Взрезая «Железо»: Как прорезать окно в корпусе
Редакция «Железа» выражает благодарность интернет-магазину моддинг продукции www.pcdesign.ru за помощь в создании статьи.
Сразу должен сказать, что идея «увековечить» название популярного журнала возникла не у меня, а, что более логично, у его издателей. Редакция предоставила команде modding.ru корпус и свой логотип в формате векторной графики. В итоге логотип должен был быть прорезан в боковине корпуса. Конечно, самым простым решением была бы лазерная резка, но для «усложнения» процесса, было решено использовать дремель. Заодно мы и узнаем, на что способен этот, без сомнения, самый популярный инструмент моддера. А задача, должен признаться, действительно, не из простых, поскольку логотип, высланный нам, прямо скажем, выполнен не самым большим шрифтом. Что ж, дизайнерам виднее, а наша задача – вырезать!
Должен оговориться, что написанное ниже не будет выдержано в стиле «мастер-класс», поскольку, по большому счету, для получения ИДЕАЛЬНОГО результата ни дремель, ни какой-либо другой «одомашненный» инструмент не подходят. Такие задачи в идеальном качестве под силу только лазеру. Но обо всем по порядку.
Пара слов о дремеле
На форуме modding.ru народ спорил, как правильно говорить: мой дремель, мое дремель или моя дремель. Конечно же, дремель мужского рода, так как человек, который придумал этот инструмент — Albert J. Dremel, он же и основал в 1932 году одноименную, то есть «однофамильную» компанию. Сейчас это зарегистрированная торговая марка, под которой выпускается целый ряд интересных инструментов и насадок. А хозяевами этой марки являются всем известные производители стиральных машинок и холодильников — Bosch.
Дремель и насадки.
Дремель – это электрический инструмент, предназначенный для резки и обработки различных материалов. Моддеры вырезают дремелем отверстия в корпусе, отрезают плексиглас и сверлят. Очень полезная вещь для людей, любящих мастерить. Инструмент многофункциональный. С помощью него можно работать с деревом, металлом, пластмассой и с другими материалами. Можно, соответственно, отрезать и вырезать сложные формы, шлифовать и полировать, сверлить. Ну а для любого чокнутого моддера дремель — вообще незаменимый инструмент. Он позволяет так уродовать… то есть модифицировать корпус компьютера, как тебе и не снилось.
Скорость вращения вала у дремеля устанавливается в диапазоне от 10000 об/мин. до 33000 об/мин, и ты выбираешь из 5 скоростей необходимую с помощью переключателя. Дремель легкий, с ним просто работать, и он гораздо более безопасен, чем ажурные пилы. В отличие от ажурной пилы, при работе с дремелем нет надобности в зажимных приспособлениях для обрабатываемой детали. Это объясняется тем, что за раз дремель делает небольшие надрезы, и отдача от него очень маленькая.
В комплект с инструментом входит руководство по эксплуатации, гаечный ключ, патрон, патронная гайка Quick-Change и целый набор насадок.
Насадки
Для моддинга необходимы, в основном, два типа насадок: круглые насадки, которые называются режущими кругами (они-то как раз и используются для вырезания), и шлифовальные круги цилиндрической, конической и сферической формы. Их используют для удаления металлических заусенцев, которые имеются по краям только что вырезанного отверстия.
Очень удобный клей в виде лака для ногтей. Им приклеили оргстекло к корпусу.
Режущие круги, прилагающиеся к дремелю, довольно хрупкие и тонкие. Они быстро ломаются в процессе резки металла, особенно, если ты приложишь слишком много силы. Поэтому их лучше использовать для резки менее прочных материалов (например, оргстекла), а для вырезания отверстий в корпусе лучше купить специальные армированные режущие круги. Как следует из их названия, армированные режущие круги сделаны из более прочного материала и усилены проволочной сеткой.
Дальше приведу описания самых полезных насадок для дремеля.
Высокоскоростная стальная насадка подходит для выполнения фрезерных работ, выборки прорезей, пазов и конических отверстий в мягких материалах, пластмассе и древесине.
Высокоскоростная плоская стальная насадка подходит для тех же материалов, что и предыдущая, но может применяться для выполнения узких прорезей.
Щетка из нержавеющей стали применяется для обработки небольших участков коррозии на таких материалах как олово, алюминий и высококачественная сталь и препятствует дальнейшему распространению коррозии.
Боковая стенка, на которой вырезан логотип (вид с внутренней стороны). Кусок плекса обклеен белой бумагой, чтобы свет распределялся ровно по всей поверхности надписи. Рядом красная неоночка и черная коробочка — инвертор для розжига лампы.
Насадка из оксида алюминия хорошо подходит для обработки металлов, чугуна, сварных соединений, заклепок, а также удаления ржавчины. Идеально подходит для шлифования, удаления заусенцев и общих работ по шлифовке большинства материалов.
Насадка из карбида кремния нужна для эффективной обработки камня, стекла, керамики, фарфора и цветных металлов.
Следующая насадка имеет алмазное покрытие и предназначена для обработки деталей, резки, гравирования, выполнения резьбы, ремонта и заключительной обработки, для древесины, жадеита, керамических материалов, стекла, твердых металлов, полудрагоценных камней и других твердых материалов.
Насадка из карбида вольфрама нужна для фрезерования, выравнивания и съема материала, для закаленной стали, высококачественной стали, чугуна, цветных металлов, керамики, пластмасс, твердой древесины и других твердых материалов.
Зазубренные насадки из карбида вольфрама — быстрорежущие, очень твердые насадки, рассчитанные на интенсивный съем материала. Применяются для обработки стеклопластиков, древесины, пластмасс, эпоксидных материалов, резины, ламинатов, твердоволокнистых плит, мягких металлов, керамических плиток.
Круг хорошо подходит для отрезания и резки металлов, древесины и пластмасс. Применение отрезных кругов упрощает сквозную и несквозную резку болтов, осей, листовых панелей, тонкой древесины и пластмассы. Отрезной круг режет только краем. Он не пригоден для шлифовальных работ и криволинейной резки.
Режем жесть!
Готовимся к резке. Обклеиваем боковину малярным скотчем. На него, собственно, я и буду переносить логотип, а заодно он защитит боковину от возможных повреждений. Затем распечатываем, например, из Corel Draw логотип на обычной бумаге. Он меньше листа формата А4 в длину, а высота не превышает четырех сантиметров! Именно об этой проблеме я говорил выше? Но отступать не в наших правилах, а сложные задачи в команде моддеров всегда только приветствовались. Наклеиваем распечатанный логотип на копирку и все вместе на боковину корпуса. Переносим логотип на боковину и обводим полученный контур для большей четкости его границ.
Можно приступать непосредственно к резке. Берем в руки дремель. Для резки я использовал армированные режущие круги. Это те, которые со стекловолоконной сеточкой в абразиве. Такие круги гораздо меньше стачиваются в процессе работы. Учти, что тебе понадобится более одного режущего круга, так что покупать имеет смысл сразу комплект из пяти кругов. Прорезать лучше сначала длинные прямые линии. Принцип резки, такой же, как и при работе с болгаркой. То есть, намечаешь линию разреза и начинаешь понемногу ее углублять. Не надо стремиться сразу прорезать металл насквозь — ты только вызовешь этим перегрев инструмента или раскрошишь диск.
Когда ты с этим справишься, имеет смысл поменять насадку на шлифовальную. Это те, которые выглядят как уменьшенный абразивный круг для точильного станка. Этой насадкой очень удобно дорабатывать внешние контуры. Для внутренних контуров больше подойдет абразивный цилиндр. Существует более 150 видов насадок и приспособлений для дремеля, и при должном желании можно подобрать подходящую насадку для любого вида работ. Хотя бывают случаи, когда без надфиля и наждачки не обойтись.
Надо заметить, что хотя дремель и выглядит достаточно безобидным инструментом, соблюдение техники безопасности является обязательным условием при работе с ним. Перед выполнением любых работ с дремелем обязательно надевай защитные очки. Абразивная крошка, попавшая в глаза, может тебе дорого обойтись, а разлетевшийся режущий диск может серьезно травмировать.
Ну да не будем о грустном, а лучше посмотрим, что у нас получилось в итоге. Острые края кромок лучше обработать надфилем или мелкой шкуркой. Так мы избавимся от заусенцев. Торец, если ты не планируешь перекрашивать корпус, можно подкрасить подходящим маркером под цвет дефолтной краски.
Кромсаем плекс!
Настало время заняться вырезанием плекса, которым мы закроем логотип изнутри. Вырезать можно как ножовкой или электролобзиком, так и тем же дремелем при помощи насадки в виде уменьшенного диска для циркулярной пилы. Вообще, должен заметить, что не даром все насадки для дремеля напоминают своих «взрослых» собратьев, только выполнены в миниатюре. Это очень четко ограничивает круг применения этого замечательного инструмента. Дремель предназначен исключительно для домашнего применения, и в этом качестве сможет заменить массу других инструментов. Не надо им резать гранитные плиты или танковую броню, и этот инструмент прослужит тебе верой и правдой долгие годы. Хотя я бы рекомендовал к приобретению модели с приставкой «pro» — они более надежны и долговечны. Экземпляр на фото активно используется командой modding.ru уже более года!
Итак, оргстекло вырезано по размеру, и осталось его только приклеить. Есть масса способов это сделать, начиная от двухстороннего скотча, заканчивая новомодным «поксиполом». Подойдет любой — лишь бы плекс хорошо держался. Я предпочитаю более прочное соединение, тем более что боковина корпуса выполняет роль ребра жесткости, и лишний запас прочности при вклеивании плекса не помешает. Также можно использовать и заклепки, но это уже должно сочетаться с общим дизайном корпуса.
В итоге к задней стороне боковины приклеили оргстекло и поднесли лампу для пробы. Свет от неоновой лампы распределялся неравномерно. Тогда поверх стекла наклеили еще и лист белой бумаги, и с помощью него достигли ровного распределения света.
Гравюры на стекле
Для гравировки, что логично, используют гравировочные насадки. Выглядят они как палочка с шариком на конце. Диаметр этого шарика и будет толщиной линии.
Насадки бываю разной формы и диаметра. Яркость подсветки линии будет зависеть от глубины реза. Поэтому злоупотреблять миниатюрностью насадок не стоит. Для начала мы должны подобрать картинку, которую будем гравировать. Можно потренироваться на выполнении различного вида орнаментов. Они гораздо проще в исполнении, потому как являются полностью «залитыми» рисунками. Рисунки же могут включать более двух видов заливок, и поэтому их гораздо тяжелее выполнять, особенно неподготовленным людям без художественного образования, типа меня. В любом случае, гравировать рисунки, состоящие из более чем трех «цветов», или рисунки с градиентными заливками могут только особо одаренные особи нашего вида, потому как градиенты невозможно сделать дремелем и очень сложно наждачкой. Так что и связываться с ними я тебе не советую. Если ты хочешь использовать картинки, а не орнаменты, я бы советовал обратить внимание на японский стиль — аниме. Особенностью этого стиля рисунка является редкое использование градиентов и довольно четкие границы между цветами. Найти подходящий рисунок среди картинок этого стиля на сайтах соответствующей тематики не составит труда.
Вот так выглядит гравировка без подсветки.
Кроме цветности к рисунку есть еще несколько требований. Он должен иметь нормальное качество, чтобы ты не пытался растянуть картинку 10х10 пикселей на все окно. Также он должен иметь достаточную контрастность.
Рисунок мы открываем в Photoshop, обесцвечиваем, делаем нужного размера, ориентации и печатаем. Картинку надо будет обвести фломастером по контурам цветов и приклеить с лицевой стороны стекла, так как гравировку надо делать изнутри. В процессе гравировки нужно учитывать скорость и направление вращения насадки. Тонкие линии лучше делать на большой скорости, а вот заливки — на маленькой. Чем больше скорость, тем меньше получается отдача, а глубина прореза больше. От глубины зависит контрастность и яркость линии.
А так — с подсветкой.
От направления вращения насадки зависит тип линии. Если вести дремелем по направлению движения, линии получатся белесыми с небольшими кусочками акрила. Такие линии хорошо видны даже без освещения неонкой. Если же выбранное направление будет обратно вращению, то получатся более глубокие и чистые линии, проявляющиеся за счет преломления света при освещении неоном. Какие линии использовать или как их совмещать — личное дело каждого, но хаотическое совмещение считается плохим тоном, ибо это просто некрасиво выглядит. Белесые линии всегда можно подчистить, проведя по ним еще раз насадкой против вращения вала.
После того как полностью нарисованы контуры рисунка, можно начинать делать заливки. Заливки надо делать кончиком большого сверла или наждачкой с мелким зерном. Заливки сверлом осуществляются такими же параллельными линиями, большей толщины, в одном направлении. Не нужно пытаться штриховать туда-сюда — получится грязно и все равно придется подчищать наждачкой, что отнимет дополнительное время.
Как говорилось выше, можно использовать несколько «цветов». Если процесс создания двух «цветов» (черного и белого), полностью понятен, то с другими еще надо разобраться. Как дополнительные цвета можно использовать разнообразные штриховки. Например, заливку сверлом можно делать не сплошной, а оставлять небольшой промежуток между линиями. Это уже будет выглядеть немного необычно. Еще одним альтернативным видом заливки может быть сетка под углом 90 градусов. Таким образом, можно выдумывать бесконечное множество «заливок», однако не перестарайся — обилие «заливок» может «замусорить» рисунок. Руководствуясь этими правилами можно на довольно профессиональном уровне сделать гравировку на акриле.
Вот так при помощи дремеля и пары насадок можно изменить свой кузов до неузнаваемости и сделать его настоящим произведением искусства. Что же касается корпуса, пострадавшего в этом материале, то для него это еще не конец. Скоро он приобретет законченный вид, и мы продемонстрируем результат тебе на страницах журнала.
Автор благодарит за помощь в подготовке материала Попело Андрея aka Димыч и Бойченко Максима aka Maximka.
daily-it.livejournal.com
Рекомендации по работе с Dremel`ем
Инструкция по работе с дремелем и аналогами дремеля.
– это универсальный инструмент для моддинг-проектов. Этим инструментом можно выполнять всевозможные операции, например резка, гравировка, сверление и многие другие операции. Дремель зачастую можно использовать в качестве замены лазерной резки, когда она недоступна или экономически нецелесообразна.
Дремель
Мы рассмотрим различную работу с дремелем, например такую как вырезание кругов или сложных объектов. Помните, чем больше вы будете работать с дремелем, тем лучше у вас будет получаться.
Инструменты:
— Dremel марки MultiPro.
— 1.5″ диски
— Защитные очки из небьющегося стекла
— Различные насадки
— Малярный скотч
Обратите внимание: В продаже появился новый армированный, полуторадюймовый диск равен груде обычных дисков, но не спешите выбрасывать ваши обычные диски ?
Оптимальное положение рук на дремеле
– стандартная проблема при использовании дисков для резки. Когда вы начинаете резку дремель начнет подскакивать. При этом есть вероятность того, что он будет касаться вашей панели и царапать краску. В этом случае вам поможет клейкая лента, которая предотвратить эти маленькие толчки. Всегда используйте обе руки при работе с дремелем.
Отдача
При резке лучшая поверхность это обычная картонная коробка из под монитора или системного блока. Потому что коробка очень устойчива и если вы ее повредите ее будет не жалко в отличии от вашего стола. При необходимости заготовку можно привязать к коробке, что уменьшит ее вибрации при резке.
Коробку дополнительно можно поставить на подставку или табурет, чтобы меньше наклонятся.
Вырезание по прямой линии
Положение ваших рук должно быть таким, будто вы держите клюшку для гольфа.
Пальцы должны быть расположены так, чтобы воздух от вентиляционных отверстий проходил свободно.
Вырезание по окружности
Положение обеих ваших рук должно быть таким, будто вы работаете гвоздодером.
Используйте свои локти для дополнительной поддержки
Инструкция по вырезанию дремелем прямых линий
Существует две техники прорезания прямой линии. Прорезаем насквозь заготовку, радом примерно в полсантиметра от первого отверстия делаем аналогичный прорез, после этого соединяем два прореза. И так до тех пор пока не прорежете линию.
Второй способ. Прорезаем насквозь заготовку и не вынимая диск двигаем по начерченной линии при этом прикладываем некоторое усилие. Этот способ быстрее, но и диски при этом стачиваются сильнее.
Инструкция по вырезанию дремелем кругов
Идиальный круг – это самая сложная форма для вырезания дремелем.
Вырезать ровный круг можно только, если у вас есть достаточный опыт при работе дремелем. Как только вы научитесь вырезать круги вы сможете вырезать любые самые сложные формы. Ниже я покажу как надо вырезать круги используя малярный скотч.
Держите дремель, как показано ниже
Запускаем дремель на скорости не ниже 15 тыс.оборотов в минуту. Только при повышенных оборотах, вы сможете контролировать свою работу и движения диском. Вначале углубляемся в заготовку на глубину 1/3 от толщины заготовки по всей окружности диска. Поворачивайте заготовку только по часовой стрелке. При прорезании заготовки держите диск по отношению к заготовки под углом 30-45 градусов.
Используя проделанное углубление вы сможете прорезать ровное отверстие
Постепенно углубитесь прорезая заготовку до глубины заготовки 1/4.
Обратите внимание, что вы режете под углом. Продолжайте резать под углом пока не прорежете заготовку насквозь
Теперь используйте круглый напильник, чтобы снять лишнюю фаску с края вырезанного круга.
Малярный скотч удален. У вас должен получился отличный круг для ручного дремеля.
Резка сложных форм и деталей
Мы рассмотрим вырезание сложных деталей на резке орла из алюминиевой панели корпуса. Алюминий как более толстый материал, чем сталь потребует большего количества дисков для вырезания и времени. Так что запаситесь и тем и другим.
Оклеиваем панель в один слой малярным скотчем.
Я применял скотч для каждого пера орла и прочертил полностью орла ручкой по скотчу.
Используйте корректирующую жидкость или ластик чтобы исправить свои ошибки при нанесении рисунка.
Вырезаем все прямые линии рисунка используя технологию описанную выше. Для вырезания закруглений или острых углов лучше всего использовать уже сточенные круги до половины или меньше. Они меньше вибрируют ими легче управлять и резка получается более ровная.
Не нагружайте дремель долгой работой, давайте ему отдохнуть примерно после каждого часа непрерывной работы или когда он сильно нагревается. Следите, чтобы дремель не перегревался иначе он может выйти из строя. В экстренных случаях дремель можно охладить включив его на пару секунд на полную мощность без нагрузки.
Всегда начинайте вырезать от центра к краю вашего рисунка
Прорезаем все полукруглые элементы используя технику для вырезания круга.
После завершения резки, удалите малярный скотч.
Переверните панель и используя напильник удалите неровности и обработайте края рисунка.
При обработке напильником панели подложите под нее тряпку, для того чтобы уменьшить царапины от стола
Напильником доводим края панели до совершенства
Для обработки различных углов используйте разные напильинки. Например для острых углов идеально подходит треугольный напильник, для прямых линий – плоский
Для овальных, круглых и дуговых – круглый.
Работайте напильником до тех пор, пока не будете удовлетворены результатом. Затем потрите края наждачной бумагой. Ваша панель готова.
modnews.ru
Резак для стеклотекстолита. / Инструмент / Сообщество EasyElectronics.ru
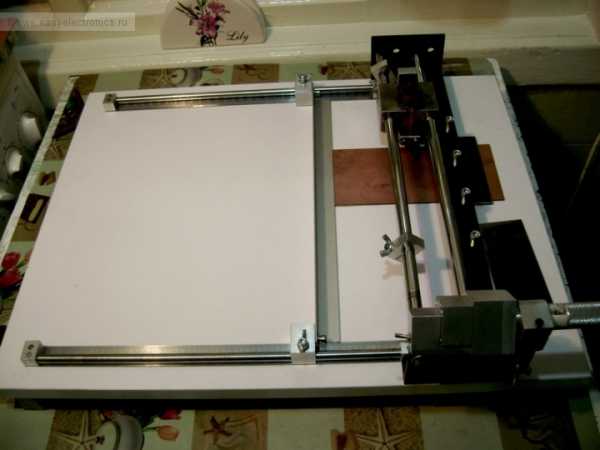
В данной статье пойдет разговор о том, как сделать своими руками из доступных средств устройство для резки фольгированного стеклотекстолита. Устройство, способное в некоторой мере облегчить труд радиолюбителя – самодельщика. Статья, полагаю, будет интересна широкому кругу радиолюбителей разного уровня. Особенно тем, для кого это больная тема. Конструкция устройства не содержит дефицитных материалов и несложна в изготовлении. При изготовлении использовался нехитрый слесарный инструмент.
Некоторое время назад, довелось мне получить небольшой заказ, на изготовление двух десятков устройств. На тебе чертежи, на тебе схемы, бери мяч и пи…… чь. Собственно поначалу ничего сложного казалось, не было, и заказчик особо не торопил. Но все же хотелось выполнить работу как можно раньше. Два десятка устройств по три платы размером в пачку сигарет. По началу, все шло нормально, но это только по началу. Усталость постепенно давала о себе знать. По концовке, пара испорченных листов материала, и плюс мозоли от резака на пальцах. Вот так!
После этого случая, я решил все радикально в этом плане поменять. Прежние методы резки стеклотекстолита меня мало чем устраивали. У каждого из них есть свои определенные недостатки. К примеру, при резке ножницами по металлу, можно порезать приблизительно ровно заготовку лишь небольших размеров. Ножовкой, ровно не всегда получается. Сабельный резак режет ровно и хорошо, но бывает иногда, затягивает материал, да и тупится довольно быстро. Гильотинные ножницы, увы, не всем доступны, и к тому же довольно небезопасны. Ручной резак из ножовочного полотна это вообще сущее издевательство.
Погуглив самоделки, я к великому своему сожалению не нашел ничего интересного для повторения. Даже как то странно, такое ощущение, что мир в этом направлении стоит на месте. Потом задался вопросом, а как же нынче в промышленности обстоят дела в этом плане? В совковое время, на сколько, я знал и видел, стеклотекстолит резали в основном на гильотинных ножницах. Сегодня же дело обстоит совершенно иначе. Режут этот материал методом скайбирования или фрезерованием, если плата имеет сложную форму. Технология скайбирования не сложная, материал пропускают между двумя заостренными дисками диаметром около 100 мм. Сами диски снабжены по периметру мелкими зубьями. Сам процесс несколько напоминает работу циркульной пилы.
Тогда я решил попробовать изготовить устройство похожее на небольшой скайбер самостоятельно. Но наткнулся на ряд проблем разного характера, в связи с чем, устройство получалось не бюджетным и сложным для повторения. В принципе я и не питал больших надежд по этому поводу, понадеялся на авось, но в плане эксперимента результат получился отрицательный. Но как говорят отрицательный результат, это тоже результат. Хотел было выбросить свое художество на помойку, но вовремя включилась соображалка, и изменил конструкцию. Идея пришла сама собой, но потребовала некоторых, переделок. Первоначально я приобрел победитовую пластину для резца размером 22 × 4 × 2 мм.
Марка победита мне не известна, как неизвестна, как я думаю, и человеку который торговал этим добром на рынке. Сегодня, к сожалению, трудно встретить человека, торгующего, чем либо, и который сможет дать вам грамотную консультацию по тому товару, который он продает. Чаще они или не понимают, о чем идет речь или задают, глупые вопросы, типа “ а для чего тебе это нужно ”. На это, для таких любопытных, у меня всегда готовый ответ. Говорю им, что делаю капкан для мышей. Сшибает с ног и с толку на раз.
Касаемо победита то это твёрдый сплав карбида вольфрама и кобальта в массовом соотношении 90:10. Обладает высокой твёрдостью 80—90 по шкале Роквелла. Существуют так же сплавы с добавками карбидов титана и тантала. Более подробную информацию можно получить тут или тут или, где ни – будь еще.
Конструктивно, устройство похоже на обычный плиткорез, да и сама идея тоже. Но изготовлено из более прочных материалов, так как в начале, предполагались более высокие нагрузки. В качестве направляющих, я использовал штоки от задних амортизаторов автомобиля Volkswagen. В первых, у них достаточная длина чтобы обеспечить разрезание заготовки формата А4, по наибольшей длине листа. Во вторых, изготовлены они из достаточно прочной стали (предположительно сталь Ст 40 или ее аналог). Поверхность штока цементирована и кроме того закалена и хромирована. И в третьих, поверхность обработана суперфинишированием. Правда, есть один незначительный минус, это две кольцевые канавки, проточенные с обоих концов штоков.
Суперфиниширование применяют для улучшения качества поверхностного слоя и удаления дефектов, возникших на предыдущих операциях. При обработке лезвийным инструментом или шлифованием на поверхности остается дефектный слой, вызванный сильной деформацией металла и действием высокой температуры. Суперфиниширование, выполняемое на мягких режимах, приводит к удалению дефектного слоя и увеличению износостойкости обработанной поверхности. Кроме того, суперфиниширование очищает поверхность от внедренных в нее при шлифовании обломков абразивных зерен. Применяя данный процесс, можно повысить размерную точность деталей и получить зеркальную поверхность. Шероховатость поверхности после суперфиниширования может достигать высшего, 14-го класса. Полированием достигают только 12-го класса шероховатости.
При повторении конструкции, если появится такое желание, плиткорез, можно смело взять за основу. Но тут все зависит от ваших запросов и кармана. Можно приобрести обычный с двумя направляющими, а можно и более дорогой, но и более качественный, рельсовый.
Прежде чем покупать, все же желательно ознакомиться с предлагаемым ассортиментом. Не следует покупать слишком навороченные и дорогие. Все навороты все равно полетят в мусорное ведро. Основное требование это прочность изделия и качество изготовления. Изделия, изготовленные ПТУшниками, не годятся однозначно. Пусть пользуются строители такими изделиями, для них плюс – минус сантиметр, не косина. А нам нужна в первую очередь точность! По большому счету, нас интересуют направляющие, ползун (или каретка) и крепление направляющих. На это следует обратить внимание в первую очередь. Направляющие и ползун нужно осмотреть более внимательно от них зависит работа устройства в дальнейшем, они не должны иметь дефектов; типа вмятин, сколов, глубоких царапин и следов коррозии. Ход ползуна должен быть легкий без заеданий и рывков. В то же время ползун, по возможности, не должен болтаться в направляющих (люфтить). Само основание устройства, если выполнено из тонкой штампованной жести, вам вряд ли будет полезно. Но если оно изготовлено из алюминиевого сплава, то тут стоит подумать, как поступить с ним в дальнейшем. В принципе можно будет использовать и его, если собираетесь резать материал только по разметке. Для этого понадобится лишь сделать дополнение в виде прижимного устройства для разрезаемой заготовки.
После моей прежней публикации в комментариях создалось обсуждение этого вопроса. Но, к сожалению, в диалоге по больной теме, приняли активное участие всего два пользователя сообщества. В частности пользователь 1essor1, предложил еще два варианта девайсов как кандидатов на рассмотрение в плане использования как полуфабрикатов. Это сабельный и дисковый резаки для бумаги. Но, ознакомившись с ними ближе, пришел к выводу, что они годятся к использованию только, по прямому назначению. Хотя если кто — то захочет подтвердить или опровергнуть мои мысли на этот счет может попробовать и поэкспериментировать.
И так о конструкции.
Как я уже писал выше, за основу взят плиткорез, по своему образу и подобию. Ползун изготовлен из дюралюминия, марки Д16Т. Диаметр отверстий, соответствует диаметру штоков. В данном случае это 11 мм. Расстояние между центрами отверстий составляет 40 мм. Первоначально, просверлил отверстия сверлом, Ø 10,8 мм. Потом развернул отверстия разверткой Ø 11 мм. Крепление направляющих изготовил из стального уголка 60 × 60 × 6 мм. Правда, одну сторону уголков обрезал до ширины 20 мм. Это было необходимо для увеличения рабочей зоны резца и экономии наружных габаритов устройства.
Механизм подачи резца, простая рычажно – винтовая кинематика, на которой я не буду заострять сильно внимание. Выглядит и устроена она очень просто. В качестве винта подачи использовал обычный длинный болт с резьбой М5. Головке болта придал шаровидную форму. Шарик винта утоплен в специально сделанном углублении резцедержателя, и стопорится Г – образной пластиной с разрезом под ось болта.
Возможны и другие варианты механизмов подачи резца, лишь бы они были просты и надежны. Все зависит от ваших возможностей и познаний в механике. Очень неплоха система вертикальной подачи резца как в поперечно – строгальном станке, если кто видел или знает о чем идет речь. Но не обязательно ее делать, как говорят один в один. За основу можно взять лишь сам принцип. Для тех же, кто не знает о чем идет речь, привожу простые, но надеюсь понятные эскизы. По габаритам, такой механизм резцедержателя может быть размером примерно со спичечный коробок.
Пару эскизов резцедержателя в полуразобранном виде.
На нижних рисунках показано как может меняться положение резца при движении вперед, и при движении назад.
Для тех кому такой механизм может оказаться не под силу, могу предложить еще один вариант крепления резца, можно сказать что самый простой и примитивный.
Но и в таком случае все равно придется придумывать механизм вертикальной подачи резца, так как рычагом плиткореза контролировать глубину реза будет крайне сложно и неудобно. К тому же победитовую пластину все равно придется паять. Механическое крепление пластины в данном члучае неприемлемо из за малой толщины и хрупкости победита.
К своему великому сожалению, дать определенные размеры деталей боюсь не смогу, тут все будет зависеть от конструктивных особенностей и размеров выбранного вами устройства. Я же в данной публикации в основном делюсь самой идеей и принципом работы устройства в целом. Поэтому первоначально вам придется определиться необходимо ли вам это, и сможете ли вы самостоятельно или с чьей либо помощью изготовить такое устройство.
Если у вас, нет определенных навыков по работе с металлом, можете поступить следующим образом. В начале, изготавливаете модель. А после можете обратиться к слесарю, или какому ни будь умельцу с просьбой, в изготовлении устройства или только какой ни будь отдельной детали.
Обычно в таких случаях часто поступают так. Изготавливается модель устройства в натуральную величину из тех материалов, с которыми легче работать. Это может быть пластик, дерево, картон, металл, гипс, глина или комбинация из этих материалов. И вот когда конструктор определился окончательно с формами и размерами устройства, он переводит их, к примеру, в металл. Предлагаю попробовать, это очень удобно. Экономятся материалы и время. И порой по концовке и дешевле.
Для крепления резца в устройстве, изготовил простую оправку из стального бруска размером 16 × 16 × 10. В ней пропилил паз под резец, и сделал отверстие с резьбой для крепления в резцедержателе. После установил в паз победитовую пластинку и припаял припоем ПСр. Паял в пламени паяльной лампы. После этого уже заправил резец. Правда, с этой задачей справился не сразу. По началу, пробовал заправить на обычном сине – зеленом, мелкозернистом камне. Но оказалось, что задача эта не так проста, как кажется на первый взгляд! Но потом вспомнил, что у меня есть алмазный круг. На алмазе вся процедура по приданию необходимой формы заняла всего пару минут. Угол заточки резца выбрал около 20 градусов.
После сборки устройства в черновом варианте провел несколько пробных резов и, убедившись в работоспособности устройства, взялся за дальнейшее его развитие.
Приобрел две стальные линейки, алюминиевый уголок и пару брусков дюраля, коллега по работе подкинул два длинных каленых и шлифованных стержня Ø 8 мм от КПП автомобиля Volkswagen. Из всего этого сделал подвижный упор. Теперь можно нарезать материал по упору, минуя разметку.
Так же стало возможным разрезать уже готовые протравленные платы, а так же групповые заготовки плат без риска их испортить. Правда, такой возможности пока еще не представилось, но думаю, что в этом плане проблем быть не должно. В качестве резки можете убедиться, рез ровный, равномерный и чистый. Сам процесс резки материала стал теперь в разы легче, и перестал быть утомительным. В процессе резки, каретка движется вперед усилием большого пальца, назад усилием среднего, а подъем и опускание резца (вращение винта подачи резца), указательным. Четыре – шесть движений резцом вперед – назад с одной стороны и столько же с другой, и готово. Ширина реза составляет около 0.5 мм, в зависимости от глубины надреза, и благодаря клиновидной форме углубления в месте надреза, материал разламывается очень легко.
Во время конструирования появилась идея оборудовать устройство лазерной меткой. Впоследствии, меня чутье не обмануло, данное дополнение оказалось весьма полезным и удобным при вырезании прямолинейных отверстий в заготовках и резке по разметке.
Заинтересовался темой преобразования лазерного пучка в линию, Порылся в интернете и кое – что нашел на этот счет. В общем, вариантов существует немало, но доступных для своих возможностей выбрал поначалу два. Первый, казалось самый простой это преобразование точки в линию с помощью цилиндрической линзы, мне не сильно понравился. Линия получалась несколько выпуклой посередине. Кроме того проекция получалась на достаточном удалении от источника света, что меня не устраивало в принципе. Вероятно все же возможно получить необходимый результат, но полагаю, что это потребует построения более сложной оптической системы.
Кое – что полезное на этот счет почерпнул отсюда.
И тогда пошел по запасному маршруту и поэкспериментировал с механической разверткой луча.
И вот тут – то я понял, что это оно. За неделю удалось изготовить из того что было и как умел устройство с механической разверткой луча.
Для этого использовал электродвигатель от DVD плеера, питанием в 3.0 V с насаженным на вал зеркалом и ПП лазер от фонарика – указки. Получилось довольно компактно, если не считать батарейный отсек, который занял две трети длины устройства. Но надеюсь, что от этого недостатка вскоре избавлюсь. Думаю приспособить зарядку от мобильного телефона в качестве сетевого блока питания.
Все устройство изготовлено из дюралюминия марки Д16Т на обычном настольно – сверлильном станке. При изготовлении деталей к примеру на фрезерном станке думаю хватило бы и двух, максимум, трех часов. Отверстие для движка просверлил обычным пером для сверления древесины. Сверло сточил до размера диаметра двигателя 24.5 мм, сверление проводил на малых оборотах с применением СОЖ (смазывающей охлаждающей жидкости). В качестве СОЖ использовалась обычная отработанная тормозная жидкость. Немогу объяснить почему, но с ней чистота отверстий при сверлении получается гораздо лучше чем в сравнении скажем с водо – масляными эмульсиями.
С зеркалом получилось тоже интересно. Обычное простое зеркало не подходило, потому что получалось двойное отражение луча, от поверхности стекла, и от амальгамы. Причем чем тоньше стекло, тем ближе сходились световые пучки. Экспериментировал с различными материалами и предметами. В общем, со всем, что попадалось под руку и на глаза. Все было не то и не так. Помог случай. Купил не барахолке, тонкое зеркальце от косметички. Когда отделил зеркало от основы, то на обратной стороне обнаружил остатки клея. Решил смыть клей растворителем, но вместе с клеем постепенно стал смываться и защитный слой. Осталась только амальгама, как раз то, что мне было необходимо. А дальше все просто, надфилем зашершавел торец пластикового шкива от этого движка и приклеил к нему отрезок полоски из латунной жести, которую согнул под угол в 45°. К другой плоскости приклеил маленький квадратик зеркальца. Немного потрудился с фокусировкой луча и получил искомый результат. ПП лазер использовал от обычного фонарика – указки, мощностью около 5 mW. До этого в своих опытах использовал фонарик с ПП лазером мощностью около 1 mW.
А теперь немного о том, как все это работает и выглядит.
К примеру, необходимо сделать в плате отверстие прямоугольной формы. Для начала, по углам будущего выреза сверлим отверстия. Это необходимо для начала захода резца в материал.
Далее устанавливаем заготовку по метке в устройстве и фиксируем прижимными винтами. Торцам винтов специально придал коническую форму. Это необходимо для того чтобы при вращении винтов заготовка не смещалась.
Углубляем резец первоначально в одном из отверстий, устанавливаем первый упор – ограничитель. Далее повторяем то же самое и со следующим отверстием и ставим второй упор. Проводим несколько раз резцом от упора к упору. И так от отверстия к отверстию с обеих сторон. Остается выдавить вырезанный фрагмент, убрать надфилем облой, и отверстие готово.
На первый взгляд может показаться, что это очень долго и нудно. Но на самом деле это не так. По времени на изготовление отверстия размером 20 × 30 мм потратил всего 10 минут. А если применить стандартную технику (сверление по контуру и опиливание) то времени требуется гораздо больше. Меня, в общем, интересовало в первую очередь, на сколько, возможна эта операция на данном устройстве. К тому же я не сильно старался, чтоб получилось очень красиво. Но как видно получается довольно неплохо. Но если все же вас заинтересует такая опция в устройстве, то тогда все же для удобства в работе лучше установить резец в передней части каретки.
Данное устройство пока что еще представляет собой экспериментальный, но уже вполне работоспособный образец. В процессе эксплуатации, я думаю, что еще придется поработать над его совершенствованием в плане добавления дополнительных опций.
И в завершение.
Если у кого – то появится здоровый интерес к данному устройству и повторит его на базе плиткореза, полагаю что было бы хорошо поделиться с народом вашим собственным вариантом конструкции.
we.easyelectronics.ru
Работаем Дремелем | Блог Евгения Дударева
Расскажу вам о том, как я открыл для себя прекрасный инструмент — Dremel.
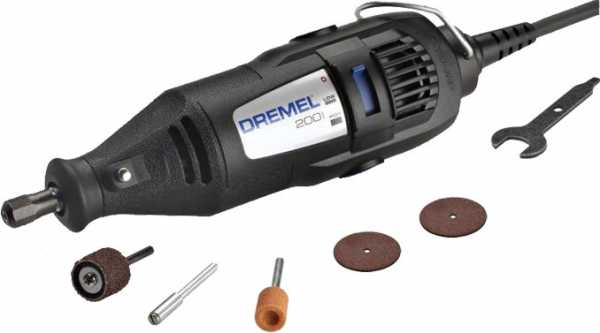
Как вы наверное уже догадались — мне периодически приходится что-то мастерить, кроить фанеру или мебельные щиты.
Раньше я использовал ножовку — хлопотно, рез не достаточно качественный.
Затем я обзавёлся электролобзиком, но рез лобзика ровным не получается, перо изгибается и всячески гуляет во время работы, обходя плотные участки, типа сучков, качественным результат тоже назвать нельзя.
Ручная циркулярная пила — оглушительна и грязь всюду, рез хоть и ровный, но очень широкий (~4-5мм выгрызает).
Вообщем, я озадачился вопросом — чем бы таким дома обзавестись, чтобы можно было не особо шумно и муторно выполнять ровный раскрой, например, фанеры.
Решение пришло не сразу, но (хвала интернету) очень меня порадовало.
Это был «гравёр» Dremel, для которого выпускается и продаётся множество разнообразных приспособлений и насадок.
К штатному комплекту пришлось приобрести вот такую насадку в виде маленький циркулярки:
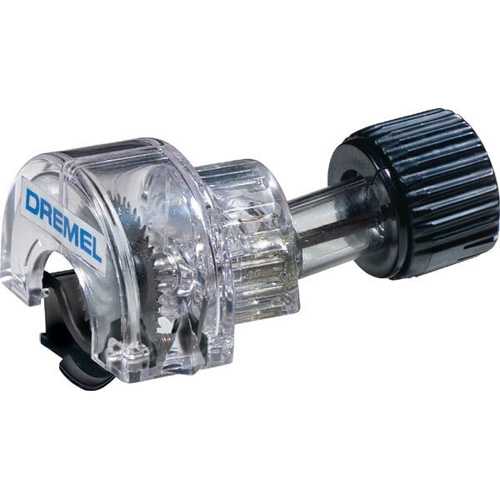
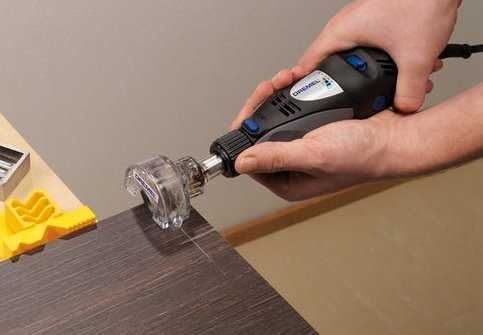
Первый же эксперимент показал очень качественный результат.
Я выпиливал несколько одинаковых деталей (для ящика) и они получились действительно одинаковыми, ни на миллиметр не отличались, все пропилы получились ровными, перпендикулярными, практически без сколов фанеры.
глубина пропила до 6.3 мм (я как раз работал с 6 мм фанерой).
Помимо этой пилки, хочется рассказать о других примочках к этому гравёру:
Перво наперво я опробовал насадку с наждачкой, которая была в комплекте
Я был поражён тем, на сколько легко на 30’000 оборотах древесина «исчезала» под этой приспособой . Шлифовать торцы, стачивать лишние миллиметры оставленные лобзиком, снять кромку — прекрасное решение.
Ещё передо мной встала задача закрепить в ванне кое что, для этого нужно было сделать несколько отверстий в керамической плитке, а за ней — в бетоне. я заранее приобрёл специальный бур по керамике, а ещё классическое «перо по керамике.
Так вот, «перо» на 30000 оборотов разогрелось до красна едва «поцарапав» поверхность плитки и развалилось (предыдущий раз я использовал перо в шуруповёрте, на малых оборотах — очень хороший инструмент для сверления плитки), а вот с дремелем — бур показал себя превосходно. глянцевый слой плитки поддался , хоть и не охотно, бетон, конечно не как «масло» но сверлился, минут за 20 я получил желаемый результат — 6 аккуратных отверстий по ~5 см в глубину, шириной по ~3 мм. Уж не знаю, из чего сделан этот бур, но он не однократно раскалялся до красна, приходилось по нескольку раз за проход остужать бур водой. После выполненых работ бур сохранил остроту своих граней. Я очень доволен.
На мой взгляд — для таких не больших работ в разы практичнее пользоваться им, чем перфоратором, разворотить дырки толщиной в палец, того и гляди расколоть плитку и напугать всех соседей ?
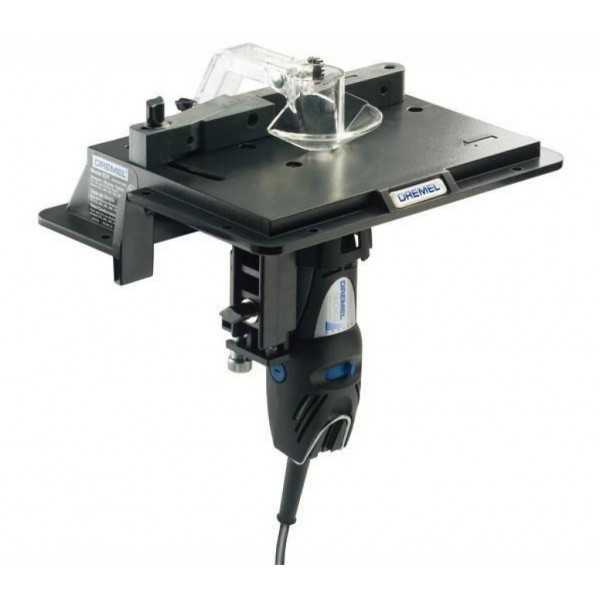
так же у этого производителя есть «фрезерный столик» Dremel 231 , с которым можно эффективно использовать несколько насадок — фрезы, наждак, и т.д.
С фрезами я ещё не поработал, но уже представляю какими и что можно получить в результате. с наждаком можно кромку выровнять и качественно обработать. очень удобно.
Заказал на Ebay несколько наборов — диски по металлу, гравёры, предметы для полировки, и прочее. так что будут ещё рассказы о том, какой полезный девайс для меня оказался этот чудо гравёр.
dudarev-art.ru
Резка пенопласта в домашних условиях без крошки и покусанных краев + Видео
Тем, кто задумал утеплить квартиру или новопостроенный дом своими руками, обязательно следует ознакомиться со способами, которыми осуществляется резка пенопласта в домашних условиях, ведь это один из самых популярных и доступных способов изоляции.
Особенности процесса резания пенопласта
Пенопласт – это вспененный материал и по большей части состоит из воздуха, поэтому он очень легкий и с ним просто работать. Однако не стоит думать, что никаких проблем не возникает, ведь кроме всего пенопласт и довольно хрупкий материл. Поэтому если воспользоваться электрической болгаркой, то на ровные края надеяться не стоит, к тому же все помещение и площадка будет усыпана раскрошенным пенопластом.
Каким бы острым ни был нож, материал все равно будет крошиться. Безусловно, это незначительный дефект и листы будут пригодны к использованию, а вот уборка превратится в хлопотное мероприятие. Из такого положения есть выход, вы можете воспользоваться термоножом. При этом края материала оплавляются и он не крошится. Но вот незадача, стоит такое приспособление очень много, но в принципе можно нагреть и обыкновенный нож. Однако в этом случае надо быть весьма аккуратным, чтобы не получить ожога, да и работа существенно затянется.
Способы разрезания листов
Для этой цели можно воспользоваться различным режущим инструментом, например, болгаркой, только тогда следует использовать самый тонкий диск. Очень часто строители пользуются и простым острым ножом. Иногда советуют брать и ножовку с очень мелкими зубьями, но последний метод весьма сомнительный. Кроме того, в магазинах продают специальные термоножи, предназначенные для работ с пенопластом.
Термонож нагревается до 600 °С всего за 10 секунд. Однако этот инструмент довольно дорогостоящий, поэтому далеко не всегда есть смысл покупать его.
Выходом же из положения во многих случаях станет приспособление для резки листов пенопласта, сделанное самостоятельно. Вероятно, оно несколько громоздкое, зато при наличии необходимых компонентов абсолютно бесплатное и всегда доступное. А если вам придется заниматься масштабной работой, например, у вас впереди утепление огромного дома, который вы возвели для своей большой семьи, то вопрос, как удобно разрезать пенопласт, да еще много и быстро, не всплывет на протяжении всего мероприятия, насколько бы оно ни затянулось.
Для того чтобы собрать резак для пенопласта, понадобится столешница, по паре пружин, винтов М4 и стоек длиной в 28 мм, а также нихромовая нить, которая и будет выступать в качестве режущего инструмента. Сначала делаем в основании два отверстия, запрессовываем в них стойки, а у основания шляпки винта пропиливаем небольшую канавку, благодаря которой нить будет надежно фиксироваться в заданном положении.
Когда все собрано, крепим к винтам струну, но так как она может провисать во время нагревания, следует соединять ее через пружины, тогда нить будет всегда находиться в натянутом положении. Источник же питания подсоединяется к такому приспособлению посредством обыкновенных скруток. Так можно сделать самодельный и очень эффективный резак для пенопласта, при этом затратив минимум сил, времени и денег.
Пробуем разрезать пенопласт самостоятельно
Теперь немного поговорим о различных технологиях, методах и, конечно же, приведем подробную инструкцию, что и как делать.
Как самостоятельно разрезать пенопласт — пошаговая схема
Шаг 1: Подготовительные работы
Неважно, каким именно инструментом вы собираетесь пользоваться – ножом, нихромовой нитью либо же иными режущими приспособлениями, все равно начинать необходимо с разметки. Так что берем линейку, угольник, рулетку, карандаш и наносим на поверхности листа отметки, затем соединяем их в линии. В общем, рисуем контуры будущего разреза.
Шаг 2: Непосредственно резка
Здесь уже все зависит от выбранного способа и, естественно, инструмента. Итак, если нет желания возиться с разными установками, то вполне можно воспользоваться простым строительным ножом, главное, чтобы он был хорошо заточен. В этом случае прикладываем к отмеченной линии линейку, зажимаем ее и делаем рез ножом. Но только не переусердствуйте, разрез должен быть неглубоким, тогда лист не будет крошиться. Затем переворачиваем панель и с другой стороны делаем аналогичный надрез. Все движения производятся «от себя». После этого просто ломаем лист в нужном месте.
Есть и еще способы, как можно порезать пенопласт. Например, с использованием нихромовой нити. В этом случае на нее подается небольшой ток, который способен раскалить струну до нужной температуры, и резка аккуратно производится по заданному контуру. Безусловно, качество реза в этом случае получится значительно лучше, однако немного придется потрудиться, чтобы сделать станок. Поэтому данный метод не всегда оправдывается, если вам необходимо обработать всего несколько листов, просто нет смысла тратить время на конструирование приспособления. Как видим, нельзя дать однозначного ответа, чем же лучше резать пенопласт, все зависит от объемов и навыков.
remoskop.ru
Мини-циркулярная пила/фреза из Дремеля своими руками
В этой статье вы найдете описание того, как превратить своими руками многофункциональный инструмент Дремель в мини-циркулярную пилу и фрезу по дереву.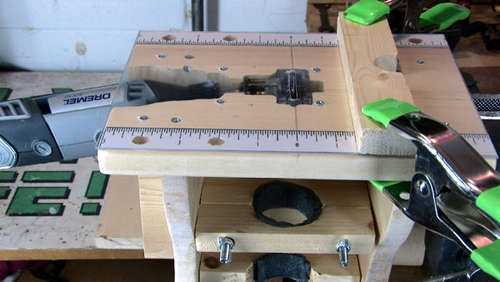
Скачайте прикрепленный PDF-файл, содержащий в себе описание всего проекта и чертежи. К сожалению, документ содержит текст полностью на английском языке, но при помощи данной статьи разобраться в нем не составит труда. При распечатке убедитесь, что в меню Print в пункте Page Scaling стоит None.
Что же нам понадобится?
Естественно, сам Дремель. В нашем случае, это модель 4000-5/36H. Это одно из лучших предложений – за 100 долларов вы получите, помимо самого инструмента, еще 5 приспособлений и 36 принадлежностей к нему.
Из материалов нам понадобятся:
Отрезок доски 2,5х20х120 см – 1 шт.
Отрезок доски 2,5х5х120 см – 1 шт.
Лист оргстекла 20х25 см (толщина – 2 мм) – 2 шт.
Хомуты для крепления труб (диаметром 2 см) – 4 шт.
Болты 1/4”x4-1/2” – 2 шт.
Гайки барашковые 1/4” – 4 шт.
Изоляция для труб (толщиной 2 см) – отрезок 1,8 м
Шурупы 6×1-1/2” — 20 шт.
Шурупы 4×5/8” – 12 шт.
Пружинные зажимы – 2 шт.
Список инструментов:
Дремель (чертежи были разработаны для модели 4000, но могут быть изменены для любой другой модели)
Мини-пила – принадлежность для Дремеля (модель 670)
Шлифовальный барабан для Дремеля ( подойдут модели 407 или 479)
Сверло 4 мм
Сверло 2 мм
Сверло 2,5 мм
Сверло 6 мм
Отвертка
Клей
Острый нож
Распилим доски на отрезки требуемой нам длины. Это можно сделать на месте покупки, если там есть соответствующее оборудование (циркулярная пила). Это сэкономит ваше время и обеспечит ровную поверхность реза.
Из доски 2,5х20х120 см:
Длина 25 см — 2 шт. (рабочая поверхность и опорная доска)
Длина 10 см – 2 шт. (правая и левая боковые панели)
Из доски 2,5х5х120 см:
Длина 14 см — 4 шт. (две скобки зажима и две подпорки)
Приступим к выпиливанию и сверлению рабочей поверхности стола и опорной доски (основания).
Когда все доски у вас нарезаны в длину, распечатайте шаблоны и просмотрите их. Для достижения наилучших результатов распечатайте их на бумаге плотностью 270 г/м².
Начав с шаблона рабочей поверхности, вы обнаружите жирный контур, блеклые пунктирные линии, расположение нескольких высверленных отверстий и жирную пунктирную линию, обозначающую вырез под дремель с насаженной мини-циркулярной пилой. Также есть блеклая сплошная черта, которая обозначает расположение хомута, который будет закреплен под мини-пилой. Блеклые линии на любом из шаблонов обозначают элементы на противоположной от наблюдателя стороне детали. Вырежьте шаблон по жирному контуру и, затем, сделайте вырез под дремель вдоль пунктирной линии. Возьмите одну из деревянных панелей длиной 25 см (из доски 2,5х20 см) – это будет рабочая (верхняя) поверхность стола, и положите на нее шаблон.
Закрепите его скотчем или просто удерживайте на месте в то время, как обводите по шаблону вырез под дремель с мини-пилой. С помощью керна, гвоздя или отвертки наметьте места сверления отверстий. Сделайте углубление на поверхности доски для облегчения стабилизации сверла в нужном месте.
Зафиксируйте доску и выпилите отмеченную вами область, используя дремель и многофункциональный отрезной комплект или фрезу.
Если у вас нет этих дополнительных насадок для дремеля, используйте лобзик или другие инструменты для резки дерева. Шаблон был разработан таким образом, чтобы дремель с мини-циркулярной пилой плотно прилегал к краям выреза. Поэтому обрабатывайте края только до тех пор, пока он не начнет проскальзывать в прорезь на рабочей поверхности стола.
Когда вы закончите выпиливание, приступите к сверлению отверстий соответствующими сверлами (они обозначены на шаблоне). Заметим, что если вы планируете применять при работе над этим проектом лишь дремель и аксессуары для него, вам понадобится набор для сверления и зенкерования отверстий.
Подсказка – если у вас нет доступа к сверлильному станку, чтобы рассверлить отверстия под шурупы, используйте на нужную глубину сверло 6 мм, а затем продолжите сверление отверстия нужным сверлом меньшего диаметра.
Используя эти советы, обработайте опорную доску. С тем лишь отличием, что при работе с ней не надо будет выпиливать сложные контуры или обрезать что-то – нужно только просверлить отверстия.
Боковые панели уже обрезаны в тот размер, который необходим нам для дальнейшей работы. Тем не менее, вы можете заметить, что на шаблоне начерчена линия декоративного фигурного отреза. Вы можете воспользоваться ею, если хотите, чтобы ваш столик выглядел более изящно. Внизу страницы с шаблоном боковых панелей вы обнаружите то, что я называю «шаблоном контура». Он относится только к левой стороне. Правая боковая панель не требует никаких дополнительных вырезов или правок деревообрабатывающими инструментами.
Вырежьте этот шаблон по контуру, затем внутри него вырежьте участок, ограниченный пунктирной линией. Согните его вдоль прямых пунктирных линий и приложите его на торцевую поверхность левой боковой панели. Убедитесь, что сторона шаблона, обозначенная как «Внешняя поверхность», находится на той поверхности панели, которую вы хотите видеть снаружи (продиктовано тем соображением, что обычно одна из поверхностей доски выглядит лучше, чем другая).
Обведите контур и с помощью дремеля обрабатывайте доску до тех пор, пока прорезь не примет очертания линии. Не надо слишком тщательно зачищать вырез на этом этапе. Сейчас надо просто приблизительно придать нужные очертания вырезу, а позже вы сможете заняться идеальной подгонкой.
Этот вырез будет опоясывать корпус дремеля и помогать зафиксировать его в рабочем положении. Если дремель у вас другой модели, вам придется подогнать вырез под очертания вашего инструмента. Для работы с белой древесиной для данной операции подойдет шлифовальный барабан. Если вы захотите использовать древесину более твердых пород, для этого этапа работ вам понадобятся другие аксессуары для дремеля.
У нас есть две скобки зажима и две подпорки. Две скобки зафиксируют инструмент, а верхняя и нижняя подпорки предохранят его от движения в то время, когда вы будете прикладывать усилие на заготовку при ее обработке.
Выполните ту же операцию для этих четырех частей, что и при вырезании контура под инструмент на левой боковой панели.
При сверлении отверстий диаметром 6 мм в скобках зажима убедитесь, что они точно соответствуют таким же отверстиям, которые были просверлены ранее в нижней опорной панели. Для большей точности вы можете сначала приставить их на соответствующие им места и отметить места сверления сквозь отверстия в опорной панели. Помните правило – «семь раз отмерь, один отрежь», в нашем случае – просверли. На данном этапе рекомендуется воспользоваться сверлильным станком. Если у вас нет возможности им воспользоваться, начинайте сверлить тонким сверлом, убедившись в точности выравнивания. После чего постепенно наращивая диаметр сверла, шаг за шагом расширяйте отверстие до требуемого диаметра.
Теперь, когда все детали выпилены, просверлены и приняли нужную нам форму, пришло время собрать их в одно целое.
Используя шурупы 6×1-1/2”, прикрутите к опорной доске боковые панели, нижнюю и верхнюю подпорки.
Предварительно просверлите направляющие отверстия, чтобы предотвратить расщепление древесины (сверло 2 мм хорошо подойдет для этого). Прежде, чем установить на место рабочую (верхнюю) поверхность стола, необходимо присоединить к ней хомут для труб (на нижней ее поверхности), используя шурупы 4 x 5/8”.
Отверстия для них были высверлены заранее и центр хомута должен точно совпадать с вырезом под мини-пилу для дремеля.
Когда вы перевернете рабочую верхнюю панель и попытаетесь установить ее на место, то обнаружите, что хомут не позволяет установить ее горизонтально. Хомут упирается в нижнюю панель. Самым простым решением является использование шлифовального барабана для проделывания выемки под хомут.
После этой операции прикрутите рабочую панель на ее место.
Заметим, что если вы попытаетесь установить на место дремель с мини-пилой, то пила не будет находиться на одном уровне с рабочей поверхностью.
Отрежьте кусок изоляции для труб длиной 5,5 см. Сожмите его, затем изогните, чтобы он приобрел очертания улыбки.
Поместите этот отрезок в полость выреза для мини-циркулярной пилы в рабочей панели выгнутой стороной вниз.
Теперь, когда вы разместите в вырезе дремель с пилой, вам нужно будет немного надавливать на него вниз, чтобы он был на уровне с рабочей поверхностью.
Теперь немного вернемся назад и закончим выемку под дремель на левой боковой панели. Установите дремель с пилой на место (выключатель должен располагаться сверху). Зафиксируйте инструмент, убедившись в том, что мини-пила находится на одном уровне со столом, и заметьте, на каком уровне располагается сам дермель относительно стола. Используя шлифовальный барабан, обработайте выемку на левой панели и снова приложите инструмент для проверки. Шлифуйте и проверяйте до тех пор, пока инструмент не будет располагаться чуть ниже поверхности. Вам потребуется повторить эту операцию и для скобок и подпорок для центровки инструмента в вертикальном положении. Потребуется срезать лишь такой контур, чтобы хватило места для того, чтобы наклеить отрезки изоляции для труб там, где будет находиться дремель.
При использовании станка в качестве мини-циркулярной пилы покрытие из оргстекла служит для удержания инструмента на месте. Листы оргстекла имеют размеры 20х25 см, поэтому их необходимо обрезать так, чтобы они соответствовали размерам рабочей поверхности.
Для этого отмерьте и обозначьте линию на поверхности оргстекла, после чего проведите по ней ножом, оставляя глубокую борозду.
Положите лист на край стола или доски и отломите по этой борозде лишнее. Теперь, когда мы имеем оргстекло нужного нам размера, можно приступать к изготовлению покрытия для рабочей поверхности в соответствии с шаблоном.
Для изготовления предохранительного кожуха воспользуйтесь теми же инструкциями, что и для изготовления скобок зажима и подпорок.
Одна сторона кожуха может использоваться при работе в качестве мини-циркулярной пилы, другая – при работе в качестве фрезы по дереву. Надеемся, что данный станок сделанный из дремеля своими руками поможет вам при работе над вашими проектами и даст новый толчок развития вашему хобби.
По материалам www.instructables.com
electronics-lab.ru