Компоненты ппу и производители пенополиуретана в России
- История создания и применение ППУ.
- Компоненты пенополиуретана и производители сырья.
- Получение пенополиуретана, характеристики и свойства.
- Оборудование для пенополиуретана.
- Бизнес-план по напылению ППУ.
Основные компоненты ППУ: полиол (компонент «А») и изоцианат (компонент «Б»).
Мы предлагаем поставку качественных компонентов ппу по ценам завода-производителя — крупнейшей российской компании «Дау-Изолан». Всегда в наличии стандартные проверенные системы для напыления плотностью 28-30 кг/м3 с закрытой ячейкой «Изолан-131» (летняя), «Изолан-132» (зимняя), с открытой ячейкой «Изолан-108» (12-15кг/м3) а также заливочные системы
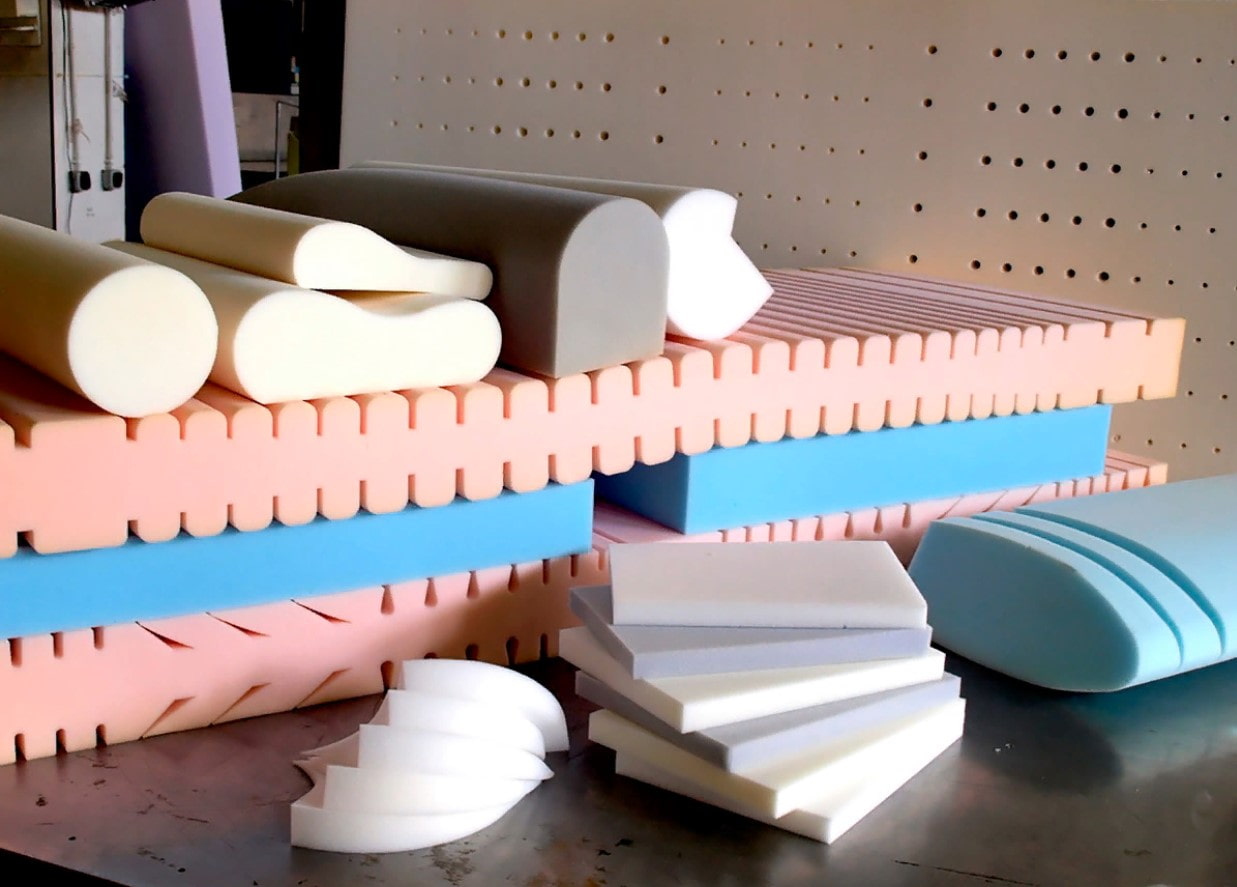
Компоненты отгружаются напрямую с завода или с нашего склада, свежие (изготовлены за 3-5 дней до отгрузки), с максимальным гарантийным сроком годности.
Отгрузка компонентов производится в металлических бочках ёмкостью 216л (стандартный комплект: бочка компонента «А» + бочка компонента «Б»). Вес сырья в стандартном комплекте составляет 480кг.
По вопросам приобретения компонентов, цен и сроков отгрузки звоните:
+7 910 673-45-43, +7 4922 77-95-17
Готовые компоненты ппу (системы) других производителей
ППУ компоненты на водной основе (бесфреоновые)
Часто производители сырья для ППУ в целях увеличения срока хранения основного компонента и получения качественного конечного материала производят и третий компонент (катализатор, компонент «С»), который обычно смешивается с полиолом непосредственно перед процессом получения ППУ.

Компонент «А» — полиол
В состав компонента «А» (полиол) добавляются специальные вещества – антипирены, призванные уменьшить пожароопасность получаемого ППУ. В настоящее время некоторыми производителями уже достигнута группа горючести для конечного продукта (ППУ) Г1, которая получается добавлением в полиол антипиренов на основе нанографита. Однако, стоимость таких компонентов, как правило, значительно выше систем со стандартной группой горючести Г3 и Г4.
Производится, в том числе, в России, рядом предприятий химической промышленности. ППУ производители в России: ООО «Дау-Изолан», ООО НВП «Владипур», ЗАО «Уретан», ЗАО «Блокформ», ЗАО «Химтраст».
Компонент «Б» — изоцианат
В отличие от компонента «А», изоцианат (компонент «Б») представляет собой токсичную пожароопасную жидкость (ПДК его паров в воздухе при производстве составляет 0,2 мг/мИсходя из этого, формируются требования к условиям его хранения в плотно закрытой таре, а также к необходимым средствам защиты при обращении с ним. Изоцианат допускает замораживание, при котором возможна его кристаллизация. Для последующего применения изоцианат разогревается до растворения кристаллов (обычно до температуры 70-80 ℃ непосредственно в металлических бочках).
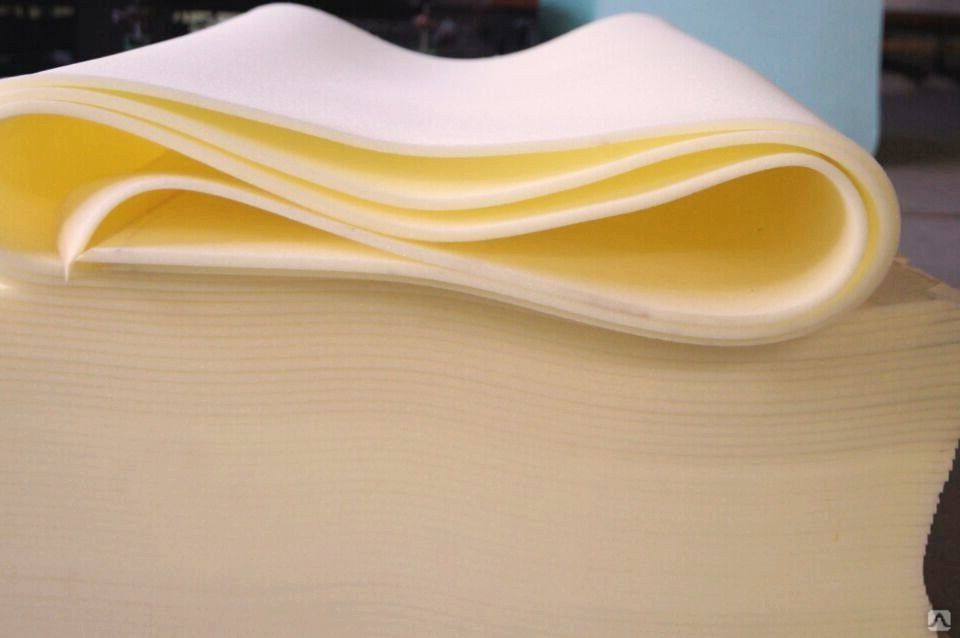
В настоящее время ППУ производители России компонент «Б» не производят. По мнению экспертов, связано это не с состоянием отечественной науки, а, в первую очередь, с нестабильностью поставок отечественных составляющих (анилина, нитробензола и других) для получения изоцианата, процесс производства которого должен и может быть только непрерывным.
В связи с этим, закупка изоцианата осуществляется за рубежом с соответствующим влиянием на стоимость готовой системы компонентов ППУ.
Наиболее известные ппу производители компонента «Б»: Bayer (Германия), Huntsman (Нидерланды), Dow Chemical (США), Ningbo Wanhua Polyurethanes (Китай), Elastogran (Германия), Mitsui Chemicals (Япония), BorsodChem Zrt (Венгрия), Kumho Mitsui Chemicals (Корея).
Защиту пенополиуретана от ультрафиолета и качественную гидроизоляцию объекта можно получить, применяя оборудование для жидкой резины ДУГА®.
Получение пенополиуретана (ППУ) | Напыление и заливка пенополиуретана в Ростове-на-Дону, Краснодаре, Волгограде, Ставрополе (ЮФО)
Сегодня жесткие пенополиуретаны являются одними из наиболее распространенных строительных материалов. Эти легкие, но достаточно прочные материалы обладают очень низкой теплопроводностью, малой паропроницаемостью, высокой адгезией к большинству строительным материалам (бумага, бетон, кирпич, пеноблок, металл, древесина, штукатурка и т.д.).
Пенополиуретан получают в результате химической реакции двух жидких компонентов — А (полиизоцианата) и В (полиола). Иногда компоненты ППУ поставляются с третьим компонентом – катализатором (компонент С), который вводят в нужной пропорции в состав компонента B перед нанесением и перемешивается. В основном это касается пенополиуретанов отечественного производства и связано с тем, что срок годности некоторых компонентов B с введенным катализатором уменьшается.
Ниже на рисунке 1 представлена химическая реакция, в результате которой из изоцианата и полиола образуется пенополиуретан.
Рис.1
Механизм образования пенополиуретана исключительно сложен, поскольку материал очень быстро увеличивается в объеме при одновременном повышении температуры и вязкости. Реакции нуклеации, вспенивания и отверждения протекают настолько быстро, что уже через несколько минут после полимеризации поверхность, покрытая ППУ, готова для дальнейшей отделки (см. Рис.2).
Рис.2
Ниже представлен видеоролик реакции полиола и полиизоцианата, в результате которой образуется пенополиуретан (ППУ).
Также рекомендуем ознакомиться со статьей на тему:
Оборудование пенополиуретан Производство изготовление ППУ
ООО «Современные Технологии» (сокращённо «СовТех» или «СТ») имеет две торговых специализации и две производственных. Мы предлагаем всем заинтересованным частным лицам и организациям в Сибири и на Дальнем Востоке:
- оборудование и технологии для производства современных строительных материалов, а именно: пенополиуретан, пеноизол, жидкая резина и стеклофибробетон.
- различные системы ППУ-компонентов для производства любых изделий из пенополиуретана в цеху и нанесения утеплителя непосредственно на стройплощадке.
- различные изделия из пенополиуретана, полученные методом заливки в форму: скорлупы, плиты, панели термоклинкер, декор, трубы, улья, элементы мебели и многое другое, в т.ч. нетиповое, по эскизам заказчика.
- выполняем любые строительные работы (общестроительные, ремонтные, отделочные), в т.ч. используем современные технологии с использованием пенополиуретана, жидкой резины и стеклофибробетона.
Кровельные работы и технологии
Теплоизоляция кровель традиционными методами и новыми технологиями: напыление пенополиуретана (ППУ).
Утепление крыш ППУ – это надежный и эффективный способ теплоизоляции кровли, который применяется во всем Мире. Фирма «СовТех» с 2005 года успешно выполняет работы в различных городах Сибири по нанесению пенополиуретановой изоляции.
Гидроизоляция кровель, наплавляемыми и мембранными материалами. Возможность круглогодичного монтажа кровли. И бесшовная гидроизоляция жидкой резиной, которая наносится методом холодного напыления.
ООО «Современные Технологии» не только выполняет работы по теплоизоляции и гидроизоляции кровель, но также предлагает всем освоить эти технологии.
Фирма «СовТех» готова поставить Вам ППУ оборудование и установку для гидроизоляции жидкой резиной. Это современные отечественные машины фирмы «Новые Строительные Технологии» (Москва), которая с 1997 года проектирует, разрабатывает и производит оборудование для пенополиуретана и жидкой резины. Вместе с оборудованием для ППУ и жидкой резины мы готовы поставить Вам компоненты для пенополиуретана и бесшовной гидроизоляции.
Для производства ППУ мы предлагаем оборудование под торговой маркой ПЕНА-98.
Это надежные, профессиональные, функциональные установки для пенополиуретана. Фирма СовТех в своей работе по ППУ использует именно это оборудование для пенополиуретана. Поэтому мы рекомендуем то, в чем уверенны сами.
ПЕНА-98 это установка, которая позволяет осуществлять не только напыление ППУ, но и заливку пенополиуретана на различных строительных объектах. Это пеногенераторы ППУ, которые позволяют плавно регулировать подачу компонентов пенополиуретана.
ППУ оборудование простое и удобное в использовании при ведении работ по производству пенополиуретана. ПЕНА-98 комплектуется специальным распылителем пенополиуретана модели ПРП.
Фирма «СовТех» – эксклюзивный и крупнейший дистрибьютор ППУ-сырья завода Владипур в Сибирском и Дальневосточном регионе. На складе в Новосибирске всегда в наличии оборудование для пенополиуретана модельного ряда ПЕНА-98 и различные марки сырья для ППУ.
Мы готовы предложить Вам ППУ компоненты для напыления пенополиуретана различных плотностей. У нас всегда имеется заливочное ППУ сырье для производства различных ППУ-изделий: теплоизоляционных скорлуп, сэндвич-панелей, предизолированных труб, элементов декора и пр.
Для гидроизоляции ООО «Современные Технологии» предлагает оборудование и технологию ЖИДКАЯ РЕЗИНА. Установка для гидроизоляции модели RX-27 разработана фирмой НСТ. Оборудование позволяет наносить гидроизоляционную мембрану на основе жидкой резины методом холодного напыления.
Получаемое покрытие отлично адгезирует к любой поверхности. Мембрана на основе жидкой резины позволяет получить бесшовное гидроизоляционное покрытие для поверхности любой сложности. Оборудование RX-27 для жидкой резины предназначено для гидроизоляции кровель, подвалов, фундаментов, бассейнов и пр. Для производства работ по гидроизоляции предлагаем компоненты Жидкая Резина различных марок.
Фасадные работы и технологии
Устройство вентилируемых фасадов с применением металлосайдинга, ПВХ сайдинга, профлиста, керамогранита, краспана, сэндвич панелей, рваного камня, дикого камня, с использованием утеплителей, в т. ч. пенополиуретана.
Теплоизоляция домов пеноизолом
Заполнение полостей стен пеноизолом: к кирпичной стене крепится декоративная панель и заливается между стеной и панелью пеноизол. Преимущества: качество, скорость, дешевизна.
Пеноизол – это одновременно теплоизоляция и звукоизоляция. Пенопласт «ПЕНОИЗОЛ» – легкий, пористый, хорошо удерживает тепло, простой в использовании утеплитель. Теплоизоляция пеноизолом – это экономично и технологично. Для производства пеноизола требуется оборудование типа ПЕНА-2000, разработанное фирмой «Новые Строительные Технологии». Последняя модификация оборудования для пеноизола – это установка ПЕНА-2000/10УМ. В первые 15 мин после получения пеноизол представляет суфлеобразную массу, которая легко закачивается через небольшие отверстия и щели и заполняет пустотелые конструкции.
Заливка в закрытые полости идеально для утепления старых конструкций, в которых утеплителя либо не было, либо осыпался. При строительстве нового дома пеноизол удобен и хорош тем, что можно сначала возвести стены и потолок, а потом сразу закачать теплоизоляцию через отверстия.
Теплоизоляция домов пенополиуретаном
Утепление любых зданий и сооружений пенополиуретаном методом напыления. В результате образуется прочная, монолитная теплоизоляционная шуба. Утепление пенополиуретаном может применяться практически везде: стены, фасады, полы, перекрытия, чердаки, фундаменты, трубопроводы. Пенополиуретан можно не только НАПЫЛЯТЬ на поверхность, но и как пеноизол ЗАЛИВАТЬ в стены – заполнять полости.
Пенополиуретан расширяется при заливке и напылении – он забивает все трещины. ППУ адгезирует к любой поверхности. ППУ – легкий, но вместе с тем и прочный материал. Пенополиуретан – идеально подходит для реконструкции старых зданий или сооружений, где требуется минимизировать нагрузку на стены и перекрытия.
Мы предлагаем Вам технологии, которые освоили и применяем сами с 2005 года. Мы накопили богатый и уникальный опыт по использованию ПЕНОПОЛИУРЕТАНА и ЖИДКОЙ РЕЗИНЫ в Сибирском регионе. И мы готовы поделиться с Вами нашими знаниями. Мы приветствуем каждого, кто готов применять и внедрять в Сибири новые строительные технологии теплоизоляции и гидроизоляции: пенополиуретан, пеноизол и жидкая резина.
Подробный перечень, предлагаемых в Новосибирской области и других регионах Сибири, строительных услуг тут.
Производство пенополиуретана по технологии заливки
Помимо работ и услуг по теплоизоляции пенополиуретаном на стройплощадке, ООО «Современные Технологии» с 2008 года открыло собственное производство методом заливки пенополиуретана.
Мы производим и реализуем:
- ППУ-скорлупы теплоизоляционные;
- Термопанели фасадные с ППУ-утеплителем и клинкерной плиткой;
- ППУ-плиты;
- Предизолированные ППУ-трубы;
- И пр. ППУ-продукцию.
Фирма «СовТех» готова поставить оборудованеи для заливки ППУ производства фирмы НСТ – заливочные ППУ-машины на базе пеногенератора ППУ типа ПЕНА-98 и Заливочной Головки ППУ модели ЗГ-016.
На складе в Новосибирске всегда в наличии оборудование и компонентны для пенополиуретана. Обучим технологии. В кратчайшие сроки изготовим для Вас любые ППУ-изделия методом заливки. Выполним утепление пенополиуретаном стен и кровель.
На любой Ваш вопрос о пенополиуретане у нас есть ответ.
ООО «СТ» это оборудование + сырье + производство + знания = ПЕНОПОЛИУРЕТАН В СИБИРИ
Стоит ли пытаться сделать ППУ самостоятельно? Все о производстве пенополиуретана.
Многие строители понимают важность высококачественной теплоизоляции, но вынуждены экономить на материалах и работах по монтажу. Из-за этого нередко возникает вопрос, как самому сделать пенополиуретан и с его помощью реализовать качественное утепление дома. Прежде, чем заняться воплощением этой идеи, мы советуем разобраться в тонкостях процесса производства ППУ.
Как делается пенополиуретан: базовый принцип
Производство ППУ подразумевает очень сложный технологический процесс. ППУ масса формируется вследствие реакции между полиолом и диизоционатом или полимерным изоционатом в присутствии определенных катализаторов и прочих добавок. Так как производить сам пенополиуретан приходится непосредственно перед заливкой или напылением, завод-изготовитель поставляет две фазы ППУ-смеси в отдельных контейнерах. Фазы смешиваются в специальных установках перед выполнением работ. Вот что происходит при смешивании двух фаз:
Из-за многообразия изоцианатов и огромного спектра полиолов можно получить полиуретаны с различными свойствами и сферами применения. Это может быть эластичная пена, жесткая пена, эластомер и т.д. Узнать все о производстве пенополиуретана невозможно, так как точная рецептура фаз держится производителями в секрете. Даже при наличии всех необходимых компонентов опытному химику придется долго подбирать нужные пропорции для обеспечения требуемых свойств смеси.
Трудности при самостоятельном изготовлении ППУ
Обычно строители закупают готовые фазы для производства пенополиуретана, так как сделать ППУ смесь своими руками можно только из готовых компонентов. Для этого необходимо правильно рассчитать расход и пропорцию фаз ППУ , учитывая все влияющие на это факторы.
Совет от профессионалаДля правильного расчета расхода и достижения максимального эффекта от теплоизоляции важно выбрать смесь ППУ подходящей плотности. В зависимости от нее, теплоизоляция также может выполнять функции влагозащиты, изоляции звука, обладать достаточной прочностью для различных механических воздействий. Все эти особенности в большой степени зависят от плотности ППУ, и вы можете выбрать марку в соответствии с необходимыми качествами материала.
Если вы решили нанести слой теплоизоляции своими силами, вам понадобится изучить, как самостоятельно сделать пенополиуретан установку. В идеале это должен быть аппарат высокого давления, который равномерно смешивает обе фазы ППУ в одну массу и под высоким давлением распыляет полученную смесь по поверхности в виде мелкодисперсной пены. Здесь требуются специальные знания, так как сделать установку для замешивания пенополиуретана необходимо с соблюдением всех технологических требований. В домашних условиях нет возможности проверить качество получаемой ППУ-пены. Химикаты могут смешиваться неравномерно и реагировать друг с другом не до конца, что может привести к опасным испарениям в процессе эксплуатации теплоизоляции. Ознакомьтесь с условиями достижения полной безопасности ППУ. Так как сделать пенополиуретановую установку самому с обеспечением регулируемого давления, температуры и прочих параметров очень сложно, чаще всего строители покупают уже готовые пеногенераторы.
При самостоятельном производстве ППУ из готовых компонентов есть три главные проблемы:
- Неправильный расчет пропорций фаз в смеси
- Неравномерное смешивание фаз ППУ, что приводит к утрате теплоизоляционных свойств и возникновению риска для здоровья
- Отсутствие необходимых навыков для напыления слоя ППУ требуемой толщины, что грозит серьезным перерасходом материалов.
Избежать подобных рисков можно только используя готовое специализированное оборудование и обладая необходимыми навыками в работе с пенополиуретаном. Профессионалы обучаются, как сделать смесь из пенополиуретана и применять ее для теплоизоляции минимум 6 месяцев. В результате специалист знает все тонкости настройки распылителей, умеет производить напыление и заливку ППУ равномерно, с минимальным расходом материалов, исключая все возможные риски для здоровья. Так как сделать и распылить пенополиуретан своими руками, можно только при серьезных финансовых и временных затратах, платные услуги профессионала по факту могут обойтись гораздо дешевле.
Производитель поролона FoamLine — изготовление пенополиуретана и изделий из ППУ
ФомЛайн – производство пенополиуретана
«ФомЛайн» — лидер рынка эластичных пенополиуретанов (ЭППУ) в России, странах СНГ и Восточной Европы.Компания включает широкую региональную сеть современных производственных комплексов, резательных центров,исследовательских лабораторий и центра научных разработок.
Пенополиуретан – это уникальный материал, который, благодаря своей структуре, отличается высокой комфортностью, долговечностью, шумо- и теплоизоляцией. Огромное количество полезных для человека характеристик обуславливает эффективное использование поролона в различных сферах нашей жизни.
На сегодняшний день на заводах «ФомЛайн» выпускается более 130 марок поролона. Ежегодный объем производства составляет 90 000 тонн.
Сфера применения ЭППУ
Широкая ассортиментная линейка продукции, разнообразие полезных свойств способствует активному использованию пен «ФомЛайн» в различных областях промышленного производства.
На наших заводах выпускаются все виды продукции из ЭППУ,от полуфабрикатов до готовых изделий. Поролон, произведенный компанией «ФомЛайн», получил широкое применение в различных отраслях промышленности:
- мебельная промышленность;
- производство товаров для сна;
- транспортная промышленность;
- легкая и обувная промышленность;
- аэрокосмическая и авиационная отрасль;
- строительство;
- производство хозяйственных товаров;
- сельское хозяйство;
- медицинская промышленность;
- производство упаковки.
Сотрудничество
Основным направлением деятельности заводов «ФомЛайн»является B2B-рынок.Мы всегда открыты к новому сотрудничеству и готовы предложить даже самые нестандартные решения.
Своим партнерам мы гарантируем комплексный подход к решению задач.
Ключевые преимущества работы с нами – это:
- Инновационный подход к производству. Команда технологов «ФомЛайн» непрерывно работает над совершенствованием рецептур пенополиуретана, изучает передовой опыт зарубежных производителей, разрабатывает новые марки ППУ.
- Самый широкий ассортимент эластичных пен в России. В линейке «ФомЛайн» представлена собственная коллекция матрасных блоков и заготовок для подушек, а также готовые решения для мебели и товаров для сна. В научно-исследовательских центрах компании возможна разработка уникальных поролонов по специальным требованиям клиентов.
- Европейское качество продукции. Автоматизация процессов, проверенное сырье, строжайший контроль качества на всех этапах производства гарантируют, что наши клиенты получают поролоны европейского уровня.
Качество продукции «ФомЛайн» подтверждено самыми строгими сертификатами (ИСО 3386-1-86, CertiPUR).
- Оперативность в производстве и доставке. Удобное расположение наших заводов по производству поролона в каждом регионе России позволяет нашим клиентам оперативно получать продукцию и не нести дополнительных расходов на его транспортировку.
- Импортозамещение. Наши клиенты могут значительно сократить затраты на импорт. Производственные возможности заводов позволяют выпускать пены технического назначения, которые традиционно поставлялись из-за границы. Компания «ФомЛайн» единственная в России выпускает высококачественные пены на основе сложных полиэфиров.
Мы нацелены на долгосрочное сотрудничество и сделаем все возможное, чтобы наши клиенты конкурентные рыночные преимущества и максимальную прибыль.
Став нашим партнером, вы останетесь им на долгие годы.
Как изобрели пенополиуретан / ППУ XXI ВЕК – Напыление ППУ
Пенополиуретан (ППУ) — материал, получающий всё большие распространение в различных областях производства, многие впервые ознакомившись с его свойствами, приходят в изумление от высочайших эксплуатационных характеристик и технологичности ППУ. Такой набор свойств по праву позволяет называть пенополиуретан одним из самых перспективных материалов нового столетия.
Интересно, что пенополиуретан был получен и начал успешно применяться уже более 60 лет назад, история его использования огромна, а при использовании в качестве теплоизоляции гораздо более обширна, нежели у сегодняшних «лидеров» этого рынка.
История пенополиуретана
Впервые работы по синтезу полиуретанов начались в Америке ещё в 30-е годы ХХ столетия, однако впервые пенополиуретан был получен в Германии, известнейшим химиком и промышленником Отто Георгом Вильгельмом Байером, в 1937 году. Именно Отто Байер также впервые наладил промышленное производство пенополиуретана начиная с 1944 года.
С середины 50- годов прошлого века пенополиуретан начинает получать всё большее распространение при использовании в строительной отрасли в странах Западной Европы, США и Канаде. Это связано, прежде всего, с удешевлением процесса его получения и началом выпуска оборудования, позволяющего получать теплоизоляционные покрытия из пенополиуретана методом напыления. С первых дней применения пенополиуретан получил положительные отзывы потребителей и строительных компаний. Таким образом, имеется более пятидесятилетний успешный опыт применения ППУ в качестве утеплителя на объектах различного назначения, в том числе при утеплении жилых домов.
Несмотря на такую широкую популярность и несомненную высокую эффективность применения в нашей стране пенополиуретан стал более менее широко применяться лишь 15-20 лет назад, при решении узкоспециализированных задач теплоизоляции холодильных камер и т.п. Единственная область где напыляемый и заливочный пенополиуретан применялся до этого — это военная промышленность, в частности именно из ППУ делалась теплозащита многих боевых советских танков.
Сегодня пенополиуретан широко применяется при утеплении разнообразных объектов:
- Утепление стен жилых, производственных и административных зданий;
Утепление скатных и плоских кровель, как наружнее, так и внутреннее;
Утепление мансард жилых домов;
Утепление холодильных камер;
Утепление ангаров, складов, овощехранилищ;
Утепление фундаментов, цоколей;
Утепление лоджий и балконов;
Заливка ППУ в зазоры и полости, заливка в систему «труба в трубе».
Преимущества пенополиуретана перед другими телпоизоляционными материалами:
Низкий коэффициент теплопроводности (0,020 Вт/м*К). 50 мм ППУ эквивалентно 120-150 мм минеральной ваты.
Способ напыления пенополиуретана позволяет получить бесшовное покрытие без элементов крепления.
Возможность нанесения слоя утеплителя любой толщины.
Высокая адгезия к любым строительным материалам.
Возможность нанесения на поверхность любой формы без специальной подготовки.
Срок эксплуатации — до 50 лет.
Не подвержен гниению, не распространяет микробы и бактерии.
- Экологически чистый материал.
Не поддерживает горения — группа горения различных марок ППУ вплоть до Г1.
Такое сочетание свойств делает пенополиуретан теплоизоляционным материалом нового столетия, утеплителем вне конкуренции. И воспользоваться всеми достоинствами современного, долговечного высококачественного материала можно уже сегодня.
Как производят сэндвич-панели с ППУ, из чего делают панели с пенополиуретаном
Сэндвич-панели с наполнителем пенополиуретан (ППУ) стремительно набирают популярность благодаря отличному комплексу свойств: наилучшей степени тепловой и звуковой изоляции среди альтернатив, очень легкому весу (немногим более 40 кг/м3), предельно низкой гигроскопичности, а также инертностью к воздействию экстремальных температур и агрессивных сред.
Именно выбор ППУ в качестве наполнителя сэндвич-панелей позволяет подобрать наименьшую толщину материала для обеспечения нужных эксплуатационных характеристик и облегчить нагрузки на несущие конструкции.
Из чего делают сэндвич-панелей с пенополиуретаном
Как и любые другие варианты, сэндвич-панели ППУ представляют собой многослойную конструкцию, которая состоит из:
- внешних слоев;
- внутреннего наполнителя.
Задача первых элементов – обеспечить прочностные характеристики панели и защитить утеплитель от механического и любого другого разрушающего или ухудшающего свойства воздействия. Исходной заготовкой для внешней защиты являются тонкие металлические листы (порядка 0,5 мм), которые имеют антикоррозионное цинковое или полимерное покрытие. Второй вариант применяется чаще: он способен не только обеспечить срок службы в несколько десятилетий, но и позволяет подобрать любой вариантов цветовых решений.
Металл может иметь гладкий профиль или волну, которая существенно увеличивает прочностные качества и, в зависимости от формы и величины, подразделяет сэндвич-панели на две большие группы – стеновые и кровельные. В производственном процессе также используются специальные составы (праймеры) для соединения пенополиуретана с металлом и непосредственно компоненты, из которых формируется пенный состав ППУ.
Основные этапы производственного цикла
Технология изготовления сэндвич-панелей с ППУ по многим этапам сходна с производством строительных материалов с другим наполнителем, что позволяет заводам использовать уже существующие мощности. Существенное отличие заключается в том, что утеплитель подается в зону монтажа не в готовом виде, а как пена.
Процесс может быть полностью или частично автоматизированным и, в зависимости от комплектаций оборудованием включать:
- подачу металла в рулонах и его размотку с очисткой поверхности от возможных загрязнений;
- придание нужной формы в профилирующих валках;
- нанесение клеевого праймера на разогретую до нужных температур поверхность;
- нанесение предварительно подготовленной пены ППУ (в виде отдельных компонентов) через заливочные головки большого давления;
- прессование на специальном оборудовании – происходит не только надежное соединение трех слоев, но и окончательная реакция компонентов с образованием (и расширением) окончательной пены;
- порезка на мерные длины;
- упаковка и складирование.
Особенностью производства сэндвич-панелей ППУ является то, что пенополиуретан из пены формируется («набирает» эксплуатационные свойства) не моментально, а на протяжении примерно суток – это время изделия должны «отлежаться» при контролируемых температурных режимах – в специальных зонах-охладителях.
Производство и характеристика пенополиуретана из простой смеси касторового масла, сырого глицерина и необработанного лигнина в виде полиолов на биологической основе
https://doi.org/10.1016/j.eurpolymj.2016.10.012Получение прав и содержаниеОсновные моменты
- •
Остаточные биополиолы были использованы для синтеза полужестких пенополиуретанов.
- •
Различное содержание лигнина, касторового масла и глицерина реагировало с MDI.
- •
Пены с 17.5% лигнин показал наилучшие размерные и термические свойства.
- •
Исследовали содержание касторового масла, соотношение NCO / OH и тип вспенивателя.
- •
В результате этого простого процесса были получены пены с хорошими свойствами для промышленного применения.
Реферат
Пенополиуретаны на основе биополиолов были исследованы для производства экологически чистых материалов из промышленных отходов биомассы. Полужесткие пенополиуретаны были синтезированы из физических смесей лигнина kraft , касторового масла и остаточного глицерина.Оценено влияние различного содержания лигнина (10, 12,5, 15, 17,5, 20, 25, 30 и 40%) на свойства пены. При увеличении количества лигнина наблюдались увеличение плотности и снижение термической стабильности. Пена, синтезированная с 17,5% лигнина, показала лучшие размерные и термические свойства, а также лучшую однородность ячеек, и этот состав был выбран для дальнейшего исследования влияния содержания касторового масла, молярного отношения изоцианат / гидроксил (NCO / OH) и продувки. тип агента.Повышенная плотность пены и прочность на сжатие наблюдались при повышенном содержании касторового масла в пенах. Подобные результаты наблюдались при увеличении молярного отношения NCO / OH из-за большего количества реакций сшивания. Оценка эффекта вспенивающего агента показала, что при использовании циклопентана и n -пентана пены показали более высокую плотность и более низкую прочность на сжатие по сравнению с пенами, синтезированными с помощью химического вспенивающего агента (воды).
Этот результат можно объяснить более быстрым улетучиванием этих органических вспенивающих агентов, что приводит к образованию ячеек меньшего размера по сравнению с CO 2 , образующимся в результате реакции воды с изоцианатом.Зеленые пенополиуретаны с хорошими свойствами и промышленным интересом были произведены с использованием смеси остаточного сырья (глицерина и лигнина) и касторового масла в качестве полиолов на биологической основе.
Ключевые слова
Пенополиуретан
Лигнин
Неочищенный глицерин
Касторовое масло
Рекомендуемые статьиЦитирующие статьи (0)
Полный текст© 2016 Elsevier Ltd. Все права защищены.
Рекомендуемые статьи
Цитирующие статьи
Разработка одностадийного процесса производства пенопластовых древесностружечных плит с использованием жесткого пенополиуретана :: BioResources
Шалбафан, А., Чайдарре, К. К., и Веллинг, Дж. (2016). «Разработка одностадийного процесса производства пенопластовых древесностружечных плит с использованием жесткого пенополиуретана», BioRes.
Abstract
Смоделированный одностадийный процесс был разработан для производства пенопластовых древесностружечных плит с использованием жесткого полиуретана в качестве внутреннего слоя. Результаты показали, что различные методы, используемые для разделения поверхностного слоя (несмолированные частицы и распыленная вода) и впрыскивания пены (открытая система и закрытая система), не влияли на характеристики панелей.На механические свойства (например, прочность на изгиб и прочность внутреннего скрепления) в основном влияла толщина поверхностного слоя, в то время как на водопоглощение и извлечение краевого винта влияла структура ячеек пены. Использование распыленной воды для отделения поверхностного слоя удвоило эмиссию формальдегида (FE) панелей. Добавление мочевины (из расчета 10% сухой смолы) к распыляемой воде имело положительный эффект снижения конечного FE. Более того, увеличение толщины поверхностного слоя имело прямую линейную связь с FE.
Скачать PDF
Полная статья
Разработка одностадийного процесса производства древесностружечных плит с пенопластом с использованием жесткого пенополиуретана
Али Шалбафан, a, * Камран Чупани Чайдарре, a и Йоханнес Веллинг b
Моделируемый одностадийный процесс был разработан для производства пенопластовых древесностружечных плит с использованием жесткого полиуретана в качестве внутреннего слоя. Результаты показали, что различные методы, используемые для разделения поверхностного слоя (несмолированные частицы и распыленная вода) и впрыскивания пены (открытая система и закрытая система), не влияли на характеристики панелей.Механические свойства (, например, прочность на изгиб и прочность внутреннего скрепления) в основном зависели от толщины поверхностного слоя, в то время как на водопоглощение и отрыв краевого винта влияла структура ячеек пены. Использование распыленной воды для отделения поверхностного слоя удвоило эмиссию формальдегида (FE) панелей. Добавление мочевины (из расчета 10% сухой смолы) к распыляемой воде имело положительный эффект снижения конечного FE. Более того, увеличение толщины поверхностного слоя имело прямую линейную связь с FE.
Ключевое слово: ДСП; Легкий; Бутерброд; Полиуретан; Жесткая пена
Контактная информация: a: Кафедра науки и технологии древесины и бумаги, Факультет природных ресурсов и морских наук, Университет Тарбиат Модарес, Нур, Иран; b: Институт исследований древесины Тюнена, 21031 Гамбург, Германия; * Автор, ответственный за переписку: [email protected]
ВВЕДЕНИЕ
Многослойные конструкции демонстрируют многообещающие легкие характеристики для использования в морской и авиационной промышленности и используются на протяжении десятилетий (Gruenewald et al .2015). Кроме того, легкие плиты значительно снижают общие выбросы парниковых газов (Feifel et al .2013). Использование сэндвич-стратегии в мебельной промышленности недостаточно развито из-за трудоемких производственных методов, которые по-прежнему препятствуют широкому применению. Вторым важным этапом производства многослойных конструкций является соединение сборных обшивок и легкого внутреннего слоя. Основными методами производства (которые уже представлены на рынке) являются либо периодический процесс, когда предварительно изготовленные слои склеиваются и собираются вместе, либо процесс, при котором вспенивающая жидкость для формирования материала сердцевины вводится между двумя предварительно изготовленными лицевыми слоями ( Аллен 1969; Ли и др. .2014). Недостатками этих процессов являются отсутствие одновременного изготовления всех слоев вместе и некоторые ограничения в отношении технологий производства.
Среди всех процессов одностадийный процесс ( вспенивания на месте, ) демонстрирует большой потенциал для упрощения производственного процесса, а также соединения сэндвич-оболочек и сердцевины (Zenkert 1997). Луедтке (2011) и Шалбафан и др. . (2012) показали, что одностадийный процесс формирования многослойных структур имеет большой потенциал для производства легких вспененных древесностружечных плит. Характеристики материалов внутреннего слоя, , например , их термореактивная или термопластичная природа, создают проблемы в одностадийном производственном процессе. В случае термопластичных материалов внутреннее охлаждение для стабилизации панели необходимо на заключительной стадии производства пресса. Шалбафан и др. . (2012) упомянули, что материалы внутреннего слоя должны иметь расширяемую твердотельную гранулированную форму для использования в одноэтапном процессе производства пенопластовых древесностружечных плит.С другой стороны, использование термореактивных вспененных материалов в качестве материалов внутреннего слоя не требует внутреннего охлаждения, но такие материалы (расширяемые термореактивные твердые гранулы), которые отвечают требованиям одностадийного производственного процесса, еще не доступны на рынке.
Полиуретан (ПУ) — это полимер, состоящий из органических звеньев, соединенных уретановыми связями. Большинство используемых полиуретанов представляют собой термореактивные полимеры, которые не нужно охлаждать для стабилизации (Sonnenschein and Koonce 2012). ПУ обычно образуются в результате реакции между компонентами полиола (ПО) и изоцианата (ISO) и имеют жидкую фазу перед вспениванием, что представляет проблему для вспенивания in-situ на месте. Различные пенополиуретаны (мягкие, эластомерные и жесткие) могут быть произведены в зависимости от типа полиолов, используемых для изготовления пенопласта (Ionescu 2005). Полиолы с числом ОН от 300 до 500 предпочтительно используются для изготовления жестких пенополиуретанов, которые представляют собой простые полиэфирполиолы и полиэфирполиолы. Жесткие пенополиуретаны можно производить в диапазоне плотности от 40 до 1000 кг / м 3 , в зависимости от их полиольной структуры.Более низкая плотность (<60 кг / м 3 ) подходит для изоляционных материалов, в то время как более высокая плотность (> 500 кг / м 3 ) подходит для декоративных применений (Ionescu 2005). Пенополиуретан высокой плотности может иметь отличные характеристики в различных областях применения, но эффект легкости, необходимый для сэндвич-структур, больше не существует в этих пенопластах.
Чтобы получить легкие панели на древесной основе, средний слой должен иметь значительно меньшую плотность (<300 кг / м 3 ), чем обычные панели.Когда плотность внутреннего слоя ниже, достигается формирование более легких панелей. Смесь двух различных полиолов (используемых для изоляционных и декоративных целей) может обеспечить легкость конструкции и отличные характеристики пены.
В этом исследовании два разных полиола, один из которых обычно используется для изоляции, а другой — для декоративных целей, были смешаны вместе, чтобы получить желаемую плотность пены и лучшую удобоукладываемость. Целью данного исследования является производство древесностружечных плит из пенопласта в моделируемом одностадийном процессе (с учетом проблем, упомянутых выше) с использованием жесткого полиуретана в качестве внутреннего слоя.Для моделирования одноэтапного производственного процесса необходимо использовать методы разделения поверхностных слоев. Таким образом, были изучены эффекты различных методов, используемых для разделения поверхностного слоя и впрыска пены в смоделированном одностадийном процессе. Также были проанализированы механические и физические свойства изготовленных таким образом панелей.
ЭКСПЕРИМЕНТАЛЬНАЯ ИНФОРМАЦИЯ
Материалы
Обычные мелкие частицы древесины, в основном бука и тополя (≤ 2 мм), использовались для облицовочных слоев и поставлялись местным заводом по производству древесно-стружечных плит в Иране.Частицы смешивали со смолой на основе формальдегида мочевины (UF) (12%) (Amol Resin Ltd., Иран) и сульфатом аммония (1%) в качестве отвердителя. Смола UF имела содержание твердого вещества и pH 62% и 7,1 соответственно. Целевая плотность поверхностного и нижнего слоев поддерживалась постоянной на уровне 700 кг / м 3 . Толщина поверхностного слоя варьировалась (3, 4 и 5 мм для каждого из двух лицевых слоев), соответственно, изменялась и соответствующая плотность панели (300, 370 и 440 кг / м 3 ).
Смесь простого полиэфира (Kupa 501) и сложных полиэфирполиолов (Kupa 150) смешивали с полимерным метилендифенилдиизоцианатом (pMDI) для получения центрального слоя. Используемые химические вещества были поставлены компанией Jazb Setareh Co., Иран. Заданная плотность подготовленного внутреннего слоя поддерживалась постоянной на уровне 120 кг / м 3 .
Подготовка образца для испытаний
Пенопластовые древесно-стружечные плиты (толщиной 19 мм) были произведены в смоделированном одностадийном процессе, состоящем из четырех последовательных стадий. Панели были изготовлены с различной толщиной поверхностного слоя 3, 4 и 5 мм, и, соответственно, внутренний слой пенопласта варьировался по толщине 13, 11 и 9 мм соответственно.Процесс, использованный в этом исследовании, описан на рис. 1. В идеальном промышленном одностадийном производственном процессе используются четыре последовательных этапа: уплотнение поверхностного слоя, разделение поверхностного слоя, впрыскивание пены и стабилизация панели. Можно констатировать, что наиболее сложными этапами являются разделение поверхностного слоя и нагнетание пены. Следовательно, были применены различные методы разделения слоев и впрыска пены, чтобы определить их эффект на таких сложных этапах.
Фиг.1. Разработка технологии производства пенопластовых древесностружечных плит в промышленных масштабах |
Иллюстрированный одностадийный производственный процесс (рис. 1) был сначала смоделирован в лабораторном масштабе. Для начала два поверхностных слоя (после смола частиц и формирования мата) уплотняли до отверждения УФ-смолы (в конце секции прессования). Затем поверхностные слои были разделены в лабораторном масштабе благодаря использованным методам разделения. После формирования нижнего слоя и перед формированием лицевого слоя применялись различные методы разделения с использованием либо несмолистых древесных частиц, либо метода распыления воды.Обычные мелкие несмолистые частицы древесины (400 г / м 2 ) использовали в качестве разделительного материала между двумя слоями. Количество распыленной воды поверх нижнего слоя составляло 60 г / м 2 , чтобы образовалась паровая масса (на стадии подготовки поверхностных слоев) между двумя слоями для разделения слоев. Более высокое количество распыляемой воды могло бы повлиять на образование пены и связь между лицевыми и сердцевинными слоями. Следовательно, необходимо поддерживать как можно более низкий уровень распыляемой воды.Для удаления несмолистых древесных частиц или плохо связанных частиц между поверхностью и нижним слоем, после отделения поверхностного слоя, но до стадии впрыска пены, использовался отсос (пылесос).
На этапе впрыска пены также использовались два разных метода; Для этого использовался либо деревянный каркас (закрытая система), либо четыре небольших деревянных кубика (открытая система). Высота деревянного каркаса и деревянных кубиков была такой же, как толщина слоя пенопласта (13, 11 или 9 мм), и они располагались поверх нижнего слоя.Затем смесь компонентов пены впрыскивалась (заливалась) на нижний слой и, соответственно, сразу на него укладывался верхний поверхностный слой. После этого вся сборка была помещена на второй пресс (без зон нагрева), чтобы сохранить желаемую толщину панели (стабилизация панели). Рисунок 2 иллюстрирует смоделированный одностадийный процесс производства пенопластовых панелей в лабораторном масштабе.
Таблица 1 показывает состав переменных панели.Чтобы подтвердить влияние методов разделения лицевого слоя на свойства панелей, контрольные образцы (с использованием периодического процесса) также были изготовлены без каких-либо методов разделения (где каждый поверхностный слой был изготовлен отдельно).
Таблица 1. Технологии производства древесностружечных плит с пенопластом
* Не смолистые древесные частицы, используемые между нижним и поверхностным слоями.
** Распыляемая вода, используемая поверх нижнего слоя.
Составы пены
Полиол простого полиэфира на нефтяной основе (Kupa 501) и полиол сложного полиэфира (Kupa 150) использовали после определения их гидроксильного числа (450 мг КОН / г и 306 мг КОН / г, соответственно) и содержания воды (0,15% и 0,1% соответственно. ). Сводка типичных физических и химических свойств обоих полиолов (от поставщиков) приведена в таблице 2. Химические вещества: полимерный метилендифенилдиизоцианат (pMDI), кремниевое поверхностно-активное вещество — полисилоксановый эфир, катализатор — диметилциклогексиламин и вспенивающий агент — ГФУ R-141b использовался в полученном виде.Содержание групп NCO в pMDI составило 31% (согласно паспорту поставщика).
Таблица 2. Физико-химические свойства полиолов
* Ароматический полиэфирный полиол.
** Значения, проверенные экспериментально.
Таблица 3. Составы и реакционная способность жестких пенополиуретанов
Методика приготовления жесткого пенополиуретана представлена в таблице 3. Он был приготовлен двухэтапным методом.Полиолы смешивали с катализатором, поверхностно-активным веществом и вспенивающим агентом для получения гомогенной смеси в соответствии с процедурой приготовления. Затем смесь полиолов смешивали с pMDI (приблизительно 10 с) перед инъекцией. Данные о реакционной способности жесткого пенополиуретана были получены в ходе «чашечного теста» и представлены в таблице 3 (Ionescu 2005).
Характеристики панелей
Чтобы охарактеризовать новые произведенные панели и изучить влияние различных методов разделения слоев и инъекции полиуретана, а также влияние толщины поверхностного слоя, были проведены механические и физические испытания.Прочность на изгиб (EN 310 (1993)), внутренняя прочность сцепления (EN 319 (1993)) и сопротивление выдергиванию торцевого / краевого винта (EN 13446 (2002)) были определены в качестве основных механических свойств. Физическое поведение (EN 317 (1993)) панелей было охарактеризовано путем измерения разбухания по толщине и тенденции водопоглощения после длительного выдерживания (до 786 ч после погружения в воду). Для каждого варианта панели готовили по три повтора. Случайным образом были отобраны и протестированы три образца из каждой повторности ( n = 9). Перед испытанием все образцы кондиционировали в климатической камере при относительной влажности 65% и температуре 20 ° C до достижения постоянной массы. Физические испытания проводились на неотшлифованных образцах.
Измерение выбросов формальдегида
Чтобы лучше понять свойства этих новых древесностружечных плит из вспененного материала, было проведено испытание на выброс формальдегида. Влияние толщины поверхностного слоя и распыляемой воды (для разделения слоев) на выделение формальдегида панелями было исследовано с использованием колбового метода (EN717-3 (1996)).Раствор мочевины и воды использовался для распыления в качестве метода разделения поверхностного слоя для контроля эмиссии формальдегида. Количество использованной мочевины составляло приблизительно 10% в расчете на твердое содержание смолы в одном лицевом слое. Более подробная информация о вариантах панелей, используемых для выделения формальдегида, представлена в таблице 4.
Таблица 4. Переменные панели , используемые для измерения выбросов формальдегида
* Каждый поверхностный слой изготавливали отдельно (контрольный образец).
** Для разделения поверхностных слоев использовали раствор мочевины и воды.
Статистический анализ
Двусторонний дисперсионный анализ (ANOVA) механических и физических свойств был выполнен с помощью статистического пакета для программного обеспечения социальных наук (программное обеспечение SPSS, IBM, США). Статистические различия между вариациями оценивались путем множественных сравнений на основе теста Дункана из-за однородности вариаций. Парный T-тест также использовался для сравнения различных значений техники разделения и закачки.Статистическая значимость была установлена на уровне P <0,05.
РЕЗУЛЬТАТЫ И ОБСУЖДЕНИЕ
Влияние методов разделения поверхностных слоев
Одним из наиболее важных этапов в разработке одностадийного процесса производства панелей с пенопластом является разделение поверхностного и нижнего слоев для впрыска пены. На рис.3. Значения обоих свойств (MOR и IB) для метода несмолистых частиц были немного выше, чем для метода распыления воды, но такие различия не были обнаружены статистически значимыми. На прочность на изгиб в основном влияли плотность панели и качество поверхностного слоя, которое было почти одинаковым для обоих типов панелей. На величину внутреннего сцепления в панелях с пенопластом влияло качество поверхности раздела (лицевой и сердцевинный слой) (Shalbafan et al .2013b).В случае метода распыления воды между поверхностным и нижним слоями образовывалась масса водяного пара, которая влияет на отверждение УФ-смолы на частицах, образующих внутренние стороны лицевых слоев. Слабые внутренние поверхности приводят к снижению значений прочности внутреннего сцепления. Кроме того, более высокое содержание влаги в мате (в случае распыления воды) может также привести к уменьшению сшивки клея и, соответственно, к ослаблению характеристик склеивания (Roffael 1993).
Фиг.![]() |
Сравнение панелей, полученных с помощью смоделированного одноэтапного процесса, с панелями, произведенными в периодическом процессе (контрольные образцы), представлено на рис. 3. Результаты показали, что контрольные образцы имели значительно более высокие значения MOR и IB, чем те, которые производятся непрерывными процессами. Как упоминалось ранее, качество поверхностного слоя из-за более плотного поверхностного слоя было причиной более высоких значений MOR в контрольных образцах.Для изготовления контрольных образцов не использовалась методика разделения. Следовательно, отсутствие слабосвязанных частиц привело к лучшей адгезии с компонентами пены. Некоторые слабые и плохо связанные частицы всегда будут присутствовать на внутренних поверхностях слоев в случае несмолистых древесных частиц и методов разделения водяным распылением, которые влияют на значения внутреннего сцепления. Этих слабых частиц не было в контрольных образцах. Хотя эталонные образцы имели более высокие MOR и IB, чем у панелей с пенопластом, они не могут быть одобрены в мебельной промышленности из-за процесса серийного производства (Shalbafan et al .2013b).
Следует отметить, что минимальные требования к значениям IB согласно EN312 / P2 были достигнуты для всех вариантов панели. Хотя MOR почти на 30 процентов меньше, чем EN312 / P2 для панелей, произведенных с помощью разработанного одноэтапного процесса, он все еще находится в желательном диапазоне для специальных применений.
Влияние методов разделения поверхностного слоя на извлечение торцевого винта (FSW) и извлечение краевого винта (ESW) представлено на рис. 4. Результаты показали, что методы разделения не оказали значительного влияния на FSW и ESW.На FSW влияло качество поверхностного слоя, которое было почти одинаковым для обоих методов. На ESW повлияли структуры пены, которые также были одинаковыми для обоих методов из-за схожего состава пены.
FSW контрольных образцов был значительно выше, чем у панелей, изготовленных с помощью одностадийного производственного процесса, поскольку они имели лучшее качество поверхности и нижнего слоя. ESW существенно не изменился на контрольных образцах, поскольку компоненты пены оставались постоянными во всех вариантах панели.
Рис. 4. Влияние техники разделения поверхностных слоев на извлечение торцевых и краевых винтов |
Влияние методов впрыска пены
Два разных метода (закрытая и открытая системы) использовались для впрыскивания пены между разделенными слоями. Влияние методов впрыска на прочность на изгиб и значения внутренней связи было проиллюстрировано на рис. 5. Результаты показали, что различные системы впрыска не влияют на прочность на изгиб и значения прочности внутренней связи.Следует отметить, что впрыскиваемая (залитая) пенная смесь не выливалась со сторон образца в случае открытого впрыска из-за высокой вязкости и очень короткого времени вспенивания (25 с) пенной смеси. Кроме того, визуальное наблюдение показало, что смесь ПУ в основном перемещалась в направлении высоты (направлении подъема), а ее боковые перемещения были довольно низкими. Полимерный изоцианат (pMDI) добавляли только к смеси полиолов перед инъекцией. Смесь перемешивали примерно 10 с и сразу выливали поверх нижнего слоя.Сливание смеси происходило сразу после заливки (впрыска) пены, излияния пены не наблюдалось. В конечном итоге можно предположить, что системы впрыска пены не оказывают существенного влияния на процесс вспенивания и, соответственно, на свойства панели.
Рис. 5. Влияние технологий впрыска пены на значения прочности на изгиб и прочности внутреннего сцепления |
На рис. 6 представлены результаты значений отвода торцевых и краевых винтов для панелей, изготовленных с использованием различных систем впрыска пены.
Рис.![]() |
Результаты показали, что значения FSW и ESW не сильно изменились при изменении систем впрыска пены. Значения торцевых винтов в основном зависят от качества поверхностных слоев, которое было одинаковым для обоих вариантов (Shalbafan et al . 2013b). Значения краевого винта зависят от процедуры вспенивания и полученной структуры пены.Таким образом, можно сделать вывод, что структура пены в обеих системах впрыска практически одинакова, поскольку значения ESW были почти сопоставимы.
Влияние толщины слоя
Плотность панели и содержание влаги в панелях после двух недель кондиционирования (при 20 ° C и относительной влажности 65%) представлены в таблице 5. Толщина панели оставалась постоянной (19 мм), в то время как толщина поверхностного слоя увеличивалась с От 3 до 5 мм. Следовательно, плотность панели была увеличена за счет увеличения толщины поверхностного слоя с 3 (302 кг / м 3 ) до 5 мм (439 кг / м 3 ). Влагосодержание было выше в панелях с более толстыми поверхностными слоями, потому что в более толстых панелях содержится больше гигроскопичных материалов.
Таблица 5. Плотность панели и содержание влаги
* Цифры в скобках — стандартное отклонение
Влияние толщины поверхностного слоя на свойства панели (MOR и IB) показано на рис. 7. Значения MOR немного увеличились с 9,5 МПа для панелей толщиной 3 мм до 10,5 МПа для слоев поверхности панелей толщиной 5 мм. Толщина, плотность и структура каждого слоя пенопластовых панелей были наиболее важными факторами, влияющими на прочность на изгиб (Vinson 2005; Link et al .2011). Плотность панелей была увеличена за счет увеличения толщины поверхностного слоя с 3 мм (300 кг / м 3 ) до 5 мм (440 кг / м 3 ). Эта увеличенная плотность панели привела к увеличению прочности на изгиб. Также можно заметить, что древесина стала жестче и прочнее, чем материал полимерного сердечника. Утолщение поверхностных слоев сопровождалось уменьшением толщины внутреннего слоя пенопласта с 13 до 9 мм, и, соответственно, были получены более высокие значения MOR. Чен и Ян (2012) также обнаружили, что уменьшение толщины сердцевины поверхностного слоя привело к увеличению изгибных свойств сэндвич-панелей.
Значения внутренней прочности связи снизились при увеличении толщины поверхностного слоя с 3 мм (0,46 Н / мм 2 ) до 5 мм (0,17 Н / мм 2 ). Шалбафан и др. . (2012) отметили, что преобладающим фактором, влияющим на значения прочности внутреннего сцепления панелей из пенопласта, является качество границы раздела лицевой и сердцевинной частей. Образцы, приготовленные с толщиной грани 3 мм, разрушились в лицевом слое в непосредственной близости от границы раздела, а для образцов с толщиной грани 5 мм разрушение произошло в середине поверхностных слоев.Как упоминалось ранее, масса водяного пара, образующаяся между поверхностным и нижним слоями, влияет на сшивание клея и, соответственно, дополнительно ослабляет характеристики склеивания в более толстых поверхностных слоях (Roffael 1993).
Рис. 7. Влияние толщины поверхностных слоев на прочность на изгиб и значения внутреннего сцепления |
Значения отвода торцевых и краевых винтов для панелей с разной толщиной поверхностного слоя показаны на рис.8. Результаты показали, что FSW линейно увеличивается с увеличением толщины поверхностного слоя. FSW увеличивается почти до 30% на каждый дополнительный миллиметр толщины поверхностного слоя. Значения извлечения краевого винта существенно не изменились, и значения ESW, безусловно, также зависели от состава пены, но они оставались постоянными для всех вариантов панели.
Рис. 8. Влияние толщины поверхностного слоя на отвод торцевых и краевых винтов |
Влияние толщины поверхностного слоя на набухание толщины и водопоглощение при времени выдержки до 786 ч представлено на рис.9. Значения набухания по толщине были выше для панелей с более толстыми поверхностными слоями. Значения TS почти достигают максимального уровня (от 5% до 7%) примерно через 48 часов замачивания. Впоследствии увеличение TS было чрезвычайно снижено до достижения 786 ч времени выдержки, в то время как TS существенно не изменилась. На TS панелей с пенопластом влияет толщина поверхностного слоя (Luedtke 2011). Похоже, что деревянные частицы были насыщены после короткого времени (48 часов) замачивания, и это состояние не меняется при продлении замачивания до 786 часов (Shalbafan et al .2013а). Следует также учитывать, что внутренний слой пенопласта не влияет на набухание по толщине из-за его гидрофобной природы.
На рис. 9В показаны значения водопоглощения панелей. Значения водопоглощения (WA) значительно увеличились при увеличении толщины лицевого слоя с 3 до 5 мм. Значения WA также неуклонно увеличивались для всех панелей во время замачивания (от 2 до 786 ч), но скорость поглощения воды изменялась во время погружения. Интенсивное впитывание можно наблюдать в течение начального периода замачивания (48 часов), а при более длительном времени замачивания (от 48 до 786 часов) наблюдается почти линейная тенденция.Большая часть воды (> 60%) была впитана в начальный период (48 ч) замачивания. На значения WA в панелях с пенопластом влияли поверхностный слой (толщина и плотность) и структура ячеек пены (пустоты между ячейками и раздробленные ячейки) (Sabbahi and Vergnaud 1993; Link et al .2011). Следовательно, сравнивая части A и B на фиг.9, можно констатировать, что поверхностные слои являются преобладающими факторами, влияющими на WA в течение начального периода выдержки (48 часов). Вода в основном поглощается как пустотами между ячейками пены, так и раздробленными ячейками при более длительном времени замачивания (от 48 до 786 часов).Также стоит упомянуть, что WA не прекращалась даже после 786 часов выдержки, что показывает, что вода медленно, но неуклонно проникает во внутренние пустоты образцов (Schwartz и др.
, 1989).
Измерение выбросов формальдегида
Эмиссия формальдегида (FE) из панелей из пенопласта была определена колбовым методом, как показано на рис. 10. Результаты показали, что FE линейно увеличивается при увеличении толщины поверхностного слоя с 3 до 5 мм (коды C, D, и E).Каждый дополнительный миллиметр толщины поверхностного слоя приводит к увеличению FE на 19%. Более высокое количество древесных частиц и смолы, используемой для увеличения толщины поверхностного слоя, приводит к более высокому выбросу формальдегида (Petersen et al . 1972).
Использование методов разделения поверхностного слоя (, например, , распыление воды или несмолистые частицы) является одним из наиболее важных этапов производства в одностадийном процессе производства панелей с пенопластом. Следовательно, чтобы понять влияние методов разделения (распыление воды) на FE, панель, полученная в результате одноэтапного процесса (код C), сравнивали с эталонной панелью (код F). Результаты показали, что КЭ панелей, изготовленных в смоделированном одноэтапном процессе, почти удвоился по сравнению с КЭ контрольных панелей. Причину этого можно увидеть в разбрызгиваемой воде (60 г / м 2 ), используемой для разделения поверхностного слоя. Петерсен и др. . (1972) заявили, что содержание влаги в мате из ДСП влияет на КЭ производимых панелей. Для контроля эмиссии формальдегида изготовленных панелей был применен раствор мочевины и воды (код K) для разделения поверхностного слоя.Сравнение кодов C и K показало, что добавление мочевины снизило вдвое (примерно на 50%) КЭ панелей, изготовленных в одностадийном производственном процессе. Мочевина является одним из наиболее эффективных и в то же время самых дешевых поглотителей формальдегида на рынке (Ashaari и др. . 2016; Boran и др. . 2011). Колочный метод подходит только для внутреннего контроля производства древесных плит. Следовательно, официальных предельных значений не публиковалось.
Фиг.10. Эмиссия формальдегида панелями из пенопласта |
ВЫВОДЫ
- Это исследование показало, что древесностружечные плиты из пенопласта с использованием жесткого полиуретана в качестве внутреннего слоя могут быть произведены в смоделированном одностадийном производственном процессе.
- Исследование показало, что методы производства (методы разделения и впрыска) не оказывают существенного влияния на характеристики панелей, но свойства панелей эталонных панелей и панелей, полученных с помощью смоделированного процесса, значительно различались.Значения MOR, IB и FSW были значительно выше в контрольных панелях из-за лучшего качества их поверхностного слоя.
- Увеличение толщины поверхностного слоя (с 3 до 5 мм) увеличивает значения MOR и FSW и приводит к значительному снижению IB. TS и WA также были увеличены за счет увеличения толщины поверхностных слоев.
- TS и WA были интенсивными в течение начального периода замачивания (48 ч), а затем замедлились. Результаты показали, что поверхностные слои были почти насыщенными после начального времени выдержки, что отражалось в чрезвычайно низком TS после начального времени выдержки.Однако вода все еще абсорбировалась в конце времени выдержки (до 786 ч), потому что она мигрировала в пустоты между ячейками пены.
- Увеличение толщины поверхностного слоя приводит к увеличению КЭ образцов. Распыляемая вода в качестве метода разделения почти вдвое увеличивает КЭ из образцов, что можно контролировать, добавляя мочевину в разбрызгиваемую воду.
- В целом ДСП из пенополиуретана показали хороший потенциал для использования в мебельной промышленности. Дальнейшие исследования в рецептуре полиуретана потребуются для улучшения структуры пены, которая, соответственно, может повлиять на характеристики панели.
БЛАГОДАРНОСТИ
Авторы выражают признательность Иранскому национальному научному фонду (INSF) за финансовую поддержку этого исследования в рамках гранта № 93012950.
ССЫЛКИ
Аллен, Х. Г. (1969). Анализ и проектирование структурных сэндвич-панелей , Pergamon Press, Оксфорд, Великобритания.
ASTM D4672 — 12 (2012). «Стандартные методы испытаний полиуретанового сырья: определение содержания воды в полиолах», ASTM International, West Conshohocken, PA, USA.
ASTM D4699-03 (2013). «Стандартный метод испытания плотности вибрационной упаковки крупных сформированных частиц катализатора и носителя катализатора», ASTM International, West Conshohocken, PA, USA.
ASTM D4890 — 13 (2013). «Стандартные методы испытаний полиуретанового сырья: определение цвета по Гарднеру и APHA полиолов», ASTM International, Вест Коншохокен, Пенсильвания, США.
ASTM D4878-15 (2015). «Стандартные методы испытаний полиуретанового сырья: определение вязкости полиолов», ASTM International, West Conshohocken, PA, USA.
ASTM D4274-16 (2016). «Стандартные методы испытаний полиуретанового сырья: определение гидроксильных чисел полиолов», ASTM International, West Conshohocken, PA, USA.
Ашаари, З., Ли, А. М. Х., Азиз, М. Х. А., и Нордин, М. Н. (2016). «Добавление гидроксида аммония в качестве поглотителя формальдегида для древесины сесендук ( Endospermum diadenum ), компрегнированной фенольными смолами», Eur. Дж. Вуд Вуд Прод . 74 (2), 277-280. DOI: 10.1007 / s00107-015-0995-9
Боран, С., Уста М., Гемуеская Е. (2011). «Снижение выбросов формальдегида из древесноволокнистых плит средней плотности, произведенных путем добавления различных аминовых соединений к карбамидоформальдегидной смоле», Int. J. Adhes. Клеи. 31 (7), 674-678. DOI: 10.1016 / j.ijadhadh.2011.06.011
Чен, З., Янь, Н. (2012). «Исследование модулей упругости сэндвич-панелей с сотовым заполнителем из крафт-бумаги», Compos. Часть B-англ. 43, 2107-2114. DOI: 10.1016 / j.compositesb.2012.03.008
EN 310 (1993).«Панели на основе древесины — Определение модуля упругости при изгибе и прочности на изгиб», Европейский комитет по стандартизации, Брюссель, Бельгия.
EN 310 (2010). «ДСП. Технические условия », Европейский комитет по стандартизации, Брюссель, Бельгия.
EN 317 (1993). «ДСП и древесноволокнистые плиты — определение разбухания по толщине после погружения в воду», Европейский комитет по стандартизации, Брюссель, Бельгия.
EN 319 (1993). «ДСП и древесноволокнистые плиты — Определение прочности на разрыв перпендикулярно плоскости плиты», Европейский комитет по стандартизации, Брюссель, Бельгия.
EN 323 (1993). «Древесные плиты — определение плотности», Европейский комитет по стандартизации, Брюссель, Бельгия.
EN 320 (1993). «ДВП. Определение сопротивления осевому извлечению винта », Европейский комитет по стандартизации, Брюссель, Бельгия.
EN 717-3 (1996). «Панели на древесной основе. Определение высвобождения формальдегида — Часть 3: Высвобождение формальдегида методом колбы », Европейский стандарт, Брюссель, Бельгия.
EN 13446 (2002).«Панели на древесной основе. Определение выносливости крепежа », Европейский стандарт, Брюссель, Бельгия.
Фейфель, С., Поганиц, В. Р., Шебек, Л. (2013). «Использование легких плит для снижения выбросов в атмосферу в деревообрабатывающей промышленности Германии — перспективы?», Environ. Sci. Евро. 25, 5. DOI: 10.1186 / 2190-4715-25-5
Грюневальд Дж., Парлевлит П. и Альтштадт В. (2015). «Производство термопластичных композитных сэндвич-конструкций; Обзор литературы », J.Термопласт. Compos . DOI: 10.1177 / 0892705715604681
Ионеску, М. (2005). Химия и технология полиолов для полиуретанов , Rapra Technology Limited, Великобритания.
Ли Дж., Хант Дж. Ф., Гонг С. и Цай З. (2014). «Высокопрочные сэндвич-панели на основе дерева, армированные стекловолокном и пеной», BioResources 9 (2), 1898-1913. DOI: 10.15376 / biores.9.2.1893-1913
Линк, М., Колбич, Ч, Тонди, Г., Эбнер, М., Виланд, С., и Петучниг, А.(2011). «Пены на основе танинов без формальдегида и их использование в качестве легких панелей», BioResources 6 (4), 4218-4228. DOI: 10.15376 / biores.6.4.4218-4228
Людтке Дж. (2011). «Разработка и оценка концепции непрерывного производства легких панелей, включающих полимерный сердечник и древесные панели», докторская диссертация , Гамбургский университет, Гамбург, Германия.
Петерсен, Х., Ройтер, В., Эйзеле, В., и Виттманн, О. (1972). «Zur Formaldehydeab-spaltung bei der Spanplattenerzeugung mit Harnstoff-Formaldehyde-Bindermitteln», Holz Roh Werkst. 31 (12), 463-469. DOI: 10.1007 / BF02613831
Э. Роффаэль (1993). Формальдегид из ДСП и других деревянных панелей , Институт лесных исследований Малайзии (FRIM), Куала-Лумпур, Малайзия.
Саббахи А. и Верно Ж. М. (1993). «Поглощение воды пенополиуретаном. Моделирование и эксперименты », евро. Polym. J. 29 (9), 1243-1246. DOI: 10.1016 / 0014-3057 (93) -9
Shalbafan, A., Welling, J., and Luedtke, J. (2012). «Влияние параметров обработки на механические свойства сэндвич-панелей с легким пенопластом», Wood Mater. Sci. Англ. 7 (2), 69-75. DOI: 10.1080 / 17480272.2012.661459
Шалбафан А., Веллинг Дж. И Людтке Дж. (2013a). «Влияние параметров обработки на физические и структурные свойства легких сэндвич-панелей с пенопластом», Wood Mater. Sci. Англ. 7 (2), 69-75. DOI: 10.1080 / 17480272.2012.684704
Шалбафан А., Людтке Дж., Веллинг Дж. И Фрювальд А. (2013b). «Физиомеханические свойства сверхлегких пенопластовых древесностружечных плит: разная плотность сердцевины», Holzforschung 67 (2), 169-175.DOI: 10.1515 / hf-2012-0058
Шварц, Н. В., Бомберг, М., и Кумаран, М. К. (1989). «Пропускание водяного пара и накопление влаги в пенополиуретане и полиискоцианурат», ASTM STP 1039, H.R. Trechsel и M. Bomberg (ред.), Американское общество испытаний и материалов, Филадельфия, Пенсильвания, стр. 63-72.
Зонненшайн, М., Кунсе, В. (2012). «Полиуретаны», в: Энциклопедия науки и технологий полимеров , 4 th Ed., H. Mark (ed. ), John Wiley & Sons, Хобокен, Нью-Джерси. DOI: 10.1002 / 0471440264.pst295
Винсон, Дж. Р. (2005). «Сэндвич-конструкции; Прошлое, настоящее и будущее »в: Многослойные конструкции 7; Продвижение сэндвич-конструкций и материалов: материалы 7-й Международной конференции по многослойным конструкциям . О. Т. Томсен, Э. Божевольная и А. Ликегард (ред.), Ольборгский университет, Ольборг, Дания, стр. 29–31.
Зенкерт, Д. (1997). Введение в сэндвич-конструкцию , Engineering Material Advisory Services Ltd., Крэдли Хит, Великобритания.
Статья подана: 12 июля 2016 г .; Рецензирование завершено: 4 сентября 2016 г .; Доработанная версия получена и принята: 5 сентября 2016 г .; Опубликовано: 22 сентября 2016 г.
DOI: 10.15376 / biores.11.4.9480-9495
Производство вспучивающегося жесткого пенополиуретана
ВВЕДЕНИЕ
Технология предлагает процесс производства пенополиуретана (ППУ), включая подготовку, производство и испытания базовых полиолов (марки PD и AM), изоцианатного компонента и полиэфирного полиола.
СВОЙСТВА ЖЕСТКОЙ ПОЛИУРЕТАНОВОЙ Пены
- Для получения вспучивающегося полукокса при сжигании в соответствии с условиями испытаний печи ASTM E2230
- Иметь частично открытую ячеистую структуру со способностью поглощать энергию при ударе с расстояния 9 м без раскола в соответствии с Регламентом МАГАТЭ
- Для поддержания минимальной скорости тепловыделения (HRR), чтобы выдерживать устойчивую температуру 800 0 C в течение 30 минут
ПРИМЕНЕНИЕ
- Пенополиуретан подходит для защиты от ударов и тепла для транспортных упаковок с радиоактивными / другими материалами весом до 100 кг.
ПРОЦЕСС
Процесс производства пенополиуретана (ППУ) включает производство и тестирование базовых полиолов (марки PD и AM) и последующий состав с катализатором и поверхностно-активными веществами. Изоцианатный компонент, смешанный с составными полиэфирполиолами, используется для производства жесткого пенополиуретана.
Основной полиол получают путем этерификации многоатомных спиртов и кислоты, где реакция проводится в сосуде из нержавеющей стали с рубашкой, с дистилляционным конденсатором и вакуумным устройством.
СЫРЬЕ
- Диэтиленгликоль
- Фталевый ангидрид
- Нонил Фенол
- Соевое масло
- Диэтаноламин
- формальдегид
- Полимерный МДИ (диизоцианид метана)
- полифосфат аммония
Сырье легко доступно на местном рынке.
ИНФРАСТРУКТУРА
Схематическая компоновка приведена на диаграмме
Производство базовых полиэфирполиолов и их последующее приготовление требует регулярного расположения реактора этерификации с конденсатором, нагревателем горячего масла и вакуумным устройством.
Приблизительная требуемая площадь составляет 1000 м 2 2 с промышленной лицензией на производство синтетических полиэфирных полиолов или смол.
Необходимое оборудование:
- Сосуд для реакции этерификации с водяным конденсатором
- Вакуумный насос со сборной емкостью.
- Котел с термическим теплоносителем.
- Емкость для смешивания с заслонкой мешалки.
НЕОБХОДИМАЯ ЧЕЛОВЕКА
- Менеджер — Производство — 1 шт.
- Химик — бакалавр наук — 1 шт.
- Квалифицированный рабочий — 2 шт.
- Полуквалифицированный рабочий — 3 шт.
Пенополиуретаны — Справочник по химической экономике (CEH)
Опубликовано в ноябре 2019 г.
Мировое потребление пенополиуретана будет продолжать неуклонно расти в течение 2018–24 годов; при этом расход жесткой пены увеличивается лишь немного быстрее, чем у эластичной пены.
Основными драйверами роста потребления гибкой пены является производство кроватей и мебели, например диванов и стульев, а также автомобильных сидений.Рост расхода жесткого пенопласта происходит преимущественно за счет утеплителя. Потребление изоляции будет продолжать расти, поскольку требуются более строгие меры по повышению энергоэффективности.
Следующая диаграмма показывает потребление пенополиуретана по основным регионам:
Среди общего потребления пенополиуретана потребление гибких пен на 10–20% больше рынка жестких пен. На Китай и другие страны Азии приходится почти половина мирового потребления пенополиуретана в 2018 году.
Этот отчет дает прекрасное представление о мировом рынке пенополиуретанов с подробной разбивкой концов как гибких пенополиуретанов, так и жестких пенополиуретанов. Он был составлен на основе первичных отраслевых исследований и объединяет элементы других отчетов IHS Markit в «Справочнике по химической экономике» (CEH) и программе обновлений по специальным химическим веществам (SCUP) для полиуретановых цепей, включая диизоцианаты и полиизоцианаты, полиэфирполиолы, полиэфирполиолы и полиуретановые эластомеры.
Для получения более подробной информации см. Приведенное ниже содержание.
Справочник IHS Markit по экономике химической промышленности — Полиуретановые пены — это исчерпывающее и надежное руководство для всех, кто ищет информацию об этой отрасли. В этом последнем отчете представлена глобальная и региональная информация, включая
Ключевые преимущества
Справочник IHS Markit по химической экономике — Полиуретановые пены были составлены на основе первичных интервью с ключевыми поставщиками, организациями и ведущими представителями промышленности в сочетании с беспрецедентным доступом IHS Markit к аналитическим данным рынка в области добычи и сбыта, экспертным анализом динамики отрасли, торговли и экономики.
Этот отчет может помочь вам:
- Определить тенденции и движущие силы, влияющие на химические рынки
- Прогноз и план будущего спроса
- Понять влияние конкурирующих материалов
- Определить и оценить потенциальных клиентов и конкурентов
- Оценить производителей
- Отслеживание изменений цен и торговых движений
- Анализ влияния сырья, нормативных требований и других факторов на рентабельность химической промышленности
Улучшенные методы производства пенополиуретана
Новые поверхностно-активные вещества — результат более экологически безопасного производственного процесса
Метиленхлорид, токсичное химическое вещество, способствующее загрязнению воздуха, недавно было исключено из использования в США.S. полиуретановая промышленность. Это обязательное исключение не позволило производить как можно больше сортов пенопласта с использованием хлористого метилена, что поставило промышленность США в невыгодное положение с точки зрения конкуренции. Air Products and Chemicals, Inc. при финансовой поддержке AMO разработала новые силиконовые поверхностно-активные вещества, позволяющие эффективно производить весь спектр сортов пенопласта с использованием более экологически безопасного вспенивателя CO 2 . Помимо снижения токсичности, новый процесс потребляет меньше энергии и снижает чистый выброс CO 2 , который влияет на глобальное потепление.
Проблемы при использовании жидкого CO 2 в качестве вспенивающего агента включают быстрое испарение, быстрое образование пузырьков и трудности в поддержании мелкопористой структуры в пене. Новые поверхностно-активные вещества решают эти проблемы за счет эмульгирования вспенивающего агента, тем самым сохраняя мелкие ячейки во время вспенивания. Силиконовые поверхностно-активные вещества достигли превосходных характеристик, что привело к более мелкой структуре ячеек (больший выход), большей высоте пучков (больший выход), лучшему градиенту физических свойств сверху вниз (консистенция продукта) и лучшей совместимости с антипиренами.
Воздействие коммерциализированной технологии
2006 | 2007 | 2008 | 2009 | 2010 | 2011 | ||||||
---|---|---|---|---|---|---|---|---|---|---|---|
Энергосбережение (трлн Btu) (трлн БТЕ) 0,087 | 0,103 | 0,117 | 0,129 | | |||||||
Снижение выбросов (тыс. Тонн) | Углерод | 0.421 | 1,452 | 1,549 | 1,834 | 2,075 | 2,281 | ||||
НЕТ x | 0,003 | 0,011 | 0,012 | 9016 0,07 9016 0,07 9016 0,07 | 9016 x | 0,003 | 0,009 | 0,009 | 0,011 | 0,012 | 0,014 |
Твердые частицы | 0.000 | 0,000 | 0,000 | 0,000 | 0,000 | 0,000 |
Произошла ошибка при настройке пользовательского файла cookie
Этот сайт использует файлы cookie для повышения производительности. Если ваш браузер не принимает файлы cookie, вы не можете просматривать этот сайт.
Настройка вашего браузера для приема файлов cookie
Существует множество причин, по которым cookie не может быть установлен правильно.Ниже приведены наиболее частые причины:
- В вашем браузере отключены файлы cookie. Вам необходимо сбросить настройки своего браузера, чтобы он принимал файлы cookie, или чтобы спросить вас, хотите ли вы принимать файлы cookie.
- Ваш браузер спрашивает вас, хотите ли вы принимать файлы cookie, и вы отказались. Чтобы принять файлы cookie с этого сайта, используйте кнопку «Назад» и примите файлы cookie.
- Ваш браузер не поддерживает файлы cookie. Если вы подозреваете это, попробуйте другой браузер.
- Дата на вашем компьютере в прошлом.Если часы вашего компьютера показывают дату до 1 января 1970 г., браузер автоматически забудет файл cookie. Чтобы исправить это, установите правильное время и дату на своем компьютере.
- Вы установили приложение, которое отслеживает или блокирует установку файлов cookie. Вы должны отключить приложение при входе в систему или проконсультироваться с системным администратором.
Почему этому сайту требуются файлы cookie?
Этот сайт использует файлы cookie для повышения производительности, запоминая, что вы вошли в систему, когда переходите со страницы на страницу.Чтобы предоставить доступ без файлов cookie потребует, чтобы сайт создавал новый сеанс для каждой посещаемой страницы, что замедляет работу системы до неприемлемого уровня.
Что сохраняется в файле cookie?
Этот сайт не хранит ничего, кроме автоматически сгенерированного идентификатора сеанса в cookie; никакая другая информация не фиксируется.
Как правило, в файлах cookie может храниться только информация, которую вы предоставляете, или выбор, который вы делаете при посещении веб-сайта.Например, сайт не может определить ваше имя электронной почты, пока вы не введете его. Разрешение веб-сайту создавать файлы cookie не дает этому или любому другому сайту доступа к остальной части вашего компьютера, и только сайт, который создал файл cookie, может его прочитать.
Характеристика пенополиуретана, полученного из сжиженных опилок с помощью сырого глицерина и полиэтиленгликоля
Кинетика процесса вспенивания
В таблице 3 показан процесс вспенивания образцов PU, полученных в результате сжижения на основе CG и CG / PEG.За характеристиками пенообразования обычно следуют время крема, время вспенивания и время высыхания [4]. В начале процесса вспенивания цвет смеси изменяется из-за образования пузырьков газа во время крема. Время подъема — это время, необходимое для того, чтобы пена достигла максимальной высоты. Во время высыхания наружная поверхность пены теряет липкость. Снижение вязкости полиола способствует увеличению подвижности и кинетической скорости пены. Таким образом, полиолы с более низкой вязкостью имеют самое продолжительное время вспенивания.Пена 1 (биополиолы разжижения на основе CG), имеющая полиолы с самой низкой вязкостью, показала самое короткое время высыхания и отлипания. С другой стороны, добавление PEG к CG в процессе сжижения уменьшало время реакции вспенивания за счет уменьшения вязкости полиола, что приводило к большей эффективности вспенивания. Следовательно, для пен, полученных в результате разжижения бинарным растворителем, пена, полученная из биополиолов с более высоким соотношением PEG и CG, показывала более низкое время реакции. Это можно объяснить более высокой реакционной способностью гидроксильных групп ПЭГ, чем у синтезированных биополиолов.
Таблица 3 Процесс вспенивания PUПлотность и прочность на сжатие полиуретановых пен
При одинаковой рецептуре вспенивания синтезированные пены имели разную плотность по разным полиолам (рис. 1). Было замечено, что добавление ПЭГ увеличивает эффективность разжижения, что приводит к увеличению производства биополиола. С увеличением содержания биополиола плотность пены увеличивалась. Это может быть связано с сжиженной биомассой, которая действует как сшивающий агент, имеющий гидроксильные группы, а не как удлинитель цепи в этой полимеризации [12].Таким образом, пены, полученные из биополиолов с более высоким массовым отношением PEG к CG при сжижении, имели более высокую плотность, чем пены, полученные из сжиженных опилок с помощью CG. С другой стороны, биополиолы пены 2 из-за более низкой реакционной способности по сравнению с другими синтезированными полиолами частично увеличивают вес пены и меньше участвуют в процессе вспенивания. Статистический анализ (ANOVA) показал, что влияние типа полиола на плотность синтезированных пенополиуретанов при уровне достоверности 95% было значительным.
Рис. 1Предел прочности на сжатие пенополиуретана составляет от 200 до 311 кПа. Механические свойства пенополиуретана зависели от нескольких параметров, таких как плотность, плотность сшивки, геометрия ячеек и эффективность выдувания [13, 14]. На рис. 2 проиллюстрировано изменение прочности на сжатие в зависимости от плотности пены. Минимальная прочность на сжатие была продемонстрирована у пены 1 с наименьшей плотностью. Плотность пены увеличивает прочность на сжатие. Таким образом, пена, полученная путем разжижения на основе CG / PEG с более высокой плотностью, имела большую прочность на сжатие.Аналогичные результаты были получены в предыдущих исследованиях [1, 4]. Помимо плотности, более высокая прочность на сжатие полиуретановых пен, полученных из полиолов сжижения на основе бинарных растворителей, может быть объяснена более высокой реакционной способностью полученных полиолов. Hu et al. [8] показали, что помимо плотности на прочность при сжатии пенополиуретана могут влиять такие факторы, как остатки биомассы или химическая структура биополиолов. Имея самую высокую плотность, пена 2 показала непостоянное поведение. Это может быть связано с меньшей реакционной способностью некоторых гидроксильных групп биополиола пены 2, которые не участвовали в образовании уретановых связей.Таким образом, полиолы без увеличения плотности сшивки и, следовательно, улучшения сжимающих свойств пен, агрегируются, увеличивая вес пенопласта. Статистический анализ показал, что существует значительная разница между прочностью на сжатие и плотностью пен (при уровне достоверности 95).
Рис. 2Влияние плотности на прочность на сжатие пенополиуретана
Водопоглощение пенополиуретана
На рисунке 3 показано влияние плотности на водопоглощение образцов в объемных процентах после выдержки в воде в течение 24 часов. .Как видно из рисунка, с уменьшением плотности водопоглощение пен увеличивалось, тогда как наибольшее водопоглощение было получено для пены 1 с наименьшей плотностью. Статистический анализ (ANOVA) показал, что влияние плотности на водопоглощение пены было значительным при уровне достоверности 98%. Ячеистая структура и содержание закрытых ячеек пен были другими эффективными факторами водопоглощения [12]. Пена 2, имеющая более высокую плотность и больший размер ячеек, имела такое же водопоглощение, как пена 3, имеющая более низкую плотность и меньший размер ячеек.Также группа Дункана поместила их в одну категорию. Это явление, вероятно, было заявлено, поскольку, в отличие от ячеек пены 2 большего размера, большинство ячеек пены было закрыто. Между тем, пена 4, имеющая меньший размер ячеек и более высокий процент закрытых ячеек, продемонстрировала более низкое водопоглощение, чем другие пены.
Рис. 3Влияние плотности на водопоглощение пен
Морфология полиуретановых пен
На рис. 4 показаны изображения, полученные с помощью сканирующих электронных микрофотографий (СЭМ) пенополиуретанов, полученных из биополиолов из сжиженных опилок.В зависимости от типа полиола, используемого при вспенивании, в синтезированных пенах менялись структура ячеек, размер ячеек и содержание закрытых или открытых ячеек. Средний размер ячеек был рассчитан по фотографиям, полученным с помощью СЭМ (рис. 5). Размер ячеек пенополиуретана уменьшился с 430 мкм пены 4 до 370 мкм пены 2 за счет добавления PEG к CG в процессе разжижения. Таким образом, в зависимости от процесса вспенивания и вспениваемых материалов наблюдалось значительное уменьшение размера ячеек. Также увеличение соотношения PEG к CG при разжижении уменьшало размер ячеек пен.Результаты показали, что более высокое отношение ПЭГ к ХГ в процессе разжижения способствовало меньшему размеру ячеек — 170 мкм пены 4.
Рис. 4СЭМ-микрофотографии пен с различной плотностью, пена 1 с 0,042 г / см 3 ( a ), пена 2 с 0,08 г / см 3 ( b ), пена 3 с 0,062 г / см 3 ( c ), пена 4 с 0,071 г / см 3 ( d )
Рис.5Средний размер ячеек полиуретановых пен, полученных из полиола разжижения на основе CG и CG / PEG
Пена 1, имеющая более низкую плотность, показала высокий процент открытых ячеек (Рис.6). Содержание открытых ячеек в пенополиуретане снизилось с 89,5% пены 1 до примерно 64,3% пены 2 из-за добавления PEG к CG в качестве разжижения и образования биополиолов, что привело к изменению свойств вспененного материала. С увеличением отношения ПЭГ к ХГ по мере разжижения содержание открытых ячеек в пене 4 уменьшилось еще больше до 10,3%. Добавление химического растворителя в процессе разжижения улучшает структуру ячеек пены и ее качество. Таким образом, пена 4 по сравнению с другими пенами имела более однородную и регулярную структуру ячеек, большее количество ячеек с меньшим диаметром.В связи с этим Xu et al. [15] указали, что с увеличением использования ПЭГ для полиола, полученного в результате разжижения опилок глицерином, ячеистая структура пен становится более регулярной.
Рис. 6Содержание открытых ячеек в пенополиуретане, полученном из полиола CG и ожижения на основе CG / PEG
FT-IR-спектры пенополиуретана
FTIR-спектры образцов пенополиуретана, полученных из биополимеров, показаны на рис. 7. Спектры для всех составов пен не показали значительных различий между ними.Во всех образцах образование уретановой связи было подтверждено с помощью FTIR и показало примерно одинаковые сигналы. Полоса поглощения при 3320 см -1 относится к группам N-H, которые образуют вытянутые водородные связи [16]. Как можно видеть, большая ширина полосы у пены 2 указывает на присутствие большего количества свободных групп ОН по сравнению с другими пенами. Что касается постоянного отношения полиола к изоцианату в рецептуре пен, это явление можно объяснить меньшей реакционной способностью полиолов и изоцианатов во время вспенивания пены 2, что приводит к меньшей активности гидроксильных групп, оставшихся в системе.Вибрация OC = O при 1730 см -1 и колебание CO-NH при 1600 см -1 подтверждают образование уретановой связи. Кроме того, интенсивности полосы пропускания при 1530 см -1 относятся к валентным и изгибным колебаниям N-H. Другие сильные полосы поглощения при 2932 и 2894 см −1 — это мостики CH 2 . Слабый пик непрореагировавшей группы NCO был примерно на 2270 см -1 . Полоса при 1900,0 см -1 представляет собой валентное колебание свободных карбонильных групп уретановых связей, а полосы при 1510 и 1600 происходят от ароматических колец лигнина.
Рис. 7Термический анализ пенополиуретана
На Рисунке 8 (A) показана теплопроводность пенополиуретана. Теплопроводность зависит от плотности пены, размера ячеек, структуры ячеек (процент закрытых и открытых ячеек) и теплопроводности вспенивающего агента [17]. Значение теплопроводности наблюдается в диапазоне от 0,031 до 0,040 Вт / м · К у пен с плотностью от 0,08 до 0,042 г / см 3 . Пена 1 с наименьшей плотностью и большим содержанием открытых ячеек имела максимальную теплопроводность из-за более высокой теплопередачи в ячейках пены.Однако при увеличении плотности пены теплопроводность снизилась, пена 2 показала другое тепловое поведение. Это свидетельство способствовало увеличению диаметра пор и, следовательно, более высокой теплопроводности. Тогда, имея высокую плотность, четко очерченную стенку ячеек, меньший размер ячеек и более низкое содержание открытых ячеек, пена 4 продемонстрировала самую низкую теплопроводность. Поскольку значительное количество воздуха может быть захвачено, это привело к усилению пассивной изоляции.
Рис. 8Кривые теплопроводности ( a ) и ТГА ( b ) пенополиуретана
Полиуретаны считались термически нестабильными из-за наличия уретановых связей, поэтому измерения проводились для получения информации о термостойкость пен.Термическое разложение зависит от природы заместителя в изоцианате и полиоле. На рисунке 8 (B) показан ТГА пенополиуретана. В исследованиях ТГА было обнаружено, что полиуретан разлагается в две стадии потери веса. Разложение первой стадии (потеря 5% массы образцов) может быть связано с разложением пиранозных колец и изоцианата, которое обычно начинается при температуре от 150 до 220 ° C [18, 19]. В одном исследовании сообщается, что пенополиуретан термически устойчив при 191,9 ° C [20]. Вторая стадия разложения (потеря веса 50%) происходила при 400–500 ° C как маркер структурного разложения пен [21], а также разложения лигнина и других сложных частей.Начало разложения (потеря веса 5%) пен в этом исследовании произошло при температуре около 212 ° C для пены 1 и 217, 226, 237 ° C для пен 2, 3 и 4 соответственно. Таким образом, в зависимости от типа полиолов, используемых в производимых пеноматериалах, температура разложения была разной. Причину повышения температуры разложения пен, полученных в результате сжижения на основе CG / PEG, можно рассматривать как результат существования полиэтиленгликоля. Добавление PEG к CG приводит к увеличению эффективности разжижения, что приводит к увеличению производства биополиолов.Увеличение процента биополиола в получаемых пенах может вызвать разветвление и большее количество поперечных связей, что требует большей тепловой энергии для инициирования движений цепи [22, 23]. Xu et al. [15] указали, что при добавлении 30% ПЭГ в качестве высокомолекулярных полиолов на нефтяной основе к биополиолам с образованием трехмерных поперечно-сшитых полиуретановых групп температура разложения пен на первой стадии повышается.