Цемент с опилками: пропорции
В современном строительстве для теплоизоляции перекрытий и других конструкций нередко используют опилочный цемент. От большинства других защищающих от температурного воздействия материалов он отличается наличием в составе органического заполнителя (в основном, древесных опилок). В такой цемент добавляют большое количество вяжущих веществ, обеспечивающих его высокую прочность и долговечность. Всё это делает стоимость материала довольно высокой, однако увеличивает и его теплоизоляционные свойства, вдвое превышающие аналогичные показатели фибролита и примерно в 15 раз – обычного кирпича.
Рецепты опилочного бетона
Блоки из опилочного цемента изготавливаются заранее, так как до производства работ по их монтажу материал должен приобрести достаточную влажность и прочность. Рецептов же приготовления блоков существует много:
- самые лёгкие блоки получаются с использованием цемента и опилок в массовой пропорции 1:1.
- более тяжёлый, зато и имеющий повышенную прочность материал получают, используя следующий состав (пропорции уже объёмные): 1 часть цемента М300, 2 части среднеразмерного песка и 6 частей опилок (или смеси). Получившийся опилочный цемент имеет марку 10–15. А сделанные из него блоки приобретают достаточную для строительных работ прочность через 90 дней.
Материал наполнителей
Органическими наполнителями, которые добавляют в различные марки опилочных цементов, могут быть:
- свежие измельчённые отходы от лесозаготовительных работ, а также из лесопильных и других деревообрабатывающих установок. Лучше всего подходят для цемента опилки хвойных деревьев;
- растительная резка, представляющая собой результат дробления стеблей риса, конопли и льна;
- старые опилки, которые перед добавлением в материал следует предварительно обработать.
Антисептиком в этом случае выступает кремнефтористый натрий и 25%-ный аммиак, которых на 100 л цементного раствора добавляют соответственно 0,4 кг и 0,65 литра.
Особенности приготовления
Приготовление материала похоже на получение обычного бетона. В первую очередь берётся вяжущий материал (с целью экономии лучше всего приобретать цемент оптом) и перемешивается с песком. Далее в смесь добавляют опилки, а потом воду – причём, малыми порциями, например, из лейки с небольшими отверстиями. Недостаточное количество воды может привести к тому, что опилочный цемент не достигнет требуемой прочности, а избыточное – к медленному затвердеванию. Правильно же приготовленный раствор не разваливается при сжатии в ладони и не смачивает кожу, а лишь увлажняет.
Поверхность цементных блоков после их изготовления затирают цементом, увеличивая их прочность. А уже после установки на место материал штукатурят или даже облицуют в половину или четверть кирпича.
Стяжка с опилок: что такое, как сделать, преимущества, недостатки
Вступление
В наше время все люди стремятся соотнести качество, с относительно не высокими затратами. В первую очередь, это касается строительства. Сегодня рассмотрим один из самых интересных, экологически чистых, экономичных и надежных вариантов бетонирования пола.
Стяжка с опилок что это такое?
Сейчас мы будем делать стяжку, при помощи обыкновенных, древесных опилок. Если вы используете опилки, тогда стяжка будет 2-х слойная.
Для первого слоя стяжки (70 мм) нужно приготовить такие материалы: цемент, опилки (через 2 месяца после пиления) и песок (сухой и чистый). Пропорции приготовления смеси такой стяжки — на ведро цемента приходится два ведра песка и шесть опилок. При этом использовать нужно цемент марки «пятьсот» или «четыреста». В некоторых рецептах можно встретить добавку к смеси в виде 3-х килограмм гашеной извести.
Примечание: Гашеная известь (пушонка, известь гидратная) порошок белого цвета, используемый в строительстве и ремонте для увеличения пластичности и водостойкости материалов.
Для второго слоя стяжки из опилок, делаем раствор с такими пропорциями смеси: на ведро цемента используем идентичное количество песка (как в первом случае) и три ведра опилок.
Какие опилки использовать в стяжке
Стяжка с опилок делается из опилок древесины, получающихся при её пилении. Желательно, чтобы опилки выдержались два месяца или были высушены. Прежде чем засыпать опилки в бетономешалку, их нужно очистить от кусочков древесины и фрагментов коры. То есть, опилки должны быть чистыми. В некоторых «рецепта» вместо опилок предлагают использовать стружку любой фракции. Сомневаюсь, что это будет правильным решением.
Преимущества
Скажем прямо, стяжка с опилок не является традиционной и для понимания целесообразности её применения нужно понять её преимущества.
- Энергосбережение. Та как, опилки являются отличным натуральным утеплителем, то стяжка с опилками в смеси будет более «теплой», то есть лучше будет удерживать тепло и не пропускать холод в помещение.
- Невысокая стоимость. Опилки можно взять совершенно бесплатно на любой лесопилке. Возможно, вам за это спасибо скажут! Это не кардинально, но всё таки, снижает стоимость стяжки.
- Долговечность. Опилки в стяжке не снижают её долговечность. Специалисты дают гарантию, что стяжка с опилок прослужит минимум 10 лет эксплуатации.
- Многие называют плюсом стяжки из опилок её экологичность. Не вижу особых причин это делать, так как не понимаю, почему опилки делают её наиболее экологически безопасным вариантом.
- Простота использования. Особых сложностей в добавлении опилок в смесь нет, поэтому простоту применения стяжки из опилок включим в её преимущества.
- Не нужно делать слой утепления пола. Утеплителем выступит первый слой стяжки.
Недостатки
Было бы несправедливым умолчать о недостатках стяжки с опилками.
- Стяжка с добавлением опилок, как компонента, сохнет классические 28-30 дней. Два слоя стяжки будут сохнуть 60 дней, а это редко вписывается в сроки строительства.
- Замечено повреждение стяжки из опилкобетона грызунами. Для защиты рекомендуют добавлять борную кислоту или медный купорос.
Вывод
Рассмотренная стяжка с опилок еще один пример технологического разнообразия в устройстве полов, а также вариант безотходного строительства. Такая стяжка проверенная временем и её можно использовать как экономный вариант строительной технологии.
©Opolax.ru
Еще статьи
Похожие статьи
Пропорции при засыпке опилок цемента и извести. Как выполняется утепление стен опилками
Опилки — это стружка, образующаяся при переработке древесины. Их используют для утепления стен, полов, крыш жилых или хозяйственных зданий, поскольку они хорошо сохраняют тепло. Основные преимущества опилок — низкая стоимость и отличная термоизоляция. Из них в промышленности выпускают арболитные плиты, опилочные гранулы, древесные блоки и опилкобетон. Не каждый знает, как применять
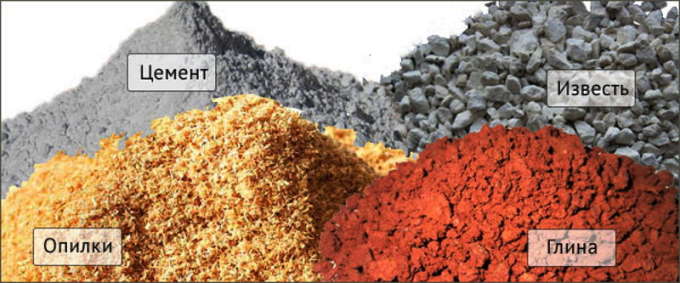
Для использования в виде утеплителя, опилки смешивают с дополнительными компонентами. К примеру: известь, цемент, гипс. Их необходимо
После приготовления утеплительной массы, опилки засыпают в предварительно подготовленные места, послойно трамбуют и ждут окончательной усадки около 2-х недель , на протяжении которых необходимо помещение проветривать.
Достоинства и недостатки утеплителя из опилок
Сегодня используют опилки для утепления очень редко, ведь на современном рынке стройматериалов предоставлен большой выбор разных новационных утеплителей. Теплоизоляция из опилок имеет такие минусы, как трудоемкость при укладке и неустойчивость к влаге. Если опилки использовать в чистом виде, они легко загораются.
Все-же, невзирая на вышеописанные недостатки, метод имеет право на существование. Его основной плюс в надежности и дешевизне. Этот утеплитель имеет очень хорошую теплоизоляцию. Обработанные опилки — натуральный и безопасный материал. По всем качествам они не уступают утеплителям, которые производятся промышленностью.
Как утеплить потолок
Теплоизоляция чердака с использованием опилок
С опилками используют в жилых и хозяйственных постройках. Этот материал недорогой, доступный и натуральный.
Поверхность, куда будет укладываться теплоизоляционный слой, следует подготовить, замазав все щели глиной или задув монтажной пеной. Если на чердаке расположен дымоход, для пожарной безопасности площадь вокруг него
Потом подготавливаются опилки. Важный момент — размер, ведь чем больше их фракция, тем меньше плотность теплоизоляционного слоя. Утепляя чердак, лучше всего применять мелкие опилки, получаемые при распиле древесины.
Для приготовления теплоизоляционного раствора потребуется: 85% опилок, 10% извести-пушенки, 5% гипса. Изначально опилки обрабатывают антисептическим раствором (например, борной кислотой) и просушивают. Затем в предварительно подготовленной емкости тщательно смешивают все компоненты. После этого смесь разводят водой, до получения нерассыпчатой, слегка влажной консистенции.
Полученный раствор засыпается по площади чердака плотным слоем, толщина его около 25 см. Его хорошо утрамбовывают, чтобы после высыхания он не был слишком пористым и не давал усадки. Процесс необходимо выполнять как можно быстрее, поскольку гипс быстро высыхает и можно не успеть вовремя его утрамбовать.
После застывания раствора из опилок, сверху настилают дощатый чердачный пол.
Характеристики утеплителя из опилок
Теплоизоляционные характеристики опилок не уступают по качеству более современным материалам, например минеральной вате. Для сравнения можно рассмотреть нижеприведенную таблицу.
Утеплитель из опилок — очень хороший теплоизоляционный материал. Он отличается дешевизной, простотой исполнения, натуральностью и долговечностью, поэтому можно смело применять его в постройках разного типа и предназначения.
Видео утепления опилками
Опилки — это отходы деревообработки в виде мелкой стружки и древесной пыли. Этот хорошо известный материал очень давно используется в качестве утеплителя, поскольку прекрасно удерживает тепло, выделяет древесные смолы и является отличным наполнителем-разрыхлителем.
Область применения
Начало истории использования опилок в малоэтажном строительстве уходит корнями в те далекие времена, когда их начали добавлять в глину и сооружать из этой смеси перекрытия в деревенских домах.
Такие перекрытия можно назвать идеальными: они служили очень долго, ничем не повреждались, не имели никаких недостатков и обладали очень значимыми преимуществами — низкой стоимостью и высокой теплоизоляцией.
Взяв за основу эту древнюю технологию, современная промышленность начала изготавливать такие же качественные строительные материалы — гранулы, арболит, бетон с опилками, деревянные блоки.
Также опилки продолжают и сейчас использовать в малоэтажном строительстве. Особенно заинтересованы в этом материале частные застройщики, которые утепляют опилками стены, пол, потолок, а также используют их с другими целями по мере необходимости.
Сегодня невозможно найти более дешевый термоизоляционный материал, чем древесные опилки. Для утепления крыш, потолков, межэтажных перекрытий, полов и стеновых конструкций применяются очень разные строительные материалы. Но именно смесь цемента, гипса или извести со стружкой и опилками является сверх экономной при утеплении любой строительной конструкции.
Зачем нужна обработка опилок
Для создания теплоизоляции используют опилки, предварительно подготовленные специальным способом. Без антисептической обработки и добавления примесей у опилок появляется два существенных недостатка:
- Они становятся очень огнеопасными
- В них заводятся грызуны и другие вредители
Поэтому перед началом работы опилки смешиваются с известью, цементом или гипсом, а затем увлажняется раствором антисептика. Полученная смесь становится пожаробезопасной и непривлекательной для вредителей.
Опилки с известью, как утеплитель стен и перегородок
Для утепления стен и перегородок используют смесь извести с чистыми сухими опилками в соотношении 1:10. Если вместо извести используется гипс, то необходимо соблюдать соотношение 1:8.
В готовую смесь вводят небольшое количество раствора антисептика (25г на ведро), засыпают ее в стены и утрамбовывают. При такой обработке опилки не проседают и не повреждаются вредителями.
Из древесных опилок можно изготовить блоки, добавив к ним цемент и медный купорос в качестве антисептика. Сначала опилки увлажняются раствором медного купороса, а затем к ним добавляется цемент в том же соотношении, что и известь (1:10). Такое количество цемента обеспечит равномерное покрытие стружки.
Воды следует добавлять столько, сколько потребуется раствору, чтобы не распадаться в руке при сжимании. При этом вода не должна выжиматься.
Готовую смесь выкладывают в перекрытия или стены, и после каждого слоя засыпки тщательно трамбуют. От того, насколько качественно утрамбована смесь, зависит усадка утеплителя.
Цемент при взаимодействии с влажными опилками сразу начинает схватываться и образует блок. После полного высыхания образуется прочный твердый пласт, который практически не проседает, а только хрустит под ногами. Таким образом, в конце этой технологической цепочки на выходе получается материал с высокими звуко- и теплоизоляционными характеристиками.
Утепляем потолок опилками
Вопрос теплоизоляции потолка очень важен, поскольку через него теряется около 20 % тепла в помещении.
Процесс утепления потолка опилками состоит из следующих этапов:
- Черновой потолок застилается пергамином
- Доски обрабатываются огнебиозащитой
- В водно-цементный раствор добавляются опилки в соотношении 1:10. Смесь должна быть влажной. Для этого на 10 ведер опилок надо взять 1,5 ведра воды
- Готовую смесь засыпают слоем в 2 см по поверхности перекрытия и утрамбовывают.
Лучше выполнять такую работу летом, чтобы все быстро высохло. Высохшая смесь не проминается, а слегка хрустит под ногой
Если при утеплении опилками учитывать все специфические нюансы и выполнять работу в соответствии с технологическими требованиями и правилами, то в результате получится сухое и теплое помещение, которое останется таковым на многие годы.
Видео про утепление потолка опилками
Опилки, как утеплитель, используются для защиты разных поверхностей: пола, крыши, перекрытий, стен. В любом из случаев теплоизоляция укладывается слоем некоторой толщины, данный параметр зависит от климата местности и типа материала несущей конструкции. С целью снижения теплопотерь применяют опилки разных видов. Прежде всего, они отличаются по размеру фракций, по свойствам. Если нужно выбрать утеплитель для изготовления рабочей смеси, рассматривают каждый из вариантов с учетом плюсов и минусов.
Материал является побочным продуктом деревообрабатывающей промышленности. Опилки в качестве утеплителя могут применяться в двух вариантах:
- труха;
- стружка.
Более мелкие фракции получают путем пиления. Результатом данного процесса является труха или древесная пыль. Этот материал отличается высокой плотностью наполнения, легче трамбуется. Параметры трухи напрямую зависят от особенностей рабочего инструмента (пилы). Стружка же отличается по размеру фракций — в данном случае они крупнее (от 5 мм до 5 см). Такой материал получают путем переработки дерева несколькими способами: сверлением, строганием.
Утепление опилками осуществляется посредством стружки из разных пород древесины:
Стоимость материала невысокая, что обусловлено способом его получения. Несмотря на это, опилки до сих пор часто используются в разных целях. Высокая популярность стружки объясняется большим количеством положительных качеств, среди которых отличные показатели тепло- и звукоизоляции.
Однако нельзя забывать, что этот материал гигроскопичен. По данной причине, когда выбирается утеплитель из опилок, учитывают породу древесины.
Например, фракции из дуба лучше прочих противостоят воздействию влаги . Значит, при контакте с жидкостью материал не потеряет свойств.
Ель, сосна и ясень сильнее подвержены воздействию влаги . Когда подбирается стружка для утепления объекта, рассматривают разные технологии теплоизоляции:
- применение отходов столярного производства в чистом виде — самый подходящий метод, т. к. при этом используют хорошо просушенную стружку, но в процессе образуется много пыли, что способствует ухудшению свойств материала;
- древесные блоки — изготавливаются из опилок, медного купороса и цемента, данный вариант подходит для утепления объекта в процессе строительства, его не применяют с целью теплоизоляции домов, которые уже введены в эксплуатацию;
- гранулы на основе опилок — содержат карбоксицеллюлозный клей, антисептические составы и антипирены, такой материал является улучшенной версией стружки, т.
к. характеризуется отличными показателями огнестойкости;
- опилкобетон — содержит цемент, песок, воду и древесную стружку;
- арболит — данный материал состоит из опилок, органических наполнителей и цемента.
Существуют и другие виды смесей на основе продуктов деревообрабатывающей промышленности: с глиной или цементом, с добавлением известкового молока. Утепление дома опилками выполняется и с помощью сухих смесей. В данном случае не применяют жидкости.
Преимущества и недостатки
Если выбирается утеплитель, мало одной информации о теплоизоляции — плюсы и мнусы должны быть тоже учтены, т. к. от того, соответствует ли стружка условиям эксплуатации, зависит срок службы материала. Положительные качества:
- экологичность;
- низкая теплопроводность;
- звукоизоляция;
- приемлемая цена;
- простая технология укладки;
- если материал обработать антипиренами и антисептиками, продлевается срок службы опилок.
К недостаткам относят подверженность возгоранию, гигроскопичность, трудоемкость монтажа
. Сам по себе способ укладки утеплителя несложен и не требует особых навыков, опыта. Однако эта работа занимает много времени. Кроме того, древесная стружка подвержена гниению, в ней могут обустраивать гнезда грызуны
. Еще в опилках заводятся насекомые
. Дополнительно к тому со временем этот материал усыхает
, а значит, теряет часть свойств. Чтобы устранить недостатки, смешивают опилки с глиной, цементом, известью или медным купоросом . При этом улучшаются свойства материала.
Опилки и известь как утеплитель
Такой метод больше подходит для теплоизоляции стен, перегородок. Подготавливают хорошо просушенную стружку. Для приготовления смеси понадобится известь. Чтобы сделать утеплитель из опилок своими руками, за основу берут соотношение данных компонентов — 10:1. Допустимо вместо извести применять гипс.
Чтобы защитить утеплитель для стен от нашествия насекомых, в смесь опилок с известью добавляют антисептик в количестве 25 г/ведро. Такая мера позволяет избежать проседания и повреждения древесной стружки вредителями. Готовую смесь укладывают в пространство между стенками. Рекомендуется трамбовать материал, прилагая при этом умеренные усилия. Не следует слишком усердствовать, т. к. стружка может потерять часть свойств.
Известковый порошок позволяет продлить срок службы теплоизоляции. Благодаря присутствию этого компонента утепление стен опилками даст хороший результат: масса приобретает твердую консистенцию, становится плотной, благодаря чему снижается риск деформаций. Также она отличается монолитностью, а значит, хорошо выполняет свою главную задачу по снижению теплопотерь. Благодаря этому самодельный утеплитель становится непривлекательным для грызунов.
Такой материал редко применяется при обустройстве пола, если планируется заливать поверхность бетонной стяжкой. Это обусловлено тем, что стружка со временем дает усадку и отличается низкой прочностью. По этой причине известь и опилки смешивают при утеплении пола только в тех случаях, когда сверху слой теплоизоляции защищается дощатой конструкцией.
Опилки с цементом как утеплитель
С помощью извести и древесной стружки готовят материал повышенной прочности. К этим компонентам добавляют цемент. Если требуется знать, какое количество материалов необходимо использовать (их соотношение, пропорции), то видео поможет правильно приготовить смесь. Главная особенность данной технологии заключается в тщательном перемешивании цемента, опилок, извести. Благодаря этому древесная стружка в дальнейшем хорошо пропитается влагой.
Компоненты:
- 1 ведро цемента;
- 1 ведро извести;
- 10 ведер опилок.
Подготавливают антисептик (25 г/ведро воды) и орошают сыпучую смесь. В результате она должна приобрести достаточную плотность. Проверить готовность материала можно, сжав его в кулаке. Если смесь сохраняет форму и при этом не выделяется вода, можно использовать опилки с цементом как утеплитель.
Из полученного материала делают блоки. Засыпка осуществляется послойно. Чтобы утеплитель полностью просох, понадобится 2 недели. Затем блоки проверяют на наличие пустот. Если неплотности остались, их заполняют этой же смесью.
Это прочный материал, который по составу напоминает классический бетон, однако в качестве наполнителей добавляются мелкие опилки, известь. Соотношение компонентов может быть разным. Выбор варианта делается с учетом требований к прочности материала. Например, чтобы изготовить опилкобетон высокой плотности, понадобятся:
- 200 кг цемента;
- 200 кг опилок;
- 500 кг песка;
- 50 кг извести.
Количество компонентов может уменьшаться/увеличиваться, но важно соблюдать пропорции. Чтобы повлиять на способность древесной стружки впитывать влагу, ее нужно вымачивать в известковом молочке, затем — в жидком стекле. На следующем этапе опилки просушивают. Это необходимо для того, чтобы в момент соединения компонентов древесная стружка не содержала влагу.
Подготовительные работы
- Древесную стружку необходимо просушить.
- Затем ее равномерно смачивают антисептиком.
При необходимости используют антипирены. Благодаря такой обработке улучшаются качества опилок: повышается огнестойкость, материал становится менее привлекательным для насекомых, грызунов, в структуре и на поверхности утеплителя не образуется грибок.
- Опилки просушивают повторно.
- Перед укладкой теплоизоляции на поверхность настилают гидроизоляционный материал.
Можно в стружку добавить известь или табак. Применение смеси глины с опилками делает материал более устойчивым к воздействию влаги. Однако и в этом случае нужно предварительно подготовить его.
При этом рекомендуется использовать крупные фракции стружки при засыпке нижнего слоя. С помощью более мелких опилок или трухи укладывают второй слой. При ответе на вопрос о том, как сделать эффективную теплоизоляцию поверхности, рекомендуется придерживаться схемы:
- На лаги настилают пленочную гидроизоляцию.
- Сверху набивают черновой дощатый пол.
- Выполняется повторная гидроизоляция.
- Насыпают опилки, делать это следует послойно. Толщина каждого слоя — 10 см.
- Материал трамбуется.
- Опилки оставляют на просушку, для чего делается перерыв в работе на 3-4 дня.
- Сверху материал защищается от влаги, настилается чистовое дощатое покрытие, и производится отделка.
Утепление стен опилками выполняется не только посредством чистой стружки, но и с помощью смесей на основе извести, цемента. В данном случае просушка уложенной изоляции займет больше времени: от 2 до 3 недель.
Принцип использования опилок одинаков при утеплении стен, потолка, пола.
Вывод
Из всех вариантов древесная стружка — наиболее экологичный материал. Она отличается хорошими показателями по теплопроводности и звукоизоляции, а значит, может использоваться наряду с технологичными аналогами. Если правильно подойти к улучшению свойств этого материала, можно добиться повышения огнестойкости, влагостойкости, продлить срок службы.
Это становится возможным благодаря обработке антисептиками, антипиренами. Кроме того, снизить интенсивность оттока тепла из помещения при использовании опилок поможет правильная укладка: послойно с трамбовкой.
Опилки и известь могут использоваться как утеплитель дома, эти материалы способны качественно сохранять тепло. Основными преимуществами такого материала является доступность, небольшая стоимость, и высокие свойства термоизоляции. Также опилки с известью в качестве утеплителя, обладают высокой звуковой изоляцией, теплоизоляцией, и экологической чистотой.
Технология утепления дома с помощью опилок и извести
Утепление дома с помощью опилок и извести поможет значительно сэкономить на расходах, и повысить теплоизоляционные свойства.
Способ № 1
Для проведения работ, необходимо подготовить такие материалы:
- опилки, известь, цемент, антисептик для обработки дерева;
- емкость для смешивания ингредиентов;
- лопата, мешалка, и лейка.
Толщина утеплительного слоя будет зависеть от местности, погодных условий, и эксплуатации здания. Если постройка используется как дача, только в летний период, то слой утеплителя для чердака должен быть до 25 сантиметров, а для стен – 15. Но при постоянном жительстве в доме, наносят слой утеплителя до 30 сантиметров.
Для обеспечения безопасности дома от пожара, всю проводку необходимо закрыть металлическими рукавами.
После этого приступают к приготовлению смеси для утепления. Чтобы состав получился правильный, необходимо взять 10 частей опилок, одну – извести, и одну – цемента или гипса. Все компоненты смешиваются, и обрабатываются борной кислотой или любым антисептиком для дерева. Затем добавляют около 10 ведер воды (на 10 ведер опилок). После замешивания, смесь нужно крепко сжать в руке, а затем посмотреть, чтобы она не рассыпалась.
Затем состав наносят на участки, которые нуждаются в утеплении, утрамбовывают её, и оставляют на две недели. По истечении этого времени, проверяют пустоты, если таковые имеются, то их необходимо засыпать опилками. При отсутствии пустот, можно приступать к дальнейшей отделке.
Способ № 2
Для того чтобы приготовить состав вторым способом понадобиться:
- опилки, глина, известь, вода;
- емкость для замешивания;
- лопата, мешалка, и лейка.
Чтобы сделать утеплительную смесь, нужно взять опилок 10 частей, глины – 5, извести – 1, воды от 7. Глина заливается двумя частями воды, она должна полностью раскиснуть, раствор должен напоминать густую сметану, и не содержать комки. Затем опилки размешивают с известью, и добавляют в разведенную глину. Все компоненты хорошо размешивают, и постепенно добавляют остальную часть опилок. Затем в раствор помещают обычную палку, если она остается стоять, и не падает, то смесь уже готова к использованию. Если состав получится жидкий, то его необходимо отстоять в течение суток, чтобы влага испарилась.
Как утеплить потолок с помощью опилок и извести?
Через верхнюю часть помещения выходит основное тепло, поэтому именно потолок требует утепления. Утеплять потолок лучше сухой смесью извести и опилок. Для этого опилки вначале обрабатывают с помощью антисептика, затем оставляют на просушку, и добавляют известь-пушенку. 10 частей опилок хорошо перемешивают с одной известью, это поможет избавиться от грызунов. После тщательного перемешивания, смесь выкладывают со стороны чердака толщиной до 30 сантиметров, а затем её уплотняют.
Также крышу и чердачную часть можно утеплить влажным составом, для её приготовления используют: 85 процентов опилок, 5 – гипса, 10 – извести. При таком приготовлении опилки не просушивают после обработки антисептическим средством. Состав быстро схватывается, поэтому его необходимо приготавливать небольшими порциями, и укладывать сразу. Опилки являются легкими, их разбавляют с более тяжелыми материалами для хорошей усадки.
Как утеплить стены с помощью опилок и извести?
Чтобы сделать утеплитель для перегородок и стен, нужно правильно приготовить состав. Высушенные и чистые опилки 10 частей, тщательно размешивают с одной известью, в этот состав добавляют антисептик. Затем приготовленную смесь засыпают в стены и утрамбовывают. При этом опилки не дают усадку, а антисептик помогает предотвратить появление вредителей и гнили в древесине.
Из опилок можно сделать утеплительные блоки, для этого понадобятся такие дополнительные материалы, как медный купорос и цемент. Вначале опилки обрабатывают медным купоросом, а затем соединяют с цементом. После тщательного перемешивания, добавляют воду так, чтобы в итоге сжатый раствор не распадался. Такой состав закладывают в стены, и места, которые нуждаются в утеплении. Каждый слой необходимо подвергать качественной утрамбовке. Цемент соприкасается с опилками, напитанными влажностью, и быстрее застывает. После высыхания поверхность является твердой и устойчивой, не деформируется от нагрузки.
Использование опилок для утепления пола
Опилки не используются в чистом виде, без добавления каких-либо примесей, так как они имеют высокую способность к возгоранию. Но опилки используются в составе таких материалов, как эковата или арболит, которые отлично подходят для утепления пола.
Если температура зимой достигает 20 градусов, то утеплитель наносится толщиной от 15 сантиметров.
Использование опилок как утеплитель
Опилки являются экономным материалом, так как имеют невысокую стоимость, их используют в качестве утеплителя крыш, междуэтажных перекрытий, полов, и потолков. Состав из опилок и извести является экологически чистым материалом, без включения синтетических добавок, он обладает высокими свойствами звукоизоляции и теплоизоляции.
В состав добавляют известь для качественной утрамбовки и усадки материала, а также она предотвращает появление грызунов. Опилки активно используют в качестве утеплителя для потолка. Благодаря опилкам и извести можно получить качественное утепление стен и потолка.
Особенности применения опилок и извести в качестве утеплителя
Вначале опилки тщательно размешивают с другими ингредиентами, затем наносят на участки, которые требуют утепления, и утрамбовывают. В итоге получается блок из древесины, который не поддается гниению и разрушению. Опилки необходимо обработать антисептиком, а затем тщательно высушить, после чего перемешивать с известью, она защищает поверхность от различных грызунов.
На участках, куда трудно подобраться, применяют опилки без всякого рода примесей. Чистые опилки, без обработки специальным средством, имеют недостатки, они являются огнеопасными, а также в таком материалы могут завестись грызуны. При правильной обработке, и добавлении примесей, этих проблем можно избежать.
Как правильно выбрать опилки?
При выборе материала, качество опилок зависит от их стоимости. То есть опилки могут быть выполнены из токсических деревьев, а их цена значительно ниже. При приобретении опилок, необходимо потребовать у фирмы документацию на материал, так можно убедиться в его экологической чистоте.
Чтобы утеплить дом, необходимо выбирать опилки фракции среднего вида. Если опилки будут крупными, то они теряют часть теплоизоляционных свойств, а при слишком мелком материале возникает неудобство в работе, так как издают много пыли, и могут разлетаться.
Если приобретены материалы с естественной влажностью, то их необходимо предварительно просушить. Для утепления жилого помещения лучше использовать опилки от хвойного дерева, они содержат смолу, и отталкивают грызунов и вредителей. Для того чтобы утеплить баню, можно использовать опилки лиственных деревьев, их перемешивают с золой или известью, в противном случае они будут подвергаться гниению.
Перед использованием, материал выдерживают от полугода до года, чтобы в опилках снизились вещества, которые способствуют гниению. Опилки не должны содержать мусор и другие включения, поэтому их можно просеять через строительное сито.
Использование опилок и извести в качестве утеплителя экономит расходы, так как стоимость материалов не является высокой. Опилки обладают высокими теплоизоляционными и звукоизоляционными свойствами, но их нельзя использовать в чистом виде, без примесей, так как они склонны к быстрому возгоранию. Благодаря использованию опилок и извести во влажном виде, получаются качественные утеплительные блоки, которые не подвергаются горению, гниению, и повреждению грызунами. Такими материалами можно утеплять потолок, стены, полы, крышу и чердачное помещение.
Существует миф, что утеплитель должен быть технологичным. На самом же деле утеплитель должен быть функциональным и максимально дешевым. В соответствие с этими требованиями такой архаичный материал, как опилки, кажется более чем подходящим для использования в качестве утеплителя.
Нужно сразу отметить, что в качестве сухой засыпки опилки не используются никогда. Используется раствор извести, глины или бетона, в котором опилки служат наполнителем. Такой раствор заливается в брикеты определенных размеров и толщины, после чего брикеты уже используются в качестве утеплителя.
Определяющим фактором использования опилок является цена. Вблизи деревообрабатывающих предприятий достать опилки можно и вовсе бесплатно. Постоянная утилизация отходов вечная головная боль подобного рода фирм. Проблема в том, что опилки нужно просушить в условиях солнечного лета. Влажные опилки для использования не подойдут. Если к этому прибавить необходимость самостоятельного изготовления брикетов, то нетрудно понять, что для утепления дома опилками понадобится весь теплый сезон.
Тем не менее, существенная экономичность, опыт поколений, подтверждающий все свойства утеплителя, и экологичность изначальных материалов – три фактора, которые делают опилки достаточно хорошим утепляющим строительным материалом.
Единственные факторы разделения опилок это способ получения. Дело в том, что при распилах древесины получается мелкофракционная древесная пыль, которую зовут трухой. В остальных случаях получается стружка. Для утепления лучше подходит стружка, так как в ней остаются древесные каналы, которые способствуют увеличению парапроницаемости и теплоизолирующих свойств.
Если говорить о древесной пыли, то она быстро комкуется, крайне гигроскопична и подвержена гниению. Ее сложно пропитать защитными составами. Поэтому, когда говорят об утеплении дома опилками, имеют в виду утепление стружкой.
Отдельное внимание нужно обратить на сорт древесины. Лучше всего для утепления подходит дуб и осина. Худшим вариантом является сосна. Опилки этого дерева обладают большей гигроскопичностью и выделяют смолы в окружающее пространство, что плохо влияет на утеплитель.
Плюсы и минусы
Поговорим о достоинствах и недостатках опилок в качестве утеплителя. Достоинства большей частью понятны и логичны:
- Экологичность
- Дешевизна
- Доступность
С недостатками немного сложнее, поэтому разберем каждый пункт в подробности:
- Трудоемкость. Утеплять дом придется самостоятельно. Потому что наемные специалисты могут взять не так много денег за работу, но утеплить дом базальтовой ватой самостоятельно будет в любом случае проще, дешевле и быстрее. Поэтому, если нужно сэкономить на утеплении, то делать всю работу придется самостоятельно.
- Гигроскопичность. Дерево подвержено воздействию влаги. В какой-то мере это нивелируется специальными пропитками, но опасность все равно сохраняется. Именно по этому редко используется сухая засыпка опилок в стены или перекрытия.
- Пожароопасность. Еще 10-15 лет назад эта проблема была бы актуальной. Сегодня огромное количество пропиток представленных на рынке практически нивелируют эффект возгораемость древесины.
- Грызуны. Экологичность древесины делает такой утеплитель любимым жилищем грызунов, насекомых и прочих вредителей. Поэтому в состав утепляющих брикетов должны входить антисептики или сушеный табак. Эффект будет примерно одинаковый, поэтому целесообразность применения табака лучше высчитывать из экономических соображений.
В общем и целом, на данный момент практически все недостатки кроме трудоемкости вполне устранимы современными средствами. Поэтому, если лишняя работа не пугает, а у владельца дома есть свободное время, то утепление опилками станет отличным вариантом сэкономить и встретить зиму в утепленном доме.
Способы применения для утепления и вяжущие составляющие
Все способы утепления можно разделить на:
- Засыпку
- Заливку
- Штукатурку
- Брикеты
Засыпка применяется крайне редко. На сегодняшний день использовать засыпку целесообразно только для чердачного перекрытия. В какой-то мере таким подходом можно заменить утепление потолка. Сухой материал смешивается с табаком или битым стеклом, после чего послойно засыпается слоями по 10 см. Желательно менять фракционность опилок в слоях от крупной к мелкой.
Перед засыпкой все щели обязательно заделываются монтажной пеной, само перекрытие покрывается пароизоляцией внахлест. Обязательно нужно озаботится защитой проводки и дымовой трубы, чтобы опилки не загорелись от высоких температур или проскочившей искры. После засыпки опилки закрываются досками. Между досками обязателен вентиляционный зазор.
Если использовать засыпку в качестве утепления, то нужно быть готовым досыпать материал через 2-3 года. Каких бы фракций не была стружка, она в любом случае сваляется.
Заливка подразумевает использование раствора с наполнителем из опилок. Раствор заливается в полости стен или потолок. Но для стен проще использовать брикеты. Это блоки удобных для утепления габаритов, которые укладывают в стену в качестве внутреннего утепления. Для наружного утепления применять опилковый утеплитель не рекомендуется, так как дерево в любом случае будет тянуть влагу, что приведет к коррозии и гниению.
Опилки – отличный утеплитель
В качестве вяжущих используется:
- Цемент
- Известь
- Глина
Нужно обратить внимание, что известь не используется без цемента. Известковый порошок добавляют в качестве присадки для экономии цементного состава. Перед тем, как рассмотреть применение каждого из вяжущих, нужно отметить, что есть два способа обработки опилок перед утеплением. В первом случае опилки пропитываются перед применением. Для этого нужно над средним слоем опилок распылить антисептик и другие пропитки. Проблема в том, что сохнут опилки долго, происходить этот процесс должен при естественной вентиляции летом, в закрытом помещении. Сохнуть с такой пропиткой опилки будут весь сезон. Это значит, что утепление придется перенести на следующий год.
Есть способ ускорить процесс. Для этого нужно пропитки добавлять в воду, которая используется для приготовления раствора. Антисептик можно добавить и вовсе на этапе приготовления раствора. В качестве антисептика можно использовать медный купорос или буру. Но нужно иметь в виду, что при нагревании эти вещества могут выделять вредные для человеческого организма вещества. Поэтому для бань такие присадки не подойдут.
Для приготовления раствора на основе цемента понадобится:
- 20 частей опилок
- 2 части цемента
- 3 части воды
Желательно раствор делать вручную. В бетономешалке опилки могут сваляться, что испортит материал. После смешения всех частей, опилки должны быть вымазаны в растворе. Для проверки готовности смеси ее сжимают в кулаке. Готовый раствор пускает влагу, но капли стекать по кулаку не будут. Это значит, что можно начинать заливку. Лют опилкобетон одним слоем, с легким уплотнением. Такая смесь подойдет для пола, поскольку по ней можно ходить, не опасаясь за целостность покрытия.
Для стен и чердака используют раствор на основе извести. В его состав входят:
- 0,85 части опилок
- 0,1 часть извести
- 0,05 частей алебастра
Вода заливается из расчета воды, необходимой для разведения строительного гипса. Преимуществом известкового раствора является экономия цемента и антисептика. В толщу известкового материала не пролезет ни один грызун. Но при этом известь делает материал более мягким. Из-за этого такой раствор не подойдет для утепления пола. В противном случае, пол придется застилать деревянными плитами и все время опасаться, что излишняя мебелировка продавит черновое покрытие пола.
Третий вариант вяжущего это глина. Глина нужна жирная, только у такого вяжущего характеристики достаточны для использования опилок. На ощупь кусок глины будет примерно как мыло. Нужно отметить необходимость замачивания глины перед созданием раствора. Глина должна около суток пролежать в воде. Если учитывать большие объемы работ, то лучше подготовить побольше готовой смеси впрок.
Глина заливается водой в отношении 5 частей глины на 2 части воды. После разбухания, глина замешивается с опилками. Опилки желательно смешать с известковым порошком в отношении 10 к 1. Раствор укладывается площадками 25 на 25 см.. Примерная толщина слоя 10 см.
Сохнет черновое покрытие около месяца. После этого готовится раствор на основе мелкофракционной щепы или древесной пыли и выполняется числовое покрытие. Чистовое покрытие может покрыться трещинами, это значит, что была выбрана слишком малая толщина второго слоя. Трещины достаточно замазать тем же составом. По получившемуся полу можно без опасений ходить ногами, расставлять мебель и накрывать разного рода покрытиями. Самый большой недостаток глины: время.
Использование опилок для утепления различных частей дома
Сильно меняться состав утеплителя не будет, но для разных покрытий лучше подойдут разные составы. Поэтому обсудим оптимальный вариант для каждой поверхности.
Стены
Стены отличаются повышенным вниманием грызунов и вредителей. При этом к стенам не предъявляется требований повышенной устойчивости к механическому воздействию. Поэтому в качестве утеплителя можно использовать штукатурку или брикеты на основе извести.
Конечно, можно воспользоваться способом литья. Так дом будет утеплен более надежно, но эффективность повысится не сильно, а трудоемкость значительно возрастет.
Пол
Для пола первого этажа лучше всего использовать бетонный или глиняный раствор. Выбор зависит от располагаемого времени и желания работать. Глиняный раствор тверже и долговечнее. Опилкобетон проще сделать и быстрее залить.
Потолок
Утепляют не потолок, а чердачное перекрытие с помощью просыпки чердачного пола опилками или смесью опилок и извести. Многие дачники советуют смешивать опилки с табаком или битым стелком, чтобы предотвратить появление грызунов. Почему все не используют известь?
При нагревании известковый порошок может начать выделть тепло в больших количествах. Вместе со свободно лежащими опилками это может привести к возгоранию.
Крыша
У крыши слишком большие требования к отсутствию гигроскопичности и устойчивости к влаге. Поэтому для утепления крыши опилки не используют. Существует множество достаточно дешевых материалов, которые проще и надежнее установить на крыше вместо опилковых брикетов.
Критерии выбора оптимального состава утепляющей смеси
На самом деле, определяющим критерием выбора смеси является располагаемое время. Если время есть, то лучше все утеплять глиняным раствором. Если со временем проблемы, то в жилой части помещения лучше использовать опилкобетон, а пол чердака просыпать смесью опилок и битого стекла. В остальном все зависит от наличных материалов. Если в наличии известь, а цемент нужно покупать, то стены лучше утеплять известковым раствором и так далее.
В общем и целом, опилки не утратили свою актуальность в качестве утеплителя. Это дешево, экологично и достаточно функционально. Единственный фактор, который может отпугнуть строителя это трудоемкость. Для того, чтобы использовать опилки их нужно обработать, высушить, распланировать место использования той или иной фракции. Приготовить раствор, заготовить брикеты и еще очень много достаточно трудоемких и долгих процедур. Тем не менее, правильный подход к утеплению опилками позволит создать теплую и долговечную конструкцию.
Эффективное и недорогое утепление цоколя бани опилками с цементом. Прошло 15 лет | Хозяйство Воронова
Небольшой слой утеплителя опилок с цементом, держат перепады температур замечательно. Зимой в бане тепло, а летом прохладно. Прошло 15 лет.
БаняБаня
Тверская область
Можно рассказывать всё что угодно, но против проверкой временем не попрёшь.15 лет прошло после моего эксперимента и теперь можно уверенно рассказать про эту технологию.
Кто ещё не знает, занимался стройкой 20 с лишним лет. Имея 33 специальности, интуиция и смекалка помогала открывать новые технологии, каких в России ещё не было и до сих пор многие ими пользуются.
Кстати, меня найти можно в Youtube или написать Вконтакте
Наверняка задумывался, как построить самый недорогой дом и ломал голову какие материалы применить. Вот и я в своё время задался этим вопросом, писал чертежи, высчитывал и экономил.
Дома получались самые недорогие, по сравнению. Кстати строительство фундаментов на бочках и винтовых сваях открыл ещё в 2000 году.
Одна из технологий, которую применил в качестве эксперимента при утеплении цоколя бани, позволила за 15 лет убедиться в эффективности и недорогой стоимости.
УТЕПЛЕНИЕ
В 1995 году, строил баню и сделал столбчатый фундамент, по периметру кирпичный в полкирпича цоколь. Который, по понятным причинам промерзал.
Тогда решил утеплить по рабоче-крестьянски…. ))) Компоненты — вода, цемент и опилки. Пропорции точно уже не помню, времени много прошло, скажем на ведро готового цементного раствора — 2 ведра опилок.
Было бы лучше, если вымочить опилки от плесневения в извести. Но этого не делал, торопился. Пропорции записал, да только компьютер устарел и нужно из кладовой доставать и подключать. А мне в облом …
Сделал опалубку, отступив 5 -7 см от кирпича и залил перемешанную смесь. Вообще желательно не менее 10 см, чтобы уж наверняка, а лучше ещё больше. Но сколько было материала из того и делал.
Снял опалубку, потрогал … эластичная, как резиновая. За эти годы такая же и осталась, упругая, открытая и незащищённая. Лишь в одном месте треснуло. Мыши не дырявили, видимо под фундаментом пролезают..))
<<<— листай 6 фото —>>>
Конечно тепло зимой и прохладно летом не только от утеплённого цоколя. В бане полы бетонные, армированы и утеплены пеноплексом. Самое то !
Читайте комментарии, там очень много интересного !
Я в интернете «Хозяйство Воронова» и подпишись на канал
Ещё мои статьи и видео:
- Установили каркас пристройки бани на фундамент из бочек
- Дополнительный фундамент из бочек под пристройку к бане
Друзья ! Ваши комментарии и лайки — это новые публикации !!!
Использование обработанных опилок в бетоне в качестве частичной замены природного песка
https://doi.
Highlights
- •
Песок в бетоне заменен на 5 , 10, 15 и 20% обработанные водой опилки.
- •
Оптимальное количество опилок, обработанных водой или силикатом натрия, составляет 5%.
- •
Плотность бетона снижается при использовании опилок.
- •
Прочностные характеристики бетона, модифицированного 5% опилок, сопоставимы.
- •
Повышенная проницаемость для ионов хлора на микрокремнеземе в бетоне, модифицированном опилками.
Abstract
Крупномасштабная добыча природного материала, такого как песок, для использования в строительстве инфраструктуры в развивающихся странах, таких как Индия, представляет угрозу для окружающей среды. Таким образом, чтобы сохранить окружающую среду, исследователям становится обязательным исследовать использование побочных продуктов промышленности вместо природного материала. В этом исследовании изучалось использование опилок, образующихся в деревообрабатывающей промышленности, в бетоне. В этой статье представлены свойства бетона с разным процентным содержанием опилок, обработанных водой и силикат натрия, вместо песка. Опилки, прошедшие через сито 4,75, перед использованием в бетоне обрабатывали водой и силикатом натрия в течение 24 ч. Природный песок заменили на 5, 10, 15 и 20% обработанных водой опилок в бетонной смеси. Влияние микрокремнезема на свойства бетона, содержащего 5 % водообработанных опилок, изучалось также при замене 4, 8 и 12 % цемента на микрокремнезем в бетоне.Было замечено, что бетон, изготовленный из опилок, обработанных 5% воды или силиката натрия, показал прочность на сжатие, сравнимую с прочностью контрольного бетона. Однако при уровне замещения 10 % прочность на сжатие и прочность на растяжение при разделении снизились на 30,30 % и 32,19 % соответственно через 28 дней. Общая пройденная загрузка, водопроницаемость и капиллярное водопоглощение увеличились на 224 %, 153 % и 117,4 % соответственно при использовании 10 % обработанных опилок.
Бетонная смесь, модифицированная опилками, обработанными силикат натрия, показала значительное улучшение в отношении сопротивления проникновению ионов хлора.Как и ожидалось, результаты показали значительное снижение плотности бетона при использовании опилок вместо песка. Добавление опилок, обработанных силикат натрия, привело к образованию большого количества эттрингита в бетоне.
Ключевые слова
Опилки
Бетон
Прочность на сжатие
Сорбционная способность
Проницаемость хлоридов
Рекомендуемые статьиСсылки на статьи (0)
Просмотр полного текста 90Рекомендуемые статьи
Ссылающиеся статьи
МОДИФИЦИРОВАННЫЙ ОПИЛИБОБЕТОН: Статыба: Том 6, № 2
Резюме
Древесно-цементные материалы широко производятся и применяются во многих развитых странах. В этом случае используются специально подготовленные древесные заполнители. Древесные опилки практически не используются.
Экстракты, содержащиеся в древесине, замедляют гидратацию цемента. Определено влияние минеральных добавок на этот процесс. Эффективность минеральных добавок зависит от их гидравлической активности.
Установлено, что минеральные компоненты (добавки) опилкобетона положительно влияют на схватывание и твердение цемента по двум причинам: 1) гидравлические и другие минеральные добавки поглощают из жидкой фазы экстракты древесины, которые тормозят и замедляют схватывание цемента и уменьшить их концентрацию в растворе; 2) снизить рН жидкой фазы, чтобы гемицеллюлоза, находящаяся в опилках или других древесных агрегатах, меньше распадалась на легкорастворимые сахара.
При различном количестве опилок оптимальное соотношение цемента и щебня непостоянно:
y = 1,29 x −0,66
где y — отношение массы цемента, 07 х — объемное соотношение опилок и вяжущего материала (цемент + щебень).
Установлено влияние влажности опилкобетона на его прочность:
где y — прочность бетона на сжатие (МПа), при влажности X (%), R — прочность бетона на сжатие (МПа) , при его влажности Вт (%).
Исследована также возможность ускорения процесса твердения бетонных смесей системы цемент-щебень (опока)-опилки путем пропаривания при 80 °С. Это невозможно при производстве обычных древесно-цементных материалов.
Определены физико-технические свойства опилкобетона, такие как деформации усадки, деформации расширения и модуль упругости.
Деформация опилкобетона при усадке в зависимости от плотности бетона может изменяться на 8…14 мм/м, а при расширении (во влажных условиях) на 1,1…2,5 мм/м. Деформация уменьшается при использовании добавки кварцевого песка. Когда бетон многократно высыхает, деформации меньше.
Модуль упругости опилкобетона такой же плотности, как и у легкого бетона с неорганическими добавками.
Морозостойкость зависит от структуры бетона и количества цемента. При использовании бетона с небольшим количеством опилок (цемент+добавка: опилки=5:1) образцы выдерживают 75 циклов замораживания.
Теплопроводность опилкобетона низкая.
Экспериментальные данные показали, что из этих бетонных смесей можно изготавливать конструкционные теплоизолированные блоки.
Экспериментальная оценка и численный прогноз
Резюме
Активированные щелочью бетоны появились в качестве перспективной альтернативы обычному бетону, в котором различные отходы были преобразованы в ценные побочные продукты.В данной статье представлено широкое экспериментальное исследование устойчивости использования отходов опилок в качестве замены мелкого/крупного заполнителя, включающего летучую золу (FA) и гранулированный доменный шлак (GBFS), для производства высокоэффективных бесцементных легких бетонов. Отработанные опилки заменяли заполнителем в количестве 0, 25, 50, 75 и 100 об.% с включением щелочного вяжущего, в том числе 70% ФК и 30% ГБФС. Смесь активировали, используя низкую концентрацию гидроксида натрия (2 М). Были оценены акустические, тепловые и прогнозируемые инженерные свойства бетонов, а также рассчитан жизненный цикл различных смесей для исследования устойчивости бетона. Кроме того, с использованием имеющейся базы данных экспериментальных испытаний была разработана оптимизированная искусственная нейронная сеть (ИНС) для оценки механических свойств разработанных растворных смесей, активированных щелочью, в зависимости от каждого объемного процента опилок. На основании полученных данных установлено, что звукопоглощение и снижение теплопроводности усиливаются с увеличением содержания опилок. Установлено, что на прочность образцов при сжатии влияет содержание опилок, при этом прочность снижается с 65 до 48 МПа при соответствующем увеличении содержания опилок от 0 до 100 %.Результаты также показали, что выбросы двуокиси углерода, использование энергии и затраты имеют тенденцию к снижению с увеличением количества опилок и показывают, что легкий бетон более устойчив для строительных целей.
Ключевые слова: легкий бетон, активированный щелочью, отходы опилок, прогнозируемые технические свойства, устойчивость
1. Введение
Опилки – хорошо известные сельскохозяйственные отходы и побочный продукт деревообрабатывающей промышленности. Он образуется как отходы, когда древесина механически измельчается до различных размеров и форм. Многие экологические проблемы вызваны отходами опилок, при этом нехватка места для захоронения отходов является серьезной проблемой и серьезной угрозой для развитых стран. Излишние опилки, которые накапливаются в результате деятельности заводов, фабрик и жилых домов, ежегодно увеличиваются. Подсчитано, что ежегодное образование древесных отходов в Соединенных Штатах Америки, Германии, Великобритании и Австралии составляет около 64,8.8, 4,6 и 4,5 млн т в год соответственно, причем более 40 % этих объемов не перерабатываются [1,2,3,4]. Высокий процент непереработанных древесных отходов свидетельствует об отсутствии достаточных процедур и стратегий переработки. Таким образом, крайне важно ежедневно перерабатывать древесные отходы и эффективно использовать их в цементных композитах/бетонах, чтобы гарантировать их безвредную утилизацию в качестве средства защиты окружающей среды.
В настоящее время перед исследователями стоит серьезная задача из-за постоянного увеличения спроса на легкие бетоны с высокими эксплуатационными характеристиками (LWC) в качестве строительных материалов, где производство новых строительных материалов из переработанных промышленных отходов стало стратегией. С этой точки зрения оценивается продвижение LWC за счет использования отходов опилок в качестве легких заполнителей. Функции опилок в цементах/бетонах оценивались несколькими исследователями, и в прошлом они использовались для изготовления легких бетонов [5]. Сообщалось о тепловых характеристиках цементного композита на основе опилок [6], при этом было обнаружено, что его включение в бетонную матрицу значительно снижает теплопроводность до 20% по сравнению с обычным бетоном (0% опилок).Столь значительное снижение значений электропроводности связывают со снижением плотности и повышенной пористостью легких бетонных композиций, модифицированных опилочными отходами. Ойедепо и др. [7] использовали отходы опилок в качестве заменителя мелкого заполнителя (природного) при различном содержании от 0% до 100% в стандартных тяжелых бетонах и показали, что соотношение более 25% заменителя к натуральным заполнителям может отрицательно влиять на прочность бетона. свойства и плотность. Другие исследователи также сделали аналогичные наблюдения, когда опилки использовались в бетоне на различных уровнях (10%, 20%, 30% и 40%) вместо песка.
Было высказано предположение, что количество опилок при замене песка до 10% может обеспечить лучшую плотность и механическую прочность бетона [8]. Буб [9] также использовал опилки в качестве заменителя мелких заполнителей (0–15%) в бетоне. Mageswari и Vidivelli [10] показали, что зола опилок в качестве агента для замены природного песка может быть подходящим выбором для мелких заполнителей в бетонах. Это может значительно уменьшить проблему вывоза опилок и одновременно позволить сохранить природные мелкие заполнители.Авторы обнаружили, что бетон, содержащий опилки, обладает уникальными характеристиками и демонстрирует лучшие результаты для тепловых и механических характеристик композита на основе цемента, что делает его экономичным по сравнению с различными другими материалами в строительном секторе.
В последнее время некоторые продукты, такие как геополимеры и активируемые щелочью материалы, были представлены в качестве альтернативы обычному бетону и стали конструкционными материалами с меньшим выбросом CO 2 [11,12,13,14,15,16,17] . Активированные щелочью пасты/растворы/бетоны представляют собой неорганические полимеры на основе кальция (CaO) и алюмосиликатов (AS), активированные раствором щелочного активатора. Их получают из пуццолановых соединений путем щелочной активации NaOH и силикатов натрия (NaSi) [18,19]. Эти вяжущие, полученные с использованием щелочной активации, показали себя экологически чистыми из-за необходимости небольшого количества энергии в процессе их изготовления [20,21]. После щелочной активации использовались различные твердые отходы различных производств, содержащие Si, Al и/или Ca, в том числе летучая зола (FA), топливная зола пальмового масла (POFA), метакаолин и гранулированный доменный шлак (GBFS). для приготовления строительных растворов/бетонов [22,23,24].
Несколько исследователей [25,26] заметили, что FA, содержащая большое количество CaO, также является подходящим исходным материалом для производства высокоэффективных геополимерных растворов и бетонов. Было показано, что смесь геополимера, приготовленная с ФА класса С (с высоким содержанием СаО), становится отверждаемой при комнатной температуре из-за реакции, опосредованной СаО. Тем не менее, геополимеризация ФА класса С в отсутствие добавки оказалась очень вялой при температуре окружающей среды [27], достигая низкой прочности.Тем не менее, использование материалов, содержащих большое количество CaO, в том числе обычного портландцемента (OPC), для повышения прочности геополимера на основе ТВС с высоким содержанием CaO остается перспективным [28]. Помимо образования гидрата силиката кальция (C-S-H) и гидрата силиката кальция-алюминия (C-A-S-H), тепло и вода, образующиеся в результате реакции, опосредованной OPC, могут помочь процессу геополимеризации. и тем самым развитие повышения прочности [29]. Путем включения OPC и отверждения при 25 ° C были получены геополимерные растворы на основе FA с высоким содержанием Ca с прочностью на сжатие (CS) 65 МПа [30].
Аморфный ГБФ, являющийся одним из самых популярных промышленных отходов, широко используется для повышения нормальной прочности бетона или изготовления бесцементных растворов/бетонов из-за избыточного содержания Al 2 O 3 , CaO и SiO 2 по своему химическому составу [31,32,33,34,35]. В щелочной среде ГБФС проявляет как связывающие, так и пуццолановые свойства [36]. Многие исследования показали [37], что образование избытка Ca из-за добавления GBFS в геополимер FA является причиной улучшения прочностных характеристик, а также микроструктуры материала.Для оценки эффективности ГФС, включающей ФК, в качестве геополимерного связующего, соотношение ФК/ГБФС широко варьировалось вместе с типами, концентрациями и составами активатора в смеси для их получения [38,39]. Было обнаружено, что включение большого количества Ca, содержащего только 4% GBFS, повышает прочность геополимера [38]. Исмаил и др. [40] оценили CS и продукт гидратации паст FA и GBFS и показали повышение CS до 50 МПа в возрасте отверждения 28 дней.Было использовано повышение отношения FA к GBFS до 1,0, и оно было активировано 10 М раствором NH перед проведением отверждения при 25 ° C. Согласно Исмаилу и др. [41], предел прочности при сжатии (CS) композита FA/GBFS, активированного NH/NS, может значительно увеличиться при незначительном количестве гашеной извести.
Этот геополимер ТВС, смешанный со шлаком, показал превосходные механические характеристики и долговечность [42]. Предыдущие исследования пытались изготовить экологически чистые высокоэффективные LWC, бесцементные бетоны и активированные щелочью геополимеры, где основное внимание уделялось достижению улучшенных характеристик прочности и долговечности.
2. Научное значение
Всесторонний обзор литературы показал, что потенциальное использование отходов опилок для разработки активированных щелочью LWC для устойчивого функционирования еще не было широко изучено. В этой работе сообщается о влиянии замены древесных опилок природными заполнителями на характеристики устойчивости LWC с щелочной активацией, содержащей FA и GBFS. Эти смеси были изготовлены с переменным содержанием опилок, включая 70% FA, 30% GBFS и раствор, активированный щелочью, чтобы найти возможность переработки промышленных отходов и их преобразования в экологически чистый, долговечный и устойчивый легкий бетон. Таким образом, натуральные заполнители были заменены различными уровнями отходов опилок (0%, 25%, 50%, 75% и 100%) на реалистичном рабочем уровне с соответствующими физическими условиями для изготовления LWC, активированных щелочным раствором. Все синтезированные образцы были проанализированы различными измерениями для оценки свежести, механических свойств и долговечности для получения оптимального состава.
3. Детали эксперимента
3.1. Материалы
Печной шлак (ГБФС грязно-белого цвета) высокой чистоты был собран на малайзийском предприятии (Ипох, Малайзия) и использован без дополнительной очистки для получения бесцементного вяжущего.Он отличался от других дополнительных компонентов как вяжущими, так и пуццолановыми свойствами. Его получают в результате гидравлических химических реакций при смешивании воды. Рентгенофлуоресцентный анализ (XRF, HORIBA, Сингапур, Сингапур) спектров шлака показал наличие Ca (51,8%), силиката (30,8%) и Al (10,9%). Низкоактивные Ca-содержащие ТВС (глиноземно-силикатный материал серого цвета) были получены с малайзийской электростанции (Танджунгбин, Джохор, Малайзия) для производства предложенных ААС. Он удовлетворял требованиям ASTM C618 для FA класса F и содержал Ca (5,2%), силикат (57,2%) и Al 2 O 3 (28,8%). Медианный размер частиц ТВС и шлака (полученный с помощью анализатора размера частиц) составил соответственно 10 и 12,8 мкм. Физические характеристики обоих связующих материалов (GBFS и FA) были проанализированы с использованием теста Брунауэра-Эммета Теллера (BET, JEOL, Куала-Лумпур, Малайзия)) с удельной поверхностью (18,1 м 2 /г для FA и 13,6 м 2 ). /г для GBFS).
представляет рентгенограмму (XRD, Rigoku, Singapore, Singapore) GBFS и FA. Наблюдаемые интенсивные рентгеновские пики FA при 2θ = 16–30° обусловлены наличием поликристаллического кремнезема и Al 2 O 3 . Однако заметные пики под другими углами были обусловлены наличием кристаллитов кварца и муллита. Отсутствие резкого пика GBFS подтверждает его аморфную природу. Присутствие пиков кремнезема и кальция играло важную роль в составе GBFS и было полезным для производства AAM. И наоборот, введение FA требовалось для преодоления низкого уровня Al 2 O 3 (10,49%) в шлаке.
XRD-дифрактограммы летучей золы (FA) и шлака (GBFS).
В качестве мелкого заполнителя для изготовления контрольных образцов бетона использовали природный речной песок. Следуя протоколу ASTM C117, сначала песок промывали водой для удаления ила и примесей [43], а затем сушили в печи при 60 °C в течение 24 часов для удаления влаги. Полученный чистый песок удовлетворял требованиям ASTM C33–33M [44].Модуль крупности, удельный вес и наибольший размер частиц приготовленного песка составили 2,9, 2,6 и 2,36 мм соответственно. Гранатовый щебень, полученный из карьера, использовался в качестве крупного заполнителя в процессе подготовки образцов. При производстве обычного бетона размер крупного заполнителя играет важную роль в обеспечении хороших характеристик бетона. Поэтому максимальный размер крупных заполнителей был ограничен до 8 мм.
Отходы опилок (№6013) были получены () от деревообрабатывающей промышленности Малайзии (Syarikat Kilang Papan Chong Wah Sdn Bhd. , Джохор, Малайзия). Эти местные агроотходы обеспечивали получение из единого ресурса (плотность 174 кг/м 3 и максимальный размер 2,36 мм) для использования в качестве мелкого заполнителя. В качестве крупного заполнителя для приготовления ЛОК использовали опилки плотностью 182 кг/м 3 и максимальным размером 6 мм. Основные характеристики опилок включают химический состав и потерю воспламенения (LOI), как показано на рис.Основным компонентом опилок была целлюлоза (87% от общей массы) и небольшое количество CaO и Al 2 O 3 . Процент LOI опилок от общей массы составил 4,76%.
( a ) Мелкие опилки, ( b ) крупные опилки.
Таблица 1
Химический состав (в %) отходов опилок.
Химический состав (%) | |||||||||
---|---|---|---|---|---|---|---|---|---|
Целлюлоза | Ал 2 О 3 | Fe 2 О 3 | СаО | MgO | К 2 О | LOI | |||
87.![]() | 2.5 | 2.0 | 2.0 | 3.50 | 3.50 | 0.23 | 0.0.23 | 0,01 | 4,76 |
Раствор (ы) для щелочной активации был изготовлен из гидроксида натрия (NH) и силиката натрия (NS). Его использовали для растворения алюмосиликата из ТВС и ГБФС. Таблетки NH ч. д. а. (чистота 98 %) растворяли в воде и готовили раствор 13,7 % Na 2 O и 86,3 % H 2 O (2 М). Смесь НС высокой чистоты была приготовлена с использованием SiO 2 (29. 5 вес. %), Na 2 O (14,70 мас.%) и H 2 O (55,80 мас.%). Полученный раствор NH (2 М) сначала выдерживали в течение 24 ч при комнатной температуре, а затем смешивали с раствором NS, чтобы получить конечный раствор щелочи с модулем (Ms SiO 2 :Na 2 O) 1,21. Отношение NS к NH для всех щелочных растворов поддерживали постоянным и равным 0,75.
3.2. Составы смесей готовых бетонов
Для всех образцов LWC значения отношения щелочного раствора к вяжущему (S:B) и содержания вяжущего были зафиксированы на 0.40 и 450 кг/м 3 соответственно. Отходы, такие как FA и GBFS, использовались для изготовления смесей LWC с постоянными количествами 70% и 30% соответственно в качестве источников SiO 2 , Al 2 O 3 и CaO. Смесь, содержащая 100 % природных заполнителей (песок и гравий), была приготовлена и рассматривалась как контрольный образец (). Молярность NH, NS к NH и модуль щелочного раствора (Ms) были фиксированы для всех бетонных смесей. Влияние различного содержания мелких и крупных опилок в качестве заменителя природного заполнителя на конструкцию ЛПК показано на рис.Для оценки влияния отходов опилок на вес предлагаемого бетона, его прочность и процесс геополимеризации использовались четыре замены.
Таблица 2
Состав предлагаемого легкого щелочеактивированного бетона (кг/м 3 ).
Mix | Binder (кг / м 3 ) | Решение (кг / м 3 ) | тонкие и грубые агрегаты (кг / м 3 ) | ||||||||||||||
---|---|---|---|---|---|---|---|---|---|---|---|---|---|---|---|---|---|
FA | GBFS | NH | NH | NS | River Prap | Cracked Gravil | Crarde Sawdust | ||||||||||
S0 | 315 | 135 | 104 | 78 | 845 | 950 | 0 | 0 | |||||||||
S25 | 634 | 712 | 22 | ||||||||||||||
22 | |||||||||||||||||
S50 | |||||||||||||||||
475 | 45 | 47 | |||||||||||||||
S75 | 211 | 237 | 67 | 71 | |||||||||||||
S100 | 0 | 0 | 90 | 95 |
Товар | Значение | ||
---|---|---|---|
Скорость грузовика, км / ч | 80 | 80207 Diesel Стоимость, L / KM | 0.09 |
Diesel Стоимость, RM / L | 2.![]() | ||
Грузоподъемность, м 3 | 12 | ||
Стоимость перевозки 1 м 3 , РМ/км | 0,20775 | ||
Плотность натурального грубого совокупности, кг / м 3 | 31820 | ||
плотность песка реки, кг / м 3 | 1640 | ||
Плотность прекрасной опилки, кг / м 3 | 176 | 176 | |
Грубовая пиломатериальная плотность, кг / м 3 | 182 | ||
CO 2 Выпуск для 1 л дизель, тонна | 0,0027 | ||
Стоимость энергии для 1 л дизель ГД | 0.![]() |
Таблица 4
Выброс CO 2 , расход и использование энергии каждого материала зависели от жизненного цикла.
Материал | CO 2 Выброс, тонна / м 3 | 3 3 9002 3 3|||
---|---|---|---|---|
Sand | ||||
0,009 | 55 | 0,134 | ||
Гравий | 0.![]() | 65 | 0.148 | 0.148 |
0,0006 | 34.56 | |||
Грубая опилки | 0,0008 | 36 | 36 | 0.021 |
Total Co 2
∑i=1nmi [(di×Di×k1i)+(Ei×k2i)]
(5)
где mi – масса компонента i (т/м 3 ) , di – расстояние транспортировки (км), Di – расход дизельного топлива (л/км), k1i обозначает выброс CO 2 на 1 литр дизельного топлива в тоннах, Ei представляет собой общее потребление электроэнергии (кВтч), а k2i представляет собой выброс CO 2 на 1 кВтч электроэнергии в тоннах.
Общее потребление энергии:
∑i=1nmi [(di×Di×k3i)+(Ei×k4i)]
(6)
где k 3 i — потребление энергии на 1 л дизельного топлива в ГДж, Ei — общее потребление электроэнергии (кВтч) и k 4 i — потребление энергии на 1 кВтч электроэнергии в ГДж.
Общая стоимость:
∑i=1nmi [(di×Di×DPi)+Ti+(Ei×EPi)]
(7)
где DPi — стоимость дизельного топлива (РМ/л), Ti — транспортный сбор 1 м 3 (РМ/км), EPi — стоимость электроэнергии (РМ/кВтч).
4. Результаты и обсуждение
4.1. Удобоукладываемость и схватывание
иллюстрирует значения осадки приготовленного бетона в зависимости от уровней замены отходов опилок как песка, так и гравия. Результаты определения осадки показали, что увеличение содержания опилок вместо натуральных заполнителей снижает удобоукладываемость приготовленных бетонов. Величина осадки снизилась со 130 до 116, 102, 91 и 74 мм при повышении степени замещения песка и гравия опилками с 0 до 25, 50, 75 и 100 % соответственно. Как правило, удобоукладываемость бетона снижается с увеличением количества опилок в смесях. Тем не менее, влияние было более заметным при более высоком содержании опилок (100%). Как правило, на удобоукладываемость бетона влияли удельная площадь поверхности опилок и высокая потребность в воде при высоком уровне опилок в матрице. С другой стороны, использование отходов опилок в качестве мелкого/крупного заполнителя существенно улучшило текстуру бетона за счет нескольких других неравномерных и очень грубых мелкопористых частиц.Следовательно, это улучшило трение между частицами, которое препятствует течению свежего бетона. При постоянном соотношении раствора и вяжущего удобоукладываемость бетонов снижалась с увеличением количества опилок вместо речного песка и гравийного щебня. Несколько исследователей [45, 46, 47] получили аналогичные тенденции результатов для снижения удобоукладываемости бетона, содержащего легкие заполнители. Ограничения, связанные со снижением удобоукладываемости бетонных смесей из-за использования древесных опилок в качестве заменителя природного песка, могут быть преодолены применением суперпластификатора.
Показатели осадки приготовленных щелочеактивированных бетонов.
Как начальное, так и окончательное время схватывания бетонов, изготовленных с использованием различных количеств отходов опилок в качестве мелких и крупных заполнителей, представлены в . Очевидно, что как начальное, так и окончательное время схватывания уменьшались с увеличением содержания опилок в бетоне. Для начального времени схватывания показания уменьшались с 39 до 37, 34, 31 и 28 мин соответственно при увеличении содержания опилок от 0 до 25, 50, 75 и 100 %.Аналогичная тенденция была обнаружена с окончательным временем схватывания и показаниями, которые были увеличены с 61 до 56, 53, 48 и 46 мин. Однако разница во времени начального и конечного схватывания для каждой смеси уменьшалась с увеличением содержания опилок. Кроме того, разница во времени схватывания каждой смеси невелика. Сокращение времени схватывания при увеличении содержания опилок было связано с высокой водопотребностью опилок, что повлияло на процесс геополимеризации и растворение алюмосиликатов и кальция. Наблюдалась обратная зависимость между содержанием отходов опилок и временем схватывания приготовленного бетона. Высокая абсорбция опилок щелочным раствором придает смеси высокую вязкость, которая быстро затвердевает. В то же время включение опилок в бетонные смеси со сравнительно более высоким водопоглощением, чем речной песок и гравий, ускоряло твердение щелочноактивированных смесей и сокращало сроки схватывания за счет поглощения дополнительной воды опилками.Наоборот, включение опилок в щелочную систему приводило к снижению рН из-за разложения лигнина, опосредованного изменением рН в пористом растворе. Настоящие результаты аналогичны выводам Duan et al. [48], где как начальное, так и окончательное время схватывания были сокращены для бетонов, изготовленных с использованием опилок.
Влияние содержания опилок на начальное и конечное время схватывания бетона.
4.2. Плотность затвердевания и скорость ультразвукового импульса
отображает значения плотности затвердевшего бетона, содержащего отходы опилок в качестве замены речного песка и гравийного щебня в возрасте отверждения 28 дней. Плотность приготовленных бетонов снижалась с 2,28 до 1,98, 1,63, 1,24 и 0,89 т·м -3 при увеличении содержания опилок от 0 до 25, 50, 75 и 100 % соответственно. Наименьшую плотность имела смесь, содержащая 100 % опилок (0,89 т·м -3 ). Кроме того, низкий удельный вес и пористость опилок существенно повлияли на плотность приготовленных бетонов. Настоящий результат согласуется с результатом, полученным Memon et al.[49] для бетона, включающего большое количество опилок в качестве крупного заполнителя. Кроме того, эти результаты способствовали улучшению и разработке высокоэффективного легкого бетона, активированного щелочью, что было подтверждено результатами, представленными Sales et al. [50]. Они оценили возможное использование легких бетонов, изготовленных из крупных заполнителей, путем обработки воды шламом и опилками.
Плотность готовых бетонов с различным содержанием опилок.
показывает влияние различных количеств опилок на значения скорости ультразвукового импульса (UPV) приготовленных бетонов. Увеличение содержания опилок от 0 до 25, 50, 75 и 100 % вызывало снижение соответствующих показателей УПВ бетонов с 3,42 до 3,02, 2,79, 2,57 и 2,32 км/с в 28-суточном возрасте твердения. Это падение произошло из-за пористой природы опилок, что отрицательно повлияло на плотность и микроструктуру приготовленного бетона. Видно, что с увеличением содержания опилок и уменьшением количества речного песка/щебня УПВ приготовленных бетонов снижалось, что объяснялось увеличением опилко-опосредованной пористости.Настоящие результаты хорошо согласуются с результатами предыдущего исследования [47].
Показатели УПВ приготовленных бетонов с различным содержанием опилок в возрасте 28 дней.
4.3. Прочность на сжатие (CS)
показывает значения CS бетонов, содержащих различные количества опилок вместо песчаных и гравийных заполнителей. Для каждой смеси исследовали три образца и принимали среднее значение. КС приготовленного бетона измеряли в возрасте твердения 1, 3, 7, 28, 56 и 90 дней. КС постоянно увеличивался с увеличением возраста отверждения. В раннем возрасте (через 24 ч) при повышении уровня замены речного песка и гравия опилками от 0 до 25, 50, 75 и 100 % ранняя прочность снижалась с 22,6 до 19,4, 18,3, 17,8. и 15,2 МПа соответственно. После 28-дневного возраста наблюдалось сопоставимое развитие, при котором КС снижался с 65,8 до 61,1, 55,7, 50,4 и 48,6 МПа при увеличении содержания опилок с 0 до 25, 50, 75 и 100% соответственно.Аналогичное поведение обнаружено в позднем возрасте 90 дней. где процент потери прочности увеличивался с увеличением содержания опилок в бетонной матрице. Было обнаружено, что бетон достиг более 96% прочности на сжатие через 28 дней от общей прочности, измеренной через 90 дней для всех смесей, и этот вывод согласуется с предыдущим выводом Ранджбара [22] и Ислама [51]. Однако было обнаружено, что потеря прочности со временем уменьшалась, а процент потери при использовании 100% опилок снизился с 32.7% в раннем возрасте (1 день) до 26,1% в возрасте 28 дней и старше.
Следовательно, общее снижение КС при увеличении содержания опилок было вызвано тремя причинами. Первая причина заключалась в том, что отработанные опилки проявляли более высокую водопоглощающую способность, чем речной песок и гравийный щебень. Тем не менее, различное распределение воды, смешивающейся с матрицей бетона, может ослабить химические связи в пасте, активированной щелочью (ГБФС + ФА) и заполнителях. Вторая причина заключалась в том, что форма частиц опилок по сравнению с формой натуральных заполнителей ослабляла связь между пастой и заполнителем и, таким образом, происходило снижение CS бетона.Третья причина заключалась в том, что наличие органического вещества привело к уменьшению связей между заполнителем и пастой и увеличило пористость, тем самым влияя на CS бетона. Четвертая причина заключалась в том, что замена более сильного вещества на более слабое и отсутствие пуццоланового действия у отходов опилок также отрицательно сказывались на наборе прочности. Этот вывод согласуется с предыдущими отчетами Kanojia и Jain, S.
[52], Martínez-García et al. [53] и Gonzalez-Fonteboa et al.[54].
Результаты определения прочности на сжатие приготовленного бетона при различном содержании опилок.
4.4. Прочность на изгиб и растяжение
Прочность на изгиб (FS) LWC была измерена для оценки их способности сопротивляться деформации при воздействии нагрузки. Испытания щелочеактивированных бетонов, приготовленных с разным содержанием опилок в качестве заменителя речного песка/гравийного заполнителя, проводили после выдержки в течение 28 сут. Для каждой смеси были оценены средние значения трех образцов, как показано на рис.ФС приготовленных образцов резко меняется с изменением уровня замещения природных заполнителей опилками. Оно снижается примерно с 6,8 МПа при содержании 0 % до 6,2, 5,7, 5,1 и 4,9 МПа при увеличении содержания опилок до 25, 50, 75 и 100 % соответственно. Что касается мелких и крупных заполнителей на основе опилок в легком бетоне, активированном щелочью, то 100-процентное добавление опилок оказывает наибольшее влияние на значение FS, а образец бетона теряет более 27 % прочности на изгиб при повышении уровня опилок от от 0 до 100%. Тем не менее, FS для всех смесей достигла приемлемой прочности для применения в строительстве.
ФС приготовленных ЛОК, содержащих различное количество опилок. В №
представлены показатели предела прочности при раскалывании (STS) ЛОК, полученных с различным содержанием опилок вместо мелкого/крупного заполнителя. Среднее значение трех цилиндров бетона, проведенное при оценке включения опилок в бетонную матрицу. Для всех смесей прочность на растяжение при раскалывании оценивали в возрасте отверждения 28 дней.Установлено, что потери в ПТР увеличиваются с увеличением содержания опилок, а значение прочности снижается с 4,2 до 3,9, 3,7, 3,4 и 3,0 МПа при увеличении содержания опилок от 0 до 25, 50, 75 МПа. и 100% соответственно. Аналогично причинам, связанным с потерей прочности (раздел 3.3), абсорбция отходов, форма частиц и содержание органических веществ в опилках привели к слабой связи между пастой и опилками как заполнителем и показали более низкую прочность на изгиб и растяжение при раскалывании. по сравнению с контрольным образцом, приготовленным с натуральными заполнителями (0% опилок) [6].
СТС ЛОК на содержание опилок.
4.5. Анализ XRD
показывает результаты XRD приготовленного бетона, содержащего различные уровни опилок, а также мелкие/крупные заполнители в качестве заменителя. Пики, соответствующие кристаллическому кварцу (SiO 2 ), гидроксиду кальция (Ca(OH) 2 ) и муллиту (3Al 2 O 3 ·2SiO 2 или 2Al 3 · 3 O Видны фазы SiO 2 ). Эти фазы появились из FA и GBFS.Интенсивность дифракционного пика Ca(OH) 2 уменьшалась с увеличением количества опилок от 0 до 25, 50, 75 и 100 %, где образовывалось меньше портландцемента, а также появлялось большее количество кварца. быть нереактивным с 75 и 100% опилок (). Они были получены в результате химической реакции между аморфными фракциями FA/GBFS, содержащими незначительные кристаллические фазы. Пики РСА OPC, CaCO 3 и муллита проявляются при 28–50°. По мере увеличения содержания опилок интенсивность пика XRD составляла 50.1°, соответствующий фазе кристаллического кварца, увеличился. Пик муллита при 16° для 25% опилок также показал более низкую интенсивность пика, чем контрольный образец. Кроме того, интенсивность этих пиков имеет тенденцию к снижению с увеличением содержания опилок. Пики, наблюдаемые при 24° и 33,8°, были отнесены к нефелину (Na 3 KAl 4 Si 4 O 16 ), где интенсивность пика уменьшалась с увеличением уровня опилок.
Рентгенофазовый анализ приготовленного бетона с различным содержанием опилок.
Таблица 5
Указатель | 9029 | 0% | 25% | 9515 50% | 75% | 100% | | ||||
---|---|---|---|---|---|---|---|---|---|---|---|
кварц, SIO 2 | 52.![]() | 52.1 | 54.8 | 60.2 | 78.4 | 78.4 | 81.8 | 81.8 | |||
Портленд, CA (OH) 2 | 43.1 | 41.3 | 41.3 | 36.4 | 18.8 | 14.![]() | |||||
Calcite, CACO | |||||||||||
2 | 2.2 | 1,5 | 1,3 | 1.1 | 1.2 | ||||||
Другие | 2.6 | 2.4 | 2,1 | 1,8 | 2,1 |
Вкратце, рентгеноструктурный анализ приготовленных LWC выявил влияние Si, Al и Ca на полученные гели C-(A)-SH и CS. Результаты XRD () ясно показали, что количество портландцемента имело тенденцию к снижению с увеличением уровня опилок, где значения упали с 43.1 до 41,3, 36,4, 18,8 и 14,9 % при увеличении содержания опилок от 0 до 25, 50, 75 и 100 % соответственно. Аналогичная тенденция была обнаружена с пиком кальцита, и все бетонные смеси, содержащие опилки, показывают меньшее количество кальцита (1,5–1,1 %) по сравнению с контрольным образцом (2,2 %). Хорошо известно, что количество ФОС в бетонной матрице играет значительную роль в производстве геля CSH, где снижение уровня ФОС и кальцита может привести к ослаблению связей в бетонной матрице, тем самым проявляя более низкие значения прочности с увеличение содержания опилок.Между тем, высокая абсорбция и водопотребность опилок напрямую повлияла на геополимеризацию и растворила силикат, а показала более низкую прочность [54].
4.6. Расчетная прочность на сжатие предлагаемого бетона
Программное обеспечение ATLAB использовалось для разработки предложенной модели ИНС. В частности, в процессе итерации было обнаружено, что наилучшее число нейронов в скрытых слоях равно четырнадцати. Этот результат привел к достижению целевой производительности 0,01 по отношению к скорости обучения 0.2. Измеренные данные были разделены на три части, а именно: обучение, тестирование и проверка. Было принято во внимание обучение ИНС с 124 тестами, в то время как 14 и 23 теста использовались для этапов проверки и тестирования, рецептивно. Обучение ИНС продолжалось до тех пор, пока оно не минимизировало значение корреляции, при котором было достигнуто значение корреляции 0,991, как показано на рис. Принимая во внимание, что значение корреляции результатов тестирования составляет 0,9878 (б). Кроме того, средняя ошибка учитывалась для оценки эффективности сети на этапах обучения и тестирования.В частности, средняя ошибка (M) для обучающих данных составила 1,377, как показано на рис. Значения этих показателей хорошо предсказывали экспериментальные данные, где предсказанная CS была чрезвычайно близка к измеренной.
Предсказанная и измеренная корреляция CS предложенных LWC для ( a ) обучающих данных и ( b ) тестовых данных.
Таблица 6
Сравнение экспериментальных данных для тестового набора и прогнозируемых результатов модели ANN.
№ эксперимента | Время (день) | GBFS / FA | Решение / Binder | Молярность (M) | NS / NH | Фактический (MPA) | Прогнозируется (MPA) | Ошибка | Абсолютная ошибка | |||
---|---|---|---|---|---|---|---|---|---|---|---|---|
1 | 1 | 30 | 40 | 2 | 0,75 | 22.![]() | 21.87 | -0.73 | 0,73 | |||
2 | 3 | 30 | 40 | 2 | 0.75 | 26.70 | 26.70 | 27.61 | 0,91 | 0,91 | ||
9 | 99 | 99 | 90,75 | 39.![]() | 38.83 | -0.97 | 0,97 | |||||
4 | 29 | 28 | 30 | 40 | 2 | 65.80 | 65.87 | 61.87 | 61.93 | — 3,93 | 393 | |
5 | 56 | 30 | 40 | 2 | 0.![]() | 67.40 | 64.90 | -2.50 | — 2,50 | 9 | ||
6 | ||||||||||||
6 | 9 9 92 | 0,75 | 68.90 | 65.75 | -3.15 | 3.15 | ||||||
7 | 40 | 40 | 2 | 0,75 | 73.![]() | 72.82 | -0.78 | 0.78 | ||||
8 | 8 | 90 | 60 | 40 | 2 | 0 .75 | 85.60 | 85.60 | 87.00 | 1.![]() | 1.40 | |
9 | ||||||||||||
9 | 9 | 9 90,75 | 89.70 | 89.38 | -0.32 | 0.32 | ||||||
10 | 90 | 90 | 20 | 40 | 2 | 0.![]() | 56.40 | 56.55 | 0,15 | 0.15 | ||
11 | 11 | 30207 30 | 30 | 2 | 0.75 | 37.60 | 32.76 | — 4.![]() | 4,84 | |||
12 | 12 | 99 | 30 9 | 9 | 2 | 0.75 | 56.10 | 55.78 | -0.32 | 0.32 | ||
13 | 30 | 45 | 2 | 9 | 0,75 | 60.![]() | 61.85 | 1.75 | ||||
14 | ||||||||||||
14 | 30 | 50 | 2 | 0.75 | 56.20210 | 56.20 | 55.02 | —1.18 | 118 | |||
15 | ||||||||||||
9 | 99 | 9 0.![]() | 74.207 | 74.26 | 0,06 | 0,06 | ||||||
16 | 90 9 | 90 | 30 | 40 | 4 | 0,75 | 71.40 | 71.40 | 66.26 | -59 9 | 5.![]() | |
17 | 17 | 9 30 | 40 | 2.5 | 0.75 | 69.30 | 70.86 | 70.86 | 1.56 | |||
18 | 9 | 9 | 1,5 | 1.![]() | 0.75 | 58.209 | 57.22 | -0.98 | 0,98 | |||
19 | 9 | 40 | 2 | 2 | 29 | 85.86 | 86.86 | 86.![]() | 1.26 | 1,26 | ||
20 | 9 | 940 | 2 | 2 | 76.90 | 76.08 | -0.82 | -0.82 | 0.82 | |||
30 | 40 | 91,5 | 71.![]() | 72.61 | 1,51 | 1,51 | ||||||
22 | ||||||||||||
22 | ||||||||||||
22 | ||||||||||||
22 | 90 | 30 | 40 | 2 | 1 | 70.10 | 71.![]() | 71.18 | 1.08 | 1,08 | ||
23 | ||||||||||||
23 | 7 30 | 40 | 2 | 0.75 | 51.60 | 51.88 | 51.88 | 0.28 | 0.![]() | |||
Среднее | 1.37 |
сравнивает экспериментальные и прогнозируемые результаты против MOLARITION, GBFS к коэффициенту FA, NS / Отношение NH, отношение раствора к связующему и время. Модель ANN могла реалистично предсказать фактическую CS активированного щелочью бетона. Этот результат доказал, что результаты модели ИНС согласуются с экспериментальными результатами.Кроме того, был сделан вывод о влиянии каждого параметра на КС бетона. Например, хорошо видна зависимость степени повышения прочности бетона, активированного щелочью, от повышения концентрации мочевины. Как экспериментальные, так и предсказанные результаты показывают высокую степень сходства. Повышение прочности бетона постепенно увеличивается с увеличением молярности. Однако за пределами значения молярности 2 наблюдается незначительное повышение прочности бетона по сравнению с эффектом затрат.Как таковой. молярность 2 была сохранена и принята за 2 для дальнейших работ. Точно так же с увеличением отношения NS/NH прочность улучшалась, как показано на рис. b. В то же время вклад концентрации летучей золы в повышение прочности бетона был незначительным, как показано в c. Напротив, с увеличением отношения GBFS к FA CS LWC улучшалась. Оптимальное улучшение прочности было достигнуто при соотношении NS/NH 70/30. Аналогичным образом оптимальное значение отношения раствора к связующему было равно 0.4 (г).
Прогнозируемое и фактическое изменение прочности, активированной щелочью, в зависимости от ( a ) молярности, ( b ) NS/NH, ( c ) FA/GBFS, ( d ) и отношения раствора к связующему .
4.7. Водопоглощение (WA)
показывает влияние отходов опилок на WA способность активируемых щелочью бетонных смесей при возрасте отверждения 28 дней. WA образцов повышалась по мере увеличения содержания опилок в бетонной матрице.Увеличение содержания опилок от 0 до 25, 50, 75 и 100 % в качестве заменителя природных заполнителей может улучшить WA на 9,7, 10,1, 13,4, 15,2 и 16,9 % соответственно. На каждом уровне замены опилок на результат WA в значительной степени влияло соотношение опилок и речного песка/гравийного щебня. При содержании опилок 25 % водопоглощение увеличивалось на 4,1 %, и это соотношение увеличивалось с увеличением замены опилок и составляло более 74 % при содержании опилок 100 %. Как обсуждалось в разделе 3.3, с увеличением содержания опилок потребность в воде увеличивалась, что приводило к увеличению количества непрореагировавшего кремнезема и структурной пористости. Бетоны, содержащие большее количество опилок, показали улучшенную WA, что было связано с образованием геля в связующей матрице. Ахмед и др. [6] связывают высокую WA бетона, содержащего отвальные опилки, с его пористостью и наличием сплошных каналов. Другой причиной такой повышенной способности WA может быть, прежде всего, наличие большого количества свободной воды, которая образовывала капилляры в бетонах, изготовленных из зольного остатка, как показано Andrade et al.
[55].
Водопоглощение готового бетона при различном содержании опилок.
4.8. Усадка при высыхании (DS)
иллюстрирует изменение в зависимости от времени испытаний значений DS для активированного щелочью бетона, приготовленного с использованием различного количества опилок вместо натуральных заполнителей. Показания DS были сняты через 3, 7, 14, 21, 28, 56 и 90 дней, и было обнаружено, что значение DS для всех образцов улучшилось с увеличением возраста отверждения. Включение отходов опилок в активированные щелочью бетоны действительно может повысить значения DS, особенно в раннем возрасте.Кроме того, значения DS снижались с увеличением уровня опилок, что было связано со спецификой микроструктуры опилок. Для всех приготовленных бетонных смесей наблюдалось уменьшение прироста усадки при высыхании со временем; после 7-дневного возраста отверждения было зафиксировано более чем 40-процентное увеличение показаний усадки при высыхании по сравнению с результатами через 3 дня. Однако этот процент со временем снижался, и менее 6% и 2% были зарегистрированы через 28 и 90 дней соответственно.В раннем 3-дневном возрасте добавление опилок в качестве заменителя природного заполнителя способствовало снижению усадки при сушке на 2,1, 3,7, 6,2 и 7,1 % при 25, 50, 75 и 100 % соответственно. Сопоставимая тенденция была обнаружена после возраста отверждения 28 дней, а включение опилок показало большую эффективность в снижении величины усадки на 3,5, 4,8, 7,1 и 7,6% соответственно на 25, 50, 75 и 100% по сравнению с контрольный образец. Наблюдаемое снижение DS опилок было приписано эффекту внутреннего отверждения опилок, обеспечивающего некоторую дополнительную влажность и, таким образом, улучшение реакции DS полученных смесей [56].Собственно опилочные каналы играли жизненно важную роль, удерживая воду внутри активируемой раствором щелочи матрицы, что, в свою очередь, обеспечивало компенсацию необходимой влажности бетонной матрицы, что впоследствии приводило к деформации ДС.
Сопоставимые результаты были получены Juarez et al. [57] и Тонг и соавт. [58] на фиброцементных системах.
Усадка при высыхании приготовленного бетона с различным содержанием опилок.
4.9. Звукопоглощение
Коэффициенты звукопоглощения характеризуют способность материалов поглощать звуковую энергию.показано влияние содержания опилок на измеренное звукопоглощение предлагаемого бетона. Все образцы были испытаны при частоте от 0 до 5000 Гц. В целом испытанные образцы показали лучшие характеристики при частоте в диапазоне от 500 до 3000 Гц и, как правило, поглощали большее количество звуковой энергии. Акустические свойства предлагаемых бетонов были улучшены за счет включения опилок. Коэффициенты звукопоглощения имеют тенденцию к увеличению от 0.43 до 0,74 при увеличении степени замещения опилок от 0 до 100 % соответственно. иллюстрирует коэффициент шумоподавления ЛОК, приготовленных с разным количеством древесных опилок в качестве замены природного заполнителя. Результаты показали, что повышение степени замещения опилок от 0% до 100% привело к улучшению акустических свойств бетона и увеличению коэффициента шумоподавления с 0,124 до 0,237 соответственно (). Несколько факторов ответственны за улучшенные характеристики звукопоглощения.Увеличение количества отходов опилок создавало больше взаимосвязанных пустот различной длины в матрице бетона, активированного щелочью, и, таким образом, повышало коэффициенты снижения шума [59,60,61,62]. Эти пористые материалы показали улучшенное звукопоглощение в области высоких частот, что указывает на сдвиг частоты звукопоглощения в сторону более высоких значений с увеличением содержания опилок в бетоне. Наблюдаемое снижение плотности бетона привело к смещению частоты в сторону более высоких значений.Фактически, опилки, будучи высокопористым веществом, могут повышать пористость паст, активированных щелочью, при включении в бетонную матрицу. Повышение коэффициента шумоподавления при добавлении заполнителя из опилок было связано с увеличением содержания воздуха и пористости в бетоне, приготовленном с более высокими концентрациями заполнителя из опилок. В предыдущих исследованиях [62,63] было установлено, что звукопоглощение сильно влияет на пористость и плотность материалов, а коэффициент шумоподавления имеет тенденцию к увеличению с уменьшением плотности материалов.
Поглощение звука пористыми материалами обусловлено потерями энергии на трение, возникающее в стенках пористых структур [64]. Следовательно, образец бетона с долей пустот в целом показал более высокие значения коэффициентов звукопоглощения во всей области частот [65].
Коэффициенты звукопоглощения бетонов, приготовленных с различным содержанием опилок.
Влияние содержания опилок на коэффициент шумоподавления предлагаемых щелочеактивированных бетонов.
Таблица 7
Влияние содержания опилок на коэффициент шумоподавления (NRC).
Частота (HZ) | 0% | 25% | 50% | 75% | ||
---|---|---|---|---|---|---|
250 | ||||||
250 | ||||||
250 | 0.![]() | 0,046065998 | 0.03238883 | 0,082436911 | ||
500 | 0,050464286 | 0,0724 | 0.060480702 | 0,047957295 | 0,038381466 | |
1000 | 0,105207679 | 0,241543934 | 0,159514703 | 0,3205 | 0,156701336 | |
2000 | 0,301440476 | 0,176171063 | 0,308779167 | 0,20956316 | 0,673137931 | |
NRC | 0,124300018 | 0,136010021 | 0,143710142 | 0,152703808 | 0.![]() |
4.10. Теплопроводность
Как правило, LWC, активированные щелочью, используются для перегородок зданий. Таким образом, важно оценить их тепловые характеристики при применении в наружных стенах. Два метода были использованы для оценки тепловых свойств предлагаемых бетонов. Во-первых, влияние включения опилок на теплопроводность бетона было измерено путем расчета времени теплопередачи в возрасте 28 дней твердения ().Результаты испытаний теплопроводности контрольного и опилкобетона показали снижение с увеличением содержания опилок в качестве частичной замены мелкого/крупного заполнителя. Образец, приготовленный с наибольшим содержанием опилок (100 %), показал максимальное время теплопередачи (188 мин) по сравнению с контрольным образцом (0 % опилок), которое составило всего 36 мин, в то время как остальные три смеси, содержащие 25, 50 и 75% опилок продемонстрировали увеличение времени теплопередачи на 61, 108 и 149 минут соответственно.Во-вторых, полученные значения коэффициента теплопроводности использовались для оценки тепловых характеристик предлагаемого легкого бетона. Представленные результаты показывают, что увеличение содержания опилок в качестве замены природного заполнителя привело к улучшению тепловых свойств предлагаемого бетона. Для всех испытанных образцов значение коэффициента теплопроводности имеет тенденцию к снижению с увеличением содержания опилок. Было обнаружено, что значение коэффициента теплопроводности k снизилось с 0.39 до 0,24, 0,19, 0,13 и 0,09 Вт/м.К с повышением степени замещения от 0 до 25, 50, 75 и 100% соответственно. В исследовании Liu et al. [65] сообщалось, что улучшение термических свойств имело тенденцию к увеличению с увеличением пористости образцов и уменьшением плотности. Это свидетельствовало о том, что включение отходов опилок привело к снижению плотности предлагаемого бетона, а также к увеличению общей пористости, что привело к снижению теплопроводности.Из-за своего легкого веса и пористости опилки с низкой плотностью могут снижать теплопроводность рецептурных бетонов. Было признано [66], что это снижение теплопроводности может быть связано с процессом конвекции, в котором существенную роль играют плотность, распределение и геометрия пор в бетонной матрице.
показана корреляция теплопроводности и плотности всех приготовленных бетонов с полученным коэффициентом корреляции 0,9048. Известно, что бетоны с легкими заполнителями обнаруживают тенденцию к снижению плотности, что приводит к большей пористости и, следовательно, к снижению теплопроводности [67,68].
Теплопроводность приготовленного бетона при различном содержании опилок.
Коэффициенты теплопроводности готовых бетонов при различном содержании опилок.
Зависимость между временем теплопередачи и плотностью приготовленного бетона.
4.11. Экологические и экономические выгоды
Общий выброс CO 2 , стоимость и использование энергии природных заполнителей, включая речной песок, дробленый гравий, мелкие и крупные опилки, были рассчитаны для определения жизненного цикла каждого материала (в разделе 3 .7). Результаты показали, что речной песок и дробленый гравий требуют большего количества дизельного топлива во время синтеза, чем опилки, что приводит к увеличению выбросов CO 2 , стоимости и энергопотребления. Природные заполнители потребляли большее количество энергии в диапазоне 0,134–0,148 ГДж/м 3 по сравнению с мелкими (0,018 ГДж/м 3 ) и крупными (0,021 ГДж/м 3 ) опилками. Это показало прямую пропорциональность расходу энергии, выбросу СО 2 и увеличению расхода природных агрегатов.Он выявил более высокое выделение углекислого газа (0,012 т/м 3 ), чем опилки (0,0008 т/т). Как и в выпуске CO 2 , затраты на речной песок и гравийный щебень были самыми высокими из опилок. Это произошло в основном из-за этапов сбора и подготовки, таких как дробление и просеивание, а также из-за более длительного расстояния транспортировки. Это, в свою очередь, повысило стоимость речного песка и гравийного щебня до 55 и 65 ринггитов/м 3 по сравнению с соответствующей стоимостью мелких и крупных опилок 34.5 и 36 РМ/м 3 . Было показано, что замена натуральных заполнителей легкими мелкими и крупными опилками в активируемой щелочью матрице необходима для достижения условий устойчивости, таких как более низкие выбросы CO 2 , затраты и использование энергии.
отображает выбросы углекислого газа из готовых бетонов в зависимости от содержания опилок. Исследовано влияние замены речного песка и дробленых заполнителей опилками на выход СО 2 легких щелочных бетонов, активированных раствором.Выброс СО 2 снижался с 10,9 до 8,3, 5,8, 3,3 и 0,8 кг/м 3 при увеличении содержания опилок от 0 до 25, 50, 75 и 100 % соответственно. Активированная щелочным раствором бетонная матрица, содержащая 100% опилок (1 кг/м 3 ), может снизить выделение CO 2 на 90% по сравнению с 10,9 кг/м 3 для натуральных заполнителей. Это снижение выделения CO 2 из активированных щелочным раствором бетонов, содержащих опилки в качестве альтернативы природным заполнителям, подтвердило возможность простого устойчивого развития в строительном секторе.
Влияние содержания опилок на выброс углекислого газа из готового бетонного заполнителя.
показывает влияние опилок, заменяющих речной песок и гравийный щебень, на совокупный расчет себестоимости готового бетона. Использование опилок на высоком уровне (100%) вместо песка и гравия также позволило сэкономить деньги. Цена материала по массе зависела от жизненного цикла (), что оказывало прямое влияние на конечную цену бетонных смесей из заполнителей. Кроме того, стоимость агрегатов была снижена с 62.3 до 55,8, 49,4, 42,9 и 36,6 РМ/м 3 с увеличением содержания опилок взамен природных заполнителей от 0 до 25, 50, 75 и 100 % соответственно. Было показано, что при использовании опилок в качестве альтернативы речному песку и гравийному щебню можно получить устойчивый бетон.
Влияние содержания опилок на стоимость готового бетонного заполнителя.
отображает энергопотребление приготовленного бетона в зависимости от содержания опилок. В зависимости от жизненного цикла и использования энергии каждого вещества был оценен общий расход энергии каждого бетона, активированного раствором щелочи.Энергоемкость произведенных бетонов была снижена за счет добавления опилок вместо речного песка/гравийной крошки. По сравнению с потреблением энергии для бетона 0,15 ГДж/м 3 с содержанием опилок 0 % значения были снижены до 0,11, 0,08, 0,05 и 0,022 ГДж/м 3 для смесей, изготовленных с содержанием опилок 25. , 50, 75 и 100% соответственно. Однако все смеси, активированные щелочным раствором, с максимальным количеством опилок (100 %) требовали гораздо меньше энергии, чем смеси, приготовленные с использованием природных заполнителей (0,000 %).15 ГДж/м 3 ). Низкое использование дизельного топлива в течение жизненного цикла опилок может напрямую влиять на конечное энергопотребление предлагаемых бетонов. Низкая цена, выброс CO 2 и использование энергии образующимися отходами опилок были основными факторами, которые позволили достичь желаемой устойчивости заполнителей, активированных щелочным раствором.
Энергоемкость бетонов, приготовленных при различном содержании опилок.
Gale Apps — Технические трудности
Технические трудности
Приложение, к которому вы пытаетесь получить доступ, в настоящее время недоступно. Приносим свои извинения за доставленные неудобства. Повторите попытку через несколько секунд.
Если проблемы с доступом сохраняются, обратитесь за помощью в наш отдел технической поддержки по телефону 1-800-877-4253. Еще раз спасибо, что выбрали Gale, обучающую компанию Cengage.
org.springframework.remoting.RemoteAccessException: невозможно получить доступ к удаленной службе [authorizationService@theBLISAuthorizationService]; вложенным исключением является Ice.Неизвестное исключение
unknown = «java.lang.IndexOutOfBoundsException: индекс 0 выходит за границы для длины 0
в java.base/jdk.internal.util.Preconditions.outOfBounds(Preconditions.java:64)
в java.base/jdk.internal.util.Preconditions.outOfBoundsCheckIndex(Preconditions.java:70)
в java.base/jdk.internal.util.Preconditions.checkIndex(Preconditions. java:248)
в java.base/java.util.Objects.checkIndex(Objects.java:372)
на Яве.база/java.util.ArrayList.get(ArrayList.java:458)
в com.gale.blis.data.subscription.dao.LazyUserSessionDataLoaderStoredProcedure.populateSessionProperties(LazyUserSessionDataLoaderStoredProcedure.java:60)
в com.gale.blis.data.subscription.dao.LazyUserSessionDataLoaderStoredProcedure.reQuery(LazyUserSessionDataLoaderStoredProcedure.java:53)
в com.gale.blis.data.model.session.UserGroupEntitlementsManager.reinitializeUserGroupEntitlements(UserGroupEntitlementsManager.ява:30)
в com.gale.blis.data.model.session.UserGroupSessionManager.getUserGroupEntitlements(UserGroupSessionManager.java:17)
в com.gale.blis.api.authorize.contentmodulefetchers.CrossSearchProductContentModuleFetcher.getProductSubscriptionCriteria(CrossSearchProductContentModuleFetcher.java:244)
на com.gale.blis.api.authorize.contentmodulefetchers.
CrossSearchProductContentModuleFetcher.getSubscribedCrossSearchProductsForUser(CrossSearchProductContentModuleFetcher.ява:71)
на com.gale.blis.api.authorize.contentmodulefetchers.CrossSearchProductContentModuleFetcher.getAvailableContentModulesForProduct(CrossSearchProductContentModuleFetcher.java:52)
на com.gale.blis.api.authorize.strategy.productentry.strategy.AbstractProductEntryAuthorizer.getContentModules(AbstractProductEntryAuthorizer.java:130)
на com.gale.blis.api.authorize.strategy.productentry.strategy.CrossSearchProductEntryAuthorizer.isAuthorized(CrossSearchProductEntryAuthorizer.ява:82)
на com.gale.blis.api.authorize.strategy.productentry.strategy.CrossSearchProductEntryAuthorizer.authorizeProductEntry(CrossSearchProductEntryAuthorizer.java:44)
на com.gale.blis.api.authorize.strategy.ProductEntryAuthorizer.authorize(ProductEntryAuthorizer.java:31)
в com.gale.blis.api.BLISAuthorizationServiceImpl.
authorize_aroundBody0(BLISAuthorizationServiceImpl.java:57)
на com.gale.blis.api.BLISAuthorizationServiceImpl.authorize_aroundBody1$advice(BLISAuthorizationServiceImpl.ява: 61)
на com.gale.blis.api.BLISAuthorizationServiceImpl.authorize(BLISAuthorizationServiceImpl.java:1)
на com.gale.blis.auth._AuthorizationServiceDisp._iceD_authorize(_AuthorizationServiceDisp.java:141)
в com.gale.blis.auth._AuthorizationServiceDisp._iceDispatch(_AuthorizationServiceDisp.java:359)
в IceInternal.Incoming.invoke(Incoming.java:209)
в Ice.ConnectionI.invokeAll(ConnectionI.java:2800)
на льду.ConnectionI.dispatch(ConnectionI.java:1385)
в Ice.ConnectionI.message(ConnectionI.java:1296)
в IceInternal.ThreadPool.run(ThreadPool.java:396)
в IceInternal.ThreadPool.access$500(ThreadPool.java:7)
в IceInternal.ThreadPool$EventHandlerThread.run(ThreadPool.java:765)
в java.
base/java.lang.Thread.run(Thread.java:834)
»
org.springframework.remoting.ice.IceClientInterceptor.convertIceAccessException(IceClientInterceptor.java:365) org.springframework.remoting.ice.IceClientInterceptor.invoke(IceClientInterceptor.java:327) org.springframework.remoting.ice.MonitoringIceProxyFactoryBean.invoke(MonitoringIceProxyFactoryBean.java:71) org.springframework.aop.framework.ReflectiveMethodInvocation.proceed(ReflectiveMethodInvocation.java:186) org.springframework.aop.framework.JdkDynamicAopProxy.invoke(JdkDynamicAopProxy.java:212) com.sun.proxy.$Proxy130.authorize(Неизвестный источник) com.gale.auth.service.BlisService.getAuthorizationResponse(BlisService.java:61) com.gale.apps.service.impl.MetadataResolverService.resolveMetadata(MetadataResolverService.java:65) com.gale.apps.controllers.DiscoveryController.resolveDocument(DiscoveryController.java:57) ком.gale.apps.controllers.DocumentController.redirectToDocument(DocumentController.
java:22) jdk.internal.reflect.GeneratedMethodAccessor301.invoke (неизвестный источник) java.base/jdk.internal.reflect.DelegatingMethodAccessorImpl.invoke(DelegatingMethodAccessorImpl.java:43) java.base/java.lang.reflect.Method.invoke(Method.java:566) org.springframework.web.method.support.InvocableHandlerMethod.doInvoke(InvocableHandlerMethod.ява: 215) org.springframework.web.method.support.InvocableHandlerMethod.invokeForRequest(InvocableHandlerMethod.java:142) org.springframework.web.servlet.mvc.method.annotation.ServletInvocableHandlerMethod.invokeAndHandle(ServletInvocableHandlerMethod.java:102) org.springframework.web.servlet.mvc.method.annotation.RequestMappingHandlerAdapter.invokeHandlerMethod (RequestMappingHandlerAdapter.java:895) org.springframework.web.servlet.mvc.method.annotation.RequestMappingHandlerAdapter.handleInternal (RequestMappingHandlerAdapter.java:800) org.springframework.web.servlet.mvc.method.AbstractHandlerMethodAdapter.handle(AbstractHandlerMethodAdapter.
java:87) org.springframework.web.servlet.DispatcherServlet.doDispatch(DispatcherServlet.java:1038) org.springframework.web.servlet.DispatcherServlet.doService(DispatcherServlet.java:942) орг.springframework.web.servlet.FrameworkServlet.processRequest(FrameworkServlet.java:998) org.springframework.web.servlet.FrameworkServlet.doGet(FrameworkServlet.java:890) javax.servlet.http.HttpServlet.service(HttpServlet.java:626) org.springframework.web.servlet.FrameworkServlet.service(FrameworkServlet.java:875) javax.servlet.http.HttpServlet.service(HttpServlet.java:733) орг.apache.catalina.core.ApplicationFilterChain.internalDoFilter(ApplicationFilterChain.java:227) org.apache.catalina.core.ApplicationFilterChain.doFilter(ApplicationFilterChain.java:162) org.apache.tomcat.websocket.server.WsFilter.doFilter(WsFilter.java:53) org.apache.catalina.core.ApplicationFilterChain.internalDoFilter(ApplicationFilterChain.java:189) org.apache.catalina.core.ApplicationFilterChain.doFilter(ApplicationFilterChain.
ява: 162) org.apache.catalina.filters.HttpHeaderSecurityFilter.doFilter(HttpHeaderSecurityFilter.java:126) org.apache.catalina.core.ApplicationFilterChain.internalDoFilter(ApplicationFilterChain.java:189) org.apache.catalina.core.ApplicationFilterChain.doFilter(ApplicationFilterChain.java:162) org.springframework.web.servlet.resource.ResourceUrlEncodingFilter.doFilter(ResourceUrlEncodingFilter.java:63) орг.apache.catalina.core.ApplicationFilterChain.internalDoFilter(ApplicationFilterChain.java:189) org.apache.catalina.core.ApplicationFilterChain.doFilter(ApplicationFilterChain.java:162) org.springframework.web.filter.OncePerRequestFilter.doFilter(OncePerRequestFilter.java:101) org.apache.catalina.core.ApplicationFilterChain.internalDoFilter(ApplicationFilterChain.java:189) org.apache.catalina.core.ApplicationFilterChain.doFilter(ApplicationFilterChain.java:162) org.springframework.web.filter.OncePerRequestFilter.doFilter(OncePerRequestFilter.java:101) org.apache.catalina.core.
ApplicationFilterChain.internalDoFilter(ApplicationFilterChain.java:189) org.apache.catalina.core.ApplicationFilterChain.doFilter(ApplicationFilterChain.java:162) org.springframework.web.filter.OncePerRequestFilter.doFilter(OncePerRequestFilter.java:101) орг.apache.catalina.core.ApplicationFilterChain.internalDoFilter(ApplicationFilterChain.java:189) org.apache.catalina.core.ApplicationFilterChain.doFilter(ApplicationFilterChain.java:162) org.springframework.boot.web.servlet.support.ErrorPageFilter.doFilter(ErrorPageFilter.java:130) org.springframework.boot.web.servlet.support.ErrorPageFilter.access$000(ErrorPageFilter.java:66) org.springframework.boot.web.servlet.support.ErrorPageFilter$1.doFilterInternal(ErrorPageFilter.java:105) org.springframework.web.filter.OncePerRequestFilter.doFilter(OncePerRequestFilter.java:107) org.springframework.boot.web.servlet.support.ErrorPageFilter.doFilter(ErrorPageFilter.java:123) org.apache.catalina.core.ApplicationFilterChain.internalDoFilter(ApplicationFilterChain.
java:189) org.apache.catalina.core.ApplicationFilterChain.doFilter(ApplicationFilterChain.ява: 162) org.springframework.boot.actuate.web.trace.servlet.HttpTraceFilter.doFilterInternal(HttpTraceFilter.java:90) org.springframework.web.filter.OncePerRequestFilter.doFilter(OncePerRequestFilter.java:107) org.apache.catalina.core.ApplicationFilterChain.internalDoFilter(ApplicationFilterChain.java:189) org.apache.catalina.core.ApplicationFilterChain.doFilter(ApplicationFilterChain.java:162) орг.springframework.web.filter.RequestContextFilter.doFilterInternal (RequestContextFilter.java: 99) org.springframework.web.filter.OncePerRequestFilter.doFilter(OncePerRequestFilter.java:107) org.apache.catalina.core.ApplicationFilterChain.internalDoFilter(ApplicationFilterChain.java:189) org.apache.catalina.core.ApplicationFilterChain.doFilter(ApplicationFilterChain.java:162) org.springframework.web.filter.FormContentFilter.doFilterInternal (FormContentFilter.java: 92) org.springframework.web.filter.
OncePerRequestFilter.doFilter(OncePerRequestFilter.java:107) org.apache.catalina.core.ApplicationFilterChain.internalDoFilter(ApplicationFilterChain.java:189) org.apache.catalina.core.ApplicationFilterChain.doFilter(ApplicationFilterChain.java:162) org.springframework.web.filter.HiddenHttpMethodFilter.doFilterInternal (HiddenHttpMethodFilter.ява:93) org.springframework.web.filter.OncePerRequestFilter.doFilter(OncePerRequestFilter.java:107) org.apache.catalina.core.ApplicationFilterChain.internalDoFilter(ApplicationFilterChain.java:189) org.apache.catalina.core.ApplicationFilterChain.doFilter(ApplicationFilterChain.java:162) org.springframework.boot.actuate.metrics.web.servlet.WebMvcMetricsFilter.filterAndRecordMetrics(WebMvcMetricsFilter.java:154) орг.springframework.boot.actuate.metrics.web.servlet.WebMvcMetricsFilter.filterAndRecordMetrics(WebMvcMetricsFilter.java:122) org.springframework.boot.actuate.metrics.web.servlet.WebMvcMetricsFilter.doFilterInternal(WebMvcMetricsFilter.
java:107) org.springframework.web.filter.OncePerRequestFilter.doFilter(OncePerRequestFilter.java:107) org.apache.catalina.core.ApplicationFilterChain.internalDoFilter(ApplicationFilterChain.java:189) орг.apache.catalina.core.ApplicationFilterChain.doFilter(ApplicationFilterChain.java:162) org.springframework.web.filter.CharacterEncodingFilter.doFilterInternal (CharacterEncodingFilter.java:200) org.springframework.web.filter.OncePerRequestFilter.doFilter(OncePerRequestFilter.java:107) org.apache.catalina.core.ApplicationFilterChain.internalDoFilter(ApplicationFilterChain.java:189) org.apache.catalina.core.ApplicationFilterChain.doFilter(ApplicationFilterChain.java:162) org.apache.catalina.core.StandardWrapperValve.invoke(StandardWrapperValve.java:202) org.apache.catalina.core.StandardContextValve.invoke(StandardContextValve.java:97) org.apache.catalina.authenticator.AuthenticatorBase.invoke(AuthenticatorBase.java:542) org.apache.catalina.core.StandardHostValve.invoke(StandardHostValve.
java:143) org.apache.каталина.клапаны.ErrorReportValve.invoke(ErrorReportValve.java:92) org.apache.catalina.valves.AbstractAccessLogValve.invoke(AbstractAccessLogValve.java:687) org.apache.catalina.core.StandardEngineValve.invoke(StandardEngineValve.java:78) org.apache.catalina.connector.CoyoteAdapter.service(CoyoteAdapter.java:357) org.apache.coyote.http11.Http11Processor.service(Http11Processor.java:374) орг.apache.койот.AbstractProcessorLight.process(AbstractProcessorLight.java:65) org.apache.coyote.AbstractProtocol$ConnectionHandler.process(AbstractProtocol.java:893) org.apache.tomcat.util.net.NioEndpoint$SocketProcessor.doRun(NioEndpoint.java:1707) org.apache.tomcat.util.net.SocketProcessorBase.run(SocketProcessorBase.java:49) java.base/java.util.concurrent.ThreadPoolExecutor.runWorker(ThreadPoolExecutor.java:1128) Ява.base/java.util.concurrent.ThreadPoolExecutor$Worker.run(ThreadPoolExecutor.java:628) org.apache.tomcat.util.threads.TaskThread$WrappingRunnable.run(TaskThread.
java:61) java.base/java.lang.Thread.run(Thread.java:834)
Как крупный международный издатель академических и исследовательских журналов, Science Alert публикует и разрабатывает игры в партнерстве с самыми престижные научные общества и издательства.Наша цель заключается в проведении высококачественных исследований в максимально широком аудитория. | ||||||
Мы прилагаем все усилия, чтобы поддержать исследователей
которые публикуются в наших журналах.![]() | ||||||
2022 цены уже доступны. Ты может получить личную / институциональную подписку на перечисленные журналы непосредственно из Science Alert. В качестве альтернативы вы возможно, вы захотите связаться с предпочитаемым агентством по подписке. Пожалуйста, направляйте заказы, платежи и запросы в службу поддержки клиентов в службу поддержки клиентов журнала Science Alert. | ||||||
Science Alert гордится своим
тесные и прозрачные отношения с обществом.![]() | ||||||
Здесь вы найдете ответы на наиболее часто задаваемые вопросы (FAQ), которые мы получили по электронной почте или через контактную веб-форму.В соответствии с характером вопросов мы разделили часто задаваемые вопросы на разные категории. | ||||||
Азиатский индекс научного цитирования (ASCI)
обязуется предоставлять авторитетный, надежный и
значимая информация путем охвата наиболее важных
и влиятельные журналы для удовлетворения потребностей глобального
научное сообщество.![]() akson-quick.ru © 2019
|