Как изготавливаются плиты ДСП — информационная статья от компании Новатор
Древесно-стружечная плита – это материал, в состав которого входит несколько видов древесины. Этот вид плит изготавливают из отходов дерева: стружек либо опилок, которые связываются при помощи специальных компонентов, а затем соединяются горячим прессом. Производители используют разные породы древесины, которые входят в состав ДСП, и от этого зависит не только качество, но и цена на материал. Изготавливать этот стройматериал стали в середине 20-го века для производства мебели.
На сегодняшний день, мебельное производство ДСП является одним из самых популярных в деревообрабатывающей промышленности. Его применяют как в строительстве, так и для производства элементов домашнего интерьера. Является экономным стройматериалом, который не требует сложной обработки.
Все производители изготавливают плиты ДСП с использованием одной технологии, однако в состав входят разные виды древесины.
Стадии изготовления
Весь процесс изготовления древесно-стружечного сырья можно условно разделить на несколько стадий:
- Сбор необходимых компонентов. На этом этапе подбирают и смешивают разные виды древесины, от которых будет зависеть качество и цена полученного ДСП. Для изготовления ДСП плиты производство используются щепки, опилки или древесная стружка.
- Дробление древесины. На этом этапе сырье нужно раздробить до необходимого размера и придать всем компонентом однородную массу. Делается это для того, чтобы готовая плита имела необходимую прочность.
- Сушка древесины. После дробления, из древесины нужно удалить избыточную влагу. Это необходимо сделать для того, чтобы в последующем материал можно было склеить. Удаляется влага в основном методом высушивания.
- Объединение элементов. Когда древесина измельчена, высушена и полностью подготовлена, ее основательно смешивают с клеящей основой. После этой процедуры появляется однородная масса, из которой производят древесно-стружечные плиты.
- Придание формы. Перемешанная с древесиной клеящая основа помещается на специальную подвижную ленту, которая имеет определенные размеры. Далее эту массу спрессовывают до необходимых габаритов. Весь процесс прессовки материала проводится под высокими температурами.
- Распил. Готовый материал распиливают до необходимых габаритов и делают дополнительную процедуру высушивания.
- Процесс обработки.
Эта стадия является завершающей. На ней происходит процесс обработки готового материала на линии производства ДСП: на поверхность материала наносится один тонкий слой бесцветного компонента (ламинирование), а вторым слоем наносят шпон. Для таких плит используют специализированную пленку, которая накладывается поверх материала. Для дополнительной обработки могут применить бумагу либо пластик. Стоимость изготовление плит ДСП не большая, но их цена многократно выше, чем у отшлифованных древесно-стружечных плит.
Производство ДСП оказывается весьма прибыльным при наличии дешевого исходного сырья
На сегодняшний день производство ДСП является весьма выгодным направлением деятельности, поскольку этот практичный, экономичный и легкий в обработке материал широко востребован среди широкого круга потребителей. Особым спросом ДСП пользуется у предприятий, занимающихся мебельным производством или строительством – из него изготавливают мебель, стеновые панели, полы, перегородки, а также используют для обшивки стен, крыш или декорирования интерьеров. Древесно-стружечные плиты успешно заменяют массив дерева, и практически ничем не уступая ему по внешнему виду, имеют более низкую стоимость.
Исходным сырьем для производства этого материала выступают отходы деревообработки и лесопиления, которые на специальных станках измельчают до состояния стружки, а затем склеивают термопрессом, добавляя связующее вещество. Обычно хорошие бревна в процессе производства ДСП почти не используются, что никак не влияет качество готового материала. Даже используя древесину малоценных пород, щепы, опилки, сучья, горбыли, мелкие ветки, на выходе получают плиты с отличными эксплуатационными характеристиками, а прочность и долговечность материала удается повысить с помощью антисептических и других добавок.
Технологии и оборудование для производства ДСП
Процесс производства ДСП плит включает в себя несколько этапов. Если используется круглая низкокачественная древесина, то на подготовительном этапе её очищают от коры, распиливают на части и помещают в бассейн с водой, где осуществляется гидротермическая обработка деревянного материала. После этого чурки отправляются на станки с ножевым валом, которые превращают их в стружку, нарезая параллельно древесным волокнам. Другой способ получения стружки – из щепы.
Подготовительный цех оснащается рубильными машинами и стружечными станками, которые и позволяют получать технологическую щепу, необходимую для дальнейшего производства ДВП и ДСП. Необходимо помнить о том, что качество склеивания ДСП напрямую зависит от формы и размера стружки, которые задаются заранее. Дело в том, что древесно-стружечная плита обычно состоит из трех слоев: для среднего слоя используется более крупная фракция, для наружных – мелкая стружка.
Мягкая стружка, имеющая небольшую толщину, более эластичная и лучше прессуется. Кроме того, сечение стружки не должно быть квадратным, в противном случае физико-механические характеристики древесно-стружечной плиты резко снижаются. Кстати, для большинства линий по производству ДСП, собранных еще в советское время, проблема «квадратной стружки» стоит очень остро. Современное оборудование для производства ДСП позволяет изготавливать однослойные плиты, с более равномерным распределением стружки – от более крупной в середине, до мелкой – по краям.
После стружечного станка материал попадает на дробилку, где уменьшается его ширина, или на молотковую мельницу, благодаря чему стружка становится более тонкой и гладкой. Особенно важна последняя операция для производства ламинированного ДСП, качество которого несколько выше, чем обычного. Поскольку крупную и мелкую щепу необходимо обрабатывать с разной скоростью, измельчение разных фракций происходит раздельно. Далее измельченная до нужного размера стружка собирается в бункеры.
Для хранения сырой стружки используют специальные бункеры, из которых механическими или пневмотранспортерами она подается на сушилки. Сушат материал до тех пор, пока его влажность не достигнет 4-6% для внешних слоев и 2-4% для внутреннего. Сушилки представляют собой конвективные агрегаты, как правило, барабанного типа, работающие на газе или мазуте. Температура в топке может доходить до 900 — 1000°, на выходе же она значительно ниже – 90 — 120°. Поднятые горячим воздухом частицы стружки попадают в циклонную установку – там более крупные частицы отсеиваются и возвращаются обратно на мельницу для доизмельчения.
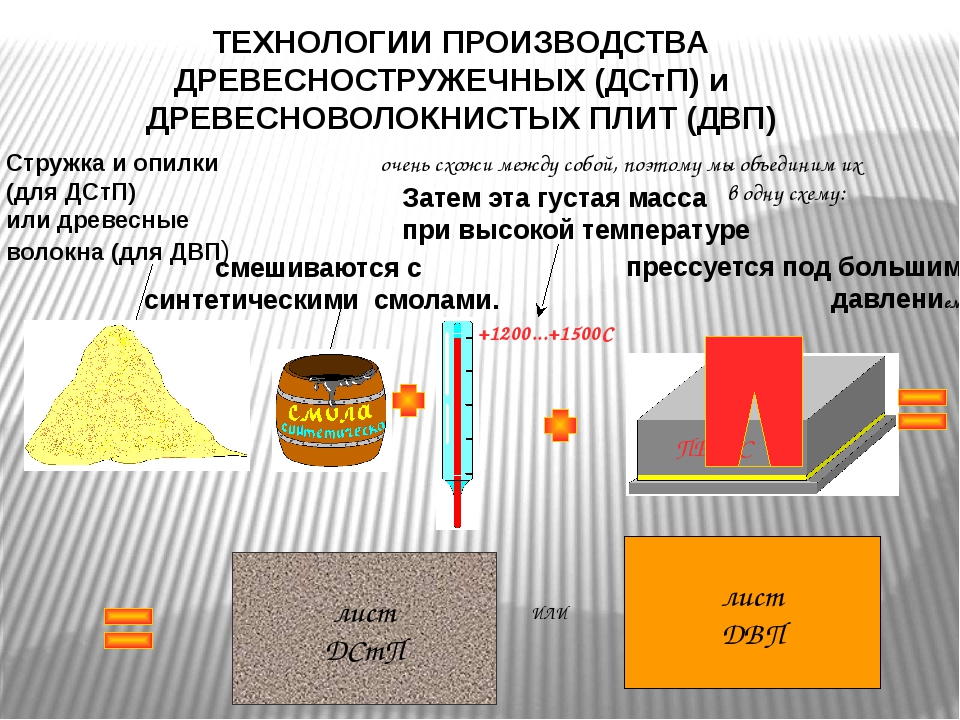
Согласно технологии производства ДСП, частицы стружки склеиваются между собой с помощью особого клеевого материала – синтетической мочевиноформальдегидной смолы. Соединение стружечной смеси со связующим составом осуществляется в смесителях непрерывного действия. Распыление клеевого состава в этих агрегатах происходит через форсунки, каждая из которых связана с дозировочным насосом. Сложность операции в том, что смолой должна быть покрыта каждая частица. При недостаточном осмолении отдельные стружки не склеиваются, а при излишнем – качество готовой плиты ухудшается, да и расход клеевого состава увеличивается.
Формирующие машины, в которые осмоленная стружка направляется ленточными или скребковыми транспортерами, укладывают материал в специальные формы – поддоны . Стружечный ковер имеет определенную ширину и толщину и при его формировании насыпка должна осуществляться равномерно.
Следующий этап – обрезка готовых плит до требуемого размера. Различают два способа обрезки – горячий и холодный. Готовые ДСП подвергают финишной обработке, в процессе которой шлифуется поверхность плиты и её торцы. Если предполагается использование ДСП в строительстве, то на этом работа заканчивается, а плиты отправляются в продажу. Если же ДСП необходимы для производства столешниц или мебели, то они должны быть облицованы различными декоративными покрытиями. Надо сказать, что в плане технологии мини производство ДСП практически ничем не отличается от производства, которое осуществляется на крупных предприятиях, основная разница – в объемах готового материала.
В России производство ДСП начало активно развиваться с середины прошло века. При этом, несмотря на появление современных технологий, часть отечественных предприятий, особенно имеющих небольшое производство,до сих пор продолжает выпускать плиты низкого качества, содержание вредных веществ в которых значительно превышает все допустимые нормы. Зарубежные заводы по производству ДСП уже давно предлагают потребителям безопасные для здоровья древесно-стружечные плиты класса «Super E», чего, к сожалению,не скажешь о нашей стране. Поэтому к покупке мебели из ДСП, особенно для детской комнаты, стоит подойти со всей серьезностью. Это именно тот случай, когда лучше переплатить, но сократить возможные негативные последствия.
Древесностружечные плиты (дсп) | Wood Products
Древесностружечные плиты изготовляются из древесной стружки и клея путем прессования. При плоском прессовании стружка обычно имеет направление параллельно поверхности.
В стандартных плитах ДСП, в качестве связующего вещества в основном используется уреаформальдегидный клей. Доля клея в плите составляет менее 10%. Многие виды продукции из плит ДСП с нанесенным поверхностным покрытием имеют классификацию степени вредности М1. Классификация плит ДСП содержит предельные показатели эмиссии вредных веществ строительных материалов, предназначенных для внутренних помещений и их классификацию. В класс М1 входят материалы, прошедшие тестирование на эмиссию вредных веществ с их содержанием ниже предельных норм.
По своим основным техническим характеристиками плиты ДСП сравнимы с деревом. При этом они имеют ряд преимуществ, связанных с особенностями изготовления :
- нет четкого направления волокон
- плита имеет равномерную структуру по всей площади и, поэтому, во всех частях плиты показатели прочности одинаковы
- поверхность плиты почти не подвержена деформации
Плотность плит ДСП колеблется в пределах от 650 до 750 кг/м3, что гораздо выше плотности хвойных пород дерева и, поэтому, плиты тяжелее хвойной древесины.
КЛАССИФИКАЦИЯ ПЛИТ ДСП ПО КАЧЕСТВУ
Lastulevyt luokitellaan seitsemään eri luokkaan ominaisuuksiensa perusteella. Lastulevyluokkien ominaisuude määritetään yleiseurooppalaisen standardin SFS-EN 312 mukaisesti. Lastulevyluokka ilmoitetaan P-kirjaimella ja numerolla.
Lastulevystandardit eivät aseta vaatimuksia levyn pinnan laadulle, mutta valmistajat lajittelevat levyt ulkonäön perusteella A- ja B-laatuun. Pinnan laadun määrittelyssä huomioon otettavia tekijöitä ovat esimerkiksi hionnan laatu, pinnan tasaisuus, pinnan puhtaus ja reunaviat.
По своим характеристикам плиты ДСП подразделяются на семь классов согласно европейскому стандарту SFS-EN 312. Классы плит ДСП отмечаются литерой «P» и цифрой.
В системе стандартизации плит ДСП нет требований к качеству поверхности плит, но производители классифицируют плиты по внешнему виду на классы А и B. При определении качества плиты по внешнему виду учитываются качество шлифовки, ровность и чистота поверхности, а также наличие дефектов по краям плит.
Класс | Назначение | Класс применения |
---|---|---|
P1 | Стройматериал для внутренних помещений | 1 |
P2 | Материал для изготовления мебели для внутренних помещений | 1 |
P3 | Для ненесущих конструкций, с требованиями улучшенной влагостойкости по сравнению со стандартными плитами | 2 |
P4 | Для внутренних помещений, с требованиями устойчивости к нагрузкам | 1 |
P5 | Для объектов с требованиями устойчивости к нагрузкам и с улучшенной влагостойкостью по сравнению со стандартными плитами | 2 |
P6 | Для напольных плит, выдерживающих большие нагрузки с использованием во внутренних помещениях | 1 |
P7 | Для объектов с большими нагрузками, с требованиями улучшенной влагостойкости по сравнению со стандартными плитами | 2 |
Стандартные плиты ДСП без обработки поверхности применяются для производства мебели, а также в строительстве. Плиты ДСП классов P3, P5 и P7 покрывают клеем и меламином, что значительно улучшает их влагостойкость.
ИЗДЕЛИЯ ИЗ ДСП
Изделия из плит ДСП обычно имеют точное целевое назначение. В зависимости от этого плиты проходят дальнейшую обработку и на их поверхность наносится покрытие.Плиты из ДСП облицовывают саыми различными материалами, например, натуральным шпоном, меламиновой пленкой, ламинатом, пластиковой пленкой, бумагой и т.п. Обычно поверхность плиты облицовывается с обеих сторон во избежание ее деформации. Плиты ДСП выпускаются также в окрашенном виде (плиты, окрашенные грунтовой краской на фабрике или с покрытием из бумаги с пропиткой). Огнеупорность плит ДСП может быть повышена путем нанесения грунтовки на алкидной основе или покрытия из меламиновой пленки.
Плиты ДСП с нанесенным на поверхность покрытием или грунтовкой используются практически для тех же назначений, что и стандартные плиты. Помимо улучшения внешнего вида плиты, покрытие повышает также ее прочность и жесткость. Самым распространенным покрытием для плит ДСП является меламиновая пленка. Шпунтовые плиты ДСП используются для внутренней облицовки стен, потолка и пола.
Шпунтовые плиты ДСП для облицовки стен и потолка выпускаются стандартных размеров: 600 x 2600/2750 мм и 1200 x 2600/2750 мм при толщине плиты 12 мм. Обычно шпунтовые выступы и пазы находятся на длинных сторонах плит. Плиты поставляются в окрашенном виде.
Плиты для пола имеют шпунты со всех сторон. Плиты для пола выпускаются стандартных размеров: 600 x 2400 мм и 1200 x 2400 мм при толщине 22 мм.
САМЫЕ РАСПРОСТРАНЕННЫЕ ОБЛАСТИ ПРИМЕНЕНИЯ ПЛИТ ДСП В СТРОИТЕЛЬСТВЕ
По своим пожаротехническим свойствам плиты ДСП являются сгораемым строительным материалом. По классификации пожарной безопасности плиты без покрытия относятся к классу возгораемости D—s2, d2, а плиты с покрытием (с гладкой поверхностью) – к классу C—s2, d1.
ПОЛЫ
Перед установкой на место плиты ДСП выдерживаются от 5 до 7 суток в условиях, максимально приближенных к эксплуатационным. Укладка плит должна проводиться при температуре и влажности, близких к эксплуатационным.Полы из ДСП
При устройстве полов из плит ДСП, шпунтованные по периметру плиты (обычно толщиной 22 мм) настилают на деревянные лаги/балки нижнего или межэтажного перекрытия. Промежутки между лагами не должны превышать 600 мм. Плиты укладываются в поперечном направлении длинных сторон к лагам. Короткие стороны плит и стыки смежных плит накладываются на лаги. Плиты крепятся к каждой лаге/балке шурупами или гвоздями, а также клеем. При этом плиты приклеиваются в шпунтовых стыках к смежным плитам. Между крайними плитами пола и стеной, а также другими конструкциями оставляется зазор в 10 мм. При укладке плит следует соблюдать следующие указания:
- плиты крепятся к лагам оцинкованными горячим способом гвоздями с резьбовой насечкой длиной 75 мм или шурупами, длина которых в 2,5-3 раза превышает толщину плит
- шляпки гвоздей и шурупов утапливаются в пол на 2-3 мм, выемки нельзя зашпаклевывать
- промежутки между гвоздями или шурупами на краях плит должны составлять 150-200 мм, а в центральной части плиты – 250-300 мм
- при укладке плит ДСП используется клей PVAc
Плавающий пол из плит ДСП
При устройстве плавающих полов из плит ДСП, шпунтованные по периметру плиты (обычно толщиной 22 мм) настилают на изоляционный слой. Основная конструкция пола может быть деревянной или бетонной. Смежные плиты приклеиваются друг к другу в шпунтовых стыках так, чтобы между крайними плитами пола и стеной, а также другими конструкциями был зазор в 10 мм. Для обеспечения хорошего склеивания в зазоры вбиваются клинья, прижимающие плиты друг к другу. После высыхания клея клинья убирают. В качестве изоляционого материала под плиты может быть использован полистирол, полиуретан, пористые древесно-волокнистые плиты или минвата достаточной жесткости. При использовании ячеистого пластика в качестве изоляционного материала, между слоем изоляции и плитами ДСП рекомендуется проложить пластиковую пленку.
Настил другого материала на пол из ДСП
На полы из плит ДСП можно настилать обычные материалы для пола. При этом следует строго соблюдать рекомендации производителя. Сначала рекомендуется выполнить следующие подготовительные работы:
- зашлифовать неровности на поверхности плит ДСП и зашпаклевать их подходящей шпаклевкой.
При необходимости выполнить выравнивание. В случае, если на пол планируется настелить линолеум, следует провести предварительную обработку грунтовкой для лучшего склеивания поверхностей
- перед настилом покрытия пол из плит ДСП должен высохнуть до эксплутационного уровня влажности
- перед укладкой покрытия полы очищают от мусора и возможных наплывов
Бетонная стяжка на пол из плит ДСП
При устройстве комбинированного пола из плит ДСП и бетонной стяжки для нижних или межэтажных перекрытий используются шпунтованные плиты ДСП толщиной 22 мм. Они являются основой, то есть черновым полом, на который заливают стяжку из фиброцемента толщиной около 45 мм. Перед заливкой пол промазывается средством для удаления влаги и в полу закрепляются специальные гвозди для лучшей связки плит ДСП с бетоном. Благодаря такому решению получается жесткая конструкция пола с хорошей шумоизоляцией, позволяющая также устроить систему подогрева пола. К тому же, этот вариант подходит для помещений с высоким уровнем влажности, так как при заливке можно устроить уклоны для стока воды.
ВНУТРЕННЯЯ ОТДЕЛКА ПОМЕЩЕНИЙ
Плиты ДСП прекрасно подходят для отделки окрашиваемых внутренних стен и потолков. Для обшивки стен и потолков обычно применяются обычные или шпунтованные с длинных сторон плиты толщиной 10, 11 или 12 мм. Обычно края шпунтованных плит имеют фаску, поэтому на месте стыка плит получается небольшой V-образный паз. В Финляндии выпускаются плиты для отделки внутренних поверхностей окрашенные грунтовой краской или с бумажной облицовкой.
Что важно учесть при облицовке плитами ДСП:
Облицовку плитами ДСП рекомендуют делать в сухих и отапливаемых помещениях. Поскольку ДСП – материал изготовленный на основе дерева, равновесная влажность плит меняется в соответствии с изменениями влажности окружающего воздуха. Перепады влажности вызывают незначительные изменения поверхности плиты. Это свойство необходимо принять во внимание при проектировании стеновых конструкций и установке плит.
Между окрашиваемыми стеновыми или потолочными панелями из плит ДСП рекомендуется оставлять открытые зазоры шириной около 3-5 мм. В стыках между шпунтовыми плитами получается V-образный паз не требующий дальнейшей обработки. В углах помещений следует оставлять также открытый зазор шириной около 3-5 мм.
Рекомендуемые расстояния между опорами для крепления плит ДСП:
- около 300 мм при толщине плиты 6-8 мм (потолки)
- около 600 мм при толщине плиты 9-12 мм
При использовании шпунтованных плит шириной 600 мм, их следует крепить к стеновым опорам гвоздями (например, пневматическим гвоздильным пистолетом) по шпунтовому выступу, а также по нижнему и верхнему краю плиты, закрываемых плинтусами и планками. В этом случае швы между плитами не будут нуждаться в обработке и шляпки гвоздей не нужно будет шпаклевать. Плиты шириной 1200 мм крепятся также посередине (к каркасной опоре), при этом шляпки гвоздей или шурупов утапливаются в плиту примерно на 1 мм и выравниваются. Шпунтовые стыки плиты, а также соединениение между опорой и плитой укрепляются путем склеивания клеем PVAc.
ОКУПКА ПЛИТ ДСП
При заказывании плит ДСП необходимо указать следующие сведения:
- номинальную толщину плиты в мм
- размер плиты (мм x мм)
- тип плиты (например P6) и качество поверхности в зависимости от применения плиты
- при заказе облицованных плит: наименование изделия или качество облицовки обеих поверхностей, а также тип защиты кромки (или защитной планки) и цвет плиты
ХРАНЕНИЕ
На время хранения и транспортировки плиты из ДСП должны быть защищены от намокания, загрязнения, соприкосновения с землей, ударов и царапин. Плиты складываются в горизонтальном положении в кипы на ровные подставки. При необходимости в качестве прокладок используются деревянные бруски, располагаемые на расстоянии около 0,5 м друг от друга. Сверху кипа плит накрывается защитным материалом.
Перед установкой на место плиты ДСП выдерживаются от 5 до 7 суток при температуре и влажности, максимально приближенных к эксплуатационным. При этом плиты можно прислонить, например, к стене, отделив от соприкосновения друг с другом при помощи реек.
ОБРАБОТКА ПЛИТ ДСП ИНСТРУМЕНТОМ
Плиты из ДСП легко обрабатываются всеми инструментами, предназначенными для деревообработки. Для распиловки подходят, например ручная или станковая дисковая пила. Небольшие пропилы можно делать также обычной ножовкой. Для фигурного выпиливания лучше воспользоваться лобзиком.
КРЕПЛЕНИЕ ПЛИТ ДСП
Для крепления плит ДСП гвоздями, длина гвоздей должна превышать толщину плиты минимум в три раза, и составлять не менее 30 мм. Длина шурупов должна быть минимум в 2,5 раза длинее ширины плиты и составлять не менее 25 мм. Плиты крепятся по краям на расстоянии от края плиты около 10 мм, с промежутком между точками крепления около 100-200 мм , а по середине плиты — с промежутком около 200-300 мм.
ОБРАБОТКА ПОВЕРХНОСТИ
Плиты ДСП можно окрашивать, оклеивать обоями и ламинировать. Для окраски плит подходят все обычные красящие средства, предназначенные для деревянных поверхностей помещений.
Maalaus Окрашивание
Перед окончательным окрашиванием плиты ДСП с необработанной поверхностью следует покрыть одним слоем водоэмульсионной грунтовой краски белого цвета, предназначенной для помещений. Углубления от шляпок гвоздей или шурупов шпаклюются и зашлифовываются. При окончательном окрашивании краска наносится одним-двумя слоями. При использовании предварительно окрашенных плит, достаточно одной окончательной окраски. Окраску плит ДСП лучше производить валиком.
Оклеивание обоями
Углубления от шляпок гвоздей или шурупов шпаклюются и высохшая шпаклевка шлифуется. Швы между плитами выравниваются с помощю эластичной ленты. После высыхания клея стыки швов выравниваются и шлифуются. Оклеивание обоями выполняется согласно указаниям производителя. В углах следует оставлять зазор.
УТИЛИЗАЦИЯ И ПОВТОРНОЕ ИСПОЛЬЗОВАНИЕ ПЛИТ ДСП
Повторное использование плит ДСП
Если плиты ДСП б/у находятся в сухом и целом состоянии, в некоторых случаях их можно использовать повторно. Повторное использование плит ДСП предпочтительнее их выбрасыванию в отходы.
Утилизация отходов из плит ДСП
Поскольку плиты ДСП состоят в основном из чистой природной древесины, их можно уничтожать (в соответствии с указаниями местных официальных органов охраны окружающей среды) путем закапывания в землю, компостирования, вывозки на свалку или сжигания при температуре 800 °C вместе с другими деревянными отходами.
РЕКОМЕНДАЦИИ ПО ИСПОЛЬЗОВАНИЮ ПЛИТ ДСП И ПРИМЕРЫ
Плиты ДСП прекрасно подходят для собственноручного изготовления мебели и прочих поделок, сделанных своими руками. Для сборки плит обычно применяются шурупы-саморезы с потайными головками, различная сборочная фурнитура и шурупы, а также штифтовые соединения.
Для изготовления корпусной мебели из ДСП хорошо подходят плиты толщиной 15-18 мм облицованные, например, меламином. Для столешниц и поверхностных плоскостей используются плиты толщиной 22-28 мм. Для изготовления задней стенки предметов мебели можно использовать тонкий лист ДСП или оргалита толщиной 3-6 мм.
Оставшиеся на виду торцы плит покрываются подходящей ленточной накладкой, шпоном или деревянной планкой. Лучшим вариантом является использовать уже готовые, облицованные на фабрике плиты с торцовыми накладками. В случае окрашивания торцев, их нужно перед окрашиванием покрыть лентой-основой, прошпаклевать и зашлифовать.
ОБЛАСТИ ПРИМЕНЕНИЯ ПЛИТ ДСП
Строительство
- внутренняя облицовка
- конструкции полов
- бетонные опалубки
Строительная промышленность
- центральная часть двутавровых балок
- встроенная мебель
- основы под паркетные полы
- основы под декоративные накладки
Производство мебели
- каркасы мебели
Прочие сферы применения
- упаковки
- выставочные конструкции
- строительство и изготовление изделий своими руками
Технология производства плит ДСП
Для оптовых покупателей нашей компанией производится продажа ДСП. Это материал, равнопрочный по всем направлениям. Плиты ДСП не растрескиваются, устойчивы против поражения гнилью и насекомыми, доступны обработке ручным инструментом и на станках, их можно соединять на шипах, крепить шурупами и гвоздями. Широко применяются в производстве мебели. В строительстве их используют для изготовления дверных полотен, встроенной мебели, для облицовки стен и потолков, для перегородок, барьеров, панелей; ими заменяют пиломатериалы и столярные плиты.
Плиты ДСП изготавливаются из древесины для технологических нужд, а также отходов от обработки древесины: стружек, срезков, обрывков шпона, карандашей (оставшиеся после лущения части чурака). Стружку, заготовленную на специальных стружечных станках, сортируют по размерам на вибрационных ситах: пыль и мелочь направляют в котельную для сжигания, крупную щепу — на повторное дробление, а отсортированную стружку — в сушилку. В сушилке стружку высушивают до влажности 4 — 6 %, после чего она поступает в бункера-накопители с весами-дозаторами, а затем в смеситель, где перемешивается со связующим. Для предлагаемых к продаже плит ДСП, связующим служат растворы синтетических смол в количестве от 6 до 12 % веса сухой стружки.
Высокую прочность плит обеспечивают карбамидные клеи М-4 и М-60. Кроме того, они наиболее экономичны. Довольно часто для изготовления предлагаемых к продаже ДСП применяют также клеи К-17и МФС-1. Лучшим отвердителем для них служит хлористый аммоний (нашатырь).
Производство плит представляет сложный, поэтапный процесс. Из подготовленной прессмассы формуют ковер, т. е. дозируют и распределяют ее равномерно по площади стальной плиты (ленты) и предварительно подвергают уплотнению в холодном прессе. После этого подготовленный ковер поступает в горячей пресс периодического или непрерывного действия, где под влиянием тепла и давления происходит склеивание плиты. Прессование предлагаемой к продаже плиты ДСП производится при температуре 135 — 140о С и давлении 5 — 20 кг/cм2 и в зависимости от заданного объема веса плиты. Режим прессования устанавливают в зависимости от вида связующего, толщины и назначения изготовляемых плит.
Нами производится продажа ДСП, широкий ассортимент различных видов изделий. Промышленность выпускает древностружечные плиты плоского прессования, в которых стружка расположена параллельно пласти, следующих пяти марок: ПС-1 — односложные среднего веса; ПТ-1 — однослойные тяжелые; ПС-3 — трехслойные среднего веса; ПТ-3 — трехслойные тяжелые; ПТП — трехслойные тяжелые с улучшенными свойствами. Плиты ДСП этих марок выпускаются необлицованными. Нами производится продажа ДСП, изделия представлены в широком ассортименте. Кроме плоскопрессованных плит промышленность выпускает плиты экструзионного прессования с расположением стружек в плите перпендикулярно ее плоскости. Марки этих изделий: ЭС — среднего веса сплошные; ЭМ — легкие многопустотные.
Также производятся и другие виды плит. Экструзионные плиты ДСП всех марок, входящие в ассортимент предлагаемых к продаже ДСП, обычно облицовывают бумагой, лущеным или строганым шпоном. Легкие многопустотные плиты имеют во всю длину каналы круглого сечения, диаметр которых в зависимости от толщины плиты бывает от 12 до 36 мм, количество их — от 29 до 50. Экструзионные плиты разделяются на группы и сорта так же, как и плиты плоскопрессованные. Объемный вес плит обеих групп марки ЭС — от 0,55 до 0, 65; марки Эм — от 0,35 до 0,45 г/см3.
Положительные характеристики продаваемого ДСП, его физические свойства характеризуются целым рядом показателей. Водопоглощение плит происходит медленнее, чем водопоглощение натуральной древесины. Так, древесина поглощает 100% влаги в среднем за 6 суток, а стружечные плиты ДСП с объемным весом 0,7 — за 28 суток. Поверхность изделия покрывается тонкой пленкой смолы, что значительно повышает биостойкости стружки. Точно так же пленка смолы, обволакивающая стружку, затрудняет воспламенение стружечных плит, особенно в случае применения формальдегидных смол, поэтому они являются более огнестойкими по сравнению с натуральной древесиной.
Древесностружечные плиты облицовывают следующими материалами: одним слоем лущеного или строганого шпона; двумя слоями лущеного шпона или одним слоем строганого шпона с подслоем лущеного шпона; бумагой; пленкой, пропитанной синтетическими смолами; слоистым пластиком. ДСП можно облицовывать текстурной бумагой разной плотности, отделывать в дальнейшем полиэфирным лаком и применять для бытовой мебели и в других целях. Плиты, облицованные полихлорвиниловыми пленками, могут применяться в производстве мебели и в строительстве. Для медицинской кухонной и детской можно применять плиты, облицованные декоративными пленками на основе декоративных бумаг повышенной плотности, пропитанных термореактивными или совмещенными смолами.
Производство плиты дсп оптом на экспорт. ТОП 50 экспортеров плиты дсп
Продукция крупнейших заводов по изготовлению плиты дсп: сравнение цены, предпочтительных стран экспорта.
- где производят плита дсп
- ⚓ Доставка в порт (CIF/FOB)
- плита дсп цена 11.08.2021
- 🇬🇧 Supplier’s chipboard plate Russia
Страны куда осуществлялись поставки из России 2018, 2019, 2020, 2021
- 🇰🇿 КАЗАХСТАН (348)
- 🇺🇿 УЗБЕКИСТАН (234)
- 🇺🇦 УКРАИНА (94)
- 🇹🇯 ТАДЖИКИСТАН (44)
- 🇰🇬 КИРГИЗИЯ (39)
- 🇦🇿 АЗЕРБАЙДЖАН (23)
- 🇩🇪 ГЕРМАНИЯ (14)
- 🇹🇲 ТУРКМЕНИЯ (13)
- 🇲🇩 МОЛДОВА, РЕСПУБЛИКА (8)
- 🇦🇹 АВСТРИЯ (4)
- 🇱🇹 ЛИТВА (3)
- 🇨🇳 КИТАЙ (3)
- 🇦🇲 АРМЕНИЯ (3)
- 🇲🇳 МОНГОЛИЯ (2)
- 🇫🇮 ФИНЛЯНДИЯ (2)
Выбрать плиту дсп: узнать наличие, цены и купить онлайн
Крупнейшие экспортеры из России, Казахстана, Узбекистана, Белоруссии, официальные контакты компаний. Через наш сайт, вы можете отправить запрос сразу всем представителям, если вы хотите купить
плиту дсп.
🔥 Внимание: на сайте находятся все крупнейшие российские производители плиты дсп, в основном производства находятся в России. Из-за низкой себестоимости, цены ниже, чем на мировом рынке
Поставки плиты дсп оптом напрямую от завода изготовителя (Россия)
Крупнейшие заводы по производству плиты дсп
Заводы по изготовлению или производству плиты дсп находятся в центральной части России. Мы подготовили для вас список заводов из России, чтобы работать напрямую и легко можно было купить плита дсп оптом
Плиты древесно-стружечные
Изготовитель Двери и их рамы и пороги
Поставщики инструменты сменные с рабочей частью из прочих материалов
Крупнейшие производители плиты из древесно-стружечные
Экспортеры Мебель деревянная типа кухонной: мебель кухонная
Компании производители плиты из древесины необработанные или без дальнейшей обработки
Производство Плиты древесно-стружечные
Изготовитель Плиты древесно-стружечные
Поставщики Мебель деревянная типа используемой в учреждениях
Крупнейшие производители плиты
Экспортеры Части мебели из древесины
Компании производители Пилы механические дисковые
Производство инструменты для прессования
Смолы меламиновые
Древесина прессованная в виде плит
Плиты из древесины с ориентированной стружкой (osb)
Производство ДСП – изготовление плит, шпонированное
Все о шпоне и мдф -> Производство древесно-стружечных плит
ДСП – широко распространенный бюджетный конструкционный материал. Для изготовления древесно-стружечной плиты используются отходы деревообрабатывающего производства (стружки, опилки и пр. мелких частиц), которые пропитываются связующим веществом. Производство ДСП ведется путем сухого прессования в условиях высокой температуры и давления, в качестве связующего материала используются смолы. Готовое изделие в дальнейшем выделяет в окружающее пространство небольшое количество формальдегида, который считается токсичным веществом. В производстве различают две категории ДСП Е1 и ДСП Е2. ДСП категории Е1 считается более экологичным материалом, излучающим незначительное количество вредного формальдегида. ДСП Е2 по гигиеническим и санитарным нормам непригоден для производства мебели для детей. Его также не рекомендуют использовать в больших количествах в качестве отделочного материала в спальнях и в помещениях, в которых организован процесс приготовления пищи. При изготовлении ДСП существует возможность придавать готовому изделию определенные (требуемые) физико-химические свойства – введение парафиновой составляющей обеспечивает влагостойкость (для отделки или изготовления мебели для ванн, кухонь и т.
п.), введение антипиренов обеспечивает огнестойкость.
Специфика материала
ДСП отличается высокой прочностью, прочностью на изгиб и растяжение. Плиты способны на протяжении длительного времени эксплуатации удерживать на достаточном уровне такие показатели как низкий процент разбухания, коробления и деформации. Материал ДСП легко поддается механической обработке (распиловка, сверление, шлифовка и т.п.), способен надежно удерживать скрепляющую и декоративную фурнитуру, однако тонкая декоративная обработка (фигурные резные детали) для него не подходит. Кроме вышеперечисленных достоинств популярного и востребованного материала, плиты ДСП выгодно отличается низкой стоимостью.
Особенности цвета и поверхности
Для придания высоких эстетических характеристик, ДСП подвергают дополнительной обработке – облицовка бумагой, полимерной пленкой, пластиком и шпоном (шпонированное ДСП).
Ламинированное ДСП получают путем специальной технологии. Бумажная основа пропитывается меламиновыми смолами, после чего при помощи пресса надежно присоединяется к поверхности ДСП. Кроме самых разнообразных имитаций фактур (натуральное дерево, камень, кожа и пр.), оттенков и цветов, ламинированные ДСП отличаются высокой устойчивостью к механическим и термическим повреждениям. Ламинированное ДСП выгодно отличается от кашированного ДСП (менее низкие показатели по устойчивости), у которого со временем защитное покрытие отслаивается.
Шпонированное ДСП производится путем нанесения натурального шпона ценных пород с последующим прессованием. После прессования поверхность поддается двойной шлифовке (грубой и тонкой) и обработке кромки. Благодаря отделке натуральным шпоном, полученный материал приобретает благородный изысканный внешний вид. Шпонированное ДСП используется в отделке помещений (стеновые панели, потолки, полы, перегородки) для производства самой различной мебели, для изготовления межкомнатных дверей, в качестве отделки металлических и бронированных дверей.
Всё о ДСП
НЕМНОГО ИСТОРИИ
Считается, что прародителем ДСП был Эрнст Хаббард, предложивший идею создания нового, ранее неизвестного науке материала из опилок и казеинового клея. В далеком 1887 году Хаббард воплотил свои мечты в реальность и представил на суд общественности первый прототип ДСП. Разработки изобретателя пришлись по вкусу его коллегам, и уже в 1918 году была создана еще одна экспериментальная модель — плита, отделанная шпоном. В наши дни ДСП ламинированное доступно каждому. А вот во времена М. Бекмена, который впервые облачил древесно-стружечную плиту в шпон, такие изделия могли позволить себе разве что привилегированные особы.
Знаковый момент в истории ДСП произошел в 1926 году. В это время немецкий ученый Фройденберг вывел формулу «идеальной» древесно-стружечной плиты и рассчитал оптимальное соотношение между связующим веществом и древесными опилками. По его подсчетам в древесно-стружечном «полуфабрикате» должно было содержаться от 3 до 10% вязкого вещества. Позднее выводы ученого были несколько откорректированы, поэтому сегодня в состав древесно-стружечных плит входит от 6 до 8% формальдегидных смол. К слову сказать, при производстве ДСП смолистые соединения начали использоваться только в 1933 году, спустя 7 лет после фундаментальных подсчетов Фройденберга.
Наши соотечественники тоже поработали, правда, не на родине. В 1935 году во Франции эмигрант Алексей Самсонов изготовил первые плиты из ориентированных частиц (ОСП — OSB), укладывая крест-накрест длинные полоски шпона. С этого же года в штате Айова начал свою работу экспериментальный завод по производству плит на фенольном связующем Эрнста Лётчера.
Значительно позже была произведена влагостойкая ДСП, в состав которой вошли соединения парафинов.
Что такое ламинированные древесностружечные плиты ?
Древесностружечные плиты, облицованные декоративными бумажными пленками на основе термореактивных полимеров, являются в настоящее время основным материалом для изготовления щитовых элементов мебели массового производства ( англ. — wood particleboards, laminated with paper impregnated with thermosetting resins).
В просторечии эти плиты часто называют «ламинированными » или «ламинатом». Помимо мебели, они используются в строительстве и др. отраслях промышленности.
Плиты, облицованные пленками на основе термореактивных полимеров, обладают высокой твердостью поверхности и устойчивостью к воздействию высокой температуры, воды и растворителей. В процессе испытаний плиты подвергают воздействию воды, спирта, бензина, хлорамина, уксусной кислоты, кофе, чая, растительного масла, ацетона . Поэтому ламинированные плиты хорошо подходят для изготовления деталей бытовой, медицинской, учебной и лабораторной мебели.
Этим свойствам они обязаны содержанию в пленке меламиносодержащей формальдегидной или карбамидоформальдегидной смолы. Химическое название меламина — 2,4,6 триамино- 1,3,5 — триазин .
Декоративные бумаги, используемые для ламинирования плит имеют самые разнообразные цвета и текстуры:
однотонные бумаги, рисунки под различные породы древесины, фантазийные декоры, геометрические орнаменты и т. д.
Для облицовывания ламинированных плит используются пропитанные декоративные пленки с неполной конденсацией смолы. Пленка изготавливается в пропиточной машине из специальной декоративной бумаги плотностью 60 — 90 г/м2.
Технология ламинирования плиты:
Ламинирование плит осуществляется в прессах проходного типа или в многоэтажных прессах. Давление пресса 20 — 35 кг/см2, температура плит 140 — 210 град. С.
В процессе прессования пропитанная бумага уплотняется и приобретает свойства пластика. Содержавшаяся в ней смола, частично выдавливается на наружную и внутреннюю поверхности пленки и быстро конденсируется ( отверждается). Таким образом, на верхней ее поверхности образуется своего рода тведая лаковая пленка, а на нижней — клеевая. Смола проникает в мельчайшие поры плиты-основы, обеспечивая прочное соединение бумаги и плиты. Если формирующая прокладка пресса имеет текстурированную поверхность , то рисунок текстуры отпечатывается на поверхности облицованной плиты. Соответственно глянцевые прокладки обеспечивают получение глянцевой поверхности, а прокладки с матовой поверхностью обеспечивают матовую поверхность плиты.
Разбивая стереотипы.
Сегодня на рынке представлены ДСП самых разнообразных назначений. Они различаются между собой по толщине, плотности, износоустойчивости, составу. Это связано с тем, что древесно-стружечные плиты используются в разных областях.
Кстати, о плотности ДСП. Существует один из самых устойчивых стереотипов, распространенных среди потребителей ДСП: «Чем выше плотность плиты, тем лучше». Разберемся, в чем состоит стереотип, и в чем его опасность.
Плиты ДСП хороши тем, что их можно делать из низкосортной древесины, практически из любого мусора — из горбыля, рейки, тонкомера. Но стружка, которая укладывается в ковер, должна все же отвечать определенным требованиям:
- Во-первых, не должно быть слишком мелкой пылеобразной фракции.
- Во-вторых, получаемая стружка должна иметь форму лепестка, т.е. ее сечение не должно быть квадратным — иначе резко снижаются физико-механические характеристики готовой плиты. «Квадратная» стружка служит концентратором напряжений в слое ДСП, резко ухудшая, главным образом, сопротивление на изгиб.
Проблема ухудшения физико-механических свойств из-за качества стружки была еще в советское время частично решена за счет повышения плотности плиты. Плотность плиты повышалась за счет увеличения доли смолы в готовом изделии. Таким образом, многие отечественные производители сегодня могут «похвастаться» плитой с плотностью до 750 кг/куб.м. Этим, в действительности, удается выйти на физико-механические характеристики, удовлетворяющие требованиям ГОСТ.
Чем же приходится за это расплачиваться?
- Во-первых, увеличение доли смолы увеличивает эмиссию формальдегида. При плотности в 750 кг/куб.м.
и выше оказывается довольно сложной задачей вписаться в требования ГОСТа по уровню Е1, а требования европейской нормы Е1 становятся просто несбыточной мечтой, вне зависимости от качества используемой смолы.
- Во-вторых, более плотная плита при раскрое требует частой замены весьма дорогостоящего режущего инструмента и создает повышенные нагрузки на весь привод оборудования распиловки.
- В-третьих, увеличение плотности влечет за собой увеличение себестоимости, а также увеличение расходов на транспортировку готовой продукции.
При оценке качества плит следует ориентироваться не на плотность, а на физико-механические показатели и на уровень эмиссии формальдегида.
Что такое ДСП?
Этот пост является частью Руководства Plyco по ДСП
ДСП (иногда с любовью именуемый «ДСП») — один из самых универсальных продуктов, которые мы храним здесь, в Plyco. Когда дело доходит до ДСП, старая пословица «никогда не доверяйте книге по ее обложке» и «внешний вид может быть обманчивым» абсолютно верна. На первый взгляд, это выглядит просто как один из наших продуктов из строительной фанеры, и многие люди могут подумать, что для чего-то еще он не пригоден.Однако, как только вы исследуете широкий мир ДСП, вы обнаружите, что это далеко от истины!
Суть древесно-стружечной плиты заключается в том, что это высокоплотная, прочная, экономичная и универсальная плита, изготовленная из крупных древесных частиц в сердцевине и более мелких частиц на отшлифованных поверхностях. Хотя относительно легко свести суть ДСП в броское описание из одного предложения, на самом деле это гораздо более сложный продукт, чем думает большинство людей.Это гораздо больше, чем просто склеить кусочки дерева и покончить с этим. Процесс создания одного из самых надежных продуктов Plyco на самом деле предлагает обширные знания о ДСП, и знание этого может помочь вам максимально эффективно использовать свои доски.
Как производится ДСП?
Процесс производства древесностружечных плит на самом деле довольно сложен. Он начинается с того, что щепа смешивается со смолой и формируется в форме листа.Затем эту необработанную древесно-стружечную плиту подают на дисковый измельчитель. Это измельчитель древесины, который, по сути, использует несколько установленных на нем ножей в качестве механизма измельчения. Это может показаться немного отрывочным, но мы обещаем, что это правильный способ делать что-то! Этот тип измельчителя древесины используется потому, что он имеет тенденцию приводить к более стабильному и надежному размеру древесной щепы. Затем эти частицы сушат, а слишком большие или слишком маленькие стружки выбрасывают.
Смола затем распыляется на лист в виде тонкого тумана.На этом этапе производственного цикла на доске будут использоваться воски, красители, смачивающие вещества и разделительные агенты, если создается влагостойкая разновидность. Хотя это не делает вашу древесно-стружечную плиту водонепроницаемой, она дает вам продукт, который легко выдерживает воздействие влаги.
После того, как древесностружечная плита проходит сквозь туман, щепа укладывается в так называемый ковер, который затем разделяется на «одеяла». Затем они сжимаются в холодном прессе и передаются на другой пресс, который использует огромное давление и тепло для затвердевания клея, нанесенного на плиту.Наконец, как только все остынет, будет завершена обрезка и шлифовка, а затем отправимся в Plyco!
Гидравлический нагревательный пресс, используемый в процессе производства древесностружечных плит.
ДСП 101
Как и многие другие изделия из фанеры, доступные на Plyco, ДСП возникло несколько столетий назад. Он возник в Германии и впервые был произведен в 1887 году, где, как утверждалось, «искусственное дерево» было получено путем сочетания древесного цветка, клея, высокой температуры и давления.Примерно в это же время начала расти популярность фанеры, в результате чего фенольная смола стала широко использоваться. Это привело к тому, что немецкий пилот и изобретатель Макс Химмельхебер создал один из первых подлинных листов ДСП из мусора, древесной стружки и обрезков во время Второй мировой войны. Примерно в это же время будет создан первый коммерческий образец древесностружечных плит. В конце концов, было обнаружено, что использование чипов одинакового размера позволит увеличить прочность, в результате чего компании массово производят продукт, который мы все знаем и любим сегодня.
ДСП — удивительный продукт. Будь то способность использовать так много разных способов, как напольные покрытия или мебель, или тот факт, что цены на ДСП настолько низкие по сравнению с другими сопоставимыми продуктами, почти каждый может найти в этом что-то, что может понравиться.
Реклама ДСП 1940-х годов.
В Plyco мы собрали наиболее полный ассортимент продукции из древесно-стружечных плит, в том числе наши настилы из древесно-стружечных плит для языка и пазов, фанерованные древесно-стружечные плиты и варианты с высокой влагостойкостью. откройте совершенно новый мир возможностей.ДСП имеет множество преимуществ, так почему бы не перейти в наш интернет-магазин, где вы можете просмотреть весь наш ассортимент! Если вам все еще интересно и вы хотите узнать больше, ознакомьтесь с другими нашими публикациями в рамках этого руководства, в которых подробно рассматриваются свойства и возможности использования этого любимого универсального устройства.
Афганистан | 0 | |||||
Албания | 10,000 | |||||
Алжир | 22900 | |||||
Американское Самоа | ||||||
Андорра | Ангола | |||||
Ангилья | ||||||
Антарктида | ||||||
Антигуа и Барбуда | ||||||
Аргентина | 552,000 | |||||
Армения | 0 | |||||
Аруба | ||||||
Австралия | ||||||
Австрия | 2,200,000 | |||||
Азербайджан | 0 | |||||
Багамы | ||||||
Бахрейн | ||||||
Бангладеш | 2200 | |||||
Барбадос | 9005 0 | |||||
Беларусь | 813,000 | |||||
Бельгия | 1,809,800 | |||||
Бельгия-Люксембург | ||||||
Белиз | ||||||
Бенин | ||||||
Бермудские острова | ||||||
Бутан | ||||||
Боливия (Многонациональное Государство) | ||||||
Босния и Герцеговина | 9000 | |||||
Ботсвана | ||||||
Бразилия | 3 261 000 | |||||
Британская территория в Индийском океане | Британские Виргинские острова | |||||
Бруней-Даруссалам | ||||||
Болгария | 781 428 | |||||
Буркина-Фасо | ||||||
Бурунди | ||||||
Кабо-Верде | 9||||||
Камбоджа | 0 | Камбоджа | 0 | 0045 | Камерун | |
Канада | 7,962,000 | |||||
Каймановы острова | ||||||
Центральноафриканская Республика | ||||||
Чад | ||||||
Нормандские острова | ||||||
Чили | 599,000 | |||||
Китай, САР Гонконг | 40,000 | |||||
Китай, САР Макао | ||||||
Китай, материковая часть | 18,583,000 | |||||
Китай, провинция Тайвань | 43,000 | |||||
Остров Рождества | ||||||
Кокосовые (Килинг) острова | ||||||
Колумбия | 250,000 | |||||
Коморские Острова | ||||||
Конго | ||||||
Острова Кука | ||||||
Коста-Рика | 22000 | |||||
Кот д Ивуар | 9004 6 0||||||
Хорватия | 128000 | |||||
Куба | 62000 | |||||
Кюрасао | ||||||
Кипр | 0 | |||||
Чешская Республика | 1,032 000 | |||||
Чехословакия | ||||||
Корейская Народно-Демократическая Республика | ||||||
Демократическая Республика Конго | 0 | |||||
Дания | 349000 | |||||
Джибути | ||||||
Доминика | ||||||
Доминиканская Республика | ||||||
Эквадор | 94000 | |||||
Египет | 6300 | |||||
Сальвадор | ||||||
Экваториальная Гвинея | ||||||
Эритрея | ||||||
Эстония | 178 300 | |||||
Эфиопия 047 | 22000 | |||||
Эфиопия PDR | ||||||
Фолклендские (Мальвинские) острова | ||||||
Фарерские острова | ||||||
Фиджи | ||||||
Финляндия | 104,624 | |||||
4 | ||||||
Французская Гвиана | ||||||
Французская Полинезия | ||||||
Французские южные и антарктические территории | ||||||
Габон | ||||||
Гамбия | ||||||
Грузия | 0 | |||||
Германия | 900 6,806,000||||||
Гана | 8,000 | |||||
Гибралтар | ||||||
Греция | 240,000 | |||||
Гренландия | ||||||
Гренада | ||||||
Гваделупа | ||||||
Гуам | ||||||
Гватемала | 7,000 | |||||
Гвинея | ||||||
Гвинея-Бисау | ||||||
Гайана | ||||||
Гаити | ||||||
Гондурас | ||||||
Венгрия | 133,130 | |||||
Исландия | 0 | |||||
Индия | 23,500 | |||||
Индонезия | 125000 | |||||
Иран (Исламская Республика) | 845000 | |||||
Ирак | 5000 | |||||
Ирландия | 261 300 | |||||
Остров Мэн | ||||||
Израиль | 0 | |||||
Италия | 2353,559 | |||||
Ямайка | 0 | |||||
Япония | 9 | |||||
Казахстан | 279,200 | |||||
Кения | 7,700 | |||||
Кирибати | ||||||
Кувейт | ||||||
Кыргызстан | 0 | |||||
Лаосская Народно-Демократическая Республика | ||||||
Латвия | 872,101 | |||||
Ливан | 12000 | |||||
Лесото | ||||||
Либерия | ||||||
Ливия | ||||||
Лихтенштейн | 0 | 69 Литва | ||||
Люксембург | 216,130 | |||||
Мадагаскар | ||||||
Малави | ||||||
Малайзия | 122700 | |||||
Мальдивы | ||||||
Мали | ||||||
Мальта | 0 | |||||
Маршалловы Острова | ||||||
Мартиника | ||||||
Мавритания | ||||||
Маврикий | 0 | |||||
Майотта | ||||||
Мексика | 580 000 | |||||
Монако | ||||||
Монголия | 600 | |||||
Черногория | 0 | |||||
Монтсеррат | ||||||
Марокко | 3400 | |||||
Мозамбик | ||||||
Мьянма | ||||||
Намибия | ||||||
Науру | ||||||
Непал | ||||||
Нидерланды | 0 | |||||
Нидерландские Антильские острова | ||||||
Новая Каледония | 9 0066||||||
Новая Зеландия | 152,652 | |||||
Никарагуа | ||||||
Нигер | ||||||
Нигерия | 40,000 | |||||
Ниуэ | ||||||
Остров Норфолк | ||||||
Северные Марианские острова | ||||||
Норвегия | 1 | |||||
Оккупированная палестинская территория | ||||||
Оман | ||||||
Подопечная территория островов Тихого океана | ||||||
Пакистан | 76000 | |||||
Палау | ||||||
Палау | ||||||
Папуа-Новая Гвинея | ||||||
Парагвай | ||||||
Перу | 0 | |||||
Филиппины | 4000 | |||||
Острова Питкэрн | ||||||
Польша | 90 046 4,950,000||||||
Португалия | 648915 | |||||
Пуэрто-Рико | ||||||
Катар | ||||||
Республика Корея | 801,000 | |||||
Республика Молдова | 0 | |||||
Румыния | 3,534,210 | |||||
Российская Федерация | 6,657,000 | |||||
Руанда | ||||||
Остров Святой Елены, Вознесения и Тристан-да-Кунья | ||||||
Сент-Китс и Невисия | Сент-Китс и Невисия | |||||
Сен-Пьер и Микелон | ||||||
Сент-Винсент и Гренадины | ||||||
Сен-Мартен (Французская часть) | ||||||
Самоа | ||||||
Сан-Марино | ||||||
Сао Томе и Принсипи 90 047 | ||||||
Саудовская Аравия | ||||||
Сенегал | ||||||
Сербия | 221000 | |||||
Сербия и Черногория | ||||||
Сейшельские острова | 0 | |||||
Сьерра-Леоне | Сьерра-Леоне | 10,000 | ||||
Словакия | 520,000 | |||||
Словения | 40,000 | |||||
Соломоновы Острова | ||||||
Сомали | 0 | |||||
Южная Африка | 392,803 | |||||
Южный Судан | ||||||
Испания | 1320 000 | |||||
Шри-Ланка | 0 | |||||
Судан | 0 | |||||
Судан (бывший) | ||||||
Суринам | 0 | |||||
Свальбард и Ян-Майен Острова 9004 7 | ||||||
Свазиленд | ||||||
Швеция | 482 710 | |||||
Швейцария | 545 000 | |||||
Сирийская Арабская Республика | 9 200 | |||||
Таджикистан | 0 | |||||
Таиланд | 2 600 000||||||
Бывшая югославская Республика Македония | 0 | |||||
Тимор-Лешти | ||||||
Того | ||||||
Токелау | ||||||
Тонга | ||||||
Тринидад и Тобаго | Тунис | 55,000 | ||||
Турция | 4,300,000 | |||||
Туркменистан | 0 | |||||
Острова Теркс и Кайкос | ||||||
Тувалу | ||||||
Уганда | 0 | |||||
Украина 900 47 | 1,609,000 | |||||
Объединенные Арабские Эмираты | ||||||
Соединенное Королевство | 2,276,000 | |||||
Объединенная Республика Танзания | 1,600 | |||||
Соединенные Штаты Америки | 15,185,000 | |||||
Виргинские острова Соединенных Штатов | ||||||
Уругвай | ||||||
СССР | ||||||
Узбекистан | 3,800 | |||||
Вануату | ||||||
Венесуэла (Боливарианская Республика) | 31000 | |||||
Вьетнам | ||||||
Остров Уэйк | ||||||
Острова Уоллис и Футуна | ||||||
Западная Сахара | ||||||
Йемен | ||||||
Югославский SFR | ||||||
Замбия | 16000 | |||||
Зимба bwe | 58,000 |
Сушка древесных стружек для ДСП — BÜTTNER Energy & Drying
Высокие стандарты качества благодаря трубчатым предварительным сушилкам и барабанным сушилкам Büttner
Древесно-стружечные плиты занимают особое место среди древесных материалов. Они традиционно использовались и до сих пор широко используются в производстве мебели. Измельченные древесные отходы, прореживание древесины и рекуперированная древесина — это сырье, используемое для производства древесностружечных плит в деревообрабатывающей промышленности. Для производства ДСП древесные стружки склеиваются, сортируются по размеру и прессуются; более крупные хлопья образуют средний слой, а мелкие чешуйки образуют твердую поверхность.
Равномерный уровень влажности хлопьев, используемых в производстве, важен для качества древесностружечных плит.Вот почему эффективные и высококачественные сушильные системы Büttner очень широко используются во всем мире: наши однопроходные барабанные сушилки, которые нагреваются непосредственно дымовыми газами, всегда обеспечивают равномерное и оптимальное содержание влаги в древесных хлопьях.
Различные топочные системы Büttner вырабатывают дымовой газ, используемый для работы однопроходных барабанных сушилок. Древесная пыль, мазут, дизельное топливо или природный газ сжигаются в специальных камерах сгорания с комбинированными горелками или муфельными горелками. В качестве альтернативы, колосниковые топочные системы также используются для сжигания измельченных продуктов биомассы, таких как древесные отходы, кора или обрезки древесно-стружечных плит.
Предварительные сушилки с испарительной трубкой перед барабанными сушилками используются для древесины с высоким содержанием влаги. Эти сушилки резко снижают содержание влаги в древесине за секунды, прежде чем высушенные продукты достигнут своего конечного уровня влажности в барабанной сушилке.
Сушилки с паровым нагревом предпочтительны при использовании в сочетании с когенерацией (комбинированное производство тепла и электроэнергии или ТЭЦ).Здесь используются либо сушилки с пучком труб (роторная сушилка), либо сушилки с трубчатым барабаном. Оба типа осушителей косвенно нагреваются выхлопным паром турбины и, таким образом, являются отличным дополнением к использованию тепла когенерационной системой.
Бюттнер обеспечивает оптимальную сушку материалов для производства ДСП благодаря плавному взаимодействию между системой горелки, предварительной сушилкой с испарительной трубкой и однопроходной барабанной сушилкой. Наши системы зарекомендовали себя по всему миру на бесчисленных предприятиях деревообрабатывающей промышленности.
Объем, доля, тенденции и рост рынка ДСП | Отчет о воздействии COVID-19 с 2021 по 2026 год
Обзор рынка
Период обучения: | г.2016 — 2026 гг. |
Базовый год: | 2020 г. |
Самый быстрорастущий рынок: | Азиатско-Тихоокеанский регион |
Крупнейший рынок: | Северная Америка |
CAGR: | > 5% |
Нужен отчет, отражающий, как COVID-19 повлиял на этот рынок и его рост?
Бесплатное скачивание ОбразецОбзор рынка
Согласно прогнозам, среднегодовой темп роста рынка стружечных плит в течение прогнозируемого периода (2021-2026 гг. ) Составит 5%.
Из-за воздействия COVID-19 правительство ввело несколько ограничений, в результате чего строительные работы были остановлены. Хотя рост жилищного строительства в 2019 году был заметным в таких регионах, как Азиатско-Тихоокеанский регион, Северная Америка, Ближний Восток и Африка, пандемия COVID-19, по оценкам, серьезно ударила по росту жилищного строительства. Блокировка, введенная правительствами для сдерживания распространения коронавируса, привела к тому, что строительные компании объявили о прекращении своей деятельности.Это может задержать реализацию проектов, что приведет к перерасходу средств и отрицательно скажется на рабочей силе. Однако ожидается, что это состояние восстановится в 2021 году, тем самым восстановив траекторию роста исследуемого рынка.
- В долгосрочной перспективе основным движущим фактором рынка является рост спроса на ДСП для мебели, что способствует росту рынка.
- Предполагается, что разработка новых методов производства древесностружечных плит открывает новые возможности для рынка в будущем.
- Ожидается, что угроза использования древесноволокнистых плит средней плотности в качестве заменителя будет препятствовать росту исследуемого рынка.
- Ожидается, что Азиатско-Тихоокеанский регион будет доминировать на рынке в течение прогнозируемого периода.
Объем отчета
Древесно-стружечная плита, также известная как ДВП, представляет собой технический материал, состоящий из отдельных волокон. Древесноволокнистые плиты обычно изготавливаются из искусственной древесины, которая бывает твердой или мягкой.Его смешивают со связующими на основе парафина и смолы, применяя высокое давление и температуру. Рынок ДСП сегментирован по сырью, применению и географическому положению. Рынок сегментирован по сырью, включая древесину, жом и другое сырье. Рынок сегментирован по таким приложениям, как строительство, мебель, инфраструктура и другие приложения. Отчет также охватывает размер рынка и прогнозы рынка стружечных плит в 16 странах в основных регионах. Для каждого сегмента размер рынка и прогнозы были сделаны на основе выручки (млн долларов США).
Сырье | ||||||
| Мешок | |||||
Другое сырье |
Применение | |
Строительство | |
Мебель | |
Инфраструктура | |
Другие приложения |
| |||||||
| |||||||
| |||||||
| |||||||
|
Объем отчета может быть
настроены в соответствии с вашими требованиями. Кликните сюда.
Ключевые тенденции рынка
Растущий спрос со стороны мебельной промышленности
- В связи с изменением образа жизни современного населения предпочтения к стилю мебели резко изменились за последние годы. Современная мебель состоит из таких элементов, как простые линии, стулья с квадратными краями и различные сочетания цветов.
- Благодаря высокой термостойкости, огнестойкости и влагостойкости использование этих плит в мебельной промышленности быстро растет. Кроме того, мебель из ДСП придает такие свойства, как легкий вес и высокое соотношение прочности и веса.
- С ростом жилищного строительства, населения и доходов во всем мире спрос на мебель, такую как стулья, столы, кровати, диваны, полки и шкафы, значительно возрастает.
- В мебельной промышленности концепции, связанные с интерьером домов, офисов и квартир, постоянно меняются.
Это стимулирует инновации и развитие, прежде всего в плане дизайна, размера и цвета. Ожидается, что это увеличит объем производства мебели во всем мире.
- Страны, включая Китай, США и Германию, составляют крупнейшие рынки мебельной промышленности. Китай является доминирующим экспортером деревянной мебели в ЕС.
- Индонезия — один из ведущих производителей мебели в мире.Мебельная промышленность Индонезии сохраняет положительный рост.
- Кроме того, в Индии расширяющийся рынок мебели также побудил такие компании, как Pepper fry (интернет-магазин мебели в Индии), расширить портфель своих домашних брендов и розничные сети в стране.
- Согласно исследованию Всемирного банка, организованная мебельная промышленность Индии росла примерно на 20% в год и к 2019 году должна была превысить 32 миллиарда долларов США. По оценкам, онлайн-рынок домашнего декора в стране за годы вырастет более чем на 50%.
- Ожидается, что все вышеупомянутые факторы будут стимулировать мировой рынок в течение прогнозируемого периода.
Чтобы понять основные тенденции, загрузите образец Отчет
Азиатско-Тихоокеанский регион будет доминировать на рынке
- Азиатско-Тихоокеанский регион, где будет наблюдаться устойчивый рост рынка стружечных плит благодаря развитию строительной и мебельной промышленности в таких странах, как Китай.
- Китай является крупнейшей рыночной базой в Азиатско-Тихоокеанском регионе благодаря постоянно растущему населению, росту доходов и быстрой урбанизации. Это также один из основных производственных центров почти для каждой отрасли. Следовательно, развитие инфраструктуры в стране будет постоянно расти.
- Строительная отрасль Китая развивалась быстрыми темпами благодаря стремлению центрального правительства инвестировать в инфраструктуру для поддержания экономического роста.
- Кроме того, в сентябре 2020 года в провинциях Шаньдун, Цзянсу, Аньхой и Гуанси были введены в эксплуатацию пять новых заводов по производству ДСП с годовой производительностью 1 миллион кубических метров, из которых 4 являются линиями непрерывного плоского прессования с годовой производительностью 950 000 кубических метров. метров, дальнейшее увеличение производственных мощностей Китая.В долгосрочной перспективе цена на древесностружечные плиты будет падать, так как по всему миру строится множество небольших заводов, которые увеличивают предложение, в свою очередь, снижают отпускную цену.
- Китай — один из крупнейших экспортеров мебели в мире, наряду с Италией. Производство деревянной мебели составляет самую большую долю в секторе производства мебели Китая, обеспечивая более 50% общей выручки от производства мебели.
- Правительство Индии активно стимулирует жилищное строительство, поскольку оно стремится предоставить жильем около 1 человека.3 миллиарда человек. В ближайшие семь лет в стране, вероятно, будет инвестировано около 1,3 триллиона долларов США в жилищное строительство, и, вероятно, будет построено 60 миллионов новых домов в стране. Ожидается, что доступность доступного жилья в стране к 2024 году вырастет примерно на 70%.
- В рамках бюджета на 2020-2021 годы правительство Индии планировало выделить в инфраструктуру около 103 крор индийских рупий в течение следующих пяти лет. В связи с этим правительство внедрило национальный инфраструктурный трубопровод (НПИ), который включает около 6500 проектов в разных секторах.Эти проекты будут включать развитие инфраструктуры жилья, здравоохранения, учебных заведений, железнодорожных вокзалов, автовокзалов, аэропортов, метро и железнодорожного транспорта, логистики и складирования и т. Д.
- Ожидается, что к 2030 году Индия станет третьим по величине строительным рынком в мире, а ее вклад в ВВП к 2030 году увеличится примерно до 15%.
- Из-за нынешней пандемии рыночный спрос на стружечные плиты в строительной и мебельной промышленности сталкивается с препятствиями.Однако предполагается, что восстановление рынка будет очевидным. Таким образом, прогнозируемый рост строительной и мебельной промышленности, как ожидается, увеличит спрос на местном рынке ДСП в период восстановления после пандемии.
Чтобы понять тенденции в географии, скачайте образец Отчет
Конкурентная среда
Рынок стружечных плит по своей природе фрагментирован из-за присутствия нескольких крупных игроков в разных странах.Ключевые игроки на рынке стружечных плит: West Fraser, Georgia-Pacific, Roseburg Forest Products, Kastamonu Entegre и Wanhua Ecoboard Co. Ltd.
.Содержание
1. ВВЕДЕНИЕ
1.1 Результаты исследования
1.2 Допущения исследования
1.3 Объем исследования
2. МЕТОДОЛОГИЯ ИССЛЕДОВАНИЯ
3. РЕЗЮМЕ
- 000
- 000
- 000
- 000
- 000
00 Драйверы
4.1.1 Повышение спроса на древесно-стружечные плиты для мебели
4.1.2 Легкая доступность сырья
4.2 ограничения
4.2.1 Угроза использования древесноволокнистых плит средней плотности в качестве заменителя
4.2.2 Неблагоприятные условия, возникающие из-за воздействия COVID-19
4.3 Анализ цепочки создания стоимости в отрасли
4.4 Анализ пяти сил Портера
4.4.1 Торговая сила поставщиков
4.4.2 Торговая сила потребителей
4.4.3 Угроза новых участников
4.4.4 Угроза заменяющих товаров и услуг
4.4.5 Степень конкуренции
5. СЕГМЕНТАЦИЯ РЫНКА
5.1 Сырье
5.1.1 Древесина
- 1.1 Опилки
5.1.1.2 Стружка
5.1.1.3 Хлопья
5.1.1.4 Стружка
5.1.2 Жмых
5.1.3 Другое сырье
5.2 Применение
5.2.1 Строительство
5.2.2 Мебель
5.2.3 Инфраструктура
5.2.4 Другие приложения
5.3 География
5.3.1 Азиатско-Тихоокеанский регион
5.3.1.1 Китай
5.3.1.2 Индия
5.3.1.3 Япония
5.3.1.4 Южная Корея
5.3.1.5 Остальная часть Азиатско-Тихоокеанского региона
5.3.2 Северная Америка
5.3.2.1 США
5.3.2.2 Канада
5,3 .2.3 Мексика
5.3.3 Европа
5.3.3.1 Германия
5.3.3.2 Великобритания
5.3.3.3 Италия
5.3.3.4 Россия
- 57 5.3.3.5 Франция
5.3.3.6 Остальная Европа
5.3.4 Южная Америка
5.3.4.1 Бразилия
5.3.4.2 Аргентина
5.3.4.3 Остальные страны Южная Америка
5.3.5 Ближний Восток и Африка
5.3.5.1 Саудовская Аравия
5.3.5.2 Южная Африка
5.3.5.3 Остальной Ближний Восток и Африка
6.КОНКУРЕНТНЫЙ ЛАНДШАФТ
6.1 Слияния и поглощения, совместные предприятия, сотрудничество и соглашения
6.2 Доля рынка ** / анализ рейтинга
6.3 Стратегии, принятые ведущими игроками
6.4.1 Associate Decor Ltd
6.4.2 Boise Cascade
6.4.3 Century Prowud
6.4.4 Columbia Forest Products
6.4.5 D&R Henderson Pty Ltd
6.4.6 Группа компаний ЭГГЕР
6.4.7 Джорджия-Тихоокеанский регион
6.4.8 Кастамону Энтегре
6.4.9 Кроноплюс Лимитед
7 Industries Pvt. Ltd6.4.11 Peter Benson (Plywood) Limited
6.4.12 Roseburg Forest Products
6.4.13 Siam Riso Wood Products Co. Ltd
6.4.14 Sonae Industria
6.4.15 Timber Products Company
6.4.16 UCS Forest Group
6.4.17 Uniboard
6.4.18 West Fraser
Ecoboard 6.4.19 Co Wan . Ltd
* Список не исчерпывающий
7. ВОЗМОЖНОСТИ РЫНКА И БУДУЩИЕ ТЕНДЕНЦИИ
7.1 Разработка новых методов производства панелей из частиц
Вы также можете приобрести части этого отчета.Вы хотите проверить раздел мудро прайс-лист?
Получить разбивку цен Сейчас жеЧасто задаваемые вопросы
Каков период изучения этого рынка?
Рынок ДСП изучается с 2016 по 2026 год.
Каковы темпы роста рынка ДСП?
Рынок ДСП растет со среднегодовыми темпами> 5% в течение следующих 5 лет.
В каком регионе наблюдается самый высокий рост рынка ДСП?
Азиатско-Тихоокеанский регион демонстрирует самый высокий среднегодовой темп роста в период с 2021 по 2026 год.
Какой регион имеет наибольшую долю на рынке ДСП?
Наибольшая доля в 2020 году принадлежит Северной Америке.
Кто являются ключевыми игроками на рынке ДСП?
West Fraser, Georgia-Pacific, Kastamonu Entegre, Wanhua Ecoboard Co., Ltd, Roseburg Forest Products — крупнейшие компании, работающие на рынке древесностружечных плит.
80% наших клиентов ищут отчеты на заказ. Как ты хотите, чтобы мы адаптировали вашу?
Пожалуйста, введите действующий адрес электронной почты!
Пожалуйста, введите правильное сообщение!
ОТПРАВИТЬЗагрузка…
Древесно-стружечная плита и плита с ориентированной стружкой, приготовленная с применением клея, армированного наноцеллюлозой
Клеи на основе карбамидоформальдегида (UF) и меламино-мочевиноформальдегида (MUF) широко используются в производстве древесных плит. В настоящем исследовании была сделана попытка улучшить механические свойства картона путем усиления этих клеев нановолокнами целлюлозы (CNF). Последние были произведены из буковой целлюлозы для растворения с помощью процесса механической гомогенизации.Адгезивные смеси с содержанием CNF 0, 1 и 3 мас.% В расчете на твердую смолу были приготовлены путем смешивания водной суспензии CNF с адгезивами UF и MUF. Были произведены древесно-стружечные плиты и плиты с ориентированной стружкой (OSB) в лабораторных масштабах, а также исследованы механические свойства и механические свойства разрушения. Древесно-стружечные плиты, изготовленные с использованием UF, содержащего 1 мас.% CNF, показали меньшее набухание по толщине и лучшую внутреннюю связь и прочность на изгиб, чем плиты, полученные с использованием чистого UF. Усиливающий эффект CNF был еще более очевиден для OSB, где было обнаружено значительное улучшение прочностных свойств на 16%.Как для древесностружечных плит, так и для OSB, энергия разрушения по моде I и вязкость разрушения были параметрами с наибольшим улучшением, указывающими на то, что адгезионные связи были заметно упрочнены добавлением CNF.
1. Введение
Спустя почти 80 лет после изобретения древесно-стружечная плита по-прежнему представляет собой наиболее важную группу древесных плит в Европе. В 2010 году доля древесностружечных плит в общем объеме производства древесных плит составляла около 63% [1]. Помимо ДСП, ориентированно-стружечные плиты (OSB) приобретают все большее значение как в декоративных, так и в конструкционных приложениях.При использовании в качестве строительного материала механические свойства плит имеют жизненно важное значение. В этом отношении качество соединений между древесными частицами является ключевым фактором, который, в свою очередь, определяется количеством и типом используемого клея. В производстве древесных плит преобладают аминопластические клеи на основе карбамидоформальдегида (UF) и меламино-мочевиноформальдегида (MUF). Эти клеи предлагают ряд преимуществ для промышленного применения; однако механические характеристики древесных клеевых соединений UF и MUF ограничены.Поскольку модуль упругости затвердевших аминопластических линий связи высок, деформация адгезионного слоя при механической нагрузке обычно мала. В результате создаются концентрации напряжений вдоль линии соединения клеевого шва по дереву [2–4], которые снижают общую прочность шва.
В прошлом предпринимались различные попытки снизить хрупкость UF и, таким образом, улучшить его прочностные свойства. Подходы варьируются от химической модификации UF-полимера до смешивания с другими полимерами (например,г., [5–11]) к армированию различными видами волокон. Поскольку известно, что УФ-смолы обладают сильной адгезией к большинству целлюлозосодержащих материалов, волокна на основе целлюлозы кажутся хорошо подходящими для усиления УФ. Это подтверждено экспериментально рядом работ (например, [12–17]). Поскольку при производстве древесностружечных плит адгезив распыляется на мелкие капли диаметром около 40–60 мкм м до связывания древесных частиц, армирующие элементы должны быть микро- или наноразмерными [18].Следовательно, применение целлюлозных нановолокон (УНВ) для армирования адгезива представляется перспективным.
В то время как можно найти значительное количество публикаций, касающихся армирования полимеров нановолокнами из целлюлозы, литературы по армированным целлюлозой клеям, подходящим для склеивания древесины, довольно мало. Richter et al. [19] обсуждали применение CNF для усиления однокомпонентных полиуретановых и поливинилацетатных (PVAc) латексных клеев для древесины на водной основе. Хотя оба целлюлозосодержащих клея показали хорошие результаты при механических испытаниях, не удалось добиться значительного и последовательного улучшения характеристик линии склеивания по сравнению с эталонными продуктами.Авторы определили сходную полярность волокон и полимера, морфологию волокна с контролируемым качеством и тщательно сбалансированную нагрузку волокна в диапазоне от 1 до 5 мас.% Как критические параметры, определяющие механические свойства адгезивов, армированных CNF. В другом исследовании [20], проведенном той же исследовательской группой, изучалась пригодность использования CNF для создания смесей ПВА с клеем, дающих линии склеивания с улучшенной термостойкостью. С помощью динамического механического анализа был обнаружен значительно увеличенный модуль упругости для пленок ПВК-латекс, армированных CNF.Кроме того, образцы для испытаний внахлестку, приготовленные с использованием клея, армированного целлюлозой, показали значительно повышенную термостойкость. В недавнем исследовании Атта-Обенг [18] армировал фенолформальдегидный клей микрокристаллической целлюлозой при различных уровнях нагрузки от 0 до 10 мас.%. Испытания на сдвиг внахлестку показали увеличение прочности при добавлении целлюлозы. С другой стороны, древесно-стружечные плиты, изготовленные с использованием целлюлозно-наполненного ПФ, показали худшие механические свойства при испытаниях на статический изгиб и более высокое разбухание по толщине, чем плиты, склеенные чистым ПФ.Это объясняется менее выраженным эффектом пружинения во время горячего прессования. Армирование целлюлозой, по-видимому, ограничивает упругую отдачу плиты после снятия сжимающего напряжения, создаваемого горячим прессом. Автор пришел к выводу, что это приводит к расслоению древесных частиц и клея, что приводит к ухудшению характеристик плиты.
Собственные исследования [21] показали, что добавление 5 мас.% CNF к коммерчески используемому УФ-клею позволяет получить клеевые соединения массивной древесины со значительно увеличенной прочностью на сдвиг внахлестку в соответствии с EN 302-1 [22].Поскольку деформация до разрушения была значительно выше для образцов, армированных CNF, был сделан вывод, что UF-адгезив, возможно, был упрочнен добавлением фибриллированной целлюлозы. В последующем исследовании [23] было изучено влияние добавления CNF на удельную энергию разрушения адгезионных связей твердой древесины. Энергия разрушения определялась на образцах с плоской двойной консолью (DCB), как описано Gagliano и Frazier [24]. Поскольку энергия разрушения UF-связей, заполненных 2 мас.% CNF, была на 45% выше по сравнению с чистыми UF-связями, это исследование доказало возможность повышения ударной вязкости UF путем добавления CNF.
Целью настоящего исследования было выяснить, приводит ли добавление CNF к клеям для древесины на основе формальдегида к улучшенным механическим свойствам древесных плит, изготовленных с их использованием. Лабораторные древесностружечные плиты и OSB были приготовлены с использованием имеющихся в продаже клеев UF и MUF, которые были усилены добавлением небольших количеств CNF. Были исследованы реологические свойства клеевых смесей и механические свойства готовых плит.
2. Материалы и методы
2.1. Получение целлюлозных нановолокон
Исходным материалом, используемым для получения CNF, была никогда не высушенная буковая пульпа растворяющегося сорта (Lenzing AG, Ленцинг, Австрия) с содержанием сухого вещества около 50 мас.%. Первоначально пульпу замачивали в дистиллированной воде на 2 часа. После этого более крупные агрегаты волокон разрушали с использованием смесителя Ultra-Turrax, работающего при 21500 мин -1 в течение 3 мин. Содержание сухого вещества в суспензии волокон было установлено на 0,5 мас.%. Для получения нановолокон суспензию фибриллировали за 30 проходов через лабораторный гомогенизатор высокого давления (APV 1000, APV Manufacturing Sp.z o.o., Быдгощ, Польша) работали при давлении 700–800 бар. Гомогенизированную суспензию сушили на воздухе при 70–80 ° C до достижения содержания целлюлозы 1,5 ± 0,1 мас.%. В дальнейшем суспензию использовали для приготовления клеевых смесей с целлюлозным наполнителем.
Нановолокна были охарактеризованы с помощью атомно-силовой микроскопии (АСМ). Одну каплю 0,002% суспензии CNF наносили на диск из слюды и оставляли сушиться при комнатной температуре до испарения воды. АСМ-изображения выполнялись на приборе Dimension Icon AFM (Bruker Corp., Санта-Барбара, США). Изображения получали в режиме постукивания со скоростью сканирования 0,5-0,6 линии в секунду с использованием стандартного силиконового кантилевера (TESPA, Bruker Corp., Санта-Барбара, США).
2.2. Приготовление и характеристика клеевых смесей
Для приготовления древесностружечных плит лабораторного масштаба применяли УФ-клей, используемый в производстве древесно-стружечных плит (Prefere 10F102, Dynea Austria GmbH, Кремс, Австрия). Адгезивные смеси с содержанием целлюлозы 1 и 3% по массе твердой смолы были приготовлены путем добавления соответствующего количества 1.5% суспензия CNF в адгезиве. Адгезив, наполненный целлюлозой, перемешивали ручным блендером в течение 3 мин для достижения надлежащего распределения CNF в UF-матрице. Раствор 10 мас.% Нитрата аммония в воде использовали в качестве отвердителя для УФ-смолы. Панели OSB были приготовлены с помощью порошкообразного клея MUF (Prefere 4681, Dynea AS, Lillestrøm, Норвегия) без какого-либо дополнительного отвердителя. Содержание целлюлозы составляло 1% от веса твердой смолы. Состав отдельных клеевых смесей приведен в таблице 1.
Клеящая смесь Количество (г / 100 г клеевой смеси) Отвердитель Твердая смола Целлюлоза Время гелеобразования Вязкость Смола Вода (г твердого вещества) (%) (% твердой смолы) (с) (Па · с) UF 66.00 — 34,00 1,65 66,0 — 49 0,48 MUF 45,00 — 55,00 — 45,0 75,0 1,62 UF-1% CNF 45,55 0,46 53,99 1,14 45,6 1,01 67 0,93 MUF-1% CNF 00 0,45 54,55 — 45,2 1,00 67 8,51 UF-3% CNF 26,14 0,79 73,07 0,65 7 0,65 119 1,41 Для дальнейшей характеристики были определены время гелеобразования и вязкость клеевых смесей. Для измерения времени гелеобразования около 2.6 г клея наливали в пробирку и должным образом смешивали с твердым нитратом аммония (2,3% по массе твердой смолы) в качестве отвердителя. Пробирку погружали в кипящую водяную баню и определяли время от погружения до гелеобразования клея. Для каждой клеевой смеси было проведено три измерения. Измерения вязкости проводили на реометре Bohlin CVO (Bohlin Instruments, Пфорцхайм, Германия). Для всех измерений использовалась измерительная система конус / пластина с размером зазора 0,15 мм.На пластину наносили 1,2–1,3 мл жидкого клея, а вязкость усредняли за 30 с. Эту процедуру повторяли 5 раз для каждой смеси. Все адгезивы были измерены без добавления отвердителя при 20 ° C и постоянной скорости сдвига 10 с -1 .
2.3. Подготовка плит
Для подготовки древесностружечных плит промышленные древесные частицы (Fritz Egger GmbH, Унтеррадльберг, Австрия) с размером частиц от 0,63 до 14 мм сушили на воздухе до содержания влаги 4.2%. Высушенные частицы покрывали клеем во вращающемся барабане путем распыления клеевой смеси УФ. Чтобы удалить излишки воды, склеенные частицы сушили, продувая холодный воздух во вращающийся склеивающий барабан. После времени сушки 2 ч и 12 ч для UF, содержащего 1 и 3 мас.% CNF, соответственно, содержание влаги в частицах снизилось примерно до 8%. Только после этого раствор отвердителя был распылен на склеенные частицы, что снова привело к увеличению влажности до заданного значения 10 ± 1%.После распыления раствора отвердителя частицы вращали еще 2 мин, чтобы обеспечить равномерное распределение отвердителя по частицам. Склеенные частицы формовали в мат и подвергали горячему прессованию при температуре 200 ° C и давлении 4,5 МПа. Время прессования для всех досок составляло 150 с. Всего было приготовлено 9 древесностружечных плит (500 × 430 × 14 мм 3 ), то есть по три плиты каждая с чистым UF, UF-1% CNF и UF-3% CNF. Содержание клея во всех древесностружечных плитах составляло 10% твердой смолы на основе высушенной в печи древесины.
Панели OSBполучали из двух различных фракций лабораторных прядей сосны ( Pinus sylvestris L.). Пряди для сердцевины и поверхностного слоя сначала сушили до содержания влаги 4,9 и 3,3% соответственно. Две фракции были покрыты клеем отдельно, используя ту же процедуру нанесения, что и для древесностружечных плит. Нити с покрытием сушили до влажности 10 ± 1% и формовали в мат с трехслойной структурой (0 ° / 90 ° / 0 °). Параметры, использованные для горячего прессования, были такими же, как для ДСП, за исключением того, что время прессования было увеличено до 220 с.Три панели OSB (500 × 430 × 19 мм 3 ) с содержанием клея 8% были произведены с чистым MUF и MUF-1% CNF. Все плиты хранили в климатической камере при 20 ° C и относительной влажности 65% до достижения равновесного содержания влаги.
2.4. Определение свойств плит
Плотность и набухание плит по толщине за 24 часа были определены в соответствии с европейскими стандартами EN 323 [25] и EN 317 [26], соответственно. Для этого на каждую клеевую смесь вырезали 18 образцов ДСП и 15 образцов OSB.Впоследствии на тех же образцах определяли набухание по плотности и толщине.
Механические испытания включали определение внутренней связи, прочности на изгиб, энергии разрушения и вязкости разрушения. Внутреннее соединение и прочность на изгиб были определены в соответствии с EN 319 [27] и EN 310 [28]. Прочность внутреннего сцепления проверялась на универсальной испытательной машине Zwick / Roell Z100, оснащенной датчиком нагрузки 5 кН, тогда как испытания на изгиб проводились на Zwick / Roell Z020. Для испытаний на механическое разрушение из досок вырезали образцы длиной 250 мм и шириной 25 мм и на одном конце каждого образца вырезали надрез длиной 20 мм.Образцы с надрезом были прикреплены к Т-образным стальным профилям цианоакрилатным клеем (Loctite 431, Henkel Central Eastern Europe GmbH, Вена, Австрия), чтобы прикрепить образцы к испытательным зажимам (рис. 1). Механические испытания на разрушение проводились на испытательной машине Zwick / Roell Z100, оснащенной датчиком нагрузки 2,5 кН. Образцы древесностружечных плит первоначально нагружали со скоростью 1 мм · мин -1 , а после 30% снижения нагрузки скорость постепенно увеличивали до 100 мм · мин -1 .Критерием окончания испытания было достижение нижнего предела усилия 5 Н или максимального смещения 50 мм соответственно. Для испытаний OSB параметры были немного изменены, то есть использовался датчик нагрузки 5 кН, скорость испытания была увеличена с 1 до 10 мм · мин. −1 после 50% падения нагрузки и максимальное смещение. 20 мм использовалось в качестве критерия отмены. Энергия разрушения каждого образца была рассчитана путем интегрирования кривой нагрузка-смещение, записанной во время испытаний.Результаты отражают работу разрушения 𝑊𝑓 (J), необходимую для разделения образца на две части при нагрузке в режиме I. Вязкость разрушения, то есть критический коэффициент интенсивности напряжения 𝐾Ic (МПа · м 1/2 ), был рассчитан согласно (1), который был получен из моделирования методом конечных элементов (FEM), выполненного Rathke et al. [29]: 𝐾Ic = max6.568⋅10−5 + 2.082⋅10−7𝑘init𝑏 − 1.498⋅10−10𝑘init𝑏2 + 5.253⋅10−14𝑘init𝑏3, (1) где 𝐹max отражает максимальную приложенную нагрузку, 𝑘init — начальный наклон кривой нагрузка-смещение, а 𝑏 — ширина образца.Для всех тестируемых параметров рассчитывались средние значения для каждой группы образцов и сравнивались с помощью одностороннего дисперсионного анализа (ANOVA, ≤0,05) с последующим тестом Шеффе.
3. Результаты и обсуждение
3.1. Свойства адгезивных смесей
Как показано на рисунке 2, CNF, используемые для приготовления армированных целлюлозой клеевых смесей, имели диаметр в диапазоне от 20 до 65 нм со средним значением 35 нм. Добавление суспензии CNF оказало значительное влияние на реологические свойства и свойства отверждения клеев.Что касается UF, вязкость постоянно увеличивалась с увеличением содержания целлюлозы, хотя содержание твердой смолы в смесях существенно снижалось из-за количества дополнительной воды из суспензии. Гораздо более низкое содержание твердой смолы также может быть причиной более медленного отверждения UF с наполнителем из целлюлозы, что отражается в более продолжительном времени гелеобразования (Таблица 1). В случае MUF увеличение вязкости еще более очевидно, поскольку содержание твердой смолы было одинаковым для чистого клея и адгезива с наполнителем из CNF.Таким образом, можно сделать вывод, что при заданном содержании твердой смолы добавление всего нескольких процентов CNF вызывает существенное увеличение вязкости. Этого следовало ожидать и хорошо согласуется с предыдущими выводами [18, 21, 23]. Поскольку вязкость должна быть достаточно низкой, чтобы клей оставался применимым к деревянной поверхности, быстро увеличивающаяся вязкость ограничивает количество CNF, которое может быть добавлено, до небольшого процента.
3.2. Механические свойства плиты
Из-за структурных различий между ДСП и OSB (рис. 3) результаты обсуждаются отдельно.Средняя плотность всех древесностружечных плит, произведенных в этом исследовании, составляла 0,67 ± 0,03 г · см −3 . В то время как плиты с наполнителем из CNF и чистой UF-смолой показали аналогичную плотность, явные различия между отдельными группами были обнаружены в разбухании по толщине (Рисунок 4). Плиты, приготовленные с UF-1% CNF, продемонстрировали меньшее набухание по сравнению с неармированным эталоном. Что касается внутреннего скрепления, эта группа показала примерно на 10% более высокие значения (0,68 ± 0,10 МПа), чем эталонные плиты (0,62 ± 0,10 МПа).Кроме того, прочность на изгиб увеличена с 18,4 ± 2,0 МПа до 19,5 ± 2,7 МПа. Наиболее очевидные улучшения были достигнуты в механических свойствах трещин. Энергия разрушения увеличилась на 20%, а вязкость разрушения даже на 28% за счет добавления 1 мас.% Целлюлозы. В последнем случае улучшение также является значительным в статистическом смысле (ANOVA, ≤0,05). В отличие от предыдущего исследования [23], в котором более высокая изменчивость значений энергии разрушения была обнаружена для древесных адгезионных связей, армированных CNF, в настоящей работе этого не происходит.В целом добавление целлюлозы не повлияло на изменение механических свойств картона. В то время как древесностружечные плиты с UF-1% CNF обычно превосходили эталонные плиты, обратный эффект наблюдался для плит с UF-3% CNF. Эта группа показала значительно худшие механические свойства и механические свойства разрушения. Предполагается, что это ухудшение не вызвано напрямую более высоким содержанием CNF, но может быть объяснено длительным временем высыхания склеенных древесных частиц перед горячим прессованием.Поскольку большая часть воды, первоначально содержащейся в клеевой смеси, была удалена во время сушки, поверхность частиц высохла почти полностью, что привело к заметному снижению холодного склеивания и, вероятно, уменьшению когезии древесных частиц в готовой плите. Кроме того, в течение 12 часов сушки могло произойти незначительное затвердевание клея. Следовательно, можно сделать вывод, что, хотя содержание CNF в 1% лучше всего работало в этом исследовании, это не обязательно является общим оптимумом. Механические свойства картона могут быть дополнительно улучшены за счет использования более высокого процентного содержания CNF.Как указано выше, постоянно увеличивающаяся вязкость является ограничивающим фактором в этом отношении. В настоящей работе клеевые смеси содержали значительное количество воды, чтобы их можно было распылять, что, в свою очередь, создавало проблемы, связанные с сушкой частиц.
Как и для древесностружечных плит, армирование целлюлозой не повлияло на плотность образцов OSB, но оказало статистически значимое влияние на их набухание и механические свойства, как показано на рисунке 5.Общее разбухание по толщине как армированных, так и неармированных образцов OSB превышает 40% и поэтому находится на очень высоком уровне, особенно при пороговых значениях согласно EN 300 [30], то есть 25% для OSB 1 и 12% для OSB 4, учитываются. В некоторой степени это можно объяснить сравнительно высокой плотностью картона 0,77 ± 0,03 г · см -3 , поскольку набухание по толщине древесных плит обычно положительно коррелирует с плотностью картона [31–33].Однако добавление 1 мас.% Целлюлозы приводит к уменьшению набухания. ANOVA (≤0,05) выявил значительные улучшения производительности для всех испытанных механических параметров и механических параметров разрушения. Прочность внутреннего скрепления увеличилась с 0,51 ± 0,09 МПа до 0,60 ± 0,10 МПа, а прочность на изгиб — с 50,8 ± 5,7 МПа до 59,0 ± 6,1 МПа, что в обоих случаях равно увеличению на 16%. Энергия разрушения и вязкость разрушения увеличились на 25 и 28% соответственно.
4. Выводы
При заданном содержании твердой смолы клеи с наполнителем из CNF обычно демонстрируют существенно более высокую вязкость, чем соответствующие клеи без целлюлозы, что ограничивает уровень добавления CNF.Механические характеристики изготовленных в лаборатории древесностружечных плит и панелей OSB могут быть значительно улучшены, в то время как содержание CNF в 1 вес.% Дает наилучшие результаты. Добавление целлюлозы в первую очередь улучшило энергию разрушения и трещиностойкость плит, что указывает на то, что панели на основе древесины можно существенно упрочнить с помощью клея с наполнителем из CNF. Что касается типа панели, то усиление CNF для OSB работает лучше, чем для древесно-стружечных плит. Очевидно, что комбинация порошкообразного клея MUF и древесных частиц большего размера лучше всего подходит для достижения оптимального армирующего эффекта.
Благодарности
Авторы выражают благодарность за финансовую поддержку Австрийскому научному фонду (FWF) в рамках гранта P22516-N22. Большое спасибо Александру Клинглеру и Еве-Мариеке Лемс за их поддержку в производстве деревянных панелей и Майклу Оберсрибнигу за то, что они сделали снимки AFM. Они также хотели бы поблагодарить Иоганна Мозера (Dynea Austria GmbH) за предоставленные древесные частицы и клеи.
Производство древесностружечных плит из жмыха сахарного тростника и молочайшего сока
Моисей Г.Ньянгау 1 , Алекс М. Муумбо 1 , Чарльз М. М. Ондики 2
1 Кафедра машиностроения и мехатроники, Технический университет Кении, Найроби, Кения
2 Кафедра машиностроения и мехатроники, Мультимедийный университет Кении, Найроби, Кения
Для корреспонденции: Моисей Г.Ньянгау, Кафедра машиностроения и мехатроники, Технический университет Кении, Найроби, Кения.
Электронная почта: Copyright © 2019 Автор (ы). Опубликовано Scientific & Academic Publishing.
Эта работа находится под лицензией Creative Commons Attribution International License (CC BY).
http://creativecommons.org/licenses/by/4.0 /Аннотация
При переработке сельскохозяйственных продуктов, таких как сахарный тростник и кукуруза, остается много сельскохозяйственных отходов. Жмых сахарного тростника — один из таких продуктов. Когда эти отходы разлагаются, они производят метан, а при сжигании выделяют углекислый газ, оба газа загрязняют окружающую среду и способствуют глобальному потеплению.Это исследование было направлено на изучение альтернативного использования жмыха сахароперерабатывающей промышленности и при прямом жевании сахарного тростника. Растущий спрос на мягкие плиты в строительной отрасли представляет угрозу для лесного покрова, поскольку это крупнейший источник сырья. Используемые синтетические связующие являются дорогостоящими и способствуют ухудшению состояния окружающей среды из-за выбросов формальдегида мочевины (UF) и фенолформальдегида (PF). Исследование заключалось в производстве плит B-E с использованием жмыха сахарного тростника и сока молочайшего, а также в определении их механических и физических свойств.Предел прочности на изгиб составил 0,66 Н / мм 2 , предел прочности при растяжении 0,18 Н / мм 2 , набухание по толщине 9,7% и водопоглощение 6%. Когда эти свойства сравнивались с соответствующими значениями, указанными в Стандарте Кении для древесноволокнистых плит (KS 2706-2: 2017), было обнаружено, что плиты подходят для ненесущих применений, таких как изоляция и акустика.
Ключевые слова: Доска багасса- молочай, доска B-E
Процитируйте эту статью: Моисей Г.Ньянгау, Алекс М. Муумбо, Чарльз М. М. Ондиеки, Производство древесностружечных плит из жмыха сахарного тростника и сока молочайшего, Международный журнал композитных материалов , Vol. 9 No. 1, 2019, pp. 1-6. DOI: 10.5923 / j.cmaterials.201
.01. 1. Введение
- Экономика Кении во многом зависит от сельского хозяйства. Переработка сельскохозяйственной продукции приводит к образованию отходов, которые в основном удаляются, в первую очередь из жома сахарного тростника.Когда эти отходы разлагаются, они производят метан, а при сжигании выделяют углекислый газ, оба газа загрязняют окружающую среду и способствуют глобальному потеплению [1]. Жевание сахарного тростника — обычная практика в кенийском обществе. В процессе жевания отходы сахарного тростника разбросаны по улицам в большинстве городских и сельских районов, что вызывает экологические и медицинские проблемы. Молочай — это доступное на местном уровне дерево, сломанные ветви которого дают белый сок, обладающий связывающими свойствами, которые можно использовать для связывания отходов сахарного тростника. Оджуок , как традиционно называют в Ньянзе, представляет собой естественную растительность в большей части Кении, которая практически не используется в хозяйственных целях. Целью этого исследования было изучение альтернативы традиционным древесным волокнам и синтетическим связующим путем использования жмыха сахарного тростника в качестве натурального волокна, которое использовалось ранее [2], и сока молочай молочай в качестве естественного связующего для производства древесно-стружечных плит. Плиты используются во внутренних частях транспортных средств, самолетов и зданий [3]. Основным источником используемого волокна является древесина, но сокращение лесного покрова в мире вызывает серьезную озабоченность как на национальном, так и на международном уровне, поскольку вызывает глобальное потепление и отрицательно влияет на климатические условия.Это, следовательно, требует поиска альтернативных источников волокна для производства древесностружечных плит. Обычно используемыми связующими являются карбамидоформальдегид и фенолформальдегид, оба из которых являются синтетическими. Оба они дороги [4] и дают выбросы по мере старения и способствуют глобальному потеплению [5]. Они связываются посредством изменения состояния во время нагрева, плавления и затвердевания, следовательно, требуют высокой мощности [6]. Основной целью этого исследования было использование жома сахарного тростника и сока молочай молочай для производства плит Багасса-молочай (B-E).Были произведены плиты из багассы-молочай (B-E), определены механические и физические свойства полученной плиты (B-E), а результаты сопоставлены со стандартом Кении KS 2706-2: 2017.
2. Методика
2.1. Материалы и методы
- Сырье, используемое для изготовления древесностружечных плит в этом исследовании, было получено из округа Найроби. Сахарный тростник был получен из округа Кисии, а растение молочай — из Руиру-Кения, где оно используется для ограждений.
На рисунке 1 показан продавец сахарного тростника в поместье Сантон в городе Найроби, что является сценарием со всеми поместьями в городе Найроби. Получить отходы сахарного тростника очень легко, поскольку они не используются в хозяйственных целях в городе. Сахарный тростник является источником клетчатки, используемой в этом исследовании, и уже использовался в прошлом с подтвержденными результатами [7].Рисунок 1 . Торговля сахарным тростником клиентам и оставшиеся запасы
Часто можно встретить отдельные дома, огороженные молочайом, в то время как сахарный тростник является популярной культурой, выращиваемой как в больших, так и в малых масштабах в различных частях страны. На рисунке 2 показан образец того, что можно найти в Найроби и во многих частях страны. Сахарный тростник был куплен, разрезан на части и передан сотрудникам университета для пережевывания; это произвело четыре килограмма жмыха.Его оставили сушиться естественным путем в течение трех недель, уменьшив вес до трех с половиной килограммов, а затем раздавили на самодельной фрезерной машине для кукурузы, но без сита.Рисунок 2 . Молочай и сахарный тростник в городе Найроби, поместье Сантон.
Листовые части стеблей молочая были разрезаны и выдавлены на прокатном станке в сварочной мастерской Технического университета Кении. Сок отбирали контейнером под машиной до тех пор, пока он не стал подходящим для образования мягкой плиты.Всего было собрано три литра. Во время экстракции из 2,24 кг молочайа образовалось 280 мл сока. Багасса была взвешена до различных количеств с помощью весов и помещена в блендер. Затем с помощью мерного стакана отмерили различные количества связующего и добавили в блендер. Затем использовали ручной блендер для их гомогенного смешивания. Затем эту смесь разделили на равные части и вручную поместили в прямоугольную формовочную коробку на опорном элементе гидравлического пресса.После обеспечения равномерного уровня в формовочном боксе и центрального положения формовочного бокса с помощью привода гидроцилиндра была включена гидравлическая система и прессование продолжалось до тех пор, пока материалы не были сжаты до толщины 15 мм. Плотность экстрагированного сока молочайшего была определена по массе и объему экстрагированного и составила 982,14 кгм -3 ; плотность рассчитывалась по формуле (плотность = масса / объем).Рисунок 3 . Экстракция сока молочай молочай с использованием листопрокатной машины.
Операция уплотнения проводилась в гидравлической лаборатории Технического университета Кении. Материалы были заполнены в прямоугольную формовочную коробку, которая была осторожно расположена в центре привода гидроцилиндра с прямоугольной прижимной пластиной на ее конце, как показано на рисунке 4. Гидравлическая система была включена, и цилиндр активизировался на такте вытяжки. на пониженной скорости с помощью регулятора переменной скорости.Рисунок 4 . Размещение формовочной коробки на гидравлическом прессе готовность к работе
Материалы были сжаты до 15 мм в толщину, как показано на рис. 5, что является важным этапом формования и прессования при производстве ДСП [8]. При производстве древесностружечных плит было замечено, что после сброса давления гидравлического цилиндра сформированные древесно-стружечные плиты из жома и молочайного дерева отскочили. Это потребовало использования ограничивающей статической нагрузки на влажные древесностружечные плиты, чтобы они не подпрыгивали.Формовочная коробка была сделана так, чтобы иметь два штифта в диагональных углах для облегчения отсоединения, чтобы избежать помех при изготовлении влажного образца.Рисунок 5 . Формовочная коробка с контрольными отверстиями сбоку
На рисунке 6 показана технологическая последовательность действий в этом исследовании, которое отличается от исследования Рональда, 1972 г., в котором было удаление поверхностной пленки, горячее прессование и использование синтетических связующих [9]. Багасса и молочай получали и обрабатывали отдельно, а затем хранили.В ходе исследования были также спроектированы и изготовлены блендер и холодный пресс. Затем багасса смешивалась с соком молочай молочай в смесителе, смесь заливалась в формовочную коробку на определенную глубину и помещалась на опоры холодного пресса, готовые к уплотнению. Материал прессовали до подходящего давления, оставляли под давлением на короткое время, а затем отпускали. Кондиционирование и отверждение уплотненного материала проводилось в естественной среде с некоторой нагрузкой на него после формования. После отверждения была снята нагрузка после формования, рассчитана плотность картона и проведены испытания физико-механических свойств.Рисунок 6 . Технологическая схема производства древесно-стружечных плит 2.2. Образец испытаний
2.2.1. Тесты на набухание по толщине и водопоглощение
Таблица 1 была получена из зарегистрированных данных образцов A1-h2. Увеличение толщины после эксперимента было разделено на исходное значение толщины и преобразовано в проценты.Это записывается в процентах от экспериментального набухания. Стандарт дает процент разбухания по толщине в зависимости от исходной толщины образца. Соответствующие значения толщины приведены в таблице 1. Что касается водопоглощения, увеличение массы образцов через 24 часа было разделено на исходную массу и преобразовано в процент. Это было записано в последнем столбце таблицы 1. Однако кенийский стандарт на древесноволокнистые плиты не дает рекомендуемых значений водопоглощения.Колонка по плотности внесена в таблицу в качестве дополнительной информации об исследуемых образцах. Стандарт, использованный в этом исследовании, — это кенийский стандарт на древесноволокнистые плиты KS 2706-2: 2017.Таблица 1 . Плотность, водопоглощение, экспериментальные и стандартные значения набухания
Гистограмма на рисунке 7 показывает сравнение между значениями набухания, полученными в ходе эксперимента, и значениями, рекомендованными стандартом.Замечено, что некоторые образцы имеют большие отклонения от стандартных рекомендуемых значений. Однако есть те, которые очень близки к рекомендуемым значениям, например F1 и h2. Необходимо провести дополнительные исследования, чтобы показать влияние плотности, соотношения смеси и свойств волокна на набухание по толщине в процентах.Рисунок 7 . Сравнение экспериментальных значений набухания в% по толщине с заданным% набухания по стандартной толщине. 2.2.2. Результаты прочности на растяжение
В таблице 2 приведены экспериментальные значения прочности на разрыв, полученные в Н / мм 2 на универсальной испытательной машине.Они сравниваются со стандартной прочностью на разрыв, рекомендованной в кенийском стандарте для конкретной толщины образца. В измеренных значениях могли быть ошибки, особенно из-за затруднения захвата образцов. Было непросто определить адекватную силу захвата без разрушения образца. Плотность и соотношения смесей приведены в таблице 2, чтобы предоставить дополнительную справочную информацию об исследуемых образцах.Таблица 2 . Плотность, соотношение смеси, экспериментальные и стандартные значения прочности на разрыв
Сравнение экспериментальных и стандартных значений, приведенных в кенийском стандарте KS 2706-2: 2017, показывает довольно большую разницу между экспериментальной прочностью на разрыв и значениями, рекомендованными в стандарт, как показано на рисунке 8. Это в значительной степени объясняется тем фактом, что в обычном способе производства используются, а именно синтетические связующие; Ст.л. и п.ф. Во время производства нагревают при температуре около 150 o ° C, в результате чего UF и PF в процессе связывания становятся термореактивными [10].Сок молочай молочай, используемый в этом исследовании, не подвергается такой трансформации, но имеет геометрию поверхности для адгезии, что является причиной его использования в данном исследовании [11]. Таким образом, полученная здесь прочность зависит от связывания и отверждения при температурах окружающей среды между волокном из жома и связующим молочайным.Рисунок 8 . Сравнение экспериментальной и стандартной прочности на разрыв 2.2.3. Результаты прочности на изгиб
В таблице 3 показаны экспериментальные значения прочности на изгиб, полученные для различных образцов, обозначенных A3-F3.Разница между экспериментальными значениями и стандартными рекомендуемыми значениями огромна и в равной степени связана с типом используемых связующих и процессом их нагрева. Однако ошибки также могли возникнуть из-за того, что в точке приложения нагрузки имело место некоторое сжатие до того, как была определена фактическая прочность на изгиб. Приведенные значения плотности и соотношения смешивания служат для справочной информации об исследуемых образцах.Таблица 3 . Экспериментальная и стандартная прочность на изгиб
Гистограмма, показанная на рисунке 9, показывает сравнение экспериментальной прочности на изгиб выбранных образцов A3-F3 со значениями, рекомендованными в кенийском стандарте образцов, соответствующих по толщине. Синтетические связующие, используемые для изготовления образцов, основанных на стандартных данных, обладают сильным сопротивлением движению молекул, следовательно, высокой прочностью [12]. Это ожидаемый фактор, способствующий расхождению между экспериментальными значениями для природных материалов в условиях температуры окружающей среды и стандартными значениями, полученными с использованием обычного метода.Сок молочай молочай, используемый в этом исследовании, в прошлом использовался в качестве клея для других целей [13].Рисунок 9 . Сравнение экспериментальной и стандартной прочности на изгиб 2.2.4. Выводы
- В таблице ниже показаны важные результаты, полученные в ходе испытаний.
Таблица 4 показывает сводку отобранных образцов, плотность которых оказалась близкой к рекомендованному значению 230 Кг / м 3 для мягких плит [14].На этих образцах плит B-E были проведены различные испытания, значения которых указаны, потому что все испытания, проведенные на водопоглощение, набухание по толщине, а также прочность на растяжение и изгиб, носят разрушительный характер [15]. Испытание на прочность на изгиб проводилось на образцах A3, B3, D3 и E3. Результаты этих испытаний показывают большое расхождение со стандартными значениями, указанными в кенийском стандарте KS 2706-2: 2017. Образцы B2, D2 и E2 прошли испытание на прочность на разрыв, результаты которого при сравнении со значениями, приведенными в кенийском стандарте KS 2706-2: 2017, довольно хорошо соотносятся, хотя и ниже, чем стандартные значения.Образцы E1, F1 и h2 прошли испытание на набухание по толщине, результаты которого хорошо сопоставимы с данными, приведенными в стандарте KS 2706-2: 2017. Соотношения смесей, нагрузки после формовки и количество загруженных дней также были даны, чтобы предоставить справочную информацию об их производственном процессе. Хотя значения прочности по результатам этого исследования низкие, плиты могут использоваться для ненесущих нагрузок, таких как изоляция и акустика, учитывая, что диапазон плотностей, полученных в ходе исследования, имеет высокий коэффициент шумоподавления [16].Ранее некоторые плиты, используемые для акустических и изоляционных целей, были изготовлены из жома [17]. Таким образом, это исследование было важным, потому что если производство картона BE будет коммерциализировано, это принесет огромную экономическую выгоду, поскольку молочай, естественно, доступен в изобилии при небольшом или нулевом экономическом использовании, в то время как жмых доступен как отходы сахароперерабатывающей промышленности в Кении. . Поскольку известно, что свойства натуральных волокон значительно различаются в зависимости от таких факторов, как диаметр и структура волокна [18], можно рекомендовать дополнительные исследования их влияния на характеристики картона молочай из жома, полученные в ходе этого исследования.Таблица 4 . Сводка основных результатов экспериментальных данных по изготовленным платам BE 3. Выводы
- Волокно из жмыха сахарного тростника и связующее из сока молочайшего успешно использовалось для производства плит молочай из жома в естественных условиях и при температуре окружающей среды. Успешно налажен процесс производства плит B-E, который отличается от обычного нагрева и использования синтетических связующих. Определены физико-механические свойства образцов плит Б-Э. Эти; испытание на водопоглощение, испытание на набухание по толщине, испытание на прочность на разрыв и испытание на прочность на изгиб.Значения, полученные в этих испытаниях, сравнивались со значениями, рекомендованными в Стандарте Кении для древесноволокнистых плит, различия в значениях прочности которых позволяют предположить, что полученные образцы плит B-E могут подходить только для приложений, не несущих нагрузку. Когда значения плотности, полученные, как показано в этом исследовании, сравниваются с табличными значениями коэффициента шумоподавления, они дают представление о пригодности для использования в приложениях для шумоподавления. В то время как жмых использовался для производства древесно-стружечных плит в прошлом, а сок молочай молочай использовался для других задач склеивания, теперь было продемонстрировано, что их можно использовать для производства плит для повседневного применения.
БЛАГОДАРНОСТИ
- Моя особая благодарность Всемогущему Богу за Его неизменную Любовь, Заботу и Милость ко мне до сих пор. Во-вторых, моим научным руководителям: профессору Алексу Муумбо и профессору Чарльзу Манассе М. Ондики за их руководство на протяжении всего периода исследования. Несколько человек, техников и технологов поддержали меня, чтобы я добился лучших результатов на протяжении всего периода исследования. В их число входят г-жа Алиса Мутаи, г-н Мачанджа из сварочного цеха и г-н.Булива из гидравлической лаборатории, где проводились эксперименты в Техническом университете Кении. Поддержка, которую я получил от Мультимедийного Университета в лаборатории материалов под руководством г-на Мусиоки, технического специалиста, очень ценится. Моральная поддержка и воодушевление, которые я всегда получал от моей дорогой жены Зиппоры Керубо для солдат, очень ценятся. Это исследование не могло бы пройти так гладко, если бы спонсоры DAAD не оплатили мне все гонорары и другие операционные расходы. Я не забуду роль, которую сыграл мой наставник, ныне покойный профессор Уилсон О.Огола, да упокоится его душа в вечном мире.
Ссылки
Котировки на оборудование для производства мебели из древесно-стружечных плит[1] Mumias Sugar CO. Ltd. (2006). Проектно-конструкторский документ. Найроби: Механизм чистого развития РКИК ООН. [2] Научно-исследовательский институт переработки сахара. (2005). Сахар и другие подсластители. Исследования переработки сахара, 2-12. [3] Олусегун, Д. С. (2015). Натуральные волокна. Журнал исследования и разработки минералов и материалов, 1-3. [4] Wuhan LVYIN Chemical Co. Ltd. (21 октября 2017 г.). Alibaba.com. Получено с международного сайта Alibaba.com: http://www.wuhan-ivyin.com. [5] Урсула и др. (2007). Натуральные связующие. В Урсуле и др., Молекулярная биотехнология древесины (стр. 347-359). Геттинген: Исследовательские ворота. [6] Сорен, Х. (2010). Производство соломенной мдф и древесноволокнистых плит. Fiber Science and Communication Network, 32. [7] Asokan, P., Firdoosus, M., & Sonai, W. (2012). Свойства и потенциал биокомпозитов. Институт перспективных материалов и процессов, Индия, 254-255. [8] Матоке, Г., Овидо, С., и Ньяанга, Д. (2012). Влияние методов производства и соотношения материалов на физические свойства композитов.Американский международный журнал современных исследований, 1-3. [9] Рональд А. С. (1972). ДСП из багассы: исследование производства и инвестиционный анализ. Массачусетский технологический институт, 37-57. [10] Пол, А. М., Эммануэль, К. Э., Е. К., Г. и Дэвид, Е. А. (2014). Сравнительное исследование фенолформальдегидных и карбамидоформальдегидных древесностружечных плит из древесных отходов для сохранения окружающей среды. Международный журнал научных и технологических исследований, том 3, выпуск 9, 54. [11] Омаре, Дж. И Фрайдей, Э. (2010). Фитохимический состав, биоактивность и ранозаживляющий потенциал экстракта листьев молочай Heterophylla (Euphorbiaceae). Международный журнал фармацевтических и биомедицинских исследований, 54-58. [12] Рольф К. (2011). Лазерная сварка пластиков. В К. Рольф, Материальные свойства пластмасс (стр. 13). Verlag GmbH: Wiley-VCH Verlag GmbH & CO. KGA. [13] Юлиус, М., & Патрик В. Д. (2011). Дерево чудес: текущий статус доступных знаний. Научные исследования и очерки, 4909-4910. [14] Acara Concepts LTD. (2017, 21 сентября). Мягкая доска Стандарт. Получено с веб-сайта Acara Concepts LTD: www.acaraconcepts.com. [15] I.Y, S., V.S, A., SHUAIBU, L., & SHANGALO, M. (2013). Разработка экологически чистых композитных древесностружечных плит с использованием частиц рисовой шелухи и гуммиарабика.Журнал материаловедения и инженерии с передовыми технологиями, 79-82. [16] Ананд, Н., М.К. Киран, и Варадараджулу, К. (2017). Влияние плотности на коэффициент звукопоглощения древесноволокнистых плит. Открытый журнал акустики, 6-8. [17] Indiamart. (2017, 25 мая). мид-лан досок. взято с mid-lanBoards: https://2.imimg.com/data2/KA/BH/MY-/plane-softboard.pdf [18] Thomas, S., Пол, С., Потан, Л., и Дипа, Б. (2011). Натуральные волокна. Целлюлозные волокна, 4-6. в режиме реального времени, цены последней продажи -Okorder.com
Сведения о товаре:
Стальной материал :: Q235B Цвет :: кремово-белый Метод управления :: ПЛК Цилиндр :: 320 * 6 шт. Сертификация:: ISO9001, CE Описание продукта:
Оборудование для производства мебели из ДСП
Деталь продукта
Оборудование для производства мебели из ДСП применяется для производства панелей / мебели или дальнейшей обработки древесины для ламинирования декоративной бумаги на ДСП , Плита МДФ с применением передовых технологий.
Оборудование для производства мебели из ДСП доступно в соответствии с вашими требованиями !
Характеристики
Оборудование для производства мебели из ДСП используется для производства ламината с широким спектром текстур, от плоской поверхности до легкого / глубокого тиснения или эффектов синхронной гравировки.
Он также подходит для ламинирования декоративной бумаги, пригодной для носки бумаги и балансировочной бумаги с обеих сторон плиты HDF для производства ламината.
Приложения ( Оборудование для производства мебели из ДСП )
Оборудование для производства мебели из ДСП для ламинирования мебельной плиты.
— Облицовочные материалы — меламиновая бумага, шпон и т. Д.
— Основные плиты — МДФ / ХДФ / ДСП.
Выставка продуктов
Упаковка и отгрузка
Упаковка: Оборудование для производства мебели из ДСП будет упаковано в соответствии с международным стандартом упаковки для пресса
Доставка: около 15 дней после получения депозита
Сертификаты
FAQ
Q: Какие материалы используются в вашей продукции?
A: Основной материал — сталь, масляный цилиндр и другие.Мы также можем выбрать материал по требованию заказчика.
4. Q: Как я могу узнать больше о прессе?
A: Для нас большая честь отправить вам несколько фотографий и видео о нашей машине.
akson-quick.ru © 2019