Технология производства пенополистирола из вспенивающегося полистирола.
Технология производства пенополистирола из вспенивающегося полистирола
1. Физико-химическая последовательность процесса.
Процесс производства пенопласта из вспенивающегося полистирола складывается из четырех
последовательных технологических операций.
А. Первоначального производства гранул из вспенивающегося полистирола
Б. Выдержки по времени вспененных гранул из вспенивающегося полистирола
В. Формирование блоков из вспенивающегося полистирола
Г. Сушка и выдержка по времени блоков из вспенивающегося полистирола.
А. Процесс производства гранул, происходящий во вспенивателе с помощью водяного пара, происходит при температуре 80-100 градусов Цельсия. Благодаря содержащемуся в гранулах порофору (обычно пентан, изопентан или пентан-изопентановая фракция), повышенной температуре и расширению водяного пара, гранулы многократно увеличивают свой объем и принимают микроячеистую структуру.
Б. Во время выдержки по времени вспененных гранул из полистирола происходит процесс диффузии воздуха вовнутрь микро ячеек и выравнивание давления внутри ячеек и атмосферным давлением.
В. Процесс формирования блоков из вспенивающегося полистирола, происходящий в закрытых формах, заключается в нагревании водяным паром вспененных и выдержанных гранул. Благодаря повышению температуры, а также заключенному в порах гранул порофору, воздуху и водяному пару, наступает дальнейшее расширение объема гранул и их взаимное слипание, приводящее к возникновению монолитного блока из пенополистирола. После охлаждения блока в форме наступает ее разъединение.
Г. Процесс выдержки по времени блоков из пенополистирола заключается в двусторонней диффузии воздуха внутрь микропор, и выравнивание давления между внутренним объемом ячеек и атмосферой. Сушка блоков заключается в выпаривании поверхностной влаги в атмосферу.
2. Сырье
Сырьем для производства блоков из пенополистирола являются гранулы полистирола, содержащие порофор. В состав порофора входят низкокипящие углеводороды – изопентан, пентан и другие.
2.2 Физико-химические свойства и требования к качеству сырья
Гранулы полистирола, предназначенные для производства блоков и плит, должны иметь вид круглых шариков белого или полупрозрачного цвета. Допускается наличие серповидных и рисообразных гранул полистирола.
Требования к гранулам
Требования | Значение |
Удельная плотность собственно гранул, г/см3 | 1.03-1.05 |
Удельная плотность гранул надіп’ю, г/см3 | Около 0,6 |
Содержание мономера стирола, %, не более | 1,2 |
Вязкость 1% раствора бензина в кПа | 1,0-1,3 |
Максимальное содержание влаги, % | 5,0 |
Просев – максимальный остаток на сите с квадратным сечением | 4,0 |
2.3. Доставка и хранение сырья.
2.3.1. Требования к доставке сырья
Сырье доставляется в виде упаковок в закрытых средствах доставки – железнодорожным или
автомобильным транспортом. Разгрузка производится на разгрузочной рампе и сырьё доставляется на закрытый склад. Контроль за количественными характеристиками доставленного сырья производится лабораторным отделом.
Контроль должен производиться следующим образом:
а) Контроль содержания влажности в гранулах
б) Определение содержания мономера в гранулах
в) Определение вязкости гранул в 1% бензиновом растворе
г) Пробное вспенивание гранул
д) Определение удельного веса вспененных гранул
е) Анализ остатка на сите
ж) Пробное формование вспененных гранул
Могут быть выполнены дополнительные испытания качества в соответствии с методикой аттестации сырья, поданной производителем или методикой, принятой в стране.
Сырье храниться на складе. Температура в складском помещении не должна превышать 25-ти градусов Цельсия. Упаковки должны храниться на деревянных поддонах с высотой штабеля не более 3 м. Металлические бочки складировать в высоту не более 1-3. В складе надлежит обеспечить хорошую вентиляцию.
3. Характеристика источников энергии
3.1. Водяной пар
Процесс производства пенопласта из вспенивающегося полистирола требует доставки тепла как
средства энергии нагрева для первичного процесса вспенивания, процесса формирования блоков, а также нагревания воздуха сушилки и пневматического транспортирования вспененного сырья. После проведения эксперимента с другими формами энергии, мы пришли к выводу, что наиболее практичный источник энергии – это водяной пар.
Водяной пар, применяемый для преобразования пенополистирола, должен быть насыщенным паром при давлении как минимум 0,25 мПа, не перенасыщенным водой. Оптимальное давление для формирования блоков и последующего вспенивания составляет 0,02-0,07 мПа.
Более высокое давление приводит к увеличению скорости поступления пара в форму (время
3.2. Электроэнергия
Электроэнергия применяется для приведения в действие вспенивателя, форм, оснащения для
разрезания блоков, пневмотранспорта и установленного освещения.
Электроэнергия поставляется от промышленных источников питания при напряжении 380 или 220 В переменного тока. Контроль и изоляция токонесущих частей производится в соответствии с требованиями службы электробезопасности предприятия.
3.3. Сжатый воздух
Сжатый воздух предназначен для приведения в действие пневматических устройств: закрывания и
открывания форм, а также выталкивания сформированных блоков. Давление сжатого воздуха от источника должно составлять не менее 5 атмосфер. Полученный сжатый воздух проходит через нагревательный элемент и распределяется при помощи системы трубопроводов. Контроль и обслуживание частей системы подачи сжатого воздуха производит служба энергобезопасности предприятия.
4. Характеристика полуфабриката
Полуфабрикатом для производства блоков из вспенивающегося полистирола являются вспененные гранулы. Они получаются на этапе вспенивания и после высушивания подаются для формирования блоков.
4.1. Физико-химические свойства
Требования | Значение | Место проведения контроля |
Удельный вес насыпью в гр./1 | 15-20 | Обслуживающая лаборатория |
Максимальный диаметр гранул в мм | 20 |
|
Минимальный диаметр гранул в мм | 0,7 |
|
Максимальное время выдержки по времени от момента вспенивания | 5 | Персонал, обслуживающий бункеры накопления |
Максимальное время выдержки по времени от момента вспенивания | 8 | Персонал, обслуживающий бункеры накопления |
Наличие агломератов размером более 4 см (вспененных | не допускается | Персонал, обслуживающий вспениватели |
Максимальное количество выкрошившихся отходов в % | 5 | Персонал, обслуживающий бункеры накопления |
4.2. Доставка и складирование
Вспененные гранулы подаются при помощи пневмотранспорта в бункеры накопления, в которых
происходит их выдержка по времени. Температура при выдержке гранул составляет 25-30°С. Время выдержки гранул составляет от 8 часов до 5 суток. Выдержанные гранулы вместе с крошкой отходов пневмотранспортом поступают в дозаторы, находящиеся над формами.
5. Характеристика продукта
Готовым продуктом являются блоки из пенополистирола. Далее их режут на плиты по размерам,
зависящим от требований заказчика, что является уже только преобразованием готового изделия, не изменяющим его свойства.
5.1. Физико-химические свойства блоков из пенополистирола
Требования | Значения |
Удельный вес, кг/м3 | 15-20 |
Сопротивление сжатию, при деформации пробки на 10%, более кг/ | 0,4 |
Термостойкость, более, °С | 60 |
Сопротивление пропусканию тепла, в ккал/м °С в час | 0,035 |
Отсутствие разбухания в воде в течение 24 часов, менее, в % | 1,5 |
Гигроскопичность в течение 120 часов, менее, в % | 0,6 |
Размеры | Соответствуют требованиям заказчика |
6. Отходы
Максимальное количество отходов, образующихся в цикле производства изделий вспенивающегося полистирола, составляет не более 6,5%. Отходы складываются из выбракованных блоков, получающихся во время формирования и крошки, образующейся при разрезании блоков на плиты.
Отходы размельчаются в дробилке (мельнице) и в качестве крошки отходов возвращаются в
производство. Крошка в смеси с выдержанными гранулами применяется для повторного производства блоков. Максимальное количество крошки при производстве и формировании блоков не должно превышать 5%.
7. Описание технологического процесса
7.1. Общее описание процесса
7.1.1. Процесс вспенивания гранул
Первой технологической операцией по производству изделий из вспенивающегося полистирола является вспенивание гранул. Процесс вспенивания происходит благодаря расширению пор гранул. Во время вспенивания, производимого во вспенивателе насыщенным водяным паром при температуре 90-100°С, в структуре полистирола образуются микропоры. Водяной пар, подающийся во вспениватель, играет двойную роль – нагревателя и дополнительной причины вспенивания (благодаря быстрой диффузии через стенки микропор), и приводит к многократному увеличению (до 50 раз) объема гранул. Во время вспенивания гранулы размешиваются с помощью механического размешивателя с целью избегания их слипания. Водяной пар подается по системе трубопроводов, подключенной к задней части вспенивателя. Во вспенивателе гранулы размешиваются вертикальным размешивателем, состоящим из системы лопастей, предотвращающих слипание гранул. Расширенные гранулы перемещаются к горловине вспенивателя и высыпаются через засыпное отверстие, размещенное в верхней части стенки вспенивателя.
Из вспенивателя гранулы полистирола выпадают в сушилку. Поток теплого воздуха высушивает их и выдувает к горловине инжектора системы пневмотранспорта, которая доставляет гранулы в бункер.
Сушилка и система пневмотранспорта обеспечиваются теплым воздухом (более 50°С) путем нагнетания вентиляторами и нагрева паром.
В целях обеспечения возможности регулирования количества поданных гранул, предусмотрена
регулировка количества оборотов червячного дозатора, давления подводимого водяного пара.
Определение количества подаваемых гранул возложено на персонал, обслуживающий вспениватели, которые наблюдают за внешним видом гранул. Контрольно-измерительное оснащение вспенивателя состоит из регулирующих вентилей и контрольного манометра измерения давления водяного пара на линии подачи пара во вспениватель, а также весов для определения веса насыпанных вспененных гранул.
Остановка вспенивателя Каждый раз при остановке вспенивателя необходимо выполнить следующие операции:
- Остановка червячного дозатора.
- Отключение подачи пара.
- Отключение механического размешивателя по остывании.
- Опорожнение вспенивателя от вспененных гранул.
Аварийная остановка вспенивателя (отключение электроэнергии, остановка размешивателя) Требует отключения подачи пара и включение сжатого воздуха для остужения гранул. Несоблюдение этих правил приводит к дальнейшему вспениванию гранул и выходу из строя привода вспенивателя. Возобновление работы при аварийной остановке может наступить после ее опорожнения от находящихся внутри гранул и осмотра вспенивателя.
7.1.2. Выдержка гранул по времени
Опорожняющая часть пневматического транспорта направляет гранулы в бункеры. В бункерах происходит процесс выдержки по времени вспененных гранул. Это простая технологическая операция, имеющая, однако, большое значение для дальнейшего производства и влияющая на качество сформованных изделий. Во время выдержки по времени вспененных гранул в бункерах со свободно поступающим воздухом происходит процесс диффузии воздуха внутрь гранул и выравнивания разницы давления между внутренностью гранул и атмосферой. Длительность процесса в зависимости от количества насыпанных гранул, их размера, температуры воздуха колеблется от нескольких до нескольких десятков часов. Общепризнанным является оптимальное время выдержки в течение 8 часов при комнатной температуре. Время выдержки гранул не следует продлевать более недели вследствие потери пор и ухудшения качества изготовленных изделий из передержанных гранул. В целях уверенности, что температура выдерживания гранул, которая должна соответствовать 22-28°С, в помещении, в котором находятся бункеры, устанавливается нагревательная аппаратура, а для контроля служит настенный термометр. В целях обеспечения выдерживания по времени следует производить записи в соответствующих журналах и опорожнение выполнять в соответствии с табличками на бункерах. Выборка гранул производится из нижней части бункеров в систему пневматического трубопровода по трубам и с помощью потока воздуха транспортируется в соответствующие приспособления над формами. Заполнение приспособлений производится периодически, каждый раз после опорожнения. Из приспособлений вспененные гранулы поступают в формы.
7.1.3. Формирование блоков из вспенивающегося полистирола
Формирование блоков из пенополистирола является наиболее важной операцией в цикле производства изделий из пенопласта. Во время этой операции засыпанные в формы вспененные гранулы дополнительно обрабатываются и слипаются между собой, образуя изделие в соответствие с заданной формой, в которой они находятся.
Смыслом этой операции является нагревание гранул, которое приводит к эффекту дальнейшего
увеличения их объема. Увеличение объема в замкнутом пространстве формы совместно с повышенной температурой материала приводит к слипанию гранул между собой и заполнению всего объема формы.
Применяемый метод производства требует использования насыщенного водяного пара как источника энергии. Водяной пар в процессе формирования, так как и при операции вспенивания, также играет роль образователя пор.
Существенным элементом цикла является его начальная фаза — это устранение воздуха, имеющегося в свободном пространстве между гранулами и стенками формы. Это производится выдуванием его струей водяного пара.
Но и дополнительная роль водяного пара в процессе формирования чрезвычайно важна. Наличие воздуха снижает скорость нагрева гранул и приводит к ухудшению качества их слипания (так называемое рассыпании блоков) или приводит к образованию в форме свободных пустот, не заполненных гранулами, так называемых каверн.
Конечной операцией цикла формирования является охлаждение сформированных блоков. От этой, как кажется, простой операции очень сильно зависит качество блоков, а также удачность цикла
формования.
Цикл формования блока состоит из следующих операций:
А. Нагревание формы. Перед наполнением формы гранулами надлежит ее нагреть до температуры 80-90°С (при более высоких температурах гранулы будут слипаться сами по себе по мере их засыпания до подачи водяного пара). Во время нагревания форма должна быть закрыта, а конденсат и избыток поступающего пара должен быть направлен выделенным трубопроводом из здания. Нагревание формы имеет конечной целью избежание увлажнения гранул конденсатом, остающимся на холодной поверхности стенок формы. Поступающий на последующих этапах формирования пар должен только дополнительно нагревать стенки формы.
Б. Смазывание поверхности формы. Производится с помощью впрыскивания на внутреннюю поверхность формы раствора мыла или другого средства с целью обеспечения свободного отлипания сформированного блока от формы. Операции можно избежать, если гладкие внутренние стенки форм позволяют лёгкую выемку сформированного блока.
В. Наполнение формы. Подготовленная в соответствии с пунктами А и Б форма заполняется гранулами через сборник под давлением. Наполнение формы должно быть полным для обеспечения соответствующего качества изделия.
Г. Продувание формы водяным паром. После заполнения формы и ее закрывания с помощью пневматического привода и герметичным замыканием – контрольная лампочка на пульте управления, водяной пар подается в верхние и боковые части стенок формы и выводится (вначале как смесь воздуха и водяного пара) через камеру в нижней части формы в коллектор конденсата и водяного пара при открыто находящемся там вентиле. Давление пара в камерах во время операции должно составлять 0,03-0,05 мПа, время продувки 10-20 сек.
Применение более длительного срока продувки нежелательно, так как приводит к ухудшению слипания гранул между собой во внешней и нижней частях формы, а наоборот, сокращение времени продувки приводит к остатку воздуха в форме и образованию пустот.
Д. Собственно формирование. После проведения продувки, закрывается вентиль отвода пара и
конденсата, а также проводятся дальнейшие операции по формованию. В это время возрастает давление пара в форме до 0,04-0,06 мПа, в том числе и в свободном пространстве между гранулами. Возрастание давления должно достигнуть максимального значения и контролироваться с помощью манометров.
Во время формования гранулы разогреваются, дополнительно вспениваются и вспененные полностью занимают объем формы. Находящийся там пар проникает через стенки гранул и приводит к слипанию гранул между собой. Время формования блоков составляет 8-12 секунд.
Е. Выемка сформованных блоков. Сформированные блоки выталкиваются из формы при помощи установленного выталкивателя. Для исправного выполнения этой операции необходимо устранение причин прилипания гранул к стенкам формы, которое достигается путем нанесения средств против прилипания перед загрузкой форм. По мере эксплуатации наступает пассивность по отношению к прилипанию стенок форм и в дальнейшем можно избегать смазки.
Контрольно-измерительная аппаратура форм размещена на пульте управления. Кроме того, на линии подачи пара имеется регулирующий вентиль и манометр, а также вентиль на коллекторе конденсатора и отвода из формы. Во время приостановки работы следует прекратить подачу пара, а также сжатого воздуха и электроэнергии. Время пребывания сформованного блока в форме зависит от сырья и составляет 10-30 минут.
7.1.4. Выдержка блоков по времени
Конечно, технологической операцией является выдержка сформованных блоков по времени, когда наступает проникновение воздуха в блоки, а также его сушение. Выдержку и сушение блоков следует производить при температуре 22-30°С в течение 8 часов.
7.1.5. Разрезание блоков на плиты
Последним действием, которое производится над блоками, является процесс их преобразования в плиты. Он заключается в разрезании блоков при помощи разделительного провода. Разрезанию следует подвергать блоки, выдержанные по времени и высушенные. Разрезание блоков разогретым проводом возможно благодаря тому, что температура разогрева провода выше температуры плавления пенопласта и оставляет за собой литую поверхность, благодаря чему усиливается значение упругости материала. Разрезание блоков на плиты производится на оснащении, состоящем из подвижного стола и стальной рамы с натянутыми проводами. Благодаря легкой системе регулировки расстояния между проводами можно регулировать толщину разрезанных плит в соответствии с требованиями заказчика. Разрезанные плиты из пенопласта измеряют в соответствии с требованиями, принятыми на производстве, упаковываются или доставляются навалом через склад заказчику.
8. Стоки и отходы
8.1. Технологические стоки
Стоки предназначены для стока пара, воды и конденсата из вспенивателей, форм и с места
расположения производственных мощностей. Единственная защита стока – это защита от механического занесения гранул.
8.2. Отходы
Отходы, образующиеся в процессе производства блоков, а также механического разрезания блоков на плиты вместе с гранулами, рассыпанными во время транспортировки пневмотранспортом, возвращаются в процесс производства. Количество отходов, образующихся на различных этапах производства не должно превышать 6,5% и это значение составляет разницу между нетто произведенным и брутто примененным. 8.3. Испаряемые газы
Образующиеся в процессе производства газы составляют пар и пентан. Наибольшее количество пентана находится в отводах из впенивателей. Выхлоп убирается вытяжной вентиляцией в атмосферу, где он становится безопасным. На рабочих местах, где установлены вспениватели и имеется максимальная концентрация выхлопа, установленное оборудование должно обеспечивать достаточный отвод газов.
Вытяжное вентиляционное оборудование обеспечивает многократную замену воздуха в помещении и не допускает концентрацию пентана, угрожающую пожаром или взрывом.
9. Безопасность и гигиена труда
На всех стадиях производства пенополистирол не является токсичным и нет необходимости применять средства для вредного производства.
В производственных помещениях, в которых имеется повышенная влажность (помещения вспенивателей и форм), пол следует выложить деревянным паркетом. Каждое место следует обеспечить общей инструкцией обслуживания, в которой определяется способ работы и соответствующие предписания, утвержденные службой безопасности труда, работы в соответствии с технологической инструкцией работы на данном оборудовании. Персонал к работе может быть допущен только после ознакомления с правилами технологии, эксплуатации, обслуживания и безопасности труда на данном оборудовании.
Во время эксплуатации следует обратить внимание на следующие вопросы:
А. Оснащение рабочих мест общей инструкцией по обслуживанию
Б. Подключить систему сигнализации и защиты от возрастания давления пара
В. Проводить обслуживание системы трубопроводов пара и воздуха под давлением
Г. Во время подачи пара в формы находиться за пультом управления за защитным экраном
Д. Проверять состояние пневмотранспорта
Е. Запретить курение в производственных и складских помещениях
Ж. Проверять состояние вытяжного оборудования
З. Не блокировать путей транспортирования и двери
Во всех помещениях следует поместить надписи о запрещении курения, гашения пожара водой
оборудования под напряжением, оборудовать помещения средствами пожаротушения.
Во время ремонтных работ в качестве местного освещения применять лампы с напряжением 24В.
10. Обеспечение пожарной безопасности
Объект производства относится к третьей категории объектов по пожарной безопасности. Здание
относится к классу «С», причем помещение склада сырья должно быть класса «А» и иметь огнеупорные двери.
Все помещения должны быть оборудованы гидрантами. Кроме того, все помещения должны быть
обеспечены средствами пожарного тушения в количестве не менее: углекислотные огнетушители (по два в каждом помещении), 2 углекислотных агрегата тушения (в помещении бункеров и выдержки блоков), 2 асбестовых тента (по 2 в каждом помещении).
11. Процесс двойного вспенивания гранул из пенополистирола.
Процесс двойного вспенивания гранул применяется для уменьшения расхода сырья, менее 14-15 кг/м3. Процесс заключается в том, что во время первого вспенивания, удельная плотность гранул насыпью находится в пределах 16-18 кг/м3, а после их высушивания проводится повторное вспенивание и удельный вес насыпью составляет 11-12 кг/м3. Гранулы после проведения процесса выдержки предназначаются для формирования изделий с плотностью 12-15 кг/м3. Процесс вспенивания можно проводить многократно и довести плотность до 5-7 кг/м3, однако формование изделий из таких интенсивно вспененных гранул затруднено, так как в них остается небольшое содержание порофора. Также изделия из него характеризуются невысокой стойкостью к механическим воздействиям, когда содержание полимера составляет 0,5-0,7 % от объема, а воздуха соответственно 99,3-99,5% объема. Процесс многократного вспенивания был запатентован еще в 1961 году.
11.1. Теоретическое обоснование процесса двукратного вспенивания.
Из кинетической кривой вспенивания следует, что процесс проходит интенсивно в течение первых 2-3 минут и масса насыпанных гранул уменьшается с 550 до 25-30 кг/м3 или в 18-22 раза, соответственно увеличивается объем, а при более долгом вспенивании процесс затормаживается, даже может иметь место увеличение плотности гранул. Это связано с потерей порофора при вспенивании. Во время нагревания гранул до температуры вспенивания (около 100°С) находящийся в них порофор-пентан (химическая формула С5Н12, температура кипения – 36,5°С) превращается в пар. Его утечка невелика и для поддержания равновесия давления гранулы расширяются. Основные потери происходят по причине увеличения объема, а главное времени вспенивания. В процессе многократного вспенивания гранул порофор разрежается воздухом, проникающим в гранулы в процессе выдержки.
Время двойного вспенивания почти совпадает со временем одинарного вспенивания, поэтому потери порофора одинаковы в обоих случаях.
Во всех случаях вспенивания существенна роль пара. Он является дополнительным источником
вспенивания. Благодаря сильной диффузии он проникает в образующиеся микропоры и приводит в соответствие давление в гранулах с внешним давлением.
11.2. Процесс двойного вспенивания.
Технологический процесс двойного вспенивания выглядит следующим образом: на первом этапе
вспенивания, проводящейся в атмосфере водяного пара, надлежит довести удельный вес гранул до 16-18 кг/м3. Условиями получения такой интенсивности вспенивания являются соответствующий подбор скорости их дозирования, времени пребывания во вспенивателе или температуры вспенивания посредством использования смеси пара и воздуха.
После первой стадии гранулы высушивают на месте в подвешенном состоянии при как можно более высокой температуре и выдерживают на месте. Расчеты по выдерживанию для 1 ступени: температура 15-25°С, время 3-8 часов. Высушенные гранулы повторно поступают во вспениватель и при помощи пара или смеси его с воздухом вспениваются до достижения удельного веса 11-12 кг/м3. Двукратно вспененные гранулы высушивают подобно 1 ступени и направляют в бункеры, в которых их выдерживают. Расчеты по выдерживанию для 2 ступени: температура 15-25°С, время 5-15 часов. После выдержки гранулы предназначаются для формирования блоков. Условия формирования блоков следует подбирать опытным путем, имея в виду повышенную деформируемость гранул при низком удельном весе на сжатие у сформированных блоков.
11.3. Технология процесса и оснащение
Первое вспенивание Во время этого этапа гранулы должны достичь удельного веса насыпью в пределах 16-18 кг/м3. Для этих целей необходимо подобрать определенные параметры вспенивания. Этого можно достичь посредством:
- уменьшения уровня засыпания во вспениватель, что приводит, однако, к уменьшению
производительности - уменьшение количества подаваемого пара во вспениватель и тем самым уменьшение температуры во вспенивателе
- применение смеси пара и воздуха
- сокращение времени пребывания гранул во вспенивателе посредством увеличения скорости
дозирования.
Последний вариант является наиболее приемлемым, потому что не уменьшает производительность вспенивателя. Чтобы количество подаваемого через шнек сырья стало меньше (при полном заполнении шнека) при максимальных оборотах надлежит увеличить количество оборотов шнека путем замены ременной передачи.
11.4. Сушение гранул после первого вспенивания
Процесс сушки проводится в существующих сушилках. Не требуется ее специальная доработка для двойного вспенивания.
11.5. Выдержка гранул после первого вспенивания
Несмотря на то, что гранулы после первого вспенивания имеют более высокий удельный вес, время выдержки гранул сокращается и составляет 3-8 часов. Как известно, время выдержки гранул меньшего диаметра меньше. Температуры выдержки составляют 15-25°С. 11.6. Второе вспенивание Процесс второго вспенивания проводится аналогично первому. Следует подобрать те же параметры:
- скорость дозирования
- температура во вспенивателе
Основными критериями оценки правильности работы вспенивателя является определяемый удельный вес гранул насыпью, а также отсутствие появления пыли по выходу из сушилки.
В случае появления пыли из гранул, надлежит уменьшить температуру вспенивания (уменьшить
количество подаваемого пара или обогатить смесь воздухом) или увеличить скорость прохождения гранул (дозирование) через вспениватель путем увеличения оборотов подающего червякового шнека.
Вспененные повторно гранулы, в связи с их малым удельным весом, более чувствительны к
механическим повреждениям во время их транспортировки. Поэтому следует уменьшить скорость
транспортировки путем изменения скорости работы вентилятора.
11.7. Выдержка гранул после второго вспенивания
Из сушилки через инжектор гранулы направляются в существующие бункеры, где происходит процесс диффузии воздуха в образовавшиеся микропоры. Оптимальное время выдержки после второй ступени вспенивания составляет несколько часов в зависимости от размера гранул. Температура выдержки должна составлять, как и во время первой выдержки, в пределах 15-25°С. Время выдержки при одинаковом удельном весе зависит от размера гранул.
11.8. Процесс формирования блоков
Процесс формирования блоков при двукратном вспенивании не сильно отличается от обычного
процесса. Также следует обеспечить продувку формы, наполненной гранулами.
Давление пара во время этой операции должно быть в пределах 0,1-0,2 атмосфер, а время продувки как можно меньшим, в границах нескольких секунд. Расчеты продувки и дальнейшая подача пара должны обеспечивать равномерное нагревание гранул во всем рабочем объеме формы.
Давление пара во время формования должно составлять 0,4-0,7 атмосфер в зависимости от качества гранул (удельного веса содержащегося полимера). Время формирования с учетом повышенной чувствительности к механическому воздействию не должно быть большим, потому что это приведет к осыпанию (появлению пыли) блоков, даже во время формирования и далее в процессе охлаждения.
Общее время воздействия пара должно составлять 15-40 секунд, время охлаждения 5-10 минут, в
зависимости от температуры формования, а также давления пара, конструкции формы и ее герметичности.
Данные должны определяться опытным путем с учетом качества сырья, а также удельного веса после второго вспенивания.
12. Описание и порядок эксплуатации вспенивателя, предназначенного для
ступенчатого вспенивания пенополистирола
12.1. Описание и порядок эксплуатации
Вспениватель следует устанавливать на твердой ровной поверхности и выравнивать по длине и ширине при помощи уровня. Первой технологической операцией является вспенивание гранул. Процесс вспенивания возможен благодаря порофору, который содержится в гранулах. Во время вспенивания, производимого при помощи водяного пара, подаваемого во вспениватель при температуре 90-100°С (давление пара 0,1 мПа) в монолите полистирола возникает микропористая структура. Водяной пар, подаваемый во вспениватель, играет двойную роль: основную – нагревание и дополнительную – источника вспенивания (благодаря высокой скорости диффузии через стенки микропор), приводит к многократному (до 50 раз) увеличению объема гранул. Во время вспенивания гранулы перемешиваются при помощи механической мешалки с целью предотвращения их слипания.
Водяной пар подается во вспениватель при помощи трубопровода к нижней его части. Во вспенивателе гранулы перемешиваются вертикальной мешалкой, состоящей из системы лопастей, предотвращающей слипание гранул. Увеличивающиеся в объеме гранулы перемещаются в верхнюю часть вспенивателя и опускаются через отверстие засыпания, размещенное в верхней части стенки вспенивателя.
Из вспенивателя гранулы полистирола выпадают в сушилку. Поток теплого воздуха высушивает их и выдувает в горловину (инжектор) пневмотранспорта, который доставляет их в бункеры.
Сушилка и транспортная часть приводится в действие теплым воздухом (более 50°С) при помощи
вентиляторов и обогревается паром.
В целях возможного регулирования производительности и насыпного веса гранул, вспениватель
имеет:
А. Возможность двукратного вспенивания,
Б. Регулировку скорости оборотов шнековых дозаторов.
Определение насыпного веса является обязанность обслуживающего персонала, который проводит внешний осмотр вспененных гранул. Контрольно-измерительное оборудование состоит из вентилей закрывания и манометра контрольного давления водяного пара на линии до вспенивателя, а также винта, регулирующего обороты червячной передачи.
12.2. Требования по безопасности труда
- вспениватель может обслуживаться только персоналом, ознакомленным с принципом его действия и устройством, а также с правилами безопасности труда
- обслуживающий персонал должен соблюдать общие правила безопасности труда, обязательные на предприятии
- рабочее место должно быть надлежащим образом освещено и быть чистым, а работник, обслуживающий вспениватель, должен работать в одежде и обуви, находящейся в надлежащем состоянии
- при манипуляциях с паровым вентилем руки должны быть одеты в рабочие рукавицы
Запрещается:
- открывание дверки главного сборника вспенивателя, а также выполнение внутреннего осмотра сборника во время работы мешалки
- включение двигателей привода при открытых защитных кожухах системы ременной передачи
- манипулирование рукой в контрольном лючке червячной передачи при работающем оборудовании.
12.3. Порядок работ перед началом работы вспенивателя
Перед началом работы вспенивателя необходимо выполнить следующие действия:
- Проверить герметичность системы подачи пара по трубопроводу при давлении 0,1 МПа.
- Убедится в правильности подключения к электросети.
- Проверить состояние защитного кожуха на ременной передаче.
- Мусор, попавший в главный сборник, может повредить мешалку и сетку.
- Мусор, попавший в сборник засыпания гранул, может повредить червячную передачу, подающую гранулы в главный сборник вспенивателя.
12.4. Обслуживание во время работ
- Тщательно закрыть дверки на главном сборнике вспенивателя.
- Осторожно открыть паровой вентиль и нагреть главный сборник в течение 10-15 минут.
- Наполнить главный сборник гранулами при помощи червячной передачи. Во время работы сборник (первая ступень вспенивания) должен заполняться автоматически.
3а. Для заполнения во второй ступени вспенивания наполнить бункер второй ступени вспенивания
гранулами, прошедшими через первую ступень при помощи червячной передачи большего диаметра. Бункер второй ступени заполняет себя при помощи вентилятора.
- Включить двигатель мешалки в главном сборнике.
- Включить червячную передачу, подающую гранулы в главный сборник.
- Включить пневмотранспорт, а также сушилку.
- Следить за текущей работой вспенивателя.
12.5. Обслуживание по окончании работ
- Выключить червячную передачу.
- Выключить червячную передачу по опорожнении засыпного сборника.
- Перекрыть подачу пара во вспениватель и подать сжатый воздух в целях охлаждения
сборника. - Выключить двигатель привода мешалки в главном сборнике по охлаждении (примерно через 60 минут).
- Выключить вентилятор, а также сушилку.
- Выключить подачу электроэнергии главным рубильником.
Каждая остановка вспенивателя требует:
- Остановка червячного дозатора.
- Отключение подачи пара.
- Отключение механической мешалки по охлаждении.
- Опорожнение вспенивателя от вспененных гранул через дверки во вспенивателе.
12.6. Порядок действий при аварии (выключение электроэнергии, остановка
мешалки)
Требует немедленного отключения подачи пара и включения подачи сжатого воздуха с целью
охлаждения гранул. Невыполнение этих правил может привести к слипанию гранул, находящихся внутри в агломерат, что может повредить оборудование привода вспенивателя.
Возобновление работы вспенивателя после аварийной остановки может производиться после опорожнения находящихся внутри гранул и осмотра вспенивателя
polistirolbeton.ru
Вспениватель ПП-4
Вспениватель ПП – 4. Высокопроизводительный комплекс на основе вспенивателя ПП – 4, позволяющий производить тепловую обработку гранул полистирола насыщенным водяным паром. Подача гранул производится шнековым питателем в камеру тепловой обработки гранул. Коагуляции (слипанию) гранул между собой препятствует равномерное вращение принудительного перемешивающего устройства вспенивающихся гранул. Для получения необходимой плотности вспененного полистирола возможно многократное вспенивание материала после промежуточной выдержки.
Комплекс на основе вспенивателя ПП – 4 это:
Встроенный паргенератор мощностью 9 кВт (3 ТЕНа по 3 кВт), с собственным водяным насосом подкачки «Patriot 350», производительностью до 4,5 м3/час.
Датчик уровня воды позволяющий в автоматическом режиме следить за уровнем воды в парогенераторе (в случае недостаточного количества включается насос и закачивает недостающую воду из водной магистрали либо расходной емкости).
Привод перемешивания установленный в камере вспенивания позволяет произвести равномерное вспенивание гранул.
Шнековый питатель для подачи гранул в камеру вспенивания, гранулы, увеличиваясь в объеме, поднимаются вверх, вытесняемые гранулами, подаваемыми шнековым питателем.
Таким образом, вспениватель ПП – 4 представляет собой автономное оборудование, не требующее никаких дополнительных устройств (например, отдельный парогенератор) для получения вспененных гранул полистирола. Камера тепловой обработки имеет дверь, облегчающую доступ ко всем основным внутренним частям вспенивателя.
Технические характеристики
Наименование | Ед. изм. | Значение |
Производительность | кг./час |
до 20 |
Установленная мощность | кВт | 19 |
Объем емкости для гранул полистирола | л. |
40 |
Объем камеры вспенивания | л. |
400 |
Давление пара в рабочей камере | атм. |
0,1-0,3 |
Габаритные размеры Д/Ш/В | мм. |
1300х900х1850 |
Масса, не более | кг. |
180 |
metembeton.ru
Что такое вспененный полистирол
Разберем что это такое — вспененный полистирол и какие плюсы и минусы его использования. Методы, способы и технологии переработки гранул при изготовлении вспененного полистирола многообразны и зависят от вида и назначения конечного продукта.
Начинается все с твёрдого и бесцветного вещества, полученного путём полимеризации стирола, называется полистиролом. Выпускается в виде цилиндрических прозрачных гранул. Заполняются гранулы стирола природным газом, для увеличения противопожарных свойств применяется углекислый газ. Возможно вспенивание в вакууме, без применения газов.
Особое место в ряду утеплителей на основе полистирола занимает пенополистирол. Получение вспененного или вспученного полистирола происходит по примерной схеме:
- заполнение гранул стирола газом;
- нагрев паром;
- увеличение объёма гранул в 30-50 раз;
- полное заполнение формы;
- спекание гранул между собой.
В составе вспененного полистирола нередко присутствуют антипирены, пластификаторы, наполнители, красители.
Плюсы
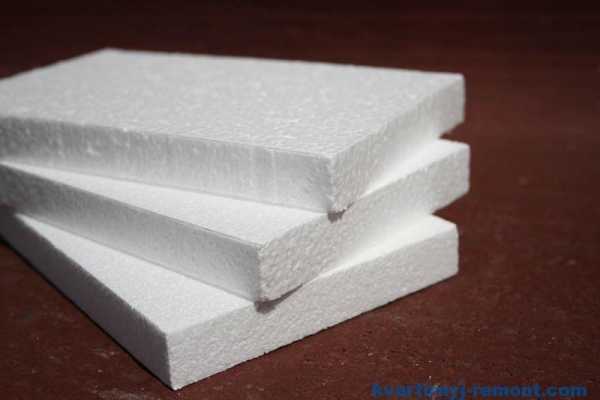
Основная сфера применения вспененного полистирола – строительство. Он лёгкий и удобный в работе, значительно удешевляет и ускоряет строительные работы. Находит применение на всех этапах строительных работ:
- утепление фундаментов;
- возведение монолитных стен с несъёмной опалубкой;
- изготовление и устройство шумоизолирующих стеновых панелей;
- утепление стен, полов, потолков и чердачных перекрытий;
- изготовление декоративных облицовочных панелей и элементов.
До недавнего времени ограниченное применение плит и панелей из вспененного полистирола было вызвано возможностью его возгорания. На сегодняшний день ГОСТ 15588-2014 обязывает производителей применять противопожарные пропитки и добавки в изделия.
Обработанные специальными антипиреновыми составами, строительные материалы из вспененного полистирола сегодня в применении не опаснее обоев.
Отдельно о токсичности
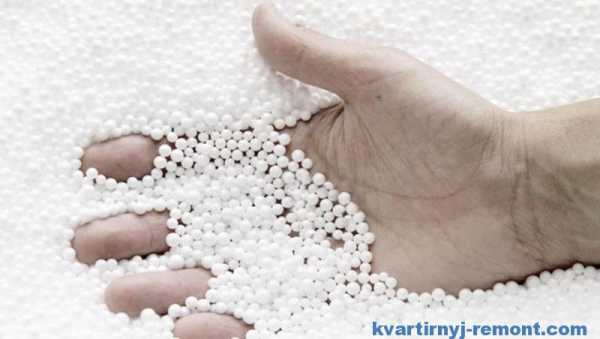
Учёные многих стран, исследовавшие исходную составляющую — стирол, дали заключение об отсутствии оснований для классификации материала как мутагенного, канцерогенного или обладающего репродуктивной токсичностью.
Стирол представляет собой бесцветную жидкость, нерастворимую в воде, но легко растворяющую другие полимеры. Вдыхание его паров опасно для здоровья человека.
В то же время он содержится в кофе, сырах, корице и даже клубнике. Иными словами, небольшая концентрация стирола в изделиях не может повлиять на самочувствие человека, а применение вспененного полистирола как строительного материала абсолютно безопасно.
О грызунах и насекомых
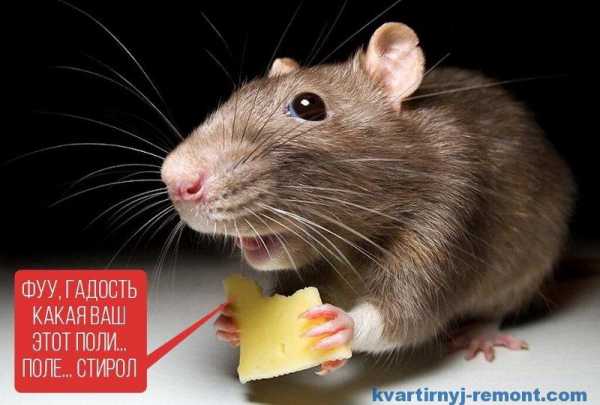
Как питательная среда для грызунов и других организмов состоящий из углеводородов вспененный полистирол не представляет никакого интереса, но жить в нём насекомые, грызуны и птицы могут.
Поэтому необходимо предусмотреть при использовании утеплителя такую возможность и исключить проникновение, либо обработать специальными составами.
Недостатки
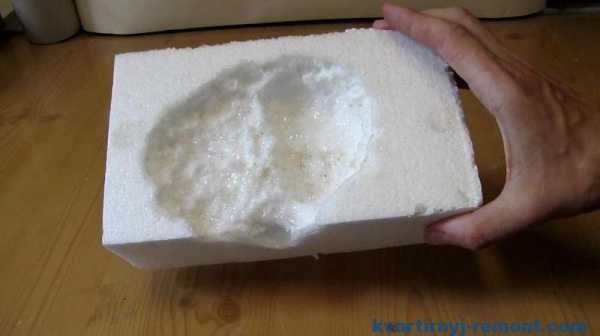
- Верхний эксплуатационный предел вспененного полистирола составляет +60 градусов, при превышении предела он размягчается и теряет свои механические свойства.
- Возможна разрушение структуры от взаимодействия с красками на основе ацетона и некоторых видов растворителей, недопустимы в лакокрасочных покрытиях и хлорированные углеводороды.
- Не является хрупким материалом, всё же при его использовании нужно воздержаться от излишнего механического воздействия.
Эти недостатки не критичны, в основном вспененный полистирол является перспективным материалом, с большим будущим.
Если вы нашли ошибку, пожалуйста, выделите фрагмент текста и нажмите Ctrl+Enter.
kvartirnyj-remont.com
Предвспениватели полистирола.
Вспениватели полистирола купить
Производим и предлагаем Вам установки непрерывного вспенивания сырья ПСВ, вспениватель он же ― предвспениватель.
Вспениватель предназначен для предварительного вспенивания гранул полистирола вспенивающего — ПСВ.
Где применяются вспененные гранулы полистирола?
В строительстве.
- При производстве пенопласта.
- В качестве тепло, звукоизолирующего материала при засыпке ограждающих конструкций;
- Для устройства кровельных покрытий с плоским уклоном.
- Для смесей с бетоном или цементом с пенопластовой крошкой.
- При производстве полистиролбетона.
- При производстве пенополистиролбетона.
- При производстве блоков с пенопластовой крошкой.
- При устройстве бетонного пола с пенопластом.
- При заливке бетона с пенопластовой крошкой.
- Заливка пола с пенопластовой крошкой.
- Для термоизоляции траншейных труб;
- Для изготовления цементно-песчаной стяжки.
- В утеплении плит фундамента и стен.
- Для утепления кровель, полов, бассейнов, многослойных стен.
- Как лучший засыпной материал для стен с воздушной прослойкой.
При изготовлении бескаркасной мебели, как наполнитель.
- Наполнитель для подушек.
- Наполнитель для кресел.
- Наполнитель для кресла мешка.
- Наполнитель для игрушек.
- Подушки для беременных наполнитель.
- Для изготовления пуфиков.
Помимо этого, шарики пенопласта применяют:
Помимо этого, шарики пенопласта применяют:
- В качестве фильтрующего компонента в установках для очистки воды.
- В качестве насыпной упаковки.
- В виде амортизирующей подстилки.
Шарики применяют в рыбной ловле.
— В качестве плавающей наживки, для ловли мирной белой рыбы: карп, карась, линь, лещ, плотва и т.д.
Дополнительно, предлагаем практические пособия, технологов:
- По технологии производства пенопласта-комплект из 2 книг.
- По технологии производства полистиролбетона — комплект из 10 книг.
- По технологии производства пенополистиролбетона -комплект из 10 книг.
У нас выгодно покупать выгодно покупать, потому что:
Профессиональные консультации при покупке в компании.
Оборудование всегда в наличии.
Разумные цены.
Надежность, проверенная временем.
Нет проблем с запчастями, потому как мы сами изготавливаем оборудование.
Любая форма оплаты.
Кроме этого.
Постоянно производим оборудование для изготовления:
- пенобетона;
- полистиролбетона;
- пенополистиролбетона;
- вспениватели полистирола
- листового и блочного пенопласта;
- фасадных стеновых термопанелей;
- термоконтейнеров из пенополистирола;
- пеногенераторы;
- героторные насосы;
- смесители строительных растворов;
- пневмонагнетатели строительных растворов;
- высокоточные формы для стеновых блоков;
Осуществляем:
- шеф- монтаж оборудования;
- пусконаладку;
- отработку технологии производства.
Кроме этого, предлагаем современное практическое пособие, для молодых технологов.
Технология производства, состав, рецептура полистиролбетона ― комплект из 9 книг.
Технология производства, состав, рецептура пенополистиролбетона ― комплект из 10 книг.
Технология производства пенопласта ― комплект из 2 книг.
Узнайте больше на сайте: www.beton57.ru
Россия.
Город Воронеж.
Ул. Малаховского 52
Мобильный тлф. +7 953 477 23 51
Контактное лицо: Владимир Петрович
Эл. почта: [email protected]
ICQ: 692672603
Skype: stroim-vsem
http://www.beton57.ru
strojoborudovanie.ru
❶ Как вспенивать полистирол ? вспененный полистирол в гранулах магнитогорск ? Строительные материалы
Полистирол – это синтетический материал, имеющий в своем составе множество пузырьков, заполненных воздухом. Он нашел широкое применение в таких областях, как строительство, изготовление мебели. Полистирол обладает рядом ценных свойств.
Во-первых, это отличный теплоизоляционный материал. Он используется при утеплении стен, полов, различных перекрытий. Во-вторых, он не боится влаги, в силу чего не изменяет своих первоначальных свойств. В-третьих, это экологически чистый продукт, поэтому его можно использовать не только при наружных, но и при внутренних работах.
В-четвертых, полистирольные шарики обладают отличными звукоизоляционными свойствами, что является очень важным в строительном деле. Шарики из полистирола имеют низкую массу, они не дороги. Полистирол – это пластичный материал, из которого можно изготавливать мебель самой разной конфигурации. В отличие от некоторых других материалов, шарики из полистирола обладают антисептическими свойствами, препятствуя размножению бактерий и других микробов.
В последние годы большую популярность приобрели шарики из полистирола для изготовления современной мебели, в частности, не имеющей каркаса. К такой мебели можно отнести кресло – мешок, где шарики выступают в качестве наполнителя и придают мебели необычный вид. Такая мебель удобна и комфортна.
Из шариков изготавливают диваны, пуфики. В отличие от обычной мебели, она повторяет контуры тела. Шарики из полистирола с успехом можно применять для изготовления теплых полов, в частности кафельного, паркета, ламината.
Чтобы приготовить смесь для покрытия пола, нужно смешать шарики со специальным раствором. Этот материал применяют при изготовлении фундамента, они отлично подходят для утепления и крыш и перекрытий. Они служат основным элементом при изготовлении специального бетона.
Производится он в виде блоков. Как уже было сказано выше, благодаря отличным теплоизоляционным свойствам, способности снижать уровень звука, шарики из полистирола используются для утепления жилых помещений. Данный материал можно встретить в пищевой промышленности при изготовлении тар и упаковочных материалов.
Актуально это потому, что полистирол является гидрофобным материалом и не впитывает влагу, хорошо переносит низкие и высокие температуры. Таким образом, шарики из полистирола нашли применение в различных областях, в том числе строительстве.
www.kakprosto.ru
Вспениватель полистирола, Предвспениватель
Установка многократного вспенивания УМВ – 850, УМВ – 900, УМВ — 1100 предназначены для производства полистирола вспененного гранулированного. Производительность: от 15 до 35 м3/час, эл. двигатель 4,0 – 5,5 кВт, 380 V. Бак делителя установки полностью алюминиевый утеплен фольгированным термофолом, обшивка из крашенного оцинкованного листа — это обеспечивает минимальные температурные потери и высокий КПД обработки гранул сырья паром, быстрый прогрев, коррозионную стойкость. Имеет два шнековых питателя: 1 — первичное вспенивание, шнек выполнен из каленого аллюминия(В-95Т1) не корродирует, отсутствует налипание и спекание сырья. 2 — питатель второго и третьего вспенивания на базе мотор-редуктора с электронным управлением подачи. Имеется контроль температуры вспенивания и возможность регулировки высоты разгрузки шибером. Основной привод — нижнего расположения, для обеспечения лучшего температурного режима. Предотвращает проблему пересыхания сальников редуктора, значительно продлевая срок службы последнего. Впрыск пара через две форсунки с давлением 0,4-1кг/см. Ответственные резьбовые соединения из нержавеющей стали. Объем бака предвспенивателя: от 0,85 до 1,1 м3, редуктора — Германия, Италия, КНР.
Для желающих купить вспениватель полистирола
Полистиролбетон относится к легким конструктивным материалам. Он легкий, плохо проводит тепло, недорогой. Его характеристики позволяют выполнять перемычки и другие несущие элементы. Для организации производства полистиролбетонных изделий, широко востребованных на современной стройке, потребуется специализорованное оборудование — вспениватель полистирола. Его цена зависит от производительности установки — ее предвспениватель полистирола может иметь объем от 0,3 до 1,2 кубического метра. Общая производительность от 15 до 35 кубометров в час. Мощность маршевого двигателя от 1,1 до 5,5 кВт. Напряжение питания 380 вольт.
Предлагаем купить вспениватель полистирола, выполненный по простой, долговечной и надежной схеме, многократно апробированной на собственном производстве. Вспениватель полистирола может быть задействован как на крупном специализированном предприятии, так и для выпуска мелкосерийных партий.
Основа установки включает в себя тщательно утепленный и защищенный от коррозии бак делителя. Сама емкость из алюминия, сделанного по специальной технологии литья, в качестве утеплителя используется фольгированный термофол. Внешняя защитная облицовка из стального оцинкованного листа.
Питатели вспенивателей защищены от коррозии и налипания, а также от спекания сырья. Привод вспенивателя выполнен таким образом, что обеспечивает наиболее оптимальный температурный режим в активной зоне установки. Контроль за высотой разгрузки производится шибером, есть функция контроля температуры вспенивания. Все ответственные детали вспенивателя выполнены из каленого алюминия или нержавеющей стали, что исключает корродирование.
В нашем магазине вы найдете большой ассортимент товаров, среди них героторная пара и дозатор воды.
stirolbeton.ru
Получение гранул полистирола для вспенивания
Получение гранул полистирола для вспенивания [c.7]В ФРГ разработан 97 промышленный способ получения гранул полистирола для вспенивания, заключающийся в нагревании при 50° С в течение 60 ч при непрерывном перемешивании смеси следующего состава (в вес. ч.) [c.9]
Для получения самозатухаемости в пенополистирол вводят тетра-бромпараксилол, дибромэтилбензол или другие антипирены (добавки для понижения горючести материалов). Изделия из полистирола для вспенивания формуют в два этапа предварительное и окончательное вспенивание. Предварительное вспенивание гранул полистирола, содержащих порообразователь, осуществляется в специальном механическом вспенивателе горячей водой при 95° С или паром. Процесс проходит в течение 2—5 мин. Окончательное вспенивание с получением изделий требуемой формы может производиться в легких металлических формах при 102—110° С. Продолжительность выдержки зависит от толщины изделия и равна примерно 10 с на каждый миллиметр толщины изделия плюс продолжительность подогрева формы. Беспрессовым способом могут быть получены изделия разных размеров и конфигураций. Процесс не требует сложного оборудования, поэтому может проводиться на месте потребления изделий. [c.88]
Беспрессовый метод производства полистирольных пенопластов заключается в следующем. Полученный бисерным методом полистирол, содержащий растворенный в нем газообразователь изопентан, подвергается предварительному вспениванию вне формы в горячей воде. Увлажненные при этом гранулы сушатся воздухом при 70—80°С, после чего следует окончательное вспенивание в формах или в экструзионной машине через щелевую головку при 116—130°С. [c.91]
МПа теплопроводность 0,027—0,032 Вт/(м-К) влагонепроницаем. Получ. 1) суспензионная полимеризация стирола в присут. агентов вспенивания — пентана и (или) изонентана полученные гранулы при переработке в изделия в результате нагревания вспениваются и спекаются 2) полимеризация в массе стирола с послед, смешением полученного полистирол,- с лимонной к-той и порофорами при экструдировании этой смеси происходит вспенивание с образованием П. сравнительно высокой плотн. (0,05— 0,1 г/смз). Примен. тепло- п. звукоизоляц. материал в стр-ве (в т. ч. для районов Крайнего Севера) упаковочный материал для транспортировки приборов, пищ. продуктов для изоляции кабелей, трубопроводов и др. Мировое произ-ио [c.426]
Беспрессовый,метод производства пенополистирола состоит из двух основных стадий 1) получение гранул полистирола, насыщенных легколетучим компонентом (изопептан, изопентановая фракция, пентан, бутан и др.) и 2) вспенивание гранул с одновременным слипанием их в алюминиевых, стальных, пластмассовых и деревянных формах. [c.128]
Пенистый полистирол, полученный суспензионным методом в виде гранул диаметром от 0,2 до 2,5 мм, подвергается предварительному вспениванию. Эта операция производится путем нагрева гранул до 100°С в горячей водяной бане, паром или смесью пара с воздухом. [c.153]
Полистирольные пенопласты получают на основе суспензионного полистирола. Полимеризация стирола проводится в присутствии углеводорода (изопентана), растворимого в стироле и нерастворимого в полистироле. При превращении капелек мономера в полимер изопентан выделяется в виде самостоятельной фазы. Поэтому в образующемся бисере полистирола появляются вкрапления равномерно распределенных капелек изо-пентана. Получение пеноизделий состоит в предварительном вспенивании бисерного полистирола и окончательном вспенивании и спекании полученных предвспененных гранул в формах. [c.389]
Предварительное вспенивание гранул полистирола проводят с помощью тепловой обработки с целью получения материала требуемой насыпной плотности. В процессе тепловой обработки -при нагревании до температуры, превышающей температуру стеклования, полимер переходит в эластичное состояние, а вспенивающий агент испаряется, что приводит к расширению гранул. Лишь 50% расширения гранул обеспечивается за счет испарения вспенивающего агента, а остальное расширение происходит вследствие проникновения в ячейки гранул теплоносителя — водяного пара или воздуха 4, Причем проникновение теплоносителя в ячейки, несмотря на некоторое избыточное давление в них, происходит значительно быстрее, чем улетучивание паров вспенивающего агента из ячеек. [c.41]
Беспрессовый метод производства полистирольных пенопла-стов заключается в следующем. Полученный суспензионным методом полистирол, содержащий газообразователь — изопентан, подвергается предварительному вспениванию вне формы в горячей воде. Увлажненные гранулы затем сушат и выдерживают на воздухе в течение 6—24 ч, после чего следует окончательное вспенивание в формах или в экструдере, со щелевой головкой при 116—130°С. Вспенивание можно сочетать с формованием изделия, например при литье под давлением. [c.100]
В последние годы разработан метод получения пенополистирола путем вспенивания не отдельного блока (заготовки), а небольших гранул с последуюшим их спеканием (склеиванием). Этот метод имеет преимущества перед блочным методом изготовления пенополистирола. Ввиду плохой теплопроводности полистирола отдельные гранулы вспениваются в 5— [c.153]
Гранулы полистирола для вспенивания получают также полимеризацией стирола в водной суспензии, содержащей один низкотемпературный и один высо.котемпе-ратурный перекисный инициатор. Смесь сначала нагревают до температуры, при которой основным инициатором реакции является низкотемпературный. После этого к смеси добавляют порофор и температуру повышают до значения, при котором основным инициатором реакции полимеризации является высокотемпературный. В полученных гранулах содержится не более — 0,5 вес.% остаточного мономера 9 . [c.9]
Полистирол суспензионный ПСБ-С для вспенивания самозатухающий — продукт суспензионной полимеризации стирола в присутствии порообразователя и антипирена. Гранулы молочного цвета. Применяют для получения самозатухающнх поропластовых изделий беспрессовым способом. Выпускают следующих марок Ах, Аа, Б и В. [c.254]
Большое значение при получении пенополистирола низкой кажущейся плотности имеет гранулометрический состав полистирола. Получить пенополистирол с кажущейся, плотностью 15 кг/м можно только при исполь-зова ии гранул размером 1—3 мм. Поэтому -рекомендуется для получения пенополистирола с кажущейся плотностью 13—16 кг/м применять полистирол суспензионный для вспенивания ПСБ марки А. [c.85]
Для получения пенополистирола с малой кажущейся плотностью предложен следующий метод обработки гранул полистирола для вспенивания, содержащих равномерно диспергированную в них летучую органическую жидкость. Гранулы выдерживают
www.chem21.info