клей пва или жидкое стекло для стяжки пола, пропорции
Для улучшения качеств строительного раствора применяют добавки. Правильно подобранный компонент увеличивает устойчивость бетона к нагрузкам и уменьшает время застывания. Перед тем, как использовать цемент с ПВА или с жидким стеклом, надо разобраться в особенностях материалов.
Свойства добавок
При выборе компонентов отталкиваются от функций, которые покрытие должно выполнять. При смешивании добавки кардинально меняют характеристики бетона. Рассмотрим сильные и слабые стороны химических веществ.
ПВА
Материал создали на основе эмульсии поливинилацетата с загустителями и присадками. Клейкая белоснежная или слегка желтая масса по структуре напоминает сметану. У вещества есть легкий, едва уловимый аромат без химического подтона. Для цемента с клеем ПВА часто используют строительную (универсальную МБ) разновидность или специальную жидкую дисперсию.
Использование добавки в цементеИсточник ozon.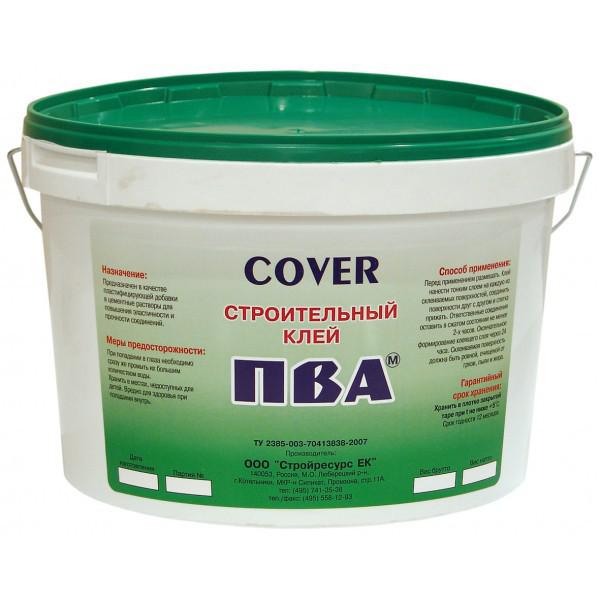
В бетоне средство выполняет функции пластификатора. При соединении с раствором вещество улучшает характеристики материала:
- Повышается пластичность. Цемент выдерживает разрывные нагрузки, снижается возможность появления трещин в конструкции.
- Увеличиваются сроки службы. Клей ПВА продлевает эксплуатационные качества бетона.
- Упрощает работу с сырьем. Клеящий состав легко замешивать, масса становится однородной, поэтому исполнитель затрачивает мало усилий.
- Держится на любой поверхности. Стяжку без проблем можно расположить в горизонтальном или вертикальном положении.
- Не деформируется. Затвердевший слой получается очень крепким, не пылится при эксплуатации.
Клей ПВА разрушается под ультрафиолетом, но при добавлении в цемент вступает в химическую реакцию. В бетоне вещество уже не боится солнца, выдерживает 8 циклов заморозки-оттаивания. Компонент часто используют при создании наливных полов и стяжек в закрытых помещениях.
Цементный раствор: состав, правильные пропорции, и необходимое оборудование
Цемент с ПВА расходуется больше, чем при обработке чистым раствором.
У готового состава высокая скорость полимеризации, поэтому средство не является универсальным. Стяжка или оштукатуренные поверхности долго сохнут. К минусам вещества относят неустойчивость к высокой влажности и запрет работы при температуре, ниже +10 С.
Жидкое стекло
У добавки на основе силиката натрия нет цвета и запаха. Химикат выпускают в виде вязкой смеси. При контакте с углекислым газом в воздухе средство начинает кристаллизироваться. В процессе затвердения возникает тонкая, крепкая пленка, устойчивая к влаге и механическим повреждениям.

Из-за хрупкости жидкое стекло никогда не используют в чистом виде, всегда добавляют в строительные растворы. При смешивании в определенной пропорции удается изменить характеристики бетона:
- Увеличивается текучесть состава. Вещество на основе силиката улучшает вязкость исходного материала. Средство равномерно распределяется по поверхности и проникает в мельчайшие трещины.
- Ускоряет застывание. Раствор с добавлением 10% силиката схватывается через 5 минут, а полное затвердение происходит через 4 часа.
При включении вещества в бетон уменьшается расход строительной массы, снижая затраты на ремонт. Жидкое стекло выдерживает высокую влажность, защищая обработанную поверхность от плесени и гниения. Средство можно нанести только на цемент или древесину, иначе будет отторжение.
Характеристики состава зависят от концентрации добавки. Слишком много силикатного материала в бетоне ухудшает качество раствора. Оптимальные параметры варьируются в пределах 5-10%, максимум – 15%. Для улучшения эластичности в цемент включают пластификаторы.
Когда использовать
Несмотря на видимое сходство у материалов разные характеристики и сфера применения. Силикат натрия – идеальный вариант при высокой влажности. Средство уменьшает пористость бетона, отталкивают воду и создают неблагоприятные условия для плесени. Обработанные поверхности не пропускают влагу и не гниют.
Из-за «эффекта стекла» жидкую добавку рекомендуют использовать при облицовке в банях и санузлах, колодцах и бассейнах. При высокой температуре раствор с добавлением прозрачного материала приобретает жаропрочные свойства. Характеристики смеси полезны при возведении дымоходов, каминов и печей.

Как правильно сделать раствор для кладки кирпичей: пропорции и требования
Цемент с ПВА применяют при создании или обновлении наливных полов. Эластичное сырье равномерно распределяется по плоскости, не трескается и долго сохраняет твердость (не пылит). Клей внутри состава облегчает облицовку стен и потолков плиткой. Вещество обеспечивает лучшую адгезию керамики с поверхностью, защищает отделку от отпадения.
Клей в бетоне уменьшает размер цементных пор и равномерно распределяет по составу. Масса становится более пластичной и податливой, чем традиционная штукатурка. Вещество удается ровно и красиво положить на поверхность. После черновых работ стены и потолок меньше скалываются при механических повреждениях, на плоскостях не возникают трещины.
Область применение ПВАИсточник liveposts.ruСмешивая цемент с ПВА, применение которых считают универсальным средством во время ремонта, стоит помнить о сфере использования.
Как правильно развести
Качество состава и простота нанесения зависит от правильности смешивания. Объем добавок не должен превышать основное вещество, поэтому профессионалы рекомендуют точно выдерживать пропорции. Разберем основные способы разведения материалов.
Технология для ПВА
Клей разрушается под воздействием солнечных лучей. Чтобы не потерять свойства, соединение проводят в помещении. Максимальная концентрация добавок – 20%. При облицовке плиткой соотношение ПВА и цемента выдерживают в пропорциях 1 к 5, для штукатурных работ – 1 к 3. Если готовят раствор для стяжки, то доля клеящего вещества варьируется в пределах 5-10%.
Бетон соединяют с песком, разбавляют холодной жидкостью. В состав вводят добавку в нужной концентрации. У клея очень вязкая консистенция, что осложняет смешивание. ПВА предварительно разводят водой до состояния молочка (1:2), после чего выливают в раствор.
Как правильно выбрать пластифицирующие добавки для цементных растворов
Для облицовки вертикальных поверхностей плиткой профессионалы рекомендуют использовать концентрированную массу. ПВА и цемент соединяют в пропорциях 1:4, без добавления жидкости. Получается очень крепкий раствор, который удерживает тяжелую отделку в труднодоступных местах.
При работе с материалом марки М400 сырье смешивают с песком (1:3), потом вливают воду и разводят до нужной консистенции. Для приготовления штукатурки на 10 л готового бетона берут 70 г ПВА. Если клей используют в форме разведенного молочка, то надо уменьшить количество влаги при смешивании раствора.
Напольная стяжка должна быть крепкой, вязкой и быстросохнущей. При работе с новым покрытием используют (в кг):
- щебень – 300;
песок – 200;- цемент – 100;
- краситель – 5 кг;
- ПВА – 20.
Жидкость добавляют в соотношении 0,45-0,55 (В/Ц). Старую напольную стяжку легко обновить смесью бетона с ПВА. Строительный материал соединяют с песком и клеевой эмульсией в пропорциях 1:3:0,5. Для крепости в состав добавляют 4% эпоксидной смолы. Аккуратно вливают воду, добиваясь нужной консистенции.
Смешивание ПВА с бетономИсточник zen.yandex.ruМетод для жидкого стекла
Раствор цемента с силикатным клеем традиционно смешивают в пропорциях 10:1. При увеличении жидкого стекла в бетоне усиливаются гидроизоляционные качества соединения, что учитывают при работе во влажных условиях. Для снижения кристаллизации полимер разбавляют водой, после чего вводят в готовый бетон и тщательно размешивают строительным миксером.
Для бытовых нужд концентрация силикатного вещества в цементе не должна быть больше 3%. Если нужен огнеупорный состав, то песок со стеклом жидким и стройматериалом соединяют в пропорциях 4:1,5:1,5. Объем влаги – 25% от общей массы раствора.
Силикатный компонент в составе штукатурки усилит водоотталкивающие свойства отделки. Готовый цементно-песочный раствор смешивают с 15% кристаллизующего вещества. Полученную массу тщательно размешивают, потом приступают к обработке поверхностей.
Жидкое стекло входит в защитный состав для колодцев. Бетон, песок и добавку соединяют в пропорциях 1 к 1. По консистенции раствор должен напоминать вязкую сметану. Для гидроизоляции бассейнов берут цемент с силикатом в соотношении 10:1.
Железнение бетона, пола, стяжки, дорожки – 3 основных способа, этапы технологии
Заключение
Улучшить характеристики бетона помогут компоненты, которые в правильной концентрации добавляют на стадии создания раствора. Выбор средства зависит от задач и места эксплуатации. Клей ПВА используют при выравнивании полов и облицовки плиткой сухих помещений. В условиях повышенной влажности отдают предпочтение жидкому стеклу.
Пва в бетон
Добавка ПВА в бетонный раствор
Довольно давно в качестве полезной добавки к цементному раствору стали применять ПВА. Главная цель – повысить качество цементно-песчаного раствора. Это клейкое вещество позволяет получить более пластичный бетон, который моментально схватывается на поверхности.
ПВА и его свойства
ПВА – это белая клейкая эмульсия на основе полимера поливинилацетата с консистенцией сметаны. Клей практически не имеем запаха, не токсичен, экологичен, может храниться длительное время без потери свойств. Существует канцелярский, мебельный и строительный тип.
Клеевой состав не влагостойкий. Он легко растворяется в воде в жидком виде. Однако в процессе застывания поливинилацетат полимеризуется, теряет цвет и приобретает стойкость к воздействию воды. После склеивания поверхность приобретает усилие на разрыв до 1300 г/см², что свидетельствует о высокой прочности застывшего полимера.
Поливинилацетат выдерживает воздействие низких температур с сохранением свойств даже при -20°С. Полимер может проходить до трех циклов заморозки и оттаивания. Сам поливинилацетат не стоек в УФ-лучам, но в бетонной смеси он приобретает это свойство, поэтому его можно применять для возведения сооружений, стяжек для уличного использования.
Особенности применения
- повышает пластичность;
- снижает твердость готового изделия путем увеличения прочности на изгиб;
- повышает адгезию бетонного раствора к поверхности.
Это достигается за счет соблюдения четких пропорций смешения бетона и ПВА. При этом количество воды не должно превышать 5%. Не каждый тип клеевого состава можно использовать. Канцелярский ПВА содержит много крахмала, а в клее для дерева есть ненужные химические наполнители, которые ухудшают свойства цементной смеси.
В зависимости от предназначения готовящейся смеси определяются пропорции цемента к поливинилацетату. Например, для стяжки и кладки нужны разные свойства раствора.
Важным критерием выбора типа клеевого вещества для цемента является конечная влажность, в которой будет эксплуатироваться готовая конструкция. Несмотря на полимеризацию, при застывании и приобретении влагостойкости клей лучше не добавлять в бетонные смеси для отделки ванн, душевых, бассейнов.
В качестве перестраховки состав клей-цемент лучше использовать для обустройства территории, где температура эксплуатации будет выше 7°С.
Правила использования
В основном клеевая добавка работает как пластификатор. Для работы с раствором для стяжки добавлять клея нужно в количестве 5%-10% или 0,5л ПВА на 2-3 ведра цемента. Если запланирована кладка плитки, то поливинилацетата лучше брать 20% и более.
Примешивать клей следует уже после его разведения водой. Это позволит получить более однородную массу в конце. Однако, если нужен состав с высокой адгезией и пластичностью, размешивать цемент с клеем лучше без предварительного растворения в воде.
Вывод
Отличительные свойства ПВА позволяют применять его в качестве добавки к бетонным смесям разного назначения. При этом получаемые поверхности будут наделены повышенной прочностью и долговечностью.
Клей облегчает кладку растворов, поэтому им обогащают строительные массы для столярных работ, отделки штукатуркой и грунтовкой.
kladembeton.ru
Раствор цемента и клей ПВА
Комментариев:
Рейтинг: 80
Оглавление: [скрыть]
- Клей ПВА и его свойства
- Особенности и применение цементного раствора с добавлением клея ПВА
Раствор цемента и клей ПВА принято смешивать в строительной индустрии достаточно давно. С помощью этого старались улучшить качество цементно-песчаного раствора. Применение началось практически с того момента, как появился клей ПВА в свободной продаже. Бетон, в который он добавлялся, приобретал более высокую пластичность и намного быстрее схватывался, чем обычный водный раствор.
Компоненты цементного раствора.
В наши дни торговля строительными материалами предлагает немалое количество разновидностей сухих смесей, в которые клей добавлен в уже сбалансированных количествах. Однако и стоимость их достаточно высока. Между тем если правильно добавить в обычный цементный раствор клей ПВА, в ряде случаев результат может получиться не хуже. Финансовые затраты же на расходные материалы существенно сократятся.
Клей ПВА и его свойства
Это вещество представляет собой белую массу без отчетливого запаха, имеющую консистенцию сметаны средней жирности. Основу его составляет поливинилацетатная эмульсия, являющаяся одной из разновидностей полимеров.
Клей ПВА способен выдерживать низкие температуры и при этом не токсичен и экологически безопасен.
По назначению он различается на канцелярский, мебельный и строительный, каждый из которых имеет в своем составе соответствующие загустители и прочие добавки. Последний расфасовывается для реализации в пластмассовые ведра и бочки емкостью 1, 2, 5, 10 и 30 кг и и может храниться при температуре от +5 до + 20°С в течение полугода.
Стоит помнить, что это вещество само по себе не является водостойким, оно легко разбавляется водой и боится высокой влажности. Тем не менее после полного завершения цикла застывания происходит его полимеризация, оно становится прозрачным и в воде уже растворению не подлежит. Склеенная поверхность выдерживает усилие на разрыв порядка 1300 г на 1 см².
В то же время этот клей способен выдерживать воздействие низких температур. Он сохраняет свои свойства при морозе до -20°С достаточно долгое время и может замерзать и оттаивать до 3 раз. При этом ПВА не обладает токсичным воздействием и совершенно экологически безопасен.
Вернуться к оглавлению
Прежде всего стоит помнить, что этот клей постепенно разрушается и теряет свои свойства под воздействием ультрафиолетового излучения. Однако добавление его в кладочный цементный раствор или бетон приводит к тому, что после того как он прореагирует с цементом, его свойства изменяются, и воздействие ультрафиолета ему уже не страшно.
Таблица пропорций ингредиентов цементного состава.
Именно поэтому бетон с такой добавкой можно использовать для заливки стяжек как в закрытом помещении, так и на улице в местах, куда беспрепятственно падают солнечные лучи. В то же время в помещениях вроде ванн или саун, где предусматривается повышенный уровень влажности, его класть все же не рекомендуется.
Обычная пропорция при добавлении клея ПВА в цементно-песчаный раствор составляет от 5 до 10% при условии, что он будет разбавлен водой. Добавка его в бетон существенно повышает адгезию и создает дополнительный запас прочности.
Если же цемент смешать с ним без добавки воды, получится достаточно мощный клеящий состав, который очень хорошо подходит для крепления керамической облицовочной плитки, особенно на вертикальную поверхность. Широкое распространение получила идея добавлять этот компонент в раствор для штукатурных работ. Он становится от этого намного пластичнее, лучше ложится на основную поверхность и быстрее схватывается.
Добавка клея ПВА в бетон или другой цементный раствор в любом случае сказывается на потребительских свойствах последних положительно. Это особенно заметно при сравнении с обычным цементно-песчаным раствором на водной основе. Адгезия, пластичность и скорость застывания однозначно возрастают.
Если отсутствует постоянный источник сырости, а температура окружающей среды не ниже +7°С, то добавлять ПВА однозначно стоит, это существенно облегчает процесс работы с цементным раствором.
tolkobeton.ru
Пропорции для введение клея ПВА в цементную смесь
Одним из способов улучшения свойств цементных смесей является добавление поливинилацетата – клеевой эмульсии, растворимой в воде. К этой практике часто обращаются при приготовлении штукатурных, выравнивающих и соединительных растворов и даже бетонов. Пропорции и последовательность ввода зависят от целевого назначения составов, в большинстве случаев ПВА предварительно разбавляют водой. К ограничениям применения относят эксплуатацию обработанных поверхностей в условиях повышенной влажности.
Эффект от добавления клея в цементный раствор
Материал представляет собой разновидность полимеров и используется в качестве пластификатора. ПВА не имеет четко выраженного запаха, он растворяется в воде (только до окончания процесса застывания ЦПС или бетона), отсутствуют токсичные вещества. Стандартная пропорция варьируется от 5 до 10 %, введение в цементно-песчаный состав позволяет:
- Повысить его пластичность.
- Увеличить его прочность на изгиб после застывания. Опыты показывают, что обработанная ПВА поверхность выдерживает усилие на разрыв от 1300 г/см2.
- Улучшить качество сцепления смесей на основе цемента.
Величина адгезии в данном случае зависит от используемых соотношений, при желании получения надежного клея для плитки его доля достигает 20 % от общего объема.
- Упростить процессы работы.
К ограничениям применения относят эксплуатацию в условиях воздействия горячего и влажного пара, это обусловлено ускорением гидролиза поливинилацетата и щелочных сред и превращением его в спирт даже в связанном виде. По этой причине клей не вводят в растворы для ванных комнат, саун, бассейнов и для облицовки участков, подверженных частым влажностным нагрузкам. Признается явное улучшение эластичности и адгезии, к минусам относят отсутствие контроля за набором прочности (процесс гидратации цементного камня комбинируется с высыханием дисперсии полимера и в целом усложняется).
В цементный состав добавляют ПВА определенной марки – а именно для строительных целей. Канцелярские или обойные содержат избыточный крахмал, клеи для дерева – посторонние добавки и примеси, плохо сочетаемые с портландцементом. Нужными для улучшения строительных растворов свойствами обладает водная дисперсия, содержащая не менее 50% полимеров. Она продается в фасованных пластмассовых емкостях от 1 до 30 кг и имеет ограниченный 6 месяцами срок годности.
Пропорции ввода и особенности приготовления строительных смесей
Существует два способа соединения раствора цемента и клея: в первом добавку разводят водой (эмульсию наливают в емкость с жидкостью и тщательно размешивают до достижения полной прозрачности), во втором его вводят в неразбавленном виде. Нарушать стандартные соотношения В/Ц не рекомендуется в любом случае. Добавление неразбавленного ПВА требуется при замесе соединительных составов, хорошо размешанного – при приготовлении бетонов или с целью улучшения пластичности. Пропорции компонентов ЦПС выбираются исходя из целевого назначения:
1. Доля стандартной добавки в разбавленном состояния для повышения пластичности и прочности на изгиб – 5-10%. В перерасчете это означает 0,5 л ПВА на 2-3 ведра (или 1 мешок) вяжущего.
2. При изготовлении цементного раствора для заливки основной стяжки пола рекомендуется смешать 100 кг портландцемента, 200 – песка, до 300 – мелкофракционного щебня, 5 – устойчивого к щелочному воздействию пигмента и 20 – непосредственно ПВА. Воду добавляют до достижения нужной подвижности, стандартное соотношение В/Ц варьируется от 0,45 до 0,55, превышать его не советуется.
3. При приготовлении цементной смеси для кладки плитки доля клея достигает 20% от общей массы. В этом случае его соединяют со смешанными в соотношении 1:5 сухими цементом и песком (марка прочности вяжущего – не ниже М400) без добавления воды. Полученный состав характеризуется высокой адгезией и подходит для крепления изделий на вертикальные стены. Некоторые специалисты советуют использовать жидкий раствор цемента, клея ПВА и воды для подготовки сложных поверхностей (на гладких бетонных плитах, к примеру, он заменяет насечки).
4. При необходимости ремонта старых бетонных стяжек рекомендуется смешать цемент, песок и эмульсию поливинилацетата в пропорциях 1:3:0,5 соответственно и добавить к ним по 4% от общей доли вяжущего эпоксидной смолы и отвердителя. Вода вводится до достижения нужной консистенции – жидкого теста. Полученный состав обладает хорошим качеством сцепления и держится даже на старом и высохшем бетоне.
5. При замесе штукатурок используются стандартные пропорции портландцемента и песка – 1:3. На 10 л готовой (уже затворенной водой) смеси добавляется 50-70 г строительного клея ПВА.
stroitel-lab.ru
Цемент с ПВА — сколько добавлять в раствор?
Метод, при котором в цементный раствор добавляют ПВА, известен еще с советских времен. Он улучшает не только технические, но и эксплуатационные характеристики.
Свойства клея ПВА
Такой раствор получается:
- более однородным;
- пластичным;
- увеличивает силу сцепления между частичками раствора;
- улучшает прочность;
- повышается износостойкость;
- препятствует образованию трещин и др.
Клей ПВА является полимером и состоит из поливинилацетатной эмульсии. Он отлично растворяется в воде, но после высыхания обладает устойчивостью к влаге. Он не токсичен, безопасен для здоровья и при этом может сохранять свои свойства при очень высоких и низких температурах.
Особенности применения
Прежде чем определить пропорции добавления ПВА в цемент, нужно отметить какой тип этого клея не подходит для строительных целей. Это, прежде всего ПВА, предназначенный для бумажных и картонных изделий. Он содержит слишком много крахмала и других наполнителей. Также не стоит брать ПВА для дерева, так как он тоже содержит различные ненужные добавки.
Вторым важным моментом является предназначение раствора. Потому что пропорции цемента с ПВА будут различными. Для стяжки, нужны одни свойства, а для кладки керамической плитки другие. И последний нюанс, какая влажность будет в помещении. Не смотря на то, что после застывания клея, он полимеризируется и ему не страшна влажность, однако использовать его во влажных помещениях (ванна, душевая, бассейн) все же не рекомендуется.
Еще одной особенностью является температурный режим. Хотя клей выдерживает большие и маленькие температуры, но чтобы не рисковать конечным результатом надежности и долговечности лучше, чтобы температура была выше, чем +7 ° С.
Правила использования
Добавление ПВА используют как пластификатор, но помимо этого он улучшает свойства цементо-песочного раствора. Пропорции ПВА по отношению к цементу составляют от 5% до 20% . Все зависит от специфики применения этого раствора. Если это стяжка, то вполне хватит и 5%-10% содержания клея, а если это для плитки, то лучше не жалеть ПВА и добавить 20%.
Чтобы было понятнее — на 2-3 ведра цементного раствора для стяжки нужно где-то 0,5л ПВА. Добавляют ПВА ужа разбавленное с водой, чтобы оно более равномерно перемешалось со всей смесью.
Если клей размешать с цементом, без предварительного растворения в воде, то получиться состав, который будет обладать отличным свойствами адгезии и пластичности.
salecement.ru
Клей ПВА строительный Bergauf Praktik 10 кг *1/44
Клей ПВА строительный Bergauf Praktik 10 кг 1п=44штОБЛАСТЬ ПРИМЕНЕНИЯ
Применяется для склеивания изделий из бумаги, легких обоев. Может применяться в качестве модификатора для улучшения свойств сухих смесей, штукатурных, шпаклевочных составов и улучшает их адгезионные свойства. Также применяется для грунтования поверхностей (допускается разбавление водой 1:2).
ДЛЯ РУЧНОГО И МЕХАНИЗИРОВАННОГО НАНЕСЕНИЯ
СВОЙСТВА
Клей готов к применению. Легко наносится, придает строительным смесям удобную для нанесения консистенцию и повышает адгезию к основанию. Может транспортироваться при отрицательных температурах.
СОСТАВ
Поливинилацетатная дисперсия, вода, специальные добавки.
РЕКОМЕНДАЦИИ ПО ПРИМЕНЕНИЮ
Перед применением выдержать клей при комнатной температуре не менее 24 часов и тщательно перемешать. Поверхность очистить от грязи и пыли. Во время проведения работ избегать воздействия прямых солнечных лучей, сквозняков и условий повышенной влажности. При использовании клея температура в помещении должна быть не ниже 12°С. Оптимальная температура (18-20)°С и относительная влажность воздуха (655) %.
НАНЕСЕНИЕ
Кистью, валиком на подготовленную сухую чистую поверхность.
РАСХОД
При поклейке обоев – 1 л на поверхность площадью (4-5) м²
Для модификации раствора – (1-1,5) л клея на 10 кг сухой массы (цемент, песок) – замещая аналогичное кол-во воды указанное на упаковке продукта, но не более 30%.
При грунтовании поверхности – 1 л клея на 2 л холодной воды.
ВРЕМЯ ВЫСЫХАНИЯ
Время полного высыхания при температуре (202) °С и относительной влажности воздуха (65±5) % — 24 ч.
ОЧИСТКА ИНСТРУМЕНТА
Инструменты очищать водой сразу после использования.
ТРАНСПОРТИРОВАНИЕ И ХРАНЕНИЕ
Хранить в плотно закрытой таре в складских помещениях при температуре выше 5°С. Гарантийный срок — 24 месяца с даты изготовления.
Клей транспортируют в плотно закрытой заводской упаковке любыми видами транспорта в крытых транспортных средствах или в контейнерах на любые расстояния, с любой скоростью в соответствии с требованиями правил перевозки, действующих на данном виде транспорта
Ограничения по транспортированию и хранению:
— Оберегать от солнечных лучей;
— Оберегать от влаги;
— Температурный режим от +5°С до +45°С.
Смеси следует хранить в упакованном виде, избегая увлажнения и обеспечивая сохранность упаковки, в крытых сухих складских помещениях с относительной влажностью воздуха не более 60%.
Клей выдерживает 4 цикла замораживания-оттаивания при -40°С до 2-х недель.
Стоит ли добавлять ПВА в цементный раствор? Польза или вред? | Скотч всему голова!
Здравия желаю, дорогие читатели!
В любой профессии есть свои лайфхаки, для упрощения жизни. Строительство не исключение. Народные мастера как только не изощряются, чтобы облегчить себе труд. Где-то это обосновано и полезно, а где то приносит только вред..
Пластификатор.
Благодаря этой добавке цементный раствор становится пластичным и прекрасно заполняет пустоты. Пластификатором называют множество добавок для стройрастворов.
Если рассматривать не специальные добавки, а ПВА, то для этой цели он очень даже подходит. Но есть и свои подводные камни.
Какой именно ПВА сгодится?
Сразу отсечём негодные варианты:
- 1. Обойный ПВА — в составе крахмал, из-за чего в нем мало поливинилацетата.
- 2. Канцелярский ПВА — тоже не годится, потому что разбавлен водой и в следствии быстро замерзает.
- 3. ПВА для дерева — так же мимо. В составе карбоксиметилцелюлоза, которая негативно влияет на цементный раствор.
Те люди, которые использовали варианты описанные выше негодовали от результата и вследствие распространяют информацию, что ПВА в этих целях использовать нельзя!
А знающие люди использовали и будут использовать ПВА-МБ.
Другие же радуются Дисперсии.
Это основа для клея. Делится на два вида, один из которых подходит для цементного раствора и называется непластифицированной дисперсией.
Где применение ПВА противопоказано?
- 1. Наружные работы лучше сразу исключить, потому что у ПВА плохая морозостойкость.
- 2. Гипсовые растворы так же мимо.
Ну а теперь самое интересное. Сколько же надо клея лить в раствор?
От 5 до 20 процентов клея в соотношении с цементом.
Такой разбег обусловлен назначением смеси. Если нужно для стяжки пола, то вполне подойдёт 8%, для плитки нужно 20%.
То есть если взять усреднённые цифры в 10%, то получается что на 1 мешок цемента нужно 5 килограмм клея.
Если было полезно, то не забывайте ставить лайк и подписаться на канал! Всем спасибо!
Клей ПВА строительный | Сухие строительные смeси
Назначение:
Предназначен для добавления в цементный раствор при изготовлении стяжки, в штукатурные смеси и при проведении работ по укладке кафельной плитки, для склеивания изделий из бумаги и картона, не пригоден для склеивания дерева и столярных работ.
Состав:
Дисперсия ПВА, загуститель целлюлозного ряда, техническая вода, пеногаситель, консервант.
Способ применения:
Перед применением клей тщательно перемешать. В цементный раствор клей добавлять только после предварительного разведения водой в соотношении не менее 500 гр. клея на 10 л воды. При склеивании бумажных и картонных изделий клей нанести тонким слоем на одну из склеиваемых поверхностей, соединить с другой и плотно прижать. Работы с клеем рекомендуется проводить при температуре воздуха не ниже 10ºС и относительной влажности не более 80%.
Технические данные:
Толщина наносимого слоя: | до 2 мм. |
Срок годности: | 12 месяцев в плотно закрытой таре |
Температура хранения: | до +5ºС, предохраняя от воздействия влаги и прямых солнечных лучей |
Отличительные особенности:
- зкологически безопасный
Фасовка: 1; 2,3 кг.
ТУ 2385-009-58599384-2004
Цены на продукцию
КупитьКлей Цемент: состав, основа, раствор
На ремонт обычно уходит много денег, но лучше когда дело не в постоянной его переделке, а в качественных материалах, которые потом прослужат много лет. Например, в случае с укладкой плитки важно не только правильно выбрать отделочный материал, но и не ошибиться с клеем. На сегодняшний день в строительных магазинах представлено просто огромное количество разнообразных клеящих смесей, разной ценовой категории и состава. Как сделать выбор? Как утверждают специалисты, если не знаешь, какой раствор выбрать – покупай цементный. Далее рассмотрим, что же представляет собой белый клей Цемент для плитки.
Клей Цемент
Состав раствора
Входящие в состав ингредиенты клея на основе цемента очень просты. Основа – это песок и цемент, а также вода, которая добавляется во время его приготовления. Дополнительными добавками являются пластификаторы. Все это соответственно смешано в определенных пропорциях. Приготовить такую смесь с песка и цемента можно и самому, но есть риск ошибиться в пропорциях, что приведет к ненадежности смеси.
Для приготовления плиточного раствора цемента и клея необходимо внимательно придерживаться инструкции, которая указана на упаковке. Обычно она выглядит следующим образом:
- берется емкость, например, ведро или тазик, в нее наливается определенное количество воды;
- согласно инструкции в воду высыпается нужное количество порошка;
- полученный раствор перемешивается с помощью дрели со специальной насадкой до получения однородной массы.
Если после приготовления состав получился слишком жидким, ему необходимо дать время немного настояться. Обычно на это уходит не более 10 минут. После этого Цемент клей ПВА 2000 готов к использованию (см. фото). Стоит отметить, что не нужно стараться приготовить всю смесь сразу, если в этом нет необходимости, ведь она достаточно быстро затвердеет и станет непригодной для дальнейшего использования. Готовить раствор лучше частями и сразу применять его в работе.
Клей Цемент
Основные преимущества
«Плюсов» у клеящего вещества Цемент 2000 для плитки достаточно много. Это позволяет использовать его в кухне, ванной комнате, туалете, на балконе, стенах и полу. К ним, кроме низкой стоимости, можно отнести:
- экологически чистый состав клея Цемент;
- простоту приготовления и быстроту высыхания;
- удобство в работе;
- высокую адгезию и пластичность;
- надежность;
- стойкость к механическим повреждениям;
- хорошую влагостойкость;
- стойкость к постоянным перепадам температур и т.д.
Зачем добавлять ПВА?
Всем известно, что ПВА боится прямого воздействия солнечных лучей, которые несут в себе ультрафиолет. Но при добавлении в цементный раствор у него меняются свойства, и он перестает бояться солнца. Кроме плиточного клея Цемент ПВА также используется для создания стяжек и наливных полов внутри помещений. А вот там, где постоянно собирается влага, использовать этот компонент не рекомендуется.
При создании клеевого раствора, основа которого цемент и песок, доля ПВА в нем должна составлять примерно 20%. Это позволяет получить мощный клеевой состав, который долго и надежно будет держать керамическую и кафельную плитку, что особенно важно для вертикальных поверхностей. В белый плиточный раствор Цемент сначала добавляется вода, все это доводиться до нужной консистенции и только затем в него добавляется ПВА с расчета 60 грамм на 10 литров.
Особенности применения
- Клей для плитки Цемент наносится на основание зубчатым шпателем.
- При монтаже керамических или кафельных материалов, которые имеют небольшой вес, наносить раствор можно только на основание, а если отделка более тяжелая, то смесь должна накладываться и на саму плитку.
- Использовать плиточный клеевой состав необходимо при определенных температурных условиях.
Так, нижняя допустимая граница температур составляет 5°С, а верхняя – 30°С. Идеальной для работы считается температура воздуха 20°С и влажность 60%. Именно при таких условиях раствор быстрее схватится.
- После укладки отделочного материала нужно знать, что сохнет раствор от 12 до 24 часов.
В зависимости от используемых в клеевой смеси пластификаторов она может быть классической или быстрой. Это нужно учитывать еще во время покупки, т.к. во время работы можно не успеть приклеить отделку. Быстрый клей, нанесенный на пенопласт или другие материалы, полностью высыхает всего за 5-10 часов.
Обзор волокон ПВС и бетона
Волокна ПВА обеспечивают подвижность в бетоне. По словам Джима Глесснера из GST International LLC, бетон с волокнами ПВА может микротрещиноваться, что позволяет ему изгибаться. Высокоэффективные волокна из поливинилового спирта, поливинилового спирта, были разработаны около 20 лет назад японской компанией Kuraray. При добавлении в бетон или раствор волокна образуют молекулярную и химическую связь с цементом во время гидратации и отверждения.Результат: бетон с высокой прочностью на растяжение и удивительной пластичностью, состав которого может значительно снизить нагрузку на сталь в проекте.
«Цементный композит на основе поливинилового спирта, PVA-ECC, был разработан для использования в высотных зданиях для ликвидации последствий землетрясений, поскольку он устраняет вертикальный сдвиг», — говорит Джим Глесснер, владелец GST International LLC, компании из Невады, которая производит а также распространяет ряд специальных бетонных изделий.
«Хотя бетон очень прочный из стороны в сторону, любое вертикальное движение приведет к тому, что он сломается или треснет», — продолжает он.«PVA-ECC позволяет двигаться как одеяло. Этот материал не трескается, но дает микротрещины, позволяющие ему сгибаться. Это буквально сгибаемый бетон».
Это отличает PVA-ECC от бетона, армированного стекловолокном (GFRC), который подвержен вертикальному сдвигу. Согласно материалам на веб-сайте Kuraray, PVA-ECC обладает способностью к деформационному упрочнению, в то время как GFRC не имеет такой способности, что означает, что деталь из PVA менее подвержена разрушению при растрескивании. «Ваши механические показатели прочности на растяжение и изгиб намного превосходят волокно ПВС по сравнению со стеклом или сталью», — отмечает Глесснер.Когда дело доходит до архитектурных и декоративных применений, Глесснер говорит, что инженерный цементный продукт можно использовать для чего угодно, большого или малого, от вертикальных стен и горизонтальных столешниц до сборных плит и торкрет-бетона для ремонта и ремонта.
Использовать или не использовать
По словам Глесснера, у использования волокон ПВА есть один большой недостаток – «иначе все бы его использовали.”
Смеси с волокнами ПВА действительно сложно составлять и использовать, говорит он. «Чтобы подобрать правильную смесь, нужно время. Иногда на это уходят даже годы».
Волокна ПВА имеют тенденцию слипаться и связываться друг с другом в процессе смешивания, говорит Глесснер, «то, что мы называем эффектом волосяного комка». Чтобы решить эту проблему, его компания вместе с некоторыми другими производит специальный диспергатор, облегчающий работу подрядчика.
Не все согласны с Глесснером в том, что ПВС трудно использовать.Джим Ральстон, президент и владелец компании Urban Concrete Design в Фениксе, говорит, что уже много лет использует этот продукт для создания самых разных вещей. Что это за вещи в частности, он не раскрывает. «Но я скажу вам, что использую его для создания плит размером 5 на 10 футов, которые я продаю производителям, которые используют их для столешниц. Они устанавливают их как гранит», — говорит он. Он смешивает ПВС с тремя другими волокнами, включая стеклопластик. Единственная его претензия к тому, что ПВА стоит недешево.
«Безусловно, это лучшее волокно на рынке. Я полностью согласен с этим», — говорит Ралстон.
С другой стороны, Брэндон Гор, владелец компании Gore Design Co. в Темпе, штат Аризона, не заинтересован в использовании волокон ПВС в своих привлекательных раковинах. «Я доволен результатами, которые получаю от использования стеклопластика, и не вижу причин для перехода», — говорит он. Один из его основных поставщиков убедил его, что стеклопластик более доступен по цене, с ним проще работать, а конструктивно он лучше подходит.
А еще есть Джон Шулер, владелец CreativeCrete в Мерфисе, Калифорния., чьи проекты включают в себя раковины, столешницы и монолитные конструкции. «Во всем, что мы делаем, есть волокна ПВА», — говорит он, добавляя, что использует вручную уложенный стеклопластик только тогда, когда этого требует определенный внешний вид.
Он использует ПВС последние четыре или пять лет. «И у нас никогда не было проблем с диспергированием волокон. Это моя рекомендация номер один, за которой следует комбинация ПВА и стекла», — говорит Шулер.
«ПВА — невероятно скрытое волокно, — продолжает он. «Когда я шлифую и полирую, я не беспокоюсь о том, что волокна проступают или торчат.В настоящее время он загружает 1/2 фунта на кубический фут, что, по его словам, дает ему такую же прочность, как 5 фунтов стекловолокна.
«Это (количество ПВС) в два-три раза больше, чем загружают другие ребята», — отмечает он. «Мы производим много продуктов, которые требуют загрузки волокна ПВС до фунта на кубический фут. Как только вы преодолели полкило, это количество клетчатки действует больше как совокупность».
Волокна ПВС позволяют ему отливать изделия намного тоньше, чем традиционный бетон. «Самое тонкое, что у меня есть, составляет около дюйма.Это моя зона комфорта, чтобы поддерживать внешний вид, которым мы известны».
Что касается стоимости, Шулер говорит: «Это не какой-то сверхдорогой продукт. Я думаю, что вы стреляете себе в ногу, если не используете его. Это действительно повышает ударопрочность и твердость поверхности».
Боб Крузо, менеджер по международным региональным продажам компании New Nycon Inc. из Род-Айленда, занимающейся дистрибьюцией различных волокон для армирования бетона, говорит, что волокна ПВА не только делают бетон более прочным, но и повышают пластичность конечного продукта. , еще один большой плюс.«Волокна ПВА позволяют бетону двигаться или быть более пластичным, поглощать больше энергии, что предотвращает растрескивание, которое может возникнуть со временем», — отмечает он.
С точки зрения стоимости, продолжает Крузо, готовое изделие не уступает изделиям, изготовленным из стеклопластика. «Вы будете использовать примерно вдвое меньше с PVA». По его оценке, стоимость составит от 5 до 6 процентов от общей стоимости проекта. «И этот материал имеет гораздо больше преимуществ, чем проволочная сетка или стальная арматура в сборных столешницах или архитектурных панелях.”
В сборных конструкциях панели могут быть отлиты тоньше, что снижает количество используемого материала и вес сборной детали, говорит он.
Наконец, Cruso утверждает, что с волокнами ПВС легче работать, чем со стекловолокном, поскольку они короче. Их размер составляет 3/8 дюйма, по сравнению с предварительно смешанными волокнами GFRC, которые имеют длину от 1/2 дюйма до 1 дюйма.
Демонстрационный стол со столешницей из мрамора смешанного цвета и точеными вручную краями. Советы для достижения наилучших результатов
По словам Крузо, ключ к успеху при работе с поливинилацетатом заключается в наличии надлежащего оборудования. В первую очередь подрядчику нужен смеситель с режущим действием.
Для достижения наилучших результатов с волокнами ПВС Cruso рекомендует подрядчикам тщательно перемешать волокна и равномерно распределить их по раствору или бетону. Он рекомендует добавлять цемент, песок, заполнитель и воду в смеситель в течение 3-4 минут перед добавлением волокон, а затем перемешивать еще несколько минут.
Шулер соглашается с Крузо. Он говорит, что при раннем добавлении волокон ПВА ко всем сухим ингредиентам у вас могут возникнуть проблемы с эффектом «слипания». Он говорит, что добавляет свои волокна в последние 3-4 минуты цикла смешивания, когда смесь полностью влажная.
Глесснер из GST высказывает еще одно важное мнение: Бетон с волокном ПВА не поддается затирке. «Это настолько агрессивное волокно, что его нельзя переутомить», — говорит он. После одного-двух проходов все начнет подтягиваться. «Это продукт для экспертного использования», — заявляет он. «Это не для обывателей.
«С продуктом нужно работать медленно», — продолжает он. «Когда дело доходит до сборного железобетона, это не будет проблемой.Но когда вы делаете наложение, вы не можете положить Magic Trowel и двигать его вперед и назад. С ним действительно сложно работать. Я просто не могу объяснить, как чертовски тяжело с ним работать».
Шулер говорит, что у него действительно нет проблем с затиркой смеси ПВА, но он соглашается, что требуется определенная ловкость, чтобы научиться правильно затирать ее. «Если вы используете низкое водоцементное отношение и более высокое содержание волокон ПВА, я рекомендую вам не следовать обычным методам затирки. Это ошибка некоторых парней.Вам нужно подождать, пока он слегка схватится, затем использовать воду или смазку, быстро размять (матерком или теркой), а затем стальным шпателем, чтобы избежать натяжения волокон.
«Если мы говорим о рекомендуемой более низкой дозировке от 1 до 2 фунтов на кубический ярд, — продолжает он, — я не понимаю, как у кого-то возникнут слишком большие проблемы с ее затиркой. Это зависит от вашей нагрузки. У вас могут быть проблемы с любым волокном, если вы нагрузите его выше, чем вы привыкли.”
Тем не менее, как только подрядчики проходят кривую обучения, Шулер призывает их загрузиться PVA. «Большая доза помогла нам уйти от проблем, связанных с размещением первичного армирования. Волокна ПВС намного проще в использовании, чем арматура и другая проволочная арматура. Это помогло нам поддерживать контроль качества».
www.gst-intl.com
www.kuraray.co.jp/en/
www.nycon.com
Есть еще вопросы по вашему проекту?
ПВА (поливиниловый спирт) Волокно
Волокна ПВА (поливиниловый спирт) — высокоэффективные армирующие волокна для бетона и строительных растворов.Волокна ПВС хорошо подходят для широкого спектра применений благодаря их превосходным свойствам по борьбе с трещинами, высокому модулю упругости, отличной прочности на растяжение и молекулярной связи, а также высокой стойкости к щелочам, ультрафиолетовому излучению, химическим веществам, усталости и истиранию. Волокна ПВС уникальны своей способностью создавать молекулярную связь с раствором и бетоном, которая на 300% выше, чем у других волокон.
Это моноволокна, которые доступны в трех вариантах длины и диаметра.
Волокно | Длина | Диаметр нити |
ПВА РЕК 7 | 0.25” (6 мм) | 5 денье (24 микрона) |
ПВА РЕК 15 | 0,375 дюйма (8 мм) | 8 денье (38 микрон) |
ПВА RECS 100 | 0,5 дюйма (13 мм) | 20 денье (100 микрон) |
Из-за тонкой природы этих волокон и того факта, что они распадаются на моноволокна, они с меньшей вероятностью будут видны на обработанных поверхностях. Насколько они видны по отношению друг к другу, прямо пропорциональна их различному диаметру (7 наименее заметен, 100 наиболее заметен).В равной степени верно и то, что чем меньше клетчатка, чем больше клетчатки приходится на данную единицу измерения, тем выше вероятность того, что они засорят смеси при более высоких дозировках. Таким образом, PVA100 дозируется с большей скоростью в более текучие смеси, чем PVA15.
PVA 100 предпочтительнее из-за простоты обработки по сравнению с 7 и 15. Это наиболее заметные волокна ПВА на готовых поверхностях из-за их длины. Идеально подходит для использования в текучих (SCC) бетонных смесях ECC. Волокна ПВА можно использовать в качестве основного или вторичного средства для армирования изделий из бетона, изготовленного вручную, включая бетонные столешницы, архитектурные бетонные элементы, бетонную мебель и многие другие применения.
Что такое волокна ПВА?
Большинство изделий из бетона кустарного производства, включая бетонные столешницы, архитектурные панели, бетонные туалетные столики и бетонные предметы мебели, часто получают первичное армирование с использованием волокнистой технологии. Понимание того, какие волокна являются функциональными в качестве основного армирования, и обоснование того, какое волокно использовать в данной ситуации, полезно для достижения хорошо усиленного объекта.
Наиболее широко используются три армирующих волокна: щелочестойкое (AR) стекловолокно, ПВА-волокно и акриловое волокно AC50. Есть много других доступных волокон, включая нейлон и полипропилен, но они обычно используются для контроля усадки и вторичного армирования, а не в качестве основного армирования. Сейчас мы сосредоточимся на преимуществах и недостатках использования волокон ПВС.
Что такое волокна ПВА?
ВолокнаPVA (поливиниловый спирт) представляют собой моноволокна, которые распределяются по бетонной матрице, создавая разнонаправленную сеть волокон, обеспечивая контроль усадки, стойкость к истиранию и защиту от теплового расширения и сжатия.При использовании при определенных скоростях нагрузки волокна ПВА могут использоваться в качестве основного армирования.
Поскольку волокна ПВА представляют собой моноволокна, в отличие от пучковых волокон, таких как стекловолокно AR, волокна рассеиваются по всей бетонной матрице с минимальной видимостью в готовом объекте. Их часто называют «невидимыми волокнами» из-за их минимальной видимости в готовых объектах.
ВОЛОКНА ПВС ОБОЗНАЧАЮТСЯ НОМЕРОМ РАЗМЕРА И НОМЕРА, НАПРИМЕР-
«ПВА РЕКС 15»
- Обозначение размеров, в данном случае «RECS», описывает «покрытие», которое наносится на волокно.
Волокна производятся как RECS и RSC, основное отличие которых заключается в том, что замасливание RECS создает волокно, которое более свободно диспергируется в бетонной смеси, особенно при более высоких дозировках. RECS менее склонен к комкованию и закупорке бетона в процессе смешивания, а также дает более гибкое волокно в отвержденном бетоне. RECS является более дорогим волокном по сравнению с RSC из-за этих дополнительных преимуществ.
- Номер, в данном случае «15», обозначает денье или диаметр волокна.Чем меньше денье, тем менее заметным будет волокно на готовой поверхности. Кроме того, чем меньше денье, тем больше площадь поверхности добавляется на фунт волокна, это важные замечания для разработки смесей с этими волокнами, которые будут рассмотрены в ближайшее время.
- Длина волокна не указана в справочнике, но обычно PVA7 имеет длину 1/4 дюйма, PVA15 имеет длину 3/8 дюйма, а PVA100 имеет длину 1/2 дюйма. Чем короче волокно, тем больше отдельных волокон будет в нем.
на фунт волокна Более короткие волокна обеспечивают большую ударопрочность (микроармирование) из-за большего количества волокон на фунт.Более длинные волокна обеспечивают лучшую прочность на растяжение (макроармирование).
Когда следует использовать волокна ПВА?
Преимущества-
- Основным преимуществом волокон ПВС является их скрытность. Они могут быть отлиты по всему бетону с минимальной видимостью на готовых поверхностях. Это верно независимо от того, создаете ли вы литой бетон или затираете готовый бетон. Армированный бетон
- PVA чрезвычайно пластичен или гибок.Бетонная деталь значительно согнется, прежде чем сломается, в отличие от внезапного катастрофического разрушения. Это не означает, что оно прочнее, чем стекловолокно AR Glass в применении, оно просто не работает. При сравнительном тестировании AR Glass обеспечивает большую прочность, но не всегда практично для использования в данном приложении.
- предназначены для «химического связывания» с бетоном. Обычному наблюдению это кажется сомнительным утверждением. Мы просто оставим это утверждение в покое и не будем придавать ему огромное значение.Если это правда, то мы победим. Если нет, то мы не будем беспокоиться.
Недостатки-
- Основной недостаток, как и у большинства вещей в природе, польза также является источником сложности. Поскольку волокна ПВА представляют собой мононити, они распределяются по всей смеси. Эта дисперсия волокнистой матрицы усложняет процесс смешивания при более высоких дозировках. Чтобы достичь скорости нагружения, необходимой для армирования определенных объектов, необходимо учитывать множество соображений в процессе проектирования смеси, а также в процессе смешивания, чтобы обеспечить успешный результат. Волокна ПВА
- стоят дороже, чем альтернативные варианты. Это компенсируется в некоторой степени, поскольку скорость загрузки ниже, чем у других волокон, но, тем не менее, это проблема.
Соображения —
- Скрытность волокон находится в прямой зависимости от денье волокна в сочетании с общей скоростью нагрузки.
- Чем меньше денье волокна, тем большую площадь поверхности и общее количество волокон оно добавит в смесь. Волокна ПВА
- можно добавлять в сочетании с другими волокнами или со стальным армированием, добавляя уникальные преимущества композиту.
- Если вы хотите, чтобы смесь была более текучей, то добавление больших PVA 100 приведет к меньшей площади поверхности и менее плотной волокнистой матрице, что позволит смеси двигаться более свободно.
- При использовании в основном для повышения ударопрочности на готовых поверхностях волокна меньшего денье будут менее заметны. Это особенно верно в отношении аэрозольных покрытий из стеклопластика.
Дозировка-
Дозировка волокон ПВА сильно различается в зависимости от области применения и желаемого результата. Дозировка может варьироваться от 0,1% до 2%.
Примечание. Все нормы дозирования основаны на весе всей смеси. (Сухая смесь + жидкость) x Норма дозировки
Все ситуации разные. Если вы не уверены в том, подходит ли приложение, вы можете поделиться своими опасениями и получить отзыв, заполнив эту форму.
Craftsman Mix и Countertop Mix. Волокна ПВА могут добавить полезные качества для всех различных рецептов и техник, обычно связанных с Craftsman Mix и Countertop Mix.
- Пресс-финиш :: Идеально подходит для использования в начальном пресс-слое. Лучше всего использовать структурную смесь с использованием стекловолокна. Дозировка- 0,2-0,5% ПВС7 или ПВС15
- Затирочная поверхность :: Идеально подходит для обработанной затирочной поверхностью. Лучше всего предшествовать структурной смеси с использованием стекловолокна.Дозировка- 0,2-0,5% ПВС7 или ПВС15
- Литая отделка :: Может использоваться в качестве вторичного армирования.
Дозировка- 0,2-1% ПВС15 или ПВС100. Может использоваться в определенных приложениях в качестве основного армирования. Дозировка — 1-1,2% ПВС15 или ПВС100. Пробное смешивание рекомендуется при дозировках более 1%
Смешанная смесь GFRC- ПВС-волокна отлично подходят для придания ударопрочности туманным покрытиям, могут использоваться в сочетании со стекловолокном в подкладочных слоях и могут использоваться в смесях SCC в качестве основного армирования.
- Туманное покрытие :: Для повышения ударопрочности и уменьшения усадки. Дозировка – 0,2% ПВА7 или ПВС15 (ПВА7 легче распылять)
- Backer Mix :: Используется в сочетании со стандартной загрузкой из стекловолокна для повышения пластичности. Дозировка- 0,2% ПВА15
- SCC :: Может использоваться в некоторых случаях в качестве основного армирования. Дозировка — 1-1,2% ПВС15 или ПВС100. Пробное смешивание рекомендуется при дозировках более 1%
- Скульптурные смеси :: Цены зависят от применения и эстетических требований
Смесь ECC Blended Mix- Эти смеси специально разработаны для использования волокон ПВА с высоким содержанием в качестве средства для первичного армирования. Вы можете найти рецепты для различных бетонных смесей ECC в нашем Каталоге продуктов и технологий. Каждая смесь содержит определенную смесь волокон ПВА, предназначенную для достижения очень специфической работоспособности и прочности. Эта смесь невероятно универсальна, в значительной степени из-за использования волокон ПВС. Наши смеси ECC часто подвергаются резке, скручиванию для получения уникальной мраморности и интенсивной обработке для декоративного воздействия заполнителя. Посмотрите на картинку ниже, чтобы понять гибкость этих миксов.
Выберите из нашего ассортимента волокон ПВС
Развитие прочности высокопрочного пластичного бетона, содержащего метакаолин и волокна ПВС
Механические свойства высокопрочного пластичного бетона (HSDC) были исследованы с использованием метакаолина (МК) в качестве материала, заменяющего цемент, и волокон ПВС.Всего было исследовано двадцать семь (27) смесей бетона с различным содержанием волокон МК и ПВА. Было обнаружено, что волокна ПВС более грубого типа обеспечивают прочность, сравнимую с контрольной или превышающую контрольную. Бетон с волокнами ПВС более крупного типа также имеет улучшенную микроструктуру, но микроструктура претерпевает изменения с увеличением соотношения размеров волокон. Микроструктура бетона с МК также более утонченная, а упаковка материала намного лучше с МК. Волокна ПВА не только обеспечивают более высокую жесткость, но также демонстрируют реакцию упрочнения на изгиб.Индекс ударной вязкости HSDC отражает улучшение ударной вязкости при изгибе по сравнению с обычным бетоном, а максимальные показатели ударной вязкости наблюдались при 10% MK и 2% объемной доле волокон PVA.
1. Введение
После промышленной революции большой экономический и промышленный рост привел к значительному увеличению использования цемента и стали, которые являются основными строительными материалами. Потребность в цементе и стали увеличилась примерно на 84% и 64% за последнее десятилетие [1, 2]; особенно гонка строительства самых высоких зданий значительно увеличила потребление цемента и стали. Кроме того, на цементную и сталелитейную промышленность приходится около 5% и 7% мировых выбросов CO 2 [3, 4], и сегодня бетонная промышленность является крупнейшим потребителем природных ресурсов, таких как вода, песок, гравий и щебень [3, 4]. 5]. Действительно, объемы истощения природных ресурсов и производства CO 2 очень велики. Каждый год около 14 % и 20 % мировой промышленной энергии потребляется цементной и сталелитейной промышленностью [6]; поэтому для устойчивого и экологически безопасного развития большое производство цемента и стали нежелательно и необходимо постепенное сокращение использования цемента и стали.На сегодняшний день несколько исследователей исследовали дополнительные материалы для цемента и стали, но цемент и сталь нельзя полностью заменить каким-либо другим дополнительным материалом. Цемент можно лишь частично дополнить минеральными добавками, такими как летучая зола, микрокремнезем, молотый гранулированный доменный шлак, зола рисовой шелухи и метакаолин (MK), а использование стали можно частично сократить за счет придания бетону пластичности.
Метакаолин (МК) в течение последних двух десятилетий получает признание в качестве минеральной добавки.Общие химические и физические свойства МК с другими минеральными добавками и обычным портландцементом (ОПЦ) представлены в таблице 1. МК обладает значительным содержанием кремнезема и глинозема по сравнению с цементом и другими минеральными добавками, проявляя способность образовывать как укрепляющий гель, то есть гидрат силиката кальция (CSH) и гидрат алюмината кальция (CAH) путем взаимодействия с первичным гидратом цемента. Максимальная прочность на сжатие, достигаемая при использовании МК в бетоне, составляет 134 МПа [7].Набранная ранняя прочность выше при добавлении МК по сравнению с летучей золой и микрокремнеземом [8]. Также увеличение прочности на растяжение и изгиб бетона и раствора с 10-15% МК составляет 32% и 38% соответственно, что лучше, чем микрокремнезема [9, 10]. В 2002 году было изучено влияние метакаолина и микрокремнезема на прочность при сжатии, коэффициент диффузии хлоридов и усадку [11], и было обнаружено, что метакаолин и микрокремнезем сопоставимы и дают более высокую начальную прочность, снижают коэффициент диффузии хлоридов и уменьшают высыхание. усадка.В 2005 году эти результаты были подтверждены, и также сообщалось, что как метакаолин, так и микрокремнезем дают низкую пористость и меньший размер пор, что приводит к улучшению микроструктуры бетона [12].
OPC-ФА | GGBS SF | МК РГА | ||||
Удельный вес | 3,05 | 2.2-2,8 | 2.69 | 2.6-3.8 | 2.5 | 2.11 |
,% | 4 2 ,%20.44 | 35-60 | 34.44 | 91.4 | 53.![]() | 88.32 |
2,84 | 10-30 | 9.0 | ||||
Fe 2 o 3 , % | 4.64 | 4-20 | 4-20 | 0.04 | 0.04 | 1.4 | 3 0.67
67.73 | 1-35 | 3 44.80, | 3 0,04||||
MgO ,% | 1,43 | 1,98 | 4,43 | 0,78 | 0,96 | 0,44 |
SO 3 ,% | 2,20 | 0,35 | 2,26 | 0,01 | — | — |
Na 2 O, % | 0.![]() | 0,48 | 0,62 | 0,39 | 0,04 | 0,12 |
К 2 О,% | 0,26 | 0,4 | 0,5 | 2,41 | 2,68 | 2,91 |
MnO ,% | 0.16 | — | — | — | 0.05 | — | 3 —
Tio 2 ,% | 0,17 | 3 —3 —0.0 | 0.95 | — | ||
10-40 | ≤45 | — | ||||
Удельная поверхность (M 2 / G) | 1.75 | 5-9 | 0,4-9 | 16.455 | 12.174 | 30.4-27.4 |
Низкая прочность бетона на растяжение обусловлена распространением одиночной внутренней трещины. Если трещина сдерживается локально, распространяясь в соседнюю с ней матрицу, зарождение трещины замедляется и достигается более высокая прочность бетона на растяжение [13]. Этого ограничения можно добиться, добавляя в бетон волокна небольшой длины. В дополнение к увеличению прочности на растяжение добавление волокон повышает сопротивление усталости [14], поглощение энергии, ударную вязкость, пластичность и долговечность [15]. Свойства нескольких армирующих волокон, которые использовались в цементных композитах, показаны в Таблице 2. На основе модуля упругости волокна подразделяются на две основные категории, а именно: жесткое внедрение и мягкое внедрение. Волокна с более высоким модулем упругости, чем у цементного раствора, называются жесткой интрузией, а волокна с более низким модулем упругости, чем у цементного раствора, называются мягкой интрузией [16]. Сталь, углерод и стекло представляют собой жесткие интрузионные волокна, а полипропиленовые и растительные волокна представляют собой мягкие интрузионные волокна.волокна с низким модулем упругости вряд ли улучшат прочность, но улучшат устойчивость к ударам и ударам благодаря способности к удлинению. Однако волокна, имеющие более высокий модуль упругости, делают бетон прочным и жестким [16].
|