Метод определения насыпной плотности
Компания «КоролёвФарм» является не только контрактным производителем косметики, но также производит и биологически активные добавки (БАД) к пище в таблетированной и капсулированной форме. В связи с этим кажется необходимым рассказать о некоторых похожих терминах и технологические свойствах этих продуктов.
Технологические свойства порошкообразных (таблетированных и капсулированных) лекарственных веществ и биологически активных добавок к пище зависят от их физико-химических свойств. При производстве биологически активных добавок в форме таблеток и в форме твёрдых желатиновых капсул необходимо учитывать различные технологические характеристики, так как активные компоненты и многие экстракты лекарственных растений поступают в виде порошков или порошковых смесей.
Насыпная плотность
Базовой характеристикой всех сыпучих материалов является плотность.
Истинная плотность – это отношение массы тела к объему этого же тела в сжатом состоянии, в котором не учитываются зазоры и поры между частицами. Истинная плотность – постоянная физическая величина, которая не может быть изменена.
В своем естественном состоянии (неуплотненном) сыпучие материалы характеризуются насыпной плотностью. Под насыпной плотностью различных сыпучих материалов понимают количество порошка (сыпучего продукта), которое находится в свободно засыпанном состоянии в определённой единице объема.
Насыпная плотность заданного порошка или любой сыпучей смеси (D нас. пл.) определяется отношением массы свободно засыпанного порошка (Mасса cып.) к объему этого порошка (Vcосуда) по формуле:
D нас.пл.= Mасса cып/Vcосуда
Насыпная плотность учитывает не только объем частиц материала, но и пространство между ними, поэтому насыпная плотность гораздо меньше, чем истинная. Например, истинная плотность каменной соли составляет 2,3 т/м3, а насыпная – 1,02 т/м3.
Зная насыпную плотность применяемых сыпучих материалов можно при проектировании емкостей или дозаторов, а так же капсул и таблеток рассчитать их объем и, соответственно, высоту засыпки. Понятно, что если нам частично известны некоторые параметры, а именно высота засыпки, а так же коэффициент засыпки, то можно рассчитать высоту предполагаемого объема, то есть высоту форматных частей, что очень важно при решении технологических задач. Конечно, если известна насыпная плотность порошка, тогда технологи могут легко рассчитать массу для одной дозы, порции или упаковки и тем самым определить величину дозировки для капсулятора или таблетпресса, а также для любого другого фасовочного оборудования.
Значение насыпной плотности определяется в соответствии со стандартом (ГОСТ 19440-94 «Порошки металлические. Определение насыпной плотности. Часть 1. Метод с использованием воронки.
Рис. 1 Прибор для определения максимальной насыпной плотности порошков |
1-измерительный цилиндр; 2-шкала; 3-тумблер; 4-регулировочный винт; 5-контргайка |
Объемная или Насыпная плотность зависит от размера, формы, влажности и плотности частиц гранул или порошка. По значению этого показателя можно прогнозировать и рассчитывать объем матричных каналов. Процедуру измерения насыпной плотности порошковой смеси или монопорошка проводят на специальном приборе (рис. 1).
Производят навеску массой 5,0 г порошка. Точность навески до 0,001 г. Далее засыпают навеску в мерный цилиндр. Устанавливают на приборе амплитуду колебаний (35-40 мм) при помощи регулировочного винта. Устанавливают отметку по шкале и фиксируют положение при помощи контргайки. Далее, с помощью трансформатора устанавливают частоту колебаний. Частота устанавливается в интервале от 100 до 120 кол/мин, по счетчику. После включения прибора тумблером оператор следит за отметкой, по которой установлен уровень порошка в цилиндре. Как правило, при работе прибора в течение 10 минут, уровень порошка или смеси становится постоянным, и прибор необходимо отключить.
Насыпную плотность рассчитывают по формуле:
где: ρн – насыпная плотность, кг/м3;
m – масса сыпучего материала, кг;
V – объем порошка в цилиндре после уплотнения, м
В зависимости от насыпной плотности порошки классифицируют следующим образом:
ρн > 2000 кг/м3 – весьма тяжелые;
2000 > ρн > 1100 кг/м3 – тяжелые;
1100 > ρн > 600 кг/м3 – средние;
ρн < 600 кг/м3 – легкие.
Одним из приборов, на котором проводят измерение насыпной плотности (а также другие характеристики порошковой смеси или монопорошка), является прибор ВТ-1000.
Рис.2 Bettersize BT-1000. Прибор для определения насыпной плотности и других характеристик порошков |
Анализатор ВТ-1000 (Рис. 2) используется для определения свойств различных сыпучих материалов, связанных с текучестью. Порошок или порошковые смеси, по определению, являются двухфазными системами. Свойства поверхности частиц порошковой смеси или монопорошка, так же как и их плотность, все эти параметры определяет его поведение в потоке и их сыпучесть. Правильное определение параметров сыпучести очень важно для расчетов процессов обработки порошка, его упаковки, транспортировки и хранения.
С помощью ВТ-1000 (Рис.3) возможно определить не только насыпную плотность, но и дисперсность, угол падения, угол естественного откоса, угол на плоской пластине и плотность утряски.
Рис.3 Определение насыпной (объемной) плотности |
(поведения порошка в аэродинамической струе).
Порошок засыпается в мерный цилиндр. Отношение занятого им объема к массе порошка является объемной или насыпной плотностью. Рис.3
Плотность — что это? | Химтраст
Плотность — скалярная физическая величина, определяемая как отношение массы тела к занимаемому этим телом объёму или площади (поверхностная плотность).
Плотность ППУ при свободном вспенивании
Для пористых материалов существуют два вида плотности:
- истинная плотность – плотность материала без учета пустот;
- кажущаяся плотность — отношение массы материала ко всему занимаемому им объему.
Кажущаяся плотность ППУ – масса единицы объема материала, включая и объем закрытых пор.
Определение кажущейся плотности проводят через 20 мин после вспенивания на образцах, вырезанных из пенополиуретана, полученного при проведении технологической пробы:
- для испытания вырезают три образца размерами (50,0 ± 0,5)×(50,0 ± 0,5)×(50,0 ± 0,5) мм из средней по высоте части пенополиуретана , при этом наличие технологической пленки не допускается. Допускается использование образцов цилиндрической формы.
- образцы взвешивают и измеряют.
Кажущуюся плотность ППУ рассчитывают по формуле:
ρ = М/V *1000, где
М – масса образца, г;
V – объем образца, см3;
ρ – кажущаяся плотность ППУ, кг/м3.
При проведении технологической пробы оценивают структуру отвержденного ППУ путем визуального осмотра вертикального среза образца пенополиуретана не ранее, чем через 20 мин после вспенивания. Структура жёсткого ППУ – мелкоячеистая, неоднородная.
Плотность жидких компонентов – величина равная отношению массы к его объему. Плотность зависит от температуры, поэтому её измерения проводят при определенной температуре, которую обязательно указывают.
Плотность жидкостей измеряется на ареометрах, гидростатических весах, пикнометрах и выражается в граммах на кубический сантиметр (г/см3).
Введение понятия «средняя плотность» при изучении темы «Плотность» в 7-м классе
В курсе физики 7 класса мы при прохождении темы “ Механическое движение” вводим понятие средней скорости, и при определенном полученном навыке решения задач большинство учащихся с расчетами средней скорости справляются. (Только жаль, что часто при решении ребята сталкиваются с громоздким математическим решением, а они пока к этому не готовы)
Через несколько уроков мы приступаем к
введению понятий массы и плотности.
На начальном уровне все основное по данному вопросу в любом учебнике-7 ,в принципе, сказано, но почему мы не оговариваем сразу такой важный закон, как закон сохранения массы? Он нам пригодится для введения понятия средней плотности!
Если растворить сахар в воде, то масса раствора строго равна массе сахара и воды.
При любом дроблении и при растворении масса остается одной и той же.
Формулировка закона: При любых изменениях изолированной системы тел или частиц масса этой системы остается неизменной и равна сумме масс составляющих ее частей.
Так как понятие изолированной системы мы пока не вводим, то можно закон сформулировать проще;
Масса тел до взаимодействия равна массе тел после взаимодействия,т. е. остается неизменной
Математическое выражение закона: m1 + m2
+ . .. + mN =m /1 + m /2 + … + m /N
Границы и условия применимости закона можно пока не вводить
Приоритет в открытии закона сохранения массы вещества принадлежит российскому ученому Михаилу Васильевичу Ломоносову и французу Антуану Лавуазье (Antoine Laurent Lavoisier).
Закон был открыт и сформулирован ими независимо друг от друга на основе анализа многочисленных опытных данных.
В 1756 г. М.В.Ломоносов самостоятельно сформулировал философский принцип сохранения материи и движения: “…все перемены, в натуре случающиеся, такого суть состояния, что сколько чего у одного тела отнимется, столько присовокупится к другому…”.
Он считал этот закон одним из основных законов природы!
Примеры проявления закона в природе
- Явления диффузии
- Процессы растворения веществ.
- Дробление и разрушение тел.
- Глобальный круговорот вещества в биосфере, перенос твердых, жидких и газообразных тел при различных давлениях и температурах, в течение веков и тысячелетий происходит в полном соответствии с законом сохранения массы. Эти же самые слова можно сказать об одном из самых грандиозных процессов – круговороте воды на поверхности земного шара.
Пример:
1) Если взять 1 кг манки, 2 кг гречки, 3 кг пшена и все крупы смешать, то получим массу строго 6 кг
mсм = mманки + mгречки + mпшена = 1 кг + 2 кг +3 кг = 6 кг
2) В пассажирский самолет перед началом рейса погрузили 300 кг продуктов. Изменилась ли масса авиалайнера после того, как в полете все продукты были съедены?
Так как заданий на закон сохранения массы в
задачниках нет, то можно предложить ребятам дома
самим поработать над их составлением. А из лучших
работ составить сборник и вклеить в задачник,
которым пользуемся на уроке. Я думаю, что многие
ребята захотят в этом поучаствовать.
А теперь о понятии плотность.
При введении этой величины в учебниках почему-то не оговаривается, что речь идет о сплошных телах! И хотя в олимпиадных задачах и в некоторых сборниках предлагаются задачи на нахождение средней плотности (или задачи, связанные с этой величиной) на уроках мы о ней не говорим. А ведь несколько уроков назад было введено понятие средней скорости, так почему по аналогии не ввести понятие средней плотности?
Истинная плотность – отношение массы к объему в абсолютно плотном состоянии (без пор и пустот)
Средняя плотность – физическая величина, определяемая отношением массы материала ко всему занимаемому им объему, включая поры и пустоты.
Средняя плотность не является величиной
постоянной и изменяется в зависимости от
пористости материала.
Интересно, что средняя плотность играет очень важное значение для человека. Его плавучесть зависит от средней плотности тканей его тела, плотности воды, вдоха и выдоха. Чем меньше средняя плотность тканей тела, тем лучше его плавучесть. При глубоком вдохе пловец, как правило, обладает положительной плавучестью, при полном выдохе – отрицательной, он тонет. Человек способен изменять свою среднюю плотность, регулируя количество воздуха в легких! При полном вдохе средняя плотность человеческого тела становится меньше плотности воды. При выдохе, когда тело теряет плавучесть, человеку приходится создавать подъемную силу движением рук. Получается, что умение плавать – это умение правильно дышать!
Когда вводится понятие выталкивающей силы,
может ребятам будет понятнее, почему такие
огромные, тяжелые корабли плавают, если
поговорить опять о средней плотности корабля и
воды! Или привести такой пример: Плотность
стекла, из которого сделана бутылка, равна 2200 кг/
м3; плотность воды – 1000 кг/ м3.
Следовательно, стекло пойдет ко дну. Но если
стеклянная бутылка, наполненная воздухом, плотно
закрыта пробкой, она будет плавать на
поверхности воды. Масса стеклянной литровой
бутылки примерно равна 0,5 кг; масса воздуха,
заключенного в ней, — около 0,001 кг, а средняя
плотность закупоренной бутылки с воздухом — 501 кг/
м3 (0,5001 кг / 0,001 м3), т.е. вдвое меньше
плотности воды!
На уроке можно решить следующие задачи:
Какова плотность смеси глицерина и спирта, если объем спирта составляет половину объема смеси?
Как изменится ответ, если масса спирта составляет половину массы смеси?
Ответ: (900 кг/ м3)
Сплав золота и серебра массой 400г имеет плотность 1,4 · 104 кг/ м3. Полагая объем сплава равным сумме объемов его составных частей, определите массу золота в сплаве.
Ответ: (0,2 кг)
(Примеры данных задач взяты из сборника
“Решение ключевых задач по физике для основной
школы. 7-9 классы. Гейндешптейн Л.Э., Кирик Л.А.,
Гельфгат И.М, там же представлены их подробные
решения)
Использованная литература:
- Гейндешптейн Л.Э., Кирик Л.А., Гельфгат И.М. “Решение ключевых задач по физике для основной школы. 7-9 классы. – М.: Илекса, 2006.
- Детская энциклопедия, том 3 , издательство “Просвещение”, 1966
- С.Е.Каменецкий, В.П.Орехов “Методика решения задач по физике в средней школе” издательство “Просвещение”, 1986
- Г.С.Ландсберг “Элементарный учебник физики”, том 3, издательство “Физматлит”, 2000
Как определить плотность цемента: истинная и насыпная
Физические значения параметров строительных материалов, одним из которых является удельный вес, необходимы для правильного выбора пропорций при смешивании. Нередко приходится учитывать плотность цемента в процессе расчетов. Для этого обращаются к специализированным справочникам или спецлитературе.
Содержание
-
Теоретические понятия
-
Активные факторы воздействия
-
Самостоятельное определение
-
Влияние состава на значение
-
Интересные нюансы
Теоретические понятия
Цемент в сухом виде является сыпучим мелкофракционным материалом. Фактически он представляет собой не однородную массу, а насыпь из микроскопических элементов, между которыми располагается воздух. Если рассматривать его фактуру под микроскопом, то станут заметны дискретные твердые кусочки, увеличенные во множество раз.
Схема состава цементов
Единого значения плотность сухого цемента не имеет. Принято два основных понятия, которые используют по отношению к данному строительному материалу. Ими являются:
- истинная плотность цемента;
-
насыпная плотность цемента.
Чтобы засчитать значение удельного веса берут отношение массы (кг) к объему (куб.м). Разделив один параметр на другой, получим необходимый результат. В первом случае в расчете принимает участие объем исключительно выбранного сырья (только крупинки строительного материала без учета воздуха между ними). Истинная плотность цемента – это физическая величина, которая участвует в школьных справочниках или научной литературе. При замерах вещество представляет собой монолит.
Насыпная плотность цемента важна для строителей. Объем минерального порошка берется с учетом пустот, имеющихся между частичками. Даже при теоретическом разборе очевидно, что у одного и того же материала, например, у марки М200 цифровые значения будут различными. Ведь в пространстве насыпь всегда будет занимать больше места, чем цельный монолит. Соответственно ее численное значение будет ниже.
Воздух составляет более половины объема в любой массе – порошкообразной, гранулированной и кусковой
Также на занимаемое место в пространстве влияет наличие статического электричества. В процессе соприкосновения между собой микрочастицы сыпучих материалов наэлектризовываются.
Трущиеся сухие частицы цемента получают постепенно статический одноименный заряд, что по законам физики вынуждает их отталкиваться друг от друга.
Во время пересыпания/ссыпания заряд постепенно повышается. Это способствует небольшому увеличению объема материала.
Наименьшее значение плотности имеет приготовленный только что портландцемент. Также сопоставимые параметры присутствуют у сыпучего вещества, которое недавно выгрузили при помощи автопродувки из автомобильной цистерны.
В период транспортировки происходит утряска материала за счет вибрации, что способствует уплотнению. Частицы находят положение, при котором максимально заполняются пустоты. Насыпной параметр плотности увеличивается. Это же происходит и во время длительного хранения. Статический заряд уходит и масса «слеживается», уплотняясь и занимая меньше места.
ВИДЕО: Определение истинной плотности материала
Активные факторы воздействия
В отличие от истинного значения насыпной параметр является не постоянной константой, а переменным значением. Это актуально как для плотности цемента М 400, так и для иных марок. Вариабельность обычно находится в пределах 1100-1600 кг/куб.м.
На параметр оказывают влияние различные факторы:
- Марка строительного материала. Исходя из этого, плотность цемента М 500 будет выше, чем у «четырехсотого».
- Производственная технология. В зависимости от способа изготовления микрочастицы имеют разнообразную форму и геометрические параметры. Фактор напрямую влияет на то, сколько места в пространстве будет занимать сыпучее вещество в итоге.
-
Химическая формула.
Плотность цемента М 500 в чистом виде без различных гидрофобных присадок или глиноземных соединений будет значительно отличаться.
- Условия и способ хранения. Герметичная упаковка способствует сохранению характеристик материала в течение длительного срока.
- Давность изготовления. Плотность цемента М 400, который произведен недавно, будет существенно выше, чем у того, который выпущен достаточно давно и успел слежаться в плотную структуру.
Примером определения параметров для «пятисотой» марки служит таблица.
Истинное значение, которое указано в справочниках, составляет 3100 кг/куб.м. Оно принимается в большинстве случаев для проведения химических или физических опытов.
Свежий насыпной состав приравнивают к 1100-1300 кг/куб.м. Для более слежавшихся масс принимают цифру из интервала 1500-1600 кг/куб.м.
Воспользоваться физическими характеристиками «четырехсотой» марки можно из приведенной таблицы.
В большинстве случаев на предприятиях, использующих в своих производственных процессах цемент в виде насыпи, в расчетах используется параметр 1300 кг/куб.м. Маркой или присадками, добавляемыми в состав, часто пренебрегают.
Самостоятельное определение
Для проведения опыта потребуется тарированная емкость, помогающая определить объем сыпучего вещества. В нее насыпаем через мерную воронку ровно 1 кг исследуемой марки цемента.
Переводим значение объема в куб.м. Делим 1 кг на полученный объем в куб.м. В результате опыта определим текущую плотность. Если нет под рукой тарированной емкости, то вычисляем объем самостоятельно. Для этого определяем площадь тары в квадратных метрах и умножаем на высоту насыпи в мерах. Главное разровнять поверхность порошкообразного средства, чтобы минимизировать погрешность. Рекомендуется проводить округления после всех вычислений для повышения точности результата.
ВИДЕО: Определение насыпной плотности материала
Влияние состава на значение
Разные сорта цементов отличаются по своему химическому составу, что отражается на итоговой массе партии. В состав входят оксидные соединения:
- кальциевые;
- кремниевые;
- алюминиевые;
- железные и пр.
Единая формула у вещества отсутствует. Процентный состав каждого из оксидов оказывает непосредственное влияние на физико-химические характеристики продукта.
Востребованным значение плотности является для нескольких популярных групп:
- глиноземный класс;
- шлаковая группа;
- портландцемент;
- пуццолановая группа.
Глиноземы относятся к быстродействующим вяжущим материалам. Состав имеет разнообразные включения, оказывающие влияние на эксплуатационные характеристики в целом. Востребованными являются марки от ГЦ40 до ГЦ60. Разница между ними заключается в скорости затвердевания.
Глинозем
Насыпной удельный вес для глиноземистых марок в отличие от портландцемента ниже и составляет 950-1150 кг/куб.м. Истинное значение не превышает 3100 кг/куб.м.
На массу портландцемента влияет химический состав, в котором преобладают силикаты. Их процентное содержание зависит от марки материала. В некоторых случаях оксиды кремния составляют до 80% от общего состава. Данный тип продукта является наиболее востребованным на всех континентах мира. Популярные марки его имеют удельный вес до 1300 кг/куб.м.
Шлаковая группа насыщена активными минеральными добавками из гранулированных доменных шлаков. Это позволяет самостоятельно быстро твердеть веществу. Обогащение сульфатно-шлаковыми компонентами снижает удельный вес. Он составляет для группы в насыпном значении 1000-1250 кг/куб.м.
Цемент со шлаком
Плотность пуцолланового цемента составляет 800-1000 кг/куб.м. Это значение он имеет в рыхлом состоянии. Для слежавшейся массы параметр будет в пределах 1200-1600 кг/куб.м.
Пуццолановый цемент
Интересные нюансы
В зависимости от времени, прошедшего от производства до использования цемента в растворах показатель его плотности постоянно изменяется. Если речь идет о свежем продукте, то она составляет порядка 1100-1200 кг/куб.м, у слежавшегося – доходит до 1600 кг/куб.м. Средний показатель при соблюдении норм хранения — 1300 кг/куб.м в течение первых двух лет с момент производства.
Истинная плотность, как было сказано, ранее более чем в 2 раза выше – у того же самого продукта при правильном хранении она составляет 3200 кг/куб.м.
Этот парадокс разницы в показателях объясняется присутствием воздуха между частицами. Даже в слежавшейся сухой массе он (воздух) составляет более половины объема. Это касается не только насыпной, но и гранулированной, и кусковой массы.
Если истинный показатель – понятие теоретической, то насыпной – чистая практика. Именно его принимают во внимание, когда определяют количество компонентов при подготовке бетонных растворов. Так, например, если зерно крупное, оно займет весь объем, а пространство между ними заполнится песком. Сочетание разных размеров позволяет добиваться максимально плотной структуры и, соответственно, наиболее мощных показателей. Именно по такому принципу делают фундаменты, дороги и другие конструкции, на которые приходится высокая нагрузка.
Освоение теории в вопросах плотности и расчета показателей позволяет даже несведущему человеку правильно определять состав бетонной смеси и соотношение компонентов для определенных видов работ.
ВИДЕО: Как понять – хороший цемент или плохой
youtube.com/embed/AdeReZzrZmY»/>
СПЕЦИФИКАЦИЯ диоксида кремния
ОПИСАНИЕ
Химическая формула: SiО2 оксид кремния (IV)
Химическая структура: О=Si=О
Молекулярная масса: 60,08 г/моль
CAS # 112945-52-5
ФИЗИКО-ХИМИЧЕСКИЕ СВОЙСТВА
Внешний вид: чрезвычайно легкий белый порошок, который в тонком слое кажется полупрозрачным, голубоватым.
Запах: отсутствует
Удельная плотность: частицы Орисила образуют физические хлопьевидные агрегаты, поэтому объём Орисила фактически на 98% заполнен воздухом. Если истинная плотность SiO2 составляет 2,2 г/см3, то кажущаяся плотность Орисила 40 — 60 г/л.
Температура плавления: 1726 °С
Температура кипения: 2230 °С
ТОКСИКОЛОГИЯ
Для рыбно-хозяйственных водоёмов ПДК — 0,25 мг/дм3.
Для водных объектов хозяйственно-питьевого и бытового назначения ПДК — 10 мг/дм3 (по кремнию).
ПДК в атмосферном воздухе населённых пунктов — 0,02 мг/дм3.
ПДК пыли диоксида кремния при вдыхании — 1 мг/м3
МАРКИ ОРИСИЛА
Количественной характеристикой, определяющей марку Орисила, является величина удельной поверхности. Между размерами первичных частиц и величиной удельной поверхности существует закономерная связь: чем меньше размер частиц, тем больше величина удельной поверхности.
В зависимости от назначения выпускают:
— гидрофильный диоксид кремния — марки Орисил 100, Орисил 150, Орисил 175, Орисил 200, Орисил 300, Орисил 380 ;
— гидрофобный диоксид кремния — марки Орисил М 130, Орисил М 200, Орисил- М 300, Орисил МА 300, модифицированный диметилдихлорсиланом (ДМДХС) непрерывным методом.
СПЕЦИФИКАЦИЯ
Показатель | Орисил 175 | Орисил 200 | Орисил 300 | Орисил 380 |
Внешний вид | Порошок белого цвета с голубоватым оттенком | |||
Удельная поверхность, м2/г, по методу БЭТ | 175±25 | 200±25 | 300±30 | 380±40 |
рН (4% суспензия) | 3,6-4,3 | 3,6-4,3 | 3,6-4,3 | 3,6-4,3 |
Насыпная плотность, г/дм3: -неуплотнённого -уплотнённого |
50 110 |
50 110 |
50 110 |
50 110 |
Потери в массе при прокаливании (2 часа при 1000°С), %, не более | 1 | 1,5 | 2 | 2 |
Массовая доля влаги на момент отгрузки (2 часа при 105 °С), %, не более | 1,5 | 1,5 | 1,5 | 1,5 |
Массовая доля диоксида кремния (SiO2) в пересчета на прокаленное вещество, %, не менее | 99,9 | 99,9 | 99,9 | 99,9 |
Массовая доля оксида железа (Fe2O3),%, не более | 0,003 | 0,003 | 0,003 | 0,003 |
Массовая доля оксида алюминия (Al2O3),%, не более | 0,05 | 0,05 | 0,05 | 0,05 |
Массовая доля диоксида титана (TiO2),%, не более | 0,03 | 0,03 | 0,02 | 0,02 |
Массовая доля крупных частиц, %, не более | 0,04 | 0,04 | 0,04 | 0,04 |
ПРИМЕНЕНИЕ
Орисил является самым активным кремнеземным наполнителем. В настоящее время он находит применение в самых различных областях. Так Орисил используется как высококачественный наполнитель в производстве резин, как загуститель смазочных материалов, клеев, герметиков, полиэфирных и эпоксидных смол, красок, лаков, для придания сыпучести порошковым и гранулированным продуктам (например, минеральным удобрениям, стиральным порошкам и т.п.), а также в текстильной, фармацевтической, парфюмерной и пищевой промышленностях.
В качестве добавок в косметических, фармацевтических и пищевых продуктах используется гидрофильный Орисил марок 200, 300, 380; обычно в концентрации от 0,1% до 30%.
Благодаря своим специфическим сгущающим свойствам, Орисил успешно используется как добавка в косметических и фармацевтических продуктах.
Орисил обеспечивает пастам и мазям желаемую консистенцию и препятствует разделению компонентов. Его добавка в количестве 0,2 — 1 % стабилизирует эмульсии и лосьоны. Порошковые продукты (такие как антисептические и косметические пудры) обретают требуемые свойства хорошего распределения и нанесения благодаря добавкам Орисила.
С большим успехом Орисил используется в производстве зубных паст. Он не разрушает зубной эмали, хорошо полирует ее, является носителем активных веществ пасты (гелевые зубные пасты).
Орисил находит применения как вспомогательное вещество для изготовления таблеток и драже. При использовании Орисила в медицине решающее значение имеет тот факт, что все ранее адсорбированные на его поверхности вещества, например лекарственные препараты, в водной среде организма человека постепенно полностью десорбируются, обеспечивая пролонгированное действие и повышая тем самым эффективность лекарственных средств.
Орисил используется как эффективный осветлитель пищевых напитков (вино, соки, пиво).
ХРАНЕНИЕ и ОБРАЩЕНИЕ
Орисил стабилен при нормальных условиях и инертен по отношению к большинству химических веществ. Пожаро- и взрывобезопасен. Не оказывает общетоксического действия.
Хотя считается, что Орисил — продукт не гигроскопичный, он способен поглощать влагу из воздуха, причем при достаточно длительном времени хранения достигается состояние равновесия. В момент получения (отгрузки) Орисил содержит не более 1,5% влаги. Допускается увеличение массовой доли влаги для марок 175, 200, 300 и 380 до не более 2, 2, 3 и 3 % соответственно в пределах гарантийного срока хранения.
Хранить в закрытой упаковке; в прохладном, сухом, хорошо проветриваемом помещении.
При нарушении целостности упаковки собрать материал в приспособленный для этого контейнер и утилизировать. Избегайте распыления. Обеспечьте вентиляцию.
Дополнительная информация по безопасности жизнедеятельности представлена в Паспорте безопасности данного продукта.
УПАКОВКА
Орисил упаковывается в клапанные многослойные бумажные мешки по 10 кг. Размеры наполненного мешка составляют приблизительно: 1050х550х300 мм.
Орисил перевозят всеми видами транспорта. Укладка мешков осуществляется в «навал» или на поддонах размером 1140х1140 мм.
ДОПОЛНИТЕЛЬНАЯ ИНФОРМАЦИЯ
По вопросам получения дополнительной информации, технического обслуживания, получения образцов продукта обращайтесь к менеджерам нашей компании.
Свойства строительных материалов SV777.RU
|
|||
Водостойкость строительного материала – это способность материала сохранять свою проектную прочность при насыщении водой. Степень снижения прочности строительного материала под действием воды называется коэффициентом размягчения. Материалы, имеющие коэффициент выше 0,8 считаются водостойкими и могут применяться в воде или в местах с повышенной влажностью. Водостойкость строительных материалов – очень важный показатель именно для тех материалов, которые используются в воде или во влажных условиях. Некоторые материалы при насыщении водой могут увеличивать свои показатели по прочности, это обусловлено, прежде всего, химическим взаимодействием компонентов. Например, при насыщении водой цемент может превратиться в цементный камень. Водостойкость характеризуется коэффициентом размягчения kp = Rв/Rс, где Rв — прочность материала насыщенного водой, а Rс — прочность сухого материала. Меняется kp от 0 (размокающие глины) до 1 (металлы).
Водопоглощение строительного материала – это способность материала впитывать и удерживать влагу. Измеряется водопоглощение отношением объема или массы впитанной влаги к объему или массе строительного материала:
wm = (m2-m1)/m1*100%,
wv = m2-m1/V*100%
Где
m2 — масса материала в насыщенном водой состоянии, кг;
m1 — масса материала в сухом состоянии, кг;
V — объем материала в естественном состоянии, м3.
Существует масса примеров, когда влаги в материале больше чем самого материала. Это происходит в том случае, когда удельный вес материала меньше плотности воды.
Практически всегда избыточное водопоглощение приводит к избыточному наличию воды в стройматериале, что ведет к изменению очень важных качеств строительного материала, таких как прочность и теплопроводность.
Влагоотдача строительного материала – это способность материала отдавать влагу, находящуюся в порах. Так, например, штукатурные растворы, отдавая лишнюю влагу, существенно изменяют свои показатели по прочности, стеновые пенобетонные блоки впитывают влагу из растворов, а потом отдают ее в атмосферу. Чем выше влажность воздуха и меньше температура, тем хуже происходит влагоотдача. Измеряется влагоотдача в процентах влаги, отдаваемой стройматериалом при среднестатистической относительной влажности воздуха 60% и температуре +20 °С.
Влажность строительного материала – величина, характеризующаяся количеством воды, находящимся в материале. Практически всегда повышенная влажность стройматериалов отрицательно влияет на качество. Так, например, увеличение влажности некоторых видов утеплителя всего на несколько процентов, ухудшают их теплозащитные свойства на порядок. Мокрый пеноблок или даже кирпич значительно теряют свои показатели по прочности и т.д. Влажность стройматериалов измеряется отношением массы воды, находящейся в стройматериале в период замера к нормативной массе сухого материала.
Водопроницаемость строительного материала – это свойство материала пропускать воду под давлением. Измеряется водопроницаемость количеством воды, прошедшей в течении одного часа через строительный материал площадью 1 кв. м. и толщиной 1 м при постоянном давлении 1МПа. Водопроницаемость строительного материала тем больше, чем больше пор в его структуре. Стройматериалы, не имеющие пор, а так же материалы которые имеют закрытые поры, например, специальный бетон, относятся к водонепроницаемым материалам. Водопроницаемость характеризуется коэффициентом фильтрации kф=Vв*а/[S(p1-p2)t], где kф=Vв — количество воды, м³, проходящей через стенку площадью S = 1 м², толщиной а = 1 м за время t = 1ч при разности гидростатического давления на границах стенки p1 — p2 = 1 м вод. ст. Строительные материалы по своей водонепроницаемости характеризуются марками W2; W4; W8; W10; W12. Чем ниже коэффициент фильтрации kф, тем выше марка по водонепроницаемости.
Воздухостойкость строительных материалов – это способность материала выдерживать многократные насыщения водой и высыхание без значительных изменений физического состояния стройматериала. Разные строительные материалы по разному «переносят» многократное намокание и высыхание. Чаще всего этот процесс вызывает деформацию, потерю прочности и как итог потерю несущей способности строительной конструкции. Для повышения воздухостойкости строительные материалы покрывают гидрофобными составами или вводят в их состав гидрофобизаторы.
Газостойкость строительных материалов – свойство материала сохранять свои основные характеристики при контакте с газами, находящимися в окружающей среде, такими как, например, углеводород.
Гигроскопичность строительных материалов – способность материалов впитывать водяной пар из воздуха. Существует огромное количество строительных материалов, которые способны впитывать в себя значительное количество водяного пара. К таким материалам относятся: дерево, пенобетон, теплоизоляционные материалы и т.д. Строительные материалы с повышенной гигроскопичностью при полном насыщении водой теряют свои свойства, а так же могут изменять геометрические размеры. Для защиты строительных материалов от насыщения водяными парами применяют водоотталкивающие защитные составы.
Звукопоглощение строительных материалов – способность материала поглощать звук или снижать его уровень при прохождении через материал. Эта способность строительных материалов в первую очередь зависит от толщины, пористости материала и многослойности материала. Чем больше пор в материале, тем выше его способность поглощать звук. Звукопоглощение строительных материалов принято оценивать коэффициентом звукопоглощения т. е. отношением энергии, поглощенной материалом, к общему количеству падающей энергии в единицу времени. За единицу звукопоглощения условно принимают звукопоглощение 1 м2 открытого окна. Коэффициент звукопоглощения может изменяться в пределах от 0 до 1. Если звукопоглощение равно 0, то звук полностью отражается от строительного материала. Если же этот коэффициент приближается к 1 то звук полностью поглощается материалом. Согласно нормативным показателям СНиП стройматериалы, имеющие коэффициент звукопоглощения не менее 0,4 при частоте 1000 Гц, могут относиться к звукопоглощающим материалам. Коэффициент звукопоглощения определяется практическим способом в акустической трубе и подсчитывается по формуле: А(зв)=Е(погл)/Е(пад)
А(зв) — коэффициент звукопоглощения;
Е(погл) — поглощённая звуковая волна;
Е(пад) — падающая звуковая волна;
Табл. Сравнительные показатели коэффициента звукопоглощения строительных материалов
Наименование стройматериала |
Коэффициент звукопоглощения при 1000 Гц |
Деревянная стена |
0,06-0,1 |
Кирпичная стена |
0,032 |
Бетонная стена |
0,015 |
Минеральная вата |
0,45-0,95 |
Звукопроницаемость строительных материалов – способность материалов пропускать через свою толщу звуковую волну. Характеризуется звукопроницаемость строительных материалов коэффициентом звукопроницаемости, который показывает относительное уменьшение силы звука при прохождении его через толщу строительного материала. Звукопроницаемость практически является отрицательным свойством строительных материалов. Например, коэффициент звукопроницаемости деревянной перегородки толщиной 2,5 см равен 0,65, а бетонной стены такой же толщины – 0,11.
Звукопроводность строительных материалов – это способность тех или иных материалов пропускать звуки и шумы через свою толщу. Хорошими проводниками звука считаются строительные материалы большой плотности и прочности. Материалы, имеющие большое количество воздушных пор плохо передают звук и шум. Силу звука измеряют в децибелах (дБ). А звукопроводность строительных материалов характеризуется коэффициентом звукопроводности (t = Iпр/Iпад) который равен отношению прошедшего через материал звука к падающему.
Звукоизоляция строительных материалов – это величина и характеризует процесс отражения звука каким-либо материалом. В связи с разной природой возникновения звуковых волн, различают звукоизоляцию от воздушного шума, это когда источник возникновения шума не связан с ограждающей конструкцией физически и и изоляцию от ударного шума, когда между источником и ограждающей конструкцией имеется контакт, например, стук молотка по стене. В СНиП нормируемым показателем звукоизоляции является индекс изоляции воздушного шума Iв, дБ. Его определяют формуле, как средневзвешенное значение звукоизоляции конструкции в диапазоне частот от 100 до 5000 Гц в третьоктавных полосах частот. Величина Rw также определяет средневзвешенную звукоизоляцию конструкции в том же диапазоне частот, но по несколько иной методике. Разница между Iв и Rw составляет 2 дБ, т.е. Rw = Iв + 2 дБ. Звукоизоляция строительных материалов и конструкций зависит от пористости материала, его толщины, наличия в материале или конструкциях отверстий и примыканий к другим конструкциям.
Истираемость строительных материалов – свойство материалов сопротивляться истирающим воздействиям. Истираемость определяется лабораторным путем на образцах. Характеристика истираемости строительных материалов указывает на стойкость материала к износу и оценивается потерей массы материала относительно ее плотности или же уменьшением толщины материала. Чем хуже истираемость строительного материала, тем он более износостоек. Облицовочнные строительные материалы делятся на 5 групп по показателям истираемости: первая группа – гранит, кварциты;
вторая группа – мрамор, плотные базальты;
третья группа – рыхлые базальты и мрамор;
четвертая группа – цветные мраморы, травентины, известняки;
пятая группа – рыхлые известняки.
Истинная плотность строительных материалов — это масса единицы объёма материала в абсолютно плотном состоянии. ρ =m/Va, где Va объём в плотном состоянии. [ρ] = г/см³; кг/м³; т/м³. Способы истинной плотности лабораторные : предварительно высушенную пробу измельчают в порошок, объём определяют в пикнометре (он равен объёму вытесненной жидкости).
Износ строительных материалов — свойство материала сопротивляться одновременно воздействию истирающих и ударных нагрузок. Износ определяют лабораторным путем в барабане со стальными шарами или без них.
Качество строительных материалов — это совокупность свойств материала, обуславливающих его способность удовлетворять определённым требованиям, в том числе и нормативным соответствии с его назначением.
Красящая способность – это свойства пигментов ЛКМ при смешивании с другими пигментами передавать свой цвет. Относительную красящую способность ЛКМ определяют лабораторным путем в соответствии с ГОСТ, или визуальным методом путем сравнивая образцов.
Кислотостойкость строительных материалов – способность материалов сохранят свои основные качества и характеристики под воздействием кислот.
Коррозионная стойкость строительных материалов – это свойство материала сохранять свои основные качества под агрессивным воздействием внешней среды. Коррозия бывает биологическая, химическая и электрохимическая. Наиболее распространенное коррозийное проявление – это старение стройматериалов под действием воздействие ультрафиолетового излучения и перепад температур и влажности воздуха.
Механические свойства строительных материалов – это твердость, пластичность, жесткость предел прочности при сжатии, растяжении и изгибе.
Морозостойкость строительных материалов – это свойство строительного материала, определяющее способность выдерживать многократное замораживание и размораживание, без проявления явных отклонений от нормы качества. Хорошими морозостойкими свойствами обладают строительные материалы, имеющие показатели с низким водопоглощением. Для определения марки стройматериала по морозостокойсти циклы попеременного замораживания производят в пределах от минус 20 °C до плюс 20 °C. Показатель морозостойкости строительных материалов обозначаются символами F100; F25; F50.. F500, где цифрами показано число циклов замораживания и оттаивания.
Таб. Морозостойкость строительных материалов в зависимости от водопоглощения и предела прочности при разрыве
Материал |
Водопоглощение, % |
Плотность, г/см3 |
Rразр, МПа |
Морозостойкость, количество циклов |
Кирпич керамический |
8. |
1,6…1,9 |
0,9..3,5 |
15…50 |
Бетон ячеистый |
40…60 |
0,5…1,2 |
0,078… 1 |
15…75 |
Бетон легкий |
— |
0,8…1,8 |
0,8..3,2 |
25…400 |
Бетон тяжелый |
3…10 |
2,2…2,5 |
0,8..3,2 |
50. |
Асбестоцемент |
20…25 |
1,6…1,8 |
10..15 |
50…100 |
Насыпная плотность строительных материалов — это масса единицы объёма насыпных рыхлых зернистых или волокнистых материалов.
Огнестойкость строительных материалов – это способность материалов сохранять свои основные характеристики под действием высоких температур. По степени огнестойкости строительные материалы делятся на: сгораемые (пластмассы, дерево, кровельные битумные материалы и т.д.), трудносгораемые и несгораемые.
Огнеупорность строительных материалов – это способность материала не терять своих основных качеств (не деформироваться, не расплавляться, не трескаться и т.п.) при длительном воздействии высоких температур. По своей огнеупорности строительные материалы делятся на легкоплавкие, тугоплавкие (до 1580°C), огнеупорные (выше 1580 °C).
Относительная плотность строительных материалов – это отношение общего объема твердого вещества в строительном материале ко всему объему материала или отношение средней плотности материала к ее истинной плотности.
Открытая пористость строительных материалов – это свойство строения материалов, когда поры сообщаются с окружающей средой и между собой. Так, например, при погружении материала с открытыми порами в воду, они должны заполниться водой. Открытые поры увеличивают проницаемость и снижают морозостойкость.
Предел огнестойкости строительных материалов – это продолжительность сопротивления строительного материала или строительной конструкции (в часах) воздействию высоких температур до исчерпания ее несущей или ограждающей способности, а так же потерей своих основных качеств. Наступление предела огнестойкости характеризуется так же повышением температуры в любой точке строительной конструкции более чем 220 °С от начальной температуры конструкции.
Плотность строительных материалов – одна из основных характеристик материала, которая определяется как отношение отношением массы к объему строительного материала (кг/кв.м.).
р0 = m/V1
где m — масса материала, кг;
V1 — объем материала в естественном состоянии, м3.
Различают истинную и среднюю плотность строительных материалов. Средняя плотность стройматериала — это отношение его массы ко всему объему, включая поры. Истинная плотность — это отношение массы материала к объему без учета пустот и пор.
Табл. Примеры истинной и средней плотности строительных материалов
Материал |
Плотность, кг/м3 |
|
Истинная плотность |
Средняя плотность |
|
Сталь строительная |
7850-7900 |
7800-7850 |
Гранит |
2700-2800 |
2600-2700 |
Известняк |
2400-2600 |
1800-2400 |
Керамический кирпич |
2600-2700 |
1600-1900 |
Тяжелый бетон |
2600-2900 |
1800-2500 |
Поропласты |
1000-1200 |
20-100 |
Пористость строительных материалов — это показатель заполнения материала порами ( пустотами, наполненными воздухом)
Пористость материала измеряется в процентах и рассчитывается по формуле:
П = (1-р0/р)*100%,
где р0 -средняя плотность материала, кг/м3;
р- истинная плотность материала, кг/м3.
Чем больше пор в строительном материале, тем больше проявляет свои теплоизоляционные качества.
Прочность строительных материалов – свойство строительного материала сопротивляться разрушению под действием внешних и внутренних сил. Прочность оценивается таким показателем как предел прочности. Для хрупких строительных материалов, таких как кирпич или бетон, основной прочностной характеристикой является предел прочности при сжатии. Для металлических материалов более важной считается прочность при изгибе и растяжении.
Предел прочности строительных материалов — отношение разрушающей нагрузки Р(Н) к площади сечения образца F (см2). Предел прочности строительных материалов устанавливается лабораторным путем. Строительные материалы в зависимости от предела прочности делятся на марки и классы. Марки записываются в кгс/см², а классы — в МПа. Класс характеризует гарантированную прочность.
Релаксация строительного материала — свойство материала самопроизвольно снижать напряжения при условии, что начальная ее величина деформации зафиксирована жесткими связями и остается неизменной. При релаксации напряжений может измениться характер начальной деформации, например из упругой постепенно перейти в необратимую, при этом изменения размеров не происходит.
Технологические свойства строительных материалов – это скорость твердения, теплоустойчивость, скорость высыхания, удобоукладываемость.
Теплопроводность строительных материалов — это способность материала передавать тепло через толщу строительного материала или строительной многослойной конструкции. Теплопроводность строительного материала зависит от многих показателей и прежде всего от структуры и наличия воздушных пор и наличием влаги в материале. Теплопроводность строительного материала измеряется количеством тепла, передающимся через материал толщиной в 1 м, площадью 1 кв.м. за 1 час при разнице температур в 1 °C.
Теплоёмкость строительных материалов — это то количество тепла, которое необходимо сообщить 1 кг материала, чтобы повысить его температуру на 1 °C. С повышением влажности возрастает теплоёмкость материалов.
Упругость строительных материалов – свойство материалов после снятия нагрузки принимать свою первоначальную форму и размеры.
Ударная вязкость строительных материалов — свойство материала сопротивляться ударным нагрузкам. Ударная вязкость строительных материалов устанавливается экспериментальным путем в лабораторных условиях.
Укрывистость ЛКМ – способность ЛКМ делать одноцветную поверхность, уменьшать контраст между предыдущим слоем и последующим. Количественно укрывистость выражают в граммах краски, необходимой для того, чтобы сделать невидимым цвет закрашиваемой поверхности площадью один квадратный метр.
Твердость строительных материалов – свойство материала оказывать сопротивление проникновению в него другого материала. Показатели твердости выводят экспериментальным путем. Показатели твердости, полученные разными способами (например, «вдавливанием» и «царапанием») нельзя сравнивать между собой.
Химическая стойкость строительных материалов – это способность материалов сопротивляться действию агрессивной среды и другим воздействиям на химическом уровне, способность противостоять химическим реакциям, приводящим к потере основных качеств материала.
Физические свойства строительных материалов – это общепринятые свойства материалов: плотность, влажность, теплопроводность и т.п.
Щелочестойкость строительных материалов – свойство материалов сохранять свои основные качества при воздействии на них щелочей. В строительстве наибольшей щелочной агрессивностью считаются каустическая сода и растворы едкого калия.
Промышленная технология лекарств. Электронный учебник
2.4. Свойства порошкообразных лекарственных субстанций
Свойства исходных лекарственных веществ во многом предопределяют рациональный способ. В качестве исходных материалов применяют сыпучие вещества в виде порошкообразных (размер частиц 0,2 мм) или гранулированных (размер частиц от 0,2 до 3 мм) форм, которые имеют следующие свойства:
- физические – плотность, форма, размер и характер поверхности частиц, удельная поверхность частиц, силы адгезии (слипание на поверхности) и когезии (слипание частиц внутри тела), поверхностная активность, температура плавления и др.
;
- химические – растворимость, реакционная способность и др.;
- технологические – объемная плотность, степень уплотнения, сыпучесть, влажность, фракционный состав, дисперсность, пористость, прессуемость и др.;
- структурно-механические – пластичность, прочность, упругость, вязкость кристаллической решетки и др.
Эти свойства часто подразделяют на две большие группы: физико-химические и технологические.
2.4.1. Физико-химические свойства
Форма и размер частиц. Порошкообразные лекарственные субстанции являются грубодисперсными системами и имеют частицы различных форм и размеров. Большинство из них является кристаллическими системами; аморфное состояние встречается реже.
У многих лекарственных препаратов частицы анизодиаметрические (несимметричные, разноосные). Они могут быть удлиненной формы, когда длина значительно превышает поперечные размеры (палочки, иголки и т. п.), или пластинчатыми, когда длина и ширина значительно больше толщины (пластинки, чешуйки, таблички, листочки и т.п.). Меньшая часть порошкообразных веществ имеет частицы изодиаметрические (симметричные, равноосные) – это шаровидные образования, глыбки, многогранники и т.п.
Форма и размер частиц порошков зависят: у кристаллических веществ (химико-фармацевтические препараты) – от структуры кристаллической решетки и условий роста частиц в процессе кристаллизации, у измельченных растительных материалов – от анатомо-морфологических особенностей измельченных органов растений и типа измельчающей машины.
Размер частиц порошков определяют по их длине и ширине, которые измеряют с помощью микроскопа, снабженного микрометрической сеткой, при увеличении в 400 или 600 раз.
Форму частиц устанавливают по отношению средней длины частиц к средней ширине. При этом методе частицы условно подразделяются на три основные вида: удлиненные – отношение длины к ширине – более чем 3:1; пластинчатые – длина превышает ширину и толщину но не более чем в 3 раза; равноосные – имеют шарообразную, многогранную форму близкую к изодиаметрической.
Существует 6 кристаллических систем: кубическая, гексагональная, тетрагональная, ромбическая, моноклиническая, триклиническая.
Наибольшее количество среди кристаллических продуктов составляют вещества моноклинической системы ~40%, кубической ~10%, гексагональной ~7%, тетрагональной ~5%, ромбической ~28%, триклинической ~10%.
Известно, что только вещества, принадлежащие к кубической системе, прессуются в таблетки непосредственно, т.е. прямым прессованием, без грануляции и вспомогательных веществ (натрия хлорид, калия бромид).
Обычно порошки, имеющие форму частиц в виде палочек, характеризуются мелкодисперсностью, хорошей уплотняемостью и достаточной пористостью (анальгин, норсульфазол, акрихин и др.).
Порошки с равноосной формой частиц – крупнодисперсные, с малой степенью уплотнения, малой пористостью (лактоза, гексаметилентетрамин, салол). Чем сложнее поверхность частиц порошка, тем больше сцепляемость и меньше сыпучесть, и наоборот.
Физические свойства порошков определяются удельной и контактной поверхностью и истинной плотностью.
Удельная поверхность – суммарная поверхность, которую занимает порошкообразное вещество, а контактная поверхность – поверхность, которая образуется при соприкосновении между собой частицами порошка.
Истинная плотность порошка определяется отношением массы препарата к его объему при нулевой пористости порошка. В качестве сравнения используют любую жидкость, смачивающую, но не растворяющую порошок. Определение проводят с помощью волюметра (пикнометра для порошкообразных твердых веществ). Истинную плотность ρ (кг/м3) порошка определяют по формуле:
,
где m – масса вещества, г;
ρж – плотность жидкости, г/см3;
m1 – масса волюметра с веществом, г;
m2 – масса волюметра с жидкостью и веществом, г.
По коэффициенту контактного трения (f) косвенно судят об абразивности таблетируемых масс. Чем больше его значение, тем более стойким к износу должен быть пресс-инструмент таблеточных машин.
Для таблетирования важное значение имеют также химические свойства исходных веществ такие как: наличие кристаллизационной воды, растворимость, смачиваемость и гигроскопичность.
Смачиваемость. Под смачиваемостью порошкообразных лекарственных веществ понимается их способность взаимодействовать с различными жидкостями (лиофильность) и прежде всего с водой (гидрофильность). На поверхности твердых частиц лекарственных субстанций содержится то или иное количество гидрофильных групп (–ОН, –СОН, –СООН и др.) или кислородных атомов, являющихся структурными элементами их кристаллической решетки, поэтому смачиваемость поверхности порошков имеет разную величину в зависимости от интенсивности взаимодействия межмолекулярных сил. Визуально склонность поверхности порошков к смачиванию водой проявляется: а) полным смачиванием – жидкость полностью растекается по поверхности порошка; б) частичным смачиванием – вода частично растекается на поверхности; в) полным несмачиванием – капля воды не растекается, сохраняя форму, близкую к сферической. Гидрофобные (не смачиваемые водой) вещества могут прекрасно смачиваться другими жидкостями – например, органическими растворителями.
Лиофильность таблетируемых поршкообразных веществ определяется коэффициентом фильности, который представляет собой отношение удельной теплоты смачивания полярной жидкостью (вода) к удельной теплоте смачивания неполярной жидкостью. Известно, что образование на поверхности твердой частицы мономолекулярного слоя смачивающей жидкости всегда сопровождается выделением так называемой теплоты смачивания.
Практическое значение смачиваемости заключается в том, что в таблетку, полученную прессованием хорошо смачиваемых водой веществ, легко проникает вода, что ускоряет распадаемость таблетки.
Гигроскопичность. Если упругость паров в воздухе больше, чем их упругость на поверхности твердых частиц, тогда порошкообразная масса, подготовленная к таблетированию, начнет поглощать пары из воздуха и расплываться в поглощенной воде. Кинетику влагопоглощения определяют весовым методом в нормальных (обычных) условиях, в экстремальных (эксикаторе над водой – 100% относительная влажность), или же в климатической камере.
Если субстанция сильно гигроскопична, это предопределяет применение вспомогательных веществ – влагостимуляторов.
Кристаллизационная вода. Молекулы кристаллизационной воды определяют механические (прочность, пластичность) и термические (отношение к температуре воздушной среды) свойства кристалла и оказывают существенное влияние на поведение кристалла под давлением. Явление «цементации» также тесно связано с наличием кристаллизационной воды в таблетируемых субстанциях.
Электрические свойства. Явление электризации порошкообразных лекарственных веществ при их обработке и прессовании дают основание сделать вывод, что при рассмотрении природы связи частиц в таблетках наряду с деформационными необходимо принимать во внимание также диэлектрические характеристики. При механическом воздействии будут склонны к поляризации все ассиметрические кристаллы, содержащие полярные группы в своей структуре или в адсорбционной водной пленке. Для неполярных веществ образование поверхностных зарядов исключается.
2.4.2. Технологические свойства
Технологические свойства порошкообразных лекарственных веществ зависят от их физико-химических свойств.
Фракционный (гранулометрический) состав, или распределение частиц порошка по крупности, оказывает определенное влияние на сыпучесть его, а следовательно, на ритмичную работу таблеточных машин, стабильность массы получаемых таблеток, точность дозировки лекарственного вещества, а также на качественные характеристики таблеток (внешний вид, распадаемость, прочность и др).
Наиболее быстрым и удобным методом определения дисперсности является ситовой анализ. Техника этого анализа заключается в том, что 100,0 г исследуемого порошка просеивают через набор сит (диаметр отверстий 2,0; 1,0; 0,5; 0,25 и 0,1 мм). Навеску материала помещают на самое крупное (верхнее) сито и весь комплект сит встряхивают (вручную или на виброустановке) в течение 5 минут, а затем находят массу каждой фракции и ее процентное содержание.
Исследования фракционного состава фармацевтических порошков, подлежащих таблетированию, показали, что большинство из них содержит в подавляющем количестве мелкую фракцию (менее 0,2 мм) и поэтому обладают плохой сыпучестью. Они плохо дозируются по объему на таблеточных машинах, таблетки получаются неодинаковыми по массе и прочности. Фракционный состав порошков можно изменить с помощью направленного гранулирования, которое позволяет получить определенное количество крупных фракций.
Очень важно определение таких объемных показателей порошков как: насыпная и относительная плотность и пористость.
Насыпная (объемная) плотность – масса единицы объема свободно насыпанного порошкообразного материала. Насыпная плотность зависит от формы, размера, плотности частиц порошка (гранул), их влажности. По значению насыпной плотности можно прогнозировать объем матричного канала. Определение насыпной плотности порошка проводят на приборе модели 545Р-АК-3 Мариупольского завода технологического оборудования (рис. 2.1).
Рис. 2.1. Прибор для определения максимальной насыпной плотности порошков
1 – измерительный цилиндр; 2 – шкала; 3 – тумблер; 4 – регулировочный винт; 5 – контргайка
Взвешивают 5,0 г порошка с точностью до 0,001 г и засыпают его в измерительный цилиндр. Устанавливают амплитуду колебаний (35-40 мм) посредством регулировочного винта и после отметки по шкале фиксируют положение контргайкой. Частоту колебаний устанавливают при помощи трансформатора в пределах 100 – 120 кол/мин по счетчику. Далее включают прибор тумблером и следят за отметкой уровня порошка в цилиндре. Когда уровень порошка становится постоянным (обычно до 10 мин), прибор отключают.
Насыпную плотность рассчитывают по формуле:
,
где ρн – насыпная плотность, кг/м3;
m – масса сыпучего материала, кг;
V – объем порошка в цилиндре после уплотнения, м3.
В зависимости от насыпной плотности различают порошки следующим образом:
ρн > 2000 кг/м3 – весьма тяжелые;
2000 > ρн > 1100 кг/м3 – тяжелые;
1100 > ρн > 600 кг/м3 – средние;
ρн < 600 кг/м3 – легкие.
Относительная плотность – отношение насыпной (объемной) плотности к истинной плотности:
,
где ρн – насыпная плотность, кг/м3;
ρ – истинная плотность (удельная масса), кг/м3.
Пористость – объем свободного пространства (пор, пустот) между частицами порошка.
Пористость определяется, исходя из значений насыпной (объемной) плотности и истинной плотности:
где ρн – насыпная плотность, кг/м3;
ρ – истинная плотность (удельная масса), кг/м3;
τ – относительная плотность.
От этих объемных характеристик зависит способность порошка к сжатию под давлением.
Коэффициент уплотнения (сжатия) – отношение высоты порошка в матрице (Н1) к высоте полученной таблетки (Н2):
.
Определение проводят в матрице. Матричный канал заполняют порошком и осуществляют давление прессования 1200 кг/см2. Полученную таблетку выталкивают пуансоном и замеряют высоту.
На способность порошкообразных препаратов к сжатию оказывают влияние форма частиц, способность последних к перемещению и деформации под влиянием давления. Коэффициент уплотнения является существенным технологическим фактором; в частности чем больше он, тем больше времени тратится на прессование. При этом расходуется больше усилий и на выталкивание таблетки из глубины матричного канала.
При таблетировании наиболее важными технологическими свойствами являются сыпучесть, прессуемость и скольжение, позволяющее легко выталкивать таблетку из матрицы.
Текучесть (сыпучесть) – способность порошкообразной системы высыпаться из емкости воронки или «течь» под силой собственной тяжести и обеспечивать равномерное заполнение матричного канала. Материал, имеющий плохую сыпучесть в воронке, прилипает к ее стенкам, что нарушает ритм его поступления в матрицу. Это приводит к тому, что заданная масса и плотность таблеток будут колебаться.
Сыпучесть определяют на вибрационном устройстве для снятия характеристик сыпучих материалов ВП-12А (Рис. 2.2).
Рис. 2.2. Устройство прибора модели ВП-12А
а – измерение сыпучести; б – измерение угла естественного откоса;
1 – воронка; 2 – крышка; 3 – тумблер; 4 – заслонка; 5 – электромагнит;
6 – якорь; 7 – амортизатор; 8 – тяга; 9 – шарнир; 10 – приемный стакан;
11 – горка; 12 – кольцо; 13 – угломер
В приборе предусмотрена вибрация конусной воронки путем жесткого соединения его с электромагнитным устройством, работающим от сети переменного тока. Навеску порошка (гранул) массой 50,0 г (с точностью до 0,01 г) засыпают в воронку при закрытой заслонке, включают прибор и секундомер. После 20 с утряски, необходимой для получения стабильных показаний, открывают заслонку и фиксируют время истечения материала из воронки. Точность времени истечения – до 0,2 с.
Сыпучесть рассчитывают по формуле:
,
где: Vc – сыпучесть, кг/с;
m – масса навески, кг;
t – полное время опыта, с;
20 – время утряски, с.
При определении сыпучести порошков с малой насыпной плотностью допускается использование навески массой 30,0 г. С помощью прибора ВП-12А определяется также угол естественного откоса – угол между образующей конуса сыпучего материала и горизонтальной плоскостью. Угол естественного откоса изменяется в широких пределах – от 25 до 30°С для хорошо сыпучих материалов и 60-70°С для связанных материалов.
Сыпучесть порошков является комплексной характеристикой, определяемой дисперсностью и формой частиц, влажностью масс, гранулометрическим составом. Эта технологическая характеристика может быть использована при выборе технологии таблетирования. Порошкообразные смеси, содержащие 80-100% мелкой фракции (размер частиц меньше 0,2 мм), плохо дозируются, поэтому необходимо проводить направленное укрупнение частиц таких масс, т.е. гранулирование. Если мелкой фракции содержится до 15%, возможно использование метода прессования.
Прессуемость – способность частиц порошка к когезии под давлением, т.е. способность частиц под влиянием сил электромагнитной природы (молекулярных, адсорбционных, электрических) и механических зацеплений ко взаимному притяжению и сцеплению с образованием устойчивой прочной прессовки.
Непосредственных методов определения прессуемости нет.
Прессуемость характеризуется прочностью модельной таблетки после снятия давления. Чем лучше прессуемость порошка, тем выше прочность таблетки. Если прессуемость плохая, таблетка получается непрочной, а иногда полностью разрушается при выталкивании из матрицы.
При определении прессуемости порошка (гранулята) навесу массой 0,3 или 0,5 г прессуют в матрице с помощью пуансонов диаметром 9 мм и 11 мм на гидравлическом прессе при давлении 120 МПа. Полученную таблетку взвешивают на торсионных весах, высоту измеряют микрометром и коэффициент прессуемости (Кпресс, г/мм) вычисляют по формуле:
,
где: m – масса таблетки, г;
Н – высота таблетки, мм.
Установлено, что:
По результатам определения прессуемости таблеточных масс делают заключение о технологии таблетирования.
Сила выталкивания таблеток из матрицы. Для выталкивания запрессованной таблетки из матрицы требуется затратить силу, чтобы преодолеть трение и сцепление между боковой поверхностью таблетки и стенкой матрицы. С учетом величины силы выталкивания прогнозируют добавки антифрикционных (скользящих или смазывающих) веществ. При определении силы выталкивания навеску порошка массой 0,3 или 0,5 г прессуют в матрице с диаметром 9 или 11 мм соответственно на гидравлическом прессе при давлении 120 МПа. Выталкивание запрессованной таблетки производят нижним пуансоном. При этом на манометре пресса регистрируется выталкивающее усилие.
Расчет выталкивающего усилия производят по формуле:
где: Рвытал – давление выталкивания, МПа;
Рман – показание манометра, МПа;
Sпл – площадь плунжера, м2;
Sбок – площадь боковой поверхности таблетки, м2.
Площадь боковой поверхности таблетки рассчитывается по формуле:
Sбок = 2 · π · r ·h,
где: r – радиус таблетки, м;
h – высота таблетки, м.
Природа связи частиц в таблетках. Таблетирование основано на использовании свойств порошкообразных лекарственных веществ уплотняться и упрочняться под давлением. При этом слабоструктурный материал превращается в связнодисперсную систему с определенной величиной пористости. Такая система во многом близка по свойствам к компактному телу, в котором действуют определенные силы сцепления.
Прессуемость порошка – это способность его частиц к когезии и адгезии под давлением, т.е. способность частиц вещества под влиянием сил различной природы и механических зацеплений к взаимному притяжению и сцеплению с образованием прочной компактной таблетки. Под давлением частицы порошка как бы спаиваются, слипаются, сцепляются между собой и слабоструктурная дисперсная система превращается в однородное твердое тело.
Предложены три теории прессования (или таблетирования): механическая, капиллярно-коллоидная и электростатическая.
Механическая теория.Прессование является определяющей операцией при изготовлении таблеток. В современных промышленных прессах производится двустороннее сжатие порошка верхним и нижним пуансонами. При движении пуансонов в матрице происходит ступенчатое изменение состояния порошка, представленное на рис. 2.3.
Рис. 2.3. Зависимость объема порошка от давления прессования
Весь процесс прессования разбивается на три стадии прессования: 1) уплотнение (подпресовка), 2) образование компактного тела, 3) объемное сжатие образовавшегося компактного тела.
В каждой из этих стадий протекают характерные для нее механические процессы. В начале сжатия происходит перераспределение частиц: малые частицы укладываются в промежутках между большими и ориентируются в направлениях, обеспечивающих максимальное сопротивление сжатию (участки А и В). Усилия, преодолеваемые при этом незначительны, уплотнение становится заметным уже при малых давлениях. Прилагаемая энергия в основном расходуется на преодоление внутреннего (между частицами) и внешнего (между частицами и стенками матрицы) трения.
При увеличении давления в области ВС происходит интенсивное уплотнение материала за счет заполнения пустот и эластичная деформация частиц, которая способствует более компактной упаковке частиц. На этой стадии прессования из сыпучего материала образуется компактное пористое тело, обладающее достаточной механической прочностью.
После того, как частицы будут плотно сжаты в точках контакта, наблюдают пластическую деформацию (отрезок CD). На этой стадии при высоких величинах давления, когда механическая прочность таблеток изменяется незначительно, происходит, возможно, объемное сжатие частиц и гранул порошка без заметного увеличения контактных поверхностей.
В действительности между тремя стадиями нет резких границ, так как процессы, протекающие во второй стадии, имеют место в первой и третьей стадиях и можно говорить только о преимущественной роли отдельных процессов в каждой из них.
Дальнейшее увеличение давления приводит к разрушению кристаллов и образованию новых плоскостей и поверхностей контактов.
Многие исследователи считают, что механическая связь в таблетке обусловлена площадью контактирующих поверхностей, а также взаимным переплетением и зацеплением поверхностных выступов и неровностей частиц под давлением. В результате приложенного давления частицы сдвигаются, скользят друг по отношению к другу и вступают в более тесный контакт; симметричные скользят легче, чем шероховатые и анизодиаметрические, но последние создают большее количество зацеплений и поэтому придают прессованной таблетке большую прочность. Следствием уплотнения порошка под давлением является увеличение контакта между частицами, вызванного необратимой деформацией частиц. Необратимые деформации могут быть пластическими и хрупкими. При пластической деформации изменяется форма частиц, но не нарушается их структурная целостность, при хрупких деформациях обламываются выступы на поверхности частиц или сами частицы дробятся на более мелкие. В этом случае, чем прочнее и эластичнее частица, тем больше вероятность, что даже при высоких давлениях она сохранит свою целостность.
Прочность связей частиц в структуре таблеток из мягких элементов значительно ниже прочности из твердых. В первом случае после деформации частиц ярче проявляются тиксотропные явления, т.е. тиксотропное восстановление разрушенных связей под давлением интенсивного броуновского движения. Во втором – прочность сцепления определяется зацеплениями и переплетениями при пластической деформации твердых частиц, обуславливающих жесткий каркас таблетки с меньшим кинетическим уравнением тиксотропного восстановления связей.
Механическая теория не дает полного представления о механизме образования связей в фармацевтических композициях.
К механической теории структурообразования тиксотропное примыкает теория «сцепления». Согласно этой теории некоторые вещества обладают низкой температурой плавления. В результате разогревания пресс-инструмента в процессе прессования и трения частиц между собой эти вещества частично подплавляются, что способствует слипанию частиц.
Капиллярно-коллоидная теория. Согласно теории П.А. Ребиндера, силы межповерхностного взаимодействия во многом определяются характером твердых и наличием жидких фаз. Прочность структурированных систем зависит от количества воды и ее расположения. В гидрофильных веществах адсорбционная вода с толщиной пленки до 3 нм вследствие наличия на поверхности частиц ненасыщенного молекулярного силового поля является прочно связанной. Она не может свободно перемещаться и не обеспечивает адгезии между частицами, но и не препятствует силам сцепления. При увеличении влажности образуется более толстый, но менее прочный слой воды, так как через него действуют ван-дер-ваальсовы силы молекулярного притяжения, в различной степени ослабленные расстоянием. Прослойки воды в местах контакта играют также роль поверхностно-активной смазки и определяют подвижность частиц структуры и ее пластичность в целом под давлением. Чем тоньше слой жидкости, обволакивающей твердые частицы, тем сильнее проявляется действие молекулярных сил сцепления. В таком случае оказывается, что в пористой структуре таблеток капиллярная система заполнена водой. Так как в таблетках диаметр капилляров составляет 10–6 – 10–7 см, то после снятия давления сжатые капилляры стремятся расшириться и, по закону капиллярного всасывания, поглотить выжатую воду. Поскольку всасывающая сила в капиллярных системах с радиусом 10–6 см равняется примерно 14,7 мН/м2 (150 кг/см2), то при малой длине капилляров в них создается отрицательное давление, приводящее к сжатию стенок капилляров, а следовательно, к увеличению сил адгезии.
Электростатическая теория сцепления частиц. Капиллярно-коллоидная теория предполагает также наличие молекулярных сил сцепления, которые имеют электрическую природу и слагаются из совместного электростатического взаимодействия разноименных зарядов и квантово-механического эффекта притяжения.
Энергия адгезии, как одна из форм межмолекулярного взаимодействия, особенно проявляется при наличии полярных соединений. На поверхности частиц порошкообразных лекарственных веществ имеются активные кислородсодержащие группы, свободные радикалы и другие функциональные группы, которые обладают определенной силой взаимодействия. Поэтому в процессе формирования таблеток сцепление частиц под действием ван-дер-ваальсовых сил и величина адгезии будут максимальными в том случае, если молекулы соприкасающихся поверхностей могут вступить в максимальное число контактов.
Современная молекулярная физика разделяет молекулярные силы на дисперсионные, индукционные и электростатические. На долю дисперсионных приходится около 100% общей величины когезионных сил, но они являются неполярными и не зависят от наличия или отсутствия электрического заряда. Индукционные силы рассматриваются как полярные, и если полярность вещества невелика, то ими можно пренебречь. Электростатические характеризуются активностью положительных и отрицательных зарядов на поверхности молекул вещества. Они особенно активизируются при обработке поверхности проводящими электричество материалами (вода, поверхностно-активные вещества), в результате чего образуется двойной электрический слой ионов противоположного значения. Для неполярных веществ электрический механизм адгезии исключается.
Сцепление различных веществ с металлом пресс-инструмента с точки зрения электростатических сил обусловлено тем, что с приближением электрического заряда к поверхности металла он поляризуется и образующееся электрическое поле приводит к сильнейшему сцеплению. Отсюда следует, что полярные вещества дают особенно прочное сцепление с металлическими поверхностями.
Электрические свойства твердых дисперсных систем определяются их физико-химическими свойствами. У большинства порошкообразных лекарственных веществ диэлектрическая проницаемость невелика и находится в пределах 4,12-6,85, что говорит о сравнительно малой их поляризации и проводимости. По этим значениям таблетируемые вещества можно отнести к категории характерных твердых диэлектриков – асимметричных кристаллов с молекулярной связью и определенным содержанием полярных групп, в частности, гидроксилов ОН–, входящих в структуру молекулы или в состав адсорбционной пленки воды. Такие вещества в какой-то мере поляризуются при механическом воздействии и на поверхности их частиц образуются заряды. Факты явления электризации порошкообразных лекарственных веществ при их обработке и прессовании позволяют сделать вывод, что диэлектрические характеристики наряду с деформационными также необходимы при рассмотрении механизма связи частиц в таблетках. При изучении электрических свойств порошкообразных лекарственных веществ оказалось, что в процессе прессования одновременно с ориентацией частиц, трением поверхностей, сжатием в каком-либо направлении происходит их поляризация и возникновение поверхностных зарядов. При соприкосновении частиц между собой или со стенкой матрицы электрические заряды, находящиеся на поверхности, притягивают равные по величине и обратные по знаку заряды. На границе возникает контактная разность потенциалов, величина которой зависит от электропроводимости поверхностей контактирующих частиц и плотности зарядов. Увеличение контактной разности потенциалов неизменно влечет и увеличение сил когезии. Когезионная способность гидрофильных веществ значительно больше так, как они обладают большей поверхностной электропроводимостью, гидрофобных – меньше.
Кажущаяся плотность – обзор
12.4.3.1 Процесс формования кокса
Кажущаяся плотность угольных брикетов настолько высока, что теоретически можно получить высокопрочный кокс из полумягких коксующихся углей, если их плотность поддерживается высокой во время карбонизации. При этом производительность в традиционной щелевой коксовой печи регулируется теплопроводностью через уголь и коксовый слой шириной 400–500 мм. Однако эту длину теплопроводности можно уменьшить за счет прямого нагрева угольных брикетов размером около 50 мм для повышения производительности.Увеличение скорости нагрева может улучшить спекаемость угля, что благоприятствует использованию полумягких коксующихся углей.
Процесс формирования кокса разрабатывался в Японии в качестве национального проекта с 1978 по 1987 год (Миура и Окухара, 1983; Окухара и др., 1990). В этом процессе смесь углей и каменноугольного пека брикетируют, а брикеты карбонизируют в шахтной печи путем подачи горячего дымового газа через верхнюю и нижнюю фурмы для непрерывного производства формируемого кокса.
Основными техническими проблемами, которые необходимо было решить в процессе карбонизации, были (1) разрушение и слипание брикетов в результате размягчения связующего на начальной стадии карбонизации, (2) набухание брикетов из-за чрезмерной слеживаемости или недостаточное плавление угольных частиц из-за отсутствия слеживаемости, и (3) образование трещин в образовавшемся коксе, вызванное усадкой к концу карбонизации.
Разрушение и слипание брикетов предотвращали их быстрым нагревом в атмосфере 300–400 °С с образованием на их поверхности тонкого твердого слоя кокса. Набухание контролировали, нагревая их с определенной скоростью нагрева, которая была не достаточно высокой, чтобы вызвать их набухание, но и не настолько низкой, чтобы нарушить их способность к слеживанию, до тех пор, пока расплавленный уголь снова не затвердеет. Трещины были предотвращены путем ограничения скорости нагрева до определенного диапазона после повторного затвердевания. Другими словами, первоначальный быстрый нагрев с последующим умеренным нагревом при температуре около 600°C, как показано на рис.12.20, применяли для эффективного успешного карбонизации брикетов.
Рисунок 12.20. Соответствующие схемы нагрева брикетов в процессе формирования кокса. VM , летучее вещество; CI , индекс слеживаемости.
Воспроизведено с разрешения Miura, Y., Okuhara, T., 1983. Современный аспект развития технологии непрерывного производства формованного кокса.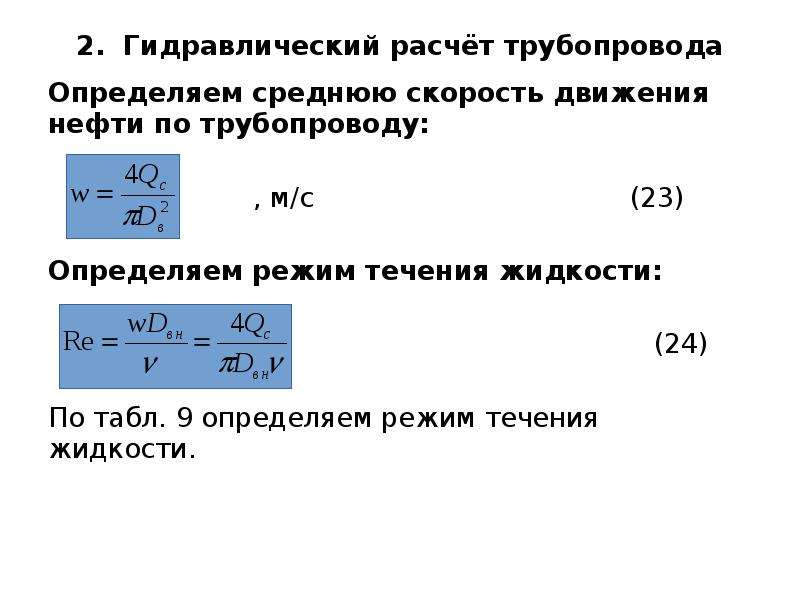
Двухступенчатый нагрев оказался идеальной схемой нагрева, как показано на рис.12.21. Профиль температуры в шахтной печи коксования показан на рис. 12.22.
Рисунок 12.21. Схема нагрева для двухстадийного нагрева в процессе формования кокса.
Воспроизведено с разрешения Miura, Y., Okuhara, T., 1983. Современный аспект развития технологии непрерывного производства формованного кокса. Сделки ISIJ 23, 700–709. © 1983, ISIJ.Рисунок 12.22. Температурный профиль в шахтной печи коксования в процессе формования кокса.
Воспроизведено с разрешения Miura, Y., Окухара Т., 1983. Современный аспект развития технологии непрерывного производства формованного кокса. Сделки ISIJ 23, 700–709. © 1983, ISIJ. Чтобы установить непрерывный процесс формирования кокса на прочной основе и производить кокс для коммерческого испытания доменной печи, на заводе Явата была построена пилотная установка производительностью 200 тонн в день. Завод начал работу в 1984 году и произвел 93 000 тонн формованного кокса за 580 дней до 1986 года. Технологическая схема процесса и составы шихты показаны на рис.12.23 и 12.24 соответственно.
Рисунок 12.23. Технологическая схема процесса образования кокса.
Воспроизведено с разрешения Miura, Y., Okuhara, T., 1983. Современный аспект развития технологии непрерывного производства формованного кокса. Сделки ISIJ 23, 700–709. © 1983, ISIJ.Рисунок 12.24. Состав угольной шихты в процессе формования кокса. VM , летучее вещество; CI , индекс слеживаемости.
Воспроизведено с разрешения Miura, Y., Okuhara, T., 1983. Современный аспект развития технологии непрерывного производства формованного кокса.Сделки ISIJ 23, 700–709. © 1983, ISIJ. Видно, что уголь из смесительных бункеров сначала высушивается, затем смешивается со вяжущим (мягкий пек), брикетируется и, наконец, хранится в брикетных бункерах. Угольные брикеты загружаются в верхнюю часть шахтной печи (6,45 м в длину, 1,25 м в ширину, 14 м в высоту), которая питается низкотемпературной газовой фурмой, высокотемпературной газовой фурмой и охлаждающей газовой фурмой. , и нагревается непосредственно восходящим горячим газом до 1000°C, в то время как брикеты опускаются в верхнюю часть печи.Температура образующегося газа, низкотемпературного газа и высокотемпературного газа составляет 350°С, 630°С и 1050°С соответственно. Образовавшийся кокс охлаждают до 100°С в нижней части путем вдувания газа с температурой 55°С и выгружают снизу печи. Генерируемый газ, извлекаемый из верхней части печи, охлаждается и рециркулирует в нагреватель высокотемпературного газа и нагреватель низкотемпературного газа. Охлаждающий газ, вводимый через дно печи, выбрасывается из зоны охлаждения и смешивается с газом, поступающим в низкотемпературную фурму.
Содержание ВМ и индекс слеживаемости углей, использованных в опытно-промышленных испытаниях, варьировались от 24% до 38% и от 45% до 72% соответственно. Качество кокса, полученного на опытной установке, было таким же, как и в коксовой печи щелевого типа. Автоматизация и герметизация устройств загрузки брикетов и выгрузки образовавшегося кокса, а также устройств циркуляции греющего газа, как и предполагалось изначально. На остановку и перезапуск оборудования карбонизации ушло 4 дня. Образовавшийся кокс, составляющий от 20% до 30% коксовой шихты, непрерывно использовался в доменной печи с внутренним объемом 4250 м 3 на заводе Явата в течение 74 дней.Это испытание подтвердило, что сформированный кокс можно использовать в настоящей доменной печи, как и кокс, полученный в коксовой печи щелевого типа. Пилотная установка была перезапущена в 1991 году, через 4 года после остановки, и на ее 239 дней эксплуатации (Oshima et al., 1993). Никаких заметных повреждений кирпичей внутри шахтной печи не наблюдалось, и было продемонстрировано, что установку можно легко перезапустить даже после ее полной остановки.
Характеристики FCP безвредны для окружающей среды благодаря карбонизации, происходящей в закрытой системе, гибкости с точки зрения производительности и способности работать с полумягкими коксующимися углями. Однако остается решить еще две проблемы. Во-первых, форма формируемого кокса, полученного на ФХП, более однородна, чем у обычного кокса, что увеличивает плотность упаковки кокса в доменной печи, а это делает газостойкость формируемого слоя кокса почти в два раза выше, чем у обычного кокса. обычного коксового слоя.Во-вторых, общее количество энергии, потребляемой в FCP, намного больше, чем в обычном процессе производства кокса. Для решения этой проблемы были проведены дальнейшие исследования, во-первых, для оптимизации формы формируемого кокса, чтобы уменьшить сопротивление сформированного слоя кокса газу, а во-вторых, для оптимизации профиля нагрева, чтобы уменьшить потребление энергии и образование трещин в коксе. (Комаки и др., 1994, 1996).
Значение плотности порошков: объемная плотность по сравнению с. Истинная плотность частиц
Какова плотность материала?
Фото Каролины Грабовской с сайта Pexels
Прежде чем мы начнем говорить конкретно об измерении плотности порошков, давайте рассмотрим концепцию измерения плотности в целом.
Что означает «плотность»?
Согласно Британской энциклопедии плотность определяется как масса единицы объема материального вещества. Формула плотности вещества: d = м / V , где d — плотность вещества, м — масса, а V — занимаемый им объем.
Измерение плотности обычно выражается в граммах на кубический сантиметр (г/см3) или (г/см3) или граммах на миллилитр (г/мл).Однако иногда его указывают в килограммах на кубический метр (кг/м3) или в килограммах на литр (кг/л).
Плотность зависит от температуры и давления, которые необходимо указать, если значение плотности должно быть известно с высокой точностью. Наличие примесей в том же объеме, таких как соленость воды, также будет влиять на плотность.
Как мы измеряем плотность?
Поскольку плотность является производным свойством, определяемым на основе взаимосвязи двух других характеристик материала, веса и объема, ее обычно не измеряют напрямую.Он вычисляется или выводится. Это зависит от того, что у нас есть надежное и точное измерение веса материала и соответствующего объема.
Задача выполнения этих измерений и расчетов кажется достаточно простой. Нам просто нужны точные весы и хороший способ измерения объема. В чем подвох?
Проблемы измерения плотности:
Фото Лины Кивака с сайта Pexels
Загвоздка заключается в том, что для многих материалов очень трудно, если вообще возможно, измерить вес и объем достаточно точно, чтобы мы могли разделить два измерения и вычислить плотность с достаточной точностью и надежностью, необходимой для проект.
Кроме того, мы делаем несколько критических допущений при измерении плотности.
Предположения:
- Мы предполагаем, что материал однороден на всем протяжении, все его части имеют одинаковую плотность. Например, мы предполагаем, что на поверхности или внутри материала нет воздушных карманов или поглощенной влаги. Очень немногие материалы в мире настолько чисты, однородны и однородны во всем.
- Мы предполагаем, что материал, состоящий из частей или компонентов, имеет идеальную упаковку, а компоненты идеально подходят друг к другу.Это определенно не относится к порошкам и любой ситуации, когда одновременно измеряется более одной части.
- Мы предполагаем, что межчастичная изменчивость отсутствует. Это может означать, что каждая крупинка соли или каждая горошинка перца в нашем образце по своей плотности идентичны всем остальным.
Эти предположения оправданы в большинстве случаев и могут быть приемлемыми, когда требуется только грубая оценка плотности. Знание этих предположений также помогает нам понять ограничения точности и прецизионности измерения плотности.
В чем разница между точностью и прецизионностью?
Фото Национального института рака на Unsplash
Плотность Точность:
Точность относится к тому, насколько надежным и последовательным является измерение. Является ли воспроизводимым и воспроизводимым ? Если два разных человека измерят его или используют две разные машины, насколько различны будут измерения? Что, если один и тот же человек несколько раз измерит один и тот же образец на одном и том же приборе, насколько различны будут результаты измерений? Насколько репрезентативна выборка? Изменится ли измерение, если будет взята другая проба?
Чем ближе измерения друг к другу, тем выше точность измерения.
Плотность Точность:
В то время как точность сравнивает, насколько близки измерения друг к другу или насколько велики различия между измерениями, точность относится к тому, насколько близки измерения к «истинному» значению. Например, если мы измеряем плотность как 1,00 г/куб. см, и наши измерения надежны и воспроизводимы, они точны. Но если фактическая плотность материала составляет 1,20 г/куб. см, наши измерения не очень точны.
Чем ближе измерение к фактическому значению, тем выше точность измерения.
Откуда мы знаем фактическое значение? Часто нет. Наши измерения объема и массы зависят от уровней калибровки нашего оборудования. Калибровка оборудования зависит от используемых калибровочных стандартов и процедур. Калибровочные стандарты сами по себе несут определенный уровень неопределенности. Невозможно провести измерение, которое было бы бесконечно точным и точным. Всегда есть какая-то степень погрешности.
Какая точность измерения плотности требуется?
Фото Жана Папийона на Unsplash
Должны ли мы знать плотность материала грубо и приблизительно, просто чтобы получить относительное представление о том, насколько он тяжел, или нам нужно знать плотность точно с точностью до многих значащих цифр, потому что это критическая переменная в дизайн нашего медицинского устройства, системы доставки лекарств, эксперимента по моделированию частиц, выделения биологической клетки или эксперимента по визуализации потока жидкости?
Бусины маркера плотности являются примером микросфер прецизионной плотности, которые используются в основном в биотехнологической промышленности для создания градиентов плотности, которые необходимы для разделения и очистки биологических клеток, вирусов и субклеточных частиц. Обычно используется набор из нескольких шариков маркеров плотности, охватывающих диапазон плотностей. Градиент калибруется с помощью шариков, которые плавают на разной высоте в колонке. Когда тестовый образец добавляется в колонку, он падает до точки нейтральной плавучести, а плотность определяется по калибровочной диаграмме.
Эти частицы прецизионной плотности с цветовой кодировкой имеют решающее значение для разделения биологических клеток на основе их плотности, что делает критически важными как точность, так и правильность плотности каждой частицы.
Исследователи и инженеры постоянно подталкивают производителей химической продукции к разработке материалов и методов измерения, обеспечивающих все более высокую точность измерения плотности материалов. Они также подталкивают нас к производству материалов с высокой точностью, точностью и настраиваемой плотностью.
Какова плотность порошков?
Здесь все становится сложнее. Нужно ответить на множество вопросов. Необходимо сделать много предположений о плотности порошка.
Фотография Евы Элиджас с сайта Pexels
Порошок состоит как минимум из тысяч, а часто из миллионов, миллиардов, триллионов и т. д. мелких частиц, которые могут сильно различаться по форме, размеру и даже плотности.
Проблемы с точным измерением плотности порошков начинаются с отбора статистически значимой и репрезентативной пробы порошка. Отбор проб порошков сам по себе является искусством и наукой по следующим причинам:
- Агрегация: В зависимости от размера и свойств поверхности порошкообразные частицы склонны агрегировать и слипаться независимо от того, сплавлены ли они вместе физически или удерживаются вместе ковалентными силами.
- Сегрегация: Меньшие частицы любят отделяться от более крупных частиц, падая через промежутки между более крупными частицами и в конечном итоге оседая на дне контейнера, создавая порошкообразную смесь, которая не является однородной по всему объему.
- Электростатические заряды: Мелкие частицы часто проявляют сильные электростатические и электрофоретические силы, которые заставляют их прилипать к поверхностям, которые используются для их транспортировки, что еще больше усложняет решение проблем агрегации и сегрегации, описанных выше.
- Однородность: Зная, что статистически маловероятно, чтобы образец мелких частиц был абсолютно однородным, как мы можем гарантировать, что все различные частицы точно представлены в нашем образце?
Поскольку ответы на приведенные выше вопросы и предположения не всегда ясны, а задействованные переменные часто не могут полностью контролироваться, существует множество способов определения плотности порошков, в зависимости от того, на какой конкретный вопрос мы пытаемся ответить и какую информацию мы ищут.
Насыпная плотность порошков:
Насыпная плотность определяется просто как измерение массы материала на единицу объема. Однако, когда мы говорим о плотности порошков, насыпная плотность уже не является значимой величиной, потому что даже если масса материала постоянна, объем , который занимает порошок, может широко варьироваться в зависимости от того, как порошок упаковано. Более того, насыпная плотность порошков может меняться со временем, так как порошок оседает в контейнере и занимаемый им объем становится меньше, а вес остается прежним.
Форма частиц также влияет на объемную плотность, поскольку форма влияет на способность отдельных частиц вкладываться в другие частицы… Некоторые материалы гигроскопичны и вытягивают воду из атмосферы, что может резко изменить объемную плотность материала. Поверхностное трение или статический заряд материала также могут влиять, хотя и незначительно, на его объемную плотность.
Объемную плотность можно рассматривать как среднюю плотность определенного объема порошка в определенной среде при определенных условиях.
Как измеряется объемная плотность порошков:
Насыпная плотность при вибрации (или постукивании) относится к объемной плотности порошка, когда контейнер, наполненный порошком, подвергается непрерывной вибрации или постукиванию. Когда они вибрируют, отдельные частицы сближаются и достигают максимальной эффективности упаковки, что делает порошковый материал более плотным, что приводит к самой высокой объемной плотности для этого конкретного порошка и создает воспроизводимые измерения.Объемная плотность при вибрации или постукивании является хорошим приближением плотности порошка после того, как он находился и сжимался в контейнере в течение значительного периода времени.
Насыпная плотность означает насыпную плотность порошка, измеренную при насыпании порошкообразного материала в контейнер. Процесс заливки помогает разрушить или уменьшить проблемы агрегации, сегрегации и электростатических зарядов, а также помогает сделать порошок более однородным. Поскольку процесс заливки создает очень рыхлую структуру частиц, он дает измерение более низкой объемной плотности.Насыпная плотность является хорошим приближением плотности порошка, поскольку он проходит через производственный процесс и транспортируется или перемещается между контейнерами или процессами.
Насыпная плотность аэрации – это насыпная плотность порошка, измеренная при аэрации порошка. Измерение объемной плотности аэрированного газа может быть важно знать по разным причинам, в том числе для правильного определения размеров или анализа систем пневмотранспорта.
Крайне важно знать, как измерялась объемная плотность порошка, чтобы грамотно и осознанно использовать информацию.
Истинная плотность частиц порошков:
Истинная плотность частиц (также известная как скелетная плотность ) представляет собой присущее материалу физическое свойство и, в отличие от насыпной плотности порошков, , а не зависит от размера частиц, формы или степени уплотнения и упаковки порошка. . Истинная плотность частиц не изменится со временем.
Предполагая, что материал имеет высокую степень однородности, можно надежно определить химический состав материала, если известна его истинная плотность частиц.Например, если мы смотрим на стеклянные микросферы, но не знаем, что это за стекло, мы можем сделать точную оценку состава, измерив истинную плотность частиц. Плотность стекла SodaLime составляет 2,5 г/куб.см, боросиликатного стекла – 2,2 г/куб.см, стекла из титаната бария – более 4 г/куб.см. Если мы знаем, что плотность поли(метилметакрилата) или ПММА составляет приблизительно 1,2 г/см3, но размеры наших акриловых частиц немного выше или ниже, это хороший признак того, что мы, вероятно, имеем дело с сополимером.
Знание истинной плотности частиц позволяет ученым и инженерам точно моделировать и прогнозировать характеристики этих частиц в конкретных приложениях.
Как измеряется истинная плотность частиц порошков:
Традиционные методы измерения объема по принципу вытеснения жидкости Архимеда представляют собой проблему при измерении истинной плотности частиц порошков. Причина этой трудности заключается в том, что нам необходимо точное измерение истинного объема, занимаемого самими частицами, исключая любые возможные внутренние пустоты, трещины или поры на поверхности частиц. Жидкости могут проникать в эти неровности в непрерывности частицы и вызывать серьезные ошибки при измерении кажущегося объема, когда плотность оценивается по вытеснению жидкости.
Для точного и точного измерения истинной плотности частиц важно, чтобы все воздушные карманы, пустоты и/или поры в упаковке порошка или на поверхности самого материала учитывались и вычитались при измерении объема частиц ( истинный объем) .
Все сферы от Cospheric LLC имеют измерения плотности, отслеживаемые NIST
Пикнометры — это приборы, предназначенные для измерения истинного объема твердых материалов с использованием закона Архимеда о вытеснении жидкости (газа) и метода расширения газа. Предпочтительным газом для измерения истинной плотности частиц порошков является газообразный гелий. Из-за своего небольшого размера газообразный гелий проникает через поверхность примерно на один ангстрем, что позволяет с большой точностью измерять объемы порошка.Измерение плотности с помощью вытеснения гелия часто позволяет выявить наличие примесей и закупоренных пор, которые невозможно определить никаким другим методом.
Все микросферы Cospheric характеризуются истинной плотностью частиц благодаря использованию нашей запатентованной методики измерения плотности , которая основана на газовой пикнометрии, откалиброванной NIST, и высокоточной шкале, откалиброванной NIST. Чтобы наилучшим образом удовлетворить исследовательские потребности наших клиентов, каждый продукт Cospheric, предлагаемый для продажи, указан на веб-сайте Cospheric с истинной плотностью частиц как часть описания продукта.
Что такое плотность микросфер?
Микросферы обычно определяются как сферические частицы диаметром от 1 микрона до 1000 микрон (мм). Некоторые микросферы являются естественным побочным продуктом химического процесса. Например, в процессе сжигания угля на тепловых электростанциях образуется летучая зола, содержащая керамические микросферы, состоящие в основном из оксида алюминия и кремнезема. Тем не менее, большинство микросфер на мировом рынке производятся на коммерческой основе как прецизионные инженерные материалы с особыми свойствами и функциональностью.Плотность микросфер является одним из критических свойств микросфер, которые контролируются в процессе производства.
Поскольку микросферы чаще всего используются как компонент системы и смешиваются с другими материалами, истинная плотность частиц (в отличие от объемной плотности) имеет решающее значение для обеспечения того, чтобы микросферы могли диспергироваться и суспендироваться в содержащей среде. , плавать на дне или всплывать на поверхность.
Статьи на этом сайте написаны специалистами по микросферам из Cospheric LLC – ведущего мирового поставщика и производителя прецизионных сферических частиц.
При представлении информации мы обращаемся к широкому кругу источников, уделяя большое внимание рецензируемым техническим статьям, которые публикуются в авторитетных журналах. Наша цель — предоставить вам всестороннее и информированное представление о рынке микросфер, технологиях и приложениях.
Как всегда, наш персонал службы технической поддержки доступен по электронной почте , чтобы ответить на любые вопросы, предложить рекомендации по продуктам, предоставить котировки или ответить на запросы по индивидуальному производству.В наличии более 2000 наименований микросфер. Если вы не нашли то, что искали на сайте Cospheric, сообщите нам об этом! Скорее всего, мы сможем порекомендовать альтернативный продукт, отвечающий вашим потребностям.
Источники:
Инструменты Квантахром
Одно из наиболее распространенных измерений плотности включает определение геометрического пространства, занимаемого внутри оболочки твердого материала… включая любые внутренние пустоты, трещины или поры.Это называется геометрической, объемной или объемной плотностью и соответствует истинной плотности только в том случае, если в измеряемом материале нет внутренних отверстий.
Плотность
Каждая частица твердого материала имеет одинаковую истинную плотность после измельчения, помола или обработки, но материал занимает больше геометрического пространства. Другими словами, геометрическая плотность меньше… примерно на 50% меньше истинной плотности, если частицы имеют сферическую форму.
Перемещение или вибрация порошкообразного материала заставляет более мелкие частицы проникать в промежутки между более крупными частицами. Геометрическое пространство, занимаемое порошком, уменьшается, а его плотность увеличивается. В конечном счете никакая дальнейшая естественная упаковка частиц не может быть измерена без добавления давления. Достигается максимальная упаковка частиц.
При контролируемых условиях скорости выпуска, усилия выпуска (падения) и диаметра цилиндра условия максимальной эффективности набивки хорошо воспроизводимы.Это измерение плотности утряски формализовано в методе Британской фармакопеи для кажущегося объема, ISO 787/11 и стандартных методах испытаний ASTM B527, D1464 и D4781 для плотности утряски.
Автоматическое определение плотности утряски выполняется либо с помощью Quantachrome Autotap, либо с помощью двух образцов Dual Autotap.
Истинная плотность
Истинная плотность порошков часто отличается от плотности сыпучего материала, поскольку процесс измельчения или измельчения изменяет кристаллическую структуру вблизи поверхности каждой частицы и, следовательно, плотность каждой частицы в порошке.Кроме того, пустоты на поверхности частицы, в которые не проникают жидкости, могут создавать кажущийся объем, что приведет к серьезным ошибкам при измерении плотности по вытеснению жидкости.
Пикнометры от Quantachrome специально разработаны для измерения истинного объема твердых материалов с использованием закона Архимеда о перемещении жидкости (газа) и техники расширения газа. Истинная плотность измеряется с использованием газообразного гелия, поскольку он проникает в каждый поверхностный дефект примерно до одного ангстрема, что позволяет с большой точностью измерять объемы порошка. Измерение плотности с помощью вытеснения гелия часто позволяет выявить наличие примесей и закупоренных пор, которые невозможно определить никаким другим методом.
Как рассчитать плотность твердых тел и жидкостей — видео и стенограмма урока
Расчет плотности твердых тел или жидкостей
Когда вас попросят рассчитать плотность, вам нужно использовать комбинацию уравнения плотности, которое мы уже представили, и понимание объема.Например, вам может не быть дан фактический объем материала или объекта, который нужно ввести в уравнение плотности. Вместо этого вам могут дать размеры объекта, и ожидается, что вы сами определите объем.
Объем куба равен длине, умноженной на ширину, умноженной на высоту ( Д * Ш * В ). Поэтому, если бы вам нужно было вычислить плотность куба, вы бы сначала измерили длину одной из сторон. Допустим, длина нашего куба получилась 3 метра.Сначала вам нужно рассчитать объем, умножив 3 на 3 на 3 ( V = 3 * 3 * 3). Вам также нужно будет поставить куб на весы, чтобы измерить его массу. Наконец, вы должны разделить свой объем на массу, чтобы получить плотность куба ( p = m/v ).
Но что, если материал не твердый? А если это жидкость?
Измерение объема жидкости не так очевидно, потому что жидкости меняют форму. Когда вы отмеряете жидкости в мерном кувшине, цифры сбоку — это такие вещи, как жидкие унции, пинты и литры (или миллилитры).Литры используются в научном оборудовании, потому что это стандартные научные единицы. И есть очень веская причина, по которой мы используем литры. Объем измеряется в кубических метрах, а 1 кубический метр равен 1000 литрам. Таким образом, преобразование очень просто. (Также обратите внимание, что 1 литр равен 1000 миллилитров).
Подводя итог, вот шаги для расчета плотности твердого тела или жидкости:
1. Вычислите объем, либо измерив размеры твердого тела, либо используя мерный кувшин для жидкости.Преобразуйте любые единицы по мере необходимости, чтобы получить число в метрах в кубе.
2. Положите предмет или материал на весы и определите его массу.
3. Разделите массу на объем, чтобы вычислить плотность ( p = m/v ).
Пример проблемы
Хорошо, давайте рассмотрим пример. Твой лучший друг очень любит молоко, и однажды тебе становится любопытно. Вам интересно, какова плотность молока, которое он пьет. Ваш друг позволяет вам одолжить его стакан молока, чтобы понять это.Вы наливаете молоко в мерный кувшин и обнаруживаете, что у него 150 миллилитров молока. Потом ставишь на весы. Масса стакана и молока вместе 0,115 кг, а масса стакана сама по себе 0,1 кг. Какова плотность молока?
Прежде всего, мы должны записать то, что мы знаем.
- Объем молока Vmilk 150 мл.
- Масса стакана и молока mglass&milk 0,115 кг.
- А масса стакана сама по себе равна 0.1 кг.
Мы знаем, что плотность равна массе, деленной на объем ( p = m/v ), поэтому нам нужно вычислить массу молока в килограммах и объем молока в кубических метрах.
Прежде чем мы подставим числа в уравнение, нам нужно сделать некоторые отдельные вычисления.
Прежде всего, какова масса молока? Итак, масса стакана и молока вместе составляет 0,115, а масса стакана сама по себе равна 0,1, поэтому масса молока должна быть (0,115).115 — 0,1), что составляет 0,015 килограмма. Теперь у нас есть масса.
Далее нам нужен объем в кубических метрах. Мы знаем, что объем молока составляет 150 миллилитров, поэтому нам просто нужно преобразовать его в метры в кубе. В литре 1000 миллилитров, поэтому 150 мл равны 0,15 литра (150/1000 = 0,15). Вы просто делите на 1000. А в метре в кубе 1000 литров, поэтому, чтобы получить наше число в метрах в кубе, нужно снова разделить на 1000. Это дает нам 0,00015 метра в кубе (0,15/1000 = 0,00015).И это наш объем.
Итак, теперь у нас есть объем молока в кубических метрах и масса молока в килограммах. Подставьте их в уравнение плотности: 0,015 кг разделить на 0,00015 кубических метров дает нам плотность 100 кг на кубический метр (0,015 / 0,00015 = 100). И это все; это наш ответ.
Краткий обзор урока
Плотность — это мера того, насколько компактна масса вещества или объекта. Плотность предмета или вещества можно рассчитать по такому уравнению: плотность в килограммах на метр в кубе равна массе в килограммах, деленной на объем в метрах в кубе ( p = m/v ).
Вот шаги для расчета плотности твердого тела или жидкости:
1. Определите объем, измерив размеры твердого тела или используя мерный кувшин для жидкости. Преобразуйте любые единицы по мере необходимости, чтобы получить число в метрах в кубе.
2. Положите предмет или материал на весы, чтобы определить его массу.
3. Разделите массу на объем, чтобы вычислить плотность ( p = m/v ).
Вам также может понадобиться знать, как вычислить объем твердого тела.Например, для куба объем равен длине, умноженной на ширину, умноженную на высоту (90 263 V 90 266 = 90 263 L 90 266 * 90 263 W 90 266 * 90 263 H 90 266). И вам нужно знать некоторые преобразования. Например, 1000 литров — это 1 метр в кубе, а 1000 миллилитров — это 1 литр.
Результаты обучения
После этого урока вы должны уметь:
- Определять плотность
- Объясните, как рассчитать плотность твердого тела или жидкости
Плотность: гелиевая пикнометрия | Есть два типа плотности, связанные с порошками: плотность оболочки (или объемная) и скелетная плотность
. Есть два типа плотности, связанных с порошками.Конвертная (или объемная) плотность определяется для пористых материалов, когда в измерение объема включаются поровые пространства внутри материала. Скелетная плотность представляет собой отношение массы твердого материала к сумме объемов твердого материала и закрытых (или слепых) пор внутри материала (ASTM D3766). Micromeritics Accupyc II 1340 измеряет скелетный объем материала путем вытеснения газа с использованием зависимости объем-давление по закону Бойля. В качестве вытесняющей среды используется инертный газ, обычно гелий. Образец помещают в герметичный стакан известного объема. Затем эту чашку помещают в камеру для образцов. Газ вводится в камеру для образца, а затем расширяется во вторую пустую камеру известного объема. Измеряют давление, наблюдаемое после заполнения ячейки для образца, и давление, сбрасываемое в расширительную камеру, а затем рассчитывают объем. Плотность определяют путем деления массы образца на измеренный объем. Плотность, измеренная с помощью гелиевой пикнометрии, часто называют «плотностью гелия», подразумевая, что открытые поры исключаются из расчета.Поскольку Он не может получить доступ к закрытым порам, они включаются в общий объем.
Технические характеристики
- Объем кюветы 10 мл (внутр. диаметр 1,80 см x глубина 3,93 см (внутр. диаметр 0,72 дюйма x глубина 1,55 дюйма) содержит 1- и 3,5-дюймовые чашки для мешков
- Размеры чашечек: объем 1 мл — диаметр 1,2 см x высота 1,1 мм; Объем 3,5 см3 – диаметр 1,7 мм x высота 1,7 мм
- Образец может быть порошком или сыпучим.
Нерасфасованная проба должна помещаться в чашку для проб
. - Для качественного результата образец должен заполнить не менее двух третей чашки
- Точность: воспроизводимость обычно в пределах ±0.01% от номинального полноразмерного объема кюветной камеры. Гарантированная воспроизводимость в пределах ± 0,02 % от номинального объема полной шкалы на чистых, сухих, термически уравновешенных образцах с использованием гелия в диапазоне от 15 до 35 ºC
- Точность: с точностью до 0,03 % от показаний плюс 0,03 % от емкости образца
Применение
- Фармацевтические препараты – полиморфные, гидратированные и аморфные формы продуктов, а также чистоту можно определить путем сравнения измеренной плотности с теоретическими и историческими значениями.
- Покрытия – плотность высушенной пленки можно использовать для определения содержания летучих органических соединений (ЛОС) в прозрачных и пигментированных покрытиях.
- Прокаливание – различные кристаллические структуры углерода и керамики претерпевают структурную перестройку в результате обработки давлением или температурой, что приводит к различной плотности.
- Керамика и порошковая металлургия – если плотность готовой детали значительно меньше плотности входящего в ее состав порошка, при обработке детали образовались закрытые поры
- Жесткие пористые пластики – пенопласты обладают различными свойствами в зависимости от соотношения открытых и закрытых ячеек, определяемого по плотности/
- Пластиковые пленки – плотность можно использовать для определения количества захваченного воздуха и степени кристалличности.
- Навозная жижа – количество жидкости в смеси навозной жижи можно рассчитать путем измерения плотности навозной жижи.
- Органические химикаты и полимеры – процессы полимеризации и органического риформинга используются для получения желаемых соединений из сырья. Конверсию и чистоту можно контролировать, сравнивая измеренную плотность с теоретической плотностью желаемого продукта.
- Смешивание материалов — точность и воспроизводимость смеси можно контролировать путем сравнения измеренных плотностей с ожидаемой плотностью на основе целевого рецепта первичных ингредиентов.
Плотность жидкостей
8 th Профессор естественных наук Шай
Эксперимент по плотности жидкостей
Раздел 3.9 Страница 51
Вы собираются измерить плотность бесцветной жидкости без запаха. У половины класса будет одна жидкость под названием Mystery A, а у другого будет Mystery B. Не пробуйте жидкость, фу!
Кому измерить плотности жидкости вы делаете то же самое, что и для твердого тела.Массируйте жидкость, найдите ее объем и разделите масса по объему.
Кому масса жидкости, взвесьте его в контейнере, вылейте его, взвесьте пустой контейнер и вычесть масса пустой тары от полной тары.
Кому найти объем жидкости, вы просто очень тщательно отмеряете ее градуированной цилиндр.
Вопрос. Следует ли сначала найти объем жидкость или масса жидкости?
Ответ. Два варианта:
.
1. Взвешивание жидкости в
стакан. Вылейте в мерный цилиндр и снова взвесьте.
Масса жидкости есть разница двух взвешиваний. То
объем — это измерение, которое вы видите в градуированном цилиндре. Примечание
что этот метод не включает остатки жидкости, которые прилипают к
стакан в массировании. Остатки также не включены в
измерение объема.
2. Налейте жидкость в
градуированный цилиндр и прочтите его объем. Затем взвесьте полученное
цилиндр.Затем вылейте жидкость и снова взвесьте. То
вес жидкости есть разница между двумя взвешиваниями.
Обратите внимание, что этот метод после заливки жидкости из градуированного
цилиндр, включает остатки жидкости в показания объема, но не
в расчете массы.
И правильный способ сделать это (1). Когда вы найдете массу или
измерьте объем жидкости, вы не будете включать жидкость, которая
цепляется за пустой контейнер, из которого вы его налили.Таким образом, вы должны сначала массировать, как в первом варианте выше. В варианте 1 после того, как вы массируете, а затем заливаете до нужного размера
объем, остатки жидкости, оставшиеся в стакане, не попадают в
вычисление массы или объема. Включение в
ни то, ни другое не справедливо. Однако если сначала найти объем, а затем
масса, остатки жидкости в градуированном цилиндре объемом будут включаться в измерение объема, но не в измерение массы.
Отчет плотность вашей жидкости на доске.
Ар два жидкости одинаковые?
Когда
ты смешиваешь соль
с водой общий объем уменьшается, но масса остается прежней. Что должно произойти с плотностью?
8 th Профессор естественных наук Шай
Плотность Рабочий лист по жидкостям
Жидкость 1 Анализ плотности
Масса фактической жидкости (A B) С._________
Объем фактической жидкости Д.
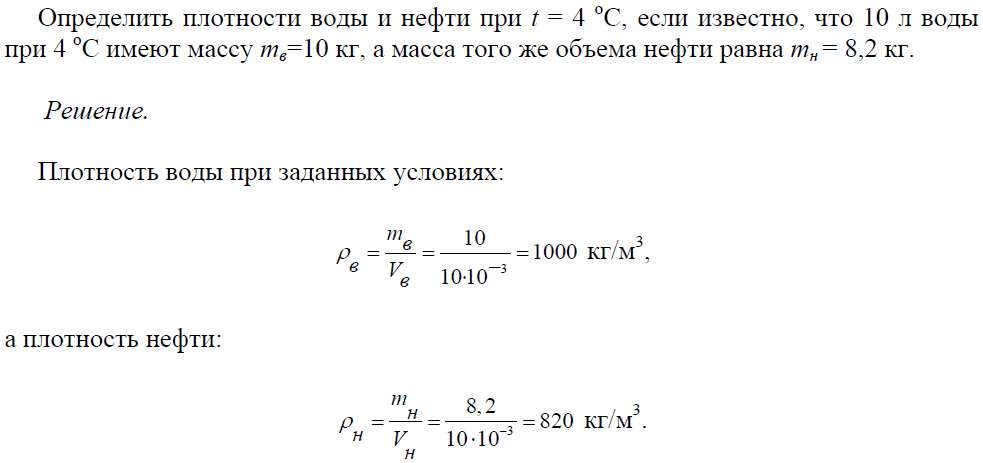
Плотность Фактическая жидкость (C / D) Е. _________
Жидкость 2 Анализ плотности
Масса фактической жидкости (A B) С. _________
Объем фактической жидкости Д._________
Плотность Фактическая жидкость (C / D) Е. _________
Сообщите о своем групповой результат на гистограмме доска.
Сделать задачу 15 в вашем тексте.
Расчет плотности
К концу этого урока вы сможете:
- вычислить одну переменную (плотность, массу или объем) из уравнения плотности
- рассчитать удельный вес объекта, а
- определяют, будет ли объект плавать или тонет, учитывая его плотность и плотность его окружения.
Введение в плотность
Плотность – это масса объекта, деленная на его объем.Плотность часто выражается в граммах на кубический сантиметр (г/см 3 ). Помните, что граммы — это масса, а кубические сантиметры — это объем (тот же объем, что и 1 миллилитр).
Коробка с большим количеством частиц будет более плотной, чем такая же коробка с меньшим количеством частиц.Плотность — фундаментальное понятие в науке; вы будете видеть это на протяжении всего обучения.Его довольно часто применяют при идентификации горных пород и минералов, так как плотность веществ редко изменяется существенно. Например, золото всегда будет иметь плотность 19,3 г/см 3 ; если минерал имеет другую плотность, это не золото.
Вероятно, у вас есть интуитивное ощущение плотности материалов, которые вы часто используете. Например, губки имеют низкую плотность; они имеют низкую массу на единицу объема. Вы не удивитесь, когда большую губку легко поднять. Напротив, железо плотное.Если вы берете в руки железную сковороду, вы ожидаете, что она будет тяжелой.
Студенты и даже преподаватели часто путают массу и плотность. Слова тяжелый и легкий сами по себе относятся к массе, а не к плотности. Очень большая губка может много весить (иметь большую массу), но ее плотность мала, потому что она все равно очень мало весит на единицу объема . Для плотности вам также необходимо учитывать размер или объем объекта.
Как определить плотность?
Бетонный куб будет весить больше, чем куб воздуха того же размера, потому что он более плотный. Плотность не является чем-то, что измеряется напрямую.Обычно, если вы хотите узнать плотность чего-либо, вы должны взвесить это, а затем измерить объем. Вы собираете валун и возвращаете его в лабораторию, где вы взвешиваете его и находите, что его масса составляет 1000 г. Затем вы определяете объем 400 см 3 . Какова плотность вашего валуна? Плотность — это масса, деленная на объем,Еще одна хитрость, связанная с плотностью, заключается в том, что вы не можете добавлять плотности. Если у меня есть камень, состоящий из двух минералов, один с плотностью 2,8 г/см 3 , а другой с плотностью 3,5 г/см 3 , камень будет иметь плотность между 3,5 и 2,8 г/см 3 , а не плотностью 6,3 г/см 3 . Это связано с тем, что и будут добавлены к массе и объему двух минералов, и поэтому, когда они разделены, чтобы получить плотность, результат будет между ними.
Типичные плотности газов составляют тысячные доли грамма на кубический сантиметр. Жидкости часто имеют плотность около 1,0 г/см 3 , и действительно, пресная вода имеет плотность 1,0 г/см 3 . Камни часто имеют плотность около 3 г/см 3 , а металлы часто имеют плотность выше 6 или 7 г/см 3 .
Как рассчитать удельный вес?
Чтобы рассчитать удельный вес (SG) объекта, вы сравниваете плотность объекта с плотностью воды:
Поскольку плотность воды в г/см 3 равна 1.0, SG объекта будет почти такой же, как его плотность в г/см 3 . Однако удельный вес является безразмерным числом и одинаков в метрической системе или любой другой системе измерения. Это очень полезно при сравнении плотности двух объектов. Поскольку удельный вес не имеет единиц измерения, не имеет значения, измерялась ли плотность в г/см 3 или в каких-то других единицах (например, в фунтах/футах 3 ).
У вас есть образец базальта плотностью 210 фунтов/фут 3 .Плотность воды составляет 62,4 фунта/фут 3 . Каков удельный вес базальта? Удельный вес — это плотность вещества, деленная на плотность воды, поэтомуИтак, мы делим базальт (210 фунтов/фут 3 ) на плотность воды (62,4 фунта/фут 3 ) и получаем S.G.= 3,37 .
Зачем мне рассчитывать плотность или удельный вес?
Плотность имеет решающее значение для многих применений. Одним из наиболее важных является то, что плотность вещества определяет, будет ли оно плавать на другом.Менее плотные вещества будут плавать на более плотных (или подниматься сквозь них). Вот несколько примеров того, как это объясняет повседневные явления:
- Задумывались ли вы, почему воздушные шары взлетают вверх? Когда воздух нагревается, он становится менее плотным, пока общая плотность воздушного шара не станет меньше плотности атмосферы; Воздушный шар буквально парит в более плотном и холодном воздухе.
- Вы когда-нибудь замечали, что в озере или океане вода теплее на поверхности и холоднее на дне? Это связано с тем, что более теплая вода немного менее плотная и в результате плавает на более плотной и холодной воде .
- Вы знаете, почему извергаются вулканы? Эта огромная лодка много весит, но ее плотность должна быть меньше 1.0 г/см 3 , потому что плавает. Основная причина того, что магма поднимается на поверхность для извержения вулканов, заключается в том, что она менее плотная, чем окружающие ее породы.
Корабль, плывущий по воде, — отличная иллюстрация разницы между массой и плотностью. Корабль должен иметь плотность менее 1,0 г/см 3 (плотность воды), иначе он утонет. Корабли имеют большую массу, потому что сделаны из стали, но поскольку они имеют большой объем, их плотность меньше 1.0 г/см 3 . Если к ним добавить достаточно массы, чтобы их плотность превысила 1,0 г/см 3 , они утонут.
Чтобы попробовать несколько практических задач, перейдите на страницу с примерами задач!
Где плотность используется в науках о Земле?
Галенит, свинцовая руда, является одним из самых плотных распространенных минералов.с http://mineral.galleries.com/.
- Изостазия — определение высоты расположения континентов на мантии
- Тектоника плит — механизмы, приводящие в движение тектонику плит
- Минералы — определение названия минерала по его плотности
- Горные породы — определение названия и состава горной породы по ее плотности
- Гипсометрическая кривая — изучение причин изменения высоты на Земле
- Океанография — некоторые океанские течения и циркуляция океана контролируются плотностью
Следующие шаги
Я ГОТОВ К ПРАКТИКЕ! Если вы считаете, что разобрались со всеми перечисленными выше вещами, нажмите на эту полосу, чтобы попробовать решить некоторые практические задачи с готовыми ответами!
Или, если вы хотите еще больше практики, см. ссылки ниже
Дополнительная помощь по плотности
Онлайн-лаборатория Edinformatics по массе, объему и плотности создана Нью-Йоркским университетом.Он позволяет просматривать изображения измерений и вводить данные.Гиперфизика, в штате Джорджия есть страница о плотности и преобразователе плотности . Это включает в себя несколько связанных страниц, включая инструкции по измерению плотности с использованием принципа Архимеда.
На странице Википедии, посвященной удельной массе, объясняется, что такое удельная плотность и как она используется, и даже обсуждается ее использование в геонауках и минералогии. Однако содержание статей в Википедии может меняться, поэтому вам стоит быть осторожными.
На странице плотности Википедии есть общее обсуждение плотности и ее истории, расчетов и единиц измерения. Однако содержание статей в Википедии может меняться, поэтому вам стоит быть осторожными.