер.2003. 35: 603–619. DOI: 10.1016 / S0167-6636 (02) 00288-0. [CrossRef] [Google Scholar] 22. Аль-Саллум Я.А., Эльсанадеди Х.М., Абадель А.А. Поведение бетона из стеклопластика после воздействия высоких температур. Констр. Строить. Матер. 2011; 25: 838–850. DOI: 10.1016 / j.conbuildmat.2010.06.103. [CrossRef] [Google Scholar] 23. Да Коста Маттос Х.С., Рейс Дж.М.Л., Пайм Л.М., да Силва М.Л., Аморим Ф.С., Перрут В.А. Анализ системы ремонта армированного стекловолокном полиуретанового композитного материала для трубопроводов, подвергшихся коррозии при повышенных температурах.Композитные конструкции. 2014; 114: 117–123. DOI: 10.1016 / j.compstruct.2014.04.015. [CrossRef] [Google Scholar] 24. ASTM C109 / C M109-02. Стандартный метод испытаний гидравлических цементных растворов на сжатие. ASTM International; Вест Коншохокен, Пенсильвания, США: 2016 г. [Google Scholar] 25. ASTM E1225-13. Стандартный метод испытания теплопроводности твердых тел с использованием метода ограниченного сравнительного продольного теплового потока. ASTM International; Вест Коншохокен, Пенсильвания, США: 2013 г. [Google Scholar] 26. Демирбога Р., Гюль Р. Влияние вспученного перлита, микрокремнезема и летучей золы на теплопроводность легкого бетона. Джем. Concr. Res. 2003. 33: 723–727. DOI: 10.1016 / S0008-8846 (02) 01032-3. [CrossRef] [Google Scholar] 27. Вонгкео В., Тонгсанитгарн П., Пимракса К., Чайпанич А. Прочность на сжатие, прочность на изгиб и теплопроводность автоклавного бетонного блока, изготовленного с использованием зольной пыли в качестве материалов для замены цемента. Матер. Des. 2012; 35: 434–439. DOI: 10.1016 / j.matdes.2011.08.046. [CrossRef] [Google Scholar]сек.gov | Превышен порог скорости запросовЧтобы обеспечить равный доступ для всех пользователей, SEC оставляет за собой право ограничивать запросы, исходящие от необъявленных автоматизированных инструментов. Ваш запрос был идентифицирован как часть сети автоматизированных инструментов за пределами допустимой политики и будет обрабатываться до тех пор, пока не будут приняты меры по объявлению вашего трафика. Укажите свой трафик, обновив свой пользовательский агент, включив в него информацию о компании. Для лучших практик по эффективной загрузке информации из SEC.gov, включая последние документы EDGAR, посетите sec.gov/developer. Вы также можете подписаться на рассылку обновлений по электронной почте о программе открытых данных SEC, включая передовые методы, которые делают загрузку данных более эффективной, и улучшения SEC.gov, которые могут повлиять на процессы загрузки по сценарию. Для получения дополнительной информации обращайтесь по адресу [email protected]. Для получения дополнительной информации см. Политику конфиденциальности и безопасности веб-сайта SEC. Благодарим вас за интерес к Комиссии по ценным бумагам и биржам США. Идентификатор ссылки: 0.7ecef50.1635454580.2c9cc89c Дополнительная информацияПолитика безопасности в ИнтернетеИспользуя этот сайт, вы соглашаетесь на мониторинг и аудит безопасности. В целях безопасности и обеспечения того, чтобы общедоступная услуга оставалась доступной для пользователей, эта правительственная компьютерная система использует программы для мониторинга сетевого трафика для выявления несанкционированных попыток загрузки или изменения информации или иного причинения ущерба, включая попытки отказать пользователям в обслуживании. Несанкционированные попытки загрузить информацию и / или изменить информацию в любой части этого сайта строго запрещены и подлежат судебному преследованию в соответствии с Законом о компьютерном мошенничестве и злоупотреблениях 1986 года и Законом о защите национальной информационной инфраструктуры 1996 года (см. Раздел 18 U.S.C. §§ 1001 и 1030). Чтобы обеспечить хорошую работу нашего веб-сайта для всех пользователей, SEC отслеживает частоту запросов на контент SEC.gov, чтобы гарантировать, что автоматический поиск не влияет на возможность доступа других лиц к контенту SEC.gov. Мы оставляем за собой право блокировать IP-адреса, которые отправляют чрезмерное количество запросов. Текущие правила ограничивают пользователей до 10 запросов в секунду, независимо от количества машин, используемых для отправки запросов. Если пользователь или приложение отправляет более 10 запросов в секунду, дальнейшие запросы с IP-адреса (-ов) могут быть ограничены на короткий период.Как только количество запросов упадет ниже порогового значения на 10 минут, пользователь может возобновить доступ к контенту на SEC.gov. Эта практика SEC предназначена для ограничения чрезмерного автоматического поиска на SEC.gov и не предназначена и не ожидается, чтобы повлиять на людей, просматривающих веб-сайт SEC.gov. Обратите внимание, что эта политика может измениться, поскольку SEC управляет SEC.gov, чтобы гарантировать, что веб-сайт работает эффективно и остается доступным для всех пользователей. Примечание: Мы не предлагаем техническую поддержку для разработки или отладки процессов загрузки по сценарию. . akson-quick.ru © 2019
|