Самостоятельное изготовление шлакоблоков | Мастер
Форма из листового металла толщиной 3 мм. Вместе с помощниками, используя бетономешалку, вы сможете в день без особых усилий «выпускать» до 300 штук блоков. Много это или мало? Судите сами: на гараж размером 6×4 м потребуется 450 таких блоков, а на один этаж дома размером 6,5×8 м — 1000 штук.
Форма для бетонных блоков (все размеры внутренние, сварные швы — снаружи).
Раствор для изготовления блоков готовится так. Замешиваете слегка увлажненную смесь (количество воды определяется опытным путем) в пропорции: цемент — 1 часть, шлак или керамзит — от 7 до 12 (пропорция дана для цемента М400). Установив форму на ровной площадке, заполняете ее раствором, трамбуете ручной трамбовкой и, выровняв по верхнему краю, срезаете металлической полосой лишнее. Теперь осторожно снимаете форму (она без дна) — блок готов.
Ставите форму рядом и повторяете процесс. В конце работы не забудьте тщательно вымыть форму водой. Через 24 часа блоки уже можно складировать (по высоте не более трех), освобождая место для следующей партии. Размер формы дан на тот случай, если вы задумаете вести кладку стен с дополнительной облицовкой в 1/2 кирпича. Если же ваша постройка будет иметь стены, оштукатуренные с обеих сторон, то вы можете размеры взять произвольные — лишь бы удалось потом поднять такой блок руками. А при кладке стен толщиной 50 см не забывайте через каждые два ряда блоков проводить «перевязку» тычковым кирпичным рядом.
Размеры самодельных шлакоблоков можно выбрать «под себя».
Самую простейшую форму, которая меня более всего удовлетворила, я изготовил следующим образом. Подобрал строганные доски шириной по высоте шлакоблока (140 мм). Длиной доски должны быть не более 2 м, так как работать с более длинной формой сложнее: приходится делать много лишних движений. Далее необходимы поперечины. Две крайние поперечины соединяют с продольными досками «на задвижных пазах” (рис).
Форма на три шлакоблока
С внутренней стороны продольных досок (между поперечинами) через каждые 140 мм формируют пропил ножовкой и стамеской поперечные пазы глубиной 7…8 мм. Ширина пропила зависит от толщины разделительных пластин из листового железа, текстолита, гетинакса. Подойдут пластины и из другого прочного листового материала, лишь бы он был достаточно гладким. Из рис. 1 понятно, как изготовить форму. Описывать ее долго и нет смысла, только одно хочу сказать, что готовую форму перед заливкой в нее раствора ставят на абсолютно ровную поверхность. Все детали формы, изготовленные из дерева, желательно покрасить любой масляной краской, что обеспечит более легкое извлечение шлакоблоков из формы. Каждый раз перед заливкой в форму раствора все ее внутренние поверхности протирают соляровым маслом (соляркой) или отработанным машинным маслом. Протирают слегка, не обильно. Чтобы уменьшить расход раствора, а
Форма, заполненная раствором
Если после установки бутылок уровень раствора повышается недостаточно, необходимое количество раствора (до верха формы) добавляют мастерком. Через 2…3 ч. раствор значительно осядет и окрепнет, тогда бутылки вытаскивают, осторожно поворачивая их вокруг оси, и сразу же промывают водой, иначе на них прочно налипнет раствор и к дальнейшему использованию бутылки окажутся непригодными.
Процесс выемки шлакоблоков из формы очень прост. Просто слегка молотком обстучите форму по периметру и разберите ее. Боковые доски отделить легко, а вот убрать разделительные пластины несколько сложнее. Придется осторожно молотком поколотить по выступающей пластине сверху и чуть вбок.
На одну часть цемента марки «400″ брал 9, а то и 10 частей шлака. Брака не было. Для чего я это рассказал? Да для того, чтобы всего с помощью нескольких форм быстро изготовить солидное число шлакоблоков отличного качества. Я делал шлакоблоки вечером после работы каждый день, и скажу, это работа была мне не в тягость. Бетономешалки у меня нет и раствор я замешивал вручную в поддоне емкостью 300 п. Ну, а если работать вдвоем, все получится играючи. Как вариант, можно изготавливать пеноблоки своими руками.
И еще один вариант самостоятельного изготовления блоков. Форма из листового железа.
Размеры блоков я выбрал 510x250x215 мм (объем в 14 кирпичей). Из отходов листового железа сварил 11 форм без днищ. С боков приварил по 2 ручки.
Прямо на земле расстилаю рубероид, ставлю форму. Чтобы смесь не схватывалась со стенками формы, изнутри протираю их тряпкой, смоченной отработанным маслом или соляркой. Засыпаю туда жесткий керамзитобетон. Трамбую не очень сильно. Первую форму снимаю после засыпки 11-ой — это примерно через 10-12 мин. Блоки стоят на месте в течение 12 ч. Затем перекладываю их под навес. Твердеют они при плюсовой температуре в течение 24 суток. Навес делаю из рубероида, брезента или полиэтиленовой пленки. Под ним блоки будут защищены от дождя и солнца.
Пробовал изготавливать блоки и с пустотами. Вставлял два деревянных кругляка, обточенных на конус и обернутых кровельным железом. Пустото образователи могут быть круглые, квадратные, прямоугольные… В зависимости от того, как уложены блоки, толщина стен получается 215, 250 или 510 мм.
Для толстых стен блоки лучше делать пустотелыми, для тонких — заполненными. Условно стены толщиной 215 мм без пустот можно назвать холодными, 250 мм — полу теплыми, 510 мм с пустотами — теплыми.
Для изготовления половинных блоков в форму по центру вставляю лист железа. В заготовки, которые используются для формирования проемов в стене дома, приходится загадывать деревянные пробки для закрепления дверных и оконных коробок.
Пробовал делать строительные блоки
Заполнителями могут быть местные не дефицитные материалы: керамзит, шлак, опилки и т.д. Я для приготовления смеси использовал цемент, керамзит и песок в соотношении 1:4:1.
Самая тяжелая работа — приготовление бетона. Желательно использовать простую самодельную бетономешалку или готовую покупную.
Шлакоблоки были и есть одним из самых востребованных материалов для возведения различных конструкций в строительстве. Характерная для них прочность, а так же хорошие теплоизоляционные свойства дают возможность строить быстро и сравнительно легко и довольно дешево. Строить из них может как профессионал, так и неискушенный опытом каменщик.
bazila.net
Изготовление опилкобетонных блоков в домашних условиях: пропорции материала, видео-инструкция
Содержание статьи
От автора: здравствуйте, дорогие читатели! Сейчас я расскажу вам о довольно новом явлении в современном строительстве — блоках из опилок. Уровень утилизации отходов при переработке дерева вышел на совершенно новый уровень развития и предполагает изготовление опилкобетонных блоков в домашних условиях без потери качества производимого продукта.
Скажу честно, с самостоятельным производством этого вида продукта я не сталкивался лично. Весь материал мы приобретали, так как именно при его помощи возводили стены. Покупали как раз у частника, который занимался этим в своей мастерской, оборудовав ее под небольшой завод. Этого не хватало для массовой продажи, однако нам было достаточно.
Проведя долгий разговор со своим другом, я готов поведать вам все секреты данного аспекта строительства. Приступим!
Что нам понадобится
Проблема подбора материалов при изготовлении подобного вида продукта заключается не столько в его составляющих, сколько в производстве форм для его создания. Начнем по порядку.
В состав самих опилкобетонных блоков входит:
- песок;
- цемент;
- древесные опилки.
Добыть каждый из этих трех элементов не тяжело. Первые два с легкостью приобретаются в строительных гипермаркетах, а третий можно дешево «урвать» на лесопилках.
А вот чтобы сделать формы для изготовления, придется изрядно попотеть. Вам понадобятся двухсантиметровые доски, с одной стороны оббитые листовой сталью для того, чтобы получаемый раствор не отдавал влагу. Обойтись можно и без покрытия, однако в таком случае нужно обязательно хорошо намочить весь каркас.
Размер блоков вы выбираете самостоятельно, конкретных стандартов не предусмотрено. Однако не стоит забывать, что в процессе сушки они будут становиться меньше, а это значит, что формы должны быть немного больше.
Секции должны насчитывать порядка двадцати, а то и тридцати ячеек, для того чтобы ускорить весь процесс. От их количества и качества напрямую зависят те же факторы конечного результата. Если вы наплевательски отнесетесь к этому моменту, то в конце концов получите неодинаковые куски непонятной субстанции.
Технические характеристики готового материала
Готовые опилкобетонные блоки имеют огромное количество положительных характеристик. Первое и самое главное — они прочные и крепкие. Это позволяет сооружать из них любые конструкции, в том числе и фундамент для невысоких зданий.
Еще одной положительной чертой является отличная теплоизоляция. При возведении стены вы можете не прибегать к процессу дополнительного искусственного утепления в виде пенопластовых, пенополистирольных материалов или пластин из минеральной ваты. Дополняется это и высокой устойчивостью к отрицательным температурам и влаге.
В том случае, если в состав будет входить еще и известковое молоко, вы можете обезопасить себя от образования грибка или любой живности. В противном случае, он начинает впитывать влагу в себя и разрушаться. Если вы упустили этот момент в процессе заготовки сырья, решить проблему поможет покраска или внешняя обработка гидроизоляционным материалом.
Для меня лично огромным плюсом является то, что опилкобетонные блоки — экологически чистые. Если честно, то я возводил бы детские сады, больницы и другие подобные здания исключительно из таких материалов. Однако лишь в том случае, если найдется технология, позволяющая увеличить срок годности дерева.
Имея возможность самостоятельно выбирать форму для блоков, вы можете создать своеобразный утеплитель и заменить им классические варианты.
Область применения
Спектр использования опилкобетонных блоков огромен, как количество цветов в фотошопе. Технические характеристики позволяют эксплуатировать его как угодно и где угодно. Самой распространенной отраслью является фермерское хозяйство.
Конкретнее — постройка хозяйственных помещений. Они получаются теплыми, крепкими и надежными. Возможность создавать их своими руками делает это все еще и дешевым.
Постройка, о которой я говорил выше, была именно такой. Мы делали денник на конной ферме. Лошади были спортивными, и их содержание играло очень большую роль. Помещение должно было быть теплым зимой и сохранять приемлемую температуру летом, потому что животные требовали нормализации климата.
Владелец фермы задал мне вопрос, смогу ли я дешево купить такое сырье. Я ответил, что смогу сделать все без проблем. После того как мы возвели всю постройку, стены были отштукатурены и прошпаклеваны. После этого мы покрыли их водоэмульсионной краской с внешней стороны и деревянными панелями с внутренней. В результате получили красивое теплое помещение, позволяющее содержать копытных в наилучших условиях.
Если вы настроитесь начать фермерский бизнес, то знания о том, как делать опилкобетонные блоки дома, вам пригодятся.
Процесс производства
Друзья, данный пункт содержит лишь те знания, которыми владеют мои знакомые, ранее встречавшиеся с подобными процессами. Не исключено, что вы придумаете что-то новое, позволяющее ускорить процесс или оптимизировать производство с целью скорейшего достижения конечного результата.
Первое, что вам нужно сделать — это определиться с размером. Классические габариты не установлены, поэтому все зависит от вас и ваших желаний. Это основное, что нужно учесть при изготовлении каркаса с формами. Решить это следует еще до закупки досок, так как их высота будет определяться высотой самого блока.
Второе — подсчитайте количество ячеек. Процесс это не самый быстрый, поэтому чем больше вы их сделаете, тем быстрее сможете перейти к непосредственным строительным работам.
Посчитали, какими будут блоки, и сколько штук за раз будем делать? Отлично. Поехали дальше. Покупаем доски и листовой нержавеющий металл. Оббивать нужно именно им, потому что влага, которой будет пропитан будущий блок, может сыграть злую шутку, вызвав процесс коррозии. Тот пагубно скажется на качестве, да и придется заново покупать и устанавливать облицовку.
Перед тем как начать сбивать доски, просчитайте с точностью до сантиметра, на каком расстоянии они должны находиться друг от друга. При вычислениях не забудьте, что каркас также имеет свою толщину. Это нужно учесть.
Приготовив его, перейдем к непосредственной подготовке раствора. Пропорции зависят от прочности, которой вы добиваетесь. Для блоков низкой прочности вам потребуется двадцать килограммов опилок, 5 кг песка и столько же цемента.
Увеличивая прочность, добавляйте больше второго и третьего элемента, при этом количество первого сырья оставляйте таким же. При увеличении объема раствора количество сырья должно увеличиваться в соответствии со стандартами.
Объем воды будет измеряться вручную. Добавляйте ее постепенно и проверяйте, разминая смесь в руке. Если на ладони остаются капли, то вы переборщили. По консистенции полученное сырье должно получится схожим на пластилин.
Заливать раствор в форму следует слоями, по пятнадцать сантиметров каждый. После заливки слоя придавите его сверху, чтобы удалить образовавшуюся воздушную подушку.
После того как все будет сделано, оставьте раствор в формах на четыре дня в помещении, температура в котором свыше пятнадцати градусов по Цельсию. Если показатель будет ниже, то смесь просто-напросто не засохнет. Увеличивать температуру сильно тоже не стоит, потому что тогда влага уйдет на порядок быстрее, чем нужно, и блок получится рыхлым.
После томных четырех дней ожидания не спешите радоваться тому, что все уже готово. Далее нужно достать блоки из форм и разместить их отдельно в том же помещении для достижения максимальной прочности.
Для полноценной просушки им потребуется около трех месяцев. В редких случаях подождать стоит четыре. После этого протестировать камень на прочность и только тогда приступить к работе.
Не нужно обходить вниманием ожидание, так как последствия могут быть плачевными. В том случае, если вы будете закладывать из блоков фундамент, тот может развалиться в течение года. Из-за этого вы потеряете все сделанное, создадите угрозу здоровью и даже жизни.
Тестируем на прочность
Тест на прочность представляет из себя довольно забавный процесс. Я бы даже сказал, что это весело. Для этого вам потребуется взять один образец и подняться на высоту порядка семи, а лучше даже десяти метров. После чего скинуть опилкобетонный блок вниз и посмотреть, что с ним произойдет. Если он разлетится на части, то всю партию придется забраковать и использовать для более мягких построек, будь то стена или перегородка, но никак не для основания дома.
В том случае, если блок останется целым или только слегка надколется, можете приступать к непосредственным работам.
Полезные советы
Некоторые специалисты советуют, помимо песка, опилок и цемента, добавлять еще и глину. Довольно адекватное решение, но только в том случае, если вам необходимо уменьшать теплоотдачу и прочность. В противном случае будет беда.
Заливать раствор нужно в течении полутора часов после приготовления. Именно столько времени ему требуется, чтобы начать засыхать.
Друзья, я уверен, что мои советы будут вам полезны. Последнее, что хочу поведать — это то, что заготовку стоит начинать за год до начала самой стройки и готовить следует на порядок больше экземпляров, чем планировалось. Удачной стройки, дорогие мои!
seberemont.ru
Изготовление шлакоблоков своими руками — 2 варианта, инструкция!
Шлакоблок является одним из наиболее востребованных строительных материалов. Изготавливается по методу вибропрессования из бетонного раствора. Из шлакоблоков возводятся самые разнообразные постройки – от сараев и гаражей до бань и жилых домов.
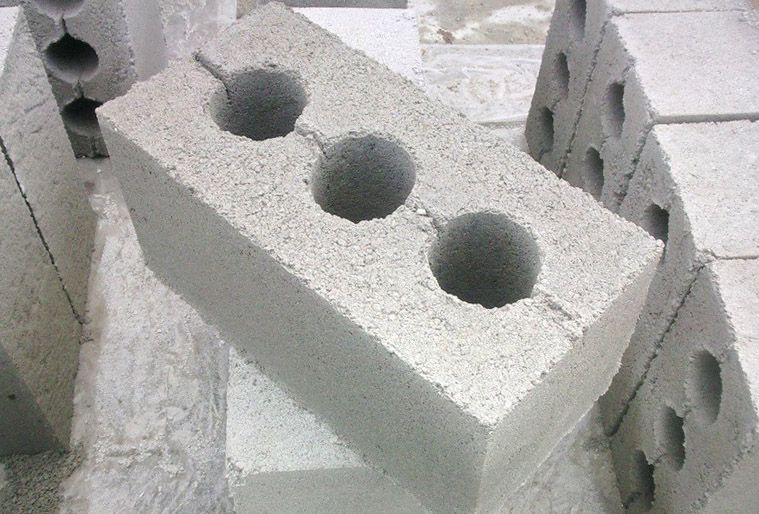
Изготовление шлакоблоков своими руками
Планируете что-нибудь построить из шлакоблоков? Сделайте их самостоятельно! Ничего сложного в технологии производства этих бетонных блоков нет. Нужно досконально разобраться в порядке работы, узнать основные требования и выдержать рецептуру.
Содержание статьи
Общие рекомендации и требования
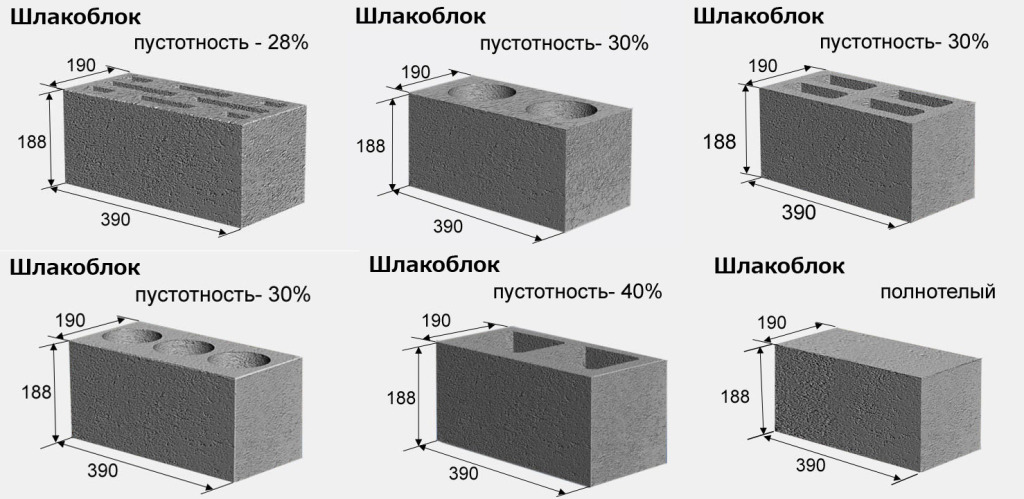
Размеры шлакоблока
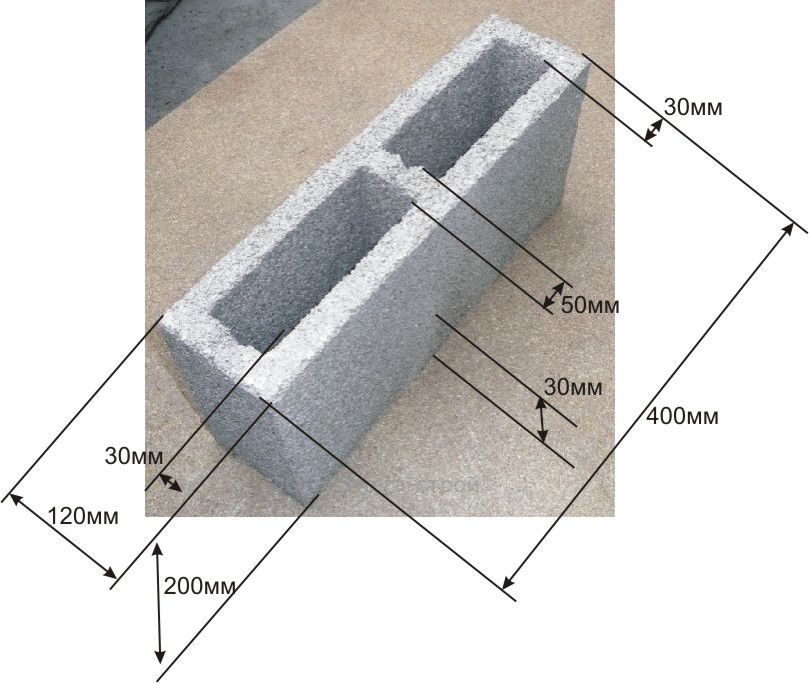
Шлакоблок для межкомнатных перегородок
Размеры шлакоблока стандартизированы – 188 х 190 х 390 мм. Каждый блок имеет отверстия. Обычно их 3. Для изготовления строительных элементов используется смесь из цемента марки не ниже М400, доменного шлака и крупнозернистого песка. Нередко добавляются дополнительные наполнители и пластификаторы.
Можно изготавливать блоки как вручную с помощью форм, так и при помощи оборудования с функцией вибропрессования.
В среднем одного мешка цемента хватает для изготовления 36 блоков. Экономия очевидна.
Шлакоблок должен иметь правильную геометрию. Даже небольшие неровности приведут к ухудшению качества кладки. Чтобы получать ровные блоки, формы нужно наполнять не просто до краев, а с небольшой горкой, т.к. во время вибрации бетон слегка утрясется и осядет.
Как готовить раствор?
Какого-то универсального состава раствора для изготовления шлакоблоков нет – у каждого мастера свой уникальный рецепт. В целом же нужно ориентироваться на особенности состава шлака.
Составляющие | Объем, л, на один блок | Прочность высохшего блока на сжатие, кг/см2 | Морозостойкость готового блока, циклов | Коэффициент теплопроводности готового шлакоблока |
---|---|---|---|---|
Шлак до 8 мм | 10 | 30-40 | 30 | 0.35-0,4 |
Песок до 3 мм | 1,8 | |||
Цемент | 2,75 | |||
Вода | 1,5 |
Есть стандартная «заводская» рецептура, можете ориентироваться на нее. Пропорции следующие:
- шлак – 7 частей;
- песок – 2 части;
- цемент – 1,5 части;
- вода – 1,5-3 части. Подробнее об определении необходимого количества воды будет рассказано далее.
Полезный совет! Ранее приводились стандартные габариты шлакобетонных блоков. Однако для частной застройки удобнее использовать изделия с размерами 400х200х200 мм.
Помимо шлака в состав таких блоков можно включать золу, опилки, гипс, бой кирпича, продукты сгорания угля, гравий и прочие подобные материалы.
Дополнительно в состав раствора рекомендуется добавить пластификатор для бетона. Хватит 5 г на блок. Благодаря пластификатору будут увеличены показатели водонепроницаемости, прочности и морозостойкости изделий.

Пластификатор для бетона
Уделите особое внимание определению необходимого объема воды. Ее надо добавить столько, чтобы изделия не растекались после формирования.
Можете сделать простой тест. Бросьте горсть раствора на землю или другую поверхность. Если он рассыпался, но при обратном сжатии руками вновь соединился в единую массу – консистенция оптимальная.
Делаем шлакоблоки вручную
Если запланировано не слишком масштабное строительство, блоки можно сделать без вибропресса.
Изготавливаем форму
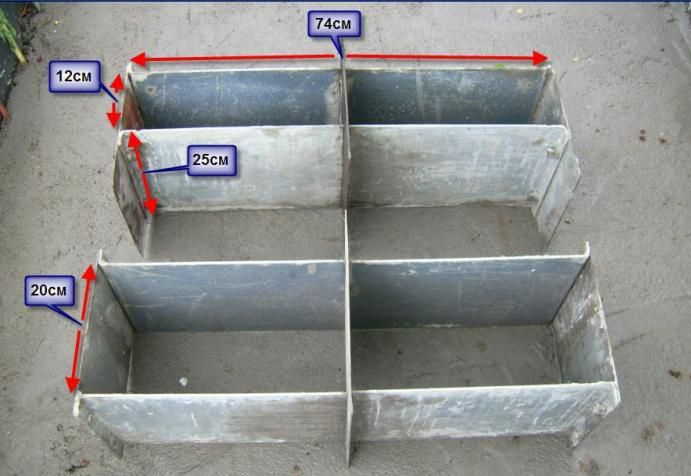
Форма для шлакоблока
Собираем форму размерами 40х20х20 см. При желании можете корректировать размеры на свое усмотрение. Для изготовления формы используем металлические листы либо деревянные доски.
Конструкция предельно простая: дно и боковые стенки. Стенки крепим с учетом выбранных ширины и длины блока. Высота граней формы также должна соответствовать запланированной высоте строительных элементов.
Полезный совет! Вы можете сделать формы с ячейками для одновременного изготовления 4-6 блоков – очень удобно. Нужно лишь увеличить длину и ширину внешних граней и установить между ними перегородки.
Подготовьте пустые стеклянные бутылки. Их вы будете использовать для создания пустот в блоках.
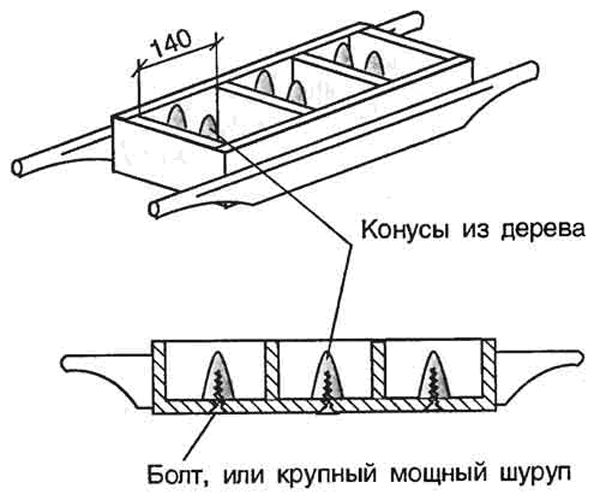
Вариант формы для шлакоблока
Заливаем блоки
Равномерно заливаем раствор в форму до краев.
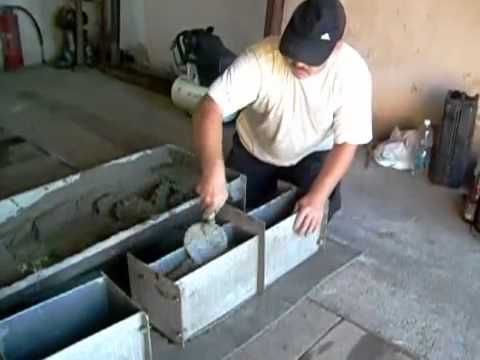
Закладка смеси в форму
Помещаем в залитую массу бутылки горлышком вверх. Разравниваем поверхность заливки, удаляя излишки раствора.
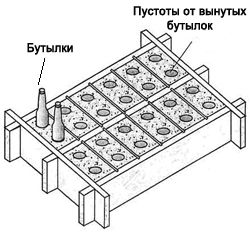
Схема размещения бутылок в залитых блоках
Ждем порядка 5 часов и достаем бутылки. Шлакоблоки же оставляем в формах на сутки, после чего аккуратно их вынимаем и раскладываем по горизонтальной поверхности штабелями.
Оставляем блоки сушиться на месяц. Лишь спустя указанное время материал можно будет использовать для строительства.
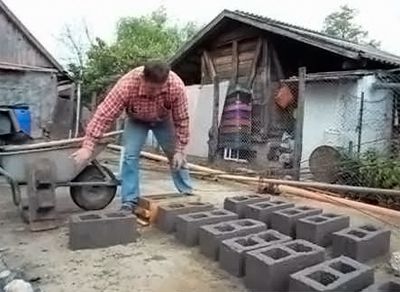
Изготовление шлакоблоков
Полезный совет! На время сушки накройте блоки полиэтиленовой пленкой. Она защитит изделия от растрескивания во время жары и не даст им намокнуть в случае дождя.
Делаем шлакоблоки на станке
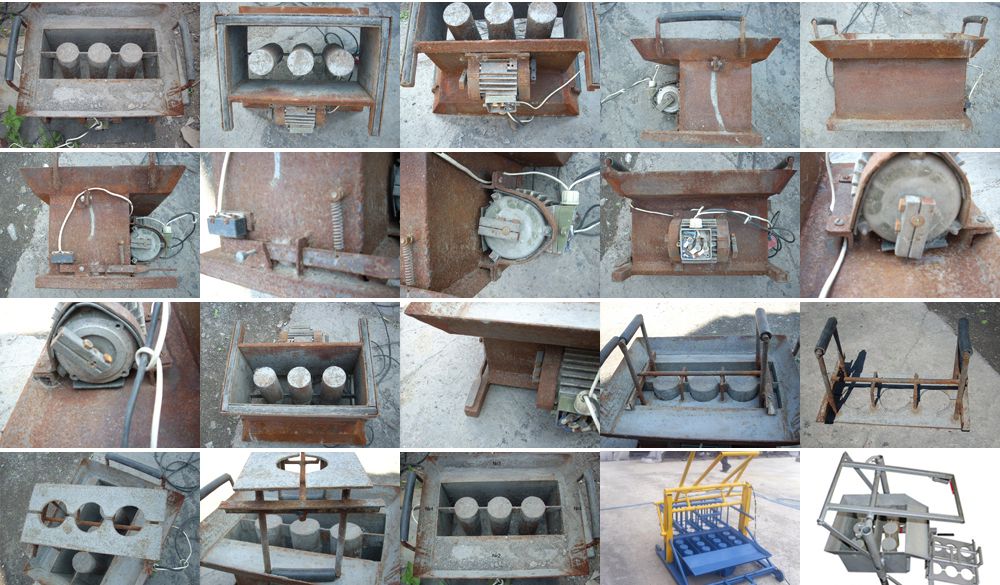
Фото конструкции в разных ракурсах
Станок позволяет существенно повысить производительность работы. Оборудование имеет довольно простую конструкцию.
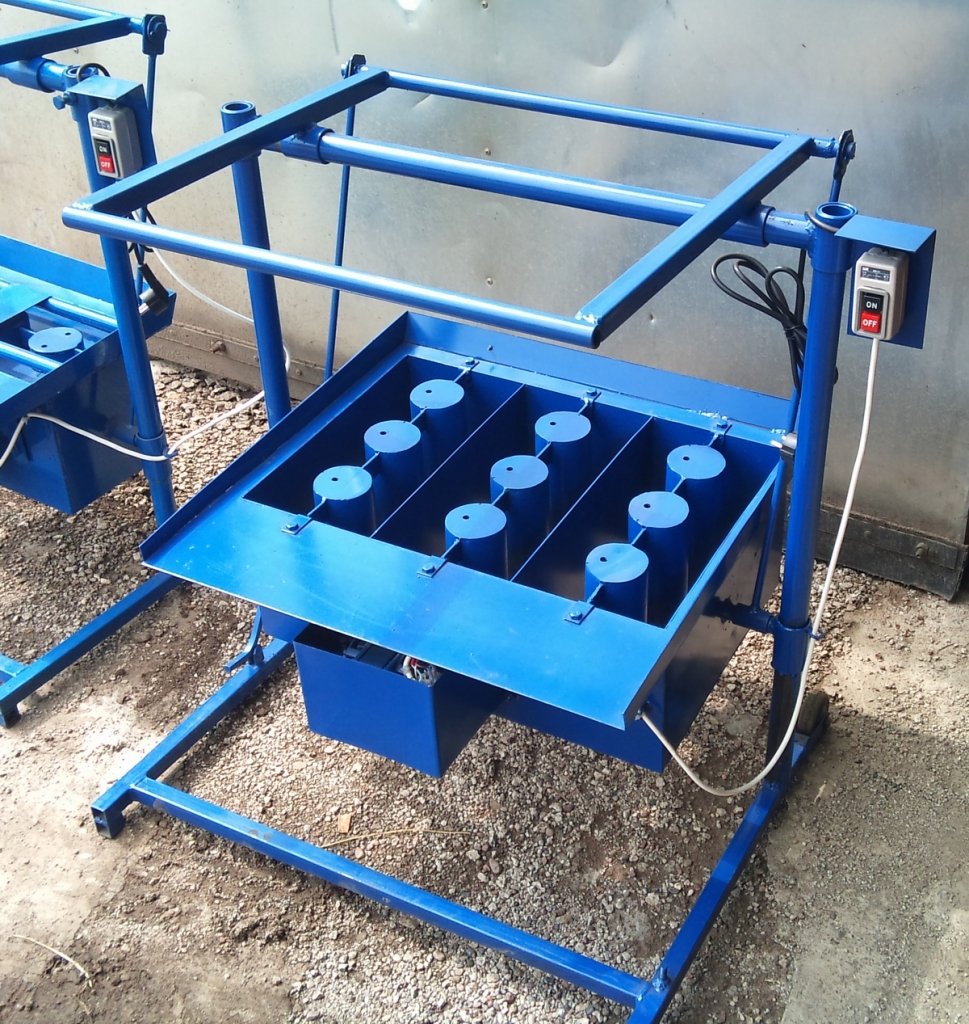
Вибростанок
Собираем станок
Главный элемент самодельного вибропрессовочного станка – форма (матрица) для шлакобетонного раствора. По своей конструкции такая форма является металлической коробкой с внутренними элементами в виде пустот. Ограничители для создания пустот также могут быть съемными.
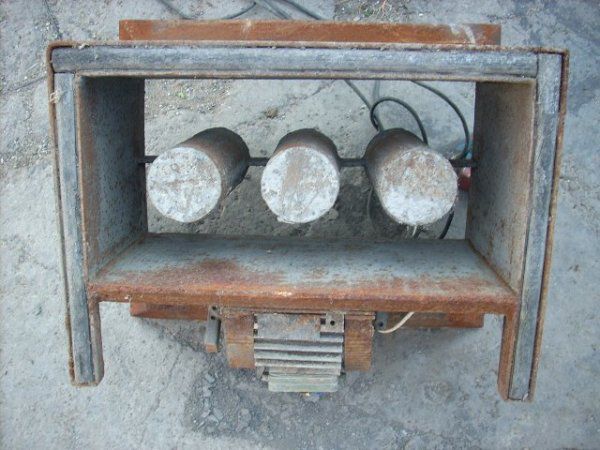
Станок для шлакоблоков компактный
Набор для работы включает следующие материалы и инструменты:
- аппарат для сварки;
- стандартный набор слесарных инструментов;
- болгарку;
- тиски;
- листовую сталь толщиной 3мм. Уйдет около 1 м2;
- трубу диаметром 7,5-9 см. Нужен примерно 1 м трубы;
- металлическую полосу толщиной 3 мм. Понадобится порядка 30 см материала;
- электродвигатель мощностью 0,5-0,75 кВт;
- гайки;
- болты.
Станок для шлакоблоков компактный
Вид сбоку
Вид спереди
Вид спереди
Первый шаг. Изготавливаем форму по размерам будущих блоков. Вырезаем из листовой стали боковые грани матрицы. Будем делать форму сразу на 2 блока. Для этого вырезаем из стали внутреннюю центральную перегородку и закрепляем ее в ящике.
Второй шаг. Определяем высоту элементов для оформления пустот.
Важно! В соответствии с технологией высота пустот должна быть такой, чтобы донная стенка имела толщину от 3 см.
Третий шаг. Отрезаем 6 кусков трубы по длине цилиндров-ограничителей для оформления пустот.
Четвертый шаг. Придаем трубам конусную форму. Для этого продольно прорезаем каждый кусок трубы до середины, обжимаем тисками и соединяем с помощью сварочного аппарата. Завариваем каждый конус с обоих краев.
Пятый шаг. Соединяем ограничители в ряд по длинной грани шлакоблока. Добавляем по краям ряда по пластине 3-сантиметровой толщины с отверстиями для скрепления с проушинами.
Шестой шаг. Делаем посередине каждого такого отсека формы пропилы. С обратной грани формы привариваем проушины. Они позволят выполнять временное крепление элементов для создания пустот. Очень удобное решение – можно будет убирать цилиндры и делать монолитные блоки.
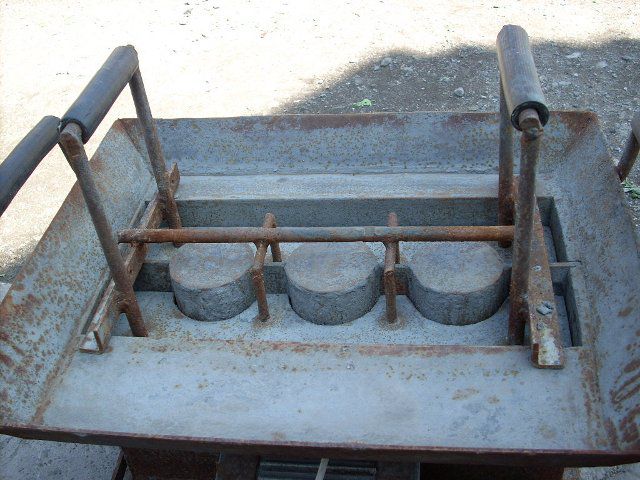
Станок для шлакоблоков компактный (пресс сверху)
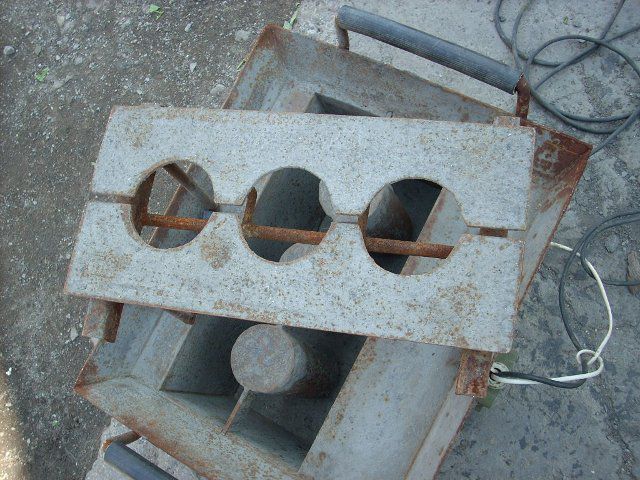
Пресс станка
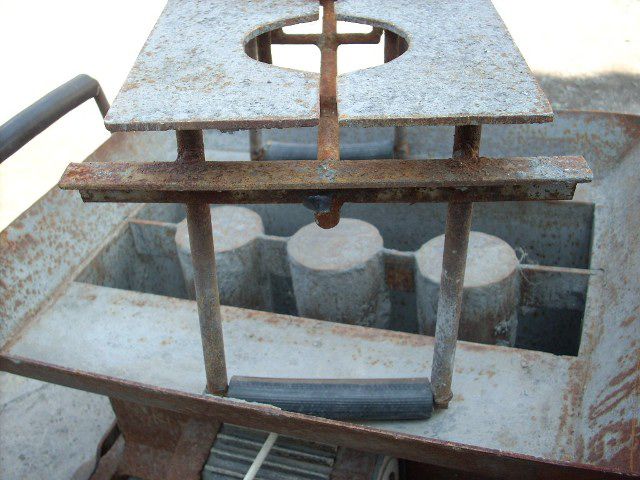
Пресс станка
Седьмой шаг. Снаружи одной из поперечных стенок навариваем 4 болта для крепежных отверстий вибромотора.
Восьмой шаг. С помощью сварки прикрепляем со стороны загрузки фартук и лопасти по краям.
Девятый шаг. Готовим все элементы конструкции к покраске – зачищаем их и тщательно полируем.
Десятый шаг. Делаем пресс. Он будет иметь вид пластины с отверстиями, повторяющими расположение отверстий в блоке.
Важно! Диаметр отверстий на пластине должен превышать аналогичный параметр для углублений в блоке примерно на 0,5 см.
Пластину изготавливаем такого размера и закрепляем ее таким образом, чтобы она могла входить вглубь коробки в месте установки ограничителей на 5-7 см.
В завершение остается приварить к прессу ручки, покрыть конструкцию грунтовочной смесью и смонтировать вибромотор.
В подходящий вибромотор можно превратить обыкновенный электрический двигатель. Для этого необходимо приварить на валы двигателя эксцентрики. Сильно заморачиваться не будем – просто приварим болты так, чтобы их оси совпадали. Для регулирования частоты и силы вибрации накручиваем на приваренные болты гайки.
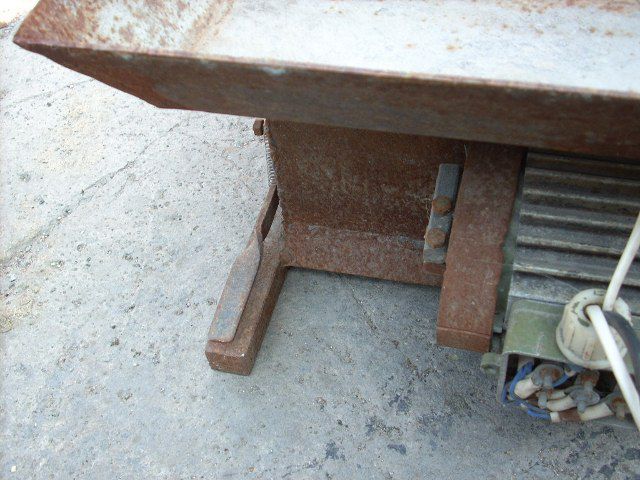
Станок для шлакоблоков компактный
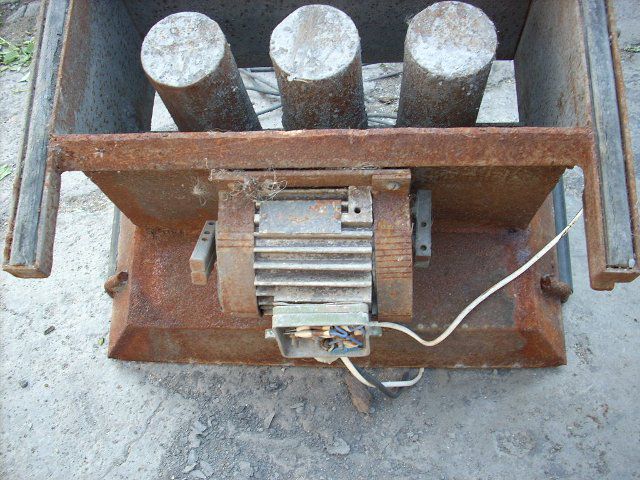
Мотор
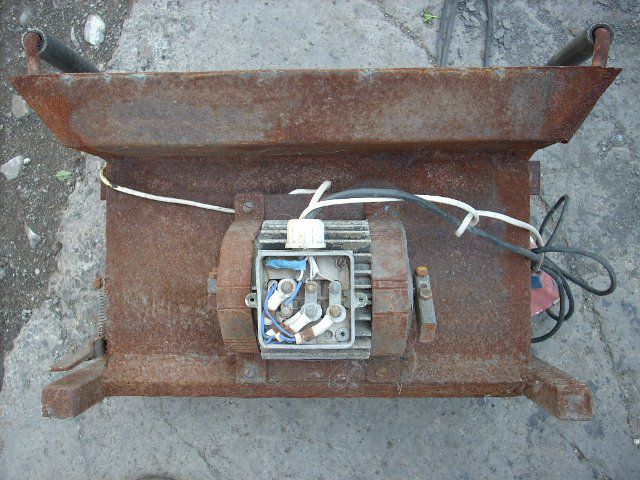
Мотор
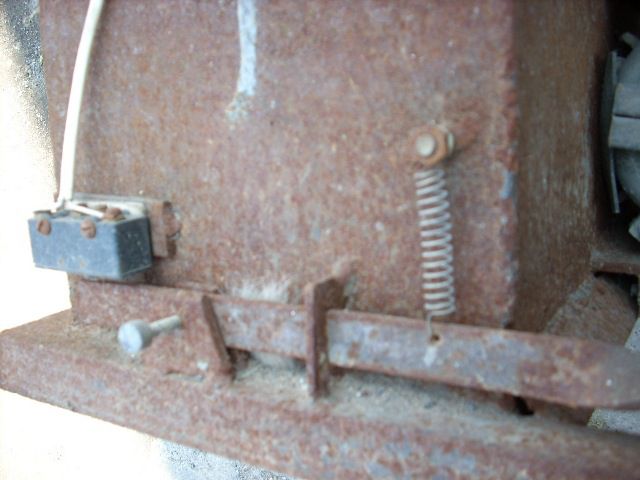
Виброустройство
Делаем блоки
Рекомендации по приготовлению раствора приводились выше. Можете использовать стандартный рецепт либо же модифицировать его на свое усмотрение. Главное получить оптимальную вязкость. Ее можно определить «на глаз» — комок смеси должен устойчиво держать форму.
Перед загрузкой смеси смазываем контактные металлические плоскости маслом. Благодаря этому раствор не будет прилипать к железу.
Укладываем готовую смесь в матрицу и приступаем к прессованию.
Устанавливаем наполненные формы на виброплиту и даем ей утрамбовать раствор на протяжении 5-15 секунд. Спустя указанное время добавьте в форму еще раствора, т.к. загруженный ранее неизбежно осядет.
Повторяем процесс, только на этот раз не выключаем виброплиту, пока прижим не достигнет ограничителей. Снимаем форму до момента остановки станка.
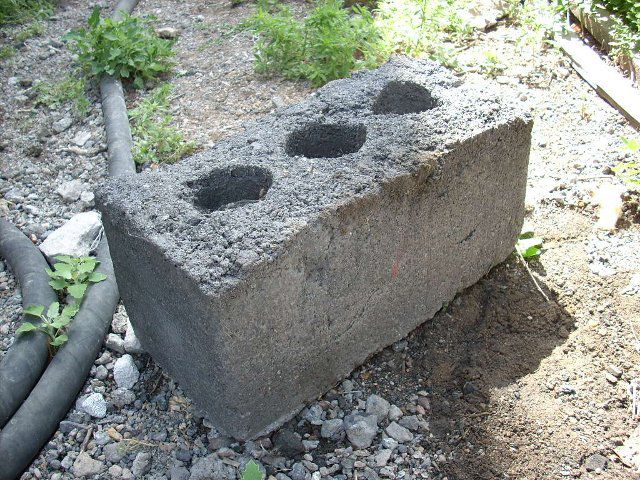
Готовый шлакоблок
Даем блокам 1-3 суток на первичную просушку, аккуратно вынимаем их из блоков, раскладываем по ровной горизонтальной поверхности и накрываем полиэтиленовой пленкой. Использовать материал по назначению можно не ранее чем через месяц.
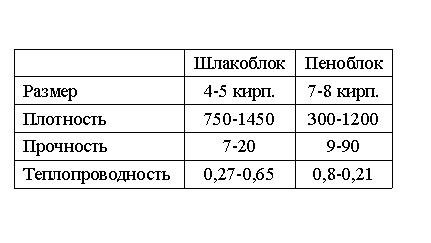
Сравнение характеристик шлакоблоков и пеноблоков
Узнайте, как делать арболитовые блоки своими руками, из нашей новой статьи.
Удачной работы!
Видео – Изготовление шлакоблоков своими руками
stroyday.ru
инструкция по эксплуатации оборудования, фото и видео-уроки
Понравилась статья? Следите за новыми идеями полезных авто советов в нашем канале. Подписывайтесь на нас в Яндекс.Дзене. Подписаться.
Шлакоблоки – современные строительные материалы, которые чрезвычайно популярны и активно используются для возведения разнообразных конструкций. Стены, для изготовления которых используются шлакоблок, будут иметь отличные характеристики прочности, надежности и теплоизоляции, тогда как стоимость их несравнимо мала.
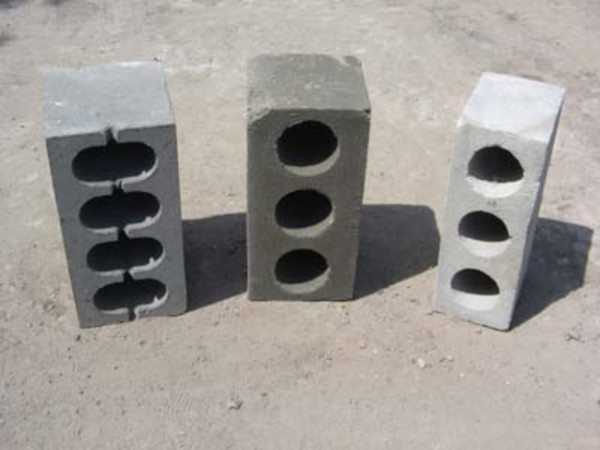
«Домашние» строительные блоки из шлака
Состав шлакоблока (как, впрочем, и пеноблока) поистине уникален. Нельзя не отметить, что сам по себе шлакоблок – материал доступный и простой, а стену из него сможет возвести даже человек, который по образованию строителем не является. Да и по сравнению с кирпичом или другими материалами со схожими характеристиками, именно шлакоблок можно изготовить даже своими руками без какого-то специального оборудования и лишних финансовых затрат.
Классификация стройматериалов и их типы
Современная технология изготовления шлакоблоков предполагает получение материалов с различными характеристиками, формами и размерами. Подобно кирпичу такие изделия могут быть как сплошными, так и с пустотами, рядовыми и лицевыми.
Также, если еще несколько лет назад для изготовления применялся только доменный шлак, то сегодня используется также гранитный отсев и прочие вещества со схожими характеристиками.
Бетонная и вяжущая основы состоят из портландцемента различных марок: начиная от самых легких и заканчивая 400-й маркой. При этом меняется состав раствора, он может изменяться в зависимости от типа используемого шлака и его фракций (крупные или мелкие).
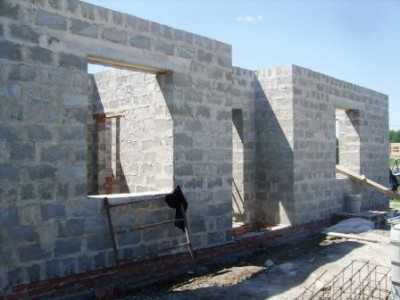
Дома из шлакоблоков, изготовленные своими руками
Следует отметить, что изготовление шлакоблоков и технология, а также рецептура, которая для этого используется, может быть самой различной – все зависит от того, что нужно получить от стройматериала в конечном итоге, и где он будет применяться.
Нужно упомянуть, что даже технология изготовления шлакоблоков в домашних условиях позволяет получить действительно качественные, прочные и надежные материалы, строения из которых прослужат не один год.
Общие требования для выполнения работ по созданию шлакоблоков
Изготовление шлакоблоков своими руками – процесс, который требует тщательного соблюдения некоторых норм и технологических требований. Так, например, стандартный размер блока из шлака составляет 39х19х188 мм, он имеет три технологических отверстия и для его получения нужно использовать ряд качественных материалов и подручных инструментов.
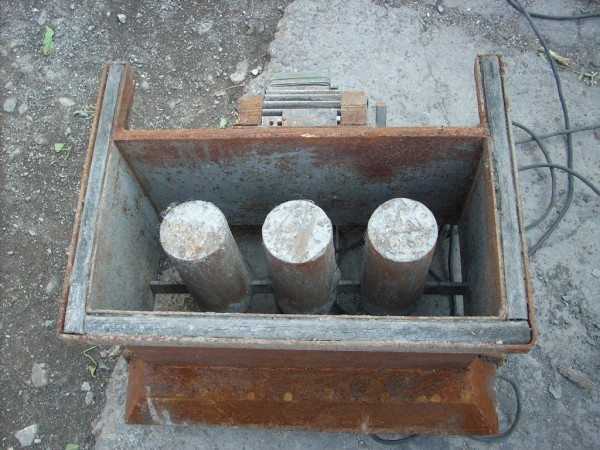
Самодельные формы для изготовления строительных блоков
Прочность, высокое качество и долговечность классического шлакоблока, изготовленного в домашних условиях, можно достичь путем соблюдения определенных требований:
- Песок обязательно должен быть крупной фракции, чистый и без лишних включений;
- Шлак берется обязательно доменный, так как именно такое сырье обладает достаточными характеристиками и не разрушается от воздействия влаги;
- Цемент. Только от качественных производителей и в достаточных количествах;
Важно. Лучше всего для изготовления современных и прочных шлакоблоков использовать цемент М400 – это оптимальная марка, характеристики которой позволяют получать лучшие стройматериалы, стойкие к воздействию влаги, нагрузок и повреждений.
- Оборудование. Если изготовление шлакоблока своими руками не является каким-то бизнесом, а нужен только для личных потребностей, то достаточно будет самой простой техники. Единственное требование – наличие специального вибропресса, который поможет добиться нужной прочности изделий.
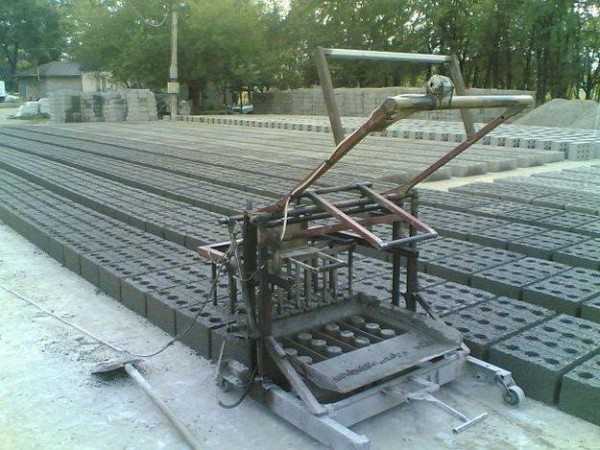
Виброустановка для изготовления строительных материалов
Если говорить про шлак, то такое сырье получается при переработке угля и, по сути, является лучшим наполнителем для строительных блоков. Нужно сказать, что если шлак найти никак не удается, то вместо него можно использовать зитобетон. Правда, в последнем случае себестоимость блоков будет несколько выше, чем в случае с использование отработки-шлака.
Строительные блоки – идеальный выбор для современного дома, а изготовление их в домашних условиях поможет существенно сэкономить средства. Если произвести приблизительные расчеты, то можно увидеть, что на создание одного блока уходит порядка 0,011 метров кубических раствора при пропорции 1:7. Это означает, что из одного мешка самого обычного цемента можно получить целых 36 шлакоблоков, что очень выгодно и привлекательно.
Важно. Самое главное, что нужно знать перед тем, как изготовить шлакоблок нужно запомнить – это правильная сушка уже готовых блоков. Любая вмятина, неровность или деформация и строить из такого деформированного материала просто-напросто станет невозможно.
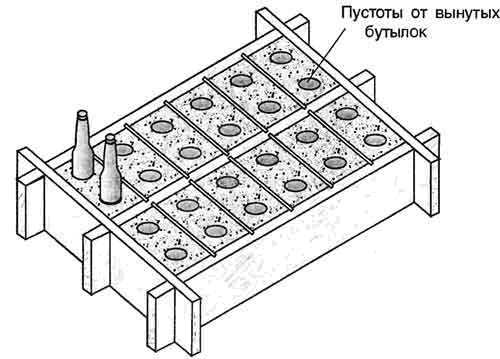
Пример простейшей емкости для формовки шлакоблоков
Статьи по теме:
Особенности и конструкция формы для блоков:
Форма для изготовления шлакоблоков представляет собой специальную емкость, в которую загружается раствор и где производится формовка и «приготовление» блоков. Следует сказать, что изготовление форм для шлакоблоков своими руками не займет большого количества времени, но важно только соблюдать определенные требования, в частности, и к геометрии подобных емкостей.
Отметим, что формы для изготовления шлакоблока могут изготавливаться из различных материалов, в том числе и древесины. Размеры также выбираются любые, но желательно, чтобы они были типовыми.
Для того чтобы повысить производительность и качество шлакоблоков, исходящих из форм, можно дополнительно установить на них специальное вибрационное оборудование, которое будет один раз включаться, а через 5-15 секунд выключаться.
Чем лучше заполнять емкости для приготовления строительных блоков
В настоящее время, как указывалось ранее, форма для изготовления шлакоблока может быть заполнена различными растворами. Для домашнего изготовления таких материалов важно помнить, что универсального состава не существует, так как каждый мастер подбирает свою собственную рецептуру, которая будет оптимальная для того или иного типа здания.
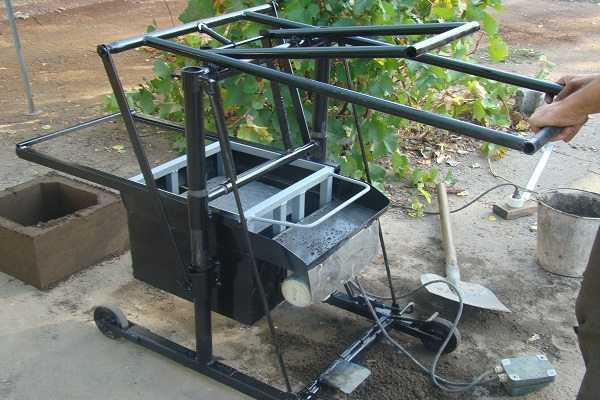
Станок с электроприводом для вибрационного формования
Тем не менее, существует также и стандартизированная инструкция по приготовлению блоков: 7 частей шлака, 2 части песка и 2 гравия, а также 1,5 части чистого качественного цемента (минимально марка М400) и 1,5-3 части воды. Это оптимальный рецепт, благодаря которому можно получить высококачественные материалы, которые идеальны для сооружения любых зданий, начиная от частных домов и заканчивая банями и прочими хозпостройками.
Нельзя не сказать о том, что в аппарат для изготовления шлакоблоков вместо традиционного шлака можно добавлять и другие наполнители. Так, например, подойдут всевозможные отходы горения угля (зола), гравий, перлит, обработанные заранее опилки, гранит, гипс и отсев камня. Кроме того, подойдет кирпичный бой и прочие схожие по характеристикам отходы строительства.
Для того чтобы раствор-заготовка была более пластичной, в её состав добавляют специальные пластификаторы (по 5 грамм на каждый блок). Таким образом, можно в разы повысить прочность блока, стойкость его к негативному воздействию низких и высоких температур, а также избавить от трещин при застывании.
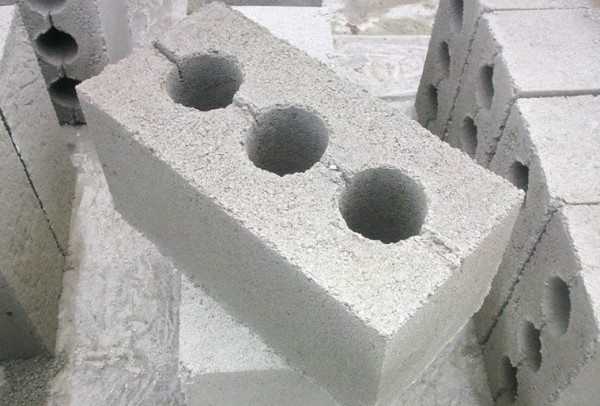
Готовый блок, созданный самостоятельно в домашних условиях
Если говорить о воде, то ее количество следует отмерять очень тщательно, в противном случае цена ошибки может быть критичной. Блоки не должны растекаться во время снятия, хорошо формоваться и быстро застывать. Соблюдать рекомендаций очень важно, так как они гарантируют долговечность и надежность строения, а также минимизируют появления каких-то дефектов и трещин в конструкции строения.
Статьи по теме:
openoblokah.ru
Шлакоблоки своими руками в домашних условиях: изготовление и кладка
Теми, кто решаются сделать шлакоблоки своими руками, движут, как минимум, две цели: стремление существенно удешевить строительство какого-либо объекта и желание построить при этом надежное, долговечное и функциональное сооружение.
И надо сказать, что организация изготовления шлакоблоков в домашних условиях вполне позволяет достичь указанных целей.
Если в процессе кустарного производства соблюдать все технологические требования и пропорции, то получающийся в конечном итоге самодельный шлакоблок обладает вполне достаточными качествами, чтобы построить не только забор, мангал, баню, гараж или сарай, но и вполне добротный дом.
Чтобы наладить изготовление шлакоблоков в домашних условиях, необходимо приложить определенные усилия и быть готовым к некоторым затратам.
Естественно, что в работе понадобятся некоторые чертежи, в которых будет показано, как сделать шлакоблок.
Впрочем, затраты эти будут не столь уж и велики, поскольку для производства шлакоблоков в домашних условиях не потребуется приобретение какого-то особо сложного станка или другого дорогостоящего оборудования.
Единственное, на что придется потратить деньги – это специальные формы, призванные обеспечить нужные размеры и конфигурацию будущих блоков.
Кроме того, приобретение бетономешалки также может существенно упростить процесс производства, поскольку размешивать рабочий состав вручную бывает достаточно утомительно.
Использование техники намного облегчит строительство.
Во всем остальном — дом, сарай, мангал, баня, забор или, к примеру, гараж, выполненные из шлакоблоков своими руками, потребуют лишь наличия необходимого сырья, материалов и трудолюбия.
Формы для изготовления шлакоблоков
Изготовление шлакоблоков, чтобы в конечном итоге возвести забор, мангал, гараж, баню, сарай или даже собственный дом своими руками, не требует определенных навыков или знаний. При желании изготовление стройматериала может провести даже непрофессионал.
Одним из главных элементов, необходимых для производства шлакоблоков в домашних условиях, являются специальные формы, в которые помещается рабочая смесь.
Конечно же, формы должны быть как можно более разнообразными, поскольку кладка, из которой состоит мангал или забор, существенно отличается от той, когда строят дом, гараж или, к примеру, сарай.
Отличия могут заключаться и в размерах, и в конфигурации. По идее, специальные формы для изготовления шлакоблоков можно приобрести в строительных магазинах.
Но в целях экономии их вполне можно сделать и собственными силами.
По своей сути, формы для изготовления шлакоблоков представляют собой не что иное, как опалубку, применяемую при производстве бетонных работ.
При определенных навыках и сноровке такие формы можно легко изготовить из любого подручного материала, например, из дерева.
Обычно при производстве формы используют следующие стандарты, обеспечивающие типоразмер будущих блоков:
- длина – 390 мм;
- ширина – 190 мм;
- высота – 180 мм.
Впрочем, можно изготовить и формы, отличающиеся по размерам от принятых стандартов, придав им свои оригинальные параметры. Ведь в каждом конкретном случае, будь то гараж или баня, кладка будет меду собой отличаться.
Ведь чем больше размеры шлакоблоков, тем меньшее их количество понадобится для того, чтобы построить мангал, забор, сарай или дом.
Однако, чрезмерно увлекаться «гигантоманией» не стоит – слишком большие габариты блока приводят к его очень большому весу, что заметно затрудняет строительство.
Видео:
Ситуация, при которой баня или гараж, выполненные из шлакоблока своими руками, требуют при возведении привлечения подъемного крана, другой специальной техники, какого-то станка и прочего оборудования, выглядит не особенно рациональной с экономической точки зрения и даже нелепой.
Кроме того, при изготовлении формы, чтобы возвести гараж или баню, собственноручно, необходимо помнить о том, что кладка должна быть, во-первых, достаточно прочной, а во-вторых, ее внутренняя поверхность должна быть гладкой.
Этого легче всего добиться путем шлифовки. Для снижения массы шлакоблоков в них предусмотрено использование специальных конструктивных пустот.
Это позволяет сделать любое строение — мангал, забор, баню, сарай или дом более легким, снизить нагрузку на фундамент и ускорить строительство.
Для обеспечения формирования таких пустот можно приварить к металлическому днищу формы три профилированные трубы.
А можно использовать и гораздо более экономичный и простой способ, применив обыкновенные стеклянные бутылки. Обычно шлакоблоки имеют три технологических отверстия.
Алгоритм самостоятельного производства шлакоблоков
В процессе производства самодельный шлакоблок не потребует применения какого-то сложного станка, не нужны и тщательно разработанные чертежи.
А вот к компонентам, которые входят в состав материала, из которого будет выполнена кладка домов или других построек, следует подходить с предельным вниманием.
Прежде всего это относится к маркам бетонных смесей, которые могут значительно отличаться друг от друга характеристиками прочности и материалами, используемыми в качестве наполнителя.
Видео:
От этого напрямую будут зависеть потребительские свойства, которыми будет обладать мангал, гараж, баня, забор, сарай или дом, построенный из самодельных шлакоблоков.
Перед тем как сделать шлакоблок собственными силами, необходимо определиться с выбором материала наполнителя.
Наиболее распространенный вид наполнителя – это шлак, образующийся в процессе металлургического производства.
Типичные пропорции необходимы для обеспечения быстрого и качественного строительства домов. Они выглядят следующим образом:
- Наполнитель – 7 частей. Это и есть тот самый шлак. Он должен быть качественно просеян и избавлен от крупных фрагментов и инородных включений. Легче всего использовать для этого специальный станок, но процесс самостоятельного изготовления шлакоблоков вполне допускает и ручной способ просева;
- Керамзитовый крупнофракционный песок – две части. Этот материал производится промышленным способом при помощи специального станка и его можно приобрести практически в любом строительном магазине. Благодаря применению этого компонента мангал, забор, баня, сарай или дом будут обладать гораздо меньшей массой;
- Гравий средней фракции (от 5 до 15 мм) – две части. Этот наполнитель необходим для того, чтобы кладка была более прочной. При определенных условиях, когда возникают проблемы с наличием керамзитового песка, гравий способен заменить и его. Но делать это рекомендуется только в крайних случаях;
- Цемент (оптимально – марки 500) – 1,5 части;
- Три части воды.
Остается только смешать все перечисленные компоненты, соблюдая указанные пропорции, при помощи бетономешалки, портативного станка или вручную.
Перемешивать рабочий раствор необходимо не до жидкого состояния, а до полусухой смеси (так называемой «гарцовки»).
Разумеется, наличие комков, посторонних включений, крупных пустот и пузырей не допускается.
После этого необходимо наполнить рабочей смесью заранее приготовленные формы, спрессовать их содержимое и дождаться засыхания раствора.
Шлакоблоки готовы – строим из них абсолютно любую постройку – дом, баню, сарай, гараж, забор или простой дачный мангал!
От качества материалов зависит конечный результат работы, поэтому необходимо очень серьезно к самому процессу производства.
При этом необходимо вести строительство по всем правилам, используя чертежи, другие строительные материалы и уделяя должное внимание соблюдению мер техники безопасности!
Тонкости и нюансы самостоятельного изготовления шлакоблоков
Хотя сам по себе процесс самостоятельного изготовления шлакоблоков достаточно прост, он не обходится без определенных тонкостей, хитростей и секретов.
Видео:
Перечислим главные из них:
- Прессовка и утрамбовка. Это – очень важный момент, от которого напрямую зависит качество будущей постройки, будь то элементарный мангал, либо более серьезное сооружение – забор, гараж, сарай или дом. Кроме предусмотренных технологических пустот, другие поры и раковины в структуре шлакоблока крайне нежелательны. Обычно для утрамбовки рабочего состава используется специальный станок. Но поскольку стоит он достаточно дорого, а его приобретение для небольшого строительства экономически нецелесообразно, то такое тяжелое оборудование вполне можно заменить обычной виброшлифовальной машинкой;
- Сушка. В промышленных условиях время сушки регламентируется техническими условиями, определенными используемой технологией, поскольку количество добавляемой в процессе производства шлакоблоков воды ограничено. В домашних условиях временные промежутки процесса сушки приходится устанавливать опытным путем. Обычно готовый шлакоблок извлекают из формы через 2-4 часа. Окончательное полное высыхание, которое позволяет готовым блокам приобрести все необходимые качества и начать строительство, может занимать от двух до семи дней.
На этом описание технологии производства шлакоблоком можно считать завершенным.
Видео:
В этой статье мы постарались изложить основные ключевые моменты, без соблюдения которых процесс был бы очень затруднительным. На самом деле, в этом нет ничего сложного.
Подобную работу можно выполнить самостоятельно, не имея специальной подготовки и не привлекая профессиональных работников.
www.stoydiz.ru
проведение работ и рецепты + вибростанок
Шлакоблок – это строительный материал, который производится путем вибропрессования из бетона. Строить из него легко, процесс идет быстро, а сама баня получается достаточно теплой. Отчего в частном строительстве шлакоблок давно завоевал свою популярность — а кто-то даже строит на нем свой собственный доходный бизнес. Нужно только знать рецептуру, технологию изготовления и уметь автоматизировать весь процесс домашнего производства шлакоблоков.
Общие требования при выполнении работ
Изготовить хорошие блоки можно и в гараже — главное, знать технологию и придерживаться рецептуры. Так, стандартный шлакоблок – 39х19х188 мм, с небольшими тремя отверстиями. А чтобы он получился качественным и прочным, важно, чтобы:
- Песок был крупным;
- Шлак – доменным;
- Цемент – качественным, не менее М400;
- Оборудование – с вибропрессованием.
Сам шлак получается при переработке угля, и, по сути, это – идеальный наполнитель для блоков. Однако в последнее время, благодаря активному проведению газа, шлак и зола от угля вырабатываться стали намного меньше. А потому шлак все чаще стали заменять на зитобетон, который, к сожалению, намного дороже.
Этот строительный материал стремительно набирает свою популярность в основном благодаря тому, что обходится он недорого, а тепло- и звукоизоляция у него отличная. Кроме того, произведем расчеты: на изготовление шлакоблоков в домашних условиях уходит 0,011 куб.метров раствора при пропорции 1:7 (это на одну штуку). А это значит, что из одного мешка цемента получится ровно 36 блоков – что вовсе не плохо!
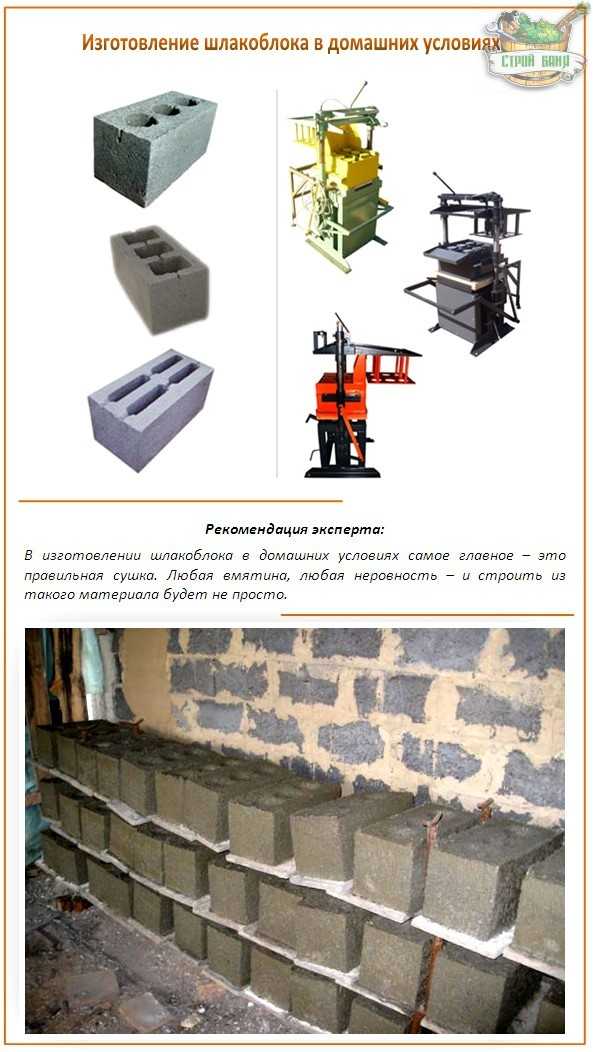
Одно из самых важных требований к качеству шлакоблоков – это их геометрия. Ведь чем большими будут неровности и изъяны в блоках, тем серьезнее придется потратиться на возведение стен. А чтобы шлакоблок получился идеально ровным, важно, чтобы сама виброформа всегда была наполнена до краев – иначе блоки будут получаться кривыми. Причем не просто до краев – а с горкой, ведь вибрация потом слегка утрясет бетон.
Весь же процесс выглядит так: виброформа включается на один раз, через 5-15 секунд выключается, и уровень раствора в форме оценивается – если оказался ниже краев формы, нужно поставить прижим, снова включить вибрацию – и когда она упрется в ограничитель, выключить. Сделать это нужно одновременно: включить вибратор и вытянуть форму.
Чем лучше наполнить формы?
Если вы налаживаете производство шлакоблоков в домашних условиях, знайте – нет универсального состава, каждый мастер подбирает свою, уникальную рецептуру, которая больше подходит для конкретной бани и которая зависит от уже имеющегося шлака. Но стандартная рецептура шлакоблока такая: 7 частей шлака, 2 части песка и 2 части гравия, 1,5 части хорошего цемента (марка от М400) и от полутора до 3-х частей воды. Принятые размеры шлакоблока – 39х19х20 см, но используются в частном строительстве и габариты 40х20х20 см.
Кроме самого шлака наполнителем для таких блоков берут золу, другие отходы горения угля, гравий, обработанные опилки, перлит, отсев камня и гранита, гипс, кирпичный бой и им подобные. Для большей пластичности блоков еще добавляется пластификатор – это 5 грамм на один блок, при вибролитье. Для чего? Именно это вещество значительно повышает прочность блока, его морозостойкость и водонепроницаемость, избавляет от трещин.
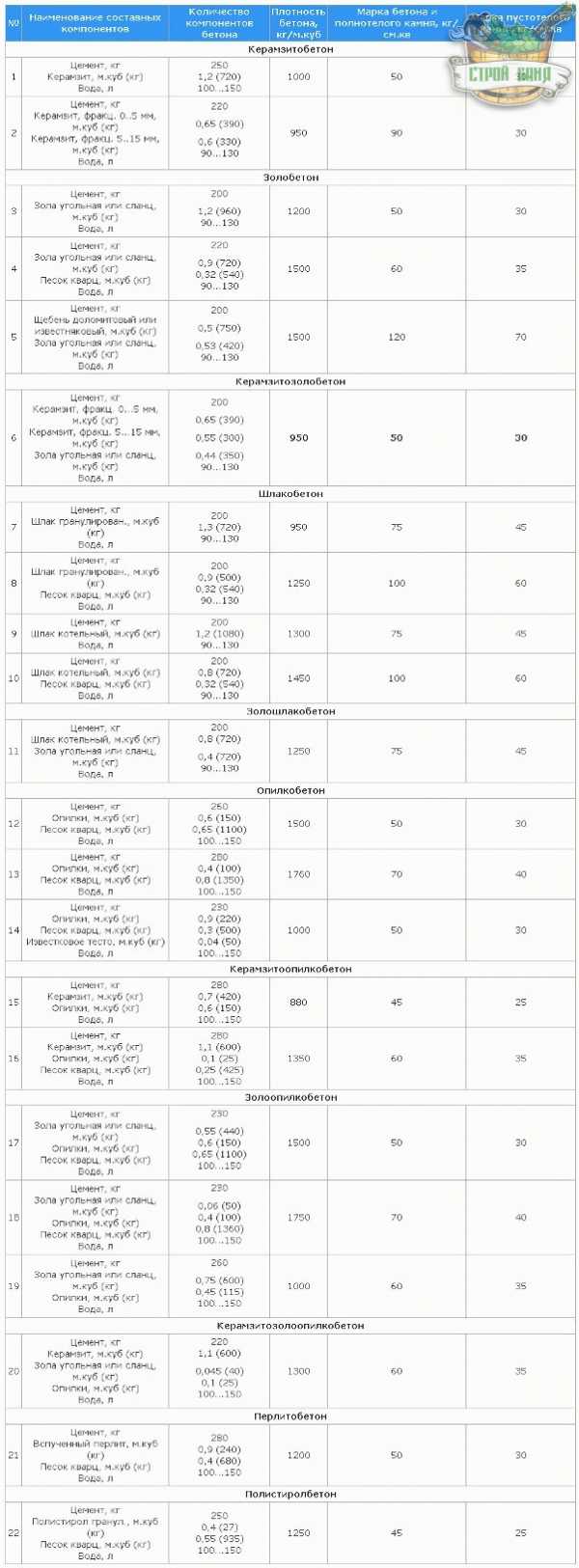
Особенно тщательно нужно отмерять количество воды: блоки не должны растекаться во время снятия. Можно провести такой тест: если при падении на землю раствор рассыпается, но в кулаке соединяется – это то, что надо. К слову, бетон для строительства небольшой бани приготовить можно и вручную, но для более серьезного строения лучше изначально обзавестись электрической бетономешалкой, рассчитанной на объем 0,2-0,5 кубических метров.
Весь процесс проведения работ за 4 шага
Производить шлакоблоки своими руками желательно не под открытым небом, как это делают мастера на видео расположенных выше, а лучше это делать в помещении с ровным полом и хорошей вентиляцией.
Вот как можно сделать в домашних условиях хороший, качественный шлакоблок:
- Шаг 1. В форму кладется с горкой раствор, на 3-5 секунд включается вибратор и раствор осаживается. Если его мало – нужно доложить, вставить прижим и снова включить вибратор. Как только прижим осядет на ограничители – формирование завершено.
- Шаг 2. Виброформа снова включается на 5-10 секунд, после чего форма снимается – не выключая машину.
- Шаг 3. От пяти до семи дней блоки нужно будет сушить. А их полное затвердевание происходит в течении месяца, при высокой влажности и в тепле.
- Шаг 4. Уже через день блоки можно аккуратно переносить – они не сломаются, однако класть вместе их нужно через неделю. А вот если в блоки добавлялся пластификатор, то через 6-8 часов их можно убирать с площадки и складировать.
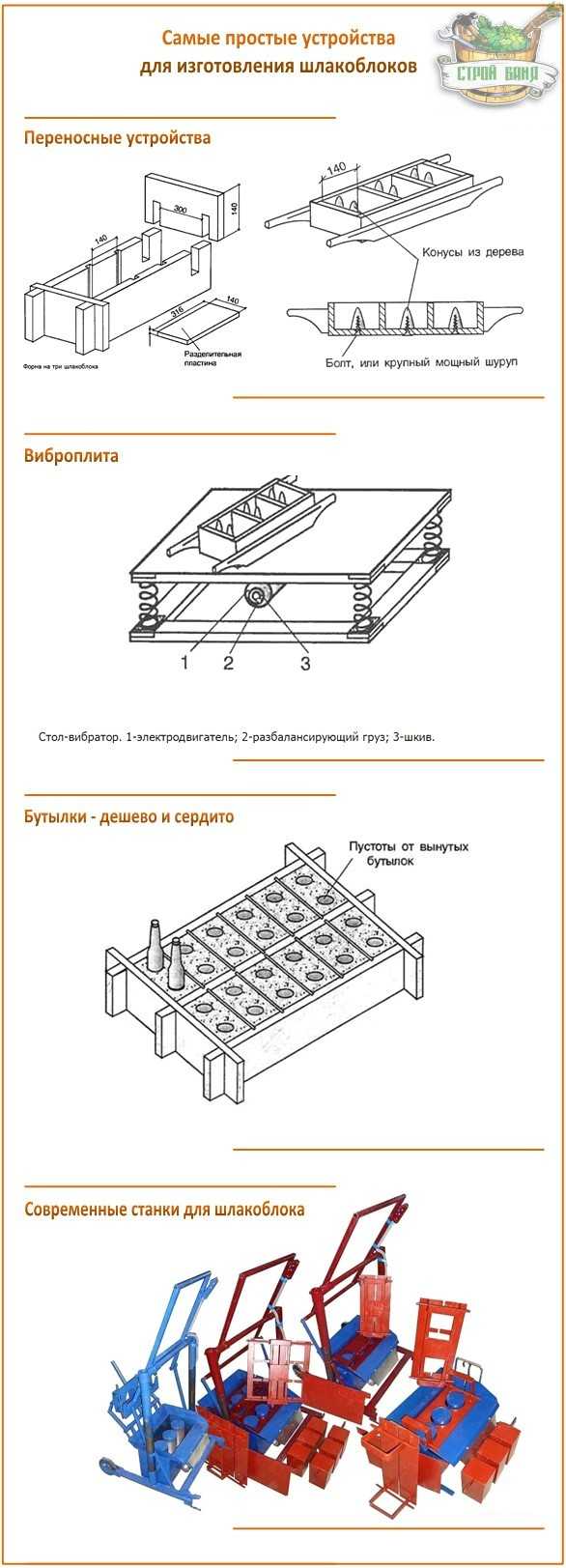
Хранятся готовые шлакоблоки в так называемых пирамидальных штабелях, сразу по сотне и с небольшими промежутками между друг дружкой – чтобы хорошо просыхали бока. Пару месяцев просушки – и можно строить новую баню!
Как сделать домашний вибростанок?
Конечно, если построить нужно всего одно строение и небольшое, как баня, то изготовлять такие блоки проще всего в стандартных ящиках-переносках с бутылками. А вот для более объемной работы уже нужен станок – пусть даже самодельный и без виброплиты. Ведь кто знает, возможно, вам настолько понравится сама кладка шлакоблока своими руками и вы увидите большую выгоду в производстве такого строительного материала, что решите открыть собственный бизнес? А для этого уже нужна автоматизация. Да и почему бы после бани не построить из такого дешевого материала и гараж, и красивую беседку, и хороший сарай? А изготовленный собственными руками из подручных материалов вибростанок значительно сэкономит время работы.
Изготовить хороший станок для шлакоблоков своими руками – не проблема. Для этого понадобится:
- Высокооборотный электродвигатель – обязательно с двумя валами, мощность – 0,5-0,7 кВт.
- Электросварка и болгарка.
- Листовое железо толщиной около 3 мм.
- Арматура диаметром около 12 мм.
Время вибрации будет составлять 5-15 секунд, после чего виброформу нужно вертикально снять и уже через сутки складировать между собой шлакоблоки. На обычном домашнем станке изготовление шлакоблоков своими руками позволяет штамповать их до 50 штук в час – а это достаточно быстро.
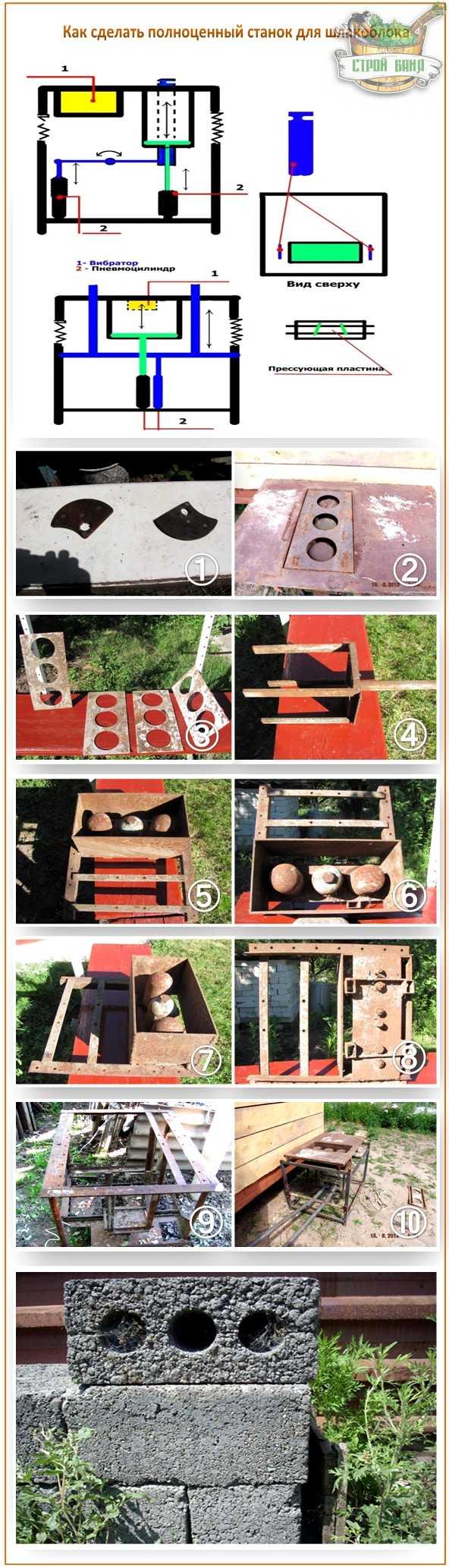
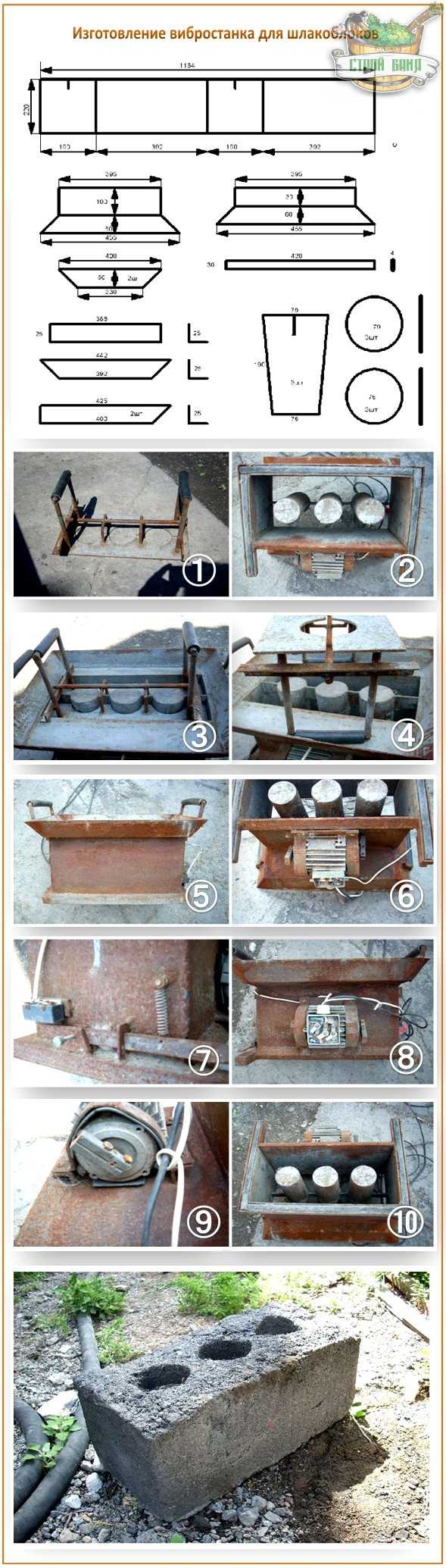
Некоторые видео-примеры с личным опытом
stroy-banya.com
Станок для блоков своими руками – простое оборудование для изготовления керамоблоков, шлакоблоков, арболитовых, газосиликатных и других строительных блоков
В наше стремительное время на рынке стройматериалов появляется все новая продукция, преуспевающая по многим показателям своих предшественников. Интересным фактом является то, что некоторые стройматериалы можно изготовить в домашних условиях. Русский народ, не избалованный деньгами и благами цивилизации, может придумать многое для того, чтобы сэкономить и самореализоваться.
Собственноручное изготовление блочных строительных материалов
Явным подтверждением этого является изготовленный своими руками станок для блоков. Он понадобится любителям, которые могут сами построить сарай, баню, гараж, и даже жилой дом, из своих пеноблоков, газоблоков, керамоблоков, шлакоблоков, опилково-бетонных (арболитовых) и других блоков с разными наполнителями. Зная пропорцию составных частей, экспериментируя на входящих ингредиентах, с ним можно изготовить блочный строительный материал собственноручно на строительство любых помещений и даже на закладку фундамента.
ЧИТАТЬ ПО ТЕМЕ:
Разработка своими руками чертежей вибростола для утрамбовки строительных смесей
Различное количество ячеек в форме
В зависимости от масштабности производства и возможностей, изготавливают формы для блоков своими руками, рассчитанные на 1-2 изделия, 6-8 изд., 10-14 шт., 21- 30 ед. и др.(фото 1). Они рассчитаны для изготовления цельных блоков и изделий с пустотами различной формы. Поменяв размеры матрицы, можно производить блоки, пригодные для стен и для фундамента. Потому размеры блоков и их количество может быть разным (ф.2). Для удобства извлечения готового изделия, следует предусмотреть разборную конструкцию. Материалом для изготовления форм может быть металл, водостойкая фанера, древесина. Формы – это своего рода съемная опалубка, которая позволяет изготовить качественный строительный материал с нужными заданными характеристиками.
-
- Фото 1 — Формы для блоков различной величины
-
- Фото 2 — Строительные пустотелые блоки
-
- Фото 3 — Заготовки стенок для форм
-
- Фото 4 — Цилиндры для заполнения пустот
Этапы изготовления форм для блоков своими руками
Для изготовления металлических матриц понадобится листовая сталь б-3 мм и металлическая труба D 8 мм для формирования пустот, а также болгарка, сварочный аппарат, другие рабочие инструменты.
- Подготавливаются заготовки для стенок. Их можно вырезать в домашних условиях болгаркой 450х210 и 220х210 по 2 заг. Дно формы должно иметь бортик высотой 3-3,5 см и ручку. На стенках делаются насечки (ф.3 ).
- Для изготовления пустот потребуются цилиндры (фото 4). Для этого, от трубы отрезается нужное количество заготовок из расчета 3 ед. на 1 блок. Высота должна быть на несколько мм меньшей от высоты стенок. Для придания трубной заготовке конусной формы, с одной стороны нужно до половины разрезать трубу и зажать тисками. Каждую трубную заготовку нужно заварить с обеих сторон, получатся пустотелые заглушенные цилиндры (заполнители). Они привариваются к планке, затем вставляются в форму и планка приваривается к стенкам формы (ф. 5).
- Заваривать все швы необходимо снаружи.
- Из толстостенной пластины делаем пресс с отверстиями с диаметром, превышающим диаметр пустотных цилиндров. Пресс должен заходить на матрицу, примерно на 50 мм. К прессу привариваются ручки (фото 6).
Готовые формы для блоков своими руками не требуют больших затрат. С ними могут работать люди, не имеющие особенной квалификации. Главное, выполнить правильный замес и уплотнить содержимое.
-
- Фото 5 — Пустотелые цилиндры привариваются к планке
-
- Фото 6 — Изготовление ручного преса
-
- Фото 7 — Чертеж самодельного станка с вибромотором
-
- Фото 8 — Поэтапное изготовление станка для блоков своими руками
Станки для блоков своими руками
Для того, чтобы хорошо утрамбовать смесь для блочных стройматериалов, можно пользоваться вибростолом или изготовить станок для блоков своими руками с прикрепленным к боковине вибратором. На фото 7 предложен чертеж вибрационного станка. Готовую конструкцию оснащают ручками, которые помогают снять матрицу без повреждения сырой бетонной заготовки. Приваренные к несущей раме колесики создают передвигающееся устройство.
Фото 8 предлагает поэтапное изготовление оборудования на одну заготовку. Оно сходно с производством форм без двигателя. Прикрепленный вибратор облегчает работу и делает готовый стройматериал более качественным. Применение станочного оборудования для изготовления стройблоков – совсем несложное. Но, при работе с ним следует придерживаться техники безопасности.
ЧИТАТЬ ПО ТЕМЕ:
Можно ли изготовить пенобетон своими руками в домашних условиях и как?
Вывод
Для мастеров, которые не бояться экспериментировать и творить, изготовление форм или вибростанка для производства блоков не составит труда. Кроме того, они сами воспользуются своими механизмами и получат достаточное количество строительного материала.
papamaster.su