Технология производства газобетона

Строительство домов из газобетона очень популярно, благодаря тому, что данный тип строительного материала имеет хорошие характеристики и сравнительно не высокие цены и за долгую историю использования газобетона, он получил много отзывов.
Технология производства газобетона, состоит из нескольких ключевых этапов. Мы опишем технологию производства блоков газобетона, расскажем про необходимое оборудование, которое используется технологией производства газобетон.
Связанные статьи:
Технология производства газобетона
Первый этап: подготавливаются формы для заливки блоков
Форма для блоков — это как правило прямоугольная конструкция, которая имеет 4 борта и дно. Все детали надежно соединены болтами. Подготовленные формы, обрабатываются внутри маслом (как правило любое машинное) и уже готовы к заливке смесью, готовку которой мы рассмотрим на следующем этапе.
Второй этап: Готовка смеси для заливки газобетонных блоков
Материалы и компоненты требуемые для приготовления смеси
Исходными компонентами являются: цемент, известь, песок, теплая вода, газообразователь. Песок может быть обычный или же карьерный, требуется отсев максимальный размер до 2.1 единиц, содержание глины подобных веществ не более 7%. Цемент — портландцемент марки М — 400, М — 500.
Газообразователь — это алюминиевая паста «Газобетолайт».
Для регулировки усадки и скорости нарастания газомассы используется щелочная добавка.
Соотношение компонентов, мас в %:
Портландцемент 51-71
Алюминиевая паста 0,04-0,09
Известь 1-5
Песок 20-40
Вода 0,25-0,8
Для того что бы приготовит газобетонную смесь раздельно готовят:
алюминиевую суспензию, путём разведения в воде алюминиевой пасты в
соотношении вода: алюминиевая паста = 10:1 ( перемешивать при разведении непрерывно, это позволит предотвратить расслоение состава) .
Вода, которая понадобится при готовке алюминиевой суспензии и является частью
общего количества воды, которое нужно для изготовления газобетонной смеси.
Оборудование для производства газобетона

Технология производства газобетона
В смеситель подается нужный объем воды, который сразу же начинает непрерывно перемешиваться. После чего, в этот же смеситель, с водой начинает добавляться поочередно: песок, цемент, известь и самой последней добавляется алюминиевая суспензия. Каждый добавленный компонент данной смеси, после добавления хорошо смешивается примерно в течение 30 секунд.
Третий этап: Заливка формы
Полученная газобетонная смесь заливается в предварительно подогретые до 35-40°С формы (если используется монолитное строительство, то разумеется в опалубку ), в которых и происходит окончательное формование изделий. После того как газобетонная смесь будет залита, можно выровнять верхний слой натянутой и закрепленной струной, после чего накрыть сверху теплоизоляционным материалом (плитами), это необходимо для снижения потерь тепла, которое необходимого для стабильного протекания процесса поризации и нормального протекания реакций гидратации цемента и твердения газобетонных изделий.
Связанные статьи: Этапы строительства дома из газобетона
Сушка блоков
Примерно спустя 1,5-2 часа, изделия приобретут нужную
Так же используются варианты заливки не отдельных блоков, а целой массы, которая после сушки разрезается на блоки.
Отличие автоклавного газобетона от не автоклавного газобетона
- автоклавный газобетон, набирает прочность при высоком давлении и высокой температуре в спец печах(сушильных камерах), которые называются — автоклав
- не автоклавный газобетон, твердеет в естественной среде, при атмосферном давлении или используется тепловлажностная обработка с использованием теплового воздействия
На сегодняшний день технология производства газобетонных блоков интересует не только людей, планирующих построить свой дом, но и предпринимателей из России, Казахстана, Узбекистана и других стран СНГ, которые решили заняться бизнесом на производстве газобетона.
Почему именно газобетон? Во-первых, благодаря высоким показателям прочности и теплоизоляции, спрос на этот материал постоянно растет. Во-вторых, технология изготовления газоблоков очень проста: вам не потребуются особые знания и умения, чтобы стать производителем газобетона.
Предлагаем подробнее ознакомиться с технологией производства газоблоков.
Неавтоклавный газобетон: технология и требования
1. Производственное помещение обязательно должно быть светлым и хорошо вентилируемым. Требуемая температура воздуха в здании – не менее 20С.
2. Особое внимание нужно уделить отсутствию сквозняков в месте подъема газобетонной смеси в формах. Наличие сквозняка может повлиять на весь процесс производства (особенно в момент подъема смеси).
Если температура в цехе меньше 20С, то необходимо добиться температуры от 20С как минимум локально (в местах подъема смеси в формах). В линиях конвейерного типа необходимо разместить камеру предварительного прогрева и установить ее от поста заливки до поста резки. Оптимальная температура в камере предварительного прогрева – 35-40С.
С подробным рецептом газобетона можно ознакомиться здесь.
Технология изготовления газобетона: пошаговая инструкция
Шаг 1. Заливаем воду в газобетоносмеситель (температура воды 45-60С).
Шаг 2. Включаем смеситель и засыпаем цемент.
Шаг 3. Добавляем химические компоненты: каустическую соду (NaOH) и сульфат натрия (Na2SO4) и засыпаем песок.
Шаг 4. Перемешиваем все компоненты в течение 3-5 минут.
Шаг 5. Добавляем приготовленную суспензию алюминиевой пудры или отмеренную массу алюминиевой пасты (в сухом виде) и перемешиваем 20-30 секунд.
Шаг 6. Пока готовится смесь, форму для заливки нужно подкатить к смесителю. К моменту слива смеси формы нужно почистить, собрать и смазать. После получения готовой смеси нужно выключить смеситель и слить раствор.
Шаг 7. После слива раствора аккуратно перемещаем форму в камеру предварительного прогрева.
Шаг 8. После набора необходимой структурной прочности (1-3 часа) выкатываем форму из камеры предварительного прогрева, срезаем горбушку, снимаем борта и разрезаем массив на отдельные блоки.
Шаг 9. Разрезанный массив перемещаем в камеру окончательной выдержки для набора прочности. Температура выдержки – 50-60С.
Шаг 10. После окончательного набора прочности (в течение 6-8 часов) готовые блоки укладываются на поддон, упаковываются стрейч пленкой и отгружаются на склад.
Технология производства газоблоков – это просто!
Как вы уже поняли, технология производства газобетона не сложнее выпечки хлеба или приготовления плова: вам не нужно иметь специальные знания и навыки, чтобы начать производить качественные газобетонные блоки. Кроме того, приобретая оборудование по производству газоблоков, технологи компании АлтайСтройМаш всегда будут на связи и смогут ответить на любые ваши вопросы.
Готовы стать производителем газобетонных блоков?
Подобрать оборудование
Газобетон обладает высокими прочностными и теплоизоляционными характеристиками. Строительный материал является удачным выбором застройщиков в сфере индивидуального и коллективного строительства.
Газобетон
Общая информация о материале
В названии строительного материала, газобетон или автоклавный ячеистый бетон, заложены его характеристики и технологии производства. Он является искусственным камнем, в полости которого расположены воздушные поры, а его изготовление подразумевает обработку сырьевого материала в условиях автоклава. Для газоблоков характерны сберегающие характеристики, которые обеспечиваются за счет пористой структуры. Они имеют небольшой вес, что выделяет их на фоне кирпичей и других видов строительной керамики.
Строительный материал может быть использован для возведения несущих конструкций сооружения или его внутренних перегородок. Он не подходит для промышленных объектов и высотных зданий, однако отлично зарекомендовал себя в сфере индивидуального строительства. Использование газоблоков обеспечивает оперативное строительство, по причине того, что они имеют большой размер. Их легкость позволяет сократить расходы на закладку фундамента, поскольку ему не нужно претерпевать большие нагрузки.
Состав
Уникальные характеристики строительного материала обусловлены его составом.
Сырьем для его изготовления являются цемент, кварцевый песок и алюминиевая пудра, выполняющая роль газообразователя. Для придания специфичных свойств газоблокам, некоторые производители в состав добавляют дополнительные ингредиенты, такие как известь, зола и гипс.
Цеховое производство
Сырье
Газобетон изготавливается на основе сухих компонентов, в смесь которых добавляется вода, с температурой не ниже 45°С. Такие условия обеспечивают быстрое твердение блоков и их прочности. Соблюдение технологии способствует увеличению производительности, улучшению качества материала и уменьшению количества используемого сырьевого цемента, поскольку соответствующий температурный режим обеспечивает стимулирование активности сухих компонентов смеси.
В производстве может быть использован карьерный или речной песок с размером зерен до 2 мм. В нем не должны содержаться илистые и глиняные включения. Сырьевой материал может быть заменен шлаком или золой, являющимися отходами металлургического производства. Такое решение производителя сократит его расходы и позволит получить продукцию с меньшей плотностью.
Планируя производство, следует закупать цемент, имеющий маркировку М 400 или М 500. Алюминиевая пудра должна быть марки ПАП-1 или ПАП – 2. Она может быть заменена на специальную пасту или суспензию, что считается более удобным для производства, ввиду упрощения этапа замешивания. Компонент вступает в реакцию в растворе, имеющем щелочной состав, в ходе которой образуется соль алюмината и выделяется водород, обеспечивающий формирование пор.
Соотношение веществ
Резка изделия
Качество строительного материала зависит от правильного подбора соотношения составляющих компонентов. Стандартные рекомендации определены только для газоблоков, изготавливаемых автоклавным способом. В них предусмотрено регламентированное соотношение сырьевых компонентов по отношению к общему объему смеси:
- цемент – 50–70 процентов;
- песок – 20–40 процентов;
- алюминиевый порошок – 0,04–0,09 процентов;
- вода – 0,25–0, 8 процентов;
- известь – 1–5 процентов.
Пример
Для получения одного кубического метра газобетона необходимо взять 90 килограмм цемента, долить до 300 литров воды. В полученную смесь добавить 35 килограмм извести, 375 килограмм песка и 50 грамм алюминиевого порошка. В условиях конкретного производства все значения могут быть скорректированы в соответствии с качественными характеристиками сырьевых материалов.
Оборудование для производства газоблоков
Несмотря на то что технология производства строительного материала не отличается сложностью, без специального оборудования и соблюдения алгоритма действий, невозможно получить газобетон хорошего качества. Для этого, до открытия цеха, необходимо приобрести автоматизированную линию. При ее покупке с завода-производителя или его официального представителя, дополнительно обычно предоставляются консультационные услуги в сфере монтажа оборудования, его настройки и подборе оптимального состава сырьевой смеси. Линия содержит оборудование и устройства:
- печь-автоклав;
- формы;
- передвижные поддоны для транспортировки;
- смесители;
- дозаторы;
- аппарат резки готового изделия.
Каждый составляющий элемент комплекса может быть приобретен отдельно, поэтому при выходе его из строя, восстановить линию не составит труда. Она также может быть сформирована из отдельных устройств, однако при таком решении предпринимателю важно учесть соответствие их параметров, которые позволили бы обеспечить гармоничное взаимодействие всей аппаратуры.
Схема производства
Оборудование для производства газобетонных блоков бывает нескольких типов. При его выборе учитывается планируемая суточная производительность, количество обслуживающего персонала и порядок организации работы.
Для стационарных линий характерна суточная производительность до 60 м3 готовых изделий. Для обеспечения бесперебойной работы, необходимо арендовать или купить производственные и складские помещения, площадью, не меньше 500 м2. Один человек вполне сможет обслужить такую линию, поскольку все операции в ней производятся в автоматическом режиме. Принцип ее функционирования заключается в подаче в стационарно расположенный смеситель сырьевых материалов, в перемешивании их и в заполнении формы смесью с последующим выполнением всех технологических этапов в автоматическом режиме.
При планировании суточной производительности до 150 м3, предпринимателю рекомендуется рассмотреть вариант приобретения конвейерных линий, позволяющих обеспечить оперативное производство строительного материала. Поскольку сроки созревания остаются прежними, необходимо позаботиться об увеличении производственного помещения в отсеке дозревания готовой продукции. Несмотря на то что большинство процессов проводится в автоматическом режиме, для обслуживания устройств понадобится штат работников в минимальном количестве до 8 человек.
Мини-линии актуальны при производстве блоков для реализации собственных потребностей при обеспечении строительных работ, а также при наличии небольшого объема заказов.
На них не получится изготавливать более, чем 15 м3 готовых изделий в сутки. В конструкции стационарно установлены формы, а подвижной частью является смеситель. Преимуществом линии является отсутствие необходимости в больших площадях. На начальном этапе достаточно до 160 м2, поэтому мини-линии пользуются популярностью в качестве стартового варианта.
Упрощенная схема
В сфере частного строительства применяются мобильные установки, с помощью которых можно самостоятельно изготавливать газоблоки. Они продаются в комплекте с компрессором и могут функционировать от бытовой электросети. Их приобретение окупается в кратчайшие сроки, поскольку расходы на строительные работы снижаются на 30 процентов.
Технология производства газобетона
Технология производства зависит от решения производителя относительно вида и характеристики готового изделия.
Газобетон бывает автоклавный и неавтоклавный. Неавтоклавный строительный материал стоит дешевле, поскольку для него характерна хрупкость, а для обеспечения производства материала затрачивается меньше средств, поскольку не нужно приобретать дорогостоящее оборудование- автоклав, оплачивать электроэнергию на его функционирование, а также вкладывать деньги в его содержание. Неавтоклавная технология производства проводится в соответствии с определенным алгоритмом:
- Взвешивание компонентов смеси в соответствии с рецептурой.
- Перемешивание вручную или при помощи специального оборудования.
- Выгрузка в формы.
- Выдержка изделия.
- Извлечение готовой продукции из формы.
В связи с тем, что в результате химических реакций, происходящих в смеси, будет происходить газообразование, формы заполняются только наполовину. Ожидание окончания реакции занимает до четырех часов, за которое компоненты полностью занимают объем формы. После отбора из форм излишек состава, его оставляют на вызревание, которое будет длиться до 16 часов, по истечении которых происходит распалубка и перегрузка на поддоны для набирания отпускной прочности, что длиться три дня. После завершения всех операций, изделие отправляется на склад, однако продавать его можно только через месяц, когда оно наберет марочную прочность.
В бизнес-план производства газобетона следует включить расходы на приобретение профессионального оборудования.
Технология производства на первых этапах работ практически не отличается от безавтоклавного метода. Набирается необходимое количество всех компонентов при помощи дозаторов, загружается в смеситель и перемешивается. Для выполнения этой задачи допускается использование бетономешалки. Через 15 минут после окончания смешения исходных ингредиентов, вводится алюминиевый порошок, являющийся газообразователем. Вещество вступает в реакцию с базовой смесью без автоклава.
Смесь сырьевых компонентов разливают по формам и выдерживают 6 часов, после чего проводится нарезка газоблоков, которые впоследствии должны набрать плотность на протяжении 18 часов. После завершения базовых операций, проводится автоклавирование. Сформированные блоки газобетона загружаются в герметичную камеру печи, в которой при высокой температуре каждый блок обрабатывается водяным паром под давлением до 12 кг/см2.
Неавтоклавное изделие сушится в естественных условиях. Автоклавная продукция не требует сушки, однако ее все равно нужно выдержать месяц до набора прочности.
Важным этапом производства обеих видов газобетона, является сохранение целостности в процессе транспортировки к потребителю. Для реализации этой задачи необходимо готовое изделие упаковать в термоусадочную пленку и транспортировать на деревянных поддонах.
Вконтакте
Одноклассники
Google+
Газобетон, как разновидность ячеистых бетонов, является популярным строительным материалом за счет своих существенных преимуществ. Подразделяется он на два вида: автоклавный и неавтоклавный. Применение второго вида газобетона позволяет использование его при монтаже монолитных сооружений. Неавтоклавный газобетон — относительно недорогой материал, применяемый для возведения несущих стен и перегородок.
Сферы использования
Неавтоклавные газобетоны применяются при возведении в малоэтажных зданиях и сооружениях несущих стен и перегородок. Применение неавтоклавного ячеистого бетона возможно при строительстве зданий и сооружений с большим количеством этажей в качестве наполнителя для каркасов стен из железобетона.
Использование газобетонов актуально при строительстве жилищных, промышленных и коммерческих построек. При строительстве малоэтажных зданий используется для наружных стен за счет своей самонесущей способности. Применяется ячеистый бетон с неавтоклавной технологией для армирования, теплоизоляции строительных элементов.
Вернуться к оглавлениюСостав
В неавтоклавном газобетоне имеются следующие составы:
- наполнители в виде чистого песка с включением золы, мела или гипса. Песок не должен содержать ил и глину;
- портландцементы;
- алюминиевая пудра для порообразования;
- хлорид кальция для ускорения процесса затвердевания, а также другие различные химические добавки, применяемые для регулировки газообразования и быстроты набора прочности;
- вода, преимущественно из поверхностных источников без содержания соли и мягкой жесткости.
Плюсы и минусы
Неавтоклавному газобетону присущи следующие преимущественные характеристики:
Неавтоклавный газобетон имеет следующие недостатки:
-
Недостатки газобетона.
прочность меньше, чем у автоклавного ячеистого бетона и зависит от пропорций цемента;
- происходит снижение свойств теплоизоляции при заполнении водой пористой структуры материала, что способствует применению гидроизоляции;
- существует риск приобрести некачественную продукцию у производителей, которые экономят на материалах и технологии изготовления;
- происходит постепенное разрушение ячеистого бетона в результате механических нагрузок, что обязывает использование армопоясов в местах с наибольшей нагрузкой;
- усадка газобетона относительно большая и обязывает оттягивать с окончательными отделками поверхности;
- отсутствует возможность в эксплуатации блоков сразу после их изготовления.
Технология производства
Технология изготовления неавтоклавного газобетона состоит из следующих этапов:
- подготовка к заливке форм;
- заливка раствора;
- резка на блоки;
- выдержка раствора до набора его прочностных характеристик;
- сортировка и упаковка продукции.
Подготовка и заливка смеси
Начинают изготовление ячеистого бетона с подготовки компонентов смеси. Для этого берут цемент, известь, газообразователи, гипс и при необходимости специальные добавки для ускорения процесса застывания и увеличения прочности материала. Все компоненты в нужных пропорциях погружают в автоматизированный смеситель, в котором происходит перемешивание цемента, извести и остальных ингредиентов до консистенции, напоминающей сметану.
Перемешивание компонентов продукции происходит по заданной программе. Готовый раствор разливают в емкости наполовину, где и происходит образование пористой структуры газобетонных изделий, и оставляют затвердевать в естественных условиях. Такой способ изготовления существенно сокращает затраты на электроэнергию и транспортные услуги.
Вернуться к оглавлениюРезка материала на блоки
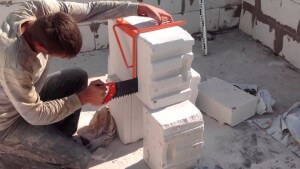
После заливки раствора выжидают полтора часа, при необходимости два часа, до приобретения его прочностных характеристик. Как только раствор приобрел распалубочную прочность, приступают к резке материала на плиты, блоки или панели.
Разрезают массив газобетона на различные формы и геометрические размеры. При небольших объемах работ применяют ручное оборудование, при больших – механическое, в виде электрических инструментов. Если отсутствует возможность приобретения специального инструмента для резки, изготавливают собственноручно ножовку, однако срок службы ее невелик. Профессиональные инструменты для резки – это рубанок, резец и штроборез.
Вернуться к оглавлениюВыдержка
После заливки емкости раствором срезают образовавшиеся верхушки с помощью металлической струны. После этого оставляют газобетонные блоки для выдержки на протяжении двенадцати часов. Оставляют заполненные емкости в помещении или на площадке с предусмотренным накрытием. Важно обеспечить защиту от проникновения прямых солнечных лучей и перегрева залитого раствора. Попадание атмосферных осадков на застывающую массу также нежелательно.
По окончании выдержки блоки извлекают и оставляют досыхать еще на несколько часов. Такая необходимость обусловлена набором прочности, нужной для их складирования. Газобетон достигнет максимальной прочности спустя двадцать восемь дней.
Вернуться к оглавлениюСортировка и упаковка
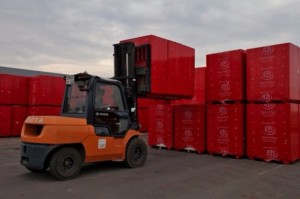
Сортируют газоблоки тремя способами, с помощью которых получают продукцию нужного типоразмера:
- формовка и сушка в емкостях кассетного типа;
- заливка раствора в емкости особой конструкции;
- заливка раствора в металлические емкости без внутренних перегородок.
Упаковку изделий осуществляют после окончательного затвердевания газоблоков. Укладывают их на поддоны и упаковывают с помощью термопленок, после чего перемещают на склад.
Вернуться к оглавлениюВывод
Усовершенствование неавтоклавного газобетона происходит постоянно и благодаря этому его применение становится целесообразней, чем использование автоклавного. Но перед выбором строительного материала и его технологического изготовления, важно обратить внимание на преимущества и недостатки газобетонов. Ведь при необходимости использования материала с высокими прочностными характеристиками, к сожалению, неавтоклавный ячеистый бетон не годится. Зато он отлично подойдет для быстрого возведения малоэтажных построек.
Газобетон – это легкий искусственный материал, полученный в результате твердения поризованной смеси, состоящей из гидравлических вяжущих веществ, тонкомолотого кремнеземистого компонента, воды и добавки газообразователя.
Для изготовления изделий из ячеистого бетона можно применять различные сырьевые материалы, но наибольшее распространение получили следующие:
— портландцемент ПЦ 400 – ПЦ 500, без активных минеральных добавок;
— известь негашеная кальциевая с содержанием CaO не менее 70%;
— кварцевый песок с содержанием кварца SiO2 не менее 85%, а глинистых примесей не более 3%;
— газообразователь алюминиевая пудра (паста) с содержанием активного алюминия не менее 80%.
Технологический процесс изготовления автоклавного газобетона включает в себя:
— прием и подготовку сырьевых материалов;
— приготовление газобетонной смеси;
— формование массивов газобетона;
— разрезку массивов на изделия;
— автоклавную обработку;
— упаковку изделий.
Сырьевые материалы могут поступать на завод различными видами транспорта (чаще всего автомобильным и железнодорожным). Хранение вяжущих предусматривается в специальных силосах. Количество и объем силосов выбирается в зависимости от мощности завода, удаленности от поставщиков материалов и вида транспорта.
Кварцевый песок выгружаются в приемный бункер, откуда по ленточному конвейеру поступает на помол для приготовления шлама. Помол производится в шаровых мельницах. Далее песчаный шлам транспортируется в шламбассейны, где гомогенизируется с помощью постоянного механического перемешивания.
Негашеная известь на предприятие поступает в тонкомолотом или комовом виде.
В первом случае, тонкомолотая негашеная известь хранится, по аналогии с портландцементом, в силосах и уже готова к употреблению. Во втором случае, если поступает комовая негашеная известь, на предприятии используется технология приготовления известково-песчаного вяжущего путем совместного сухого помола в шаровых мельницах извести и кварцевого песка.
Приготовление газобетонной смеси производится в дозаторно-смесительном отделении. Портландцемент, известь (известково-песчаное вяжущее), песчаный шлам, шлам из отходов резки, вода и алюминиевая суспензия дозируются в соответствии с установленной рецептурой в специальный смеситель, обеспечивающий высокую гомогенность смеси.
Процесс формования включает разгрузку (заливку) смеси из смесителя в форму и вспучивание смеси. Окончание процесса формования наступает после достижения максимальной высоты вспучивания смеси и прекращения активного газовыделения.
После вспучивания формы с газобетонной смесью выдерживаются на постах, желательно при температуре воздуха не менее +15-20oС до приобретения требуемой пластической прочности сырца. Для ускорения процесса набора первоначальной прочности формы со смесью могут выдерживаться в специальных термокамерах при температуре до +70-80oС. Время выдержки при использовании термокамер уменьшается.
После достижения сырцом пластической прочности 0,04-0,12 МПа (в зависимости от технологии) формы подаются на резательный комплекс. Газобетонный массив калибруется со всех сторон и разрезается проволочными струнами в продольном и поперечном направлениях на изделия требуемых размеров. Метод резки газобетонных массивов в полупластическом состоянии с помощью тонких проволочных струн хорошо зарекомендовал себя и на современных резательных машинах позволяет получать изделия точных размеров с отклонениями от номинальных до ±1,0-1,5 мм. Такая точность позволяет осуществлять кладку блоков на тонкослойную клеевую смесь вместо традиционного цементно-песчаного раствора.
Разрезанные на изделия массивы устанавливаются на автоклавные тележки и загружаются в автоклав. После полной загрузки автоклава начинается тепловлажностная обработка по определенному режиму, включающему плавный набор температуры и давления, изотермическую выдержку при температуре около 190°С и давлении 12 атм, плавный спуск давления и подготовка изделий к выгрузке.
Из компонентов CaO и SiO2, вяжущих материалов и кварцевого песка, а также воды, в условиях автоклавной обработки (высокое давление и температура) происходит образование новых минералов – низкоосновных гидросиликатов кальция, что предопределяет более высокие физико-механические характеристики автоклавного газобетона в сравнении с неавтоклавными ячеистыми бетонами (пенобетон, газобетон).
После завершения цикла тепловлажностной обработки изделия подаются на участок деления и упаковки, а затем на склад готовой продукции.
Основные моменты технологии производства блоков из автоклавного газобетона показаны на видео одного из участников ассоциации ВААГ:
Газобетон является пористым материалом и относится к ячеистым бетонам, делится на автоклавный и неавтоклавный. Различия в плане состава между ними незначительны, но в процессе производства разница существенна.
Компоненты газобетона:
- Портландцемент высокой марки (35%).
- Песок очень мелкой фракции (35%).
- Измельченная известь (1%).
- Алюминиевая пудра (0.05%).
- Вода (28%).
Чем лучше измельчены все компоненты, тем прочнее получается газобетон.
Сама технология изготовления газобетона заключается в смешивании наполнителей (цемента и песка) с газообразующими добавками (известь и алюминиевая пудра). После их перемешивания, между алюминиевой пудрой и известью начинается химическая реакция с выделением газа – водорода. Именно этот газ и создает в газобетоне поры, которые обеспечивают хорошую теплоизоляцию и легкий вес.
Меняя количество газообразующих добавок, можно добиться различной плотности газобетона, то есть, чем больше газа в бетоне, тем он легче, соответственно, меньше его плотность и прочность. На рынке стройматериалов можно найти газобетон плотностью от D150 до D700.
Газобетон хорош тем, что поры в его составе распределены очень равномерно, что обеспечивает одинаковую прочность и теплопроводность по всей толщине блоков.
После процесса газообразования и первичного схватывания смеси, общий массив разрезается струной на отдельные блоки нужной толщины. Далее газоблоки набирают прочность.
Что такое автоклавирование газобетона
Если мы говорим про автоклавный газобетон, то он обязательно проходит процесс автоклавирования. Автоклавами называют большие емкости, в которых создается высокая температура (160-180 С) и давление насыщенного водяного пара.
Процесс автоклавирования длится около 12 часов, и его задача заключается в быстром наборе прочности газобетона. Обычный тяжелый бетон набирает 70% своей марочной прочности примерно через месяц, но если увеличить температуру до 180 градусов, то прочность наберется в 100 раз быстрее.
Это решает сразу несколько проблем: усадка блоков отсутствует, не требуется время для набора прочности газобетона. Далее газобетон упаковывают в защитную пленку и развозят заказчикам.
Свежий автоклавный газобетон является очень влажным, воды в нем около 30-40%. Из-за влаги, его плотность значительно выше заявленной. По этому, перед отделочными работами, выложенная газобетонная стена должна просохнуть хотя бы два сезона.
Автоклавный газобетон имеет более высокую прочность, в отличии от неавтоклавного.
В научной терминологии, автоклавный газобетон называют тоберморитом – искусственным пористым камнем. Так как камни являются минералами, то они абсолютно экологичны. Газобетон не выделяет никаких вредных веществ, и не является радиоактивным.
Отличия газобетона и пенобетона
В плане наполнителей эти ячеистые бетоны похожи, отличие в газообразующих добавках. Если в газобетоне пузыри образуются из-за выделяющихся пузырей газа, то в пенобетоне из-за пены, которую добавляют в смесь отдельно. Проблемой пенобетона может быть его неоднородность, то есть, в одном месте пузырей будет больше, а в другой – меньше.
Процесс изготовления пенобетона намного проще, из-за чего его производством занимаются в гаражных условиях. Доверие к качеству заводского автоклавного газобетона и его составу намного выше. Прочность и геометрия автоклавного газобетона лучше, чем у пенобетона.
Из чего состоит газобетон(видео)
Технология производства газобетона
Газобетонные блоки, как и пенобетонные изделия, являются одной из разновидностей ячеистых бетонов. Пористая структура придает этому материалу хорошие тепло и шумоизоляционные свойства, малый вес при больших размерах и достаточную прочность, что качественно выделяет его среди остальных стеновых материалов, широко использующихся при строительстве перегородок, гаража, дачи и др. Кроме этого, сама технология производства газобетона довольно проста, при этом она не требует больших затрат, а цена готового продукта приятно удивляет.
Виды изготовления
Существует 2 разновидности технологии производства газобетонных блоков, а именно: автоклавного твердения и естественной выдержки. В первом случае используют специальные камеры – автоклавы, снабженные регулятором давления и температуры. Газобетон, получаемый таким способом более качественный и прочный, нежели тот, который был высушен в естественных условиях, но зато вторая технология приемлема для тех, кто хочет изготовить блоки в домашних условиях, хоть он получится не настолько надежный как хотелось бы, но он все равно будет пригоден для строительства малоэтажных частных домов.
Сырьевые компоненты
Для изготовления газобетонных блоков по любой технологии понадобятся следующие его составляющие:
Вода
Для блоков пригодна любая питьевая и техническая чистая вода, однако она должна отвечать всем требованиям ГОСТ 23732-79. Вода с температурой 45, качественно увеличит скорость твердения, прочность и производительность линии изготовления. Подогрев воды поможет снизить количество применяемого цемента, за счет искусственной стимуляции его активности.
Песок
Подойдет любой речной или карьерный, главное, чтобы в нем содержалось минимальное количество глинистых и илистых частиц, а максимальная крупность зерен не превышала 2 мм.
Портландцемент
Предпочтительно вяжущее марок М 400 и М 500, лучший цемент тот, который по всем критериям удовлетворяет требования ГОСТ 10178-85.
Газообразователь
В его качестве используется алюминиевая пудра марок ПАП-1 или ПАП-2.
Оборудование
Технологическая линия изготовления газоблоков подразумевает наличие специального оборудования, которое приобретается в комплексе у производителя. Как правило, такой комплекс представляет собой автоматизированный мини–завод, который имеет довольно компактные размеры. Некоторые производители, бонусом к приобретаемому оборудованию предоставляют услуги временного технолога, который обучит вас, настроит производственную линию и подберет оптимальный состав газобетонной смеси.
Основные этапы
Конкретный алгоритм производства зависит от специфики приобретенного оборудования, но в общем он подразумевает 3-этапное производство газоблоков:
- Первым делом происходит точная дозировка компонентов и их перемешивание, в среднем этот цикл длится не более 10 минут.
- После чего, приготовленную бетонную массу, посредством специального оборудования, выгружают в заранее смазанные формы ровно до половины. Далее, в течении 4-часов смесь «растет» и заполняет весь объем форм, еще через 2 часа излишки смеси убираются.
- И третий, завершающий этап – распалубка изделий после 16-часовой выдержки и складирование их на поддоны для дальнейшего набора отпускной прочности, которая происходит в течение 2 или 3 суток, после чего изделия отправляются на склад. Марочной прочности газобетонные блоки достигают на 28 сутки.
Вывод
Чтобы получить на выходе хороший газобетон, нужно приобрести надежное оборудование и качественное сырье. Также обязательно следование всем правилам технологии, и только три эти составляющие в совокупности помогут не только окупить вложения, но и принести хорошую прибыль.
Удачной стройки!
Автор: Elvirosa Brancaccio — Serintel Srl — Рим (Италия)
1. Введение
Газ-в-жидкости (GTL) — это технология, позволяющая производить дизельное топливо чистого горения, жидкий нефтяной газ, базовое масло и нафту из природного газа. Процесс GTL превращает природный газ в очень чистое дизельное топливо, потому что продукты представляют собой углеводороды без цвета и запаха с очень низким уровнем примесей.
Большая часть природного газа в мире классифицируется как «застрявший», что означает, что он находится в отдаленном районе, вдали от существующей трубопроводной инфраструктуры. Объемы часто слишком малы, чтобы сделать строительство крупной установки для очистки газа экономически эффективным. В результате газ, как правило, повторно закачивается в пласт, остается в земле или сжигается, что вредно для окружающей среды. Тем не менее, доступность этого недорогого многожильного газа стимулировала компании к разработке инновационных технологий, которые могут экономично и эффективно использовать этот газ, превращая его в транспортное топливо, такое как дизельное топливо и топливо для реактивных двигателей.
НПЗ также могут использовать GTL для преобразования некоторых своих газообразных углеводородных отходов в ценный мазут, который можно использовать для получения дохода.
Небольшие установки GTL представляют собой контейнеры, состоящие из риформера для производства синтез-газа, реактора Фишера-Тропша (FT) для производства синкруда и, в некоторых случаях, пакета для модернизации, который используется для дальнейшей переработки продуктов FT в желаемое транспортабельное топливо. Поскольку на этих контейнерных установках уже около 70 процентов их строительства завершено до прибытия на площадку завода, затраты на строительство на месте значительно снижаются.В случаях, когда необходимо увеличить производительность, дополнительные агрегаты могут быть легко отправлены грузовиком или кораблем и подключены параллельно существующему процессу. В зависимости от технологии пропускная способность может варьироваться от 100 баррелей в сутки до 15 000 баррелей в сутки.
2. Этапы процесса GTL
Fischer-Tropsch — это процесс химического преобразования природного газа в жидкости (GTL), угля в жидкости (CTL), биомассы в жидкости (BTL) или битума из нефтеносных песков в жидкости (OTL).
Все четыре процесса состоят из трех технологических разделов.
- Производство синтез-газа (синтез-газа).
Углерод и водород первоначально отделены от молекулы метана и реконфигурированы путем паровой конверсии и / или частичного окисления. Произведенный синтез-газ состоит в основном из окиси углерода и водорода.
- Каталитический (F-T) синтез.
Сингаз обрабатывается в реакторах Фишера-Тропша (F-T) различной конструкции в зависимости от технологии, создающей широкий спектр парафиновых углеводородных продуктов (синтетических неочищенных или синкрудированных), особенно с молекулами с длинной цепью (например,грамм. те, которые содержат до 100 атомов углерода в молекуле).
- Крекинг — обработка продукта.
Синкруд очищается с использованием традиционных процессов крекинга на нефтеперерабатывающем заводе для производства дизельного топлива, нафты и смазочных масел для коммерческих рынков. Начиная с очень длинноцепочечных молекул, процессы крекинга могут быть отрегулированы до некоторой степени, чтобы производить больше продуктов, востребованных рынком в любой момент времени. В большинстве случаев именно дизельное топливо со средним дистиллятом и реактивное топливо представляют собой сыпучие продукты с наивысшей ценностью, а смазочные материалы предлагают продукты с высокой маржой для рынков с более ограниченными объемами.На современных заводах конструкции и операции агрегатов F-T GTL, как правило, модулируются для достижения желаемого распределения продуктов и ассортимента продуктов.
Рис. 1 — Технологический процесс GTL с реактором синтеза Фишера-Тропша
Исследования и разработки в области технологии GTL и установки включают несколько частей установки:
- прирост эффективности производства для каждого отдельного устройства, используемого вверх и вниз по течению
- катализатора в реактор ФТ с целью повышения его селективности и долговечности
- проект реакторов для уменьшения всей установки или модуля отпечатка стопы
3.Начало и развитие
Технология производства синтетического топлива, известная как GTL, была изобретена в 1920-х годах. Одним из наиболее известных способов создания синтетического топлива является синтез Фишера-Тропша (ФТ). Технология FT была первоначально разработана в Германии для решения проблемы нехватки нефти, которая привела к мировой войне. К 1944 году Германия производила 124 млн. Баррелей в сутки синтетического топлива из угля на заводах 25 футов.
Технология нового поколения была разработана в Южной Африке, которая стремилась поддержать свою экономику без нефти.В 1970-х годах технология развивалась в Западной Европе и США с большим заводом и крупномасштабным производством.
Начиная с последних десятилетий, достижения в технологиях GTL позволили сделать маломасштабные GTL и даже микромасштабные GTL эксплуатационно и потенциально экономически целесообразными.
Несколько факторов сходятся, чтобы стимулировать рост в отрасли GTL:
- Желание монетизировать существующие запасы попутного газа;
- энергетических компаний стремятся получить доступ к новым газовым ресурсам;
- Рыночный спрос на более чистое топливо и новое, более дешевое химическое сырье;
- Быстрое развитие технологий существующими и новыми игроками;
- Увеличение интереса со стороны принимающих правительств, богатых газом
Поскольку цены на нефть остаются высокими, благодаря новым открытиям природный газ становится более доступным и дешевым, и более продвинутые энергетические компании изучают способы снижения капитальных вложений в производство синтетического топлива.В рамках этой цели компании рассматривают возможность создания небольших модульных установок, которые могут работать в удаленных местах [1].
За последние три десятилетия появилось несколько технологий «газ-жидкость» (GTL) в качестве надежной альтернативы монетизации газа для стран-производителей газа для расширения и диверсификации на рынках транспортного топлива. Конечный продукт GTL может быть синкрудным, который может быть впрыснут в нефтепровод, тем самым избегая необходимости транспортировать другой продукт на рынок, или более ценное жидкое топливо или химическое сырье, такое как бензин, дизельное топливо (без серы и с высоким содержанием цетана). число), нафта, топливо для реактивных двигателей, метанол или диметиловый эфир (ДМЭ).
4. Заводы и проекты
МИРОВЫХ КОММЕРЧЕСКИХ УСТАНОВОК GTL
В настоящее время в эксплуатации находятся пять промышленных установок GTL (рис. 1). Эти пять растений включают в себя:
- Bintulu GTL, Малайзия
- Escravos GTL, Нигерия
- Моссел Бей GTL, Южная Африка
- Oryx GTL, Катар
- Pearl GTL, Катар.
Эти пять заводов представляют почти 259 Мбит / с. Компонент Shell Pearl GTL с пропускной способностью 140 Мбит / с составляет более 50% от общего объема коммерческих GTL в мире.
Рис. 2 — Промышленные установки GTL, работающие по всему миру [2]
Первый завод GTL был разработан PetroSA в 1992 году. Этот завод с пропускной способностью 36 Мбит / с находится в заливе Моссел, Южная Африка. На заводе используется технология FT для переработки богатого метаном природного газа в высококачественное синтетическое топливо с низким содержанием серы. Продукция включает неэтилированный бензин, керосин, дизельное топливо, пропан, дистилляты, технологическое масло и спирты.
Shell ввела в эксплуатацию свой первый коммерческий завод GTL в Бинтулу, Малайзия, в 1993 году. Первоначальная стоимость строительства завода составила 850 млн. Долл. США. На заводе в 12,5 Мбит / с произошло устранение уязвимостей в размере 50 млн. Долл. США, что увеличило общую емкость до 14,7 Мбит / с. С 1993 года производится следующая продукция: сжиженный нефтяной газ (до 5%), нафта (до 30%), дизельная фракция (до 60%) и парафин (до 5-10%).
Рис. 3 — завод Bintulu GTL [3]
Комплекс Pearl GTL является крупнейшим в мире объектом GTL.Объект мощностью 140 Мбит / с расположен в промышленном городе Рас-Лаффан, Катар. Комплекс по переработке природного газа стоимостью 19 миллиардов долларов США и комплексной GTL был разработан совместными усилиями компаний Shell и Qatar Petroleum.
Oryx GTL был первым заводом GTL на Ближнем Востоке. Разработанная Qatar Petroleum и Sasol, установка стоимостью 6 млрд долларов также перерабатывает природный газ с северного месторождения Катара. Строительство завода началось в конце 2003 года, а его производство началось в начале 2007 года. Завод перерабатывает 330 млн куб. Футов богатого метаном газа с северного месторождения Катара и производит 34 млн баррелей в день жидкостей, большинство из которых составляют низко-серные высокооктановые ГТЛ. дизель.
Самым последним коммерческим заводом GTL для запуска является завод Escravos GTL. Завод стоимостью 10 млрд. Долларов был создан совместным предприятием, состоящим из Chevron, Sasol и Nigerian National Petroleum Corp. Завод использует технологию обоих партнеров по СП для преобразования до 325 млн. Куб. Футов природного газа в 33 млн. Баррелей в сутки дизельного топлива GTL и нафты GTL. Завод работает с 2014 года.
НОВЫЕ УСТАНОВКИ GTL В РАЗВИТИИ
Завод GTL ENVIA Energy на свалке по утилизации отходов в Оклахоме вступил в строй в 2017 году.Завод, частично снабженный свалочным газом, объявил о своей первой готовой к продаже продукции 30 июня 2017 года, но в январе 2018 года еще не достиг проектной мощности в 250 баррелей в сутки.
Запуск других 4 заводов (Greyrock 1, Juniper GTL, Primus 1 и Primus 2) произойдет в 2018 году. Новый владелец Juniper GTL, York Capital, вероятно, будет ориентироваться на будущие заводы более 5000 баррелей в сутки (потребляя 50 млн. Куб. Футов газа). Greyrock и Primus GE объявили о продолжении активных усилий по развитию бизнеса на газовой факельной арене.
Haldor Topsoe объединил усилия с Modular Plant Solutions (MPS) и разработал и спроектировал небольшую метанольную установку (215 тонн в день) под названием «Метанол-To-GoTM». Размеры установки аналогичны размерам установок Primus 1 и 2 с расходом газа 7 MMscfd.
BgtL — новый игрок на арене микро-GTL (20-200 баррелей в день). Однако их запатентованные технологии основаны на двух десятилетиях научно-исследовательской работы в научно-исследовательских институтах. Их портфель продуктов включает в себя заводские модули, которые преобразуют объемы газа от 2 млн. Куб. Футов в ряд продуктов, включая нефть, дизельное топливо, метанол и другие.
Подводя итог, на данный момент ведущие поставщики технологий GTL с коммерческими предложениями:
Micro-GTL: необслуживаемые операционные устройства ниже ~ 1Mscscd и ниже ~ 10 млн. Долл. США
Mini-GTL: небольшие модульные установки с некоторыми операторами и стоимостью> 10 млн. Долларов США
- Серый 9009
- EFT / Black and Veatch
- INFRA
- Primus GE
- Topsoe / MPS
- Expander Energy
Более подробную информацию об этих компаниях и их проектах можно найти в последнем бюллетене по технологии GTL [4].
На следующем рисунке представлен прогноз, представленный EIA для производства GTL в следующие несколько лет:
Рис. 4 — Глобальное производство газа и жидкости, 2017 [5]
4.1 Обзор доступных технологий
Рынок GTL движется в сторону небольших и модульных блоков. Эти типы заводов могут быть построены при значительно сниженных капитальных затратах, которые могут достигать миллиардов долларов для крупных объектов.
Газовые единицы, используемые технологии, размеры и другие функциональные данные для нескольких компаний, участвующих в технологии GTL, приведены в таблицах ниже [6]:
Calvert Energy Group / OXEON
Рис. 5 — Завод Calvert Energy Group GTL
Calvert Energy Group предлагает модульные установки GTL (для сжигания факелов и дизельного газа на дизельном топливе) в диапазоне от 0,2 до 100 млн. Футов в день.Используемая технология OEXON исключительно лицензирована для Calvert Energy Group компанией OXEON.
Таб. 1 — Данные Calvert Energy Group
CompactGTL
Рис. 6 — Компактная модульная установка GTL
Модульное устройствоCompactGTL предлагает маломасштабное решение «газ-жидкость» (GTL) для малых и средних нефтяных месторождений, где не существует жизнеспособного варианта монетизации газа, так что попутный газ либо сжигается, либо вводится повторно.
Таб. 2 — Данные модульного устройства Compact GTL
GasTechno Energy & Fuels (GEF)
Рис. 7 — Модуль ООО «Газ Технологии»
Gas Technologies LLC производит, устанавливает и эксплуатирует модульные установки для газожидкостного производства, в которых используется запатентованный одностадийный процесс преобразования GTL GasTechno®.Установки GasTechno® Mini-GTL® преобразуют попутный газ и многожильный природный газ в высокоценные виды топлива и химикаты, включая смеси метанола, этанола и бензина / дизельного топлива, а также сокращают выбросы парниковых газов. Удельные капитальные затраты заводов примерно на 70% ниже, чем у традиционных установок по производству метанола, и они требуют относительно ограниченных затрат на эксплуатацию и техническое обслуживание.
Таб. 3 — данные ООО «Газовые технологии»
Greyrock
Рис.8 — Энергетический модуль Greyrock P-5000
Greyrock Energy была основана в 2006 году и имеет штаб-квартиру в Сакраменто, штат Калифорния, с офисами и демонстрационным заводом в Толедо, штат Огайо. Он специализируется исключительно на небольших заводах GTL Fischer-Tropsch для распределенного производства топлива®, и у него есть коммерческое предложение как полностью интегрированной установки с производительностью 2000 баррелей в сутки, потребляющей около 20 млн. Кубических футов в сутки, так и более мелких установок MicroGTL (5-50 баррелей в сутки).
Таб.4 — Данные Greyrock Energy
Velocys
Рис. 9 — Завод Velocys
Velocys — это небольшая GTL-компания, которая предоставляет мост, соединяющий сырое и малоценное сырье, такое как попутный газ и свалочный газ, с рынками высококачественной продукции, такой как возобновляемое дизельное топливо, реактивное топливо и воски. Компания была основана в 2001 году, как дочерняя компания Battelle, независимой научно-технической организации.В 2008 году она объединилась с Оксфордскими катализаторами, продуктом Оксфордского университета. Velocys стремится предлагать экономически выгодные конверсионные решения. Он торгуется на Лондонской фондовой бирже с офисами в Хьюстоне, штат Техас; Колумбус, штат Огайо; и Оксфорд, Великобритания.
Таб. 5 — данные Velocys
Primus Green Energy
Рис. 10 — Primus System
Primus Green Energy находится в Хиллсборо, штат Нью-Джерси, США.Компания поддерживается Kenon Holdings, компанией, зарегистрированной на NYSE, с офисами в Великобритании и Сингапуре, которая ведет динамичный, в первую очередь, ориентированный на рост бизнес. Primus Green Energy ™ разработала технологию «газ-жидкость», которая производит ценные жидкости, такие как бензин, разбавители и метанол, непосредственно из природного газа или другого богатого углеродом исходного газа.
Таб. 6 — Данные Primus Green Energy
5.События Примечания
СНИЖЕНИЕ ПРЕИМУЩЕСТВ
Используя преимущества новых технологий, таких как микроканальные реакторы, для сокращения оборудования FT и SMR, заводы GTL могут быть сокращены, чтобы обеспечить экономически эффективный способ использования меньших ресурсов газа. Установки GTL, основанные на использовании микроканальных реакторов FT, могут эксплуатироваться на распределенной основе, при этом более мелкие установки расположены вблизи газовых ресурсов и потенциальных рынков.
Меньшие, модульные установки GTL подходят для использования в удаленных местах.В отличие от традиционных установок GTL, они предназначены для экономичной переработки небольшого количества газа в диапазоне от 100 млн. Кубометров (1 млн. Кубометров) до 1500 млн. Кубометров, и они могут производить 1000 — 15 000 баррелей в сутки жидкого топлива. Установки можно масштабировать в соответствии с размером ресурса, расширять по мере необходимости и потенциально интегрировать с существующими установками на площадках нефтеперерабатывающего завода.
Операции GTL меньшего масштаба также представляют меньший риск для производителей. Поскольку заводы меньше, затраты на строительство снижаются; и, поскольку заводы являются модульными, инвестиции могут быть поэтапными.Время строительства короткое, 18-24 месяца. Кроме того, поскольку модули и реакторы спроектированы только один раз, а затем изготовлены многократно, большая часть установки может быть стандартизирована и изготовлена в цехе в модулях, установленных на раме Это снижает стоимость и риски, связанные со строительством заводов в отдаленных местах. Кроме того, компоненты могут быть спроектированы для использования стандартного стандартного оборудования, что позволяет снизить нагрузку на цепочки поставок и снизить потребность в строительных работах на месте.
Поскольку процесс FT также лежит в основе процессов биомассы в жидкость (BTL), эта же технология может быть использована для производства высококачественного, сверхчистого дизельного топлива и топлива для реактивных двигателей из отходов биомассы, включая муниципальные отходы. Установки GTL меньшего масштаба предлагают преимущества на всех этапах производства: вверх по течению, в середине и ниже по течению [7].
6. Технология GTL-FT Новые концепции
Мелкомасштабная переработка природного газа требует принципиально новых технологий для превращения углеводородов в жидкие химикаты и топливо.Есть несколько возможностей.
Первый заключается в разработке более эффективных и менее сложных методов преобразования углеводородных газов в синтез-газ.
- Очень многообещающим способом повышения эффективности и гибкости преобразования углеводородных газов в синтез-газ является газофазное сгорание очень богатых смесей углеводород-воздух или углеводород-кислород в объемных проницаемых матрицах. Частичное окисление углеводородных газов является очень привлекательным методом для мелкомасштабного производства синтез-газа, так как это экзотермический процесс, который не требует внешнего нагрева и, следовательно, громоздкого и дорогого теплообменного оборудования.Это обстоятельство позволяет значительно уменьшить размер и, следовательно, стоимость реформатора.
Второе — разработать принципиально разные методы преобразования природного газа в химические вещества без промежуточной стадии производства синтез-газа, работая над составом использованных катализаторов или путем разработки новых.
- Альтернативной возможностью получения полезных химикатов и жидкого топлива из природного газа является их прямое окисление.Можно обсудить несколько прямых методов преобразования природного газа в полезные химические вещества без промежуточного производства синтез-газа. Среди них наиболее известными и развитыми являются Прямое окисление. На самом деле, прямое частичное окисление с последующим карбонилированием и / или олигомеризацией продуктов окисления может рассматриваться как альтернативный путь для процессов превращения газа в жидкость, что позволяет избежать производства синтез-газа, наиболее дорогостоящая потребляющая энергию энергия стадии традиционного GTL [8].
На небольших установках GTL самая сложная задача — найти способы объединить и уменьшить размер и стоимость реакционного оборудования, сохраняя при этом достаточную мощность.Это, в свою очередь, зависит от поиска путей уменьшения размера реактора за счет улучшения свойств теплопередачи и массообмена для увеличения производительности и интенсификации процессов генерации синтез-газа и ФТ. Использование микроканальных реакторов предлагает способ достижения этих целей.
- Микроканальная технология — развивающаяся область химической обработки, которая интенсифицирует химические реакции, уменьшая размеры каналов в реакторных системах. Поскольку теплопередача обратно пропорциональна размеру каналов, уменьшение диаметра канала является эффективным способом увеличения теплопередачи, тем самым интенсифицируя процесс и позволяя реакциям протекать со значительно более высокими скоростями, чем те, которые наблюдаются в обычных реакторах.
Технология может применяться как к сильно экзотермическим процессам, таким как FT, так и к высокоэндотермическим процессам, таким как SMR. Микроканальные реакторы FT содержат тысячи тонких технологических каналов, заполненных катализатором FT, чередующихся с заполненными водой каналами охлаждающей жидкости. Поскольку каналы малого диаметра рассеивают тепло быстрее, чем обычные реакторы, можно использовать более активные катализаторы FT, чтобы значительно ускорить реакции FT, тем самым повышая производительность.
В микроканальных реакторах SMR процессы выработки тепла и SMR происходят в соседних каналах.Высокие теплообменные свойства микроканалов делают процесс очень эффективным (рис. 4).
Рис. 11 — Схема микроканального реактора FT (слева) и реактора в корпусе полного давления (справа) [9]
Дополнительное улучшение может быть получено путем исследования катализатора.
- INFRA Technology представляет новое поколение технологии GTL, позволяющей получать легкую синтетическую сырую нефть прямо из реактора FT, с четырехкратной производительностью и без побочных продуктов (рис.12). Процесс не требует дополнительной обработки восков, а синтетическая сырая нефть полностью совместима с существующей нефтяной инфраструктурой.
Рис. 12 Применение новых технологий [10]
Технология стала возможной благодаря созданию нового катализатора с использованием кобальта в качестве активного металла в многокомпонентном композите. Исключение определенных этапов обработки и производство высококачественного одножидкостного продукта делает решения INFRA GTL экономически целесообразными из небольших, предварительно сконструированных, стандартизированных, модульных (таких как контейнеры), легко развертываемых и транспортируемых блоков вплоть до крупные интегрированные газоперерабатывающие заводы.
7. Анализ затрат
Предоставляя возможность нацеливать поставки на мировые рынки транспортировки жидкого топлива, заводы GTL значительно диверсифицируют рыночные возможности и помогают сгладить финансовую отдачу в нестабильных условиях, когда цены на рынках газа и цены на нефть и нефтепродукты становятся несвязанными.
7.1 Методология анализа денежных потоков для оценки коммерциализации проектов GTL
Существует несколько факторов, которые определяют денежные потоки и потоки доходов, связанные с заводами GTL.Ключевые факторы, необходимые для методологии, которая анализирует коммерческую привлекательность завода GTL в многолетней модели денежных потоков, включают:
- Стоимость сырья (природный газ, уголь, нефтяной кокс или биомасса)
- Цены на нефтепродукты и химикаты, производимые и продаваемые с заводов.
Цены на эти продукты в большинстве случаев сильно зависят от базовых цен на сырую нефть. Продукты GTL обычно продаются в ценовых диапазонах, которые отражают преобладающее распространение трещин на нефтеперерабатывающих и нефтехимических заводах.Иногда продукты GTL продаются с небольшими надбавками к продуктам нефтепереработки из-за их высокого качества (то есть с низким содержанием серы, с низким содержанием ароматических соединений в случае дизельного топлива и бензина).
Аспекты, которые необходимо рассмотреть:
- Если проект GTL является комплексным проектом, то выручка от сжиженного природного газа, извлеченного из потока сырьевого газа, должна быть включена в расчет денежных потоков проекта и доходов
- Капитальные затраты на строительство завода GTL, которые можно с пользой сравнить с единицей долларов США / баррель / день пропускной способности продукции завода
- Как капитальные затраты компенсируются, восстанавливаются и / или амортизируются с течением времени и вычитаются в рамках методологии налогооблагаемого дохода Эффективность установки
- GTL (т.е.е. количество единиц исходного сырья, необходимое для производства одной единицы продукта) в расчете на энергию и / или массу
- GTL годовой коэффициент использования завода (дней / год) на основе требований к техническому обслуживанию и ремонту
- Расходы на эксплуатацию и техническое обслуживание установки GTL, включая затраты на катализаторы, химикаты, коммунальные услуги
- Стоимость перевозки (отгрузки) между заводом GTL и рынком, на котором продается продукция
- Применяются налоговые вычеты, которые значительно различаются в разных юрисдикциях
7.2 Прогноз стоимости
ТехнологияFT обычно состоит из четырех компонентов: производство синтез-газа (синтез-газа), очистка газа, синтез FT и модернизация продукта. Третий этап представляет собой отличительную технологию, которая послужила основой для будущих технологических разработок и инноваций. Остальные три технологии были хорошо известны до изобретения FT и были разработаны отдельно.
Обычно синтез-газ получают путем высокотемпературной газификации в присутствии кислорода и пара.
Для компонентов завода, некоторые аспекты могут быть рассмотрены для анализа затрат:
- Воздухоразделительная установка обычно представляет собой значительные капиталовложения.
- Экономические преимущества или прорыв в малых установках GTL произошли с достижениями в 4 областях:
- Коммерческое внедрение микроканальной технологии F-T;
- Высокоактивные кобальтовые катализаторы;
- Массовое производство реакторов F-T;
- Модульное строительство заводов.
- Другая фундаментальная проблема заключается в том, что из-за экологических норм тяжелые сырьевые сланцы (в основном асфальты и тяжелые топливные масла) становятся все более трудными для сбыта и, следовательно, становятся нежелательными остатками, а не источниками дохода. Технология GTL имеет здесь явное преимущество из-за полного отсутствия тяжелых сланцев. Это может стать сильным аргументом для GTL в будущем, особенно для установок FT на существующих нефтеперерабатывающих заводах, которые могут быть использованы для увеличения доли легких и средних дистиллятов в общем портфеле продуктов [11].
8. Экологические аспекты и преимущества
ТехнологииGTL могут трансформировать газовые потоки, которые в противном случае превратились бы в ценные жидкие топлива и химикаты для транспортировки, включая высококачественный бензин или метанол, или отдельный поток обогащенного водородом отходящего газа, который можно использовать в качестве дополнительного водорода или топлива на месте. источник, так что это идеальное решение для снижения сжигания газа при одновременном повышении отдачи.
Кроме того, выбросы парниковых газов могут быть дополнительно снижены с помощью систем GTL путем ввода потоков CO 2 в качестве совместной подачи, которая преобразуется в бензин или метанол, что представляет собой ценное использование для того, что обычно считается низкоценным или даже поток газа с отрицательным значением.
Свойства GTL Fuel включают повышенную биоразлагаемость в воде и почве, снижение экотоксичности для воды и почвы. Топливо, полученное в процессе FT, обладает значительно лучшими характеристиками, чем его аналоги на нефтяной основе. Дизельное топливо, производное от FT, не содержит ароматических соединений или серы и сгорает чище, чем топливо, полученное из нефти, что приводит к снижению выбросов оксида азота (NOx), оксида серы (SOx) и твердых частиц. Эксперименты по выбросам отработавших газов на продуктах GTL показали общее значительное снижение содержания CO (22–25%), углеводородов (30–40%) и NOx (6–8%).GTL дизель имеет потенциал для продажи в качестве премиальной смеси [12].
Комбинация этих функций указывает на то, что GTL Fuel с меньшей вероятностью будет оказывать вредное воздействие на окружающую среду, чем чистое традиционное топливо. Кроме того, FT-дизель можно смешивать с низкоцетановыми дизелями более низкого качества для достижения коммерческих экологических требований к дизельным двигателям.
Когда сырье включает возобновляемый компонент, будь то возобновляемый биогаз (как в случае проекта ENVIA Energy), или отходы лесного хозяйства и лесопилки (как в случае предлагаемого проекта Red Rock Biofuels в Орегоне), произведенное топливо обеспечивает значительное сокращение выбросов парниковых газов в течение жизненного цикла по сравнению с традиционными видами топлива.
Нажмите здесь, чтобы посмотреть видео:
или свяжитесь с нами для получения дополнительной информации о технологии GTL.
[1] http://www.gasprocessingnews.com/features/201610/smaller-scale-gtl-enters-the-mainstream.aspx
[2] www.gasprocessingnews.com/features/201706/smaller-scale-and-modular-technologies-drive-gtl-industry-forward.aspx
[3] www.theoildrum.com
[4] http: // pubdocs.worldbank.org/en/492881520264957368/Mini-GTL-Bulletin-No-4-Jan-2018.pdf
[5] EIA: Международная энергетическая перспектива, 2017.
[6] Обзор технологии GGFR — использование малых ассоциированных компаний февраль 2018 г.
[7] http://www.gasprocessingnews.com/features/201310/smaller-scale-gtl-enters-the-mainstream.aspx
[8] www.researchgate.net/profile/Vladimir_Arutyunov/publication/276778347_New_concept_for_smallscale_GTL/links/59e37aefa6fdcc7154dba94a/New-concept-for-smallLscale-GTpdf
[9] http://www.gasprocessingnews.com
[10] http://www.gasprocessingnews.com/columns/201706/gtl-viewpoint.aspx
[11] http://www.gasprocessingnews.com/features/201606/evaluate-gtl-processes-compare d-with-обычный-refining.aspx
[12] http://www.gasprocessingnews.com/features/201606/evaluate-gtl-processes-compared-with-conventional-refining.aspx
,Производственная линия для производства блоков AAC
1. Профиль компании:
ShanDong SUNITE Machinery Group Co., Ltd, основана в Октябрь, 1998 г. , является Китайский производитель специализированной производственной линии AAC для производства блоков и панелей, оборудование для автоклавирования пенобетонных блоков .Зарегистрированный капитал составляет более 10 миллионов REB, а количество сотрудников превышает 500, включая 6 старших инженеров и 28 промежуточных инженеров . Это первый профессиональный производитель в Китае, специализирующийся на производстве оборудования для газобетонных блоков в автоклаве, оборудования для стеновых панелей из газобетона, оборудования для парового и автоклавного кирпича.
Производственная линия станка для производства блоков AAC
2.Блок из автоклавного газобетона (AAC) Введение:
Блок из автоклавного газобетона (AAC) — блок-блок, также называемый легким блоком, используется кремнезем ( летучей золы, песка, шлака) и известняк ( известь и цемент ) в качестве основного сырья, который посредством процесса дозирования, разливки, резки, автоклавирования, разделения и упаковки для превращения в конечные продукты .Это новый тип и экологический строительный материал, широко используемый для промышленного и гражданского строительства. aac block machine является самой зрелой технологией производства и применения в мире на сегодняшний день.
AAC Производственная линия машины для производства блоков
3. Преимущества и особенности газобетонных блоков в автоклаве:
1. Легкий вес: 400 ~ 700 кг / м 3 3 3 3 ,Высокая интенсивность: 3,5 ~ 10,0 МПа
3. Хорошие теплоизоляционные свойства: 0,1 ~ 0,20 Вт / (м · К)
4. Сохранение температуры, сохранение тепла, огнестойкие
5. Хорошая звукоизоляция
6. Доказательство землетрясения
7. Хорошая эксплуатация
8. Удобная механическая конструкция
Линия производства машин для изготовления блоков AAC
4.Песок и золе AAC Блок Сырье:
Имя | Unit | Доля | Имя | Unit | Доля | ||||||
летучей золы | % | 60-70 | Песок | % | 55-65 | ||||||
Цемент | % | 6-15 | 000 000 000 000000 20 | ||||||||
Лайм | % | 18-25 | Lime | % | 20-30 | ||||||
Гипс | % | 901 9 9000 9 9 9 9 9 9 9 9 9 9 9 9 9 9 9 9 9 9 9 9 9 9 9 9 9 9 9 9 9 9 9 9 9 9 9 9 9 9 9 000 9 до 9 000 9 9 9000 Алюминий0001/10000 | 8 | Алюминиевая порошковая паста | 1/10000 | 9016 9000 9000 |
| 0.60-0.65 | воды и скорость материала |
| 0,65-0,75 |
Температура литья | ° C | 36-40 | температура литья | ° C | 35-38 | ||||||
Алюминий время смешивания | с | 30-40 | Время смешивания алюминия | с | 30-40 |
5.Каков нормальный размер блока AAC?
Длина (мм): 600
Ширина (мм): 75, 100, 125, 150, 175, 200, 250
Высота (мм): 200, 240, 250, 300
Примечания: размеры могут быть настроены по индивидуальному заказу
Продукция нашего станка произведена
AAC Производственная линия для производства блоков
6.Оборудование для производства блоков AAC:
AAC Производственная линия для производства блоков
8. Преимущество выбора нас:
1) Мы владеем передовой технологией и командой специалистов.
2) Наш завод имеет долгую историю и достаточно опыта.
3) У нас есть полная система послепродажного обслуживания
Наш технологический инструктор, предлагающий технологические рекомендации в Индии
Производственная линия для производства блоков AAC
9. Сертификация и выставка:
Мы гарантируем, предлагаем вам лучшие продукты с лучшими услугами и ценой.
Приглашаем посетить наш завод.
,Машины для производства блоков Машина для производства газовых блоков Без станка для производства поддонов
Описание продукта
Гидравлические блокировочные машины для кирпичей, типичные для многих видов естественного строительства: песок, цемент, бетон и т. Д.
Естественное строительство имеет тенденцию полагаться на человеческий труд, а не на технологии. Эта машина очень доступна для малых предприятий.Другими словами, кирпичи или блоки, произведенные с использованием этой машины, являются относительно дешевыми и доступными для тех, кто живет в сельской местности, и для людей с низким доходом.
Технические параметры блокировки гидравлического кирпича
QTY5-20B | |
Цикл литья | 15-20S |
Модель трансмиссии | Гидравлическое давление |
Всего | 7.5T |
Размеры | 4300 * 2110 * 2800 мм |
Общая мощность | 26,85 кВт |
Применение | Стандартный кирпич, пустотелый блок, кирпич для отверстий, голландский кирпич |
Основные технические характеристики изделия и производство российского кирпича
Стандартный кирпич | 240 * 53 * 115 мм | 32 |
Пустотелый блок | 390 * 190 * 190 мм | 5 |
Отверстия Кирпич | 240 * 115 * 90 мм | 16 |
Голландский кирпич | 200 * 100 * 55 мм | 20 |
Функции и особенности 2-10 кирпичного станка
(1) Прочность может быть сконструирована в соответствии с требованиям инженерного строительства из кирпича разной прочности.
(2) Форма в соответствии с требованиями проекта для определения различных спецификаций блочного кирпича.
(3) Это может быть пустотелый блок, многорядный кирпич, монолитный кирпич и другие виды бетонных кирпичей.
(4) Брошенный бетонный кирпич также может быть переработан и использован, что увеличивает всестороннее использование ресурсов.
Кирпич из готового продукта из Китая. Машина для производства бетонных блоков., а также могут быть настроены в соответствии с потребностями клиентов.
машина для производства бетонного / цементного кирпича, широко используемая в жилищном строительстве, на дорогах, площадях, в проектах по сохранению воды, в ландшафтном строительстве.
Упаковка и отгрузка
Детали упаковки машины для производства кирпича: деревянная коробка или контейнер, достойный моря.
Доставка TiPme: 15-20 дней после сдачи на хранение.
Возможность поставки: 60Комплектов в месяц.
Информация о компании
Сертификаты
Наши машины регулярно калибруются и модернизируются нашей командой профессионалов, что помогает нам поддерживать отличную производительность. И мы получили сертификат на соответствующий продукт. Чертежи могут быть сделаны в соответствии с требованиями заказчика, и может быть предоставлен дизайн проекта.
Отзывы покупателей
У нас есть профессиональный отдел производственных технологий, который может предоставить подходящие станки в соответствии с требованиями клиентов, а также может настроить пресс-формы и двигатели для удовлетворения потребностей различных клиентов в стране и за рубежом.Только довольный клиент делает нас довольными. Мы хотим создать долгосрочные деловые отношения с нашими потенциальными клиентами.
FAQ
1. В: Какие размеры пресс-форм? Я хочу сделать особенный.
A: Это не проблема, все виды пресс-форм могут быть изготовлены по чертежам заказчика.
2. Вопрос: каковы ваши условия оплаты?
A: TT, Western Union. L / C и т. Д. 30% депозита, а остальные будут оплачены до того, как машина покинет завод.
3. Вопрос: Когда ваша сторона доставит мне машину?
A: Машина обычно отправляется в течение 20 дней после сдачи на хранение, и это также зависит от других условий.
4. Вопрос: как насчет пакета?
A: Обнаженная упаковка, стандартная деревянная упаковка или в соответствии с вашими потребностями.
5.Q: как насчет цены?
A: мы являемся фабрикой и можем предложить вам самую низкую цену, чем рыночная, и у нас есть политика, которая «для экономии времени и абсолютно честного делового отношения, мы приводим максимально низкие цены для любого клиента, и скидка может быть дано по количеству «.
Наши услуги
Обладает следующими преимуществами:
1) У нас есть большая команда технических дизайнеров с многолетним опытом в области производства кирпичных машин и мы предоставляем вам настоящую технологию производства кирпича.
2) Мы можем разработать макет обработки, подходящий для вашей мастерской.
3) у нас есть многолетний опыт производства машин, и у нас есть персонал по контролю качества для осмотра машин во время и после отделки машин.
4) У нас есть большая мастерская для запасных частей в магазине.Если вам понадобятся запасные части в будущем, они могут предоставить вам вовремя.
,»Переработка природного газа NaturalGas.org
Переработка природного газа
Источник: Duke Energy Gas Transmission Канада
Природный газ в том виде, как он используется потребителями, сильно отличается от природного газа, который доставляется из недр до устья скважины. Хотя обработка природного газа во многих отношениях менее сложна, чем обработка и переработка сырой нефти, она в равной степени необходима перед его использованием конечными пользователями.
Природный газ, используемый потребителями, почти полностью состоит из метана.Тем не менее, природный газ, найденный в устье скважины, хотя по-прежнему состоит в основном из метана, ни в коем случае не является таким чистым. Сырой природный газ поступает из трех типов скважин: нефтяных скважин, газовых скважин и конденсатных скважин. Природный газ, который поступает из нефтяных скважин, обычно называют «попутным газом». Этот газ может существовать отдельно от нефти в пласте (свободный газ) или растворяться в сырой нефти (растворенный газ). Природный газ из газовых и конденсатных скважин, в которых почти нет сырой нефти, называется «неассоциированным газом».Газовые скважины обычно добывают неочищенный природный газ, а конденсатные скважины производят свободный природный газ вместе с полужидким углеводородным конденсатом. Каким бы ни был источник природного газа, после отделения от сырой нефти (если он присутствует) он обычно существует в смеси с другими углеводородами; главным образом этан, пропан, бутан и пентаны. Кроме того, сырой природный газ содержит водяной пар, сероводород (H 2 S), диоксид углерода, гелий, азот и другие соединения. Чтобы узнать об основах природного газа, включая его состав, нажмите здесь.
Обработка природного газа состоит из отделения всех различных углеводородов и жидкостей от чистого природного газа с целью получения так называемого сухого природного газа «качества трубопровода». Крупные транспортные трубопроводы обычно накладывают ограничения на подпитку природного газа, который допускается в трубопровод. Это означает, что перед транспортировкой природного газа его необходимо очистить. Хотя этан, пропан, бутан и пентаны должны быть удалены из природного газа, это не означает, что все они являются «отходами».
Фактически, попутные углеводороды, известные как «газоконденсатные жидкости» (NGL), могут быть очень ценными побочными продуктами переработки природного газа. НГЛ включают этан, пропан, бутан, изобутан и природный бензин. Эти NGL продаются отдельно и имеют множество различных применений; включая повышение нефтеотдачи в нефтяных скважинах, обеспечение сырьем для нефтеперерабатывающих или нефтехимических заводов, а также в качестве источников энергии.
A Завод по переработке природного газа |
Источник: Duke Energy Gas Transmission Канада |
Хотя некоторая необходимая обработка может быть выполнена на устье скважины или вблизи него (полевая обработка), полная обработка природного газа происходит на обогатительной фабрике, обычно расположенной в области добычи природного газа.Добытый природный газ транспортируется на эти перерабатывающие заводы через сеть сборных трубопроводов, которые представляют собой трубы низкого давления малого диаметра. Сложная система сбора может состоять из тысяч миль труб, соединяющих перерабатывающий завод с более чем 100 скважинами в этом районе. Согласно «Газовым фактам» Американской газовой ассоциации за 2000 год, в 1999 году в США было проведено около 36 100 миль сборочных трубопроводов.
В дополнение к обработке, проводимой на устье скважины и на централизованных перерабатывающих заводах, некоторая окончательная обработка также иногда выполняется на «установках извлечения с разгрузочной способности».Эти заводы расположены на основных системах трубопроводов. Хотя природный газ, который поступает на эти экстракционные установки, уже имеет качество трубопровода, в некоторых случаях все еще существуют небольшие количества сжиженных природных газов, которые добываются на градирнях.
Фактическая практика обработки природного газа до уровня качества сухого газа в трубопроводе может быть довольно сложной, но обычно включает четыре основных процесса удаления различных примесей:
Прокрутите вниз или нажмите на ссылку выше, чтобы перейти к определенному разделу.
В дополнение к четырем вышеуказанным процессам установлены нагреватели и скрубберы, обычно на устье скважины или рядом с ним. Скрубберы служат главным образом для удаления песка и других крупных частиц. Нагреватели гарантируют, что температура газа не будет слишком низкой. При использовании природного газа, который содержит даже небольшое количество воды, гидраты природного газа имеют тенденцию образовываться при понижении температуры. Эти гидраты представляют собой твердые или полутвердые соединения, напоминающие ледяные кристаллы. Если эти гидраты накапливаются, они могут препятствовать прохождению природного газа через клапаны и системы сбора.Чтобы уменьшить количество гидратов, небольшие обогреватели, работающие на природном газе, обычно устанавливаются вдоль сборочной трубы везде, где есть вероятность образования гидратов.
Удаление масла и конденсата
Для переработки и транспортировки попутного растворенного природного газа его необходимо отделить от масла, в котором он растворен. Такое отделение природного газа от нефти чаще всего осуществляется с использованием оборудования, установленного на устье скважины или вблизи него.
Фактический процесс, используемый для отделения нефти от природного газа, а также используемого оборудования, может широко варьироваться.Хотя качество сухого природного газа в разных географических зонах практически одинаково, сырой природный газ из разных регионов может иметь разные составы и требования к разделению. Во многих случаях природный газ растворяется в подземных нефтяных скважинах в основном из-за давления, под которым находится пласт. Когда этот природный газ и нефть добываются, возможно, что они разделятся сами по себе, просто из-за пониженного давления; так же, как открытие банки с газировкой позволяет выпускать растворенный углекислый газ.В этих случаях разделение нефти и газа сравнительно легко, и два углеводорода направляются отдельными путями для дальнейшей переработки. Самый основной тип сепаратора известен как обычный сепаратор. Он состоит из простого закрытого резервуара, в котором сила тяжести служит для отделения более тяжелых жидкостей, таких как нефть, и более легких газов, таких как природный газ.
Инженеры по газопереработке |
Источник: ChevronTexaco Corporation |
Однако в некоторых случаях для разделения нефти и природного газа необходимо специальное оборудование.Примером оборудования такого типа является низкотемпературный сепаратор (LTX). Это чаще всего используется для скважин, добывающих газ под высоким давлением наряду с легкой сырой нефтью или конденсатом. Эти сепараторы используют перепады давления для охлаждения влажного природного газа и отделения масла и конденсата. Влажный газ поступает в сепаратор и слегка охлаждается теплообменником. Затем газ проходит через жидкостную пробку высокого давления, которая служит для удаления любых жидкостей в низкотемпературный сепаратор. Затем газ поступает в этот низкотемпературный сепаратор через дроссельный механизм, который расширяет газ при поступлении в сепаратор.Такое быстрое расширение газа позволяет снизить температуру в сепараторе. После удаления жидкости сухой газ затем возвращается через теплообменник и нагревается поступающим влажным газом. Изменяя давление газа в различных секциях сепаратора, можно варьировать температуру, которая вызывает конденсацию масла и воды из потока влажного газа. Эта базовая зависимость давления от температуры может работать и в обратном направлении, чтобы извлечь газ из потока жидкой нефти.
Водоотведение
Помимо отделения масла и некоторого конденсата от потока влажного газа, необходимо удалить большую часть попутной воды. Большая часть жидкой свободной воды, связанной с добываемым природным газом, удаляется простыми методами разделения в устье скважины или вблизи него. Однако удаление водяного пара, который существует в растворе в природном газе, требует более сложной обработки. Эта обработка состоит из «дегидратации» природного газа, который обычно включает один из двух процессов: либо абсорбцию, либо адсорбцию.
Поглощение происходит, когда водяной пар выводится дегидратирующим агентом. Адсорбция происходит, когда водяной пар конденсируется и собирается на поверхности.
Обезвоживание гликоля
Пример абсорбционной дегидратации известен как дегидратация гликоля. В этом процессе дегидратор жидкого осушителя служит для поглощения водяного пара из газового потока. Гликоль, основной агент в этом процессе, имеет химическое сродство к воде. Это означает, что при контакте с потоком природного газа, который содержит воду, гликоль будет «красть» воду из газового потока.По сути, дегидратация гликоля включает использование раствора гликоля, обычно либо диэтиленгликоля (DEG), либо триэтиленгликоля (TEG), который приводится в контакт с потоком влажного газа в так называемом «контакторе». Раствор гликоля будет поглощать воду из влажного газа. После поглощения частицы гликоля становятся более тяжелыми и опускаются на дно контактора, где они удаляются. Природный газ, лишенный большей части содержания воды, затем транспортируется из дегидратора.Раствор гликоля, содержащий всю воду, очищенную от природного газа, подается через специализированный котел, предназначенный для испарения только воды из раствора. В то время как вода имеет температуру кипения 212 градусов по Фаренгейту, гликоль не кипит до 400 градусов по Фаренгейту. Этот перепад температур кипения позволяет относительно легко удалить воду из раствора гликоля, что позволяет повторно использовать ее в процессе дегидратации.
Новшеством в этом процессе было добавление сепаратора-конденсатора испарительного бака.Помимо поглощения воды из потока влажного газа, раствор гликоля иногда несет с собой небольшие количества метана и других соединений, содержащихся во влажном газе. В прошлом этот метан просто выходил из котла. В дополнение к потере части добытого природного газа, эта вентиляция способствует загрязнению воздуха и парниковому эффекту. Чтобы уменьшить количество метана и других соединений, которые теряются, сепаратор-конденсаторы испарительного резервуара работают для удаления этих соединений до того, как раствор гликоля достигнет котла.По существу, сепаратор испарительного резервуара состоит из устройства, которое снижает давление потока раствора гликоля, позволяя испаряться метану и другим углеводородам («вспышка»). Затем раствор гликоля поступает в котел, который также может быть оснащен конденсаторами с воздушным или водяным охлаждением, которые служат для улавливания любых оставшихся органических соединений, которые могут оставаться в растворе гликоля. На практике, по данным Управления ископаемой энергии Министерства энергетики, эти системы извлекают от 90 до 99 процентов метана, который в противном случае мог бы попасть в атмосферу.
Чтобы узнать больше о дегидратации гликоля, посетите веб-сайт Института газовой технологии здесь.
Обезвоживание твердого осушителя
Обезвоживание твердого осушителя является основной формой обезвоживания природного газа с использованием адсорбции и обычно состоит из двух или более адсорбционных колонн, которые заполнены твердым осушителем. Типичные осушители включают активированный оксид алюминия или гранулированный материал силикагеля. Мокрый природный газ пропускается через эти башни сверху вниз.Когда влажный газ проходит вокруг частиц влагопоглощающего материала, вода остается на поверхности этих частиц влагопоглотителя. Проходя через весь слой осушителя, почти вся вода адсорбируется на материале осушителя, оставляя сухой газ для выхода из нижней части башни.
Абсорбционные башни |
Источник: Duke Energy Gas Transmission Канада |
Дегидраторы с твердым влагопоглотителем обычно более эффективны, чем дегидраторы гликоля, и обычно устанавливаются в качестве типовой системы вдоль трубопроводов природного газа.Эти типы систем обезвоживания лучше всего подходят для больших объемов газа под очень высоким давлением и, таким образом, обычно расположены на трубопроводе ниже по потоку от компрессорной станции. Требуются две или более башни в связи с тем, что после определенного периода использования влагопоглотитель в конкретной башне насыщается водой. Для «регенерации» осушителя высокотемпературный нагреватель используется для нагрева газа до очень высокой температуры. Проходя этот нагретый газ через слой насыщенного осушителя, вода в башне осушителя испаряется, оставляя ее сухой и обеспечивая дальнейшую дегидратацию природного газа.
Газоперерабатывающий завод с абсорбционными башнями |
Источник: Duke Energy Gas Transmission Канада |
Разделение жидкостей природного газа
Природный газ, поступающий непосредственно из скважины, содержит много газовых жидкостей, которые обычно удаляются. В большинстве случаев газоконденсатные газы (NGL) имеют более высокую ценность в качестве отдельных продуктов, и, следовательно, экономически выгодно удалять их из газового потока.Удаление жидкостей из природного газа обычно происходит на относительно централизованной перерабатывающей установке и использует методы, аналогичные тем, которые используются для обезвоживания природного газа.
Существует два основных этапа обработки жидкостей природного газа в потоке природного газа. Во-первых, жидкости должны быть извлечены из природного газа. Во-вторых, эти жидкости природного газа должны быть отделены друг от друга, вплоть до их основных компонентов.
NGL Добыча
Существует два основных метода удаления СПГ из потока природного газа: метод абсорбции и процесс криогенного детандера.По данным Ассоциации переработчиков газа, на эти два процесса приходится около 90 процентов общего объема производства природного газа.
Способ поглощения
Трубы и абсорбционные башни |
Источник: Duke Energy Gas Transmission Канада |
Способ абсорбции для экстракции NGL очень похож на использование абсорбции для дегидратации.Основное отличие состоит в том, что при абсорбции СПГ используется абсорбирующее масло, а не гликоль. Это поглощающее масло обладает «сродством» к НГЛ во многом так же, как гликоль имеет сродство к воде. До того, как масло улавливает какие-либо НГЛ, его называют «бедным» абсорбционным маслом. Когда природный газ пропускается через абсорбционную колонну, он вступает в контакт с абсорбционной нефтью, которая впитывает значительную долю газовых добавок. «Богатое» абсорбционное масло, теперь содержащее сжиженный природный газ, выходит из абсорбционной колонны через дно.Теперь это смесь абсорбционной нефти, пропана, бутанов, пентанов и других более тяжелых углеводородов. Богатое масло подается в бидоны для бедного масла, где смесь нагревают до температуры выше температуры кипения газовой смеси, но ниже температуры кипения масла. Этот процесс позволяет извлекать около 75 процентов бутанов и 85–90 процентов пентанов и более тяжелых молекул из потока природного газа.
Вышеописанный базовый процесс поглощения может быть изменен для повышения его эффективности или для целевого извлечения специфических НГЛ.В способе абсорбции охлажденного масла, где бедное масло охлаждается посредством охлаждения, извлечение пропана может составлять более 90 процентов, и около 40 процентов этана может быть извлечено из потока природного газа. С помощью этого процесса извлечение других, более тяжелых НГЛ может быть близким к 100%.
Криогенный процесс расширения
Криогенные процессы также используются для извлечения СПГ из природного газа. Хотя абсорбционные методы могут извлечь практически все более тяжелые ПГК, более легкие углеводороды, такие как этан, часто труднее извлечь из потока природного газа.В некоторых случаях экономически целесообразно просто оставлять более легкие ПГ в потоке природного газа. Однако, если экономически выгодно добывать этан и другие более легкие углеводороды, требуются криогенные процессы для высоких скоростей извлечения. По сути, криогенные процессы состоят в снижении температуры газового потока примерно до -120 градусов по Фаренгейту.
Существует несколько различных способов охлаждения газа до этих температур, но один из наиболее эффективных известен как процесс турбодетандера.В этом процессе внешние хладагенты используются для охлаждения потока природного газа. Затем турбина расширения используется для быстрого расширения охлажденных газов, что приводит к значительному падению температуры. Это быстрое падение температуры конденсирует этан и другие углеводороды в газовом потоке, сохраняя метан в газообразной форме. Этот процесс позволяет извлекать около 90-95 процентов этана, первоначально находящегося в потоке газа. Кроме того, расширительная турбина способна преобразовывать часть энергии, выделяющейся при расширении потока природного газа, в повторное сжатие потока газообразного метана, тем самым экономя затраты на энергию, связанные с извлечением этана.
Извлечение СПГ из потока природного газа дает как более чистый, более чистый природный газ, так и ценные углеводороды, которые сами являются СПГ.
Фракция жидкого природного газа
После того, как СПГ были удалены из потока природного газа, они должны быть разбиты на базовые компоненты, чтобы быть полезными. То есть смешанный поток разных NGL должен быть выделен. Процесс, используемый для выполнения этой задачи, называется фракционированием.Фракционирование работает на основе различных температур кипения различных углеводородов в потоке СПГ. По существу, фракционирование происходит на стадиях, состоящих из выпаривания углеводородов один за другим. Название конкретного фракционатора дает представление о его назначении, так как оно условно названо для испаряющегося углеводорода. Весь процесс фракционирования разбивается на этапы, начиная с удаления более легких СПГ из потока. Конкретные фракционаторы используются в следующем порядке:
- Deethanizer — этот этап отделяет этан от потока NGL.
- Депропанизатор — следующий шаг отделяет пропан.
- Debutanizer — на этом этапе выкипают бутаны, оставляя пентаны и более тяжелые углеводороды в потоке природного газа.
- Бутановый сплиттер или деизобутанизатор — этот шаг разделяет изо и нормальные бутаны.
Переходя от самых легких углеводородов к самым тяжелым, можно довольно легко разделить различные СПГ.
Чтобы узнать больше о фракционировании НГЛ, нажмите здесь.
Удаление серы и диоксида углерода
В дополнение к удалению воды, нефти и сжиженного природного газа, одна из наиболее важных частей обработки газа включает удаление серы и углекислого газа. Природный газ из некоторых скважин содержит значительные количества серы и углекислого газа. Этот природный газ из-за гниющего запаха, обусловленного содержанием в нем серы, обычно называют «кислым газом». Кислый газ нежелателен, потому что содержащиеся в нем соединения серы могут быть чрезвычайно вредными, даже смертельно опасными для дыхания.Кислый газ также может быть очень агрессивным. Кроме того, сера, которая существует в потоке природного газа, может быть извлечена и реализована самостоятельно. Фактически, согласно USGS, производство серы в США на газоперерабатывающих заводах составляет около 15 процентов от общего производства серы в США. Для получения информации о производстве серы в Соединенных Штатах, посетите USGS здесь.
Газ подслащивающая установка |
Источник: Duke Energy Gas Transmission Канада |
Сера существует в природном газе в виде сероводорода (H 2 S), и газ обычно считается кислым, если содержание сероводорода превышает 5.7 миллиграммов H 2 S на кубический метр природного газа. Процесс удаления сероводорода из кислого газа обычно называют «подслащиванием» газа.
Первичный процесс подслащивания кислого природного газа очень похож на процессы дегидратации гликоля и абсорбции природного газа. В этом случае, однако, растворы амина используются для удаления сероводорода. Этот процесс известен просто как «аминный процесс» или, альтернативно, как процесс Гирдлера, и используется в 95 процентах U.S. Газ подслащивающие операции. Кислый газ проходит через колонну, которая содержит раствор амина. Этот раствор обладает сродством к сере и поглощает ее так же, как и гликоль, поглощающий воду. Используются два основных раствора амина: моноэтаноламин (МЭА) и диэтаноламин (ДЭА). Любое из этих соединений в жидкой форме будет поглощать соединения серы из природного газа при его прохождении. Выходящий газ практически не содержит соединений серы и, таким образом, теряет статус кислого газа. Как и в случае процесса извлечения СПГ и дегидратации гликоля, используемый раствор амина можно регенерировать (то есть абсорбированная сера удаляется), что позволяет использовать его повторно для обработки большего количества кислого газа.
Несмотря на то, что большая часть подслащивания кислым газом включает процесс абсорбции амина, также возможно использовать твердые осушители, такие как губки железа, для удаления сульфида и диоксида углерода.
Сера может быть продана и использована, если уменьшить ее до элементарной формы. Элементарная сера представляет собой ярко-желтый порошкообразный материал, и ее часто можно увидеть в больших кучах возле газоперерабатывающих заводов, как показано на рисунке. Чтобы извлечь элементарную серу из газоперерабатывающего завода, серосодержащие отходы от процесса подслащивания газа должны быть дополнительно обработаны.Процесс, используемый для извлечения серы, известен как процесс Клауса и включает использование термических и каталитических реакций для извлечения элементарной серы из раствора сероводорода.
Для получения дополнительной информации о восстановлении серы и процессе Клауса, нажмите здесь.
Производство элементарной серы на установке подготовки газа |
Источник: Duke Energy Gas Transmission Канада |
В целом процесс Клауса обычно способен извлечь 97 процентов серы, которая была удалена из потока природного газа.Поскольку это такое загрязняющее и вредное вещество, дальнейшая фильтрация, сжигание и очистка от «хвостовых газов» гарантируют, что будет извлечено более 98 процентов серы.
Чтобы узнать больше об экологических последствиях обработки и сжигания кислого газа, нажмите здесь.
Газопереработка — инструментальная часть цепочки создания стоимости природного газа. Это способствует тому, чтобы природный газ, предназначенный для использования, был как можно более чистым и чистым, что делает его чистым сжиганием и экологически безопасным выбором энергии.Как только природный газ полностью переработан и готов к употреблению, его необходимо транспортировать из тех районов, где производится природный газ, в те районы, где он требуется.
Нажмите здесь, чтобы узнать о транспортировке природного газа.
,