Стеновые блоки своими руками. Дом из пустых бутылок
В этой статье мы рассмотрим применение альтернативного варианта для возведения стен — из бросового, отходного материала.
Вы узнаете о том, как построить стены из пустых стеклянных и пластиковых бутылок. В статье приведена подробная инструкция с рецептами раствора и видеоматериалы.
В то время как подавляющее большинство размышляет над сомнительной перспективой жить в бутылочном доме, немногочисленные энтузиасты воплощают эту идею в жизнь. Мысль использовать бутылки вместо камня в кладке стены вполне справедлива, учитывая изобилие бросового стройматериала и количество потенциальных поставщиков.
Бутылки. Блоки
Использование стеклянной тары в стеновом материале — непривычное и сомнительное занятие на первый взгляд. Однако, если «переосмыслить» обычную пустую бутылку, мы увидим воздух, заключённый в довольно прочную оболочку. Как известно, именно воздух с его низкой теплопроводностью является эффективным термобарьером. Эффект пустот в стеновом материале успешно реализован в традиционном шлакоблоке.
Для того чтобы изготовить бутылочный блок, понадобится примитивный вибростанок для блоков. Инструкцию по его сборке мы рассмотрим в следующей статье. Если использовать бутылки, его конструкция упростится до стальной коробки без дна и верха с вибромотором. И ещё понадобится ручной пресс, который можно изготовить из подручного материала.
Блоки для стен из бутылок видео
В самом процессе производства блоков нет никакой «изюминки» — он прост и понятен: подсыпаем смесь, укладываем бутылки, снова смесь и снова бутылки. Правило одно — стекло не должно соприкасаться со стеклом и стенками короба.
Бутылки. Кладка
Кладка бутылок осуществляется аналогично каменной, высота бутылки — толщина стены. При оценке долговечности такого сооружения возникают сомнения в надёжности сцепления раствора с гладким стеклом. Оно практически нулевое. Поэтому нагрузку следует распределять более эффективно. Например, прокладывать полимерную сетку каждые 3–4 ряда.
Подбирая материал по цвету, можно создавать стены с узорами и незатейливыми панно в виде полос, цветов и геометрических фигур. Преимущества стекла в наружной отделке — гладкая беспористая поверхность не накапливает грязь и пыль и очищается легко. К тому же в помещении всегда будет естественная подсветка.
Бутылочный дом видео
Благодаря развитию стеклодувной промышленности, появилась возможность использовать бутылки прямоугольного сечения, которые к тому же имеют рельефную поверхность, улучшающую сцепление с раствором.
Зарубежные энтузиасты не отстают от наших. Разумеется, не от избытка средств, а из экономии они строят стены из пластиковых бутылок, заполненных землёй.
Дом из пластиковых бутылок видео
Одним словом, «бутылочный дом» — реальность. Требование к конструктиву единственное — чтобы раствор полностью облегал поверхность стекла и стенки не соприкасались. Это обеспечит оптимальное распределение нагрузки для устройства полноценной стропильной системы и проёмов достаточного размера.
Раствор для «бутылочной кладки и блоков
В зависимости от этажности и конструкции кровли раствор для блоков и кладки следует подбирать по-разному. Мы рассмотрим основные случаи переменного состава раствора в «бутылочной» конструкции на разных уровнях.
Фундамент, подземная часть, нижняя часть стен (60 мм). Эти элементы не должны содержать потенциально хрупких элементов. Домов из бутылок единицы и построены они в пределах последних 15 лет, поэтому конструкция не изучена лабораторным способом. Кроме того, бутылка не имеет статус строительного материала. Ответственные участки следует выполнить из традиционно надёжных материалов — бетон, кирпич, заводской стеновой блок.
Стены первого этажа. В кладочный раствор можно добавить шлак для утепления. Также есть вариант замены песка шлаком. Состав раствора для бутылочной кладки и блоков несущих стен 1-го этажа:
- Обычный кладочный — 1 часть цемента, 3 части песка.
- Утеплённый кладочный — 1 часть цемента, 1 часть песка, 2 части шлака.
- Раствор на шлаке — 1 часть цемента, 3 части шлака.
- Раствор на опилках — 1 часть цемента, 2 части опилок, 1 часть песка или шлака.
Особое внимание следует обратить на толщину слоя раствора. При кладке блоков она стандартная — 10–20 мм, при кладке бутылок её лучше изменять. В нижней части стен применяйте слой 40–50 мм, постепенно уменьшая его до 20–30 мм в верхней части. Этим вы усилите кладку снизу, одновременно облегчив её сверху.
Армирование — залог стабильности стен, поэтому обязательно используйте кладочную или полимерную сетку каждые 2–4 ряда. В качестве материала лучше применять толстостенные бутылки от шампанского.
Любой альтернативный материал всегда вызывает сомнения, тем более, когда он не считается строительным. Из пустых бутылок можно выполнить не только стены, но и другие элементы самодельного экстерьера — навесы, парники, козырьки (пластик) или просто светопрозрачное заполнение окон — вместо дорогих стеклоблоков. Главное здесь — решительность, аккуратность и соблюдение правил.
Виталий Долбинов, рмнт.ру
rmnt.mirtesen.ru
Как сделать строительные блоки — основной материал в возведении здания
Блок — очень распространенный материал в строительстве. Из них можно сложить любое строение: дом, баню, гараж, хозблок. Стены из блока обладают хорошими прочностными характеристиками, тепло и звукоизоляционными свойствами. Иметь этот строительный материал в своем свободном распоряжении настолько выгодно, что многие задумываются, как сделать строительные блоки своими руками.
Виды строительных блоков
Основой каждого бетонного блока является цемент, песок и вода. Помимо этого, используется наполнитель. В зависимости от его типа, получаем тот или иной вид блока.
- Шлакоблок. В качестве наполнителя используются отходы металлургического производства. Такие блоки наиболее часто используют в строительстве подсобных помещений. Шлакоблок не горюч, устойчив к промерзанию, удобен в кладке
- Блок из опилкобетона. Самый удобный вид блока. Он легко сверлится, режется, устанавливается. Является самым «теплым» блоком из всех бетонных. Небольшой вес делает процесс кладки удобным и быстрым. Наполнителем в смеси для строительного камня являются опилки. Для того, чтобы избежать их гниения в блоке, и, тем самым его вспучивания, перед закладкой в бетон они вымачиваются в растворе гашеной извести. Но можно просто перемешать свежие опилки с известкой «пушенкой», и использовать по прямому назначению.
- Блок с наполнителем из гравия различной фракции. Наиболее «холодный» блок. Он довольно таки тяжел, что увеличивает трудоемкость при его кладке. Является обычным бетонным блоком.
- Керамзитный блок. Наполнитель-керамзит. Такой блок обладает хорошими теплоизоляционными свойствами, довольно легок и прочен, удобен в кладке.
- Блоки с наполнителями из хвои, древесной стружки, колотого камня, измельченного строительного мусора. Если знать процесс изготовления камня, то не возникнет вопроса как сделать строительные блоки своими руками.
Процесс изготовления блоков
Для их изготовления имеется специальное оборудование: станки для производства строительных блоков. Они рассчитаны на одну, две, три и более блокформ. Такой станок представляет собой вибростол и, собственно, сами блокформы — емкости для формования блоков. Стандартный размер изделия — 190x190x390 см. Блокформа имеет множество съемных перегородок, которые позволяют производить разные размеры бетонных изделий в пределах установленных. Также она оборудуется приспособлением для изготовления пустотного блока. Эта деталь представляет собой два (или три) соединенных отрезком стального прута цилиндра, которые вставляются в блокформу перед заливкой в нее бетона. Эти цилиндры после затвердевания камня изымаются, и, таким образом получаются пустоты в готовом блоке. Этот способ позволяет значительно сэкономить на цементном растворе.
Процесс изготовления блока на этом оборудовании довольно прост. В бетоносмесителе изготавливается раствор с выбранным или доступным наполнителем. Блокформа смазывается отработанным машинным маслом для облегчения процесса выемки готового изделия. Далее в нее заливается цементный состав.
Включаем вибростол и в течение 1,5-2 минут происходит процесс формования изделий. Посредством вибрации из бетона изгоняются пузырьки воздуха, состав уплотняется, выходит лишняя жидкость. После формования поверхность блока разравнивается шпателем.
Затем блокформу переносят в место сушки изделий. Им может служить как пропарочная камера, так и обыкновенный участок земли с навесом над ним. Поверхность, на которую выкладываются для сушки блоки, должна быть ровной и горизонтально выдержанной. Благодаря особому устройству блокформы, выемка изделия не составляет труда. Из-под формы вытягивается лист железа, который является ее нижним основанием, а сами боковые стенки поднимаются вверх. Готовый блок остается в месте просушки в течение нескольких дней. Затем он переносится в место складирования.
semidelov.ru
Стеновые бетонные юлоки — как сделать своими руками — Блоги
Строительство частного дома на дачном участке это непростое и очень важное дело, у нас строят такие дома из стеновых стандартных блоков. Из кирпича красного глиняного уже почти не строят дома по той причине, что кирпичный дом строится дольше, он будет иметь больший вес а, следовательно, и давление на фундамент будет больше. Также дом из кирпича стоит дороже, а тепло сберегающие характеристики и звукоизоляция также хуже, чем у ряда других стеновых материалов, также установка несколько сложнее, а раствора на кладку уходит больше. Когда пришло время строить мою свою дачу, то я для этого специально отпуск взял на работе, а сам дом решил строить дом и гараж только из стеновых блоков. Но опять же выбрать конкретный вид блока не так просто, сегодня строительный рынок богат такими блоками, например газобетонными, пенобетонными, керамзитобетонными и так далее. Ракушечник я решил не использовать, просто не совсем я доволен его качеством, он хрупкий и не такой прочный, поэтому для дачи этажностью более двух этажей он не подходит, во всяком случае, я так считаю. Долго я, значит, выбирал какой стеновой блок лучше купить, но пришла мне в голову отличная идея — почему нельзя сделать такой блок самому?
В принципе состав всех готовых таких блоков идет при добавлении основных компонентов, таких как бетон, шлак и уголь, а также некоторые добавки. Делать блоки такие намного проще чем это может казаться, блоки стеновые я приготовлял двух стандартных размеров, то есть 510x250x150 и 250x250x150 мм, а раствор для блока делать не сложно — цемент 500 две части, вода одна часть, песок одна часть, а также немного гравия и шлака угольного вместе примерно 0,5 частей. Для таких блоков продаются специальные формы-станки, устройство станка очень простое, он имеет форму из металлического сплава в виде коробки с толщиной стенок более 3-4 см. Такая металлическая форма имеет внутри от 3 до 5 цилиндров, благодаря которым внутри блока получаются отверстия — это так называемый пустотелый блок. Сбоку такой формы установлен небольшой мотор для вибрации раствора в форме, то есть, чтобы воздух, получаемый неизбежно в растворе выходил из блока при заливке смеси. Форма очень простая, но в принципе ее не обязательно покупать, а можно сделать и самому, вместо мотора удалить воздух из раствора можно и вручную. Такие блоки стеновые получаются дешевле, чем обычные блоки, также не надо тратить деньги на доставку блоков на участок и разгрузку их.
Только если будете сами делать такие блоки, то цемент лучше подбирайте качественный не ниже чем марка 300-400, это очень важно. Песок должен быть средней или крупной фракции, сильно мелкие и пылеватые пески не подходят, также естественно нельзя применять морской песок с большим количеством солей, песок должен быть только речной. Если добавляете гравий то лучше использовать размеры гравия не менее 5 мм и не больше 15 мм, угольный шлак добавляйте поменьше, можно еще добавить немного битого кирпича. Раствор размешать тщательно и заливать его в очень густом виде в форму, включаете потом мотор для вибрации на 5-10 секунд, потом надо выключить мотор и вставить специальный прижим и опять включить вибрацию на 5 секунд. Примерно через 10-15 минут блок готов и его можно снимать с формы, теперь блоку надо дать высохнуть одну неделю и можно его уже применять в строительстве. Можно добавлять только цемент и песок для изготовления бетонных пустотных блоков, можно добавлять шлак, гравий и битый кирпич для изготовления шлакобетонного блока. Прочность таких блоков очень большая также блок имеет отличные звуко- и теплоизоляционные характеристики, так что можете смело сами делать такие блоки стеновые, они ничем не хуже обычных блоков продаваемых на рынке.
Зарегистрируйтесь, чтобы голосовать!
Проголосовало: 0
Оценка: 0
Стеновые блоки, кирпичи из грунта своими руками — Строительство, обустройство — Каталог статей
Стеновые блокиБезобжиговые материалы из глинистого грунта во многих районах все еще являются основными стеновыми материалами. Сырьем для изготовления безобжиговых стеновых блоков или камней (саман, грунтоблоки, кирпич-сырец) служат обычные глинистые (связные) грунты, из которых различными способами формуют стеновые блоки. Безобжиговые грунтовые стеновые блоки изготовляют из различных по качеству грунтов, без добавки или с добавкой к ним различных веществ: связующих материалов, стабилизаторов, утеплителей (в зависимости от назначения строящегося из них здания и его местонахождения).
Кирпич-сырец представляет собой полуфабрикат при производстве обожженного строительного кирпича. Его используют в качестве основного стенового материала для одноэтажных построек, с небольшой нагрузкой на стены. Изготовляют кирпич-сырец из средних по жирности глин. В жирные глины в качестве отощителя добавляют песок. Содержание песка в глине должно быть в такой пропорции, чтобы линейная усадка после сушки не превышала 6%. Содержание песка в глине нельзя допускать более 35%. Подготовка сырья, формовочной массы и формовка кирпича-сырца аналогичны операциям при производстве красного строительного кирпича.
Среднеазиатский кирпич-сырец формуют преимущественно из лёсса. Для этого на площадке, где должна производиться формовка сырца, вскрывают верхний растительный слой земли и перекапывают лёсс на глубину двух штыков. Перекопанный лёсс заливают водой и оставляют на 2—3 суток. После того как лёсс достаточно размокнет, его перелопачивают и переминают до получения однородной массы нужной пластичности. Лёсс легко поддается обработке, и поэтому при изготовлении из него кирпича-сырца можно обходиться без специальных глиномялок.
Формовка кирпича-сырца производится как вручную, так и машинным способом. При формовке сырца на кирпичеделательных агрегатах целесообразно в формуемую массу вводить стабилизаторы, повышающие водостойкость сырца. В качестве стабилизаторов обычно используют остатки растений и листьев, сгнивших без доступа воздуха, каменноугольные и газовые смолы и особенно торфяную крошку.
В районах, где отсутствует торф, стабилизатор можно приготовить из ботвы овощных растений, сорных трав и древесной листвы, подвергнув их гниению в специальных ямах. Для этого в глинистом грунте выкапывают яму, засыпают в нее траву или ботву и заливают жидким глинистым раствором. В таком состоянии массу выдерживают в течение 80—90 суток.
Отформованный кирпич-сырец сушат
на открытых площадках или в закрытых сараях. Режим и технология сушки
кирпича-сырца аналогичны тем, которые применяются при производстве
красного строительного кирпича.
Кирпич-сырец должен быть правильной
формы, не иметь трещин от сушки; брошенный на землю с высоты 1,5—1,8 м
не должен ломаться, временное сопротивление его сжатию должно быть не
менее 20 кг/см2, объемный вес 1800—1900 кг/м3, коэффициент
теплопроводности 0,7. Кирпич-сырец представляет собой хрупкий материал, а
поэтому его не следует перевозить на дальние расстояния.
Саман изготовляют из жирной пластичной глины с добавкой в нее соломенной сечки в количестве 10—20 кг на 1 м3 глины. Чтобы более точно определить потребное количество соломы для добавки в глину, изготовляют несколько пробных блоков. Для этого берут 1 м3 глины, делят его на пять равных частей и в каждую из них добавляют солому в различных количествах (кг): в одну часть — 4, во вторую — 3,5, в третью —3, в четвертую —2,5 и в пятую —2. Затем каждую часть глины хорошо перемешивают с соломенной сечкой и изготовляют саман, который после высушивания подвергают соответствующим испытаниям и по лучшему образцу устанавливают норму добавки соломы.
Практически саман изготовляют следующим образом. На
площадке, отведенной для изготовления самана, срезают верхний
растительный слой и размечают яму для замеса (обычно круглую, диаметром
5—6 м). Грунт в яме перекапывают на два штыка, затем в яму загружают
резаную солому (длина соломенной резки 5—12 см) и заливают водой. По
истечении 2—3 суток глину хорошо перемешивают.
Саман можно формовать и
на кирпичеделательных агрегатах типа «Колхозный». Для этого на головку
пресса устанавливают мундштук соответствующих размеров. Отформованный
саман раскладывают на ровной площадке «на платок», а через 2—3 дня
«ребруют». Еще через 2— 3 дня его складывают в «козелки». Когда саман
достаточно окрепнет, его укладывают в разреженные пирамиды по 120— 150
штук в каждой и оставляют до полного высыхания.
Окончательно высушенный саман отправляют на стройку или укладывают в плотные клетки и укрывают досками, камышом или соломенными матами для предохранения от дождя. Саман считается окончательно высохшим, когда в изломе в середине его не будет темных пятен. Саман хорошего качества должен иметь ровные кромки, хорошо тесаться топором, иметь хорошую гвоздимость (не раскалываться, когда в него вбивают гвоздь толщиной 5—6 мм и длиной 150 мм), не разбиваться при падении на землю с высоты 1,5—1,8 м и не размокать в воде в течение 8 часов. Прочность самана хорошего качества должна быть около 25 кг/см2.
Грунтоблоки изготовляют из обычных кирпичных глин и любых грунтов, обладающих достаточной связностью, с содержанием в них 12—18% влаги, то есть в состоянии естественной или карьерной влажности грунтов. Пригодность грунта для изготовления грунтоблоков можно предварительно определить по двум признакам: во-первых, при копке пласт грунта не должен рассыпаться на заступе; во-вторых, сжатый в руке грунт должен образовывать ком, не рассыпающийся при падении на землю с высоты 1 м. Более точное определение пригодности грунта проводят лабораторным путем.
В тяжелые грунты (с содержанием глины свыше 20%) для уменьшения веса блоков и их теплопроводности вносят легкие малотеплопроводные добавки (шлак, опилки, мякину, лузгу и т. п.). Для повышения водостойкости в смесь идущую на изготовление блоков, вводят стабилизаторы в виде глино-смоляных или известково-смоляных эмульсий.
Известково-смоляную эмульсию приготовляют следующим образом: в растворомешалку или бочку наливают 4—5 частей воды, затем в воду добавляют столько же известкового теста, все это хорошо перемешивают и в смесь добавляют одну часть смолы. При вливании смолы продолжают перемешивать всю смесь до получения однородной эмульсии.
Заготовленный
для грунтоблоков грунт, чистый от мусора, засыпают в растворомешалку,
заливают эмульсией и хорошо все перемешивают. Затем добавляют
наполнитель и всю массу перемешивают до однородного состава. При
подготовке грунтовой массы ручным способом грунт засыпают на выровненную
поверхность двумя грядами высотой 15—20 см и поливают
эмульсией-стабилизатором, затем в гряды добавляют наполнитель и всю
массу хорошо перелопачивают (при введении органических добавок их
следует увлажнять до смешивания с грунтом). Перемешанная масса должна
иметь влажность 14—20%.
Формуют грунтоблоки вручную — трамбовками,
на ручных станках, а также на механизированных станках или
кирпичеделательных агрегатах.
http://www.domremstroy.ru/
Саманные кирпичи
Мы решили попробовать совмещённую технологию, и часть стены будем делать набивным способом, другую – выкладывать из предварительно сделанных и высушенных саманных кирпичей.
Мы так решили, когда у нас собралось много людей, а опалубка из поддонов ещё не была сделана. Пока одни её делали, другие делали кирпичи. Их мы будем использовать на надземную часть стены.
По опыту мы определили, что:
- такую работу лучше всего выполнять впятером: двое месят саман, двое делают кирпичи на форме, один носит или возит на тачке глину, солому и готовый саман.
- лучше выкопать яму глубиной на один-полтора штыка с отвесными краями и плоским горизонтальным дном. Если сделать глубже – трудно будет хорошо перемешать слишком толстый слой самана; уж лучше делать шире. На пологих краях или неровном дне труднее мешать и легко поскользнуться, на наклонном дне вода сливается в одну сторону.
- яма застилается прочной водонепроницаемой тканью (тент, брезент и т. п.; мы использовали ткань от военной палатки), выходящей за края ямы (фото 1). Водонепроницаемая ткань существенно экономит воду, не давая ей уходить без пользы под землю. Кроме того, перемешивание облегчается перетягиванием ткани с саманом (фото 3).
- вначале яма заливается водой, потом в неё засыпается глина (лучше её сразу же и размешивать). И только когда в яме будет раствор консистенции жиденького теста, на него насыпается и втаптывается ногами солома (фото 2). Если раньше добавлять солому – она будет плавать по поверхности «лужи», если позже – трудно будет втоптать солому в загустевшую глину.
- Саман для заполнения формы должен быть по консистенции как средне-густое тесто. Так, чтобы водяная плёнка на поверхности глины ещё блестела, но «лужиц» воды или очень жиденькой глины нигде уже не было. Для этого можно в конце замеса понемногу и равномерно добавлять воды, глины или соломы. Кирпичи из более жидкого самана будут оплывать, растекаться по земле. Более густой саман трудно будет извлечь из формы, не испортив кирпич.
Мы использовали две формы: одну на один большой кирпич, металлическую (фото 4), другую на 4 кирпича чуть поменьше, деревянную без дна (фото 5). Деревянную изготовили на месте, и большинство кирпичей делали именно в ней, как более удобной и производительной.
Перед заполнением ячейки этой формы нужно большой влажной тряпкой или щёткой очистить от прилипшего самана и хорошо промочить (иначе кирпичи будут плохо вылезать и часто получаться ущербными, так как куски глины из них останутся на форме). Особенно нужно очищать углы ячеек. На дно ячеек застилается солома или скошенная трава, чтобы мокрый саман не прилипал к земле (фото 6).
Заполнив ячейку, разравниваем саман сверху (фото 7). Форму поднимают 2 человека за торцы: разом, медленно и аккуратно. Если нужно, третий помогает кирпичам вылезти вниз, аккуратно надавливая на них сверху (фото 8).
И вот готовы сразу четыре кирпича. Они на земле остаются сохнуть (от 2 – 3 дней до недели и более, в зависимости от погоды). А пустая форма ставится рядом, снова промывается и делается следующая четвёрка кирпичиков (фото 9).
Так за один день нам удавалось изготовить до сотни кирпичей.
Фото 1.
Фото 2.
Фото 3.
Фото 4.
Фото 5.
Фото 6.
Фото 7.
Фото 8.
Фото 9.
Фото 10.
Фото 11.
http://yav.org.ru
poselenie.ucoz.ru
Опилкобетон своими руками для изготовления стеновых блоков — каталог статей на сайте
Теплые стеновые блоки из опилкобетона изготовить самостоятельно вполне реально.
Безусловно, повозиться придется, зато в результате получим экономию немалую на материале для постройки дома, либо другого строения. К тому же, стеновые блоки из опилкобетона относятся к категории теплых, поэтому, если нужен не конструкционный материал, а утеплитель, опилкобетон и в этом плане выгоден – теплоизолятор он мощный.
Формы для опилкобетонных блоков
Формы для блоков нужны разборные. Можно использовать для их изготовления тонкие строганные доски, а изнутри прикрепить пластик или кровельную сталь, чтобы изделия легко вынимались. А можно просто прикрепить толстую полиэтиленовую пленку. Хотя сегодня не обязательно мастерить формы для блоков своими руками: в продаже есть специальные пресс формы из прочного пластика для изготовления блоков распространенных размеров. Что хорошо в таких покупных формах – выверенная геометрия, а также наличие пуансонов – верхних элементов наподобие крышек, с помощью которых смесь в формах трамбуется.
Конечно, чем больше строение, которое вы хотите возвести, тем больше форм для блоков понадобится. Можно обойтись и минимальным их количеством, но тогда изготовление блоков растянется во времени до невозможности. Дело в том, что форму с крупных блоков снимают приблизительно через 5 дней, а с более мелких изделий – через 3 дня. Исходя их этого, лучше все-таки обзавестись большим количеством форм (хотя бы, 10-15 шт.).
Размеры стеновых блоков из опилкобетона различны. Имейте в виду, что при высыхании изделия дают усушку, поэтому формы нужны чуть больше по размерам (примерно на 10%).
Опилкобетон своими руками: рецепты
1. Опилок – 12 ведер, цемента – 3 ведра, глины – 5 ведер, вода – 10-15% от объема замеса.
+ Изделия из опилкобетона, приготовленного по этому рецепту, обладают большим запасом прочности, а также высокими теплоизоляционными свойствами.
2. Опилки – 10 ведер, цемент – 3 ведра, известь – 10 ведер, вода – 10-15% от объема замеса.
* Теплоизоляционные свойства стеновых блоков их опилкобетона по данному рецепту невысоки, их изготавливают, в основном, для строительства подсобных помещений (например, гаражей).
- Соединяют цемент с песком.
- К массе добавляют известь (по второму рецепту).
- Всыпают опилки.
- Вливают воду.
На каждом этапе все ингредиенты хорошо перемешивают – вручную или в бетономешалке. Массу укладывают в формы, утрамбовывают как можно тщательнее, чтобы в теле стеновых блоков не осталось пустот.
Стеновые блоки из опилкобетона к началу возведения стен должны быть готовы, то есть, хорошо высушены. Времени на сушку понадобится немало: в зависимости от размеров блоков – от 1,5 до 3-х месяцев.
ЕЩЕ СТЕНОВЫЕ БЛОКИ
Теплостен или полиблок
Стеновые блоки арболит
Как рассчитать нужное количество блоков
Поризованные блоки
Стеновые блоки керамзитобетонные
Бетонные блоки своими руками
Хочу больше статей:
Оставьте Ваш отзыв
Average rating: 0 reviewsTags:
газобетон панели штукатуркаwww.domstoy.ru
Бетонные блоки стеновые — как их облицевать просто, недорого и самим! | Бетон и строительные технологии
Главная >> Сделай своими руками >> бетонные, блоки, стеновые, облицовка, фасадов, облицовочные, материалы, офактуривание, технология
admin 16.01.2014
Уважаемые коллеги и посетители моего сайта — о бетоне и строительных технологиях. Вы, конечно прекрасно знаете, что сегодня основным строительным материалом для возведения стен, являются бетонные блоки стеновые, это могут быть ячеистые стеновые блоки из пенобетона или газобетона, керамзитобетона, арболита, грунтоблоков и так далее.
Фасадная часть стеновых конструкций, в которых используются бетонные блоки стеновые в обязательном порядке подлежит защите от внешней среды, так как они впитывают влагу, выветриваются и чувствительны к любым изменениям погоды, что влияет на их характеристиках и долговечности.
Их внешний вид тоже оставляет желать лучшего, это некая безликая «серость».
Как лучше облицевать стеноые блоки бетонные и из других материалов?
Сегодня есть десятки способов сделать фасад красивым и устойчивым к атмосферным явлениям:
- облицовка кирпичем или другими отделочными материалами;
- покрытие акриловыми красителями;
- штукатурка ;
- вентилируемые фасады;
- покрытие гелькоутом;
- другие облицовочные материалы;
И многое, многое другое, не буду все перечислять, Вы наверное и сами сможете добавить еще десяток вариантов. Нужно отдать справедливость, среди этих способов есть и весьма достойные, но у них всех несколько существенных недостатков:
- по большей части они дороги;
- требуют периодического обновления или существенного ухода;
- они тиражируемы, то есть повторяемы и не уникальны;
Вот я и хочу предложить Вам простой, недорогой, уникальный, неповторяемый по дизайну способ и технологию, как офактурить стеновые блоки, вернее только их фасадную часть.
Вы будете приятно поражены насколько это просто, ведь недаром говорят «Все гениальное, как правило просто, но не все простое гениально».
Технология облицовки и офактуривания стеновых блоков
Сразу хочу предупредить, эту технологию можно внедрить при следующих условиях:
- на мой взгляд это подходит в основном для частного домостроения
- если Вы не обременены излишками денежных средств – думаю таких большинство
- Вы хотите, чтобы Ваш дом, вернее его фасад был уникальным и неповторимым – таких неверное тоже будет много
- Вы человек творческий и как сейчас говорят креативный – таких наверное поменьше
- Вы умеете и любите делать, что то своими собственными руками – таких я думаю еще меньше
Так вот, если Вы соответствуете этим критериям читаем дальше, а впрочем остальным тоже советую прочесть, а вдруг да понравится.
Перейдем к сути технологии, если коротко и в нескольких словах, это нанесение тонкого фактурного слоя 3-6 мм из цветной цементно песчаной смеси на стеновые блоки методом виброформования.
Причем, сцепление фактурного слоя и блока происходит идеально и как говорят «намертво», из за специфики структуры бетона и особенно ячеистого, подробнее почитайте здесь мою ранее опубликованную статью и еще одну и еще .
Теперь немного подробнее. Что для этого нужно?
— вибростол, мешалка, формы.
— песок, цемент, пигмент.
Как видите, оборудование самое простое, причем его можно взять на время в аренду, в зависимости от объема и наличия форм, это максимально месяц.
Подготовительные работы при облицовке стеновых блоков
Итак, подробнее о подготовке и технологии:
- Вам следует выбрать пластиковые формы по размеру точно соответствующие размерам вашего блока;
- Рельеф дна формы выбираете исходя из предполагаемого дизайна фасада и естественно Ваших предпочтений. Для экономии, высоту или глубину формы выбираете минимальную;
- Сначала купите по 2 штуки с разным рисунком, когда офактурите убедитесь. Что рисунок Вам подходит, часто офактуривание на блоке выглядит, вернее смотрится несколько чем на форме;
- Если рисунок Вас устраивает, купите такое количество форм, сколько изделий Вы можете сделать в день, распалубка производится через сутки;
- Вибростол желательно выбирать минимального размера, площадка стола должна быть чуть больше размера примерное 5 форм. Более подробно как выбрать вибростол можно почитать здесь, по этой ссылке;
- Бетономешалку можно взять «Грушу» самого минимального объема. Конечно в идеальном варианте лучше бы найти мешалку принудительного действия, в принципе подойдет и растворомешалка, это зависит от ваших возможностей;
- Песок нужно брать обязательно речной, он уже как правило мытый, лучше купить на бетонном заводе можно и карьерный, но он должен обязательно быть мытым, в нем не должно быть глины;
- Цемент берете обычный ПЦ500Д0 или ПЦ400Д0,можно в принципе и Д20, конечно в идеально варианте лучше взять белый цемент, офактуривание будет просто великолепно красивое;
- 9 Пигменты выбираете исходя из Ваших предпочтений по дизайну, они есть на любом строительном рынке, обычно это окиси железу, хрома, никеля меди, и так далее, цвет на пакете всегда обозначается;
Пигмент не должен растворяться в воде!
Дозировка пигмента обычно 3-8% от массы цемента, чуть ниже я дам дозировку состава для цементно песчаных смесей для офактуривания,
Подготовку закончили. теперь подробнее о составах облицовочной смеси
Ориентировочный состав цементно песчаной смеси марки М250, П1, на1 куб:
- Цемент ПЦ500 – 400,0 кг
- Песок 1600,0 кг
- Вода 220,0 литров
- Пигмент 16,0 – 32,0 кг (в зависимости от желаемого получить эффекта)
- Если цемент ПЦ400 – 440,0 кг, тогда песка будет – 1560,0 кг
- Рецептура дана по сухому песку, придется «на глазок» учитывать влажность песка (обычно если он не находился под дождем), средняя влажность песка примерно равна 7,0%, поэтому сами пересчитайте, то есть по весу добавьте песка на 7,0% и убавьте на такой же вес воду.
Я пишу как делать правильно, но обычно загружают ведрами (пересчитайте тогда по весу все компоненты на ведро), а зачастую и лопатами, что делать не рекомендую, это уж совсем примитив.
Дозировка компонентов облицовочного состава для офактуривания
Делаем это так:
- Дозировку соответственно пересчитываете на объем Вашей мешалки, я думаю это понятно.
- Загружаете в работающую мешалку все компоненты в такой последовательности – песок, цемент, вода и пигмент, причем воду выливайте не всю, оставьте примерное 10,0%.
- Перемешиваете не менее 3,0 минут (в зависимости какая у Вас мешалка), консистенция смеси должна быть в виде густой но «рассыпчатой каши», при необходимости добавляйте «резервную воду».
- Для «тренировки» попробуйте без пигмента, он очень дорогой, когда получится нормально делайте с пигментом.
- Нормально ли получилась консистенция можно проверить только на вибростоле.
- Для этого выложите пластиковые формы на вибростол, включите его и ковшом или мастерком, накладываете смесь, чтобы толщина фактурного слоя была не более 6,0 мм, вибрируете примерное 30 секунд, смесь должна равномерно «растечься» по форме, сверху должен появиться тонкий слой «цементного молочка», если молочка много. следует убавить воды.
- Все это приходит с опытом, ну наверное испортите штук 5-10 проб. Не отчаивайтесь, я тоже через это прошел лет 20 тому назад, когда делал тротуарную плитку. Помните наверное лозунг «Тротуарная плитка – победительница асфальта», не занимался этим только ленивый. Как говорят писатели, все мы выросли из Гоголевской шинели.
- Двигаемся дальше. Итак вы добились нормальной консистенции, нужной цветовой гаммы и нужной толщины слоя. Когда вы отвибрировали смесь в форме и получили желаемый результат, вибрацию останавливаете, укладываете в форма блок и снова включаете вибратор примерное на 10,0 секунд.
- Забыл сказать, при большом весе блока под форму желательно сделать, что то вроде поддона, иначе трудно будет поднять форму вместе с блоком, хотя можно брать руками прямо за верхнюю часть блока форма не упадет, ну в общем посмотрите сами. Как Вам будет удобнее.
- Снимаете форму вместе с блоком, переносите и укладываете на стеллаж, можно просто на пол, когда накопится дневная выработка, укрываете все это пленкой. В помещении кде будут находится изделия должно быть тепло. Не менее +20 градусов и выдеживаете около суток
- На следующий день аккуратно вынимаете изделия из формы и любуетесь результатами своего труда, как на картинке ниже, фактурный слой и блок срастутся, как говорят навечно.
[important] Хочу дать один совет из своего опыта, как сделать бетонные блоки стеновые с фоном одного цвета, « разводы» другого цвета, здесь нужно работать на контрастных цветах. К примеру Вы хотите на светло желтом фоне сделать синие разводы.
Делается это так:
- Основной фон делается как обычно, как я описал выше. Смесь для разводов приготавливается отдельно, в количестве примерное 5,0% от общей массы смеси. Для этого берется только цемент, пигмент и вода, замешивается вручную в любой посудине, консистенция должна быть в виде сметаны;
- Далее, если у Вас принудительная мешалка просто выкладываете эту смесь равномерно сверху на основную и включаете мешалку и делаете ровно 3 оборота, получится неравномерное распределение разводов, но в этом и есть прелесть и неповторимость рисунка;
- Если же у Вас Груша, это сложнее, но даже получается красивее. Делается это так, вываливаем приготовленную основную смесь в какое либо корыто, можно и просто на лист металла, смесь не растечется. Она же у нас достаточно густая, далее сверху раскладываем смесь для разводов, которую мы заранее приготовили и деревянным черенком от лопаты, мешайте недолго 1-2 минуты и не старайтесь идеально все перемешать, на а далее все делаете как описано выше, уверен результаты будут потрясающие.
- Не отчаивайтесь, если на каких то блоках офактуривание получилось немножко не так, эти блоки всегда можно будет уложить с тыльной стороны дома, где это не совсем бросается в глаза. [/important]
Ну а дальше уже строители будут укладывать офактуренные блоки в стену и Вы получите неповторимый фасад, как на картинках и ни у кого подобного не будет, это будет, как сейчас говорят, ваша фишка.
Ну вот на этом вроде и все по этой теме, постарался написать очень подробно, если что то непонятно, пишите отвечу всем, желаю Вам сделать Ваш дом красивым.
[note] Не забывайте также, вспомнить и основную мою рубрику, «Производство бетонных работ», для удобства пользования можете скачать +Файл со ссылками-Производство бетонных работ, там уже накопилось около 30 постов и посмотрите самое интересное, кстати «зима все таки» и посмотрите как делать, укладывать и ухаживать за бетоном в зимнее время. [/note]
Уважаемые коллеги, не забудьте зайти по ссылке на главную страницу моего сайта, найдете много полезной информации и не только о бетоне , стройматериалах, но и вообще о строительстве .
И еще напоследок рекомендую Вам скачать бесплатные видеоуроки «Как самим построить дом»!
На этом все, кликните по этой ссылке, чтобы посмотреть другие интересные и полезные материалы моего сайта.
Желаю Вам успехов.
Творите, дерзайте и побеждайте!
С уважением, Николай Пастухов.
Рекомендую прочесть похожие посты!
www.helpbeton.ru
Строительные блоки своими руками | Мастер
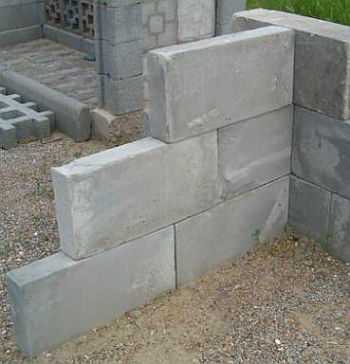
Как с экономить и зарабатывать, изготавливая строительные блоки самому.
Производство качественного блока в бытовых условиях было не доступно. Но если есть спрос, значит неотвратимо и предложение. И оно есть! Я из промышленной установки производства блоков из пенобетона сделал аппарат, который может изготовить любой желающий (имеющий необходимый бытовой инструмент), не уступающий по качеству производства заводскому, изготовлен на колёсах с возможностью буксировки легковым автомобилем. Изготовив такой аппарат, вы сможете сократить расходы на своём строительстве почти на 40%. Закончив свою стройку, вы сможете изготовить блоки для соседа и заработать при этом. При правильном подходе можно организовать маленькое производство на дому.
Что такое пенобетон — это смесь из цемента, песка, воды, пенообразователя, взбитая миксером при определённом давлении. Для того, чтобы получить такую смесь необходимы —
1. Ёмкость с герметически закрываемой крышкой, для загрузки компонентов и механизмом взбивания (перемешивания на высоких оборотах) Выдерживающая давление 3 кг.
2. Бытовой компрессор (достаточно с производительностью от 200 л./ час)
3. Ресивер для компрессора объёмом не менее 200л (обязателен) для давления 8 кг.
4. Форму (можно самодельную)
Процесс приготовления пенобетонной смеси длится 4-5 минут, загрузка компонентов и перемешивание в процессе загрузки 10 минут. Я сделал объёмом 0,17 м.куб. На выходе получается 0,32 м.куб. готовых блоков — 9 штук. Времени на заливку одного замеса уходит 20-25 минут. В результате — за 3 часа работы имеем 63 залитых блока (2,27 м.куб.) Время сушки в формах примерно сутки. Утром залили – на следующее утро вынимаем и готовим формы под следующую заливку. После обеда залили – на другой день после обеда вынимаем и готовим формы. И так получаем — за 3 дня имеем 63х3=189 блоков (6,82 м.куб.) При стоимости 1м.куб. 700 гривен в продаже, мы экономим (на простом, без добавления ускоряющих добавок, фибры, утепляющих компонентов) 280 гривен, при оплате помощнику 40 гривен с куба. При использовании моей технологии, разработанной многими месяцами проб, экономия составляет 150 гривен. Блок получается отвечающий всем стандартам марки 700, имеющий армировку и утеплитель, замешанный внутри блока. Стены из такого блока толщиной 20 см. не обязательно утеплять пенопластом, так как теплоизоляционные качества его улучшены. А при испытаниях он выдерживает давление 25 кг/см.кв. Обслуживать аппарат должны 2 человека.
Подробное описание изготовления форм для изготовления шлакоблоков в домашних условиях, а так же сам процесс изготовления шлакоблоков.
bazila.net