Производство сэндвич панелей: основы технологии
Основные критерии при выборе материалов для строительства различных объектов ─ определенные технико-эксплуатационные показатели, простота применения и доступная цена. Стеновые и кровельные сэндвич панели полностью соответствуют этим требованиям, поскольку отличаются приемлемой стоимостью и небольшой трудоемкостью сборки. Используя их при сооружении различных объектов, можно значительно сократить затраты на строительство и сроки введения в эксплуатацию.
Преимущества применения
Популярность сэндвич панелей объяснима и другими характеристиками. Среди них можно выделить:
Устойчивость к воздействию климата и влаги. Полимерное покрытие защищает металл от появления ржавчины.
Долговечность эксплуатации. Прочная сталь сохраняет свои параметры в течение длительного срока.
Небольшой вес. Благодаря этомусэндвич панели не требуют использования тяжелой техники при их погрузке и перемещении, а также не нуждаются в устройстве массивного фундамента.
Хорошие изоляционные показатели. Пенополистирол и минеральная вата отличаются низкой теплопроводностью, поэтому являются эффективной защитой в условиях низких температур. Кроме того, для них характерны и хорошие звукоизоляционные свойства
Стойкость к возгоранию и экологичность. Для изготовления сэндвич панелей используются материалы, которые не содержат ядовитых компонентов. Они устойчивы к воспламенению и не выделяют вредных веществ во время монтажа и эксплуатации.
Разнообразие оттенков сэндвич панелей позволяет подобрать цвет, который будет сочетаться с объектами на прилегающей территории. Состав покрытия защищает от солнечных лучей и сохраняет интенсивность окраски длительное время. Простота сборки изделий обусловлена их конструктивными особенностями и наличием замков со специальным механизмом фиксации. Он надежно скрепляет отдельные листы между собой, обеспечивая прочность и герметичность соединений.
Особенности технологии
В качестве основы для изготовления сэндвич панелей служит оцинкованная или алюмоцинкованная сталь, толщина которой составляет 5-7 мм. Степень защиты материала от появления коррозии определяется параметрами слоя цинка или алюмоцинка. Для первого варианта достаточно 7-20 мкм при оцинковке второго класса, а для оцинковки первого класса ─ более 20 мкм. Толщина алюмоцинкового покрытия обычно составляет 13-23 мкм. Нанесение поверх полимерного слоя обеспечивает дополнительную защиту металла от коррозии.
Производство сэндвич панелей может выполняться двумя способами: стендовым и непрерывным. В первом случае изготовление изделий осуществляется периодически и применимо для небольших партий продукции. Непрерывный выпуск производится в промышленных масштабах. Каждый метод имеет свои особенности и необходимое для его реализации оснащение.
Стендовая технология
Для ее внедрения не требуются значительные производственные площади: обычно все оборудование можно расположить поблизости от строительной площадки. Технологический цикл изготовления сэндвич панелей включает следующие операции:
- резку листов стали и их профилирование;
- нанесение специального клея на внутренние поверхности;
- укладка утеплителя и его совмещение с листами металла;
- прессование.
Для фиксации слоев используют однокомпонентные или двухкомпонентные составы на основе полиуретана.
Непрерывная технология
Более эффективным является производство сэндвич панелей непрерывным методом, который позволяет получать продукцию высокого качества. Для этого служат специальные автоматизированные линии. Технологический процесс проходит следующим образом:
- устанавливают два рулона оцинкованной стали на линию, располагая их так, чтобы поверхности с полимерным слоем находились снаружи;
- используя форсунки высокого давления, наносят полиуретановый клей на металлические листы;
- раскладывают утеплитель по ширине с помощью толкателей;
- выполняют прессование с одновременным формированием замковых соединений, вид и конструкция которых зависят от назначения сэндвич панелей;
- нарезают материал на отдельные элементы определенных размеров;
- упаковывают готовую продукцию.
Благодаря такой технологии можно купить сэндвич панели и для возведения несущих стен и перегородок, и для сооружения кровли. Прочность соединения отдельных слоев обеспечивается за счет отвердевания клея под воздействием высокой температуры и давления. Упаковка готовых изделий необходима для защиты полимерного слоя во время транспортировки и разгрузки.
В компании и «ТермоСпецПанель» изготовление сэндвич панелей и металлоконструкций осуществляется согласно установленным стандартам и требованиям системы менеджмента качества ISO. Наличие современных производственных линий и персонала высокой квалификации позволяет выпускать изделия, которые отличаются хорошими технико-эксплуатационными характеристиками и приемлемой стоимостью.
У нас вы можете купить сэндвич панели стеновые и кровельные разных размеров и цветовых решений. В качестве утеплителя мы используем пенополистирол и минеральную вату, которые отличаются низкой теплопроводностью и обеспечивают надежную защиту внутреннего пространства помещений от низких температур.
Скрепление теплоизоляции и металлических листов выполняется с помощью двухкомпонентного клея на полиуретановой основе. Он прочно фиксирует все слои и не теряет свои параметры в процессе эксплуатации.
Специальные доборные элементы, которые поставляются и в комплекте с пачками сэндвич панелей, обеспечивают защиту стыков и узлов соединения от воздействий климата и влаги. Кроме того, они выполняют и эстетические функции, придавая сооружениям из сэндвич панелей завершенность и привлекательный вид. Декоративное оформление доборных элементов может сочетаться по цвету с основными конструктивными элементами или контрастировать с ними.
Как это делается? Производство сэндвич панелей
Технологии производства сэндвич-панелей в зависимости от степени автоматизации
Производство сэндвич-панелей можно условно разделить на два вида. Первый вид — изготовление сборных изделий, включающее несколько технологических операций:
- резка на требуемые размеры листов облицовки;
- профилирование листов облицовок;
- нанесение клеевого состава на лист облицовки;
- укладка утеплителя;
- установка второго листа облицовки;
- нагрев и выдержка панели под давлением в прессовом оборудовании;
- упаковка.
Существенным недостатком данного вида является высокая трудоемкость вследствие обилия ручных операций, необходимости в дополнительных транспортировочных манипуляциях и простоев. Монтаж сэндвич-панелей из отдельных элементов целесообразен в случаях, когда автоматизированное производство не позволяет добиться требуемой конфигурации изделий.
Второй вид производства сэндвич-панелей — потоковый (непрерывный). При данном способе производства все технологические операции — от разматывания рулона листовой стали до штабелирования и упаковки готовых изделий — осуществляются автоматически при помощи оборудования, объединенного в единую производственную линию. Как результат, существенное сокращение временных затрат обеспечивает и параллельное выполнение некоторых операций.
Следует понимать, что ручной труд высоко ценится лишь в случае производства штучных изделий высокой сложности. Минимизация ручного труда при производстве сэндвич-панелей не только исключает влияние человеческого фактора на качество готовой продукции, но и позволяет производителю устанавливать доступные цены.
Тип утеплителя
Существует немало разновидностей теплоизоляционных материалов, но монтаж сэндвич-панелей подразумевает лишь два способа их объединения с облицовкой:
- приклеиванием;
- напылением.
Соответственно, речь идет о твердом утеплителе, поступающем на производство в виде матов или рулонов, и о вспененной изоляции. Качество сэндвич-панелей с сердечником из минеральной ваты или другого твердого утеплителя определяется множеством факторов: от качества клеевого состава до наличия в технологическом процессе операции очистки поверхности облицовки для лучшей адгезии.
Получение вспененного утеплителя, в качестве которого чаще всего используется пенополиизоцианурат (выполненный на основе полиуретана), является весьма ответственным и трудоемким процессом, поскольку требует точного соблюдения дозировки химических компонентов, контроля температуры и т.
Еще одним часто встречаемым дефектом является отслоение утеплителя после деформаций панелей из-за разницы в температуре наружной и внутренней облицовки. С изделиями производителей, располагающих новейшим оборудованием и работающих исключительно с качественным сырьем, подобные казусы — большая редкость.
Качественная сэндвич-панель — это материал, строго соответствующий заявленным производителем параметрам. Компания Металл Профиль не только производит изделия, отвечающие самым высоким стандартам качества, но и обеспечивает свою продукцию официальной гарантией, если монтаж сэндвич-панелей был выполнен по рекомендованной технологии.
Технология производства сэндвич-панелей: инструкция по изготовлению
MesterulManole4025 0 1
На фото показан самый популярный стройматериал для каркасного строительства и его можно делать в условиях малого производственного предприятия
Планируете начать производство стройматериалов и не знаете, какое направление в этом бизнесе выбрать? Ознакомьтесь с тем, насколько проста технология изготовления сэндвич панелей.
Все что нужно знать о сэндвич панелях
Расположение слоев в толще стенового материала — посредине утеплитель, по краям жесткая оболочка
Сэндвич панели — это многослойная структура, состоящая из внешних листов жесткого материала и теплоизоляции между ними. Все комплектующие в конструкции склеиваются методом холодного или горячего прессования. В качестве утеплителя используется минеральная вата высокой плотности, пенополистирол или пенополиуретан.
Примеры использования в строительстве промышленных и коммерческих зданий
Готовые панели применяются в строительстве для возведения стен и кровель быстросборных каркасных домов. Стройматериалы, изготовленные в соответствии с технологическими нормами, отличает высокая прочность, низкая теплопроводность и малый вес.
Примеры использования в частном строительстве
Из-за особенностей теплоизоляционного слоя, панели и построенные из них конструкции отличаются нулевой воздухопроницаемостью.
Поэтому, еще при проектировании быстросборного дома нужно предусмотреть эффективную систему вентиляции.
Разновидности в соответствии с техническими параметрами
Иллюстрации | Разновидности по типу профиля |
Стеновые. Такие панели изготавливаются для закладки в металлический или деревянный каркас, выстроенный по периметру будущего здания. Стеновые изделия выпускаются со стандартными габаритами и их вес различается в зависимости от материалов, примененных при формировании внешнего слоя и в зависимости от типа теплоизоляции. В соответствии с фактурой внешнего слоя готовые плиты могут быть гладкими, профилированными и декоративными. | |
Кровельные. Такие панели облицовываются металлом и используются для устройства скатных кровель в быстросборных домах. Для того чтобы обеспечить эффективный сток атмосферных осадков, поверхность изделия имеет характерную рифленую поверхность. |
Иллюстрации | Разновидности по типу внешнего слоя |
С внешним слоем из листового металла. В качестве внешнего слоя используется тонколистовая оцинкованная сталь, реже алюминий. Для дополнительной защиты материала от коррозии поверхность плит окрашивается или покрывается специальным полимерным напылением. | |
С внешним слоем из древесных плит. Такие панели используются как стеновой материал. В качестве внешнего слоя применяется ориентированно-стружечная плита (ОСП), реже ламинированная фанера.
| |
С внешним слоем из ПВХ. В качестве внешней оболочки применяются гладкие пластиковые плиты.![]() |
Технология фабричного производства панелей из древесных плит
Технология фабричного производства панелей с покрытием из металла
Нарезка утеплителя. Плита минеральной ваты закладывается в резак, где раскраивается на полосы с квадратным сечением. Делается это затем, чтобы уложить вату в панели, так чтобы волокна располагались не продольно как в плите, а поперечно. Такое расположение ваты обеспечивает готовому изделию дополнительную прочность на сжатие. | |
Изготовление панелей. Производственный процесс автоматизирован. В машину подается тонколистовая сталь и утеплитель. Внутри оборудования формируется и склеивается изделие. После этого с помощью металлических вальцов поверхность металлического листа профилируется. На выходе из машины получается полностью готовое изделие. | |
Упаковка и складирование. Готовые изделия складываются в штабеля по 6-7 шт. и затягиваются в полиэтиленовую пленку. Затем, сложенные таким образом штабеля складируются. |
Подведем итоги
Теперь вы знаете, какова технология изготовления сэндвич панелей, а значит дело за малым — разрабатываем бизнес-план, закупаем оборудование и приступаем к работе!
Если вы хотите выразить благодарность, добавить уточнение или возражение, что-то спросить у автора — добавьте комментарий или скажите спасибо!
Последние ответы на форуме
Возможно вас заинтресуют
Изготовление сэндвич панелей своими руками – фото и видео инструкция
Потребность изготовления такого материала как панели сэндвич растет с каждым днем. Это объясняется тем, что панели пользуются огромным спросом. Данный материал довольно легкий, и для его транспортировки не нужен тяжелый грузовой транспорт. Благодаря таким панелям не нужно возводить фундамент с большой мощностью, а значит, можно будет сэкономить значительную часть средств. Наверняка многих интересует такой вопрос, как происходит процесс изготовления сэндвич панелей. Можно своими глазами увидеть, как происходит изготовления сэндвич панелей. Видео в нашей статье помогут вам в этом.
Линия производства
Способ кустарного производства: насколько это реально
Кто-то подумает, что изготовление сэндвич панелей своими руками – это несложный процесс. Им кажется, что необходимо всего-навсего взять две плиты, уложить между ними слой теплоизоляции, пленку пароизоляционного типа и скрепить все это. Однако толщина утеплителя и его тип играют очень важную роль. Данный этап возможен только после проведения специальных расчетов технологического характера. Также в учет берутся климатические условия того места, в котором будет возведено строение. Также необходимо отметить, что данный способ является очень неудобным. Также потребуется оборудование для изготовления сэндвич панелей. К тому же самодельные панели не будут отличаться высокой производительностью.
Схема
Требования к клею
Для изготовления панелей не подойдет любой клей, какого качества он бы не был. Клей должен сохранить свои свойства на протяжении как минимум нескольких десятилетий. Также клей должен отвечать и нормам безопасности и не смог нанести вред человеческому организму. Идеальным решением будет покупка клея от таких известных европейских производителей как Henkel и Kleiberit, как показано на фото. Клеи таких марок используют для изготовления панелей почти на всех ведущих заводах мира.
Специальное оборудование
Есть несколько причин, которые объясняют ответ на вопрос, почему необходимо специальное оборудование. Во-первых, технология изготовления сэндвич панелей требует чтобы процесс проходил с соблюдением точного интервала времени. Клей после распаковки может быть использован не позже чем через пять минут. Если клей затвердеет, то его не получится смыть ничем.
Вторая причина состоит в том, что клей может увеличиваться в объеме, и выделяется пена. В такой момент нужно чтобы что-то сжимало склеивающиеся элементы. Для этого, в заводских условиях используется специальный пресс. Такое оборудование может создать довольно большое усилие, которое достигает 18 тонн. В итоге можно сказать, что без специального оборудования не получится изготовить сэндвичи.
Преимущество
Специальное оборудование стоит не так дорого как кажется некоторым. Окупается такое оборудование после того как будут изготовлены примерно 500 единиц панелей. Такое оборудование будет работать при участии двух человек. Для изготовления сэндвича линии необходимо не более 10-12 минут. Можно использовать не только 5 минутный клей, но также и 10 минутный. Благодаря такому оборудованию можно производить сэндвичи из таких плит как Green Board GB3, как показано на фото.
Изготовление
Как выглядит производство слоеных панелей? ОСП плита покрывается посредством клея. Сверху ставиться лист из такого материала как пенополистирол, а после этого снова наносят клей. После этого ставиться еще одна плита ОСП и изделие оставляется до полного высыхания, как показано на видео.
Во время использования данной технологии необходимо следовать таким условиям как:
- наносить клей нужно не дольше чем 8-10 минут. Также необходимо следить за тем, чтобы он равномерным образом покрыл всю плоскость. Если клей будет находиться под воздействием воздуха длительный период времени, начнется процесс полимеризации, и тогда никакой растворитель не поможет его очистить;
- во время процесса полимеризации может появиться пена, также произойдет увеличение клея в объеме. Элементы, которые нужно склеить должны сжиматься посредством специального пресса. Усилие такого пресса может достигать 18 тонн;
- под прессом сэндвичи должны находиться не меньше чем 2-3 часа;
- чтобы панель высохла полностью, потребуется, чтобы прошло около 20-30 часов.
Время высыхания зависит от того, какой тип материала был использован;
- с помощью ножа потребуется отрезать ненужные части утеплителя, как показано на фото;
- раскрой сэндвичей должен осуществляться согласно чертежам на листы нужной формы и размеров;
- для осуществления процесса потребуется 2 человека, так как один может не успеть и полимерный состав застынет.
Подведем итоги
Изготовление и монтаж сэндвич панелей не требует много времени. Благодаря этому и другим преимуществам такие панели пользуются большой популярностью. Процесс изготовления сэндвичей зависит от многих факторов. Среди них можно перечислить выбор клея, утеплителя, использование специального оборудования и многие другие.
Сэндвич-панели ППУ: особенности и технология производства
Как производят сэндвич панели ППУ
В Западной Европе самыми распространенными из сэндвич панелей являются конструкции с пенополиуретаном или ППУ, они занимают на европейском рынке неоспоримо большую долю, порядка 90-95%. В России пока ситуация другая, до таких рекордных результатов нам еще далеко, но, как показывает статистика, процесс идет, и доля сэндвич панелей ППУ на отечественном рынке увеличивается с каждым годом. А чем популярнее становится материал, чем больше к нему интереса и у проектировщиков, и у строителей, и у населения, тем и вопросов возникает больше. О том, что материал из себя представляет, какими свойствами обладает, как производится, мы и поговорим в этой статье.
Строительный «бутерброд»
Даже тот, кто с сэндвич панелями ППУ дела никогда не имел, может легко представить себе, что это такое. Уже из названия становится понятно, что сэндвич панели представляют собой многослойную конструкцию: обычно по краям металлические листы, а в середине утеплитель. Впрочем, вместо металла могут быть другие материалы.
Утеплители тоже бывают разные, в основном вариантов три: минеральная вата, пенополистирол, ППУ (подробнее о каждом из вариантов мы поговорим чуть ниже).
Разновидности «сердцевины»
Конечно, у каждого материала есть свои достоинства и недостатки, просто у кого-то их больше, а у кого-то меньше. И не всегда нам известна вся правда про тот или иной утеплитель, а она может быть очень неприглядной. Впрочем, давайте по порядку.
Пенополистирол
Полистирол знают многие, чаще в «модификации» пенопласт. Основное преимущество материала – невысокая цена. А мы, надо признаться, любим, «чтобы подешевле», часто не задумываясь о том, что, приобретая дешевую продукцию, впоследствии можем столкнуться с непредвиденными проблемами.
Например, полистирол может оказаться недолговечным. А еще – привлекательным для грызунов. Но главное в другом – если материал подвергается воздействию пламени, он начинает выделять очень едкий дым, опасный для здоровья.
Минеральная вата
Минеральная вата считается экологичным и негорючим материалом. Почему считается? Да потому, что в жизни иногда бывает и по-другому. Известно много случаев, когда минеральная вата горела, причем интенсивно.
С экологичностью все вообще иногда бывает очень серьезно, так как в составе волокон могут оказаться канцерогенные составляющие (это зависит от выбора сырья и порядочности производителя), а в качестве связующего материала могут использовать фенолформальдегидную смолу, выделяющую вредный фенол, который для здоровья человека опасен.
Кроме того, минеральная вата гигроскопична, то есть сильно впитывает воду и водяные пары, после чего набухает и теряет форму, а вместе с ней и свои теплоизоляционные качества.
Пенополиуретан
Наконец, есть и еще один материал, пенополиуретан или, сокращенно, ППУ. Как уже упоминалось выше, на Западе самый популярный. Популярность ППУ объясняется именно наличием многих полезных характеристик.
1. Это и очень низкий уровень теплопроводности, то есть способности удерживать температуру в помещении, например, тепло в морозы. По показателям теплопроводности ППУ в полтора раза эффективнее, чем полистирол и в два, чем минеральная вата.
2. ППУ не страшна влага, а также плесень, бактерии, грибки и пр.
3. Не боится материал и перепадов температур. Хотя пенополиуретан и относится к категории горючих веществ, является умеренно горючим и самозатухающим, то есть, горение не поддерживает. PIR, одна из разновидностей ППУ, выдерживает 140°С благодаря особой структуре, при которой пламя не попадает во внутренние слои.
Как удается достигнуть таких свойств? Как производят сэндвич панели ППУ?
Производство сэндвич панелей ППУ
Сэндвич панели ППУ – продукт высокотехнологичный. При его производстве жестко соблюдаются все необходимые требования – только так можно получить продукт высокого качества.
Давайте проследим, как протекает процесс производства сэндвич панелей ППУ. Наблюдать будем на примере завода ПрофХолод, одного из лидеров отрасли.
Непрерывная линия по производству стеновых и кровельных сэндвич панелей из пенополиуретана, установленная на заводе, позволяет получать 2 500 000 квадратных метров сэндвич панелей в год.
В качестве поставщика оборудования выбран итальянский концерн Pu.Ma., один из мировых лидеров. Непрерывная автоматизированная линия Pu.Ma позволяет почти полностью исключить человеческий фактор при производстве сэндвич панелей ППУ.
Линия имеет длину свыше 180 метров, на ней можно производить панели толщиной от 40 до 200 мм, выпуская до 15 метров продукции в минуту.
Линия разделяется на несколько участков.
Все начинается с подготовки производства. Входящее сырье обязательно проходит лабораторный контроль. Также строго отслеживается соблюдение всех входящих параметров и технологических режимов. Только так можно выпускать продукцию неизменно высокого качества.
Металл поступает на завод в рулонах, а значит, прежде чем приступить к непосредственной работе по производству сэндвич панелей, рулоны нужно размотать. Для этого требуются специальные размотчики, то есть система непрерывной подачи металлического листа, обеспечивающая непрерывность и высокую скорость работы.
Чтобы металлические листы лучше соединились с полиуретановой пеной, то есть, для улучшения адгезии, необходимо снять с металлического листа электричество. Это делается при помощи коронарного разряда.
Следующий этап – участок профилирования. Он может состоять из 12 или 24 клетей (соответственно для стеновых и кровельных панелей). Металлическая часть панелей формируется с повышенной точностью, при этом минимизируются механические нагрузки на лакокрасочное покрытие.
Теперь следует нанести праймер, то есть тонкий слой клея, который близок по составу к основному материалу пены и при этом обладает повышенной адгезией к металлу.
Механический лист разогревают – это необходимо для обеспечения оптимального температурного режима, чтобы добиться идеальной адгезии праймерного слоя к металлу.
Настало время подачи пентана, который используется в качестве вспенивателя. Пентан соответствует европейским стандартам по экологии.
(Между прочим, эксклюзивную рецептуру пенополиуретана (PUR) и полиизоцианурата (PIR) для компании ПрофХолод разработала всемирно известная компания Dow Chemical).
Компоненты смешиваются, формируется пена. Непрерывный процесс производства обеспечивают две взаимозаменяемые заливочные головки высокого давления. Пену наносят равномерно по площади панели на праймерный слой. Равномерности удается достичь за счет дифференцированной скорости движения заливочной головки.
Далее конструкция попадает на гусеничный пресс. Пока она движется в 26-метровом прессе, происходят реакции химических компонентов, ограничение расширения пены. Так происходит формирование геометрии панели. Горизонтальные плоскости пресса представляют идеально ровные стальные пластины, которые обеспечивают фиксированную толщину панелей – в каждом случае разную, в зависимости от пожеланий заказчика. Профиль замка формируется системой боковых ограничителей.
Длина панели также бывает разной: кому-то нужно 3 метра, а кому-то и 15 метров (больше обычно не делают из-за возможных сложностей при транспортировке). Соответственно, конструкцию нужно порезать на необходимые отрезки. Участок резки, снабженный дисковой пилой и системой снятия заусенцев, оснащают вытяжкой для удаления стружки. Скорость пилы синхронизируют со скоростью движения линии, что позволяет даже на максимальной скорости нарезать панели длиной от 2 метров.
Между тем, пена еще не сформировалась на выходе из гусеничного пресса. Процесс продолжается в охладителе, который рассчитан на 28 позиций (длина панелей до 15 метров).
Практически готовые панели нужно правильно уложить. Для этого существует укладчик, точнее, кантователь-стопоукладчик, который переворачивает панели в автоматическом режиме, чтобы сформировать компактные стопки, которые потом подают на участок упаковки.
Благодаря упаковщику обеспечивается автоматическое формирование паллет, а также упаковка в стрейч пленку. Участок может работать от нескольких линий – завод ПрофХолод планирует в будущем запуск второй непрерывной линии.
Готовая продукция отправляется, соответственно, на склад готовой продукции. Причем там она не только ждет заказчика, но и… продолжает формироваться. Дело в том, что процесс формирования пены на выходе из линии не заканчивается, продолжаясь еще около суток, так что готовым сэндвич панелям необходимо отстояться на складе при контролируемом температурном режиме. Этот этап очень важен (впрочем, как и все остальные), так что его ни в коем случае нельзя игнорировать.
В конце – снова проверка, ОТК. Строжайший лабораторный контроль качества проходит не только сырье, но и готовая продукция компании ПрофХолод. Для этого на производстве и была организована испытательная лаборатория.
Именно так одно их ведущих предприятий отрасли Компания ПрофХолод (www.profpanel.ru) производит современный эффективный продукт на строительном рынке – сэндвич панели ППУ.
Источник: http://best—stroy.ru
Сэндвич-панели: разновидности и технология изготовления
История появления
В 1930 году американский архитектор Франк Ллойд Райт при строительстве недорогих жилых домов, впервые применил трехслойные стеновые панели, которые состояли из двух листов фанеры, между которыми вставили слой утеплителя.
Эта технология не осталась незамеченной и в дальнейшем получила свое распространение, особенно в Америке. Появились новые утеплители, такие как минеральная вата, пенополистирол и пенополиуретан.
Производство сэндвич панелейВ качестве наружных слоев стали применять оцинкованный стальной лист с полимерным покрытием, различные древесноволокнистые плиты и фанеру.
В настоящее время панели сэндвич стали массово применяться при строительстве промышленных зданий, торговых центров, складов и каркасных деревянных домов.
Классификация и конструкция панелей
Для более ясного представления о конструкции сэндвич-панелей можно привести следующие сравнения: панель толщиной 10 см, по теплоизоляции заменяет 230 мм деревянного бруса, 560 мм керамзитобетона, 900 мм пустотелого кирпича и 1150 мм полнотелого.
По своему назначению делятся на два вида:
Кровельные. Используются для монтажа совмещенных кровель промышленных зданий. Состоят из двух листов оцинкованного профнастила, между которыми запрессован полиуретановым клеем слой утеплителя в виде жестких минераловатных плит на базальтовой основе.
Профнастил имеет волнистый профиль высотой до 40 мм для увеличения несущей способности конструкции, полноценного водоотвода и специальный боковой замок для плотного соединения между панелями.
- Стеновые. Представляют собой самонесущую ограждающую конструкцию. Применяется для монтажа стен и перегородок при строительстве различных промышленных объектов и жилых домов малой этажности
В качестве утеплителя используется жесткая базальтовая минплита, пенополиуретан или пенополиизоцианурат. Внешние слои состоят из оцинкованного профнастила покрытого защитным декоративным полимерным покрытием. Боковые стороны панелей имеют специальные монтажные замки для плотного прилегания друг к другу.
Существуют варианты, где в качестве внешних слоев применяются плиты УСБ или фанера. Такие панели применяются для строительства каркасных деревянных домов малой этажности.
Технология производства
Качественные сэндвич-панели изготовляются на специальных высокопроизводительных и полностью автоматизированных технологических линиях. Стальной оцинкованный лист разматывается с рулона и обрезается на нужную длину, но не более 10 м, штампуется под определённый профиль, нагревается и грунтуется специальным клеем.
Далее на лист наносится слой двухкомпонентной массы, в которой начинается реакция полимеризации. Она увеличивается в объеме до определенного размера, который ограничивается вторым листом под специальным прессом.
Готовая заготовка выдерживается в специальной камере, поступает на стенд, где режется на нужные размеры и покрывается защитным слоем. Реакция полимеризации продолжается вплоть до отправки изделия потребителю.
Монтаж сэндвич панелейТолщина панелей составляет от 50 до 300 мм. Стеновые панели имеют общую ширину 1208 мм, рабочую 1190 мм. Кровельные 1070 мм и 1000 мм соответственно. Длина для всех панелей любая под заказ, но не более 10 метров.
Такое современное производство успешно функционирует на Нелидовском кровельном заводе http://nelidovokrz.ru/, который использует технологическую линию корпорации Hilleng. Оптимизация технологического процесса, позволило предприятию применять гибкую ценовую политику в зависимости от объема заказа, толщины и типа утеплителя. Продукция данного предприятия пользуется постоянным повышенным спросом.
Технология производства сэндвич-панелей
Возведение зданий из сэндвич-панелей не является новшеством современной строительной индустрии. Данная технология производства сэндвич-панелей практикуется уже не один десяток лет и за эти годы успела зарекомендовать себя как практичный и экономичный метод строительства не только промышленных и коммерческих сооружений, но и частных построек жилого типа. Огромная доля популярности сэндвич-панелей объясняется тем, что данные изделия производятся исключительно на новейших высокотехнологичных линиях под строжайшим контролем качества, что гарантирует готовым зданиям долговечность и отличные эксплуатационные характеристики.
Методы сборки сэндвич-панелей
Существует несколько методов сборки сэндвич-панелей и независимо от вида производственной линии, непосредственный монтаж осуществляется на саморезы для крепления сэндвич панелей. Самым распространённым из методов сборки считается ручной. Данный способ подразумевает сборку панелей на специальных полуавтоматических линиях, требующих обязательного присутствия человека для контроля всего процесса и стендового оборудования. Второй тип называется автоматическим и его управление также осуществляется рабочим.
Полуавтоматическое производство
Технология производства сэндвич-панелей в полуавтоматическом режиме начинается с профилирования металла. Далее листы покрываются специальным клеящим составом, на который кладётся утеплитель. В качестве него, в свою очередь, может выступать полистирол, минеральная вата либо полиуретан. После получения трёхслойной продукции, её отправляют под пресс, где происходит закрепление слоёв посредством воздействия высокой температуры и давления. Завершающим этапом производства является подрезка краёв и сушка.
Полностью автоматизированное производство
Принципы полностью автоматизированная сборка сэндвич-панелей исключает ручное человеческое вмешательство. Начинается производство с разматывания металлических рулонов, которые уже покрыты специальным полимерным составом защитного назначения. Затем на металл равномерно наносятся двухкомпонентный клей и утеплитель, после чего изделие проходит линии профилирования, нагрева и прессования.
Известен ещё один, не менее надёжный способ изготовления качественных сэндвич-панелей. Он основан на вспенивании наполнителя уже между двумя металлическими листами. Осуществляется это посредством специального шприца, который заполняет пространство между внешними слоями.
Технология производства сэндвич-панелей видео:
Линия по производству сэндвич-панелей — Непрерывная линия по производству сэндвич-панелей из ПУ, ПИР
Главная > Линия по производству сэндвич-панелей > Непрерывная линия по производству сэндвич-панелей из ПУ, ПИР
Непрерывная линия по производству сэндвич-панелей из ПУ, ПИР
Непрерывная линия по производству сэндвич-панелей из ПУ, ПИР , произведенный компанией KINDUS, которая первой в Южной Корее успешно локализовала все оборудование, производится на более высоком техническом уровне на всех этапах проектирования, производства, монтажа и ввода в эксплуатацию.
Наша линия по производству сэндвич-панелей представляет собой полностью автоматизированную систему оборудования для производства сэндвич-панелей различных форм с использованием жесткого пенополиуретана или полиизоцианурата в качестве основного материала, который в настоящее время известен как верхняя изоляция с низкой теплопроводностью, теплосбережением, защита от запотевания, высокая прочность и доступность на строительной площадке.
Линия сэндвич-панелей KINDUS из полиуретана и полиизоцианурата состоит из следующих компонентов:
Кроме того, KINDUS, мы можем изготовить полный комплект непрерывной линии по производству сэндвич-панелей из ПУ, ПИР по собственной технологии, включая систему вспенивания ПУ/ПИР, а также пентановый магазин для использования его в качестве выдувного агент.В связи с этим мы можем предоставить нашим клиентам 100% безупречную поддержку/услуги от А до Я.
Наша непрерывная линия по производству сэндвич-панелей из полиуретана, PIR уже признана своей ценностью благодаря экспорту в европейские страны с CE и другими крупными компаниями-производителями линий сэндвич-панелей в стране и за рубежом, KINDUS, мы будем продолжать попытки развития в соответствии с потребностями клиентов. для высококачественных сэндвич-панелей.
Общая спецификация линейки сэндвич-панели
Вид продуктов | внутренняя стена, наружная стена, гофрированная крыша, сайдинг, металл, черепичная крыша и более |
плотность основного материала | стандарт 35K ± 5 · 40k ± 5 |
скорость производства | в среднем 4 ~ 12 м / мин |
годовая мощность | Около 1 000 000 000 0032 |
Необходимое измерение | примерно W20M X L120M X H7M |
требуемая электроэнергия | Около 400 кВт |
Требуемое давление воздуха | Минимум 6~7 бар |

В связи с этим, KINDUS, мы можем предоставить специальные и дифференцированные услуги всем нашим клиентам, которые поставляют производственную линию вместе с различными технологиями и ноу-хау, которые очень полезны для обслуживания и эксплуатации оборудования на реальной рабочей площадке.
Видеоролик
Линия непрерывного производства сэндвич-панелей из ПУ, ПИР
Справочные фотографии линии сэндвич-панелей
Производство и стоимость современных монолитных сэндвич-панелей и будущих 90Введение
Спойлеры больших коммерческих самолетов часто выполняются в многослойной композитной конструкции. Корпус спойлера выполнен из карбон-эпоксидных слоев. Они покрывают сотовый заполнитель из арамида. В настоящее время исследования сосредоточены на монолитных высокоинтегрированных композитных конструкциях, которые заменяют такие многослойные конструкции, в основном из-за коммерческих аспектов. С структурной точки зрения это трудно оправдать. Многослойные конструкции обладают свойством высокой жесткости на изгиб и поэтому идеально подходят для пластинчатой конструкции спойлера самолета.Однако монолитные конструкции могут быть изготовлены с меньшими затратами, а их составные части могут быть легко интегрированы в единую деталь.
В литературе только несколько исследований посвящены монолитным спойлерам. Одним из них является статья Qi et al. [1], в котором представлен демонстратор трехсекционной кормовой коробки, упрощенный спойлер. В публикации Raju [2] дано несколько концепций монолитных спойлеров. Для одного из них наконец был изготовлен демонстратор. В бумагах Choi at al.[3,4] авторы представляют инженерный инструмент, основанный на знаниях, для оценки веса и стоимости композитных компонентов. В обоих исследованиях ранее упомянутый монолитный спойлер используется в качестве примера передовой практики. Также следует упомянуть текущую разработку бионического спойлера Airbus ([5], http://dw. com/p/1HFMJ и http://www.nwzonline.de/wirtschaft/flugzeugteilefuerairbusausdem3ddrucker_a_30,0,2923359360.html). ). Этот дизайн спойлера мотивирован листом гигантской кувшинки, чья плавающая кожа поддерживается с нижней стороны сеткой радиальных и периферийных ребер.Если расстояние между двумя радиальными ребрами становится слишком большим, вводят новую ветвь. Тем не менее, разработка сосредоточена на спекании металлов с помощью технологии быстрого прототипирования. В предыдущих публикациях [6,7] были установлены две разные концепции монолитной конструкции, которые удовлетворяют статическим требованиям спойлера самолета. При этом они имеют примерно равную массу по сравнению со спойлером-сэндвичем. Однако при разработке конструкций из армированного волокном пластика области проектирования, производственных процессов и материалов тесно связаны между собой.Изменение в одной области может оказать существенное влияние на другие области. Поэтому разработанные концепции переносятся на два монолитных варианта конструкции существующего сэндвич-спойлера.
Требования к монолитным альтернативам: одинаковая аэродинамическая поверхность и геометрия интерфейса, одинаковые критерии размеров, аналогичные общие характеристики жесткости и аналогичная масса по сравнению со спойлером типа «сэндвич». Вместо материалов, используемых для многослойного спойлера, применяются новые материалы, пригодные для самолетов, и их свойства.Дизайнерское пространство определяется объемом многослойного спойлера. В этой публикации оба варианта конструкции рассматриваются с точки зрения применяемых материалов, производственных процессов и связанных с этим производственных затрат. По сравнению со стандартным многослойным спойлером они дают целостное представление об альтернативных конструкциях будущих спойлеров самолетов.
Этот документ состоит из трех разделов. Во-первых, объясняется многослойная конструкция и ее монолитные альтернативы, дается обзор различных подходов к монолитной конструкции и выделяются критические критерии проектирования для каждого типа спойлера. Во-вторых, зарисовываются производственные процессы и применяемые материалы для отдельных конструкций. Детали конструкции сильно зависят от выбранных процессов и материалов. Поэтому некоторые из них представлены и в этом разделе. В-третьих, представлено сравнение производственных затрат между многослойным спойлером и монолитным спойлером. Изменение конструкции с многослойной на монолитную не приводит автоматически к снижению производственных затрат. Как правило, сложность смещается, например, со сборки соединения на оснастку.Следовательно, необходим компромисс между всеми аспектами возможных вариантов конструкции, чтобы в конечном итоге найти наиболее экономичное решение. Однако, прежде чем приводятся подробности, кратко излагаются функциональные возможности спойлеров самолетов, производство сэндвич-конструкций и производство монолитных конструкций.
Представленные варианты дизайна не претендуют на роль единственных решений; например, менее затратные производственные процессы могут быть применены также к многослойным спойлерам, если вместо современных сотовых заполнителей используются пенопластовые заполнители. Однако пенопластовые решения не рассматриваются, так как основные недостатки пенопластов аналогичны сотовым решениям. Пенопласты требуют дорогостоящей пятиосевой обработки с ЧПУ, и, насколько известно авторам, ни один другой производитель коммерческих самолетов, за исключением Airbus, в настоящее время не имеет квалифицированного пенопластового сердечника для конструкционных применений.
A. Функции спойлера самолета
Согласно Rossow et al. [8] и Niu [9], интерцепторы расположены на крыле за задним лонжероном кессона крыла (рис.1) и вообще отклоняются в верхнее положение. Спойлеры развернуты для нескольких задач. Отклоняясь во время полета, они действуют как воздушный тормоз и снижают скорость самолета (тормоз скорости). Сразу после приземления спойлеры выдвигаются до максимального отклонения (наземный спойлер). Опять сопротивление увеличивается; однако основной эффект заключается в том, что поверхности крыла, расположенные за спойлерами (например, закрылки), не могут обеспечивать подъемную силу. Поэтому контактные силы между колесами и взлетно-посадочной полосой увеличиваются, что повышает эффективность торможения.Когда интерцепторы применяются в качестве интерцептора крена для поддержки спиралевидности, они отклоняются только в ту сторону, где элерон смещен вверх. Одностороннее снижение подъемной силы заставляет самолет крениться. При этом из-за одностороннего повышенного лобового сопротивления самолет начинает рыскать в сторону отклонения спойлеров. В самолетах с электронным управлением полетом интерцепторы могут использоваться для уменьшения нагрузок, действующих на крыло. Это известно как смягчение порывистых нагрузок. Вертикальные порывы ветра увеличивают действующую воздушную нагрузку.За счет быстрых отклонений при порывах ветра можно уменьшить воздушную нагрузку, что позволяет облегчить конструкцию крыла. В недавно разработанных самолетах спойлеры слегка опускаются, когда закрылки выдвигаются в выдвинутое положение (например, Airbus A350 и Boeing 787). Причина в том, чтобы сохранить определенный зазор между задней кромкой спойлера и выпущенным закрылком, чтобы обеспечить контролируемый поток воздуха с нижней стороны крыла на верхнюю.
Здесь опущенные спойлеры функционируют как подъемное устройство.
Схема крыла самолета.
B. Производственные процессы
Многослойные конструкции, такие как спойлеры, обычно изготавливаются из предварительно пропитанного смолой углеродного волокна и арамидного сотового заполнителя. Из-за их сложности сборка отдельных слоев и сегментов сотового заполнителя выполняется в несколько этапов отверждения. Отверждение выполняется в автоклаве, что является дорогостоящим, поскольку в среде, заполненной азотом, применяются высокие давления и температуры.Монолитные конструкции позволяют использовать различные полуфабрикаты из волокна и производственные процессы, то есть формование с переносом смолы (RTM) и инфузию смолы (RI). В обоих случаях преформы из сухих углеродных волокон пропитываются эпоксидной смолой в процессе отверждения. Для RI вакуум используется для протягивания смолы через преформу. В случае RTM смола впрыскивается под высоким давлением. Процесс отверждения можно проводить в простой печи или в нагреваемых формах. Использование преформ имеет еще одно преимущество.Подкомпоненты могут быть объединены в одну сложную монолитную структуру, которая может быть изготовлена за один этап укладки и отверждения. Обзор различных производственных процессов и их плюсов и минусов можно найти в монографиях Шюрмана [10], Барберо [11] и Брейера [12].
II. Различные конструкции спойлера
Результаты, представленные в этой публикации, основаны на втором (если считать от фюзеляжа наружу) многослойном спойлере самолетов Airbus A330 и A340.Спойлеры этих самолетов разработаны и производятся компанией FACC Operations GmbH, Рид-им-Инкрайс, Австрия (FACC). Габаритные размеры спойлера в миллиметрах составляют 2400х800х150. Величина действующей нагрузки определяется силами, действующими на шток привода, который прикреплен к проушинам привода и используется для выдвижения или втягивания спойлера. Спойлер сконструирован таким образом, что в выдвинутом положении может выдерживать аэродинамические нагрузки, вызывающие усилие сжатия 180 кН в штоке привода. Растягивающая нагрузка привода возникает, когда спойлер прижимается к закрылку, чтобы предотвратить отрыв из-за аэродинамических нагрузок. В этом случае дополнительно рассматривается неисправность актуатора, поэтому спойлер должен выдерживать усилие натяжения 130 кН в актуаторе. Пространство проектирования, геометрия интерфейса, критерии определения размеров, поведение конструкции и масса конструкции составляют основу для альтернатив монолитной конструкции. Ниже представлены сэндвич-конструкция в качестве эталона и две производные монолитные конструкции спойлера.
A. Многослойный спойлер: эталонный проект
На рис. 2 показана схема многослойного спойлера. Спойлер соединен шарнирами и приводными подшипниками с конструкцией крыла. Корпус спойлера изготовлен из сотового заполнителя Nomex, который покрыт ламинатом верхней и нижней обшивки. По передней кромке сэндвич закрывается С-образным лонжероном. На задней кромке применен ламинированный клин. Все ламинаты производятся из предварительно пропитанных эпоксидной смолой углеродных слоев. В направлении распространения сэндвич-структура просто закрывается пандусом на внутреннем и внешнем краях. Особенности интерфейса реализованы с помощью одной скобы в центре передней кромки и двух меньших скобок на внешних углах кабины. Кронштейн центральной петли (CH), изготовленный из пластика, армированного углеродным волокном (CFRP), производится по технологии RTM. Затем, после нескольких технологических операций, центральная петля интегрируется в узел соединения сэндвич-структуры. CH состоит из четырех проушин, двух внешних, используемых для подшипников основного шарнира, и двух центральных проушин, к которым крепится привод.Краевые кронштейны представляют собой обработанные алюминиевые детали.
Схематическое изображение спойлера Airbus A330 и A340 № 2 левого.
Критерии проектирования конструкции можно условно разделить на прочность конструкции, устойчивость конструкции и принципы проектирования, безопасный срок службы, отказоустойчивость или устойчивость к повреждениям [8]. Общая жесткость конструкции в данном случае является результатом вышеуказанных требований, а не самим требованием. Достаточно большие смещения допустимы, если обеспечивается прочность конструкции.Прочность конструкции рассчитывается путем применения критериев максимального напряжения для всех случаев предельной нагрузки. Если используются однонаправленные (UD) слои углеродного волокна, критерии разрушения первого слоя Tsai-Wu применяются для разрушения матрицы в случаях предельных нагрузок. Устойчивость проверяется линейным анализом потери устойчивости. Здесь коэффициент запаса против потери устойчивости должен быть больше единицы для предельной нагрузки. В отношении философии дизайна применяется комбинация различных подходов. Для кронштейнов шарнира по внутреннему и внешнему краю применена отказоустойчивая конструкция (рис.2). Если один из этих кронштейнов выйдет из строя, конструкция все еще должна выдерживать предельную нагрузку. Перед разрушением кронштейна нагрузка передается непосредственно на конструкцию крыла.
После разрушения кронштейна нагрузка передается через центральный шарнир на конструкцию крыла. Композитные ламинаты разработаны с учетом устойчивости к повреждениям. Если плоские деформации не превышают определенного значения, например 0,0045 для продольного и поперечного растяжения, дается ресурс выносливости. Это справедливо даже при наличии едва заметных повреждений.
Наиболее важным критерием для многослойной конструкции является критерий максимальной деформации для устойчивости к повреждениям. За исключением особых случаев, можно считать, что прочность конструкции удовлетворяется, если выполняются критерии устойчивости к повреждениям в отношении максимально допустимой деформации. Сэндвич-конструкции, естественно, некритичны к глобальному выпучиванию. Местное выпучивание клеточных стенок не является значимым критерием.
B. Монолитный спойлер I: система интегрированных ребер жесткости
Идея первого варианта монолитной конструкции состоит в том, чтобы заменить сэндвич в качестве несущей конструкции воздушной несущей обшивкой и несущей конструкцией, основанной на системе ребер жесткости. .Однако применение сэндвич-конструкции идеально подходит для гибки нагруженных конструкций, таких как спойлеры. Таким образом, отсутствие нижней обшивки оказывает большое влияние на жесткость и прочность конструкции, которые необходимо уменьшить, чтобы создать конструкцию с примерно равной массой. Поэтому оптимизация топологии [13] использовалась для создания макета опорной конструкции, близкого к оптимальному. На основе заданного проектного пространства формулируется целевая функция вместе с ограничениями, которые отражают критерии проектирования спойлера самолетов A330 и A340, как описано в предыдущем разделе.Кроме того, применяется ограничение отрисовки [14] по нормали к верхней обшивке. Это подталкивает решатель к решениям, показывающим распределение ребер. Подробности опубликованы в [6].
Результаты оптимизации топологии интерпретируются в соответствии с конструкцией, представленной на рис. 3. Здесь спойлер состоит из простой верхней обшивки и довольно сложной основы, которые соединены вместе. Структура позвоночника разработана как система интегрированных омега-ребер жесткости, которые распределяются по площади кожи, чтобы поддерживать кожу, нагруженную давлением.Кронштейн CH интегрирован в каркасную конструкцию, которая производится в один слой. Опять же, рядом с внутренней и внешней кромкой спойлера установлены алюминиевые скобы. Они немного адаптированы для соответствия новым геометрическим особенностям корпуса спойлера.
Схема монолитного спойлера I на основе интегрированной системы ребер жесткости.
По сравнению с многослойной конструкцией решающими становятся два критерия дизайна. Критерии максимальной деформации по-прежнему доминируют в конструкции.Кроме того, критичен запас по выпучиванию, что разумно из-за неподдерживаемых участков обшивки между омега-ребрами жесткости.
C. Монолитный спойлер II: конструкция закрытого типа
Во второй концепции монолитной конструкции первоначальная идея многослойной конструкции заменена ребрами, ориентированными по хорде. Низкая плотность является одной из причин использования сэндвич-материала. Он используется для получения расстояния между двумя жесткими обшивками. Кроме того, верхняя и нижняя обшивки воспринимают растягивающие и сжимающие напряжения, а многослойная сердцевина воспринимает напряжения сдвига.Таким образом можно производить панели с высокой жесткостью на изгиб. Это преимущество используется для конструкции монолитного спойлера II. Таким образом, основные компоненты многослойного спойлера (рис. 2) приняты, и только многослойная сердцевина заменена простыми оболочками, как показано на рис. 4. Четыре проушины CH состоят из четырех таких оболочек, и, таким образом, реализовано подходящее введение нагрузки. Для передачи поперечных усилий конструкция закрыта С-образными профилями. Кроме того, эти С-образные профили предотвращают коробление свободных краев.На количество оболочек и расстояние между ними сильно влияют критерии потери устойчивости, местные смещения из-за несущей воздушные нагрузки верхней обшивки и толщина ламината.
Схема монолитного спойлера II на хордовых ребрах.
D. Сравнение веса
Вес монолитного спойлера I примерно на 8% выше, а вес монолитного спойлера II примерно на 14% меньше по сравнению с многослойным спойлером. Однако эти значения получены из разных уровней развития.Вес монолитного спойлера I обусловлен конструкцией, которая находится на высоком уровне разработки, т.е. были изготовлены демонстрационные детали, проведены испытания на статическую нагрузку и уже выполнен второй цикл оптимизации веса. Конструкция монолитного спойлера II все еще находится в стадии разработки, и возможно некоторое увеличение веса из-за проработки деталей.
III. Производственные процессы и детали конструкции
В этом разделе описываются производственные процессы отдельных конструкций.Детали конструкции сильно зависят от выбранных процессов и материалов. Поэтому некоторые из них представлены и в этом разделе.
A. Многослойный спойлер
Первым этапом изготовления многослойного спойлера, представленного на рис. 2, является изготовление кронштейна центральной петли. Из-за его сложной геометрии и жестких допусков это делается с использованием процесса RTM. Поэтому сухие переплетения углеродного волокна собираются в заготовку. Затем преформа помещается в пресс RTM, где все поверхности покрываются нагреваемыми формовочными блоками.Смола впрыскивается, и СН отверждается. Для изготовленной композитной детали требуется этап обработки с ЧПУ, необходим неразрушающий контроль (НК), а затем поверхности склеивания должны быть подготовлены для дальнейшей обработки. На втором этапе происходит укладка С-образного шпата. Поэтому центральный шарнир помещается в форму для укладки для совместного склеивания. Затем слои препрега наносятся для формирования ламината из С-спарта, который отверждается в автоклаве.
Сначала на последнем этапе укладки слоев, который показан на рис.5, слои препрега верхней обшивки помещают в форму для укладки. Они покрыты пленочным клеем. Затем накладывают С-образный лонжерон, подготовленный для склеивания, и обработанные сегменты сотового заполнителя. Сегменты соединяются вместе расширяющимся клеевым соединением во время отверждения. Сборка снова покрывается клейкой пленкой и, наконец, наносятся нижние слои препрега обшивки. Вся конструкция отверждается в автоклаве, после чего следует распаковка, обработка с ЧПУ, неразрушающий контроль, сборка деталей оборудования, покраска и этапы проверки.
Процесс сборки многослойного спойлера.
B. Монолитный спойлер I
Монолитный спойлер, представленный в гл. II.B изготавливается из двух отдельных частей: верхней обшивки и хребта, как показано на рис. 3. Геометрия верхней обшивки проста по границам и кривизне. Таким образом, процесс укладки можно легко автоматизировать. В данном случае ламинат изготовлен из углеродных лент UD, предварительно пропитанных эпоксидной смолой. Слои наносятся автоматически с помощью лентоукладочной машины.Затем предварительно подготовленный ламинат помещается в форму для укладки, изготавливается вакуумный пакет и, наконец, он отверждается в автоклаве.
Вся сложность конструкции встроенного ребра жесткости сосредоточена в хребте. Исходя из геометрии, для изготовления преформы применяются сухие углеродные переплетения с хорошей драпируемостью (например, пять атласных переплетений жгута), которые затем пропитываются смолой и отверждаются с помощью RI. Процесс укладки показан на рис. 6 и может быть разделен на четыре этапа. На первом этапе ламинирования сплошные слои и, при необходимости, усиливающие слои накладываются на полость пресс-формы для укладки в определенных ориентациях.Затем три инструментальных блока оборачивают углеродным материалом (шаг ламинирования 2). Эти субпреформы собираются на шаге 3 ламинирования и помещаются на уже существующий ламинат для создания СН. На этапе ламинирования 4 укладываются армирующие и полнотелые слои для завершения ламинирования.
Рис. 6Процесс сборки карбоновых слоев каркаса монолитного спойлера I.
Перед склеиванием верхней обшивки и каркаса обе детали проверяются неразрушающим контролем, после чего производится очистка и шлифовка склеиваемых поверхностей. Для склеивания пленки применяется клей. Клеевой шов отверждают в печи; давление создается с помощью вакуумного мешка. После этого конструкция дорабатывается. Выполняются механическая обработка, неразрушающий контроль вторичного склеивания, проверка размеров, сборка оборудования, покраска и проверка качества.
На рис. 7 показан полностью изготовленный спойлер с разных сторон. Центральная часть верхней обшивки удалена, чтобы можно было заглянуть внутрь полой конструкции.
Рис. 7Виды изготовленного монолитного спойлера I с частично снятой верхней обшивкой.
C. Монолитный спойлер II
Во втором предложении по монолитной конструкции корпус спойлера изготавливается в один этап укладки и отверждения в качестве основной детали, а компоненты С-образного лонжерона, которые представляют собой простые детали из углепластика, производятся для окончательного закрытия конструкции. , как показано на рис. 4. Корпус спойлера изготовлен с использованием RI. Поэтому сухие ткани из углеродного волокна (UD и тканые) собираются в заготовку. Этот процесс описан на рис. 8. Сначала на форму для укладки накладываются слои UD, чтобы сформировать верхнюю поверхность обшивки.На втором этапе все блоки инструментов оборачивают фанерным материалом. Здесь предпочтительны волокнистые переплетения с хорошей драпируемостью, например пятижгутовые атласные переплетения. Затем эти блоки укладываются на верхний слой обшивки. На четвертом этапе изготавливается клин. Он проходит вдоль задней кромки на концах блоков субпреформ и изготавливается путем укладки углеродного фанерного материала. Наконец, сборка покрыта слоями UD, которые образуют верхнюю обшивку.
Процесс сборки углеродных слоев для корпуса монолитного спойлера II.
Можно рассмотреть два варианта оформления ламината спойлера. Вариант I: Ламинат верхней обшивки и ламинат нижней обшивки изготавливаются только из полнотелых слоев. Это позволит использовать только стандартизированные неизвитые ткани, и, следовательно, будет дан быстрый процесс укладки. Все двойные слои, необходимые для усиления конструкции, встроены в ламинат вспомогательных блоков. Вариант I представлен на рис. 8. Вариант II: В ламинат нижней и верхней обшивки интегрировано как можно больше двойных слоев.Однако это ограничило бы использование негофрированной ткани. Напротив, укладка блоков инструментов остается простой, а уменьшенная толщина ламината снижает риск образования складок на радиусах углов во время заливки и отверждения смолы.
Профили из углеродного шпата довольно просты в производстве, и могут быть эффективно применены различные полуфабрикаты из волокна и производственные процессы. Однако в данной публикации рассматриваются те же материалы и заливка смолы, что и для корпуса спойлера.Для склеивания корпуса спойлера и С-образного лонжерона важно, чтобы внешняя сторона С-образных лонжеронов была формованной поверхностью. Причина в том, чтобы обеспечить склеиваемую поверхность с высокой геометрической точностью. Перед сборкой склеивания проводится неразрушающий контроль всех деталей, после чего следует подготовка (очистка и придание шероховатости) склеиваемых поверхностей. Для соединения поверхностей используется пленочный клей. Клеевой шов отверждают в печи; давление прикладывается с помощью надлежащей системы зажима. После этого выполняются механическая обработка, неразрушающий контроль вторичного склеивания, проверка размеров, сборка оборудования, покраска и проверка качества.
IV. Затраты на производство
Далее производственные затраты рассматриваются с точки зрения используемых материалов, применяемых процессов и необходимого оборудования, например форм для укладки, приспособлений для механической обработки и приспособлений для сборки. Индивидуальные характеристики сравниваются со спойлером-сэндвичем.
A. Метод анализа затрат
Существует несколько программных приложений для оценки стоимости составных приложений в авиационной промышленности. Одним из общих аспектов всех программных приложений является выявление основных факторов, влияющих на общие производственные затраты, на ранних этапах проектирования новых программ разработки. Известно, что затраты, выделяемые на ранних стадиях проектирования, составляют более 80% конечной стоимости изготовления нестандартных деталей. Однако большинство программных приложений являются проприетарными и действительны только при определенных ограничениях. Хьюбер и соавт. [15] дают обзор программного обеспечения и базовую классификацию параметрических, аналоговых и восходящих методов. Далее перечислены преимущества и ограничения.
Поскольку многие детали, влияющие на стоимость, неизвестны на этапе ранних этапов проектирования, FACC решила использовать информацию, основанную на знаниях, для расчета стоимости и разработала собственное программное обеспечение для оценки стоимости под названием FACC Advanced Cost Estimator for Research or Development Projects ( ОБЛИЦОВАЯ ДОРОГА).Это приложение следует параметрическому подходу; знания, полученные в ходе предыдущих программ разработки и производства, собираются и хранятся в базе данных. Пока вновь разработанная деталь имеет достаточно схожий характер с базой данных, можно выполнить точную оценку стоимости и принять обоснованное решение в отношении наилучшего варианта конструкции. Таким образом, оценка стоимости монолитных спойлеров I и II с помощью FACERoad хорошо подходит, поскольку доступны данные по нескольким спойлерам, разработанным и изготовленным FACC.Введение в программное обеспечение дано в Horejsi et al. [16].
B. Основные допущения и ограничения
Затраты на производство обычно делятся на две основные категории затрат: единовременные затраты (NRC) и периодические затраты (RC). NRC включает затраты на оснастку, оборудование и установку оборудования. Эти расходы возникают только один раз или, по крайней мере, не регулярно в случае технического обслуживания или замены оборудования. RC — это расходы на материалы, почасовые ставки, общие и административные расходы (G&A), транспортные расходы и таможенные расходы, которые могут быть непосредственно связаны с одной изготовленной деталью.
Для обоснования коммерческого эффекта монолитного спойлера необходимо сделать несколько допущений. Во-первых, предполагается, что все необходимое оборудование (например, автоклавы, прессы, фрезерные станки и машины для неразрушающего контроля) имеется на заводе-изготовителе. Инвестиции в новую технологию вызовут значительный NRC, что дает существующим производственным технологиям большое преимущество и не позволяет провести справедливое сравнение затрат. Таким образом, на NRC влияет только количество и сложность инструментального оборудования, необходимого для производства.В случае RC, G&A, расходы на перевозку и таможню не учитываются, т.к. они примерно одинаковы для всех вариантов.
Поскольку количество произведенных деталей, то есть ежегодное количество деталей, может отдавать предпочтение одному методу производства по сравнению с другим и, следовательно, влиять на NRC и RC, делаются дополнительные предположения. Они основаны на фактическом многослойном спойлере самолетов A330 и A340, где годовая производительность FACC, производственные требования и почасовые ставки известны и приведены в таблице 1.Чтобы представить сравнимые данные без ущерба для соглашений о неразглашении, почасовая ставка для RI и отверждения в печи была нормализована с почасовой ставкой для автоклавного отверждения и RTM. Также по причинам соглашений о неразглашении данные о стоимости для каждого варианта были нормализованы с использованием многослойного спойлера в качестве базового уровня.
C. Сравнение используемых материалов
Основным фактором стоимости производства многослойного спойлера является сотовый заполнитель, который, как правило, должен быть меньше по сравнению с углеродным материалом.Фактически, арамидный сотовый заполнитель является одной из самых дорогих частей сэндвич-спойлера. Это связано со сложной геометрией, для которой требуется пятиосевой процесс обработки с ЧПУ, а также с нестабильным поведением сотового заполнителя, обработка является узкоспециализированной задачей. Однако в случае монолитных спойлеров I и II требуется дополнительный углеродный материал для замены сотового заполнителя. Следовательно, переход от сэндвич-конструкции к монолитной конструкции с точки зрения затрат на материалы оправдан только в том случае, если количество углеродного материала, необходимого для монолитной конструкции, дешевле, чем стоимость углеродного материала и сотового заполнителя, применяемых в сэндвич-конструкции.
Полуфабрикаты из углеродных волокон, как правило, дороги и определяют стоимость; тем не менее, экономия средств возможна. Сырье для жидкого восстановительного восстановления можно приобрести примерно за 80–90% от сопоставимой цены препрега. Стадия пропитки не является дополнительным процессом в цепочке создания стоимости, а включена в последующий процесс у производителя композитных деталей, что способствует более низкой цене материала согласно монографии Брейера [12]. Кроме того, транспортировка и хранение менее затратны, потому что только эпоксидная смола должна подвергаться глубокой заморозке.
Детали крепления одинаковые или как минимум одинаковые для всех трех представленных конструкций. Конструкция кронштейна шарнира по краям должна быть обновлена в соответствии с новой геометрией составной детали. Тем не менее, количество алюминиевого сплава и усилия по обработке не сильно отличаются между сэндвич-спойлером и монолитным спойлером. Таким образом, части крепления не учитываются. Третий элемент, из которого состоит сэндвич-спойлер, состоит из пленочного клея и клея для сращивания. Первая часть применяется для крепления углеродных ламинатов к сотовому заполнителю, а вторая часть используется для соединения отдельных сегментов сотового заполнителя.В конструкции монолитных спойлеров I и II отсутствует клей для сращивания, а количество пленочного клея, используемого для соединения деталей из углепластика, невелико. Распределение относительной стоимости применяемых материалов, как обсуждалось, представлено на рис. 9 для всех трех конструкций.
Распределение стоимости применяемых материалов для монолитных спойлеров по сравнению со спойлером типа «сэндвич».
D. Сравнение применяемых процессов
На рис. 10 производственные процессы и их последовательность представлены в трех столбцах, по одному для каждой конструкции спойлера.Окончательные этапы изготовления, проверка размеров, сборка и покраска внизу рис. 10 считаются одинаковыми для всех конструкций спойлеров и поэтому перечислены только один раз. Очевидно, что все процессы для многослойного спойлера соединены последовательно, тогда как для монолитных конструкций подкомпоненты могут изготавливаться параллельно. Подсчет количества необходимых процессов показывает, что количество процессов, необходимых для изготовления монолитного спойлера I, равно 14, что на один больше, чем количество, необходимое для многослойного спойлера.Поэтому реальное сокращение технологических операций возможно только при использовании монолитного спойлера II, который можно изготовить за 12 технологических операций.
Последовательность основных процессов, необходимых для производства спойлеров различных конструкций.
Однако следует уделить внимание самим процессам. Таким образом, далее обсуждаются резка материала, укладка слоев, отверждение и неразрушающий контроль. Процессы, необходимые для окончательной доработки конструкции, не сильно различаются между вариантами конструкции, и поэтому механическая обработка с ЧПУ, проверка размеров, сборка и покраска далее не обсуждаются. На рис. 11 затраты на основные процессы для монолитного спойлера I и II сравниваются с затратами на сэндвич-спойлер. Во-первых, приведены нормированные значения для резки материалов. Поскольку в монолитных конструкциях сотовый заполнитель заменяется, для восстановления структурной целостности применяется дополнительный углеродный материал. Однако верхняя обшивка монолитного спойлера I изготавливается автоматически на лентоукладочном станке, поэтому резка является частью процесса укладки. В случае монолитного спойлера II применяются стандартизированные безгофрированные ткани (НКТ), что сокращает время на раскрой.Следовательно, время, затрачиваемое на резку углеродного материала, можно оценить как одинаковое для всех трех конструкций. Во-вторых, процессы укладки и соединения отдельных конструкций сравниваются на рис. 11. Многослойный спойлер изготовлен из предварительно пропитанного волокнистого материала, который требует нескольких этапов уплотнения. Кроме того, применяется множество различных материалов и деталей: лента, ткань, пленочный клей, клей для сращивания, сотовый заполнитель и дорогой предварительно изготовленный CH.
Напротив, остов монолитного спойлера I имеет очень сложную геометрию, но применяются сухие волокнистые полуфабрикаты, и поэтому требуется лишь несколько этапов преформования вместо многих этапов консолидации для многослойного спойлера.Верхняя обшивка изготавливается с помощью автоматической укладки ленты и отверждается в автоклаве, и, наконец, требуется этап сборки бонда для соединения позвоночника и верхней обшивки. Компоновка монолитного спойлера II остается простой; однако необходимо изготовить много заготовок, что в некоторой степени увеличивает трудозатраты. Наконец, считается, что усилие для укладки слоев и сборки монолитного спойлера I несколько выше, чем усилие для многослойного спойлера, а усилие для монолитного спойлера II явно ниже.
Сравнение затрат на производственные процессы для всех спойлеров и их финансовые последствия.
Для изготовления сэндвич-спойлера требуется два цикла автоклавирования и один цикл RTM. Известно, что автоклавные циклы дороги, а RTM-процесс экономичен только при больших объемах производства, как, например, в автомобильной промышленности. Производство монолитного спойлера I требует автоклавного цикла и для верхней обшивки, но здесь процесс укладки автоматизирован с помощью лентоукладчика, что несколько снижает затраты на автоклавный цикл.Процесс RI для остова рассматривается как наиболее экономичный способ изготовления конструкции такого типа, а для сборки соединения требуется только отверждение в печи. Таким образом, вместо одного RTM и двух автоклавных процессов требуется один автоклавный процесс, один процесс RI и один этап отверждения в печи. Суммарно затраты на циклы отверждения, необходимые для изготовления монолитного спойлера I, рассчитаны на 15 % меньше (рис. 11). Для монолитного спойлера II предоставляется возможность использовать один и тот же шаг RI для корпуса спойлера и секций С-образного лонжерона, что является явным преимуществом в затратах на процесс и количестве необходимых процессов.Поэтому возможно снижение цены примерно на 50%.
Другим важным фактором в производстве является стоимость неразрушающего контроля. Все три представленных варианта в определенной степени сложны для НК. В то время как для многослойного спойлера указаны только два отдельных этапа неразрушающего контроля, для монолитных спойлеров I и II необходимы три этапа. Однако на первом этапе неразрушающего контроля многослойного спойлера СН проверяется вручную с помощью ультразвукового эхо-импульса, а на втором этапе неразрушающего контроля применяются три различных метода.Сэндвич-панели контролируются автоматически с помощью ультразвукового сквозного пропускания, состыкованные зоны контролируются вручную с помощью ультразвукового импульсного эхо-сигнала, а клеевые соединения сегментов сотового заполнителя контролируются рентгеновским излучением. В случае монолитного спойлера I контроль верхней обшивки с помощью неразрушающего контроля автоматизирован, а позвоночника частично выполняется вручную с помощью ультразвукового импульсного эха и частично автоматизирован с применением ультразвукового сквозного пропускания. Проверка клеевого шва после процесса сборки снова автоматизирована с использованием ультразвуковой сквозной передачи.
Проверка методом неразрушающего контроля монолитного спойлера II до некоторой степени остается открытым вопросом. Осмотр верхней и нижней части кожи можно автоматизировать с помощью ультразвукового эхоимпульса. Однако из-за небольшого расстояния между верхней и нижней обшивками на задней кромке (рис. 4) осмотр ребер представляется затруднительным и требует решения. Для неразрушающего контроля профилей C-лонжерона возможен автоматизированный процесс. Наконец, считается, что неразрушающий контроль для монолитного спойлера I примерно на 10 % дешевле, а на момент публикации стоимость неразрушающего контроля для монолитного спойлера II оценивается на 20 % выше по сравнению с многослойными спойлерами, представленными на рис.11.
E. Сложность инструментального оборудования
Для отдельных процессов на рис. 10 требуется инструментальное оборудование. Что касается гл. IV.C (материалы) и гл. IV.D (процессы), разница в необходимом производственном оборудовании сосредоточена в процессах укладки и сборки. Здесь обычно используются пресс-формы для укладки. Для механообработки и сборки применяемое оборудование одинаковое или даже одинаковое для всех представленных конструкций. На рис.12. Приведенные значения основаны на уровне большинства, который подходит для производства деталей для разработки или небольшого количества деталей для серийного производства. Кроме того, дается распределение различных типов оснастки по конструкции. Цена оборудования, необходимого для сэндвич-спойлера, известна, поскольку эта деталь уже находится в серийном производстве. Также хороший опыт по ценообразованию оборудования накоплен для монолитного спойлера I, на котором был изготовлен первый демонстратор (рис. 7). В обоих случаях оценивается консервативная стоимость оснастки, необходимой для сборки монолитного спойлера II.
Распределение затрат на инструментальное оборудование, необходимое для изготовления сборки спойлеров.
В случае применения процесса RTM для CH многослойного спойлера укладка слоев выполняется на инструменте для изготовления преформ, а процесс RTM выполняется в отдельной форме для отверждения. Оба состоят из многих частей и их уровень сложности очень высок. Кроме того, необходимы сборочная форма средней сложности для изготовления С-образного лонжерона и сборочная форма низкой сложности для изготовления конечной составной части представленного многослойного спойлера, что дает в общей сложности четыре комплекта форм.
Для сравнения: монолитный спойлер I изготавливается с использованием двух пресс-форм. Один для изготовления остова и один для изготовления верхней обшивки, которая также применяется на этапе склеивания-сборки. В то время как инструмент для верхней обшивки имеет низкую сложность, инструмент для остова имеет высокий уровень сложности из-за геометрии, формирующей систему интегрированных ребер жесткости и СН, который интегрирован в ламинат остова. Форма для сборки корпуса монолитного спойлера II состоит из множества деталей и поэтому может быть причислена к инструменту повышенной сложности.Однако сам процесс укладки остается простым. Кроме того, для изготовления секций С-образного лонжерона необходимы пять полостей пресс-формы. Однако они просты и могут быть объединены в одну форму для укладки.
F. Сравнение общей стоимости
Наконец, интерес представляют общие затраты, поэтому необходима сумма затрат на материалы, процессы и оборудование для каждого варианта конструкции. Однако материальные и технологические затраты являются частью RC, тогда как оборудование является частью NRC, как описано в гл.IV.Б. Чтобы связать затраты на оборудование с затратами на производство одного спойлера, их делят на годовой объем производства 110 штук, указанный в таблице 1. Это соответствует предположению, что будет произведено всего 110 штук или что после производства 110 спойлеров необходима замена оборудования. После преобразования NRC можно построить диаграмму, представленную на рис. 13.
Рис. 13Распределение стоимости компонентов для монолитных спойлеров по сравнению со спойлером типа «сэндвич».
Согласно сделанным соображениям и предположениям обе монолитные конструкции спойлера могут быть изготовлены с меньшими затратами по сравнению со спойлером типа «сэндвич». Монолитный спойлер II кажется более удачным вариантом с привлекательным RC и приемлемым NRC. Риск для этой концепции дизайна заключается в процессе неразрушающего контроля, который окончательно не решен, как описано в разд. IV.D. Его основное преимущество заключается в более простой укладке, сокращении дорогостоящего времени мастерской и меньшем количестве применяемых менее дорогих процессов отверждения.В случае монолитного спойлера I низкие затраты на оборудование способствуют уровню 85% затрат по сравнению со спойлером типа «сэндвич». Следовательно, монолитный спойлер I больше влияет на годовой объем производства, чем монолитный спойлер II.
Сравнивая существующую сэндвич-конструкцию с монолитными вариантами I и II, можно добиться снижения производственных затрат на небольшое двузначное число процентов. Это удивительно, особенно в данных условиях, так как не учитывался инвестиционный фактор, огромный бонус для монолитных версий.
V. Выводы
Представлено изготовление двух разных конструктивных решений авиационных спойлеров, состоящих только из углепластика. Это означает, что сэндвич-дизайн, очень часто используемый для спойлеров, был полностью забыт. Обе концепции основаны на геометрии и конструктивных требованиях существующего многослойного спойлера, который находится в эксплуатации, и поэтому очень хорошо сопоставимы. Цель заключалась в сокращении производственных усилий и производственных затрат, с одной стороны, за счет интеграции отдельных деталей в единый компонент, а с другой — за счет использования альтернативных производственных процессов и систем материалов.
Затраты на производство многослойного спойлера и двух монолитных спойлеров были рассчитаны с использованием программного инструмента FACERoaD, разработанного в FACC. Предполагаемая стоимость производства многослойного спойлера совпадает с известными затратами на производство, демонстрируя лишь небольшое отклонение. Также в случае монолитного спойлера I оценка стоимости может быть подтверждена, поскольку его уровень зрелости высок: имеется рабочий проект и расчет, изготовлены демонстрационные образцы и проведены испытания на статическую нагрузку. В соответствии с этими результатами предполагается, что оценка для монолитного спойлера II также является достаточно точной, чтобы сделать предварительные выводы относительно экономической эффективности, даже если еще нет детального проекта и структурного анализа и пока не изготовлены демонстрационные образцы.
С помощью двух концепций, монолитных спойлеров I и II, было продемонстрировано, что существует потенциал для снижения затрат.
Система сэндвич-панелей из термопласта, подходящая для массового производства
На недавней выставке JEC в Париже компания SMTC представила Dynatech, систему термопластичных панелей, которая была разработана специально для использования в самолетах и высокоскоростных поездах, где требуется легкий вес в сочетании с высокими характеристиками, такими как устойчивость к повреждениям и превосходная огнестойкость, дымообразование и значения токсичности (FST).
Благодаря своей термопластичной природе как готовая к формованию сэндвич-система для массового производства, Dynatech может использоваться для изготовления различных деталей сложной формы в салоне самолетов и поездов, таких как сиденья, багаж, боковые стенки, тележки, кухни, столы и двери. Созданная на основе вспененной на месте панели PEI, она также обеспечивает лучшую тепловую и акустическую изоляцию по сравнению с традиционными сотовыми термореактивными панелями. Приобретя эту инновацию у изобретателя и патентообладателя FITS Technology, SMTC, которая ранее занималась производством сотовых систем на основе алюминия, теперь инвестирует в совершенно новую технологию массового рынка термопластов.
Автоматизированное производство Dynatech гарантирует более высокие стандарты качества и возможности контроля, что высоко ценится OEM-производителями. Благодаря запатентованному методу закрытого ящика, эта система позволяет создать сложную конструкцию закрытия кромки, которая фактически становится самой прочной частью системы. Таким образом, система может обеспечить снижение общей стоимости системы на 20-30%, помимо снижения веса на 20-40%.
Пилотное производство уже запущено, и первые заказчики получили прототипы.Полноценное коммерческое производство будет готово в 2016 году.
www.smtc.fr
www.fits-technology.com
Формованная термопластичная сэндвич-панель Dynatech со вставками (фото: SMTC)
аэрокосмическая · сэндвич-технологияЛазерное формование сэндвич-панелей с наполнителем из металлической пены | Дж.Произв. науч. англ.
За последнее десятилетие лазерное формование эффективно использовалось для гибки различных металлических пенопластов, открывая возможность применения этих уникальных материалов в новых инженерных приложениях. Цель исследования состояла в том, чтобы распространить лазерное формование на гибку сэндвич-панелей, состоящих из металлических лицевых листов, соединенных с сердцевиной из металлической пены. Сэндвич-панели из металлической пены сочетают в себе превосходные амортизирующие свойства и малый вес металлической пены с износостойкостью и прочностью металлических лицевых листов, что делает их востребованными во многих областях, таких как аэрокосмическая промышленность, автомобильная промышленность и солнечные электростанции. Чтобы лучше понять поведение сэндвич-панелей из металлической пены при изгибе, а также влияние лазерной формовки на свойства материала, были проанализированы основные механизмы, управляющие деформацией изгиба во время лазерной формовки. Было обнаружено, что хорошо зарекомендовавшие себя механизмы гибки, которые отдельно управляют лазерной формовкой твердого металла и металлической пены, все еще применимы к лазерной формовке сэндвич-панелей. Однако два механизма работают в тандеме, и отдельный механизм отвечает за деформацию твердого лицевого листа и сердцевины из пенопласта.На основании анализа механизма изгиба был сделан вывод о максимально достижимом угле изгиба и общей эффективности процесса лазерной формовки при различных условиях процесса. На протяжении всего анализа экспериментальные результаты дополнялись численным моделированием, полученным с использованием двух моделей конечных элементов, которые следовали различным геометрическим подходам.
уже давно известна своими превосходными свойствами поглощения ударов и шума, а также высоким соотношением прочности и веса [1,2]. Несмотря на свои желательные характеристики, металлическая пена сама по себе обычно не подходит для конструкционных применений, поскольку ее тонкая ячеистая структура может быть легко повреждена и часто затрудняет практическое внедрение. Поэтому во многих случаях желательно заключать металлическую пену в оболочку из твердого металла. Особый интерес представляют так называемые «сэндвич-панели», в которых пластины металлической пены «зажаты» между сплошными металлическими листами. Металлические листы («лицевые листы») не только защищают сердцевину из пенопласта от повреждений, но и значительно улучшают жесткость композита, сохраняя при этом высокое соотношение прочности и веса.
Потенциальные области применения сэндвич-панелей с наполнителем из металлической пены варьируются от различных компонентов автомобилей [3–5] до солнечных электростанций [6] и конструкций поездов/судов [7,8]. Пожалуй, наибольший потенциал для применения существует в аэрокосмической отрасли. В частности, сэндвич-панели могут использоваться в качестве кожухов турбин для фиксации лопастей в случае отказа и снижения шума при сохранении небольшого веса [9]. Сэндвич-панели из металлической пены могут также использоваться в «носовой части» самолетов для поглощения энергии удара при столкновении с птицами [10].В некоторых приложениях они также могут заменить сотовые конструкции, которые часто используются в современных самолетах. В отличие от сотовых структур, которые анизотропны и не могут быть легко изогнуты, металлический пенопласт изотропен и может быть изогнут в форме двойной кривизны [2]. Кроме того, плотность и геометрия, которые могут быть использованы для сотовых конструкций, ограничены, тогда как сэндвич-панели с сердцевиной из металлической пены могут быть изготовлены с различной плотностью, формой ячеек (с использованием пенопласта с открытыми/закрытыми ячейками) и размерами ячеек [11]. .
Проблема, связанная с использованием сэндвич-панелей с сердцевиной из пенометалла в промышленных целях, заключается в том, что они должны изготавливаться в соответствии со специфическими и часто сложными формами. Возможно изготовление сэндвич-панелей непосредственно требуемой формы с использованием процессов порошковой металлургии [11]. Этот процесс включает в себя создание материала-предшественника, состоящего из порошков прессованного металла и пенообразователя, размещение его между твердыми металлическими «лицевыми листами» и изгибание сборки до желаемой формы.После этого сборку перемещают в печь, в которой пенообразователь выделяет газ, превращающий прекурсор в пену. Повышенные температуры вызывают образование металлических связей между пеной и соседними лицевыми листами. Хотя это и возможно, недостатком этого процесса является то, что он требует форм как для первоначального формования, так и для последующего нагрева. Это ограничивает размер детали и делает процесс очень дорогим при небольших объемах производства. Кроме того, структура и плотность полученного пенопластового сердечника часто нерегулярны, поскольку он был изготовлен в неоднородной форме.
Альтернативный метод изготовления инженерных деталей состоит в том, чтобы начать с типовых форм, таких как плоские панели, а затем согнуть их в требуемые формы. Этот метод значительно дешевле и позволяет лучше контролировать свойства металлической пены. В то же время этот метод сложен, так как сэндвич-панели с наполнителем из пенометалла трудно сгибаются. Были предприняты попытки механического изгиба, например трехточечного изгиба [12,13] или штамповки [14], но они вызывали множество различных типов дефектов и отказов.Кроме того, были предприняты попытки трехточечного изгиба при повышенных температурах, однако не наблюдалось никаких улучшений, кроме незначительного отсрочивания возникновения отказов при механическом изгибе при комнатной температуре [15]. Хотя гидроформинг позволял формировать куполообразные детали, он сильно уплотнял сердцевину из металлической пены и, таким образом, снижал благоприятные свойства сэндвич-панели [16].
Жизнеспособной альтернативой вышеупомянутым процессам является лазерная формовка, так как она основана на термически индуцированной механической деформации и не требует физического контакта с обрабатываемым материалом. Этот процесс успешно использовался для гибки различных металлических пенопластов, таких как пенопласты с закрытыми порами [17,18], пенопласты с открытыми порами [19], а также пенопласты с защитным покрытием [20]. Тем не менее, не было предпринято никаких попыток применить лазерную формовку для сэндвич-панелей с сердцевиной из пенометалла. Распространение исследования лазерного формования на сэндвич-панели является сложной задачей, поскольку интерфейсы и взаимодействия между лицевыми листами и пенопластовой сердцевиной имеют решающее значение для материала в целом и должны учитываться.Существование интерфейса значительно усложняет теплообмен и механику, и, следовательно, для понимания этих явлений требуется более сложное численное моделирование. Эти вопросы, наряду с подробным обсуждением механизмов изгиба и применимого окна процесса, исследуются в данном исследовании.
Сэндвич-панели состоят из трех компонентов: сердцевины из пеноматериала (в данном исследовании – металлической пены) и двух сплошных металлических «лицевых листов», которые крепятся с обеих сторон сердцевины из пенопласта. В некоторых исследованиях сэндвич-панелями называют материалы, в которых сердцевина и облицовочные листы являются единой частью. Примерами являются металлические пены, которые образуют защитную оболочку во время процессов порошковой металлургии [11,20]. Однако чаще всего сэндвич-панели состоят из лицевых листов и пенопластовой сердцевины, которые представляют собой отдельные объекты и изначально разделены. Эти сэндвич-панели имеют более прочные лицевые листы, которые лучше защищают сердцевину из пенопласта и повышают жесткость сэндвич-панели. Кроме того, эти сэндвич-панели обеспечивают большую гибкость в отношении состава материалов, поскольку для лицевых панелей и комбинаций вспененного наполнителя могут использоваться различные типы материалов и сплавов.
Для производства этих сэндвич-панелей лицевые панели должны быть прикреплены к основе, что может быть достигнуто различными способами. В этом исследовании использовался типичный метод, в котором использовался прекурсорный блок, состоящий из прессованного порошка алюминия и пенообразователя. Прекурсор помещают между двумя лицевыми листами и нагревают до температуры плавления металлического порошка. Во время нагрева пенообразователь выделяет газ, который создает полости внутри предшественника и образует пену.Чтобы обеспечить однородную толщину сэндвич-панели и возможность образования металлических связей между пеной и лицевыми листами, во время процесса вспенивания ограничивают расширение в направлении толщины панели [11].

I= ∫−s0/2s0/2z2y(z)dz
(1) где s 0 – толщина листа [2].Как следствие, сэндвич-панель имеет гораздо более высокую жесткость на изгиб S , чем соответствующее твердое тело, как показано на рисунке, где l — половина длины балки, E — модуль Юнга, а δ — вертикальное отклонение балки. при изгибе [2]. Следовательно, для достижения того же изгибающего прогиба δ требуется больший изгибающий момент M , что, в свою очередь, увеличивает напряжения в сердцевине пены, делая ее еще более склонной к разрушению при сдвиге.Высокие напряжения также возникают в лицевых листах, что может привести к их разрушению или образованию складок [2,13].Рис. 1
Пример сэндвича из металлической пены (пористость 89 %, общая толщина 10 мм, толщина лицевого листа 1 мм), который имеет в 17,4 раза больший момент площади относительно оси y , чем твердое тело с одинаковой площади поперечного сечения (толщина 3,2 мм). Следовательно, сэндвичи из металлической пены имеют более высокую жесткость к деформации изгиба.Поперечные сечения были разделены на квадраты длиной 0,1 мм, моменты площади которых рассчитывались индивидуально и складывались с использованием теоремы о параллельных осях. Оси y- и z относятся к количеству квадратов на направление координат. Общее количество квадратов было одинаковым для твердого тела и сэндвича.
Рис. 1
Пример, показывающий сэндвич из металлической пены (пористость 89%, общая толщина 10 мм, толщина лицевых листов 1 мм), который имеет момент площади в 17,4 раза выше относительно оси y , чем твердое тело с такая же площадь поперечного сечения (толщина 3.2 мм). Следовательно, сэндвичи из металлической пены имеют более высокую жесткость к деформации изгиба. Поперечные сечения были разделены на квадраты длиной 0,1 мм, моменты площади которых рассчитывались индивидуально и складывались с использованием теоремы о параллельных осях. Оси y- и z относятся к количеству квадратов на направление координат. Общее количество квадратов было одинаковым для твердого тела и сэндвича.
, где E — модуль Юнга. Знак указывает на то, что деформация является сжимающей и растягивающей выше и ниже нейтральной оси соответственно. Поскольку радиус кривизны постоянен, величина разрыва напряжения зависит от разницы в модуле Юнга между лицевым листом и пеной, которая легко может достигать 100 раз.На границе раздела эта неоднородность напряжения ощущается как сдвиговое растяжение и может вызвать расслоение [12,13].
Рис. 2
Две различные геометрии были использованы для моделирования ядра пены: ( a ) твердотельная геометрия («эквивалентная модель»), посредством которой были заданы свойства пены, и ( b ) геометрия ячейки Кельвина («модель Кельвина»). »), где каждая полость была аппроксимирована ячейкой Кельвина. Не видны когезивные слои, которые были вставлены между лицевыми панелями и пенопластовым сердечником.
Рис. 2
Две различные геометрии были использованы для моделирования ядра пены: ( a ) сплошная геометрия («эквивалентная модель»), посредством которой были заданы свойства пены, и ( b ) геометрия ячейки Кельвина («Кельвин модель»), где каждая полость была аппроксимирована ячейкой Кельвина. Не видны когезивные слои, которые были вставлены между лицевыми панелями и пенопластовым сердечником.
Наконец, взаимодействие лицевого листа и пены может вызвать дополнительные нежелательные эффекты.Из-за высоких сжимающих напряжений, возникающих при механическом изгибе, лицевой лист может вклиниваться в сердцевину из пенопласта, сжимая пену до доли ее первоначальной толщины [2, 13]. Как следствие, пена теряет большую часть своей локальной сжимаемости и делает сэндвич непригодным для амортизирующих применений.
Лазерное формование твердого листового металла хорошо изучено; несколько механизмов объясняют поведение изгиба при различных условиях процесса [22].Первый механизм изгиба, механизм температурного градиента (TGM), определяет сценарий, в котором толщина листа образца относительно велика по сравнению с размером лазерного пятна. Крутые температурные градиенты возникают по толщине листа, а нагрев сильно локализован под лазерным источником. Как следствие, тепловое расширение нагретого материала ограничивается холодным окружающим материалом, и происходит пластическое сжатие. Пластическое сжатие распространяется по всему лазерному скану, укорачивая верхнюю часть листа по отношению к нижней и в конечном итоге изгибает материал в сторону лазера.Второй механизм, механизм коробления (BM), управляет сценарием, когда лазерное пятно намного больше, чем толщина листа, вызывая равномерный нагрев по толщине. Лист снова пытается расшириться, но ему мешает окружающий материал, и в конечном итоге он изгибается в сторону или в сторону источника лазера. Область изгиба распространяется вдоль лазерного сканирования, и лист в конечном итоге изгибается в направлении, противоположном направлению изгиба. Третий механизм, механизм осадки (UM), управляет тем же сценарием, что и BM, за исключением того, что секция геометрически защищена от коробления и вместо этого подвергается утолщению.
Для металлических пен было показано, что ни один из вышеупомянутых механизмов в точности не применим, и был предложен модифицированный температурно-градиентный механизм (MTGM) [18]. В MTGM, как и в TGM, по толщине развивается крутой температурный градиент, но укорочение при сжатии вблизи верхней поверхности происходит за счет дробления клеток, а не за счет пластических деформаций сжатия.
Для сэндвич-панелей с наполнителем из металлической пены анализ механизма изгиба становится более сложным.Во-первых, необходимо учитывать взаимодействие между лицевыми панелями и металлической пеной. Лицевые листы имеют тенденцию изгибаться с большей скоростью, чем сердцевина из металлической пены, и, таким образом, «сдерживаются», что может привести к возникновению напряжений на границе раздела. Более того, не существует механизма изгиба, который был бы справедлив как для твердого листового металла, так и для пенопласта, и, следовательно, нет механизма, который мог бы объяснить поведение изгиба всей сэндвич-панели. ТГМ и МТГМ, например, не могут регулировать изгиб всей сэндвич-панели, поскольку деформация пенопласта в основном не основана на пластическом сжатии, а лицевой лист соответственно не может подвергаться смятию.BM также не может быть действительным, так как толщина композита слишком велика, чтобы подвергнуться короблению. UM может только частично объяснить деформацию сэндвича для набора условий процесса, как будет показано ниже, но не объясняет, как сердцевина из пенопласта может изгибаться, не подвергаясь разрушению. Получается, что деформацию сэндвич-панелей можно объяснить сочетанием двух механизмов, которые взаимодействуют и порождают новое явление на границе между верхним облицовочным листом и пенопластовым заполнителем.
Для моделирования сэндвич-панелей можно использовать несколько методов. Простейший метод заключается в том, чтобы смоделировать сэндвич как блок, разделить его на три области и присвоить свойства лицевого листа и пены соответствующим областям [23]. Несмотря на исключительную простоту, недостаток этого метода состоит в том, что лицевая панель и сердцевина всегда жестко связаны, а теплообмен между ними предполагается идеальным (бесконечная проводимость).Однако, поскольку лицевой лист и сердцевина из пенопласта не полностью расплавляются во время производства, поверхность раздела содержит микропустоты, и адгезия несовершенна. Следовательно, следует ожидать конечной теплопроводности, которая может быть учтена только в моделях, в которых лицевые листы и сердцевина из пенопласта изначально отделены.
Для изначально отсоединенных моделей требуется метод соединения, для которого также существует несколько альтернатив.Упрощенный метод включает в себя соединение лицевого листа и пенопластовой сердцевины с использованием связей или контактных взаимодействий [13,16]. Оба метода могут моделировать контактные сопротивления, но не допускают расслоения. Когезионные поверхности обладают такими же тепловыми характеристиками, но также допускают расслаивание при превышении заданных параметров повреждения [24]. Тот же результат может быть достигнут путем введения тонкого слоя (например, 10 90 299 μ 90 300 м) на границе раздела, состоящего из когезивных элементов, с дополнительным преимуществом, заключающимся в том, что расслоение можно контролировать и визуализировать [25].Несмотря на то, что в текущем исследовании расслаивания не произошло, этот подход был использован для обоих интерфейсов в ожидании будущих исследований, в которых влияние расслоения станет важным.
[tntstt]=[Knn000Kss000Ktt][unusut]
(4), где индексы n , s , t относятся к нормальному, первому и второму направлениям сдвига соответственно. Жесткость когезионного слоя устанавливается очень высокой, чтобы не влиять на реакцию сэндвича [26].
Для моделирования неидеального теплообмена на границах раздела были заданы зависящие от температуры значения проводимости G(T) . Данные G(T) в настоящее время доступны только для металлов, находящихся в прямом контакте и подвергающихся давлению. Несколько ссылок предполагают экспоненциальное увеличение G с температурой T [27–29].Для сэндвич-панелей проводимость должна быть больше, чем при прямом контакте из-за наличия металлических связей; однако из-за отсутствия доступных справочных данных зависимость G(T) из Ref. [27].
Моделирование лазерной формовки было выполнено несвязанным образом с использованием тепловых результатов в качестве входных данных для механического анализа. Лицевые панели были смоделированы с использованием критерия текучести фон Мизеса, а свойства материалов, зависящие от температуры, были взяты из Ref.[30]. Моделирование было реализовано в программе abaqus для конечных элементов с использованием элементов DC3D20 и C3D20R для термического и механического анализа соответственно. Верхняя и нижняя лицевые панели моделировались тремя и двумя элементами по толщине соответственно.
F=[11+(α/3)2(σe2+α2σm2)]1/2−Y≤0
(5) где σ e — эквивалентное напряжение фон Мизеса, σ m — среднее напряжение, Y — предел текучести, α — отношение размеров поверхности текучести [31].
ε˙ijp=Y˙H∂F∂σij
(6) где ε˙ijp — скорость пластической деформации, а H — модуль упрочнения, определяемый какH=σeσ̂hσ+(1−σeσ̂)hp
(7), где h σ и h p — тангенсные модули при одноосном и гидростатическом сжатии соответственно, а σ̂ — эквивалентное напряжение, равное первому члену уравнения.(5). Предположения этой модели и источники материальных данных подробно обсуждаются в работах. [17] и [18]. Уточнение сетки x и y было таким же, как в Ref. [18], в направлении z сетка была более мелкой по направлению к границам раздела и более крупной по направлению к центру пены. Во втором методе («модель Кельвина») полость пены аппроксимировалась ячейкой Кельвина, показанной на рис. 2(б), и задавались свойства твердого AlSi10. Типы элементов и метод построения сетки были такими же, как в Ref.[18], за исключением того, что использовался размер полости 2 мм, что дает плотность 700 кг/м 3 .
В эквивалентной модели когезионный слой был сцеплен с элементами COh4D8, размер которых составлял половину размера соседних элементов из металлической пены. В модели Кельвина для когезионного слоя использовался тот же размер элемента, что и для соседних элементов из металлической пены. Термические и механические граничные условия были такими же, как и в предыдущих анализах [17,18], и коэффициент поглощения A = 0.6 [32].
В этом исследовании использовались сэндвич-панели производства Havel Metal Foam Gmbh, состоящие из лицевых листов AW 5005 и сердцевины из металлической пены AlSi10. Толщина сэндвичей составляла 10 мм, а средняя плотность металлической пены была измерена как 700 кг/м 3 . Способ изготовления обсуждался в гл. 2.1. Образцы сэндвичей были вырезаны до длины 100 мм и ширины 35 мм и установлены на теплоизолированном столике, как показано на рис.3. Лазер CO 2 с длиной волны 10,6 мкм м использовался для сканирования образцов в направлении x . Для улучшения естественно плохого поглощения излучения 10,6 мкм м в алюминии [33] образцы были покрыты черной графитовой краской. Образцы охлаждали до комнатной температуры после каждого лазерного сканирования, после чего измеряли отклонение с помощью циферблатного индикатора.
Рис.3
Экспериментальная установка. Образцы сканировали в направлении x , и между образцом и держателем помещали теплоизолирующий материал. Циферблатный индикатор был удален во время лазерного сканирования.
Рис. 3
Экспериментальная установка. Образцы сканировали в направлении x , и между образцом и держателем помещали теплоизолирующий материал. Циферблатный индикатор был удален во время лазерного сканирования.
При определении условий процесса применялись два разных подхода.В первом подходе вдохновение было получено из исследований лазерного формования многослойных композитов [34], в которых TGM индуцировался в верхнем слое, а остальные участки композита изгибались под действием возникающего изгибающего момента. Во втором подходе была предпринята попытка согнуть всю сэндвич-панель с помощью механизма лазерной формовки, подвергая всю секцию резкому градиенту температуры. Для обоих подходов изгиб был успешным, но механизмы изгиба оказались иными, чем предполагалось, что будет обсуждаться позже.Первый подход дал небольшой размер пятна D = 4 мм с высокой скоростью сканирования v = 30 мм/с, тогда как второй подход дал большой размер пятна D = 12 мм и более низкое сканирование. скорость v = 10 мм/с. Мощность поддерживали на уровне P = 800 Вт для поддержания постоянной энергии площади AE = P/Dv .
Поскольку оба условия процесса вызывают принципиально разные механизмы изгиба, большая часть этого исследования была посвящена сравнению двух условий.Однако окно процесса не ограничивается этими двумя условиями, и лазерное формование также может быть достигнуто с промежуточными размерами лазерного пятна между D = 4–12 мм и скоростями сканирования между v = 10–30 мм/с, как будет продемонстрировано в гл. 5.3.
Температура на нижней поверхности сэндвича измерялась с помощью ИК-камеры. ИК-камера была установлена под образцом, а к предметному столику был добавлен алюминиевый экран, чтобы не повредить ИК-камеру.Использовалась максимальная частота кадров 120 Гц, что обеспечивало достаточную детализацию для захвата температурно-временной истории. Пространственное разрешение ИК-камеры составляет примерно 0,1 мм на измеряемом расстоянии, а разрешение по температуре — 0,1 К.
Для изучения механизма изгиба образцы сэндвича и «изолированные» лицевые панели, которые были удалены из сэндвича, были подвергнуты лазерной формовке под углом около 15°.Затем типичное поперечное сечение сэндвич-образцов (рис. 4 (а) и 4 (б)) сравнивали с поперечным сечением изолированных лицевых листов (рис. 4 (в) и 4 (г)). Технологические условия, использованные для ( a ) и ( c ), представляли собой небольшой размер пятна D = 4 мм со скоростью сканирования v = 30 мм/с, а для ( b ) и ( d ) большой размер пятна D = 12 мм со скоростью сканирования v = 10 мм/с. Мощность и энергия площади были постоянными и составляли P = 800 Вт и AE = 6.67 Дж/мм 2 соответственно.
Рис. 4
Крестовые сечения сэндвич-панелей, отсканированные на ( A ) D = 4 мм и V = 30 мм / с (100 сканов) и ( B ) D = 12 мм и v = 10 мм/с (24 скана) и поперечное сечение отдельных лицевых листов, отсканированных при ( c ) D = 4 мм и v = 30 мм/с (7 сканирований), и ( = 30 мм/с (7 сканирований)29 ) D = 12 мм и v = 10 мм/с (6 сканирований).Энергии мощности и площади были P = 800 Вт и 6,67 Дж/мм 2 во всех случаях соответственно, а окончательный угол изгиба составил 15 град. Верхний лицевой лист согнулся через TGM в ( a ) и ( c ), BM в ( d ) и UM в ( b ).
Рис. 4
Крестовые сечения сэндвич-панелей, отсканированные на ( A ) D = 4 мм и V = 30 мм / с (100 сканов) и ( B ) D = 12 мм и v = 10 мм/с (24 сканирования), и поперечное сечение отдельных лицевых листов, отсканированных при ( c ) D = 4 мм и v = 30 мм/с (7 сканирований2), и ( d ) D = 12 мм и v = 10 мм/с (6 сканирований). Энергии мощности и площади были P = 800 Вт и 6,67 Дж/мм 2 во всех случаях соответственно, а окончательный угол изгиба составил 15 град. Верхний лицевой лист согнулся через TGM в ( a ) и ( c ), BM в ( d ) и UM в ( b ).
Изгиб изолированных лицевых панелей регулируется хорошо известными механизмами изгиба. При D = 4 мм на верхней поверхности произошло некоторое утолщение (рис.4(c)), что является установленным следствием изгиба с преобладанием TGM [35]. При D = 12 мм (рис. 4(г)) было незначительное изменение толщины лицевого листа, а размер пятна был существенно больше толщины лицевого листа, что указывает на то, что БМ является управляющим механизмом [22].
Для сравнения видно, что изгиб сэндвич-панелей управляется разными механизмами, поскольку поперечное сечение выглядит совершенно по-разному в обоих условиях процесса. При D = 12 мм (рис. 4(b)) верхний лицевой лист больше не изгибался из-за BM, потому что он был защищен от коробления прикрепленной металлической пеной. Вместо этого лицевая панель была утолщена, что свидетельствует о хорошо зарекомендовавшей себя единой системе обмена сообщениями. Распределения температуры по толщине, показанные на рис. 5 при прохождении лазера, подтверждают этот вывод. Как в изолированной конфигурации, так и в сэндвич-конфигурации почти не было температурного градиента на верхней лицевой панели, что говорило в пользу BM и UM для каждой конфигурации соответственно.
Рис. 5
Моделирование распределения температуры в поперечном сечении (плоскость yz) при прохождении лазера как во всем сэндвиче (эквивалентная модель сэндвича), так и в изолированной лицевой панели. При D = 4 мм и v = 30 мм/с в верхнем лицевом листе существует крутой температурный градиент, независимо от того, изолирован ли лицевой лист или имеет многослойную конфигурацию, что указывает на то, что TGM всегда является управляющим механизмом. При D = 12 мм и v = 10 мм/с практически отсутствует какой-либо градиент над верхней лицевой панелью в обоих сценариях, что указывает на то, что BM и UM преобладают в изолированной и многослойной конфигурациях соответственно.
Рис. 5
Моделирование распределения температуры в поперечном сечении (плоскость yz) при прохождении лазера как во всем сэндвиче (эквивалентная модель сэндвича), так и в изолированной лицевой панели. При D = 4 мм и v = 30 мм/с в верхнем лицевом листе существует крутой температурный градиент, независимо от того, изолирован ли лицевой лист или имеет многослойную конфигурацию, что указывает на то, что TGM всегда является управляющим механизмом.При D = 12 мм и v = 10 мм/с практически отсутствует какой-либо градиент над верхней лицевой панелью в обоих сценариях, что указывает на то, что BM и UM преобладают в изолированной и многослойной конфигурациях соответственно.
При D = 4 мм (рис. 4, а) верхний лицевой лист в сэндвич-конфигурации утолщается не только вверх, но и вниз, что нехарактерно для ТГМ и свидетельствует о том, что деформация определяется другим механизмом изгиба.Тем не менее, тепловые результаты на рис. 5 говорят об обратном, поскольку крутой температурный градиент развивался по всему верхнему лицевому листу независимо от того, был ли он изолирован или прикреплен к пенопластовой сердцевине.
Дополнительные доказательства можно получить из экспериментальных и численных результатов на рис. 6, показывающих изменение температуры на нижней поверхности сэндвич-панели на линии сканирования. При D = 12 мм через сэндвич передается значительное количество тепла.Это косвенно указывает на то, что верхний лицевой лист нагревался равномерно, что опять-таки предполагает, что UM управлял изгибом верхнего лицевого листа. С другой стороны, при D = 4 мм до нижней поверхности сэндвича доходит мало тепла, что позволяет предположить наличие перепада температуры в верхней лицевой панели, что приводит к ТГМ. Следует отметить, что в эксперименте лазерный экран располагался очень близко к нижней поверхности сэндвича для защиты ИК-камеры. Этот экран поглощал некоторое количество тепла и является причиной несоответствия между экспериментальной и численной пиковой температурой.Кроме того, на верхнем интерфейсе наблюдается значительное падение температуры, что можно объяснить конечной проводимостью интерфейса. Падение температуры было более значительным при D = 12 мм, чем при D = 4 мм из-за экспоненциальной температурной зависимости проводимости интерфейса Г(Т) .
Рис. 6
Экспериментальные и расчетные графики изменения температуры на нижней поверхности сэндвич-панели при D = 4 мм и D = 12 мм.При D = 12 мм наблюдается более значительное повышение температуры, что указывает на то, что через верхний лицевой лист передается больше тепла. При D = 4 мм до нижней поверхности доходит мало тепла, что подразумевает наличие температурного градиента в верхней лицевой панели.
Рис. 6
Экспериментальные и расчетные температурные графики на нижней поверхности сэндвич-панели при D = 4 мм и D = 12 мм. При D = 12 мм наблюдается более значительное повышение температуры, что указывает на то, что через верхний лицевой лист передается больше тепла.При D = 4 мм до нижней поверхности доходит мало тепла, что подразумевает наличие температурного градиента в верхней лицевой панели.
До сих пор анализ механизма изгиба был сосредоточен исключительно на верхнем лицевом листе, и были обнаружены доказательства того, что TGM и UM определяют изгиб лицевого листа при D = 4 мм и D = 12 мм соответственно. Теперь возникает вопрос, как изгибается остальная часть сэндвич-панели.Два доказательства показывают, что сердцевина из пеноматериала также активно изгибается благодаря механизму лазерной формовки, а не изгибается исключительно из-за изгибающего момента, создаваемого верхней лицевой панелью.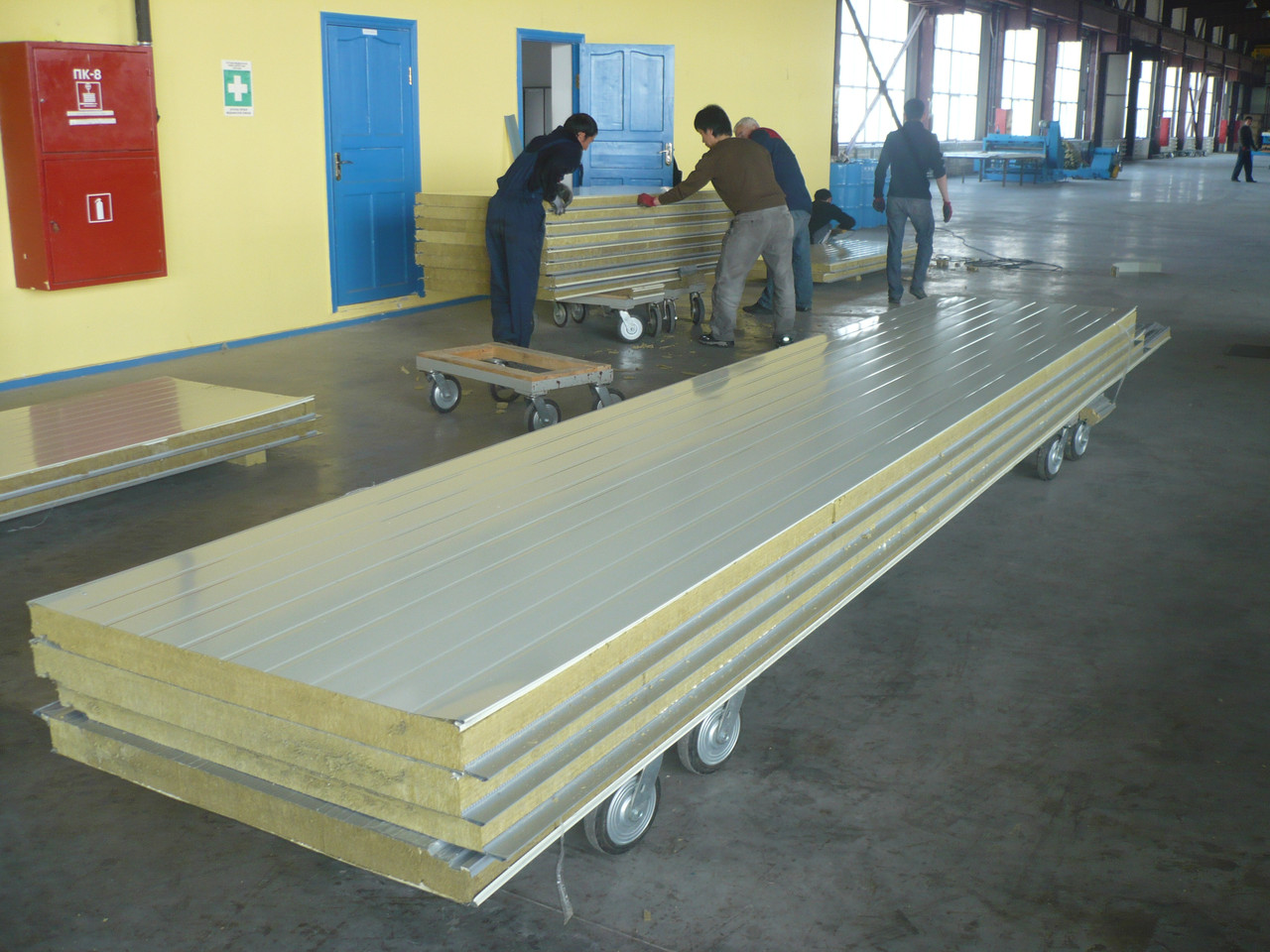
ρρ0=e−(ε11+ε22+ε33)=e−(εii)
(8), где ρ 0 — начальная плотность, ε ii — компоненты нормальной деформации [14]. Начальная плотность ( ρ = ρ 0 ) представлена 100%. Оба результата предполагают изгиб металлической пены в результате МТГМ [18]. Экспериментальные результаты подтверждают этот вывод, поскольку при малых углах изгиба можно наблюдать некоторое смятие клеток (рис.4(а) и 4(б)), и особенно при больших углах изгиба (см. п. 5.2).
Рис. 7
Распределение плотности после лазерного сканирования на ( A ) D = 4 мм и V = 30 мм / с, а ( B ) D = 12 мм и V = 10 мм/с. Начальная плотность 100%. В обоих условиях пенопластовый сердечник уплотнился, как постулируется MTGM. При D = 4 мм уплотнение имеет большую величину, но происходит более локально.При D = 12 мм уплотнение происходит на гораздо большей площади, что позволяет более эффективно деформировать при больших углах изгиба. Был использован масштабный коэффициент деформации 5. Половина образца показана из-за симметрии.
Рис. 70005
Рис. 70005
Распределение плотности после лазерного сканирования на ( A ) D = 4 мм и V = 30 мм / с, а ( B ) D = 12 мм и V = 10 мм/с. Начальная плотность 100%. В обоих условиях пенопластовый сердечник уплотнился, как постулируется MTGM. При D = 4 мм уплотнение имеет большую величину, но происходит более локально. При D = 12 мм уплотнение происходит на гораздо большей площади, что позволяет более эффективно деформировать при больших углах изгиба. Был использован масштабный коэффициент деформации 5. Половина образца показана из-за симметрии.
Таким образом, как верхний лицевой лист, так и сердцевина из пеноматериала активно способствуют деформации изгиба за счет различных механизмов изгиба.Последним компонентом сэндвича, требующим анализа, является нижний лицевой лист. Согласно рис. 5 градиент температуры по нижнему полотну отсутствует, а величина нагрева также мала. Таким образом, нижняя лицевая панель является единственным компонентом сэндвич-панели, не вносящим активного вклада в изгиб. Вместо этого он механически сгибается под действием изгибающего момента, создаваемого сердцевиной из вспененного материала и верхним лицевым листом.
Обсудив механизмы изгиба, становится ясно, почему сэндвич-панели, формованные лазером, не подвержены отказам, упомянутым в гл.2.1. Разрушения сердечника при сдвиге не происходят, потому что деформация пены через MTGM в основном носит сжимающий характер [18]. Точно так же не происходит коробления верхнего лицевого листа, поскольку верхний лицевой лист подвергается укорочению при сжатии посредством TGM. Сморщивание лицевого листа не происходит либо из-за того, что лицевой лист слишком толстый, либо из-за размягчения под воздействием тепла предотвращается разрушение нижнего лицевого листа. В зависимости от метода соединения может произойти отслоение лицевой панели. В этом исследовании был использован очень прочный метод соединения, который не привел к расслаиванию.
Еще одной темой, требующей обсуждения, является утолщение на нижней поверхности верхнего облицовочного листа (рис. 4(а)). За такое поведение могут быть ответственны два механизма. Сначала металлическая пена уплотняется, как показано на рис. 7(a) и 7(b), и связанное с этим уменьшение объема оставляет пустоту в пене, которую необходимо заполнить. Поскольку сцепление между верхним лицевым листом и металлической пеной остается неповрежденным, лицевой лист должен заполнить эту пустоту, что легко может быть выполнено, поскольку он подвержен высоким сжимающим напряжениям, а также размягчается из-за лазерного нагрева.Во-вторых, верхний лицевой лист расширяется вниз прямо при прохождении лазера. На рисунке 8 показано распределение деформации ε 33 в направлении z ( a ) непосредственно перед проходом лазера, ( b ) во время прохождения лазера и ( c ) в конце лазера. сканирование. Непосредственно перед проходом лазера верхний лицевой лист начинает равномерно расширяться. По мере того, как лазер проходит, лицевой лист быстро расширяется как вверх, так и вниз, вызывая деформацию сжатия металлической пены под ним.
Тем временем пена подвергается некоторой собственной деформации сжатия через MTGM, тем самым «тяня» лицевой лист вниз и вызывая растягивающую деформацию лицевого листа. Это условие сохраняется до конца лазерного сканирования, как показано на рис. 8(c).
Рис. 8
Вертикальное распределение пластического деформации на Z -Дерекция ( ε 33 ) на линии сканирования на D = 4 мм и V = 30 мм / с ( A ) до прохождения лазера, ( b ) при прохождении лазера и ( c ) после лазерного сканирования.Как только лазер проходит, верхний лицевой лист (три верхних слоя элементов) расширяется вверх и вниз рядом с линией сканирования, сжимая пену под ним. Пена, в свою очередь, уплотняется из-за MTGM и «тянет» лицевой лист вниз, вызывая растягивающие напряжения в верхнем лицевом листе. Был использован масштабный коэффициент деформации 5. Половина образца показана из-за симметрии.
Рис. 80005
Рис. 8
Вертикальное распределение штамма на деформации в Z -Дерекция ( ε 33 ) на линии сканирования на D = 4 мм и V = 30 мм / с ( A ) непосредственно перед прохождением лазера, ( b ) при прохождении лазера и ( c ) после лазерного сканирования.Как только лазер проходит, верхний лицевой лист (три верхних слоя элементов) расширяется вверх и вниз рядом с линией сканирования, сжимая пену под ним. Пена, в свою очередь, уплотняется из-за MTGM и «тянет» лицевой лист вниз, вызывая растягивающие напряжения в верхнем лицевом листе. Был использован масштабный коэффициент деформации 5. Половина образца показана из-за симметрии.
В сек. 5.1 было показано, что маленькие ( D = 4 мм) и большие ( D = 12 мм) размеры лазерного пятна индуцируют различные механизмы изгиба верхней лицевой панели. Гибочные механизмы, в свою очередь, существенно влияют как на эффективность изгиба, так и на предел изгиба.
На рис. 9 показано, что углы изгиба, достигнутые при D = 12 мм, более чем в два раза превышали углы изгиба, достигнутые при D = 4 мм в течение 8 лазерных сканирований, даже несмотря на то, что энергия площади была постоянной в обоих случаях (AE = 6,67 Дж/мм 2 ). Эти результаты ясно показывают, что изгиб значительно эффективнее при больших размерах лазерного пятна.
Рис. 9
Экспериментальные углы изгиба по восьми сканам при D = 4 мм при v = 30 мм/с и D = 12 мм/с при v = мм. Мощность и энергия площади постоянны и равны P = 800 Вт и AE = 6,67 Дж/мм 2 соответственно. Углы изгиба усреднены по пяти образцам, показаны стандартные ошибки. При D = 12 мм гибка более эффективна, чем при D = 4 мм.
Рис. 9
Экспериментальные углы изгиба по восьми сканам при D = 4 мм с v = 30 мм/с и D = 12 мм с v Мощность и энергия площади постоянны и равны P = 800 Вт и AE = 6,67 Дж/мм 2 соответственно. Углы изгиба усреднены по пяти образцам, показаны стандартные ошибки. При D = 12 мм гибка более эффективна, чем при D = 4 мм.
Чтобы объяснить тенденции, наблюдаемые на рис.9, распределения пластической деформации сжатия в направлении y (ε22p) были проанализированы по поперечному сечению сэндвич-панели. При D = 4 мм (рис. 10(а)) в центре верхней лицевой панели возникли большие деформации сжатия из-за интенсивного нагрева и больших сил теплового расширения, характерных для ТГМ. Остальные сегменты лицевого листа вносили гораздо меньший вклад в деформацию сжатия, а область пластической деформации в основном локализовалась вблизи линии лазерного сканирования. При D = 12 мм (рис. 10(б)) пластически деформированная область простиралась дальше от линии лазерного сканирования, а деформации сжатия были более равномерно распределены по всему верхнему облицовочному листу. Следовательно, изгиб был более эффективным при D = 12 мм, потому что больший сегмент верхнего лицевого листа способствовал укорочению при сжатии.
Рис. 10
Пластичное распределение штамма после лазерного сканирования на ( A ) D = 4 мм с V = 30 мм / с и ( B ) D = 12 мм с V = 10 мм/с.При D = 4 мм значительное укорочение при сжатии произошло только в небольшом сегменте верхнего лицевого листа (три верхних слоя элементов), в отличие от D = 12 мм, где весь верхний лицевой лист способствовал укорочению при сжатии и деформациям сжатия. дальше от линии лазерного сканирования. Был использован масштабный коэффициент деформации 5. Половина образца показана из-за симметрии.
Рис. 10
Пластическое распределение штамма после лазерного сканирования на ( A ) D = 4 мм с V = 30 мм / с и ( B ) D = 12 мм с V = 10 мм/с.При D = 4 мм значительное укорочение при сжатии произошло только в небольшом сегменте верхнего лицевого листа (три верхних слоя элементов), в отличие от D = 12 мм, где весь верхний лицевой лист способствовал укорочению при сжатии и деформациям сжатия. дальше от линии лазерного сканирования. Был использован масштабный коэффициент деформации 5. Половина образца показана из-за симметрии.
Кроме того, изгиб был более эффективным при D = 12 мм, поскольку сердцевина из пеноматериала более эффективно изгибалась с помощью MTGM.В отличие от D = 4 мм (рис. 10(а)), где пена подвергалась пластическому сжатию только рядом с линией сканирования, область пластического сжатия была намного больше при D = 12 мм (рис. 10(б). )). Такой же вывод можно сделать из графиков уплотнения на рис. 7(а) и 7(б), а также результаты экспериментов при больших углах изгиба (рис. 11).
Рис. 11
Поперечное сечение сэндвич-образца, изогнутого под углом 65° при D = 12 мм и v = 10 мм/с.Верхний лицевой лист значительно утолщается, и на большой площади происходит уплотнение пены. Тем не менее, прочность верхнего облицовочного листа сохраняется, если не увеличивается. Произошло гораздо меньшее уплотнение, чем при механическом изгибе.
Рис. 11
Поперечное сечение сэндвич-образца, изогнутого под углом 65° при D = 12 мм и v = 10 мм/с. Верхний лицевой лист значительно утолщается, и на большой площади происходит уплотнение пены. Тем не менее, прочность верхнего облицовочного листа сохраняется, если не увеличивается.Произошло гораздо меньшее уплотнение, чем при механическом изгибе.
Наконец, гибка была более эффективной при D = 12 мм, потому что нижний лицевой лист достиг более высоких температур во время лазерного сканирования, как показано на рис. 6, и, следовательно, подвергся большему размягчению под воздействием тепла, чем при D = 4 мм.
Подобно эффективности изгиба, максимально достижимый угол изгиба очень чувствителен к размеру лазерного пятна.При D = 4 мм максимальный угол изгиба составляет всего ∼15 градусов, как показано на рис. 4(а). Большие углы изгиба могут быть достигнуты исключительно за счет выполнения нескольких параллельных лазерных сканирований. На рис. 12(а), например, выполнялось два сканирования на строку сканирования, и каждая строка сканирования была смещена на 1 мм. С другой стороны, при D = 12 мм углы изгиба до 65 градусов и выше могут быть достигнуты по одной линии сканирования, как показано на рис. 12(b).
Рис.12
При D = 4 мм заметные углы изгиба могут быть получены только при выполнении параллельных сканирований, как показано на ( a ), где два сканирования выполнялись на линию сканирования со смещением на 1 мм. При D = 12 мм большие углы изгиба до 65 градусов и выше могут быть получены по одной строке сканирования, как показано на ( b ).
Рис. 12
При D = 4 мм заметные углы изгиба могут быть получены только при выполнении параллельных сканирований, как показано на ( a ), где два сканирования выполнялись на линию сканирования со смещением на 1 мм.При D = 12 мм большие углы изгиба до 65 градусов и выше могут быть получены по одной строке сканирования, как показано на ( b ).
Одной из причин различных ограничивающих характеристик является механизм изгиба, который определяет деформацию верхнего облицовочного листа. При D = 4 мм верхний лицевой лист прогибается через ТГМ, и на небольшом участке вокруг линии лазерного сканирования происходит значительное утолщение (рис.4(а)). Это утолщение вызывает значительное падение приращения угла изгиба Δα, так как Δα обратно пропорциональна квадрату толщины листа для условий ТГМ [22]. В конце концов лицевой лист становится слишком жестким, и Δα→0 для всего сэндвича. При D = 12 мм также происходит значительное утолщение, особенно при больших углах изгиба, как показано на Рис. размер лазерного пятна, а тепловое условие для единой системы обмена сообщениями по-прежнему выполняется.
Другой причиной различных ограничивающих характеристик является эффективность уплотнения пены с помощью MTGM. Как упоминалось в гл. 5.1 уплотнение происходит очень локально при D = 4 мм, в отличие от D = 12 мм, где уплотняется большой сегмент пены, как видно на рис. 11. Следовательно, пена может неограниченно уплотняться при D = 12 мм, тогда как он может локально приближаться к затвердеванию при D = 4 мм, снижая эффективность изгиба [18].
Изучив поведение сэндвич-панелей при больших углах изгиба, можно изучить влияние лазерной формовки на характеристики сэндвича. Первая проблема, которую необходимо рассмотреть, — это утолщение лицевой панели. С одной стороны, утолщенный лицевой лист увеличивает прочность и жесткость сэндвич-панели. И наоборот, утолщенный сегмент подвергается многочисленным циклам быстрого нагрева и охлаждения, что может привести к охрупчиванию материала [36].Однако, поскольку утолщение лицевого листа происходит в большем масштабе, а алюминий менее восприимчив к пагубным эффектам охрупчивания, ожидается, что характеристики верхнего лицевого листа сохранятся, если не улучшатся. Вторая проблема – уплотнение пены. При D = 4 мм уплотнение напоминает уплотнение, наблюдаемое при лазерном формовании свободностоящей металлической пены [18]. С увеличением числа сканирований уплотнение становится более локальным и, таким образом, минимально влияет на разрушаемость пенопласта.При D = 12 мм уплотнение широко распространено за счет МТГМ, а также крупномасштабного утолщения верхнего облицовочного листа. Тем не менее, уплотнение намного меньше, чем при механическом изгибе, когда верхний лицевой лист глубоко проникает в сердцевину из пенопласта и может уменьшить его толщину до 75% [12,13].
Окно процесса не ограничивается двумя условиями процесса, которые сравнивались до сих пор, но охватывает весь спектр между ними.Как показано на рис. 13, любой размер лазерного пятна от D = 4 мм до D = 12 мм дает успешный результат (при AE = const.). При каждом размере пятна кривая изгиба слегка выравнивалась с увеличением числа лазерных сканирований. При D = 4 мм и D = 6 мм кривая изгиба выравнивалась быстрее, поскольку ТГМ, более чувствительная к утолщению облицовочного листа (см. п. 5.2), доминировала в верхнем облицовочном листе. Кроме того, краска стиралась быстрее из-за более высоких температур верхнего лицевого листа.При D = 10 мм и D = 12 мм кривые изгиба выровнялись в наименьшей степени, так как в верхнем облицовочном листе преобладал БМ, менее чувствительный к утолщению лицевого листа. Кроме того, температура в верхней лицевой панели была самой низкой и вызывала наименьшее количество испарений краски. Наконец, D = 8 мм находится где-то посередине и выравнивается только при большом количестве лазерных сканирований.
Рис.13
Экспериментальные углы изгиба по результатам восьми сканирований при размерах пятна от D = 4 мм до D = 12 мм. Мощность и энергия площади постоянны и равны P = 800 Вт и AE = 6,67 Дж/мм 2 соответственно. Углы изгиба усреднены по пяти образцам, показаны стандартные ошибки. При малых размерах пятна кривые изгиба выравниваются быстрее из-за повышенного испарения краски и большей чувствительности к утолщению лицевого листа.
Рис.13
Экспериментальные углы изгиба по результатам восьми сканирований при размерах пятна от D = 4 мм до D = 12 мм. Мощность и энергия площади постоянны и равны P = 800 Вт и AE = 6,67 Дж/мм 2 соответственно. Углы изгиба усреднены по пяти образцам, показаны стандартные ошибки. При малых размерах пятна кривые изгиба выравниваются быстрее из-за повышенного испарения краски и большей чувствительности к утолщению лицевого листа.
Более полное представление об эффективности изгиба можно получить, сравнив углы изгиба, достигнутые при каждом условии после одного и восьми лазерных сканирований, как показано на рис.14. После одного сканирования наблюдалось отчетливое увеличение угла изгиба с D = 4 мм до D = 8 мм, которое стало еще более выраженным после 8 сканирований. Опять же, причина в том, что по мере увеличения размера пятна происходит меньшее испарение краски, а механизм гибки менее чувствителен к утолщению лицевого листа. Кроме того, при D = 4 мм и D = 6 мм температуры лицевого листа были очень близки к температурам плавления (см. рис. 5), следовательно, могло произойти локализованное плавление, сбрасывающее часть сжимающих напряжений.На рис. 14 также показано небольшое снижение угла изгиба с D = 8 мм до D = 12 мм после одного лазерного сканирования. После восьми сканирований эта тенденция исчезла, а углы изгиба вышли за пределы D = 8 мм. Первоначальная тенденция связана с тем, что увеличение скорости сканирования при постоянной подводимой энергии сокращает время диффузии тепла, тем самым увеличивая температуры и, следовательно, углы изгиба [37]. Этот эффект сводится на нет после многократного сканирования, поскольку пятна большего размера меньше испаряют краску и менее чувствительны к утолщению лицевой панели.
Рис. 14
Экспериментальные углы изгиба после 1 сканирования и 8 сканирований при размерах пятна от D = 4 мм до D = 12 мм. Мощность и энергия площади постоянны и равны P = 800 Вт и AE = 6,67 Дж/мм 2 соответственно. Углы изгиба усреднены по пяти образцам, показаны стандартные ошибки.
Рис. 14
Экспериментальные углы изгиба после 1 сканирования и 8 сканирований при размерах пятна от D = 4 мм до D = 12 мм.Мощность и энергия площади постоянны и равны P = 800 Вт и AE = 6,67 Дж/мм 2 соответственно. Углы изгиба усреднены по пяти образцам, показаны стандартные ошибки.
Лазерное формование сэндвич-панелей возможно не только с различными размерами пятна, но также имеется значительная свобода в выборе энергии площади. Как показано на рис. 15, 40-процентное изменение скорости сканирования (и, следовательно, площади энергии) по-прежнему приводило к заметным углам изгиба.Размер пятна и мощность поддерживались на уровне D = 12 мм и P = 800 Вт соответственно. Увеличение скорости сканирования привело к падению энергии площади и, следовательно, к уменьшению угла изгиба, тенденция, которая хорошо отражена в моделировании.
Рис. 15
Экспериментальные и числовые значения углов изгиба после однократного сканирования при размере пятна D = 12 мм и мощности P = 800 Вт.Результаты экспериментов усреднены по пяти образцам, приведены стандартные ошибки. С увеличением скорости сканирования энергия площади и, следовательно, угол изгиба уменьшаются. Можно использовать значительный диапазон энергий площади.
Рис. 15
Экспериментальные и расчетные углы изгиба после однократного сканирования при размере пятна D = 12 мм и мощности P = 800 Вт. Результаты экспериментов усреднены по пяти образцам, стандартные ошибки показано. С увеличением скорости сканирования энергия площади и, следовательно, угол изгиба уменьшаются.Можно использовать значительный диапазон энергий площади.
До сих пор все представленные численные результаты были получены с использованием эквивалентной сэндвич-модели, показанной на рис. 2(а). В этом разделе эквивалентная сэндвич-модель сравнивается с сэндвич-моделью Кельвина, показанной на рис. 2(b), в которой полости сердцевины из пенопласта явно моделируются с использованием геометрии ячеек Кельвина.
С одной стороны, геометрия модели пенопласта кажется менее важной для сэндвич-панелей, чем для отдельно стоящих пенопластов [17], поскольку поглощение лазерного излучения в верхнем лицевом листе одинаково независимо от геометрии пенопласта. Кроме того, распределения температуры во время лазерного сканирования в обеих моделях очень похожи, как показано на рис. 16 для D = 12 мм, v = 10 мм/с и P = 800 Вт.
Рис. 16
Распределение температуры в сэндвич-образце, сканированном при D = 12 мм и v = 10 мм/с с использованием ( a ) эквивалентной сэндвич-модели и ( b ) модели сэндвича по Кельвину.Половина образца показана из-за симметрии. Рисунок 16 . Половина образца показана из-за симметрии.
С другой стороны, геометрия сердцевины из пеноматериала оказывает существенное влияние на теплопередачу между лицевыми панелями и сердцевиной из металлической пены.В эквивалентной модели сэндвича нет геометрических ограничений для теплового потока между лицевой панелью и металлической пеной, тогда как тепловой поток в модели сэндвича Кельвина проходит через тонкие стенки ячеек. Это приводит к расхождению градиентов температуры, как показано на рис. 17 (аналогично рис. 5). Из-за геометрического ограничения теплового потока больше тепла «удерживается» в верхней лицевой панели сэндвич-модели Кельвина. Как следствие, верхний лицевой лист нагревается больше, и на интерфейсе возникает больший перепад температуры.Это несоответствие более выражено при D = 12 мм, чем при D = 4 мм, поскольку тепло имеет больше времени для рассеивания из-за уменьшенной скорости сканирования [37], что делает свойство интерфейса более важным.
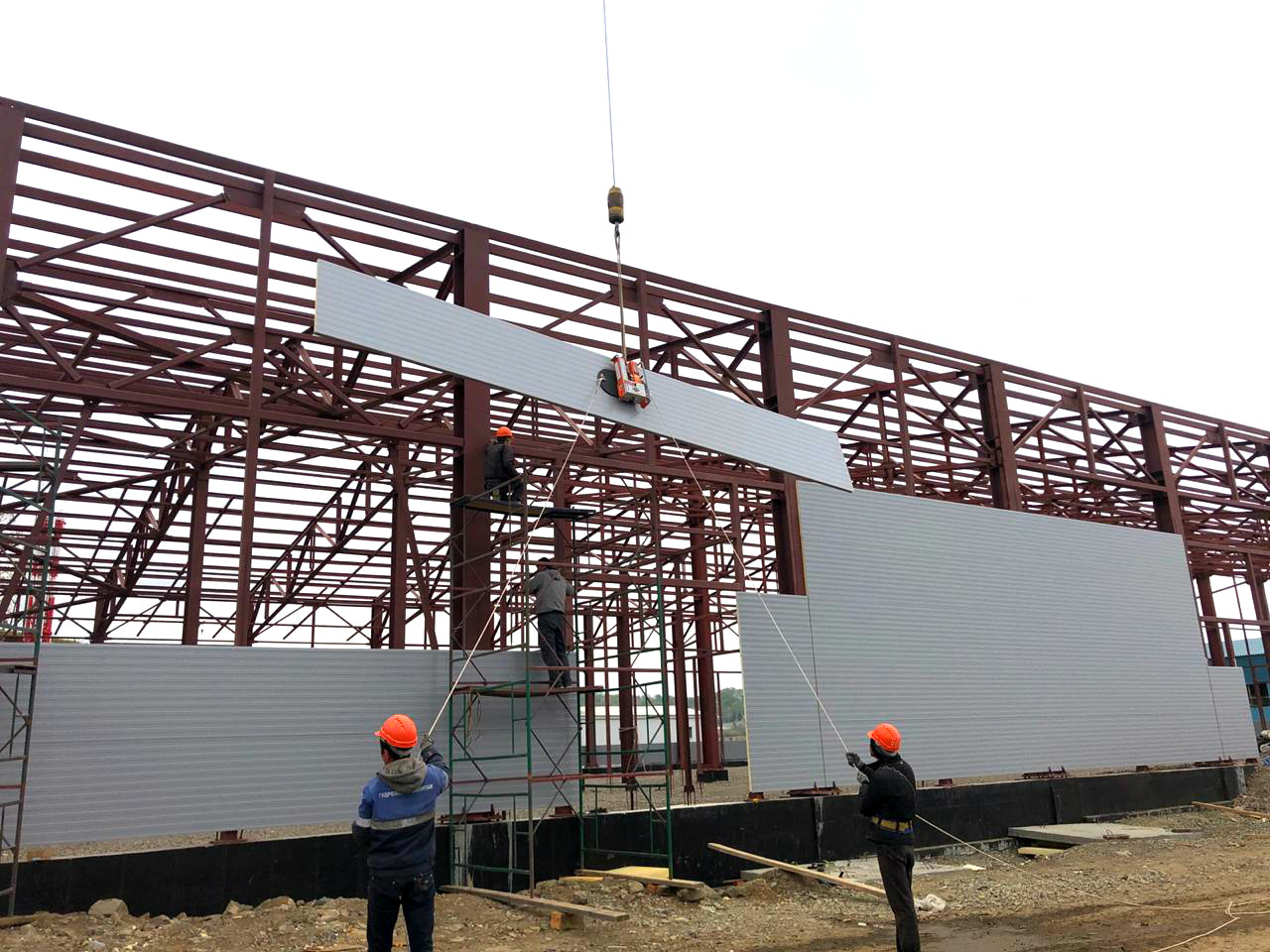
Геометрия сердцевины из пеноматериала также оказывает значительное влияние на механическое взаимодействие между лицевыми панелями и сердцевиной из пеноматериала. В эквивалентной сэндвич-модели верхний лицевой лист утолщается одинаково по всему пути лазерного сканирования (см.8). С другой стороны, в сэндвич-модели Кельвина пенопластовый сердечник имеет высокую жесткость, вызванную геометрией, которая локально ограничивает расширение лицевого листа, явление, которое также наблюдалось в экспериментах. На участках, где под лицевым листом на линии развертки находится полость (рис. 18, а)), лицевой лист может неограниченно расширяться вниз, и в лицевом листе развиваются значительные пластические деформации сжатия. На участках, где клеточная стенка расположена под лицевым листом на линии сканирования (рис. 18(b)), расширение лицевого листа ограничено и развиваются менее пластические деформации сжатия. Это явление происходит преимущественно при D = 4 мм, потому что расширение лицевого листа сильно локализовано на линии лазерного сканирования. При D = 12 мм лицевой лист утолщается на большем расстоянии от линии лазерного сканирования, а влияние геометрии сердцевины из пенопласта уменьшается.
Рис. 18
Распределение пластической деформации в модели сэндвича Кельвина после лазерного сканирования при D = 4 мм при v = 30 мм/с.Был использован масштабный коэффициент деформации 10. Половина образца показана из-за симметрии. В ( и ) полость расположена под лицевым листом на линии сканирования, и лицевой лист может неограниченно расширяться вниз. В (b ) стенка ячейки расположена под лицевым листом, и расширение лицевого листа вниз ограничено. Рис. 18Был использован масштабный коэффициент деформации 10. Половина образца показана из-за симметрии. В ( и ) полость расположена под лицевым листом на линии сканирования, и лицевой лист может неограниченно расширяться вниз. В (b ) стенка ячейки расположена под лицевым листом, и расширение лицевого листа вниз ограничено.
Благодаря повышенной геометрической точности сэндвич-модель Кельвина обладает повышенной чувствительностью к изменениям условий процесса, как показано на рис.19. В то время как эквивалентная сэндвич-модель предсказала небольшую разницу в угле изгиба между малым размером пятна ( D = 4 мм) и большим размером пятна ( D = 12 мм), сэндвич-модель Кельвина предсказала более значительную разницу между два, что более близко согласуется с экспериментальными результатами. Обе модели завышают значения углов изгиба при D = 4 мм, поскольку ни одна из моделей не учитывает испарение краски и возможные эффекты локального плавления, возникающие при D = 4 мм.
Рис. 19
Экспериментальные и числовые углы изгиба после одного лазерного сканирования при г = 4 мм и V = 30 мм / с, и D = 12 мм и V = 10 мм / с ( P = 800 Вт = пост.). Модель Кельвина более чувствительна к изменениям условий процесса благодаря более высокой геометрической точности. Обе модели завышали значения углов изгиба при D = 4 мм, поскольку они не учитывали испарение краски и локализованное плавление.
Рис. 19
Экспериментальные и числовые углы изгиба после одного лазерного сканирования при г = 4 мм и V = 30 мм / с, и D = 12 мм и V = 10 мм / с ( P = 800 Вт = пост.). Модель Кельвина более чувствительна к изменениям условий процесса благодаря более высокой геометрической точности. Обе модели завышали значения углов изгиба при D = 4 мм, поскольку они не учитывали испарение краски и локализованное плавление.
Это исследование показало, что сэндвич-панели с наполнителем из металлической пены можно формовать лазером в широком диапазоне технологических условий. Было показано, что как верхний лицевой лист, так и сердцевина из металлической пены изгибаются посредством механизма лазерной формовки и активно способствуют деформации изгиба. Механизм изгиба верхней лицевой панели зависит от размера лазерного пятна и варьируется от TGM (для малых размеров пятна около D = 4 мм) до UM (для больших размеров пятна около D = 12 мм).Сердцевина из металлической пены изгибается с помощью MTGM для пятен любого размера. Также было продемонстрировано, что сэндвич-панели изгибаются более эффективно при больших размерах пятна, чем при малых размерах пятна, поскольку более крупные сегменты верхнего лицевого листа и металлической пены способствуют укорочению при сжатии. Кроме того, было показано, что гораздо большие углы изгиба могут быть достигнуты при больших размерах пятна из-за меньшего влияния утолщения лицевого листа на эффективность механизма изгиба. Наконец, было показано, что сэндвич-модели Кельвина обеспечивают более точное предсказание углов изгиба и взаимодействие лицевого листа и пенопласта, чем эквивалентные сэндвич-модели, благодаря их более высокой геометрической точности.
Из этого исследования стало ясно, что поверхность раздела лицевого листа и пенопласта играет центральную роль в лазерном формовании сэндвич-панелей. Различные типы адгезии могут существенно повлиять на теплопередачу и механику и, следовательно, изменить результат процесса лазерной формовки.
Сэндвич-панели | Научный.Net
Сэндвич-панели из перфорированных металлических материаловАвторы: Виктор Миронов, Михаил Лисицын, Ирина Бойко
Аннотация: В настоящее время все большее внимание уделяется композитным материалам (панелям) сэндвич-структуры, особенно экологически безопасным. Сэндвич-панели представляют собой особый тип композитов, состоящих как минимум из трех слоев: сердцевины и обшивки, приклеенных к каждой стороне. Целью данной работы является исследование возможности использования перфорированных металлических материалов для изготовления сэндвич-панелей различного назначения в гражданском строительстве. Используя перфорированные металлические материалы в сочетании с различными материалами сердцевины или используя перфорированные металлические материалы в качестве материала сердцевины, можно производить широкий ассортимент изделий для строительства, демпфирования или изоляции.В статье предложен пример использования листовых перфорированных металлических материалов для изготовления сэндвич-панелей. Были проведены как модельные, так и экспериментальные исследования (механические испытания) для оценки несущей способности сэндвич-панелей и подтверждения применимости предлагаемых сэндвич-панелей для строительных конструкций. Для анализа полученных структур использовалось программное обеспечение анализа методом конечных элементов (FEA).
Результаты моделирования хорошо совпадают с результатами экспериментальных исследований.Таким образом, новые виды сэндвич-панелей и технология их изготовления показывают свою надежность и могут быть рекомендованы для применения в различных отраслях, в частности для изготовления облегченных потолочных панелей с наполнителем из теплоизоляционных материалов.
155
Оценка профиля динамической температуры в огненагруженных многослойных конструкциях на основе древесины в сравнении с традиционными конструктивными системамиАвторы: Мари Русинова, Милош Калоусек, Йиржи Шланхоф
Аннотация: Пожарная безопасность – важная характеристика здоровой внутренней среды.В случае возникновения пожара внутренняя часть противопожарных отсеков внутри здания подвергается воздействию очень высоких температур и другим явлениям, сопровождающим процесс горения. Все они воздействуют на границы структур отсеков, в том числе и на структуры, находящиеся внутри них. Некоторые конструкции выполняют несущую функцию вместе с противопожарными преградами, некоторые являются только противопожарными преградами. Что касается резкого повышения температуры, то следует учитывать его влияние на противоположную поверхность противопожарной перегородки, в частности, на поведение несущих элементов и их устойчивость.Это актуально на сегодняшний день, так как традиционные строительные материалы уступают место деревянным многослойным конструкциям, которым отдают предпочтение прежде всего по теплоизоляционным свойствам, малому весу, малой толщине и быстроте возведения. В статье используется динамическое моделирование, чтобы проиллюстрировать, как эти современные конструкции реагируют на высокие температуры в определенные промежутки времени, предлагая сравнения с традиционными кирпичными конструкциями.
98
Расчет трехслойных панелей с пенополиуретановым наполнителем с учетом реологических свойств среднего слоя Авторы: Батыр М. Языев, Антон Сергеевич Чепурненко, А.А. Савченко
Аннотация: В статье рассматривается обработка кривых сдвиговой ползучести вспененных полимеров, а также методика расчета трехслойных балок с учетом нелинейной ползучести заполнителя. В качестве закона ползучести используется уравнение Максвелла-Гуревича. Приведен пример расчета трехслойной панели со средним слоем из пенополиуретана.
144
Огнестойкость сэндвич-панелей для кровельных работАвторы: Джулио Дзани, Марко Карло Рампини, Маттео Коломбо, Марко ди Приско
Аннотация: Многослойные панели на цементной основе представляют собой перспективное и экономичное решение для кровли современных быстровозводимых зданий.В связи с распространением таких технологий считается необходимым оценивать характеристики конструкции также с учетом сценария пожара. В рамках исследовательского проекта, финансируемого национальными и региональными властями, Политехнический университет Милана координировал широкую экспериментальную кампанию, направленную на оценку механических свойств инновационных композитных элементов (ширина 2,5 м, длина 5 м). В документе представлены результаты полномасштабных испытаний прототипа при высоких температурах, в основном с акцентом на диаграммах температура-время и перемещение-время, а также приведена классификация огнестойкости, совместимая с наблюдаемым режимом отказа.
775
Экспериментально-теоретические исследования механических свойств перфорированных композитных сэндвич-панелейАвторы: А.Н. Аношкин, В.Ю. Зуйко, А.В. Чугайнова, Е.Н. Шустова
Аннотация: Работа посвящена экспериментально-теоретическому анализу механических свойств сэндвич-панелей из волокнистых полимерных композиционных материалов. Рассмотрены конструкции с трубчатым сердечником. Проведено численное моделирование механического поведения и испытания на растяжение натурных образцов сэндвич-панелей. Также проведен анализ влияния перфорации на механические свойства стеклопластиков и сэндвич-панелей.
1
Акустические характеристики гибридных композитных сэндвич-панелейАвторы: Сержиу Патинья, Фернандо Кунья, Рауль Фангейро, Соэль Рана, Фернандо Прего
Аннотация: В данной статье рассматривается характеристика звукоизоляционных свойств гибридных сэндвич-композитных панелей для применения в модульном домостроении.Эти сэндвич-панели представляют собой устойчивое, легкое и прочное решение, так как в их основе структура натуральных волокон, пропитанных термореактивным полимером. Таким образом, были изготовлены и проанализированы три разных типа гибридных композитных панелей, содержащих полиуретановую сердцевину и слоистую композитную оболочку, с различным составом ламинатов. Композитные ламинаты прототипов были изготовлены методом вакуумной инфузии и состояли из стеклянных и джутовых волокон, пропитанных полиэфирной смолой.Разработанные решения сравнивались с эталоном, составленным из гипсокартонных листов разной толщины и используемых для тепло- и звукоизоляции. Звукоизоляционные характеристики проводились на образцах размером 220×220 мм в звуконепроницаемой акустической камере. Протестированные сэндвич-панели показали многообещающие результаты; однако их общая производительность была ниже по сравнению с производительностью стандартных решений, использованных для сравнения. Тем не менее, конкретные характеристики звукоизоляции, т.е.е. Снижение уровня шума на единицу массы материала для разработанных сэндвич-панелей было значительно выше по сравнению со стандартными материалами, что свидетельствует о большей пригодности этого инновационного решения для облегченного строительства и модульного домостроения.
455
Исследование поведения при поперечном сдвиге сэндвич-конструкции из углепластика с М-образным складчатым заполнителемАвторы: Ли Синь Цун, Юй Го Сунь
Резюме: Для того, чтобы решить проблему качества соединения лицевой части и сердцевины сэндвич-структуры, в этой статье была предложена М-образная складчатая сэндвич-структура. Структурные характеристики при прямом (чистом) сдвиге были исследованы для сэндвич-структуры. Для возможных режимов разрушения был представлен FE-анализ прочности многослойной конструкции в условиях сдвиговой нагрузки. Панели с сердцевиной разной толщины были испытаны на различные режимы разрушения и механические свойства. В целом, измеренные разрушающие нагрузки показали хорошее соответствие прогнозам КЭ-анализа. Результаты показали, что режимами разрушения многослойной конструкции с низкой относительной плотностью были коробление при сдвиге и разрушение тонкостенных стержней соответственно.Для сэндвич-структуры с высокой относительной плотностью доминирующим режимом отказа было межфазное отслоение поверхности/сердцевины и инициирующий отказ вдоль концов образцов.
173
Эффективный анализ разработки приспособлений для сшивания сэндвич-панелей в аэрокосмической отрасли Авторы: Р. Сантханакришнан, Дариус Стэнли, Тангавел Сандживираджа, А. Джозеф Стэнли
Аннотация: В последние годы в качестве жизнеспособных инженерных сооружений рассматриваются сэндвич-конструкции. Использование композитных конструкций в аэрокосмических и гражданских конструкциях растет, особенно из-за их чрезвычайно малого веса, что приводит к снижению общего веса, высокой стойкости к изгибу и коррозии в дополнение к более высокой жесткости на поперечный сдвиг.Многие исследователи по всему миру оценивали различные комбинации толщины заполнителя и лицевого листа. В этом исследовании оцениваются аспекты соединения лицевых листов и сердцевины посредством сшивания, а также изучается эффект и эффективность сшивания. В этой статье в основном рассматривается конструкция приспособления, используемого для сшивания сэндвич-панелей, которое помогает сшивать файлы с различными ориентациями, такими как 90 0 , 45 0 , 90 0 /45 0 /90 0 и 90 . 0 /45 0 .Ключевые слова: сэндвич-панели, композиционные материалы, конструкция крепления, сшивные панели, сшитая пенопластовая конструкция.
1055
Влияние размера ячейки на результаты конечно-элементного анализа Z-образных прогонов, поддерживаемых сэндвич-панелямиАннотация: В работе рассмотрены вопросы численного анализа тонкостенных Z-образных прогонов в покрытиях зданий из сэндвич-панелей.Численный анализ выполнен в программе MSC.NASTRAN. Исследовано влияние сетки элементов на результаты расчетов. Результаты проведенного численного анализа позволили разработать методику определения жесткости соединения прогона с сэндвич-панелями.
1483
Анализ методом конечных элементов холодногнутых Z-образных прогонов, поддерживаемых сэндвич-панелями Аннотация: В настоящее время в гражданском и промышленном строительстве широко распространены здания на основе облегченных стальных каркасов. В качестве ограждающих конструкций здания может использоваться профнастил или кровельные сэндвич-панели, крепящиеся к тонкостенным холодногнутым прогонам. В данной работе исследуются вопросы численного анализа тонкостенных Z-образных прогонов в покрытиях из сэндвич-панелей. Численный анализ выполнен в программе MSC.NASTRAN. Рассмотрена полномасштабная модель кровли с прогонами и сэндвич-панелями. Численный анализ основан на лабораторных экспериментах. Результаты описанных анализов сравниваются с результатами испытаний.Эти исследования проводятся для изучения поведения кровельной системы, состоящей из Z-образных прогонов и сэндвич-панелей, и для разработки корректной конечно-элементной модели для расчета холодногнутых прогонов, опирающихся на сэндвич-панели.
398
Моделирование процесса формования изогнутых композитных сэндвич-панелей
Композитные сэндвич-панели обладают высокой удельной жесткостью на изгиб, открывая возможности для облегчения конструкции. Однако производство сэндвич-компонентов сложной формы может быть дорогостоящим, поскольку в дополнение к процессам формования оболочек требуются операции механической обработки сердцевины.
В хорошо зарекомендовавших себя крупносерийных изделиях, таких как легкие компоненты грузового пола салона автомобиля, сравнительно недорогой композитный сэндвич изготавливается путем прессования материала сердцевины для придания формы одновременно с обшивкой за одну операцию формования. В то время как процесс формования вызывает локальное коробление или разрушение структуры сердечника, механические характеристики готового компонента оказались достаточными для этого типа применения [1, 2, 3, 4, 5, 6, 7].Типичные комбинации материалов для сэндвич-структур, формованных прессованием, включают композитные покрытия из стекловолокна, обычно изготавливаемые из мата из рубленого волокна с длиной волокна более 25 мм, шестиугольные бумажные сердцевины и пенополиуретановую смолу. Арматура в обшивках пропитана смолой. Поскольку смола расширяется во время отверждения, она частично заполняет открытые ячейки сердцевины (на границе с оболочкой), что способствует развитию прочных связей между сердцевиной и оболочками. Существуют варианты этого процесса с использованием различных типов сердечников и текстильной оболочки из углеродного волокна для более высоких структурных требований.
При изготовлении панелей переменного сечения и сложной кривизны сердечник может подвергаться многоосным режимам деформирования, включая плоскостное растяжение, сжатие и сдвиг, а также сжатие по толщине и внеплоскостной изгиб [8,9,10]. Одновременно армирующие обшивки подвергаются сдвигу в плоскости и изгибу вне плоскости при формировании ткани. Также может иметь место относительное перемещение между сердцевиной и оболочкой во время формования. Типичными проблемами, возникающими в процессе, являются сморщивание обшивки из-за локального коробления волокна, разрыв сердцевины из-за чрезмерных напряжений в плоскости и плохое прилегание многослойной сборки к поверхностям инструмента из-за низкой жесткости по толщине смятого материала. основной.
Применение методов моделирования облегчает оценку осуществимости процесса до его реализации. Однако в настоящее время не существует подхода к моделированию для выявления проблем, связанных с формованием, и оптимизации параметров процесса. Почти все доступные методы моделирования учитывают несущую способность сэндвич-панелей, включая прогнозирование повреждений [11,12,13,14]. Модель потребуется для моделирования процесса формования сэндвичей, чтобы предсказать дефекты, вызванные формованием.В то время как разрушение сотового заполнителя по всей толщине считается видом отказа в проектировании конструкций [15,16,17], это формирующий механизм при изготовлении компонентов. Кроме того, существующие модели конечных элементов (КЭ) разработаны для многослойных конструкций, в которых обшивка соединена с сердцевиной, что необходимо для передачи нагрузки [18,19,20]. Однако процесс формирования зависит от относительного проскальзывания между обшивкой и сердцевиной. Следовательно, адгезия сердцевины к коже здесь не является проблемой.
Полная модель процесса требует интеграции трех одновременных эффектов: формирование армирующих обшивок, многоосная деформация структуры сердечника и эффекты трения (инструмент-армирование и армирование-сердцевина).Высокоточное прогнозное моделирование формирования армирования (драпирования) хорошо развито. Как правило, тканые и неизвитые ткани можно моделировать с использованием неортогональной конститутивной модели, включающей несколько слоев и эффекты трения [21, 22, 23, 24, 25, 26, 27, 28, 29, 30, 31, 32]. . Многоосное деформационное поведение ядра является сложным, требующим модели материала, которая отражает формообразующие характеристики, возникающие в результате искажения ячеистой структуры и разрушения ядра по всей толщине в результате неупругого выпячивания и складывания клеточных стенок.Структура ядра может быть детально смоделирована в мезомасштабе с использованием элементов оболочки для представления клеточных стенок с соответствующей плотностью сетки для захвата процесса неупругого дробления. Однако этот подход невозможен для моделей в масштабе компонентов, так как потребуется большое количество конечных элементов, что приведет к длительному времени процессора.
В качестве альтернативы можно разработать макромасштабные модели материала сердцевины, основанные на объемных конечных элементах и гомогенизации структуры сердцевины для получения эффективных механических свойств.Это может уменьшить общее количество степеней свободы в модели и свести к минимуму риск численной нестабильности. Недостатком этого подхода является то, что он требует в качестве входных данных многоосных нелинейных свойств материала, которые может быть трудно охарактеризовать экспериментально. Кроме того, взаимодействие между оболочками и сердцевиной является сложным.
Настоящая работа направлена на разработку нелинейной явной конечно-элементной модели процесса формования сэндвич-панелей и ее проверку на основе экспериментальных исследований, включая полномасштабный демонстрационный образец технологии.
Наука и технология композиционных материалов
Послушать эту тему
В таком развитом обществе, как наше, мы все зависим от композитных материалов в некоторых аспектах нашей жизни. Стекловолокно был разработан в конце 1940-х годов и стал первым современным композитом. Он по-прежнему остается самым распространенным, составляя около 65 процентов всех производимых сегодня композитов. Он используется для изготовления корпусов лодок, досок для серфинга, спортивных товаров, облицовки бассейнов, строительных панелей и кузовов автомобилей.Вы вполне можете использовать что-то из стекловолокна, не подозревая об этом.
Лодки, доски для серфинга, автомобили и многое другое: стекловолокно и другие композитные материалы окружают нас. Источник изображения: sobri/Flickr.Что делает материал композитным
Композитные материалы образуются путем объединения двух или более материалов, обладающих совершенно разными свойствами. Различные материалы работают вместе, чтобы придать композиту уникальные свойства, но внутри композита вы можете легко отличить разные материалы — они не растворяются и не смешиваются друг с другом.
Композиты существуют в природе. Кусок дерева представляет собой композит, состоящий из длинных волокон целлюлозы (очень сложной формы крахмала), скрепленных гораздо более слабым веществом, называемым лигнином. Целлюлоза также содержится в хлопке и льне, но именно связывающая способность лигнина делает кусок древесины намного прочнее пучка хлопковых волокон.
Это не новая идея
Человечество использует композитные материалы тысячи лет. Возьмем, к примеру, глиняные кирпичи.Если вы попытаетесь согнуть лепешку из засохшей грязи, она легко сломается, но будет прочной, если вы попытаетесь раздавить или сжать ее. С другой стороны, кусок соломы обладает большой силой, когда вы пытаетесь его растянуть, но почти не имеет силы, когда вы его смываете. Когда вы смешиваете глину и солому в блоке, свойства двух материалов также объединяются, и вы получаете кирпич, который устойчив как к сжатию, так и к разрыву или изгибу. Говоря более технически, у него есть как хорошие
прочность на сжатие и хорошо
предел прочности .
Еще одним известным композитом является бетон. Здесь заполнитель (мелкие камни или гравий) связан цементом. Бетон обладает хорошей прочностью при сжатии, и его можно сделать более прочным при растяжении, добавив в композит металлические стержни, проволоку, сетку или тросы (таким образом создавая железобетон).
Композиты были изготовлены из формы углерода, называемой графеном, в сочетании с металлической медью, в результате чего получается материал, в 500 раз прочнее, чем медь сама по себе. Точно так же композит графена и никеля имеет прочность, превышающую прочность никеля более чем в 180 раз.
Что касается стекловолокна, то оно изготовлено из
пластик армированный нитями или стеклянными волокнами. Эти нити можно либо связать вместе и сплести в мат, либо иногда нарезать на короткие отрезки, которые произвольно ориентированы в пластиковой матрице.
Больше, чем сила
В настоящее время многие композиты производятся не только для повышения прочности или других механических свойств, но и для других целей. Многие композиты предназначены для того, чтобы быть хорошими проводниками или изоляторами тепла или обладать определенными магнитными свойствами; свойства, которые являются очень специфическими и специализированными, но также очень важными и полезными. Эти композиты используются в огромном количестве электрических устройств, включая транзисторы, солнечные элементы, датчики, детекторы, диоды и лазеры, а также для изготовления антикоррозионных и антистатических покрытий поверхностей.
Композиты, изготовленные из оксидов металлов, также могут обладать особыми электрическими свойствами и используются для производства кремниевых чипов, которые могут быть меньше и более плотно упакованы в компьютер. Это увеличивает объем памяти и скорость компьютера. Оксидные композиты также используются для создания высокотемпературных сверхпроводящих свойств, которые теперь используются в электрических кабелях.
Изготовление композита
Большинство композитов состоят всего из двух материалов.Один материал (матрица или связующее) окружает и связывает вместе группу волокон или фрагментов гораздо более прочного материала (армирования). В случае сырцовых кирпичей две роли выполняют глина и солома; в бетоне цементом и заполнителем; в куске дерева, целлюлозой и лигнином. В стекловолокне армирование обеспечивается тонкими нитями или волокнами стекла, часто вплетенными в своего рода ткань, а матрица представляет собой пластик.
Примеры различных форм армирования стекла, используемых при создании стеклопластика.Источник изображения: Cjp24/Викисклад. Стеклянные нити в стекловолокне очень прочны при растяжении, но они также хрупкие и ломаются при резком изгибе. Матрица не только удерживает волокна вместе, но и защищает их от повреждений, разделяя любые
стресс из их. Матрица достаточно мягкая, чтобы ее можно было формировать с помощью инструментов, и ее можно смягчить подходящими растворителями, чтобы можно было произвести ремонт. Любая деформация листа стеклопластика обязательно растягивает часть стеклянных волокон, а они способны этому противостоять, поэтому даже тонкий лист очень прочен.Он также довольно легкий, что является преимуществом во многих приложениях.
За последние десятилетия было разработано много новых композитов, некоторые из которых обладают очень ценными свойствами. Тщательно выбирая армирование, матрицу и производственный процесс, который объединяет их, инженеры могут адаптировать свойства в соответствии с конкретными требованиями. Они могут, например, сделать композитный лист очень прочным в одном направлении, выровняв таким образом волокна, но более слабым в другом направлении, где прочность не так важна.Они также могут выбрать такие свойства, как устойчивость к теплу, химическим веществам и атмосферным воздействиям, выбрав соответствующий матричный материал.
Выбор материалов для матрицы
В качестве матрицы во многих современных композитах используются термореактивные или термопластичные пластмассы (также называемые смолами). (Использование пластика в матрице объясняет название «армированный пластик», обычно данное композитам). Пластмассы полимеры которые скрепляют арматуру и помогают определить физические свойства конечного продукта.
Термореактивные пластмассы жидкие при приготовлении, но затвердевают и становятся жесткими (т.е. отверждаются) при нагревании. Процесс схватывания необратим, поэтому эти материалы не становятся мягкими при высоких температурах. Эти пластмассы также устойчивы к износу и воздействию химических веществ, что делает их очень прочными даже в экстремальных условиях.
Термопластичные пластмассы, как следует из названия, являются твердыми при низких температурах, но размягчаются при нагревании. Хотя они используются реже, чем термореактивные пластмассы, у них есть некоторые преимущества, такие как более высокая вязкость разрушения, длительный срок хранения сырья, способность к переработке и более чистое и безопасное рабочее место, поскольку для процесса отверждения не требуются органические растворители.
Керамика, углерод и металлы используются в качестве матрицы для некоторых узкоспециализированных целей. Например, керамика используется, когда материал будет подвергаться воздействию высоких температур (например, теплообменники), а углерод используется для продуктов, подверженных трению и износу (например, подшипники и шестерни).
Электронно-микроскопическое изображение в искусственном цвете композита с магниевой матрицей, армированного карбидом титана-алюминия. Источник изображения: микроскопия ZEISS / Flickr.Выбор материалов для армирования
Хотя стекловолокно является наиболее распространенным армирующим материалом, во многих передовых композитах теперь используются тонкие волокна из чистого углерода.Можно использовать два основных типа углерода — графит и углеродные нанотрубки. Оба они представляют собой чистый углерод, но атомы углерода расположены в разных кристаллических конфигурациях. Графит — очень мягкое вещество (используется в «графитовых» карандашах) и состоит из листов атомов углерода, расположенных в виде шестиугольников. Связи, скрепляющие шестиугольники вместе, очень прочные, но связи, скрепляющие листы шестиугольников, довольно слабые, что и делает графит мягким. Углеродные нанотрубки изготавливаются путем скручивания одного листа графита (известного как графен) в трубку.Получается чрезвычайно прочная конструкция. Также возможно иметь трубки, состоящие из нескольких цилиндров — трубки внутри трубок.
Композиты из углеродного волокна легче и намного прочнее стекловолокна, но и дороже. Из этих двух графитовые волокна дешевле и проще в производстве, чем углеродные нанотрубки. Они используются в конструкциях самолетов и высокоэффективном спортивном оборудовании, таком как клюшки для гольфа, теннисные ракетки и гребные лодки, и все чаще используются вместо металлов для ремонта или замены поврежденных костей.
Нити из бора еще прочнее (и дороже), чем углеродные волокна. Нанотрубки из нитрида бора имеют дополнительное преимущество, заключающееся в том, что они намного более устойчивы к теплу, чем углеродные волокна. Они также обладают пьезоэлектрическими свойствами, что означает, что они могут генерировать электричество при воздействии на них физического давления, такого как скручивание или растяжение.
Полимеры также могут использоваться в качестве армирующего материала в композитах. Например, кевлар, изначально разработанный для замены стали в радиальных шинах, но наиболее известный своим использованием в пуленепробиваемых жилетах и шлемах, представляет собой полимерное волокно, обладающее чрезвычайной прочностью и повышающее прочность композита.Применяется в качестве армирования в композитных изделиях, требующих легкой и надежной конструкции (например, конструкционные детали корпуса самолета). Еще более прочным, чем кевлар, является вещество, изготовленное из комбинации графена и углеродных нанотрубок.
Выбор производственного процесса
Для изготовления объекта из композитного материала обычно используется какая-либо форма. Армирующий материал сначала помещается в форму, а затем напыляется или закачивается полужидкий матричный материал для формирования объекта.Можно приложить давление, чтобы вытеснить любые пузырьки воздуха, а затем форму нагреть, чтобы матрица затвердела.
Процесс формования часто выполняется вручную, но автоматическая обработка на машинах становится все более распространенной. Один из этих методов называется пултрузия (термин, образованный от слов «тянуть» и «экструзия»). Этот процесс идеально подходит для изготовления прямых изделий с постоянным поперечным сечением, таких как мостовые балки.
Во многих тонких конструкциях сложной формы, таких как изогнутые панели, композитная структура строится путем наложения листов тканого волокнистого армирования, пропитанного пластиковым матричным материалом, на базовую форму соответствующей формы.Когда панель изготовлена до необходимой толщины, матричный материал отверждается.
Многослойные композиты
Многие новые типы композитов производятся не методом матрицы и армирования, а путем укладки нескольких слоев материала. Структура многих композитов (например, используемых в панелях крыльев и корпусов самолетов) состоит из сот из пластика, зажатых между двумя обшивками из композитного материала, армированного углеродным волокном.
Сэндвич-структура из сотового композита от НАСА.Источник изображения: НАСА/Викисклад.Эти сэндвич-композиты сочетают в себе высокую прочность и особенно жесткость на изгиб с малым весом. Другие методы включают простое наложение нескольких чередующихся слоев различных веществ (например, графена и металла) для получения композита.
Зачем использовать композиты?
Самым большим преимуществом композитных материалов является прочность и жесткость в сочетании с легкостью.Выбирая подходящую комбинацию армирующего и матричного материала, производители могут добиться свойств, точно соответствующих требованиям к конкретной конструкции для конкретной цели.
- Композиты в Австралии
Австралия, как и все развитые страны, проявляет большой интерес к композитным материалам, которые многие считают «материалами будущего». Основная задача состоит в том, чтобы снизить затраты, чтобы композиты можно было использовать в продуктах и приложениях, которые в настоящее время не оправдывают затрат.В то же время исследователи хотят улучшить характеристики композитов, например, сделать их более устойчивыми к ударам.
Один из новых методов включает «текстильные композиты». Вместо того, чтобы укладывать армирующие волокна по отдельности, что медленно и дорого, их можно связать или сплести вместе, чтобы сделать своего рода ткань. Это может быть даже трехмерным, а не плоским. Пространства между текстильными волокнами и вокруг них затем заполняются матричным материалом (например, смолой) для изготовления изделия.
Этот процесс может быть легко выполнен машинами, а не вручную, что делает его быстрее и дешевле. Соединение всех волокон вместе также означает, что композит с меньшей вероятностью будет поврежден при ударе.
По мере снижения затрат другие варианты использования композитов начинают казаться привлекательными. При изготовлении корпусов и надстроек лодок из композитов используется их устойчивость к коррозии. У минных охотников ВМС Австралии композитный корпус, поскольку магнитный эффект стального корпуса будет мешать обнаружению мин.
Также в разработке находятся вагоны для поездов, трамваев и других «движителей людей», изготовленных из композитов, а не из стали или алюминия. Здесь привлекательность заключается в легкости композитов, поскольку в этом случае транспортные средства потребляют меньше энергии. По той же причине мы будем видеть все больше и больше композитов в автомобилях в будущем.
Ярким примером является современная авиация, как военная, так и гражданская. Без композитов было бы гораздо менее эффективно. Фактически, потребность этой отрасли в легких и прочных материалах была главной движущей силой разработки композитов.В настоящее время часто можно найти секции крыла и хвостового оперения, пропеллеры и лопасти несущего винта, изготовленные из передовых композитов, а также большую часть внутренней конструкции и фурнитуры. Планеры некоторых небольших самолетов полностью сделаны из композитных материалов, как и крылья, хвостовое оперение и панели корпуса больших коммерческих самолетов.
Размышляя о самолетах, стоит помнить, что композиты менее склонны к полному разрушению под нагрузкой, чем металлы (например, алюминий). Небольшая трещина в куске металла может очень быстро распространиться с очень серьезными последствиями (особенно в случае с самолетом).Волокна в композите блокируют расширение любой небольшой трещины и распределяют напряжение вокруг.
Подходящие композиты также хорошо противостоят нагреву и коррозии. Это делает их идеальными для использования в продуктах, которые подвергаются воздействию экстремальных условий, таких как лодки, оборудование для обработки химикатов и космические корабли. В целом композитные материалы очень прочны.
Еще одним преимуществом композитных материалов является то, что они обеспечивают гибкость дизайна. Композитным материалам можно придавать сложные формы, что очень удобно при производстве чего-то вроде доски для серфинга или корпуса лодки.