Π’Π΅Ρ Π½ΠΎΠ»ΠΎΠ³ΠΈΡ ΠΏΡΠΎΠΈΠ·Π²ΠΎΠ΄ΡΡΠ²Π° ΠΏΠ΅Π½ΠΎΠΏΠΎΠ»ΠΈΡΡΠΈΡΠΎΠ»Π° ΠΈΠ· Π²ΡΠΏΠ΅Π½ΠΈΠ²Π°ΡΡΠ΅Π³ΠΎΡΡ ΠΏΠΎΠ»ΠΈΡΡΠΈΡΠΎΠ»Π°.
Π’Π΅Ρ Π½ΠΎΠ»ΠΎΠ³ΠΈΡ ΠΏΡΠΎΠΈΠ·Π²ΠΎΠ΄ΡΡΠ²Π° ΠΏΠ΅Π½ΠΎΠΏΠΎΠ»ΠΈΡΡΠΈΡΠΎΠ»Π° ΠΈΠ· Π²ΡΠΏΠ΅Π½ΠΈΠ²Π°ΡΡΠ΅Π³ΠΎΡΡΒ ΠΏΠΎΠ»ΠΈΡΡΠΈΡΠΎΠ»Π°
1. Π€ΠΈΠ·ΠΈΠΊΠΎ-Ρ ΠΈΠΌΠΈΡΠ΅ΡΠΊΠ°Ρ ΠΏΠΎΡΠ»Π΅Π΄ΠΎΠ²Π°ΡΠ΅Π»ΡΠ½ΠΎΡΡΡ ΠΏΡΠΎΡΠ΅ΡΡΠ°.
ΠΡΠΎΡΠ΅ΡΡ ΠΏΡΠΎΠΈΠ·Π²ΠΎΠ΄ΡΡΠ²Π° ΠΏΠ΅Π½ΠΎΠΏΠ»Π°ΡΡΠ° ΠΈΠ· Π²ΡΠΏΠ΅Π½ΠΈΠ²Π°ΡΡΠ΅Π³ΠΎΡΡ ΠΏΠΎΠ»ΠΈΡΡΠΈΡΠΎΠ»Π° ΡΠΊΠ»Π°Π΄ΡΠ²Π°Π΅ΡΡΡ ΠΈΠ· ΡΠ΅ΡΡΡΠ΅Ρ
ΠΏΠΎΡΠ»Π΅Π΄ΠΎΠ²Π°ΡΠ΅Π»ΡΠ½ΡΡ
ΡΠ΅Ρ
Π½ΠΎΠ»ΠΎΠ³ΠΈΡΠ΅ΡΠΊΠΈΡ
ΠΎΠΏΠ΅ΡΠ°ΡΠΈΠΉ.
Π. ΠΠ΅ΡΠ²ΠΎΠ½Π°ΡΠ°Π»ΡΠ½ΠΎΠ³ΠΎ ΠΏΡΠΎΠΈΠ·Π²ΠΎΠ΄ΡΡΠ²Π° Π³ΡΠ°Π½ΡΠ» ΠΈΠ· Π²ΡΠΏΠ΅Π½ΠΈΠ²Π°ΡΡΠ΅Π³ΠΎΡΡ ΠΏΠΎΠ»ΠΈΡΡΠΈΡΠΎΠ»Π°
Π. ΠΡΠ΄Π΅ΡΠΆΠΊΠΈ ΠΏΠΎ Π²ΡΠ΅ΠΌΠ΅Π½ΠΈ Π²ΡΠΏΠ΅Π½Π΅Π½Π½ΡΡ
Π³ΡΠ°Π½ΡΠ» ΠΈΠ· Π²ΡΠΏΠ΅Π½ΠΈΠ²Π°ΡΡΠ΅Π³ΠΎΡΡ ΠΏΠΎΠ»ΠΈΡΡΠΈΡΠΎΠ»Π°
Π. Π€ΠΎΡΠΌΠΈΡΠΎΠ²Π°Π½ΠΈΠ΅ Π±Π»ΠΎΠΊΠΎΠ² ΠΈΠ· Π²ΡΠΏΠ΅Π½ΠΈΠ²Π°ΡΡΠ΅Π³ΠΎΡΡ ΠΏΠΎΠ»ΠΈΡΡΠΈΡΠΎΠ»Π°
Π. Π‘ΡΡΠΊΠ° ΠΈ Π²ΡΠ΄Π΅ΡΠΆΠΊΠ° ΠΏΠΎ Π²ΡΠ΅ΠΌΠ΅Π½ΠΈ Π±Π»ΠΎΠΊΠΎΠ² ΠΈΠ· Π²ΡΠΏΠ΅Π½ΠΈΠ²Π°ΡΡΠ΅Π³ΠΎΡΡ ΠΏΠΎΠ»ΠΈΡΡΠΈΡΠΎΠ»Π°.
Π. ΠΡΠΎΡΠ΅ΡΡ ΠΏΡΠΎΠΈΠ·Π²ΠΎΠ΄ΡΡΠ²Π° Π³ΡΠ°Π½ΡΠ», ΠΏΡΠΎΠΈΡΡ ΠΎΠ΄ΡΡΠΈΠΉ Π²ΠΎ Π²ΡΠΏΠ΅Π½ΠΈΠ²Π°ΡΠ΅Π»Π΅ Ρ ΠΏΠΎΠΌΠΎΡΡΡ Π²ΠΎΠ΄ΡΠ½ΠΎΠ³ΠΎ ΠΏΠ°ΡΠ°, ΠΏΡΠΎΠΈΡΡ ΠΎΠ΄ΠΈΡ ΠΏΡΠΈ ΡΠ΅ΠΌΠΏΠ΅ΡΠ°ΡΡΡΠ΅ 80-100 Π³ΡΠ°Π΄ΡΡΠΎΠ² Π¦Π΅Π»ΡΡΠΈΡ. ΠΠ»Π°Π³ΠΎΠ΄Π°ΡΡ ΡΠΎΠ΄Π΅ΡΠΆΠ°ΡΠ΅ΠΌΡΡΡ Π² Π³ΡΠ°Π½ΡΠ»Π°Ρ ΠΏΠΎΡΠΎΡΠΎΡΡ (ΠΎΠ±ΡΡΠ½ΠΎ ΠΏΠ΅Π½ΡΠ°Π½, ΠΈΠ·ΠΎΠΏΠ΅Π½ΡΠ°Π½ ΠΈΠ»ΠΈ ΠΏΠ΅Π½ΡΠ°Π½-ΠΈΠ·ΠΎΠΏΠ΅Π½ΡΠ°Π½ΠΎΠ²Π°Ρ ΡΡΠ°ΠΊΡΠΈΡ), ΠΏΠΎΠ²ΡΡΠ΅Π½Π½ΠΎΠΉ ΡΠ΅ΠΌΠΏΠ΅ΡΠ°ΡΡΡΠ΅ ΠΈ ΡΠ°ΡΡΠΈΡΠ΅Π½ΠΈΡ Π²ΠΎΠ΄ΡΠ½ΠΎΠ³ΠΎ ΠΏΠ°ΡΠ°, Π³ΡΠ°Π½ΡΠ»Ρ ΠΌΠ½ΠΎΠ³ΠΎΠΊΡΠ°ΡΠ½ΠΎ ΡΠ²Π΅Π»ΠΈΡΠΈΠ²Π°ΡΡ ΡΠ²ΠΎΠΉ ΠΎΠ±ΡΠ΅ΠΌ ΠΈ ΠΏΡΠΈΠ½ΠΈΠΌΠ°ΡΡ ΠΌΠΈΠΊΡΠΎΡΡΠ΅ΠΈΡΡΡΡ ΡΡΡΡΠΊΡΡΡΡ.
Π. ΠΠΎ Π²ΡΠ΅ΠΌΡ Π²ΡΠ΄Π΅ΡΠΆΠΊΠΈ ΠΏΠΎ Π²ΡΠ΅ΠΌΠ΅Π½ΠΈ Π²ΡΠΏΠ΅Π½Π΅Π½Π½ΡΡ Π³ΡΠ°Π½ΡΠ» ΠΈΠ· ΠΏΠΎΠ»ΠΈΡΡΠΈΡΠΎΠ»Π° ΠΏΡΠΎΠΈΡΡ ΠΎΠ΄ΠΈΡ ΠΏΡΠΎΡΠ΅ΡΡ Π΄ΠΈΡΡΡΠ·ΠΈΠΈ Π²ΠΎΠ·Π΄ΡΡ Π° Π²ΠΎΠ²Π½ΡΡΡΡ ΠΌΠΈΠΊΡΠΎ ΡΡΠ΅Π΅ΠΊ ΠΈ Π²ΡΡΠ°Π²Π½ΠΈΠ²Π°Π½ΠΈΠ΅ Π΄Π°Π²Π»Π΅Π½ΠΈΡ Π²Π½ΡΡΡΠΈ ΡΡΠ΅Π΅ΠΊ ΠΈ Π°ΡΠΌΠΎΡΡΠ΅ΡΠ½ΡΠΌ Π΄Π°Π²Π»Π΅Π½ΠΈΠ΅ΠΌ.
Π. ΠΡΠΎΡΠ΅ΡΡ ΡΠΎΡΠΌΠΈΡΠΎΠ²Π°Π½ΠΈΡ Π±Π»ΠΎΠΊΠΎΠ² ΠΈΠ· Π²ΡΠΏΠ΅Π½ΠΈΠ²Π°ΡΡΠ΅Π³ΠΎΡΡ ΠΏΠΎΠ»ΠΈΡΡΠΈΡΠΎΠ»Π°, ΠΏΡΠΎΠΈΡΡ ΠΎΠ΄ΡΡΠΈΠΉ Π² Π·Π°ΠΊΡΡΡΡΡ ΡΠΎΡΠΌΠ°Ρ , Π·Π°ΠΊΠ»ΡΡΠ°Π΅ΡΡΡ Π² Π½Π°Π³ΡΠ΅Π²Π°Π½ΠΈΠΈ Π²ΠΎΠ΄ΡΠ½ΡΠΌ ΠΏΠ°ΡΠΎΠΌ Π²ΡΠΏΠ΅Π½Π΅Π½Π½ΡΡ ΠΈ Π²ΡΠ΄Π΅ΡΠΆΠ°Π½Π½ΡΡ Π³ΡΠ°Π½ΡΠ». ΠΠ»Π°Π³ΠΎΠ΄Π°ΡΡ ΠΏΠΎΠ²ΡΡΠ΅Π½ΠΈΡ ΡΠ΅ΠΌΠΏΠ΅ΡΠ°ΡΡΡΡ, Π° ΡΠ°ΠΊΠΆΠ΅ Π·Π°ΠΊΠ»ΡΡΠ΅Π½Π½ΠΎΠΌΡ Π² ΠΏΠΎΡΠ°Ρ Π³ΡΠ°Π½ΡΠ» ΠΏΠΎΡΠΎΡΠΎΡΡ, Β Π²ΠΎΠ·Π΄ΡΡ Ρ ΠΈ Π²ΠΎΠ΄ΡΠ½ΠΎΠΌΡ ΠΏΠ°ΡΡ, Π½Π°ΡΡΡΠΏΠ°Π΅Ρ Π΄Π°Π»ΡΠ½Π΅ΠΉΡΠ΅Π΅ ΡΠ°ΡΡΠΈΡΠ΅Π½ΠΈΠ΅ ΠΎΠ±ΡΠ΅ΠΌΠ° Π³ΡΠ°Π½ΡΠ» ΠΈ ΠΈΡ Π²Π·Π°ΠΈΠΌΠ½ΠΎΠ΅ ΡΠ»ΠΈΠΏΠ°Π½ΠΈΠ΅, ΠΏΡΠΈΠ²ΠΎΠ΄ΡΡΠ΅Π΅ ΠΊ Π²ΠΎΠ·Π½ΠΈΠΊΠ½ΠΎΠ²Π΅Π½ΠΈΡ ΠΌΠΎΠ½ΠΎΠ»ΠΈΡΠ½ΠΎΠ³ΠΎ Π±Π»ΠΎΠΊΠ° ΠΈΠ· ΠΏΠ΅Π½ΠΎΠΏΠΎΠ»ΠΈΡΡΠΈΡΠΎΠ»Π°. ΠΠΎΡΠ»Π΅ ΠΎΡ Π»Π°ΠΆΠ΄Π΅Π½ΠΈΡ Π±Π»ΠΎΠΊΠ° Π² ΡΠΎΡΠΌΠ΅ Π½Π°ΡΡΡΠΏΠ°Π΅Ρ Π΅Π΅ ΡΠ°Π·ΡΠ΅Π΄ΠΈΠ½Π΅Π½ΠΈΠ΅.
Π. ΠΡΠΎΡΠ΅ΡΡ Π²ΡΠ΄Π΅ΡΠΆΠΊΠΈ ΠΏΠΎ Π²ΡΠ΅ΠΌΠ΅Π½ΠΈ Π±Π»ΠΎΠΊΠΎΠ² ΠΈΠ· ΠΏΠ΅Π½ΠΎΠΏΠΎΠ»ΠΈΡΡΠΈΡΠΎΠ»Π° Π·Π°ΠΊΠ»ΡΡΠ°Π΅ΡΡΡ Π² Π΄Π²ΡΡΡΠΎΡΠΎΠ½Π½Π΅ΠΉ Π΄ΠΈΡΡΡΠ·ΠΈΠΈ Π²ΠΎΠ·Π΄ΡΡ
Π° Π²Π½ΡΡΡΡ ΠΌΠΈΠΊΡΠΎΠΏΠΎΡ, ΠΈ Π²ΡΡΠ°Π²Π½ΠΈΠ²Π°Π½ΠΈΠ΅ Π΄Π°Π²Π»Π΅Π½ΠΈΡ ΠΌΠ΅ΠΆΠ΄Ρ Π²Π½ΡΡΡΠ΅Π½Π½ΠΈΠΌ ΠΎΠ±ΡΠ΅ΠΌΠΎΠΌ ΡΡΠ΅Π΅ΠΊ ΠΈ Π°ΡΠΌΠΎΡΡΠ΅ΡΠΎΠΉ. Π‘ΡΡΠΊΠ° Π±Π»ΠΎΠΊΠΎΠ² Π·Π°ΠΊΠ»ΡΡΠ°Π΅ΡΡΡ Π² Π²ΡΠΏΠ°ΡΠΈΠ²Π°Π½ΠΈΠΈ ΠΏΠΎΠ²Π΅ΡΡ
Π½ΠΎΡΡΠ½ΠΎΠΉ Π²Π»Π°Π³ΠΈ Π² Π°ΡΠΌΠΎΡΡΠ΅ΡΡ.
2. Π‘ΡΡΡΠ΅
Π‘ΡΡΡΠ΅ΠΌ Π΄Π»Ρ ΠΏΡΠΎΠΈΠ·Π²ΠΎΠ΄ΡΡΠ²Π° Π±Π»ΠΎΠΊΠΎΠ² ΠΈΠ· ΠΏΠ΅Π½ΠΎΠΏΠΎΠ»ΠΈΡΡΠΈΡΠΎΠ»Π° ΡΠ²Π»ΡΡΡΡΡ Π³ΡΠ°Π½ΡΠ»Ρ ΠΏΠΎΠ»ΠΈΡΡΠΈΡΠΎΠ»Π°, ΡΠΎΠ΄Π΅ΡΠΆΠ°ΡΠΈΠ΅ ΠΏΠΎΡΠΎΡΠΎΡ. Π ΡΠΎΡΡΠ°Π² ΠΏΠΎΡΠΎΡΠΎΡΠ° Π²Ρ ΠΎΠ΄ΡΡ Π½ΠΈΠ·ΠΊΠΎΠΊΠΈΠΏΡΡΠΈΠ΅ ΡΠ³Π»Π΅Π²ΠΎΠ΄ΠΎΡΠΎΠ΄Ρ β ΠΈΠ·ΠΎΠΏΠ΅Π½ΡΠ°Π½, ΠΏΠ΅Π½ΡΠ°Π½ ΠΈ Π΄ΡΡΠ³ΠΈΠ΅.
2.2 Π€ΠΈΠ·ΠΈΠΊΠΎ-Ρ ΠΈΠΌΠΈΡΠ΅ΡΠΊΠΈΠ΅ ΡΠ²ΠΎΠΉΡΡΠ²Π° ΠΈ ΡΡΠ΅Π±ΠΎΠ²Π°Π½ΠΈΡ ΠΊ ΠΊΠ°ΡΠ΅ΡΡΠ²Ρ ΡΡΡΡΡ
ΠΡΠ°Π½ΡΠ»Ρ ΠΏΠΎΠ»ΠΈΡΡΠΈΡΠΎΠ»Π°, ΠΏΡΠ΅Π΄Π½Π°Π·Π½Π°ΡΠ΅Π½Π½ΡΠ΅ Π΄Π»Ρ ΠΏΡΠΎΠΈΠ·Π²ΠΎΠ΄ΡΡΠ²Π° Π±Π»ΠΎΠΊΠΎΠ² ΠΈ ΠΏΠ»ΠΈΡ, Π΄ΠΎΠ»ΠΆΠ½Ρ ΠΈΠΌΠ΅ΡΡ Π²ΠΈΠ΄ ΠΊΡΡΠ³Π»ΡΡ ΡΠ°ΡΠΈΠΊΠΎΠ² Π±Π΅Π»ΠΎΠ³ΠΎ ΠΈΠ»ΠΈ ΠΏΠΎΠ»ΡΠΏΡΠΎΠ·ΡΠ°ΡΠ½ΠΎΠ³ΠΎ ΡΠ²Π΅ΡΠ°. ΠΠΎΠΏΡΡΠΊΠ°Π΅ΡΡΡ Π½Π°Π»ΠΈΡΠΈΠ΅ ΡΠ΅ΡΠΏΠΎΠ²ΠΈΠ΄Π½ΡΡ ΠΈ ΡΠΈΡΠΎΠΎΠ±ΡΠ°Π·Π½ΡΡ Π³ΡΠ°Π½ΡΠ» ΠΏΠΎΠ»ΠΈΡΡΠΈΡΠΎΠ»Π°.
Π’ΡΠ΅Π±ΠΎΠ²Π°Π½ΠΈΡ ΠΊ Π³ΡΠ°Π½ΡΠ»Π°ΠΌ
Π’ΡΠ΅Π±ΠΎΠ²Π°Π½ΠΈΡ | ΠΠ½Π°ΡΠ΅Π½ΠΈΠ΅ |
Π£Π΄Π΅Π»ΡΠ½Π°Ρ ΠΏΠ»ΠΎΡΠ½ΠΎΡΡΡ ΡΠΎΠ±ΡΡΠ²Π΅Π½Π½ΠΎ Π³ΡΠ°Π½ΡΠ», Π³/ΡΠΌ3 | 1.03-1.05 |
Π£Π΄Π΅Π»ΡΠ½Π°Ρ ΠΏΠ»ΠΎΡΠ½ΠΎΡΡΡ Π³ΡΠ°Π½ΡΠ» Π½Π°Π΄ΡΠΏβΡ, Π³/ΡΠΌ3 | ΠΠΊΠΎΠ»ΠΎ 0,6 |
Π‘ΠΎΠ΄Π΅ΡΠΆΠ°Π½ΠΈΠ΅ ΠΌΠΎΠ½ΠΎΠΌΠ΅ΡΠ° ΡΡΠΈΡΠΎΠ»Π°, %, Π½Π΅ Π±ΠΎΠ»Π΅Π΅ | 1,2 |
ΠΡΠ·ΠΊΠΎΡΡΡ 1% ΡΠ°ΡΡΠ²ΠΎΡΠ° Π±Π΅Π½Π·ΠΈΠ½Π° Π² ΠΊΠΠ° | 1,0-1,3 |
ΠΠ°ΠΊΡΠΈΠΌΠ°Π»ΡΠ½ΠΎΠ΅ ΡΠΎΠ΄Π΅ΡΠΆΠ°Π½ΠΈΠ΅ Π²Π»Π°Π³ΠΈ, % | 5,0 |
ΠΡΠΎΡΠ΅Π² β ΠΌΠ°ΠΊΡΠΈΠΌΠ°Π»ΡΠ½ΡΠΉ ΠΎΡΡΠ°ΡΠΎΠΊ Π½Π° ΡΠΈΡΠ΅ Ρ ΠΊΠ²Π°Π΄ΡΠ°ΡΠ½ΡΠΌ ΡΠ΅ΡΠ΅Π½ΠΈΠ΅ΠΌ | 4,0 |
Β
2.3. ΠΠΎΡΡΠ°Π²ΠΊΠ° ΠΈ Ρ ΡΠ°Π½Π΅Π½ΠΈΠ΅ ΡΡΡΡΡ.
Β 2.3.1. Π’ΡΠ΅Π±ΠΎΠ²Π°Π½ΠΈΡ ΠΊ Π΄ΠΎΡΡΠ°Π²ΠΊΠ΅ ΡΡΡΡΡ
Π‘ΡΡΡΠ΅ Π΄ΠΎΡΡΠ°Π²Π»ΡΠ΅ΡΡΡ Π² Π²ΠΈΠ΄Π΅ ΡΠΏΠ°ΠΊΠΎΠ²ΠΎΠΊ Π² Π·Π°ΠΊΡΡΡΡΡ
ΡΡΠ΅Π΄ΡΡΠ²Π°Ρ
Π΄ΠΎΡΡΠ°Π²ΠΊΠΈ β ΠΆΠ΅Π»Π΅Π·Π½ΠΎΠ΄ΠΎΡΠΎΠΆΠ½ΡΠΌ ΠΈΠ»ΠΈ
Π°Π²ΡΠΎΠΌΠΎΠ±ΠΈΠ»ΡΠ½ΡΠΌ ΡΡΠ°Π½ΡΠΏΠΎΡΡΠΎΠΌ. Π Π°Π·Π³ΡΡΠ·ΠΊΠ° ΠΏΡΠΎΠΈΠ·Π²ΠΎΠ΄ΠΈΡΡΡ Π½Π° ΡΠ°Π·Π³ΡΡΠ·ΠΎΡΠ½ΠΎΠΉ ΡΠ°ΠΌΠΏΠ΅ ΠΈ ΡΡΡΡΡ Π΄ΠΎΡΡΠ°Π²Π»ΡΠ΅ΡΡΡ Π½Π° Π·Π°ΠΊΡΡΡΡΠΉ ΡΠΊΠ»Π°Π΄. ΠΠΎΠ½ΡΡΠΎΠ»Ρ Π·Π° ΠΊΠΎΠ»ΠΈΡΠ΅ΡΡΠ²Π΅Π½Π½ΡΠΌΠΈ Ρ
Π°ΡΠ°ΠΊΡΠ΅ΡΠΈΡΡΠΈΠΊΠ°ΠΌΠΈ Π΄ΠΎΡΡΠ°Π²Π»Π΅Π½Π½ΠΎΠ³ΠΎ ΡΡΡΡΡ ΠΏΡΠΎΠΈΠ·Π²ΠΎΠ΄ΠΈΡΡΡ Π»Π°Π±ΠΎΡΠ°ΡΠΎΡΠ½ΡΠΌ ΠΎΡΠ΄Π΅Π»ΠΎΠΌ.
ΠΠΎΠ½ΡΡΠΎΠ»Ρ Π΄ΠΎΠ»ΠΆΠ΅Π½ ΠΏΡΠΎΠΈΠ·Π²ΠΎΠ΄ΠΈΡΡΡΡ ΡΠ»Π΅Π΄ΡΡΡΠΈΠΌ ΠΎΠ±ΡΠ°Π·ΠΎΠΌ:
Π°) ΠΠΎΠ½ΡΡΠΎΠ»Ρ ΡΠΎΠ΄Π΅ΡΠΆΠ°Π½ΠΈΡ Π²Π»Π°ΠΆΠ½ΠΎΡΡΠΈ Π² Π³ΡΠ°Π½ΡΠ»Π°Ρ
Π±) ΠΠΏΡΠ΅Π΄Π΅Π»Π΅Π½ΠΈΠ΅ ΡΠΎΠ΄Π΅ΡΠΆΠ°Π½ΠΈΡ ΠΌΠΎΠ½ΠΎΠΌΠ΅ΡΠ° Π² Π³ΡΠ°Π½ΡΠ»Π°Ρ
Π²) ΠΠΏΡΠ΅Π΄Π΅Π»Π΅Π½ΠΈΠ΅ Π²ΡΠ·ΠΊΠΎΡΡΠΈ Π³ΡΠ°Π½ΡΠ» Π² 1% Π±Π΅Π½Π·ΠΈΠ½ΠΎΠ²ΠΎΠΌ ΡΠ°ΡΡΠ²ΠΎΡΠ΅
Π³) ΠΡΠΎΠ±Π½ΠΎΠ΅ Π²ΡΠΏΠ΅Π½ΠΈΠ²Π°Π½ΠΈΠ΅ Π³ΡΠ°Π½ΡΠ»
Π΄) ΠΠΏΡΠ΅Π΄Π΅Π»Π΅Π½ΠΈΠ΅ ΡΠ΄Π΅Π»ΡΠ½ΠΎΠ³ΠΎ Π²Π΅ΡΠ° Π²ΡΠΏΠ΅Π½Π΅Π½Π½ΡΡ
Π³ΡΠ°Π½ΡΠ»
Π΅) ΠΠ½Π°Π»ΠΈΠ· ΠΎΡΡΠ°ΡΠΊΠ° Π½Π° ΡΠΈΡΠ΅
ΠΆ) ΠΡΠΎΠ±Π½ΠΎΠ΅ ΡΠΎΡΠΌΠΎΠ²Π°Π½ΠΈΠ΅ Π²ΡΠΏΠ΅Π½Π΅Π½Π½ΡΡ
Π³ΡΠ°Π½ΡΠ»
ΠΠΎΠ³ΡΡ Π±ΡΡΡ Π²ΡΠΏΠΎΠ»Π½Π΅Π½Ρ Π΄ΠΎΠΏΠΎΠ»Π½ΠΈΡΠ΅Π»ΡΠ½ΡΠ΅ ΠΈΡΠΏΡΡΠ°Π½ΠΈΡ ΠΊΠ°ΡΠ΅ΡΡΠ²Π° Π² ΡΠΎΠΎΡΠ²Π΅ΡΡΡΠ²ΠΈΠΈ Ρ ΠΌΠ΅ΡΠΎΠ΄ΠΈΠΊΠΎΠΉ Π°ΡΡΠ΅ΡΡΠ°ΡΠΈΠΈ ΡΡΡΡΡ, ΠΏΠΎΠ΄Π°Π½Π½ΠΎΠΉ ΠΏΡΠΎΠΈΠ·Π²ΠΎΠ΄ΠΈΡΠ΅Π»Π΅ΠΌ ΠΈΠ»ΠΈ ΠΌΠ΅ΡΠΎΠ΄ΠΈΠΊΠΎΠΉ, ΠΏΡΠΈΠ½ΡΡΠΎΠΉ Π² ΡΡΡΠ°Π½Π΅.
2.3.2. Π‘ΠΊΠ»Π°Π΄ΠΈΡΠΎΠ²Π°Π½ΠΈΠ΅ ΡΡΡΡΡ
Π‘ΡΡΡΠ΅ Ρ ΡΠ°Π½ΠΈΡΡΡΡ Π½Π° ΡΠΊΠ»Π°Π΄Π΅. Π’Π΅ΠΌΠΏΠ΅ΡΠ°ΡΡΡΠ° Π² ΡΠΊΠ»Π°Π΄ΡΠΊΠΎΠΌ ΠΏΠΎΠΌΠ΅ΡΠ΅Π½ΠΈΠΈ Π½Π΅ Π΄ΠΎΠ»ΠΆΠ½Π° ΠΏΡΠ΅Π²ΡΡΠ°ΡΡ 25-ΡΠΈ Π³ΡΠ°Π΄ΡΡΠΎΠ² Π¦Π΅Π»ΡΡΠΈΡ. Π£ΠΏΠ°ΠΊΠΎΠ²ΠΊΠΈ Π΄ΠΎΠ»ΠΆΠ½Ρ Ρ ΡΠ°Π½ΠΈΡΡΡΡ Π½Π° Π΄Π΅ΡΠ΅Π²ΡΠ½Π½ΡΡ ΠΏΠΎΠ΄Π΄ΠΎΠ½Π°Ρ Ρ Π²ΡΡΠΎΡΠΎΠΉ ΡΡΠ°Π±Π΅Π»Ρ Π½Π΅ Π±ΠΎΠ»Π΅Π΅ 3 ΠΌ. ΠΠ΅ΡΠ°Π»Π»ΠΈΡΠ΅ΡΠΊΠΈΠ΅ Π±ΠΎΡΠΊΠΈ ΡΠΊΠ»Π°Π΄ΠΈΡΠΎΠ²Π°ΡΡ Π² Π²ΡΡΠΎΡΡ Π½Π΅ Π±ΠΎΠ»Π΅Π΅ 1-3. Π ΡΠΊΠ»Π°Π΄Π΅ Π½Π°Π΄Π»Π΅ΠΆΠΈΡ ΠΎΠ±Π΅ΡΠΏΠ΅ΡΠΈΡΡ Ρ ΠΎΡΠΎΡΡΡ Π²Π΅Π½ΡΠΈΠ»ΡΡΠΈΡ.
3. Π₯Π°ΡΠ°ΠΊΡΠ΅ΡΠΈΡΡΠΈΠΊΠ° ΠΈΡΡΠΎΡΠ½ΠΈΠΊΠΎΠ² ΡΠ½Π΅ΡΠ³ΠΈΠΈ
Β 3.1. ΠΠΎΠ΄ΡΠ½ΠΎΠΉ ΠΏΠ°Ρ
ΠΡΠΎΡΠ΅ΡΡ ΠΏΡΠΎΠΈΠ·Π²ΠΎΠ΄ΡΡΠ²Π° ΠΏΠ΅Π½ΠΎΠΏΠ»Π°ΡΡΠ° ΠΈΠ· Π²ΡΠΏΠ΅Π½ΠΈΠ²Π°ΡΡΠ΅Π³ΠΎΡΡ ΠΏΠΎΠ»ΠΈΡΡΠΈΡΠΎΠ»Π° ΡΡΠ΅Π±ΡΠ΅Ρ Π΄ΠΎΡΡΠ°Π²ΠΊΠΈ ΡΠ΅ΠΏΠ»Π° ΠΊΠ°ΠΊ
ΡΡΠ΅Π΄ΡΡΠ²Π° ΡΠ½Π΅ΡΠ³ΠΈΠΈ Π½Π°Π³ΡΠ΅Π²Π° Π΄Π»Ρ ΠΏΠ΅ΡΠ²ΠΈΡΠ½ΠΎΠ³ΠΎ ΠΏΡΠΎΡΠ΅ΡΡΠ° Π²ΡΠΏΠ΅Π½ΠΈΠ²Π°Π½ΠΈΡ, ΠΏΡΠΎΡΠ΅ΡΡΠ° ΡΠΎΡΠΌΠΈΡΠΎΠ²Π°Π½ΠΈΡ Π±Π»ΠΎΠΊΠΎΠ², Π° ΡΠ°ΠΊΠΆΠ΅ Π½Π°Π³ΡΠ΅Π²Π°Π½ΠΈΡ Π²ΠΎΠ·Π΄ΡΡ
Π° ΡΡΡΠΈΠ»ΠΊΠΈ ΠΈ ΠΏΠ½Π΅Π²ΠΌΠ°ΡΠΈΡΠ΅ΡΠΊΠΎΠ³ΠΎ ΡΡΠ°Π½ΡΠΏΠΎΡΡΠΈΡΠΎΠ²Π°Π½ΠΈΡ Π²ΡΠΏΠ΅Π½Π΅Π½Π½ΠΎΠ³ΠΎ ΡΡΡΡΡ. ΠΠΎΡΠ»Π΅ ΠΏΡΠΎΠ²Π΅Π΄Π΅Π½ΠΈΡ ΡΠΊΡΠΏΠ΅ΡΠΈΠΌΠ΅Π½ΡΠ° Ρ Π΄ΡΡΠ³ΠΈΠΌΠΈ ΡΠΎΡΠΌΠ°ΠΌΠΈ ΡΠ½Π΅ΡΠ³ΠΈΠΈ, ΠΌΡ ΠΏΡΠΈΡΠ»ΠΈΒ ΠΊ Π²ΡΠ²ΠΎΠ΄Ρ, ΡΡΠΎ Π½Π°ΠΈΠ±ΠΎΠ»Π΅Π΅ ΠΏΡΠ°ΠΊΡΠΈΡΠ½ΡΠΉ ΠΈΡΡΠΎΡΠ½ΠΈΠΊ ΡΠ½Π΅ΡΠ³ΠΈΠΈ β ΡΡΠΎ Π²ΠΎΠ΄ΡΠ½ΠΎΠΉ ΠΏΠ°Ρ.
ΠΠΎΠ΄ΡΠ½ΠΎΠΉ ΠΏΠ°Ρ, ΠΏΡΠΈΠΌΠ΅Π½ΡΠ΅ΠΌΡΠΉ Π΄Π»Ρ ΠΏΡΠ΅ΠΎΠ±ΡΠ°Π·ΠΎΠ²Π°Π½ΠΈΡ ΠΏΠ΅Π½ΠΎΠΏΠΎΠ»ΠΈΡΡΠΈΡΠΎΠ»Π°, Π΄ΠΎΠ»ΠΆΠ΅Π½ Π±ΡΡΡ Π½Π°ΡΡΡΠ΅Π½Π½ΡΠΌ ΠΏΠ°ΡΠΎΠΌ ΠΏΡΠΈ Π΄Π°Π²Π»Π΅Π½ΠΈΠΈ ΠΊΠ°ΠΊ ΠΌΠΈΠ½ΠΈΠΌΡΠΌ 0,25 ΠΌΠΠ°, Π½Π΅ ΠΏΠ΅ΡΠ΅Π½Π°ΡΡΡΠ΅Π½Π½ΡΠΌ Π²ΠΎΠ΄ΠΎΠΉ. ΠΠΏΡΠΈΠΌΠ°Π»ΡΠ½ΠΎΠ΅ Π΄Π°Π²Π»Π΅Π½ΠΈΠ΅ Π΄Π»Ρ ΡΠΎΡΠΌΠΈΡΠΎΠ²Π°Π½ΠΈΡ Π±Π»ΠΎΠΊΠΎΠ² ΠΈ ΠΏΠΎΡΠ»Π΅Π΄ΡΡΡΠ΅Π³ΠΎ Π²ΡΠΏΠ΅Π½ΠΈΠ²Π°Π½ΠΈΡ ΡΠΎΡΡΠ°Π²Π»ΡΠ΅Ρ 0,02-0,07 ΠΌΠΠ°.
ΠΠΎΠ»Π΅Π΅ Π²ΡΡΠΎΠΊΠΎΠ΅ Π΄Π°Π²Π»Π΅Π½ΠΈΠ΅ ΠΏΡΠΈΠ²ΠΎΠ΄ΠΈΡ ΠΊ ΡΠ²Π΅Π»ΠΈΡΠ΅Π½ΠΈΡ ΡΠΊΠΎΡΠΎΡΡΠΈ ΠΏΠΎΡΡΡΠΏΠ»Π΅Π½ΠΈΡ ΠΏΠ°ΡΠ° Π² ΡΠΎΡΠΌΡ (Π²ΡΠ΅ΠΌΡ
Β 3.2. ΠΠ»Π΅ΠΊΡΡΠΎΡΠ½Π΅ΡΠ³ΠΈΡ
ΠΠ»Π΅ΠΊΡΡΠΎΡΠ½Π΅ΡΠ³ΠΈΡ ΠΏΡΠΈΠΌΠ΅Π½ΡΠ΅ΡΡΡ Π΄Π»Ρ ΠΏΡΠΈΠ²Π΅Π΄Π΅Π½ΠΈΡ Π² Π΄Π΅ΠΉΡΡΠ²ΠΈΠ΅ Π²ΡΠΏΠ΅Π½ΠΈΠ²Π°ΡΠ΅Π»Ρ, ΡΠΎΡΠΌ, ΠΎΡΠ½Π°ΡΠ΅Π½ΠΈΡ Π΄Π»Ρ
ΡΠ°Π·ΡΠ΅Π·Π°Π½ΠΈΡ Π±Π»ΠΎΠΊΠΎΠ², ΠΏΠ½Π΅Π²ΠΌΠΎΡΡΠ°Π½ΡΠΏΠΎΡΡΠ° ΠΈ ΡΡΡΠ°Π½ΠΎΠ²Π»Π΅Π½Π½ΠΎΠ³ΠΎ ΠΎΡΠ²Π΅ΡΠ΅Π½ΠΈΡ.
ΠΠ»Π΅ΠΊΡΡΠΎΡΠ½Π΅ΡΠ³ΠΈΡ ΠΏΠΎΡΡΠ°Π²Π»ΡΠ΅ΡΡΡ ΠΎΡ ΠΏΡΠΎΠΌΡΡΠ»Π΅Π½Π½ΡΡ
ΠΈΡΡΠΎΡΠ½ΠΈΠΊΠΎΠ² ΠΏΠΈΡΠ°Π½ΠΈΡ ΠΏΡΠΈ Π½Π°ΠΏΡΡΠΆΠ΅Π½ΠΈΠΈ 380 ΠΈΠ»ΠΈ 220 Π ΠΏΠ΅ΡΠ΅ΠΌΠ΅Π½Π½ΠΎΠ³ΠΎ ΡΠΎΠΊΠ°. ΠΠΎΠ½ΡΡΠΎΠ»Ρ ΠΈ ΠΈΠ·ΠΎΠ»ΡΡΠΈΡ ΡΠΎΠΊΠΎΠ½Π΅ΡΡΡΠΈΡ
ΡΠ°ΡΡΠ΅ΠΉ ΠΏΡΠΎΠΈΠ·Π²ΠΎΠ΄ΠΈΡΡΡ Π² ΡΠΎΠΎΡΠ²Π΅ΡΡΡΠ²ΠΈΠΈ Ρ ΡΡΠ΅Π±ΠΎΠ²Π°Π½ΠΈΡΠΌΠΈ ΡΠ»ΡΠΆΠ±Ρ ΡΠ»Π΅ΠΊΡΡΠΎΠ±Π΅Π·ΠΎΠΏΠ°ΡΠ½ΠΎΡΡΠΈ ΠΏΡΠ΅Π΄ΠΏΡΠΈΡΡΠΈΡ.
Β 3.3. Π‘ΠΆΠ°ΡΡΠΉ Π²ΠΎΠ·Π΄ΡΡ
Π‘ΠΆΠ°ΡΡΠΉ Π²ΠΎΠ·Π΄ΡΡ
ΠΏΡΠ΅Π΄Π½Π°Π·Π½Π°ΡΠ΅Π½ Π΄Π»Ρ ΠΏΡΠΈΠ²Π΅Π΄Π΅Π½ΠΈΡ Π² Π΄Π΅ΠΉΡΡΠ²ΠΈΠ΅ ΠΏΠ½Π΅Π²ΠΌΠ°ΡΠΈΡΠ΅ΡΠΊΠΈΡ
ΡΡΡΡΠΎΠΉΡΡΠ²: Π·Π°ΠΊΡΡΠ²Π°Π½ΠΈΡ ΠΈ
ΠΎΡΠΊΡΡΠ²Π°Π½ΠΈΡ ΡΠΎΡΠΌ, Π° ΡΠ°ΠΊΠΆΠ΅ Π²ΡΡΠ°Π»ΠΊΠΈΠ²Π°Π½ΠΈΡ ΡΡΠΎΡΠΌΠΈΡΠΎΠ²Π°Π½Π½ΡΡ
Π±Π»ΠΎΠΊΠΎΠ². ΠΠ°Π²Π»Π΅Π½ΠΈΠ΅ ΡΠΆΠ°ΡΠΎΠ³ΠΎ Π²ΠΎΠ·Π΄ΡΡ
Π° ΠΎΡ ΠΈΡΡΠΎΡΠ½ΠΈΠΊΠ° Π΄ΠΎΠ»ΠΆΠ½ΠΎ ΡΠΎΡΡΠ°Π²Π»ΡΡΡ Π½Π΅ ΠΌΠ΅Π½Π΅Π΅ 5 Π°ΡΠΌΠΎΡΡΠ΅Ρ. ΠΠΎΠ»ΡΡΠ΅Π½Π½ΡΠΉ ΡΠΆΠ°ΡΡΠΉ Π²ΠΎΠ·Π΄ΡΡ
ΠΏΡΠΎΡ
ΠΎΠ΄ΠΈΡ ΡΠ΅ΡΠ΅Π· Π½Π°Π³ΡΠ΅Π²Π°ΡΠ΅Π»ΡΠ½ΡΠΉ ΡΠ»Π΅ΠΌΠ΅Π½Ρ ΠΈ ΡΠ°ΡΠΏΡΠ΅Π΄Π΅Π»ΡΠ΅ΡΡΡ ΠΏΡΠΈ ΠΏΠΎΠΌΠΎΡΠΈ ΡΠΈΡΡΠ΅ΠΌΡ ΡΡΡΠ±ΠΎΠΏΡΠΎΠ²ΠΎΠ΄ΠΎΠ². ΠΠΎΠ½ΡΡΠΎΠ»Ρ ΠΈ ΠΎΠ±ΡΠ»ΡΠΆΠΈΠ²Π°Π½ΠΈΠ΅ ΡΠ°ΡΡΠ΅ΠΉ ΡΠΈΡΡΠ΅ΠΌΡ ΠΏΠΎΠ΄Π°ΡΠΈ ΡΠΆΠ°ΡΠΎΠ³ΠΎ Π²ΠΎΠ·Π΄ΡΡ
Π° ΠΏΡΠΎΠΈΠ·Π²ΠΎΠ΄ΠΈΡ ΡΠ»ΡΠΆΠ±Π° ΡΠ½Π΅ΡΠ³ΠΎΠ±Π΅Π·ΠΎΠΏΠ°ΡΠ½ΠΎΡΡΠΈ ΠΏΡΠ΅Π΄ΠΏΡΠΈΡΡΠΈΡ.
4. Π₯Π°ΡΠ°ΠΊΡΠ΅ΡΠΈΡΡΠΈΠΊΠ° ΠΏΠΎΠ»ΡΡΠ°Π±ΡΠΈΠΊΠ°ΡΠ°
ΠΠΎΠ»ΡΡΠ°Π±ΡΠΈΠΊΠ°ΡΠΎΠΌ Π΄Π»Ρ ΠΏΡΠΎΠΈΠ·Π²ΠΎΠ΄ΡΡΠ²Π° Π±Π»ΠΎΠΊΠΎΠ² ΠΈΠ· Π²ΡΠΏΠ΅Π½ΠΈΠ²Π°ΡΡΠ΅Π³ΠΎΡΡ ΠΏΠΎΠ»ΠΈΡΡΠΈΡΠΎΠ»Π° ΡΠ²Π»ΡΡΡΡΡ Π²ΡΠΏΠ΅Π½Π΅Π½Π½ΡΠ΅ Π³ΡΠ°Π½ΡΠ»Ρ. ΠΠ½ΠΈ ΠΏΠΎΠ»ΡΡΠ°ΡΡΡΡ Π½Π° ΡΡΠ°ΠΏΠ΅ Π²ΡΠΏΠ΅Π½ΠΈΠ²Π°Π½ΠΈΡ ΠΈ ΠΏΠΎΡΠ»Π΅ Π²ΡΡΡΡΠΈΠ²Π°Π½ΠΈΡ ΠΏΠΎΠ΄Π°ΡΡΡΡ Π΄Π»Ρ ΡΠΎΡΠΌΠΈΡΠΎΠ²Π°Π½ΠΈΡ Π±Π»ΠΎΠΊΠΎΠ².
Β 4.1. Π€ΠΈΠ·ΠΈΠΊΠΎ-Ρ ΠΈΠΌΠΈΡΠ΅ΡΠΊΠΈΠ΅ ΡΠ²ΠΎΠΉΡΡΠ²Π°
Π’ΡΠ΅Π±ΠΎΠ²Π°Π½ΠΈΡ | ΠΠ½Π°ΡΠ΅Π½ΠΈΠ΅ | ΠΠ΅ΡΡΠΎ ΠΏΡΠΎΠ²Π΅Π΄Π΅Π½ΠΈΡ ΠΊΠΎΠ½ΡΡΠΎΠ»Ρ |
Π£Π΄Π΅Π»ΡΠ½ΡΠΉ Π²Π΅Ρ Π½Π°ΡΡΠΏΡΡ Π² Π³Ρ./1 | 15-20 | ΠΠ±ΡΠ»ΡΠΆΠΈΠ²Π°ΡΡΠ°Ρ Π»Π°Π±ΠΎΡΠ°ΡΠΎΡΠΈΡ |
ΠΠ°ΠΊΡΠΈΠΌΠ°Π»ΡΠ½ΡΠΉ Π΄ΠΈΠ°ΠΌΠ΅ΡΡ Π³ΡΠ°Π½ΡΠ» Π² ΠΌΠΌ | 20 | Β |
ΠΠΈΠ½ΠΈΠΌΠ°Π»ΡΠ½ΡΠΉ Π΄ΠΈΠ°ΠΌΠ΅ΡΡ Π³ΡΠ°Π½ΡΠ» Π² ΠΌΠΌ | 0,7 | Β |
ΠΠ°ΠΊΡΠΈΠΌΠ°Π»ΡΠ½ΠΎΠ΅ Π²ΡΠ΅ΠΌΡ Π²ΡΠ΄Π΅ΡΠΆΠΊΠΈ ΠΏΠΎ Π²ΡΠ΅ΠΌΠ΅Π½ΠΈ ΠΎΡ ΠΌΠΎΠΌΠ΅Π½ΡΠ° Π²ΡΠΏΠ΅Π½ΠΈΠ²Π°Π½ΠΈΡ | 5 | ΠΠ΅ΡΡΠΎΠ½Π°Π», ΠΎΠ±ΡΠ»ΡΠΆΠΈΠ²Π°ΡΡΠΈΠΉ Π±ΡΠ½ΠΊΠ΅ΡΡ Π½Π°ΠΊΠΎΠΏΠ»Π΅Π½ΠΈΡ |
ΠΠ°ΠΊΡΠΈΠΌΠ°Π»ΡΠ½ΠΎΠ΅ Π²ΡΠ΅ΠΌΡ Π²ΡΠ΄Π΅ΡΠΆΠΊΠΈ ΠΏΠΎ Π²ΡΠ΅ΠΌΠ΅Π½ΠΈ ΠΎΡ ΠΌΠΎΠΌΠ΅Π½ΡΠ° Π²ΡΠΏΠ΅Π½ΠΈΠ²Π°Π½ΠΈΡ | 8 | ΠΠ΅ΡΡΠΎΠ½Π°Π», ΠΎΠ±ΡΠ»ΡΠΆΠΈΠ²Π°ΡΡΠΈΠΉ Π±ΡΠ½ΠΊΠ΅ΡΡ Π½Π°ΠΊΠΎΠΏΠ»Π΅Π½ΠΈΡ |
ΠΠ°Π»ΠΈΡΠΈΠ΅ Π°Π³Π»ΠΎΠΌΠ΅ΡΠ°ΡΠΎΠ² ΡΠ°Π·ΠΌΠ΅ΡΠΎΠΌ Π±ΠΎΠ»Π΅Π΅ 4 ΡΠΌ (Π²ΡΠΏΠ΅Π½Π΅Π½Π½ΡΡ
| Π½Π΅ Π΄ΠΎΠΏΡΡΠΊΠ°Π΅ΡΡΡ | ΠΠ΅ΡΡΠΎΠ½Π°Π», ΠΎΠ±ΡΠ»ΡΠΆΠΈΠ²Π°ΡΡΠΈΠΉ Π²ΡΠΏΠ΅Π½ΠΈΠ²Π°ΡΠ΅Π»ΠΈ |
ΠΠ°ΠΊΡΠΈΠΌΠ°Π»ΡΠ½ΠΎΠ΅ ΠΊΠΎΠ»ΠΈΡΠ΅ΡΡΠ²ΠΎ Π²ΡΠΊΡΠΎΡΠΈΠ²ΡΠΈΡ ΡΡ ΠΎΡΡ ΠΎΠ΄ΠΎΠ² Π² % | 5 | ΠΠ΅ΡΡΠΎΠ½Π°Π», ΠΎΠ±ΡΠ»ΡΠΆΠΈΠ²Π°ΡΡΠΈΠΉ Π±ΡΠ½ΠΊΠ΅ΡΡ Π½Π°ΠΊΠΎΠΏΠ»Π΅Π½ΠΈΡ |
Β
4.2. ΠΠΎΡΡΠ°Π²ΠΊΠ° ΠΈ ΡΠΊΠ»Π°Π΄ΠΈΡΠΎΠ²Π°Π½ΠΈΠ΅
ΠΡΠΏΠ΅Π½Π΅Π½Π½ΡΠ΅ Π³ΡΠ°Π½ΡΠ»Ρ ΠΏΠΎΠ΄Π°ΡΡΡΡ ΠΏΡΠΈ ΠΏΠΎΠΌΠΎΡΠΈ ΠΏΠ½Π΅Π²ΠΌΠΎΡΡΠ°Π½ΡΠΏΠΎΡΡΠ° Π² Π±ΡΠ½ΠΊΠ΅ΡΡ Π½Π°ΠΊΠΎΠΏΠ»Π΅Π½ΠΈΡ, Π² ΠΊΠΎΡΠΎΡΡΡ
5. Π₯Π°ΡΠ°ΠΊΡΠ΅ΡΠΈΡΡΠΈΠΊΠ° ΠΏΡΠΎΠ΄ΡΠΊΡΠ°
ΠΠΎΡΠΎΠ²ΡΠΌ ΠΏΡΠΎΠ΄ΡΠΊΡΠΎΠΌ ΡΠ²Π»ΡΡΡΡΡ Π±Π»ΠΎΠΊΠΈ ΠΈΠ· ΠΏΠ΅Π½ΠΎΠΏΠΎΠ»ΠΈΡΡΠΈΡΠΎΠ»Π°. ΠΠ°Π»Π΅Π΅ ΠΈΡ
ΡΠ΅ΠΆΡΡ Π½Π° ΠΏΠ»ΠΈΡΡ ΠΏΠΎ ΡΠ°Π·ΠΌΠ΅ΡΠ°ΠΌ,
Π·Π°Π²ΠΈΡΡΡΠΈΠΌ ΠΎΡ ΡΡΠ΅Π±ΠΎΠ²Π°Π½ΠΈΠΉ Π·Π°ΠΊΠ°Π·ΡΠΈΠΊΠ°, ΡΡΠΎ ΡΠ²Π»ΡΠ΅ΡΡΡ ΡΠΆΠ΅ ΡΠΎΠ»ΡΠΊΠΎ ΠΏΡΠ΅ΠΎΠ±ΡΠ°Π·ΠΎΠ²Π°Π½ΠΈΠ΅ΠΌ Π³ΠΎΡΠΎΠ²ΠΎΠ³ΠΎ ΠΈΠ·Π΄Π΅Π»ΠΈΡ, Π½Π΅ ΠΈΠ·ΠΌΠ΅Π½ΡΡΡΠΈΠΌ Π΅Π³ΠΎ ΡΠ²ΠΎΠΉΡΡΠ²Π°.
Β Β 5.1. Π€ΠΈΠ·ΠΈΠΊΠΎ-Ρ ΠΈΠΌΠΈΡΠ΅ΡΠΊΠΈΠ΅ ΡΠ²ΠΎΠΉΡΡΠ²Π° Π±Π»ΠΎΠΊΠΎΠ² ΠΈΠ· ΠΏΠ΅Π½ΠΎΠΏΠΎΠ»ΠΈΡΡΠΈΡΠΎΠ»Π°
Π’ΡΠ΅Π±ΠΎΠ²Π°Π½ΠΈΡ | ΠΠ½Π°ΡΠ΅Π½ΠΈΡ |
Π£Π΄Π΅Π»ΡΠ½ΡΠΉ Π²Π΅Ρ, ΠΊΠ³/ΠΌ3 | 15-20 |
Π‘ΠΎΠΏΡΠΎΡΠΈΠ²Π»Π΅Π½ΠΈΠ΅ ΡΠΆΠ°ΡΠΈΡ, ΠΏΡΠΈ Π΄Π΅ΡΠΎΡΠΌΠ°ΡΠΈΠΈ ΠΏΡΠΎΠ±ΠΊΠΈ Π½Π° 10%, Π±ΠΎΠ»Π΅Π΅ ΠΊΠ³/ | 0,4 |
Π’Π΅ΡΠΌΠΎΡΡΠΎΠΉΠΊΠΎΡΡΡ, Π±ΠΎΠ»Π΅Π΅, Β°Π‘ | 60 |
Π‘ΠΎΠΏΡΠΎΡΠΈΠ²Π»Π΅Π½ΠΈΠ΅ ΠΏΡΠΎΠΏΡΡΠΊΠ°Π½ΠΈΡ ΡΠ΅ΠΏΠ»Π°, Π² ΠΊΠΊΠ°Π»/ΠΌ Β°Π‘ Π² ΡΠ°Ρ | 0,035 |
ΠΡΡΡΡΡΡΠ²ΠΈΠ΅ ΡΠ°Π·Π±ΡΡ
Π°Π½ΠΈΡ Π² Π²ΠΎΠ΄Π΅ Π² ΡΠ΅ΡΠ΅Π½ΠΈΠ΅ 24 ΡΠ°ΡΠΎΠ², ΠΌΠ΅Π½Π΅Π΅, Π² % | 1,5 |
ΠΠΈΠ³ΡΠΎΡΠΊΠΎΠΏΠΈΡΠ½ΠΎΡΡΡ Π² ΡΠ΅ΡΠ΅Π½ΠΈΠ΅ 120 ΡΠ°ΡΠΎΠ², ΠΌΠ΅Π½Π΅Π΅, Π² % | 0,6 |
Π Π°Π·ΠΌΠ΅ΡΡ | Π‘ΠΎΠΎΡΠ²Π΅ΡΡΡΠ²ΡΡΡ ΡΡΠ΅Π±ΠΎΠ²Π°Π½ΠΈΡΠΌ Π·Π°ΠΊΠ°Π·ΡΠΈΠΊΠ° |
Β
6. ΠΡΡ ΠΎΠ΄Ρ
ΠΠ°ΠΊΡΠΈΠΌΠ°Π»ΡΠ½ΠΎΠ΅ ΠΊΠΎΠ»ΠΈΡΠ΅ΡΡΠ²ΠΎ ΠΎΡΡ
ΠΎΠ΄ΠΎΠ², ΠΎΠ±ΡΠ°Π·ΡΡΡΠΈΡ
ΡΡ Π² ΡΠΈΠΊΠ»Π΅ ΠΏΡΠΎΠΈΠ·Π²ΠΎΠ΄ΡΡΠ²Π° ΠΈΠ·Π΄Π΅Π»ΠΈΠΉ Π²ΡΠΏΠ΅Π½ΠΈΠ²Π°ΡΡΠ΅Π³ΠΎΡΡ ΠΏΠΎΠ»ΠΈΡΡΠΈΡΠΎΠ»Π°, ΡΠΎΡΡΠ°Π²Π»ΡΠ΅Ρ Π½Π΅ Π±ΠΎΠ»Π΅Π΅ 6,5%. ΠΡΡ
ΠΎΠ΄Ρ ΡΠΊΠ»Π°Π΄ΡΠ²Π°ΡΡΡΡ ΠΈΠ· Π²ΡΠ±ΡΠ°ΠΊΠΎΠ²Π°Π½Π½ΡΡ
Π±Π»ΠΎΠΊΠΎΠ², ΠΏΠΎΠ»ΡΡΠ°ΡΡΠΈΡ
ΡΡ Π²ΠΎ Π²ΡΠ΅ΠΌΡ ΡΠΎΡΠΌΠΈΡΠΎΠ²Π°Π½ΠΈΡ ΠΈ ΠΊΡΠΎΡΠΊΠΈ, ΠΎΠ±ΡΠ°Π·ΡΡΡΠ΅ΠΉΡΡ ΠΏΡΠΈ ΡΠ°Π·ΡΠ΅Π·Π°Π½ΠΈΠΈ Π±Π»ΠΎΠΊΠΎΠ² Π½Π° ΠΏΠ»ΠΈΡΡ.
ΠΡΡ
ΠΎΠ΄Ρ ΡΠ°Π·ΠΌΠ΅Π»ΡΡΠ°ΡΡΡΡ Π² Π΄ΡΠΎΠ±ΠΈΠ»ΠΊΠ΅ (ΠΌΠ΅Π»ΡΠ½ΠΈΡΠ΅) ΠΈ Π² ΠΊΠ°ΡΠ΅ΡΡΠ²Π΅ ΠΊΡΠΎΡΠΊΠΈ ΠΎΡΡ
ΠΎΠ΄ΠΎΠ² Π²ΠΎΠ·Π²ΡΠ°ΡΠ°ΡΡΡΡ Π²
ΠΏΡΠΎΠΈΠ·Π²ΠΎΠ΄ΡΡΠ²ΠΎ. ΠΡΠΎΡΠΊΠ° Π² ΡΠΌΠ΅ΡΠΈ Ρ Π²ΡΠ΄Π΅ΡΠΆΠ°Π½Π½ΡΠΌΠΈ Π³ΡΠ°Π½ΡΠ»Π°ΠΌΠΈ ΠΏΡΠΈΠΌΠ΅Π½ΡΠ΅ΡΡΡ Π΄Π»Ρ ΠΏΠΎΠ²ΡΠΎΡΠ½ΠΎΠ³ΠΎ ΠΏΡΠΎΠΈΠ·Π²ΠΎΠ΄ΡΡΠ²Π° Π±Π»ΠΎΠΊΠΎΠ². ΠΠ°ΠΊΡΠΈΠΌΠ°Π»ΡΠ½ΠΎΠ΅ ΠΊΠΎΠ»ΠΈΡΠ΅ΡΡΠ²ΠΎ ΠΊΡΠΎΡΠΊΠΈ ΠΏΡΠΈ ΠΏΡΠΎΠΈΠ·Π²ΠΎΠ΄ΡΡΠ²Π΅ ΠΈ ΡΠΎΡΠΌΠΈΡΠΎΠ²Π°Π½ΠΈΠΈ Π±Π»ΠΎΠΊΠΎΠ² Π½Π΅ Π΄ΠΎΠ»ΠΆΠ½ΠΎ ΠΏΡΠ΅Π²ΡΡΠ°ΡΡ 5%.
7. ΠΠΏΠΈΡΠ°Π½ΠΈΠ΅ ΡΠ΅Ρ Π½ΠΎΠ»ΠΎΠ³ΠΈΡΠ΅ΡΠΊΠΎΠ³ΠΎ ΠΏΡΠΎΡΠ΅ΡΡΠ°
Β 7.1. ΠΠ±ΡΠ΅Π΅ ΠΎΠΏΠΈΡΠ°Π½ΠΈΠ΅ ΠΏΡΠΎΡΠ΅ΡΡΠ°
Β Β Β Β Β 7.1.1. ΠΡΠΎΡΠ΅ΡΡ Π²ΡΠΏΠ΅Π½ΠΈΠ²Π°Π½ΠΈΡ Π³ΡΠ°Π½ΡΠ»
ΠΠ΅ΡΠ²ΠΎΠΉ ΡΠ΅Ρ
Π½ΠΎΠ»ΠΎΠ³ΠΈΡΠ΅ΡΠΊΠΎΠΉ ΠΎΠΏΠ΅ΡΠ°ΡΠΈΠ΅ΠΉ ΠΏΠΎ ΠΏΡΠΎΠΈΠ·Π²ΠΎΠ΄ΡΡΠ²Ρ ΠΈΠ·Π΄Π΅Π»ΠΈΠΉ ΠΈΠ· Π²ΡΠΏΠ΅Π½ΠΈΠ²Π°ΡΡΠ΅Π³ΠΎΡΡ ΠΏΠΎΠ»ΠΈΡΡΠΈΡΠΎΠ»Π° ΡΠ²Π»ΡΠ΅ΡΡΡ Π²ΡΠΏΠ΅Π½ΠΈΠ²Π°Π½ΠΈΠ΅ Π³ΡΠ°Π½ΡΠ». ΠΡΠΎΡΠ΅ΡΡ Π²ΡΠΏΠ΅Π½ΠΈΠ²Π°Π½ΠΈΡ ΠΏΡΠΎΠΈΡΡ
ΠΎΠ΄ΠΈΡ Π±Π»Π°Π³ΠΎΠ΄Π°ΡΡ ΡΠ°ΡΡΠΈΡΠ΅Π½ΠΈΡ ΠΏΠΎΡ Π³ΡΠ°Π½ΡΠ». ΠΠΎ Π²ΡΠ΅ΠΌΡ Π²ΡΠΏΠ΅Π½ΠΈΠ²Π°Π½ΠΈΡ, ΠΏΡΠΎΠΈΠ·Π²ΠΎΠ΄ΠΈΠΌΠΎΠ³ΠΎ Π²ΠΎ Π²ΡΠΏΠ΅Π½ΠΈΠ²Π°ΡΠ΅Π»Π΅ Π½Π°ΡΡΡΠ΅Π½Π½ΡΠΌ Π²ΠΎΠ΄ΡΠ½ΡΠΌ ΠΏΠ°ΡΠΎΠΌ ΠΏΡΠΈ ΡΠ΅ΠΌΠΏΠ΅ΡΠ°ΡΡΡΠ΅ 90-100Β°Π‘, Π² ΡΡΡΡΠΊΡΡΡΠ΅ ΠΏΠΎΠ»ΠΈΡΡΠΈΡΠΎΠ»Π° ΠΎΠ±ΡΠ°Π·ΡΡΡΡΡ ΠΌΠΈΠΊΡΠΎΠΏΠΎΡΡ. ΠΠΎΠ΄ΡΠ½ΠΎΠΉ ΠΏΠ°Ρ, ΠΏΠΎΠ΄Π°ΡΡΠΈΠΉΡΡ Π²ΠΎ Π²ΡΠΏΠ΅Π½ΠΈΠ²Π°ΡΠ΅Π»Ρ, ΠΈΠ³ΡΠ°Π΅Ρ Π΄Π²ΠΎΠΉΠ½ΡΡ ΡΠΎΠ»Ρ β Π½Π°Π³ΡΠ΅Π²Π°ΡΠ΅Π»Ρ ΠΈ Π΄ΠΎΠΏΠΎΠ»Π½ΠΈΡΠ΅Π»ΡΠ½ΠΎΠΉ ΠΏΡΠΈΡΠΈΠ½Ρ Π²ΡΠΏΠ΅Π½ΠΈΠ²Π°Π½ΠΈΡ (Π±Π»Π°Π³ΠΎΠ΄Π°ΡΡ Π±ΡΡΡΡΠΎΠΉ Π΄ΠΈΡΡΡΠ·ΠΈΠΈ ΡΠ΅ΡΠ΅Π· ΡΡΠ΅Π½ΠΊΠΈ ΠΌΠΈΠΊΡΠΎΠΏΠΎΡ), ΠΈ ΠΏΡΠΈΠ²ΠΎΠ΄ΠΈΡ ΠΊ ΠΌΠ½ΠΎΠ³ΠΎΠΊΡΠ°ΡΠ½ΠΎΠΌΡ ΡΠ²Π΅Π»ΠΈΡΠ΅Π½ΠΈΡ (Π΄ΠΎ 50 ΡΠ°Π·) ΠΎΠ±ΡΠ΅ΠΌΠ° Π³ΡΠ°Π½ΡΠ». ΠΠΎ Π²ΡΠ΅ΠΌΡ Π²ΡΠΏΠ΅Π½ΠΈΠ²Π°Π½ΠΈΡ Π³ΡΠ°Π½ΡΠ»Ρ ΡΠ°Π·ΠΌΠ΅ΡΠΈΠ²Π°ΡΡΡΡ Ρ ΠΏΠΎΠΌΠΎΡΡΡ ΠΌΠ΅Ρ
Π°Π½ΠΈΡΠ΅ΡΠΊΠΎΠ³ΠΎ ΡΠ°Π·ΠΌΠ΅ΡΠΈΠ²Π°ΡΠ΅Π»Ρ Ρ ΡΠ΅Π»ΡΡ ΠΈΠ·Π±Π΅Π³Π°Π½ΠΈΡ ΠΈΡ
ΡΠ»ΠΈΠΏΠ°Π½ΠΈΡ. ΠΠΎΠ΄ΡΠ½ΠΎΠΉ ΠΏΠ°Ρ ΠΏΠΎΠ΄Π°Π΅ΡΡΡ ΠΏΠΎ ΡΠΈΡΡΠ΅ΠΌΠ΅ ΡΡΡΠ±ΠΎΠΏΡΠΎΠ²ΠΎΠ΄ΠΎΠ², ΠΏΠΎΠ΄ΠΊΠ»ΡΡΠ΅Π½Π½ΠΎΠΉ ΠΊ Π·Π°Π΄Π½Π΅ΠΉ ΡΠ°ΡΡΠΈ Π²ΡΠΏΠ΅Π½ΠΈΠ²Π°ΡΠ΅Π»Ρ. ΠΠΎ Π²ΡΠΏΠ΅Π½ΠΈΠ²Π°ΡΠ΅Π»Π΅ Π³ΡΠ°Π½ΡΠ»Ρ ΡΠ°Π·ΠΌΠ΅ΡΠΈΠ²Π°ΡΡΡΡ Π²Π΅ΡΡΠΈΠΊΠ°Π»ΡΠ½ΡΠΌ ΡΠ°Π·ΠΌΠ΅ΡΠΈΠ²Π°ΡΠ΅Π»Π΅ΠΌ, ΡΠΎΡΡΠΎΡΡΠΈΠΌ ΠΈΠ· ΡΠΈΡΡΠ΅ΠΌΡ Π»ΠΎΠΏΠ°ΡΡΠ΅ΠΉ, ΠΏΡΠ΅Π΄ΠΎΡΠ²ΡΠ°ΡΠ°ΡΡΠΈΡ
ΡΠ»ΠΈΠΏΠ°Π½ΠΈΠ΅ Π³ΡΠ°Π½ΡΠ». Π Π°ΡΡΠΈΡΠ΅Π½Π½ΡΠ΅ Π³ΡΠ°Π½ΡΠ»Ρ ΠΏΠ΅ΡΠ΅ΠΌΠ΅ΡΠ°ΡΡΡΡ ΠΊ Π³ΠΎΡΠ»ΠΎΠ²ΠΈΠ½Π΅ Π²ΡΠΏΠ΅Π½ΠΈΠ²Π°ΡΠ΅Π»Ρ ΠΈ Π²ΡΡΡΠΏΠ°ΡΡΡΡ ΡΠ΅ΡΠ΅Π· Π·Π°ΡΡΠΏΠ½ΠΎΠ΅ ΠΎΡΠ²Π΅ΡΡΡΠΈΠ΅, ΡΠ°Π·ΠΌΠ΅ΡΠ΅Π½Π½ΠΎΠ΅ Π² Π²Π΅ΡΡ
Π½Π΅ΠΉ ΡΠ°ΡΡΠΈ ΡΡΠ΅Π½ΠΊΠΈ Π²ΡΠΏΠ΅Π½ΠΈΠ²Π°ΡΠ΅Π»Ρ.
ΠΠ· Π²ΡΠΏΠ΅Π½ΠΈΠ²Π°ΡΠ΅Π»Ρ Π³ΡΠ°Π½ΡΠ»Ρ ΠΏΠΎΠ»ΠΈΡΡΠΈΡΠΎΠ»Π° Π²ΡΠΏΠ°Π΄Π°ΡΡ Π² ΡΡΡΠΈΠ»ΠΊΡ. ΠΠΎΡΠΎΠΊ ΡΠ΅ΠΏΠ»ΠΎΠ³ΠΎ Π²ΠΎΠ·Π΄ΡΡ
Π° Π²ΡΡΡΡΠΈΠ²Π°Π΅Ρ ΠΈΡ
ΠΈ Π²ΡΠ΄ΡΠ²Π°Π΅Ρ ΠΊ Π³ΠΎΡΠ»ΠΎΠ²ΠΈΠ½Π΅ ΠΈΠ½ΠΆΠ΅ΠΊΡΠΎΡΠ° ΡΠΈΡΡΠ΅ΠΌΡ ΠΏΠ½Π΅Π²ΠΌΠΎΡΡΠ°Π½ΡΠΏΠΎΡΡΠ°, ΠΊΠΎΡΠΎΡΠ°Ρ Π΄ΠΎΡΡΠ°Π²Π»ΡΠ΅Ρ Π³ΡΠ°Π½ΡΠ»Ρ Π² Π±ΡΠ½ΠΊΠ΅Ρ.
Π‘ΡΡΠΈΠ»ΠΊΠ° ΠΈ ΡΠΈΡΡΠ΅ΠΌΠ° ΠΏΠ½Π΅Π²ΠΌΠΎΡΡΠ°Π½ΡΠΏΠΎΡΡΠ° ΠΎΠ±Π΅ΡΠΏΠ΅ΡΠΈΠ²Π°ΡΡΡΡ ΡΠ΅ΠΏΠ»ΡΠΌ Π²ΠΎΠ·Π΄ΡΡ
ΠΎΠΌ (Π±ΠΎΠ»Π΅Π΅ 50Β°Π‘) ΠΏΡΡΠ΅ΠΌ Π½Π°Π³Π½Π΅ΡΠ°Π½ΠΈΡ Π²Π΅Π½ΡΠΈΠ»ΡΡΠΎΡΠ°ΠΌΠΈ ΠΈ Π½Π°Π³ΡΠ΅Π²Π° ΠΏΠ°ΡΠΎΠΌ.
Π ΡΠ΅Π»ΡΡ
ΠΎΠ±Π΅ΡΠΏΠ΅ΡΠ΅Π½ΠΈΡ Π²ΠΎΠ·ΠΌΠΎΠΆΠ½ΠΎΡΡΠΈ ΡΠ΅Π³ΡΠ»ΠΈΡΠΎΠ²Π°Π½ΠΈΡ ΠΊΠΎΠ»ΠΈΡΠ΅ΡΡΠ²Π° ΠΏΠΎΠ΄Π°Π½Π½ΡΡ
Π³ΡΠ°Π½ΡΠ», ΠΏΡΠ΅Π΄ΡΡΠΌΠΎΡΡΠ΅Π½Π°
ΡΠ΅Π³ΡΠ»ΠΈΡΠΎΠ²ΠΊΠ° ΠΊΠΎΠ»ΠΈΡΠ΅ΡΡΠ²Π° ΠΎΠ±ΠΎΡΠΎΡΠΎΠ² ΡΠ΅ΡΠ²ΡΡΠ½ΠΎΠ³ΠΎ Π΄ΠΎΠ·Π°ΡΠΎΡΠ°, Π΄Π°Π²Π»Π΅Π½ΠΈΡ ΠΏΠΎΠ΄Π²ΠΎΠ΄ΠΈΠΌΠΎΠ³ΠΎ Π²ΠΎΠ΄ΡΠ½ΠΎΠ³ΠΎ ΠΏΠ°ΡΠ°.
ΠΠΏΡΠ΅Π΄Π΅Π»Π΅Π½ΠΈΠ΅ ΠΊΠΎΠ»ΠΈΡΠ΅ΡΡΠ²Π° ΠΏΠΎΠ΄Π°Π²Π°Π΅ΠΌΡΡ
Π³ΡΠ°Π½ΡΠ» Π²ΠΎΠ·Π»ΠΎΠΆΠ΅Π½ΠΎ Π½Π° ΠΏΠ΅ΡΡΠΎΠ½Π°Π», ΠΎΠ±ΡΠ»ΡΠΆΠΈΠ²Π°ΡΡΠΈΠΉ Π²ΡΠΏΠ΅Π½ΠΈΠ²Π°ΡΠ΅Π»ΠΈ, ΠΊΠΎΡΠΎΡΡΠ΅ Π½Π°Π±Π»ΡΠ΄Π°ΡΡ Π·Π° Π²Π½Π΅ΡΠ½ΠΈΠΌ Π²ΠΈΠ΄ΠΎΠΌ Π³ΡΠ°Π½ΡΠ». ΠΠΎΠ½ΡΡΠΎΠ»ΡΠ½ΠΎ-ΠΈΠ·ΠΌΠ΅ΡΠΈΡΠ΅Π»ΡΠ½ΠΎΠ΅ ΠΎΡΠ½Π°ΡΠ΅Π½ΠΈΠ΅ Π²ΡΠΏΠ΅Π½ΠΈΠ²Π°ΡΠ΅Π»Ρ ΡΠΎΡΡΠΎΠΈΡ ΠΈΠ· ΡΠ΅Π³ΡΠ»ΠΈΡΡΡΡΠΈΡ
Π²Π΅Π½ΡΠΈΠ»Π΅ΠΉ ΠΈ ΠΊΠΎΠ½ΡΡΠΎΠ»ΡΠ½ΠΎΠ³ΠΎ ΠΌΠ°Π½ΠΎΠΌΠ΅ΡΡΠ° ΠΈΠ·ΠΌΠ΅ΡΠ΅Π½ΠΈΡ Π΄Π°Π²Π»Π΅Π½ΠΈΡ Π²ΠΎΠ΄ΡΠ½ΠΎΠ³ΠΎ ΠΏΠ°ΡΠ° Π½Π° Π»ΠΈΠ½ΠΈΠΈ ΠΏΠΎΠ΄Π°ΡΠΈ ΠΏΠ°ΡΠ° Π²ΠΎ Π²ΡΠΏΠ΅Π½ΠΈΠ²Π°ΡΠ΅Π»Ρ, Π° ΡΠ°ΠΊΠΆΠ΅ Π²Π΅ΡΠΎΠ² Π΄Π»Ρ ΠΎΠΏΡΠ΅Π΄Π΅Π»Π΅Π½ΠΈΡ Π²Π΅ΡΠ° Π½Π°ΡΡΠΏΠ°Π½Π½ΡΡ
Π²ΡΠΏΠ΅Π½Π΅Π½Π½ΡΡ
Π³ΡΠ°Π½ΡΠ».
ΠΡΡΠ°Π½ΠΎΠ²ΠΊΠ° Π²ΡΠΏΠ΅Π½ΠΈΠ²Π°ΡΠ΅Π»Ρ ΠΠ°ΠΆΠ΄ΡΠΉ ΡΠ°Π· ΠΏΡΠΈ ΠΎΡΡΠ°Π½ΠΎΠ²ΠΊΠ΅ Π²ΡΠΏΠ΅Π½ΠΈΠ²Π°ΡΠ΅Π»Ρ Π½Π΅ΠΎΠ±Ρ
ΠΎΠ΄ΠΈΠΌΠΎ Π²ΡΠΏΠΎΠ»Π½ΠΈΡΡ ΡΠ»Π΅Π΄ΡΡΡΠΈΠ΅ ΠΎΠΏΠ΅ΡΠ°ΡΠΈΠΈ:
- ΠΡΡΠ°Π½ΠΎΠ²ΠΊΠ° ΡΠ΅ΡΠ²ΡΡΠ½ΠΎΠ³ΠΎ Π΄ΠΎΠ·Π°ΡΠΎΡΠ°.
- ΠΡΠΊΠ»ΡΡΠ΅Π½ΠΈΠ΅ ΠΏΠΎΠ΄Π°ΡΠΈ ΠΏΠ°ΡΠ°.
- ΠΡΠΊΠ»ΡΡΠ΅Π½ΠΈΠ΅ ΠΌΠ΅Ρ Π°Π½ΠΈΡΠ΅ΡΠΊΠΎΠ³ΠΎ ΡΠ°Π·ΠΌΠ΅ΡΠΈΠ²Π°ΡΠ΅Π»Ρ ΠΏΠΎ ΠΎΡΡΡΠ²Π°Π½ΠΈΠΈ.
- ΠΠΏΠΎΡΠΎΠΆΠ½Π΅Π½ΠΈΠ΅ Π²ΡΠΏΠ΅Π½ΠΈΠ²Π°ΡΠ΅Π»Ρ ΠΎΡ Π²ΡΠΏΠ΅Π½Π΅Π½Π½ΡΡ Π³ΡΠ°Π½ΡΠ».
ΠΠ²Π°ΡΠΈΠΉΠ½Π°Ρ ΠΎΡΡΠ°Π½ΠΎΠ²ΠΊΠ° Π²ΡΠΏΠ΅Π½ΠΈΠ²Π°ΡΠ΅Π»Ρ (ΠΎΡΠΊΠ»ΡΡΠ΅Π½ΠΈΠ΅ ΡΠ»Π΅ΠΊΡΡΠΎΡΠ½Π΅ΡΠ³ΠΈΠΈ, ΠΎΡΡΠ°Π½ΠΎΠ²ΠΊΠ° ΡΠ°Π·ΠΌΠ΅ΡΠΈΠ²Π°ΡΠ΅Π»Ρ) Π’ΡΠ΅Π±ΡΠ΅Ρ ΠΎΡΠΊΠ»ΡΡΠ΅Π½ΠΈΡ ΠΏΠΎΠ΄Π°ΡΠΈ ΠΏΠ°ΡΠ° ΠΈ Π²ΠΊΠ»ΡΡΠ΅Π½ΠΈΠ΅ ΡΠΆΠ°ΡΠΎΠ³ΠΎ Π²ΠΎΠ·Π΄ΡΡ Π° Π΄Π»Ρ ΠΎΡΡΡΠΆΠ΅Π½ΠΈΡ Π³ΡΠ°Π½ΡΠ». ΠΠ΅ΡΠΎΠ±Π»ΡΠ΄Π΅Π½ΠΈΠ΅ ΡΡΠΈΡ ΠΏΡΠ°Π²ΠΈΠ» ΠΏΡΠΈΠ²ΠΎΠ΄ΠΈΡ ΠΊ Π΄Π°Π»ΡΠ½Π΅ΠΉΡΠ΅ΠΌΡ Π²ΡΠΏΠ΅Π½ΠΈΠ²Π°Π½ΠΈΡ Π³ΡΠ°Π½ΡΠ» ΠΈ Π²ΡΡ ΠΎΠ΄Ρ ΠΈΠ· ΡΡΡΠΎΡ ΠΏΡΠΈΠ²ΠΎΠ΄Π° Π²ΡΠΏΠ΅Π½ΠΈΠ²Π°ΡΠ΅Π»Ρ. ΠΠΎΠ·ΠΎΠ±Π½ΠΎΠ²Π»Π΅Π½ΠΈΠ΅ ΡΠ°Π±ΠΎΡΡ ΠΏΡΠΈ Π°Π²Π°ΡΠΈΠΉΠ½ΠΎΠΉ ΠΎΡΡΠ°Π½ΠΎΠ²ΠΊΠ΅ ΠΌΠΎΠΆΠ΅Ρ Π½Π°ΡΡΡΠΏΠΈΡΡ ΠΏΠΎΡΠ»Π΅ Π΅Π΅ ΠΎΠΏΠΎΡΠΎΠΆΠ½Π΅Π½ΠΈΡ ΠΎΡ Π½Π°Ρ ΠΎΠ΄ΡΡΠΈΡ ΡΡ Π²Π½ΡΡΡΠΈ Π³ΡΠ°Π½ΡΠ» ΠΈ ΠΎΡΠΌΠΎΡΡΠ° Π²ΡΠΏΠ΅Π½ΠΈΠ²Π°ΡΠ΅Π»Ρ.
Β Β Β Β Β 7.1.2. ΠΡΠ΄Π΅ΡΠΆΠΊΠ° Π³ΡΠ°Π½ΡΠ» ΠΏΠΎ Π²ΡΠ΅ΠΌΠ΅Π½ΠΈ
ΠΠΏΠΎΡΠΎΠΆΠ½ΡΡΡΠ°Ρ ΡΠ°ΡΡΡ ΠΏΠ½Π΅Π²ΠΌΠ°ΡΠΈΡΠ΅ΡΠΊΠΎΠ³ΠΎ ΡΡΠ°Π½ΡΠΏΠΎΡΡΠ° Π½Π°ΠΏΡΠ°Π²Π»ΡΠ΅Ρ Π³ΡΠ°Π½ΡΠ»Ρ Π² Π±ΡΠ½ΠΊΠ΅ΡΡ. Π Π±ΡΠ½ΠΊΠ΅ΡΠ°Ρ ΠΏΡΠΎΠΈΡΡ ΠΎΠ΄ΠΈΡ ΠΏΡΠΎΡΠ΅ΡΡ Π²ΡΠ΄Π΅ΡΠΆΠΊΠΈ ΠΏΠΎ Π²ΡΠ΅ΠΌΠ΅Π½ΠΈ Π²ΡΠΏΠ΅Π½Π΅Π½Π½ΡΡ Π³ΡΠ°Π½ΡΠ». ΠΡΠΎ ΠΏΡΠΎΡΡΠ°Ρ ΡΠ΅Ρ Π½ΠΎΠ»ΠΎΠ³ΠΈΡΠ΅ΡΠΊΠ°Ρ ΠΎΠΏΠ΅ΡΠ°ΡΠΈΡ, ΠΈΠΌΠ΅ΡΡΠ°Ρ, ΠΎΠ΄Π½Π°ΠΊΠΎ, Π±ΠΎΠ»ΡΡΠΎΠ΅ Π·Π½Π°ΡΠ΅Π½ΠΈΠ΅ Π΄Π»Ρ Π΄Π°Π»ΡΠ½Π΅ΠΉΡΠ΅Π³ΠΎ ΠΏΡΠΎΠΈΠ·Π²ΠΎΠ΄ΡΡΠ²Π° ΠΈ Π²Π»ΠΈΡΡΡΠ°Ρ Π½Π° ΠΊΠ°ΡΠ΅ΡΡΠ²ΠΎ ΡΡΠΎΡΠΌΠΎΠ²Π°Π½Π½ΡΡ ΠΈΠ·Π΄Π΅Π»ΠΈΠΉ. ΠΠΎ Π²ΡΠ΅ΠΌΡ Π²ΡΠ΄Π΅ΡΠΆΠΊΠΈ ΠΏΠΎ Π²ΡΠ΅ΠΌΠ΅Π½ΠΈ Π²ΡΠΏΠ΅Π½Π΅Π½Π½ΡΡ Π³ΡΠ°Π½ΡΠ» Π² Π±ΡΠ½ΠΊΠ΅ΡΠ°Ρ ΡΠΎ ΡΠ²ΠΎΠ±ΠΎΠ΄Π½ΠΎ ΠΏΠΎΡΡΡΠΏΠ°ΡΡΠΈΠΌ Π²ΠΎΠ·Π΄ΡΡ ΠΎΠΌ ΠΏΡΠΎΠΈΡΡ ΠΎΠ΄ΠΈΡ ΠΏΡΠΎΡΠ΅ΡΡ Π΄ΠΈΡΡΡΠ·ΠΈΠΈ Π²ΠΎΠ·Π΄ΡΡ Π° Π²Π½ΡΡΡΡ Π³ΡΠ°Π½ΡΠ» ΠΈ Π²ΡΡΠ°Π²Π½ΠΈΠ²Π°Π½ΠΈΡ ΡΠ°Π·Π½ΠΈΡΡ Π΄Π°Π²Π»Π΅Π½ΠΈΡ ΠΌΠ΅ΠΆΠ΄Ρ Π²Π½ΡΡΡΠ΅Π½Π½ΠΎΡΡΡΡ Π³ΡΠ°Π½ΡΠ» ΠΈ Π°ΡΠΌΠΎΡΡΠ΅ΡΠΎΠΉ. ΠΠ»ΠΈΡΠ΅Π»ΡΠ½ΠΎΡΡΡ ΠΏΡΠΎΡΠ΅ΡΡΠ° Π² Π·Π°Π²ΠΈΡΠΈΠΌΠΎΡΡΠΈ ΠΎΡ ΠΊΠΎΠ»ΠΈΡΠ΅ΡΡΠ²Π° Π½Π°ΡΡΠΏΠ°Π½Π½ΡΡ Π³ΡΠ°Π½ΡΠ», ΠΈΡ ΡΠ°Π·ΠΌΠ΅ΡΠ°, ΡΠ΅ΠΌΠΏΠ΅ΡΠ°ΡΡΡΡ Π²ΠΎΠ·Π΄ΡΡ Π° ΠΊΠΎΠ»Π΅Π±Π»Π΅ΡΡΡ ΠΎΡ Π½Π΅ΡΠΊΠΎΠ»ΡΠΊΠΈΡ Π΄ΠΎ Π½Π΅ΡΠΊΠΎΠ»ΡΠΊΠΈΡ Π΄Π΅ΡΡΡΠΊΠΎΠ² ΡΠ°ΡΠΎΠ².Β ΠΠ±ΡΠ΅ΠΏΡΠΈΠ·Π½Π°Π½Π½ΡΠΌ ΡΠ²Π»ΡΠ΅ΡΡΡ ΠΎΠΏΡΠΈΠΌΠ°Π»ΡΠ½ΠΎΠ΅ Π²ΡΠ΅ΠΌΡ Π²ΡΠ΄Π΅ΡΠΆΠΊΠΈ Π² ΡΠ΅ΡΠ΅Π½ΠΈΠ΅ 8 ΡΠ°ΡΠΎΠ² ΠΏΡΠΈ ΠΊΠΎΠΌΠ½Π°ΡΠ½ΠΎΠΉ ΡΠ΅ΠΌΠΏΠ΅ΡΠ°ΡΡΡΠ΅. ΠΡΠ΅ΠΌΡ Π²ΡΠ΄Π΅ΡΠΆΠΊΠΈ Π³ΡΠ°Π½ΡΠ» Π½Π΅ ΡΠ»Π΅Π΄ΡΠ΅Ρ ΠΏΡΠΎΠ΄Π»Π΅Π²Π°ΡΡ Π±ΠΎΠ»Π΅Π΅ Π½Π΅Π΄Π΅Π»ΠΈ Π²ΡΠ»Π΅Π΄ΡΡΠ²ΠΈΠ΅ ΠΏΠΎΡΠ΅ΡΠΈ ΠΏΠΎΡ ΠΈ ΡΡ ΡΠ΄ΡΠ΅Π½ΠΈΡ ΠΊΠ°ΡΠ΅ΡΡΠ²Π° ΠΈΠ·Π³ΠΎΡΠΎΠ²Π»Π΅Π½Π½ΡΡ ΠΈΠ·Π΄Π΅Π»ΠΈΠΉ ΠΈΠ· ΠΏΠ΅ΡΠ΅Π΄Π΅ΡΠΆΠ°Π½Π½ΡΡ Π³ΡΠ°Π½ΡΠ». Π ΡΠ΅Π»ΡΡ ΡΠ²Π΅ΡΠ΅Π½Π½ΠΎΡΡΠΈ, ΡΡΠΎ ΡΠ΅ΠΌΠΏΠ΅ΡΠ°ΡΡΡΠ° Π²ΡΠ΄Π΅ΡΠΆΠΈΠ²Π°Π½ΠΈΡ Π³ΡΠ°Π½ΡΠ», ΠΊΠΎΡΠΎΡΠ°Ρ Π΄ΠΎΠ»ΠΆΠ½Π° ΡΠΎΠΎΡΠ²Π΅ΡΡΡΠ²ΠΎΠ²Π°ΡΡ 22-28Β°Π‘, Π² ΠΏΠΎΠΌΠ΅ΡΠ΅Π½ΠΈΠΈ, Π² ΠΊΠΎΡΠΎΡΠΎΠΌ Π½Π°Ρ ΠΎΠ΄ΡΡΡΡ Π±ΡΠ½ΠΊΠ΅ΡΡ, ΡΡΡΠ°Π½Π°Π²Π»ΠΈΠ²Π°Π΅ΡΡΡ Π½Π°Π³ΡΠ΅Π²Π°ΡΠ΅Π»ΡΠ½Π°Ρ Π°ΠΏΠΏΠ°ΡΠ°ΡΡΡΠ°, Π° Π΄Π»Ρ ΠΊΠΎΠ½ΡΡΠΎΠ»Ρ ΡΠ»ΡΠΆΠΈΡ Π½Π°ΡΡΠ΅Π½Π½ΡΠΉ ΡΠ΅ΡΠΌΠΎΠΌΠ΅ΡΡ. Π ΡΠ΅Π»ΡΡ ΠΎΠ±Π΅ΡΠΏΠ΅ΡΠ΅Π½ΠΈΡ Π²ΡΠ΄Π΅ΡΠΆΠΈΠ²Π°Π½ΠΈΡ ΠΏΠΎ Π²ΡΠ΅ΠΌΠ΅Π½ΠΈ ΡΠ»Π΅Π΄ΡΠ΅Ρ ΠΏΡΠΎΠΈΠ·Π²ΠΎΠ΄ΠΈΡΡ Π·Π°ΠΏΠΈΡΠΈ Π² ΡΠΎΠΎΡΠ²Π΅ΡΡΡΠ²ΡΡΡΠΈΡ ΠΆΡΡΠ½Π°Π»Π°Ρ ΠΈ ΠΎΠΏΠΎΡΠΎΠΆΠ½Π΅Π½ΠΈΠ΅ Π²ΡΠΏΠΎΠ»Π½ΡΡΡ Π² ΡΠΎΠΎΡΠ²Π΅ΡΡΡΠ²ΠΈΠΈ Ρ ΡΠ°Π±Π»ΠΈΡΠΊΠ°ΠΌΠΈ Π½Π° Π±ΡΠ½ΠΊΠ΅ΡΠ°Ρ . ΠΡΠ±ΠΎΡΠΊΠ° Π³ΡΠ°Π½ΡΠ» ΠΏΡΠΎΠΈΠ·Π²ΠΎΠ΄ΠΈΡΡΡ ΠΈΠ· Π½ΠΈΠΆΠ½Π΅ΠΉ ΡΠ°ΡΡΠΈ Π±ΡΠ½ΠΊΠ΅ΡΠΎΠ² Π² ΡΠΈΡΡΠ΅ΠΌΡ ΠΏΠ½Π΅Π²ΠΌΠ°ΡΠΈΡΠ΅ΡΠΊΠΎΠ³ΠΎ ΡΡΡΠ±ΠΎΠΏΡΠΎΠ²ΠΎΠ΄Π° ΠΏΠΎ ΡΡΡΠ±Π°ΠΌ ΠΈ Ρ ΠΏΠΎΠΌΠΎΡΡΡ ΠΏΠΎΡΠΎΠΊΠ° Π²ΠΎΠ·Π΄ΡΡ Π° ΡΡΠ°Π½ΡΠΏΠΎΡΡΠΈΡΡΠ΅ΡΡΡ Π² ΡΠΎΠΎΡΠ²Π΅ΡΡΡΠ²ΡΡΡΠΈΠ΅ ΠΏΡΠΈΡΠΏΠΎΡΠΎΠ±Π»Π΅Π½ΠΈΡ Π½Π°Π΄ ΡΠΎΡΠΌΠ°ΠΌΠΈ. ΠΠ°ΠΏΠΎΠ»Π½Π΅Π½ΠΈΠ΅ ΠΏΡΠΈΡΠΏΠΎΡΠΎΠ±Π»Π΅Π½ΠΈΠΉ ΠΏΡΠΎΠΈΠ·Π²ΠΎΠ΄ΠΈΡΡΡ ΠΏΠ΅ΡΠΈΠΎΠ΄ΠΈΡΠ΅ΡΠΊΠΈ, ΠΊΠ°ΠΆΠ΄ΡΠΉ ΡΠ°Π· ΠΏΠΎΡΠ»Π΅ ΠΎΠΏΠΎΡΠΎΠΆΠ½Π΅Π½ΠΈΡ. ΠΠ· ΠΏΡΠΈΡΠΏΠΎΡΠΎΠ±Π»Π΅Π½ΠΈΠΉ Π²ΡΠΏΠ΅Π½Π΅Π½Π½ΡΠ΅ Π³ΡΠ°Π½ΡΠ»Ρ ΠΏΠΎΡΡΡΠΏΠ°ΡΡ Π² ΡΠΎΡΠΌΡ.
Β Β Β Β 7.1.3. Π€ΠΎΡΠΌΠΈΡΠΎΠ²Π°Π½ΠΈΠ΅ Π±Π»ΠΎΠΊΠΎΠ² ΠΈΠ· Π²ΡΠΏΠ΅Π½ΠΈΠ²Π°ΡΡΠ΅Π³ΠΎΡΡ ΠΏΠΎΠ»ΠΈΡΡΠΈΡΠΎΠ»Π°
Π€ΠΎΡΠΌΠΈΡΠΎΠ²Π°Π½ΠΈΠ΅ Π±Π»ΠΎΠΊΠΎΠ² ΠΈΠ· ΠΏΠ΅Π½ΠΎΠΏΠΎΠ»ΠΈΡΡΠΈΡΠΎΠ»Π° ΡΠ²Π»ΡΠ΅ΡΡΡ Π½Π°ΠΈΠ±ΠΎΠ»Π΅Π΅ Π²Π°ΠΆΠ½ΠΎΠΉ ΠΎΠΏΠ΅ΡΠ°ΡΠΈΠ΅ΠΉ Π² ΡΠΈΠΊΠ»Π΅ ΠΏΡΠΎΠΈΠ·Π²ΠΎΠ΄ΡΡΠ²Π° ΠΈΠ·Π΄Π΅Π»ΠΈΠΉ ΠΈΠ· ΠΏΠ΅Π½ΠΎΠΏΠ»Π°ΡΡΠ°. ΠΠΎ Π²ΡΠ΅ΠΌΡ ΡΡΠΎΠΉ ΠΎΠΏΠ΅ΡΠ°ΡΠΈΠΈ Π·Π°ΡΡΠΏΠ°Π½Π½ΡΠ΅ Π² ΡΠΎΡΠΌΡ Π²ΡΠΏΠ΅Π½Π΅Π½Π½ΡΠ΅ Π³ΡΠ°Π½ΡΠ»Ρ Π΄ΠΎΠΏΠΎΠ»Π½ΠΈΡΠ΅Π»ΡΠ½ΠΎ ΠΎΠ±ΡΠ°Π±Π°ΡΡΠ²Π°ΡΡΡΡ ΠΈ ΡΠ»ΠΈΠΏΠ°ΡΡΡΡ ΠΌΠ΅ΠΆΠ΄Ρ ΡΠΎΠ±ΠΎΠΉ, ΠΎΠ±ΡΠ°Π·ΡΡ ΠΈΠ·Π΄Π΅Π»ΠΈΠ΅ Π² ΡΠΎΠΎΡΠ²Π΅ΡΡΡΠ²ΠΈΠ΅ Ρ Π·Π°Π΄Π°Π½Π½ΠΎΠΉ ΡΠΎΡΠΌΠΎΠΉ, Π² ΠΊΠΎΡΠΎΡΠΎΠΉ ΠΎΠ½ΠΈ Π½Π°Ρ
ΠΎΠ΄ΡΡΡΡ.
Π‘ΠΌΡΡΠ»ΠΎΠΌ ΡΡΠΎΠΉ ΠΎΠΏΠ΅ΡΠ°ΡΠΈΠΈ ΡΠ²Π»ΡΠ΅ΡΡΡ Π½Π°Π³ΡΠ΅Π²Π°Π½ΠΈΠ΅ Π³ΡΠ°Π½ΡΠ», ΠΊΠΎΡΠΎΡΠΎΠ΅ ΠΏΡΠΈΠ²ΠΎΠ΄ΠΈΡ ΠΊ ΡΡΡΠ΅ΠΊΡΡ Π΄Π°Π»ΡΠ½Π΅ΠΉΡΠ΅Π³ΠΎ
ΡΠ²Π΅Π»ΠΈΡΠ΅Π½ΠΈΡ ΠΈΡ
ΠΎΠ±ΡΠ΅ΠΌΠ°. Π£Π²Π΅Π»ΠΈΡΠ΅Π½ΠΈΠ΅ ΠΎΠ±ΡΠ΅ΠΌΠ° Π² Π·Π°ΠΌΠΊΠ½ΡΡΠΎΠΌ ΠΏΡΠΎΡΡΡΠ°Π½ΡΡΠ²Π΅ ΡΠΎΡΠΌΡ ΡΠΎΠ²ΠΌΠ΅ΡΡΠ½ΠΎ Ρ ΠΏΠΎΠ²ΡΡΠ΅Π½Π½ΠΎΠΉ ΡΠ΅ΠΌΠΏΠ΅ΡΠ°ΡΡΡΠΎΠΉ ΠΌΠ°ΡΠ΅ΡΠΈΠ°Π»Π° ΠΏΡΠΈΠ²ΠΎΠ΄ΠΈΡ ΠΊ ΡΠ»ΠΈΠΏΠ°Π½ΠΈΡ Π³ΡΠ°Π½ΡΠ» ΠΌΠ΅ΠΆΠ΄Ρ ΡΠΎΠ±ΠΎΠΉ ΠΈ Π·Π°ΠΏΠΎΠ»Π½Π΅Π½ΠΈΡ Π²ΡΠ΅Π³ΠΎ ΠΎΠ±ΡΠ΅ΠΌΠ° ΡΠΎΡΠΌΡ.
ΠΡΠΈΠΌΠ΅Π½ΡΠ΅ΠΌΡΠΉ ΠΌΠ΅ΡΠΎΠ΄ ΠΏΡΠΎΠΈΠ·Π²ΠΎΠ΄ΡΡΠ²Π° ΡΡΠ΅Π±ΡΠ΅Ρ ΠΈΡΠΏΠΎΠ»ΡΠ·ΠΎΠ²Π°Π½ΠΈΡ Π½Π°ΡΡΡΠ΅Π½Π½ΠΎΠ³ΠΎ Π²ΠΎΠ΄ΡΠ½ΠΎΠ³ΠΎ ΠΏΠ°ΡΠ° ΠΊΠ°ΠΊ ΠΈΡΡΠΎΡΠ½ΠΈΠΊΠ° ΡΠ½Π΅ΡΠ³ΠΈΠΈ. ΠΠΎΠ΄ΡΠ½ΠΎΠΉ ΠΏΠ°Ρ Π² ΠΏΡΠΎΡΠ΅ΡΡΠ΅ ΡΠΎΡΠΌΠΈΡΠΎΠ²Π°Π½ΠΈΡ, ΡΠ°ΠΊ ΠΊΠ°ΠΊ ΠΈ ΠΏΡΠΈ ΠΎΠΏΠ΅ΡΠ°ΡΠΈΠΈ Π²ΡΠΏΠ΅Π½ΠΈΠ²Π°Π½ΠΈΡ, ΡΠ°ΠΊΠΆΠ΅ ΠΈΠ³ΡΠ°Π΅Ρ ΡΠΎΠ»Ρ ΠΎΠ±ΡΠ°Π·ΠΎΠ²Π°ΡΠ΅Π»Ρ ΠΏΠΎΡ.
Π‘ΡΡΠ΅ΡΡΠ²Π΅Π½Π½ΡΠΌ ΡΠ»Π΅ΠΌΠ΅Π½ΡΠΎΠΌ ΡΠΈΠΊΠ»Π° ΡΠ²Π»ΡΠ΅ΡΡΡ Π΅Π³ΠΎ Π½Π°ΡΠ°Π»ΡΠ½Π°Ρ ΡΠ°Π·Π° — ΡΡΠΎ ΡΡΡΡΠ°Π½Π΅Π½ΠΈΠ΅ Π²ΠΎΠ·Π΄ΡΡ
Π°, ΠΈΠΌΠ΅ΡΡΠ΅Π³ΠΎΡΡ Π² ΡΠ²ΠΎΠ±ΠΎΠ΄Π½ΠΎΠΌ ΠΏΡΠΎΡΡΡΠ°Π½ΡΡΠ²Π΅ ΠΌΠ΅ΠΆΠ΄Ρ Π³ΡΠ°Π½ΡΠ»Π°ΠΌΠΈ ΠΈ ΡΡΠ΅Π½ΠΊΠ°ΠΌΠΈ ΡΠΎΡΠΌΡ. ΠΡΠΎ ΠΏΡΠΎΠΈΠ·Π²ΠΎΠ΄ΠΈΡΡΡ Π²ΡΠ΄ΡΠ²Π°Π½ΠΈΠ΅ΠΌ Π΅Π³ΠΎ ΡΡΡΡΠ΅ΠΉ Π²ΠΎΠ΄ΡΠ½ΠΎΠ³ΠΎ ΠΏΠ°ΡΠ°.
ΠΠΎ ΠΈ Π΄ΠΎΠΏΠΎΠ»Π½ΠΈΡΠ΅Π»ΡΠ½Π°Ρ ΡΠΎΠ»Ρ Π²ΠΎΠ΄ΡΠ½ΠΎΠ³ΠΎ ΠΏΠ°ΡΠ° Π² ΠΏΡΠΎΡΠ΅ΡΡΠ΅ ΡΠΎΡΠΌΠΈΡΠΎΠ²Π°Π½ΠΈΡ ΡΡΠ΅Π·Π²ΡΡΠ°ΠΉΠ½ΠΎ Π²Π°ΠΆΠ½Π°. ΠΠ°Π»ΠΈΡΠΈΠ΅ Π²ΠΎΠ·Π΄ΡΡ
Π° ΡΠ½ΠΈΠΆΠ°Π΅Ρ ΡΠΊΠΎΡΠΎΡΡΡ Π½Π°Π³ΡΠ΅Π²Π° Π³ΡΠ°Π½ΡΠ» ΠΈ ΠΏΡΠΈΠ²ΠΎΠ΄ΠΈΡ ΠΊ ΡΡ
ΡΠ΄ΡΠ΅Π½ΠΈΡ ΠΊΠ°ΡΠ΅ΡΡΠ²Π° ΠΈΡ
ΡΠ»ΠΈΠΏΠ°Π½ΠΈΡ (ΡΠ°ΠΊ Π½Π°Π·ΡΠ²Π°Π΅ΠΌΠΎΠ΅ ΡΠ°ΡΡΡΠΏΠ°Π½ΠΈΠΈ Π±Π»ΠΎΠΊΠΎΠ²) ΠΈΠ»ΠΈ ΠΏΡΠΈΠ²ΠΎΠ΄ΠΈΡ ΠΊ ΠΎΠ±ΡΠ°Π·ΠΎΠ²Π°Π½ΠΈΡ Π² ΡΠΎΡΠΌΠ΅ ΡΠ²ΠΎΠ±ΠΎΠ΄Π½ΡΡ
ΠΏΡΡΡΠΎΡ, Π½Π΅ Π·Π°ΠΏΠΎΠ»Π½Π΅Π½Π½ΡΡ
Π³ΡΠ°Π½ΡΠ»Π°ΠΌΠΈ, ΡΠ°ΠΊ Π½Π°Π·ΡΠ²Π°Π΅ΠΌΡΡ
ΠΊΠ°Π²Π΅ΡΠ½.
ΠΠΎΠ½Π΅ΡΠ½ΠΎΠΉ ΠΎΠΏΠ΅ΡΠ°ΡΠΈΠ΅ΠΉ ΡΠΈΠΊΠ»Π° ΡΠΎΡΠΌΠΈΡΠΎΠ²Π°Π½ΠΈΡ ΡΠ²Π»ΡΠ΅ΡΡΡ ΠΎΡ
Π»Π°ΠΆΠ΄Π΅Π½ΠΈΠ΅ ΡΡΠΎΡΠΌΠΈΡΠΎΠ²Π°Π½Π½ΡΡ
Π±Π»ΠΎΠΊΠΎΠ². ΠΡ ΡΡΠΎΠΉ, ΠΊΠ°ΠΊ ΠΊΠ°ΠΆΠ΅ΡΡΡ, ΠΏΡΠΎΡΡΠΎΠΉ ΠΎΠΏΠ΅ΡΠ°ΡΠΈΠΈ ΠΎΡΠ΅Π½Ρ ΡΠΈΠ»ΡΠ½ΠΎ Π·Π°Π²ΠΈΡΠΈΡ ΠΊΠ°ΡΠ΅ΡΡΠ²ΠΎ Π±Π»ΠΎΠΊΠΎΠ², Π° ΡΠ°ΠΊΠΆΠ΅ ΡΠ΄Π°ΡΠ½ΠΎΡΡΡ ΡΠΈΠΊΠ»Π°
ΡΠΎΡΠΌΠΎΠ²Π°Π½ΠΈΡ.
Π¦ΠΈΠΊΠ» ΡΠΎΡΠΌΠΎΠ²Π°Π½ΠΈΡ Π±Π»ΠΎΠΊΠ° ΡΠΎΡΡΠΎΠΈΡ ΠΈΠ· ΡΠ»Π΅Π΄ΡΡΡΠΈΡ ΠΎΠΏΠ΅ΡΠ°ΡΠΈΠΉ:
Π. ΠΠ°Π³ΡΠ΅Π²Π°Π½ΠΈΠ΅ ΡΠΎΡΠΌΡ. ΠΠ΅ΡΠ΅Π΄ Π½Π°ΠΏΠΎΠ»Π½Π΅Π½ΠΈΠ΅ΠΌ ΡΠΎΡΠΌΡ Π³ΡΠ°Π½ΡΠ»Π°ΠΌΠΈ Π½Π°Π΄Π»Π΅ΠΆΠΈΡ Π΅Π΅ Π½Π°Π³ΡΠ΅ΡΡ Π΄ΠΎ ΡΠ΅ΠΌΠΏΠ΅ΡΠ°ΡΡΡΡ 80-90Β°Π‘ (ΠΏΡΠΈ Π±ΠΎΠ»Π΅Π΅ Π²ΡΡΠΎΠΊΠΈΡ
ΡΠ΅ΠΌΠΏΠ΅ΡΠ°ΡΡΡΠ°Ρ
Π³ΡΠ°Π½ΡΠ»Ρ Π±ΡΠ΄ΡΡ ΡΠ»ΠΈΠΏΠ°ΡΡΡΡ ΡΠ°ΠΌΠΈ ΠΏΠΎ ΡΠ΅Π±Π΅ ΠΏΠΎ ΠΌΠ΅ΡΠ΅ ΠΈΡ
Π·Π°ΡΡΠΏΠ°Π½ΠΈΡ Π΄ΠΎ ΠΏΠΎΠ΄Π°ΡΠΈ Π²ΠΎΠ΄ΡΠ½ΠΎΠ³ΠΎ ΠΏΠ°ΡΠ°). ΠΠΎ Π²ΡΠ΅ΠΌΡ Π½Π°Π³ΡΠ΅Π²Π°Π½ΠΈΡ ΡΠΎΡΠΌΠ° Π΄ΠΎΠ»ΠΆΠ½Π° Π±ΡΡΡ Π·Π°ΠΊΡΡΡΠ°, Π° ΠΊΠΎΠ½Π΄Π΅Π½ΡΠ°Ρ ΠΈ ΠΈΠ·Π±ΡΡΠΎΠΊ ΠΏΠΎΡΡΡΠΏΠ°ΡΡΠ΅Π³ΠΎ ΠΏΠ°ΡΠ° Π΄ΠΎΠ»ΠΆΠ΅Π½ Π±ΡΡΡ Π½Π°ΠΏΡΠ°Π²Π»Π΅Π½ Π²ΡΠ΄Π΅Π»Π΅Π½Π½ΡΠΌ ΡΡΡΠ±ΠΎΠΏΡΠΎΠ²ΠΎΠ΄ΠΎΠΌ ΠΈΠ· Π·Π΄Π°Π½ΠΈΡ. ΠΠ°Π³ΡΠ΅Π²Π°Π½ΠΈΠ΅ ΡΠΎΡΠΌΡ ΠΈΠΌΠ΅Π΅Ρ ΠΊΠΎΠ½Π΅ΡΠ½ΠΎΠΉ ΡΠ΅Π»ΡΡ ΠΈΠ·Π±Π΅ΠΆΠ°Π½ΠΈΠ΅ ΡΠ²Π»Π°ΠΆΠ½Π΅Π½ΠΈΡ Π³ΡΠ°Π½ΡΠ» ΠΊΠΎΠ½Π΄Π΅Π½ΡΠ°ΡΠΎΠΌ, ΠΎΡΡΠ°ΡΡΠΈΠΌΡΡ Π½Π° Ρ
ΠΎΠ»ΠΎΠ΄Π½ΠΎΠΉ ΠΏΠΎΠ²Π΅ΡΡ
Π½ΠΎΡΡΠΈ ΡΡΠ΅Π½ΠΎΠΊ ΡΠΎΡΠΌΡ. ΠΠΎΡΡΡΠΏΠ°ΡΡΠΈΠΉ Π½Π° ΠΏΠΎΡΠ»Π΅Π΄ΡΡΡΠΈΡ
ΡΡΠ°ΠΏΠ°Ρ
ΡΠΎΡΠΌΠΈΡΠΎΠ²Π°Π½ΠΈΡ ΠΏΠ°Ρ Π΄ΠΎΠ»ΠΆΠ΅Π½ ΡΠΎΠ»ΡΠΊΠΎ Π΄ΠΎΠΏΠΎΠ»Π½ΠΈΡΠ΅Π»ΡΠ½ΠΎ Π½Π°Π³ΡΠ΅Π²Π°ΡΡ ΡΡΠ΅Π½ΠΊΠΈ ΡΠΎΡΠΌΡ.
Π. Π‘ΠΌΠ°Π·ΡΠ²Π°Π½ΠΈΠ΅ ΠΏΠΎΠ²Π΅ΡΡ
Π½ΠΎΡΡΠΈ ΡΠΎΡΠΌΡ. ΠΡΠΎΠΈΠ·Π²ΠΎΠ΄ΠΈΡΡΡ Ρ ΠΏΠΎΠΌΠΎΡΡΡ Π²ΠΏΡΡΡΠΊΠΈΠ²Π°Π½ΠΈΡ Π½Π° Π²Π½ΡΡΡΠ΅Π½Π½ΡΡ ΠΏΠΎΠ²Π΅ΡΡ
Π½ΠΎΡΡΡ ΡΠΎΡΠΌΡ ΡΠ°ΡΡΠ²ΠΎΡΠ° ΠΌΡΠ»Π° ΠΈΠ»ΠΈ Π΄ΡΡΠ³ΠΎΠ³ΠΎ ΡΡΠ΅Π΄ΡΡΠ²Π° Ρ ΡΠ΅Π»ΡΡ ΠΎΠ±Π΅ΡΠΏΠ΅ΡΠ΅Π½ΠΈΡ ΡΠ²ΠΎΠ±ΠΎΠ΄Π½ΠΎΠ³ΠΎ ΠΎΡΠ»ΠΈΠΏΠ°Π½ΠΈΡ ΡΡΠΎΡΠΌΠΈΡΠΎΠ²Π°Π½Π½ΠΎΠ³ΠΎ Π±Π»ΠΎΠΊΠ° ΠΎΡ ΡΠΎΡΠΌΡ. ΠΠΏΠ΅ΡΠ°ΡΠΈΠΈ ΠΌΠΎΠΆΠ½ΠΎ ΠΈΠ·Π±Π΅ΠΆΠ°ΡΡ, Π΅ΡΠ»ΠΈ Π³Π»Π°Π΄ΠΊΠΈΠ΅ Π²Π½ΡΡΡΠ΅Π½Π½ΠΈΠ΅ ΡΡΠ΅Π½ΠΊΠΈ ΡΠΎΡΠΌ ΠΏΠΎΠ·Π²ΠΎΠ»ΡΡΡ Π»ΡΠ³ΠΊΡΡ Π²ΡΠ΅ΠΌΠΊΡ ΡΡΠΎΡΠΌΠΈΡΠΎΠ²Π°Π½Π½ΠΎΠ³ΠΎ Π±Π»ΠΎΠΊΠ°.
Π. ΠΠ°ΠΏΠΎΠ»Π½Π΅Π½ΠΈΠ΅ ΡΠΎΡΠΌΡ. ΠΠΎΠ΄Π³ΠΎΡΠΎΠ²Π»Π΅Π½Π½Π°Ρ Π² ΡΠΎΠΎΡΠ²Π΅ΡΡΡΠ²ΠΈΠΈ Ρ ΠΏΡΠ½ΠΊΡΠ°ΠΌΠΈ Π ΠΈ Π ΡΠΎΡΠΌΠ° Π·Π°ΠΏΠΎΠ»Π½ΡΠ΅ΡΡΡ Π³ΡΠ°Π½ΡΠ»Π°ΠΌΠΈ ΡΠ΅ΡΠ΅Π· ΡΠ±ΠΎΡΠ½ΠΈΠΊ ΠΏΠΎΠ΄ Π΄Π°Π²Π»Π΅Π½ΠΈΠ΅ΠΌ. ΠΠ°ΠΏΠΎΠ»Π½Π΅Π½ΠΈΠ΅ ΡΠΎΡΠΌΡ Π΄ΠΎΠ»ΠΆΠ½ΠΎ Π±ΡΡΡ ΠΏΠΎΠ»Π½ΡΠΌ Π΄Π»Ρ ΠΎΠ±Π΅ΡΠΏΠ΅ΡΠ΅Π½ΠΈΡ ΡΠΎΠΎΡΠ²Π΅ΡΡΡΠ²ΡΡΡΠ΅Π³ΠΎ ΠΊΠ°ΡΠ΅ΡΡΠ²Π° ΠΈΠ·Π΄Π΅Π»ΠΈΡ.
Π. ΠΡΠΎΠ΄ΡΠ²Π°Π½ΠΈΠ΅ ΡΠΎΡΠΌΡ Π²ΠΎΠ΄ΡΠ½ΡΠΌ ΠΏΠ°ΡΠΎΠΌ. ΠΠΎΡΠ»Π΅ Π·Π°ΠΏΠΎΠ»Π½Π΅Π½ΠΈΡ ΡΠΎΡΠΌΡ ΠΈ Π΅Π΅ Π·Π°ΠΊΡΡΠ²Π°Π½ΠΈΡ Ρ ΠΏΠΎΠΌΠΎΡΡΡ ΠΏΠ½Π΅Π²ΠΌΠ°ΡΠΈΡΠ΅ΡΠΊΠΎΠ³ΠΎ ΠΏΡΠΈΠ²ΠΎΠ΄Π° ΠΈ Π³Π΅ΡΠΌΠ΅ΡΠΈΡΠ½ΡΠΌ Π·Π°ΠΌΡΠΊΠ°Π½ΠΈΠ΅ΠΌ β ΠΊΠΎΠ½ΡΡΠΎΠ»ΡΠ½Π°Ρ Π»Π°ΠΌΠΏΠΎΡΠΊΠ° Π½Π° ΠΏΡΠ»ΡΡΠ΅ ΡΠΏΡΠ°Π²Π»Π΅Π½ΠΈΡ, Π²ΠΎΠ΄ΡΠ½ΠΎΠΉ ΠΏΠ°Ρ ΠΏΠΎΠ΄Π°Π΅ΡΡΡ Π² Π²Π΅ΡΡ
Π½ΠΈΠ΅ ΠΈ Π±ΠΎΠΊΠΎΠ²ΡΠ΅ ΡΠ°ΡΡΠΈ ΡΡΠ΅Π½ΠΎΠΊ ΡΠΎΡΠΌΡ ΠΈ Π²ΡΠ²ΠΎΠ΄ΠΈΡΡΡ (Π²Π½Π°ΡΠ°Π»Π΅ ΠΊΠ°ΠΊ ΡΠΌΠ΅ΡΡ Π²ΠΎΠ·Π΄ΡΡ
Π° ΠΈ Π²ΠΎΠ΄ΡΠ½ΠΎΠ³ΠΎ ΠΏΠ°ΡΠ°) ΡΠ΅ΡΠ΅Π· ΠΊΠ°ΠΌΠ΅ΡΡ Π² Π½ΠΈΠΆΠ½Π΅ΠΉ ΡΠ°ΡΡΠΈ ΡΠΎΡΠΌΡ Π² ΠΊΠΎΠ»Π»Π΅ΠΊΡΠΎΡ ΠΊΠΎΠ½Π΄Π΅Π½ΡΠ°ΡΠ° ΠΈ Π²ΠΎΠ΄ΡΠ½ΠΎΠ³ΠΎ ΠΏΠ°ΡΠ° ΠΏΡΠΈ ΠΎΡΠΊΡΡΡΠΎ Π½Π°Ρ
ΠΎΠ΄ΡΡΠ΅ΠΌΡΡ ΡΠ°ΠΌ Π²Π΅Π½ΡΠΈΠ»Π΅. ΠΠ°Π²Π»Π΅Π½ΠΈΠ΅ ΠΏΠ°ΡΠ° Π² ΠΊΠ°ΠΌΠ΅ΡΠ°Ρ
Π²ΠΎ Π²ΡΠ΅ΠΌΡ ΠΎΠΏΠ΅ΡΠ°ΡΠΈΠΈ Π΄ΠΎΠ»ΠΆΠ½ΠΎ ΡΠΎΡΡΠ°Π²Π»ΡΡΡ 0,03-0,05 ΠΌΠΠ°, Π²ΡΠ΅ΠΌΡ ΠΏΡΠΎΠ΄ΡΠ²ΠΊΠΈ 10-20 ΡΠ΅ΠΊ.
ΠΡΠΈΠΌΠ΅Π½Π΅Π½ΠΈΠ΅ Π±ΠΎΠ»Π΅Π΅ Π΄Π»ΠΈΡΠ΅Π»ΡΠ½ΠΎΠ³ΠΎ ΡΡΠΎΠΊΠ° ΠΏΡΠΎΠ΄ΡΠ²ΠΊΠΈ Π½Π΅ΠΆΠ΅Π»Π°ΡΠ΅Π»ΡΠ½ΠΎ, ΡΠ°ΠΊ ΠΊΠ°ΠΊ ΠΏΡΠΈΠ²ΠΎΠ΄ΠΈΡ ΠΊ ΡΡ
ΡΠ΄ΡΠ΅Π½ΠΈΡ ΡΠ»ΠΈΠΏΠ°Π½ΠΈΡ Π³ΡΠ°Π½ΡΠ» ΠΌΠ΅ΠΆΠ΄Ρ ΡΠΎΠ±ΠΎΠΉ Π²ΠΎ Π²Π½Π΅ΡΠ½Π΅ΠΉ ΠΈ Π½ΠΈΠΆΠ½Π΅ΠΉ ΡΠ°ΡΡΡΡ
ΡΠΎΡΠΌΡ, Π° Π½Π°ΠΎΠ±ΠΎΡΠΎΡ, ΡΠΎΠΊΡΠ°ΡΠ΅Π½ΠΈΠ΅ Π²ΡΠ΅ΠΌΠ΅Π½ΠΈ ΠΏΡΠΎΠ΄ΡΠ²ΠΊΠΈ ΠΏΡΠΈΠ²ΠΎΠ΄ΠΈΡ ΠΊ ΠΎΡΡΠ°ΡΠΊΡ Π²ΠΎΠ·Π΄ΡΡ
Π° Π² ΡΠΎΡΠΌΠ΅ ΠΈ ΠΎΠ±ΡΠ°Π·ΠΎΠ²Π°Π½ΠΈΡ ΠΏΡΡΡΠΎΡ.
Π. Π‘ΠΎΠ±ΡΡΠ²Π΅Π½Π½ΠΎ ΡΠΎΡΠΌΠΈΡΠΎΠ²Π°Π½ΠΈΠ΅. ΠΠΎΡΠ»Π΅ ΠΏΡΠΎΠ²Π΅Π΄Π΅Π½ΠΈΡ ΠΏΡΠΎΠ΄ΡΠ²ΠΊΠΈ, Π·Π°ΠΊΡΡΠ²Π°Π΅ΡΡΡ Π²Π΅Π½ΡΠΈΠ»Ρ ΠΎΡΠ²ΠΎΠ΄Π° ΠΏΠ°ΡΠ° ΠΈ
ΠΊΠΎΠ½Π΄Π΅Π½ΡΠ°ΡΠ°, Π° ΡΠ°ΠΊΠΆΠ΅ ΠΏΡΠΎΠ²ΠΎΠ΄ΡΡΡΡ Π΄Π°Π»ΡΠ½Π΅ΠΉΡΠΈΠ΅ ΠΎΠΏΠ΅ΡΠ°ΡΠΈΠΈ ΠΏΠΎ ΡΠΎΡΠΌΠΎΠ²Π°Π½ΠΈΡ. Π ΡΡΠΎ Π²ΡΠ΅ΠΌΡ Π²ΠΎΠ·ΡΠ°ΡΡΠ°Π΅Ρ Π΄Π°Π²Π»Π΅Π½ΠΈΠ΅ ΠΏΠ°ΡΠ° Π² ΡΠΎΡΠΌΠ΅ Π΄ΠΎ 0,04-0,06 ΠΌΠΠ°, Π² ΡΠΎΠΌ ΡΠΈΡΠ»Π΅ ΠΈ Π² ΡΠ²ΠΎΠ±ΠΎΠ΄Π½ΠΎΠΌ ΠΏΡΠΎΡΡΡΠ°Π½ΡΡΠ²Π΅ ΠΌΠ΅ΠΆΠ΄Ρ Π³ΡΠ°Π½ΡΠ»Π°ΠΌΠΈ. ΠΠΎΠ·ΡΠ°ΡΡΠ°Π½ΠΈΠ΅ Π΄Π°Π²Π»Π΅Π½ΠΈΡ Π΄ΠΎΠ»ΠΆΠ½ΠΎ Π΄ΠΎΡΡΠΈΠ³Π½ΡΡΡ ΠΌΠ°ΠΊΡΠΈΠΌΠ°Π»ΡΠ½ΠΎΠ³ΠΎ Π·Π½Π°ΡΠ΅Π½ΠΈΡ ΠΈ ΠΊΠΎΠ½ΡΡΠΎΠ»ΠΈΡΠΎΠ²Π°ΡΡΡΡ Ρ ΠΏΠΎΠΌΠΎΡΡΡ ΠΌΠ°Π½ΠΎΠΌΠ΅ΡΡΠΎΠ².
ΠΠΎ Π²ΡΠ΅ΠΌΡ ΡΠΎΡΠΌΠΎΠ²Π°Π½ΠΈΡ Π³ΡΠ°Π½ΡΠ»Ρ ΡΠ°Π·ΠΎΠ³ΡΠ΅Π²Π°ΡΡΡΡ, Π΄ΠΎΠΏΠΎΠ»Π½ΠΈΡΠ΅Π»ΡΠ½ΠΎ Π²ΡΠΏΠ΅Π½ΠΈΠ²Π°ΡΡΡΡ ΠΈ Π²ΡΠΏΠ΅Π½Π΅Π½Π½ΡΠ΅ ΠΏΠΎΠ»Π½ΠΎΡΡΡΡ Π·Π°Π½ΠΈΠΌΠ°ΡΡ ΠΎΠ±ΡΠ΅ΠΌ ΡΠΎΡΠΌΡ. ΠΠ°Ρ
ΠΎΠ΄ΡΡΠΈΠΉΡΡ ΡΠ°ΠΌ ΠΏΠ°Ρ ΠΏΡΠΎΠ½ΠΈΠΊΠ°Π΅Ρ ΡΠ΅ΡΠ΅Π· ΡΡΠ΅Π½ΠΊΠΈ Π³ΡΠ°Π½ΡΠ» ΠΈ ΠΏΡΠΈΠ²ΠΎΠ΄ΠΈΡ ΠΊ ΡΠ»ΠΈΠΏΠ°Π½ΠΈΡ Π³ΡΠ°Π½ΡΠ» ΠΌΠ΅ΠΆΠ΄Ρ ΡΠΎΠ±ΠΎΠΉ. ΠΡΠ΅ΠΌΡ ΡΠΎΡΠΌΠΎΠ²Π°Π½ΠΈΡ Π±Π»ΠΎΠΊΠΎΠ² ΡΠΎΡΡΠ°Π²Π»ΡΠ΅Ρ 8-12 ΡΠ΅ΠΊΡΠ½Π΄.
Π. ΠΡΠ΅ΠΌΠΊΠ° ΡΡΠΎΡΠΌΠΎΠ²Π°Π½Π½ΡΡ Π±Π»ΠΎΠΊΠΎΠ². Π‘ΡΠΎΡΠΌΠΈΡΠΎΠ²Π°Π½Π½ΡΠ΅ Π±Π»ΠΎΠΊΠΈ Π²ΡΡΠ°Π»ΠΊΠΈΠ²Π°ΡΡΡΡ ΠΈΠ· ΡΠΎΡΠΌΡ ΠΏΡΠΈ ΠΏΠΎΠΌΠΎΡΠΈΒ ΡΡΡΠ°Π½ΠΎΠ²Π»Π΅Π½Π½ΠΎΠ³ΠΎ Π²ΡΡΠ°Π»ΠΊΠΈΠ²Π°ΡΠ΅Π»Ρ. ΠΠ»Ρ ΠΈΡΠΏΡΠ°Π²Π½ΠΎΠ³ΠΎ Π²ΡΠΏΠΎΠ»Π½Π΅Π½ΠΈΡ ΡΡΠΎΠΉ ΠΎΠΏΠ΅ΡΠ°ΡΠΈΠΈ Π½Π΅ΠΎΠ±Ρ ΠΎΠ΄ΠΈΠΌΠΎ ΡΡΡΡΠ°Π½Π΅Π½ΠΈΠ΅ ΠΏΡΠΈΡΠΈΠ½ ΠΏΡΠΈΠ»ΠΈΠΏΠ°Π½ΠΈΡ Π³ΡΠ°Π½ΡΠ» ΠΊ ΡΡΠ΅Π½ΠΊΠ°ΠΌ ΡΠΎΡΠΌΡ, ΠΊΠΎΡΠΎΡΠΎΠ΅ Π΄ΠΎΡΡΠΈΠ³Π°Π΅ΡΡΡ ΠΏΡΡΠ΅ΠΌ Π½Π°Π½Π΅ΡΠ΅Π½ΠΈΡ ΡΡΠ΅Π΄ΡΡΠ² ΠΏΡΠΎΡΠΈΠ² ΠΏΡΠΈΠ»ΠΈΠΏΠ°Π½ΠΈΡ ΠΏΠ΅ΡΠ΅Π΄ Π·Π°Π³ΡΡΠ·ΠΊΠΎΠΉ ΡΠΎΡΠΌ. ΠΠΎ ΠΌΠ΅ΡΠ΅ ΡΠΊΡΠΏΠ»ΡΠ°ΡΠ°ΡΠΈΠΈ Π½Π°ΡΡΡΠΏΠ°Π΅Ρ ΠΏΠ°ΡΡΠΈΠ²Π½ΠΎΡΡΡ ΠΏΠΎ ΠΎΡΠ½ΠΎΡΠ΅Π½ΠΈΡ ΠΊ ΠΏΡΠΈΠ»ΠΈΠΏΠ°Π½ΠΈΡ ΡΡΠ΅Π½ΠΎΠΊ ΡΠΎΡΠΌ ΠΈ Π² Π΄Π°Π»ΡΠ½Π΅ΠΉΡΠ΅ΠΌ ΠΌΠΎΠΆΠ½ΠΎ ΠΈΠ·Π±Π΅Π³Π°ΡΡ ΡΠΌΠ°Π·ΠΊΠΈ.
ΠΠΎΠ½ΡΡΠΎΠ»ΡΠ½ΠΎ-ΠΈΠ·ΠΌΠ΅ΡΠΈΡΠ΅Π»ΡΠ½Π°Ρ Π°ΠΏΠΏΠ°ΡΠ°ΡΡΡΠ° ΡΠΎΡΠΌ ΡΠ°Π·ΠΌΠ΅ΡΠ΅Π½Π° Π½Π° ΠΏΡΠ»ΡΡΠ΅ ΡΠΏΡΠ°Π²Π»Π΅Π½ΠΈΡ. ΠΡΠΎΠΌΠ΅ ΡΠΎΠ³ΠΎ, Π½Π° Π»ΠΈΠ½ΠΈΠΈ ΠΏΠΎΠ΄Π°ΡΠΈ ΠΏΠ°ΡΠ° ΠΈΠΌΠ΅Π΅ΡΡΡ ΡΠ΅Π³ΡΠ»ΠΈΡΡΡΡΠΈΠΉ Π²Π΅Π½ΡΠΈΠ»Ρ ΠΈ ΠΌΠ°Π½ΠΎΠΌΠ΅ΡΡ, Π° ΡΠ°ΠΊΠΆΠ΅ Π²Π΅Π½ΡΠΈΠ»Ρ Π½Π° ΠΊΠΎΠ»Π»Π΅ΠΊΡΠΎΡΠ΅ ΠΊΠΎΠ½Π΄Π΅Π½ΡΠ°ΡΠΎΡΠ° ΠΈ ΠΎΡΠ²ΠΎΠ΄Π° ΠΈΠ· ΡΠΎΡΠΌΡ. ΠΠΎ Π²ΡΠ΅ΠΌΡ ΠΏΡΠΈΠΎΡΡΠ°Π½ΠΎΠ²ΠΊΠΈ ΡΠ°Π±ΠΎΡΡ ΡΠ»Π΅Π΄ΡΠ΅Ρ ΠΏΡΠ΅ΠΊΡΠ°ΡΠΈΡΡ ΠΏΠΎΠ΄Π°ΡΡ ΠΏΠ°ΡΠ°, Π° ΡΠ°ΠΊΠΆΠ΅ ΡΠΆΠ°ΡΠΎΠ³ΠΎ Π²ΠΎΠ·Π΄ΡΡ Π° ΠΈ ΡΠ»Π΅ΠΊΡΡΠΎΡΠ½Π΅ΡΠ³ΠΈΠΈ. ΠΡΠ΅ΠΌΡ ΠΏΡΠ΅Π±ΡΠ²Π°Π½ΠΈΡ ΡΡΠΎΡΠΌΠΎΠ²Π°Π½Π½ΠΎΠ³ΠΎ Π±Π»ΠΎΠΊΠ° Π² ΡΠΎΡΠΌΠ΅ Π·Π°Π²ΠΈΡΠΈΡ ΠΎΡ ΡΡΡΡΡ ΠΈ ΡΠΎΡΡΠ°Π²Π»ΡΠ΅Ρ 10-30 ΠΌΠΈΠ½ΡΡ.
Β Β Β Β 7.1.4. ΠΡΠ΄Π΅ΡΠΆΠΊΠ° Π±Π»ΠΎΠΊΠΎΠ² ΠΏΠΎ Π²ΡΠ΅ΠΌΠ΅Π½ΠΈ
ΠΠΎΠ½Π΅ΡΠ½ΠΎ, ΡΠ΅Ρ Π½ΠΎΠ»ΠΎΠ³ΠΈΡΠ΅ΡΠΊΠΎΠΉ ΠΎΠΏΠ΅ΡΠ°ΡΠΈΠ΅ΠΉ ΡΠ²Π»ΡΠ΅ΡΡΡ Π²ΡΠ΄Π΅ΡΠΆΠΊΠ° ΡΡΠΎΡΠΌΠΎΠ²Π°Π½Π½ΡΡ Π±Π»ΠΎΠΊΠΎΠ² ΠΏΠΎ Π²ΡΠ΅ΠΌΠ΅Π½ΠΈ, ΠΊΠΎΠ³Π΄Π° Π½Π°ΡΡΡΠΏΠ°Π΅Ρ ΠΏΡΠΎΠ½ΠΈΠΊΠ½ΠΎΠ²Π΅Π½ΠΈΠ΅ Π²ΠΎΠ·Π΄ΡΡ Π° Π² Π±Π»ΠΎΠΊΠΈ, Π° ΡΠ°ΠΊΠΆΠ΅ Π΅Π³ΠΎ ΡΡΡΠ΅Π½ΠΈΠ΅. ΠΡΠ΄Π΅ΡΠΆΠΊΡ ΠΈ ΡΡΡΠ΅Π½ΠΈΠ΅ Π±Π»ΠΎΠΊΠΎΠ² ΡΠ»Π΅Π΄ΡΠ΅Ρ ΠΏΡΠΎΠΈΠ·Π²ΠΎΠ΄ΠΈΡΡ ΠΏΡΠΈ ΡΠ΅ΠΌΠΏΠ΅ΡΠ°ΡΡΡΠ΅ 22-30Β°Π‘ Π² ΡΠ΅ΡΠ΅Π½ΠΈΠ΅ 8 ΡΠ°ΡΠΎΠ².
Β Β Β Β 7.1.5. Π Π°Π·ΡΠ΅Π·Π°Π½ΠΈΠ΅ Π±Π»ΠΎΠΊΠΎΠ² Π½Π° ΠΏΠ»ΠΈΡΡ
ΠΠΎΡΠ»Π΅Π΄Π½ΠΈΠΌ Π΄Π΅ΠΉΡΡΠ²ΠΈΠ΅ΠΌ, ΠΊΠΎΡΠΎΡΠΎΠ΅ ΠΏΡΠΎΠΈΠ·Π²ΠΎΠ΄ΠΈΡΡΡ Π½Π°Π΄ Π±Π»ΠΎΠΊΠ°ΠΌΠΈ, ΡΠ²Π»ΡΠ΅ΡΡΡ ΠΏΡΠΎΡΠ΅ΡΡ ΠΈΡ ΠΏΡΠ΅ΠΎΠ±ΡΠ°Π·ΠΎΠ²Π°Π½ΠΈΡ Π² ΠΏΠ»ΠΈΡΡ. ΠΠ½ Π·Π°ΠΊΠ»ΡΡΠ°Π΅ΡΡΡ Π² ΡΠ°Π·ΡΠ΅Π·Π°Π½ΠΈΠΈ Π±Π»ΠΎΠΊΠΎΠ² ΠΏΡΠΈ ΠΏΠΎΠΌΠΎΡΠΈ ΡΠ°Π·Π΄Π΅Π»ΠΈΡΠ΅Π»ΡΠ½ΠΎΠ³ΠΎ ΠΏΡΠΎΠ²ΠΎΠ΄Π°. Π Π°Π·ΡΠ΅Π·Π°Π½ΠΈΡ ΡΠ»Π΅Π΄ΡΠ΅Ρ ΠΏΠΎΠ΄Π²Π΅ΡΠ³Π°ΡΡ Π±Π»ΠΎΠΊΠΈ, Π²ΡΠ΄Π΅ΡΠΆΠ°Π½Π½ΡΠ΅ ΠΏΠΎ Π²ΡΠ΅ΠΌΠ΅Π½ΠΈ ΠΈ Π²ΡΡΡΡΠ΅Π½Π½ΡΠ΅. Π Π°Π·ΡΠ΅Π·Π°Π½ΠΈΠ΅ Π±Π»ΠΎΠΊΠΎΠ² ΡΠ°Π·ΠΎΠ³ΡΠ΅ΡΡΠΌ ΠΏΡΠΎΠ²ΠΎΠ΄ΠΎΠΌ Π²ΠΎΠ·ΠΌΠΎΠΆΠ½ΠΎ Π±Π»Π°Π³ΠΎΠ΄Π°ΡΡ ΡΠΎΠΌΡ, ΡΡΠΎ ΡΠ΅ΠΌΠΏΠ΅ΡΠ°ΡΡΡΠ° ΡΠ°Π·ΠΎΠ³ΡΠ΅Π²Π° ΠΏΡΠΎΠ²ΠΎΠ΄Π° Π²ΡΡΠ΅ ΡΠ΅ΠΌΠΏΠ΅ΡΠ°ΡΡΡΡ ΠΏΠ»Π°Π²Π»Π΅Π½ΠΈΡ ΠΏΠ΅Π½ΠΎΠΏΠ»Π°ΡΡΠ° ΠΈ ΠΎΡΡΠ°Π²Π»ΡΠ΅Ρ Π·Π° ΡΠΎΠ±ΠΎΠΉ Π»ΠΈΡΡΡ ΠΏΠΎΠ²Π΅ΡΡ Π½ΠΎΡΡΡ, Π±Π»Π°Π³ΠΎΠ΄Π°ΡΡ ΡΠ΅ΠΌΡ ΡΡΠΈΠ»ΠΈΠ²Π°Π΅ΡΡΡ Π·Π½Π°ΡΠ΅Π½ΠΈΠ΅ ΡΠΏΡΡΠ³ΠΎΡΡΠΈ ΠΌΠ°ΡΠ΅ΡΠΈΠ°Π»Π°. Π Π°Π·ΡΠ΅Π·Π°Π½ΠΈΠ΅ Π±Π»ΠΎΠΊΠΎΠ² Π½Π° ΠΏΠ»ΠΈΡΡ ΠΏΡΠΎΠΈΠ·Π²ΠΎΠ΄ΠΈΡΡΡ Π½Π° ΠΎΡΠ½Π°ΡΠ΅Π½ΠΈΠΈ, ΡΠΎΡΡΠΎΡΡΠ΅ΠΌ ΠΈΠ· ΠΏΠΎΠ΄Π²ΠΈΠΆΠ½ΠΎΠ³ΠΎ ΡΡΠΎΠ»Π° ΠΈ ΡΡΠ°Π»ΡΠ½ΠΎΠΉ ΡΠ°ΠΌΡ Ρ Π½Π°ΡΡΠ½ΡΡΡΠΌΠΈ ΠΏΡΠΎΠ²ΠΎΠ΄Π°ΠΌΠΈ. ΠΠ»Π°Π³ΠΎΠ΄Π°ΡΡ Π»Π΅Π³ΠΊΠΎΠΉ ΡΠΈΡΡΠ΅ΠΌΠ΅ ΡΠ΅Π³ΡΠ»ΠΈΡΠΎΠ²ΠΊΠΈ ΡΠ°ΡΡΡΠΎΡΠ½ΠΈΡ ΠΌΠ΅ΠΆΠ΄Ρ ΠΏΡΠΎΠ²ΠΎΠ΄Π°ΠΌΠΈ ΠΌΠΎΠΆΠ½ΠΎ ΡΠ΅Π³ΡΠ»ΠΈΡΠΎΠ²Π°ΡΡ ΡΠΎΠ»ΡΠΈΠ½Ρ ΡΠ°Π·ΡΠ΅Π·Π°Π½Π½ΡΡ ΠΏΠ»ΠΈΡ Π² ΡΠΎΠΎΡΠ²Π΅ΡΡΡΠ²ΠΈΠΈ Ρ ΡΡΠ΅Π±ΠΎΠ²Π°Π½ΠΈΡΠΌΠΈ Π·Π°ΠΊΠ°Π·ΡΠΈΠΊΠ°. Π Π°Π·ΡΠ΅Π·Π°Π½Π½ΡΠ΅ ΠΏΠ»ΠΈΡΡ ΠΈΠ· ΠΏΠ΅Π½ΠΎΠΏΠ»Π°ΡΡΠ° ΠΈΠ·ΠΌΠ΅ΡΡΡΡ Π² ΡΠΎΠΎΡΠ²Π΅ΡΡΡΠ²ΠΈΠΈ Ρ ΡΡΠ΅Π±ΠΎΠ²Π°Π½ΠΈΡΠΌΠΈ, ΠΏΡΠΈΠ½ΡΡΡΠΌΠΈ Π½Π° ΠΏΡΠΎΠΈΠ·Π²ΠΎΠ΄ΡΡΠ²Π΅, ΡΠΏΠ°ΠΊΠΎΠ²ΡΠ²Π°ΡΡΡΡ ΠΈΠ»ΠΈ Π΄ΠΎΡΡΠ°Π²Π»ΡΡΡΡΡ Π½Π°Π²Π°Π»ΠΎΠΌ ΡΠ΅ΡΠ΅Π· ΡΠΊΠ»Π°Π΄ Π·Π°ΠΊΠ°Π·ΡΠΈΠΊΡ.
8. Π‘ΡΠΎΠΊΠΈ ΠΈ ΠΎΡΡ ΠΎΠ΄Ρ
Β 8.1. Π’Π΅Ρ Π½ΠΎΠ»ΠΎΠ³ΠΈΡΠ΅ΡΠΊΠΈΠ΅ ΡΡΠΎΠΊΠΈ
Π‘ΡΠΎΠΊΠΈ ΠΏΡΠ΅Π΄Π½Π°Π·Π½Π°ΡΠ΅Π½Ρ Π΄Π»Ρ ΡΡΠΎΠΊΠ° ΠΏΠ°ΡΠ°, Π²ΠΎΠ΄Ρ ΠΈ ΠΊΠΎΠ½Π΄Π΅Π½ΡΠ°ΡΠ° ΠΈΠ· Π²ΡΠΏΠ΅Π½ΠΈΠ²Π°ΡΠ΅Π»Π΅ΠΉ, ΡΠΎΡΠΌ ΠΈ Ρ ΠΌΠ΅ΡΡΠ°
ΡΠ°ΡΠΏΠΎΠ»ΠΎΠΆΠ΅Π½ΠΈΡ ΠΏΡΠΎΠΈΠ·Π²ΠΎΠ΄ΡΡΠ²Π΅Π½Π½ΡΡ
ΠΌΠΎΡΠ½ΠΎΡΡΠ΅ΠΉ. ΠΠ΄ΠΈΠ½ΡΡΠ²Π΅Π½Π½Π°Ρ Π·Π°ΡΠΈΡΠ° ΡΡΠΎΠΊΠ° β ΡΡΠΎ Π·Π°ΡΠΈΡΠ° ΠΎΡ ΠΌΠ΅Ρ
Π°Π½ΠΈΡΠ΅ΡΠΊΠΎΠ³ΠΎ Π·Π°Π½Π΅ΡΠ΅Π½ΠΈΡ Π³ΡΠ°Π½ΡΠ».
Β 8.2. ΠΡΡ ΠΎΠ΄Ρ
ΠΡΡ ΠΎΠ΄Ρ, ΠΎΠ±ΡΠ°Π·ΡΡΡΠΈΠ΅ΡΡ Π² ΠΏΡΠΎΡΠ΅ΡΡΠ΅ ΠΏΡΠΎΠΈΠ·Π²ΠΎΠ΄ΡΡΠ²Π° Π±Π»ΠΎΠΊΠΎΠ², Π° ΡΠ°ΠΊΠΆΠ΅ ΠΌΠ΅Ρ Π°Π½ΠΈΡΠ΅ΡΠΊΠΎΠ³ΠΎ ΡΠ°Π·ΡΠ΅Π·Π°Π½ΠΈΡ Π±Π»ΠΎΠΊΠΎΠ² Π½Π° ΠΏΠ»ΠΈΡΡ Π²ΠΌΠ΅ΡΡΠ΅ Ρ Π³ΡΠ°Π½ΡΠ»Π°ΠΌΠΈ, ΡΠ°ΡΡΡΠΏΠ°Π½Π½ΡΠΌΠΈ Π²ΠΎ Π²ΡΠ΅ΠΌΡ ΡΡΠ°Π½ΡΠΏΠΎΡΡΠΈΡΠΎΠ²ΠΊΠΈ ΠΏΠ½Π΅Π²ΠΌΠΎΡΡΠ°Π½ΡΠΏΠΎΡΡΠΎΠΌ, Π²ΠΎΠ·Π²ΡΠ°ΡΠ°ΡΡΡΡ Π² ΠΏΡΠΎΡΠ΅ΡΡ ΠΏΡΠΎΠΈΠ·Π²ΠΎΠ΄ΡΡΠ²Π°. ΠΠΎΠ»ΠΈΡΠ΅ΡΡΠ²ΠΎ ΠΎΡΡ ΠΎΠ΄ΠΎΠ², ΠΎΠ±ΡΠ°Π·ΡΡΡΠΈΡ ΡΡ Π½Π° ΡΠ°Π·Π»ΠΈΡΠ½ΡΡ ΡΡΠ°ΠΏΠ°Ρ ΠΏΡΠΎΠΈΠ·Π²ΠΎΠ΄ΡΡΠ²Π° Π½Π΅ Π΄ΠΎΠ»ΠΆΠ½ΠΎ ΠΏΡΠ΅Π²ΡΡΠ°ΡΡ 6,5% ΠΈ ΡΡΠΎ Π·Π½Π°ΡΠ΅Π½ΠΈΠ΅ ΡΠΎΡΡΠ°Π²Π»ΡΠ΅Ρ ΡΠ°Π·Π½ΠΈΡΡ ΠΌΠ΅ΠΆΠ΄Ρ Π½Π΅ΡΡΠΎ ΠΏΡΠΎΠΈΠ·Π²Π΅Π΄Π΅Π½Π½ΡΠΌ ΠΈ Π±ΡΡΡΡΠΎ ΠΏΡΠΈΠΌΠ΅Π½Π΅Π½Π½ΡΠΌ. Β 8.3. ΠΡΠΏΠ°ΡΡΠ΅ΠΌΡΠ΅ Π³Π°Π·Ρ
ΠΠ±ΡΠ°Π·ΡΡΡΠΈΠ΅ΡΡ Π² ΠΏΡΠΎΡΠ΅ΡΡΠ΅ ΠΏΡΠΎΠΈΠ·Π²ΠΎΠ΄ΡΡΠ²Π° Π³Π°Π·Ρ ΡΠΎΡΡΠ°Π²Π»ΡΡΡ ΠΏΠ°Ρ ΠΈ ΠΏΠ΅Π½ΡΠ°Π½. ΠΠ°ΠΈΠ±ΠΎΠ»ΡΡΠ΅Π΅ ΠΊΠΎΠ»ΠΈΡΠ΅ΡΡΠ²ΠΎ ΠΏΠ΅Π½ΡΠ°Π½Π° Π½Π°Ρ
ΠΎΠ΄ΠΈΡΡΡ Π² ΠΎΡΠ²ΠΎΠ΄Π°Ρ
ΠΈΠ· Π²ΠΏΠ΅Π½ΠΈΠ²Π°ΡΠ΅Π»Π΅ΠΉ. ΠΡΡ
Π»ΠΎΠΏ ΡΠ±ΠΈΡΠ°Π΅ΡΡΡ Π²ΡΡΡΠΆΠ½ΠΎΠΉ Π²Π΅Π½ΡΠΈΠ»ΡΡΠΈΠ΅ΠΉ Π² Π°ΡΠΌΠΎΡΡΠ΅ΡΡ, Π³Π΄Π΅ ΠΎΠ½ ΡΡΠ°Π½ΠΎΠ²ΠΈΡΡΡ Π±Π΅Π·ΠΎΠΏΠ°ΡΠ½ΡΠΌ. ΠΠ° ΡΠ°Π±ΠΎΡΠΈΡ
ΠΌΠ΅ΡΡΠ°Ρ
, Π³Π΄Π΅ ΡΡΡΠ°Π½ΠΎΠ²Π»Π΅Π½Ρ Π²ΡΠΏΠ΅Π½ΠΈΠ²Π°ΡΠ΅Π»ΠΈ ΠΈ ΠΈΠΌΠ΅Π΅ΡΡΡ ΠΌΠ°ΠΊΡΠΈΠΌΠ°Π»ΡΠ½Π°Ρ ΠΊΠΎΠ½ΡΠ΅Π½ΡΡΠ°ΡΠΈΡ Π²ΡΡ
Π»ΠΎΠΏΠ°, ΡΡΡΠ°Π½ΠΎΠ²Π»Π΅Π½Π½ΠΎΠ΅ ΠΎΠ±ΠΎΡΡΠ΄ΠΎΠ²Π°Π½ΠΈΠ΅ Π΄ΠΎΠ»ΠΆΠ½ΠΎ ΠΎΠ±Π΅ΡΠΏΠ΅ΡΠΈΠ²Π°ΡΡ Π΄ΠΎΡΡΠ°ΡΠΎΡΠ½ΡΠΉ ΠΎΡΠ²ΠΎΠ΄ Π³Π°Π·ΠΎΠ².
ΠΡΡΡΠΆΠ½ΠΎΠ΅ Π²Π΅Π½ΡΠΈΠ»ΡΡΠΈΠΎΠ½Π½ΠΎΠ΅ ΠΎΠ±ΠΎΡΡΠ΄ΠΎΠ²Π°Π½ΠΈΠ΅ ΠΎΠ±Π΅ΡΠΏΠ΅ΡΠΈΠ²Π°Π΅Ρ ΠΌΠ½ΠΎΠ³ΠΎΠΊΡΠ°ΡΠ½ΡΡ Π·Π°ΠΌΠ΅Π½Ρ Π²ΠΎΠ·Π΄ΡΡ
Π° Π² ΠΏΠΎΠΌΠ΅ΡΠ΅Π½ΠΈΠΈ ΠΈ Π½Π΅ Π΄ΠΎΠΏΡΡΠΊΠ°Π΅Ρ ΠΊΠΎΠ½ΡΠ΅Π½ΡΡΠ°ΡΠΈΡ ΠΏΠ΅Π½ΡΠ°Π½Π°, ΡΠ³ΡΠΎΠΆΠ°ΡΡΡΡ ΠΏΠΎΠΆΠ°ΡΠΎΠΌ ΠΈΠ»ΠΈ Π²Π·ΡΡΠ²ΠΎΠΌ.
9. ΠΠ΅Π·ΠΎΠΏΠ°ΡΠ½ΠΎΡΡΡ ΠΈ Π³ΠΈΠ³ΠΈΠ΅Π½Π° ΡΡΡΠ΄Π°
ΠΠ° Π²ΡΠ΅Ρ
ΡΡΠ°Π΄ΠΈΡΡ
ΠΏΡΠΎΠΈΠ·Π²ΠΎΠ΄ΡΡΠ²Π° ΠΏΠ΅Π½ΠΎΠΏΠΎΠ»ΠΈΡΡΠΈΡΠΎΠ» Π½Π΅ ΡΠ²Π»ΡΠ΅ΡΡΡ ΡΠΎΠΊΡΠΈΡΠ½ΡΠΌ ΠΈ Π½Π΅Ρ Π½Π΅ΠΎΠ±Ρ
ΠΎΠ΄ΠΈΠΌΠΎΡΡΠΈ ΠΏΡΠΈΠΌΠ΅Π½ΡΡΡ ΡΡΠ΅Π΄ΡΡΠ²Π° Π΄Π»Ρ Π²ΡΠ΅Π΄Π½ΠΎΠ³ΠΎ ΠΏΡΠΎΠΈΠ·Π²ΠΎΠ΄ΡΡΠ²Π°.
Π ΠΏΡΠΎΠΈΠ·Π²ΠΎΠ΄ΡΡΠ²Π΅Π½Π½ΡΡ
ΠΏΠΎΠΌΠ΅ΡΠ΅Π½ΠΈΡΡ
, Π² ΠΊΠΎΡΠΎΡΡΡ
ΠΈΠΌΠ΅Π΅ΡΡΡ ΠΏΠΎΠ²ΡΡΠ΅Π½Π½Π°Ρ Π²Π»Π°ΠΆΠ½ΠΎΡΡΡ (ΠΏΠΎΠΌΠ΅ΡΠ΅Π½ΠΈΡ Π²ΡΠΏΠ΅Π½ΠΈΠ²Π°ΡΠ΅Π»Π΅ΠΉ ΠΈ ΡΠΎΡΠΌ), ΠΏΠΎΠ» ΡΠ»Π΅Π΄ΡΠ΅Ρ Π²ΡΠ»ΠΎΠΆΠΈΡΡ Π΄Π΅ΡΠ΅Π²ΡΠ½Π½ΡΠΌ ΠΏΠ°ΡΠΊΠ΅ΡΠΎΠΌ. ΠΠ°ΠΆΠ΄ΠΎΠ΅ ΠΌΠ΅ΡΡΠΎ ΡΠ»Π΅Π΄ΡΠ΅Ρ ΠΎΠ±Π΅ΡΠΏΠ΅ΡΠΈΡΡ ΠΎΠ±ΡΠ΅ΠΉ ΠΈΠ½ΡΡΡΡΠΊΡΠΈΠ΅ΠΉ ΠΎΠ±ΡΠ»ΡΠΆΠΈΠ²Π°Π½ΠΈΡ, Π² ΠΊΠΎΡΠΎΡΠΎΠΉ ΠΎΠΏΡΠ΅Π΄Π΅Π»ΡΠ΅ΡΡΡ ΡΠΏΠΎΡΠΎΠ± ΡΠ°Π±ΠΎΡΡ ΠΈ ΡΠΎΠΎΡΠ²Π΅ΡΡΡΠ²ΡΡΡΠΈΠ΅ ΠΏΡΠ΅Π΄ΠΏΠΈΡΠ°Π½ΠΈΡ, ΡΡΠ²Π΅ΡΠΆΠ΄Π΅Π½Π½ΡΠ΅ ΡΠ»ΡΠΆΠ±ΠΎΠΉ Π±Π΅Π·ΠΎΠΏΠ°ΡΠ½ΠΎΡΡΠΈ ΡΡΡΠ΄Π°, ΡΠ°Π±ΠΎΡΡ Π² ΡΠΎΠΎΡΠ²Π΅ΡΡΡΠ²ΠΈΠΈ Ρ ΡΠ΅Ρ
Π½ΠΎΠ»ΠΎΠ³ΠΈΡΠ΅ΡΠΊΠΎΠΉ ΠΈΠ½ΡΡΡΡΠΊΡΠΈΠ΅ΠΉ ΡΠ°Π±ΠΎΡΡ Π½Π° Π΄Π°Π½Π½ΠΎΠΌ ΠΎΠ±ΠΎΡΡΠ΄ΠΎΠ²Π°Π½ΠΈΠΈ. ΠΠ΅ΡΡΠΎΠ½Π°Π» ΠΊ ΡΠ°Π±ΠΎΡΠ΅ ΠΌΠΎΠΆΠ΅Ρ Π±ΡΡΡ Π΄ΠΎΠΏΡΡΠ΅Π½ ΡΠΎΠ»ΡΠΊΠΎ ΠΏΠΎΡΠ»Π΅ ΠΎΠ·Π½Π°ΠΊΠΎΠΌΠ»Π΅Π½ΠΈΡ Ρ ΠΏΡΠ°Π²ΠΈΠ»Π°ΠΌΠΈ ΡΠ΅Ρ
Π½ΠΎΠ»ΠΎΠ³ΠΈΠΈ, ΡΠΊΡΠΏΠ»ΡΠ°ΡΠ°ΡΠΈΠΈ, ΠΎΠ±ΡΠ»ΡΠΆΠΈΠ²Π°Π½ΠΈΡ ΠΈ Π±Π΅Π·ΠΎΠΏΠ°ΡΠ½ΠΎΡΡΠΈ ΡΡΡΠ΄Π° Π½Π° Π΄Π°Π½Π½ΠΎΠΌ ΠΎΠ±ΠΎΡΡΠ΄ΠΎΠ²Π°Π½ΠΈΠΈ.
ΠΠΎ Π²ΡΠ΅ΠΌΡ ΡΠΊΡΠΏΠ»ΡΠ°ΡΠ°ΡΠΈΠΈ ΡΠ»Π΅Π΄ΡΠ΅Ρ ΠΎΠ±ΡΠ°ΡΠΈΡΡ Π²Π½ΠΈΠΌΠ°Π½ΠΈΠ΅ Π½Π° ΡΠ»Π΅Π΄ΡΡΡΠΈΠ΅ Π²ΠΎΠΏΡΠΎΡΡ:
Π. ΠΡΠ½Π°ΡΠ΅Π½ΠΈΠ΅ ΡΠ°Π±ΠΎΡΠΈΡ
ΠΌΠ΅ΡΡ ΠΎΠ±ΡΠ΅ΠΉ ΠΈΠ½ΡΡΡΡΠΊΡΠΈΠ΅ΠΉ ΠΏΠΎ ΠΎΠ±ΡΠ»ΡΠΆΠΈΠ²Π°Π½ΠΈΡ
Π. ΠΠΎΠ΄ΠΊΠ»ΡΡΠΈΡΡ ΡΠΈΡΡΠ΅ΠΌΡ ΡΠΈΠ³Π½Π°Π»ΠΈΠ·Π°ΡΠΈΠΈ ΠΈ Π·Π°ΡΠΈΡΡ ΠΎΡ Π²ΠΎΠ·ΡΠ°ΡΡΠ°Π½ΠΈΡ Π΄Π°Π²Π»Π΅Π½ΠΈΡ ΠΏΠ°ΡΠ°
Π. ΠΡΠΎΠ²ΠΎΠ΄ΠΈΡΡ ΠΎΠ±ΡΠ»ΡΠΆΠΈΠ²Π°Π½ΠΈΠ΅ ΡΠΈΡΡΠ΅ΠΌΡ ΡΡΡΠ±ΠΎΠΏΡΠΎΠ²ΠΎΠ΄ΠΎΠ² ΠΏΠ°ΡΠ° ΠΈ Π²ΠΎΠ·Π΄ΡΡ
Π° ΠΏΠΎΠ΄ Π΄Π°Π²Π»Π΅Π½ΠΈΠ΅ΠΌ
Π. ΠΠΎ Π²ΡΠ΅ΠΌΡ ΠΏΠΎΠ΄Π°ΡΠΈ ΠΏΠ°ΡΠ° Π² ΡΠΎΡΠΌΡ Π½Π°Ρ
ΠΎΠ΄ΠΈΡΡΡΡ Π·Π° ΠΏΡΠ»ΡΡΠΎΠΌ ΡΠΏΡΠ°Π²Π»Π΅Π½ΠΈΡ Π·Π° Π·Π°ΡΠΈΡΠ½ΡΠΌ ΡΠΊΡΠ°Π½ΠΎΠΌ
Π. ΠΡΠΎΠ²Π΅ΡΡΡΡ ΡΠΎΡΡΠΎΡΠ½ΠΈΠ΅ ΠΏΠ½Π΅Π²ΠΌΠΎΡΡΠ°Π½ΡΠΏΠΎΡΡΠ°
Π. ΠΠ°ΠΏΡΠ΅ΡΠΈΡΡ ΠΊΡΡΠ΅Π½ΠΈΠ΅ Π² ΠΏΡΠΎΠΈΠ·Π²ΠΎΠ΄ΡΡΠ²Π΅Π½Π½ΡΡ
ΠΈ ΡΠΊΠ»Π°Π΄ΡΠΊΠΈΡ
ΠΏΠΎΠΌΠ΅ΡΠ΅Π½ΠΈΡΡ
Π. ΠΡΠΎΠ²Π΅ΡΡΡΡ ΡΠΎΡΡΠΎΡΠ½ΠΈΠ΅ Π²ΡΡΡΠΆΠ½ΠΎΠ³ΠΎ ΠΎΠ±ΠΎΡΡΠ΄ΠΎΠ²Π°Π½ΠΈΡ
Π. ΠΠ΅ Π±Π»ΠΎΠΊΠΈΡΠΎΠ²Π°ΡΡ ΠΏΡΡΠ΅ΠΉ ΡΡΠ°Π½ΡΠΏΠΎΡΡΠΈΡΠΎΠ²Π°Π½ΠΈΡ ΠΈ Π΄Π²Π΅ΡΠΈ
ΠΠΎ Π²ΡΠ΅Ρ
ΠΏΠΎΠΌΠ΅ΡΠ΅Π½ΠΈΡΡ
Β ΡΠ»Π΅Π΄ΡΠ΅Ρ ΠΏΠΎΠΌΠ΅ΡΡΠΈΡΡ Π½Π°Π΄ΠΏΠΈΡΠΈ ΠΎ Π·Π°ΠΏΡΠ΅ΡΠ΅Π½ΠΈΠΈ ΠΊΡΡΠ΅Π½ΠΈΡ, Π³Π°ΡΠ΅Π½ΠΈΡ ΠΏΠΎΠΆΠ°ΡΠ° Π²ΠΎΠ΄ΠΎΠΉ
ΠΎΠ±ΠΎΡΡΠ΄ΠΎΠ²Π°Π½ΠΈΡ ΠΏΠΎΠ΄ Π½Π°ΠΏΡΡΠΆΠ΅Π½ΠΈΠ΅ΠΌ, ΠΎΠ±ΠΎΡΡΠ΄ΠΎΠ²Π°ΡΡ ΠΏΠΎΠΌΠ΅ΡΠ΅Π½ΠΈΡ ΡΡΠ΅Π΄ΡΡΠ²Π°ΠΌΠΈ ΠΏΠΎΠΆΠ°ΡΠΎΡΡΡΠ΅Π½ΠΈΡ.
ΠΠΎ Π²ΡΠ΅ΠΌΡ ΡΠ΅ΠΌΠΎΠ½ΡΠ½ΡΡ
ΡΠ°Π±ΠΎΡ Π² ΠΊΠ°ΡΠ΅ΡΡΠ²Π΅ ΠΌΠ΅ΡΡΠ½ΠΎΠ³ΠΎ ΠΎΡΠ²Π΅ΡΠ΅Π½ΠΈΡ ΠΏΡΠΈΠΌΠ΅Π½ΡΡΡ Π»Π°ΠΌΠΏΡ Ρ Π½Π°ΠΏΡΡΠΆΠ΅Π½ΠΈΠ΅ΠΌ 24Π.
10. ΠΠ±Π΅ΡΠΏΠ΅ΡΠ΅Π½ΠΈΠ΅ ΠΏΠΎΠΆΠ°ΡΠ½ΠΎΠΉ Π±Π΅Π·ΠΎΠΏΠ°ΡΠ½ΠΎΡΡΠΈ
ΠΠ±ΡΠ΅ΠΊΡ ΠΏΡΠΎΠΈΠ·Π²ΠΎΠ΄ΡΡΠ²Π° ΠΎΡΠ½ΠΎΡΠΈΡΡΡ ΠΊ ΡΡΠ΅ΡΡΠ΅ΠΉ ΠΊΠ°ΡΠ΅Π³ΠΎΡΠΈΠΈ ΠΎΠ±ΡΠ΅ΠΊΡΠΎΠ² ΠΏΠΎ ΠΏΠΎΠΆΠ°ΡΠ½ΠΎΠΉ Π±Π΅Π·ΠΎΠΏΠ°ΡΠ½ΠΎΡΡΠΈ. ΠΠ΄Π°Π½ΠΈΠ΅
ΠΎΡΠ½ΠΎΡΠΈΡΡΡ ΠΊ ΠΊΠ»Π°ΡΡΡ Β«Π‘Β», ΠΏΡΠΈΡΠ΅ΠΌ ΠΏΠΎΠΌΠ΅ΡΠ΅Π½ΠΈΠ΅ ΡΠΊΠ»Π°Π΄Π° ΡΡΡΡΡ Π΄ΠΎΠ»ΠΆΠ½ΠΎ Π±ΡΡΡ ΠΊΠ»Π°ΡΡΠ° Β«ΠΒ» ΠΈ ΠΈΠΌΠ΅ΡΡ ΠΎΠ³Π½Π΅ΡΠΏΠΎΡΠ½ΡΠ΅ Π΄Π²Π΅ΡΠΈ.
ΠΡΠ΅ ΠΏΠΎΠΌΠ΅ΡΠ΅Π½ΠΈΡ Π΄ΠΎΠ»ΠΆΠ½Ρ Π±ΡΡΡ ΠΎΠ±ΠΎΡΡΠ΄ΠΎΠ²Π°Π½Ρ Π³ΠΈΠ΄ΡΠ°Π½ΡΠ°ΠΌΠΈ. ΠΡΠΎΠΌΠ΅ ΡΠΎΠ³ΠΎ, Π²ΡΠ΅ ΠΏΠΎΠΌΠ΅ΡΠ΅Π½ΠΈΡ Π΄ΠΎΠ»ΠΆΠ½Ρ Π±ΡΡΡ
ΠΎΠ±Π΅ΡΠΏΠ΅ΡΠ΅Π½Ρ ΡΡΠ΅Π΄ΡΡΠ²Π°ΠΌΠΈ ΠΏΠΎΠΆΠ°ΡΠ½ΠΎΠ³ΠΎ ΡΡΡΠ΅Π½ΠΈΡ Π² ΠΊΠΎΠ»ΠΈΡΠ΅ΡΡΠ²Π΅ Π½Π΅ ΠΌΠ΅Π½Π΅Π΅: ΡΠ³Π»Π΅ΠΊΠΈΡΠ»ΠΎΡΠ½ΡΠ΅ ΠΎΠ³Π½Π΅ΡΡΡΠΈΡΠ΅Π»ΠΈ (ΠΏΠΎ Π΄Π²Π° Π² ΠΊΠ°ΠΆΠ΄ΠΎΠΌ ΠΏΠΎΠΌΠ΅ΡΠ΅Π½ΠΈΠΈ), 2 ΡΠ³Π»Π΅ΠΊΠΈΡΠ»ΠΎΡΠ½ΡΡ
Π°Π³ΡΠ΅Π³Π°ΡΠ° ΡΡΡΠ΅Π½ΠΈΡ (Π² ΠΏΠΎΠΌΠ΅ΡΠ΅Π½ΠΈΠΈ Π±ΡΠ½ΠΊΠ΅ΡΠΎΠ² ΠΈ Π²ΡΠ΄Π΅ΡΠΆΠΊΠΈ Π±Π»ΠΎΠΊΠΎΠ²), 2 Π°ΡΠ±Π΅ΡΡΠΎΠ²ΡΡ
ΡΠ΅Π½ΡΠ° (ΠΏΠΎ 2 Π² ΠΊΠ°ΠΆΠ΄ΠΎΠΌ ΠΏΠΎΠΌΠ΅ΡΠ΅Π½ΠΈΠΈ).
11. ΠΡΠΎΡΠ΅ΡΡ Π΄Π²ΠΎΠΉΠ½ΠΎΠ³ΠΎ Π²ΡΠΏΠ΅Π½ΠΈΠ²Π°Π½ΠΈΡ Π³ΡΠ°Π½ΡΠ» ΠΈΠ· ΠΏΠ΅Π½ΠΎΠΏΠΎΠ»ΠΈΡΡΠΈΡΠΎΠ»Π°.
ΠΡΠΎΡΠ΅ΡΡ Π΄Π²ΠΎΠΉΠ½ΠΎΠ³ΠΎ Π²ΡΠΏΠ΅Π½ΠΈΠ²Π°Π½ΠΈΡ Π³ΡΠ°Π½ΡΠ» ΠΏΡΠΈΠΌΠ΅Π½ΡΠ΅ΡΡΡ Π΄Π»Ρ ΡΠΌΠ΅Π½ΡΡΠ΅Π½ΠΈΡ ΡΠ°ΡΡ ΠΎΠ΄Π° ΡΡΡΡΡ, ΠΌΠ΅Π½Π΅Π΅ 14-15 ΠΊΠ³/ΠΌ3. ΠΡΠΎΡΠ΅ΡΡ Π·Π°ΠΊΠ»ΡΡΠ°Π΅ΡΡΡ Π² ΡΠΎΠΌ, ΡΡΠΎ Π²ΠΎ Π²ΡΠ΅ΠΌΡ ΠΏΠ΅ΡΠ²ΠΎΠ³ΠΎ Π²ΡΠΏΠ΅Π½ΠΈΠ²Π°Π½ΠΈΡ, ΡΠ΄Π΅Π»ΡΠ½Π°Ρ ΠΏΠ»ΠΎΡΠ½ΠΎΡΡΡ Π³ΡΠ°Π½ΡΠ» Π½Π°ΡΡΠΏΡΡ Π½Π°Ρ ΠΎΠ΄ΠΈΡΡΡ Π² ΠΏΡΠ΅Π΄Π΅Π»Π°Ρ 16-18 ΠΊΠ³/ΠΌ3, Π° ΠΏΠΎΡΠ»Π΅ ΠΈΡ Π²ΡΡΡΡΠΈΠ²Π°Π½ΠΈΡ ΠΏΡΠΎΠ²ΠΎΠ΄ΠΈΡΡΡ ΠΏΠΎΠ²ΡΠΎΡΠ½ΠΎΠ΅ Π²ΡΠΏΠ΅Π½ΠΈΠ²Π°Π½ΠΈΠ΅ ΠΈ ΡΠ΄Π΅Π»ΡΠ½ΡΠΉ Π²Π΅Ρ Π½Π°ΡΡΠΏΡΡ ΡΠΎΡΡΠ°Π²Π»ΡΠ΅Ρ 11-12 ΠΊΠ³/ΠΌ3. ΠΡΠ°Π½ΡΠ»Ρ ΠΏΠΎΡΠ»Π΅ ΠΏΡΠΎΠ²Π΅Π΄Π΅Π½ΠΈΡ ΠΏΡΠΎΡΠ΅ΡΡΠ° Π²ΡΠ΄Π΅ΡΠΆΠΊΠΈ ΠΏΡΠ΅Π΄Π½Π°Π·Π½Π°ΡΠ°ΡΡΡΡ Π΄Π»Ρ ΡΠΎΡΠΌΠΈΡΠΎΠ²Π°Π½ΠΈΡ ΠΈΠ·Π΄Π΅Π»ΠΈΠΉ Ρ ΠΏΠ»ΠΎΡΠ½ΠΎΡΡΡΡ 12-15 ΠΊΠ³/ΠΌ3. ΠΡΠΎΡΠ΅ΡΡ Π²ΡΠΏΠ΅Π½ΠΈΠ²Π°Π½ΠΈΡ ΠΌΠΎΠΆΠ½ΠΎ ΠΏΡΠΎΠ²ΠΎΠ΄ΠΈΡΡ ΠΌΠ½ΠΎΠ³ΠΎΠΊΡΠ°ΡΠ½ΠΎ ΠΈ Π΄ΠΎΠ²Π΅ΡΡΠΈ ΠΏΠ»ΠΎΡΠ½ΠΎΡΡΡ Π΄ΠΎ 5-7 ΠΊΠ³/ΠΌ3, ΠΎΠ΄Π½Π°ΠΊΠΎ ΡΠΎΡΠΌΠΎΠ²Π°Π½ΠΈΠ΅ ΠΈΠ·Π΄Π΅Π»ΠΈΠΉ ΠΈΠ· ΡΠ°ΠΊΠΈΡ ΠΈΠ½ΡΠ΅Π½ΡΠΈΠ²Π½ΠΎ Π²ΡΠΏΠ΅Π½Π΅Π½Π½ΡΡ Π³ΡΠ°Π½ΡΠ» Π·Π°ΡΡΡΠ΄Π½Π΅Π½ΠΎ, ΡΠ°ΠΊ ΠΊΠ°ΠΊ Π² Π½ΠΈΡ ΠΎΡΡΠ°Π΅ΡΡΡ Π½Π΅Π±ΠΎΠ»ΡΡΠΎΠ΅ ΡΠΎΠ΄Π΅ΡΠΆΠ°Π½ΠΈΠ΅ ΠΏΠΎΡΠΎΡΠΎΡΠ°. Π’Π°ΠΊΠΆΠ΅ ΠΈΠ·Π΄Π΅Π»ΠΈΡ ΠΈΠ· Π½Π΅Π³ΠΎ Ρ Π°ΡΠ°ΠΊΡΠ΅ΡΠΈΠ·ΡΡΡΡΡ Π½Π΅Π²ΡΡΠΎΠΊΠΎΠΉ ΡΡΠΎΠΉΠΊΠΎΡΡΡΡ ΠΊ ΠΌΠ΅Ρ Π°Π½ΠΈΡΠ΅ΡΠΊΠΈΠΌ Π²ΠΎΠ·Π΄Π΅ΠΉΡΡΠ²ΠΈΡΠΌ, ΠΊΠΎΠ³Π΄Π° ΡΠΎΠ΄Π΅ΡΠΆΠ°Π½ΠΈΠ΅ ΠΏΠΎΠ»ΠΈΠΌΠ΅ΡΠ° ΡΠΎΡΡΠ°Π²Π»ΡΠ΅Ρ 0,5-0,7 % ΠΎΡ ΠΎΠ±ΡΠ΅ΠΌΠ°, Π° Π²ΠΎΠ·Π΄ΡΡ Π° ΡΠΎΠΎΡΠ²Π΅ΡΡΡΠ²Π΅Π½Π½ΠΎ 99,3-99,5% ΠΎΠ±ΡΠ΅ΠΌΠ°. ΠΡΠΎΡΠ΅ΡΡ ΠΌΠ½ΠΎΠ³ΠΎΠΊΡΠ°ΡΠ½ΠΎΠ³ΠΎ Π²ΡΠΏΠ΅Π½ΠΈΠ²Π°Π½ΠΈΡ Π±ΡΠ» Π·Π°ΠΏΠ°ΡΠ΅Π½ΡΠΎΠ²Π°Π½ Π΅ΡΠ΅ Π² 1961 Π³ΠΎΠ΄Ρ.
Β Β 11.1. Π’Π΅ΠΎΡΠ΅ΡΠΈΡΠ΅ΡΠΊΠΎΠ΅ ΠΎΠ±ΠΎΡΠ½ΠΎΠ²Π°Π½ΠΈΠ΅Β ΠΏΡΠΎΡΠ΅ΡΡΠ° Π΄Π²ΡΠΊΡΠ°ΡΠ½ΠΎΠ³ΠΎ Π²ΡΠΏΠ΅Π½ΠΈΠ²Π°Π½ΠΈΡ.
ΠΠ· ΠΊΠΈΠ½Π΅ΡΠΈΡΠ΅ΡΠΊΠΎΠΉ ΠΊΡΠΈΠ²ΠΎΠΉ Π²ΡΠΏΠ΅Π½ΠΈΠ²Π°Π½ΠΈΡ ΡΠ»Π΅Π΄ΡΠ΅Ρ, ΡΡΠΎ ΠΏΡΠΎΡΠ΅ΡΡ ΠΏΡΠΎΡ
ΠΎΠ΄ΠΈΡ ΠΈΠ½ΡΠ΅Π½ΡΠΈΠ²Π½ΠΎ Π² ΡΠ΅ΡΠ΅Π½ΠΈΠ΅ ΠΏΠ΅ΡΠ²ΡΡ
2-3 ΠΌΠΈΠ½ΡΡ ΠΈ ΠΌΠ°ΡΡΠ° Π½Π°ΡΡΠΏΠ°Π½Π½ΡΡ
Π³ΡΠ°Π½ΡΠ» ΡΠΌΠ΅Π½ΡΡΠ°Π΅ΡΡΡ Ρ 550 Π΄ΠΎ 25-30 ΠΊΠ³/ΠΌ3 ΠΈΠ»ΠΈ Π² 18-22 ΡΠ°Π·Π°, ΡΠΎΠΎΡΠ²Π΅ΡΡΡΠ²Π΅Π½Π½ΠΎ ΡΠ²Π΅Π»ΠΈΡΠΈΠ²Π°Π΅ΡΡΡ ΠΎΠ±ΡΠ΅ΠΌ, Π° ΠΏΡΠΈ Π±ΠΎΠ»Π΅Π΅ Π΄ΠΎΠ»Π³ΠΎΠΌ Π²ΡΠΏΠ΅Π½ΠΈΠ²Π°Π½ΠΈΠΈ ΠΏΡΠΎΡΠ΅ΡΡ Π·Π°ΡΠΎΡΠΌΠ°ΠΆΠΈΠ²Π°Π΅ΡΡΡ, Π΄Π°ΠΆΠ΅ ΠΌΠΎΠΆΠ΅Ρ ΠΈΠΌΠ΅ΡΡ ΠΌΠ΅ΡΡΠΎ ΡΠ²Π΅Π»ΠΈΡΠ΅Π½ΠΈΠ΅ ΠΏΠ»ΠΎΡΠ½ΠΎΡΡΠΈ Π³ΡΠ°Π½ΡΠ». ΠΡΠΎ ΡΠ²ΡΠ·Π°Π½ΠΎ Ρ ΠΏΠΎΡΠ΅ΡΠ΅ΠΉ ΠΏΠΎΡΠΎΡΠΎΡΠ° ΠΏΡΠΈ Π²ΡΠΏΠ΅Π½ΠΈΠ²Π°Π½ΠΈΠΈ. ΠΠΎ Π²ΡΠ΅ΠΌΡ Π½Π°Π³ΡΠ΅Π²Π°Π½ΠΈΡ Π³ΡΠ°Π½ΡΠ» Π΄ΠΎ ΡΠ΅ΠΌΠΏΠ΅ΡΠ°ΡΡΡΡ Π²ΡΠΏΠ΅Π½ΠΈΠ²Π°Π½ΠΈΡ (ΠΎΠΊΠΎΠ»ΠΎ 100Β°Π‘) Π½Π°Ρ
ΠΎΠ΄ΡΡΠΈΠΉΡΡ Π² Π½ΠΈΡ
ΠΏΠΎΡΠΎΡΠΎΡ-ΠΏΠ΅Π½ΡΠ°Π½ (Ρ
ΠΈΠΌΠΈΡΠ΅ΡΠΊΠ°Ρ ΡΠΎΡΠΌΡΠ»Π° Π‘5Π12, ΡΠ΅ΠΌΠΏΠ΅ΡΠ°ΡΡΡΠ° ΠΊΠΈΠΏΠ΅Π½ΠΈΡ β 36,5Β°Π‘) ΠΏΡΠ΅Π²ΡΠ°ΡΠ°Π΅ΡΡΡ Π² ΠΏΠ°Ρ. ΠΠ³ΠΎ ΡΡΠ΅ΡΠΊΠ° Π½Π΅Π²Π΅Π»ΠΈΠΊΠ° ΠΈ Π΄Π»Ρ ΠΏΠΎΠ΄Π΄Π΅ΡΠΆΠ°Π½ΠΈΡ ΡΠ°Π²Π½ΠΎΠ²Π΅ΡΠΈΡ Π΄Π°Π²Π»Π΅Π½ΠΈΡ Π³ΡΠ°Π½ΡΠ»Ρ ΡΠ°ΡΡΠΈΡΡΡΡΡΡ. ΠΡΠ½ΠΎΠ²Π½ΡΠ΅ ΠΏΠΎΡΠ΅ΡΠΈ ΠΏΡΠΎΠΈΡΡ
ΠΎΠ΄ΡΡ ΠΏΠΎ ΠΏΡΠΈΡΠΈΠ½Π΅ ΡΠ²Π΅Π»ΠΈΡΠ΅Π½ΠΈΡ ΠΎΠ±ΡΠ΅ΠΌΠ°, Π° Π³Π»Π°Π²Π½ΠΎΠ΅ Π²ΡΠ΅ΠΌΠ΅Π½ΠΈ Π²ΡΠΏΠ΅Π½ΠΈΠ²Π°Π½ΠΈΡ. Π ΠΏΡΠΎΡΠ΅ΡΡΠ΅ ΠΌΠ½ΠΎΠ³ΠΎΠΊΡΠ°ΡΠ½ΠΎΠ³ΠΎ Π²ΡΠΏΠ΅Π½ΠΈΠ²Π°Π½ΠΈΡ Π³ΡΠ°Π½ΡΠ» ΠΏΠΎΡΠΎΡΠΎΡ ΡΠ°Π·ΡΠ΅ΠΆΠ°Π΅ΡΡΡ Π²ΠΎΠ·Π΄ΡΡ
ΠΎΠΌ, ΠΏΡΠΎΠ½ΠΈΠΊΠ°ΡΡΠΈΠΌ Π² Π³ΡΠ°Π½ΡΠ»Ρ Π² ΠΏΡΠΎΡΠ΅ΡΡΠ΅ Π²ΡΠ΄Π΅ΡΠΆΠΊΠΈ.
ΠΡΠ΅ΠΌΡ Π΄Π²ΠΎΠΉΠ½ΠΎΠ³ΠΎ Π²ΡΠΏΠ΅Π½ΠΈΠ²Π°Π½ΠΈΡ ΠΏΠΎΡΡΠΈ ΡΠΎΠ²ΠΏΠ°Π΄Π°Π΅Ρ ΡΠΎ Π²ΡΠ΅ΠΌΠ΅Π½Π΅ΠΌ ΠΎΠ΄ΠΈΠ½Π°ΡΠ½ΠΎΠ³ΠΎ Π²ΡΠΏΠ΅Π½ΠΈΠ²Π°Π½ΠΈΡ, ΠΏΠΎΡΡΠΎΠΌΡ ΠΏΠΎΡΠ΅ΡΠΈ ΠΏΠΎΡΠΎΡΠΎΡΠ° ΠΎΠ΄ΠΈΠ½Π°ΠΊΠΎΠ²Ρ Π² ΠΎΠ±ΠΎΠΈΡ
ΡΠ»ΡΡΠ°ΡΡ
.
ΠΠΎ Π²ΡΠ΅Ρ
ΡΠ»ΡΡΠ°ΡΡ
Π²ΡΠΏΠ΅Π½ΠΈΠ²Π°Π½ΠΈΡ ΡΡΡΠ΅ΡΡΠ²Π΅Π½Π½Π° ΡΠΎΠ»Ρ ΠΏΠ°ΡΠ°. ΠΠ½ ΡΠ²Π»ΡΠ΅ΡΡΡ Π΄ΠΎΠΏΠΎΠ»Π½ΠΈΡΠ΅Π»ΡΠ½ΡΠΌ ΠΈΡΡΠΎΡΠ½ΠΈΠΊΠΎΠΌ
Π²ΡΠΏΠ΅Π½ΠΈΠ²Π°Π½ΠΈΡ. ΠΠ»Π°Π³ΠΎΠ΄Π°ΡΡ ΡΠΈΠ»ΡΠ½ΠΎΠΉ Π΄ΠΈΡΡΡΠ·ΠΈΠΈ ΠΎΠ½ ΠΏΡΠΎΠ½ΠΈΠΊΠ°Π΅Ρ Π² ΠΎΠ±ΡΠ°Π·ΡΡΡΠΈΠ΅ΡΡ ΠΌΠΈΠΊΡΠΎΠΏΠΎΡΡΒ ΠΈ ΠΏΡΠΈΠ²ΠΎΠ΄ΠΈΡ Π² ΡΠΎΠΎΡΠ²Π΅ΡΡΡΠ²ΠΈΠ΅ Π΄Π°Π²Π»Π΅Π½ΠΈΠ΅ Π² Π³ΡΠ°Π½ΡΠ»Π°Ρ
Ρ Π²Π½Π΅ΡΠ½ΠΈΠΌ Π΄Π°Π²Π»Π΅Π½ΠΈΠ΅ΠΌ.
Β Β 11.2. ΠΡΠΎΡΠ΅ΡΡ Π΄Π²ΠΎΠΉΠ½ΠΎΠ³ΠΎ Π²ΡΠΏΠ΅Π½ΠΈΠ²Π°Π½ΠΈΡ.
Π’Π΅Ρ
Π½ΠΎΠ»ΠΎΠ³ΠΈΡΠ΅ΡΠΊΠΈΠΉ ΠΏΡΠΎΡΠ΅ΡΡ Π΄Π²ΠΎΠΉΠ½ΠΎΠ³ΠΎ Π²ΡΠΏΠ΅Π½ΠΈΠ²Π°Π½ΠΈΡ Π²ΡΠ³Π»ΡΠ΄ΠΈΡ ΡΠ»Π΅Π΄ΡΡΡΠΈΠΌ ΠΎΠ±ΡΠ°Π·ΠΎΠΌ: Π½Π° ΠΏΠ΅ΡΠ²ΠΎΠΌ ΡΡΠ°ΠΏΠ΅
Π²ΡΠΏΠ΅Π½ΠΈΠ²Π°Π½ΠΈΡ, ΠΏΡΠΎΠ²ΠΎΠ΄ΡΡΠ΅ΠΉΡΡ Π² Π°ΡΠΌΠΎΡΡΠ΅ΡΠ΅ Π²ΠΎΠ΄ΡΠ½ΠΎΠ³ΠΎ ΠΏΠ°ΡΠ°, Π½Π°Π΄Π»Π΅ΠΆΠΈΡ Π΄ΠΎΠ²Π΅ΡΡΠΈ ΡΠ΄Π΅Π»ΡΠ½ΡΠΉ Π²Π΅Ρ Π³ΡΠ°Π½ΡΠ» Π΄ΠΎ 16-18 ΠΊΠ³/ΠΌ3. Π£ΡΠ»ΠΎΠ²ΠΈΡΠΌΠΈ ΠΏΠΎΠ»ΡΡΠ΅Π½ΠΈΡ ΡΠ°ΠΊΠΎΠΉ ΠΈΠ½ΡΠ΅Π½ΡΠΈΠ²Π½ΠΎΡΡΠΈ Π²ΡΠΏΠ΅Π½ΠΈΠ²Π°Π½ΠΈΡ ΡΠ²Π»ΡΡΡΡΡ ΡΠΎΠΎΡΠ²Π΅ΡΡΡΠ²ΡΡΡΠΈΠΉ ΠΏΠΎΠ΄Π±ΠΎΡ ΡΠΊΠΎΡΠΎΡΡΠΈ ΠΈΡ
Π΄ΠΎΠ·ΠΈΡΠΎΠ²Π°Π½ΠΈΡ, Π²ΡΠ΅ΠΌΠ΅Π½ΠΈ ΠΏΡΠ΅Π±ΡΠ²Π°Π½ΠΈΡ Π²ΠΎ Π²ΡΠΏΠ΅Π½ΠΈΠ²Π°ΡΠ΅Π»Π΅ ΠΈΠ»ΠΈ ΡΠ΅ΠΌΠΏΠ΅ΡΠ°ΡΡΡΡ Π²ΡΠΏΠ΅Π½ΠΈΠ²Π°Π½ΠΈΡ ΠΏΠΎΡΡΠ΅Π΄ΡΡΠ²ΠΎΠΌ ΠΈΡΠΏΠΎΠ»ΡΠ·ΠΎΠ²Π°Π½ΠΈΡ ΡΠΌΠ΅ΡΠΈ ΠΏΠ°ΡΠ° ΠΈ Π²ΠΎΠ·Π΄ΡΡ
Π°.
ΠΠΎΡΠ»Π΅ ΠΏΠ΅ΡΠ²ΠΎΠΉ ΡΡΠ°Π΄ΠΈΠΈ Π³ΡΠ°Π½ΡΠ»Ρ Π²ΡΡΡΡΠΈΠ²Π°ΡΡ Π½Π° ΠΌΠ΅ΡΡΠ΅ Π² ΠΏΠΎΠ΄Π²Π΅ΡΠ΅Π½Π½ΠΎΠΌ ΡΠΎΡΡΠΎΡΠ½ΠΈΠΈ ΠΏΡΠΈ ΠΊΠ°ΠΊ ΠΌΠΎΠΆΠ½ΠΎ Π±ΠΎΠ»Π΅Π΅ Π²ΡΡΠΎΠΊΠΎΠΉ ΡΠ΅ΠΌΠΏΠ΅ΡΠ°ΡΡΡΠ΅ ΠΈ Π²ΡΠ΄Π΅ΡΠΆΠΈΠ²Π°ΡΡ Π½Π° ΠΌΠ΅ΡΡΠ΅. Π Π°ΡΡΠ΅ΡΡ ΠΏΠΎ Π²ΡΠ΄Π΅ΡΠΆΠΈΠ²Π°Π½ΠΈΡ Π΄Π»Ρ 1 ΡΡΡΠΏΠ΅Π½ΠΈ: ΡΠ΅ΠΌΠΏΠ΅ΡΠ°ΡΡΡΠ° 15-25Β°Π‘, Π²ΡΠ΅ΠΌΡ 3-8 ΡΠ°ΡΠΎΠ². ΠΡΡΡΡΠ΅Π½Π½ΡΠ΅ Π³ΡΠ°Π½ΡΠ»Ρ ΠΏΠΎΠ²ΡΠΎΡΠ½ΠΎ ΠΏΠΎΡΡΡΠΏΠ°ΡΡ Π²ΠΎ Π²ΡΠΏΠ΅Π½ΠΈΠ²Π°ΡΠ΅Π»Ρ ΠΈ ΠΏΡΠΈ ΠΏΠΎΠΌΠΎΡΠΈ ΠΏΠ°ΡΠ° ΠΈΠ»ΠΈ ΡΠΌΠ΅ΡΠΈ Π΅Π³ΠΎ Ρ Π²ΠΎΠ·Π΄ΡΡ
ΠΎΠΌ Π²ΡΠΏΠ΅Π½ΠΈΠ²Π°ΡΡΡΡ Π΄ΠΎ Π΄ΠΎΡΡΠΈΠΆΠ΅Π½ΠΈΡ ΡΠ΄Π΅Π»ΡΠ½ΠΎΠ³ΠΎ Π²Π΅ΡΠ° 11-12 ΠΊΠ³/ΠΌ3. ΠΠ²ΡΠΊΡΠ°ΡΠ½ΠΎ Π²ΡΠΏΠ΅Π½Π΅Π½Π½ΡΠ΅ Π³ΡΠ°Π½ΡΠ»Ρ Π²ΡΡΡΡΠΈΠ²Π°ΡΡ ΠΏΠΎΠ΄ΠΎΠ±Π½ΠΎ 1 ΡΡΡΠΏΠ΅Π½ΠΈ ΠΈ Π½Π°ΠΏΡΠ°Π²Π»ΡΡΡ Π² Π±ΡΠ½ΠΊΠ΅ΡΡ, Π² ΠΊΠΎΡΠΎΡΡΡ
ΠΈΡ
Π²ΡΠ΄Π΅ΡΠΆΠΈΠ²Π°ΡΡ. Π Π°ΡΡΠ΅ΡΡ ΠΏΠΎ Π²ΡΠ΄Π΅ΡΠΆΠΈΠ²Π°Π½ΠΈΡ Π΄Π»Ρ 2 ΡΡΡΠΏΠ΅Π½ΠΈ: ΡΠ΅ΠΌΠΏΠ΅ΡΠ°ΡΡΡΠ° 15-25Β°Π‘, Π²ΡΠ΅ΠΌΡ 5-15 ΡΠ°ΡΠΎΠ². ΠΠΎΡΠ»Π΅ Π²ΡΠ΄Π΅ΡΠΆΠΊΠΈ Π³ΡΠ°Π½ΡΠ»Ρ ΠΏΡΠ΅Π΄Π½Π°Π·Π½Π°ΡΠ°ΡΡΡΡ Π΄Π»Ρ ΡΠΎΡΠΌΠΈΡΠΎΠ²Π°Π½ΠΈΡ Π±Π»ΠΎΠΊΠΎΠ². Π£ΡΠ»ΠΎΠ²ΠΈΡ ΡΠΎΡΠΌΠΈΡΠΎΠ²Π°Π½ΠΈΡ Π±Π»ΠΎΠΊΠΎΠ² ΡΠ»Π΅Π΄ΡΠ΅Ρ ΠΏΠΎΠ΄Π±ΠΈΡΠ°ΡΡ ΠΎΠΏΡΡΠ½ΡΠΌ ΠΏΡΡΠ΅ΠΌ, ΠΈΠΌΠ΅Ρ Π² Π²ΠΈΠ΄Ρ ΠΏΠΎΠ²ΡΡΠ΅Π½Π½ΡΡ Π΄Π΅ΡΠΎΡΠΌΠΈΡΡΠ΅ΠΌΠΎΡΡΡ Π³ΡΠ°Π½ΡΠ» ΠΏΡΠΈ Π½ΠΈΠ·ΠΊΠΎΠΌ ΡΠ΄Π΅Π»ΡΠ½ΠΎΠΌ Π²Π΅ΡΠ΅ Π½Π° ΡΠΆΠ°ΡΠΈΠ΅ Ρ ΡΡΠΎΡΠΌΠΈΡΠΎΠ²Π°Π½Π½ΡΡ
Π±Π»ΠΎΠΊΠΎΠ².
Β Β 11.3. Π’Π΅Ρ Π½ΠΎΠ»ΠΎΠ³ΠΈΡ ΠΏΡΠΎΡΠ΅ΡΡΠ° ΠΈ ΠΎΡΠ½Π°ΡΠ΅Π½ΠΈΠ΅
ΠΠ΅ΡΠ²ΠΎΠ΅ Π²ΡΠΏΠ΅Π½ΠΈΠ²Π°Π½ΠΈΠ΅ ΠΠΎ Π²ΡΠ΅ΠΌΡ ΡΡΠΎΠ³ΠΎ ΡΡΠ°ΠΏΠ° Π³ΡΠ°Π½ΡΠ»Ρ Π΄ΠΎΠ»ΠΆΠ½Ρ Π΄ΠΎΡΡΠΈΡΡ ΡΠ΄Π΅Π»ΡΠ½ΠΎΠ³ΠΎ Π²Π΅ΡΠ° Π½Π°ΡΡΠΏΡΡ Π² ΠΏΡΠ΅Π΄Π΅Π»Π°Ρ 16-18 ΠΊΠ³/ΠΌ3. ΠΠ»Ρ ΡΡΠΈΡ ΡΠ΅Π»Π΅ΠΉ Π½Π΅ΠΎΠ±Ρ ΠΎΠ΄ΠΈΠΌΠΎ ΠΏΠΎΠ΄ΠΎΠ±ΡΠ°ΡΡ ΠΎΠΏΡΠ΅Π΄Π΅Π»Π΅Π½Π½ΡΠ΅ ΠΏΠ°ΡΠ°ΠΌΠ΅ΡΡΡ Π²ΡΠΏΠ΅Π½ΠΈΠ²Π°Π½ΠΈΡ. ΠΡΠΎΠ³ΠΎ ΠΌΠΎΠΆΠ½ΠΎ Π΄ΠΎΡΡΠΈΡΡ ΠΏΠΎΡΡΠ΅Π΄ΡΡΠ²ΠΎΠΌ:
- ΡΠΌΠ΅Π½ΡΡΠ΅Π½ΠΈΡ ΡΡΠΎΠ²Π½Ρ Π·Π°ΡΡΠΏΠ°Π½ΠΈΡ Π²ΠΎ Π²ΡΠΏΠ΅Π½ΠΈΠ²Π°ΡΠ΅Π»Ρ, ΡΡΠΎ ΠΏΡΠΈΠ²ΠΎΠ΄ΠΈΡ, ΠΎΠ΄Π½Π°ΠΊΠΎ, ΠΊ ΡΠΌΠ΅Π½ΡΡΠ΅Π½ΠΈΡ
ΠΏΡΠΎΠΈΠ·Π²ΠΎΠ΄ΠΈΡΠ΅Π»ΡΠ½ΠΎΡΡΠΈ - ΡΠΌΠ΅Π½ΡΡΠ΅Π½ΠΈΠ΅ ΠΊΠΎΠ»ΠΈΡΠ΅ΡΡΠ²Π° ΠΏΠΎΠ΄Π°Π²Π°Π΅ΠΌΠΎΠ³ΠΎ ΠΏΠ°ΡΠ° Π²ΠΎ Π²ΡΠΏΠ΅Π½ΠΈΠ²Π°ΡΠ΅Π»Ρ ΠΈ ΡΠ΅ΠΌ ΡΠ°ΠΌΡΠΌ ΡΠΌΠ΅Π½ΡΡΠ΅Π½ΠΈΠ΅ ΡΠ΅ΠΌΠΏΠ΅ΡΠ°ΡΡΡΡ Π²ΠΎ Π²ΡΠΏΠ΅Π½ΠΈΠ²Π°ΡΠ΅Π»Π΅
- ΠΏΡΠΈΠΌΠ΅Π½Π΅Π½ΠΈΠ΅ ΡΠΌΠ΅ΡΠΈ ΠΏΠ°ΡΠ° ΠΈ Π²ΠΎΠ·Π΄ΡΡ Π°
- ΡΠΎΠΊΡΠ°ΡΠ΅Π½ΠΈΠ΅ Π²ΡΠ΅ΠΌΠ΅Π½ΠΈ ΠΏΡΠ΅Π±ΡΠ²Π°Π½ΠΈΡ Π³ΡΠ°Π½ΡΠ» Π²ΠΎ Π²ΡΠΏΠ΅Π½ΠΈΠ²Π°ΡΠ΅Π»Π΅ ΠΏΠΎΡΡΠ΅Π΄ΡΡΠ²ΠΎΠΌ ΡΠ²Π΅Π»ΠΈΡΠ΅Π½ΠΈΡ ΡΠΊΠΎΡΠΎΡΡΠΈ
Π΄ΠΎΠ·ΠΈΡΠΎΠ²Π°Π½ΠΈΡ.
ΠΠΎΡΠ»Π΅Π΄Π½ΠΈΠΉ Π²Π°ΡΠΈΠ°Π½Ρ ΡΠ²Π»ΡΠ΅ΡΡΡ Π½Π°ΠΈΠ±ΠΎΠ»Π΅Π΅ ΠΏΡΠΈΠ΅ΠΌΠ»Π΅ΠΌΡΠΌ, ΠΏΠΎΡΠΎΠΌΡ ΡΡΠΎ Π½Π΅ ΡΠΌΠ΅Π½ΡΡΠ°Π΅Ρ ΠΏΡΠΎΠΈΠ·Π²ΠΎΠ΄ΠΈΡΠ΅Π»ΡΠ½ΠΎΡΡΡ Π²ΡΠΏΠ΅Π½ΠΈΠ²Π°ΡΠ΅Π»Ρ. Π§ΡΠΎΠ±Ρ ΠΊΠΎΠ»ΠΈΡΠ΅ΡΡΠ²ΠΎ ΠΏΠΎΠ΄Π°Π²Π°Π΅ΠΌΠΎΠ³ΠΎ ΡΠ΅ΡΠ΅Π· ΡΠ½Π΅ΠΊ ΡΡΡΡΡ ΡΡΠ°Π»ΠΎ ΠΌΠ΅Π½ΡΡΠ΅ (ΠΏΡΠΈ ΠΏΠΎΠ»Π½ΠΎΠΌ Π·Π°ΠΏΠΎΠ»Π½Π΅Π½ΠΈΠΈ ΡΠ½Π΅ΠΊΠ°) ΠΏΡΠΈ ΠΌΠ°ΠΊΡΠΈΠΌΠ°Π»ΡΠ½ΡΡ ΠΎΠ±ΠΎΡΠΎΡΠ°Ρ Π½Π°Π΄Π»Π΅ΠΆΠΈΡ ΡΠ²Π΅Π»ΠΈΡΠΈΡΡ ΠΊΠΎΠ»ΠΈΡΠ΅ΡΡΠ²ΠΎ ΠΎΠ±ΠΎΡΠΎΡΠΎΠ² ΡΠ½Π΅ΠΊΠ° ΠΏΡΡΠ΅ΠΌ Π·Π°ΠΌΠ΅Π½Ρ ΡΠ΅ΠΌΠ΅Π½Π½ΠΎΠΉ ΠΏΠ΅ΡΠ΅Π΄Π°ΡΠΈ.
Β Β 11.4. Π‘ΡΡΠ΅Π½ΠΈΠ΅ Π³ΡΠ°Π½ΡΠ» ΠΏΠΎΡΠ»Π΅ ΠΏΠ΅ΡΠ²ΠΎΠ³ΠΎ Π²ΡΠΏΠ΅Π½ΠΈΠ²Π°Π½ΠΈΡ
ΠΡΠΎΡΠ΅ΡΡ ΡΡΡΠΊΠΈ ΠΏΡΠΎΠ²ΠΎΠ΄ΠΈΡΡΡ Π² ΡΡΡΠ΅ΡΡΠ²ΡΡΡΠΈΡ ΡΡΡΠΈΠ»ΠΊΠ°Ρ . ΠΠ΅ ΡΡΠ΅Π±ΡΠ΅ΡΡΡ Π΅Π΅ ΡΠΏΠ΅ΡΠΈΠ°Π»ΡΠ½Π°Ρ Π΄ΠΎΡΠ°Π±ΠΎΡΠΊΠ° Π΄Π»Ρ Π΄Π²ΠΎΠΉΠ½ΠΎΠ³ΠΎ Π²ΡΠΏΠ΅Π½ΠΈΠ²Π°Π½ΠΈΡ.
Β Β 11.5. ΠΡΠ΄Π΅ΡΠΆΠΊΠ° Π³ΡΠ°Π½ΡΠ» ΠΏΠΎΡΠ»Π΅ ΠΏΠ΅ΡΠ²ΠΎΠ³ΠΎ Π²ΡΠΏΠ΅Π½ΠΈΠ²Π°Π½ΠΈΡ
ΠΠ΅ΡΠΌΠΎΡΡΡ Π½Π° ΡΠΎ, ΡΡΠΎ Π³ΡΠ°Π½ΡΠ»Ρ ΠΏΠΎΡΠ»Π΅ ΠΏΠ΅ΡΠ²ΠΎΠ³ΠΎ Π²ΡΠΏΠ΅Π½ΠΈΠ²Π°Π½ΠΈΡ ΠΈΠΌΠ΅ΡΡ Π±ΠΎΠ»Π΅Π΅ Π²ΡΡΠΎΠΊΠΈΠΉ ΡΠ΄Π΅Π»ΡΠ½ΡΠΉ Π²Π΅Ρ, Π²ΡΠ΅ΠΌΡ Π²ΡΠ΄Π΅ΡΠΆΠΊΠΈ Π³ΡΠ°Π½ΡΠ» ΡΠΎΠΊΡΠ°ΡΠ°Π΅ΡΡΡ ΠΈ ΡΠΎΡΡΠ°Π²Π»ΡΠ΅Ρ 3-8 ΡΠ°ΡΠΎΠ². ΠΠ°ΠΊ ΠΈΠ·Π²Π΅ΡΡΠ½ΠΎ, Π²ΡΠ΅ΠΌΡ Π²ΡΠ΄Π΅ΡΠΆΠΊΠΈ Π³ΡΠ°Π½ΡΠ» ΠΌΠ΅Π½ΡΡΠ΅Π³ΠΎ Π΄ΠΈΠ°ΠΌΠ΅ΡΡΠ° ΠΌΠ΅Π½ΡΡΠ΅. Π’Π΅ΠΌΠΏΠ΅ΡΠ°ΡΡΡΡ Π²ΡΠ΄Π΅ΡΠΆΠΊΠΈ ΡΠΎΡΡΠ°Π²Π»ΡΡΡ 15-25Β°Π‘. Β Β 11.6. ΠΡΠΎΡΠΎΠ΅ Π²ΡΠΏΠ΅Π½ΠΈΠ²Π°Π½ΠΈΠ΅ ΠΡΠΎΡΠ΅ΡΡ Π²ΡΠΎΡΠΎΠ³ΠΎ Π²ΡΠΏΠ΅Π½ΠΈΠ²Π°Π½ΠΈΡ ΠΏΡΠΎΠ²ΠΎΠ΄ΠΈΡΡΡ Π°Π½Π°Π»ΠΎΠ³ΠΈΡΠ½ΠΎ ΠΏΠ΅ΡΠ²ΠΎΠΌΡ. Π‘Π»Π΅Π΄ΡΠ΅Ρ ΠΏΠΎΠ΄ΠΎΠ±ΡΠ°ΡΡ ΡΠ΅ ΠΆΠ΅ ΠΏΠ°ΡΠ°ΠΌΠ΅ΡΡΡ:
- ΡΠΊΠΎΡΠΎΡΡΡ Π΄ΠΎΠ·ΠΈΡΠΎΠ²Π°Π½ΠΈΡ
- ΡΠ΅ΠΌΠΏΠ΅ΡΠ°ΡΡΡΠ° Π²ΠΎ Π²ΡΠΏΠ΅Π½ΠΈΠ²Π°ΡΠ΅Π»Π΅
ΠΡΠ½ΠΎΠ²Π½ΡΠΌΠΈ ΠΊΡΠΈΡΠ΅ΡΠΈΡΠΌΠΈ ΠΎΡΠ΅Π½ΠΊΠΈ ΠΏΡΠ°Π²ΠΈΠ»ΡΠ½ΠΎΡΡΠΈ ΡΠ°Π±ΠΎΡΡ Π²ΡΠΏΠ΅Π½ΠΈΠ²Π°ΡΠ΅Π»Ρ ΡΠ²Π»ΡΠ΅ΡΡΡ ΠΎΠΏΡΠ΅Π΄Π΅Π»ΡΠ΅ΠΌΡΠΉ ΡΠ΄Π΅Π»ΡΠ½ΡΠΉ Π²Π΅Ρ Π³ΡΠ°Π½ΡΠ» Π½Π°ΡΡΠΏΡΡ, Π° ΡΠ°ΠΊΠΆΠ΅ ΠΎΡΡΡΡΡΡΠ²ΠΈΠ΅ ΠΏΠΎΡΠ²Π»Π΅Π½ΠΈΡ ΠΏΡΠ»ΠΈ ΠΏΠΎ Π²ΡΡ
ΠΎΠ΄Ρ ΠΈΠ· ΡΡΡΠΈΠ»ΠΊΠΈ.
Π ΡΠ»ΡΡΠ°Π΅ ΠΏΠΎΡΠ²Π»Π΅Π½ΠΈΡ ΠΏΡΠ»ΠΈ ΠΈΠ· Π³ΡΠ°Π½ΡΠ», Π½Π°Π΄Π»Π΅ΠΆΠΈΡ ΡΠΌΠ΅Π½ΡΡΠΈΡΡ ΡΠ΅ΠΌΠΏΠ΅ΡΠ°ΡΡΡΡ Π²ΡΠΏΠ΅Π½ΠΈΠ²Π°Π½ΠΈΡ (ΡΠΌΠ΅Π½ΡΡΠΈΡΡ
ΠΊΠΎΠ»ΠΈΡΠ΅ΡΡΠ²ΠΎ ΠΏΠΎΠ΄Π°Π²Π°Π΅ΠΌΠΎΠ³ΠΎ ΠΏΠ°ΡΠ° ΠΈΠ»ΠΈ ΠΎΠ±ΠΎΠ³Π°ΡΠΈΡΡ ΡΠΌΠ΅ΡΡ Π²ΠΎΠ·Π΄ΡΡ
ΠΎΠΌ) ΠΈΠ»ΠΈ ΡΠ²Π΅Π»ΠΈΡΠΈΡΡ ΡΠΊΠΎΡΠΎΡΡΡ ΠΏΡΠΎΡ
ΠΎΠΆΠ΄Π΅Π½ΠΈΡ Π³ΡΠ°Π½ΡΠ» (Π΄ΠΎΠ·ΠΈΡΠΎΠ²Π°Π½ΠΈΠ΅) ΡΠ΅ΡΠ΅Π· Π²ΡΠΏΠ΅Π½ΠΈΠ²Π°ΡΠ΅Π»Ρ ΠΏΡΡΠ΅ΠΌ ΡΠ²Π΅Π»ΠΈΡΠ΅Π½ΠΈΡ ΠΎΠ±ΠΎΡΠΎΡΠΎΠ² ΠΏΠΎΠ΄Π°ΡΡΠ΅Π³ΠΎ ΡΠ΅ΡΠ²ΡΠΊΠΎΠ²ΠΎΠ³ΠΎ ΡΠ½Π΅ΠΊΠ°.
ΠΡΠΏΠ΅Π½Π΅Π½Π½ΡΠ΅ ΠΏΠΎΠ²ΡΠΎΡΠ½ΠΎ Π³ΡΠ°Π½ΡΠ»Ρ, Π² ΡΠ²ΡΠ·ΠΈ Ρ ΠΈΡ
ΠΌΠ°Π»ΡΠΌ ΡΠ΄Π΅Π»ΡΠ½ΡΠΌ Π²Π΅ΡΠΎΠΌ, Π±ΠΎΠ»Π΅Π΅ ΡΡΠ²ΡΡΠ²ΠΈΡΠ΅Π»ΡΠ½Ρ ΠΊ
ΠΌΠ΅Ρ
Π°Π½ΠΈΡΠ΅ΡΠΊΠΈΠΌ ΠΏΠΎΠ²ΡΠ΅ΠΆΠ΄Π΅Π½ΠΈΡΠΌ Π²ΠΎ Π²ΡΠ΅ΠΌΡ ΠΈΡ
ΡΡΠ°Π½ΡΠΏΠΎΡΡΠΈΡΠΎΠ²ΠΊΠΈ. ΠΠΎΡΡΠΎΠΌΡ ΡΠ»Π΅Π΄ΡΠ΅Ρ ΡΠΌΠ΅Π½ΡΡΠΈΡΡ ΡΠΊΠΎΡΠΎΡΡΡ
ΡΡΠ°Π½ΡΠΏΠΎΡΡΠΈΡΠΎΠ²ΠΊΠΈ ΠΏΡΡΠ΅ΠΌ ΠΈΠ·ΠΌΠ΅Π½Π΅Π½ΠΈΡ ΡΠΊΠΎΡΠΎΡΡΠΈ ΡΠ°Π±ΠΎΡΡ Π²Π΅Π½ΡΠΈΠ»ΡΡΠΎΡΠ°.
Β Β 11.7. ΠΡΠ΄Π΅ΡΠΆΠΊΠ° Π³ΡΠ°Π½ΡΠ» ΠΏΠΎΡΠ»Π΅ Π²ΡΠΎΡΠΎΠ³ΠΎ Π²ΡΠΏΠ΅Π½ΠΈΠ²Π°Π½ΠΈΡ
ΠΠ· ΡΡΡΠΈΠ»ΠΊΠΈ ΡΠ΅ΡΠ΅Π· ΠΈΠ½ΠΆΠ΅ΠΊΡΠΎΡ Π³ΡΠ°Π½ΡΠ»Ρ Π½Π°ΠΏΡΠ°Π²Π»ΡΡΡΡΡ Π² ΡΡΡΠ΅ΡΡΠ²ΡΡΡΠΈΠ΅ Π±ΡΠ½ΠΊΠ΅ΡΡ, Π³Π΄Π΅ ΠΏΡΠΎΠΈΡΡ ΠΎΠ΄ΠΈΡ ΠΏΡΠΎΡΠ΅ΡΡ Π΄ΠΈΡΡΡΠ·ΠΈΠΈ Π²ΠΎΠ·Π΄ΡΡ Π° Π² ΠΎΠ±ΡΠ°Π·ΠΎΠ²Π°Π²ΡΠΈΠ΅ΡΡ ΠΌΠΈΠΊΡΠΎΠΏΠΎΡΡ. ΠΠΏΡΠΈΠΌΠ°Π»ΡΠ½ΠΎΠ΅ Π²ΡΠ΅ΠΌΡ Π²ΡΠ΄Π΅ΡΠΆΠΊΠΈ ΠΏΠΎΡΠ»Π΅ Π²ΡΠΎΡΠΎΠΉ ΡΡΡΠΏΠ΅Π½ΠΈ Π²ΡΠΏΠ΅Π½ΠΈΠ²Π°Π½ΠΈΡ ΡΠΎΡΡΠ°Π²Π»ΡΠ΅Ρ Π½Π΅ΡΠΊΠΎΠ»ΡΠΊΠΎ ΡΠ°ΡΠΎΠ² Π² Π·Π°Π²ΠΈΡΠΈΠΌΠΎΡΡΠΈ ΠΎΡ ΡΠ°Π·ΠΌΠ΅ΡΠ° Π³ΡΠ°Π½ΡΠ». Π’Π΅ΠΌΠΏΠ΅ΡΠ°ΡΡΡΠ° Π²ΡΠ΄Π΅ΡΠΆΠΊΠΈ Π΄ΠΎΠ»ΠΆΠ½Π° ΡΠΎΡΡΠ°Π²Π»ΡΡΡ, ΠΊΠ°ΠΊ ΠΈ Π²ΠΎ Π²ΡΠ΅ΠΌΡ ΠΏΠ΅ΡΠ²ΠΎΠΉ Π²ΡΠ΄Π΅ΡΠΆΠΊΠΈ, Π² ΠΏΡΠ΅Π΄Π΅Π»Π°Ρ 15-25Β°Π‘. ΠΡΠ΅ΠΌΡ Π²ΡΠ΄Π΅ΡΠΆΠΊΠΈ ΠΏΡΠΈ ΠΎΠ΄ΠΈΠ½Π°ΠΊΠΎΠ²ΠΎΠΌ ΡΠ΄Π΅Π»ΡΠ½ΠΎΠΌ Π²Π΅ΡΠ΅ Π·Π°Π²ΠΈΡΠΈΡ ΠΎΡ ΡΠ°Π·ΠΌΠ΅ΡΠ° Π³ΡΠ°Π½ΡΠ».
Β Β 11.8. ΠΡΠΎΡΠ΅ΡΡ ΡΠΎΡΠΌΠΈΡΠΎΠ²Π°Π½ΠΈΡ Π±Π»ΠΎΠΊΠΎΠ²
ΠΡΠΎΡΠ΅ΡΡ ΡΠΎΡΠΌΠΈΡΠΎΠ²Π°Π½ΠΈΡ Π±Π»ΠΎΠΊΠΎΠ² ΠΏΡΠΈ Π΄Π²ΡΠΊΡΠ°ΡΠ½ΠΎΠΌ Π²ΡΠΏΠ΅Π½ΠΈΠ²Π°Π½ΠΈΠΈ Π½Π΅ ΡΠΈΠ»ΡΠ½ΠΎ ΠΎΡΠ»ΠΈΡΠ°Π΅ΡΡΡ ΠΎΡ ΠΎΠ±ΡΡΠ½ΠΎΠ³ΠΎ
ΠΏΡΠΎΡΠ΅ΡΡΠ°. Π’Π°ΠΊΠΆΠ΅ ΡΠ»Π΅Π΄ΡΠ΅Ρ ΠΎΠ±Π΅ΡΠΏΠ΅ΡΠΈΡΡ ΠΏΡΠΎΠ΄ΡΠ²ΠΊΡ ΡΠΎΡΠΌΡ, Π½Π°ΠΏΠΎΠ»Π½Π΅Π½Π½ΠΎΠΉ Π³ΡΠ°Π½ΡΠ»Π°ΠΌΠΈ.
ΠΠ°Π²Π»Π΅Π½ΠΈΠ΅ ΠΏΠ°ΡΠ° Π²ΠΎ Π²ΡΠ΅ΠΌΡ ΡΡΠΎΠΉ ΠΎΠΏΠ΅ΡΠ°ΡΠΈΠΈ Π΄ΠΎΠ»ΠΆΠ½ΠΎ Π±ΡΡΡ Π² ΠΏΡΠ΅Π΄Π΅Π»Π°Ρ
0,1-0,2 Π°ΡΠΌΠΎΡΡΠ΅Ρ, Π° Π²ΡΠ΅ΠΌΡ ΠΏΡΠΎΠ΄ΡΠ²ΠΊΠΈ ΠΊΠ°ΠΊ ΠΌΠΎΠΆΠ½ΠΎ ΠΌΠ΅Π½ΡΡΠΈΠΌ, Π² Π³ΡΠ°Π½ΠΈΡΠ°Ρ
Π½Π΅ΡΠΊΠΎΠ»ΡΠΊΠΈΡ
ΡΠ΅ΠΊΡΠ½Π΄. Π Π°ΡΡΠ΅ΡΡ ΠΏΡΠΎΠ΄ΡΠ²ΠΊΠΈ ΠΈ Π΄Π°Π»ΡΠ½Π΅ΠΉΡΠ°Ρ ΠΏΠΎΠ΄Π°ΡΠ° ΠΏΠ°ΡΠ° Π΄ΠΎΠ»ΠΆΠ½Ρ ΠΎΠ±Π΅ΡΠΏΠ΅ΡΠΈΠ²Π°ΡΡ ΡΠ°Π²Π½ΠΎΠΌΠ΅ΡΠ½ΠΎΠ΅ Π½Π°Π³ΡΠ΅Π²Π°Π½ΠΈΠ΅ Π³ΡΠ°Π½ΡΠ» Π²ΠΎ Π²ΡΠ΅ΠΌ ΡΠ°Π±ΠΎΡΠ΅ΠΌ ΠΎΠ±ΡΠ΅ΠΌΠ΅ ΡΠΎΡΠΌΡ.
ΠΠ°Π²Π»Π΅Π½ΠΈΠ΅ ΠΏΠ°ΡΠ° Π²ΠΎ Π²ΡΠ΅ΠΌΡ ΡΠΎΡΠΌΠΎΠ²Π°Π½ΠΈΡ Π΄ΠΎΠ»ΠΆΠ½ΠΎ ΡΠΎΡΡΠ°Π²Π»ΡΡΡ 0,4-0,7 Π°ΡΠΌΠΎΡΡΠ΅Ρ Π² Π·Π°Π²ΠΈΡΠΈΠΌΠΎΡΡΠΈ ΠΎΡ ΠΊΠ°ΡΠ΅ΡΡΠ²Π° Π³ΡΠ°Π½ΡΠ» (ΡΠ΄Π΅Π»ΡΠ½ΠΎΠ³ΠΎ Π²Π΅ΡΠ° ΡΠΎΠ΄Π΅ΡΠΆΠ°ΡΠ΅Π³ΠΎΡΡ ΠΏΠΎΠ»ΠΈΠΌΠ΅ΡΠ°). ΠΡΠ΅ΠΌΡ ΡΠΎΡΠΌΠΈΡΠΎΠ²Π°Π½ΠΈΡ Ρ ΡΡΠ΅ΡΠΎΠΌ ΠΏΠΎΠ²ΡΡΠ΅Π½Π½ΠΎΠΉ ΡΡΠ²ΡΡΠ²ΠΈΡΠ΅Π»ΡΠ½ΠΎΡΡΠΈ ΠΊ ΠΌΠ΅Ρ
Π°Π½ΠΈΡΠ΅ΡΠΊΠΎΠΌΡ Π²ΠΎΠ·Π΄Π΅ΠΉΡΡΠ²ΠΈΡ Π½Π΅ Π΄ΠΎΠ»ΠΆΠ½ΠΎ Π±ΡΡΡ Π±ΠΎΠ»ΡΡΠΈΠΌ, ΠΏΠΎΡΠΎΠΌΡ ΡΡΠΎ ΡΡΠΎ ΠΏΡΠΈΠ²Π΅Π΄Π΅Ρ ΠΊ ΠΎΡΡΠΏΠ°Π½ΠΈΡ (ΠΏΠΎΡΠ²Π»Π΅Π½ΠΈΡ ΠΏΡΠ»ΠΈ) Π±Π»ΠΎΠΊΠΎΠ², Π΄Π°ΠΆΠ΅ Π²ΠΎ Π²ΡΠ΅ΠΌΡ ΡΠΎΡΠΌΠΈΡΠΎΠ²Π°Π½ΠΈΡ ΠΈ Π΄Π°Π»Π΅Π΅ Π² ΠΏΡΠΎΡΠ΅ΡΡΠ΅ ΠΎΡ
Π»Π°ΠΆΠ΄Π΅Π½ΠΈΡ.
ΠΠ±ΡΠ΅Π΅ Π²ΡΠ΅ΠΌΡ Π²ΠΎΠ·Π΄Π΅ΠΉΡΡΠ²ΠΈΡ ΠΏΠ°ΡΠ° Π΄ΠΎΠ»ΠΆΠ½ΠΎ ΡΠΎΡΡΠ°Π²Π»ΡΡΡ 15-40 ΡΠ΅ΠΊΡΠ½Π΄, Π²ΡΠ΅ΠΌΡ ΠΎΡ
Π»Π°ΠΆΠ΄Π΅Π½ΠΈΡ 5-10 ΠΌΠΈΠ½ΡΡ, Π²
Π·Π°Π²ΠΈΡΠΈΠΌΠΎΡΡΠΈ ΠΎΡ ΡΠ΅ΠΌΠΏΠ΅ΡΠ°ΡΡΡΡ ΡΠΎΡΠΌΠΎΠ²Π°Π½ΠΈΡ, Π° ΡΠ°ΠΊΠΆΠ΅ Π΄Π°Π²Π»Π΅Π½ΠΈΡ ΠΏΠ°ΡΠ°, ΠΊΠΎΠ½ΡΡΡΡΠΊΡΠΈΠΈ ΡΠΎΡΠΌΡ ΠΈ Π΅Π΅ Π³Π΅ΡΠΌΠ΅ΡΠΈΡΠ½ΠΎΡΡΠΈ.
ΠΠ°Π½Π½ΡΠ΅ Π΄ΠΎΠ»ΠΆΠ½Ρ ΠΎΠΏΡΠ΅Π΄Π΅Π»ΡΡΡΡΡ ΠΎΠΏΡΡΠ½ΡΠΌ ΠΏΡΡΠ΅ΠΌ Ρ ΡΡΠ΅ΡΠΎΠΌ ΠΊΠ°ΡΠ΅ΡΡΠ²Π° ΡΡΡΡΡ, Π° ΡΠ°ΠΊΠΆΠ΅ ΡΠ΄Π΅Π»ΡΠ½ΠΎΠ³ΠΎ Π²Π΅ΡΠ° ΠΏΠΎΡΠ»Π΅ Π²ΡΠΎΡΠΎΠ³ΠΎ Π²ΡΠΏΠ΅Π½ΠΈΠ²Π°Π½ΠΈΡ.
12. ΠΠΏΠΈΡΠ°Π½ΠΈΠ΅ ΠΈ ΠΏΠΎΡΡΠ΄ΠΎΠΊ ΡΠΊΡΠΏΠ»ΡΠ°ΡΠ°ΡΠΈΠΈ Π²ΡΠΏΠ΅Π½ΠΈΠ²Π°ΡΠ΅Π»Ρ, ΠΏΡΠ΅Π΄Π½Π°Π·Π½Π°ΡΠ΅Π½Π½ΠΎΠ³ΠΎ Π΄Π»Ρ
ΡΡΡΠΏΠ΅Π½ΡΠ°ΡΠΎΠ³ΠΎ Π²ΡΠΏΠ΅Π½ΠΈΠ²Π°Π½ΠΈΡ ΠΏΠ΅Π½ΠΎΠΏΠΎΠ»ΠΈΡΡΠΈΡΠΎΠ»Π°
Β Β Β 12.1. ΠΠΏΠΈΡΠ°Π½ΠΈΠ΅ ΠΈ ΠΏΠΎΡΡΠ΄ΠΎΠΊ ΡΠΊΡΠΏΠ»ΡΠ°ΡΠ°ΡΠΈΠΈ
ΠΡΠΏΠ΅Π½ΠΈΠ²Π°ΡΠ΅Π»Ρ ΡΠ»Π΅Π΄ΡΠ΅Ρ ΡΡΡΠ°Π½Π°Π²Π»ΠΈΠ²Π°ΡΡ Π½Π° ΡΠ²Π΅ΡΠ΄ΠΎΠΉ ΡΠΎΠ²Π½ΠΎΠΉ ΠΏΠΎΠ²Π΅ΡΡ
Π½ΠΎΡΡΠΈ ΠΈ Π²ΡΡΠ°Π²Π½ΠΈΠ²Π°ΡΡ ΠΏΠΎ Π΄Π»ΠΈΠ½Π΅ ΠΈ ΡΠΈΡΠΈΠ½Π΅ ΠΏΡΠΈ ΠΏΠΎΠΌΠΎΡΠΈ ΡΡΠΎΠ²Π½Ρ. ΠΠ΅ΡΠ²ΠΎΠΉ ΡΠ΅Ρ
Π½ΠΎΠ»ΠΎΠ³ΠΈΡΠ΅ΡΠΊΠΎΠΉ ΠΎΠΏΠ΅ΡΠ°ΡΠΈΠ΅ΠΉ ΡΠ²Π»ΡΠ΅ΡΡΡ Π²ΡΠΏΠ΅Π½ΠΈΠ²Π°Π½ΠΈΠ΅ Π³ΡΠ°Π½ΡΠ». ΠΡΠΎΡΠ΅ΡΡ Π²ΡΠΏΠ΅Π½ΠΈΠ²Π°Π½ΠΈΡ Π²ΠΎΠ·ΠΌΠΎΠΆΠ΅Π½ Π±Π»Π°Π³ΠΎΠ΄Π°ΡΡ ΠΏΠΎΡΠΎΡΠΎΡΡ, ΠΊΠΎΡΠΎΡΡΠΉ ΡΠΎΠ΄Π΅ΡΠΆΠΈΡΡΡ Π² Π³ΡΠ°Π½ΡΠ»Π°Ρ
. ΠΠΎ Π²ΡΠ΅ΠΌΡ Π²ΡΠΏΠ΅Π½ΠΈΠ²Π°Π½ΠΈΡ, ΠΏΡΠΎΠΈΠ·Π²ΠΎΠ΄ΠΈΠΌΠΎΠ³ΠΎ ΠΏΡΠΈ ΠΏΠΎΠΌΠΎΡΠΈ Π²ΠΎΠ΄ΡΠ½ΠΎΠ³ΠΎ ΠΏΠ°ΡΠ°, ΠΏΠΎΠ΄Π°Π²Π°Π΅ΠΌΠΎΠ³ΠΎ Π²ΠΎ Π²ΡΠΏΠ΅Π½ΠΈΠ²Π°ΡΠ΅Π»Ρ ΠΏΡΠΈ ΡΠ΅ΠΌΠΏΠ΅ΡΠ°ΡΡΡΠ΅ 90-100Β°Π‘ (Π΄Π°Π²Π»Π΅Π½ΠΈΠ΅ ΠΏΠ°ΡΠ° 0,1 ΠΌΠΠ°) Π² ΠΌΠΎΠ½ΠΎΠ»ΠΈΡΠ΅ ΠΏΠΎΠ»ΠΈΡΡΠΈΡΠΎΠ»Π° Π²ΠΎΠ·Π½ΠΈΠΊΠ°Π΅Ρ ΠΌΠΈΠΊΡΠΎΠΏΠΎΡΠΈΡΡΠ°Ρ ΡΡΡΡΠΊΡΡΡΠ°. ΠΠΎΠ΄ΡΠ½ΠΎΠΉ ΠΏΠ°Ρ, ΠΏΠΎΠ΄Π°Π²Π°Π΅ΠΌΡΠΉ Π²ΠΎ Π²ΡΠΏΠ΅Π½ΠΈΠ²Π°ΡΠ΅Π»Ρ, ΠΈΠ³ΡΠ°Π΅Ρ Π΄Π²ΠΎΠΉΠ½ΡΡ ΡΠΎΠ»Ρ: ΠΎΡΠ½ΠΎΠ²Π½ΡΡ β Π½Π°Π³ΡΠ΅Π²Π°Π½ΠΈΠ΅ ΠΈ Π΄ΠΎΠΏΠΎΠ»Π½ΠΈΡΠ΅Π»ΡΠ½ΡΡ β ΠΈΡΡΠΎΡΠ½ΠΈΠΊΠ° Π²ΡΠΏΠ΅Π½ΠΈΠ²Π°Π½ΠΈΡ (Π±Π»Π°Π³ΠΎΠ΄Π°ΡΡ Π²ΡΡΠΎΠΊΠΎΠΉ ΡΠΊΠΎΡΠΎΡΡΠΈ Π΄ΠΈΡΡΡΠ·ΠΈΠΈ ΡΠ΅ΡΠ΅Π· ΡΡΠ΅Π½ΠΊΠΈ ΠΌΠΈΠΊΡΠΎΠΏΠΎΡ), ΠΏΡΠΈΠ²ΠΎΠ΄ΠΈΡ ΠΊ ΠΌΠ½ΠΎΠ³ΠΎΠΊΡΠ°ΡΠ½ΠΎΠΌΡ (Π΄ΠΎ 50 ΡΠ°Π·) ΡΠ²Π΅Π»ΠΈΡΠ΅Π½ΠΈΡ ΠΎΠ±ΡΠ΅ΠΌΠ° Π³ΡΠ°Π½ΡΠ». ΠΠΎ Π²ΡΠ΅ΠΌΡ Π²ΡΠΏΠ΅Π½ΠΈΠ²Π°Π½ΠΈΡ Π³ΡΠ°Π½ΡΠ»Ρ ΠΏΠ΅ΡΠ΅ΠΌΠ΅ΡΠΈΠ²Π°ΡΡΡΡ ΠΏΡΠΈ ΠΏΠΎΠΌΠΎΡΠΈ ΠΌΠ΅Ρ
Π°Π½ΠΈΡΠ΅ΡΠΊΠΎΠΉ ΠΌΠ΅ΡΠ°Π»ΠΊΠΈ Ρ ΡΠ΅Π»ΡΡ ΠΏΡΠ΅Π΄ΠΎΡΠ²ΡΠ°ΡΠ΅Π½ΠΈΡ ΠΈΡ
ΡΠ»ΠΈΠΏΠ°Π½ΠΈΡ.
ΠΠΎΠ΄ΡΠ½ΠΎΠΉ ΠΏΠ°Ρ ΠΏΠΎΠ΄Π°Π΅ΡΡΡ Π²ΠΎ Π²ΡΠΏΠ΅Π½ΠΈΠ²Π°ΡΠ΅Π»Ρ ΠΏΡΠΈ ΠΏΠΎΠΌΠΎΡΠΈ ΡΡΡΠ±ΠΎΠΏΡΠΎΠ²ΠΎΠ΄Π° ΠΊ Π½ΠΈΠΆΠ½Π΅ΠΉ Π΅Π³ΠΎ ΡΠ°ΡΡΠΈ. ΠΠΎ Π²ΡΠΏΠ΅Π½ΠΈΠ²Π°ΡΠ΅Π»Π΅ Π³ΡΠ°Π½ΡΠ»Ρ ΠΏΠ΅ΡΠ΅ΠΌΠ΅ΡΠΈΠ²Π°ΡΡΡΡ Π²Π΅ΡΡΠΈΠΊΠ°Π»ΡΠ½ΠΎΠΉ ΠΌΠ΅ΡΠ°Π»ΠΊΠΎΠΉ, ΡΠΎΡΡΠΎΡΡΠ΅ΠΉ ΠΈΠ· ΡΠΈΡΡΠ΅ΠΌΡ Π»ΠΎΠΏΠ°ΡΡΠ΅ΠΉ, ΠΏΡΠ΅Π΄ΠΎΡΠ²ΡΠ°ΡΠ°ΡΡΠ΅ΠΉ ΡΠ»ΠΈΠΏΠ°Π½ΠΈΠ΅ Π³ΡΠ°Π½ΡΠ». Π£Π²Π΅Π»ΠΈΡΠΈΠ²Π°ΡΡΠΈΠ΅ΡΡ Π² ΠΎΠ±ΡΠ΅ΠΌΠ΅ Π³ΡΠ°Π½ΡΠ»Ρ ΠΏΠ΅ΡΠ΅ΠΌΠ΅ΡΠ°ΡΡΡΡ Π² Π²Π΅ΡΡ
Π½ΡΡ ΡΠ°ΡΡΡ Π²ΡΠΏΠ΅Π½ΠΈΠ²Π°ΡΠ΅Π»Ρ ΠΈ ΠΎΠΏΡΡΠΊΠ°ΡΡΡΡ ΡΠ΅ΡΠ΅Π· ΠΎΡΠ²Π΅ΡΡΡΠΈΠ΅ Π·Π°ΡΡΠΏΠ°Π½ΠΈΡ, ΡΠ°Π·ΠΌΠ΅ΡΠ΅Π½Π½ΠΎΠ΅ Π² Π²Π΅ΡΡ
Π½Π΅ΠΉ ΡΠ°ΡΡΠΈ ΡΡΠ΅Π½ΠΊΠΈ Π²ΡΠΏΠ΅Π½ΠΈΠ²Π°ΡΠ΅Π»Ρ.
ΠΠ· Π²ΡΠΏΠ΅Π½ΠΈΠ²Π°ΡΠ΅Π»Ρ Π³ΡΠ°Π½ΡΠ»Ρ ΠΏΠΎΠ»ΠΈΡΡΠΈΡΠΎΠ»Π° Π²ΡΠΏΠ°Π΄Π°ΡΡ Π² ΡΡΡΠΈΠ»ΠΊΡ. ΠΠΎΡΠΎΠΊ ΡΠ΅ΠΏΠ»ΠΎΠ³ΠΎ Π²ΠΎΠ·Π΄ΡΡ
Π° Π²ΡΡΡΡΠΈΠ²Π°Π΅Ρ ΠΈΡ
ΠΈ Π²ΡΠ΄ΡΠ²Π°Π΅Ρ Π² Π³ΠΎΡΠ»ΠΎΠ²ΠΈΠ½Ρ (ΠΈΠ½ΠΆΠ΅ΠΊΡΠΎΡ) ΠΏΠ½Π΅Π²ΠΌΠΎΡΡΠ°Π½ΡΠΏΠΎΡΡΠ°, ΠΊΠΎΡΠΎΡΡΠΉ Π΄ΠΎΡΡΠ°Π²Π»ΡΠ΅Ρ ΠΈΡ
Π² Π±ΡΠ½ΠΊΠ΅ΡΡ.
Π‘ΡΡΠΈΠ»ΠΊΠ° ΠΈ ΡΡΠ°Π½ΡΠΏΠΎΡΡΠ½Π°Ρ ΡΠ°ΡΡΡ ΠΏΡΠΈΠ²ΠΎΠ΄ΠΈΡΡΡ Π² Π΄Π΅ΠΉΡΡΠ²ΠΈΠ΅ ΡΠ΅ΠΏΠ»ΡΠΌ Π²ΠΎΠ·Π΄ΡΡ
ΠΎΠΌ (Π±ΠΎΠ»Π΅Π΅ 50Β°Π‘) ΠΏΡΠΈ ΠΏΠΎΠΌΠΎΡΠΈ
Π²Π΅Π½ΡΠΈΠ»ΡΡΠΎΡΠΎΠ² ΠΈ ΠΎΠ±ΠΎΠ³ΡΠ΅Π²Π°Π΅ΡΡΡ ΠΏΠ°ΡΠΎΠΌ.
Π ΡΠ΅Π»ΡΡ
Π²ΠΎΠ·ΠΌΠΎΠΆΠ½ΠΎΠ³ΠΎ ΡΠ΅Π³ΡΠ»ΠΈΡΠΎΠ²Π°Π½ΠΈΡ ΠΏΡΠΎΠΈΠ·Π²ΠΎΠ΄ΠΈΡΠ΅Π»ΡΠ½ΠΎΡΡΠΈ ΠΈ Π½Π°ΡΡΠΏΠ½ΠΎΠ³ΠΎ Π²Π΅ΡΠ° Π³ΡΠ°Π½ΡΠ», Π²ΡΠΏΠ΅Π½ΠΈΠ²Π°ΡΠ΅Π»Ρ
ΠΈΠΌΠ΅Π΅Ρ:
Π. ΠΠΎΠ·ΠΌΠΎΠΆΠ½ΠΎΡΡΡ Π΄Π²ΡΠΊΡΠ°ΡΠ½ΠΎΠ³ΠΎ Π²ΡΠΏΠ΅Π½ΠΈΠ²Π°Π½ΠΈΡ,
Π. Π Π΅Π³ΡΠ»ΠΈΡΠΎΠ²ΠΊΡ ΡΠΊΠΎΡΠΎΡΡΠΈ ΠΎΠ±ΠΎΡΠΎΡΠΎΠ² ΡΠ½Π΅ΠΊΠΎΠ²ΡΡ
Π΄ΠΎΠ·Π°ΡΠΎΡΠΎΠ².
ΠΠΏΡΠ΅Π΄Π΅Π»Π΅Π½ΠΈΠ΅ Π½Π°ΡΡΠΏΠ½ΠΎΠ³ΠΎ Π²Π΅ΡΠ° ΡΠ²Π»ΡΠ΅ΡΡΡ ΠΎΠ±ΡΠ·Π°Π½Π½ΠΎΡΡΡ ΠΎΠ±ΡΠ»ΡΠΆΠΈΠ²Π°ΡΡΠ΅Π³ΠΎ ΠΏΠ΅ΡΡΠΎΠ½Π°Π»Π°, ΠΊΠΎΡΠΎΡΡΠΉ ΠΏΡΠΎΠ²ΠΎΠ΄ΠΈΡ Π²Π½Π΅ΡΠ½ΠΈΠΉ ΠΎΡΠΌΠΎΡΡ Π²ΡΠΏΠ΅Π½Π΅Π½Π½ΡΡ
Π³ΡΠ°Π½ΡΠ». ΠΠΎΠ½ΡΡΠΎΠ»ΡΠ½ΠΎ-ΠΈΠ·ΠΌΠ΅ΡΠΈΡΠ΅Π»ΡΠ½ΠΎΠ΅ ΠΎΠ±ΠΎΡΡΠ΄ΠΎΠ²Π°Π½ΠΈΠ΅ ΡΠΎΡΡΠΎΠΈΡ ΠΈΠ· Π²Π΅Π½ΡΠΈΠ»Π΅ΠΉ Π·Π°ΠΊΡΡΠ²Π°Π½ΠΈΡ ΠΈ ΠΌΠ°Π½ΠΎΠΌΠ΅ΡΡΠ° ΠΊΠΎΠ½ΡΡΠΎΠ»ΡΠ½ΠΎΠ³ΠΎ Π΄Π°Π²Π»Π΅Π½ΠΈΡ Π²ΠΎΠ΄ΡΠ½ΠΎΠ³ΠΎ ΠΏΠ°ΡΠ° Π½Π° Π»ΠΈΠ½ΠΈΠΈ Π΄ΠΎ Π²ΡΠΏΠ΅Π½ΠΈΠ²Π°ΡΠ΅Π»Ρ, Π° ΡΠ°ΠΊΠΆΠ΅ Π²ΠΈΠ½ΡΠ°, ΡΠ΅Π³ΡΠ»ΠΈΡΡΡΡΠ΅Π³ΠΎ ΠΎΠ±ΠΎΡΠΎΡΡ ΡΠ΅ΡΠ²ΡΡΠ½ΠΎΠΉ ΠΏΠ΅ΡΠ΅Π΄Π°ΡΠΈ.
12.2. Π’ΡΠ΅Π±ΠΎΠ²Π°Π½ΠΈΡ ΠΏΠΎ Π±Π΅Π·ΠΎΠΏΠ°ΡΠ½ΠΎΡΡΠΈ ΡΡΡΠ΄Π°
- Π²ΡΠΏΠ΅Π½ΠΈΠ²Π°ΡΠ΅Π»Ρ ΠΌΠΎΠΆΠ΅Ρ ΠΎΠ±ΡΠ»ΡΠΆΠΈΠ²Π°ΡΡΡΡ ΡΠΎΠ»ΡΠΊΠΎ ΠΏΠ΅ΡΡΠΎΠ½Π°Π»ΠΎΠΌ, ΠΎΠ·Π½Π°ΠΊΠΎΠΌΠ»Π΅Π½Π½ΡΠΌ Ρ ΠΏΡΠΈΠ½ΡΠΈΠΏΠΎΠΌ Π΅Π³ΠΎ Π΄Π΅ΠΉΡΡΠ²ΠΈΡ ΠΈ ΡΡΡΡΠΎΠΉΡΡΠ²ΠΎΠΌ, Π° ΡΠ°ΠΊΠΆΠ΅ Ρ ΠΏΡΠ°Π²ΠΈΠ»Π°ΠΌΠΈ Π±Π΅Π·ΠΎΠΏΠ°ΡΠ½ΠΎΡΡΠΈ ΡΡΡΠ΄Π°
- ΠΎΠ±ΡΠ»ΡΠΆΠΈΠ²Π°ΡΡΠΈΠΉ ΠΏΠ΅ΡΡΠΎΠ½Π°Π» Π΄ΠΎΠ»ΠΆΠ΅Π½ ΡΠΎΠ±Π»ΡΠ΄Π°ΡΡ ΠΎΠ±ΡΠΈΠ΅ ΠΏΡΠ°Π²ΠΈΠ»Π° Π±Π΅Π·ΠΎΠΏΠ°ΡΠ½ΠΎΡΡΠΈ ΡΡΡΠ΄Π°, ΠΎΠ±ΡΠ·Π°ΡΠ΅Π»ΡΠ½ΡΠ΅ Π½Π° ΠΏΡΠ΅Π΄ΠΏΡΠΈΡΡΠΈΠΈ
- ΡΠ°Π±ΠΎΡΠ΅Π΅ ΠΌΠ΅ΡΡΠΎ Π΄ΠΎΠ»ΠΆΠ½ΠΎ Π±ΡΡΡ Π½Π°Π΄Π»Π΅ΠΆΠ°ΡΠΈΠΌ ΠΎΠ±ΡΠ°Π·ΠΎΠΌ ΠΎΡΠ²Π΅ΡΠ΅Π½ΠΎ ΠΈ Π±ΡΡΡ ΡΠΈΡΡΡΠΌ, Π° ΡΠ°Π±ΠΎΡΠ½ΠΈΠΊ, ΠΎΠ±ΡΠ»ΡΠΆΠΈΠ²Π°ΡΡΠΈΠΉ Π²ΡΠΏΠ΅Π½ΠΈΠ²Π°ΡΠ΅Π»Ρ, Π΄ΠΎΠ»ΠΆΠ΅Π½ ΡΠ°Π±ΠΎΡΠ°ΡΡ Π² ΠΎΠ΄Π΅ΠΆΠ΄Π΅ ΠΈ ΠΎΠ±ΡΠ²ΠΈ, Π½Π°Ρ ΠΎΠ΄ΡΡΠ΅ΠΉΡΡ Π² Π½Π°Π΄Π»Π΅ΠΆΠ°ΡΠ΅ΠΌ ΡΠΎΡΡΠΎΡΠ½ΠΈΠΈ
- ΠΏΡΠΈ ΠΌΠ°Π½ΠΈΠΏΡΠ»ΡΡΠΈΡΡ Ρ ΠΏΠ°ΡΠΎΠ²ΡΠΌ Π²Π΅Π½ΡΠΈΠ»Π΅ΠΌ ΡΡΠΊΠΈ Π΄ΠΎΠ»ΠΆΠ½Ρ Π±ΡΡΡ ΠΎΠ΄Π΅ΡΡ Π² ΡΠ°Π±ΠΎΡΠΈΠ΅ ΡΡΠΊΠ°Π²ΠΈΡΡ
ΠΠ°ΠΏΡΠ΅ΡΠ°Π΅ΡΡΡ:
- ΠΎΡΠΊΡΡΠ²Π°Π½ΠΈΠ΅ Π΄Π²Π΅ΡΠΊΠΈ Π³Π»Π°Π²Π½ΠΎΠ³ΠΎ ΡΠ±ΠΎΡΠ½ΠΈΠΊΠ° Π²ΡΠΏΠ΅Π½ΠΈΠ²Π°ΡΠ΅Π»Ρ, Π° ΡΠ°ΠΊΠΆΠ΅ Π²ΡΠΏΠΎΠ»Π½Π΅Π½ΠΈΠ΅ Π²Π½ΡΡΡΠ΅Π½Π½Π΅Π³ΠΎ ΠΎΡΠΌΠΎΡΡΠ° ΡΠ±ΠΎΡΠ½ΠΈΠΊΠ° Π²ΠΎ Π²ΡΠ΅ΠΌΡ ΡΠ°Π±ΠΎΡΡ ΠΌΠ΅ΡΠ°Π»ΠΊΠΈ
- Π²ΠΊΠ»ΡΡΠ΅Π½ΠΈΠ΅ Π΄Π²ΠΈΠ³Π°ΡΠ΅Π»Π΅ΠΉ ΠΏΡΠΈΠ²ΠΎΠ΄Π° ΠΏΡΠΈ ΠΎΡΠΊΡΡΡΡΡ Π·Π°ΡΠΈΡΠ½ΡΡ ΠΊΠΎΠΆΡΡ Π°Ρ ΡΠΈΡΡΠ΅ΠΌΡ ΡΠ΅ΠΌΠ΅Π½Π½ΠΎΠΉ ΠΏΠ΅ΡΠ΅Π΄Π°ΡΠΈ
- ΠΌΠ°Π½ΠΈΠΏΡΠ»ΠΈΡΠΎΠ²Π°Π½ΠΈΠ΅ ΡΡΠΊΠΎΠΉ Π² ΠΊΠΎΠ½ΡΡΠΎΠ»ΡΠ½ΠΎΠΌ Π»ΡΡΠΊΠ΅ ΡΠ΅ΡΠ²ΡΡΠ½ΠΎΠΉ ΠΏΠ΅ΡΠ΅Π΄Π°ΡΠΈ ΠΏΡΠΈ ΡΠ°Π±ΠΎΡΠ°ΡΡΠ΅ΠΌ ΠΎΠ±ΠΎΡΡΠ΄ΠΎΠ²Π°Π½ΠΈΠΈ.
Β Β 12.3. ΠΠΎΡΡΠ΄ΠΎΠΊ ΡΠ°Π±ΠΎΡ ΠΏΠ΅ΡΠ΅Π΄ Π½Π°ΡΠ°Π»ΠΎΠΌ ΡΠ°Π±ΠΎΡΡ Π²ΡΠΏΠ΅Π½ΠΈΠ²Π°ΡΠ΅Π»Ρ
ΠΠ΅ΡΠ΅Π΄ Π½Π°ΡΠ°Π»ΠΎΠΌ ΡΠ°Π±ΠΎΡΡ Π²ΡΠΏΠ΅Π½ΠΈΠ²Π°ΡΠ΅Π»Ρ Π½Π΅ΠΎΠ±Ρ ΠΎΠ΄ΠΈΠΌΠΎ Π²ΡΠΏΠΎΠ»Π½ΠΈΡΡ ΡΠ»Π΅Π΄ΡΡΡΠΈΠ΅ Π΄Π΅ΠΉΡΡΠ²ΠΈΡ:
- ΠΡΠΎΠ²Π΅ΡΠΈΡΡ Π³Π΅ΡΠΌΠ΅ΡΠΈΡΠ½ΠΎΡΡΡ ΡΠΈΡΡΠ΅ΠΌΡ ΠΏΠΎΠ΄Π°ΡΠΈ ΠΏΠ°ΡΠ° ΠΏΠΎ ΡΡΡΠ±ΠΎΠΏΡΠΎΠ²ΠΎΠ΄Ρ ΠΏΡΠΈ Π΄Π°Π²Π»Π΅Π½ΠΈΠΈ 0,1 ΠΠΠ°.
- Π£Π±Π΅Π΄ΠΈΡΡΡ Π² ΠΏΡΠ°Π²ΠΈΠ»ΡΠ½ΠΎΡΡΠΈ ΠΏΠΎΠ΄ΠΊΠ»ΡΡΠ΅Π½ΠΈΡ ΠΊ ΡΠ»Π΅ΠΊΡΡΠΎΡΠ΅ΡΠΈ.
- ΠΡΠΎΠ²Π΅ΡΠΈΡΡ ΡΠΎΡΡΠΎΡΠ½ΠΈΠ΅ Π·Π°ΡΠΈΡΠ½ΠΎΠ³ΠΎ ΠΊΠΎΠΆΡΡ Π° Π½Π° ΡΠ΅ΠΌΠ΅Π½Π½ΠΎΠΉ ΠΏΠ΅ΡΠ΅Π΄Π°ΡΠ΅.
- ΠΡΡΠΎΡ, ΠΏΠΎΠΏΠ°Π²ΡΠΈΠΉ Π² Π³Π»Π°Π²Π½ΡΠΉ ΡΠ±ΠΎΡΠ½ΠΈΠΊ, ΠΌΠΎΠΆΠ΅Ρ ΠΏΠΎΠ²ΡΠ΅Π΄ΠΈΡΡ ΠΌΠ΅ΡΠ°Π»ΠΊΡ ΠΈ ΡΠ΅ΡΠΊΡ.
- ΠΡΡΠΎΡ, ΠΏΠΎΠΏΠ°Π²ΡΠΈΠΉ Π² ΡΠ±ΠΎΡΠ½ΠΈΠΊ Π·Π°ΡΡΠΏΠ°Π½ΠΈΡ Π³ΡΠ°Π½ΡΠ», ΠΌΠΎΠΆΠ΅Ρ ΠΏΠΎΠ²ΡΠ΅Π΄ΠΈΡΡ ΡΠ΅ΡΠ²ΡΡΠ½ΡΡ ΠΏΠ΅ΡΠ΅Π΄Π°ΡΡ, ΠΏΠΎΠ΄Π°ΡΡΡΡ Π³ΡΠ°Π½ΡΠ»Ρ Π² Π³Π»Π°Π²Π½ΡΠΉ ΡΠ±ΠΎΡΠ½ΠΈΠΊ Π²ΡΠΏΠ΅Π½ΠΈΠ²Π°ΡΠ΅Π»Ρ.
Β Β 12.4. ΠΠ±ΡΠ»ΡΠΆΠΈΠ²Π°Π½ΠΈΠ΅ Π²ΠΎ Π²ΡΠ΅ΠΌΡ ΡΠ°Π±ΠΎΡ
- Π’ΡΠ°ΡΠ΅Π»ΡΠ½ΠΎ Π·Π°ΠΊΡΡΡΡ Π΄Π²Π΅ΡΠΊΠΈ Π½Π° Π³Π»Π°Π²Π½ΠΎΠΌ ΡΠ±ΠΎΡΠ½ΠΈΠΊΠ΅ Π²ΡΠΏΠ΅Π½ΠΈΠ²Π°ΡΠ΅Π»Ρ.
- ΠΡΡΠΎΡΠΎΠΆΠ½ΠΎ ΠΎΡΠΊΡΡΡΡ ΠΏΠ°ΡΠΎΠ²ΠΎΠΉ Π²Π΅Π½ΡΠΈΠ»Ρ ΠΈ Π½Π°Π³ΡΠ΅ΡΡ Π³Π»Π°Π²Π½ΡΠΉ ΡΠ±ΠΎΡΠ½ΠΈΠΊ Π² ΡΠ΅ΡΠ΅Π½ΠΈΠ΅ 10-15 ΠΌΠΈΠ½ΡΡ.
- ΠΠ°ΠΏΠΎΠ»Π½ΠΈΡΡ Π³Π»Π°Π²Π½ΡΠΉ ΡΠ±ΠΎΡΠ½ΠΈΠΊ Π³ΡΠ°Π½ΡΠ»Π°ΠΌΠΈ ΠΏΡΠΈ ΠΏΠΎΠΌΠΎΡΠΈ ΡΠ΅ΡΠ²ΡΡΠ½ΠΎΠΉ ΠΏΠ΅ΡΠ΅Π΄Π°ΡΠΈ. ΠΠΎ Π²ΡΠ΅ΠΌΡ ΡΠ°Π±ΠΎΡΡ ΡΠ±ΠΎΡΠ½ΠΈΠΊ (ΠΏΠ΅ΡΠ²Π°Ρ ΡΡΡΠΏΠ΅Π½Ρ Π²ΡΠΏΠ΅Π½ΠΈΠ²Π°Π½ΠΈΡ) Π΄ΠΎΠ»ΠΆΠ΅Π½ Π·Π°ΠΏΠΎΠ»Π½ΡΡΡΡΡ Π°Π²ΡΠΎΠΌΠ°ΡΠΈΡΠ΅ΡΠΊΠΈ.
3Π°. ΠΠ»Ρ Π·Π°ΠΏΠΎΠ»Π½Π΅Π½ΠΈΡ Π²ΠΎ Π²ΡΠΎΡΠΎΠΉ ΡΡΡΠΏΠ΅Π½ΠΈ Π²ΡΠΏΠ΅Π½ΠΈΠ²Π°Π½ΠΈΡ Π½Π°ΠΏΠΎΠ»Π½ΠΈΡΡ Π±ΡΠ½ΠΊΠ΅Ρ Π²ΡΠΎΡΠΎΠΉ ΡΡΡΠΏΠ΅Π½ΠΈ Π²ΡΠΏΠ΅Π½ΠΈΠ²Π°Π½ΠΈΡ
Π³ΡΠ°Π½ΡΠ»Π°ΠΌΠΈ, ΠΏΡΠΎΡΠ΅Π΄ΡΠΈΠΌΠΈ ΡΠ΅ΡΠ΅Π· ΠΏΠ΅ΡΠ²ΡΡ ΡΡΡΠΏΠ΅Π½Ρ ΠΏΡΠΈ ΠΏΠΎΠΌΠΎΡΠΈ ΡΠ΅ΡΠ²ΡΡΠ½ΠΎΠΉ ΠΏΠ΅ΡΠ΅Π΄Π°ΡΠΈ Π±ΠΎΠ»ΡΡΠ΅Π³ΠΎ Π΄ΠΈΠ°ΠΌΠ΅ΡΡΠ°. ΠΡΠ½ΠΊΠ΅Ρ Π²ΡΠΎΡΠΎΠΉ ΡΡΡΠΏΠ΅Π½ΠΈ Π·Π°ΠΏΠΎΠ»Π½ΡΠ΅Ρ ΡΠ΅Π±Ρ ΠΏΡΠΈ ΠΏΠΎΠΌΠΎΡΠΈ Π²Π΅Π½ΡΠΈΠ»ΡΡΠΎΡΠ°.
Β
- ΠΠΊΠ»ΡΡΠΈΡΡ Π΄Π²ΠΈΠ³Π°ΡΠ΅Π»Ρ ΠΌΠ΅ΡΠ°Π»ΠΊΠΈ Π² Π³Π»Π°Π²Π½ΠΎΠΌ ΡΠ±ΠΎΡΠ½ΠΈΠΊΠ΅.
- ΠΠΊΠ»ΡΡΠΈΡΡ ΡΠ΅ΡΠ²ΡΡΠ½ΡΡ ΠΏΠ΅ΡΠ΅Π΄Π°ΡΡ, ΠΏΠΎΠ΄Π°ΡΡΡΡ Π³ΡΠ°Π½ΡΠ»Ρ Π² Π³Π»Π°Π²Π½ΡΠΉ ΡΠ±ΠΎΡΠ½ΠΈΠΊ.
- ΠΠΊΠ»ΡΡΠΈΡΡ ΠΏΠ½Π΅Π²ΠΌΠΎΡΡΠ°Π½ΡΠΏΠΎΡΡ, Π° ΡΠ°ΠΊΠΆΠ΅ ΡΡΡΠΈΠ»ΠΊΡ.
- Π‘Π»Π΅Π΄ΠΈΡΡ Π·Π° ΡΠ΅ΠΊΡΡΠ΅ΠΉ ΡΠ°Π±ΠΎΡΠΎΠΉ Π²ΡΠΏΠ΅Π½ΠΈΠ²Π°ΡΠ΅Π»Ρ.
Β Β 12.5. ΠΠ±ΡΠ»ΡΠΆΠΈΠ²Π°Π½ΠΈΠ΅ ΠΏΠΎ ΠΎΠΊΠΎΠ½ΡΠ°Π½ΠΈΠΈ ΡΠ°Π±ΠΎΡ
- ΠΡΠΊΠ»ΡΡΠΈΡΡ ΡΠ΅ΡΠ²ΡΡΠ½ΡΡ ΠΏΠ΅ΡΠ΅Π΄Π°ΡΡ.
- ΠΡΠΊΠ»ΡΡΠΈΡΡ ΡΠ΅ΡΠ²ΡΡΠ½ΡΡ ΠΏΠ΅ΡΠ΅Π΄Π°ΡΡ ΠΏΠΎ ΠΎΠΏΠΎΡΠΎΠΆΠ½Π΅Π½ΠΈΠΈ Π·Π°ΡΡΠΏΠ½ΠΎΠ³ΠΎ ΡΠ±ΠΎΡΠ½ΠΈΠΊΠ°.
- ΠΠ΅ΡΠ΅ΠΊΡΡΡΡ ΠΏΠΎΠ΄Π°ΡΡ ΠΏΠ°ΡΠ° Π²ΠΎ Π²ΡΠΏΠ΅Π½ΠΈΠ²Π°ΡΠ΅Π»Ρ ΠΈ ΠΏΠΎΠ΄Π°ΡΡ ΡΠΆΠ°ΡΡΠΉ Π²ΠΎΠ·Π΄ΡΡ
Π² ΡΠ΅Π»ΡΡ
ΠΎΡ
Π»Π°ΠΆΠ΄Π΅Π½ΠΈΡ
ΡΠ±ΠΎΡΠ½ΠΈΠΊΠ°. - ΠΡΠΊΠ»ΡΡΠΈΡΡ Π΄Π²ΠΈΠ³Π°ΡΠ΅Π»Ρ ΠΏΡΠΈΠ²ΠΎΠ΄Π° ΠΌΠ΅ΡΠ°Π»ΠΊΠΈ Π² Π³Π»Π°Π²Π½ΠΎΠΌ ΡΠ±ΠΎΡΠ½ΠΈΠΊΠ΅ ΠΏΠΎ ΠΎΡ Π»Π°ΠΆΠ΄Π΅Π½ΠΈΠΈ (ΠΏΡΠΈΠΌΠ΅ΡΠ½ΠΎ ΡΠ΅ΡΠ΅Π· 60 ΠΌΠΈΠ½ΡΡ).
- ΠΡΠΊΠ»ΡΡΠΈΡΡ Π²Π΅Π½ΡΠΈΠ»ΡΡΠΎΡ, Π° ΡΠ°ΠΊΠΆΠ΅ ΡΡΡΠΈΠ»ΠΊΡ.
- ΠΡΠΊΠ»ΡΡΠΈΡΡ ΠΏΠΎΠ΄Π°ΡΡ ΡΠ»Π΅ΠΊΡΡΠΎΡΠ½Π΅ΡΠ³ΠΈΠΈ Π³Π»Π°Π²Π½ΡΠΌ ΡΡΠ±ΠΈΠ»ΡΠ½ΠΈΠΊΠΎΠΌ.
ΠΠ°ΠΆΠ΄Π°Ρ ΠΎΡΡΠ°Π½ΠΎΠ²ΠΊΠ° Π²ΡΠΏΠ΅Π½ΠΈΠ²Π°ΡΠ΅Π»Ρ ΡΡΠ΅Π±ΡΠ΅Ρ:
- ΠΡΡΠ°Π½ΠΎΠ²ΠΊΠ° ΡΠ΅ΡΠ²ΡΡΠ½ΠΎΠ³ΠΎ Π΄ΠΎΠ·Π°ΡΠΎΡΠ°.
- ΠΡΠΊΠ»ΡΡΠ΅Π½ΠΈΠ΅ ΠΏΠΎΠ΄Π°ΡΠΈ ΠΏΠ°ΡΠ°.
- ΠΡΠΊΠ»ΡΡΠ΅Π½ΠΈΠ΅ ΠΌΠ΅Ρ Π°Π½ΠΈΡΠ΅ΡΠΊΠΎΠΉ ΠΌΠ΅ΡΠ°Π»ΠΊΠΈ ΠΏΠΎ ΠΎΡ Π»Π°ΠΆΠ΄Π΅Π½ΠΈΠΈ.
- ΠΠΏΠΎΡΠΎΠΆΠ½Π΅Π½ΠΈΠ΅ Π²ΡΠΏΠ΅Π½ΠΈΠ²Π°ΡΠ΅Π»Ρ ΠΎΡ Π²ΡΠΏΠ΅Π½Π΅Π½Π½ΡΡ Π³ΡΠ°Π½ΡΠ» ΡΠ΅ΡΠ΅Π· Π΄Π²Π΅ΡΠΊΠΈ Π²ΠΎ Π²ΡΠΏΠ΅Π½ΠΈΠ²Π°ΡΠ΅Π»Π΅.
Β Β 12.6. ΠΠΎΡΡΠ΄ΠΎΠΊ Π΄Π΅ΠΉΡΡΠ²ΠΈΠΉ ΠΏΡΠΈ Π°Π²Π°ΡΠΈΠΈ (Π²ΡΠΊΠ»ΡΡΠ΅Π½ΠΈΠ΅ ΡΠ»Π΅ΠΊΡΡΠΎΡΠ½Π΅ΡΠ³ΠΈΠΈ, ΠΎΡΡΠ°Π½ΠΎΠ²ΠΊΠ°
ΠΌΠ΅ΡΠ°Π»ΠΊΠΈ)
Π’ΡΠ΅Π±ΡΠ΅Ρ Π½Π΅ΠΌΠ΅Π΄Π»Π΅Π½Π½ΠΎΠ³ΠΎ ΠΎΡΠΊΠ»ΡΡΠ΅Π½ΠΈΡ ΠΏΠΎΠ΄Π°ΡΠΈ ΠΏΠ°ΡΠ° ΠΈ Π²ΠΊΠ»ΡΡΠ΅Π½ΠΈΡ ΠΏΠΎΠ΄Π°ΡΠΈ ΡΠΆΠ°ΡΠΎΠ³ΠΎ Π²ΠΎΠ·Π΄ΡΡ
Π° Ρ ΡΠ΅Π»ΡΡ
ΠΎΡ
Π»Π°ΠΆΠ΄Π΅Π½ΠΈΡ Π³ΡΠ°Π½ΡΠ». ΠΠ΅Π²ΡΠΏΠΎΠ»Π½Π΅Π½ΠΈΠ΅ ΡΡΠΈΡ
ΠΏΡΠ°Π²ΠΈΠ» ΠΌΠΎΠΆΠ΅Ρ ΠΏΡΠΈΠ²Π΅ΡΡΠΈ ΠΊ ΡΠ»ΠΈΠΏΠ°Π½ΠΈΡ Π³ΡΠ°Π½ΡΠ», Π½Π°Ρ
ΠΎΠ΄ΡΡΠΈΡ
ΡΡ Π²Π½ΡΡΡΠΈ Π² Π°Π³Π»ΠΎΠΌΠ΅ΡΠ°Ρ, ΡΡΠΎ ΠΌΠΎΠΆΠ΅Ρ ΠΏΠΎΠ²ΡΠ΅Π΄ΠΈΡΡ ΠΎΠ±ΠΎΡΡΠ΄ΠΎΠ²Π°Π½ΠΈΠ΅ ΠΏΡΠΈΠ²ΠΎΠ΄Π° Π²ΡΠΏΠ΅Π½ΠΈΠ²Π°ΡΠ΅Π»Ρ.
ΠΠΎΠ·ΠΎΠ±Π½ΠΎΠ²Π»Π΅Π½ΠΈΠ΅ ΡΠ°Π±ΠΎΡΡ Π²ΡΠΏΠ΅Π½ΠΈΠ²Π°ΡΠ΅Π»Ρ ΠΏΠΎΡΠ»Π΅ Π°Π²Π°ΡΠΈΠΉΠ½ΠΎΠΉ ΠΎΡΡΠ°Π½ΠΎΠ²ΠΊΠΈ ΠΌΠΎΠΆΠ΅Ρ ΠΏΡΠΎΠΈΠ·Π²ΠΎΠ΄ΠΈΡΡΡΡ ΠΏΠΎΡΠ»Π΅ ΠΎΠΏΠΎΡΠΎΠΆΠ½Π΅Π½ΠΈΡ Π½Π°Ρ
ΠΎΠ΄ΡΡΠΈΡ
ΡΡ Π²Π½ΡΡΡΠΈ Π³ΡΠ°Π½ΡΠ» ΠΈ ΠΎΡΠΌΠΎΡΡΠ° Π²ΡΠΏΠ΅Π½ΠΈΠ²Π°ΡΠ΅Π»Ρ
Π’Π΅Ρ Π½ΠΎΠ»ΠΎΠ³ΠΈΡ ΠΏΡΠΎΠΈΠ·Π²ΠΎΠ΄ΡΡΠ²Π° ΠΏΠ΅Π½ΠΎΠΏΠ»Π°ΡΡΠ° (ΠΏΠ΅Π½ΠΎΠΏΠΎΠ»ΠΈΡΡΠΈΡΠΎΠ»Π°) — ΠΠΠ «ΠΠ ΠΠΈΠΊΠ ΡΡ»
ΠΠ»Π°Π²Π½Π°Ρ / Π’Π΅Ρ Π½ΠΎΠ»ΠΎΠ³ΠΈΡ ΠΏΡΠΎΠΈΠ·Π²ΠΎΠ΄ΡΡΠ²Π° ΠΏΠ΅Π½ΠΎΠΏΠ»Π°ΡΡΠ° (ΠΏΠ΅Π½ΠΎΠΏΠΎΠ»ΠΈΡΡΠΈΡΠΎΠ»Π°)Π‘ΠΎΠ΄Π΅ΡΠΆΠ°Π½ΠΈΠ΅:
- ΠΡΠ΅Π΄Π²Π°ΡΠΈΡΠ΅Π»ΡΠ½ΠΎΠ΅ Π²ΡΠΏΠ΅Π½ΠΈΠ²Π°Π½ΠΈΠ΅ Π³ΡΠ°Π½ΡΠ».
- ΠΠΎΠ½Π΄ΠΈΡΠΈΠΎΠ½ΠΈΡΠΎΠ²Π°Π½ΠΈΠ΅ ΠΏΡΠ΅Π΄Π²Π°ΡΠΈΡΠ΅Π»ΡΠ½ΠΎ Π²ΡΠΏΠ΅Π½Π΅Π½Π½ΡΡ Π³ΡΠ°Π½ΡΠ».
- Π€ΠΎΡΠΌΠΎΠ²Π°Π½ΠΈΠ΅ ΠΏΠ΅Π½ΠΎΠΏΠΎΠ»ΠΈΡΡΠΈΡΠΎΠ»ΡΠ½ΡΡ Π±Π»ΠΎΠΊΠΎΠ².
- ΠΠΎΠ½Π΄ΠΈΡΠΈΠΎΠ½ΠΈΡΠΎΠ²Π°Π½ΠΈΠ΅ ΠΏΠ΅Π½ΠΎΠΏΠΎΠ»ΠΈΡΡΠΈΡΠΎΠ»ΡΠ½ΡΡ Π±Π»ΠΎΠΊΠΎΠ².
- Π Π°Π·ΡΠ΅Π·Π°Π½ΠΈΠ΅ ΠΏΠ΅Π½ΠΎΠΏΠΎΠ»ΠΈΡΡΠΈΡΠΎΠ»ΡΠ½ΡΡ Π±Π»ΠΎΠΊΠΎΠ² Π½Π° ΠΏΠ»ΠΈΡΡ.
- ΠΡΠΏΠΎΠ»ΡΠ·ΠΎΠ²Π°Π½ΠΈΠ΅ ΠΏΠ΅Π½ΠΎΠΏΠΎΠ»ΠΈΡΡΠΈΡΠΎΠ»ΡΠ½ΡΡ ΠΎΡΡ ΠΎΠ΄ΠΎΠ².
1. ΠΠ ΠΠΠΠΠ ΠΠ’ΠΠΠ¬ΠΠΠ ΠΠ‘ΠΠΠΠΠΠΠΠΠ
1.1. ΠΡΠ°ΡΠΊΠ°Ρ Ρ Π°ΡΠ°ΠΊΡΠ΅ΡΠΈΡΡΠΈΠΊΠ° ΡΡΡΡΡ
Π ΠΊΠ°ΡΠ΅ΡΡΠ²Π΅ ΡΡΡΡΡ ΠΈΡΠΏΠΎΠ»ΡΠ·ΡΠ΅ΡΡΡ Π²ΡΠΏΠ΅Π½ΠΈΠ²Π°Π΅ΠΌΡΠΉ ΡΠ°ΠΌΠΎΠ·Π°ΡΡΡ Π°ΡΡΠΈΠΉ ΠΏΠΎΠ»ΠΈΡΡΠΈΡΠΎΠ», ΡΠΎΠ΄Π΅ΡΠΆΠ°ΡΠΈΠΉ 5-6% ΡΠΌΠ΅ΡΠΈ ΠΏΠ΅Π½ΡΠ°Π½Π° ΠΈ ΠΈΠ·ΠΎΠΏΠ΅Π½ΡΠ°Π½Π°, ΡΠ²Π»ΡΡΡΠ΅ΠΉΡΡ Π²ΡΠΏΠ΅Π½ΠΈΠ²Π°ΡΡΠΈΠΌ ΡΠ°ΠΊΡΠΎΡΠΎΠΌ. ΠΡΠ° ΡΠΌΠ΅ΡΡ ΡΠΎΠ΄Π΅ΡΠΆΠΈΡΡΡ Π² Π³ΡΠ°Π½ΡΠ»Π°Ρ ΠΏΠΎΠ»ΠΈΡΡΠΈΡΠΎΠ»Π° Π² ΡΠ°ΡΡΠ²ΠΎΡΠ΅Π½Π½ΠΎΠΌ Π²ΠΈΠ΄Π΅.
Π‘ΡΡΡΠ΅ ΠΈΠΌΠ΅Π΅Ρ Π²ΠΈΠ΄ Π³ΡΠ°Π½ΡΠ», ΠΏΠΎΠ»ΡΡΠ°Π΅ΠΌΡΡ ΠΏΡΡΠ΅ΠΌ ΡΡΡΠΏΠ΅Π½Π·ΠΈΠΎΠ½Π½ΠΎΠΉ ΠΏΠΎΠ»ΠΈΠΌΠ΅ΡΠΈΠ·Π°ΡΠΈΠΈ ΡΡΠΈΡΠΎΠ»Π°. ΠΠ½ΠΎ ΡΠΎΠ΄Π΅ΡΠΆΠΈΡ Π²Π΅ΡΠ΅ΡΡΠ²ΠΎ, ΡΠ½ΠΈΠΆΠ°ΡΡΠ΅Π΅ Π³ΠΎΡΡΡΠ΅ΡΡΡ -Π°Π½ΡΠΈΠΏΠΈΡΠ΅Π½.
ΠΠΎΡΠ»Π΅ ΠΏΠΎΠ΄ΠΎΠ³ΡΠ΅Π²Π° Π΄ΠΎ ΡΠ΅ΠΌΠΏΠ΅ΡΠ°ΡΡΡΡ 90-100Β°Π‘, ΠΏΠΎΠ΄ Π΄Π΅ΠΉΡΡΠ²ΠΈΠ΅ΠΌ ΡΠ»Π΅ΡΡΡΠΈΠ²Π°ΡΡΠ΅Π³ΠΎΡΡ ΠΏΠ΅Π½ΡΠ°Π½Π° Π³ΡΠ°Π½ΡΠ»Ρ ΡΠ²Π΅Π»ΠΈΡΠΈΠ²Π°ΡΡ ΡΠ²ΠΎΠΉ ΠΎΠ±ΡΠ΅ΠΌ (ΠΏΡΠΎΡΠ΅ΡΡ Π²ΡΠΏΠ΅Π½ΠΈΠ²Π°Π½ΠΈΡ) ΠΏΡΠΈΠΌΠ΅ΡΠ½ΠΎ Π² 30-65 ΡΠ°Π·. Π ΠΏΡΠΎΠΌΡΡΠ»Π΅Π½Π½ΠΎΠΉ ΠΏΡΠ°ΠΊΡΠΈΠΊΠ΅ Π΄Π»Ρ Π²ΡΠΏΠ΅Π½ΠΈΠ²Π°Π½ΠΈΡ ΠΏΠΎΠ»ΠΈΡΡΠΈΡΠΎΠ»Π° ΠΈΡΠΏΠΎΠ»ΡΠ·ΡΠ΅ΡΡΡ Π²ΠΎΠ΄ΡΠ½ΠΎΠΉ ΠΏΠ°Ρ, ΠΊΠΎΡΠΎΡΡΠΉ ΠΏΡΠΎΠ½ΠΈΠΊΠ°Π΅Ρ ΡΠ°ΠΊΠΆΠ΅ Π²Π½ΡΡΡΡ Π³ΡΠ°Π½ΡΠ» ΠΈ ΡΠΏΠΎΡΠΎΠ±ΡΡΠ²ΡΠ΅Ρ Π΄Π΅ΠΉΡΡΠ²ΠΈΡ ΠΏΠ΅Π½ΡΠ°Π½Π°.
ΠΠ΅ΠΆΠ΄ΡΠ½Π°ΡΠΎΠ΄Π½ΠΎΠ΅ ΠΎΠ±ΠΎΠ·Π½Π°ΡΠ΅Π½ΠΈΠ΅ Π²ΡΠΏΠ΅Π½ΠΈΠ²Π°Π΅ΠΌΠΎΠ³ΠΎ ΠΏΠΎΠ»ΠΈΡΡΠΈΡΠΎΠ»Π°: EPS ΡΠ°ΠΌΠΎΠ·Π°ΡΡΡ Π°ΡΡΠΈΠΉ FS.
Π₯ΡΠ°Π½Π΅Π½ΠΈΠ΅:
Π₯ΡΠ°Π½ΠΈΡΡ ΠΈΡΠΊΠ»ΡΡΠΈΡΠ΅Π»ΡΠ½ΠΎ Π² Π·Π°Π²ΠΎΠ΄ΡΠΊΠΎΠΉ, ΠΏΠ»ΠΎΡΠ½ΠΎ Π·Π°ΠΊΡΡΡΠΎΠΉ ΡΠ°ΡΠ΅ ΠΈΠ»ΠΈ ΠΊΠΎΠ½ΡΠ΅ΠΉΠ½Π΅ΡΠ°Ρ , ΡΡΡΠ°Π½ΠΎΠ²Π»Π΅Π½Π½ΡΡ Π² ΠΏΡΠΎΠ²Π΅ΡΡΠΈΠ²Π°Π΅ΠΌΡΡ ΠΏΠΎΠΌΠ΅ΡΠ΅Π½ΠΈΡΡ ΠΈΠ»ΠΈ ΠΏΠΎΠ΄ Π½Π°Π²Π΅ΡΠΎΠΌ, Π΄Π°Π»Π΅ΠΊΠΎ ΠΎΡ ΠΈΡΡΠΎΡΠ½ΠΈΠΊΠΎΠ² ΡΠ΅ΠΏΠ»Π° ΠΈ ΠΎΠ³Π½Ρ. Π Π΅ΠΊΠΎΠΌΠ΅Π½Π΄ΡΠ΅ΡΡΡ Ρ ΡΠ°Π½ΠΈΡΡ ΡΡΡΡΠ΅ ΠΏΡΠΈ ΡΠ΅ΠΌΠΏΠ΅ΡΠ°ΡΡΡΠ΅, Π½Π΅ ΠΏΡΠ΅Π²ΡΡΠ°ΡΡΠ΅ΠΉ 20Β°Π‘.
ΠΡΠΎΠ΄ΡΠΊΡ, Ρ ΡΠ°Π½ΠΈΠΌΡΠΉ ΠΏΡΠΈ ΡΠ΅ΠΊΠΎΠΌΠ΅Π½Π΄ΡΠ΅ΠΌΠΎΠΉ ΡΠ΅ΠΌΠΏΠ΅ΡΠ°ΡΡΡΠ΅, ΡΠ»Π΅Π΄ΡΠ΅Ρ ΠΈΡΠΏΠΎΠ»ΡΠ·ΠΎΠ²Π°ΡΡ Π½Π΅ ΠΏΠΎΠ·Π΄Π½Π΅Π΅ 3-6 ΠΌΠ΅ΡΡΡΠ΅Π² Ρ Π΄Π°ΡΡ ΠΈΡΡΠ»Π΅Π΄ΠΎΠ²Π°Π½ΠΈΡ ΠΏΡΠΎΠ΄ΡΠΊΡΠ°, ΡΠΊΠ°Π·Π°Π½Π½ΠΎΠΉ Π² ΡΠ΅ΡΡΠΈΡΠΈΠΊΠ°ΡΠ΅ ΠΊΠ°ΡΠ΅ΡΡΠ²Π°. ΠΡΠΎΠ΄ΡΠΊΡ ΠΈΠ· ΡΠ°ΡΡΠΈΡΠ½ΠΎ ΠΎΠΏΠΎΡΠΎΠΆΠ½Π΅Π½Π½ΠΎΠΉ ΠΈΠ»ΠΈ ΠΏΠΎΠ²ΡΠ΅ΠΆΠ΄Π΅Π½Π½ΠΎΠΉ ΡΠ°ΡΡ ΡΠ»Π΅Π΄ΡΠ΅Ρ ΠΈΡΠΏΠΎΠ»ΡΠ·ΠΎΠ²Π°ΡΡ Π½Π΅ΠΌΠ΅Π΄Π»Π΅Π½Π½ΠΎ.
Π ΠΏΡΠΎΠΈΠ·Π²ΠΎΠ΄ΡΡΠ²Π΅Π½Π½ΡΡ ΠΏΠΎΠΌΠ΅ΡΠ΅Π½ΠΈΡΡ ΠΌΠΎΠΆΠ½ΠΎ Ρ ΡΠ°Π½ΠΈΡΡ ΡΡΡΡΠ΅ Π² ΠΊΠΎΠ»ΠΈΡΠ΅ΡΡΠ²Π΅, Π½Π΅ ΠΏΡΠ΅Π²ΡΡΠ°ΡΡΠ΅ΠΌ Π΅Π³ΠΎ ΡΡΠ΅Π΄Π½Π΅ΡΡΡΠΎΡΠ½ΡΠΉ ΡΠ°ΡΡ ΠΎΠ΄.
1.2. ΠΠ΅ΡΠ΅ΡΠ°Π±ΠΎΡΠΊΠ° Π²ΡΠΏΠ΅Π½ΠΈΠ²Π°Π΅ΠΌΠΎΠ³ΠΎ ΠΏΠΎΠ»ΠΈΡΡΠΈΡΠΎΠ»Π° .
ΠΠΊΠΎΠ½ΡΠ°ΡΠ΅Π»ΡΠ½Π°Ρ ΠΏΠ»ΠΎΡΠ½ΠΎΡΡΡ Π³ΠΎΡΠΎΠ²ΠΎΠ³ΠΎ ΠΏΡΠΎΠ΄ΡΠΊΡΠ° ΠΎΠΏΡΠ΅Π΄Π΅Π»Π΅Π½Π° ΡΠΆΠ΅ Π½Π° ΡΡΠ°ΠΏΠ΅ ΠΏΡΠ΅Π΄Π²Π°ΡΠΈΡΠ΅Π»ΡΠ½ΠΎΠ³ΠΎ Π²ΡΠΏΠ΅Π½ΠΈΠ²Π°Π½ΠΈΡ.
ΠΠ°ΠΆΠ½ΡΠΌ ΠΏΠΎΠΊΠ°Π·Π°ΡΠ΅Π»Π΅ΠΌ ΡΠ²Π»ΡΠ΅ΡΡΡ ΠΊΠΎΠ½ΡΡΠΎΠ»Ρ Π΄Π°Π²Π»Π΅Π½ΠΈΡ ΠΏΡΠΈ ΠΏΡΠΎΡΠ΅ΡΡΠ΅ Π²ΡΠΏΠ΅Π½ΠΈΠ²Π°Π½ΠΈΡ, Π΄Π»Ρ Π½Π΅ΠΏΡΠ΅ΡΡΠ²Π½ΡΡ ΠΏΡΠ΅Π΄Π²ΡΠΏΠ΅Π½ΠΈΠ²Π°ΡΠ΅Π»Π΅ΠΉ 0,015-0,03 ΠΠΠ°, Π΄Π»Ρ ΡΠΈΠΊΠ»ΠΈΡΠ΅ΡΠΊΠΈΡ 0,015-0,02 ΠΠΠ°.
Β
ΠΠΎ Π²ΡΠΏΠ΅Π½ΠΈΠ²Π°ΡΠ΅Π»Π΅ Π΄Π²Π° ΡΠΏΠΎΡΠΎΠ±Π° ΠΈΠ·ΠΌΠ΅Π½Π΅Π½ΠΈΡ ΠΌΠ½ΠΈΠΌΠΎΠΉ ΠΏΠ»ΠΎΡΠ½ΠΎΡΡΠΈ ΠΏΡΠΎΠ΄ΡΠΊΡΠ°:
- ΠΏΡΡΠ΅ΠΌ ΠΈΠ·ΠΌΠ΅Π½Π΅Π½ΠΈΡ ΠΊΠΎΠ»ΠΈΡΠ΅ΡΡΠ²Π° ΠΏΠΎΠ΄Π°Π²Π°Π΅ΠΌΠΎΠ³ΠΎ ΡΡΡΡΡ;
- ΠΏΡΡΠ΅ΠΌ ΠΈΠ·ΠΌΠ΅Π½Π΅Π½ΠΈΡ ΡΡΠΎΠ²Π½Ρ Π²ΡΠΏΠ΅Π½ΠΈΠ²Π°Π΅ΠΌΠΎΠ³ΠΎ ΠΌΠ°ΡΠ΅ΡΠΈΠ°Π»Π° Π² ΡΠ°Π±ΠΎΡΠ΅ΠΉ ΠΊΠ°ΠΌΠ΅ΡΠ΅;
ΠΠ΅ΡΠ²ΡΠΉ ΠΈ Π²ΡΠΎΡΠΎΠΉ ΡΠΏΠΎΡΠΎΠ± ΠΎΠΊΠ°Π·ΡΠ²Π°ΡΡ Π²Π»ΠΈΡΠ½ΠΈΠ΅ Π½Π° Π²ΡΠ΅ΠΌΡ Π½Π°Ρ ΠΎΠΆΠ΄Π΅Π½ΠΈΡ Π²ΡΠΏΠ΅Π½ΠΈΠ²Π°Π΅ΠΌΠΎΠ³ΠΎ ΠΌΠ°ΡΠ΅ΡΠΈΠ°Π»Π° Π² ΡΠ°Π±ΠΎΡΠ΅ΠΉ ΠΊΠ°ΠΌΠ΅ΡΠ΅. Π’ΡΠ΅ΡΠΈΠΉ ΡΠΏΠΎΡΠΎΠ± Π²Π»ΠΈΡΠ΅Ρ Π½Π° ΡΠ΅ΠΌΠΏΠ΅ΡΠ°ΡΡΡΡ Π² ΠΊΠ°ΠΌΠ΅ΡΠ΅.
ΠΠ»ΠΈΡΠ½ΠΈΠ΅ Π²ΡΠ΅ΠΌΠ΅Π½ΠΈ Π½Π°Ρ ΠΎΠΆΠ΄Π΅Π½ΠΈΡ ΡΡΡΡΡ Π²ΠΎ Π²ΡΠΏΠ΅Π½ΠΈΠ²Π°ΡΠ΅Π»Π΅ Π½Π° ΠΌΠ½ΠΈΠΌΡΡ ΠΏΠ»ΠΎΡΠ½ΠΎΡΡΡ ΠΏΡΠΎΠ΄ΡΠΊΡΠ° ΠΏΡΠ΅Π΄ΡΡΠ°Π²Π»Π΅Π½ΠΎ Π½Π° ΡΠΈΡ.1.2.
ΠΡΠ»ΠΈ Π²ΡΠ΅ΠΌΡ Π½Π°Ρ ΠΎΠΆΠ΄Π΅Π½ΠΈΡ ΡΡΡΡΡ Π²ΠΎ Π²ΡΠΏΠ΅Π½ΠΈΠ²Π°ΡΠ΅Π»Π΅ ΡΠ»ΠΈΡΠΊΠΎΠΌ ΠΏΡΠΎΠ΄ΠΎΠ»ΠΆΠΈΡΠ΅Π»ΡΠ½ΠΎ, ΡΠΎ Π³ΡΠ°Π½ΡΠ»Ρ Π½Π°ΡΠΈΠ½Π°ΡΡ ΡΡΠ°ΠΆΠΈΠ²Π°ΡΡΡΡ ΠΈ ΠΏΠ»ΠΎΡΠ½ΠΎΡΡΡ ΡΠ°ΡΡΠ΅Ρ; ΠΏΡΠΈ ΡΠ»ΠΈΡΠΊΠΎΠΌ Π²ΡΡΠΎΠΊΠΎΠΉ ΡΠ΅ΠΌΠΏΠ΅ΡΠ°ΡΡΡΠ΅ Π²ΡΠΏΠ΅Π½Π΅Π½Π½ΡΠ΅ Π³ΡΠ°Π½ΡΠ»Ρ ΠΌΠΎΠ³ΡΡ ΠΎΠ±ΡΠ°Π·ΠΎΠ²Π°ΡΡ ΠΊΠΎΠΌΠΊΠΈ. ΠΠ±Π° ΡΡΠΈ ΡΠ²Π»Π΅Π½ΠΈΡ ΠΌΠΎΠ³ΡΡ ΠΏΡΠΎΠΈΡΡ ΠΎΠ΄ΠΈΡΡ ΠΎΠ΄Π½ΠΎΠ²ΡΠ΅ΠΌΠ΅Π½Π½ΠΎ. Π ΠΎΠΊΠ°Π·ΡΠ²Π°ΡΡ Π½Π΅ΠΏΠΎΡΡΠ΅Π΄ΡΡΠ²Π΅Π½Π½ΠΎΠ΅ Π²Π»ΠΈΡΠ½ΠΈΠ΅ Π½Π° ΠΊΠ°ΡΠ΅ΡΡΠ²ΠΎ ΠΊΠΎΠ½Π΅ΡΠ½ΠΎΠ³ΠΎ ΠΏΡΠΎΠ΄ΡΠΊΡΠ°.
ΠΠ»ΠΎΡΠ½ΠΎΡΡΡ
Β
ΠΡΠΎΠ΄ΠΎΠ»ΠΆΠΈΡΠ΅Π»ΡΠ½ΠΎΡΡΡ ΠΏΡΠ΅Π΄Π²Π°ΡΠΈΡΠ΅Π»ΡΠ½ΠΎΠ³ΠΎ Π²ΡΠΏΠ΅Π½ΠΈΠ²Π°Π½ΠΈΡ
Π ΠΈΡ.1.2. ΠΠ°Π²ΠΈΡΠΈΠΌΠΎΡΡΡ ΠΌΠ΅ΠΆΠ΄Ρ ΠΌΠ½ΠΈΠΌΠΎΠΉ ΠΏΠ»ΠΎΡΠ½ΠΎΡΡΡΡ ΠΈ ΠΏΡΠΎΠ΄ΠΎΠ»ΠΆΠΈΡΠ΅Π»ΡΠ½ΠΎΡΡΡΡ Π²ΡΠΏΠ΅Π½ΠΈΠ²Π°Π½ΠΈΡ
Π‘ ΡΠ΅Π»ΡΡ ΠΏΠΎΠ»ΡΡΠ΅Π½ΠΈΡ Π½ΠΈΠ·ΠΊΠΎΠΉ ΠΏΠ»ΠΎΡΠ½ΠΎΡΡΠΈ (< 12 ΠΊΠ³/ΠΌ3) ΠΏΡΠΈΠΌΠ΅Π½ΡΡΡ Π΄Π²ΡΡ ΡΡΡΠΏΠ΅Π½ΡΠ°ΡΠΎΠ΅ Π²ΡΠΏΠ΅Π½ΠΈΠ²Π°Π½ΠΈΠ΅. ΠΠ²ΡΡ ΡΡΡΠΏΠ΅Π½ΡΠ°ΡΠΎΠ΅ Π²ΡΠΏΠ΅Π½ΠΈΠ²Π°Π½ΠΈΠ΅ ΠΏΡΠΎΠ²ΠΎΠ΄ΡΡ Ρ ΠΏΠΎΠΌΠΎΡΡΡ ΡΠΎΠ³ΠΎ ΠΆΠ΅ ΡΠ°ΠΌΠΎΠ³ΠΎ ΠΎΠ±ΠΎΡΡΠ΄ΠΎΠ²Π°Π½ΠΈΡ, ΠΊΠΎΡΠΎΡΠΎΠ΅ ΠΈΡΠΏΠΎΠ»ΡΠ·ΡΠ΅ΡΡΡ Π΄Π»Ρ ΠΎΠ΄Π½ΠΎΡΡΡΠΏΠ΅Π½ΡΠ°ΡΠΎΠ³ΠΎ Π²ΡΠΏΠ΅Π½ΠΈΠ²Π°Π½ΠΈΡ, Ρ ΠΏΠΎΠ΄Π°ΡΠ΅ΠΉ ΠΏΡΠ΅Π΄Π²Π°ΡΠΈΡΠ΅Π»ΡΠ½ΠΎ Π²ΡΠΏΠ΅Π½Π΅Π½Π½ΠΎΠ³ΠΎ ΡΡΡΡΡ ΡΠ΅ΡΠ΅Π· ΡΠΈΡΡΠ΅ΠΌΡ Π²ΡΠΎΡΠΈΡΠ½ΠΎΠ³ΠΎ Π²ΡΠΏΠ΅Π½ΠΈΠ²Π°Π½ΠΈΡ.
Π‘ ΡΠ΅Π»ΡΡ Π΄ΠΎΡΡΠΈΠΆΠ΅Π½ΠΈΡ ΠΎΠΏΡΠΈΠΌΠ°Π»ΡΠ½ΡΡ ΡΠ΅Π·ΡΠ»ΡΡΠ°ΡΠΎΠ² Π²ΡΠΏΠ΅Π½ΠΈΠ²Π°Π½ΠΈΡ Π³ΡΠ°Π½ΡΠ»Ρ ΠΏΠ΅ΡΠ΅Π΄ Π²ΡΠΏΠ΅Π½ΠΈΠ²Π°Π½ΠΈΠ΅ΠΌ Π²ΡΠΎΡΠΎΠΉ ΡΡΡΠΏΠ΅Π½ΠΈ Π΄ΠΎΠ»ΠΆΠ½Ρ Π±ΡΡΡ Π½Π°ΡΡΡΠ΅Π½Ρ Π²ΠΎΠ·Π΄ΡΡ ΠΎΠΌ (ΠΏΡΠΎΡΠ΅ΡΡ ΠΊΠΎΠ½Π΄ΠΈΡΠΈΠΎΠ½ΠΈΡΠΎΠ²Π°Π½ΠΈΡ).
ΠΡΠ΅Π΄Π²Π°ΡΠΈΡΠ΅Π»ΡΠ½ΠΎ Π²ΡΠΏΠ΅Π½Π΅Π½Π½ΡΠ΅ Π³ΡΠ°Π½ΡΠ»Ρ ΠΏΠΎΡΡΡΠΏΠ°ΡΡ Π² ΡΡΡΠΈΠ»ΠΊΡ Ρ ΠΊΠΈΠΏΡΡΠΈΠΌ ΡΠ»ΠΎΠ΅ΠΌ, Π² ΠΊΠΎΡΠΎΡΠΎΠΉ ΡΠ΅ΠΏΠ»ΡΠΉ Π²ΠΎΠ·Π΄ΡΡ (ΡΠ΅ΠΌΠΏ. ΠΏΡΠΈΠΌΠ΅ΡΠ½ΠΎ 30-40Β°Π‘) ΠΏΡΠΎΡ ΠΎΠ΄ΠΈΡ ΡΠ΅ΡΠ΅Π· ΠΏΠ΅ΡΡΠΎΡΠΈΡΠΎΠ²Π°Π½Π½ΠΎΠ΅ Π΄Π½ΠΈΡΠ΅ ΡΡΡΠΈΠ»ΠΊΠΈ, ΡΡΡΠΈΡ ΠΈ ΠΏΡΠΎΠ΄Π²ΠΈΠ³Π°Π΅Ρ Π³ΡΠ°Π½ΡΠ»Ρ Π² Π½Π°ΠΏΡΠ°Π²Π»Π΅Π½ΠΈΠΈ Π²ΡΠ³ΡΡΠ·ΠΎΡΠ½ΠΎΠ³ΠΎ Π²Π΅Π½ΡΠΈΠ»ΡΡΠΎΡΠ°.
ΠΠΎΠ·Π΄ΡΡΠ½Π°Ρ ΡΡΡΡΡ Π΄ΠΎΠ»ΠΆΠ½Π° ΡΠ°ΡΠΏΡΠ΅Π΄Π΅Π»ΡΡΡΡΡ ΡΠ°ΠΊΠΈΠΌ ΠΎΠ±ΡΠ°Π·ΠΎΠΌ, ΡΡΠΎΠ±Ρ ΠΏΡΠΎΡΠ΅ΡΡ ΡΡΡΠΊΠΈ ΠΈ ΠΏΠ΅ΡΠ΅ΠΌΠ΅ΡΠ΅Π½ΠΈΡ Π³ΡΠ°Π½ΡΠ» ΠΏΡΠΎΡΠ΅ΠΊΠ°Π» ΡΠ°Π²Π½ΠΎΠΌΠ΅ΡΠ½ΠΎ ΠΏΠΎ Π²ΡΠ΅ΠΉ Π΄Π»ΠΈΠ½Π΅ ΡΡΡΠΈΠ»ΠΊΠΈ (ΡΠ΅Π³ΡΠ»ΠΈΡΠΎΠ²ΠΊΠ° ΠΎΡΡΡΠ΅ΡΡΠ²Π»ΡΠ΅ΡΡΡ Ρ ΠΏΠΎΠΌΠΎΡΡΡ Π·Π°ΡΠ»ΠΎΠ½ΠΎΠΊ Π² Π²ΠΎΠ·Π΄ΡΡΠ½ΡΡ ΠΊΠ°ΠΌΠ΅ΡΠ°Ρ ΡΡΡΠΈΠ»ΠΊΠΈ).
ΠΠ΄Π½ΠΈΠΌ ΠΈΠ· ΡΡΠ΅Π·Π²ΡΡΠ°ΠΉΠ½ΠΎ Π²Π°ΠΆΠ½ΡΡ ΡΠ°ΠΊΡΠΎΡΠΎΠ², ΠΎΠΊΠ°Π·ΡΠ²Π°ΡΡΠΈΡ Π²Π»ΠΈΡΠ½ΠΈΠ΅ Π½Π° Π²ΡΠΏΠ΅Π½ΠΈΠ²Π°Π½ΠΈΠ΅ ΠΏΠΎΠ»ΠΈΡΡΠΈΡΠΎΠ»Π°, ΡΠ²Π»ΡΠ΅ΡΡΡ ΠΏΡΠΎΠ΄ΠΎΠ»ΠΆΠΈΡΠ΅Π»ΡΠ½ΠΎΡΡΡ Ρ ΡΠ°Π½Π΅Π½ΠΈΡ ΡΡΡΡΡ. Π§Π΅ΠΌ ΡΡΠ°ΡΡΠ΅ ΡΡΡΡΠ΅, ΡΠ΅ΠΌ ΠΏΡΠΎΠ΄ΠΎΠ»ΠΆΠΈΡΠ΅Π»ΡΠ½Π΅Π΅ Π²ΡΠΏΠ΅Π½ΠΈΠ²Π°Π½ΠΈΠ΅ ΠΈ ΡΠ΅ΠΌ ΡΡΡΠ΄Π½Π΅Π΅ Π΄ΠΎΡΡΠΈΡΡ ΡΡΠ΅Π±ΡΠ΅ΠΌΠΎΠΉ ΠΌΠ½ΠΈΠΌΠΎΠΉ ΠΏΠ»ΠΎΡΠ½ΠΎΡΡΠΈ Π²ΡΠΏΠ΅Π½Π΅Π½Π½ΡΡ Π³ΡΠ°Π½ΡΠ». ΠΠΎΡΡΠΎΠΌΡ ΡΡΠΎΠΊ Ρ ΡΠ°Π½Π΅Π½ΠΈΡ ΡΡΡΡΡ Π² Π³Π΅ΡΠΌΠ΅ΡΠΈΡΠ½ΠΎΠΉ ΡΠΏΠ°ΠΊΠΎΠ²ΠΊΠ΅ ΠΎΠ³ΡΠ°Π½ΠΈΡΠ΅Π½ Π΄ΠΎ ΡΠ΅ΡΡΠΈ ΠΌΠ΅ΡΡΡΠ΅Π².
1.3. Π’Π΅Ρ Π½ΠΈΡΠ΅ΡΠΊΠΎΠ΅ ΠΎΡΠ½Π°ΡΠ΅Π½ΠΈΠ΅ ΡΠ·Π»Π° ΠΏΡΠ΅Π΄Π²Π°ΡΠΈΡΠ΅Π»ΡΠ½ΠΎΠ³ΠΎ Π²ΡΠΏΠ΅Π½ΠΈΠ²Π°Π½ΠΈΡ
a) Π²ΡΠΏΠ΅Π½ΠΈΠ²Π°ΡΠ΅Π»Ρ ΠΠ-03
b) ΡΠΈΡΡΠ΅ΠΌΠ° Π²ΡΠΎΡΠΈΡΠ½ΠΎΠ³ΠΎ Π²ΡΠΏΠ΅Π½ΠΈΠ²Π°Π½ΠΈΡ Π‘ΠΠ-1
c) ΠΏΠΎΡΠΎΡΠ½Π°Ρ ΡΡΡΠΈΠ»ΠΊΠ° Π³ΡΠ°Π½ΡΠ» Π‘Π‘-106
d) Π²ΡΠ³ΡΡΠ·ΠΎΡΠ½ΡΠΉ Π²Π΅Π½ΡΠΈΠ»ΡΡΠΎΡ ΠΠΠ-2,5
2. ΠΠΠΠΠΠ¦ΠΠΠΠΠ ΠΠΠΠΠΠ ΠΠ ΠΠΠΠΠ ΠΠ’ΠΠΠ¬ΠΠ ΠΠ‘ΠΠΠΠΠΠΠ«Π₯ ΠΠ ΠΠΠ£Π
2.1. ΠΡΠ½ΠΎΠ²Ρ ΠΏΡΠΎΡΠ΅ΡΡΠ° ΠΊΠΎΠ½Π΄ΠΈΡΠΈΠΎΠ½ΠΈΡΠΎΠ²Π°Π½ΠΈΡ Π³ΡΠ°Π½ΡΠ»
Π Ρ ΠΎΠ΄Π΅ ΠΊΠΎΠ½Π΄ΠΈΡΠΈΠΎΠ½ΠΈΡΠΎΠ²Π°Π½ΠΈΡ Π²ΠΎΠ·Π΄ΡΡ ΠΏΡΠΎΠ½ΠΈΠΊΠ°Π΅Ρ Π²Π½ΡΡΡΡ Π²ΡΠΏΠ΅Π½Π΅Π½Π½ΡΡ Π³ΡΠ°Π½ΡΠ» Π²ΡΠ»Π΅Π΄ΡΡΠ²ΠΈΠ΅ ΠΎΠ±ΡΠ°Π·ΠΎΠ²Π°Π²ΡΠ΅Π³ΠΎΡΡ Π² Π½ΠΈΡ Π²Π°ΠΊΡΡΠΌΠ°, Π° ΠΈΠ· Π²ΡΠΏΠ΅Π½Π΅Π½Π½ΡΡ Π³ΡΠ°Π½ΡΠ» Π² Π°ΡΠΌΠΎΡΡΠ΅ΡΡ Π²ΡΠΏΡΡΠΊΠ°Π΅ΡΡΡ Π²Π»Π°Π³Π° Π² Π²ΠΈΠ΄Π΅ ΠΏΠ°ΡΠ° ΠΈ ΠΏΠ΅Π½ΡΠ°Π½, Π½Π΅ ΠΏΡΠΎΡΠ΅Π°Π³ΠΈΡΠΎΠ²Π°Π²ΡΠΈΠ΅ ΠΎΡΡΠ°ΡΠΊΠΈ ΠΏΡΠΎΡΠ΅ΡΡΠ° ΠΏΠΎΠ»ΠΈΠΌΠ΅ΡΠΈΠ·Π°ΡΠΈΠΈ ΡΡΡΡΡ. Π£ΠΊΠ°Π·Π°Π½Π½ΡΠΉ Π³Π°Π·ΠΎΠΎΠ±ΠΌΠ΅Π½ Π²ΠΎΠ·ΠΌΠΎΠΆΠ΅Π½ Π±Π»Π°Π³ΠΎΠ΄Π°ΡΡ Π³Π°Π·ΠΎΠΏΡΠΎΠ½ΠΈΡΠ°Π΅ΠΌΠΎΡΡΠΈ ΠΏΠΎΠ»ΠΈΡΡΠΈΡΠΎΠ»ΠΎΠ²ΡΡ ΠΎΠ±ΠΎΠ»ΠΎΡΠ΅ΠΊ.

Π ΠΈΡ.2.1. ΠΡΠ°Π½ΡΠ»Ρ Π²ΡΠΏΠ΅Π½ΠΈΠ²Π°Π΅ΠΌΠΎΠ³ΠΎ ΠΏΠΎΠ»ΠΈΡΡΠΈΡΠΎΠ»Π° Π² ΠΏΡΠΎΡΠ΅ΡΡΠ΅ ΠΊΠΎΠ½Π΄ΠΈΡΠΈΠΎΠ½ΠΈΡΠΎΠ²Π°Π½ΠΈΡ
Β
Π‘ΠΊΠΎΡΠΎΡΡΡ Π΄ΠΈΡΡΡΠ·ΠΈΠΈ Π²ΠΎΠ·Π΄ΡΡ Π° Π²Π½ΡΡΡΡ Π³ΡΠ°Π½ΡΠ» ΠΎΠ±ΡΡΠ»ΠΎΠ²Π»Π΅Π½Π°, Π³Π»Π°Π²Π½ΡΠΌ ΠΎΠ±ΡΠ°Π·ΠΎΠΌ, ΠΌΠ½ΠΈΠΌΠΎΠΉ ΠΏΠ»ΠΎΡΠ½ΠΎΡΡΡΡ, ΡΠ΅ΠΌΠΏΠ΅ΡΠ°ΡΡΡΠΎΠΉ ΠΎΠΊΡΡΠΆΠ°ΡΡΠ΅ΠΉ ΡΡΠ΅Π΄Ρ ΠΈ ΡΠ°Π·ΠΌΠ΅ΡΠΎΠΌ Π³ΡΠ°Π½ΡΠ». Π¦Π΅Π»ΡΡ ΡΠ΄Π°Π»Π΅Π½ΠΈΡ Π²Π»Π°Π³ΠΈ Ρ ΠΏΠΎΠ²Π΅ΡΡ Π½ΠΎΡΡΠΈ Π³ΡΠ°Π½ΡΠ» Π² ΡΡΡΠΈΠ»ΠΊΠ΅ Ρ ΠΊΠΈΠΏΡΡΠΈΠΌ ΡΠ»ΠΎΠ΅ΠΌ ΡΠ²Π»ΡΠ΅ΡΡΡ ΠΏΠΎΠ»ΡΡΠ΅Π½ΠΈΠ΅ 100% ΠΌΠ½ΠΈΠΌΠΎΠΉ ΠΏΠΎΠ²Π΅ΡΡ Π½ΠΎΡΡΠΈ, ΡΠ΅ΡΠ΅Π· ΠΊΠΎΡΠΎΡΡΡ ΠΎΡΡΡΠ΅ΡΡΠ²Π»ΡΠ΅ΡΡΡ Π³Π°Π·ΠΎΠΎΠ±ΠΌΠ΅Π½.
Π‘ΠΊΠΎΡΠΎΡΡΡ ΠΈΡΠΏΠ°ΡΠ΅Π½ΠΈΡ ΠΏΠ΅Π½ΡΠ°Π½Π° ΡΠ°ΠΊΠΆΠ΅ Π·Π°Π²ΠΈΡΠΈΡ ΠΎΡ ΠΏΠ»ΠΎΡΠ½ΠΎΡΡΠΈ, ΡΠ΅ΠΌΠΏΠ΅ΡΠ°ΡΡΡΡ ΠΎΠΊΡΡΠΆΠ°ΡΡΠ΅ΠΉ ΡΡΠ΅Π΄Ρ ΠΈ ΡΠ°Π·ΠΌΠ΅ΡΠ° Π³ΡΠ°Π½ΡΠ». ΠΠ· ΠΊΡΡΠΏΠ½ΡΡ Π³ΡΠ°Π½ΡΠ» ΠΏΠ΅Π½ΡΠ°Π½ ΠΈΡΠΏΠ°ΡΡΠ΅ΡΡΡ ΠΌΠ΅Π΄Π»Π΅Π½Π½Π΅Π΅, ΡΠ΅ΠΌ ΠΈΠ· Π³ΡΠ°Π½ΡΠ» ΠΌΠ°Π»ΠΎΠ³ΠΎ Π΄ΠΈΠ°ΠΌΠ΅ΡΡΠ°, ΡΡΠΎ ΠΎΠ±ΡΡΠ»ΠΎΠ²Π»Π΅Π½ΠΎ ΡΠΎΠΎΡΠ½ΠΎΡΠ΅Π½ΠΈΠ΅ΠΌ ΠΌΠ΅ΠΆΠ΄Ρ ΠΏΠΎΠ²Π΅ΡΡ Π½ΠΎΡΡΡΡ Π³ΡΠ°Π½ΡΠ»Ρ ΠΈ Π΅Π΅ ΠΌΠ°ΡΡΠΎΠΉ.
2.2. Π’Π΅Ρ Π½ΠΈΡΠ΅ΡΠΊΠΎΠ΅ ΠΎΡΠ½Π°ΡΠ΅Π½ΠΈΠ΅ ΡΠ·Π»Π° ΠΊΠΎΠ½Π΄ΠΈΡΠΈΠΎΠ½ΠΈΡΠΎΠ²Π°Π½ΠΈΡ Π³ΡΠ°Π½ΡΠ»
Π‘ΠΈΠ»ΠΎΡΡ, ΠΈΡΠΏΠΎΠ»ΡΠ·ΡΠ΅ΠΌΡΠ΅ Π΄Π»Ρ ΠΊΠΎΠ½Π΄ΠΈΡΠΈΠΎΠ½ΠΈΡΠΎΠ²Π°Π½ΠΈΡ Π²ΡΠΏΠ΅Π½Π΅Π½Π½ΡΡ Π³ΡΠ°Π½ΡΠ», ΠΈΠ·Π³ΠΎΡΠΎΠ²Π»ΡΡΡΡΡ Π² Π²ΠΈΠ΄Π΅ Π»Π΅Π³ΠΊΠΎΠΉ ΠΌΠ΅ΡΠ°Π»Π»ΠΈΡΠ΅ΡΠΊΠΎΠΉ ΠΊΠΎΠ½ΡΡΡΡΠΊΡΠΈΠΈ ΡΡΠ΅Π»Π»Π°ΠΆΠ½ΠΎΠ³ΠΎ ΡΠΈΠΏΠ° Ρ ΠΊΠΎΠ½ΡΠ΅ΠΉΠ½Π΅ΡΠ°ΠΌΠΈ ΠΈΠ· ΡΠΊΠ°Π½ΠΈ, ΠΏΡΠΎΠΏΡΡΠΊΠ°ΡΡΠ΅ΠΉ Π²ΠΎΠ·Π΄ΡΡ .
ΠΡΠΈ ΠΏΠ΅ΡΠ΅ΠΌΠ΅ΡΠ΅Π½ΠΈΠΈ Π²ΡΠΏΠ΅Π½Π΅Π½Π½ΡΡ Π³ΡΠ°Π½ΡΠ» Ρ ΠΏΠΎΠΌΠΎΡΡΡ ΡΡΡΡΠΈ Π²ΠΎΠ·Π΄ΡΡ Π°, Π½Π° ΠΏΠΎΠ²Π΅ΡΡ Π½ΠΎΡΡΠΈ Π³ΡΠ°Π½ΡΠ» Π½Π°ΠΊΠ°ΠΏΠ»ΠΈΠ²Π°ΡΡΡΡ ΡΠΈΠ»ΡΠ½ΡΠ΅ ΡΠ»Π΅ΠΊΡΡΠΎΡΡΠ°ΡΠΈΡΠ΅ΡΠΊΠΈΠ΅ Π·Π°ΡΡΠ΄Ρ. ΠΠΎΡΡΠΎΠΌΡ ΡΡΠ΅Π·Π²ΡΡΠ°ΠΉΠ½ΠΎ Π²Π°ΠΆΠ½ΠΎ ΡΡΠ°ΡΠ΅Π»ΡΠ½ΠΎ Π·Π°Π·Π΅ΠΌΠ»ΠΈΡΡ Π²ΡΠ΅ ΠΌΠ΅ΡΠ°Π»Π»ΠΈΡΠ΅ΡΠΊΠΈΠ΅ ΡΠ»Π΅ΠΌΠ΅Π½ΡΡ ΡΠΈΠ»ΠΎΡΠΎΠ², ΡΡΠ°Π½ΡΠΏΠΎΡΡΠ½ΡΡ ΡΡΡΠ±ΠΎΠΏΡΠΎΠ²ΠΎΠ΄ΠΎΠ² ΠΈ ΠΎΡΡΠ°Π»ΡΠ½ΠΎΠ³ΠΎ ΠΎΠ±ΠΎΡΡΠ΄ΠΎΠ²Π°Π½ΠΈΡ.
2.3. ΠΠ°ΡΠ°ΠΌΠ΅ΡΡΡ ΠΊΠΎΠ½Π΄ΠΈΡΠΈΠΎΠ½ΠΈΡΠΎΠ²Π°Π½ΠΈΡ Π³ΡΠ°Π½ΡΠ»
Π’Π΅ΠΌΠΏΠ΅ΡΠ°ΡΡΡΠ° ΠΎΠΊΡΡΠΆΠ°ΡΡΠ΅ΠΉ ΡΡΠ΅Π΄Ρ Π² ΡΠ΅Ρ Π΅ ΠΊΠΎΠ½Π΄ΠΈΡΠΈΠΎΠ½ΠΈΡΠΎΠ²Π°Π½ΠΈΡ Π³ΡΠ°Π½ΡΠ» Π½Π΅ Π΄ΠΎΠ»ΠΆΠ½Π° Π±ΡΡΡ Π½ΠΈΠΆΠ΅ 15Β°Π‘, ΠΏΡΠΈ Π±ΠΎΠ»Π΅Π΅ Π½ΠΈΠ·ΠΊΠΎΠΉ ΡΠ΅ΠΌΠΏΠ΅ΡΠ°ΡΡΡΠ΅ ΠΏΡΠΎΠ΄ΠΎΠ»ΠΆΠΈΡΠ΅Π»ΡΠ½ΠΎΡΡΡ ΠΊΠΎΠ½Π΄ΠΈΡΠΈΠΎΠ½ΠΈΡΠΎΠ²Π°Π½ΠΈΡ ΡΠ²Π΅Π»ΠΈΡΠΈΠ²Π°Π΅ΡΡΡ. Π Π»Π΅ΡΠ½ΠΈΠΉ ΠΏΠ΅ΡΠΈΠΎΠ΄, ΠΏΡΠΈ ΡΠ΅ΠΌΠΏΠ΅ΡΠ°ΡΡΡΠ΅ ΡΠ²ΡΡΠ΅ 20Β°Π‘ Π²ΡΠ΅ΠΌΡ ΠΊΠΎΠ½Π΄ΠΈΡΠΈΠΎΠ½ΠΈΡΠΎΠ²Π°Π½ΠΈΡ ΡΠΎΠΊΡΠ°ΡΠ°ΡΡ, Π° ΠΏΡΠΈ Π±ΠΎΠ»Π΅Π΅ Π½ΠΈΠ·ΠΊΠΈΡ ΡΠ΅ΠΌΠΏΠ΅ΡΠ°ΡΡΡΠ°Ρ β ΠΏΡΠΎΠ΄Π»Π΅Π²Π°ΡΡ.
ΠΡΠΈ ΡΡΠ°Π½ΡΠΏΠΎΡΡΠΈΡΠΎΠ²ΠΊΠ΅ ΡΠ²Π΅ΠΆΠΈΡ Π³ΡΠ°Π½ΡΠ» Π² ΡΠΈΠ»ΠΎΡΡ, ΠΈΡ ΠΌΠ½ΠΈΠΌΠ°Ρ ΠΏΠ»ΠΎΡΠ½ΠΎΡΡΡ ΡΠ²Π΅Π»ΠΈΡΠΈΠ²Π°Π΅ΡΡΡ Π² ΡΠ΅Π·ΡΠ»ΡΡΠ°ΡΠ΅ ΡΡΠΎΠ»ΠΊΠ½ΠΎΠ²Π΅Π½ΠΈΠΉ ΡΠΎ ΡΡΠ΅Π½ΠΊΠ°ΠΌΠΈ ΡΡΡΠ±ΠΎΠΏΡΠΎΠ²ΠΎΠ΄Π°. ΠΠΎΡΡΠΎΠΌΡ ΠΏΡΠΈ ΡΡΡΠ°Π½ΠΎΠ²ΠΊΠ΅ ΠΏΠ°ΡΠ°ΠΌΠ΅ΡΡΠΎΠ² Π²ΡΠΏΠ΅Π½ΠΈΠ²Π°Π½ΠΈΡ Π½Π΅ΠΎΠ±Ρ ΠΎΠ΄ΠΈΠΌΠΎ ΡΡΠΈΡΡΠ²Π°ΡΡ ΡΠ²Π΅Π»ΠΈΡΠ΅Π½ΠΈΠ΅ ΠΏΠ»ΠΎΡΠ½ΠΎΡΡΠΈ ΠΏΡΠΈ ΡΡΠ°Π½ΡΠΏΠΎΡΡΠΈΡΠΎΠ²ΠΊΠ΅.
3. Π€ΠΠ ΠΠΠΠΠΠΠ ΠΠΠΠΠΠΠΠΠ‘Π’ΠΠ ΠΠΠ¬ΠΠ«Π₯ ΠΠΠΠΠΠ
3.1. Π₯Π°ΡΠ°ΠΊΡΠ΅ΡΠΈΡΡΠΈΠΊΠ° ΠΏΡΠΎΡΠ΅ΡΡΠ° ΡΠΎΡΠΌΠΎΠ²Π°Π½ΠΈΡ
ΠΡΠΈ Π²ΡΡΠ°Π±ΠΎΡΠΊΠ΅ Π±Π»ΠΎΠΊΠΎΠ² Π²ΡΠΏΠ΅Π½Π΅Π½Π½ΡΠ΅ Π³ΡΠ°Π½ΡΠ»Ρ ΡΠ²ΠΎΠ±ΠΎΠ΄Π½ΠΎ Π·Π°ΡΡΠΏΠ°ΡΡ Π² ΠΊΠ°ΠΌΠ΅ΡΡ ΡΠΎΡΠΌΡ Π΄ΠΎ Π΅Π΅ ΠΏΠΎΠ»Π½ΠΎΠ³ΠΎ Π½Π°ΠΏΠΎΠ»Π½Π΅Π½ΠΈΡ. ΠΠ°ΡΠ΅ΠΌ Π² ΡΠΎΡΠΌΡ ΠΏΠΎΠ΄Π°ΡΡ Π½Π°ΡΡΡΠ΅Π½Π½ΡΠΉ ΡΡΡ ΠΎΠΉ Π²ΠΎΠ΄ΡΠ½ΠΎΠΉ ΠΏΠ°Ρ ΠΏΠΎΠ΄ Π΄Π°Π²Π»Π΅Π½ΠΈΠ΅ΠΌ 0,2-0,4 ΠΠΠ°, ΡΡΠΎ ΠΏΡΠΈΠ²ΠΎΠ΄ΠΈΡ ΠΊ Π΄Π°Π»ΡΠ½Π΅ΠΉΡΠ΅ΠΌΡ ΡΠ²Π΅Π»ΠΈΡΠ΅Π½ΠΈΡ ΠΎΠ±ΡΠ΅ΠΌΠ° Π³ΡΠ°Π½ΡΠ». Π ΡΠ²ΡΠ·ΠΈ Ρ ΡΠ΅ΠΌ, ΡΡΠΎ Π³ΡΠ°Π½ΡΠ»Ρ Π½Π°Ρ ΠΎΠ΄ΡΡΡΡ Π² Π·Π°ΠΊΡΡΡΠΎΠΉ ΠΊΠ°ΠΌΠ΅ΡΠ΅, ΡΠ½Π°ΡΠ°Π»Π° Π·Π°ΠΏΠΎΠ»Π½ΡΠ΅ΡΡΡ ΡΠ²ΠΎΠ±ΠΎΠ΄Π½ΠΎΠ΅ ΠΏΡΠΎΡΡΡΠ°Π½ΡΡΠ²ΠΎ ΠΌΠ΅ΠΆΠ΄Ρ Π½ΠΈΠΌΠΈ, Π° Π·Π°ΡΠ΅ΠΌ Π³ΡΠ°Π½ΡΠ»Ρ ΡΡΠ΅ΠΏΠ»ΡΡΡΡΡ Π΄ΡΡΠ³ Ρ Π΄ΡΡΠ³ΠΎΠΌ.
Π ΠΈΡ.3.1.1. ΠΡΠΈΠΌΠ΅Ρ ΡΠ°Π·ΠΎΠ²ΠΎΠ³ΠΎ ΡΠΈΠΊΠ»Π° ΡΠΎΡΠΌΠΎΠ²Π°Π½ΠΈΡ Π±Π»ΠΎΠΊΠΎΠ² Π±Π΅Π· ΠΈΡΠΏΠΎΠ»ΡΠ·ΠΎΠ²Π°Π½ΠΈΡ Π²Π°ΠΊΡΡΠΌΠ°
1) Π½Π°ΠΏΠΎΠ»Π½Π΅Π½ΠΈΠ΅ 2) ΠΏΡΠΎΠ΄ΡΠ²Π°Π½ΠΈΠ΅ 3) Π·Π°ΠΏΠ°ΡΠΈΠ²Π°Π½ΠΈΠ΅ 4) ΠΎΡ Π»Π°ΠΆΠ΄Π΅Π½ΠΈΠ΅ 5) ΡΠ°ΡΡΠΎΡΠΌΠΎΠ²ΠΊΠ°
Β
Π ΠΈΡ.3.1.2. ΠΡΠΈΠΌΠ΅Ρ ΡΠ°Π·ΠΎΠ²ΠΎΠ³ΠΎ ΡΠΈΠΊΠ»Π° ΡΠΎΡΠΌΠΎΠ²Π°Π½ΠΈΡ Π±Π»ΠΎΠΊΠΎΠ² Ρ ΠΈΡΠΏΠΎΠ»ΡΠ·ΠΎΠ²Π°Π½ΠΈΠ΅ΠΌ Π²Π°ΠΊΡΡΠΌΠ°Β
1) Π½Π°ΠΏΠΎΠ»Π½Π΅Π½ΠΈΠ΅ 2) Π²Π°ΠΊΡΡΠΌ 3) ΠΏΡΠΎΠ΄ΡΠ²Π°Π½ΠΈΠ΅ 4) Π·Π°ΠΏΠ°ΡΠΈΠ²Π°Π½ΠΈΠ΅ β ΡΠΎΡΡ | 5) Π·Π°ΠΏΠ°ΡΠΈΠ²Π°Π½ΠΈΠ΅ β Π²ΡΠ΄Π΅ΡΠΆΠΊΠ° 6) Π²ΡΠΏΡΡΠΊ 7) Π²Π°ΠΊΡΡΠΌΠ½ΠΎΠ΅ ΠΎΡ Π»Π°ΠΆΠ΄Π΅Π½ΠΈΠ΅ 8) ΡΠ°Π·Π³ΡΡΠ·ΠΊΠ° |
ΠΠ°ΠΆΠ½ΡΠΌ ΡΠ°ΠΊΡΠΎΡΠΎΠΌ ΠΏΡΠΈ Π·Π°ΠΏΠ°ΡΠΈΠ²Π°Π½ΠΈΠΈ Π±Π»ΠΎΠΊΠ° ΡΠ²Π»ΡΠ΅ΡΡΡ ΠΏΠΎΠ΄Π°ΡΠ° Π² ΠΊΠ°ΠΌΠ΅ΡΡ Π² ΡΠ²ΠΎΠ±ΠΎΠ΄Π½ΠΎΠ΅ ΠΏΡΠΎΡΡΡΠ°Π½ΡΡΠ²ΠΎ ΠΌΠ΅ΠΆΠ΄Ρ Π³ΡΠ°Π½ΡΠ»Π°ΠΌΠΈ ΡΠΎΠΎΡΠ²Π΅ΡΡΡΠ²ΡΡΡΠ΅Π³ΠΎ ΠΊΠΎΠ»ΠΈΡΠ΅ΡΡΠ²Π° ΠΏΠ°ΡΠ° Π² ΠΊΡΠ°ΡΡΠ°ΠΉΡΠ΅Π΅ Π²ΡΠ΅ΠΌΡ. ΠΠ»Ρ ΡΡΠΎΠ³ΠΎ Π½Π΅ΠΎΠ±Ρ ΠΎΠ΄ΠΈΠΌΠ° ΡΠΎΠΎΡΠ²Π΅ΡΡΡΠ²ΡΡΡΠ°Ρ Π²Π΅Π½ΡΠΈΠ»ΡΡΠΈΡ (ΠΏΡΠΎΠ΄ΡΠ²Π°Π½ΠΈΠ΅), ΡΠ΅Π»ΡΡ ΠΊΠΎΡΠΎΡΠΎΠΉ ΡΠ²Π»ΡΠ΅ΡΡΡ ΡΠ΄Π°Π»Π΅Π½ΠΈΠ΅ Π²ΠΎΠ·Π΄ΡΡ Π° ΠΏΠ΅ΡΠ΅Π΄ Π½Π°ΡΠ°Π»ΠΎΠΌ ΠΏΡΠΎΡΠ΅ΡΡΠ° Π·Π°ΠΏΠ°ΡΠΈΠ²Π°Π½ΠΈΡ. ΠΠ΅Π΄ΠΎΡΡΠ°ΡΠΎΡΠ½Π°Ρ ΠΏΡΠΎΠ΄ΠΎΠ»ΠΆΠΈΡΠ΅Π»ΡΠ½ΠΎΡΡΡ ΠΏΡΠΎΠ΄ΡΠ²Π°Π½ΠΈΡ ΠΏΡΠΈΠ²ΠΎΠ΄ΠΈΡ ΠΊ Π½Π΅ΠΎΠ΄Π½ΠΎΡΠΎΠ΄Π½ΠΎΠΉ ΠΏΠ»ΠΎΡΠ½ΠΎΡΡΠΈ ΠΈ ΠΏΠ»ΠΎΡ ΠΎΠΌΡ ΡΠΏΠ΅ΠΊΠ°Π½ΠΈΡ Π±Π»ΠΎΠΊΠ°.
ΠΠ°ΠΆΠ½ΠΎ ΡΠ°ΠΊΠΆΠ΅ ΠΏΠΎΠ΄Π΄Π΅ΡΠΆΠΈΠ²Π°ΡΡ ΠΏΠΎΡΡΠΎΡΠ½Π½ΡΡ Π²ΡΡΠΎΠΊΡΡ ΡΠ΅ΠΌΠΏΠ΅ΡΠ°ΡΡΡΡ ΡΠΎΡΠΌΡ, Π² ΠΏΡΠΎΡΠΈΠ²Π½ΠΎΠΌ ΡΠ»ΡΡΠ°Π΅ Π·Π½Π°ΡΠΈΡΠ΅Π»ΡΠ½ΠΎ ΡΠ°ΡΡΠ΅Ρ ΡΠ°ΡΡ ΠΎΠ΄ ΠΏΠ°ΡΠ° (ΡΠΈΡ.3.1.3) ΠΈ ΠΏΠ°Ρ ΡΡΠ°Π½ΠΎΠ²ΠΈΡΡΡ ΠΌΠΎΠΊΡΡΠΌ, ΡΡΠΎ ΡΠ½ΠΈΠΆΠ°Π΅Ρ ΠΊΠ°ΡΠ΅ΡΡΠ²ΠΎ ΡΡΠ΅ΠΏΠ»Π΅Π½ΠΈΡ Π³ΡΠ°Π½ΡΠ».


3.2. Π’Π΅Ρ Π½ΠΈΡΠ΅ΡΠΊΠΎΠ΅ ΠΎΡΠ½Π°ΡΠ΅Π½ΠΈΠ΅ ΡΠ·Π»Π° ΡΠΎΡΠΌΠΎΠ²Π°Π½ΠΈΡ
a) Π±Π»ΠΎΠΊ ΡΠΎΡΠΌΠ° Π£Π¦ΠΠ 1030.
b) ΡΡΡΠ°Π½ΠΎΠ²ΠΊΠ° Π²Π°ΠΊΡΡΠΌΠΈΡΠΎΠ²Π°Π½ΠΈΡ ΠΠ£-3,3 Ρ Π°ΠΊΠΊΡΠΌΡΠ»ΡΡΠΎΡΠΎΠΌ Π²Π°ΠΊΡΡΠΌΠ° ΠΠ-1.
c) ΡΠΈΡΡΠ΅ΠΌΠ° Π²Π°ΠΊΡΡΠΌΠ½ΠΎΠΉ Π·Π°Π³ΡΡΠ·ΠΊΠΈ ΠΈ ΠΎΡ Π»Π°ΠΆΠ΄Π΅Π½ΠΈΡ Π±Π»ΠΎΠΊΠΎΠ².
d) ΠΊΠΎΠΌΠΏΡΠ΅ΡΡΠΎΡΠ½Π°Ρ ΡΡΡΠ°Π½ΠΎΠ²ΠΊΠ° Π‘Π4/Π€-500
e) Π°ΠΊΠΊΡΠΌΡΠ»ΡΡΠΎΡ ΠΏΠ°ΡΠ° ΠΠ-5000
f) ΠΊΠΎΡΠ΅Π» ΠΏΠ°ΡΠΎΠ²ΠΎΠΉ
Β
4. ΠΠΠΠΠΠ¦ΠΠΠΠΠ ΠΠΠΠΠΠ ΠΠΠΠΠΠ
4.1. ΠΡΠ°ΡΠΊΠ°Ρ Ρ Π°ΡΠ°ΠΊΡΠ΅ΡΠΈΡΡΠΈΠΊΠ° ΠΏΡΠΎΡΠ΅ΡΡΠ° ΠΊΠΎΠ½Π΄ΠΈΡΠΈΠΎΠ½ΠΈΡΠΎΠ²Π°Π½ΠΈΡ Π±Π»ΠΎΠΊΠΎΠ²
Β
ΠΠΎΡΠ»Π΅ ΠΎΠΊΠΎΠ½ΡΠ°Π½ΠΈΡ ΠΏΡΠΎΡΠ΅ΡΡΠ° ΡΠΎΡΠΌΠΎΠ²Π°Π½ΠΈΡ Π±Π»ΠΎΠΊΠΈ ΠΊΠΎΠ½Π΄ΠΈΡΠΈΠΎΠ½ΠΈΡΡΡΡ. ΠΠΎΠ½Π΄ΠΈΡΠΈΠΎΠ½ΠΈΡΠΎΠ²Π°Π½ΠΈΠ΅ ΠΏΡΠΎΠ²ΠΎΠ΄ΠΈΡΡΡ Ρ ΡΠ΅Π»ΡΡ ΡΠ½ΠΈΠΆΠ΅Π½ΠΈΡ Π²Π»Π°ΠΆΠ½ΠΎΡΡΠΈ ΠΈ ΡΡΡΡΠ°Π½Π΅Π½ΠΈΡ Π²Π½ΡΡΡΠ΅Π½Π½ΠΈΡ Π½Π°ΠΏΡΡΠΆΠ΅Π½ΠΈΠΉ, Π²ΠΎΠ·Π½ΠΈΠΊΠ°ΡΡΠΈΡ ΠΏΡΠΈ ΡΠΎΡΠΌΠΎΠ²Π°Π½ΠΈΠΈ. ΠΡΠΎΠΌΠ΅ ΡΠΎΠ³ΠΎ, ΠΏΡΠΈ ΡΡΠΎΠΌ ΠΏΡΠΎΡΠ΅ΠΊΠ°ΡΡ ΠΏΡΠΎΡΠ΅ΡΡΡ Π΄ΠΈΡΡΡΠ·ΠΈΠΈ Π³Π°Π·ΠΎΠ² ΠΈ Π²ΡΡΠ°Π²Π½ΠΈΠ²Π°Π½ΠΈΡ Π΄Π°Π²Π»Π΅Π½ΠΈΡ Π²Π½ΡΡΡΠΈ Π³ΡΠ°Π½ΡΠ» Ρ Π°ΡΠΌΠΎΡΡΠ΅ΡΠ½ΡΠΌ Π΄Π°Π²Π»Π΅Π½ΠΈΠ΅ΠΌ, ΠΏΠΎΠ΄ΠΎΠ±Π½ΡΠ΅ ΠΏΡΠΎΡΠ΅ΡΡΠ°ΠΌ, ΠΏΡΠΎΠΈΡΡ ΠΎΠ΄ΡΡΠΈΠΌ ΠΏΡΠΈ ΠΊΠΎΠ½Π΄ΠΈΡΠΈΠΎΠ½ΠΈΡΠΎΠ²Π°Π½ΠΈΠΈ ΠΏΡΠ΅Π΄Π²Π°ΡΠΈΡΠ΅Π»ΡΠ½ΠΎ Π²ΡΠΏΠ΅Π½Π΅Π½Π½ΡΡ Π³ΡΠ°Π½ΡΠ».
Π ΠΏΡΠΎΡΠ΅ΡΡΠ΅ ΠΊΠΎΠ½Π΄ΠΈΡΠΈΠΎΠ½ΠΈΡΠΎΠ²Π°Π½ΠΈΡ Π±Π»ΠΎΠΊΠΎΠ² ΠΎΡΠ΅Π½Ρ Π²Π°ΠΆΠ½ΡΡ ΡΠΎΠ»Ρ ΠΈΠ³ΡΠ°Π΅Ρ ΠΎΡΠ΅ΡΠ΅Π΄Π½ΠΎΡΡΡ ΠΈΡ ΠΈΡΠΏΠΎΠ»ΡΠ·ΠΎΠ²Π°Π½ΠΈΡ, ΡΠΎΠΎΡΠ²Π΅ΡΡΡΠ²ΡΡΡΠ°Ρ ΠΎΡΠ΅ΡΠ΅Π΄Π½ΠΎΡΡΠΈ ΡΠΎΡΠΌΠΎΠ²Π°Π½ΠΈΡ, ΡΠΎ Π΅ΡΡΡ ΠΏΡΠΈ ΠΎΡΠ±ΠΎΡΠ΅ Π±Π»ΠΎΠΊΠΎΠ² Π΄Π»Ρ ΡΠ°Π·ΡΠ΅Π·Π°Π½ΠΈΡ ΡΠ»Π΅Π΄ΡΠ΅Ρ Π½Π°ΡΠΈΠ½Π°ΡΡ Ρ ΡΠ°ΠΌΡΡ Β«ΡΡΠ°ΡΡΡ Β».
5. Π ΠΠΠ ΠΠΠΠΠΠ ΠΠΠΠΠΠΠΠΠ‘Π’ΠΠ ΠΠΠΠΠ«Π₯ ΠΠΠΠΠΠ ΠΠ ΠΠΠΠ’Π«
5.1. Π₯Π°ΡΠ°ΠΊΡΠ΅ΡΠΈΡΡΠΈΠΊΠ° ΠΏΡΠΎΡΠ΅ΡΡΠ° ΡΠ΅Π·ΠΊΠΈ ΠΏΠ΅Π½ΠΎΠΏΠΎΠ»ΠΈΡΡΠΈΡΠΎΠ»Π°
Π Π°Π·ΡΠ΅Π·Π°Π½ΠΈΠ΅ Π±Π»ΠΎΠΊΠΎΠ² ΠΎΡΡΡΠ΅ΡΡΠ²Π»ΡΠ΅ΡΡΡ Ρ ΠΏΠΎΠΌΠΎΡΡΡ ΡΠ΅ΠΎΡΡΠ°ΡΠ½ΠΎΠΉ ΠΏΡΠΎΠ²ΠΎΠ»ΠΎΠΊΠΈ, Π½Π°Π³ΡΠ΅ΡΠΎΠΉ Π΄ΠΎ ΡΠΎΠΎΡΠ²Π΅ΡΡΠ²ΡΡΡΠ΅ΠΉ ΡΠ΅ΠΌΠΏΠ΅ΡΠ°ΡΡΡΡ.
ΠΡΠ΅ ΠΎΡΡ ΠΎΠ΄Ρ ΠΏΠΎΠ΄Π°ΡΡΡΡ Π² ΠΈΠ·ΠΌΠ΅Π»ΡΡΠΈΡΠ΅Π»Ρ, ΠΎΡΠΊΡΠ΄Π° Π² ΠΈΠ·ΠΌΠ΅Π»ΡΡΠ΅Π½Π½ΠΎΠΌ Π²ΠΈΠ΄Π΅ ΠΏΠ½Π΅Π²ΠΌΠ°ΡΠΈΡΠ΅ΡΠΊΠΈ ΡΡΠ°Π½ΡΠΏΠΎΡΡΠΈΡΡΡΡΡΡ Π½Π° Π²ΡΠΎΡΠΈΡΠ½ΠΎΠ΅ ΠΈΡΠΏΠΎΠ»ΡΠ·ΠΎΠ²Π°Π½ΠΈΠ΅.
5.2. Π’ΡΠ΅Π±ΠΎΠ²Π°Π½ΠΈΡ ΠΏΠΎ ΠΊΠ°ΡΠ΅ΡΡΠ²Ρ
ΠΠ½Π΅ΡΠ½ΠΈΠΉ Π²ΠΈΠ΄
ΠΠΊΡΠ°ΡΠΊΠ° ΠΏΠ΅Π½ΠΎΠΏΠΎΠ»ΠΈΡΡΠΈΡΠΎΠ»ΠΎΠ²ΡΡ ΠΏΠ»ΠΈΡ Π΄ΠΎΠ»ΠΆΠ½Π° Π±ΡΡΡ ΡΠ°ΠΊΠΎΠΉ ΠΆΠ΅, ΠΊΠ°ΠΊ ΠΎΠΊΡΠ°ΡΠΊΠ° ΠΏΡΠ΅Π΄Π²Π°ΡΠΈΡΠ΅Π»ΡΠ½ΠΎ Π²ΡΠΏΠ΅Π½Π΅Π½Π½ΡΡ Π³ΡΠ°Π½ΡΠ» ΠΏΠΎΠ»ΠΈΡΡΠΈΡΠΎΠ»Π°.
ΠΠ΅ΠΎΠ±Ρ ΠΎΠ΄ΠΈΠΌΠΎ ΠΏΡΠΎΠ²ΠΎΠ΄ΠΈΡΡ Π²ΡΠ±ΠΎΡΠΎΡΠ½ΡΡ ΠΏΡΠΎΠ²Π΅ΡΠΊΡ ΠΏΠ»ΠΈΡ β ΠΏΠΎ ΠΊΡΠ°ΠΉΠ½Π΅ΠΉ ΠΌΠ΅ΡΠ΅ 2 ΡΡ. Π½Π° Π΄Π»ΠΈΠ½Π΅ ΠΊΠ°ΠΆΠ΄ΠΎΠ³ΠΎ Π±Π»ΠΎΠΊΠ°.
ΠΡΠ»ΠΈ ΠΏΠ»ΠΈΡΡ ΠΎΡΠ²Π΅ΡΠ°ΡΡ ΠΏΡΠ΅Π΄ΡΡΠ²Π»ΡΠ΅ΠΌΡΠΌ ΡΡΠ΅Π±ΠΎΠ²Π°Π½ΠΈΡΠΌ, ΡΠΎ ΠΏΠΎΡΠ»Π΅ ΡΠΊΠ»Π°Π΄ΠΊΠΈ Π² ΡΡΠΎΠΏΠΊΠΈ ΠΎΠ½ΠΈ Π½Π°ΠΏΡΠ°Π²Π»ΡΡΡΡΡ Π½Π° ΡΠΏΠ°ΠΊΠΎΠ²ΠΊΡ.
ΠΡΠ»ΠΈ ΠΎΡΠΊΠ»ΠΎΠ½Π΅Π½ΠΈΠ΅ ΠΎΡ ΡΡΠ΅Π±ΡΠ΅ΠΌΡΡ ΡΠ°Π·ΠΌΠ΅ΡΠΎΠ² ΠΏΡΠ΅Π²ΡΡΠ°Π΅Ρ Π΄ΠΎΠΏΡΡΡΠΈΠΌΡΡ Π²Π΅Π»ΠΈΡΠΈΠ½Ρ, ΡΠΎ ΡΠ»Π΅Π΄ΡΠ΅Ρ Π΅ΡΠ΅ ΡΠ°Π· ΠΏΡΠΎΠ²Π΅ΡΠΈΡΡ ΠΏΠΎ ΠΎΠ΄Π½ΠΎΠΉ ΠΏΠ»ΠΈΡΠ΅ Π½Π° Π²ΡΠ΅ΠΉ Π΄Π»ΠΈΠ½Π΅ Π±Π»ΠΎΠΊΠ°, ΠΎΠΏΡΠ΅Π΄Π΅Π»ΠΈΡΡ ΠΏΡΠΈΡΠΈΠ½Ρ, ΠΏΡΠΎΠΈΠ·Π²Π΅ΡΡΠΈ ΡΠΎΠΎΡΠ²Π΅ΡΡΡΠ²ΡΡΡΡΡ ΠΊΠΎΡΡΠ΅ΠΊΡΠΈΡΠΎΠ²ΠΊΡ ΠΏΡΠΎΠΌΠ΅ΠΆΡΡΠΊΠΎΠ² ΠΌΠ΅ΠΆΠ΄Ρ ΠΎΡΡΠ΅Π·ΠΊΠ°ΠΌΠΈ ΡΠ΅ΠΎΡΡΠ°ΡΠ½ΠΎΠΉ ΠΏΡΠΎΠ²ΠΎΠ»ΠΎΠΊΠΈ.
ΠΡΠΎΠ²Π΅ΡΠΈΡΡ ΡΠ°ΠΊΠΈΠΌ ΠΆΠ΅ ΠΎΠ±ΡΠ°Π·ΠΎΠΌ ΡΠ°Π·ΠΌΠ΅ΡΡ ΠΏΠ»ΠΈΡ, ΠΏΠΎΠ»ΡΡΠ΅Π½Π½ΡΡ Π² ΡΠ΅Π·ΡΠ»ΡΡΠ°ΡΠ΅ ΡΠ°Π·ΡΠ΅Π·Π°Π½ΠΈΡ ΡΠ»Π΅Π΄ΡΡΡΠ΅Π³ΠΎ Π±Π»ΠΎΠΊΠ°.
ΠΠ»ΠΈΡΡ, ΠΊΠΎΡΠΎΡΡΠ΅ Π½Π΅ ΠΎΡΠ²Π΅ΡΠ°ΡΡ ΠΏΡΠ΅Π΄ΡΡΠ²Π»ΡΠ΅ΠΌΡΠΌ ΡΡΠ΅Π±ΠΎΠ²Π°Π½ΠΈΡΠΌ, Π½Π°ΠΏΡΠ°Π²Π»ΡΡΡΡΡ Π½Π° Π²ΡΠΎΡΠΈΡΠ½ΠΎΠ΅ ΠΈΡΠΏΠΎΠ»ΡΠ·ΠΎΠ²Π°Π½ΠΈΠ΅.
6. ΠΠ‘ΠΠΠΠ¬ΠΠΠΠΠΠΠ ΠΠΠΠΠΠΠΠΠ‘Π’ΠΠ ΠΠΠ¬ΠΠ«Π₯ ΠΠ’Π₯ΠΠΠΠ
ΠΡΡ ΠΎΠ΄Ρ ΠΈΡΠΏΠΎΠ»ΡΠ·ΡΠ΅ΡΡΡ Π²ΡΠΎΡΠΈΡΠ½ΠΎ Π² ΠΏΡΠΎΠΈΠ·Π²ΠΎΠ΄ΡΡΠ²Π΅ Π±Π»ΠΎΠΊΠΎΠ².
6.1. Π’Π΅Ρ Π½ΠΈΡΠ΅ΡΠΊΠΎΠ΅ ΠΎΡΠ½Π°ΡΠ΅Π½ΠΈΠ΅ ΡΠ·Π»Π°
a) Π΄ΡΠΎΠ±ΠΈΠ»ΠΊΠ° ΠΏΠ΅Π½ΠΎΠΏΠΎΠ»ΠΈΡΡΠΈΡΠΎΠ»ΡΠ½ΡΡ ΠΎΡΡ ΠΎΠ΄ΠΎΠ²
b) ΡΠ΅Ρ Π½ΠΎΠ»ΠΎΠ³ΠΈΡΠ΅ΡΠΊΠΈΠΉ ΡΠΈΠ»ΠΎΡ
6.2. Π‘ΠΈΡΡΠ΅ΠΌΠ° ΠΈΠ·ΠΌΠ΅Π»ΡΡΠ΅Π½ΠΈΡ
Π£ΡΡΡΠΎΠΉΡΡΠ²ΠΎ ΠΏΡΠ΅Π΄Π½Π°Π·Π½Π°ΡΠ΅Π½ΠΎ Π΄Π»Ρ ΠΈΠ·ΠΌΠ΅Π»ΡΡΠ΅Π½ΠΈΡ ΠΏΠ΅Π½ΠΎΠΏΠΎΠ»ΠΈΡΡΠΈΡΠΎΠ»ΠΎΠ²ΡΡ ΠΎΡΡ ΠΎΠ΄ΠΎΠ², Π² ΡΠ΅Π·ΡΠ»ΡΡΠ°ΡΠ΅ ΡΠ΅Π³ΠΎ ΠΏΠΎΠ»ΡΡΠ°ΡΡ ΠΊΡΠΎΡΠΊΡ, ΠΈΡΠΏΠΎΠ»ΡΠ·ΡΠ΅ΠΌΡΡ Π² ΠΊΠ°ΡΠ΅ΡΡΠ²Π΅ Π΄ΠΎΠ±Π°Π²ΠΊΠΈ ΠΊ Π³ΡΠ°Π½ΡΠ»Π°ΠΌ ΠΏΠΎΠ»ΠΈΡΡΠΈΡΠΎΠ»Π° ΠΏΡΠΈ ΠΏΡΠΎΠΈΠ·Π²ΠΎΠ΄ΡΡΠ²Π΅ ΠΏΠ΅Π½ΠΎΠΏΠΎΠ»ΠΈΡΡΠΈΡΠΎΠ»ΠΎΠ²ΡΡ Π±Π»ΠΎΠΊΠΎΠ². Π Π°Π·ΠΌΠ΅ΡΡ ΠΏΠΎΠ»ΡΡΠ°Π΅ΠΌΠΎΠΉ ΡΠ°ΠΊΠΈΠΌ ΠΎΠ±ΡΠ°Π·ΠΎΠΌ ΠΊΡΠΎΡΠΊΠΈ ΡΠΎΡΡΠ°Π²Π»ΡΡΡ Π΄ΠΎ 15 ΠΌΠΌ.
Β
ΠΠ½ΡΠ΅ΡΠ΅ΡΠ½ΠΎ? ΠΡΡΠ°Π²ΡΡΠ΅ Π·Π°ΠΊΠ»Π°Π΄ΠΊΡ, ΡΡΠΎ Π±Ρ Π²Π΅ΡΠ½ΡΡΡΡΡ ΡΡΠ΄Π° ΠΏΠΎΠ·ΠΆΠ΅!
Β
ΠΠΠ «ΠΠ ΠΠΈΠΊΠ ΡΡ»
Π‘ΠΎΠ΄Π΅ΡΠΆΠ°Π½ΠΈΠ΅:
- ΠΡΠ΅Π΄Π²Π°ΡΠΈΡΠ΅Π»ΡΠ½ΠΎΠ΅ Π²ΡΠΏΠ΅Π½ΠΈΠ²Π°Π½ΠΈΠ΅ Π³ΡΠ°Π½ΡΠ».
- ΠΠΎΠ½Π΄ΠΈΡΠΈΠΎΠ½ΠΈΡΠΎΠ²Π°Π½ΠΈΠ΅ ΠΏΡΠ΅Π΄Π²Π°ΡΠΈΡΠ΅Π»ΡΠ½ΠΎ Π²ΡΠΏΠ΅Π½Π΅Π½Π½ΡΡ Π³ΡΠ°Π½ΡΠ».
- Π€ΠΎΡΠΌΠΎΠ²Π°Π½ΠΈΠ΅ ΠΏΠ΅Π½ΠΎΠΏΠΎΠ»ΠΈΡΡΠΈΡΠΎΠ»ΡΠ½ΡΡ Π±Π»ΠΎΠΊΠΎΠ².
- ΠΠΎΠ½Π΄ΠΈΡΠΈΠΎΠ½ΠΈΡΠΎΠ²Π°Π½ΠΈΠ΅ ΠΏΠ΅Π½ΠΎΠΏΠΎΠ»ΠΈΡΡΠΈΡΠΎΠ»ΡΠ½ΡΡ Π±Π»ΠΎΠΊΠΎΠ².
- Π Π°Π·ΡΠ΅Π·Π°Π½ΠΈΠ΅ ΠΏΠ΅Π½ΠΎΠΏΠΎΠ»ΠΈΡΡΠΈΡΠΎΠ»ΡΠ½ΡΡ Π±Π»ΠΎΠΊΠΎΠ² Π½Π° ΠΏΠ»ΠΈΡΡ.
- ΠΡΠΏΠΎΠ»ΡΠ·ΠΎΠ²Π°Π½ΠΈΠ΅ ΠΏΠ΅Π½ΠΎΠΏΠΎΠ»ΠΈΡΡΠΈΡΠΎΠ»ΡΠ½ΡΡ ΠΎΡΡ ΠΎΠ΄ΠΎΠ².
1. ΠΠ ΠΠΠΠΠ ΠΠ’ΠΠΠ¬ΠΠΠ ΠΠ‘ΠΠΠΠΠΠΠΠΠ
1.1. ΠΡΠ°ΡΠΊΠ°Ρ Ρ Π°ΡΠ°ΠΊΡΠ΅ΡΠΈΡΡΠΈΠΊΠ° ΡΡΡΡΡ
Π ΠΊΠ°ΡΠ΅ΡΡΠ²Π΅ ΡΡΡΡΡ ΠΈΡΠΏΠΎΠ»ΡΠ·ΡΠ΅ΡΡΡ Π²ΡΠΏΠ΅Π½ΠΈΠ²Π°Π΅ΠΌΡΠΉ ΡΠ°ΠΌΠΎΠ·Π°ΡΡΡ Π°ΡΡΠΈΠΉ ΠΏΠΎΠ»ΠΈΡΡΠΈΡΠΎΠ», ΡΠΎΠ΄Π΅ΡΠΆΠ°ΡΠΈΠΉ 5-6% ΡΠΌΠ΅ΡΠΈ ΠΏΠ΅Π½ΡΠ°Π½Π° ΠΈ ΠΈΠ·ΠΎΠΏΠ΅Π½ΡΠ°Π½Π°, ΡΠ²Π»ΡΡΡΠ΅ΠΉΡΡ Π²ΡΠΏΠ΅Π½ΠΈΠ²Π°ΡΡΠΈΠΌ ΡΠ°ΠΊΡΠΎΡΠΎΠΌ. ΠΡΠ° ΡΠΌΠ΅ΡΡ ΡΠΎΠ΄Π΅ΡΠΆΠΈΡΡΡ Π² Π³ΡΠ°Π½ΡΠ»Π°Ρ ΠΏΠΎΠ»ΠΈΡΡΠΈΡΠΎΠ»Π° Π² ΡΠ°ΡΡΠ²ΠΎΡΠ΅Π½Π½ΠΎΠΌ Π²ΠΈΠ΄Π΅.
Π‘ΡΡΡΠ΅ ΠΈΠΌΠ΅Π΅Ρ Π²ΠΈΠ΄ Π³ΡΠ°Π½ΡΠ», ΠΏΠΎΠ»ΡΡΠ°Π΅ΠΌΡΡ ΠΏΡΡΠ΅ΠΌ ΡΡΡΠΏΠ΅Π½Π·ΠΈΠΎΠ½Π½ΠΎΠΉ ΠΏΠΎΠ»ΠΈΠΌΠ΅ΡΠΈΠ·Π°ΡΠΈΠΈ ΡΡΠΈΡΠΎΠ»Π°. ΠΠ½ΠΎ ΡΠΎΠ΄Π΅ΡΠΆΠΈΡ Π²Π΅ΡΠ΅ΡΡΠ²ΠΎ, ΡΠ½ΠΈΠΆΠ°ΡΡΠ΅Π΅ Π³ΠΎΡΡΡΠ΅ΡΡΡ -Π°Π½ΡΠΈΠΏΠΈΡΠ΅Π½.
ΠΠΎΡΠ»Π΅ ΠΏΠΎΠ΄ΠΎΠ³ΡΠ΅Π²Π° Π΄ΠΎ ΡΠ΅ΠΌΠΏΠ΅ΡΠ°ΡΡΡΡ 90-100Β°Π‘, ΠΏΠΎΠ΄ Π΄Π΅ΠΉΡΡΠ²ΠΈΠ΅ΠΌ ΡΠ»Π΅ΡΡΡΠΈΠ²Π°ΡΡΠ΅Π³ΠΎΡΡ ΠΏΠ΅Π½ΡΠ°Π½Π° Π³ΡΠ°Π½ΡΠ»Ρ ΡΠ²Π΅Π»ΠΈΡΠΈΠ²Π°ΡΡ ΡΠ²ΠΎΠΉ ΠΎΠ±ΡΠ΅ΠΌ (ΠΏΡΠΎΡΠ΅ΡΡ Π²ΡΠΏΠ΅Π½ΠΈΠ²Π°Π½ΠΈΡ) ΠΏΡΠΈΠΌΠ΅ΡΠ½ΠΎ Π² 30-65 ΡΠ°Π·. Π ΠΏΡΠΎΠΌΡΡΠ»Π΅Π½Π½ΠΎΠΉ ΠΏΡΠ°ΠΊΡΠΈΠΊΠ΅ Π΄Π»Ρ Π²ΡΠΏΠ΅Π½ΠΈΠ²Π°Π½ΠΈΡ ΠΏΠΎΠ»ΠΈΡΡΠΈΡΠΎΠ»Π° ΠΈΡΠΏΠΎΠ»ΡΠ·ΡΠ΅ΡΡΡ Π²ΠΎΠ΄ΡΠ½ΠΎΠΉ ΠΏΠ°Ρ, ΠΊΠΎΡΠΎΡΡΠΉ ΠΏΡΠΎΠ½ΠΈΠΊΠ°Π΅Ρ ΡΠ°ΠΊΠΆΠ΅ Π²Π½ΡΡΡΡ Π³ΡΠ°Π½ΡΠ» ΠΈ ΡΠΏΠΎΡΠΎΠ±ΡΡΠ²ΡΠ΅Ρ Π΄Π΅ΠΉΡΡΠ²ΠΈΡ ΠΏΠ΅Π½ΡΠ°Π½Π°.
ΠΠ΅ΠΆΠ΄ΡΠ½Π°ΡΠΎΠ΄Π½ΠΎΠ΅ ΠΎΠ±ΠΎΠ·Π½Π°ΡΠ΅Π½ΠΈΠ΅ Π²ΡΠΏΠ΅Π½ΠΈΠ²Π°Π΅ΠΌΠΎΠ³ΠΎ ΠΏΠΎΠ»ΠΈΡΡΠΈΡΠΎΠ»Π°: EPS ΡΠ°ΠΌΠΎΠ·Π°ΡΡΡ Π°ΡΡΠΈΠΉ FS.
Π₯ΡΠ°Π½Π΅Π½ΠΈΠ΅:
Π₯ΡΠ°Π½ΠΈΡΡ ΠΈΡΠΊΠ»ΡΡΠΈΡΠ΅Π»ΡΠ½ΠΎ Π² Π·Π°Π²ΠΎΠ΄ΡΠΊΠΎΠΉ, ΠΏΠ»ΠΎΡΠ½ΠΎ Π·Π°ΠΊΡΡΡΠΎΠΉ ΡΠ°ΡΠ΅ ΠΈΠ»ΠΈ ΠΊΠΎΠ½ΡΠ΅ΠΉΠ½Π΅ΡΠ°Ρ , ΡΡΡΠ°Π½ΠΎΠ²Π»Π΅Π½Π½ΡΡ Π² ΠΏΡΠΎΠ²Π΅ΡΡΠΈΠ²Π°Π΅ΠΌΡΡ ΠΏΠΎΠΌΠ΅ΡΠ΅Π½ΠΈΡΡ ΠΈΠ»ΠΈ ΠΏΠΎΠ΄ Π½Π°Π²Π΅ΡΠΎΠΌ, Π΄Π°Π»Π΅ΠΊΠΎ ΠΎΡ ΠΈΡΡΠΎΡΠ½ΠΈΠΊΠΎΠ² ΡΠ΅ΠΏΠ»Π° ΠΈ ΠΎΠ³Π½Ρ. Π Π΅ΠΊΠΎΠΌΠ΅Π½Π΄ΡΠ΅ΡΡΡ Ρ ΡΠ°Π½ΠΈΡΡ ΡΡΡΡΠ΅ ΠΏΡΠΈ ΡΠ΅ΠΌΠΏΠ΅ΡΠ°ΡΡΡΠ΅, Π½Π΅ ΠΏΡΠ΅Π²ΡΡΠ°ΡΡΠ΅ΠΉ 20Β°Π‘.
ΠΡΠΎΠ΄ΡΠΊΡ, Ρ ΡΠ°Π½ΠΈΠΌΡΠΉ ΠΏΡΠΈ ΡΠ΅ΠΊΠΎΠΌΠ΅Π½Π΄ΡΠ΅ΠΌΠΎΠΉ ΡΠ΅ΠΌΠΏΠ΅ΡΠ°ΡΡΡΠ΅, ΡΠ»Π΅Π΄ΡΠ΅Ρ ΠΈΡΠΏΠΎΠ»ΡΠ·ΠΎΠ²Π°ΡΡ Π½Π΅ ΠΏΠΎΠ·Π΄Π½Π΅Π΅ 3-6 ΠΌΠ΅ΡΡΡΠ΅Π² Ρ Π΄Π°ΡΡ ΠΈΡΡΠ»Π΅Π΄ΠΎΠ²Π°Π½ΠΈΡ ΠΏΡΠΎΠ΄ΡΠΊΡΠ°, ΡΠΊΠ°Π·Π°Π½Π½ΠΎΠΉ Π² ΡΠ΅ΡΡΠΈΡΠΈΠΊΠ°ΡΠ΅ ΠΊΠ°ΡΠ΅ΡΡΠ²Π°. ΠΡΠΎΠ΄ΡΠΊΡ ΠΈΠ· ΡΠ°ΡΡΠΈΡΠ½ΠΎ ΠΎΠΏΠΎΡΠΎΠΆΠ½Π΅Π½Π½ΠΎΠΉ ΠΈΠ»ΠΈ ΠΏΠΎΠ²ΡΠ΅ΠΆΠ΄Π΅Π½Π½ΠΎΠΉ ΡΠ°ΡΡ ΡΠ»Π΅Π΄ΡΠ΅Ρ ΠΈΡΠΏΠΎΠ»ΡΠ·ΠΎΠ²Π°ΡΡ Π½Π΅ΠΌΠ΅Π΄Π»Π΅Π½Π½ΠΎ.
Π ΠΏΡΠΎΠΈΠ·Π²ΠΎΠ΄ΡΡΠ²Π΅Π½Π½ΡΡ ΠΏΠΎΠΌΠ΅ΡΠ΅Π½ΠΈΡΡ ΠΌΠΎΠΆΠ½ΠΎ Ρ ΡΠ°Π½ΠΈΡΡ ΡΡΡΡΠ΅ Π² ΠΊΠΎΠ»ΠΈΡΠ΅ΡΡΠ²Π΅, Π½Π΅ ΠΏΡΠ΅Π²ΡΡΠ°ΡΡΠ΅ΠΌ Π΅Π³ΠΎ ΡΡΠ΅Π΄Π½Π΅ΡΡΡΠΎΡΠ½ΡΠΉ ΡΠ°ΡΡ ΠΎΠ΄.
1.2. ΠΠ΅ΡΠ΅ΡΠ°Π±ΠΎΡΠΊΠ° Π²ΡΠΏΠ΅Π½ΠΈΠ²Π°Π΅ΠΌΠΎΠ³ΠΎ ΠΏΠΎΠ»ΠΈΡΡΠΈΡΠΎΠ»Π° .
ΠΠΊΠΎΠ½ΡΠ°ΡΠ΅Π»ΡΠ½Π°Ρ ΠΏΠ»ΠΎΡΠ½ΠΎΡΡΡ Π³ΠΎΡΠΎΠ²ΠΎΠ³ΠΎ ΠΏΡΠΎΠ΄ΡΠΊΡΠ° ΠΎΠΏΡΠ΅Π΄Π΅Π»Π΅Π½Π° ΡΠΆΠ΅ Π½Π° ΡΡΠ°ΠΏΠ΅ ΠΏΡΠ΅Π΄Π²Π°ΡΠΈΡΠ΅Π»ΡΠ½ΠΎΠ³ΠΎ Π²ΡΠΏΠ΅Π½ΠΈΠ²Π°Π½ΠΈΡ.
ΠΠ°ΠΆΠ½ΡΠΌ ΠΏΠΎΠΊΠ°Π·Π°ΡΠ΅Π»Π΅ΠΌ ΡΠ²Π»ΡΠ΅ΡΡΡ ΠΊΠΎΠ½ΡΡΠΎΠ»Ρ Π΄Π°Π²Π»Π΅Π½ΠΈΡ ΠΏΡΠΈ ΠΏΡΠΎΡΠ΅ΡΡΠ΅ Π²ΡΠΏΠ΅Π½ΠΈΠ²Π°Π½ΠΈΡ, Π΄Π»Ρ Π½Π΅ΠΏΡΠ΅ΡΡΠ²Π½ΡΡ ΠΏΡΠ΅Π΄Π²ΡΠΏΠ΅Π½ΠΈΠ²Π°ΡΠ΅Π»Π΅ΠΉ 0,015-0,03 ΠΠΠ°, Π΄Π»Ρ ΡΠΈΠΊΠ»ΠΈΡΠ΅ΡΠΊΠΈΡ 0,015-0,02 ΠΠΠ°.
ΠΠΎ Π²ΡΠΏΠ΅Π½ΠΈΠ²Π°ΡΠ΅Π»Π΅ Π΄Π²Π° ΡΠΏΠΎΡΠΎΠ±Π° ΠΈΠ·ΠΌΠ΅Π½Π΅Π½ΠΈΡ ΠΌΠ½ΠΈΠΌΠΎΠΉ ΠΏΠ»ΠΎΡΠ½ΠΎΡΡΠΈ ΠΏΡΠΎΠ΄ΡΠΊΡΠ°:
- ΠΏΡΡΠ΅ΠΌ ΠΈΠ·ΠΌΠ΅Π½Π΅Π½ΠΈΡ ΠΊΠΎΠ»ΠΈΡΠ΅ΡΡΠ²Π° ΠΏΠΎΠ΄Π°Π²Π°Π΅ΠΌΠΎΠ³ΠΎ ΡΡΡΡΡ;
- ΠΏΡΡΠ΅ΠΌ ΠΈΠ·ΠΌΠ΅Π½Π΅Π½ΠΈΡ ΡΡΠΎΠ²Π½Ρ Π²ΡΠΏΠ΅Π½ΠΈΠ²Π°Π΅ΠΌΠΎΠ³ΠΎ ΠΌΠ°ΡΠ΅ΡΠΈΠ°Π»Π° Π² ΡΠ°Π±ΠΎΡΠ΅ΠΉ ΠΊΠ°ΠΌΠ΅ΡΠ΅;
ΠΠ΅ΡΠ²ΡΠΉ ΠΈ Π²ΡΠΎΡΠΎΠΉ ΡΠΏΠΎΡΠΎΠ± ΠΎΠΊΠ°Π·ΡΠ²Π°ΡΡ Π²Π»ΠΈΡΠ½ΠΈΠ΅ Π½Π° Π²ΡΠ΅ΠΌΡ Π½Π°Ρ ΠΎΠΆΠ΄Π΅Π½ΠΈΡ Π²ΡΠΏΠ΅Π½ΠΈΠ²Π°Π΅ΠΌΠΎΠ³ΠΎ ΠΌΠ°ΡΠ΅ΡΠΈΠ°Π»Π° Π² ΡΠ°Π±ΠΎΡΠ΅ΠΉ ΠΊΠ°ΠΌΠ΅ΡΠ΅. Π’ΡΠ΅ΡΠΈΠΉ ΡΠΏΠΎΡΠΎΠ± Π²Π»ΠΈΡΠ΅Ρ Π½Π° ΡΠ΅ΠΌΠΏΠ΅ΡΠ°ΡΡΡΡ Π² ΠΊΠ°ΠΌΠ΅ΡΠ΅.
ΠΠ»ΠΈΡΠ½ΠΈΠ΅ Π²ΡΠ΅ΠΌΠ΅Π½ΠΈ Π½Π°Ρ ΠΎΠΆΠ΄Π΅Π½ΠΈΡ ΡΡΡΡΡ Π²ΠΎ Π²ΡΠΏΠ΅Π½ΠΈΠ²Π°ΡΠ΅Π»Π΅ Π½Π° ΠΌΠ½ΠΈΠΌΡΡ ΠΏΠ»ΠΎΡΠ½ΠΎΡΡΡ ΠΏΡΠΎΠ΄ΡΠΊΡΠ° ΠΏΡΠ΅Π΄ΡΡΠ°Π²Π»Π΅Π½ΠΎ Π½Π° ΡΠΈΡ.1.2.
ΠΡΠ»ΠΈ Π²ΡΠ΅ΠΌΡ Π½Π°Ρ ΠΎΠΆΠ΄Π΅Π½ΠΈΡ ΡΡΡΡΡ Π²ΠΎ Π²ΡΠΏΠ΅Π½ΠΈΠ²Π°ΡΠ΅Π»Π΅ ΡΠ»ΠΈΡΠΊΠΎΠΌ ΠΏΡΠΎΠ΄ΠΎΠ»ΠΆΠΈΡΠ΅Π»ΡΠ½ΠΎ, ΡΠΎ Π³ΡΠ°Π½ΡΠ»Ρ Π½Π°ΡΠΈΠ½Π°ΡΡ ΡΡΠ°ΠΆΠΈΠ²Π°ΡΡΡΡ ΠΈ ΠΏΠ»ΠΎΡΠ½ΠΎΡΡΡ ΡΠ°ΡΡΠ΅Ρ; ΠΏΡΠΈ ΡΠ»ΠΈΡΠΊΠΎΠΌ Π²ΡΡΠΎΠΊΠΎΠΉ ΡΠ΅ΠΌΠΏΠ΅ΡΠ°ΡΡΡΠ΅ Π²ΡΠΏΠ΅Π½Π΅Π½Π½ΡΠ΅ Π³ΡΠ°Π½ΡΠ»Ρ ΠΌΠΎΠ³ΡΡ ΠΎΠ±ΡΠ°Π·ΠΎΠ²Π°ΡΡ ΠΊΠΎΠΌΠΊΠΈ. ΠΠ±Π° ΡΡΠΈ ΡΠ²Π»Π΅Π½ΠΈΡ ΠΌΠΎΠ³ΡΡ ΠΏΡΠΎΠΈΡΡ ΠΎΠ΄ΠΈΡΡ ΠΎΠ΄Π½ΠΎΠ²ΡΠ΅ΠΌΠ΅Π½Π½ΠΎ. Π ΠΎΠΊΠ°Π·ΡΠ²Π°ΡΡ Π½Π΅ΠΏΠΎΡΡΠ΅Π΄ΡΡΠ²Π΅Π½Π½ΠΎΠ΅ Π²Π»ΠΈΡΠ½ΠΈΠ΅ Π½Π° ΠΊΠ°ΡΠ΅ΡΡΠ²ΠΎ ΠΊΠΎΠ½Π΅ΡΠ½ΠΎΠ³ΠΎ ΠΏΡΠΎΠ΄ΡΠΊΡΠ°.
ΠΠ»ΠΎΡΠ½ΠΎΡΡΡ
ΠΡΠΎΠ΄ΠΎΠ»ΠΆΠΈΡΠ΅Π»ΡΠ½ΠΎΡΡΡ ΠΏΡΠ΅Π΄Π²Π°ΡΠΈΡΠ΅Π»ΡΠ½ΠΎΠ³ΠΎ Π²ΡΠΏΠ΅Π½ΠΈΠ²Π°Π½ΠΈΡ
Π ΠΈΡ.1.2. ΠΠ°Π²ΠΈΡΠΈΠΌΠΎΡΡΡ ΠΌΠ΅ΠΆΠ΄Ρ ΠΌΠ½ΠΈΠΌΠΎΠΉ ΠΏΠ»ΠΎΡΠ½ΠΎΡΡΡΡ ΠΈ ΠΏΡΠΎΠ΄ΠΎΠ»ΠΆΠΈΡΠ΅Π»ΡΠ½ΠΎΡΡΡΡ Π²ΡΠΏΠ΅Π½ΠΈΠ²Π°Π½ΠΈΡ
Π‘ ΡΠ΅Π»ΡΡ ΠΏΠΎΠ»ΡΡΠ΅Π½ΠΈΡ Π½ΠΈΠ·ΠΊΠΎΠΉ ΠΏΠ»ΠΎΡΠ½ΠΎΡΡΠΈ (< 12 ΠΊΠ³/ΠΌ3) ΠΏΡΠΈΠΌΠ΅Π½ΡΡΡ Π΄Π²ΡΡ ΡΡΡΠΏΠ΅Π½ΡΠ°ΡΠΎΠ΅ Π²ΡΠΏΠ΅Π½ΠΈΠ²Π°Π½ΠΈΠ΅. ΠΠ²ΡΡ ΡΡΡΠΏΠ΅Π½ΡΠ°ΡΠΎΠ΅ Π²ΡΠΏΠ΅Π½ΠΈΠ²Π°Π½ΠΈΠ΅ ΠΏΡΠΎΠ²ΠΎΠ΄ΡΡ Ρ ΠΏΠΎΠΌΠΎΡΡΡ ΡΠΎΠ³ΠΎ ΠΆΠ΅ ΡΠ°ΠΌΠΎΠ³ΠΎ ΠΎΠ±ΠΎΡΡΠ΄ΠΎΠ²Π°Π½ΠΈΡ, ΠΊΠΎΡΠΎΡΠΎΠ΅ ΠΈΡΠΏΠΎΠ»ΡΠ·ΡΠ΅ΡΡΡ Π΄Π»Ρ ΠΎΠ΄Π½ΠΎΡΡΡΠΏΠ΅Π½ΡΠ°ΡΠΎΠ³ΠΎ Π²ΡΠΏΠ΅Π½ΠΈΠ²Π°Π½ΠΈΡ, Ρ ΠΏΠΎΠ΄Π°ΡΠ΅ΠΉ ΠΏΡΠ΅Π΄Π²Π°ΡΠΈΡΠ΅Π»ΡΠ½ΠΎ Π²ΡΠΏΠ΅Π½Π΅Π½Π½ΠΎΠ³ΠΎ ΡΡΡΡΡ ΡΠ΅ΡΠ΅Π· ΡΠΈΡΡΠ΅ΠΌΡ Π²ΡΠΎΡΠΈΡΠ½ΠΎΠ³ΠΎ Π²ΡΠΏΠ΅Π½ΠΈΠ²Π°Π½ΠΈΡ.
Π‘ ΡΠ΅Π»ΡΡ Π΄ΠΎΡΡΠΈΠΆΠ΅Π½ΠΈΡ ΠΎΠΏΡΠΈΠΌΠ°Π»ΡΠ½ΡΡ ΡΠ΅Π·ΡΠ»ΡΡΠ°ΡΠΎΠ² Π²ΡΠΏΠ΅Π½ΠΈΠ²Π°Π½ΠΈΡ Π³ΡΠ°Π½ΡΠ»Ρ ΠΏΠ΅ΡΠ΅Π΄ Π²ΡΠΏΠ΅Π½ΠΈΠ²Π°Π½ΠΈΠ΅ΠΌ Π²ΡΠΎΡΠΎΠΉ ΡΡΡΠΏΠ΅Π½ΠΈ Π΄ΠΎΠ»ΠΆΠ½Ρ Π±ΡΡΡ Π½Π°ΡΡΡΠ΅Π½Ρ Π²ΠΎΠ·Π΄ΡΡ ΠΎΠΌ (ΠΏΡΠΎΡΠ΅ΡΡ ΠΊΠΎΠ½Π΄ΠΈΡΠΈΠΎΠ½ΠΈΡΠΎΠ²Π°Π½ΠΈΡ).
ΠΡΠ΅Π΄Π²Π°ΡΠΈΡΠ΅Π»ΡΠ½ΠΎ Π²ΡΠΏΠ΅Π½Π΅Π½Π½ΡΠ΅ Π³ΡΠ°Π½ΡΠ»Ρ ΠΏΠΎΡΡΡΠΏΠ°ΡΡ Π² ΡΡΡΠΈΠ»ΠΊΡ Ρ ΠΊΠΈΠΏΡΡΠΈΠΌ ΡΠ»ΠΎΠ΅ΠΌ, Π² ΠΊΠΎΡΠΎΡΠΎΠΉ ΡΠ΅ΠΏΠ»ΡΠΉ Π²ΠΎΠ·Π΄ΡΡ (ΡΠ΅ΠΌΠΏ. ΠΏΡΠΈΠΌΠ΅ΡΠ½ΠΎ 30-40Β°Π‘) ΠΏΡΠΎΡ ΠΎΠ΄ΠΈΡ ΡΠ΅ΡΠ΅Π· ΠΏΠ΅ΡΡΠΎΡΠΈΡΠΎΠ²Π°Π½Π½ΠΎΠ΅ Π΄Π½ΠΈΡΠ΅ ΡΡΡΠΈΠ»ΠΊΠΈ, ΡΡΡΠΈΡ ΠΈ ΠΏΡΠΎΠ΄Π²ΠΈΠ³Π°Π΅Ρ Π³ΡΠ°Π½ΡΠ»Ρ Π² Π½Π°ΠΏΡΠ°Π²Π»Π΅Π½ΠΈΠΈ Π²ΡΠ³ΡΡΠ·ΠΎΡΠ½ΠΎΠ³ΠΎ Π²Π΅Π½ΡΠΈΠ»ΡΡΠΎΡΠ°.
ΠΠΎΠ·Π΄ΡΡΠ½Π°Ρ ΡΡΡΡΡ Π΄ΠΎΠ»ΠΆΠ½Π° ΡΠ°ΡΠΏΡΠ΅Π΄Π΅Π»ΡΡΡΡΡ ΡΠ°ΠΊΠΈΠΌ ΠΎΠ±ΡΠ°Π·ΠΎΠΌ, ΡΡΠΎΠ±Ρ ΠΏΡΠΎΡΠ΅ΡΡ ΡΡΡΠΊΠΈ ΠΈ ΠΏΠ΅ΡΠ΅ΠΌΠ΅ΡΠ΅Π½ΠΈΡ Π³ΡΠ°Π½ΡΠ» ΠΏΡΠΎΡΠ΅ΠΊΠ°Π» ΡΠ°Π²Π½ΠΎΠΌΠ΅ΡΠ½ΠΎ ΠΏΠΎ Π²ΡΠ΅ΠΉ Π΄Π»ΠΈΠ½Π΅ ΡΡΡΠΈΠ»ΠΊΠΈ (ΡΠ΅Π³ΡΠ»ΠΈΡΠΎΠ²ΠΊΠ° ΠΎΡΡΡΠ΅ΡΡΠ²Π»ΡΠ΅ΡΡΡ Ρ ΠΏΠΎΠΌΠΎΡΡΡ Π·Π°ΡΠ»ΠΎΠ½ΠΎΠΊ Π² Π²ΠΎΠ·Π΄ΡΡΠ½ΡΡ ΠΊΠ°ΠΌΠ΅ΡΠ°Ρ ΡΡΡΠΈΠ»ΠΊΠΈ).
ΠΠ΄Π½ΠΈΠΌ ΠΈΠ· ΡΡΠ΅Π·Π²ΡΡΠ°ΠΉΠ½ΠΎ Π²Π°ΠΆΠ½ΡΡ ΡΠ°ΠΊΡΠΎΡΠΎΠ², ΠΎΠΊΠ°Π·ΡΠ²Π°ΡΡΠΈΡ Π²Π»ΠΈΡΠ½ΠΈΠ΅ Π½Π° Π²ΡΠΏΠ΅Π½ΠΈΠ²Π°Π½ΠΈΠ΅ ΠΏΠΎΠ»ΠΈΡΡΠΈΡΠΎΠ»Π°, ΡΠ²Π»ΡΠ΅ΡΡΡ ΠΏΡΠΎΠ΄ΠΎΠ»ΠΆΠΈΡΠ΅Π»ΡΠ½ΠΎΡΡΡ Ρ ΡΠ°Π½Π΅Π½ΠΈΡ ΡΡΡΡΡ. Π§Π΅ΠΌ ΡΡΠ°ΡΡΠ΅ ΡΡΡΡΠ΅, ΡΠ΅ΠΌ ΠΏΡΠΎΠ΄ΠΎΠ»ΠΆΠΈΡΠ΅Π»ΡΠ½Π΅Π΅ Π²ΡΠΏΠ΅Π½ΠΈΠ²Π°Π½ΠΈΠ΅ ΠΈ ΡΠ΅ΠΌ ΡΡΡΠ΄Π½Π΅Π΅ Π΄ΠΎΡΡΠΈΡΡ ΡΡΠ΅Π±ΡΠ΅ΠΌΠΎΠΉ ΠΌΠ½ΠΈΠΌΠΎΠΉ ΠΏΠ»ΠΎΡΠ½ΠΎΡΡΠΈ Π²ΡΠΏΠ΅Π½Π΅Π½Π½ΡΡ Π³ΡΠ°Π½ΡΠ». ΠΠΎΡΡΠΎΠΌΡ ΡΡΠΎΠΊ Ρ ΡΠ°Π½Π΅Π½ΠΈΡ ΡΡΡΡΡ Π² Π³Π΅ΡΠΌΠ΅ΡΠΈΡΠ½ΠΎΠΉ ΡΠΏΠ°ΠΊΠΎΠ²ΠΊΠ΅ ΠΎΠ³ΡΠ°Π½ΠΈΡΠ΅Π½ Π΄ΠΎ ΡΠ΅ΡΡΠΈ ΠΌΠ΅ΡΡΡΠ΅Π².
1.3. Π’Π΅Ρ Π½ΠΈΡΠ΅ΡΠΊΠΎΠ΅ ΠΎΡΠ½Π°ΡΠ΅Π½ΠΈΠ΅ ΡΠ·Π»Π° ΠΏΡΠ΅Π΄Π²Π°ΡΠΈΡΠ΅Π»ΡΠ½ΠΎΠ³ΠΎ Π²ΡΠΏΠ΅Π½ΠΈΠ²Π°Π½ΠΈΡ
a) Π²ΡΠΏΠ΅Π½ΠΈΠ²Π°ΡΠ΅Π»Ρ ΠΠ-03
b) ΡΠΈΡΡΠ΅ΠΌΠ° Π²ΡΠΎΡΠΈΡΠ½ΠΎΠ³ΠΎ Π²ΡΠΏΠ΅Π½ΠΈΠ²Π°Π½ΠΈΡ Π‘ΠΠ-1
c) ΠΏΠΎΡΠΎΡΠ½Π°Ρ ΡΡΡΠΈΠ»ΠΊΠ° Π³ΡΠ°Π½ΡΠ» Π‘Π‘-106
d) Π²ΡΠ³ΡΡΠ·ΠΎΡΠ½ΡΠΉ Π²Π΅Π½ΡΠΈΠ»ΡΡΠΎΡ ΠΠΠ-2,5
2. ΠΠΠΠΠΠ¦ΠΠΠΠΠ ΠΠΠΠΠΠ ΠΠ ΠΠΠΠΠ ΠΠ’ΠΠΠ¬ΠΠ ΠΠ‘ΠΠΠΠΠΠΠ«Π₯ ΠΠ ΠΠΠ£Π
2.1. ΠΡΠ½ΠΎΠ²Ρ ΠΏΡΠΎΡΠ΅ΡΡΠ° ΠΊΠΎΠ½Π΄ΠΈΡΠΈΠΎΠ½ΠΈΡΠΎΠ²Π°Π½ΠΈΡ Π³ΡΠ°Π½ΡΠ»
Π Ρ ΠΎΠ΄Π΅ ΠΊΠΎΠ½Π΄ΠΈΡΠΈΠΎΠ½ΠΈΡΠΎΠ²Π°Π½ΠΈΡ Π²ΠΎΠ·Π΄ΡΡ ΠΏΡΠΎΠ½ΠΈΠΊΠ°Π΅Ρ Π²Π½ΡΡΡΡ Π²ΡΠΏΠ΅Π½Π΅Π½Π½ΡΡ Π³ΡΠ°Π½ΡΠ» Π²ΡΠ»Π΅Π΄ΡΡΠ²ΠΈΠ΅ ΠΎΠ±ΡΠ°Π·ΠΎΠ²Π°Π²ΡΠ΅Π³ΠΎΡΡ Π² Π½ΠΈΡ Π²Π°ΠΊΡΡΠΌΠ°, Π° ΠΈΠ· Π²ΡΠΏΠ΅Π½Π΅Π½Π½ΡΡ Π³ΡΠ°Π½ΡΠ» Π² Π°ΡΠΌΠΎΡΡΠ΅ΡΡ Π²ΡΠΏΡΡΠΊΠ°Π΅ΡΡΡ Π²Π»Π°Π³Π° Π² Π²ΠΈΠ΄Π΅ ΠΏΠ°ΡΠ° ΠΈ ΠΏΠ΅Π½ΡΠ°Π½, Π½Π΅ ΠΏΡΠΎΡΠ΅Π°Π³ΠΈΡΠΎΠ²Π°Π²ΡΠΈΠ΅ ΠΎΡΡΠ°ΡΠΊΠΈ ΠΏΡΠΎΡΠ΅ΡΡΠ° ΠΏΠΎΠ»ΠΈΠΌΠ΅ΡΠΈΠ·Π°ΡΠΈΠΈ ΡΡΡΡΡ. Π£ΠΊΠ°Π·Π°Π½Π½ΡΠΉ Π³Π°Π·ΠΎΠΎΠ±ΠΌΠ΅Π½ Π²ΠΎΠ·ΠΌΠΎΠΆΠ΅Π½ Π±Π»Π°Π³ΠΎΠ΄Π°ΡΡ Π³Π°Π·ΠΎΠΏΡΠΎΠ½ΠΈΡΠ°Π΅ΠΌΠΎΡΡΠΈ ΠΏΠΎΠ»ΠΈΡΡΠΈΡΠΎΠ»ΠΎΠ²ΡΡ ΠΎΠ±ΠΎΠ»ΠΎΡΠ΅ΠΊ.

Π ΠΈΡ.2.1. ΠΡΠ°Π½ΡΠ»Ρ Π²ΡΠΏΠ΅Π½ΠΈΠ²Π°Π΅ΠΌΠΎΠ³ΠΎ ΠΏΠΎΠ»ΠΈΡΡΠΈΡΠΎΠ»Π° Π² ΠΏΡΠΎΡΠ΅ΡΡΠ΅ ΠΊΠΎΠ½Π΄ΠΈΡΠΈΠΎΠ½ΠΈΡΠΎΠ²Π°Π½ΠΈΡ
Π‘ΠΊΠΎΡΠΎΡΡΡ Π΄ΠΈΡΡΡΠ·ΠΈΠΈ Π²ΠΎΠ·Π΄ΡΡ Π° Π²Π½ΡΡΡΡ Π³ΡΠ°Π½ΡΠ» ΠΎΠ±ΡΡΠ»ΠΎΠ²Π»Π΅Π½Π°, Π³Π»Π°Π²Π½ΡΠΌ ΠΎΠ±ΡΠ°Π·ΠΎΠΌ, ΠΌΠ½ΠΈΠΌΠΎΠΉ ΠΏΠ»ΠΎΡΠ½ΠΎΡΡΡΡ, ΡΠ΅ΠΌΠΏΠ΅ΡΠ°ΡΡΡΠΎΠΉ ΠΎΠΊΡΡΠΆΠ°ΡΡΠ΅ΠΉ ΡΡΠ΅Π΄Ρ ΠΈ ΡΠ°Π·ΠΌΠ΅ΡΠΎΠΌ Π³ΡΠ°Π½ΡΠ». Π¦Π΅Π»ΡΡ ΡΠ΄Π°Π»Π΅Π½ΠΈΡ Π²Π»Π°Π³ΠΈ Ρ ΠΏΠΎΠ²Π΅ΡΡ Π½ΠΎΡΡΠΈ Π³ΡΠ°Π½ΡΠ» Π² ΡΡΡΠΈΠ»ΠΊΠ΅ Ρ ΠΊΠΈΠΏΡΡΠΈΠΌ ΡΠ»ΠΎΠ΅ΠΌ ΡΠ²Π»ΡΠ΅ΡΡΡ ΠΏΠΎΠ»ΡΡΠ΅Π½ΠΈΠ΅ 100% ΠΌΠ½ΠΈΠΌΠΎΠΉ ΠΏΠΎΠ²Π΅ΡΡ Π½ΠΎΡΡΠΈ, ΡΠ΅ΡΠ΅Π· ΠΊΠΎΡΠΎΡΡΡ ΠΎΡΡΡΠ΅ΡΡΠ²Π»ΡΠ΅ΡΡΡ Π³Π°Π·ΠΎΠΎΠ±ΠΌΠ΅Π½.
Π‘ΠΊΠΎΡΠΎΡΡΡ ΠΈΡΠΏΠ°ΡΠ΅Π½ΠΈΡ ΠΏΠ΅Π½ΡΠ°Π½Π° ΡΠ°ΠΊΠΆΠ΅ Π·Π°Π²ΠΈΡΠΈΡ ΠΎΡ ΠΏΠ»ΠΎΡΠ½ΠΎΡΡΠΈ, ΡΠ΅ΠΌΠΏΠ΅ΡΠ°ΡΡΡΡ ΠΎΠΊΡΡΠΆΠ°ΡΡΠ΅ΠΉ ΡΡΠ΅Π΄Ρ ΠΈ ΡΠ°Π·ΠΌΠ΅ΡΠ° Π³ΡΠ°Π½ΡΠ». ΠΠ· ΠΊΡΡΠΏΠ½ΡΡ Π³ΡΠ°Π½ΡΠ» ΠΏΠ΅Π½ΡΠ°Π½ ΠΈΡΠΏΠ°ΡΡΠ΅ΡΡΡ ΠΌΠ΅Π΄Π»Π΅Π½Π½Π΅Π΅, ΡΠ΅ΠΌ ΠΈΠ· Π³ΡΠ°Π½ΡΠ» ΠΌΠ°Π»ΠΎΠ³ΠΎ Π΄ΠΈΠ°ΠΌΠ΅ΡΡΠ°, ΡΡΠΎ ΠΎΠ±ΡΡΠ»ΠΎΠ²Π»Π΅Π½ΠΎ ΡΠΎΠΎΡΠ½ΠΎΡΠ΅Π½ΠΈΠ΅ΠΌ ΠΌΠ΅ΠΆΠ΄Ρ ΠΏΠΎΠ²Π΅ΡΡ Π½ΠΎΡΡΡΡ Π³ΡΠ°Π½ΡΠ»Ρ ΠΈ Π΅Π΅ ΠΌΠ°ΡΡΠΎΠΉ.
2.2. Π’Π΅Ρ Π½ΠΈΡΠ΅ΡΠΊΠΎΠ΅ ΠΎΡΠ½Π°ΡΠ΅Π½ΠΈΠ΅ ΡΠ·Π»Π° ΠΊΠΎΠ½Π΄ΠΈΡΠΈΠΎΠ½ΠΈΡΠΎΠ²Π°Π½ΠΈΡ Π³ΡΠ°Π½ΡΠ»
Π‘ΠΈΠ»ΠΎΡΡ, ΠΈΡΠΏΠΎΠ»ΡΠ·ΡΠ΅ΠΌΡΠ΅ Π΄Π»Ρ ΠΊΠΎΠ½Π΄ΠΈΡΠΈΠΎΠ½ΠΈΡΠΎΠ²Π°Π½ΠΈΡ Π²ΡΠΏΠ΅Π½Π΅Π½Π½ΡΡ Π³ΡΠ°Π½ΡΠ», ΠΈΠ·Π³ΠΎΡΠΎΠ²Π»ΡΡΡΡΡ Π² Π²ΠΈΠ΄Π΅ Π»Π΅Π³ΠΊΠΎΠΉ ΠΌΠ΅ΡΠ°Π»Π»ΠΈΡΠ΅ΡΠΊΠΎΠΉ ΠΊΠΎΠ½ΡΡΡΡΠΊΡΠΈΠΈ ΡΡΠ΅Π»Π»Π°ΠΆΠ½ΠΎΠ³ΠΎ ΡΠΈΠΏΠ° Ρ ΠΊΠΎΠ½ΡΠ΅ΠΉΠ½Π΅ΡΠ°ΠΌΠΈ ΠΈΠ· ΡΠΊΠ°Π½ΠΈ, ΠΏΡΠΎΠΏΡΡΠΊΠ°ΡΡΠ΅ΠΉ Π²ΠΎΠ·Π΄ΡΡ .
ΠΡΠΈ ΠΏΠ΅ΡΠ΅ΠΌΠ΅ΡΠ΅Π½ΠΈΠΈ Π²ΡΠΏΠ΅Π½Π΅Π½Π½ΡΡ Π³ΡΠ°Π½ΡΠ» Ρ ΠΏΠΎΠΌΠΎΡΡΡ ΡΡΡΡΠΈ Π²ΠΎΠ·Π΄ΡΡ Π°, Π½Π° ΠΏΠΎΠ²Π΅ΡΡ Π½ΠΎΡΡΠΈ Π³ΡΠ°Π½ΡΠ» Π½Π°ΠΊΠ°ΠΏΠ»ΠΈΠ²Π°ΡΡΡΡ ΡΠΈΠ»ΡΠ½ΡΠ΅ ΡΠ»Π΅ΠΊΡΡΠΎΡΡΠ°ΡΠΈΡΠ΅ΡΠΊΠΈΠ΅ Π·Π°ΡΡΠ΄Ρ. ΠΠΎΡΡΠΎΠΌΡ ΡΡΠ΅Π·Π²ΡΡΠ°ΠΉΠ½ΠΎ Π²Π°ΠΆΠ½ΠΎ ΡΡΠ°ΡΠ΅Π»ΡΠ½ΠΎ Π·Π°Π·Π΅ΠΌΠ»ΠΈΡΡ Π²ΡΠ΅ ΠΌΠ΅ΡΠ°Π»Π»ΠΈΡΠ΅ΡΠΊΠΈΠ΅ ΡΠ»Π΅ΠΌΠ΅Π½ΡΡ ΡΠΈΠ»ΠΎΡΠΎΠ², ΡΡΠ°Π½ΡΠΏΠΎΡΡΠ½ΡΡ ΡΡΡΠ±ΠΎΠΏΡΠΎΠ²ΠΎΠ΄ΠΎΠ² ΠΈ ΠΎΡΡΠ°Π»ΡΠ½ΠΎΠ³ΠΎ ΠΎΠ±ΠΎΡΡΠ΄ΠΎΠ²Π°Π½ΠΈΡ.
2.3. ΠΠ°ΡΠ°ΠΌΠ΅ΡΡΡ ΠΊΠΎΠ½Π΄ΠΈΡΠΈΠΎΠ½ΠΈΡΠΎΠ²Π°Π½ΠΈΡ Π³ΡΠ°Π½ΡΠ»
Π’Π΅ΠΌΠΏΠ΅ΡΠ°ΡΡΡΠ° ΠΎΠΊΡΡΠΆΠ°ΡΡΠ΅ΠΉ ΡΡΠ΅Π΄Ρ Π² ΡΠ΅Ρ Π΅ ΠΊΠΎΠ½Π΄ΠΈΡΠΈΠΎΠ½ΠΈΡΠΎΠ²Π°Π½ΠΈΡ Π³ΡΠ°Π½ΡΠ» Π½Π΅ Π΄ΠΎΠ»ΠΆΠ½Π° Π±ΡΡΡ Π½ΠΈΠΆΠ΅ 15Β°Π‘, ΠΏΡΠΈ Π±ΠΎΠ»Π΅Π΅ Π½ΠΈΠ·ΠΊΠΎΠΉ ΡΠ΅ΠΌΠΏΠ΅ΡΠ°ΡΡΡΠ΅ ΠΏΡΠΎΠ΄ΠΎΠ»ΠΆΠΈΡΠ΅Π»ΡΠ½ΠΎΡΡΡ ΠΊΠΎΠ½Π΄ΠΈΡΠΈΠΎΠ½ΠΈΡΠΎΠ²Π°Π½ΠΈΡ ΡΠ²Π΅Π»ΠΈΡΠΈΠ²Π°Π΅ΡΡΡ. Π Π»Π΅ΡΠ½ΠΈΠΉ ΠΏΠ΅ΡΠΈΠΎΠ΄, ΠΏΡΠΈ ΡΠ΅ΠΌΠΏΠ΅ΡΠ°ΡΡΡΠ΅ ΡΠ²ΡΡΠ΅ 20Β°Π‘ Π²ΡΠ΅ΠΌΡ ΠΊΠΎΠ½Π΄ΠΈΡΠΈΠΎΠ½ΠΈΡΠΎΠ²Π°Π½ΠΈΡ ΡΠΎΠΊΡΠ°ΡΠ°ΡΡ, Π° ΠΏΡΠΈ Π±ΠΎΠ»Π΅Π΅ Π½ΠΈΠ·ΠΊΠΈΡ ΡΠ΅ΠΌΠΏΠ΅ΡΠ°ΡΡΡΠ°Ρ β ΠΏΡΠΎΠ΄Π»Π΅Π²Π°ΡΡ.
ΠΡΠΈ ΡΡΠ°Π½ΡΠΏΠΎΡΡΠΈΡΠΎΠ²ΠΊΠ΅ ΡΠ²Π΅ΠΆΠΈΡ Π³ΡΠ°Π½ΡΠ» Π² ΡΠΈΠ»ΠΎΡΡ, ΠΈΡ ΠΌΠ½ΠΈΠΌΠ°Ρ ΠΏΠ»ΠΎΡΠ½ΠΎΡΡΡ ΡΠ²Π΅Π»ΠΈΡΠΈΠ²Π°Π΅ΡΡΡ Π² ΡΠ΅Π·ΡΠ»ΡΡΠ°ΡΠ΅ ΡΡΠΎΠ»ΠΊΠ½ΠΎΠ²Π΅Π½ΠΈΠΉ ΡΠΎ ΡΡΠ΅Π½ΠΊΠ°ΠΌΠΈ ΡΡΡΠ±ΠΎΠΏΡΠΎΠ²ΠΎΠ΄Π°. ΠΠΎΡΡΠΎΠΌΡ ΠΏΡΠΈ ΡΡΡΠ°Π½ΠΎΠ²ΠΊΠ΅ ΠΏΠ°ΡΠ°ΠΌΠ΅ΡΡΠΎΠ² Π²ΡΠΏΠ΅Π½ΠΈΠ²Π°Π½ΠΈΡ Π½Π΅ΠΎΠ±Ρ ΠΎΠ΄ΠΈΠΌΠΎ ΡΡΠΈΡΡΠ²Π°ΡΡ ΡΠ²Π΅Π»ΠΈΡΠ΅Π½ΠΈΠ΅ ΠΏΠ»ΠΎΡΠ½ΠΎΡΡΠΈ ΠΏΡΠΈ ΡΡΠ°Π½ΡΠΏΠΎΡΡΠΈΡΠΎΠ²ΠΊΠ΅.
3. Π€ΠΠ ΠΠΠΠΠΠΠ ΠΠΠΠΠΠΠΠΠ‘Π’ΠΠ ΠΠΠ¬ΠΠ«Π₯ ΠΠΠΠΠΠ
3.1. Π₯Π°ΡΠ°ΠΊΡΠ΅ΡΠΈΡΡΠΈΠΊΠ° ΠΏΡΠΎΡΠ΅ΡΡΠ° ΡΠΎΡΠΌΠΎΠ²Π°Π½ΠΈΡ
ΠΡΠΈ Π²ΡΡΠ°Π±ΠΎΡΠΊΠ΅ Π±Π»ΠΎΠΊΠΎΠ² Π²ΡΠΏΠ΅Π½Π΅Π½Π½ΡΠ΅ Π³ΡΠ°Π½ΡΠ»Ρ ΡΠ²ΠΎΠ±ΠΎΠ΄Π½ΠΎ Π·Π°ΡΡΠΏΠ°ΡΡ Π² ΠΊΠ°ΠΌΠ΅ΡΡ ΡΠΎΡΠΌΡ Π΄ΠΎ Π΅Π΅ ΠΏΠΎΠ»Π½ΠΎΠ³ΠΎ Π½Π°ΠΏΠΎΠ»Π½Π΅Π½ΠΈΡ. ΠΠ°ΡΠ΅ΠΌ Π² ΡΠΎΡΠΌΡ ΠΏΠΎΠ΄Π°ΡΡ Π½Π°ΡΡΡΠ΅Π½Π½ΡΠΉ ΡΡΡ ΠΎΠΉ Π²ΠΎΠ΄ΡΠ½ΠΎΠΉ ΠΏΠ°Ρ ΠΏΠΎΠ΄ Π΄Π°Π²Π»Π΅Π½ΠΈΠ΅ΠΌ 0,2-0,4 ΠΠΠ°, ΡΡΠΎ ΠΏΡΠΈΠ²ΠΎΠ΄ΠΈΡ ΠΊ Π΄Π°Π»ΡΠ½Π΅ΠΉΡΠ΅ΠΌΡ ΡΠ²Π΅Π»ΠΈΡΠ΅Π½ΠΈΡ ΠΎΠ±ΡΠ΅ΠΌΠ° Π³ΡΠ°Π½ΡΠ». Π ΡΠ²ΡΠ·ΠΈ Ρ ΡΠ΅ΠΌ, ΡΡΠΎ Π³ΡΠ°Π½ΡΠ»Ρ Π½Π°Ρ ΠΎΠ΄ΡΡΡΡ Π² Π·Π°ΠΊΡΡΡΠΎΠΉ ΠΊΠ°ΠΌΠ΅ΡΠ΅, ΡΠ½Π°ΡΠ°Π»Π° Π·Π°ΠΏΠΎΠ»Π½ΡΠ΅ΡΡΡ ΡΠ²ΠΎΠ±ΠΎΠ΄Π½ΠΎΠ΅ ΠΏΡΠΎΡΡΡΠ°Π½ΡΡΠ²ΠΎ ΠΌΠ΅ΠΆΠ΄Ρ Π½ΠΈΠΌΠΈ, Π° Π·Π°ΡΠ΅ΠΌ Π³ΡΠ°Π½ΡΠ»Ρ ΡΡΠ΅ΠΏΠ»ΡΡΡΡΡ Π΄ΡΡΠ³ Ρ Π΄ΡΡΠ³ΠΎΠΌ.
Π ΠΈΡ.3.1.1. ΠΡΠΈΠΌΠ΅Ρ ΡΠ°Π·ΠΎΠ²ΠΎΠ³ΠΎ ΡΠΈΠΊΠ»Π° ΡΠΎΡΠΌΠΎΠ²Π°Π½ΠΈΡ Π±Π»ΠΎΠΊΠΎΠ² Π±Π΅Π· ΠΈΡΠΏΠΎΠ»ΡΠ·ΠΎΠ²Π°Π½ΠΈΡ Π²Π°ΠΊΡΡΠΌΠ°
1) Π½Π°ΠΏΠΎΠ»Π½Π΅Π½ΠΈΠ΅ 2) ΠΏΡΠΎΠ΄ΡΠ²Π°Π½ΠΈΠ΅ 3) Π·Π°ΠΏΠ°ΡΠΈΠ²Π°Π½ΠΈΠ΅ 4) ΠΎΡ Π»Π°ΠΆΠ΄Π΅Π½ΠΈΠ΅ 5) ΡΠ°ΡΡΠΎΡΠΌΠΎΠ²ΠΊΠ°
Π ΠΈΡ.3.1.2. ΠΡΠΈΠΌΠ΅Ρ ΡΠ°Π·ΠΎΠ²ΠΎΠ³ΠΎ ΡΠΈΠΊΠ»Π° ΡΠΎΡΠΌΠΎΠ²Π°Π½ΠΈΡ Π±Π»ΠΎΠΊΠΎΠ² Ρ ΠΈΡΠΏΠΎΠ»ΡΠ·ΠΎΠ²Π°Π½ΠΈΠ΅ΠΌ Π²Π°ΠΊΡΡΠΌΠ°
1) Π½Π°ΠΏΠΎΠ»Π½Π΅Π½ΠΈΠ΅ 2) Π²Π°ΠΊΡΡΠΌ 3) ΠΏΡΠΎΠ΄ΡΠ²Π°Π½ΠΈΠ΅ 4) Π·Π°ΠΏΠ°ΡΠΈΠ²Π°Π½ΠΈΠ΅ β ΡΠΎΡΡ | 5) Π·Π°ΠΏΠ°ΡΠΈΠ²Π°Π½ΠΈΠ΅ β Π²ΡΠ΄Π΅ΡΠΆΠΊΠ° 6) Π²ΡΠΏΡΡΠΊ 7) Π²Π°ΠΊΡΡΠΌΠ½ΠΎΠ΅ ΠΎΡ Π»Π°ΠΆΠ΄Π΅Π½ΠΈΠ΅ 8) ΡΠ°Π·Π³ΡΡΠ·ΠΊΠ° |
ΠΠ°ΠΆΠ½ΡΠΌ ΡΠ°ΠΊΡΠΎΡΠΎΠΌ ΠΏΡΠΈ Π·Π°ΠΏΠ°ΡΠΈΠ²Π°Π½ΠΈΠΈ Π±Π»ΠΎΠΊΠ° ΡΠ²Π»ΡΠ΅ΡΡΡ ΠΏΠΎΠ΄Π°ΡΠ° Π² ΠΊΠ°ΠΌΠ΅ΡΡ Π² ΡΠ²ΠΎΠ±ΠΎΠ΄Π½ΠΎΠ΅ ΠΏΡΠΎΡΡΡΠ°Π½ΡΡΠ²ΠΎ ΠΌΠ΅ΠΆΠ΄Ρ Π³ΡΠ°Π½ΡΠ»Π°ΠΌΠΈ ΡΠΎΠΎΡΠ²Π΅ΡΡΡΠ²ΡΡΡΠ΅Π³ΠΎ ΠΊΠΎΠ»ΠΈΡΠ΅ΡΡΠ²Π° ΠΏΠ°ΡΠ° Π² ΠΊΡΠ°ΡΡΠ°ΠΉΡΠ΅Π΅ Π²ΡΠ΅ΠΌΡ. ΠΠ»Ρ ΡΡΠΎΠ³ΠΎ Π½Π΅ΠΎΠ±Ρ ΠΎΠ΄ΠΈΠΌΠ° ΡΠΎΠΎΡΠ²Π΅ΡΡΡΠ²ΡΡΡΠ°Ρ Π²Π΅Π½ΡΠΈΠ»ΡΡΠΈΡ (ΠΏΡΠΎΠ΄ΡΠ²Π°Π½ΠΈΠ΅), ΡΠ΅Π»ΡΡ ΠΊΠΎΡΠΎΡΠΎΠΉ ΡΠ²Π»ΡΠ΅ΡΡΡ ΡΠ΄Π°Π»Π΅Π½ΠΈΠ΅ Π²ΠΎΠ·Π΄ΡΡ Π° ΠΏΠ΅ΡΠ΅Π΄ Π½Π°ΡΠ°Π»ΠΎΠΌ ΠΏΡΠΎΡΠ΅ΡΡΠ° Π·Π°ΠΏΠ°ΡΠΈΠ²Π°Π½ΠΈΡ. ΠΠ΅Π΄ΠΎΡΡΠ°ΡΠΎΡΠ½Π°Ρ ΠΏΡΠΎΠ΄ΠΎΠ»ΠΆΠΈΡΠ΅Π»ΡΠ½ΠΎΡΡΡ ΠΏΡΠΎΠ΄ΡΠ²Π°Π½ΠΈΡ ΠΏΡΠΈΠ²ΠΎΠ΄ΠΈΡ ΠΊ Π½Π΅ΠΎΠ΄Π½ΠΎΡΠΎΠ΄Π½ΠΎΠΉ ΠΏΠ»ΠΎΡΠ½ΠΎΡΡΠΈ ΠΈ ΠΏΠ»ΠΎΡ ΠΎΠΌΡ ΡΠΏΠ΅ΠΊΠ°Π½ΠΈΡ Π±Π»ΠΎΠΊΠ°.
ΠΠ°ΠΆΠ½ΠΎ ΡΠ°ΠΊΠΆΠ΅ ΠΏΠΎΠ΄Π΄Π΅ΡΠΆΠΈΠ²Π°ΡΡ ΠΏΠΎΡΡΠΎΡΠ½Π½ΡΡ Π²ΡΡΠΎΠΊΡΡ ΡΠ΅ΠΌΠΏΠ΅ΡΠ°ΡΡΡΡ ΡΠΎΡΠΌΡ, Π² ΠΏΡΠΎΡΠΈΠ²Π½ΠΎΠΌ ΡΠ»ΡΡΠ°Π΅ Π·Π½Π°ΡΠΈΡΠ΅Π»ΡΠ½ΠΎ ΡΠ°ΡΡΠ΅Ρ ΡΠ°ΡΡ ΠΎΠ΄ ΠΏΠ°ΡΠ° (ΡΠΈΡ.3.1.3) ΠΈ ΠΏΠ°Ρ ΡΡΠ°Π½ΠΎΠ²ΠΈΡΡΡ ΠΌΠΎΠΊΡΡΠΌ, ΡΡΠΎ ΡΠ½ΠΈΠΆΠ°Π΅Ρ ΠΊΠ°ΡΠ΅ΡΡΠ²ΠΎ ΡΡΠ΅ΠΏΠ»Π΅Π½ΠΈΡ Π³ΡΠ°Π½ΡΠ».

ΠΠ°Π²Π»Π΅Π½ΠΈΠ΅, ΠΊΠΎΡΠΎΡΠΎΠ΅ Π±Π»ΠΎΠΊ ΠΎΠΊΠ°Π·ΡΠ²Π°Π΅Ρ Π½Π° Π²Π½ΡΡΡΠ΅Π½Π½ΠΈΠ΅ ΡΡΠ΅Π½ΠΊΠΈ ΡΠΎΡΠΌΠΎΠ²ΠΎΡΠ½ΠΎΠΉ ΠΊΠ°ΠΌΠ΅ΡΡ, ΡΠΎΡΡΠ°Π²Π»ΡΠ΅Ρ ΠΏΡΠΈΠΌΠ΅ΡΠ½ΠΎ 0,08 ΠΠΠ°. ΠΠ»Ρ ΡΠΎΠ³ΠΎ, ΡΡΠΎΠ±Ρ Π±Π»ΠΎΠΊ ΠΌΠΎΠΆΠ½ΠΎ Π±ΡΠ»ΠΎ Π²ΡΠ½ΡΡΡ ΠΈΠ· ΡΠΎΡΠΌΡ Π±Π΅Π· Π΅Π³ΠΎ ΠΏΠΎΠ²ΡΠ΅ΠΆΠ΄Π΅Π½ΠΈΡ, ΡΡΠΎ Π΄Π°Π²Π»Π΅Π½ΠΈΠ΅ Π½Π΅ΠΎΠ±Ρ
ΠΎΠ΄ΠΈΠΌΠΎ ΡΠΌΠ΅Π½ΡΡΠΈΡΡ Π΄ΠΎ Π²Π΅Π»ΠΈΡΠΈΠ½Ρ ΠΎΠΊΠΎΠ»ΠΎ 0,01 ΠΠΠ°. ΠΡΠ΅ΠΌΡ, Π½Π΅ΠΎΠ±Ρ
ΠΎΠ΄ΠΈΠΌΠΎΠ΅ Π΄Π»Ρ ΡΠΌΠ΅Π½ΡΡΠ΅Π½ΠΈΡ Π΄Π°Π²Π»Π΅Π½ΠΈΡ Π±Π»ΠΎΠΊΠ°, ΡΠΎ Π΅ΡΡΡ Π²ΡΠ΅ΠΌΡ ΠΎΡ
Π»Π°ΠΆΠ΄Π΅Π½ΠΈΡ, Π·Π°Π²ΠΈΡΠΈΡ ΠΎΡ ΠΌΠ°ΡΠΊΠΈ ΠΏΠ΅Π½ΠΎΠΏΠ»Π°ΡΡΠ°.

Π ΠΈΡ.3.1.4. ΠΡΠΈΠΌΠ΅ΡΠ½ΠΎΠ΅ Π²ΡΠ΅ΠΌΡ ΠΎΡ Π»Π°ΠΆΠ΄Π΅Π½ΠΈΡ Π±Π»ΠΎΠΊΠ° Π² Π·Π°Π²ΠΈΡΠΈΠΌΠΎΡΡΠΈ ΠΎΡ ΠΏΡΠΎΠ΄ΠΎΠ»ΠΆΠΈΡΠ΅Π»ΡΠ½ΠΎΡΡΠΈ ΠΊΠΎΠ½Π΄ΠΈΡΠΈΠΎΠ½ΠΈΡΠΎΠ²Π°Π½ΠΈΡ
Π ΡΠ°Π·Π΅ ΠΏΡΠΎΠ΄ΡΠ²Π°Π½ΠΈΡ ΠΈ ΠΎΡ Π»Π°ΠΆΠ΄Π΅Π½ΠΈΡ ΠΏΡΠΈΠΌΠ΅Π½ΡΠ΅ΡΡΡ Π²Π°ΠΊΡΡΠΌ Ρ ΡΠ΅Π»ΡΡ ΠΈΠ½ΡΠ΅Π½ΡΠΈΡΠΈΠΊΠ°ΡΠΈΠΈ ΠΏΡΠΎΡΠ΅ΡΡΠ° Π·Π°ΠΏΠ°ΡΠΈΠ²Π°Π½ΠΈΡ ΠΈ ΡΡΠΊΠΎΡΠ΅Π½ΠΈΡ ΠΏΡΠΎΡΠ΅ΡΡΠ° ΠΎΡ Π»Π°ΠΆΠ΄Π΅Π½ΠΈΡ.
3.2. Π’Π΅Ρ Π½ΠΈΡΠ΅ΡΠΊΠΎΠ΅ ΠΎΡΠ½Π°ΡΠ΅Π½ΠΈΠ΅ ΡΠ·Π»Π° ΡΠΎΡΠΌΠΎΠ²Π°Π½ΠΈΡ
a) Π±Π»ΠΎΠΊ ΡΠΎΡΠΌΠ° Π£Π¦ΠΠ 1030.
b) ΡΡΡΠ°Π½ΠΎΠ²ΠΊΠ° Π²Π°ΠΊΡΡΠΌΠΈΡΠΎΠ²Π°Π½ΠΈΡ ΠΠ£-3,3 Ρ Π°ΠΊΠΊΡΠΌΡΠ»ΡΡΠΎΡΠΎΠΌ Π²Π°ΠΊΡΡΠΌΠ° ΠΠ-1.
c) ΡΠΈΡΡΠ΅ΠΌΠ° Π²Π°ΠΊΡΡΠΌΠ½ΠΎΠΉ Π·Π°Π³ΡΡΠ·ΠΊΠΈ ΠΈ ΠΎΡ Π»Π°ΠΆΠ΄Π΅Π½ΠΈΡ Π±Π»ΠΎΠΊΠΎΠ².
d) ΠΊΠΎΠΌΠΏΡΠ΅ΡΡΠΎΡΠ½Π°Ρ ΡΡΡΠ°Π½ΠΎΠ²ΠΊΠ° Π‘Π4/Π€-500
e) Π°ΠΊΠΊΡΠΌΡΠ»ΡΡΠΎΡ ΠΏΠ°ΡΠ° ΠΠ-5000
f) ΠΊΠΎΡΠ΅Π» ΠΏΠ°ΡΠΎΠ²ΠΎΠΉ
4. ΠΠΠΠΠΠ¦ΠΠΠΠΠ ΠΠΠΠΠΠ ΠΠΠΠΠΠ
4.1. ΠΡΠ°ΡΠΊΠ°Ρ Ρ Π°ΡΠ°ΠΊΡΠ΅ΡΠΈΡΡΠΈΠΊΠ° ΠΏΡΠΎΡΠ΅ΡΡΠ° ΠΊΠΎΠ½Π΄ΠΈΡΠΈΠΎΠ½ΠΈΡΠΎΠ²Π°Π½ΠΈΡ Π±Π»ΠΎΠΊΠΎΠ²
ΠΠΎΡΠ»Π΅ ΠΎΠΊΠΎΠ½ΡΠ°Π½ΠΈΡ ΠΏΡΠΎΡΠ΅ΡΡΠ° ΡΠΎΡΠΌΠΎΠ²Π°Π½ΠΈΡ Π±Π»ΠΎΠΊΠΈ ΠΊΠΎΠ½Π΄ΠΈΡΠΈΠΎΠ½ΠΈΡΡΡΡ. ΠΠΎΠ½Π΄ΠΈΡΠΈΠΎΠ½ΠΈΡΠΎΠ²Π°Π½ΠΈΠ΅ ΠΏΡΠΎΠ²ΠΎΠ΄ΠΈΡΡΡ Ρ ΡΠ΅Π»ΡΡ ΡΠ½ΠΈΠΆΠ΅Π½ΠΈΡ Π²Π»Π°ΠΆΠ½ΠΎΡΡΠΈ ΠΈ ΡΡΡΡΠ°Π½Π΅Π½ΠΈΡ Π²Π½ΡΡΡΠ΅Π½Π½ΠΈΡ Π½Π°ΠΏΡΡΠΆΠ΅Π½ΠΈΠΉ, Π²ΠΎΠ·Π½ΠΈΠΊΠ°ΡΡΠΈΡ ΠΏΡΠΈ ΡΠΎΡΠΌΠΎΠ²Π°Π½ΠΈΠΈ. ΠΡΠΎΠΌΠ΅ ΡΠΎΠ³ΠΎ, ΠΏΡΠΈ ΡΡΠΎΠΌ ΠΏΡΠΎΡΠ΅ΠΊΠ°ΡΡ ΠΏΡΠΎΡΠ΅ΡΡΡ Π΄ΠΈΡΡΡΠ·ΠΈΠΈ Π³Π°Π·ΠΎΠ² ΠΈ Π²ΡΡΠ°Π²Π½ΠΈΠ²Π°Π½ΠΈΡ Π΄Π°Π²Π»Π΅Π½ΠΈΡ Π²Π½ΡΡΡΠΈ Π³ΡΠ°Π½ΡΠ» Ρ Π°ΡΠΌΠΎΡΡΠ΅ΡΠ½ΡΠΌ Π΄Π°Π²Π»Π΅Π½ΠΈΠ΅ΠΌ, ΠΏΠΎΠ΄ΠΎΠ±Π½ΡΠ΅ ΠΏΡΠΎΡΠ΅ΡΡΠ°ΠΌ, ΠΏΡΠΎΠΈΡΡ ΠΎΠ΄ΡΡΠΈΠΌ ΠΏΡΠΈ ΠΊΠΎΠ½Π΄ΠΈΡΠΈΠΎΠ½ΠΈΡΠΎΠ²Π°Π½ΠΈΠΈ ΠΏΡΠ΅Π΄Π²Π°ΡΠΈΡΠ΅Π»ΡΠ½ΠΎ Π²ΡΠΏΠ΅Π½Π΅Π½Π½ΡΡ Π³ΡΠ°Π½ΡΠ».
Π ΠΏΡΠΎΡΠ΅ΡΡΠ΅ ΠΊΠΎΠ½Π΄ΠΈΡΠΈΠΎΠ½ΠΈΡΠΎΠ²Π°Π½ΠΈΡ Π±Π»ΠΎΠΊΠΎΠ² ΠΎΡΠ΅Π½Ρ Π²Π°ΠΆΠ½ΡΡ ΡΠΎΠ»Ρ ΠΈΠ³ΡΠ°Π΅Ρ ΠΎΡΠ΅ΡΠ΅Π΄Π½ΠΎΡΡΡ ΠΈΡ ΠΈΡΠΏΠΎΠ»ΡΠ·ΠΎΠ²Π°Π½ΠΈΡ, ΡΠΎΠΎΡΠ²Π΅ΡΡΡΠ²ΡΡΡΠ°Ρ ΠΎΡΠ΅ΡΠ΅Π΄Π½ΠΎΡΡΠΈ ΡΠΎΡΠΌΠΎΠ²Π°Π½ΠΈΡ, ΡΠΎ Π΅ΡΡΡ ΠΏΡΠΈ ΠΎΡΠ±ΠΎΡΠ΅ Π±Π»ΠΎΠΊΠΎΠ² Π΄Π»Ρ ΡΠ°Π·ΡΠ΅Π·Π°Π½ΠΈΡ ΡΠ»Π΅Π΄ΡΠ΅Ρ Π½Π°ΡΠΈΠ½Π°ΡΡ Ρ ΡΠ°ΠΌΡΡ Β«ΡΡΠ°ΡΡΡ Β».
5. Π ΠΠΠ ΠΠΠΠΠΠ ΠΠΠΠΠΠΠΠΠ‘Π’ΠΠ ΠΠΠΠΠ«Π₯ ΠΠΠΠΠΠ ΠΠ ΠΠΠΠ’Π«
5.1. Π₯Π°ΡΠ°ΠΊΡΠ΅ΡΠΈΡΡΠΈΠΊΠ° ΠΏΡΠΎΡΠ΅ΡΡΠ° ΡΠ΅Π·ΠΊΠΈ ΠΏΠ΅Π½ΠΎΠΏΠΎΠ»ΠΈΡΡΠΈΡΠΎΠ»Π°
Π Π°Π·ΡΠ΅Π·Π°Π½ΠΈΠ΅ Π±Π»ΠΎΠΊΠΎΠ² ΠΎΡΡΡΠ΅ΡΡΠ²Π»ΡΠ΅ΡΡΡ Ρ ΠΏΠΎΠΌΠΎΡΡΡ ΡΠ΅ΠΎΡΡΠ°ΡΠ½ΠΎΠΉ ΠΏΡΠΎΠ²ΠΎΠ»ΠΎΠΊΠΈ, Π½Π°Π³ΡΠ΅ΡΠΎΠΉ Π΄ΠΎ ΡΠΎΠΎΡΠ²Π΅ΡΡΠ²ΡΡΡΠ΅ΠΉ ΡΠ΅ΠΌΠΏΠ΅ΡΠ°ΡΡΡΡ.
ΠΡΠ΅ ΠΎΡΡ ΠΎΠ΄Ρ ΠΏΠΎΠ΄Π°ΡΡΡΡ Π² ΠΈΠ·ΠΌΠ΅Π»ΡΡΠΈΡΠ΅Π»Ρ, ΠΎΡΠΊΡΠ΄Π° Π² ΠΈΠ·ΠΌΠ΅Π»ΡΡΠ΅Π½Π½ΠΎΠΌ Π²ΠΈΠ΄Π΅ ΠΏΠ½Π΅Π²ΠΌΠ°ΡΠΈΡΠ΅ΡΠΊΠΈ ΡΡΠ°Π½ΡΠΏΠΎΡΡΠΈΡΡΡΡΡΡ Π½Π° Π²ΡΠΎΡΠΈΡΠ½ΠΎΠ΅ ΠΈΡΠΏΠΎΠ»ΡΠ·ΠΎΠ²Π°Π½ΠΈΠ΅.
5.2. Π’ΡΠ΅Π±ΠΎΠ²Π°Π½ΠΈΡ ΠΏΠΎ ΠΊΠ°ΡΠ΅ΡΡΠ²Ρ
ΠΠ½Π΅ΡΠ½ΠΈΠΉ Π²ΠΈΠ΄
ΠΠΊΡΠ°ΡΠΊΠ° ΠΏΠ΅Π½ΠΎΠΏΠΎΠ»ΠΈΡΡΠΈΡΠΎΠ»ΠΎΠ²ΡΡ ΠΏΠ»ΠΈΡ Π΄ΠΎΠ»ΠΆΠ½Π° Π±ΡΡΡ ΡΠ°ΠΊΠΎΠΉ ΠΆΠ΅, ΠΊΠ°ΠΊ ΠΎΠΊΡΠ°ΡΠΊΠ° ΠΏΡΠ΅Π΄Π²Π°ΡΠΈΡΠ΅Π»ΡΠ½ΠΎ Π²ΡΠΏΠ΅Π½Π΅Π½Π½ΡΡ Π³ΡΠ°Π½ΡΠ» ΠΏΠΎΠ»ΠΈΡΡΠΈΡΠΎΠ»Π°.
ΠΠ΅ΠΎΠ±Ρ ΠΎΠ΄ΠΈΠΌΠΎ ΠΏΡΠΎΠ²ΠΎΠ΄ΠΈΡΡ Π²ΡΠ±ΠΎΡΠΎΡΠ½ΡΡ ΠΏΡΠΎΠ²Π΅ΡΠΊΡ ΠΏΠ»ΠΈΡ β ΠΏΠΎ ΠΊΡΠ°ΠΉΠ½Π΅ΠΉ ΠΌΠ΅ΡΠ΅ 2 ΡΡ. Π½Π° Π΄Π»ΠΈΠ½Π΅ ΠΊΠ°ΠΆΠ΄ΠΎΠ³ΠΎ Π±Π»ΠΎΠΊΠ°.
ΠΡΠ»ΠΈ ΠΏΠ»ΠΈΡΡ ΠΎΡΠ²Π΅ΡΠ°ΡΡ ΠΏΡΠ΅Π΄ΡΡΠ²Π»ΡΠ΅ΠΌΡΠΌ ΡΡΠ΅Π±ΠΎΠ²Π°Π½ΠΈΡΠΌ, ΡΠΎ ΠΏΠΎΡΠ»Π΅ ΡΠΊΠ»Π°Π΄ΠΊΠΈ Π² ΡΡΠΎΠΏΠΊΠΈ ΠΎΠ½ΠΈ Π½Π°ΠΏΡΠ°Π²Π»ΡΡΡΡΡ Π½Π° ΡΠΏΠ°ΠΊΠΎΠ²ΠΊΡ.
ΠΡΠ»ΠΈ ΠΎΡΠΊΠ»ΠΎΠ½Π΅Π½ΠΈΠ΅ ΠΎΡ ΡΡΠ΅Π±ΡΠ΅ΠΌΡΡ ΡΠ°Π·ΠΌΠ΅ΡΠΎΠ² ΠΏΡΠ΅Π²ΡΡΠ°Π΅Ρ Π΄ΠΎΠΏΡΡΡΠΈΠΌΡΡ Π²Π΅Π»ΠΈΡΠΈΠ½Ρ, ΡΠΎ ΡΠ»Π΅Π΄ΡΠ΅Ρ Π΅ΡΠ΅ ΡΠ°Π· ΠΏΡΠΎΠ²Π΅ΡΠΈΡΡ ΠΏΠΎ ΠΎΠ΄Π½ΠΎΠΉ ΠΏΠ»ΠΈΡΠ΅ Π½Π° Π²ΡΠ΅ΠΉ Π΄Π»ΠΈΠ½Π΅ Π±Π»ΠΎΠΊΠ°, ΠΎΠΏΡΠ΅Π΄Π΅Π»ΠΈΡΡ ΠΏΡΠΈΡΠΈΠ½Ρ, ΠΏΡΠΎΠΈΠ·Π²Π΅ΡΡΠΈ ΡΠΎΠΎΡΠ²Π΅ΡΡΡΠ²ΡΡΡΡΡ ΠΊΠΎΡΡΠ΅ΠΊΡΠΈΡΠΎΠ²ΠΊΡ ΠΏΡΠΎΠΌΠ΅ΠΆΡΡΠΊΠΎΠ² ΠΌΠ΅ΠΆΠ΄Ρ ΠΎΡΡΠ΅Π·ΠΊΠ°ΠΌΠΈ ΡΠ΅ΠΎΡΡΠ°ΡΠ½ΠΎΠΉ ΠΏΡΠΎΠ²ΠΎΠ»ΠΎΠΊΠΈ.
ΠΡΠΎΠ²Π΅ΡΠΈΡΡ ΡΠ°ΠΊΠΈΠΌ ΠΆΠ΅ ΠΎΠ±ΡΠ°Π·ΠΎΠΌ ΡΠ°Π·ΠΌΠ΅ΡΡ ΠΏΠ»ΠΈΡ, ΠΏΠΎΠ»ΡΡΠ΅Π½Π½ΡΡ Π² ΡΠ΅Π·ΡΠ»ΡΡΠ°ΡΠ΅ ΡΠ°Π·ΡΠ΅Π·Π°Π½ΠΈΡ ΡΠ»Π΅Π΄ΡΡΡΠ΅Π³ΠΎ Π±Π»ΠΎΠΊΠ°.
ΠΠ»ΠΈΡΡ, ΠΊΠΎΡΠΎΡΡΠ΅ Π½Π΅ ΠΎΡΠ²Π΅ΡΠ°ΡΡ ΠΏΡΠ΅Π΄ΡΡΠ²Π»ΡΠ΅ΠΌΡΠΌ ΡΡΠ΅Π±ΠΎΠ²Π°Π½ΠΈΡΠΌ, Π½Π°ΠΏΡΠ°Π²Π»ΡΡΡΡΡ Π½Π° Π²ΡΠΎΡΠΈΡΠ½ΠΎΠ΅ ΠΈΡΠΏΠΎΠ»ΡΠ·ΠΎΠ²Π°Π½ΠΈΠ΅.
6. ΠΠ‘ΠΠΠΠ¬ΠΠΠΠΠΠΠ ΠΠΠΠΠΠΠΠΠ‘Π’ΠΠ ΠΠΠ¬ΠΠ«Π₯ ΠΠ’Π₯ΠΠΠΠ
ΠΡΡ ΠΎΠ΄Ρ ΠΈΡΠΏΠΎΠ»ΡΠ·ΡΠ΅ΡΡΡ Π²ΡΠΎΡΠΈΡΠ½ΠΎ Π² ΠΏΡΠΎΠΈΠ·Π²ΠΎΠ΄ΡΡΠ²Π΅ Π±Π»ΠΎΠΊΠΎΠ².
6.1. Π’Π΅Ρ Π½ΠΈΡΠ΅ΡΠΊΠΎΠ΅ ΠΎΡΠ½Π°ΡΠ΅Π½ΠΈΠ΅ ΡΠ·Π»Π°
a) Π΄ΡΠΎΠ±ΠΈΠ»ΠΊΠ° ΠΏΠ΅Π½ΠΎΠΏΠΎΠ»ΠΈΡΡΠΈΡΠΎΠ»ΡΠ½ΡΡ ΠΎΡΡ ΠΎΠ΄ΠΎΠ²
b) ΡΠ΅Ρ Π½ΠΎΠ»ΠΎΠ³ΠΈΡΠ΅ΡΠΊΠΈΠΉ ΡΠΈΠ»ΠΎΡ
6.2. Π‘ΠΈΡΡΠ΅ΠΌΠ° ΠΈΠ·ΠΌΠ΅Π»ΡΡΠ΅Π½ΠΈΡ
Π£ΡΡΡΠΎΠΉΡΡΠ²ΠΎ ΠΏΡΠ΅Π΄Π½Π°Π·Π½Π°ΡΠ΅Π½ΠΎ Π΄Π»Ρ ΠΈΠ·ΠΌΠ΅Π»ΡΡΠ΅Π½ΠΈΡ ΠΏΠ΅Π½ΠΎΠΏΠΎΠ»ΠΈΡΡΠΈΡΠΎΠ»ΠΎΠ²ΡΡ ΠΎΡΡ ΠΎΠ΄ΠΎΠ², Π² ΡΠ΅Π·ΡΠ»ΡΡΠ°ΡΠ΅ ΡΠ΅Π³ΠΎ ΠΏΠΎΠ»ΡΡΠ°ΡΡ ΠΊΡΠΎΡΠΊΡ, ΠΈΡΠΏΠΎΠ»ΡΠ·ΡΠ΅ΠΌΡΡ Π² ΠΊΠ°ΡΠ΅ΡΡΠ²Π΅ Π΄ΠΎΠ±Π°Π²ΠΊΠΈ ΠΊ Π³ΡΠ°Π½ΡΠ»Π°ΠΌ ΠΏΠΎΠ»ΠΈΡΡΠΈΡΠΎΠ»Π° ΠΏΡΠΈ ΠΏΡΠΎΠΈΠ·Π²ΠΎΠ΄ΡΡΠ²Π΅ ΠΏΠ΅Π½ΠΎΠΏΠΎΠ»ΠΈΡΡΠΈΡΠΎΠ»ΠΎΠ²ΡΡ Π±Π»ΠΎΠΊΠΎΠ². Π Π°Π·ΠΌΠ΅ΡΡ ΠΏΠΎΠ»ΡΡΠ°Π΅ΠΌΠΎΠΉ ΡΠ°ΠΊΠΈΠΌ ΠΎΠ±ΡΠ°Π·ΠΎΠΌ ΠΊΡΠΎΡΠΊΠΈ ΡΠΎΡΡΠ°Π²Π»ΡΡΡ Π΄ΠΎ 15 ΠΌΠΌ.
ΠΠ½ΡΠ΅ΡΠ΅ΡΠ½ΠΎ? ΠΡΡΠ°Π²ΡΡΠ΅ Π·Π°ΠΊΠ»Π°Π΄ΠΊΡ, ΡΡΠΎ Π±Ρ Π²Π΅ΡΠ½ΡΡΡΡΡ ΡΡΠ΄Π° ΠΏΠΎΠ·ΠΆΠ΅!
ΠΠ΅Π½ΠΎΠΏΠ»Π°ΡΡΠΎΠ²Π°Ρ ΠΌΠΎΠ΄Π΅Π»Ρ — ΠΠΈΡΠ΅ΠΉΠ½ΡΠΉ ΡΠ΅Ρ
ΠΠ²Π° Π΄Π½Ρ ΡΠΆΠ΅ ΠΈΠ³ΡΠ°ΡΡΡ Π² ΠΏΡΠΎΠΈΠ·Π²ΠΎΠ΄ΡΡΠ²ΠΎ ΠΏΠ΅Π½ΠΎΠΏΠΎΠ»ΠΈΡΡΠΈΡΠΎΠ»ΠΎΠ²ΡΡ ΠΌΠΎΠ΄Π΅Π»Π΅ΠΉ.
Β
Π Π΅ΠΆΠΈΠΌ ΡΠ΅ΡΠΌΠΎΠΎΠ±ΡΠ°Π±ΠΎΡΠΊΠΈ ΡΠΎΠΆΠ΅ Π·Π°Π²ΠΈΡΠΈΡ ΠΎΡ ΠΌΠ°ΡΠΊΠΈ ΠΏΠΎΠ»ΠΈΡΡΠΈΡΠΎΠ»Π° ΠΈ ΠΏΡΠΎΠΈΠ·Π²ΠΎΠ΄ΠΈΡΠ΅Π»Ρ, ΠΈΡΠΈ ΡΠ΅Ρ Π½ΠΎΠ»ΠΎΠ³ΠΈΡΠ΅ΡΠΊΠΈΠ΅ ΡΠ΅ΠΊΠΎΠΌΠ΅Π½Π΄Π°ΡΠΈΠΈ ΠΏΠΎ ΠΌΠ°ΡΠΊΠ΅ Π² ΠΈΠ½ΡΠ΅ΡΠ½Π΅ΡΠ΅.
Β
ΠΠ°Π»ΡΡΠ΅ ΠΌΠΎΠΆΠ΅ΡΡ ΠΏΠΎΠΉΡΠΈ ΠΈ ΠΊΡΠΏΠΈΡΡ ΠΎΠ±ΡΡΠ½ΡΡ Π±ΡΡΠΎΠ²ΡΡ ΡΠΊΠΎΡΠΎΠ²Π°ΡΠΊΡ( Π½Π΅ ΠΏΡΡΠ°ΡΡ Ρ ΠΏΠ°ΡΠΎΠ²Π°ΡΠΊΠΎΠΉ) — ΡΡΠΎ Π±ΡΠ΄Π΅Ρ ΡΠ΅Π±Π΅ Π±ΡΠ΄ΠΆΠ΅ΡΠ½ΡΠΉ Π°Π²ΡΠΎΠΊΠ»Π°Π² π
ΠΠ΅Π»Π°ΡΠ΅Π»ΡΠ½ΠΎ Π΅Ρ Π½Π΅ΠΌΠ½ΠΎΠ³ΠΎ Π΄ΠΎΡΠ°Π±ΠΎΡΠ°ΡΡ ΠΈ ΡΠ½ΠΈΠ·ΠΈΡΡ ΡΠ΅ΠΌΠΏΠ΅ΡΠ°ΡΡΡΡ ΡΠ°Π±ΠΎΡΡ ΡΠΎ 125-130 Π³ΡΠ°Π΄ΡΡΠΎΠ² Π΄ΠΎ 110, ΠΌΠ΅ΡΠΎΠ΄ΠΎΠΌ ΡΠΌΠ΅Π½ΡΡΠ΅Π½ΠΈΡ ΠΌΠ°ΡΡΡ Π³ΡΡΠ·ΠΈΠΊΠ° ΠΊΠ»Π°ΠΏΠ°Π½Π°. ΠΠΎ ΠΌΠΎΠΆΠ½ΠΎ ΠΈ Π±Π΅Π· ΠΌΠΎΠ΄Π΅ΡΠ½ΠΈΠ·Π°ΡΠΈΠΈ.
1 Π¨Π°Π³: ΠΏΡΠ΅Π΄Π²Π°ΡΠΈΡΠ΅Π»ΡΠ½ΠΎΠ΅ Π²ΡΠΏΠ΅Π½ΠΈΠ²Π°Π½ΠΈΠ΅. ΠΠ΅ΡΠ΅ΡΡ Π°Π»ΡΠΌΠΈΠ½ΠΈΠ΅Π²ΡΡ ΡΠ°ΡΠΊΡ, ΠΊΠΎΡΠΎΡΠ°Ρ ΠΏΡΠΎΠ»Π°Π·ΠΈΡ Π² ΠΆΠ΅ΡΠ»ΠΎ ΡΠΊΠΎΡΠΎΠ²Π°ΡΠΊΠΈ, Π½Π° Π΄Π½ΠΎ Π½Π°Π»ΠΈΠ²Π°Π΅ΡΡ Π²ΠΎΠ΄Ρ ΠΈ ΡΡΠ°Π²ΠΈΡΡ ΠΏΠΎΠ΄ΡΡΠ°Π²ΠΊΡ Π΄Π»Ρ ΡΠ°ΡΠΊΠΈ. Π‘ΡΠ°Π²ΠΈΡΡ Π²ΠΎ Π²Π½ΡΡΡΡ ΡΠ°ΡΠΊΡ ΠΈ Π½Π΅ Π·Π°ΠΊΡΡΠ²Π°Ρ Π°Π²ΡΠΎΠΊΠ»Π°Π²Π° ΠΆΠ΄Π΅ΡΡ Π½Π°ΡΠ°Π»Π° ΠΊΠΈΠΏΠ΅Π½ΠΈΡ. ΠΠ°ΠΊ Π·Π°ΠΊΠΈΠΏΠ΅Π»ΠΎ, ΡΡΠΏΠ΅ΡΡ Π³ΡΠ°Π½ΡΠ»Ρ, Π½Π°ΡΠΈΠ½Π°ΠΉ Ρ ΠΏΠΎΠ» ΡΡΠΎΠ»ΠΎΠ²ΠΎΠΉ Π»ΠΎΠΆΠΊΠΈ. ΠΠ°ΠΊΡΡΠ²Π°Π΅ΡΡ ΡΠΊΠΎΡΠΎΠ²Π°ΡΠΊΡ ΠΈ ΠΏΠΎ ΡΠ΅ΠΊΡΠ½Π΄ΠΎΠΌΠ΅ΡΡ ΠΆΠ΄Π΅ΡΡ 2 ΠΌΠΈΠ½.( Π²ΡΠ΅ΠΌΡ Π½Π°Π΄ΠΎ ΠΏΠΎΠ΄Π±ΠΈΡΠ°ΡΡ) ΠΡΠΊΡΡΠ²Π°Π΅ΡΡ ΠΈ Π²ΡΡΡΠΏΠ°Π΅ΡΡ Π²ΡΠΏΠ΅Π½Π΅Π½Π½ΡΠ΅ Π³ΡΠ°Π½ΡΠ»Ρ Π΄Π°Π»Π΅Π΅ ΡΡΡΠΊΠ° ΠΈ Π²ΡΠ»Π΅ΠΆΠΈΠ²Π°Π½ΠΈΠ΅ 3-8 ΡΠ°ΡΠΎΠ².
ΠΠ°Π»Π΅Π΅ ΠΈΠ·ΠΌΠ΅ΡΡΠ΅ΡΡ ΠΎΠ±ΡΠ΅ΠΌΠ½ΡΠΉ Π²Π΅Ρ — Π² Π³ΡΠ°ΠΌΠΌΠ°Ρ Π½Π° Π»ΠΈΡΡΡ. Π ΠΊΠΎΡΡΠ΅ΠΊΡΠΈΡΡΠ΅ΡΡ ΠΏΡΠ΅Π΄Π²Π°ΡΠΈΡΠ΅Π»ΡΠ½ΠΎΠ΅ Π²ΡΠΏΠ΅Π½ΠΈΠ²Π°Π½ΠΈΠ΅ — Π² Π·Π°Π²ΠΈΡΠΈΠΌΠΎΡΡΠΈ ΡΠΎ ΡΠΎΠ±ΠΈ Π½Π°Π΄ΠΎ.20 ΠΈΠ»ΠΈ 28 ΠΈΠ»ΠΈ 45 … Π³Ρ/Π»ΠΈΡΡ
ΠΠ΅ΠΊΠΎΡΠΎΡΡΠ΅ ΠΌΠΎΠΆΠ½ΠΎ ΠΏΡΠ΅Π΄Π²ΡΠΏΠ΅Π½ΠΈΠ²Π°ΡΡ Π΄ΠΎ 3Ρ ΡΠ°Π·, ΠΏΠΎΡΠ»Π΅ ΠΊΠ°ΠΆΠ΄ΠΎΠ³ΠΎ, ΡΠ΅Ρ Π½ΠΎΠ»ΠΎΠ³ΠΈΡΠ΅ΡΠΊΠ°Ρ Π²ΡΠ»Π΅ΠΆΠΊΠ° ΠΈ ΡΡΡΠΊΠ°.
Β
ΠΠΎΡΠΎΠΌ Π΄Π΅Π»Π°Π΅ΡΡ «Π·Π°Π΄ΡΠ²Π½ΠΎΠΉ ΠΏΡΡΡΠΎΠ»Π΅Ρ» Π½Π° Π±Π°Π·Π΅ Π°Π²ΡΠΎΠΌΠΎΠ±ΠΈΠ»ΡΠ½ΡΡ ΠΈΠ· ΠΏΠ΅ΡΠΊΠΎΡΡΡΡΠΉΠ½ΠΎΠ³ΠΎ ΠΈΠ»ΠΈ Π³ΡΠ°Π²ΠΈΡΠ΅ΠΊΡΠ½ΠΎΠ³ΠΎ.
Β
2 Π¨Π°Π³. ΠΠ°Π΄ΡΠ²Π°Π΅ΡΡ Π² Π°Π½ΡΡ ΡΠΎΡΠΌΡ Π³ΡΠ°Π½ΡΠ»Ρ, Π·Π°ΠΊΡΡΠ²Π°Π΅ΡΡ ΠΏΡΠΎΠ±ΠΊΡ. Π€ΠΎΡΠΌΠ° ΠΆΠ΅Π»Π°ΡΠ΅Π»ΡΠ½ΠΎ ΠΈΠ· Π»ΡΠΌΠΈΠ½ΠΈΡ, Π΄ΡΡΠ°Π»ΠΈ. ΠΠ±ΡΠ·Π°ΡΠ΅Π»ΡΠ½ΠΎ Π΄ΠΎΠ»ΠΆΠ½Ρ Π±ΡΡΡ Π²ΠΠ½ΡΡ ( Π΄ΡΡΠΊΠΈ Π΄Π»Ρ Π²ΡΡ ΠΎΠ΄Π° Π²ΠΎΠ·Π΄ΡΡ Π° ΠΈ ΠΏΠΎΠΏΠ°Π΄Π°Π½ΠΈΡ ΠΏΠ°ΡΠ°)
3. Π¨Π°Π³. ΠΠΈΠ΄Π°Π΅ΡΡ Π² Π°Π²ΡΠΎΠΊΠ»Π°Π² ΠΏΡΠΎΠΏΠ°ΡΠΈΠ²Π°Π΅ΡΡ ( Π²ΡΠ΅ΠΌΡ ΠΏΠΎΠ΄Π±ΠΈΡΠ°Π΅ΡΡ) ΠΎΡ Π»Π°ΠΆΠ΄Π°Π΅ΡΡ ΡΠΎΡΠΌΡ, ΠΎΡΠΊΡΡΠ²Π°Π΅ΡΡ ΠΈ Π½Π°ΡΠ»Π°ΠΆΠ΄Π°Π΅ΡΡΡΡ Π²ΠΈΠ΄ΠΎΠΌ ΠΌΠΎΠ΄Π΅Π»ΠΈ.
ΠΠ»Ρ ΠΎΡΠΎΠ±ΠΎ Π½Π΅ΡΠ΅ΡΠΏΠ΅Π»ΠΈΠ²ΡΡ ΠΌΠΎΠΆΠ½ΠΎ ΠΎΡ Π»Π°ΠΆΠ΄Π°ΡΡ ΡΠΊΠΎΡΠΎΠ²Π°ΡΠΊΡ ΠΏΠΎΠ³ΡΡΠΆΠ΅Π½ΠΈΠ΅ΠΌ Π½ΠΈΠΆΠ½Π΅ΠΉ ΡΠ°ΡΡΠΈ Π² ΡΠΎΡΡΠ΄ Ρ Ρ ΠΎΠ»ΠΎΠ΄Π½ΠΎΠΉ Π²ΠΎΠ΄ΠΎΠΉ — ΡΠΌΠ΅Π½ΡΡΠ°Π΅Ρ Π²ΡΠ΅ΠΌΡ ΠΎΠΆΠΈΠ΄Π°Π½ΠΈΡ Π΄Π»Ρ ΡΠ±ΡΠΎΡΠ° ΠΏΠ°ΡΠ°.
Β
ΠΠ°ΠΊ Π³ΠΎΠ²ΠΎΡΠΈΡΡΠ° ΡΠ΅ΠΏΠ΅ΡΡ ΡΠ»Π°Π³ Π² ΡΡΠΊΠΈ ΠΈ Π±Π°ΡΠ°Π±Π°Π½ Π½Π° ΡΠ΅Ρ π
Β
Π Π²Π°Π°ΡΠ΅ ΠΏΠΎΡΠΈΡΠ°ΠΉ ΠΊΠ½ΠΈΠΆΠΊΡ Π² ΡΡΡΠ½Π΅ΡΠ΅ Π΅ΡΡΡ, ΠΏΠΎ ΠΠΠ
ΠΠ·ΠΌΠ΅Π½Π΅Π½ΠΎ ΠΏΠΎΠ»ΡΠ·ΠΎΠ²Π°ΡΠ΅Π»Π΅ΠΌ komrad.isaevΠΠΎΠ»ΠΈΡΡΠΈΡΠΎΠ» — ΠΎΠ±Π·ΠΎΡ | Π’Π΅ΠΌΡ ScienceDirect
7.13 ΠΡΠ²ΠΎΠ΄Ρ ΠΈ ΡΠ΅ΠΊΠΎΠΌΠ΅Π½Π΄Π°ΡΠΈΠΈ
EPS Π² ΠΎΡΠ½ΠΎΠ²Π½ΠΎΠΌ ΠΈΡΠΏΠΎΠ»ΡΠ·ΡΠ΅ΡΡΡ Π² ΠΊΠ°ΡΠ΅ΡΡΠ²Π΅ ΡΠΏΠ°ΠΊΠΎΠ²ΠΎΡΠ½ΠΎΠ³ΠΎ ΠΈΠ»ΠΈ ΠΈΠ·ΠΎΠ»ΡΡΠΈΠΎΠ½Π½ΠΎΠ³ΠΎ ΠΌΠ°ΡΠ΅ΡΠΈΠ°Π»Π° Π² ΡΡΡΠΎΠΈΡΠ΅Π»ΡΠ½ΠΎΠΉ ΠΏΡΠΎΠΌΡΡΠ»Π΅Π½Π½ΠΎΡΡΠΈ ΠΈ Π΄ΡΡΠ³ΠΈΡ ΠΎΡΡΠ°ΡΠ»ΡΡ . ΠΠ½ ΠΈΠΌΠ΅Π΅Ρ Π½ΠΈΠ·ΠΊΡΡ ΡΠ΅ΠΏΠ»ΠΎΠΏΡΠΎΠ²ΠΎΠ΄Π½ΠΎΡΡΡ, ΡΡΠΎ Π΄Π΅Π»Π°Π΅Ρ Π΅Π³ΠΎ Ρ ΠΎΡΠΎΡΠΈΠΌ ΠΈΠ·ΠΎΠ»ΡΡΠΈΠΎΠ½Π½ΡΠΌ ΠΌΠ°ΡΠ΅ΡΠΈΠ°Π»ΠΎΠΌ, ΠΊΠΎΡΠΎΡΡΠΉ Π»Π΅Π³ΠΊΠΎ ΡΡΠ°Π½ΡΠΏΠΎΡΡΠΈΡΠΎΠ²Π°ΡΡ. EPS ΠΈΠΌΠ΅Π΅Ρ Π½ΠΈΠ·ΠΊΡΡ ΠΏΠ»ΠΎΡΠ½ΠΎΡΡΡ ΠΈ ΠΏΠΎΡΡΠΈ Π½ΡΠ»Π΅Π²ΡΡ ΠΏΡΠΎΡΠ½ΠΎΡΡΡ Π½Π° ΡΠΆΠ°ΡΠΈΠ΅. ΠΠΎΠ»ΡΡΠΎΠ΅ ΠΊΠΎΠ»ΠΈΡΠ΅ΡΡΠ²ΠΎ ΠΏΠ΅Π½ΠΎΠΏΠΎΠ»ΠΈΡΡΠΈΡΠΎΠ»Π° ΠΎΠ±ΡΠ°Π·ΡΠ΅ΡΡΡ ΠΈ ΠΏΠΎΠΏΠ°Π΄Π°Π΅Ρ Π² ΠΎΡΡ ΠΎΠ΄Ρ. Π‘ΡΡΠ΅ΡΡΠ²ΡΠ΅Ρ ΠΌΠ½ΠΎΠΆΠ΅ΡΡΠ²ΠΎ ΡΠ΅Ρ Π½ΠΈΡΠ΅ΡΠΊΠΈΡ , ΡΠΊΠΎΠ»ΠΎΠ³ΠΈΡΠ΅ΡΠΊΠΈΡ ΠΈ ΡΠΊΠΎΠ½ΠΎΠΌΠΈΡΠ΅ΡΠΊΠΈΡ ΡΡΠΈΠΌΡΠ»ΠΎΠ² Π΄Π»Ρ ΠΏΠ΅ΡΠ΅ΡΠ°Π±ΠΎΡΠΊΠΈ ΠΎΡΡ ΠΎΠ΄ΠΎΠ² EPS.ΠΡΡ ΠΎΠ΄Ρ EPS ΠΌΠΎΠΆΠ½ΠΎ ΠΈΠ·ΠΌΠ΅Π»ΡΡΠΈΡΡ ΠΈ ΠΎΡΡΠΎΡΡΠΈΡΠΎΠ²Π°ΡΡ, ΡΡΠΎΠ±Ρ ΠΈΡΠΏΠΎΠ»ΡΠ·ΠΎΠ²Π°ΡΡ ΠΈΡ Π² ΠΊΠ°ΡΠ΅ΡΡΠ²Π΅ LWA Π΄Π»Ρ ΠΏΡΠΎΠΈΠ·Π²ΠΎΠ΄ΡΡΠ²Π° LWAC; ΡΠ°ΠΊΠΈΠΌ ΠΎΠ±ΡΠ°Π·ΠΎΠΌ, ΡΠΏΠΎΡΠΎΠ±ΡΡΠ²ΡΡ ΡΡΡΠΎΠΉΡΠΈΠ²ΠΎΠΌΡ ΡΠ°Π·Π²ΠΈΡΠΈΡ. ΠΠ΄Π½Π°ΠΊΠΎ ΠΈΡΠΏΠΎΠ»ΡΠ·ΠΎΠ²Π°Π½ΠΈΠ΅ Π½Π΅ ΡΠΎΠ»ΡΠΊΠΎ ΡΠΊΠΎΠ»ΠΎΠ³ΠΈΡΠ΅ΡΠΊΠΈ ΡΠΈΡΡΡΡ ΠΌΠ°ΡΠ΅ΡΠΈΠ°Π»ΠΎΠ², Π½ΠΎ ΠΈ ΡΠΊΠΎΠ»ΠΎΠ³ΠΈΡΠ΅ΡΠΊΠΈ ΡΠΈΡΡΡΡ ΡΠ΅Ρ Π½ΠΎΠ»ΠΎΠ³ΠΈΠΉ ΠΈΠΌΠ΅Π΅Ρ Π²Π°ΠΆΠ½ΠΎΠ΅ Π·Π½Π°ΡΠ΅Π½ΠΈΠ΅ Π΄Π»Ρ ΡΡΡΠΎΠΉΡΠΈΠ²ΠΎΠ³ΠΎ ΡΠ°Π·Π²ΠΈΡΠΈΡ.
ΠΠ°ΠΈΠ±ΠΎΠ»Π΅Π΅ ΡΠΊΠΎΠ½ΠΎΠΌΠΈΡΠ½ΡΠΌ Π²Π°ΡΠΈΠ°Π½ΡΠΎΠΌ ΠΈΡΠΏΠΎΠ»ΡΠ·ΠΎΠ²Π°Π½ΠΈΡ ΠΎΡΡ ΠΎΠ΄ΠΎΠ² EPS Π² Π±Π΅ΡΠΎΠ½Π΅, ΠΏΠΎ-Π²ΠΈΠ΄ΠΈΠΌΠΎΠΌΡ, ΡΠ²Π»ΡΠ΅ΡΡΡ ΠΈΡΠΏΠΎΠ»ΡΠ·ΠΎΠ²Π°Π½ΠΈΠ΅ Π½Π΅ΠΌΠΎΠ΄ΠΈΡΠΈΡΠΈΡΠΎΠ²Π°Π½Π½ΡΡ ΠΈΠ·ΠΌΠ΅Π»ΡΡΠ΅Π½Π½ΡΡ ΠΎΡΡ ΠΎΠ΄ΠΎΠ² EPS Π½Π΅ΠΏΠΎΡΡΠ΅Π΄ΡΡΠ²Π΅Π½Π½ΠΎ Π² Π±Π΅ΡΠΎΠ½Π΅ ΠΈΠ»ΠΈ ΡΠ°ΡΡΠ²ΠΎΡΠ΅ Π² ΠΊΠ°ΡΠ΅ΡΡΠ²Π΅ LWA. ΠΡΠΎ Π±ΡΠ΄Π΅Ρ ΠΎΡΠ΅Π½Ρ ΠΏΠΎΠ»Π΅Π·Π½ΠΎ, ΡΠ°ΠΊ ΠΊΠ°ΠΊ ΡΠΎΠΊΡΠ°ΡΠΈΡ ΠΊΠΎΠ»ΠΈΡΠ΅ΡΡΠ²ΠΎ ΠΎΡΡ ΠΎΠ΄ΠΎΠ², ΠΎΡΠΏΡΠ°Π²Π»ΡΠ΅ΠΌΡΡ Π½Π° ΡΠ²Π°Π»ΠΊΠΈ, ΠΈ ΡΡΠΈΠ»ΠΈΠ·ΠΈΡΡΠ΅Ρ ΠΈΡ Π΄Π»Ρ ΡΠ°ΡΡΠΈΡΠ½ΠΎΠΉ Π·Π°ΠΌΠ΅Π½Ρ ΠΏΠ΅ΡΠ²ΠΈΡΠ½ΡΡ ΠΌΠ°ΡΠ΅ΡΠΈΠ°Π»ΠΎΠ², Π΄ΠΎΠ±ΡΡΡΡ Π² ΠΊΠ°ΡΡΠ΅ΡΠ°Ρ .ΠΠ°ΠΏΠΎΠ»Π½ΠΈΡΠ΅Π»ΠΈ EPS Π»Π΅Π³ΠΊΠΈ ΠΈ ΠΌΠΎΠ³ΡΡ Π²ΡΠ·ΡΠ²Π°ΡΡ ΡΠ°ΡΡΠ»ΠΎΠ΅Π½ΠΈΠ΅ ΠΏΡΠΈ ΡΠΌΠ΅ΡΠΈΠ²Π°Π½ΠΈΠΈ Ρ Π±Π΅ΡΠΎΠ½ΠΎΠΌ. Π‘Π»Π΅Π΄ΠΎΠ²Π°ΡΠ΅Π»ΡΠ½ΠΎ, ΠΎΠ±ΡΠ°Π±ΠΎΡΠΊΠ° Π·Π°ΠΏΠΎΠ»Π½ΠΈΡΠ΅Π»Ρ ΠΏΠ΅Π½ΠΎΠΏΠΎΠ»ΠΈΡΡΠΈΡΠΎΠ»ΠΎΠΌ ΡΠ°Π·Π»ΠΈΡΠ½ΡΠΌΠΈ ΠΌΠ΅ΡΠΎΠ΄Π°ΠΌΠΈ Π΄ΠΎΠ»ΠΆΠ½Π° ΠΎΠ±Π΅ΡΠΏΠ΅ΡΠΈΡΡ ΠΏΠΎΠ»ΡΡΠ΅Π½ΠΈΠ΅ Π»Π΅Π³ΠΊΠΎΠ³ΠΎ Π±Π΅ΡΠΎΠ½Π° Ρ ΠΌΠ΅Π½ΡΡΠ΅ΠΉ ΡΠ΅Π³ΡΠ΅Π³Π°ΡΠΈΠ΅ΠΉ. ΠΠ±ΡΠ°Π±ΠΎΡΠΊΠ° ΠΌΠΎΠΆΠ΅Ρ Π²ΠΊΠ»ΡΡΠ°ΡΡ Π΄ΠΎΠ±Π°Π²Π»Π΅Π½ΠΈΠ΅ ΡΠ²ΡΠ·ΡΡΡΠ΅Π³ΠΎ, ΡΠ΅ΡΠΌΠΎΠΎΠ±ΡΠ°Π±ΠΎΡΠΊΡ ΠΈ ΠΏΠΎΠΊΡΡΡΠΈΠ΅. Π‘Π»Π΅Π΄ΡΠ΅Ρ ΡΡΠΈΡΡΠ²Π°ΡΡ ΠΏΡΠ΅ΠΈΠΌΡΡΠ΅ΡΡΠ²Π° ΠΈ Π½Π΅Π΄ΠΎΡΡΠ°ΡΠΊΠΈ ΠΊΠ°ΠΆΠ΄ΠΎΠ³ΠΎ Π»Π΅ΡΠ΅Π½ΠΈΡ. ΠΠ΅ΠΊΠΎΡΠΎΡΡΠ΅ ΠΈΠ· ΡΡΠΈΡ ΠΌΠ΅ΡΠΎΠ΄ΠΎΠ² ΠΌΠΎΠ³ΡΡ Π±ΡΡΡ Π½Π΅ΡΠΊΠΎΠ½ΠΎΠΌΠΈΡΠ½ΡΠΌΠΈ, ΡΡΡΠ΅ΠΊΡΠΈΠ²Π½ΡΠΌΠΈ, ΠΏΡΠΎΡΡΡΠΌΠΈ Π² ΠΏΡΠΈΠΌΠ΅Π½Π΅Π½ΠΈΠΈ, Π΄ΠΎΡΡΡΠΏΠ½ΡΠΌΠΈ Π² ΡΠ°Π·Π²ΠΈΠ²Π°ΡΡΠΈΡ ΡΡ ΡΡΡΠ°Π½Π°Ρ ΠΈ ΡΠΊΠΎΠ»ΠΎΠ³ΠΈΡΠ΅ΡΠΊΠΈ Π±Π΅Π·ΠΎΠΏΠ°ΡΠ½ΡΠΌΠΈ, ΠΏΠΎΡΠΊΠΎΠ»ΡΠΊΡ ΡΡΠΈΠ»ΠΈΠ·Π°ΡΠΈΡ ΠΎΡΡ ΠΎΠ΄ΠΎΠ² Π² ΡΡΠΈΡ ΡΡΡΠ°Π½Π°Ρ Π²ΡΠ΅ Π΅ΡΠ΅ Π½Π°Ρ ΠΎΠ΄ΠΈΡΡΡ Π² ΡΡΠ°Π΄ΠΈΠΈ ΡΠ°Π·ΡΠ°Π±ΠΎΡΠΊΠΈ.
Π‘ΠΎΠ³Π»Π°ΡΠ½ΠΎ ΠΈΡΡΠ»Π΅Π΄ΠΎΠ²Π°ΡΠ΅Π»ΡΡΠΊΠΎΠΉ ΡΠ°Π±ΠΎΡΠ΅, ΠΏΡΠ΅Π΄ΡΡΠ°Π²Π»Π΅Π½Π½ΠΎΠΉ Π² ΡΡΠΎΠΉ Π³Π»Π°Π²Π΅, Π±ΠΎΠ»ΡΡΠΈΠ½ΡΡΠ²ΠΎ ΠΏΡΠΎΠ²Π΅Π΄Π΅Π½Π½ΡΡ ΡΠΊΡΠΏΠ΅ΡΠΈΠΌΠ΅Π½ΡΠΎΠ² ΠΊΠ°ΡΠ°Π»ΠΎΡΡ ΠΌΠ΅Ρ Π°Π½ΠΈΡΠ΅ΡΠΊΠΈΡ ΡΠ²ΠΎΠΉΡΡΠ² Π±Π΅ΡΠΎΠ½Π°, ΡΠΎΠ΄Π΅ΡΠΆΠ°ΡΠ΅Π³ΠΎ ΠΌΠΎΠ΄ΠΈΡΠΈΡΠΈΡΠΎΠ²Π°Π½Π½ΡΠ΅ ΠΈ Π½Π΅ΠΌΠΎΠ΄ΠΈΡΠΈΡΠΈΡΠΎΠ²Π°Π½Π½ΡΠ΅ ΡΠ°ΡΡΠΈΡΡ EPS. ΠΠ΅ΠΎΠ±Ρ ΠΎΠ΄ΠΈΠΌΠΎ ΠΈΠ·ΡΡΠΈΡΡ ΠΏΡΠΎΠ³Π½ΠΎΠ· ΡΠ²ΠΎΠΉΡΡΠ² Π±Π΅ΡΠΎΠ½Π°, ΡΠΎΠ΄Π΅ΡΠΆΠ°ΡΠ΅Π³ΠΎ ΡΠ°Π·Π»ΠΈΡΠ½ΡΠ΅ ΡΠΎΡΠΌΡ EPS. Π’Π°ΠΊΠΆΠ΅ ΡΠ»Π΅Π΄ΡΠ΅Ρ ΡΠ°ΡΡΠΌΠΎΡΡΠ΅ΡΡ Π²ΠΎΠ·ΠΌΠΎΠΆΠ½ΠΎΡΡΡ ΠΈΡΠΏΠΎΠ»ΡΠ·ΠΎΠ²Π°Π½ΠΈΡ ΠΏΠ΅Π½ΠΎΠΏΠΎΠ»ΠΈΡΡΠΈΡΠΎΠ»Π° Π² ΡΠ°ΠΌΠΎΡΠΏΠ»ΠΎΡΠ½ΡΡΡΠ΅ΠΌΡΡ Π»Π΅Π³ΠΊΠΎΠΌ Π±Π΅ΡΠΎΠ½Π΅.
Π‘ΠΎΠ³Π»Π°ΡΠ½ΠΎ ΠΏΡΠ΅Π΄ΡΠ΄ΡΡΠΈΠΌ ΠΈΡΡΠ»Π΅Π΄ΠΎΠ²Π°Π½ΠΈΡΠΌ, ΠΏΡΠΎΠ²Π΅Π΄Π΅Π½Π½ΡΠΌ Π½Π° Π±Π΅ΡΠΎΠ½Π΅ EPS, ΠΏΡΠ΅Π΄ΡΡΠ°Π²Π»Π΅Π½Π½ΡΠΌ Π² Π’Π°Π±Π»ΠΈΡΠ΅ 7.2, ΡΠ΅Π½Π΄Π΅Π½ΡΠΈΡ Π²ΡΠ΅Ρ ΡΡΠΈΡ ΠΈΡΡΠ»Π΅Π΄ΠΎΠ²Π°Π½ΠΈΠΉ ΡΠΎΡΡΠΎΠΈΡ Π² ΡΠΎΠΌ, ΡΡΠΎ ΡΠ²Π΅Π»ΠΈΡΠ΅Π½ΠΈΠ΅ ΡΠΎΠ΄Π΅ΡΠΆΠ°Π½ΠΈΡ Π·Π°ΠΏΠΎΠ»Π½ΠΈΡΠ΅Π»Ρ EPS ΠΏΡΠΈΠ²Π΅Π΄Π΅Ρ ΠΊ Π±ΠΎΠ»Π΅Π΅ ΡΠ»Π°Π±ΠΎΠΌΡ Π±Π΅ΡΠΎΠ½Ρ; ΡΡΠΎ ΠΏΡΠΎΠΈΡΡ ΠΎΠ΄ΠΈΡ ΠΈΠ·-Π·Π° ΡΠΎΠ³ΠΎ, ΡΡΠΎ ΡΠ°ΡΡΠΈΡΡ EPS Π΄ΠΎΡΡΠ°ΡΠΎΡΠ½ΠΎ ΡΠ»Π°Π±ΡΠ΅.ΠΡΠ»ΠΎ ΠΎΠ±Π½Π°ΡΡΠΆΠ΅Π½ΠΎ, ΡΡΠΎ ΠΏΡΠΎΡΠ½ΠΎΡΡΡ Π±Π΅ΡΠΎΠ½Π° Π½Π° ΡΠΆΠ°ΡΠΈΠ΅ ΠΈΠ· ΠΏΠ΅Π½ΠΎΠΏΠΎΠ»ΠΈΡΡΠΈΡΠΎΠ»Π° ΠΏΡΡΠΌΠΎ ΠΏΡΠΎΠΏΠΎΡΡΠΈΠΎΠ½Π°Π»ΡΠ½Π° ΠΏΠ»ΠΎΡΠ½ΠΎΡΡΠΈ Π±Π΅ΡΠΎΠ½Π°. ΠΡΠΎ ΠΎΠ·Π½Π°ΡΠ°Π΅Ρ, ΡΡΠΎ ΠΏΡΠΎΡΠ½ΠΎΡΡΡ Π½Π° ΡΠΆΠ°ΡΠΈΠ΅ ΠΏΠ΅Π½ΠΎΠΏΠΎΠ»ΠΈΡΡΠΈΡΠΎΠ»Π° ΡΠ²Π΅Π»ΠΈΡΠΈΠ²Π°Π΅ΡΡΡ Ρ ΡΠ²Π΅Π»ΠΈΡΠ΅Π½ΠΈΠ΅ΠΌ ΠΏΠ»ΠΎΡΠ½ΠΎΡΡΠΈ Π±Π΅ΡΠΎΠ½Π°. ΠΡΠΎΡΠ½ΠΎΡΡΡ Π½Π° ΡΠΆΠ°ΡΠΈΠ΅ ΠΏΠ΅Π½ΠΎΠΏΠΎΠ»ΠΈΡΡΠΈΡΠΎΠ»Π° ΡΠ²Π΅Π»ΠΈΡΠΈΠ²Π°Π»Π°ΡΡ ΠΏΡΠΈ ΡΠΌΠ΅Π½ΡΡΠ΅Π½ΠΈΠΈ ΡΠ°Π·ΠΌΠ΅ΡΠ° Π²Π°Π»ΠΈΠΊΠ° ΠΏΠ΅Π½ΠΎΠΏΠΎΠ»ΠΈΡΡΠΈΡΠΎΠ»Π° ΠΈ ΠΏΠΎΠ²ΡΡΠ°Π»Π°ΡΡ ΠΏΡΠΈ ΡΠ²Π΅Π»ΠΈΡΠ΅Π½ΠΈΠΈ Π΅ΡΡΠ΅ΡΡΠ²Π΅Π½Π½ΠΎΠ³ΠΎ ΠΊΡΡΠΏΠ½ΠΎΠ³ΠΎ Π·Π°ΠΏΠΎΠ»Π½ΠΈΡΠ΅Π»Ρ. ΠΡΠ»ΠΎ ΠΏΠΎΠΊΠ°Π·Π°Π½ΠΎ, ΡΡΠΎ Π΄Π»Ρ Π±Π΅ΡΠΎΠ½Π°
.ΠΠΏΡΠΈΠΌΠΈΠ·Π°ΡΠΈΡ Π²ΡΠΏΠ΅Π½ΠΈΠ²Π°ΡΡΠΈΡ Π°Π³Π΅Π½ΡΠΎΠ² Π΄Π»Ρ ΠΏΠΎΠ»ΠΈΠΈΠ·ΠΎ — Π‘ΠΊΠ°ΡΠ°ΡΡ PDF Π±Π΅ΡΠΏΠ»Π°ΡΠ½ΠΎ
Π’ΡΠ°Π½ΡΠΊΡΠΈΠΏΡΠΈΡ
1 ΠΠΏΡΠΈΠΌΠΈΠ·Π°ΡΠΈΡ ΡΡΠ΅Π΄ΡΡΠ² Π΄Π»Ρ Π²ΡΠ΄ΡΠ²Π°Π½ΠΈΡ ΠΏΠΎΠ»ΠΈΠΈΠ·ΠΎ Π‘ΠΠ§Π§ΠΠΠ Π. Π‘ΠΠΠΠ₯, ΠΠΠΠΠΠ ΠΠ’ΠΠ Π£-ΠΠΠ ΠΠΠΠΠ Π ΠΠΠΠΠ Π ΠΠ’Π§Π Π¦Π΅Π½ΡΡ ΠΏΠ΅ΡΠ΅Π΄ΠΎΠ²ΡΡ ΡΠ΅Ρ Π½ΠΎΠ»ΠΎΠ³ΠΈΠΉ Π₯Π°Π½ΡΡΠΌΠ°Π½ 86 Gosling Road The Woodlands, TX Π ΠΠ€ΠΠ ΠΠ’ Π Π½Π°ΡΡΠΎΡΡΠ΅Π΅ Π²ΡΠ΅ΠΌΡ Π²ΡΠ΄ΡΠ²Π°ΡΡΡΡ ΠΏΠ»ΠΈΡΡ ΠΈΠ· ΠΏΠΎΠ»ΠΈΠΈΠ·ΠΎΡΠΈΠ°Π½ΡΡΠ°ΡΠ° (ΠΏΠΎΠ»ΠΈΠΈΠ·ΠΎ), ΠΊΠΎΡΠΎΡΡΠ΅ ΠΈΡΠΏΠΎΠ»ΡΠ·ΡΡΡΡΡ Π² ΠΊΠΎΠΌΠΌΠ΅ΡΡΠ΅ΡΠΊΠΈΡ ΠΊΡΠΎΠ²Π΅Π»ΡΠ½ΡΡ ΠΏΠΎΠΊΡΡΡΠΈΡΡ Π² Π‘Π΅Π²Π΅ΡΠ½ΠΎΠΉ ΠΠΌΠ΅ΡΠΈΠΊΠ΅ ΠΈ ΠΠ²ΡΠΎΠΏΠ΅. Ρ ΠΏΠ΅Π½ΡΠ°Π½ΠΎΠΌ.ΠΡΠ»Π΅Π²ΠΎΠΉ ΠΏΠΎΡΠ΅Π½ΡΠΈΠ°Π» ΡΠ°Π·ΡΡΡΠ΅Π½ΠΈΡ ΠΎΠ·ΠΎΠ½ΠΎΠ²ΠΎΠ³ΠΎ ΡΠ»ΠΎΡ (ODP), Π½Π΅Π·Π½Π°ΡΠΈΡΠ΅Π»ΡΠ½ΡΠΉ ΠΏΠΎΡΠ΅Π½ΡΠΈΠ°Π» Π³Π»ΠΎΠ±Π°Π»ΡΠ½ΠΎΠ³ΠΎ ΠΏΠΎΡΠ΅ΠΏΠ»Π΅Π½ΠΈΡ (GWP) ΠΈ Π½ΠΈΠ·ΠΊΠΈΠΉ ΡΡΠΎΠΊ ΡΠ»ΡΠΆΠ±Ρ ΠΏΠ΅Π½ΡΠ°Π½ΠΎΠ² Π² Π°ΡΠΌΠΎΡΡΠ΅ΡΠ΅ ΠΎΠ·Π½Π°ΡΠ°ΡΡ, ΡΡΠΎ ΠΏΡΠΎΠΈΠ·Π²ΠΎΠ΄ΠΈΡΠ΅Π»ΡΠΌ ΠΏΠΎΠ»ΠΈΠΈΠ·ΠΎ-ΠΏΠ»ΠΈΡ Π±ΠΎΠ»ΡΡΠ΅ Π½Π΅ Π½ΡΠΆΠ½ΠΎ Π±Π΅ΡΠΏΠΎΠΊΠΎΠΈΡΡΡΡ ΠΎ Π±ΡΠ΄ΡΡΠΈΡ ΠΏΡΠ°Π²ΠΈΠ»Π°Ρ , ΠΊΠ°ΡΠ°ΡΡΠΈΡ ΡΡ ΡΠ°Π·ΡΡΡΠ΅Π½ΠΈΡ ΠΎΠ·ΠΎΠ½ΠΎΠ²ΠΎΠ³ΠΎ ΡΠ»ΠΎΡ ΠΈΠ»ΠΈ Π³Π»ΠΎΠ±Π°Π»ΡΠ½ΠΎΠ³ΠΎ ΠΏΠΎΡΠ΅ΠΏΠ»Π΅Π½ΠΈΡ. ΠΠ»Π°Π³ΠΎΠ΄Π°ΡΡ ΠΈΠ·ΠΌΠ΅Π½Π΅Π½ΠΈΡ ΡΠ΅ΡΠ΅ΠΏΡΡΡ ΠΈ ΠΏΠ°ΡΠ°ΠΌΠ΅ΡΡΠΎΠ² ΠΎΠ±ΡΠ°Π±ΠΎΡΠΊΠΈ, Ρ Π°ΡΠ°ΠΊΡΠ΅ΡΠΈΡΡΠΈΠΊΠΈ ΠΏΠΎΠ»ΠΈΠΈΠ·ΠΎ Π²ΠΎ ΠΌΠ½ΠΎΠ³ΠΈΡ ΠΎΡΠ½ΠΎΡΠ΅Π½ΠΈΡΡ ΡΠ»ΡΡΡΠΈΠ»ΠΈΡΡ, ΠΊΠΎΠ³Π΄Π° ΡΠ΅ΡΡ ΠΈΠ΄Π΅Ρ ΠΎ ΡΠΎΠ±Π»ΡΠ΄Π΅Π½ΠΈΠΈ ΡΡΡΠΎΠ³ΠΈΡ ΡΡΠ΅Π±ΠΎΠ²Π°Π½ΠΈΠΉ ΡΡΡΠΎΠΈΡΠ΅Π»ΡΠ½ΡΡ Π½ΠΎΡΠΌ, ΠΊΠ°ΡΠ°ΡΡΠΈΡ ΡΡ ΠΏΠΎΠΆΠ°ΡΠ½ΠΎΠΉ Π±Π΅Π·ΠΎΠΏΠ°ΡΠ½ΠΎΡΡΠΈ, ΡΡΡΡΠΊΡΡΡΠ½ΠΎΠΉ ΡΠ΅Π»ΠΎΡΡΠ½ΠΎΡΡΠΈ ΠΈ ΡΠ΅ΠΏΠ»ΠΎΠΈΠ·ΠΎΠ»ΡΡΠΈΠΈ.Π₯ΠΎΡΡ ΡΡΠΎ Π²ΡΡΠΎΠΊΠΈΠ΅ ΠΈ ΠΏΠΎΡ Π²Π°Π»ΡΠ½ΡΠ΅ Π΄ΠΎΡΡΠΈΠΆΠ΅Π½ΠΈΡ, ΠΏΠΎΡΡΠ΅Π±Π½ΠΎΡΡΡ Π² Π»ΡΡΡΠ΅ΠΉ ΠΈ Π±ΠΎΠ»Π΅Π΅ ΡΠ΅Π½ΡΠ°Π±Π΅Π»ΡΠ½ΠΎΠΉ ΠΈΠ·ΠΎΠ»ΡΡΠΈΠΈ ΠΎΡΡΠ°Π΅ΡΡΡ Π² ΡΡΠΎΠΌ ΠΏΠΎΡΡΠΎΡΠ½Π½ΠΎ ΡΠ°ΡΡΡΡΠ΅ΠΌ ΠΎΠ±ΡΠ΅ΡΡΠ²Π΅, Π·Π°Π±ΠΎΡΡΡΠ΅ΠΌΡΡ ΠΎ ΡΠ½Π΅ΡΠ³ΠΈΠΈ ΠΈ ΠΎΠΊΡΡΠΆΠ°ΡΡΠ΅ΠΉ ΡΡΠ΅Π΄Π΅. ΠΡΠΎΠΌΠ΅ ΡΠΎΠ³ΠΎ, ΡΡΠ΅Π±ΠΎΠ²Π°Π½ΠΈΡ ΠΊ ΠΈΠ·ΠΎΠ»ΡΡΠΈΠΎΠ½Π½ΠΎΠΉ ΠΏΠ΅Π½Π΅ ΠΏΡΠΎΠ΄ΠΎΠ»ΠΆΠ°ΡΡ ΡΠ°Π·Π²ΠΈΠ²Π°ΡΡΡΡ. ΠΠ΅Π΄Π°Π²Π½Π΅ΠΉ ΡΠ°Π·ΡΠ°Π±ΠΎΡΠΊΠΎΠΉ ΡΡΠ°Π»ΠΎ ΠΈΡΠΏΠΎΠ»ΡΠ·ΠΎΠ²Π°Π½ΠΈΠ΅ ΠΌΠ΅ΡΠΎΠ΄Π° Π΄Π»ΠΈΡΠ΅Π»ΡΠ½ΠΎΠ³ΠΎ ΡΠ΅ΡΠΌΠΈΡΠ΅ΡΠΊΠΎΠ³ΠΎ ΡΠΎΠΏΡΠΎΡΠΈΠ²Π»Π΅Π½ΠΈΡ (LTTR) Π² ΠΊΠ°ΡΠ΅ΡΡΠ²Π΅ ΠΌΠ΅ΡΡ ΡΠ΅ΠΏΠ»ΠΎΠΈΠ·ΠΎΠ»ΡΡΠΈΠΈ. Π Π‘Π΅Π²Π΅ΡΠ½ΠΎΠΉ ΠΠΌΠ΅ΡΠΈΠΊΠ΅ LTTR ΠΎΠΏΡΠ΅Π΄Π΅Π»ΡΠ΅ΡΡΡ ΠΊΠ°ΠΊ Π²Π·Π²Π΅ΡΠ΅Π½Π½ΠΎΠ΅ ΠΏΠΎ Π²ΡΠ΅ΠΌΠ΅Π½ΠΈ ΡΡΠ΅Π΄Π½Π΅Π΅ ΡΠ΅ΠΏΠ»ΠΎΠ²ΠΎΠ΅ ΡΠΎΠΏΡΠΎΡΠΈΠ²Π»Π΅Π½ΠΈΠ΅ Π·Π° 15-Π»Π΅ΡΠ½ΠΈΠΉ ΠΏΠ΅ΡΠΈΠΎΠ΄. ΠΡΠ΅ ΠΎΠ΄Π½ΠΈΠΌ ΡΠΎΠ±ΡΡΠΈΠ΅ΠΌ ΡΠ²Π»ΡΠ΅ΡΡΡ ΠΏΠΎΠ²ΡΡΠ΅Π½ΠΈΠ΅ ΡΡΠ΅Π±ΠΎΠ²Π°Π½ΠΈΠΉ ΠΊ ΡΠΈΠ·ΠΈΡΠ΅ΡΠΊΠΎΠΉ ΡΠΎΠ±ΡΡΠ²Π΅Π½Π½ΠΎΡΡΠΈ Π΄Π»Ρ ΠΏΠΎΠ»ΠΈΠΈΠ·ΠΎ, Π²ΠΎΡΡΡΠ΅Π±ΠΎΠ²Π°Π½Π½ΠΎΠ³ΠΎ ΡΡΠ½ΠΊΠΎΠΌ.ΠΠ°ΠΏΡΠΈΠΌΠ΅Ρ, ΠΌΠΈΠ½ΠΈΠΌΠ°Π»ΡΠ½Π°Ρ ΠΏΡΠΎΡΠ½ΠΎΡΡΡ Π½Π° ΡΠΆΠ°ΡΠΈΠ΅ Π² Π½Π°ΠΏΡΠ°Π²Π»Π΅Π½ΠΈΠΈ ΡΠΎΠ»ΡΠΈΠ½Ρ ΠΈ ΡΡΠ°Π±ΠΈΠ»ΡΠ½ΠΎΡΡΡ ΡΠ°Π·ΠΌΠ΅ΡΠΎΠ² ΠΏΠΎΠ»ΠΈΠΈΠ·ΠΎ-ΠΊΠ°ΡΡΠΎΠ½Π°, ΠΊΠ°ΠΊ ΠΎΠΏΡΠ΅Π΄Π΅Π»Π΅Π½ΠΎ Π² 21 ΠΈΠ·Π΄Π°Π½ΠΈΠΈ ASTM C1289, ΡΠ²Π»ΡΡΡΡΡ Π±ΠΎΠ»Π΅Π΅ ΡΡΡΠΎΠ³ΠΈΠΌΠΈ, ΡΠ΅ΠΌ Π² ΠΈΠ·Π΄Π°Π½ΠΈΠΈ 98. Π’Π°ΠΊΠΈΠ΅ ΠΈΠ·ΠΌΠ΅Π½Π΅Π½ΠΈΡ Π² ΡΡΠ΅Π±ΠΎΠ²Π°Π½ΠΈΡΡ ΠΊ ΠΊΠΎΠ½Π΅ΡΠ½ΠΎΠΌΡ ΠΈΡΠΏΠΎΠ»ΡΠ·ΠΎΠ²Π°Π½ΠΈΡ ΠΈ Π½Π΅ΠΎΠ±Ρ ΠΎΠ΄ΠΈΠΌΠΎΡΡΡ ΠΏΠΎΠ΄Π΄Π΅ΡΠΆΠΈΠ²Π°ΡΡ ΠΊΠΎΠ½ΠΊΡΡΠ΅Π½ΡΠ½ΠΎΠ΅ ΠΏΡΠ΅ΠΈΠΌΡΡΠ΅ΡΡΠ²ΠΎ ΠΏΠΎΠ»ΠΈΠΈΠ·ΠΎ ΠΏΠΎ ΡΡΠ°Π²Π½Π΅Π½ΠΈΡ Ρ Π΄ΡΡΠ³ΠΈΠΌΠΈ ΡΠΈΠΏΠ°ΠΌΠΈ ΠΏΠ΅Π½ΠΎΠΏΠ»Π°ΡΡΠ° ΠΏΠΎΠ±ΡΠ΄ΠΈΠ»ΠΈ Π½Π°Ρ ΠΏΠ΅ΡΠ΅ΡΠΌΠΎΡΡΠ΅ΡΡ ΠΎΠΏΡΠΈΠΌΠΈΠ·Π°ΡΠΈΡ ΠΏΠ°ΡΠ°ΠΌΠ΅ΡΡΠΎΠ² ΡΠ΅ΡΠ΅ΠΏΡΡΡΡ ΠΈ ΠΎΠ±ΡΠ°Π±ΠΎΡΠΊΠΈ. ΠΡΠ½ΠΎΠ²ΡΠ²Π°ΡΡΡ Π½Π° ΡΠ΅ΠΊΡΡΠ΅ΠΌ ΠΊΠΎΠΌΠΌΠ΅ΡΡΠ΅ΡΠΊΠΎΠΌ ΠΏΡΠΎΠΈΠ·Π²ΠΎΠ΄ΡΡΠ²Π΅ ΠΏΠ΅Π½ΡΠ°Π½ΠΎΠ² Π² Π‘Π΅Π²Π΅ΡΠ½ΠΎΠΉ ΠΠΌΠ΅ΡΠΈΠΊΠ΅ ΠΈ ΠΠ²ΡΠΎΠΏΠ΅, Π° ΡΠ°ΠΊΠΆΠ΅ Π½Π° ΠΎΠΏΡΠ±Π»ΠΈΠΊΠΎΠ²Π°Π½Π½ΡΡ ΡΠ°Π±ΠΎΡΠ°Ρ , Π² ΡΡΠΎΠΌ ΠΈΡΡΠ»Π΅Π΄ΠΎΠ²Π°Π½ΠΈΠΈ ΠΈΠ·ΡΡΠ°Π»ΠΎΡΡ Π²Π»ΠΈΡΠ½ΠΈΠ΅ ΠΈΠ·ΠΌΠ΅Π½Π΅Π½ΠΈΠΉ Π² ΡΠΈΠ·ΠΈΡΠ΅ΡΠΊΠΎΠΌ ΡΠΎΡΡΠ°Π²Π΅ Π²ΡΠΏΠ΅Π½ΠΈΠ²Π°ΡΡΠ΅Π³ΠΎ Π°Π³Π΅Π½ΡΠ° Π½Π° ΠΊΠ»ΡΡΠ΅Π²ΡΠ΅ ΡΠ°Π±ΠΎΡΠΈΠ΅ Ρ Π°ΡΠ°ΠΊΡΠ΅ΡΠΈΡΡΠΈΠΊΠΈ ΠΏΠΎΠ»ΠΈΠΈΠ·ΠΎ, ΠΊΠ°ΠΊ ΡΡΠΎ ΠΎΠΏΡΠ΅Π΄Π΅Π»Π΅Π½ΠΎ Π½ΠΎΠ²ΡΠΌΠΈ ΡΡΠ΅Π±ΠΎΠ²Π°Π½ΠΈΡΠΌΠΈ, ΡΠΎΠ΄Π΅ΡΠΆΠ°ΡΠΈΠΌΠΈΡΡ Π² ASTM C1289.ΠΡΠ½ΠΎΠ²ΡΠ²Π°ΡΡΡ Π½Π° ΡΡΠΈΡ ΠΎΡΠ΅Π½ΠΊΠ°Ρ , Π΄Π°Π½Π½ΠΎΠ΅ ΠΈΡΡΠ»Π΅Π΄ΠΎΠ²Π°Π½ΠΈΠ΅ ΠΏΡΠ΅Π΄ΠΏΠΎΠ»Π°Π³Π°Π΅Ρ, ΡΡΠΎ Π΄Π΅ΠΉΡΡΠ²ΠΈΡΠ΅Π»ΡΠ½ΠΎ ΡΡΡΠ΅ΡΡΠ²ΡΠ΅Ρ ΠΏΠΎΡΠ΅Π½ΡΠΈΠ°Π» Π΄Π»Ρ Π΄Π°Π»ΡΠ½Π΅ΠΉΡΠ΅Π³ΠΎ ΡΠ½ΠΈΠΆΠ΅Π½ΠΈΡ Π·Π°ΡΡΠ°Ρ ΠΏΡΠΈ ΡΠΎΡ ΡΠ°Π½Π΅Π½ΠΈΠΈ ΠΏΡΠΎΠΈΠ·Π²ΠΎΠ΄ΠΈΡΠ΅Π»ΡΠ½ΠΎΡΡΠΈ. ΠΠΎΡΠ΅Π½ΡΠΈΠ°Π»ΡΠ½Π°Ρ ΡΠΊΠΎΠ½ΠΎΠΌΠΈΡ ΡΡΠ΅Π΄ΡΡΠ² ΠΌΠΎΠΆΠ΅Ρ Π±ΡΡΡ Π΄ΠΎΡΡΠΈΠ³Π½ΡΡΠ° Π·Π° ΡΡΠ΅Ρ Π±ΠΎΠ»Π΅Π΅ Π½ΠΈΠ·ΠΊΠΈΡ Π·Π°ΡΡΠ°Ρ Π½Π° Π²ΡΠΏΠ΅Π½ΠΈΠ²Π°ΡΠ΅Π»Ρ ΠΈ, ΡΡΠΎ Π±ΠΎΠ»Π΅Π΅ Π²Π°ΠΆΠ½ΠΎ, ΡΠΌΠ΅Π½ΡΡΠ΅Π½ΠΈΡ ΠΏΠ»ΠΎΡΠ½ΠΎΡΡΠΈ ΠΏΠ΅Π½Ρ, Π½Π΅ΠΎΠ±Ρ ΠΎΠ΄ΠΈΠΌΠΎΠΉ Π΄Π»Ρ ΠΈΠ·Π³ΠΎΡΠΎΠ²Π»Π΅Π½ΠΈΡ ΠΏΠ»ΠΈΡ, ΠΎΡΠ²Π΅ΡΠ°ΡΡΠΈΡ Π²ΡΠ΅ΠΌ ΡΡΠ΅Π±ΠΎΠ²Π°Π½ΠΈΡΠΌ ΠΊ ΠΊΠΎΠ½ΡΡΡΡΠΊΡΠΈΠΈ, ΠΈΠ·ΠΎΠ»ΡΡΠΈΠΈ ΠΈ ΠΎΠ³Π½Π΅ΡΡΠΎΠΉΠΊΠΎΡΡΠΈ. ΠΠΠΠΠΠΠΠ ΠΡΠΈ ΠΈΡΠΏΠΎΠ»ΡΠ·ΠΎΠ²Π°Π½ΠΈΠΈ Π±ΠΎΠ»Π΅Π΅ 35 ΠΌΠΈΠ»Π»ΠΈΠΎΠ½ΠΎΠ² ΡΡΠ½ΡΠΎΠ² ΠΆΠ΅ΡΡΠΊΠ°Ρ ΠΏΠΎΠ»ΠΈΠΈΠ·ΠΎΡΠΈΠ°Π½ΡΡΠ°ΡΠ½Π°Ρ ΠΏΠ΅Π½Π° Π±ΡΠ»Π° ΠΎΠ΄Π½ΠΈΠΌ ΠΈΠ· ΠΊΡΡΠΏΠ½Π΅ΠΉΡΠΈΡ ΡΠ΅Π³ΠΌΠ΅Π½ΡΠΎΠ² ΡΡΠ½ΠΊΠ° ΠΏΠΎΠ»ΠΈΡΡΠ΅ΡΠ°Π½ΠΎΠ² Π‘Π¨Π Π² 22 Π³ΠΎΠ΄Ρ [1].Π‘ ΡΠ΅Ρ ΠΏΠΎΡ ΠΏΠΎΠΊΠ°Π·Π°ΡΠ΅Π»Ρ ΡΠΎΡΡΠ° ΠΏΡΠΎΠΈΠ·Π²ΠΎΠ΄ΡΡΠ²Π° ΠΏΠΎΠ»ΠΈΠΈΠ·ΠΎ ΠΏΡΠ΅Π²ΡΡΠΈΠ» 1% ΠΈ, Π²Π΅ΡΠΎΡΡΠ½ΠΎ, ΠΎΡΡΠ°Π½Π΅ΡΡΡ ΠΊΠ»ΡΡΠ΅Π²ΡΠΌ ΡΠ΅Π³ΠΌΠ΅Π½ΡΠΎΠΌ Π΄Π»Ρ Π΄Π°Π»ΡΠ½Π΅ΠΉΡΠ΅Π³ΠΎ ΡΡΠΏΠ΅Ρ Π° ΠΏΠΎΠ»ΠΈΡΡΠ΅ΡΠ°Π½ΠΎΠ²ΠΎΠΉ ΠΏΡΠΎΠΌΡΡΠ»Π΅Π½Π½ΠΎΡΡΠΈ. ΠΠ»ΠΈΡΡ ΠΈΠ· ΠΏΠΎΠ»ΠΈΠΈΠ·ΠΎ ΠΈΡΠΏΠΎΠ»ΡΠ·ΡΡΡΡΡ Π² ΠΎΡΠ½ΠΎΠ²Π½ΠΎΠΌ Π² ΠΊΠΎΠΌΠΌΠ΅ΡΡΠ΅ΡΠΊΠΈΡ ΠΊΡΠΎΠ²Π»ΡΡ , Π³Π΄Π΅ ΠΎΠ½ΠΈ ΠΊΠΎΠ½ΠΊΡΡΠΈΡΡΡΡ Ρ Π΄ΡΡΠ³ΠΈΠΌΠΈ ΡΠΈΠΏΠ°ΠΌΠΈ ΠΈΠ·ΠΎΠ»ΡΡΠΈΠΎΠ½Π½ΡΡ ΠΌΠ°ΡΠ΅ΡΠΈΠ°Π»ΠΎΠ², ΡΠ°ΠΊΠΈΠΌΠΈ ΠΊΠ°ΠΊ ΠΏΠ΅Π½ΠΎΠΏΠΎΠ»ΠΈΡΡΠΈΡΠΎΠ», ΠΏΠ΅ΡΠ»ΠΈΡ ΠΈ Π΄ΡΠ΅Π²Π΅ΡΠ½ΠΎΠ²ΠΎΠ»ΠΎΠΊΠ½ΠΈΡΡΡΠ΅ ΠΏΠ»ΠΈΡΡ. Π 22 Π³. ΠΏΠΎΠ»ΠΈΠΈΠ·ΠΎ-ΠΏΠ»ΠΈΡΡ ΡΠΎΡΡΠ°Π²Π»ΡΠ»ΠΈ ΠΏΠΎΡΡΠΈ 55,6% Π½ΠΈΠ·ΠΊΠΎΡΠΊΠ°ΡΠ½ΠΎΠΉ (ΠΊΠΎΠΌΠΌΠ΅ΡΡΠ΅ΡΠΊΠΎΠΉ) ΠΊΡΠΎΠ²Π΅Π»ΡΠ½ΠΎΠΉ ΠΈΠ·ΠΎΠ»ΡΡΠΈΠΈ (ΡΠΌ. Π ΠΈΡ. 1). ΠΡΠΎΠ²Π΅Π»ΡΠ½ΡΠ΅ ΠΏΠΎΠΊΡΡΡΠΈΡ Ρ Π½ΠΈΠ·ΠΊΠΈΠΌ ΡΠΊΠ»ΠΎΠ½ΠΎΠΌ ΡΠΎΡΡΠ°Π²Π»ΡΡΡ ΠΎΠΊΠΎΠ»ΠΎ 64% ββΠ²ΡΠ΅Ρ ΠΊΡΠΎΠ²Π΅Π»ΡΠ½ΡΡ ΠΏΠΎΠΊΡΡΡΠΈΠΉ, Π° ΠΎΡΡΠ°Π»ΡΠ½Π°Ρ ΡΠ°ΡΡΡ ΠΏΡΠΈΡ ΠΎΠ΄ΠΈΡΡΡ Π½Π° ΡΡΡΡΠΎΠΉΡΡΠ²Π° Ρ ΠΊΡΡΡΡΠΌ ΡΠΊΠ»ΠΎΠ½ΠΎΠΌ (ΠΆΠΈΠ»ΡΠ΅) [2].ΠΠ΅ΡΠΌΠΎΡΡΡ Π½Π° Π²ΠΏΠ΅ΡΠ°ΡΠ»ΡΡΡΡΡ Π΄ΠΎΠ»Ρ ΡΡΠ½ΠΊΠ°, Π΄ΠΎΠ»Ρ ΠΏΠΎΠ»ΠΈΠΈΠ·ΠΎ-ΠΊΠ°ΡΡΠΎΠ½Π° Π² ΡΠ΅ΡΠ΅Π½ΠΈΠ΅ ΡΡΠ΄Π° Π»Π΅Ρ ΠΎΡΡΠ°Π²Π°Π»Π°ΡΡ Π² ΠΏΡΠ΅Π΄Π΅Π»Π°Ρ 5-6% ΠΎΡ ΠΊΠΎΠΌΠΌΠ΅ΡΡΠ΅ΡΠΊΠΎΠ³ΠΎ ΡΡΠ½ΠΊΠ° ΠΊΡΠΎΠ²Π΅Π»ΡΠ½ΡΡ ΠΌΠ°ΡΠ΅ΡΠΈΠ°Π»ΠΎΠ² Π² Π‘Π΅Π²Π΅ΡΠ½ΠΎΠΉ ΠΠΌΠ΅ΡΠΈΠΊΠ΅. Π‘ΡΠ΅ΠΊΠ»ΠΎΠ²ΠΎΠ»ΠΎΠΊΠ½ΠΎ, 3,7 EPS, 8 ΠΏΠ΅ΡΠ»ΠΈΡ, 12,1 Π΄ΡΡΠ³ΠΈΠ΅, 5,9 XPS, 2,5 Π΄ΡΠ΅Π²Π΅ΡΠ½ΠΎΠ²ΠΎΠ»ΠΎΠΊΠ½ΠΈΡΡΡΠ΅ ΠΏΠ»ΠΈΡΡ, 12,2 ΠΏΠΎΠ»ΠΈΠΈΠ·ΠΎ, 55,6 Π ΠΈΡΡΠ½ΠΎΠΊ 1. ΠΠΎΠ»Ρ ΡΡΠ½ΠΊΠ° ΠΊΠΎΠΌΠΌΠ΅ΡΡΠ΅ΡΠΊΠΈΡ ΠΊΡΠΎΠ²Π΅Π»ΡΠ½ΡΡ ΠΌΠ°ΡΠ΅ΡΠΈΠ°Π»ΠΎΠ² 42
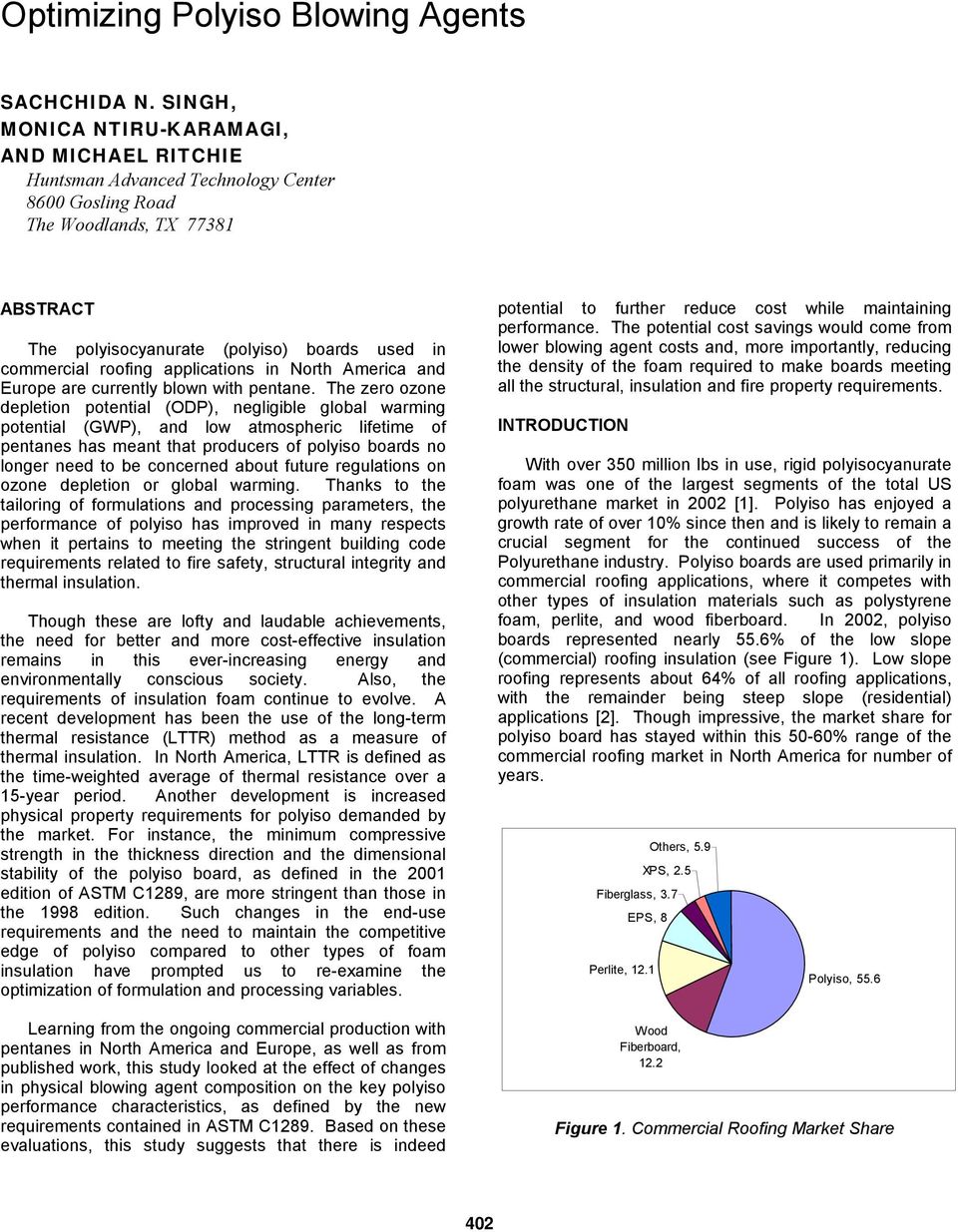
2 ΠΡΠΈ Π²ΡΡΠΎΠΊΠΈΡ ΡΠ΅Π½Π°Ρ Π½Π° ΡΠ½Π΅ΡΠ³ΠΎΠ½ΠΎΡΠΈΡΠ΅Π»ΠΈ ΠΈ ΠΏΠΎΡΡΠΈ Π²ΡΠ΅ΠΎΠ±ΡΠ΅ΠΌ ΠΏΠΎΠ΄ΡΠ²Π΅ΡΠΆΠ΄Π΅Π½ΠΈΠΈ ΡΠ²Π»Π΅Π½ΠΈΡ Π³Π»ΠΎΠ±Π°Π»ΡΠ½ΠΎΠ³ΠΎ ΠΏΠΎΡΠ΅ΠΏΠ»Π΅Π½ΠΈΡ ΠΈΠΌΠΏΡΠ»ΡΡ Π΄Π»Ρ ΡΠΎΡΡΠ° ΠΈΠ·ΠΎΠ»ΡΡΠΈΠΎΠ½Π½ΡΡ ΠΌΠ°ΡΠ΅ΡΠΈΠ°Π»ΠΎΠ² Π² ΡΠ΅Π»ΠΎΠΌ ΠΈ Π²ΡΡΠΎΠΊΠΎΠΈΠ·ΠΎΠ»ΡΡΠΈΠΎΠ½Π½ΡΡ ΠΏΠΎΠ»ΠΈΠΈΠ·ΠΎ-ΠΏΠ»ΠΈΡ Π² ΡΠ°ΡΡΠ½ΠΎΡΡΠΈ Π½ΠΈΠΊΠΎΠ³Π΄Π° Π½Π΅ Π±ΡΠ» ΡΠ°ΠΊΠΈΠΌ Π±ΠΎΠ»ΡΡΠΈΠΌ.Π§ΡΠΎΠ±Ρ Π²ΠΎΡΠΏΠΎΠ»ΡΠ·ΠΎΠ²Π°ΡΡΡΡ ΡΡΠΈΠΌ ΠΌΠΎΠΌΠ΅Π½ΡΠΎΠΌ, Π½Π°ΠΌ Π½ΡΠΆΠ½ΠΎ Π΅ΡΠ΅ Π±ΠΎΠ»Π΅Π΅ Π°ΠΊΡΠΈΠ²Π½ΠΎ ΠΏΡΠΎΠ΄Π²ΠΈΠ³Π°ΡΡ ΠΌΠ½ΠΎΠ³ΠΈΠ΅ Π°ΡΡΠΈΠ±ΡΡΡ ΠΏΠΎΠ»ΠΈΠΈΠ·ΠΎ. ΠΡΠΎ Π²ΠΊΠ»ΡΡΠ°Π΅Ρ Π½Π΅ ΡΠΎΠ»ΡΠΊΠΎ Π΅Π³ΠΎ ΠΏΡΠ΅Π²ΠΎΡΡ ΠΎΠ΄Π½ΡΠ΅ ΡΠΊΡΠΏΠ»ΡΠ°ΡΠ°ΡΠΈΠΎΠ½Π½ΡΠ΅ Ρ Π°ΡΠ°ΠΊΡΠ΅ΡΠΈΡΡΠΈΠΊΠΈ, Π½ΠΎ ΠΈ ΡΠΎΡ ΡΠ°ΠΊΡ, ΡΡΠΎ ΡΡΠΎ Π΅Π΄ΠΈΠ½ΡΡΠ²Π΅Π½Π½Π°Ρ Π²ΡΠΏΠ΅Π½Π΅Π½Π½Π°Ρ ΠΈΠ·ΠΎΠ»ΡΡΠΈΡ, ΠΊΠΎΡΠΎΡΠ°Ρ Π² Π½Π°ΡΡΠΎΡΡΠ΅Π΅ Π²ΡΠ΅ΠΌΡ Π²ΡΠ΄ΡΠ²Π°Π΅ΡΡΡ Ρ Π²ΡΠΏΠ΅Π½ΠΈΠ²Π°ΡΡΠΈΠΌ Π°Π³Π΅Π½ΡΠΎΠΌ Ρ Π½ΡΠ»Π΅Π²ΡΠΌ ODP ΠΈ ΡΡΠ΅Π·Π²ΡΡΠ°ΠΉΠ½ΠΎ Π½ΠΈΠ·ΠΊΠΈΠΌ GWP. ΠΡΠΎΠΌΠ΅ ΡΠΎΠ³ΠΎ, Π½Π°ΠΌ Π½Π΅ΠΎΠ±Ρ ΠΎΠ΄ΠΈΠΌΠΎ ΡΠ°Π·ΡΠ°Π±ΠΎΡΠ°ΡΡ ΡΠ΅Ρ Π½ΠΎΠ»ΠΎΠ³ΠΈΡ, ΠΊΠΎΡΠΎΡΠ°Ρ ΠΏΠΎΠ²ΡΡΠΈΡ ΡΠ΅Π½ΡΠ°Π±Π΅Π»ΡΠ½ΠΎΡΡΡ ΠΏΠΎΠ»ΠΈΠΈΠ·ΠΎ-ΠΊΠ°ΡΡΠΎΠ½Π° ΠΏΠΎ ΡΡΠ°Π²Π½Π΅Π½ΠΈΡ Ρ Π΄ΡΡΠ³ΠΈΠΌΠΈ ΠΈΠ·ΠΎΠ»ΡΡΠΈΠΎΠ½Π½ΡΠΌΠΈ ΠΌΠ°ΡΠ΅ΡΠΈΠ°Π»Π°ΠΌΠΈ. Π ΠΊΠΎΠ½ΡΠ΅ ΠΊΠΎΠ½ΡΠΎΠ², Π½Π΅ΠΈΠ·ΠΌΠ΅Π½Π½ΡΠΉ ΡΡΠΏΠ΅Ρ ΠΏΠΎΠ»ΠΈΠΈΠ·ΠΎ-ΠΏΠ»ΠΈΡ ΠΌΠΎΠΆΠ½ΠΎ ΠΎΠ±ΡΡΡΠ½ΠΈΡΡ ΠΌΠ½ΠΎΠ³ΠΈΠΌΠΈ ΡΠ°ΠΊΡΠΎΡΠ°ΠΌΠΈ, ΡΠ°ΠΊΠΈΠΌΠΈ ΠΊΠ°ΠΊ ΠΏΡΠ΅Π²ΠΎΡΡ ΠΎΠ΄Π½Π°Ρ ΡΠ΅ΡΠΌΠΈΡΠ΅ΡΠΊΠ°Ρ ΡΡΠΎΠΉΠΊΠΎΡΡΡ, Ρ ΠΎΡΠΎΡΠΈΠ΅ ΡΡΡΡΠΊΡΡΡΠ½ΡΠ΅ ΡΠ²ΠΎΠΉΡΡΠ²Π° ΠΈ ΠΎΡΠ»ΠΈΡΠ½ΡΠ΅ ΠΎΠ³Π½Π΅ΡΡΠΎΠΉΠΊΠΎΡΡΡ, Π½ΠΎ, ΠΏΡΠ΅ΠΆΠ΄Π΅ Π²ΡΠ΅Π³ΠΎ, ΡΠΊΠΎΠ½ΠΎΠΌΠΈΡΠ΅ΡΠΊΠΎΠΉ ΡΡΡΠ΅ΠΊΡΠΈΠ²Π½ΠΎΡΡΡΡ.ΠΠ»ΠΈΡΡ Polyiso Π²ΡΠ΅Π³Π΄Π° ΡΡΡΠ΅ΠΌΠΈΠ»ΠΈΡΡ Π±ΡΡΡ ΠΈΠ·ΠΎΠ»ΡΡΠΈΠ΅ΠΉ Ρ Π½Π°ΠΈΠΌΠ΅Π½ΡΡΠΈΠΌΠΈ Π·Π°ΡΡΠ°ΡΠ°ΠΌΠΈ Π½Π° ΡΡΡΠ°Π½ΠΎΠ²ΠΊΡ Π½Π° Π΅Π΄ΠΈΠ½ΠΈΡΡ R-ΡΠ΅Π½Π½ΠΎΡΡΠΈ, Π² ΡΠΎ ΠΆΠ΅ Π²ΡΠ΅ΠΌΡ ΠΎΡΠ²Π΅ΡΠ°Ρ ΡΡΡΡΠΊΡΡΡΠ½ΡΠΌ ΠΈ ΠΏΡΠΎΡΠΈΠ²ΠΎΠΏΠΎΠΆΠ°ΡΠ½ΡΠΌ ΡΡΠ΅Π±ΠΎΠ²Π°Π½ΠΈΡΠΌ ΡΡΡΠΎΠΈΡΠ΅Π»ΡΠ½ΡΡ Π½ΠΎΡΠΌ ΠΈ ΠΏΡΠ°Π²ΠΈΠ» EPA. ΠΠΎΠΌΠΏΠ°Π½ΠΈΡ Huntsman ΡΠΆΠ΅ Π΄Π°Π²Π½ΠΎ ΠΈΠ³ΡΠ°Π΅Ρ Π²Π΅Π΄ΡΡΡΡ ΡΠΎΠ»Ρ Π² ΡΠ°Π·Π²ΠΈΡΠΈΠΈ ΠΈΠ½Π΄ΡΡΡΡΠΈΠΈ ΠΏΠΎΠ»ΠΈΠΈΠ·ΠΎ. Π ΠΊΠ°ΡΠ΅ΡΡΠ²Π΅ ΠΏΡΠΈΠΌΠ΅ΡΠ°, ΠΎΠΆΠΈΠ΄Π°Ρ ΠΏΠΎΡΡΠ°ΠΏΠ½ΠΎΠ³ΠΎ ΠΎΡΠΊΠ°Π·Π° ΠΎΡ 1,1-Π΄ΠΈΡ Π»ΠΎΡ-1-ΡΡΠΎΡΡΡΠ°Π½Π° (HCFC-141b) Π² Π‘Π¨Π Π² ΠΊΠΎΠ½ΡΠ΅ 22-Π³ΠΎ Π³ΠΎΠ΄Π°, ΠΌΡ ΠΏΡΠ΅Π΄ΡΡΠ°Π²ΠΈΠ»ΠΈ Π΄ΠΎΠΊΡΠΌΠ΅Π½Ρ Π½Π° Π²ΡΡΡΠ°Π²ΠΊΠ΅ Polyurethanes Expo 98 Π² ΠΠ°Π»Π»Π°ΡΠ΅ Ρ ΡΠ΅ΠΊΠΎΠΌΠ΅Π½Π΄Π°ΡΠΈΠ΅ΠΉ, ΡΡΠΎ ΡΠΌΠ΅ΡΡ ΡΠΈΠΊΠ»ΠΎ ΠΈ ΠΈΠ·ΠΎΠΏΠ΅Π½ΡΠ°Π½ Π±ΡΠ»ΠΈ Π±Ρ ΠΎΠΏΡΠΈΠΌΠ°Π»ΡΠ½ΡΠΌ ΡΠΈΠ·ΠΈΡΠ΅ΡΠΊΠΈΠΌ Π²ΡΠΏΠ΅Π½ΠΈΠ²Π°ΡΡΠΈΠΌ Π°Π³Π΅Π½ΡΠΎΠΌ Ρ Π½ΡΠ»Π΅Π²ΡΠΌ ΠΠ Π [3].ΠΡΠΎΠΉ ΡΠ΅ΠΊΠΎΠΌΠ΅Π½Π΄Π°ΡΠΈΠΈ ΠΏΠΎΡΠ»Π΅Π΄ΠΎΠ²Π°Π»ΠΈ ΠΌΠ½ΠΎΠ³ΠΈΠ΅ ΠΏΡΠΎΠΈΠ·Π²ΠΎΠ΄ΠΈΡΠ΅Π»ΠΈ ΠΊΠ°ΡΡΠΎΠ½Π°. Π Π½Π°ΡΡΠΎΡΡΠ΅Π΅ Π²ΡΠ΅ΠΌΡ Π²ΡΠ΅ ΠΏΡΠΎΠΈΠ·Π²ΠΎΠ΄ΠΈΡΠ΅Π»ΠΈ ΠΊΠ°ΡΡΠΎΠ½Π° ΠΈΡΠΏΠΎΠ»ΡΠ·ΡΡΡ ΠΏΠ΅Π½ΡΠ°Π½ Π² ΠΊΠ°ΡΠ΅ΡΡΠ²Π΅ ΡΠΈΠ·ΠΈΡΠ΅ΡΠΊΠΈΡ Π²ΡΠΏΠ΅Π½ΠΈΠ²Π°ΡΡΠΈΡ Π°Π³Π΅Π½ΡΠΎΠ², Ρ ΠΎΡΡ ΡΠΎΡΠ½ΡΠΉ ΡΠΎΡΡΠ°Π² ΠΈΠ·ΠΎΠΌΠ΅ΡΠΎΠ² ΡΠΈΡΠΎΠΊΠΎ Π²Π°ΡΡΠΈΡΡΠ΅ΡΡΡ. ΠΠΎΡΠ»Π΅ ΠΏΠ΅ΡΠ΅Ρ ΠΎΠ΄Π° Π½Π° ΠΏΠ΅Π½ΡΠ°Π½ ΠΏΡΠΎΠΈΠ·Π²ΠΎΠ΄ΠΈΡΠ΅Π»ΠΈ ΠΊΠ°ΡΡΠΎΠ½Π° ΠΈΡΡΡ ΠΏΡΡΠΈ Π΄Π°Π»ΡΠ½Π΅ΠΉΡΠ΅Π³ΠΎ ΠΏΠΎΠ²ΡΡΠ΅Π½ΠΈΡ ΡΠ²ΠΎΠ΅ΠΉ ΡΠ΅Π½ΡΠ°Π±Π΅Π»ΡΠ½ΠΎΡΡΠΈ ΠΏΡΠΈ ΡΠΎΠ±Π»ΡΠ΄Π΅Π½ΠΈΠΈ ΡΡΠ΅Π±ΠΎΠ²Π°Π½ΠΈΠΉ ΠΊ ΠΏΡΠΎΠΈΠ·Π²ΠΎΠ΄ΠΈΡΠ΅Π»ΡΠ½ΠΎΡΡΠΈ. Π’ΡΠ΅Π±ΠΎΠ²Π°Π½ΠΈΡ ΠΊ Ρ Π°ΡΠ°ΠΊΡΠ΅ΡΠΈΡΡΠΈΠΊΠ°ΠΌ ΡΠ°ΠΊΡΠΈΡΠ΅ΡΠΊΠΈ ΠΈΠ·ΠΌΠ΅Π½ΠΈΠ»ΠΈΡΡ Ρ ΠΌΠΎΠΌΠ΅Π½ΡΠ° ΠΏΡΠ±Π»ΠΈΠΊΠ°ΡΠΈΠΈ ΡΡΠ°ΡΡΠΈ Π² 98. R-value Π±ΠΎΠ»ΡΡΠ΅ Π½Π΅ ΠΈΠ·ΠΌΠ΅ΡΡΠ΅ΡΡΡ ΡΠΎΠ»ΡΠΊΠΎ Ρ ΠΏΠΎΠΌΠΎΡΡΡ PIMA-11, ΠΊΠΎΡΠΎΡΡΠΉ Π²Π»Π΅ΡΠ΅Ρ Π·Π° ΡΠΎΠ±ΠΎΠΉ ΠΈΠ·ΠΌΠ΅ΡΠ΅Π½ΠΈΠ΅ k-ΡΠ°ΠΊΡΠΎΡΠ° ΠΏΠ»ΠΈΡ, Π²ΡΠ΄Π΅ΡΠΆΠ°Π½Π½ΡΡ Π² ΡΠ΅ΡΠ΅Π½ΠΈΠ΅ ΡΠ΅ΡΡΠΈ ΠΌΠ΅ΡΡΡΠ΅Π² ΠΏΡΠΈ ΠΊΠΎΠΌΠ½Π°ΡΠ½ΠΎΠΉ ΡΠ΅ΠΌΠΏΠ΅ΡΠ°ΡΡΡΠ΅.Π’Π΅ΠΏΠ΅ΡΡ ΠΎΠ½ΠΎ ΡΠ°ΠΊΠΆΠ΅ ΠΈΠ·ΠΌΠ΅ΡΡΠ΅ΡΡΡ Ρ ΠΈΡΠΏΠΎΠ»ΡΠ·ΠΎΠ²Π°Π½ΠΈΠ΅ΠΌ ΡΠ°ΠΊ Π½Π°Π·ΡΠ²Π°Π΅ΠΌΠΎΠ³ΠΎ ΠΌΠ΅ΡΠΎΠ΄Π° Π΄ΠΎΠ»Π³ΠΎΠ²ΡΠ΅ΠΌΠ΅Π½Π½ΠΎΠ³ΠΎ ΡΠ΅ΡΠΌΠΈΡΠ΅ΡΠΊΠΎΠ³ΠΎ ΡΠΎΠΏΡΠΎΡΠΈΠ²Π»Π΅Π½ΠΈΡ (LTTR) ΠΈ ΠΎΠΏΡΠ΅Π΄Π΅Π»ΡΠ΅ΡΡΡ ΠΊΠ°ΠΊ ΡΡΠ΅Π΄Π½Π΅Π²Π·Π²Π΅ΡΠ΅Π½Π½ΠΎΠ΅ ΠΏΠΎ Π²ΡΠ΅ΠΌΠ΅Π½ΠΈ ΡΠ΅ΠΏΠ»ΠΎΠ²ΠΎΠ΅ ΡΠΎΠΏΡΠΎΡΠΈΠ²Π»Π΅Π½ΠΈΠ΅ Π·Π° 15-Π»Π΅ΡΠ½ΠΈΠΉ ΠΏΠ΅ΡΠΈΠΎΠ΄. Π’ΠΎΡΠ½Π°Ρ ΠΌΠ΅ΡΠΎΠ΄ΠΎΠ»ΠΎΠ³ΠΈΡ, ΠΈΡΠΏΠΎΠ»ΡΠ·ΡΠ΅ΠΌΠ°Ρ Π΄Π»Ρ ΠΈΠ·ΠΌΠ΅ΡΠ΅Π½ΠΈΡ LTTR, ΠΈΠ·Π»ΠΎΠΆΠ΅Π½Π° Π² ASTM C Π² Π‘Π¨Π ΠΈ CAN / ULC S77 Π² ΠΠ°Π½Π°Π΄Π΅ ΠΈ ΠΎΠ±ΡΡΠΆΠ΄Π°Π΅ΡΡΡ Π² ΡΡΠ°ΡΡΠ΅, ΠΏΡΠ΅Π΄ΡΡΠ°Π²Π»Π΅Π½Π½ΠΎΠΉ Π₯Π°Π½ΡΡΠΌΠ°Π½ΠΎΠΌ Π² 22 API [4]. ΠΡΠ΅ ΠΎΠ΄Π½ΠΎ Π½ΠΎΠ²ΠΎΠ²Π²Π΅Π΄Π΅Π½ΠΈΠ΅ — ΡΠΆΠ΅ΡΡΠΎΡΠ΅Π½ΠΈΠ΅ ΡΡΠ΅Π±ΠΎΠ²Π°Π½ΠΈΠΉ ΠΊ ΡΠΈΠ·ΠΈΡΠ΅ΡΠΊΠΈΠΌ ΡΠ²ΠΎΠΉΡΡΠ²Π°ΠΌ ΠΏΠ»ΠΈΡ ΠΈΠ· ΠΏΠΎΠ»ΠΈΠΈΠ·ΠΎ, ΠΊΠΎΡΠΎΡΡΡ ΡΡΠ΅Π±ΡΠ΅Ρ ΡΡΠ½ΠΎΠΊ. ΠΠ°ΠΏΡΠΈΠΌΠ΅Ρ, ΠΌΠΈΠ½ΠΈΠΌΠ°Π»ΡΠ½Π°Ρ ΠΏΡΠΎΡΠ½ΠΎΡΡΡ Π½Π° ΡΠΆΠ°ΡΠΈΠ΅ Π² Π½Π°ΠΏΡΠ°Π²Π»Π΅Π½ΠΈΠΈ ΡΠΎΠ»ΡΠΈΠ½Ρ ΠΈ ΡΡΠ°Π±ΠΈΠ»ΡΠ½ΠΎΡΡΡ ΡΠ°Π·ΠΌΠ΅ΡΠΎΠ² ΠΏΠΎΠ»ΠΈΠΈΠ·ΠΎ-ΠΊΠ°ΡΡΠΎΠ½Π°, ΠΊΠ°ΠΊ ΠΎΠΏΡΠ΅Π΄Π΅Π»Π΅Π½ΠΎ Π² 21 ΠΈΠ·Π΄Π°Π½ΠΈΠΈ ASTM C1289, ΡΠ²Π»ΡΡΡΡΡ Π±ΠΎΠ»Π΅Π΅ ΡΡΡΠΎΠ³ΠΈΠΌΠΈ, ΡΠ΅ΠΌ Π² ΠΈΠ·Π΄Π°Π½ΠΈΠΈ 98.Π’Π°ΠΊΠΈΠ΅ ΠΈΠ·ΠΌΠ΅Π½Π΅Π½ΠΈΡ Π² ΡΡΠ΅Π±ΠΎΠ²Π°Π½ΠΈΡΡ ΠΊ ΠΊΠΎΠ½Π΅ΡΠ½ΠΎΠΌΡ ΠΈΡΠΏΠΎΠ»ΡΠ·ΠΎΠ²Π°Π½ΠΈΡ ΠΈ Π½Π΅ΠΎΠ±Ρ ΠΎΠ΄ΠΈΠΌΠΎΡΡΡ ΠΏΠΎΠ΄Π΄Π΅ΡΠΆΠΈΠ²Π°ΡΡ ΠΊΠΎΠ½ΠΊΡΡΠ΅Π½ΡΠ½ΠΎΠ΅ ΠΏΡΠ΅ΠΈΠΌΡΡΠ΅ΡΡΠ²ΠΎ ΠΏΠΎΠ»ΠΈΠΈΠ·ΠΎ ΠΏΠΎ ΡΡΠ°Π²Π½Π΅Π½ΠΈΡ Ρ Π΄ΡΡΠ³ΠΈΠΌΠΈ ΡΠΈΠΏΠ°ΠΌΠΈ Π²ΡΠΏΠ΅Π½Π΅Π½Π½ΠΎΠΉ ΠΈΠ·ΠΎΠ»ΡΡΠΈΠΈ ΠΏΠΎΠ±ΡΠ΄ΠΈΠ»ΠΈ Π½Π°Ρ ΠΏΠ΅ΡΠ΅ΡΠΌΠΎΡΡΠ΅ΡΡ ΠΎΠΏΡΠΈΠΌΠ°Π»ΡΠ½ΡΠΉ ΡΠΈΠ·ΠΈΡΠ΅ΡΠΊΠΈΠΉ Π²ΡΠΏΠ΅Π½ΠΈΠ²Π°ΡΡΠΈΠΉ Π°Π³Π΅Π½Ρ Π΄Π»Ρ ΠΈΡΠΏΠΎΠ»ΡΠ·ΠΎΠ²Π°Π½ΠΈΡ Π² ΠΊΠ°ΡΡΠΎΠ½Π΅. ΠΡΠΈ ΠΎΡΠ΅Π½ΠΊΠ΅ ΠΈ ΡΠ°ΡΡΠΌΠΎΡΡΠ΅Π½ΠΈΠΈ ΡΡΠΎΠΈΠΌΠΎΡΡΠΈ Π²ΡΠΏΠ΅Π½ΠΈΠ²Π°ΡΡΠΈΡ Π°Π³Π΅Π½ΡΠΎΠ², ΡΠΎΠ²ΠΌΠ΅ΡΡΠΈΠΌΠΎΡΡΠΈ Ρ ΡΠ΅Π³Π΅Π½Π΅ΡΠ°ΡΠΈΠ²Π½ΡΠΌΠΈ ΡΠ΅ΡΠΌΠΈΡΠ΅ΡΠΊΠΈΠΌΠΈ ΠΎΠΊΠΈΡΠ»ΠΈΡΠ΅Π»ΡΠΌΠΈ ΠΈ Π΄ΠΎΡΡΡΠΏΠ½ΠΎΡΡΠΈ Π΄Π»Ρ ΠΈΡΠΏΠΎΠ»ΡΠ·ΠΎΠ²Π°Π½ΠΈΡ Π½Π° ΡΡΠ½ΠΊΠ΅ Π‘Π΅Π²Π΅ΡΠ½ΠΎΠΉ ΠΠΌΠ΅ΡΠΈΠΊΠΈ ΠΌΡ Π²ΡΠ±ΡΠ°Π»ΠΈ ΡΠΈΠΊΠ»ΠΎ-, Π½- ΠΈ ΠΈΠ·ΠΎΠΏΠ΅Π½ΡΠ°Π½ Π΄Π»Ρ ΡΠ³Π»ΡΠ±Π»Π΅Π½Π½ΡΡ ΠΎΡΠ΅Π½ΠΎΠΊ. Π ΠΏΡΠΎΡΠ»ΠΎΠΌ ΠΏΠΎΠ»ΠΈΠΈΠ·ΠΎΠΈΠ½Π΄ΡΡΡΡΠΈΡ ΠΈΡΠΏΠΎΠ»ΡΠ·ΠΎΠ²Π°Π»Π° Π½ΠΈΠ·ΠΊΠΎΠΊΠΈΠΏΡΡΠΈΠ΅ ΠΏΠΎΡΠΎΠΎΠ±ΡΠ°Π·ΠΎΠ²Π°ΡΠ΅Π»ΠΈ (LBBA) Π² ΠΊΠ°ΡΠ΅ΡΡΠ²Π΅ ΡΠΎΠ²ΠΌΠ΅ΡΡΠ½ΡΡ Π²ΡΠΏΠ΅Π½ΠΈΠ²Π°ΡΡΠΈΡ Π°Π³Π΅Π½ΡΠΎΠ², Π° ΠΈΠΌΠ΅Π½Π½ΠΎ Π΄ΠΈΡ Π»ΠΎΡΠ΄ΠΈΡΡΠΎΡΠΌΠ΅ΡΠ°Π½ (CFC-12) Ρ ΡΡΠΈΡ Π»ΠΎΡΡΡΠΎΡΠΌΠ΅ΡΠ°Π½ΠΎΠΌ (CFC-) ΠΈ Ρ Π»ΠΎΡΠ΄ΠΈΡΡΠΎΡΠΌΠ΅ΡΠ°Π½ (HCFC-22) Ρ HCFC-141b, Π΄Π»Ρ ΡΠ»ΡΡΡΠ΅Π½ΠΈΡ ΡΠ΅ΠΊΡΡΠ΅ΡΡΠΈ ΠΈ ΡΠΌΠ΅Π½ΡΡΠΈΡΠ΅ ΠΌΠΈΠ½ΠΈΠΌΠ°Π»ΡΠ½ΡΡ ΡΡΠ°Π±ΠΈΠ»ΡΠ½ΡΡ ΠΏΠ»ΠΎΡΠ½ΠΎΡΡΡ.ΠΡ ΡΠ°ΡΡΠΌΠΎΡΡΠ΅Π»ΠΈ ΠΌΠ½ΠΎΠΆΠ΅ΡΡΠ²ΠΎ ΡΠ°Π·Π»ΠΈΡΠ½ΡΡ LBBA, Π° ΠΈΠΌΠ΅Π½Π½ΠΎ Π½-Π±ΡΡΠ°Π½, ΠΈΠ·ΠΎΠ±ΡΡΠ°Π½, 1,1-Π΄ΠΈΡΡΠΎΡΡΡΠ°Π½ (HFC-152a) ΠΈ 1,1,1,2-ΡΠ΅ΡΡΠ°ΡΡΠΎΡΡΡΠ°Π½ (HFC-134a). ΠΠΎΡΠ»Π΅ ΡΠΎΠΎΠ±ΡΠ°ΠΆΠ΅Π½ΠΈΠΉ, Π°Π½Π°Π»ΠΎΠ³ΠΈΡΠ½ΡΡ ΡΠ΅ΠΌ, ΠΊΠΎΡΠΎΡΡΠ΅ ΠΎΠΏΠΈΡΠ°Π½Ρ Π² ΠΏΡΠ΅Π΄ΡΠ΄ΡΡΠ΅ΠΌ Π°Π±Π·Π°ΡΠ΅, ΠΌΡ Π²ΡΠ±ΡΠ°Π»ΠΈ ΠΈΠ·ΠΎΠ±ΡΡΠ°Π½ Π΄Π»Ρ ΡΠ³Π»ΡΠ±Π»Π΅Π½Π½ΠΎΠΉ ΠΎΡΠ΅Π½ΠΊΠΈ. ΠΠ»Ρ ΠΎΡΠ΅Π½ΠΊΠΈ Π² ΡΡΠΎΠΌ ΠΈΡΡΠ»Π΅Π΄ΠΎΠ²Π°Π½ΠΈΠΈ Π±ΡΠ»ΠΈ Π²ΡΠ±ΡΠ°Π½Ρ ΡΠ»Π΅Π΄ΡΡΡΠΈΠ΅ ΡΠ΅ΠΌΡ ΡΠΏΠ°ΠΊΠΎΠ²ΠΎΠΊ ΡΠΈΠ·ΠΈΡΠ΅ΡΠΊΠΈΡ ΠΏΠΎΡΠΎΠΎΠ±ΡΠ°Π·ΠΎΠ²Π°ΡΠ΅Π»Π΅ΠΉ: (a) (b) (c) (d) (e) (f) (g) 8: 2 ΡΠΈΠΊΠ»ΠΎΠΏΠ΅Π½ΡΠ°Π½: ΠΈΠ·ΠΎΠΏΠ΅Π½ΡΠ°Π½ ΠΏΠΎ ΠΌΠ°ΡΡΠ΅ 1% ΠΈΠ·ΠΎΠΏΠ΅Π½ΡΠ°Π½ 7: 3 ΠΈΠ·ΠΎΠΏΠ΅Π½ΡΠ°Π½: Π½-ΠΏΠ΅Π½ΡΠ°Π½ 3: 7 ΠΈΠ·ΠΎΠΏΠ΅Π½ΡΠ°Π½: Π½-ΠΏΠ΅Π½ΡΠ°Π½ 1% Π½-ΠΏΠ΅Π½ΡΠ°Π½ 64: 28: 8 ΠΈΠ·ΠΎΠΏΠ΅Π½ΡΠ°Π½: Π½-ΠΏΠ΅Π½ΡΠ°Π½: ΠΈΠ·ΠΎΠ±ΡΡΠ°Π½ 73:: 8 ΡΠΈΠΊΠ»ΠΎΠΏΠ΅Π½ΡΠ°Π½: ΠΈΠ·ΠΎΠΏΠ΅Π½ΡΠ°Π½: ΠΈΠ·ΠΎΠ±ΡΡΠ°Π½ ΠΠ΅Π½ΠΎΠΎΠ±ΡΠ°Π·ΠΎΠ²Π°ΡΠ΅Π»Ρ (Π°) ΡΠ²Π»ΡΠ΅ΡΡΡ ΡΡΡΠ»ΠΊΠΎΠΉ ΠΈΠ· Π½Π°ΡΠ΅Π³ΠΎ 98 Π‘ΡΠ°ΡΡΡ API Π½Π° ΡΡΡ ΡΠ΅ΠΌΡ [2].ΠΠ°ΠΊ Π²ΠΈΠ΄Π½ΠΎ ΠΈΠ· ΡΠ°Π±Π»ΠΈΡΡ 1, ΡΠ΅ΠΌΠΏΠ΅ΡΠ°ΡΡΡΠ° ΠΊΠΈΠΏΠ΅Π½ΠΈΡ ΠΈ ΡΡΠΎΠΈΠΌΠΎΡΡΡ ΡΠΈΠΊΠ»ΠΎΠΏΠ΅Π½ΡΠ°Π½Π° (ΡΠΈΠΊΠ»ΠΎΠΏΠ΅Π½ΡΠ°Π½Π°) Π²ΡΡΠ΅ ΠΏΠΎ ΡΡΠ°Π²Π½Π΅Π½ΠΈΡ Ρ ΠΈΠ·ΠΎΠΏΠ΅Π½ΡΠ°Π½ΠΎΠΌ (iso-p) ΠΈ Π½-ΠΏΠ΅Π½ΡΠ°Π½ΠΎΠΌ (np), ΠΏΠΎΡΡΠΎΠΌΡ Π΄Π»Ρ Π΄Π°Π½Π½ΠΎΠ³ΠΎ ΠΈΡΡΠ»Π΅Π΄ΠΎΠ²Π°Π½ΠΈΡ ΠΌΡ ΡΠ΅ΡΠΈΠ»ΠΈ Π½Π΅ ΠΈΡΠΏΠΎΠ»ΡΠ·ΠΎΠ²Π°ΡΡ ΡΠΈΠΊΠ»ΠΎΠΏΠ΅Π½ΡΠ°Π½. Π² Π»ΡΠ±ΡΡ ΡΠΌΠ΅ΡΡΡ , Π½Π΅ ΡΠΎΠ΄Π΅ΡΠΆΠ°ΡΠΈΡ ΡΡΠ½Ρ-ΡΠΈΠ»Π°. ΠΡΠΏΠ΅Π½ΠΈΠ²Π°ΡΡΠΈΠ΅ Π°Π³Π΅Π½ΡΡ (b) — (e) ΠΏΡΠ΅Π΄ΡΡΠ°Π²Π»ΡΡΡ ΡΠΎΠ±ΠΎΠΉ ΡΠΌΠ΅ΡΠΈ ΠΈΠ·ΠΎ-ΠΏ ΠΈ Π½-ΠΏ Ρ ΡΠ΅Π»ΡΡ Π½Π°ΠΉΡΠΈ ΠΎΠΏΡΠΈΠΌΠ°Π»ΡΠ½ΡΡ ΡΠΌΠ΅ΡΡ ΠΈΠ· Π΄Π²ΡΡ . Π ΠΏΠΎΡΠΎΠΎΠ±ΡΠ°Π·ΠΎΠ²Π°ΡΠ΅Π»Π΅ (f) ΠΈ (g) ΠΌΡ Π²Π·ΡΠ»ΠΈ Π΄Π²Π° ΠΈΠ· ΡΠΊΠ°Π·Π°Π½Π½ΡΡ Π²ΡΡΠ΅ Π²ΡΠΏΠ΅Π½ΠΈΠ²Π°ΡΡΠΈΡ Π°Π³Π΅Π½ΡΠΎΠ² ΠΈ Π΄ΠΎΠ±Π°Π²ΠΈΠ»ΠΈ 1 ΠΌΠΎΠ»ΡΡΠ½ΡΠΉ% (8 ΠΌΠ°Ρ.%) ΠΠ·ΠΎΠ±ΡΡΠ°Π½Π°. ΠΠΎΠ΄ΠΎΠ±Π½ΡΠΉ ΡΡΠΎΠ²Π΅Π½Ρ CFC-12 ΠΈΠ»ΠΈ HCFC-22 ΠΈΡΡΠΎΡΠΈΡΠ΅ΡΠΊΠΈ ΠΈΡΠΏΠΎΠ»ΡΠ·ΠΎΠ²Π°Π»ΡΡ ΠΏΡΠΎΠΌΡΡΠ»Π΅Π½Π½ΠΎΡΡΡΡ.ΠΠΠ‘ΠΠΠ ΠΠΠΠΠ’ΠΠΠ¬ΠΠΠ― Π§ΠΠ‘Π’Π¬ ΠΠ»Ρ ΡΠΎΠ³ΠΎ, ΡΡΠΎΠ±Ρ ΠΎΡΠ΅Π½ΠΈΡΡ ΠΏΠ΅ΡΠ΅ΡΠΈΡΠ»Π΅Π½Π½ΡΠ΅ Π²ΡΡΠ΅ ΠΏΠΎΡΠΎΠΎΠ±ΡΠ°Π·ΠΎΠ²Π°ΡΠ΅Π»ΠΈ, Π½Π΅ΠΎΠ±Ρ ΠΎΠ΄ΠΈΠΌΠΎ Π±ΡΠ»ΠΎ Π²ΡΠ±ΡΠ°ΡΡ ΡΠΎΡΡΠ°Π², ΠΊΠΎΡΠΎΡΡΠΉ Π±ΡΠ΄Π΅Ρ Π΄Π°Π²Π°ΡΡ ΠΏΠ΅Π½Ρ Ρ ΠΎΡΠΎΡΠ΅Π³ΠΎ ΠΊΠ°ΡΠ΅ΡΡΠ²Π° Ρ ΠΊΠ°ΠΆΠ΄ΡΠΌ ΠΈΠ· Π²ΡΠΏΠ΅Π½ΠΈΠ²Π°ΡΡΠΈΡ Π°Π³Π΅Π½ΡΠΎΠ². Π§ΡΠΎΠ±Ρ ΡΡΡΠ°Π½ΠΎΠ²ΠΈΡΡ ΡΠ°ΠΊΡΡ ββΡΠΎΡΠΌΡΠ»ΠΈΡΠΎΠ²ΠΊΡ, Π±ΡΠ»Π° ΠΏΡΠΎΠ²Π΅Π΄Π΅Π½Π° ΡΠ΅ΡΠΈΡ ΠΎΡΠ΅Π½ΠΎΠΊ ΡΠΈΠΏΠ° ΡΠΊΡΠΈΠ½ΠΈΠ½Π³Π°. ΠΠΎ-ΠΏΠ΅ΡΠ²ΡΡ , ΡΠ΅ΡΠΈΡ ΠΏΠΎΠ»ΠΈΠΎΠ»ΠΎΠ² ΠΈ ΠΏΠΎΠ²Π΅ΡΡ Π½ΠΎΡΡΠ½ΠΎ-Π°ΠΊΡΠΈΠ²Π½ΡΡ Π²Π΅ΡΠ΅ΡΡΠ² ΠΏΡΠΎΠ²Π΅ΡΡΠ»ΠΈ Π½Π° ΡΡΠ°Π±ΠΈΠ»ΡΠ½ΠΎΡΡΡ ΡΠΌΠ΅ΡΠΈ. ΠΠ°ΡΠ΅ΠΌ Π²ΡΠ±ΡΠ°Π½Π½ΡΠ΅ ΡΠΎΡΡΠ°Π²Ρ Π±ΡΠ»ΠΈ ΡΠΌΠ΅ΡΠ°Π½Ρ Π²ΡΡΡΠ½ΡΡ, ΡΡΠΎΠ±Ρ ΠΏΠΎΠ»ΡΡΠΈΡΡ ΠΏΠ΅Π½Ρ Π² ΡΠ°ΡΠΊΠ΅, ΡΡΠΎΠ±Ρ ΡΠ±Π΅Π΄ΠΈΡΡΡΡ Π² ΠΊΠ°ΡΠ΅ΡΡΠ²Π΅ ΠΏΠ΅Π½Ρ, ΠΎ ΡΠ΅ΠΌ ΡΡΠ΄ΡΡ ΠΏΠΎ ΡΠ°Π·ΠΌΠ΅ΡΡ ΡΡΠ΅Π΅ΠΊ, ΠΎΠ΄Π½ΠΎΡΠΎΠ΄Π½ΠΎΡΡΠΈ ΡΡΠ΅Π΅ΠΊ, ΠΏΡΠΎΠ΄ΡΠ²ΠΊΠ°ΠΌ ΠΈ Ρ.Π΄. ΡΠΈΡΠΎΠΊΠ°Ρ, 2 Π³Π»ΡΠ±ΠΎΠΊΠΈΡ ΠΈ 42 Π΄Π»ΠΈΠ½Π½ΡΡ ΡΠΎΡΠΌΡ.Π€ΠΎΡΠΌΠ° Π½Π°Ρ ΠΎΠ΄ΠΈΠ»Π°ΡΡ Π½Π° ΠΊΠΎΠ½Π²Π΅ΠΉΠ΅ΡΠ΅, ΠΊΠΎΡΠΎΡΡΠΉ Π΄Π²ΠΈΠ³Π°Π»ΡΡ, ΠΊΠΎΠ³Π΄Π° Π½Π° Π½Π΅Π΅ Π·Π°Π»ΠΈΠ²Π°Π»ΠΈ ΠΏΠ΅Π½Ρ. Π‘ΠΊΠΎΡΠΎΡΡΡ ΠΊΠΎΠ½Π²Π΅ΠΉΠ΅ΡΠ° Π±ΡΠ»Π° ΠΎΡΡΠ΅Π³ΡΠ»ΠΈΡΠΎΠ²Π°Π½Π° ΡΠ°ΠΊΠΈΠΌ ΠΎΠ±ΡΠ°Π·ΠΎΠΌ, ΡΡΠΎΠ±Ρ ΠΏΠΎΠ»ΡΡΠΈΡΡ ΠΏΠ΅Π½ΠΎΠΏΠ»Π°ΡΡ ΡΠΎΠ»ΡΠΊΠΎ Ρ Π·Π°ΠΏΠΎΠ»Π½Π΅Π½ΠΈΠ΅ΠΌ Ρ ΠΎΡΠΈΠ΅Π½ΡΠ°ΡΠΈΠ΅ΠΉ ΡΡΠ΅Π΅ΠΊ, ΡΠΈΠΏΠΈΡΠ½ΠΎΠΉ Π΄Π»Ρ ΠΏΡΠΎΠΌΡΡΠ»Π΅Π½Π½ΠΎΠΉ Π»ΠΈΠ½ΠΈΠΈ Π»Π°ΠΌΠΈΠ½ΠΈΡΠΎΠ²Π°Π½ΠΈΡ. ΠΡΠ»ΠΈ Π½Π΅ ΡΠΊΠ°Π·Π°Π½ΠΎ ΠΈΠ½ΠΎΠ΅, Π΄Π»Ρ ΠΈΠ·Π³ΠΎΡΠΎΠ²Π»Π΅Π½ΠΈΡ Π²ΡΠ΅Ρ Π»Π°ΠΌΠΈΠ½Π°ΡΠΎΠ² ΠΈΡΠΏΠΎΠ»ΡΠ·ΠΎΠ²Π°Π»ΠΈΡΡ ΡΠ»Π΅Π΄ΡΡΡΠΈΠ΅ ΡΡΠ»ΠΎΠ²ΠΈΡ: Π ΡΡΠΎΠΌ ΠΈΡΡΠ»Π΅Π΄ΠΎΠ²Π°Π½ΠΈΠΈ ΡΠ°ΡΡΠΌΠ°ΡΡΠΈΠ²Π°Π»ΠΈΡΡ ΠΊΠ°ΠΊ ΠΆΠΈΠ΄ΠΊΠΈΠ΅, ΡΠ°ΠΊ ΠΈ Π½ΠΈΠ·ΠΊΠΎΠΊΠΈΠΏΡΡΠΈΠ΅ Π²ΡΠΏΠ΅Π½ΠΈΠ²Π°ΡΠ΅Π»ΠΈ. Π Π°ΡΡΠΌΠ°ΡΡΠΈΠ²Π°Π΅ΠΌΡΠ΅ ΠΆΠΈΠ΄ΠΊΠΈΠ΅ ΠΏΠ΅Π½ΠΎΠΎΠ±ΡΠ°Π·ΠΎΠ²Π°ΡΠ΅Π»ΠΈ Π²ΠΊΠ»ΡΡΠ°Π»ΠΈ Π²ΡΠ΅ ΠΈΠ·ΠΎΠΌΠ΅ΡΡ ΠΏΠ΅Π½ΡΠ°Π½Π°, 1,1,1,3,3-ΠΏΠ΅Π½ΡΠ°ΡΡΠΎΡΠΏΡΠΎΠΏΠ°Π½ (HFC-245fa), 1,1,1,3,3-ΠΏΠ΅Π½ΡΠ°ΡΡΠΎΡΠ±ΡΡΠ°Π½ (HFC-365mfc), 2-Ρ Π»ΠΎΡΠΏΡΠΎΠΏΠ°Π½ ΠΈ ΡΡΠ°Π½Ρ -1,2-Π΄ΠΈΡ Π»ΠΎΡΡΡΠΈΠ»Π΅Π½.ΠΠΎΡΠ»Π΅ Π»Π°Π±ΠΎΡΠ°ΡΠΎΡΠ½ΡΡ ΠΌΠ°ΡΡΡΠ°Π±ΠΎΠ² Π Π°ΡΡ ΠΎΠ΄ Ρ ΠΈΠΌΠΈΠΊΠ°ΡΠΎΠ² ΠΠ°Π²Π»Π΅Π½ΠΈΠ΅ ΡΠΌΠ΅ΡΠΈ Π’Π΅ΠΌΠΏΠ΅ΡΠ°ΡΡΡΠ° ΠΈΠ·ΠΎΡΠΈΠ°Π½Π°ΡΠ° Π’Π΅ΠΌΠΏΠ΅ΡΠ°ΡΡΡΠ° ΠΏΠΎΠ»ΠΈΠΎΠ»Π° Π’Π΅ΠΌΠΏΠ΅ΡΠ°ΡΡΡΠ° ΡΠΎΡΠΌΡ ΠΡΠ΅ΠΌΡ ΠΈΠ·Π²Π»Π΅ΡΠ΅Π½ΠΈΡ ΠΈΠ· ΡΠΎΡΠΌΡ = ΡΡΠ½Ρ / ΠΌΠΈΠ½. = 2 ΡΡΠ½ΡΠ° Π½Π° ΠΊΠ². ΠΡΠΉΠΌ = 8 Β° F = 8 Β° F = Β° F = 2 ΠΌΠΈΠ½ΡΡΡ 43
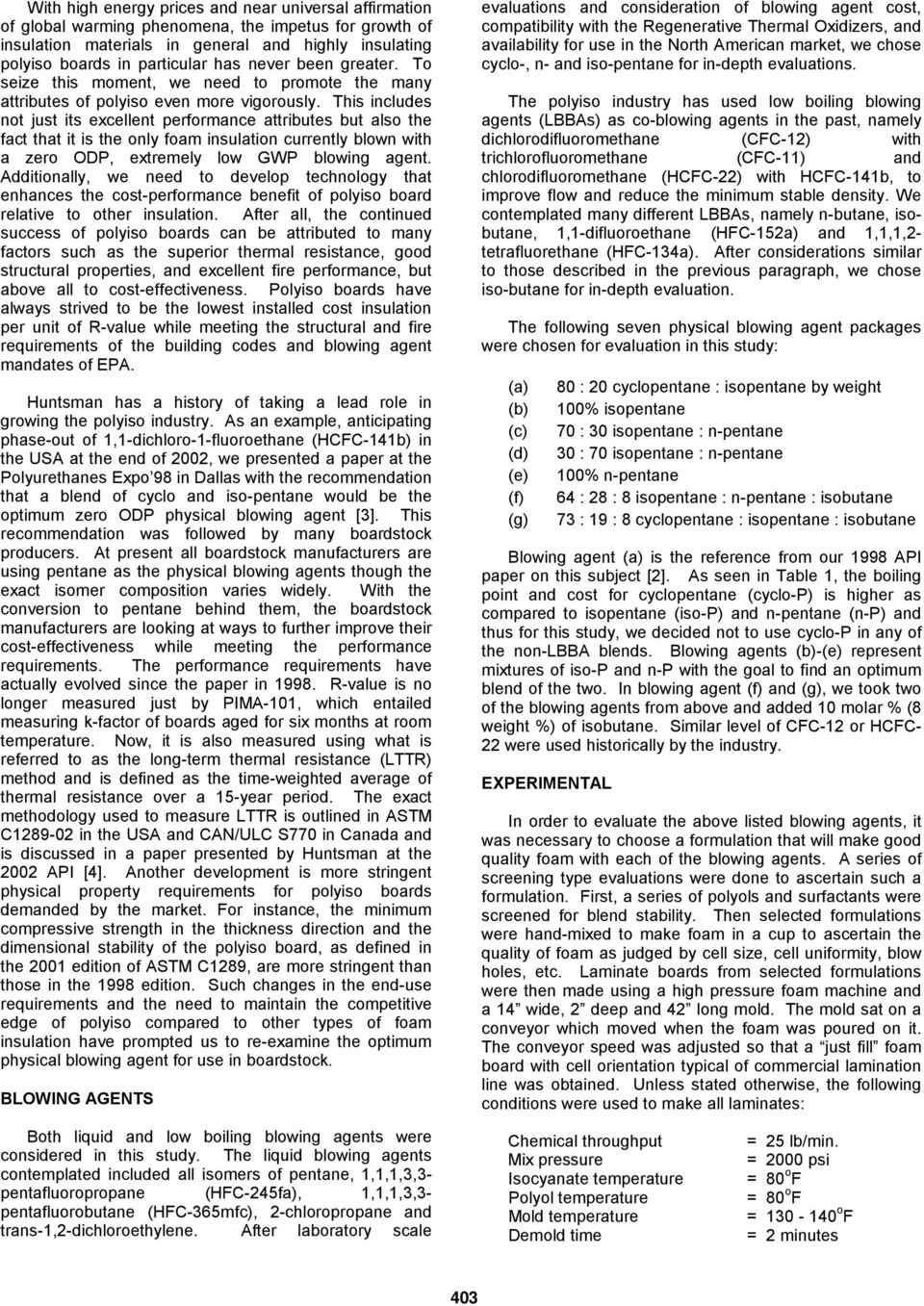
3 Π’Π°Π±Π»ΠΈΡΠ° 1. Π‘Π²ΠΎΠΉΡΡΠ²Π° Π²ΡΠ±ΡΠ°Π½Π½ΡΡ ΠΏΠ΅Π½ΠΎΠΎΠ±ΡΠ°Π·ΠΎΠ²Π°ΡΠ΅Π»Π΅ΠΉ Ρ Π½ΡΠ»Π΅Π²ΡΠΌ ΠΠ Π Π¦ΠΈΠΊΠ»ΠΎΠΏΠ΅Π½ΡΠ°Π½ N-ΠΏΠ΅Π½ΡΠ°Π½ ΠΠ·ΠΎΠΏΠ΅Π½ΡΠ°Π½ N-Π±ΡΡΠ°Π½ ΠΠ·ΠΎΠ±ΡΡΠ°Π½ HFC-134a ΠΠΎΠ»Π΅ΠΊΡΠ»ΡΡΠ½ΠΎ-ΠΌΠ°ΡΡΠΎΠ²Π°Ρ ΡΠΎΡΠΊΠ° ΠΊΠΈΠΏΠ΅Π½ΠΈΡ, o F ΠΠ°Π²Π»Π΅Π½ΠΈΠ΅ ΠΏΠ°ΡΠ°, oo C Π’Π΅ΠΏΠ»ΠΎΠΏΡΠΎΠ²ΠΎΠ΄Π½ΠΎΡΡΡ, ΠΠ’Π-Π΄ΡΠΉΠΌ / ΡΠ°Ρ -ft 2 — o F ΠΏΡΠΈ o C ΠΡΠ΅Π΄Π΅Π» Π²ΠΎΡΠΏΠ»Π°ΠΌΠ΅Π½ΡΠ΅ΠΌΠΎΡΡΠΈ Π² Π²ΠΎΠ·Π΄ΡΡ Π΅, ΠΎΠ±.% ΠΠ΅Ρ ΠΠΠ ΠΈΠ»ΠΈ OEL, ppm ΠΠ΅Ρ Π΄Π°Π½Π½ΡΡ 1 GWP (CO 2 = 1) <1 16 ΠΡΠ½ΠΎΡΠΈΡΠ΅Π»ΡΠ½Π°Ρ ΡΡΠΎΠΈΠΌΠΎΡΡΡ $ $ $ $ $ $$$ ΠΠ°ΠΌΠΈΠ½Π°Ρ Π±ΡΠ» Π²ΠΈΠ·ΡΠ°Π»ΡΠ½ΠΎ ΠΎΡΠΌΠΎΡΡΠ΅Π½ Π΄Π»Ρ ΠΊΠ°ΡΠ΅ΡΡΠ²Π° ΠΏΠ΅Π½Ρ ΠΈ Π°Π΄Π³Π΅Π·ΠΈΠΈ ΠΎΠ±Π»ΠΈΡΠΎΠ²ΠΊΠΈ.ΠΠ°ΡΠ΅ΠΌ Π±ΡΠ»ΠΎ ΠΏΡΠΈΠ½ΡΡΠΎ ΡΠ΅ΡΠ΅Π½ΠΈΠ΅ ΠΎ ΡΠΎΡΡΠ°Π²Π΅, ΠΊΠΎΡΠΎΡΡΠΉ Π±ΡΠ΄Π΅Ρ ΠΈΡΠΏΠΎΠ»ΡΠ·ΠΎΠ²Π°ΡΡΡΡ Π΄Π»Ρ ΠΎΡΠ½ΠΎΠ²Π½ΠΎΠΉ ΡΠ°ΡΡΠΈ ΡΡΠΎΠ³ΠΎ ΠΈΡΡΠ»Π΅Π΄ΠΎΠ²Π°Π½ΠΈΡ, ΡΠΎ Π΅ΡΡΡ Π΄Π»Ρ ΠΎΡΠ΅Π½ΠΊΠΈ ΡΠ°Π·Π»ΠΈΡΠ½ΡΡ Π²ΡΠΏΠ΅Π½ΠΈΠ²Π°ΡΡΠΈΡ Π°Π³Π΅Π½ΡΠΎΠ². ΠΠ°ΠΊ ΠΏΠΎΠΊΠ°Π·Π°Π½ΠΎ Π² ΡΠ°Π±Π»ΠΈΡΠ΅ 2, ΡΠΌΠ΅ΡΡ ΠΏΠΎΠ»ΠΈΠΎΠ»ΠΎΠ² ΡΠΎΡΡΠΎΡΠ»Π° ΠΈΠ· 1 ΡΠ°ΡΡΠΈ Π²ΡΠ±ΡΠ°Π½Π½ΠΎΠ³ΠΎ Π°ΡΠΎΠΌΠ°ΡΠΈΡΠ΅ΡΠΊΠΎΠ³ΠΎ ΡΠ»ΠΎΠΆΠ½ΠΎΠ³ΠΎ ΠΏΠΎΠ»ΠΈΡΡΠΈΡΠΏΠΎΠ»ΠΈΠΎΠ»Π°, 1 ΡΠ°ΡΡΠΈ ΡΡΠΈ (Π±Π΅ΡΠ°Ρ Π»ΠΎΡΠΈΠ·ΠΎΠΏΡΠΎΠΏΠΈΠ») ΡΠΎΡΡΠ°ΡΠ°, 4,2 ΡΠ°ΡΡΠ΅ΠΉ ΠΎΠΊΡΠΎΠ°ΡΠ° ΠΊΠ°Π»ΠΈΡ Π² Π΄ΠΈΡΡΠΈΠ»Π΅Π½Π³Π»ΠΈΠΊΠΎΠ»Π΅, 0,3 ΡΠ°ΡΡΠΈ ΠΊΠ°ΡΠ°Π»ΠΈΠ·Π°ΡΠΎΡΠ° Π½Π° ΠΎΡΠ½ΠΎΠ²Π΅ ΡΡΠ΅ΡΠΈΡΠ½ΠΎΠ³ΠΎ Π°ΠΌΠΈΠ½Π°, 2 ΡΠ°ΡΡΠΈ ΡΠΈΠ»ΠΈΠΊΠΎΠ½Π°. ΠΏΠΎΠ²Π΅ΡΡ Π½ΠΎΡΡΠ½ΠΎ-Π°ΠΊΡΠΈΠ²Π½ΠΎΠ΅ Π²Π΅ΡΠ΅ΡΡΠ²ΠΎ ΠΈ 5 ΡΠ°ΡΡΠ΅ΠΉ Π²ΠΎΠ΄Ρ. ΠΡΠΏΠ΅Π½ΠΈΠ²Π°ΡΡΠΈΠ΅ Π°Π³Π΅Π½ΡΡ (Π°) (ΠΆ) ΠΎΡΠ΅Π½ΠΈΠ²Π°Π»ΠΈ ΠΏΡΡΠ΅ΠΌ ΠΈΠ·Π³ΠΎΡΠΎΠ²Π»Π΅Π½ΠΈΡ ΠΌΠ½ΠΎΠ³ΠΎΡΠ»ΠΎΠΉΠ½ΡΡ ΠΏΠ»ΠΈΡ Ρ ΠΏΠΎΠΌΠΎΡΡΡ ΠΊΠΎΠ½Π²Π΅ΠΉΠ΅ΡΠ½ΠΎΠΉ ΡΠΎΡΠΌΡ ΠΈ ΠΌΠ°ΡΠΈΠ½Ρ Π²ΡΡΠΎΠΊΠΎΠ³ΠΎ Π΄Π°Π²Π»Π΅Π½ΠΈΡ Ρ ΠΈΡΠΏΠΎΠ»ΡΠ·ΠΎΠ²Π°Π½ΠΈΠ΅ΠΌ ΠΏΡΠΎΡΠ΅Π΄ΡΡΡ, ΠΏΡΠΈΠ²Π΅Π΄Π΅Π½Π½ΠΎΠΉ Π²ΡΡΠ΅.ΠΡΠ΅ Π»Π°ΠΌΠΈΠ½Π°ΡΠ½ΡΠ΅ ΠΏΠ»ΠΈΡΡ Π±ΡΠ»ΠΈ ΠΏΡΠΎΡΠ΅ΡΡΠΈΡΠΎΠ²Π°Π½Ρ Π½Π° ΠΏΠ»ΠΎΡΠ½ΠΎΡΡΡ (ASTM D1622), ΡΠ΅ΠΏΠ»ΠΎΠΏΡΠΎΠ²ΠΎΠ΄Π½ΠΎΡΡΡ (ASTM C518), LTTR (ASTM C1289, ΠΏΡΠΈΠ»ΠΎΠΆΠ΅Π½ΠΈΠ΅ A), ΠΏΡΠΎΡΠ½ΠΎΡΡΡ Π½Π° ΡΠΆΠ°ΡΠΈΠ΅ (ASTM D1621, ΠΏΡΠΎΡΠ΅Π΄ΡΡΠ° A), ΡΡΠ°Π±ΠΈΠ»ΡΠ½ΠΎΡΡΡ ΡΠ°Π·ΠΌΠ΅ΡΠΎΠ² (ASTM D2126, 7 Π΄Π½Π΅ΠΉ ΠΏΡΠΈ -4 Β° C). C / ΠΎΠΊΡ.% RH ΠΈ 7 o C / 97% RH), Π°Π΄Π³Π΅Π·ΠΈΡ ΠΊ ΠΎΡΡΠ»Π°ΠΈΠ²Π°Π½ΠΈΡ [4], Ρ ΡΡΠΏΠΊΠΎΡΡΡ (ASTM C421), ΡΠΎΠΎΡΠ½ΠΎΡΠ΅Π½ΠΈΠ΅ PIR / PUR [5], Π΄ΡΠΌΠΎΡ ΠΎΠ΄Π° ΠΠ°ΡΠ»Π΅ΡΠ° (ASTM D314) ΠΈ ΠΏΠ»ΠΎΡΠ½ΠΎΡΡΡ Π΄ΡΠΌΠ° (ASTM E662). Π‘ΠΎΡΡΠ°Π² ΡΡΠ΅Π΅ΡΠ½ΠΎΠ³ΠΎ Π³Π°Π·Π° ΠΈΠ·ΠΌΠ΅ΡΡΠ»ΡΡ Π½Π° Π²ΡΠ±ΡΠ°Π½Π½ΡΡ ΠΏΠ»Π°ΡΠ°Ρ [6]. Π ΠΠΠ£ΠΠ¬Π’ΠΠ’Π« Π ΠΠΠ‘Π£ΠΠΠΠΠΠ ΠΠΈΡΠΏΠ΅ΡΡΠΈΠΎΠ½Π½ΡΠΉ Π°Π½Π°Π»ΠΈΠ· Π΄Π°Π½Π½ΡΡ Π±ΡΠ» ΠΏΡΠΎΠ²Π΅Π΄Π΅Π½ Ρ ΠΈΡΠΏΠΎΠ»ΡΠ·ΠΎΠ²Π°Π½ΠΈΠ΅ΠΌ ΠΏΡΠΎΠ³ΡΠ°ΠΌΠΌΠ½ΠΎΠ³ΠΎ ΠΎΠ±Π΅ΡΠΏΠ΅ΡΠ΅Π½ΠΈΡ Π΄Π»Ρ ΡΡΠ°ΡΠΈΡΡΠΈΡΠ΅ΡΠΊΠΎΠ³ΠΎ Π°Π½Π°Π»ΠΈΠ·Π° Π΄Π°Π½Π½ΡΡ .Π ΡΠ°Π±Π»ΠΈΡΠ΅ 2 ΠΏΠΎΠΊΠ°Π·Π°Π½Ρ Π²ΡΠ΅ ΡΠΎΡΡΠ°Π²Ρ ΠΈ ΡΠ΅Π·ΡΠ»ΡΡΠ°ΡΡ. ΠΡΠΈΡΠΈΡΠ΅ΡΠΊΠΎΠ΅ Π·Π½Π°ΡΠ΅Π½ΠΈΠ΅ p, ΡΠ°Π²Π½ΠΎΠ΅ 5, Π±ΡΠ»ΠΎ Π²ΡΠ±ΡΠ°Π½ΠΎ, ΡΡΠΎΠ±Ρ ΠΎΠΏΡΠ΅Π΄Π΅Π»ΠΈΡΡ, Π±ΡΠ»ΠΎ Π»ΠΈ ΡΠ²ΠΎΠΉΡΡΠ²ΠΎ ΡΡΡΠ΅ΡΡΠ²Π΅Π½Π½ΠΎ Π·Π°ΡΡΠΎΠ½ΡΡΠΎ ΠΏΠ΅ΡΠ΅ΠΌΠ΅Π½Π½ΡΠΌΠΈ ΠΈΠ»ΠΈ Π½Π΅Ρ. ΠΠ° ΠΈΡΠΊΠ»ΡΡΠ΅Π½ΠΈΠ΅ΠΌ ΠΌΠ°ΠΊΡΠΈΠΌΠ°Π»ΡΠ½ΠΎΠΉ ΠΏΠ»ΠΎΡΠ½ΠΎΡΡΠΈ Π΄ΡΠΌΠ° ΡΠΎ Π·Π½Π°ΡΠ΅Π½ΠΈΠ΅ΠΌ 241 ΠΈ ΡΡΡ Π»ΠΎΡΡΠΈ ΡΠΎ Π·Π½Π°ΡΠ΅Π½ΠΈΠ΅ΠΌ 65, Π·Π½Π°ΡΠ΅Π½ΠΈΠ΅ p Π΄Π»Ρ Π²ΡΠ΅Ρ Π΄ΡΡΠ³ΠΈΡ ΡΠ²ΠΎΠΉΡΡΠ², ΠΏΠ΅ΡΠ΅ΡΠΈΡΠ»Π΅Π½Π½ΡΡ Π² ΡΠ°Π±Π»ΠΈΡΠ΅ 2, Π±ΡΠ»ΠΎ ΠΌΠ΅Π½ΡΡΠ΅ 5, ΡΡΠΎ ΡΠ²ΠΈΠ΄Π΅ΡΠ΅Π»ΡΡΡΠ²ΡΠ΅Ρ ΠΎ ΡΠΎΠΌ, ΡΡΠΎ Π²ΡΠ±ΠΎΡ Π²ΡΠΏΠ΅Π½ΠΈΠ²Π°ΡΡΠ΅Π³ΠΎ Π°Π³Π΅Π½ΡΠ° Π΄Π΅ΠΉΡΡΠ²ΠΈΡΠ΅Π»ΡΠ½ΠΎ ΠΈΠΌΠ΅Π΅Ρ ΡΡΠ°ΡΠΈΡΡΠΈΡΠ΅ΡΠΊΠΈ Π·Π½Π°ΡΠΈΠΌΠΎΠ΅ Π·Π½Π°ΡΠ΅Π½ΠΈΠ΅. Π²Π»ΠΈΡΠ½ΠΈΠ΅ Π½Π° ΠΎΡΡΠ°Π»ΡΠ½ΡΠ΅ ΡΠ²ΠΎΠΉΡΡΠ²Π°. ΠΠ°ΡΠ΅ΡΡΠ²ΠΎ ΠΏΠ΅Π½Ρ ΠΠ°ΡΠ΅ΡΡΠ²ΠΎ ΠΏΠ΅Π½Ρ ΠΎΡΠ΅Π½ΠΈΠ²Π°Π»ΠΈ Π²ΠΈΠ·ΡΠ°Π»ΡΠ½ΠΎ.ΠΠ° ΠΈΡΠΊΠ»ΡΡΠ΅Π½ΠΈΠ΅ΠΌ ΠΏΠ΅Π½, ΠΈΠ·Π³ΠΎΡΠΎΠ²Π»Π΅Π½Π½ΡΡ Ρ ΠΈΡΠΏΠΎΠ»ΡΠ·ΠΎΠ²Π°Π½ΠΈΠ΅ΠΌ ΠΈΠ·ΠΎΠ±ΡΡΠ°Π½Π°, Π²ΡΠ΅ ΠΏΠ΅Π½Ρ Π²ΡΠ³Π»ΡΠ΄Π΅Π»ΠΈ Ρ ΠΎΡΠΎΡΠΎ, ΡΠΎ Π΅ΡΡΡ ΠΌΠ΅Π»ΠΊΠΈΠ΅ ΠΈ ΠΎΠ΄Π½ΠΎΡΠΎΠ΄Π½ΡΠ΅ ΠΏΠΎ ΡΠ°Π·ΠΌΠ΅ΡΡ ΡΡΠ΅ΠΉΠΊΠΈ, ΠΎΡΠ΅Π½Ρ ΠΌΠ°Π»ΠΎ ΠΏΡΡΡΠΎΡ, ΠΎΡΡΡΡΡΡΠ²ΠΈΠ΅ Π½Π΅ΡΠΌΠ΅ΡΠ°Π½Π½ΡΡ ΠΎΠ±Π»Π°ΡΡΠ΅ΠΉ ΠΈ ΡΠΈΠΏΠΈΡΠ½Π°Ρ ΡΡΠ΅ΠΊΠ»ΠΎΠ²ΠΈΠ΄Π½ΠΎΡΡΡ ΠΏΠ΅Π½ΠΎΠΌΠ°ΡΠ΅ΡΠΈΠ°Π»ΠΎΠ² PIR. ΠΠ΅Π½Π°, ΠΏΡΠΎΠ΄ΡΠ²Π°Π΅ΠΌΠ°Ρ Π²ΡΠΏΠ΅Π½ΠΈΠ²Π°ΡΡΠΈΠΌ Π°Π³Π΅Π½ΡΠΎΠΌ, ΡΠΎΠ΄Π΅ΡΠΆΠ°ΡΠΈΠΌ ΠΈΠ·ΠΎΠ±ΡΡΠ°Π½, Π²ΡΠ³Π»ΡΠ΄Π΅Π»Π° ΡΠ°ΠΊ ΠΆΠ΅, Π·Π° ΠΈΡΠΊΠ»ΡΡΠ΅Π½ΠΈΠ΅ΠΌ ΡΠΎΠ³ΠΎ, ΡΡΠΎ ΠΎΠ½Π° ΡΠΎΠ΄Π΅ΡΠΆΠ°Π»Π° ΡΡΠ΅Π·ΠΌΠ΅ΡΠ½ΡΠ΅ ΠΏΡΡΡΠΎΡΡ. ΠΡΠΎ Π³ΠΎΠ²ΠΎΡΠΈΡ ΠΎ ΠΏΡΠ΅ΠΆΠ΄Π΅Π²ΡΠ΅ΠΌΠ΅Π½Π½ΠΎΠΌ ΡΠ»Π΅ΡΡΡΠΈΠ²Π°Π½ΠΈΠΈ ΠΈΠ·ΠΎΠ±ΡΡΠ°Π½Π°. ΠΡΠΎ ΡΠΈΠΏΠΈΡΠ½ΠΎ Π΄Π»Ρ Π½Π°Π±Π»ΡΠ΄Π΅Π½ΠΈΠΉ, ΡΠ΄Π΅Π»Π°Π½Π½ΡΡ ΠΏΡΠΈ ΠΏΠ΅ΡΠ²ΠΎΠΉ ΠΏΠΎΠΏΡΡΠΊΠ΅ Ρ ΠΈΡΠΏΠΎΠ»ΡΠ·ΠΎΠ²Π°Π½ΠΈΠ΅ΠΌ Π΄ΡΡΠ³ΠΈΡ LBBA, ΠΈ Π²ΠΏΠΎΠ»Π½Π΅ Π²Π΅ΡΠΎΡΡΠ½ΠΎ, ΡΡΠΎ ΠΎΠΏΡΠΈΠΌΠΈΠ·Π°ΡΠΈΡ ΠΏΠΎΠ²Π΅ΡΡ Π½ΠΎΡΡΠ½ΠΎ-Π°ΠΊΡΠΈΠ²Π½ΠΎΠ³ΠΎ Π²Π΅ΡΠ΅ΡΡΠ²Π° ΠΌΠΎΠΆΠ΅Ρ ΠΏΡΠ΅ΠΎΠ΄ΠΎΠ»Π΅ΡΡ ΡΡΠΎ. Π ΡΠ°Π±Π»ΠΈΡΠ΅ 2 ΠΏΡΠ΅Π΄ΡΡΠ°Π²Π»Π΅Π½Ρ ΡΡΠΈ Π½Π°Π±ΠΎΡΠ° ΡΡΠ΅Π΄Π½ΠΈΡ ΠΏΠ»ΠΎΡΠ½ΠΎΡΡΠ΅ΠΉ: ΠΏΠ΅Π½ΠΎΠΏΠ»Π°ΡΡ Π΄Π»Ρ ΡΠ΅ΡΠ΄ΡΠ΅Π²ΠΈΠ½Ρ, Π²Π·ΡΡΡΠΉ ΠΈΠ· Π²Π΅ΡΡ Π½Π΅ΠΉ ΡΠ°ΡΡΠΈ ΡΠ²ΠΎΠ±ΠΎΠ΄Π½ΠΎ ΠΏΠΎΠ΄Π½ΠΈΠΌΠ°ΡΡΠ΅ΠΉΡΡ ΡΠ°ΡΠΊΠΈ, ΠΏΠ΅Π½ΠΎΠΏΠ»Π°ΡΡ Π΄Π»Ρ ΡΠ΅ΡΠ΄ΡΠ΅Π²ΠΈΠ½Ρ, Π²Π·ΡΡΡΠΉ ΠΈΠ· ΡΠΎΡΠΌΠΎΠ²Π°Π½Π½ΠΎΠ³ΠΎ ΠΏΠ΅Π½ΠΎΠΏΠ»Π°ΡΡΠ°, ΠΈ Π»Π°ΠΌΠΈΠ½Π°Ρ (Ρ ΠΎΠ±Π»ΠΈΡΠΎΠ²ΠΊΠΎΠΉ), ΠΈΡΠΏΠΎΠ»ΡΠ·ΡΠ΅ΠΌΡΠΉ Π΄Π»Ρ ΠΈΠ·ΠΌΠ΅ΡΠ΅Π½ΠΈΡ ΠΊΠΎΡΡΡΠΈΡΠΈΠ΅Π½ΡΠ° k.Π ΠΎΠ±ΡΠ΅ΠΌ, ΠΏΠ»ΠΎΡΠ½ΠΎΡΡΡ ΠΏΠ΅Π½, Π²ΡΠ΄ΡΡΡΡ ΠΈΠ·ΠΎ-ΠΏ ΠΈ Π½-ΠΏ ΠΈ ΠΈΡ ΡΠΌΠ΅ΡΠ΅ΠΉ, Π΄Π°Π΅Ρ Π±ΠΎΠ»Π΅Π΅ Π½ΠΈΠ·ΠΊΡΡ ΠΏΠ»ΠΎΡΠ½ΠΎΡΡΡ, ΡΠ΅ΠΌ Ρ ΡΠΌΠ΅ΡΠ΅ΠΉ ΡΠΈΠΊΠ»ΠΎ-ΠΏ / ΠΈΠ·ΠΎ-ΠΏ. Π‘ΡΠ΅Π΄ΠΈ ΠΈΠ·ΠΎ-Π, Π½-ΠΏ ΠΈ ΠΈΡ ΡΠΌΠ΅ΡΠ΅ΠΉ ΠΏΠ»ΠΎΡΠ½ΠΎΡΡΠΈ Π½Π΅ΡΠΊΠΎΠ»ΡΠΊΠΎ ΠΏΠ΅ΡΠ΅ΠΊΡΡΠ²Π°ΡΡΡΡ, Π½ΠΎ Π²ΡΠ΅ ΡΠΌΠ΅ΡΠΈ, Π±ΠΎΠ³Π°ΡΡΠ΅ ΠΈΠ·ΠΎ-ΠΏ ΠΈ ΠΈΠ·ΠΎ-ΠΏ, Π΄Π°Π»ΠΈ Π½Π΅ΠΌΠ½ΠΎΠ³ΠΎ ΠΌΠ΅Π½ΡΡΡΡ ΠΏΠ»ΠΎΡΠ½ΠΎΡΡΡ, ΡΠ΅ΠΌ Π½-ΠΏ. ΠΠΎΠ±Π°Π²Π»Π΅Π½ΠΈΠ΅ ΠΈΠ·ΠΎΠ±ΡΡΠ°Π½Π° ΡΠ²Π΅Π»ΠΈΡΠΈΠ²Π°Π»ΠΎ ΠΏΠ»ΠΎΡΠ½ΠΎΡΡΡ, ΡΡΠΎ, Π²Π΅ΡΠΎΡΡΠ½ΠΎ, ΠΏΠΎ ΠΊΡΠ°ΠΉΠ½Π΅ΠΉ ΠΌΠ΅ΡΠ΅ ΡΠ°ΡΡΠΈΡΠ½ΠΎ, ΡΠ²Π»ΡΠ΅ΡΡΡ ΠΎΡΡΠ°ΠΆΠ΅Π½ΠΈΠ΅ΠΌ ΠΎΠ±ΡΠ°Π·ΠΎΠ²Π°Π½ΠΈΡ ΠΏΠ»Π΅Π½ΠΊΠΈ, ΡΠ²ΡΠ·Π°Π½Π½ΠΎΠ³ΠΎ Ρ ΡΡΠ΅Π·ΠΌΠ΅ΡΠ½ΡΠΌΠΈ ΠΏΡΡΡΠΎΡΠ°ΠΌΠΈ Π² ΠΏΠ΅Π½Π΅. ΠΠ·ΠΌΠ΅ΡΠ΅Π½ΠΈΠ΅ ΠΏΠ΅Π½ΠΎΠΎΠ±ΡΠ°Π·ΠΎΠ²Π°ΡΠ΅Π»Π΅ΠΉ Π² Π³Π°Π·Π΅ ΡΡΠ΅Π΅ΠΊ ΠΈ ΠΏΠΎΠ»ΠΈΠΌΠ΅ΡΠ½ΠΎΠΉ ΠΌΠ°ΡΡΠΈΡΠ΅ ΠΏΡΠΎΠ»ΠΈΠ»ΠΎ Π½Π΅ΠΊΠΎΡΠΎΡΡΠΉ ΡΠ²Π΅Ρ Π½Π° Π°ΡΡΠΈΠ±ΡΡΡ ΠΏΠ»ΠΎΡΠ½ΠΎΡΡΠΈ, ΠΎΠΏΠΈΡΠ°Π½Π½ΡΠ΅ Π²ΡΡΠ΅.ΠΠ°ΠΊ Π²ΠΈΠ΄Π½ΠΎ Π½Π° Π ΠΈΡΡΠ½ΠΊΠ΅ 2, ΠΎΡΠ½ΠΎΡΠΈΡΠ΅Π»ΡΠ½ΡΠ΅ ΠΊΠΎΠ»ΠΈΡΠ΅ΡΡΠ²Π° Π²ΡΠΏΠ΅Π½ΠΈΠ²Π°ΡΡΠ΅Π³ΠΎ Π°Π³Π΅Π½ΡΠ°, ΠΎΠ±Π½Π°ΡΡΠΆΠ΅Π½Π½ΠΎΠ³ΠΎ Π² Π³Π°Π·Π΅ ΡΡΠ΅ΠΉΠΊΠΈ, ΠΏΠΎ ΡΡΠ°Π²Π½Π΅Π½ΠΈΡ Ρ ΠΊΠΎΠ»ΠΈΡΠ΅ΡΡΠ²ΠΎΠΌ Π² ΠΏΠΎΠ»ΠΈΠΌΠ΅ΡΠ΅ Π²Π°ΡΡΠΈΡΡΡΡΡΡ. ΠΡΠΎ ΠΈ ΠΌΠ½ΠΎΠ³ΠΈΠ΅ Π΄ΡΡΠ³ΠΈΠ΅ ΠΈΡΡΠ»Π΅Π΄ΠΎΠ²Π°Π½ΠΈΡ, ΠΏΡΠΎΠ²Π΅Π΄Π΅Π½Π½ΡΠ΅ Π² Huntsman, ΠΏΠΎΠΊΠ°Π·Π°Π»ΠΈ, ΡΡΠΎ ΠΊΠΎΠ»ΠΈΡΠ΅ΡΡΠ²ΠΎ ΠΏΠ΅Π½ΡΠ°Π½Π°, ΡΠ΅ΡΡΠ΅ΠΌΠΎΠ³ΠΎ Π² Π°ΡΠΌΠΎΡΡΠ΅ΡΡ Π²ΠΎ Π²ΡΠ΅ΠΌΡ Π²ΡΠΏΠ΅Π½ΠΈΠ²Π°Π½ΠΈΡ, Π½Π΅Π²Π΅Π»ΠΈΠΊΠΎ ΠΈ ΡΠΎΡΡΠ°Π²Π»ΡΠ΅Ρ ΠΏΠΎΡΡΠΈ 44
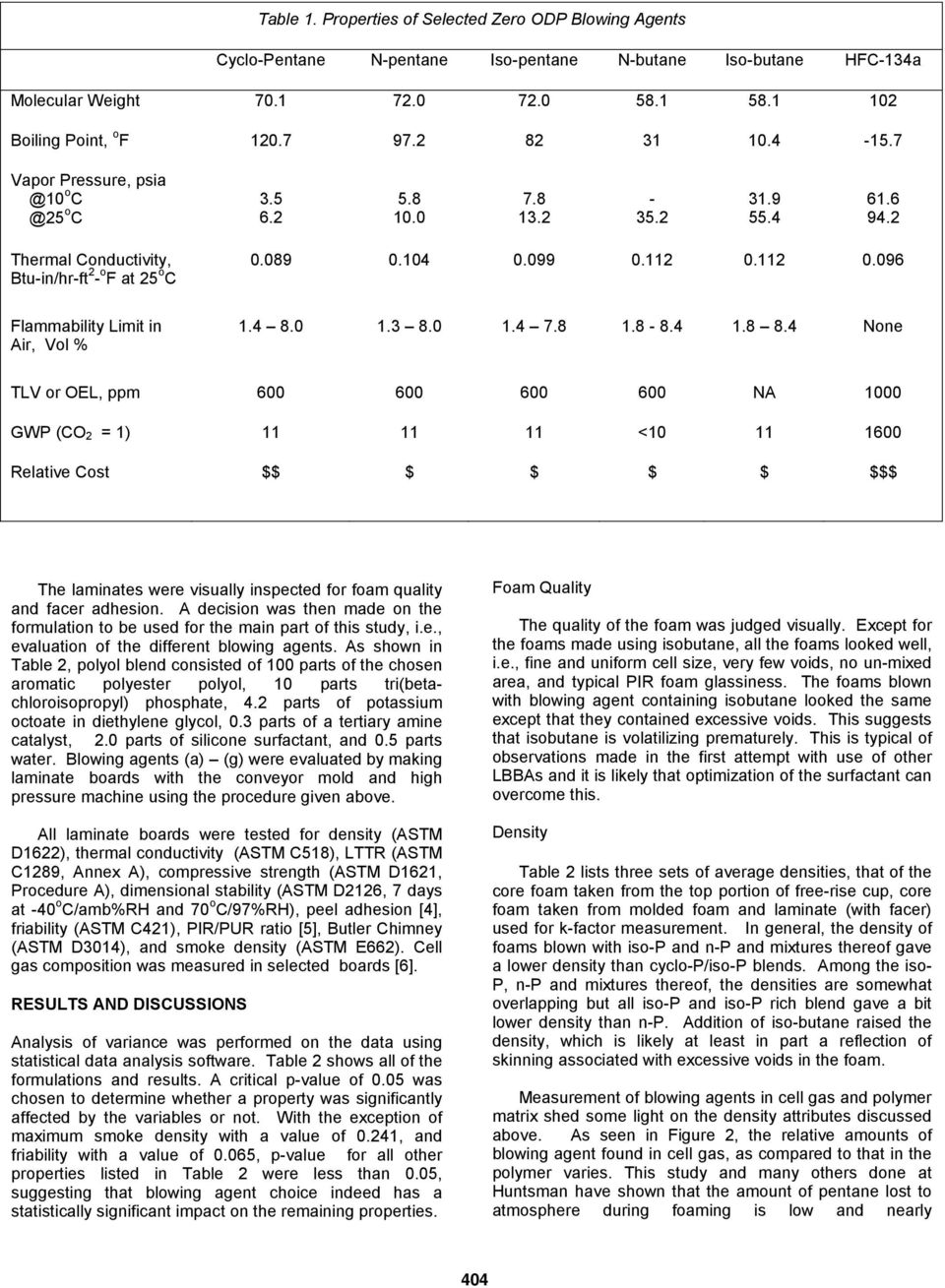
4 Π’Π°Π±Π»ΠΈΡΠ° 2. Π‘ΠΎΡΡΠ°Π²Ρ ΠΈ ΡΠ²ΠΎΠΉΡΡΠ²Π° 8: 2 ΡΠΈΠΊΠ»ΠΎ: ΠΈΠ·ΠΎ-ΠΏ ΠΈΠ·ΠΎ-ΠΏ 7: 3 ΠΈΠ·ΠΎ: Π½ΠΏ 3: 7 ΠΈΠ·ΠΎ: Π½ΠΏ Π½ΠΏ 64: 28: 8 ΡΠΈΠΊΠ»ΠΎ: ΠΈΠ·ΠΎ-ΠΏ: ΠΈΠ·ΠΎ-b 73:: 8 iso: np: iso-b Π‘ΠΌΠ΅ΡΡ ΠΏΠΎΠ»ΠΈΠΎΠ»ΠΎΠ² Π¦ΠΈΠΊΠ»ΠΎΠΏΠ΅Π½ΡΠ°Π½ ΠΠ·ΠΎΠΏΠ΅Π½ΡΠ°Π½ N-ΠΠ΅Π½ΡΠ°Π½ ΠΠ·ΠΎΠ±ΡΡΠ°Π½ RUBINATE 185 ΠΠ½Π΄Π΅ΠΊΡ MDI ΠΠ°ΡΠ΅ΡΡΠ²ΠΎ ΠΏΠ΅Π½Ρ Π₯ΠΎΡΠΎΡΠ΅Π΅ Π₯ΠΎΡΠΎΡΠ΅Π΅ Π₯ΠΎΡΠΎΡΠ΅Π΅ Π₯ΠΎΡΠΎΡΠ΅Π΅ Π₯ΠΎΡΠΎΡΠ΅Π΅ ΠΡΡΡΠΎΡΡ ΠΠ»ΠΎΡΠ½ΠΎΡΡΡ ΡΠ²ΠΎΠ±ΠΎΠ΄Π½ΠΎΠ³ΠΎ Π½Π°ΡΠ°ΡΡΠ°Π½ΠΈΡ, pcf ΠΠ»ΠΎΡΠ½ΠΎΡΡΡ ΠΏΠ΅Π½Ρ Π² ΡΠ΅ΡΠ΄Π΅ΡΠ½ΠΈΠΊΠ΅, pcf ΠΠ»ΠΎΡΠ½ΠΎΡΡΡ Π»Π°ΠΌΠΈΠ½Π°ΡΠ°, pcf R- Π·Π½Π°ΡΠ΅Π½ΠΈΠ΅, ΡΠ°Ρ-ΡΡΡ 2 — o F / BTU-Π΄ΡΠΉΠΌ, ΠΠ°ΡΠ°Π»ΡΠ½ΠΎΠ΅ Π·Π½Π°ΡΠ΅Π½ΠΈΠ΅ 3 LTTR 2 LTTR Π Π°Π·ΠΌ.Stab.,% ΠΠ±. ΠΠ·ΠΌΠ΅Π½Π΅Π½ΠΈΠ΅ 1 -4 o F 1 o F / 97% ΠΎΡΠ½ΠΎΡΠΈΡΠ΅Π»ΡΠ½ΠΎΠΉ Π²Π»Π°ΠΆΠ½ΠΎΡΡΠΈ ΠΡΠΎΡΠ½ΠΎΡΡΡ Π½Π° ΡΠΆΠ°ΡΠΈΠ΅, ΡΡΠ½Ρ / ΠΊΠ².Π΄ΡΠΉΠΌ ΠΠ°ΡΠΈΠ½Π° Π΄Π»Ρ ΠΏΠΎΠ΄ΡΠ΅ΠΌΠ° ΠΏΠΎΠΏΠ΅ΡΠ΅ΡΠ½ΠΎΠΉ ΠΌΠ°ΡΠΈΠ½Ρ pcf Π₯ΡΡΠΏΠΊΠΎΡΡΡ,% Π°Π΄Π³Π΅Π·ΠΈΠΈ ΠΊ ΠΎΡΡΠ»Π°ΠΈΠ²Π°Π½ΠΈΡ, ΡΡΠ½Ρ / ΠΊΠ².Π΄ΡΠΉΠΌ Π£Π΄Π΅ΡΠΆΠ°Π½ΠΈΠ΅ Π²Π΅ΡΠ° Π΄ΡΠΌΠΎΡ ΠΎΠ΄Π°,% ΠΡΠ΅ΠΌΡ Π³Π°ΡΠ΅Π½ΠΈΡ, ΡΠ΅ΠΊ ΠΠ°ΠΊΡΠΈΠΌΠ°Π»ΡΠ½Π°Ρ ΠΏΠ»ΠΎΡΠ½ΠΎΡΡΡ Π΄ΡΠΌΠ° ΠΡΠ½ΠΎΡΠ΅Π½ΠΈΠ΅ PIR / PUR RUBINATE — ΡΡΠΎ Π·Π°ΡΠ΅Π³ΠΈΡΡΡΠΈΡΠΎΠ²Π°Π½Π½Π°Ρ ΡΠΎΡΠ³ΠΎΠ²Π°Ρ ΠΌΠ°ΡΠΊΠ° Huntsman LLC Π² ΠΎΠ΄Π½ΠΎΠΉ ΠΈΠ»ΠΈ Π½Π΅ΡΠΊΠΎΠ»ΡΠΊΠΈΡ , Π½ΠΎ Π½Π΅ Π²ΠΎ Π²ΡΠ΅Ρ ΡΡΡΠ°Π½Π°Ρ . 45
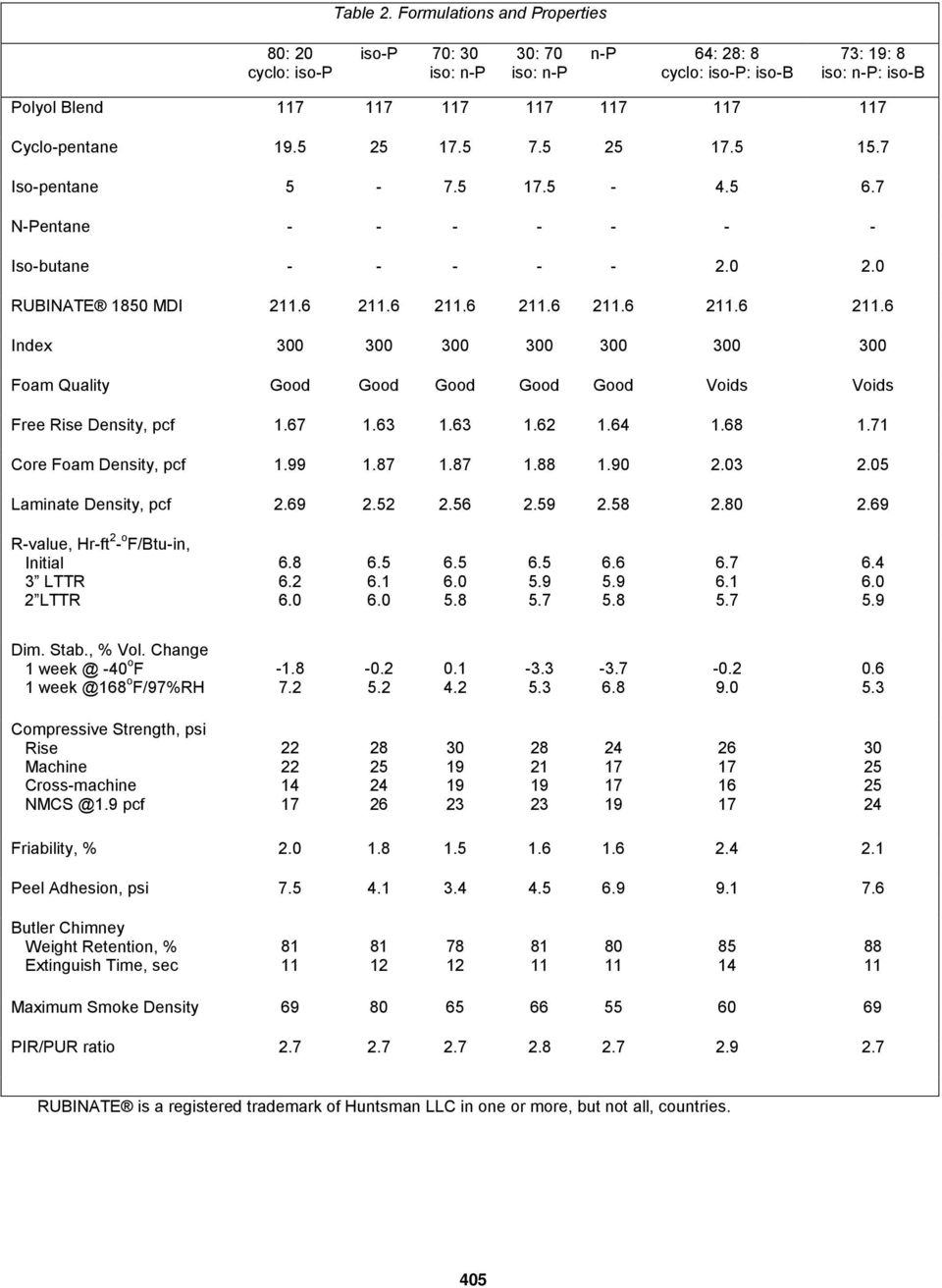
5 Π Π°Π·Π΄Π΅Π»Π΅Π½ΠΈΠ΅ Π²ΡΠΏΠ΅Π½ΠΈΠ²Π°ΡΡΠ΅Π³ΠΎ Π°Π³Π΅Π½ΡΠ° Π¦ΠΈΠΊΠ»ΠΎΠΏΠ΅Π½ΡΠ°Π½, Π½-ΠΏΠ΅Π½ΡΠ°Π½, ΠΈΠ·ΠΎΠΏΠ΅Π½ΡΠ°Π½, ΠΈΠ·ΠΎΠ±ΡΡΠ°Π½, ΠΏΠΎΠ»ΠΈΠΌΠ΅ΡΠ½ΡΠΉ Π³Π°Π· Π² ΡΡΠ΅ΠΉΠΊΠ΅ Π ΠΈΡ. 2.ΠΡΠ½ΠΎΡΠΈΡΠ΅Π»ΡΠ½ΠΎΠ΅ ΡΠ°ΡΠΏΡΠ΅Π΄Π΅Π»Π΅Π½ΠΈΠ΅ Π²ΡΠΏΠ΅Π½ΠΈΠ²Π°ΡΡΠ΅Π³ΠΎ Π°Π³Π΅Π½ΡΠ° Π½Π΅ Π·Π°Π²ΠΈΡΠΈΡ ΠΎΡ Π²ΡΠ±ΠΎΡΠ° ΠΈΠ·ΠΎΠΌΠ΅ΡΠ°, Π½ΠΎ ΠΊΠΎΠ»ΠΈΡΠ΅ΡΡΠ²ΠΎ, ΠΎΠ±Π½Π°ΡΡΠΆΠ΅Π½Π½ΠΎΠ΅ Π² ΡΠ»Π΅ΠΊΡΡΠΎΠ»ΠΈΠ·Π½ΠΎΠΌ Π³Π°Π·Π΅, ΡΠ²Π»ΡΠ΅ΡΡΡ ΡΠ°ΠΌΡΠΌ Π²ΡΡΠΎΠΊΠΈΠΌ Π΄Π»Ρ ΠΈΠ·ΠΎΠΏΠ΅Π½ΡΠ°Π½Π° ΠΈ ΡΠ°ΠΌΡΠΌ Π½ΠΈΠ·ΠΊΠΈΠΌ Π΄Π»Ρ ΡΠΈΠΊΠ»ΠΎΠΏΠ΅Π½ΡΠ°Π½Π°. ΠΠ»Ρ ΠΈΠ·ΠΎΠ±ΡΡΠ°Π½Π° ΠΊΠΎΠ»ΠΈΡΠ΅ΡΡΠ²ΠΎ, ΠΏΠΎΡΠ΅ΡΡΠ½Π½ΠΎΠ΅ Π² Π°ΡΠΌΠΎΡΡΠ΅ΡΡ Π²ΠΎ Π²ΡΠ΅ΠΌΡ Π²ΡΠΏΠ΅Π½ΠΈΠ²Π°Π½ΠΈΡ, Π±ΡΠ»ΠΎ ΡΠΎΠΏΠΎΡΡΠ°Π²ΠΈΠΌΠΎ Ρ ΠΊΠΎΠ»ΠΈΡΠ΅ΡΡΠ²ΠΎΠΌ Π΄Π»Ρ ΠΏΠ΅Π½ΡΠ°Π½Π° Π² ΡΡΠΎΠΌ ΠΈΡΡΠ»Π΅Π΄ΠΎΠ²Π°Π½ΠΈΠΈ, Π½ΠΎ ΠΌΡ Π½Π΅ ΠΏΠΎΠ²ΡΠΎΡΡΠ»ΠΈ ΡΠ°ΠΊΠΈΠ΅ ΠΈΡΡΠ»Π΅Π΄ΠΎΠ²Π°Π½ΠΈΡ. ΠΠΎΠ»Π΅Π΅ Π²ΡΡΠΎΠΊΠ°Ρ ΠΏΠ»ΠΎΡΠ½ΠΎΡΡΡ ΠΏΠ΅Π½Ρ, ΡΠΎΠ΄Π΅ΡΠΆΠ°ΡΠ΅ΠΉ ΠΈΠ·ΠΎΠ±ΡΡΠ°Π½, Π² ΡΡΠΎΠΌ ΠΈΡΡΠ»Π΅Π΄ΠΎΠ²Π°Π½ΠΈΠΈ, Π²Π΅ΡΠΎΡΡΠ½ΠΎ, ΠΎΠ±ΡΡΡΠ½ΡΠ΅ΡΡΡ ΡΠ½ΡΡΠΈΠ΅ΠΌ ΠΏΠ»Π΅Π½ΠΊΠΈ, ΡΠ²ΡΠ·Π°Π½Π½ΡΠΌ Ρ ΡΡΠ΅Π·ΠΌΠ΅ΡΠ½ΡΠΌ ΠΎΠ±ΡΠ°Π·ΠΎΠ²Π°Π½ΠΈΠ΅ΠΌ ΠΏΡΡΡΠΎΡ. ΠΠ½Π°ΡΠ΅Π½ΠΈΠ΅ R Π‘ΡΠ°Π±ΠΈΠ»ΡΠ½ΠΎΡΡΡ ΡΠ°Π·ΠΌΠ΅ΡΠΎΠ² Π‘ΡΠ°Π±ΠΈΠ»ΡΠ½ΠΎΡΡΡ ΡΠ°Π·ΠΌΠ΅ΡΠΎΠ² Π² Ρ ΠΎΠ»ΠΎΠ΄Π½ΠΎΠΌ ΡΠΎΡΡΠΎΡΠ½ΠΈΠΈ (ΡΠ°Π·ΠΌ.ΡΠ΄Π°Ρ) ΠΏΠ΅Π½Ρ, ΠΈΠ·ΠΌΠ΅ΡΠ΅Π½Π½ΠΎΠΉ ΠΏΡΡΠ΅ΠΌ ΡΡΠ°ΡΠ΅Π½ΠΈΡ ΠΏΠ΅Π½ΠΎΠΏΠ»Π°ΡΡΠ° 4 x 4 x 1 Π² ΡΠ΅ΡΠ΅Π½ΠΈΠ΅ ΠΎΠ΄Π½ΠΎΠΉ Π½Π΅Π΄Π΅Π»ΠΈ ΠΏΡΠΈ -4 o F Π²ΠΌΠ΅ΡΡΠ΅ Ρ ΠΏΠ»ΠΎΡΠ½ΠΎΡΡΡΡ ΠΏΠ΅Π½Ρ, ΠΊΠ°ΠΊ ΠΏΠΎΠΊΠ°Π·Π°Π½ΠΎ Π½Π° ΡΠΈΡΡΠ½ΠΊΠ΅ 4. ΠΠ°Π½Π½ΡΠ΅ ΠΏΠΎΠΊΠ°Π·ΡΠ²Π°ΡΡ, ΡΡΠΎ Ρ ΠΎΠ»ΠΎΠ΄Π½Π°Ρ ΡΡΡΠΊΠ»ΠΎΡΡΡ. ΡΠ΄Π°Ρ. Π²ΡΠ΅Ρ ΠΈΠ·ΠΎ-ΠΏ ΠΈ 7: 3 ΠΈΠ·ΠΎ-ΠΏ / Π½-ΠΏ ΡΠ²Π»ΡΠ΅ΡΡΡ Ρ ΠΎΡΠΎΡΠΈΠΌ ΠΏΡΠΈ ΠΏΠ»ΠΎΡΠ½ΠΎΡΡΠΈ 1,87 ΠΏΠΊΡ, ΡΠΎΠ³Π΄Π° ΠΊΠ°ΠΊ ΡΠΎ ΠΆΠ΅ ΡΠ°ΠΌΠΎΠ΅ Π΄Π»Ρ ΡΡΠ°Π»ΠΎΠ½Π½ΠΎΠ³ΠΎ 8: 2 ΡΠΈΠΊΠ»ΠΎ-ΠΏ / ΠΈΠ·ΠΎ-ΠΏ ΡΠ²Π»ΡΠ΅ΡΡΡ ΠΌΠ°ΡΠ³ΠΈΠ½Π°Π»ΡΠ½ΡΠΌ ΠΏΡΠΈ Π±ΠΎΠ»Π΅Π΅ Π²ΡΡΠΎΠΊΠΎΠΉ ΠΏΠ»ΠΎΡΠ½ΠΎΡΡΠΈ, ΠΏΡΠΈΠΌΠ΅ΡΠ½ΠΎ 2 ΠΏΠΊΡ. Π₯ΠΎΠ»ΠΎΠ΄Π½ΡΠΉ ΡΡΡΠΊΠ»ΡΠΉ. ΡΠ΄Π°Ρ. Π²ΡΠ΅Ρ n-p ΠΈ 3: 7 iso-p / n-p ΠΏΠ»ΠΎΡ ΠΎΠ΅ ΠΏΡΠΈ ΠΏΠ»ΠΎΡΠ½ΠΎΡΡΠΈ ~ 1.9 pcf. Π₯ΠΎΠ»ΠΎΠ΄Π½ΡΠΉ ΡΡΡΠΊΠ»ΡΠΉ. ΡΠ΄Π°Ρ. ΠΏΠ΅Π½, ΠΏΡΠΎΠ΄ΡΠ²Π°Π΅ΠΌΡΡ ΡΠΌΠ΅ΡΡΠΌΠΈ, ΡΠΎΠ΄Π΅ΡΠΆΠ°ΡΠΈΠΌΠΈ ΠΈΠ·ΠΎΠ±ΡΡΠ°Π½, Ρ ΠΎΡΠΎΡ, Π½ΠΎ ΠΏΠ»ΠΎΡΠ½ΠΎΡΡΡ ΠΏΠ΅Π½ ΡΠ°ΠΊΠΆΠ΅ Π²ΡΡΠ΅.ΠΠΎΡΡΡΠΈΠΉ / Π²Π»Π°ΠΆΠ½ΡΠΉ ΡΡΡΠΊΠ»ΡΠΉ. ΡΠ΄Π°Ρ. ΠΏΠ΅Π½Ρ, ΠΈΠ·ΠΌΠ΅ΡΠ΅Π½Π½ΠΎΠΉ ΠΏΡΡΠ΅ΠΌ ΡΡΠ°ΡΠ΅Π½ΠΈΡ ΠΏΠ΅Π½ΠΎΠΏΠ»Π°ΡΡΠ° 4 x 4 x 1 Π² ΡΠ΅ΡΠ΅Π½ΠΈΠ΅ ΠΎΠ΄Π½ΠΎΠΉ Π½Π΅Π΄Π΅Π»ΠΈ ΠΏΡΠΈ 168 o F / 97% ΠΎΡΠ½ΠΎΡΠΈΡΠ΅Π»ΡΠ½ΠΎΠΉ Π²Π»Π°ΠΆΠ½ΠΎΡΡΠΈ, ΠΏΠΎΠΊΠ°Π·Π°Π½ΠΎ Π½Π° ΡΠΈΡΡΠ½ΠΊΠ΅ 5. ΠΠ°Π½Π½ΡΠ΅ ΠΏΠΎΠΊΠ°Π·ΡΠ²Π°ΡΡ, ΡΡΠΎ Π³ΠΎΡΡΡΠ΅Π΅ ΡΡΡΠΊΠ»ΠΎΠ΅ ΠΏΠΎΠΊΡΡΡΠΈΠ΅. ΡΠ΄Π°Ρ. ΠΈΠ· Π²ΡΠ΅Ρ iso-p, 7: 3 ΠΈ 3: 7 iso / n-p Π»ΡΡΡΠ΅, ΡΠ΅ΠΌ Ρ ΡΡΠ°Π»ΠΎΠ½Π°, 8: 2 cyclo / iso-p ΠΈ Π²ΡΠ΅Ρ n-p. ΠΡΠ»ΠΈ ΠΏΡΠΈΠ½ΡΡΡ Π²ΠΎ Π²Π½ΠΈΠΌΠ°Π½ΠΈΠ΅ ΠΏΠ»ΠΎΡΠ½ΠΎΡΡΡ ΠΏΠ΅Π½Ρ, ΡΡΠ°Π½ΠΎΠ²ΠΈΡΡΡ ΡΡΠ½ΠΎ, ΡΡΠΎ ΡΠΌΠ΅ΡΡ, Π±ΠΎΠ³Π°ΡΠ°Ρ ΠΈΠ·ΠΎ-ΠΏ ΠΈ ΠΈΠ·ΠΎ-ΠΏ, Π΄Π°Π΅Ρ ΡΡΠ°Π±ΠΈΠ»ΡΠ½ΡΡ ΠΏΠΎ ΡΠ°Π·ΠΌΠ΅ΡΡ ΠΏΠ΅Π½Ρ ΠΏΡΠΈ Π±ΠΎΠ»Π΅Π΅ Π½ΠΈΠ·ΠΊΠΎΠΉ ΠΏΠ»ΠΎΡΠ½ΠΎΡΡΠΈ ΠΏΠΎ ΡΡΠ°Π²Π½Π΅Π½ΠΈΡ ΡΠΎ ΡΠΌΠ΅ΡΡΠΌΠΈ, Π±ΠΎΠ³Π°ΡΡΠΌΠΈ ΡΠΈΠΊΠ»ΠΎΠΏ-ΠΏ ΠΈΠ»ΠΈ Π½-ΠΏ. ΠΠ΅ ΡΠ΄ΠΈΠ²ΠΈΡΠ΅Π»ΡΠ½ΠΎ, ΡΡΠΎ Π΄ΠΎΠ±Π°Π²Π»Π΅Π½ΠΈΠ΅ ΠΈΠ·ΠΎΠ±ΡΡΠ°Π½Π° ΡΠΏΠΎΡΠΎΠ±ΡΡΠ²ΡΠ΅Ρ ΡΡΠ°Π±ΠΈΠ»ΡΠ½ΠΎΡΡΠΈ ΡΠ°Π·ΠΌΠ΅ΡΠΎΠ² Π² Ρ ΠΎΠ»ΠΎΠ΄Π½ΠΎΠΌ ΡΠΎΡΡΠΎΡΠ½ΠΈΠΈ, Π½ΠΎ Π½Π΅ΡΠΊΠΎΠ»ΡΠΊΠΎ ΡΡ ΡΠ΄ΡΠ°Π΅Ρ ΡΡΠ°Π±ΠΈΠ»ΡΠ½ΠΎΡΡΡ ΡΠ°Π·ΠΌΠ΅ΡΠΎΠ² Π² Π³ΠΎΡΡΡΠ΅ΠΉ Π²Π»Π°ΠΆΠ½ΠΎΠΉ ΡΡΠ΅Π΄Π΅ (ΡΠΌ. Π’Π°Π±Π»ΠΈΡΡ 2).Π’ΡΠΈ Π½Π°Π±ΠΎΡΠ° R-Π·Π½Π°ΡΠ΅Π½ΠΈΠΉ, Π½Π°ΡΠ°Π»ΡΠ½ΡΠ΅, 3 LTTR ΠΈ 2 LTTR ΠΏΠ΅ΡΠ΅ΡΠΈΡΠ»Π΅Π½Ρ Π² Π’Π°Π±Π»ΠΈΡΠ΅ 2 ΠΈ ΠΏΠΎΠΊΠ°Π·Π°Π½Ρ Π½Π° Π ΠΈΡΡΠ½ΠΊΠ΅ 3. ΠΠ»Ρ Π½Π°ΡΠ°Π»ΡΠ½ΠΎΠ³ΠΎ R-Π·Π½Π°ΡΠ΅Π½ΠΈΡ ΡΠΌΠ΅ΡΠΈ ΡΠΈΠΊΠ»ΠΎ-p / ΠΈΠ·ΠΎ-p Π΄Π°ΡΡ Π½Π°ΠΈΠ²ΡΡΡΠΈΠ΅ Π·Π½Π°ΡΠ΅Π½ΠΈΡ, Π° iso-p, np ΠΈ ΡΠΌΠ΅ΡΠΈ Π΄Π²ΡΡ Π΄Π°ΡΡ ΠΏΠ΅ΡΠ΅ΠΊΡΡΠ²Π°ΡΡΠΈΠ΅ΡΡ, Π½ΠΎ Π½Π΅ΠΌΠ½ΠΎΠ³ΠΎ Π±ΠΎΠ»Π΅Π΅ Π½ΠΈΠ·ΠΊΠΈΠ΅ Π·Π½Π°ΡΠ΅Π½ΠΈΡ. ΠΠ»ΡΠ΄Ρ Π½Π° Π·Π½Π°ΡΠ΅Π½ΠΈΡ LTTR 3 ΠΈ 2, ΠΌΡ Π²ΠΈΠ΄ΠΈΠΌ, ΡΡΠΎ, Ρ ΠΎΡΡ ΡΠΌΠ΅ΡΠΈ ΡΠΈΠΊΠ»ΠΎ-p / ΠΈΠ·ΠΎ-p Π΄Π°ΡΡ ΡΠ°ΠΌΡΠ΅ Π²ΡΡΠΎΠΊΠΈΠ΅ Π·Π½Π°ΡΠ΅Π½ΠΈΡ LTTR, Π²ΡΠ΅ iso-p Π΄Π°ΡΡ Ρ ΠΎΡΠΎΡΠΈΠ΅ ΡΠ΅Π·ΡΠ»ΡΡΠ°ΡΡ LTTR, Π° ΡΠ°Π·Π½ΠΈΡΠ° ΠΌΠ΅ΠΆΠ΄Ρ ΡΠΈΠΊΠ»ΠΎ-p / iso-p ΠΈ Π²ΡΠ΅ΠΌΠΈ iso-p -p ΡΡΠΆΠ°Π΅ΡΡΡ ΠΏΠΎ ΠΌΠ΅ΡΠ΅ ΡΡΠ°ΡΠ΅Π½ΠΈΡ. ΠΠΎΡΠΌΠ°Π»ΡΠ½ΡΠΉ ΠΏΠ΅Π½ΡΠ°Π½ ΠΈ ΡΠΌΠ΅ΡΠΈ, ΡΠΎΠ΄Π΅ΡΠΆΠ°ΡΠΈΠ΅ Π΅Π³ΠΎ Π±ΠΎΠ»Π΅Π΅ Π²ΡΡΠΎΠΊΠΈΠ΅ ΠΊΠΎΠ»ΠΈΡΠ΅ΡΡΠ²Π°, ΠΏΠΎ-Π²ΠΈΠ΄ΠΈΠΌΠΎΠΌΡ, Π΄Π°ΡΡ Ρ ΡΠ΄ΡΠΈΠ΅ Π·Π½Π°ΡΠ΅Π½ΠΈΡ LTTR ΠΏΠΎ ΡΡΠ°Π²Π½Π΅Π½ΠΈΡ ΡΠΎ Π²ΡΠ΅ΠΌΠΈ ΠΈΠ·ΠΎ-p.Π’Π°ΠΊΠΎΠ΅ ΠΏΠΎΠ²Π΅Π΄Π΅Π½ΠΈΠ΅ R-Π·Π½Π°ΡΠ΅Π½ΠΈΡ, Π²Π΅ΡΠΎΡΡΠ½ΠΎ, ΠΎΠ±ΡΡΡΠ½ΡΠ΅ΡΡΡ ΡΠ°Π·Π½ΠΈΡΠ΅ΠΉ Π² ΠΊΠΎΡΡΡΠΈΡΠΈΠ΅Π½ΡΠ΅ Π΄ΠΈΡΡΡΠ·ΠΈΠΈ ΡΠ΅ΡΠ΅Π· ΠΏΠ΅Π½Ρ ΠΈ ΡΠΎΠ³Π»Π°ΡΡΠ΅ΡΡΡ Ρ ΠΏΡΠ΅Π΄ΡΠ΄ΡΡΠΈΠΌΠΈ Π²ΡΠ²ΠΎΠ΄Π°ΠΌΠΈ [3, 7]. ΠΠ·ΠΌΠ΅Π½Π΅Π½ΠΈΠ΅ ΠΎΠ±ΡΠ΅ΠΌΠ°,%: 2 pcf pcf 7: 3 pcf 3: 7 pcf pcf ΠΠ°ΠΌΠΈΠ½Π°ΡΡ, ΡΠΎΠ΄Π΅ΡΠΆΠ°ΡΠΈΠ΅ ΠΈΠ·ΠΎΠ±ΡΡΠ°Π½, Π΄Π°Π»ΠΈ Ρ ΠΎΡΠΎΡΠ΅Π΅ Π½Π°ΡΠ°Π»ΡΠ½ΠΎΠ΅ Π·Π½Π°ΡΠ΅Π½ΠΈΠ΅ R, Π½Π΅ΡΠΌΠΎΡΡΡ Π½Π° ΡΡΠ΅Π·ΠΌΠ΅ΡΠ½ΠΎΠ΅ ΠΊΠΎΠ»ΠΈΡΠ΅ΡΡΠ²ΠΎ ΠΏΡΡΡΠΎΡ. ΠΠ΄Π½Π°ΠΊΠΎ Π·Π½Π°ΡΠ΅Π½ΠΈΡ LTTR Π΄Π»Ρ ΡΠΌΠ΅ΡΠ΅ΠΉ, ΡΠΎΠ΄Π΅ΡΠΆΠ°ΡΠΈΡ ΠΈΠ·ΠΎΠ±ΡΡΠ°Π½, Π½Π΅ ΡΠ°ΠΊ Ρ ΠΎΡΠΎΡΠΈ, ΠΎΡΠΎΠ±Π΅Π½Π½ΠΎ Ρ ΡΡΠ΅ΡΠΎΠΌ Π±ΠΎΠ»Π΅Π΅ Π²ΡΡΠΎΠΊΠΎΠΉ ΠΏΠ»ΠΎΡΠ½ΠΎΡΡΠΈ Π»Π°ΠΌΠΈΠ½Π°ΡΠ°. Π§ΡΠ΅Π·ΠΌΠ΅ΡΠ½ΡΠ΅ ΠΏΡΡΡΠΎΡΡ ΠΌΠΎΠ³ΡΡ ΡΠΏΠΎΡΠΎΠ±ΡΡΠ²ΠΎΠ²Π°ΡΡ ΡΡΠ°ΡΠ΅Π½ΠΈΡ Π»Π°ΠΌΠΈΠ½Π°ΡΠ° ΠΈ, ΡΠ°ΠΊΠΈΠΌ ΠΎΠ±ΡΠ°Π·ΠΎΠΌ, ΡΡ ΡΠ΄ΡΠ°ΡΡ Π·Π½Π°ΡΠ΅Π½ΠΈΡ LTTR.Π ΠΈΡ. 4. Π‘ΡΠ°Π±ΠΈΠ»ΡΠ½ΠΎΡΡΡ ΡΠ°Π·ΠΌΠ΅ΡΠΎΠ² ΠΏΠ΅Π½ΠΎΠΏΠ»Π°ΡΡΠ° Π² Ρ ΠΎΠ»ΠΎΠ΄Π½ΠΎΠΌ ΡΠΎΡΡΠΎΡΠ½ΠΈΠΈ. ΠΠΎΠΊΠ°Π·Π°ΡΠ΅Π»Ρ R: 2 ΡΠΈΠΊΠ»ΠΎ-Π: ΠΈΠ·ΠΎ-Π ΠΈΠ·ΠΎ-p 7: 3 ΠΈΠ·ΠΎ: Π½ΠΏ 3: 7 ΠΈΠ·ΠΎ: Π½ΠΏ ΠΡΡ ΠΎΠ΄Π½ΡΠΉ 3 «LTTR 2» LTTR np ΠΠ·ΠΌΠ΅Π½Π΅Π½ΠΈΠ΅ ΠΎΠ±ΡΠ΅ΠΌΠ°,%: 2 pcf pcf 7: 3 pcf 3: 7 pcf pcf Π ΠΈΡ. 3. R-Π·Π½Π°ΡΠ΅Π½ΠΈΡ Π ΠΈΡ. 5. Π‘ΡΠ°Π±ΠΈΠ»ΡΠ½ΠΎΡΡΡ ΡΠ°Π·ΠΌΠ΅ΡΠΎΠ² ΡΠ΅ΡΠ΄Π΅ΡΠ½ΠΈΠΊΠ° Π² Π³ΠΎΡΡΡΠ΅ΠΌ / Π²Π»Π°ΠΆΠ½ΠΎΠΌ ΡΠΎΡΡΠΎΡΠ½ΠΈΠΈ 46
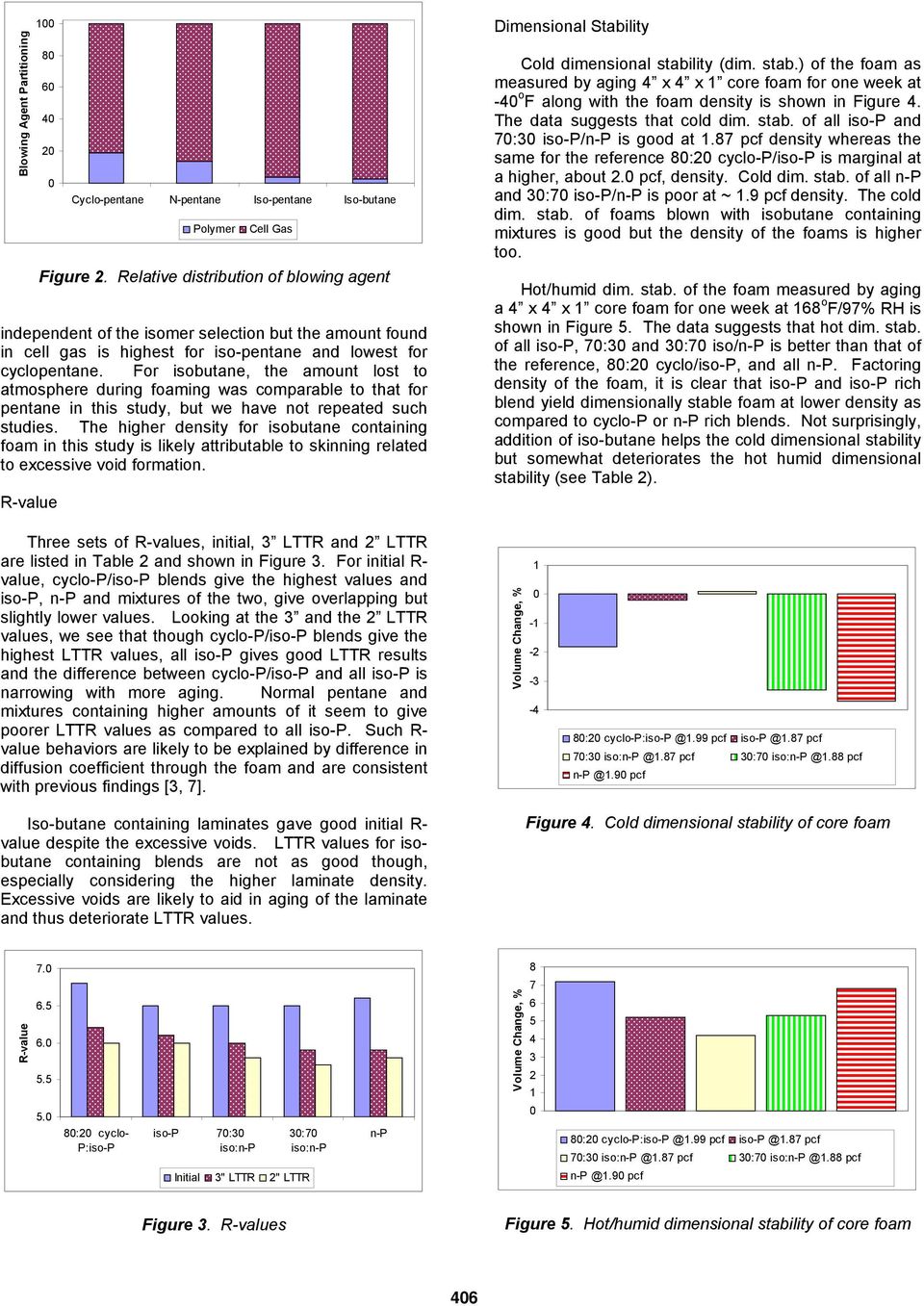
6 ΠΠΎΡΠΌΠ°Π»ΠΈΠ·ΠΎΠ²Π°Π½Π½ΠΎΠ΅ ΡΡΠ΅Π΄Π½Π΅Π΅ ΡΠΆΠ°ΡΠΈΠ΅ 1,9 ΡΡΠ½Ρ / ΠΊΠ². ΠΡΠΉΠΌ, ΡΡΠ½Ρ / ΠΊΠ². ΠΡΠΉΠΌ: 2 cyclo-p: iso-p iso-p 7: 3 iso: n-p 3: 7 iso: n-p n-p Π ΠΈΡ.ΠΠΎΡΠΌΠ°Π»ΠΈΠ·ΠΎΠ²Π°Π½Π½Π°Ρ ΡΡΠ΅Π΄Π½ΡΡ ΠΏΡΠΎΡΠ½ΠΎΡΡΡ Π½Π° ΡΠΆΠ°ΡΠΈΠ΅ ΠΏΠ΅Π½ΠΎΠΏΠ»Π°ΡΡΠ° ΠΏΡΠΈ ΠΏΠ»ΠΎΡΠ½ΠΎΡΡΠΈ 1,9 ΡΡΠ½Ρ / ΡΡΡ ΠΡΠΎΡΠ½ΠΎΡΡΡ Π½Π° ΡΠΆΠ°ΡΠΈΠ΅ ΠΡΠΎΡΠ½ΠΎΡΡΡ Π½Π° ΡΠΆΠ°ΡΠΈΠ΅ (CS) Π² Π²Π΅ΡΡΠΈΠΊΠ°Π»ΡΠ½ΠΎΠΌ, ΠΌΠ°ΡΠΈΠ½Π½ΠΎΠΌ ΠΈ ΠΏΠΎΠΏΠ΅ΡΠ΅ΡΠ½ΠΎΠΌ Π½Π°ΠΏΡΠ°Π²Π»Π΅Π½ΠΈΡΡ , Π° ΡΠ°ΠΊΠΆΠ΅ ΡΠ°ΡΡΠ΅ΡΠ½Π°Ρ Π½ΠΎΡΠΌΠ°Π»ΠΈΠ·ΠΎΠ²Π°Π½Π½Π°Ρ ΡΡΠ΅Π΄Π½ΡΡ ΠΏΡΠΎΡΠ½ΠΎΡΡΡ Π½Π° ΡΠΆΠ°ΡΠΈΠ΅ (NMCS) ΠΏΡΠΈ ΠΏΠ»ΠΎΡΠ½ΠΎΡΡΠΈ ΠΏΠ΅Π½ΠΎΠΏΠ»Π°ΡΡΠ° 1,9 ΡΡΠ½Ρ / ΡΡΡ (ΡΠ°ΡΡΡΠΈΡΡΠ²Π°Π΅ΡΡΡ ΠΏΠΎ ΡΠΎΡΠΌΡΠ»Π΅ ΠΏΡΠΈΠ²Π΅Π΄Π΅Π½Π½ΡΠΉ Π² ΡΡΡΠ»ΠΊΠ΅ 5) ΠΏΡΠΈΠ²Π΅Π΄Π΅Π½ Π² ΡΠ°Π±Π»ΠΈΡΠ΅ 2. NMCS ΠΏΠΎΠ·Π²ΠΎΠ»ΡΠ΅Ρ Π½Π°ΠΌ ΡΡΠ°Π²Π½ΠΈΠ²Π°ΡΡ ΡΡΡΠ΅ΠΊΡΡ BA Π½Π° ΠΈΡΡΠΈΠ½Π½ΡΡ ΠΏΡΠΎΡΠ½ΠΎΡΡΡ ΠΏΠ΅Π½Ρ, ΠΏΠΎΡΠΊΠΎΠ»ΡΠΊΡ ΠΎΠ½ ΡΡΡΡΠ°Π½ΡΠ΅Ρ ΠΎΡΠΊΠ»ΠΎΠ½Π΅Π½ΠΈΡ ΠΈΠ·-Π·Π° ΠΎΡΠΈΠ΅Π½ΡΠ°ΡΠΈΠΈ ΡΡΠ΅Π΅ΠΊ ΠΈ ΠΏΠ»ΠΎΡΠ½ΠΎΡΡΠΈ, ΠΈ ΡΠΎ ΠΈ Π΄ΡΡΠ³ΠΎΠ΅ ΠΌΠΎΠΆΠ½ΠΎ Π½Π΅Π·Π°Π²ΠΈΡΠΈΠΌΠΎ ΠΊΠΎΠ½ΡΡΠΎΠ»ΠΈΡΠΎΠ²Π°ΡΡ Π½Π° Π»Π°ΠΌΠΈΠ½Π°ΡΠΎΡΠ΅.ΠΠ°ΠΊ Π²ΠΈΠ΄Π½ΠΎ Π½Π° Π ΠΈΡΡΠ½ΠΊΠ΅ 6, ΡΠΌΠ΅ΡΠΈ ΠΈΠ·ΠΎ-ΠΏ / Π½-ΠΏ Π΄Π°ΡΡ Π±ΠΎΠ»Π΅Π΅ Π²ΡΡΠΎΠΊΡΡ ΠΏΡΠΎΡΠ½ΠΎΡΡΡ Π½Π° ΡΠΆΠ°ΡΠΈΠ΅ ΠΏΠΎ ΡΡΠ°Π²Π½Π΅Π½ΠΈΡ ΡΠΎ ΡΠΌΠ΅ΡΡΡ ΡΠΈΠΊΠ»ΠΎ-ΠΏ / ΠΈΠ·ΠΎ-Π. ΠΡΠΎΠΌΠ΅ ΡΠΎΠ³ΠΎ, ΡΠ΅ΠΌ Π²ΡΡΠ΅ ΠΊΠΎΠ»ΠΈΡΠ΅ΡΡΠ²ΠΎ ΠΈΠ·ΠΎ-ΠΏ Π² ΡΠΌΠ΅ΡΠΈ ΠΈΠ·ΠΎ-ΠΏ / Π½-ΠΏ, ΡΠ΅ΠΌ Π²ΡΡΠ΅ NMCS. Π Π΅Π·ΡΠ»ΡΡΠ°ΡΡ ΠΏΠΎ ΠΏΡΠΎΡΠ½ΠΎΡΡΠΈ Π½Π° ΡΠΆΠ°ΡΠΈΠ΅ Π²ΠΌΠ΅ΡΡΠ΅ Ρ ΡΠ΅Π·ΡΠ»ΡΡΠ°ΡΠ°ΠΌΠΈ ΠΏΠΎ ΡΡΠ°Π±ΠΈΠ»ΡΠ½ΠΎΡΡΠΈ ΡΠ°Π·ΠΌΠ΅ΡΠΎΠ² ΠΏΡΠ΅Π΄ΠΏΠΎΠ»Π°Π³Π°ΡΡ, ΡΡΠΎ ΠΎΠ΄ΠΈΠ½ ΠΈΠ·ΠΎΠΏΠ΅Π½ΡΠ°Π½ ΠΈΠ»ΠΈ ΡΠΌΠ΅ΡΡ, Π±ΠΎΠ³Π°ΡΠ°Ρ ΠΈΠ·ΠΎΠΏΠ΅Π½ΡΠ°Π½ΠΎΠΌ ΠΈ Π½-ΠΏΠ΅Π½ΡΠ°Π½ΠΎΠΌ, Π΄Π΅ΠΌΠΎΠ½ΡΡΡΠΈΡΡΡΡ ΠΏΠΎΡΠ΅Π½ΡΠΈΠ°Π» ΡΠ½ΠΈΠΆΠ΅Π½ΠΈΡ ΠΏΠ»ΠΎΡΠ½ΠΎΡΡΠΈ ΠΏΠΎ ΡΡΠ°Π²Π½Π΅Π½ΠΈΡ Ρ ΠΊΠ°ΡΡΠΎΠ½ΠΎΠΌ ΠΈΠ· Π²ΡΠΏΠ΅Π½Π΅Π½Π½ΠΎΠ³ΠΎ Π²ΡΠΏΠ΅Π½Π΅Π½Π½ΠΎΠ³ΠΎ ΠΌΠ°ΡΠ΅ΡΠΈΠ°Π»Π° ΡΠΈΠΊΠ»ΠΎΠΏΠ΅Π½ΡΠ°Π½ / ΠΈΠ·ΠΎΠΏΠ΅Π½ΡΠ°Π½ 8: 2. ΠΠ³Π½Π΅ΡΡΠΎΠΉΠΊΠΎΡΡΡ ΠΠ³Π½Π΅ΡΡΠΎΠΉΠΊΠΈΠ΅ ΡΠ²ΠΎΠΉΡΡΠ²Π° Π»Π°ΠΌΠΈΠ½Π°ΡΠ° Π±ΡΠ»ΠΈ ΠΎΡ Π°ΡΠ°ΠΊΡΠ΅ΡΠΈΠ·ΠΎΠ²Π°Π½Ρ ΡΠΎΠ»ΡΠΊΠΎ Ρ ΠΏΠΎΠΌΠΎΡΡΡ Π»Π°Π±ΠΎΡΠ°ΡΠΎΡΠ½ΡΡ ΠΈΡΠΏΡΡΠ°Π½ΠΈΠΉ.Π£Π΄Π΅ΡΠΆΠ°Π½ΠΈΠ΅ Π²Π΅ΡΠ° ΠΏΠ΅Π½Ρ ΠΈ Π²ΡΠ΅ΠΌΡ Π΄ΠΎ ΡΡΡΠ΅Π½ΠΈΡ Π±ΡΠ»ΠΈ ΠΈΠ·ΠΌΠ΅ΡΠ΅Π½Ρ Π² ΠΈΡΠΏΡΡΠ°Π½ΠΈΠΈ Ρ Π΄ΡΠΌΠΎΡ ΠΎΠ΄ΠΎΠΌ ΠΠ°ΡΠ»Π΅ΡΠ°. ΠΠ°ΠΊΡΠΈΠΌΠ°Π»ΡΠ½Π°Ρ ΠΏΠ»ΠΎΡΠ½ΠΎΡΡΡ Π΄ΡΠΌΠ° Π±ΡΠ»Π° ΠΈΠ·ΠΌΠ΅ΡΠ΅Π½Π° Π² ΡΠ΅ΡΡΠ΅ NBS, Π° ΡΠΎΠΎΡΠ½ΠΎΡΠ΅Π½ΠΈΠ΅ PIR / PUR Π±ΡΠ»ΠΎ ΠΈΠ·ΠΌΠ΅ΡΠ΅Π½ΠΎ Ρ ΠΏΠΎΠΌΠΎΡΡΡ FTIR [5]. ΠΡΠΈ ΡΠ΅Π·ΡΠ»ΡΡΠ°ΡΡ ΠΏΠΎΠΊΠ°Π·Π°Π½Ρ Π² ΡΠ°Π±Π»ΠΈΡΠ΅ 2. ΠΠ΅ΡΠ΄ΠΈΠ²ΠΈΡΠ΅Π»ΡΠ½ΠΎ, ΡΡΠΎ Π²ΡΠ±ΠΎΡ Π²ΡΠΏΠ΅Π½ΠΈΠ²Π°ΡΡΠ΅Π³ΠΎ Π°Π³Π΅Π½ΡΠ° Π½Π΅ ΠΎΠΊΠ°Π·ΡΠ²Π°Π΅Ρ ΠΊΠ°ΠΊΠΎΠ³ΠΎ-Π»ΠΈΠ±ΠΎ Π·Π½Π°ΡΠΈΠΌΠΎΠ³ΠΎ Π² ΠΏΡΠΎΠΌΡΡΠ»Π΅Π½Π½ΠΎΠΌ ΠΎΡΠ½ΠΎΡΠ΅Π½ΠΈΠΈ Π²Π»ΠΈΡΠ½ΠΈΡ Π½Π° ΠΈΠ·ΠΌΠ΅ΡΠ΅Π½Π½ΡΠ΅ Π² Π»Π°Π±ΠΎΡΠ°ΡΠΎΡΠ½ΠΎΠΌ ΠΌΠ°ΡΡΡΠ°Π±Π΅ ΠΎΠ³Π½Π΅ΡΡΠΎΠΉΠΊΠΈΠ΅ ΡΠ²ΠΎΠΉΡΡΠ²Π°. Π₯ΡΡΠΏΠΊΠΎΡΡΡ ΠΈ Π°Π΄Π³Π΅Π·ΠΈΡ ΠΊ ΠΎΡΡΠ»Π°ΠΈΠ²Π°Π½ΠΈΡ Π’Π°ΠΊΠΆΠ΅ Π² ΡΡΠΎΠΌ ΠΈΡΡΠ»Π΅Π΄ΠΎΠ²Π°Π½ΠΈΠΈ Π±ΡΠ»ΠΈ ΠΈΠ·ΠΌΠ΅ΡΠ΅Π½Ρ ΡΡΡ Π»ΠΎΡΡΡ ΠΈ Π°Π΄Π³Π΅Π·ΠΈΡ ΠΎΠ±Π»ΠΈΡΠΎΠ²ΠΎΡΠ½ΠΎΠ³ΠΎ ΡΡΠ΅Π΄ΡΡΠ²Π° ΠΊ ΠΎΡΡΠ»Π°ΠΈΠ²Π°Π½ΠΈΡ ΠΏΠΎΡΠ»Π΅ 24 ΡΠ°ΡΠΎΠ² ΠΎΡΠ²Π΅ΡΠΆΠ΄Π΅Π½ΠΈΡ.ΠΠ΅Π»ΠΈΡΠΈΠ½Ρ Π°Π΄Π³Π΅Π·ΠΈΠΈ ΠΊ ΠΎΡΡΠ»Π°ΠΈΠ²Π°Π½ΠΈΡ Π΄Π»Ρ Π²ΡΠΏΠ΅Π½Π΅Π½Π½ΡΡ ΠΈΠ·ΠΎ / Π½-ΠΏΠ΅Π½ΡΠ°Π½ΠΎΠΌ ΠΏΠ΅Π½ Π±ΡΠ»ΠΈ Π½ΠΈΠΆΠ΅, ΡΠ΅ΠΌ Ρ ΠΏΠ΅Π½, ΡΠΎΠ΄Π΅ΡΠΆΠ°ΡΠΈΡ ΡΠΈΠΊΠ»ΠΎΠΏΠ΅Π½ΡΠ°Π½, ΠΊΠ°ΠΊ ΠΈ Π·Π½Π°ΡΠ΅Π½ΠΈΡ Ρ ΡΡΠΏΠΊΠΎΡΡΠΈ. ΠΠ°Π½Π½ΡΠ΅ ΡΡΠΎΠ³ΠΎ ΠΈΡΡΠ»Π΅Π΄ΠΎΠ²Π°Π½ΠΈΡ ΡΠ²ΠΈΠ΄Π΅ΡΠ΅Π»ΡΡΡΠ²ΡΡΡ ΠΎ ΠΏΠΎΡΡΠΈ Π»ΠΈΠ½Π΅ΠΉΠ½ΠΎΠΉ Π·Π°Π²ΠΈΡΠΈΠΌΠΎΡΡΠΈ ΠΌΠ΅ΠΆΠ΄Ρ Π°Π΄Π³Π΅Π·ΠΈΠ΅ΠΉ ΠΎΡ ΠΎΡΡΠ»Π°ΠΈΠ²Π°Π½ΠΈΡ ΠΈ ΡΡΡ Π»ΠΎΡΡΡΡ ΠΏΡΠΈ ΠΏΠ΅ΡΠ΅ΠΌΠ΅ΡΠΈΠ²Π°Π½ΠΈΠΈ. ΠΠ°ΠΆΠ΅ Π½Π΅ΡΠΌΠΎΡΡΡ Π½Π° ΡΠΎ, ΡΡΠΎ ΠΈΠ·ΠΌΠ΅ΡΠ΅Π½Π½Π°Ρ Ρ ΡΡΠΏΠΊΠΎΡΡΡ ΠΎΡΠ½ΠΎΡΠΈΡΡΡ ΠΊ ΠΎΠ±ΡΠ΅ΠΌΠ½ΠΎΠΉ ΠΏΠ΅Π½Π΅, Π° Π½Π΅ ΠΊ ΠΏΠΎΠ²Π΅ΡΡ Π½ΠΎΡΡΠΈ ΠΈΠ»ΠΈ ΠΊΠΎΠΆΠ΅, ΡΡΠ° ΡΠ΅Π½Π΄Π΅Π½ΡΠΈΡ ΠΏΡΠΎΡΠΈΠ²ΠΎΡΠ΅ΡΠΈΡ ΠΎΠ±ΡΠ΅ΠΏΡΠΈΠ½ΡΡΠΎΠΌΡ ΠΌΠ½Π΅Π½ΠΈΡ, ΡΠΎΠ³Π»Π°ΡΠ½ΠΎ ΠΊΠΎΡΠΎΡΠΎΠΌΡ ΠΏΠ»ΠΎΡ Π°Ρ Π°Π΄Π³Π΅Π·ΠΈΡ Π² ΠΏΠ΅Π½ΠΎΠΏΠΎΠ»ΠΈΠΈΠ·ΠΎ ΠΎΠ±ΡΡΠ»ΠΎΠ²Π»Π΅Π½Π° ββΠ²ΡΡΠΎΠΊΠΎΠΉ Ρ ΡΡΠΏΠΊΠΎΡΡΡΡ. ΠΡ Π½Π΅ ΠΈΡΡΠ»Π΅Π΄ΠΎΠ²Π°Π»ΠΈ ΡΡΠΎΡ Π²ΠΎΠΏΡΠΎΡ Π΄ΠΎΠΏΠΎΠ»Π½ΠΈΡΠ΅Π»ΡΠ½ΠΎ, Π½ΠΎ Π±ΡΠ»ΠΎ ΡΡΡΠ°Π½ΠΎΠ²Π»Π΅Π½ΠΎ, ΡΡΠΎ Π²ΡΠ±ΠΎΡ ΡΠΈΠ»ΠΈΠΊΠΎΠ½ΠΎΠ²ΠΎΠ³ΠΎ ΠΏΠΎΠ²Π΅ΡΡ Π½ΠΎΡΡΠ½ΠΎ-Π°ΠΊΡΠΈΠ²Π½ΠΎΠ³ΠΎ Π²Π΅ΡΠ΅ΡΡΠ²Π° ΠΈ ΡΠΎΠ²ΠΌΠ΅ΡΡΠΈΠΌΠΎΡΡΡ ΠΌΠ΅ΠΆΠ΄Ρ ΠΏΠΎΠ»ΠΈΠΎΠ»ΠΎΠΌ ΠΈ Π²ΡΠΏΠ΅Π½ΠΈΠ²Π°ΡΡΠΈΠΌ Π°Π³Π΅Π½ΡΠΎΠΌ ΠΈΠ³ΡΠ°ΡΡ Π²Π°ΠΆΠ½ΡΡ ΡΠΎΠ»Ρ Π² Π°Π΄Π³Π΅Π·ΠΈΠΈ ΠΊ ΠΎΡΡΠ»Π°ΠΈΠ²Π°Π½ΠΈΡ.ΠΠ±ΡΠΈΠ΅ ΡΠ΅Π·ΡΠ»ΡΡΠ°ΡΡ Π Π΅Π·ΡΠ»ΡΡΠ°ΡΡ ΡΡΠΎΠ³ΠΎ ΠΈΡΡΠ»Π΅Π΄ΠΎΠ²Π°Π½ΠΈΡ Π² ΡΠΎΡΠ΅ΡΠ°Π½ΠΈΠΈ Ρ ΡΠ΅Π·ΡΠ»ΡΡΠ°ΡΠ°ΠΌΠΈ Π½Π°ΡΠΈΡ ΠΏΡΠ΅Π΄ΡΠ΄ΡΡΠΈΡ ΠΈΡΡΠ»Π΅Π΄ΠΎΠ²Π°Π½ΠΈΠΉ [3, 8] ΠΏΠΎΠΊΠ°Π·ΡΠ²Π°ΡΡ, ΡΡΠΎ ΠΊΠ°ΠΆΠ΄ΡΠΉ ΠΈΠ· ΠΈΠ·ΠΎΠΌΠ΅ΡΠΎΠ² ΠΏΠ΅Π½ΡΠ°Π½Π° ΠΏΡΠΈΠ²Π½ΠΎΡΠΈΡ ΡΠ°Π·Π½ΡΠ΅ ΡΠ²ΠΎΠΉΡΡΠ²Π° Π² ΠΏΡΠΎΠΈΠ·Π²ΠΎΠ΄ΡΡΠ²ΠΎ ΠΏΠΎΠ»ΠΈΠΈΠ·ΠΎ ΠΈ Π΅Π³ΠΎ ΡΠ°Π±ΠΎΡΠΈΠ΅ Ρ Π°ΡΠ°ΠΊΡΠ΅ΡΠΈΡΡΠΈΠΊΠΈ. Π¦ΠΈΠΊΠ»ΠΎΠΏΠ΅Π½ΡΠ°Π½ ΠΎΠ±Π΅ΡΠΏΠ΅ΡΠΈΠ²Π°Π΅Ρ Π½Π°ΠΈΠ²ΡΡΡΠ΅Π΅ Π½Π°ΡΠ°Π»ΡΠ½ΠΎΠ΅ Π·Π½Π°ΡΠ΅Π½ΠΈΠ΅ R, Ρ ΠΎΡΠΎΡΡΡ Π°Π΄Π³Π΅Π·ΠΈΡ ΠΊ ΠΎΡΡΠ»Π°ΠΈΠ²Π°Π½ΠΈΡ ΠΈ Ρ ΠΎΡΠΎΡΡΡ ΡΠ°ΡΡΠ²ΠΎΡΠΈΠΌΠΎΡΡΡ / ΡΠΎΠ²ΠΌΠ΅ΡΡΠΈΠΌΠΎΡΡΡ Ρ ΡΡΡΠ΅ΡΡΠ²ΡΡΡΠΈΠΌ ΡΡΡΡΠ΅ΠΌ. ΠΠ·ΠΎΠΏΠ΅Π½ΡΠ°Π½ ΠΎΠ±Π΅ΡΠΏΠ΅ΡΠΈΠ²Π°Π΅Ρ Ρ ΠΎΡΠΎΡΠ΅Π΅ LTTR, ΠΏΡΠΎΡΠ½ΠΎΡΡΡ Π½Π° ΡΠΆΠ°ΡΠΈΠ΅ ΠΈ ΡΡΠ°Π±ΠΈΠ»ΡΠ½ΠΎΡΡΡ ΡΠ°Π·ΠΌΠ΅ΡΠΎΠ². ΠΠΎΡΠΌΠ°Π»ΡΠ½ΡΠΉ ΠΏΠ΅Π½ΡΠ°Π½ ΠΎΠ±Π»Π°Π΄Π°Π΅Ρ ΡΡΠ΅Π΄Π½ΠΈΠΌΠΈ Ρ Π°ΡΠ°ΠΊΡΠ΅ΡΠΈΡΡΠΈΠΊΠ°ΠΌΠΈ, Π° Π΅Π³ΠΎ ΡΠ΅ΠΌΠΏΠ΅ΡΠ°ΡΡΡΠ° ΠΊΠΈΠΏΠ΅Π½ΠΈΡ Π½Π°ΠΈΠ±ΠΎΠ»Π΅Π΅ Π±Π»ΠΈΠ·ΠΊΠ° ΠΊ HCFC-141b, ΡΡΠΎ ΠΎΠ±Π΅ΡΠΏΠ΅ΡΠΈΠ²Π°Π΅Ρ ΡΠ΄ΠΎΠ±ΡΡΠ²ΠΎ ΠΎΠ±ΡΠ°Π±ΠΎΡΠΊΠΈ.ΠΡΠ΅Π²ΠΈΠ΄Π½ΠΎ, ΡΡΠΎ ΠΎΠΏΡΠΈΠΌΠ°Π»ΡΠ½ΡΠΉ ΡΠΎΡΡΠ°Π² Π±ΡΠ΄Π΅Ρ Π·Π°Π²ΠΈΡΠ΅ΡΡ ΠΎΡ Π²ΡΠ±ΡΠ°Π½Π½ΡΡ ΠΊΡΠΈΡΠ΅ΡΠΈΠ΅Π² ΠΏΡΠΎΠΈΠ·Π²ΠΎΠ΄ΡΡΠ²Π° ΠΈ ΠΏΠ΅ΡΠ΅ΡΠ°Π±ΠΎΡΠΊΠΈ ΠΏΠΎΠ»ΠΈΠΈΠ·ΠΎ-ΠΊΠ°ΡΡΠΎΠ½Π°. Π‘ ΡΡΠ΅ΡΠΎΠΌ ΡΠ΅Π»ΠΈ ΡΠ½ΠΈΠΆΠ΅Π½ΠΈΡ Π·Π°ΡΡΠ°Ρ ΠΏΡΠΈ ΡΠΎΡ ΡΠ°Π½Π΅Π½ΠΈΠΈ ΡΠ°Π±ΠΎΡΠΈΡ Ρ Π°ΡΠ°ΠΊΡΠ΅ΡΠΈΡΡΠΈΠΊ Π²Π΅ΡΡ ΠΈΠ·ΠΎΠΏΠ΅Π½ΡΠ°Π½, ΠΏΠΎ-Π²ΠΈΠ΄ΠΈΠΌΠΎΠΌΡ, ΡΠ²Π»ΡΠ΅ΡΡΡ ΠΏΡΠ΅Π΄ΠΏΠΎΡΡΠΈΡΠ΅Π»ΡΠ½ΡΠΌ ΠΆΠΈΠ΄ΠΊΠΈΠΌ Π²ΡΠΏΠ΅Π½ΠΈΠ²Π°ΡΡΠΈΠΌ Π°Π³Π΅Π½ΡΠΎΠΌ. ΠΠ½ ΠΏΡΠ΅Π΄Π»Π°Π³Π°Π΅Ρ ΡΠ°ΠΌΡΠΉ Π²ΡΡΠΎΠΊΠΈΠΉ ΠΏΠΎΡΠ΅Π½ΡΠΈΠ°Π» Π΄Π»Ρ ΡΠ½ΠΈΠΆΠ΅Π½ΠΈΡ ΠΏΠ»ΠΎΡΠ½ΠΎΡΡΠΈ Π΄ΠΎΡΠΊΠΈ. ΠΠΎ ΠΈΠ·-Π·Π° Π±ΠΎΠ»Π΅Π΅ Π½ΠΈΠ·ΠΊΠΎΠΉ ΡΠΎΡΠΊΠΈ ΠΊΠΈΠΏΠ΅Π½ΠΈΡ ΠΈ ΠΎΠ³ΡΠ°Π½ΠΈΡΠ΅Π½Π½ΠΎΠΉ ΡΠ°ΡΡΠ²ΠΎΡΠΈΠΌΠΎΡΡΠΈ Π² ΡΡΡΠ΅ΡΡΠ²ΡΡΡΠ΅ΠΌ ΡΡΡΡΠ΅ ΠΎΠ½ ΡΠΎΠ·Π΄Π°Π΅Ρ Π½Π΅ΡΠΊΠΎΠ»ΡΠΊΠΎ ΠΏΡΠΎΠ±Π»Π΅ΠΌ ΠΏΡΠΈ ΠΏΡΠΎΠΈΠ·Π²ΠΎΠ΄ΡΡΠ²Π΅. ΠΠ°ΠΊ ΠΈ CFC-, ΠΈΠ·ΠΎΠΏΠ΅Π½ΡΠ°Π½, ΠΏΠΎ ΡΡΡΠ΅ΡΡΠ²Ρ, ΡΠ²Π»ΡΠ΅ΡΡΡ Π²ΡΠΏΠ΅Π½ΠΈΠ²Π°ΡΡΠΈΠΌ Π°Π³Π΅Π½ΡΠΎΠΌ, ΠΊΠΈΠΏΡΡΠΈΠΌ ΠΏΡΠΈ ΠΊΠΎΠΌΠ½Π°ΡΠ½ΠΎΠΉ ΡΠ΅ΠΌΠΏΠ΅ΡΠ°ΡΡΡΠ΅, ΠΈ ΠΏΠΎΡΡΠΎΠΌΡ ΡΡΠ΅Π±ΡΠ΅Ρ Π±ΠΎΠ»Π΅Π΅ Ρ ΠΎΠ»ΠΎΠ΄Π½ΠΎΠ³ΠΎ ΠΊΠΎΠΌΠΏΠΎΠ½Π΅Π½ΡΠ° ΠΈ ΡΠ΅ΠΌΠΏΠ΅ΡΠ°ΡΡΡΡ ΡΠΌΠ΅ΡΠΈΡΠ΅Π»ΡΠ½ΠΎΠΉ Π³ΠΎΠ»ΠΎΠ²ΠΊΠΈ.Π§ΡΠΎΠ±Ρ ΡΠ»ΡΡΡΠΈΡΡ Π°Π΄Π³Π΅Π·ΠΈΡ ΠΊ ΠΎΡΡΠ»Π°ΠΈΠ²Π°Π½ΠΈΡ ΠΈ ΠΏΡΠ΅Π΄ΠΎΡΠ²ΡΠ°ΡΠΈΡΡ Π½Π΅Π·Π°ΠΏΠ»Π°Π½ΠΈΡΠΎΠ²Π°Π½Π½ΠΎΠ΅ ΠΏΠΎΠ²ΡΡΠ΅Π½ΠΈΠ΅ ΡΠ΅ΠΌΠΏΠ΅ΡΠ°ΡΡΡΡ ΠΊΠΎΠΌΠΏΠΎΠ½Π΅Π½ΡΠ° / ΡΠΌΠ΅ΡΠΈΡΠ΅Π»ΡΠ½ΠΎΠΉ Π³ΠΎΠ»ΠΎΠ²ΠΊΠΈ, Π½Π΅ΠΎΠ±Ρ ΠΎΠ΄ΠΈΠΌΠΎ Π΄ΠΎΠΏΠΎΠ»Π½ΠΈΡΠ΅Π»ΡΠ½ΠΎ ΡΠ»ΡΡΡΠΈΡΡ ΡΠΎΠ²ΠΌΠ΅ΡΡΠΈΠΌΠΎΡΡΡ ΠΈΠ·ΠΎΠΏΠ΅Π½ΡΠ°Π½Π° ΡΠΎ ΡΠΌΠ΅ΡΡΠΌΠΈ ΠΏΠΎΠ»ΠΈΠΎΠ»ΠΎΠ². ΠΡΠ»ΠΈ ΠΏΡΠΎΠΈΠ·Π²ΠΎΠ΄ΡΡΠ²ΠΎ Ρ ΠΈΡΠΏΠΎΠ»ΡΠ·ΠΎΠ²Π°Π½ΠΈΠ΅ΠΌ ΠΈΠ·ΠΎΠΏΠ΅Π½ΡΠ°Π½Π° Π² ΠΊΠ°ΡΠ΅ΡΡΠ²Π΅ Π΅Π΄ΠΈΠ½ΡΡΠ²Π΅Π½Π½ΠΎΠ³ΠΎ ΠΆΠΈΠ΄ΠΊΠΎΠ³ΠΎ Π²ΡΠΏΠ΅Π½ΠΈΠ²Π°ΡΡΠ΅Π³ΠΎ Π°Π³Π΅Π½ΡΠ° ΠΌΠ°Π»ΠΎΠ²Π΅ΡΠΎΡΡΠ½ΠΎ, ΠΈΡΠΏΠΎΠ»ΡΠ·ΠΎΠ²Π°Π½ΠΈΠ΅ Π½-ΠΏΠ΅Π½ΡΠ°Π½Π° Π² ΠΊΠ°ΡΠ΅ΡΡΠ²Π΅ Π²ΡΠΎΡΠΎΡΡΠ΅ΠΏΠ΅Π½Π½ΠΎΠ³ΠΎ Π²ΡΠΏΠ΅Π½ΠΈΠ²Π°ΡΡΠ΅Π³ΠΎ Π°Π³Π΅Π½ΡΠ° ΡΠΎΠ»ΡΠΊΠΎ Π² ΡΠΎΠΉ ΡΡΠ΅ΠΏΠ΅Π½ΠΈ, ΠΊΠΎΡΠΎΡΠ°Ρ Π½Π΅ΠΎΠ±Ρ ΠΎΠ΄ΠΈΠΌΠ° Π΄Π»Ρ ΠΎΠ±Π΅ΡΠΏΠ΅ΡΠ΅Π½ΠΈΡ Ρ ΠΎΡΠΎΡΠ΅ΠΉ ΠΎΠ±ΡΠ°Π±ΠΎΡΠΊΠΈ, Π±ΡΠ΄Π΅Ρ ΠΎΡΠ»ΠΈΡΠ½ΡΠΌ Π²Π°ΡΠΈΠ°Π½ΡΠΎΠΌ. Π¦ΠΈΠΊΠ»ΠΎΠΏΠ΅Π½ΡΠ°Π½ ΡΠ°ΠΊΠΆΠ΅ ΠΌΠΎΠΆΠ½ΠΎ ΠΈΡΠΏΠΎΠ»ΡΠ·ΠΎΠ²Π°ΡΡ Π² ΠΊΠ°ΡΠ΅ΡΡΠ²Π΅ Π²ΡΠΎΡΠΎΡΡΠ΅ΠΏΠ΅Π½Π½ΠΎΠ³ΠΎ Π²ΡΠΏΠ΅Π½ΠΈΠ²Π°ΡΡΠ΅Π³ΠΎ Π°Π³Π΅Π½ΡΠ°, Ρ ΠΎΡΡ ΠΎΠ½, Π²Π΅ΡΠΎΡΡΠ½ΠΎ, Π±ΡΠ΄Π΅Ρ ΠΌΠ΅Π½Π΅Π΅ ΡΠ΅Π½ΡΠ°Π±Π΅Π»ΡΠ½ΡΠΌ ΠΏΠΎ ΡΡΠ°Π²Π½Π΅Π½ΠΈΡ Ρ Π½-ΠΏΠ΅Π½ΡΠ°Π½ΠΎΠΌ ΠΈΠ·-Π·Π° Π΅Π³ΠΎ Π²ΡΠ΅Π΄Π½ΠΎΠ³ΠΎ Π²ΠΎΠ·Π΄Π΅ΠΉΡΡΠ²ΠΈΡ Π½Π° ΠΏΡΠΎΡΠ½ΠΎΡΡΡ Π½Π° ΡΠΆΠ°ΡΠΈΠ΅ ΠΈ ΡΡΠ°Π±ΠΈΠ»ΡΠ½ΠΎΡΡΡ ΡΠ°Π·ΠΌΠ΅ΡΠΎΠ².Π₯ΠΎΡΡ ΡΡΠΎ ΠΈΡΡΠ»Π΅Π΄ΠΎΠ²Π°Π½ΠΈΠ΅ Π½Π΅ ΠΏΡΠΎΠ΄Π΅ΠΌΠΎΠ½ΡΡΡΠΈΡΠΎΠ²Π°Π»ΠΎ ΡΠ±Π΅Π΄ΠΈΡΠ΅Π»ΡΠ½ΡΡ Π°ΡΠ³ΡΠΌΠ΅Π½ΡΠΎΠ² Π² ΠΏΠΎΠ»ΡΠ·Ρ ΠΈΡΠΏΠΎΠ»ΡΠ·ΠΎΠ²Π°Π½ΠΈΡ LBBA, ΠΈΠ·ΠΎΠ±ΡΡΠ°Π½Π°, ΡΡΠΎ, Π²Π΅ΡΠΎΡΡΠ½ΠΎ, ΡΠ²ΡΠ·Π°Π½ΠΎ Ρ ΡΠ½ΠΎΡΠΎΠΌ ΡΡΠ΅Π·ΠΌΠ΅ΡΠ½ΡΡ ΠΏΡΡΡΠΎΡ Π² ΠΏΠ΅Π½Ρ. ΠΠ΅ΡΠΎΡΡΠ½ΠΎ, ΡΡΠΎ ΡΠ°ΠΊΠΈΠ΅ ΠΏΡΡΡΠΎΡΡ ΠΌΠΎΠ³ΡΡ Π±ΡΡΡ ΡΡΡΡΠ°Π½Π΅Π½Ρ ΠΏΡΡΠ΅ΠΌ Π΄Π°Π»ΡΠ½Π΅ΠΉΡΠ΅ΠΉ ΠΎΠΏΡΠΈΠΌΠΈΠ·Π°ΡΠΈΠΈ ΠΏΠ°ΡΠ°ΠΌΠ΅ΡΡΠΎΠ² ΠΎΠ±ΡΠ°Π±ΠΎΡΠΊΠΈ Π²ΠΌΠ΅ΡΡΠ΅ Ρ ΠΏΠΎΠ²Π΅ΡΡ Π½ΠΎΡΡΠ½ΠΎ-Π°ΠΊΡΠΈΠ²Π½ΡΠΌ Π²Π΅ΡΠ΅ΡΡΠ²ΠΎΠΌ ΠΈ / ΠΈΠ»ΠΈ Π΄ΡΡΠ³ΠΈΠΌΠΈ ΠΊΠΎΠΌΠΏΠΎΠ½Π΅Π½ΡΠ°ΠΌΠΈ. ΠΡΠΈΠ½ΠΈΠΌΠ°Ρ Π²ΠΎ Π²Π½ΠΈΠΌΠ°Π½ΠΈΠ΅, ΡΡΠΎ Π³ΠΎΡΡΡΠΈΠ΅ Π³Π°Π·Ρ, ΡΠ°ΠΊΠΈΠ΅ ΠΊΠ°ΠΊ ΠΈΠ·ΠΎΠ±ΡΡΠ°Π½, Π²Π΅ΡΠΎΡΡΠ½ΠΎ, ΠΏΠΎΡΡΠ΅Π±ΡΡΡ Π΄ΠΎΠΏΠΎΠ»Π½ΠΈΡΠ΅Π»ΡΠ½ΡΡ ΠΌΠ΅Ρ Π±Π΅Π·ΠΎΠΏΠ°ΡΠ½ΠΎΡΡΠΈ ΠΈ ΠΎΠ±ΡΠ°ΡΠ΅Π½ΠΈΡ, ΠΏΠΎΠΌΠΈΠΌΠΎ ΡΠ΅Ρ , ΠΊΠΎΡΠΎΡΡΠ΅ Π² Π½Π°ΡΡΠΎΡΡΠ΅Π΅ Π²ΡΠ΅ΠΌΡ ΠΏΡΠΈΠΌΠ΅Π½ΡΡΡΡΡ Π΄Π»Ρ ΠΏΠ΅Π½ΡΠ°Π½ΠΎΠ², ΠΈ ΡΡΠΈΡΡΠ²Π°Ρ Π²ΡΠ²ΠΎΠ΄ ΠΎ ΡΠΎΠΌ, ΡΡΠΎ ΡΡΡΠ΅ΡΡΠ²Π΅Π½Π½Π°Ρ ΡΠΊΠΎΠ½ΠΎΠΌΠΈΡ Π·Π°ΡΡΠ°Ρ ΠΌΠΎΠΆΠ΅Ρ Π±ΡΡΡ Π΄ΠΎΡΡΠΈΠ³Π½ΡΡΠ° Π·Π° ΡΡΠ΅Ρ ΠΈΡΠΏΠΎΠ»ΡΠ·ΠΎΠ²Π°Π½ΠΈΡ ΠΈΠ·ΠΎΠΏΠ΅Π½ΡΠ°Π½Π° Π² ΠΊΠ°ΡΠ΅ΡΡΠ²Π΅ Π΅Π΄ΠΈΠ½ΡΡΠ²Π΅Π½Π½ΠΎΠ³ΠΎ ΠΆΠΈΠ΄ΠΊΠΎΠ³ΠΎ Π²ΡΠΏΠ΅Π½ΠΈΠ²Π°ΡΡΠ΅Π³ΠΎ Π°Π³Π΅Π½ΡΠ° , Π΄ΠΎΠΏΠΎΠ»Π½ΠΈΡΠ΅Π»ΡΠ½ΠΎΠ΅ ΠΈΡΡΠ»Π΅Π΄ΠΎΠ²Π°Π½ΠΈΠ΅ ΠΈΠ·ΠΎΠ±ΡΡΠ°Π½Π° ΠΊΠ°ΠΆΠ΅ΡΡΡ Π½Π΅ΠΎΠ±ΠΎΡΠ½ΠΎΠ²Π°Π½Π½ΡΠΌ.ΠΠ«ΠΠΠΠ« ΠΡΠΎ ΠΈΡΡΠ»Π΅Π΄ΠΎΠ²Π°Π½ΠΈΠ΅ ΠΏΡΠ΅Π΄ΠΏΠΎΠ»Π°Π³Π°Π΅Ρ, ΡΡΠΎ Π²Π΅ΡΡ ΠΈΠ·ΠΎΠΏΠ΅Π½ΡΠ°Π½ ΠΈΠ»ΠΈ ΡΠΌΠ΅ΡΡ ΠΈΠ·ΠΎΠΏΠ΅Π½ΡΠ°Π½Π° / Π½-ΠΏΠ΅Π½ΡΠ°Π½Π°, Π±ΠΎΠ³Π°ΡΠ°Ρ ΠΈΠ·ΠΎΠΏΠ΅Π½ΡΠ°Π½ΠΎΠΌ, ΠΈΠΌΠ΅Π΅Ρ ΠΌΠ°ΠΊΡΠΈΠΌΠ°Π»ΡΠ½ΡΠΉ ΠΏΠΎΡΠ΅Π½ΡΠΈΠ°Π» Π΄Π»Ρ ΡΠ΅Π°Π»ΠΈΠ·Π°ΡΠΈΠΈ ΡΠΊΠΎΠ½ΠΎΠΌΠΈΠΈ Π·Π°ΡΡΠ°Ρ ΠΏΡΠΈ ΡΠΎΡ ΡΠ°Π½Π΅Π½ΠΈΠΈ ΠΈΠ»ΠΈ ΠΏΠΎΠ²ΡΡΠ΅Π½ΠΈΠΈ ΠΏΡΠΎΠΈΠ·Π²ΠΎΠ΄ΠΈΡΠ΅Π»ΡΠ½ΠΎΡΡΠΈ. ΠΠΎΡΠ΅Π½ΡΠΈΠ°Π»ΡΠ½Π°Ρ ΡΠΊΠΎΠ½ΠΎΠΌΠΈΡ Π·Π°ΡΡΠ°Ρ ΠΌΠΎΠΆΠ΅Ρ Π±ΡΡΡ Π΄ΠΎΡΡΠΈΠ³Π½ΡΡΠ° Π·Π° ΡΡΠ΅Ρ Π±ΠΎΠ»Π΅Π΅ Π½ΠΈΠ·ΠΊΠΎΠΉ ΡΡΠΎΠΈΠΌΠΎΡΡΠΈ Π²ΡΠΏΠ΅Π½ΠΈΠ²Π°ΡΡΠ΅Π³ΠΎ Π°Π³Π΅Π½ΡΠ°, ΠΏΠΎΡΠΊΠΎΠ»ΡΠΊΡ ΠΈΠ·ΠΎΠΏΠ΅Π½ΡΠ°Π½ ΠΈ Π½-ΠΏΠ΅Π½ΡΠ°Π½ Π½Π° ΡΠΎΠ²ΡΠ΅ΠΌΠ΅Π½Π½ΠΎΠΌ ΡΡΠ½ΠΊΠ΅ Π·Π½Π°ΡΠΈΡΠ΅Π»ΡΠ½ΠΎ Π΄Π΅ΡΠ΅Π²Π»Π΅ ΡΠΈΠΊΠ»ΠΎΠΏΠ΅Π½ΡΠ°Π½Π°. ΠΠΎ Π±ΠΎΠ»ΡΡΠ°Ρ ΡΠΊΠΎΠ½ΠΎΠΌΠΈΡ ΠΏΠΎΡΠ΅Π½ΡΠΈΠ°Π»ΡΠ½ΠΎ ΠΌΠΎΠΆΠ΅Ρ Π±ΡΡΡ ΠΏΠΎΠ»ΡΡΠ΅Π½Π° Π·Π° ΡΡΠ΅Ρ ΡΠΏΠΎΡΠΎΠ±Π½ΠΎΡΡΠΈ ΠΏΡΠΎΠΈΠ·Π²ΠΎΠ΄ΠΈΡΡ 47

7 ΠΏΠ»ΠΈΡ Ρ Π±ΠΎΠ»Π΅Π΅ Π½ΠΈΠ·ΠΊΠΎΠΉ ΠΏΠ»ΠΎΡΠ½ΠΎΡΡΡΡ ΠΏΠ΅Π½ΠΎΠΏΠ»Π°ΡΡΠ°, Π½ΠΎ ΠΏΡΠΈ ΡΡΠΎΠΌ ΠΎΡΠ²Π΅ΡΠ°Π΅Ρ ΡΡΠ΅Π±ΠΎΠ²Π°Π½ΠΈΡΠΌ ΠΊ ΠΊΠΎΠ½ΡΡΡΡΠΊΡΠΈΠΎΠ½Π½ΡΠΌ, ΠΈΠ·ΠΎΠ»ΡΡΠΈΠΎΠ½Π½ΡΠΌ ΠΈ ΠΏΡΠΎΡΠΈΠ²ΠΎΠΏΠΎΠΆΠ°ΡΠ½ΡΠΌ ΡΠ²ΠΎΠΉΡΡΠ²Π°ΠΌ.ΠΡΡ ΠΈΠ½ΡΠΎΡΠΌΠ°ΡΠΈΡ, ΡΠΎΠ΄Π΅ΡΠΆΠ°ΡΠ°ΡΡΡ Π² Π΄Π°Π½Π½ΠΎΠΌ Π΄ΠΎΠΊΡΠΌΠ΅Π½ΡΠ΅, ΠΏΡΠ΅Π΄ΠΎΡΡΠ°Π²Π»ΡΠ΅ΡΡΡ Β«ΠΊΠ°ΠΊ Π΅ΡΡΡΒ» Π±Π΅Π· ΠΊΠ°ΠΊΠΈΡ -Π»ΠΈΠ±ΠΎ Π³Π°ΡΠ°Π½ΡΠΈΠΉ, ΡΠ²Π½ΡΡ ΠΈΠ»ΠΈ ΠΏΠΎΠ΄ΡΠ°Π·ΡΠΌΠ΅Π²Π°Π΅ΠΌΡΡ , ΠΈ Π½ΠΈ ΠΏΡΠΈ ΠΊΠ°ΠΊΠΈΡ ΠΎΠ±ΡΡΠΎΡΡΠ΅Π»ΡΡΡΠ²Π°Ρ Π°Π²ΡΠΎΡΡ ΠΈΠ»ΠΈ Huntsman Π½Π΅ Π½Π΅ΡΡΡ ΠΎΡΠ²Π΅ΡΡΡΠ²Π΅Π½Π½ΠΎΡΡΠΈ Π·Π° Π»ΡΠ±ΠΎΠΉ ΡΡΠ΅ΡΠ± Π»ΡΠ±ΠΎΠ³ΠΎ Ρ Π°ΡΠ°ΠΊΡΠ΅ΡΠ°, Π²ΠΎΠ·Π½ΠΈΠΊΡΠΈΠΉ Π² ΡΠ΅Π·ΡΠ»ΡΡΠ°ΡΠ΅ ΠΈΡΠΏΠΎΠ»ΡΠ·ΠΎΠ²Π°Π½ΠΈΡ ΡΠ°ΠΊΠΎΠΉ ΠΈΠ½ΡΠΎΡΠΌΠ°ΡΠΈΠΈ ΠΈΠ»ΠΈ ΠΈΡΠΏΠΎΠ»ΡΠ·ΠΎΠ²Π°Π½ΠΈΡ ΡΠ°ΠΊΠΎΠΉ ΠΈΠ½ΡΠΎΡΠΌΠ°ΡΠΈΠΈ. ΠΠΈΡΡΠΎ, ΡΠΎΠ΄Π΅ΡΠΆΠ°ΡΠ΅Π΅ΡΡ Π² ΡΡΠΎΠΉ ΠΏΡΠ±Π»ΠΈΠΊΠ°ΡΠΈΠΈ, Π½Π΅ Π΄ΠΎΠ»ΠΆΠ½ΠΎ ΡΠΎΠ»ΠΊΠΎΠ²Π°ΡΡΡΡ ΠΊΠ°ΠΊ Π»ΠΈΡΠ΅Π½Π·ΠΈΡ Π½Π° ΠΊΠ°ΠΊΠΎΠ΅-Π»ΠΈΠ±ΠΎ ΠΏΡΠ°Π²ΠΎ ΠΈΠ½ΡΠ΅Π»Π»Π΅ΠΊΡΡΠ°Π»ΡΠ½ΠΎΠΉ ΡΠΎΠ±ΡΡΠ²Π΅Π½Π½ΠΎΡΡΠΈ ΠΊΠ°ΠΊΠΎΠΉ-Π»ΠΈΠ±ΠΎ ΠΎΡΠ³Π°Π½ΠΈΠ·Π°ΡΠΈΠΈ ΠΈΠ»ΠΈ ΠΊΠ°ΠΊ ΠΏΡΠ΅Π΄Π»ΠΎΠΆΠ΅Π½ΠΈΠ΅, ΡΠ΅ΠΊΠΎΠΌΠ΅Π½Π΄Π°ΡΠΈΡ ΠΈΠ»ΠΈ ΡΠ°Π·ΡΠ΅ΡΠ΅Π½ΠΈΠ΅ Π½Π° ΡΠΎΠ²Π΅ΡΡΠ΅Π½ΠΈΠ΅ ΠΊΠ°ΠΊΠΈΡ -Π»ΠΈΠ±ΠΎ Π΄Π΅ΠΉΡΡΠ²ΠΈΠΉ, Π½Π°ΡΡΡΠ°ΡΡΠΈΡ Π»ΡΠ±ΠΎΠΉ ΠΏΠ°ΡΠ΅Π½Ρ. Π’Π΅ΡΠΌΠΈΠ½ Β«HuntsmanΒ» ΠΈΡΠΏΠΎΠ»ΡΠ·ΡΠ΅ΡΡΡ Π·Π΄Π΅ΡΡ ΡΠΎΠ»ΡΠΊΠΎ Π΄Π»Ρ ΡΠ΄ΠΎΠ±ΡΡΠ²Π° ΠΈ ΠΎΡΠ½ΠΎΡΠΈΡΡΡ ΠΊ Huntsman LLC, Π΅Π΅ ΠΏΡΡΠΌΡΠΌ ΠΈ ΠΊΠΎΡΠ²Π΅Π½Π½ΡΠΌ Π°ΡΡΠΈΠ»ΠΈΡΠΎΠ²Π°Π½Π½ΡΠΌ Π»ΠΈΡΠ°ΠΌ, Π° ΡΠ°ΠΊΠΆΠ΅ ΠΈΡ ΡΠΎΡΡΡΠ΄Π½ΠΈΠΊΠ°ΠΌ, Π΄ΠΎΠ»ΠΆΠ½ΠΎΡΡΠ½ΡΠΌ Π»ΠΈΡΠ°ΠΌ ΠΈ Π΄ΠΈΡΠ΅ΠΊΡΠΎΡΠ°ΠΌ.Π‘ΠΠΠ‘ΠΠ ΠΠΠ’ΠΠ ΠΠ’Π£Π Π« 1. Ducker Research Company, Inc. ΠΠ²Π³ΡΡΡ, ΠΠ±Π·ΠΎΡ ΡΡΠ½ΠΊΠ° ΠΊΠΎΠ½Π΅ΡΠ½ΠΎΠ³ΠΎ ΠΈΡΠΏΠΎΠ»ΡΠ·ΠΎΠ²Π°Π½ΠΈΡ Π² ΠΏΠΎΠ»ΠΈΡΡΠ΅ΡΠ°Π½ΠΎΠ²ΠΎΠΉ ΠΏΡΠΎΠΌΡΡΠ»Π΅Π½Π½ΠΎΡΡΠΈ, ΡΡΡ. RFP1. 2. Π‘ΠΈΠ³Π΅Π» Π. ΠΠΆΠ΅Π³ΠΎΠ΄Π½ΠΎΠ΅ ΠΈΡΡΠ»Π΅Π΄ΠΎΠ²Π°Π½ΠΈΠ΅ ΡΡΠ½ΠΊΠ° NRCA ΠΎΡ 23 Π°ΠΏΡΠ΅Π»Ρ ΠΏΠΎΠΊΠ°Π·ΡΠ²Π°Π΅Ρ, ΡΡΠΎ ΠΏΠΎΠ΄ΡΡΠ΄ΡΠΈΠΊΠΈ ΠΎΠΏΡΠΈΠΌΠΈΡΡΠΈΡΠ½ΠΎ ΠΎΡΠ½ΠΎΡΡΡΡΡ ΠΊ 23, ΠΏΡΠΎΡΠ΅ΡΡΠΈΠΎΠ½Π°Π»ΡΠ½ΡΠΌ ΠΊΡΠΎΠ²Π΅Π»ΡΠ½ΡΠΌ ΠΏΠΎΠΊΡΡΡΠΈΡΠΌ. 3. ΠΠ΅ΡΡΠΈΠ΅Ρ Π . Π., Π‘. Π. Π‘ΠΈΠ½Π³Ρ , ΠΠΆ. Π‘. ΠΠΎΡΡΠ° ΠΈ Π. ΠΠΎΠ½Π°ΠΏΠ΅ΡΡΠΎΠ½Π°. 98, ΠΠ΅ΡΡΠΊΠΈΠΉ ΠΏΠ΅Π½ΠΎΠΏΠΎΠ»ΠΈΡΡΠ΅ΡΠ°Π½ Π΄Π»Ρ ΠΏΡΠΎΠΈΠ·Π²ΠΎΠ΄ΡΡΠ²Π° ΠΊΠ°ΡΡΠΎΠ½Π°, ΠΏΠΎΠ»ΡΡΠ΅Π½Π½ΡΠΉ ΠΌΠ΅ΡΠΎΠ΄ΠΎΠΌ ΡΠΊΡΡΡΡΠ·ΠΈΠΈ Ρ ΡΠ°Π·Π΄ΡΠ²ΠΎΠΌ, Π΄Π»Ρ ΠΈΠ½Π΄ΡΡΡΡΠΈΠΈ ΠΊΠ°ΡΡΠΎΠ½Π°. ΠΠΎΠ²ΡΠΉ ΠΏΠΎΠ΄Ρ ΠΎΠ΄, ΠΠ°ΡΠ΅ΡΠΈΠ°Π»Ρ Π²ΡΡΡΠ°Π²ΠΊΠΈ Polyurethanes Expo 98, ΡΡΡ. Π₯Π°Π½ΡΡΠΌΠ°Π½, 23, ΠΠ΄Π³Π΅Π·ΠΈΡ ΠΊ ΠΎΡΡΠ»Π°ΠΈΠ²Π°Π½ΠΈΡ Π΄Π»Ρ Π»Π°ΠΌΠΈΠ½Π°ΡΠ½ΡΡ ΠΏΠ»ΠΈΡ PTP Burns., S. B., and E.Π. Π¨ΠΌΠΈΠ΄Ρ, 93, Π‘ΠΎΠΎΡΠ½ΠΎΡΠ΅Π½ΠΈΠ΅ PIR / PUR, ΠΡΠ΅ΠΌΠΈΡΠ½ΡΠΉ ΠΊΠΎΠ½Π³ΡΠ΅ΡΡ ΠΏΠΎΠ»ΠΈΡΡΠ΅ΡΠ°Π½ΠΎΠ², ΡΡΡ. ΠΠΈΡΠΌΠ°Π½Ρ, Π., Π . ΠΠ΅ ΠΠΎΡ ΠΈ Π. Π. Π ΠΎΡΠ±ΠΎΡΡΠΌ. 93. ΠΡΠΏΠΎΠ»ΡΠ·ΠΎΠ²Π°Π½ΠΈΠ΅ Π°Π»ΡΡΠ΅ΡΠ½Π°ΡΠΈΠ²Π½ΡΡ Π²ΡΠΏΠ΅Π½ΠΈΠ²Π°ΡΡΠΈΡ Π°Π³Π΅Π½ΡΠΎΠ² Π² ΠΏΠ΅Π½ΠΎΠΏΠΎΠ»ΠΈΡΡΠ΅ΡΠ°Π½Π΅ — Π‘ΡΠ°Π²Π½Π΅Π½ΠΈΠ΅ ΡΠΊΡΠΏΠ΅ΡΠΈΠΌΠ΅Π½ΡΠ°Π»ΡΠ½ΡΡ ΠΈ ΠΏΡΠΎΠ³Π½ΠΎΠ·ΠΈΡΡΠ΅ΠΌΡΡ ΠΌΠ°ΡΠ΅ΡΠΈΠ°Π»ΠΎΠ² ΠΡΠ΅ΠΌΠΈΡΠ½ΠΎΠ³ΠΎ ΠΊΠΎΠ½Π³ΡΠ΅ΡΡΠ° ΠΏΠΎ ΡΡΠ°ΡΠ΅Π½ΠΈΡ 93, ΡΡΡ Π‘ΠΈΠ½Π³Ρ Π‘.Π., Π. ΠΡΠΈΡΡ ΠΈ Π. ΠΠ΅Π΄Π΅ΠΊΠ΅Ρ, 22, ΠΠΎΠ»Π³ΠΎΡΡΠΎΡΠ½Π°Ρ ΡΠ΅ΡΠΌΠΎΡΡΠΎΠΉΠΊΠΎΡΡΡ ΠΏΠΎΠ»ΠΈΠΈΠ·ΠΎΡΠΈΠ°Π½ΡΡΠ°ΡΠ½ΠΎΠ³ΠΎ Π»Π°ΠΌΠΈΠ½Π°ΡΠ°, ΠΏΠΎΠ»ΡΡΠ΅Π½Π½ΠΎΠ³ΠΎ ΡΠΊΡΡΡΡΠ·ΠΈΠ΅ΠΉ Ρ ΡΠ°Π·Π΄ΡΠ²ΠΎΠΌ ΠΏΠ΅Π½ΡΠ°Π½ΠΎΠΌ. Boards, Proceedings of the Polyurethanes Conference 22, pp Singh SN, SB Burns, JS Costa, and V. Bonapersona, 97 ΠΠ΅ΡΠΎΠ΄Ρ ΡΠ²Π΅Π»ΠΈΡΠ΅Π½ΠΈΡ ΡΠ°ΡΡΠ²ΠΎΡΠΈΠΌΠΎΡΡΠΈ ΡΠ³Π»Π΅Π²ΠΎΠ΄ΠΎΡΠΎΠ΄Π° Π² ΠΏΠΎΠ»ΠΈΡΡΠ΅ΡΠ°Π½ΠΎΠ²ΠΎΠΌ ΡΡΡΡΠ΅, Π’ΡΡΠ΄Ρ ΠΡΠ΅ΠΌΠΈΡΠ½ΠΎΠ³ΠΎ ΠΊΠΎΠ½Π³ΡΠ΅ΡΡΠ° ΠΏΠΎ ΠΏΠΎΠ»ΠΈΡΡΠ΅ΡΠ°Π½Π°ΠΌ 97, ΡΡΡ. ΠΠΠΠΠ ΠΠ€ΠΠ Sachchida N Singh Π‘Π°ΡΡΠΈΠ΄Π° Π² Π½Π°ΡΡΠΎΡΡΠ΅Π΅ Π²ΡΠ΅ΠΌΡ ΡΠ²Π»ΡΠ΅ΡΡΡ ΡΠ΅Ρ Π½ΠΈΡΠ΅ΡΠΊΠΈΠΌ ΡΠΊΡΠΏΠ΅ΡΡΠΎΠΌ ΠΏΠΎΠ΄ΡΠ°Π·Π΄Π΅Π»Π΅Π½ΠΈΡ ΠΏΠΎ ΠΏΡΠΎΠΈΠ·Π²ΠΎΠ΄ΡΡΠ²Ρ ΠΏΠΎΠ»ΠΈΡΡΠ΅ΡΠ°Π½ΠΎΠ² Π² ΠΊΠΎΠΌΠΏΠ°Π½ΠΈΠΈ Huntsman.Π‘ ΠΌΠΎΠΌΠ΅Π½ΡΠ° ΠΏΡΠΈΡ ΠΎΠ΄Π° Π² 87 ΠΎΠ½ Π·Π°Π½ΠΈΠΌΠ°Π» Π²ΡΠ΅ Π±ΠΎΠ»Π΅Π΅ ΠΎΡΠ²Π΅ΡΡΡΠ²Π΅Π½Π½ΡΠ΅ Π΄ΠΎΠ»ΠΆΠ½ΠΎΡΡΠΈ Π² ΠΎΡΠ΄Π΅Π»Π°Ρ ΡΠ°Π·Π²ΠΈΡΠΈΡ ΡΠ΅Ρ Π½ΠΎΠ»ΠΎΠ³ΠΈΠΉ ΠΊΠΎΠΌΠΏΠ°Π½ΠΈΠΈ. ΠΠ½ ΡΠ°Π±ΠΎΡΠ°Π» Π²ΠΎ ΠΌΠ½ΠΎΠ³ΠΈΡ ΡΠ°Π·Π»ΠΈΡΠ½ΡΡ ΠΎΠ±Π»Π°ΡΡΡΡ ΠΏΡΠΈΠΌΠ΅Π½Π΅Π½ΠΈΡ Ρ ΠΈΠΌΠΈΠΈ ΠΈ ΡΠ΅Ρ Π½ΠΎΠ»ΠΎΠ³ΠΈΠΉ ΠΏΠΎΠ»ΠΈΡΡΠ΅ΡΠ°Π½Π°, Π° Π² ΠΏΠΎΡΠ»Π΅Π΄Π½Π΅Π΅ Π²ΡΠ΅ΠΌΡ ΠΏΡΠΈΠ»ΠΎΠΆΠΈΠ» Π·Π½Π°ΡΠΈΡΠ΅Π»ΡΠ½ΡΠ΅ ΡΡΠΈΠ»ΠΈΡ Π² ΡΠ΅ΠΊΡΠΎΡΠ΅ ΠΆΠ΅ΡΡΠΊΠΈΡ ΠΏΠ΅Π½ΠΎΠΏΠ»Π°ΡΡΠΎΠ². ΠΠ½ ΠΈΠΌΠ΅Π΅Ρ Π΄ΠΎΠΊΡΠΎΡΡΠΊΡΡ ΡΡΠ΅ΠΏΠ΅Π½Ρ Π² ΠΎΠ±Π»Π°ΡΡΠΈ ΠΌΠ°ΡΠ΅ΡΠΈΠ°Π»ΠΎΠ²Π΅Π΄Π΅Π½ΠΈΡ ΠΈ ΠΈΠ½ΠΆΠ΅Π½Π΅ΡΠΈΠΈ ΠΠ°ΡΡΠ°ΡΡΡΠ΅ΡΡΠΊΠΎΠ³ΠΎ ΡΠ΅Ρ Π½ΠΎΠ»ΠΎΠ³ΠΈΡΠ΅ΡΠΊΠΎΠ³ΠΎ ΠΈΠ½ΡΡΠΈΡΡΡΠ° ΠΈ ΡΡΠ΅ΠΏΠ΅Π½Ρ ΠΌΠ°Π³ΠΈΡΡΡΠ° Π½Π°ΡΠΊ Π² ΠΎΠ±Π»Π°ΡΡΠΈ Ρ ΠΈΠΌΠΈΡΠ΅ΡΠΊΠΎΠ³ΠΎ ΠΌΠ°ΡΠΈΠ½ΠΎΡΡΡΠΎΠ΅Π½ΠΈΡ Π² ΠΠΎΠ»ΠΈΡΠ΅Ρ Π½ΠΈΡΠ΅ΡΠΊΠΎΠΌ ΠΈΠ½ΡΡΠΈΡΡΡΠ΅ Π Π΅Π½ΡΡΠ΅Π»Π΅ΡΠ°. ΠΠΎΠ½ΠΈΠΊΠ° ΠΡΠΈΡΡ-ΠΠ°ΡΠ°ΠΌΠ°Π³ΠΈ ΠΠΎΠ½ΠΈΠΊΠ° — ΠΌΠ΅Π½Π΅Π΄ΠΆΠ΅Ρ ΠΏΠΎ ΡΠ°Π±ΠΎΡΠ΅ Ρ ΠΊΠ»ΠΈΠ΅Π½ΡΠ°ΠΌΠΈ Π² Huntsman.ΠΡΠΈΡΠΎΠ΅Π΄ΠΈΠ½ΠΈΠ²ΡΠΈΡΡ ΠΊ Π±ΠΈΠ·Π½Π΅ΡΡ ΠΏΠΎ ΠΏΡΠΎΠΈΠ·Π²ΠΎΠ΄ΡΡΠ²Ρ ΠΏΠΎΠ»ΠΈΡΡΠ΅ΡΠ°Π½ΠΎΠ² Π² 97 Π³ΠΎΠ΄Ρ Π² ΠΊΠ°ΡΠ΅ΡΡΠ²Π΅ ΡΠ΅Ρ Π½ΠΈΡΠ΅ΡΠΊΠΎΠ³ΠΎ ΡΠΏΠ΅ΡΠΈΠ°Π»ΠΈΡΡΠ°, ΠΎΠ½Π° ΠΎΠ±Π΅ΡΠΏΠ΅ΡΠΈΠ²Π°Π»Π° ΡΠ΅Ρ Π½ΠΈΡΠ΅ΡΠΊΠΈΠ΅ ΡΡΠ»ΡΠ³ΠΈ ΠΈ ΡΠ°Π·ΡΠ°Π±ΠΎΡΠΊΠΈ Π΄Π»Ρ ΡΠ°Π·Π»ΠΈΡΠ½ΡΡ ΡΠ΅ΠΊΡΠΎΡΠΎΠ² ΡΡΡΠΎΠΈΡΠ΅Π»ΡΠ½ΠΎΠΉ ΠΈΠ½Π΄ΡΡΡΡΠΈΠΈ. Π Π½Π°ΡΡΠΎΡΡΠ΅Π΅ Π²ΡΠ΅ΠΌΡ ΠΎΠ½Π° ΡΠ°Π±ΠΎΡΠ°Π΅Ρ ΠΌΠ΅Π½Π΅Π΄ΠΆΠ΅ΡΠΎΠΌ ΠΏΠΎ ΡΠ°Π±ΠΎΡΠ΅ Ρ ΠΊΠ»ΠΈΠ΅Π½ΡΠ°ΠΌΠΈ Π² ΡΠ΅ΠΊΡΠΎΡΠ΅ System House. ΠΠ½Π° ΠΈΠΌΠ΅Π΅Ρ ΡΡΠ΅ΠΏΠ΅Π½Ρ ΠΌΠ°Π³ΠΈΡΡΡΠ° Π½Π°ΡΠΊ Π² ΠΎΠ±Π»Π°ΡΡΠΈ Ρ ΠΈΠΌΠΈΡΠ΅ΡΠΊΠΎΠΉ ΠΈΠ½ΠΆΠ΅Π½Π΅ΡΠΈΠΈ Π² Π£Π½ΠΈΠ²Π΅ΡΡΠΈΡΠ΅ΡΠ΅ Π₯ΠΎΠ²Π°ΡΠ΄Π° ΠΈ ΡΡΠ΅ΠΏΠ΅Π½Ρ Π±Π°ΠΊΠ°Π»Π°Π²ΡΠ° Π² ΠΎΠ±Π»Π°ΡΡΠΈ Ρ ΠΈΠΌΠΈΡΠ΅ΡΠΊΠΎΠΉ ΠΈΠ½ΠΆΠ΅Π½Π΅ΡΠΈΠΈ Π² Π’Π΅Ρ Π°ΡΡΠΊΠΎΠΌ ΡΠ½ΠΈΠ²Π΅ΡΡΠΈΡΠ΅ΡΠ΅ A&M. ΠΠ°ΠΉΠΊΠ» ΠΠΆ. Π ΠΈΡΠΈ-ΠΌΠ»Π°Π΄ΡΠΈΠΉ. ΠΠ°ΠΉΠΊΠ» ΠΏΡΠΈΡΠΎΠ΅Π΄ΠΈΠ½ΠΈΠ»ΡΡ ΠΊ Π₯Π°Π½ΡΡΠΌΠ°Π½Ρ ΡΠ΅ΡΠ΅Π· 2 Π³ΠΎΠ΄Π° ΠΏΠΎΡΠ»Π΅ ΠΏΠΎΠ»ΡΡΠ΅Π½ΠΈΡ ΡΡΠ΅ΠΏΠ΅Π½ΠΈ Π±Π°ΠΊΠ°Π»Π°Π²ΡΠ° Π² ΠΎΠ±Π»Π°ΡΡΠΈ Ρ ΠΈΠΌΠΈΡΠ΅ΡΠΊΠΎΠΉ ΠΈΠ½ΠΆΠ΅Π½Π΅ΡΠΈΠΈ ΠΎΡ Π£Π½ΠΈΠ²Π΅ΡΡΠΈΡΠ΅Ρ ΠΡΠ΅ΠΊΡΠ΅Π»Ρ.Π Π½Π°ΡΡΠΎΡΡΠ΅Π΅ Π²ΡΠ΅ΠΌΡ ΠΎΠ½ ΡΠ²Π»ΡΠ΅ΡΡΡ ΡΠ΅Ρ Π½ΠΈΡΠ΅ΡΠΊΠΈΠΌ ΡΠΏΠ΅ΡΠΈΠ°Π»ΠΈΡΡΠΎΠΌ Π³ΡΡΠΏΠΏΡ ΠΏΠΎΠ»ΠΈΡΡΠ΅ΡΠ°Π½ΠΎΠ², ΡΠΏΠ΅ΡΠΈΠ°Π»ΠΈΠ·ΠΈΡΡΡΡΠ΅ΠΉΡΡ Π½Π° ΠΆΠ΅ΡΡΠΊΠΈΡ ΠΏΠ΅Π½ΠΎΠΏΠ»Π°ΡΡΠ°Ρ Π΄Π»Ρ ΡΡΡΠΎΠΈΡΠ΅Π»ΡΡΡΠ²Π°. 48
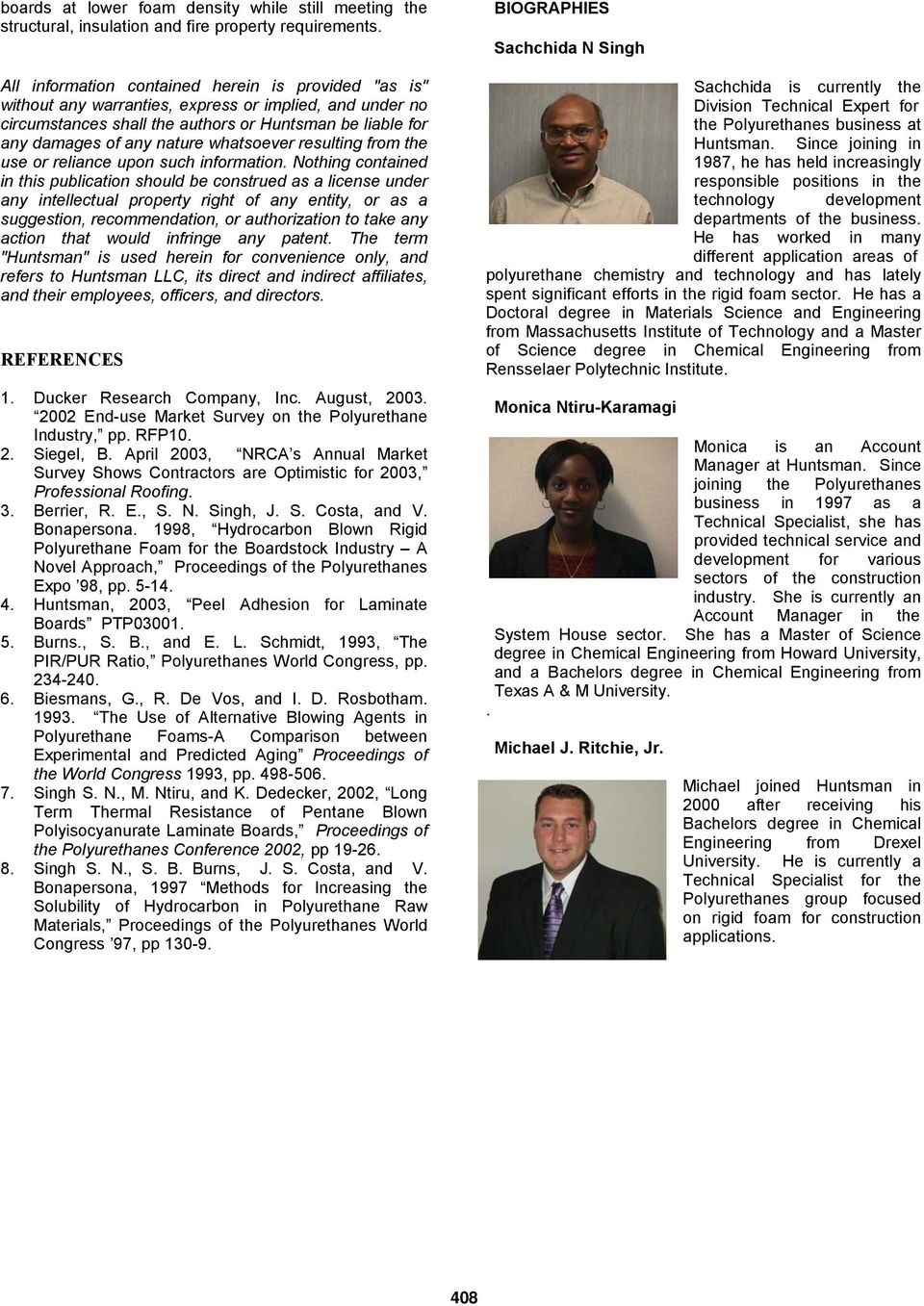
ΠΠ±ΡΠ΅ΠΌ ΡΡΠ½ΠΊΠ° ΠΏΠ΅Π½ΠΎΠΎΠ±ΡΠ°Π·ΠΎΠ²Π°ΡΠ΅Π»Π΅ΠΉ, Π΄ΠΎΠ»Ρ
ΠΠ΅ΡΠ΅ΠΊΠ»ΡΡΠΈΡΡ Π½Π°Π²ΠΈΠ³Π°ΡΠΈΡ
- ΠΡΡΠ΅ΡΡ
- ΠΠΎΡΡΠ΅Π±ΠΈΡΠ΅Π»ΡΡΠΊΠΈΠ΅ ΡΠΎΠ²Π°ΡΡ Β»
- ΠΡΠ°ΡΠΎΡΠ° ΠΈ Π»ΠΈΡΠ½Π°Ρ Π³ΠΈΠ³ΠΈΠ΅Π½Π°
- ΠΠ΄Π΅ΠΆΠ΄Π°, ΠΎΠ±ΡΠ²Ρ ΠΈ Π°ΠΊΡΠ΅ΡΡΡΠ°ΡΡ
- ΠΠΎΡΡΠ΅Π±ΠΈΡΠ΅Π»ΡΡΠΊΠΈΠ΅ ΠΏΡΠΎΠ΄ΡΠΊΡΡ ΠΈ Π½Π°ΠΏΠΈΡΠΊΠΈ
- ΠΠ»Π΅ΠΊΡΡΠΎΠ½Π½ΠΎΠ΅ ΠΈ ΡΠ»Π΅ΠΊΡΡΠΈΡΠ΅ΡΠΊΠΎΠ΅ ΠΎΠ±ΠΎΡΡΠ΄ΠΎΠ²Π°Π½ΠΈΠ΅
- Π£Ρ ΠΎΠ΄ Π·Π° Π΄ΠΎΠΌΠΎΠΌ ΠΈ Π΄Π΅ΠΊΠΎΡ
- ΠΠΎΠ»ΡΠΏΡΠΎΠ²ΠΎΠ΄Π½ΠΈΠΊΠΈ ΠΈ ΡΠ»Π΅ΠΊΡΡΠΎΠ½ΠΈΠΊΠ° Β»
- Π’Π΅Ρ Π½ΠΎΠ»ΠΎΠ³ΠΈΠΈ ΠΎΡΠΎΠ±ΡΠ°ΠΆΠ΅Π½ΠΈΡ
- ΠΠ»Π΅ΠΊΡΡΠΎΠ½Π½ΡΠ΅ ΡΠΈΡΡΠ΅ΠΌΡ Π±Π΅Π·ΠΎΠΏΠ°ΡΠ½ΠΎΡΡΠΈ
- ΠΠ»Π΅ΠΊΡΡΠΎΠ½Π½ΡΠ΅ ΡΡΡΡΠΎΠΉΡΡΠ²Π°
- ΠΠΎΠ»ΡΠΏΡΠΎΠ²ΠΎΠ΄Π½ΠΈΠΊΠΈ
- ΠΠ°ΡΡΠΈΠΊΠΈ ΠΈ ΠΎΡΠ³Π°Π½Ρ ΡΠΏΡΠ°Π²Π»Π΅Π½ΠΈΡ
- Π‘ΠΏΠ΅ΡΠΈΠ°Π»ΡΠ½ΡΠ΅ ΠΈ ΡΠΎΠ½ΠΊΠΈΠ΅ Ρ ΠΈΠΌΠΈΠΊΠ°ΡΡ Β»
- ΠΠ°ΡΠ°Π»ΠΈΠ·Π°ΡΠΎΡΡ ΠΈ ΡΠ΅ΡΠΌΠ΅Π½ΡΡ
- ΠΠΈΡΠ΅Π²ΡΠ΅ Π΄ΠΎΠ±Π°Π²ΠΊΠΈ ΠΈ Π½ΡΡΡΠΈΠΊΠΎΡΠΌΠ΅ΡΠΈΠΊΠ°
- ΠΠΎΠ·ΠΎΠ±Π½ΠΎΠ²Π»ΡΠ΅ΠΌΡΠ΅ Ρ ΠΈΠΌΠΈΡΠ΅ΡΠΊΠΈΠ΅ Π²Π΅ΡΠ΅ΡΡΠ²Π°
- Π‘ΠΏΠ΅ΡΠΈΠ°Π»ΡΠ½ΡΠ΅ ΠΏΠΎΠ»ΠΈΠΌΠ΅ΡΡ ΠΈ ΠΏΠΎΠ»ΠΈΠΌΠ΅ΡΡ Π½Π° Π±ΠΈΠΎΠ»ΠΎΠ³ΠΈΡΠ΅ΡΠΊΠΎΠΉ ΠΎΡΠ½ΠΎΠ²Π΅
- ΠΡΠΎΠ΄ΡΠΊΡΡ ΠΏΠΈΡΠ°Π½ΠΈΡ ΠΈ Π½Π°ΠΏΠΈΡΠΊΠΈ Β»
- ΠΠΎΡΠΌ ββΠ΄Π»Ρ ΠΆΠΈΠ²ΠΎΡΠ½ΡΡ ΠΈ ΠΊΠΎΡΠΌΠΎΠ²ΡΠ΅ Π΄ΠΎΠ±Π°Π²ΠΊΠΈ
- ΠΠ΅Π·ΠΎΠΏΠ°ΡΠ½ΠΎΡΡΡ ΠΏΠΈΡΠ΅Π²ΡΡ ΠΏΡΠΎΠ΄ΡΠΊΡΠΎΠ² ΠΈ ΠΎΠ±ΡΠ°Π±ΠΎΡΠΊΠ°
- ΠΠΈΠΎΠ»ΠΎΠ³ΠΈΡΠ΅ΡΠΊΠΈ Π°ΠΊΡΠΈΠ²Π½ΡΠ΅ Π΄ΠΎΠ±Π°Π²ΠΊΠΈ ΠΈ ΡΡΠ½ΠΊΡΠΈΠΎΠ½Π°Π»ΡΠ½ΡΠ΅ ΠΏΡΠΎΠ΄ΡΠΊΡΡ
- ΠΠ±ΡΠ°Π±ΠΎΡΠ°Π½Π½ΡΠ΅ ΠΈ Π·Π°ΠΌΠΎΡΠΎΠΆΠ΅Π½Π½ΡΠ΅ ΠΏΡΠΎΠ΄ΡΠΊΡΡ
- ΠΠΎΠΏΠΎΠ»Π½ΠΈΡΠ΅Π»ΡΠ½ΡΠ΅ ΠΌΠ°ΡΠ΅ΡΠΈΠ°Π»Ρ Β»
- ΠΡΠΎΠ΄Π²ΠΈΠ½ΡΡΡΠ΅ Π²Π½ΡΡΡΠ΅Π½Π½ΠΈΠ΅ ΠΌΠ°ΡΠ΅ΡΠΈΠ°Π»Ρ
- ΠΠ΅Π»Π΅Π½ΡΠ΅ ΡΡΡΠΎΠΈΡΠ΅Π»ΡΠ½ΡΠ΅ ΠΌΠ°ΡΠ΅ΡΠΈΠ°Π»Ρ
- ΠΠΈΠΊΡΠΎΡΠΎΡΠΌΠΎΠ²ΠΊΠΈ ΠΈ ΠΌΠΈΠΊΡΠΎΡΡΠ΅ΡΡ
- ΠΠ°Π½ΠΎΡΠ°ΡΡΠΈΡΡ
- Π£ΠΌΠ½ΡΠΉ ΡΠ΅ΠΊΡΡΠΈΠ»Ρ
- Π‘ΡΠ΅ΠΊΠ»ΠΎ, ΠΊΠ΅ΡΠ°ΠΌΠΈΠΊΠ° ΠΈ Π²ΠΎΠ»ΠΎΠΊΠ½Π°
- ΠΠ΄ΡΠ°Π²ΠΎΠΎΡ ΡΠ°Π½Π΅Π½ΠΈΠ΅ Β»
- ΠΠΈΠΎΡΠ΅Ρ Π½ΠΎΠ»ΠΎΠ³ΠΈΠΈ
- ΠΠ»ΠΈΠ½ΠΈΡΠ΅ΡΠΊΠ°Ρ Π΄ΠΈΠ°Π³Π½ΠΎΡΡΠΈΠΊΠ°
- ΠΠ’ Π² ΡΡΠ΅ΡΠ΅ Π·Π΄ΡΠ°Π²ΠΎΠΎΡ ΡΠ°Π½Π΅Π½ΠΈΡ
- ΠΠ΅Π΄ΠΈΡΠΈΠ½ΡΠΊΠΎΠ΅ ΠΎΠ±ΠΎΡΡΠ΄ΠΎΠ²Π°Π½ΠΈΠ΅
- ΠΠ΅Π΄ΠΈΡΠΈΠ½ΡΠΊΠ°Ρ Π²ΠΈΠ·ΡΠ°Π»ΠΈΠ·Π°ΡΠΈΡ
- Π€Π°ΡΠΌΠ°ΡΠ΅Π²ΡΠΈΡΠ΅ΡΠΊΠΈΠ΅ ΠΏΡΠ΅ΠΏΠ°ΡΠ°ΡΡ
- ΠΠ΄ΠΎΡΠΎΠ²ΡΠ΅ ΠΆΠΈΠ²ΠΎΡΠ½ΡΡ
- Π’Π΅Ρ Π½ΠΎΠ»ΠΎΠ³ΠΈΠΈ Β»
- ΠΠ²ΡΠΎΠΌΠΎΠ±ΠΈΠ»Π΅ΡΡΡΠΎΠ΅Π½ΠΈΠ΅ ΠΈ ΡΡΠ°Π½ΡΠΏΠΎΡΡ
- ΠΠ½ΡΡΠ°ΡΡΡΡΠΊΡΡΡΠ° ΡΠ²ΡΠ·ΠΈ
- Π£ΡΠ»ΡΠ³ΠΈ ΡΠ²ΡΠ·ΠΈ
- Π¦ΠΈΡΡΠΎΠ²ΡΠ΅ ΠΌΠ΅Π΄ΠΈΠ°
- ΠΠΠ ΠΈ ΡΡΡΠΎΠΈΡΠ΅Π»ΡΡΡΠ²ΠΎ
- Π‘Π΅ΡΠ΅Π²Π°Ρ Π±Π΅Π·ΠΎΠΏΠ°ΡΠ½ΠΎΡΡΡ
- Π’Π΅Ρ Π½ΠΎΠ»ΠΎΠ³ΠΈΠΈ Π½ΠΎΠ²ΠΎΠ³ΠΎ ΠΏΠΎΠΊΠΎΠ»Π΅Π½ΠΈΡ
- Π₯ΠΈΠΌΠΈΡΠ΅ΡΠΊΠΈΠ΅ ΠΏΡΠΎΠ΄ΡΠΊΡΡ Β»
- ΠΠ³ΡΠΎΡ ΠΈΠΌΠΈΠΊΠ°ΡΡ ΠΈ ΡΠ΄ΠΎΠ±ΡΠ΅Π½ΠΈΡ
- ΠΠ΅Π·ΠΈΠ½ΡΠΈΡΠΈΡΡΡΡΠΈΠ΅ ΠΈ ΠΊΠΎΠ½ΡΠ΅ΡΠ²Π°Π½ΡΡ
- ΠΠ±ΠΎΡΡΠ΄ΠΎΠ²Π°Π½ΠΈΠ΅ Π΄Π»Ρ Π±ΡΡΠ΅Π½ΠΈΡ ΠΈ Π΄ΠΎΠ±ΡΡΠΈ
- ΠΡΠ³Π°Π½ΠΈΡΠ΅ΡΠΊΠΈΠ΅ Ρ ΠΈΠΌΠΈΡΠ΅ΡΠΊΠΈΠ΅ Π²Π΅ΡΠ΅ΡΡΠ²Π°
- ΠΡΠ°ΡΠΊΠΈ, ΠΏΠΎΠΊΡΡΡΠΈΡ ΠΈ ΡΠ΅ΡΠ½ΠΈΠ»Π° Π΄Π»Ρ ΠΏΠ΅ΡΠ°ΡΠΈ
- ΠΠΈΡΠ½Π°Ρ Π³ΠΈΠ³ΠΈΠ΅Π½Π° ΠΈ ΠΊΠΎΡΠΌΠ΅ΡΠΈΠΊΠ°
- ΠΠ΅ΡΡΠ΅Ρ ΠΈΠΌΠΈΡ
- ΠΠ»Π°ΡΡΠΌΠ°ΡΡΡ, ΠΏΠΎΠ»ΠΈΠΌΠ΅ΡΡ ΠΈ ΡΠΌΠΎΠ»Ρ
- ΠΡΠΈΡΡΠΊΠ° Π²ΠΎΠ΄Ρ ΠΈ ΠΎΡΠ°Π΄ΠΊΠ°
- Π£ΡΠ»ΡΠ³ΠΈ
- ΠΠΎΠ½ΡΡΠ»ΡΡΠ°ΡΠΈΠΎΠ½Π½ΡΠ΅ ΡΡΠ»ΡΠ³ΠΈ
- ΠΡΡΠ΅ΡΡ ΠΎΠ± ΠΈΡΡΠ»Π΅Π΄ΠΎΠ²Π°Π½ΠΈΡΡ ΡΡΠ½ΠΊΠ°
- Π Π°Π±ΠΎΡΠ° Π½Π° ΠΏΠΎΠ»Π½ΡΡ ΡΡΠ°Π²ΠΊΡ
- Π‘Π»ΡΠΆΠ±Π° ΡΠ°ΠΌΠΎΠΆΠ΅Π½Π½ΡΡ ΠΈΡΡΠ»Π΅Π΄ΠΎΠ²Π°Π½ΠΈΠΉ
- ΠΠΎΠ½ΠΈΡΠΎΡΠΈΠ½Π³ ΡΡΠ½ΠΊΠ°
- ΠΠΎΠ΄ΠΏΠΈΡΠΊΠ°
- ΠΠΎΠΌΠΏΠ°Ρ
- Π Π½Π°Ρ
- ΠΡΠΎ ΠΌΡ
- ΠΠΎΡΠ΅ΠΌΡ Π²ΡΠ±ΠΈΡΠ°ΡΡ Π½Π°Ρ
- ΠΠ΅ΡΠΎΠ΄ΠΎΠ»ΠΎΠ³ΠΈΡ ΠΈΡΡΠ»Π΅Π΄ΠΎΠ²Π°Π½ΠΈΡ
- ΠΡΠ·ΡΠ²Ρ ΠΊΠ»ΠΈΠ΅Π½ΡΠΎΠ²
- ΠΠΎΠ½ΡΠ΅ΡΠ΅Π½ΡΠΈΠΈ
- Π‘ΡΡΠ»ΠΊΠΈ Π² Π‘ΠΠ
- ΠΠ½Π°Π»ΠΈΡΠΈΠΊΠ°
- Research Insights
- Π’Π΅ΠΊΡΡΠΈΠ΅ ΠΎΡΡΠ΅ΡΡ
- ΠΡΠΈΠΌΠ΅ΡΡ ΠΈΠ· ΠΏΡΠ°ΠΊΡΠΈΠΊΠΈ
- ΠΡΠ΅ΡΡ-ΡΠ΅Π½ΡΡ
- ΠΠΎΠ½ΡΠ°ΠΊΡ
- ΠΠΎΠ³ΠΈΠ½
- ΠΠΎΠΌΠΎΠΉ
- Β»
- Π‘ΠΏΠ΅ΡΠΈΠ°Π»ΡΠ½ΡΠ΅ ΠΏΠΎΠ»ΠΈΠΌΠ΅ΡΡ
- Β»
- ΠΠ±ΡΠ΅ΠΌ ΡΡΠ½ΠΊΠ° ΠΏΠ΅Π½ΠΎΠΎΠ±ΡΠ°Π·ΡΡΡΠΈΡ Π°Π³Π΅Π½ΡΠΎΠ², Π΄ΠΎΠ»Ρ, Π³Π»ΠΎΠ±Π°Π»ΡΠ½ΡΠΉ ΠΎΡΡΠ°ΡΠ»Π΅Π²ΠΎΠΉ ΠΎΡΡΠ΅Ρ, 2019-2025 Π³Π³.
Π ΡΠ½ΠΎΠΊ Π²ΡΠΏΠ΅Π½ΠΈΠ²Π°ΡΡΠΈΡ Π°Π³Π΅Π½ΡΠΎΠ², ΠΊΠ°ΠΊ ΠΎΠΆΠΈΠ΄Π°Π΅ΡΡΡ, ΠΊ 2022 Π³ΠΎΠ΄Ρ Π΄ΠΎΡΡΠΈΠ³Π½Π΅Ρ 963 ΠΌΠΈΠ»Π»ΠΈΠΎΠ½Π° Π΄ΠΎΠ»Π»Π°ΡΠΎΠ² Π²ΠΎ Π²ΡΠ΅ΠΌ ΠΌΠΈΡΠ΅
ΠΡΡΠ΅Ρ ΠΎ ΡΡΠ½ΠΊΠ΅ ΠΏΠ΅Π½ΠΎΠΎΠ±ΡΠ°Π·ΠΎΠ²Π°ΡΠ΅Π»Π΅ΠΉ , ΠΎΠΏΡΠ±Π»ΠΈΠΊΠΎΠ²Π°Π½Π½ΡΠΉ Allied Market Research, ΠΏΡΠΎΠ³Π½ΠΎΠ·ΠΈΡΡΠ΅Ρ, ΡΡΠΎ ΠΊ 2022 Π³ΠΎΠ΄Ρ ΠΌΠΈΡΠΎΠ²ΠΎΠΉ ΡΡΠ½ΠΎΠΊ Π΄ΠΎΡΡΠΈΠ³Π½Π΅Ρ 963 ΠΌΠ»Π½ Π΄ΠΎΠ»Π»Π°ΡΠΎΠ² Ρ 684 ΠΌΠ»Π½ Π΄ΠΎΠ»Π»Π°ΡΠΎΠ² Π² 2015 Π³ΠΎΠ΄Ρ Ρ ΡΡΠ΅Π΄Π½Π΅Π³ΠΎΠ΄ΠΎΠ²ΡΠΌ ΡΠ΅ΠΌΠΏΠΎΠΌ ΡΠΎΡΡΠ° 5,21% Ρ 2016 ΠΏΠΎ 2022 Π³ΠΎΠ΄. Π 2015 Π³ΠΎΠ΄Ρ Π½Π° Π΄ΠΎΠ»Ρ ΠΏΠΎΠ»ΠΈΡΡΠ΅ΡΠ°Π½Π° ΠΏΡΠΈΡ ΠΎΠ΄ΠΈΠ»ΠΎΡΡ ΠΏΡΠΈΠΌΠ΅ΡΠ½ΠΎ ΠΏΠΎΠ»ΠΎΠ²ΠΈΠ½Π° ΠΎΡ ΠΎΠ±ΡΠ΅ΠΉ Π΄ΠΎΠ»ΠΈ ΠΏΠΎ ΠΎΠ±ΡΠ΅ΠΌΡ.
ΠΠΎΡΡΡΠΏ ΠΊ ΠΏΠΎΠ»Π½ΠΎΠΉ ΡΠ²ΠΎΠ΄ΠΊΠ΅ ΠΏΠΎ : https: // www.alliedmarketresearch.com/foam-blowing-agents-market
Π ΠΎΡΡ ΡΠΏΡΠΎΡΠ° Π½Π° ΠΏΠ΅Π½ΠΎΠΏΠΎΠ»ΠΈΡΡΠ΅ΡΠ°Π½, ΡΠ»ΡΡΡΠ΅Π½ΠΈΠ΅ ΠΈΠ·ΠΎΠ»ΡΡΠΈΠΎΠ½Π½ΡΡ ΡΠ²ΠΎΠΉΡΡΠ² ΠΏΠ΅Π½ ΠΈ ΡΠ΅Ρ Π½ΠΎΠ»ΠΎΠ³ΠΈΡΠ΅ΡΠΊΠΈΠ΅ Π΄ΠΎΡΡΠΈΠΆΠ΅Π½ΠΈΡ ΡΠ²Π»ΡΡΡΡΡ ΠΎΡΠ½ΠΎΠ²Π½ΡΠΌΠΈ ΡΠ°ΠΊΡΠΎΡΠ°ΠΌΠΈ, ΡΠΏΠΎΡΠΎΠ±ΡΡΠ²ΡΡΡΠΈΠΌΠΈ ΡΠΎΡΡΡ ΠΌΠΈΡΠΎΠ²ΠΎΠ³ΠΎ ΡΡΠ½ΠΊΠ° Π²ΡΠΏΠ΅Π½ΠΈΠ²Π°ΡΡΠΈΡ Π°Π³Π΅Π½ΡΠΎΠ². Π ΠΎΡΡ ΡΡΡΠΎΠΈΡΠ΅Π»ΡΡΡΠ²Π° ΡΡΠΈΠΌΡΠ»ΠΈΡΠΎΠ²Π°Π» ΡΠΏΡΠΎΡ Π½Π° ΠΏΠ΅Π½ΠΎΠΏΠΎΠ»ΠΈΡΡΠ΅ΡΠ°Π½, ΠΈΡΠΏΠΎΠ»ΡΠ·ΡΠ΅ΠΌΡΠΉ Π΄Π»Ρ ΠΈΠ·ΠΎΠ»ΡΡΠΈΠΈ ΠΊΡΡΡ ΠΈ Π·Π΄Π°Π½ΠΈΠΉ. ΠΡΠΎΠΌΠ΅ ΡΠΎΠ³ΠΎ, ΠΎΠΆΠΈΠ΄Π°Π΅ΡΡΡ, ΡΡΠΎ ΡΠΏΡΠΎΡ Π½Π° Π²ΡΡΠΎΠΊΠΎΡΡΡΠ΅ΠΊΡΠΈΠ²Π½ΡΠ΅ ΠΏΠΎΠ»ΠΈΠΌΠ΅ΡΠ½ΡΠ΅ ΠΏΠ΅Π½Ρ Π² ΡΡΡΠΎΠΈΡΠ΅Π»ΡΠ½ΠΎΠΌ ΡΠ΅ΠΊΡΠΎΡΠ΅ ΡΠ²Π΅Π»ΠΈΡΠΈΡ ΡΠΏΡΠΎΡ Π½Π° Π²ΡΠΏΠ΅Π½ΠΈΠ²Π°ΡΡΠΈΠ΅ Π°Π³Π΅Π½ΡΡ.ΠΠΆΠΈΠ΄Π°Π΅ΡΡΡ, ΡΡΠΎ ΡΠΏΡΠΎΡ Π½Π° ΠΏΠΎΠ»ΠΈΡΡΠΈΡΠΎΠ» Π·Π½Π°ΡΠΈΡΠ΅Π»ΡΠ½ΠΎ Π²ΡΡΠ°ΡΡΠ΅Ρ ΠΈΠ·-Π·Π° Π΅Π³ΠΎ ΠΏΡΠΈΠΌΠ΅Π½Π΅Π½ΠΈΡ Π² ΡΠΏΠ°ΠΊΠΎΠ²ΠΊΠ΅ ΠΈ ΡΠ»Π΅ΠΊΡΡΠΎΠ½ΠΈΠΊΠ΅. ΠΡΠΎΠ³Π½ΠΎΠ·ΠΈΡΡΠ΅ΡΡΡ, ΡΡΠΎ ΠΠ·ΠΈΠ°ΡΡΠΊΠΎ-Π’ΠΈΡ ΠΎΠΎΠΊΠ΅Π°Π½ΡΠΊΠΈΠΉ ΡΠ΅Π³ΠΈΠΎΠ½ ΠΎΡΡΠ°Π½Π΅ΡΡΡ Π΄ΠΎΠΌΠΈΠ½ΠΈΡΡΡΡΠΈΠΌ ΡΠ΅Π³ΠΈΠΎΠ½ΠΎΠΌ Π² ΠΌΠΈΡΠ΅, Π·Π° Π½ΠΈΠΌ ΠΏΠΎΡΠ»Π΅Π΄ΡΡΡ Π‘Π΅Π²Π΅ΡΠ½Π°Ρ ΠΠΌΠ΅ΡΠΈΠΊΠ° ΠΈ ΠΠ²ΡΠΎΠΏΠ°.
Π‘ΡΡΠΎΠ³ΠΈΠ΅ ΡΠΊΠΎΠ»ΠΎΠ³ΠΈΡΠ΅ΡΠΊΠΈΠ΅ Π½ΠΎΡΠΌΡ, Π·Π°ΠΏΡΠ΅ΡΠ°ΡΡΠΈΠ΅ ΠΈΡΠΏΠΎΠ»ΡΠ·ΠΎΠ²Π°Π½ΠΈΠ΅ Π²ΡΠ΅Π΄Π½ΡΡ ΠΏΠ΅Π½ΠΎΠΎΠ±ΡΠ°Π·ΠΎΠ²Π°ΡΠ΅Π»Π΅ΠΉ Π½Π° ΠΎΡΠ½ΠΎΠ²Π΅ F, ΡΠ²Π΅Π»ΠΈΡΠΈΠ»ΠΈ ΡΠΏΡΠΎΡ Π½Π° ΡΠ΅Π½ΡΠ°Π±Π΅Π»ΡΠ½ΡΠ΅, ΡΠ½Π΅ΡΠ³ΠΎΡΡΡΠ΅ΠΊΡΠΈΠ²Π½ΡΠ΅ ΠΈ ΡΠΊΠΎΠ»ΠΎΠ³ΠΈΡΠ½ΡΠ΅ ΠΏΠ΅Π½ΠΎΠΎΠ±ΡΠ°Π·ΠΎΠ²Π°ΡΠ΅Π»ΠΈ. Π 2015 Π³ΠΎΠ΄Ρ Π½Π° ΡΠ³Π»Π΅Π²ΠΎΠ΄ΠΎΡΠΎΠ΄Ρ Π±ΡΠ» Π·Π°ΡΠΈΠΊΡΠΈΡΠΎΠ²Π°Π½ ΠΌΠ°ΠΊΡΠΈΠΌΠ°Π»ΡΠ½ΡΠΉ ΡΠΏΡΠΎΡ Π½Π° ΡΡΠ½ΠΊΠ΅ Π±Π»Π°Π³ΠΎΠ΄Π°ΡΡ ΠΈΡ ΠΏΡΠΈΠΌΠ΅Π½Π΅Π½ΠΈΡ Π² Ρ ΠΎΠ»ΠΎΠ΄ΠΈΠ»ΡΠ½ΠΎΠΌ ΠΎΠ±ΠΎΡΡΠ΄ΠΎΠ²Π°Π½ΠΈΠΈ, ΠΎΠ±ΡΠΈΠ²ΠΊΠ΅ ΡΡΠ΅Π½ ΠΈ ΠΊΡΠΎΠ²Π»Π΅, Π·Π° ΠΊΠΎΡΠΎΡΡΠΌΠΈ ΠΏΠΎΡΠ»Π΅Π΄ΠΎΠ²Π°Π»ΠΈ Π³ΠΈΠ΄ΡΠΎΡΡΠΎΡΡΠ³Π»Π΅ΡΠΎΠ΄Ρ.
Π ΡΠ½ΠΎΠΊ ΠΏΠ΅Π½ΠΎΠΎΠ±ΡΠ°Π·ΠΎΠ²Π°ΡΠ΅Π»Π΅ΠΉ ΠΡΠ½ΠΎΠ²Π½ΡΠ΅ ΡΠ΅Π·ΡΠ»ΡΡΠ°ΡΡ:
- Π 2015 Π³ΠΎΠ΄Ρ ΡΠ³Π»Π΅Π²ΠΎΠ΄ΠΎΡΠΎΠ΄Ρ ΡΠΎΡΡΠ°Π²ΠΈΠ»ΠΈ ΠΏΡΠΈΠΌΠ΅ΡΠ½ΠΎ Π΄Π²Π΅ ΠΏΡΡΡΡ ΠΎΠ±ΡΠ΅ΠΉ Π΄ΠΎΠ»ΠΈ Π²ΡΡΡΡΠΊΠΈ.
- ΠΠΆΠΈΠ΄Π°Π΅ΡΡΡ, ΡΡΠΎ ΡΡΠ΅Π΄Π½Π΅Π³ΠΎΠ΄ΠΎΠ²ΠΎΠΉ ΡΠ΅ΠΌΠΏ ΡΠΎΡΡΠ° Π²ΡΡΡΡΠΊΠΈ ΡΠ³Π»Π΅Π²ΠΎΠ΄ΠΎΡΠΎΠ΄Π½ΠΎΠ³ΠΎ ΡΠ΅Π³ΠΌΠ΅Π½ΡΠ° Π½Π° ΡΡΠ½ΠΊΠ΅ ΠΏΠ΅Π½ΠΎΠΎΠ±ΡΠ°Π·ΠΎΠ²Π°ΡΠ΅Π»Π΅ΠΉ ΡΠΎΡΡΠ°Π²ΠΈΡ 5,37% Ρ 2016 ΠΏΠΎ 2022 Π³ΠΎΠ΄.
- ΠΠΆΠΈΠ΄Π°Π΅ΡΡΡ, ΡΡΠΎ ΡΡΠ΅Π΄Π½Π΅Π³ΠΎΠ΄ΠΎΠ²ΠΎΠΉ ΡΠ΅ΠΌΠΏ ΡΠΎΡΡΠ° ΠΎΠ±ΡΠ΅ΠΌΠΎΠ² ΡΡΠΎΡΡΠ³Π»Π΅ΡΠΎΠ΄ΠΎΠ² Π½Π° ΡΡΠ½ΠΊΠ΅ Π²ΡΠΏΠ΅Π½ΠΈΠ²Π°ΡΡΠΈΡ Π°Π³Π΅Π½ΡΠΎΠ² ΡΠΎΡΡΠ°Π²ΠΈΡ 6,24% Π² 2016-2022 Π³ΠΎΠ΄Π°Ρ .
- ΠΡΠ΅Π΄ΠΏΠΎΠ»Π°Π³Π°Π΅ΡΡΡ, ΡΡΠΎ ΠΠ·ΠΈΠ°ΡΡΠΊΠΎ-Π’ΠΈΡ ΠΎΠΎΠΊΠ΅Π°Π½ΡΠΊΠΈΠΉ ΡΠ΅Π³ΠΈΠΎΠ½ ΡΡΠ°Π½Π΅Ρ ΡΠ°ΠΌΡΠΌ Π±ΡΡΡΡΠΎΡΠ°ΡΡΡΡΠΈΠΌ ΡΠ΅Π³ΠΈΠΎΠ½ΠΎΠΌ Π΄Π»Ρ ΡΠ΅Π³ΠΌΠ΅Π½ΡΠ° ΠΏΠΎΠ»ΠΈΡΡΠ΅ΡΠ°Π½Π° Π½Π° ΡΡΠ½ΠΊΠ΅ Π²ΡΠΏΠ΅Π½ΠΈΠ²Π°ΡΡΠΈΡ Π°Π³Π΅Π½ΡΠΎΠ².
- ΠΠ° Π΄ΠΎΠ»Ρ Π‘Π΅Π²Π΅ΡΠ½ΠΎΠΉ ΠΠΌΠ΅ΡΠΈΠΊΠΈ ΠΏΡΠΈΡ ΠΎΠ΄ΠΈΠ»Π°ΡΡ ΠΏΡΠΈΠΌΠ΅ΡΠ½ΠΎ ΡΠ΅ΡΠ²Π΅ΡΡΠ°Ρ ΡΠ°ΡΡΡ Π²ΡΡΡΡΠΊΠΈ Π² 2015 Π³ΠΎΠ΄Ρ.
ΠΠ½Π²Π΅ΡΡΠΈΡΠΈΠΈ ΡΡΠ°Π½ΡΠ½Π°ΡΠΈΠΎΠ½Π°Π»ΡΠ½ΡΡ ΠΊΠΎΠΌΠΏΠ°Π½ΠΈΠΉ ΠΈ Π½ΠΈΠ·ΠΊΠΈΠ΅ Π·Π°ΡΡΠ°ΡΡ Π½Π° ΡΠ°Π·ΡΠ°Π±ΠΎΡΠΊΡ Π² ΠΠΈΡΠ°Π΅ ΠΈ ΠΠ½Π΄ΠΈΠΈ ΡΠΏΠΎΡΠΎΠ±ΡΡΠ²ΠΎΠ²Π°Π»ΠΈ ΡΠΎΡΡΡ ΡΡΠ½ΠΊΠ° Π²ΡΠΏΠ΅Π½ΠΈΠ²Π°ΡΡΠΈΡ Π°Π³Π΅Π½ΡΠΎΠ². ΠΡΠΎΠΌΠ΅ ΡΠΎΠ³ΠΎ, ΠΠΈΡΠ°ΠΉ ΠΈΠΌΠ΅Π΅Ρ ΠΊΡΡΠΏΠ½Π΅ΠΉΡΠΈΠΉ ΡΡΠ½ΠΎΠΊ Π²ΡΠΏΠ΅Π½ΠΈΠ²Π°ΡΡΠΈΡ Π°Π³Π΅Π½ΡΠΎΠ² Π² ΠΠ·ΠΈΠ°ΡΡΠΊΠΎ-Π’ΠΈΡ ΠΎΠΎΠΊΠ΅Π°Π½ΡΠΊΠΎΠΌ ΡΠ΅Π³ΠΈΠΎΠ½Π΅, Π·Π° Π½ΠΈΠΌ ΡΠ»Π΅Π΄ΡΠ΅Ρ ΠΠ½Π΄ΠΈΡ ΠΈΠ·-Π·Π° ΡΠ²Π΅Π»ΠΈΡΠ΅Π½ΠΈΡ ΡΠΏΡΠΎΡΠ° Π½Π° ΠΏΠ΅Π½ΠΎΠΏΠΎΠ»ΠΈΡΡΠ΅ΡΠ°Π½Ρ Π² ΡΡΡΠΎΠΈΡΠ΅Π»ΡΠ½ΠΎΠΉ ΠΈ Π°Π²ΡΠΎΠΌΠΎΠ±ΠΈΠ»ΡΠ½ΠΎΠΉ ΠΏΡΠΎΠΌΡΡΠ»Π΅Π½Π½ΠΎΡΡΠΈ.
ΠΠΈΠ΄Π½ΡΠΌΠΈ ΠΈΠ³ΡΠΎΠΊΠ°ΠΌΠΈ Π½Π° ΡΡΠΎΠΌ ΡΡΠ½ΠΊΠ΅ ΡΠ²Π»ΡΡΡΡΡ Arkema S.A. (Π€ΡΠ°Π½ΡΠΈΡ), Honeywell International Inc. (Π‘Π¨Π), Exxon Mobil Corporation (Π‘Π¨Π), E.I. du Pont de Nemours & Company (Π‘Π¨Π), Haltermann GmbH (ΠΠ΅ΡΠΌΠ°Π½ΠΈΡ), Harp International Ltd. (ΠΠ΅Π»ΠΈΠΊΠΎΠ±ΡΠΈΡΠ°Π½ΠΈΡ), Daikin Industries, Ltd. (Π―ΠΏΠΎΠ½ΠΈΡ), Sinochem Group (ΠΠΈΡΠ°ΠΉ), Solvay S.A. (ΠΠ΅ΡΠΌΠ°Π½ΠΈΡ ΠΈ ZEON Corporation.
) ,