Блоки из глины и опилок
Опилкобетон относится к категории легких материалов. Он изготавливается из опилок, песка и цемента. Блоки, сделанные из этих материалов, широко применяются при возведении домов, коттеджей, хозяйственных построек. Из опилкобетона можно создать довольно прочный фундамент под любое строение.
Блоки опилкобетонные изготавливаются из цемента, опилок и песка.
Характеристики и разновидности материала
Опилкобетонные блоки обладают отличными санитарно-гигиеническими качествами. Поэтому их можно использовать даже при строительстве медицинских и детских объектов. Данному материалу не страшна механическая обработка.
Блоки из опилок обладают следующими характеристиками:
- отличной теплоизоляцией;
- огнестойкостью;
- устойчивостью к воздействию морозов;
- прочностью.
Характеристики опилкобетоных блоков.
Основной недостаток этого материала заключается в том, что они способны впитывать влагу.
В зависимости от плотности существуют следующие типы опилкобетона: М5, М10, М15 и М20. Наиболее плотным материалом являются блоки М5. Они применяются при строительстве фундамента и стен жилого дома. С помощью изделий М10 осуществляется реконструкция стен и подвальных помещений. Для проведения облицовочных работ и возведения перегородок внутри помещения подойдут блоки М15 и М20.
Несомненным преимуществом опилкобетона является то, что его можно сделать своими руками. Для этого нам понадобятся:
- опилки;
- цемент;
- песок;
- глина;
- вода;
- доски;
- толь;
- стальные стержни с резьбой;
- барашковые гайки;
- листовая сталь;
- вибротрамбовка;
- бетономешалка;
- полиэтиленовая пленка;
- сито с ячейками 10*10 мм;
- лейка;
- гвоздь;
- шпатель.
Изготовление форм для бетона
Форма для арболитовых блоков.
Для производства опилкобетонных блоков понадобятся формы. Если планируется выпускать материал больших размеров, то формы лучше сделать разъемными. Для небольших блоков подойдут формы, которые имеют ячеистую структуру.
Формы изготавливаются из досок толщиной 2 см, которые внутри покрываются листовой сталью. Благодаря наличию металла достигается максимальная гидроизоляция. Доски не должны впитывать влагу из рабочей смеси. Вдобавок из форм, отделанных листовой сталью, легче вынимать сделанные блоки.
Если решено использовать формы без стали, то перед укладкой приготовленной смеси и в процессе изготовления блоков конструкция обильно увлажняется. Нельзя допускать преждевременного высыхания опилкобетона.
При изготовлении форм следует учесть еще один нюанс. При высыхании смесь подвергается усушке, а материал становится по размерам немного меньше. Поэтому, если планируется делать материал определенного размера, то габариты формы должны быть на 10% больше блоков.
Деревянные формы устанавливаются на пластиковые или металлические поддоны, которые покрываются тонким слоем опилок. Если в опилкобетоне нужно сделать внутренние отверстия, то в форме должны находиться листы толя, свернутые трубочкой. Для ускорения производственного процесса создается сразу 15-20 форм. Это значительно сэкономит время для проведения последующих строительных работ.
Производство блоков
Сравнительная таблица характеристик блоков из различных материалов.
Хорошо высушенные опилки просеиваются через сито и перемешиваются с песком и цементом. В раствор добавляется заблаговременно смоченная и скомканная глина. Все компоненты снова перемешиваются, после чего в смесь постепенно из лейки добавляется вода.
Приготовление рабочей смеси производится исходя из того, на какие цели будет использован строительный материал. Для получения блоков из опилок с различной плотностью исходные материалы добавляются в следующих пропорциях:
- Из 20 кг опилок, 20 кг глины, 5 кг песка, 5 кг цемента делаются блоки с низкой плотностью.
- Из 20 кг опилок, 10 кг глины, 35 кг песка, 15 кг цемента — изделия со средней плотностью.
- Из 20 кг опилок, 5 кг глины, 50 кг песка, 20 кг цемента — блоки с высокой плотностью.
Качество полученного раствора проверяется таким образом. Немного смеси сжимается в руке. Должен получиться пластичный комок со следами от руки. Если на комке появились маленькие капельки воды, то это свидетельствует о плохом качестве раствора.
При возведении построек в местности, где преобладает влажная погода, понадобится осуществить дополнительную обработку смеси с помощью минерализаторов (вымачивание в известковом «молочке» и жидком стекле). Благодаря этому увеличатся влагоотталкивающие и огнестойкие показатели материала.
Сразу необходимо определить размер изготавливаемых опилкобетонных блоков. Обычно стандартной считается толщина материала, равная толщине двух красных кирпичей. При создании больших блоков следует учесть, что они будут высыхать в течение довольно продолжительного времени. Для ускорения данного процесса в материале делаются отверстия.
Делать блоки из опилок нужно в течение 1,5 часов после приготовления раствора. Иначе смесь начнет затвердевать. Смесь укладывается в формы слоями толщиной 15-20 см. Каждый слой тщательно трамбуется. Весь воздух из заготовок должен быть удален.
Состав блоков и расход цемента при изготовлении блоков из опилок.
На протяжении 3-4 дней происходит процесс отвердевания материала. Чтобы он достиг максимальной плотности, необходимо соблюдать определенный температурный режим. Оптимальная температура должна составлять +15ºС и выше.
Спустя 3 дня опилкобетон нужно проверить. Берется гвоздь и проводится по поверхности материала. Если на нем не появилась глубокая царапина, то блоки можно вынимать и укладывать для дальнейшей просушки. После чего происходит аккуратное изъятие пробок и толя. Формы разбираются.
Для приобретения максимальной прочности блоки выдерживаются еще в течение 3-4 дней.
Наиболее качественный материал получится тогда, когда он уложен на сквозняке с наличием небольших зазоров между блоками.
В таком случае процесс высыхания будет происходить более равномерно. Чтобы избежать намокания блоков во время дождя, его укрывают полиэтиленовой пленкой.
При окончательной сушке, которая займет более 3 месяцев, рекомендуется построить столбы из сделанных заготовок. В основании укладываются обожженные кирпичи. На них укладываются два опилкобетонных блока. На них в поперечном направлении укладываются два следующих блока. Процедура повторяется до тех пор, пока строительный материал будет удобно укладывать и впоследствии снимать.
Спустя 3 месяца материал должен полностью высохнуть и затвердеть. На нем не должно быть никаких трещин. Проверка качества опилкобетона осуществляется следующим образом. Берется один из блоков и сбрасывается с метровой высоты. Если материал останется целым, то можно приступать к строительству дома или хозяйственных построек.
Современная строительная индустрия предлагает хозяевам частных домов множество вариантов утепления стен, новые материалы обладают большим количеством положительных характеристик, но зачастую стоят слишком дорого, их трудно монтировать, они требуют особых условий эксплуатации.
Преимущества и недостатки
В последнее время возрастает популярность экологичного строительства без применения искусственных материалов и без вреда для окружающей среды. Глина — это доступный материал, а опилки — это способ безотходно использовать древесину. Опилки обладают очень низкой теплопроводностью и могут надолго сохранить тепло. Глина является связующим и дает опилкам возможность сохранять свои свойства в течение длительного времени.
- Утепление стен опилками обойдется очень дешево или даже бесплатно.
- Ремонт готового утеплителя можно выполнить самостоятельно и очень быстро. Достаточно замешать небольшое количество смеси и устранить неполадки.
- Полученный материал является отличным звукоизолятором наравне с самыми современными изобретениями строительной индустрии.
- Стены с глиной «дышат», на них не образуется конденсат, им не требуется монтаж пароизоляционного слоя.
Глиняную смесь не всегда можно применять в качестве утеплителя. Перед началом работ следует ознакомиться с недостатками материала и способами их устранения:
- Опилки — это легко воспламеняющийся материал и даже негорючий глиняный слой лишь незначительно снижает риск возгорания. Вблизи стен, утепленных глиной с опилками, следует внимательно следить за состоянием электропроводки, помещать ее в специальные короба, не подверженные возгоранию, глиняные стены необходимо оградить от печей с помощью негорючего материала.
- Применять глиняный утеплитель можно только внутри дома. При намокании теплоизоляционные характеристики материала значительно снижаются (после высыхания они полностью восстанавливаются).
- Материал обладает большой плотностью, для достижения хорошего теплоизоляционного эффекта придется нанести на стены толстый слой глины, перед началом работ следует убедиться, что несущая конструкция дома это выдержит.
Блоки из глины с опилками
Будет интересно — Глина для печки: обзор и подготовка материала.
Технология
Процесс утепления стен опилкобетоном — это непростой и трудоемкий процесс, требующий большой физической силы, выносливости и терпения. Выполнить все работы может один человек, но с помощниками процесс займет гораздо меньше времени.
Глина — это пучинистый материал, а значит, при замерзании в насыщенном водой состоянии будет сильно набухать и разрушаться. Утепление стен советуют выполнять летом, тогда до начала первых холодов смесь успеет высохнуть и набраться прочности.
Как приготовить раствор?
Глина с опилками хорошо работает как утеплитель для стен, только если материалы выбраны, подготовлены и нанесены правильно. Процесс утепления дома начинается с приготовления раствора и подбора материалов. Обе составляющие смеси можно получить бесплатно. Но стоит обратить внимание на их качество.
Глина
Материал доступен, стоит недорого, а в некоторых случаях его можно достать бесплатно. Следует обратить внимание на качество материала: не допускается наличие посторонних предметов в материале.
Можно использовать только что привезенную глину, но для получения идеальной консистенции смеси и долговечности утеплителя необходимо подготовить глину. Для этого ее заливают водой, перемешивают и оставляют на зиму. За это время материал переживает несколько циклов оттаивания и заморозки. Природная пучинистость вынуждает материал несколько раз расширяться и снова сужаться, глина становится однородной и пластичной.
Глина бывает «тощая» и «жирная», от показателя жирности зависит пластичность. При использовании «жирной» (пластичной) глины необходимо добавлять в состав утеплителя немного песка.
Глина для приготовления раствора
Глину перед началом работ необходимо подготовить: оставить на зиму в насыщенном водой состоянии.
Опилки
Опилки — это отход деревообрабатывающей промышленности. Их можно специально купить по невысокой цене на любом предприятии. Для утепления стен можно использовать разные опилки, обладающие своими полезными свойствами:
- Дуб почти не меняет свой размер и плотность под действием влаги, почти не гниет, стоек к воздействию бактерий.
- Хвойные опилки меньше чем остальные породы древесины подвержены образованию плесени из-за высокого содержания эфирных масел.
При утеплении стен можно использовать смесь из нескольких видов опилок.
Перед началом работ опилки необходимо подготовить:
- Сначала опилки избавляют от примесей, просеивают и промывают.
- После этого опилки тщательно высушивают.
- Сухие опилки необходимо пропитать составами, защищающими дерево от гниения, плесени и возгорания.
Опилки для приготовления смеси
Можно использовать смешанные опилки для получения лучших свойств теплоизоляционного материала.
Приготовление раствора
Чтобы правильно приготовить смесь, необходим набор инструментов:
Сначала в одной из бочек замачивается глина. Ее оставляют на несколько часов и периодически помешивая, ждут, когда она станет однородной. После этого 1–2 ведра глины заливают в бетономешалку и постепенно добавляют туда опилки в пропорции 3:2 соответственно.
Для достижения лучших теплоизоляционных свойств в смесь добавляют техническую соль, но в этом случае пропорция глины и опилок меняется на 1:1.
После непродолжительного нахождения в бетономешалке смесь готова к использованию, ее переливают во вторую бочку или сразу приступают к монтажу.
Нанесение
Для нанесения утеплителя на стены можно применять опалубку, но этот метод очень трудоемкий, гораздо проще подготовить плиты из утеплителя:
- Чтобы изготовить плиты, необходимо заранее изготовить несколько форм для них. Их размер будет зависеть от параметров стены. Формы можно приготовить самостоятельно, собрав их из фанеры и брусков с помощью гвоздей и молотка. Толщина плит утеплителя будет зависеть от средней зимней температуры и наличия в составе смеси технической соли.
- Форму заливают приготовленным раствором небольшими порциями и периодически разравнивают. Желательно максимально сократить количество воздушных пузырьков и толще смеси.
- Монтаж плит осуществляется после затвердевания материала, можно использовать не до конца высушенные плиты, достаточно, чтобы они просто держали форму.
- Плиты устанавливаются вплотную друг у другу, закрепляются.
- Места стыков, сколы углов и зазоры замазывают остатками глиняной смеси.
Монтаж плит из глины с опилками
Для монтажа используются деревянные направляющие, между ними помещают плиты и после этого затирают стыки остатками глиняной смеси.
Эта технология утепления дома обеспечивает чистоту в помещении во время монтажа. Сырая глина — это очень грязный и плохо отмывающийся материал. Не рекомендуется использовать его в помещениях, где уже завершены монтажные работы. Плиты же можно подготовить в другом месте, сохранив комнату чистой.
Очень важно правильно сушить плиты утеплителя. При быстром высыхании на поверхности плит образуется плотная сухая корка, мешающая воде, находящейся внутри выходить наужу, это приводит к неравномерному высыханию, повреждению и потере теплоизоляционных свойств. Чтобы высушить плиты равномерно их необходимо оставить в помещении с достаточной влажностью и оградить от попадания прямых солнечных лучей.
Чистовая отделка
Сами по себе плиты их глины с опилками имеют неровную поверхность, выровнять ее можно с помощью специальной штукатурной смеси из опилок — арболита.
Смесь наносится после полного высыхания плит утеплителя. Штукатурка стен происходит в 2 слоя: сначала грубая черновая штукатурка, потом — затирка без добавления опилок.
Чтобы приготовить раствор необходимо взять мелкие опилки, воду и глину с известью. Материалы смешиваются по ранее описанной технологии и сразу наносятся на стены, дополнительно увеличивая теплоизоляцию. Наносится раствор шпателем и максимально выравнивается. Толщина слоя составляет 2–3 мм.
Финальным слоем будет такой же раствор, но без добавления опилок, он аккуратно наносится на стены, выравнивается и вскоре застывает. После этого комнату можно оклеить обоями или покрасить. Материал долговечен, надежен и прост в ремонте, утеплитель прослужит хозяевам долгие годы.
Древняя технология строительства получила новое дыхание среди дачных застройщиков. Натуральный материал отличается массой положительных характеристик. Глина прекрасно аккумулирует тепло, поэтому в таких домах зимой тепло, а летом – прохладно. В статье речь пойдет о технологии строительства дома из глины и соломы.
Содержание:
Общие характеристики глины для строительства дома
Эта горная порода в чистом виде встречается редко (каолин). В зависимости от количества содержащихся примесей (песка, известняка и т. д.) глину делят на жирную, среднюю и тощую. Основными свойствами данного материала является:
- пластичность;
- водонепроницаемость;
- звукоизоляция;
- негорючесть;
- экологическая чистота;
- возможность обработки обжигом.
Дома из глины фото
В домах из глины поддерживается оптимальный микроклимат. Влажность воздуха в помещении составляет около 50%. Такие стены не накапливают заряды статического электричества.
Стоит отметить еще одно преимущество материала – передача тепловой энергии. Коэффициент данного параметра равен 0,5, этот показатель равняется теплопроводности минеральной ваты.
Преимущества строительства из глины
Из основных достоинств строительства дома из глины можно отметить:
- доступность материала. Залежи присутствуют практически по всей территории России и бывших стран СССР. Из данного факта вытекает еще одно неоспоримое преимущество – дешевизна;
- благодаря естественному происхождению и отсутствию вредных примесей глину относят к экологически чистым материалам. В сравнение можно привести тот же кирпич, газо-, пенобетонные блоки, которые при определенных условиях могут выделять вредные вещества;
- дом из глины «дышит», способен впитывать запахи, пыль и даже пятна.
Благодаря такому качеству строения из глины показаны для проживания людям, страдающим аллергическими заболеваниями;
- глина и деревянные элементы отлично взаимодействуют друг с другом. Дерево словно консервируется в каолине. За счет этого свойства пиломатериалы можно не обрабатывать защитными средствами, в составе которых присутствует практически одна химия;
- долговечность материала выше всяческих похвал. В доказательство к этому утверждению можно привести постройки, которым ученые насчитывают более 1000 лет;
- готовые блоки можно размочить и полученную массу использовать повторно. Таким образом, материал не образует строительных отходов;
- в некотором смысле глина несет в себе божественную составляющую. В нескольких религиях именно этот материал использовался для сотворения человека, в частности Адама.
Единственным недостатком можно считать трудоемкие работы по внутренней и внешней отделке стен. Потому как блоки не отличаются ни идеальной геометрией, ни декоративной поверхностью. Слой выравнивающего материла, может составлять до 3 см.
- Такие поверхности можно лишь побелить, к сожалению, обои и краска «держаться» на глине не будут. Хотя в помещениях можно обшить гипсокартонными листами, тогда оформить интерьер можно будет любыми материалами.
- Но это касается лишь жилых домов, для хозяйственных построек вопросы, относящиеся к интерьеру или экстерьеру не актуальны.
Глина в строительстве
Глину используют в качестве основного материала для изготовления кирпичей, самана, черепицы и других керамических изделий. Также ее применяют в сыром виде для набивки стен, смазке (утеплении) потолков, при обустройстве кровли и оштукатуривании деревянных стен.
Из необожженных кирпичей возводят в основном одноэтажные постройки, хозяйственные блоки, гаражи. Такой строительный материал имеет несколько подвидов:
- кирпич-сырец – в основном используется для кладки внутренних стен и перегородок, потому как имеет слабую сопротивляемость к воздействию сырости и влаги;
- саман, в свою очередь, подразделяется на легкий и тяжелый.
Это зависит от того, сколько частей соломы содержится в массе. Как правило, легкие блоки используются как утеплитель, а тяжелые – для кладки стен.
Изготовление саманного кирпича
- Стандартные размеры саманного кирпича, изготовленного своими руками – 40х20х20 см, габариты кирпича заводского исполнения – 33х16х12 или 33х17х13 см. Основное сырье лучше заготовить по осени, многократное замерзание/оттаивание глины лишь улучшает ее характеристики.
- В качестве армирования выступает рубленая солома (15-20 см), так как длинные стебли затрудняют работу. Солому и глину, необходимо заранее вымочить.
- Глина берется средней жирности, это позволит избежать больших трещин при сушке. Перед замесом глина освобождается от крупных примесей: веток, камней и т. д. Все составляющие тщательно перемешиваются посредством бетономешалки или по старому методу – ногами.
- Кирпичи формируют вручную, помещая глиняную массу в подготовленные формы без дна. Учитывая усушку, размеры матрицы должны быть на 1 см больше готового блока.
Формы изготавливаются из пиломатериала, влагоустойчивой фанеры или металлических листов.
- Матрицы заранее выкладываются на ровную поверхность. При закладке смеси особое внимание уделяется угловым местам. Важно следить за плотным наполнением формы массой по краям и углам.
- Площадка должна иметь хороший сток, тогда несильный дождь для блоков не страшен. В противном случае заготовки лучше спрятать под навесом, закрыть досками или пленкой.
- В таком виде кирпичи будут сохнуть 3-ое суток, затем их вынимают и ставят на ребро, по истечении 2-3 дней блоки выставляются на другое ребро или на торец. Качество готовых блоков можно определить следующим образом:
- скинуть кирпич с 2-х метровой высоты, если он остался невредимым, значит, изготовление прошло правильно;
- изделие не должно размокнуть, потерять форму при длительном (1-2 дня) контакте с водой;
- на разломе блока не должны проявляться темные пятна влаги.
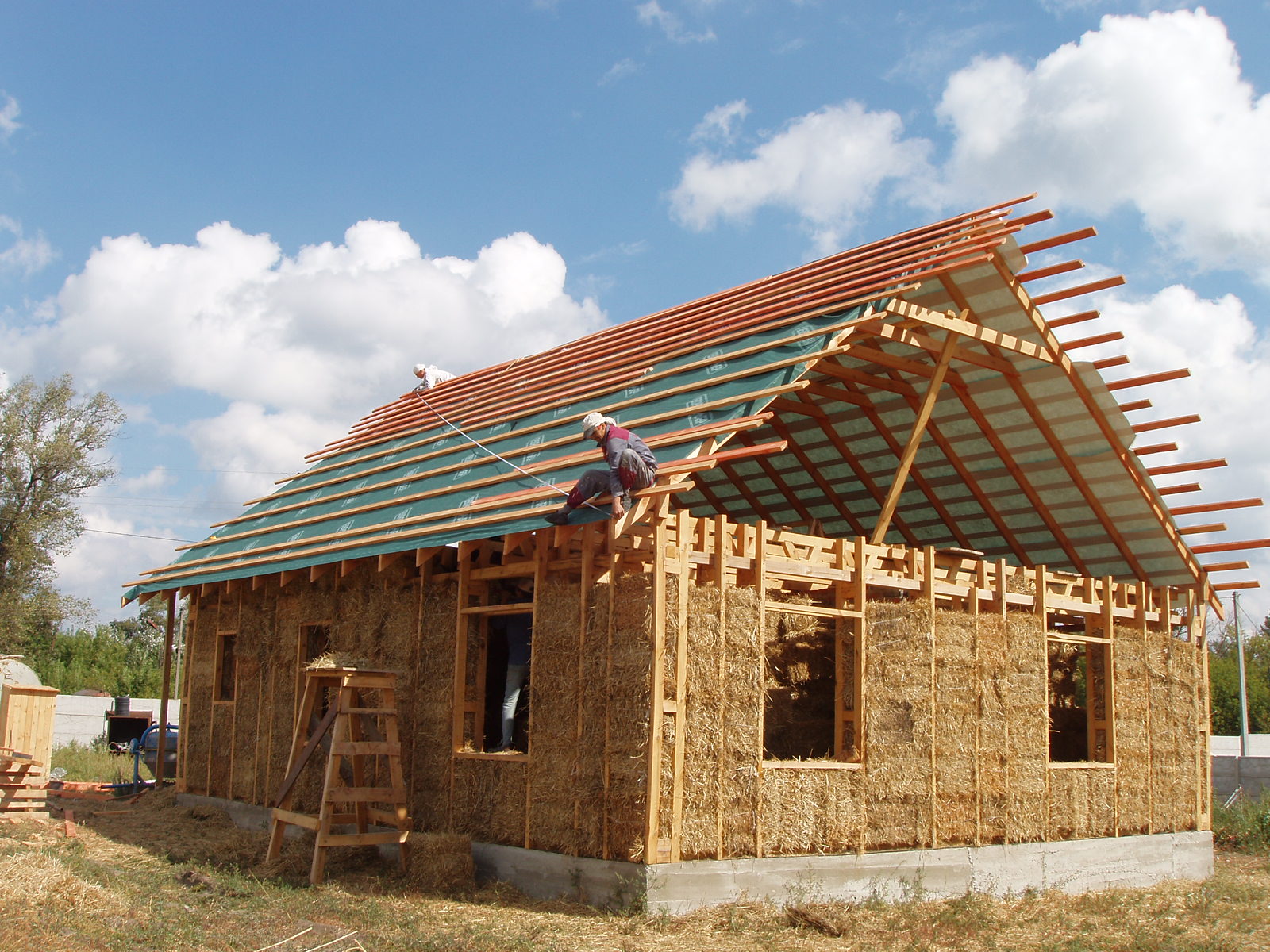
Как построить дом из глины
Строительство стен можно осуществить четырьмя способами.
- Первый способ. Возведение строений посредством готовых блоков. В качестве связующего раствора выступает глинопесчаная смесь. Технология строительства ничем не отличается от кладки стен посредством газо-, пенобетонных блоков и подобных материалов.
- Второй способ. Данная технология требует определенных навыков. Сначала устанавливаются вертикальные стойки из бруса или бревен. Между ними переплетаются прутья (дранка). На каркас накидывается тонкими слоями саманная смесь с одной стороны, а после ее высыхания – с другой. Затем поверхность выравнивается при помощи этого же раствора.
- Третий способ. Он предполагает наличие большого количества пиломатериала.
Сооружается опалубка, свободное пространство заполняется саманной массой и тщательно уминается (трамбуется). В процессе опалубка надстраивается до тех пор, пока стены не достигнут требуемой высоты.
- Четвертый способ. Это дом из дров и глины, в котором древесина выступает в роли блоков, а глина является связующим раствором.
Дом из глины своими руками
- Саманные строения не любят влажность, поэтому фундамент и цоколь делают из влагоустойчивых материалов. Для этого применяют кирпич, бутовый камень, бетонные блоки. Оптимальным основанием под дом послужит ленточный или свайно-набивной фундамент.
- Высота нижней части стены должна быть не менее 50 см. В обязательном порядке прокладываются гидроизоляционные материалы (толь, рубероид). Толщина цоколя должна превышать толщину стен, как с внутренней, так и внешней стороны примерно на 30 см.
- Защитить стены от попадания дождевых вод помогут карнизные свесы, которые должны выступать на 50 см.
Также необходимо обустроить отмостки, чтобы снег и дождь не попадали на стеновые поверхности.
- При возведении стен летом в качестве связующего раствора используют глинопесчаную смесь с добавлением опилок или мелкорубленой соломы (пшеничной, ржаной и т. д.). Если строительство проходит весной или осенью, то лучше применить известково-цементный раствор.
Дом из глины видео
- Минимизировать усадку дома из глиняных блоков поможет тонкий слой связующей смеси в горизонтальных швах (до 1 см).
- Оконные и дверные проемы армируют толстыми стеблями тростника или тонкими досками. Этот же материал укладывают и в угловых сопряжениях. Проемы не следует располагать слишком близко к углам дома, минимальное расстояние 1,5 м.
- Для саманных стен используют только деревянные перекрытия. Крыша должна быть простых форм, а кровельные материалы – легкими.
Для этих целей подойдет профильный лист, шифер, ондулин. Чтобы экстерьер строения выглядел современно, внешние стены можно обшить сайдингом или облицевать кирпичом.
- Оштукатуривание осуществляют спустя год после строительства. За данный период дом полностью усядется.
Штукатурка глиняных стен
- Оштукатуривание проводится в 2 слоя – черновое и финишное. Для 1-го слоя понадобится:
- глина;
- чистый песок средней фракции;
- опилки, которые должны быть просушенными и не иметь грибковых заболеваний.

- Стоит отметить, что сушка слоев должна проходить в естественных условиях, и этот процесс может занять до 2-3 недель. Категорически запрещается использовать строительные фены для ускорения сушки. Подобные манипуляции приведут к растрескиванию слоев, тогда необходимо будет заделать все трещины и провести повторное финишное выравнивание.
И в заключение
Экологическая и экономическая составляющая жилого дома из глины очевидна. При соблюдении всех правил изготовления блоков и возведения стен, строение прослужит долгие десятилетия.
Как вариант можно рассмотреть довольно интересную идею, которую предложили итальянские разработчики – делать дома из глины на 3D-принтере для малоимущих граждан. Привести оборудование в рабочее состояние можно буквально за пару часов. Для обслуживания принтера необходимо всего 2 человека.
Конечно, эксплуатация такого жилья довольно коротка – около 5 лет, но как утверждают «строители» к этому времени можно напечатать и новый дом.
Как правильно возвести дом из глины?
Существует несколько способов возведения дома из глины- Первый. Он ничем не отличается от кирпичной кладки. Только в этом случае используются саманные блоки. Они укладываются и закрепляются с помощью раствора, в состав которого входит глина и песок.
- Второй. Он более сложный и требует дополнительных средств. Сначала сооружают деревянный каркас с двух сторон.
Между ними устанавливают прутья, способны удержать укладываемую массу. Ее накладывают сначала на одну сторону, дают ей высохнуть, а затем — на другую. После полного высыхания поверхность стен выравнивают тем же раствором.
- Третий. Он подойдет в том случае, если имеется большое количество древесных материалов. Чтобы возвести стену дома этим способом, сначала нужно установить опалубку, а затем утрамбовывать массу в пространство. Опалубку нужно наращивать до максимальной высоты стен.
- Четвертый. В нем глина используется в качестве связующего элемента, а главным материалом выступает дерево.
- Главный этап успешного строительства дома из глины – это надежный фундамент. Глиняный дом боится сырости и влаги. Поэтому фундамент лучше заложить цельный и влагоустойчивый. Можно использовать блоки, кирпичи и др. материалы. Нужно помнить, что экономить на этом этапе нельзя, поскольку фундамент – этот основа дома.
- Высота фундамента должна быть достаточно высокой – не менее 50 см. Нужно позаботиться об укладке гидроизоляционных материалов, способных уберечь стены от проникновения влаги снизу. Это могут быть рубероид, толь.
- Чтобы влага не попадала под фундамент, необходимо по периметру фундамента соорудить отмостки. А также предусмотреть карнизы для дождевых вод, которые будут в дальнейшем защищать стены от размокания.
- В качестве раствора, связующего между собой саманные блоки, можно использовать опилки, мелко нарезанную солому. Когда же эти материалы недоступны, тогда подойдет раствор из извести и цемента.
- Проемы под будущие двери и окна обозначают с помощью тонких досок или веток тростника. Так же надо поступать и с углами. Следует отметить, что проемы не стоит размещать вблизи углов. Расстояние между ними должно составлять около полутора метра.
- Чтобы внешность дома соответствовала современным требованиям, стены можно облицевать снаружи кирпичами или другими материалами.
- Крыша дома должна быть легкой, для этого используют легкие материалы: шифер, профильные листы и пр. Для перекрытий рекомендуют применять деревянные балки.
- Когда дом усядется, для этого потребуется минимум год, стены рекомендуется оштукатурить.
Этот процесс имеет две стадии: черновую и финишную
Для проведения первого этапа потребуются такие материалы:
- песок,
- глина;
- просушенные чистые опилки.
- Сначала готовят раствор из песка и опилок, затем подмешивают глину, разбавляют до необходимой консистенции водой.
- Чтобы выдержать пропорции, нужно сначала взять три части песка, затем добавить по одной части опилок и глины. Поскольку глина бывает разной консистенции, то именно от нее зависит, насколько смесь будет эластичной. Из полученной массы нужно скрутить веревочку в диаметре около двух сантиметров и дать ей высохнуть. Если после высыхания трещины не образуются, значит, смесь идеально подходит для нанесения.
Продолжайте готовить ее в тех же пропорциях.
- Данная смесь наносится шпателем небольшим слоем, разравнивается. Если смесь загустела или пересохла, ее нужно разбавить водой до первоначальной консистенции. Слой штукатурки должен в среднем равняться двум-трем сантиметрам.
- Финишная штукатурка в своем составе, кроме песка, глины и воды, также имеет цемент. Пропорции предусматривают три части цемента и по одной – других элементов. Эта смесь должна быть несколько жидковатой, что поможет добиться идеальной поверхности.
- Специалисты рекомендуют естественное высыхание штукатурки, хотя этот процесс может длиться несколько недель. Не рекомендуется ускорять его при помощи фенов, так как это может привести к образованию трещин, и работу придется переделывать заново.
Дом из глины выгодный и с точки зрения материальных затрат, и с точки зрения физических усилий, и с точки зрения экологии. Материалы, которые используются для его строительства, не вызывают аллергических реакций в людей, страдающих этими заболеваниями. При соблюдении технологий дом простоит не одну сотню лет. Живя в доме, сделанном своими руками, вы всегда будете чувствовать тепло и уют. А последующие поколения близких вам людей будут благодарны вам за теплый и уютный дом.
Как сделать кирпич своими руками, Кирпич из глины и соломы
Как сделать кирпич своими руками? Это смотря какой кирпич, поскольку их придумано великое множество – сырцовых и обожженных для печи, элитно-декоративных и с добавкой навоза. Но основная технология для различных кирпичей все же имеет больше сходства, чем различий: сначала подбирают состав смеси по наличию материалов в данной местности, уточняют рецептуру и заготавливают сырье. Например, для глиняного кирпича на постройку дома нужно очень большое количество сланцевой карьерной тугоплавкой глины, а для саманного – нужны глины с несколько другими качествами и особым образом заготовленный наполнитель из резаной соломы. Затем замешивают, добиваются однородности и пластичности массы, формуют, обжигают или сушат кирпич. Кирпичи ручной формовки делают штучно и применяют для художественного декора, а кирпичи для забора или сарайчика можно сделать своими руками из глины и песка. В наше время множество секретов старых мастеров утеряно, но интерес к натуральным стройматериалам неуклонно растет: например, к саманному строительству.
Кирпич из глины и соломы
Кирпич из глины и соломы чаще называют саманным кирпичом, а солома (сечка, мох, древесные опилки и стружки, резаный камыш или измельченное волокно натуральных утеплителей и др.) применяется в качестве утеплителя. Вяжущее в саманных кирпичах – это глина, также обязательны добавки кварцевого песка, торфа или навоза в естественно-влажном состоянии. Чтобы сделать саман прочнее, на современной частной стройке добавляют в замес цементные и известковые вяжущие (пушонку).
Навоз (или торф) для самана – не наполнитель или заменимая добавка, а стабилизирующий агент, и если достать коровий (конский) навоз сложно, то для его замены готовят особый перегной. Процесс похож на сооружение компостной кучи, но сырье берут очень влажное (овощная ботва и очистки, трава и лист, различные сочные сорняки) и перемешивают с вязким раствором глины. Готовность стабилизатора в нормальных условиях тепла и влаги – примерно через 3-4 месяца. Саман — древнейшее изобретение наших предков и отличный, теплый дом для современных последователей зеленых технологий. Внешне дом из самана может быть сараем, а может быть верхом эстетики.
Размешивают саман ногами в ямах или больших емкостях вроде ванн. Есть специальные приспособления – грунтомесы, похожи на миниатюрные бетономешалки.
Сушка самана тоже имеет свои особенности: кирпич сушат три дня плашмя, а дальше – на боку, причем каждые 2-4 дня переворачивают кирпичи другим боком. Зимой сушка самана в средней полосе невозможна, для качественного кирпича нужно оборудовать отапливаемое закрытое помещение.
Кирпич из глины и песка
Для хорошего кирпича из глины и песка самое важно условие успеха – наличие подходящей глины. Глина для обыкновенного красного кирпича должна быть достаточно, но не чрезмерно жирной, а проверяют глину на жирность несколькими способами – визуально, делая комок в ладони и наблюдая за его «поведением» при падении с высоты и сдавливании; лепят блины диаметром 10 см и после особой сушки без атмосферной воды и солнца тестируют на трещины – это стандартный способ проверки глин.
На частной стройке кирпич из глины имеет смысл изготавливать в больших объемах, сделав предварительно ряд тестов: проверяют качества смеси из глины и песка на каждом этапе формовки и сушки кирпича, вносят коррективы в подбор состава глина/песок. Кирпичи из глины в домашних условиях можно делать только двух видов – сырец и обожженный кирпич. Но этого вполне достаточно для любых построек на участке, декора и благоустройства. Кирпич без обжига обходится дешево и годен для небольших построек, заборов, беседок, малых форм.
Обожженные кирпичи собственного изделия у мастеров не уступают фабричным и подходят для стройки дома. Различные виды ручных кирпичей и плиток ручной формовки выполняются штучно и порой имеют немалую ценность. Домашний кирпич можно делать любых размеров, но проверенная временем стандартная форма 250*120*65 мм всегда себя оправдывает. В самодельных формах для кирпича можно делать оснастку для пустот – конические или прямоугольные выступы. Такой кирпич легче не в ущерб прочности, поскольку отлично сцепляется с раствором, удобнее в кладке и требует значительно меньше сырья. Учитывая, что самородную глину готовить в высшей степени трудоемко, а покупать в больших объемах дорого, многие мастера предпочитают формовать пустотелые кирпичи.
Кирпич из опилок и цемента
Такие кирпичи привычнее называть арболитом. По технологии эти кирпичи одни из самых сложных, поскольку требуют выполнения целого ряда условий при подготовке древесного наполнителя:
- Опилки и стружка предпочтительны хвойных пород, в идеале – сосновые;
- Вся древесная органика перед замесом должна быть совершенно сухой, а это не так просто, поскольку в древесине много внутренней влаги.
Хранение и сушка опилок должны полностью исключить влагу в будущем наполнителе, а если применить опилки с прелью, можно получить арболит с грибком и плесенью. Даже остаточное брожение целлюлозной массы приводит к вздутию готовых блоков в период созревания, а иногда можно наблюдать даже разрывы.
- Химическая нейтрализация опилочного наполнителя выполняется добавлением ингибитора (хлорида кальция, сульфата алюминия и др.). Также применяют жидкое стекло и другие силикаты, известь, глинозем сернокислый – с той же целью: минимизировать действие сахаров и бродильные свойства свежей древесины.
Простота подготовки опилок для арболита и незатратность – это плюс, кроме того, из арболита можно прессовать кирпичи «для себя», то есть в индивидуальных формах и нужного размера, стандартный предельный габарит блоков от 200 до 300 мм по высоте и ширине; и 500 мм по длине. При точной технологии можно делать даже панели из смеси сухих нейтрализованных опилок (примерно 90%) и цемента М500 (до 10% по массе).
Саман. Изготовление саманных блоков | HouseDB.ru
Сегодня для строительства часто используются такие виды строительных материалов, как саман и опилкобетон, популярность которых объясняется их недорогой ценой и доступностью: для изготовления самана необходимы вода, песок и глина, а в качестве волокнистого наполнителя используется солома; в состав опилкобетона входят известь, песок и цемент, вода и опилки.
Простая технология изготовления саманных блоков позволяет изготавливать их самостоятельно и использовать для возведения домов, хозяйственных построек и гаражей. Однако огромное значение для качества блоков имеет исходный материал, использованный для их изготовления.
Подбор материалов
Глина
Основным компонентом, входящим в состав самана, является глина. Прежде, чем производить отбор глины для производства, необходимо для определения ее качества взять несколько образцов грунта. Такие образцы берутся из разных мест участка, откуда планируется добыча глины. Исходя из результатов анализа процента содержания глины в почве, определяется пригодность материала для использования при изготовлении самана.
Так выглядит типичная кладка из саманных блоков
Заготавливать глину для изготовления саманных блоков рекомендуется осенью – после воздействия морозов, она будет легко распадаться на мелкие частички. На зиму глину укладывают для хранения в бурты. Такие бурты рекомендуется делать размером 2 м х1,5 м, его высота не должна превышать 1 м. В бурт такого размера поместится около 3 куб.м глины – учитывая расход глины на изготовления самана, из такого количества можно получить 600 штук блоков 200x200x400 см.
В бурт глина укладывается пластами по 30 см, каждый из которых обильно смачивается водой. Сверху бурт укрывается смоченной соломой. При такой укладке даже в сухую осень глина в бурте не пересохнет до того, как наступят морозы. Укрытый соломой бурт накрывают рубероидом, а сверху – пленкой из полиэтилена. В размещенном на улице бурте, уложенном таким образом, глине не грозит пересыхание – она будет равномерно терять влагу и хорошо вымерзнет, что приведет к улучшению ее свойств, необходимых для переработки глины в процессе изготовления саманной смеси.
Весной, после окончания морозов и установившейся плюсовой температуре воздуха, бурт можно раскрывать. Процесс открывания бурта также имеет свои особенности: сначала его очищают от соломы и оставляют, накрыв полиэтиленовой пленкой. Таким образом создается парниковый эффект, способствующий быстрому оттаиванию глины. Кроме того, полиэтиленовая пленка не дает глине пересыхать и позволяет избежать возникновения в верхнем слое глины нежелательной пленки. Такое хранение обеспечивает хорошую сохранность таких важных свойств глины, как клейкость и эластичность.
Солома
Также одним из важным компонентов саманного блока является солома, которая играет роль волокнистого наполнителя. Обычно для этого используется солома от озимой пшеницы или яровых культур – ячменя или ржи. Лучше всего, если будет использоваться свежая солома. Однако, можно брать и прошлогоднюю сухую солому – использование гнилой соломы не допускается.
При отсутствии соломы для производства самана можно использовать и сено из грубой травы – в данном случае клевер или мышиный горошек не подойдет. Еще одним вариантом для наполнителя может быть веревка из натуральных материалов или льняной шпагат. Однако всё это является некоторыми вариантами замены – лучше всего использовать солому.
Песок
Еще один вспомогательный компонент, необходимый для производства самана – песок. Лучше всего брать грубый крупнозернистый песок многогранной формы – округлая форма песчинок в данном случае не рекомендуется. Лучше всего для саманного блока подойдет карьерный песок. При его отсутствии можно воспользоваться речным песком – главное, не стоит заменять карьерный песок морским.
Процесс изготовления смеси из самана
Для приготовления смеси для изготовления блоков, сначала необходимо смешать глину и песок. При этом добавлять воду необходимо постепенно – полученная смесь должна быть густая. После тщательного вымешивания смеси, необходимо проверить ее консистенцию. Для этого из небольшого количества смеси нужно скатать шарик размером куриного яйца. Прилипание шарика к ладоням при скатывании свидетельствует о превышении глины в составе смеси и необходимости добавления песка. Если при скатывании шарик рассыпается, в смесь необходимо добавить еще глину.
Видео: Производство самана
После получения правильной пропорции можно готовить основную смесь для изготовления самана. Для этого выкапывают небольшой котлован полуметровой глубины. Размер котлована зависит от необходимого количества саманной смеси: в котловане 1,5 м х 2,5 м получится 1 куб. м смеси.
На дно подготовленного котлована укладывается глина слоем около 25 см, который заливается водой (вода должна полностью покрыть глину). Залитую глину оставляют на ночь – за это время комки полностью размокнут и глина станет достаточно податливой для того, чтобы ее можно было хорошо размешать с песком и соломой. Перед добавлением в глину остальных компонентов, из нее выбирают крупные камни. Далее ее следует замесить ногами и размять все раскисшие комки. Затем добавляется песок и солома, и все это вымешивается, пока не будет получена однородная масса.
Утепление полов глиной
Главная / Монтаж, ремонт, уход / Утепление / Применение глины для утепления пола
Глина очень универсальный материал. Из нее можно даже дом построить. Однако, в нашем случае столь серьезных целей не ставится – требуется всего лишь произвести утепление полов глиной. Для этого не годится чистый материал – стандартные поверхности, которые состоят из смеси песка и глины обладают не слишком высокими теплоизолирующими характеристиками. Если же добавить опилки и получится то, что нужно.
Как это можно сделать и как провести подготовку
Для начала можно решить, как будет происходить работа — есть два варианта:
- Можно создать плоскость, залив смесь опилок и глины.
- Можно сделать кирпичи и уже из них создать поверхность.
Оба способа применяются активно и преимущества есть у каждого из них: заливку можно осуществить немного быстрее, а кирпичи укладывать немного легче. Однако, в обоих вариантах потребуется много времени и сил на предполагаемые работы. Подготовка происходит практически одинаково, независимо от выбранного вида работ:
- Поверхность, которая будет утепляться, гидроизолируют и покрывают защитой от плесени – разные пропитки и грунтовки придут на помощь.
- Дальше готовят смесь воды и исходного компонента. Она будет готовиться несколько дней – зависит от начальной влажности исходного материала.
- После этого можно начинать работы – смешивать полученный раствор с опилками и осуществлять заливку или приступать к изготовлению кирпичей.
Если вы собираетесь утеплить пол глиной с помощью заливки, то смесь разводится таким образом: на ведро раствора добавляют два или три ведра опилок. Для изготовления саманных блоков необходима другая пропорция – один к одному.
Процесс утепления
Дальше процесс может происходить по разному. Для использования блоков нужно их сначала высушить. Обычно, для этого они трамбуются в специальных ячейках из досок, придающих им необходимый размер и форму. Они оставляются в покое до высыхания. Если же вы собираетесь просто залить раствор, то тут работать будет проще – замешанная смесь сразу используется и предварительно ее сушить не нужно. Остальные процессы выглядят так:
- Сформированные готовые блоки выкладываются на основание с наименьшими зазорами, которые только возможны.
- Пространства между кирпичами следует заполнить жидкой глиной без опилок – она выступит в роли цемента, скрепляющего между собой уложенные блоки.
Когда все просохнет останется лишь провести обработку утепляющего слоя льняным маслом. Для заливок процедура выглядит немного по другому.
- Сперва укладывается база – толстый не очень хорошо выровненный слой раствора. Его обязательно требуется тщательно утрамбовать.
- Когда первый проход сделан, раствор остается сохнуть – может понадобиться несколько недель, это зависит от температуры и влажности в помещении.
- Второй слой укладывают по высохшему первому и его толщина будет уже гораздо меньше – около одного или двух сантиметров. Здесь также смесь утрамбовывают, но, еще понадобится и качественно выровнять плоскость.
Последним этапом во всех вариантах будет обработка льняным маслом. Этот особенно важно, если глина используется для утепления пола в бане – здесь влажность обычно высокая, а масло придает поверхности водостойкость. При этом, обработка происходит в несколько этапов. Первый раз можно использовать чистое масло. На втором слое уже требуется разбавить его растворителем в соотношении масло – растворитель четыре к одному. Далее – один на один и последний проход – растворителя будет четыре части, а масла – одна. Можно сделать и больше слоев. Готовность и качество пропитки можно узнать так: если на ней после обработки появляются лужицы масла, то необходимая водостойкость достигнута.
При необходимости недорого и самостоятельно сделать утепление самым простым с точки зрения сложности процесса образом, рассмотренный вариант может стать очень подходящим решением. Основные работы очень просты и лишь нужная консистенция раствора может стать небольшой проблемой – при некачественном замесе проведенная работа может пойти насмарку. Однако, это не слишком сложно и самой большой проблемой станет необходимость потратить слишком много времени на предусмотренные технологией процессы. Тем не менее, временные затраты, а также затраты сил на обустройство с лихвой окупаются долговечностью и дешевизной создания такого пола.
Опилки в качестве утеплителя: варианты использования опилок, как утеплителя
Несмотря на то, что в последние годы в продаже появилось большое разнообразие современных утеплителей, экологически чистые отходы от деревообрабатывающей промышленности не потеряли своей актуальности в качестве термоизоляционных материалов. Речь идет, конечно же, прежде всего об опилках.
Опилки в качестве утеплителя
Особенно часто используют опилки в качестве утеплителя при постройке домов в регионах, богатых лесными просторами, так как здесь обычно располагается большое количество лесопильных предприятий. А это значит, что есть возможность приобрести материал по низкой цене, а порой – даже найти практически задаром.
Содержание статьи
- 1 Опилки в качестве утеплителя – «плюсы» и «минусы»
- 2 Подготовка опилок
- 3 Способы утепления дома опилками
- 3.1 Опилки с глиной
- 3.1.1 Приготовление смеси
- 3.2 Процесс утепления глиняно-опилочным составом
- 3.2.1 Утепление глиняно-опилочной сырой массой
- 3.2.2 Утепление стен и перекрытия глиняно-опилочными матами
- 3.3 Опилки с цементом
- 3.4 Утепление сыпучим материалом
- 3.4.1 Видео: утепление чердака сухими опилками
- 3.1 Опилки с глиной
Опилки и материалы, изготовленные на их основе, используются для утепления практически любых элементов дома — чердачных перекрытий, стен, полов, погребов и т.п. Кроме этого, из древесных отходов изготавливают блоки, которые широко применяются для возведения жилых и подсобных зданий.
Опилки — отходы, которым найдется широчайшее применение
Этот материал не теряет своей популярности, благодаря положительным характеристикам, к которым можно отнести следующее:
- Одним из самых важных достоинств можно смело назвать абсолютную экологическую чистоту опилок. Они не выделяют токсичных для здоровья человека веществ, поэтому их можно использовать в любом количестве.
- Важное преимущество — уже упомянутая доступная для всех низкая цена материала, а иногда и возможность достать их бесплатно.
Опилки отлично подходят для утепления чердачных помещений
- Опилки — прекрасный утеплитель для крыши, естественно, при правильном соблюдении технологии укладки. Если термоизоляционный слой будет соответствовать необходимой толщине, в соответствии с климатическими условиями региона, то подобное утепление ничуть не будет уступать по своей эффективности другим современным материалам.
Материал | Удельный вес кг/м3 | Толщина засыпки в мм при средней зимней температуре воздуха на улице, оС | ||
---|---|---|---|---|
-15 | -20 | -25 | ||
Опилки древесные | 250 | 50 | 50 | 60 |
Стружка древесная | 300 | 60 | 70 | 80 |
- Опилки можно применять для утепления, как в обычном сыпучем состоянии, так и в других формах. Например, это могут быть плиты смеси с другими природными или искусственными материалами.
К недостаткам в использовании этого утеплителя в чистом виде можно отнести высокую горючесть. Однако, если использовать опилки в глиняных или цементных смесях, то их возгораемость значительно снижается.
Если рассуждать с тех позиций, что стропила, чердачные перекрытия и стены каркасных домов выполнены из древесины, предварительно обработанной антипиренами, то опилки прекрасно впишутся в этот комплекс постройки, при условии, что будут также подвергнуты специальной обработке. Кроме того, необходимо будет предусмотреть качественную изоляцию всех электрических кабелей, которые будут пересекать слой утеплителя или располагаться в его толще. Требует особого внимания и термоизоляция дымоходной трубы в местах прохождения через чердачное перекрытие или расположенной около стены.
Надо заметить, что опилки – отнюдь не единственный природный материал, который с давних пор используется для утепления жилья. И если посмотреть на таблицу, предложенную ниже, то они ничуть не проигрывают другим натуральным «термоизоляторам».
Натуральный утеплительный материал | Масса материала кг/м3 | Коэффициент теплопроводности |
---|---|---|
Пакля | 180 | 0,037-0,041 |
Вата | 80 | 0,036 |
Войлоки разные | — | 0,031-0,050 |
Костра разная | 150-350 | 0,04-0,065 |
Мох | 135 | 0.04 |
Торф-сфагнум | 150 | 0,05-0,07 |
Хвоя | 430 | 0.08 |
Нарезанная солома в набивке | 120 | 0.04 |
Соломенные маты | — | 0,05-0,06 |
Тонкая древесная стружка в набивке | 140-300 | 0,05-1,0 |
Сухие листья | — | 0,05-0,06 |
Древесные опилки | 190-250 | 0,05-0,08 |
Конечно, не все опилки одинаковы – многое зависит от породы и качества древесины, при переработке которой они получены.
Так, практически безоговорочным «лидером» в этом вопросе являются дубовые опилки. Они менее гигроскопичны, чем опилки, полученные от деревьев других пород. Даже если влага попадет на них, она не принесет им особого вреда, так как дуб имеет в своем составе природные антисептические вещества. Поэтому они не подвержены появлению гнили и не разбухают при попадании на них воды.
Однако, дубовые опилки слишком распространенным материалом не назовешь. Ничего страшного – хорошо подойдут в качестве утеплителя и отходы от хвойных пород: ели, лиственницы или сосны. Хвойная древесина в избытке имеет в своем составе эфирные масла, стойко противостоящие появлению грибка или гнили, то есть самой природой в материал заложены противогрибковые и антисептические качества.
Подготовка опилокОпилки, в чистом, не подготовленном виде нельзя считать полностью пригодными для изготовления блоков или для засыпки в качестве утеплителя. После окончательного просыхания они становятся весьма пожароопасным материалом. Кроме того, их могут облюбовать для устройства гнезд различные насекомые или грызуны.
Поэтому, с чистым материалом необходимо предварительно поработать:
В первую очередь опилки обрабатываются специальными составами, имеющими свойства антисептика и антипирена.
Антипирен сделает опилки практически негорючими …
Сначала опилки перемешивают с антисептиком глубокого проникновения, а после просыхания — с антипиреном. Все процессы можно проводит на застеленной пленкой проветриваемой площадке под крышей, например, под навесом.
… а антисептик предотвратит биологические процессы гниения, появление грибка, гнезд насекомых и грызунов
- После обработки антипиреном, опилки перемешиваются с гашеной известью, которая не позволит поселиться в утеплителе грызунам и насекомым.
Известь добавляется в опилки в пропорциях 1:5, то есть одна часть извести на пять частей опилок. Измерение можно проводить мешками – например, высыпается пять мешков опилок и один мешок сухой извести, а затем тщательно перемешивается. Если работа будет проводиться вручную, то перемешивание можно проводить, используя обычную мотыгу и совковую лопату.
- Кроме этого, нужно учесть, что опилки, использованные для утепления в сыпучем виде, со временем имеют свойство проседать, уменьшая образованную воздушную прослойку и, естественно, теряя свои утепляющие качества. Поэтому по прошествии определенного периода придется делать их досыпку или укладывать поверх них другой утеплитель.
Учитывая такой негативный фактор проседания, чтобы не допустить необходимости периодического обновления или усиления термоизоляционной прослойки, делается смесь, состоящая из опилок, извести и гипса, в пропорциях 9: 1: 5. Затем смесь смачивают водой, перемешивают, и сразу же укладывают на подготовленную основу.
Так как гипс затвердевает очень быстро, состав нужно готовить небольшими порциями, чтобы успеть выложить их до застывания в предназначенном для них месте, иначе материал будет испорчен.
Если нет желания торопиться, подстраиваясь под время застывания гипса, его можно заменить цементным раствором.
При использовании такого метода утепления, предварительная просушка опилок не потребуется. Их можно будет применять сразу после доставки с лесопилки.
Способы утепления дома опилкамиКак говорилось выше, для утепления с применением опилок используются несколько вариантов различных смесей с добавлением гипса и цемента, но самым популярным все-таки остается старый народный способ — состав с глиной.
Опилки с глинойГлина и опилки — это два натуральных материала, которые абсолютно безопасны для здоровья жильцов дома. В смеси они образуют материал, обладающий отличными теплоизолирующими и гидроизолирующими качествами, поэтому хорошо подойдут для утепления стен и перекрытия бани. После застывания глина не подвержена влиянию горячего пара, что нельзя сказать о большинстве других современных утеплителей или гидроизоляционных материалов. Ну а опилки, находящиеся в смеси, создадут хороший теплоизоляционный эффект.
Кроме этого, глиняно-опилочная смесь достаточно стойко переносит высокие температуры и пожаробезопасна.
К преимуществам этого состава можно отнести и то, что подобный утеплитель прекрасно подойдет для дома, выстроенного в любом регионе – и там, где летняя жара достигает критических отметок термометра, и там, где зимой стоят трескучие морозы.
Смесь из глины и опилок не только сохраняет тепло в холодный период, но и не дает нагреваться помещениям в самую сильную жару, поэтому в доме, термоизолированном этой смесью, тепло зимой и прохладно летом.
В отличие от современных утеплителей, глиняно-опилочный материал может прослужить века, не разлагаясь и не теряя своих первоначальных качеств.
Утеплить строение с помощью древесных отходов и глины — не так уж и просто. Чтобы была достичь нужного эффекта термоизоляции, необходимо проводить работы в соответствии с определенными требованиями:
- Смесь должна быть приготовлена с соблюдением определенных пропорций, иначе у состава будет низкая адгезия, и если стены будут им обмазываться, то после высыхания не исключено осыпание.
Стена, обмазанная глиняно-опилочным составом
- Чтобы достичь максимального эффекта от утепления, смесь на стены должна быть нанесена правильно и иметь определенную толщину.
В современных условиях этот состав редко используют для нанесения на стены — чаще всего опилки с глиной применяют для создания утеплительного слоя в чердачном перекрытии, где материал не будет подвергаться серьезной нагрузке.
Стена, утепленная матами из смеси глины с опилками
Если есть желание произвести утепление стен, то лучше всего изготовить утепляющие плиты из глины и мелких опилок или из рубленого камыша или соломы.
Опытные строители, работающие с таким материалом, рекомендуют использовать камыш, так как его по каким-то причинам абсолютно не переносят грызуны.
Растительные волокна в смеси с глиной станут для раствора своеобразной «арматурой», которая повысит несущую способность утеплительного слоя на стенах.
Приготовление смесиСуществует несколько способов изготовления глиняно-опилочной смеси для утепления дома. Также есть и несколько методик ее укладывания. Так, из готовой смеси могут быть изготовлены маты, которые закрепляются на стенах и укладываются на чердачное перекрытие.
Другим вариантом является выкладывание замешанной влажной массы между балок перекрытия или же нанесение ее на стену, на заранее закрепленную обрешетку.
Для изготовления утеплительной смеси и ее дальнейшего использования необходимо подготовить определенные материалы и инструменты. Потребуются:
- Опилки, глина и вода.
- Пергамин и водостойкий скотч для скрепления.
- Металлический короб с низкими бортиками (или корыто) для замешивания массы.
- Большая емкость для замачивания глины.
- Ведро.
- Совковая лопата и мотыга.
- Ровные доски, из которых будут собираться формы для изготовления блоков-панелей.
Чтобы смесь получилась пластичной и по высыханию не растрескивалась, необходимо соблюдать правильные пропорции исходных материалов.
А. В том случае, если масса в сыром виде будет укладываться на перекрытие или на поверхность стен, берется ⅔ ведра опилок на ведро глины, разведенной до сметанообразного состояния.
Чтобы получить такую консистенцию глины, ее выкладывают в большую емкость, например, в старую ванну или корыто, и заливается водой, в пропорциях 1:1. Глина оставляется набухать на сутки или более — в зависимости от исходной сухости материала.
Глина готовится к предварительному замачиванию
Затем масса хорошо перемешивается до однородного состояния. Если смесь получилась очень густая, в нее можно добавить небольшое количество воды, снова хорошенько перемешать и оставить еще на 5 ÷ 6 часов. Чтобы процесс прошел быстрее, массу периодически нужно помешивать.
Если есть возможность, то лучше всего замочить всю необходимую для работы глину разом – она от этого никак не испортится, сколько бы ни находилась в воде. А смешивание раствора можно будет проводить по мере расходования ранее приготовленной порции.
Если в хозяйстве есть бетономешалка, то работа пойдет значительно быстрее. Но а вручную удобнее всего перемешивание проводить с помощью мотыги и лопаты.
Перемешивание опилок с глиной
Для смешивания глиняно-опилочного раствора будет необходима еще одна большая, но неглубокая емкость из тонкого металла, с бортиками высотой в 150 ÷ 200 мм. Туда высыпается необходимое количество опилок для одной порции замеса, и, согласно пропорциям, выкладывается глиняная смесь. Затем состав хорошо перемешивается и выкладывается на подготовленное чердачное перекрытие или наносится на стены.
Б. Если решено утеплить дом матами из глиняно-опилочной смеси, то материалы берутся в пропорциях 1:1. Пока будет набухать глина, за этот период нужно изготовить формы нужного размера, в которые будет укладываться готовая смесь.
Если маты будут укладываться на чердачное перекрытие, то стоит определить расстояние между балками и их высоту — по этим параметрам и изготавливаются формы. Они, по сути, представляют собой ящик без дна.
Изготовление глиняно-опилочных блоков-матов в самодельных формах
Лучше всего изготовить несколько форм, для изготовления сразу несколько матов. Чтобы блоки получились ровными со всех сторон, рекомендовано поступить следующим образом:
- На ровную поверхность укладывается один или несколько фанерных листов, которые накрываются плотной полиэтиленовой пленкой.
- Сверху устанавливаются формы.
- В них выкладывается приготовленная глиняно-опилочная смесь и, насколько это возможно, утрамбовывается.
- Сверху состав выравнивается с помощью правила — маячками в этом случае будут служить бортики формы.
- После схватывания и небольшого усыхания смеси, маты можно извлечь, и дальнейшее высыхание будет проходить без формы, в хорошо проветриваемом месте под крышей. На солнце их выносить нельзя, так как при окончательном просыхании может произойти растрескивание получившихся блоков.
- Освободившиеся формы снова заполняются смесью — и так продолжается до тех пор, пока не будет изготовлено необходимое количество матов.
Технология утепления глиняно-опилочной смесью достаточно проста, как с помощью матов, так и с путем выкладывания смеси во влажном состоянии.
Утепление глиняно-опилочной сырой массой1. При утеплении чердачного перекрытия с помощью глиняно-опилочной массы, необходимо вначале подготовить поверхность, на которую она будет выкладываться.
- Доски и балки перекрытия обрабатываются антисептическими составами. Если между досок имеются широкие зазоры, то между балок перекрытия может быть настелен пергамин. В том случае, когда настилаются несколько листов пергамина, их необходимо уложить внахлест и желательно скрепить водостойким скотчем.
Подготовка поверхности перекрытия к укладке утеплителя
- Далее, на настил выкладывается глиняно-опилочная смесь и разравнивается с помощью правила.
Укладка и выравнивание смеси
- Затем выровненную поверхность можно смочить водой и выровнять дополнительно с помощью шпателя.
- После полного застывания глины, она станет плотной, и по ней спокойно можно будет ходить.
Работа проводится по участкам
2. Утепление стен может проводиться двумя способами — это набрасывание влажной смеси на стены или же заливка ее в опалубку, пристроенную к готовой капитальной или каркасной стене.
- На капитальную стену глиняный раствор наносится между установленных маячков с помощью мастерка или набрасывается рукой и выравнивается правилом.
Наброска и выравнивание глиняно-опилочной смеси
- Другим вариантом является наброска смеси на стену, на которой закреплена дранка. Но в этом случае толстого слоя уложить не получится. На дранке сможет удержаться наброс из глины не более 30 мм.
Деревянное армирование стены дранкой
- После просыхания глиняно-опилочного слоя, его выравнивают песочно-цементным раствором, а затем — штукатуркой.
3. Третьим вариантом утепления стен влажной массой является закладывание ее в опалубку, установленную вдоль капитальных стен, или же закрепленную с двух сторон на стойки каркаса.
- Щиты для опалубки изготавливаются высотой в 1000 мм из досок. Они закрепляются с двух сторон стоек каркаса или параллельно капитальной стене, на расстоянии от нее в 200÷250 мм.
- В опалубку производится закладка опилочно-глиняной смеси с тщательной трамбовкой. После этого составу дают время на просыхание.
- После высыхания смеси опалубка снимается и поднимается выше, где снова закрепляется таким же образом.
- Процесс заполнения повторяется в таком же порядке, пока не будет достигнут верх стены.
Утепление стен каркасного дома
- Так как сверху между каркасным брусом или стеной и потолком останутся проемы, которые невозможно заполнить по данной технологии, придется сделать маты нужного размера, установить и закрепить их на глиняный раствор поверх готовых нижних участков стен.
Опилочно-глиняные маты укладываются таким же образом, как и маты их других утеплительных материалов.
- Схема утепления потолка выглядит следующим образом:
Схема утепления перекрытия опилочно-глиняным матом
1 – Балки чердачного перекрытия.
2 – Потолок.
3 – Черновой пол чердачного перекрытия.
4 – Снизу и сверху утеплителя укладывается пергамин.
5 – Опилочно-глиняная плита.
6 – Доски чердачного чистового пола.
- Подготовка досок перекрытия проводится таким же образом, как и при заливке глиняной массы.
- Далее, на застеленную поверхность укладываются готовые плиты. Если между балками перекрытия и матами останутся большие зазоры, то их придется заполнить влажной массой из глины и опилок.
- Для утепления капитальных стен, на них закрепляется обрешетка из бруска, имеющего размер толщины мата (если она не больше 100 мм). Расстояние между брусками обрешетки должна быть равно ширине мата. Установленные плиты удобнее всего будет зафиксировать рейками, прибив их на бруски обрешетки.
- В том случае, если утепление проводится в холодном регионе, где средние зимние температуры достигают минус 25 ÷ 30 градусов, утеплительные плиты должны быть толщиной не менее 300 ÷ 400 мм. Такие плиты, а вернее сказать – блоки монтируются на глиняно-песчаный раствор, по принципу кирпичной кладки.
Из таких глиняно-опилочных блоков можно даже возводить стенку
- Если проводится утепление каркасных стен, то нужно предусмотреть установку двух рядов брусков или досок толщиной не менее 70 ÷ 80 мм. Если устанавливаются два бруска, определяющие толщину стены дома, то опилочно-глиняные блоки будут укладываться между ними. Чтобы блоки плотно стыковались друг с другом в местах установки каркасных брусков, в них по углам делают квадратные вырезы, повторяющие формы и размеры бруска.
Примерная схема утепления стены опилочными матами
- Когда утепляются капитальные стены, рекомендовано делать кладку из блоков на расстоянии от стены в 70 ÷ 100 мм.
- После того как утеплительный слой поднят на 800 ÷ 1000 мм, между ним и стеной рекомендовано сделать засыпку из керамзита.
- Затем утепляющая стена поднимается еще на 700 ÷ 1000 мм, снова делается засыпка — и так до самого верха стены.
- По завершении утепления стены должны быть обязательно заштукатурены цементным или глиняным раствором.
Если вместо глины в «напарники» к опилкам выбран цемент, то процесс изготовления, нанесения или укладки смеси мало чем отличается от работы с опилочно-глиняным раствором, но составляющие и пропорции несколько изменены.
Так, в этом случае кроме цемента и опилок потребуется известь. Составляющие берутся в пропорции 1:10:1. Дополнительно в смесь можно добавить в качестве антисептика медный купорос или борную кислоту. Этих компонентов потребуется примерно 50 г на 50 кг смеси. На каждую порцию массы потребуется от 5 до 10 литров воды в зависимости от способа утепления.
Приготовление опилочно-цементного раствора
Если все ингредиенты в наличии, замешивается смесь:
- В подготовленную для смешивания емкость высыпаются все составляющие, перемешиваются с помощью мотыги в сухом виде до однородного состояния.
- Антисептики добавляются в последнюю очередь, а после этого смесь сразу заливается водой и перемешивается. Лучше будет, если антисептические составляющие будут разведены в заливаемой в смесь воде — тогда они быстрее впитаются в опилки.
- Перемешанную смесь нужно проверить на готовность. Это делается так — смесь набирается в ладонь и сжимается. Если из комка не сочится вода, и он не рассыпается, значит, состав готов для изготовления плит, для закладки в опалубку или для распределения по поверхности чердачного перекрытия.
На чердачном перекрытии, так же, как и в случае с глиной, под выкладываемую смесь укладывается пергамин, но в данном случаем он может быть заменен полиэтиленовой пленкой.
После того как укладка влажного утеплителя будет завершена, его оставляют для застывания.
Утепление сыпучим материаломУтепление сухими опилками проводить совсем просто. Обработанные и просушенные опилки просто засыпаются на чердачное перекрытие. Толщина их слоя варьируется в зависимости от зимних и летних температур региона. Точнее этот параметр можно узнать таблицы, размещенной в начале статьи.
Опилки для утепления применяются сухими или в виде опилочных гранул — окатышей.
Их изготавливают из мелких опилок с добавлением антисептика, антипирена и клея из карбоксиметилцеллюлозы. Готовые гранулы практически не горючи, и в них не заводятся грызуны. Нужно отметить, что они более удобны и практичны для утепления перекрытий, чем просто опилки, так как не дают усадки и отлично сохраняют тепло.
- Засыпку гранул производят на подготовленную поверхность — щели досок промазывают глиняно-известковым составом, или же застилают черновой пол перекрытия пергамином.
- Гранулы распределяют ровным слоем между балок перекрытия. Если же требуется слой большей толщины, то по периметру чердака устанавливают бортики, высотой равной нужной толщине засыпного слоя — тогда гранулы укладываются до их верха.
- Если планируется на чердаке сделать пол из дощатого покрытия, уложенного сверху утеплителя, то дополнительную обрешетку закрепляют на балки перекрытия, то есть поднимают их в высоту.
Сухими опилками или гранулами утепляют и стены, засыпая их вовнутрь. Если используются обычные опилки, то они должны быть хорошо обработаны антисептиками. Кроме этого, чтобы утяжелить их, но сохранить их низкую теплопроводность, опилки иногда смешивают со шлаком. Стены, выстроенные и утепленные таким образом, надежно защищают дом от проникновения холода и летней жары.
- Засыпка утеплителя производится по мере поднятия капитальных стен на 700 ÷ 1000 мм, с обязательной, но не чрезмерно сильной трамбовкой для уплотнения.
Схема утепления полой кирпичной стены опилками
- После засыпки и трамбовки стены снова поднимаются на определенную высоту, и так процесс продолжается до тех пор, пока не будет выведена вся нужная высота.
⃰ ⃰ ⃰ ⃰ ⃰
Вывод:
При должной предварительной обработке и сами опилки, и составы, изготовленные с их применением, являются отличным термоизолятором, который вполне способен заменить любой из современных материалов. Используя их, можно быть уверенным на все 100%!,(MISSING) что ни у кого из домочадцев не появится аллергии или других заболеваний, связанных с выделением токсичных веществ, чем иногда «грешат» некоторые синтетические утеплители.
Дом из глины: особенности строительства
Древняя технология строительства получила новое дыхание среди дачных застройщиков. Натуральный материал отличается массой положительных характеристик. Глина прекрасно аккумулирует тепло, поэтому в таких домах зимой тепло, а летом – прохладно. В статье речь пойдет о технологии строительства дома из глины и соломы.
Содержание:
- Общие характеристики глины для строительства дома
- Преимущества строительства из глины
- Глина в строительстве
- Изготовление саманного кирпича
- Как построить дом из глины
- Дом из глины своими руками
- Штукатурка глиняных стен
- И в заключение
Общие характеристики глины для строительства дома
Эта горная порода в чистом виде встречается редко (каолин). В зависимости от количества содержащихся примесей (песка, известняка и т. д.) глину делят на жирную, среднюю и тощую. Основными свойствами данного материала является:
- пластичность;
- водонепроницаемость;
- звукоизоляция;
- негорючесть;
- экологическая чистота;
- возможность обработки обжигом.
Дома из глины фото
В домах из глины поддерживается оптимальный микроклимат. Влажность воздуха в помещении составляет около 50%. Такие стены не накапливают заряды статического электричества.
Стоит отметить еще одно преимущество материала – передача тепловой энергии. Коэффициент данного параметра равен 0,5, этот показатель равняется теплопроводности минеральной ваты.
Преимущества строительства из глины
Из основных достоинств строительства дома из глины можно отметить:
- доступность материала. Залежи присутствуют практически по всей территории России и бывших стран СССР. Из данного факта вытекает еще одно неоспоримое преимущество – дешевизна;
- благодаря естественному происхождению и отсутствию вредных примесей глину относят к экологически чистым материалам. В сравнение можно привести тот же кирпич, газо-, пенобетонные блоки, которые при определенных условиях могут выделять вредные вещества;
- дом из глины «дышит», способен впитывать запахи, пыль и даже пятна. Благодаря такому качеству строения из глины показаны для проживания людям, страдающим аллергическими заболеваниями;
- глина и деревянные элементы отлично взаимодействуют друг с другом. Дерево словно консервируется в каолине. За счет этого свойства пиломатериалы можно не обрабатывать защитными средствами, в составе которых присутствует практически одна химия;
- долговечность материала выше всяческих похвал. В доказательство к этому утверждению можно привести постройки, которым ученые насчитывают более 1000 лет;
- готовые блоки можно размочить и полученную массу использовать повторно. Таким образом, материал не образует строительных отходов;
- в некотором смысле глина несет в себе божественную составляющую. В нескольких религиях именно этот материал использовался для сотворения человека, в частности Адама.
Единственным недостатком можно считать трудоемкие работы по внутренней и внешней отделке стен. Потому как блоки не отличаются ни идеальной геометрией, ни декоративной поверхностью. Слой выравнивающего материла, может составлять до 3 см.
- Такие поверхности можно лишь побелить, к сожалению, обои и краска «держаться» на глине не будут. Хотя в помещениях можно обшить гипсокартонными листами, тогда оформить интерьер можно будет любыми материалами.
- Но это касается лишь жилых домов, для хозяйственных построек вопросы, относящиеся к интерьеру или экстерьеру не актуальны.
Глина в строительстве
Глину используют в качестве основного материала для изготовления кирпичей, самана, черепицы и других керамических изделий. Также ее применяют в сыром виде для набивки стен, смазке (утеплении) потолков, при обустройстве кровли и оштукатуривании деревянных стен.
Из необожженных кирпичей возводят в основном одноэтажные постройки, хозяйственные блоки, гаражи. Такой строительный материал имеет несколько подвидов:
- кирпич-сырец – в основном используется для кладки внутренних стен и перегородок, потому как имеет слабую сопротивляемость к воздействию сырости и влаги;
- саман, в свою очередь, подразделяется на легкий и тяжелый. Это зависит от того, сколько частей соломы содержится в массе. Как правило, легкие блоки используются как утеплитель, а тяжелые – для кладки стен.
Изготовление саманного кирпича
- Стандартные размеры саманного кирпича, изготовленного своими руками – 40х20х20 см, габариты кирпича заводского исполнения – 33х16х12 или 33х17х13 см. Основное сырье лучше заготовить по осени, многократное замерзание/оттаивание глины лишь улучшает ее характеристики.
- В качестве армирования выступает рубленая солома (15-20 см), так как длинные стебли затрудняют работу. Солому и глину, необходимо заранее вымочить.
- Глина берется средней жирности, это позволит избежать больших трещин при сушке. Перед замесом глина освобождается от крупных примесей: веток, камней и т. д. Все составляющие тщательно перемешиваются посредством бетономешалки или по старому методу — ногами.
- Кирпичи формируют вручную, помещая глиняную массу в подготовленные формы без дна. Учитывая усушку, размеры матрицы должны быть на 1 см больше готового блока. Формы изготавливаются из пиломатериала, влагоустойчивой фанеры или металлических листов.
- Матрицы заранее выкладываются на ровную поверхность. При закладке смеси особое внимание уделяется угловым местам. Важно следить за плотным наполнением формы массой по краям и углам.
- Площадка должна иметь хороший сток, тогда несильный дождь для блоков не страшен. В противном случае заготовки лучше спрятать под навесом, закрыть досками или пленкой.
- В таком виде кирпичи будут сохнуть 3-ое суток, затем их вынимают и ставят на ребро, по истечении 2-3 дней блоки выставляются на другое ребро или на торец. Качество готовых блоков можно определить следующим образом:
- скинуть кирпич с 2-х метровой высоты, если он остался невредимым, значит, изготовление прошло правильно;
- изделие не должно размокнуть, потерять форму при длительном (1-2 дня) контакте с водой;
- на разломе блока не должны проявляться темные пятна влаги.
- Если взять около 13 тыс. кг глины, 70-75 кг соломы и 4 тыс. литров воды, то из полученной массы можно получить примерно 1 000 кирпичей. По теплоизоляции саманный блок толщиной в 30 см соответствует кирпичной кладке в 50-60 см.
Как построить дом из глины
Строительство стен можно осуществить четырьмя способами.
- Первый способ. Возведение строений посредством готовых блоков. В качестве связующего раствора выступает глинопесчаная смесь. Технология строительства ничем не отличается от кладки стен посредством газо-, пенобетонных блоков и подобных материалов.
- Второй способ. Данная технология требует определенных навыков. Сначала устанавливаются вертикальные стойки из бруса или бревен. Между ними переплетаются прутья (дранка). На каркас накидывается тонкими слоями саманная смесь с одной стороны, а после ее высыхания – с другой. Затем поверхность выравнивается при помощи этого же раствора.
- Третий способ. Он предполагает наличие большого количества пиломатериала. Сооружается опалубка, свободное пространство заполняется саманной массой и тщательно уминается (трамбуется). В процессе опалубка надстраивается до тех пор, пока стены не достигнут требуемой высоты.
- Четвертый способ. Это дом из дров и глины, в котором древесина выступает в роли блоков, а глина является связующим раствором.
Дом из глины своими руками
- Саманные строения не любят влажность, поэтому фундамент и цоколь делают из влагоустойчивых материалов. Для этого применяют кирпич, бутовый камень, бетонные блоки. Оптимальным основанием под дом послужит ленточный или свайно-набивной фундамент.
- Высота нижней части стены должна быть не менее 50 см. В обязательном порядке прокладываются гидроизоляционные материалы (толь, рубероид). Толщина цоколя должна превышать толщину стен, как с внутренней, так и внешней стороны примерно на 30 см.
- Защитить стены от попадания дождевых вод помогут карнизные свесы, которые должны выступать на 50 см. Также необходимо обустроить отмостки, чтобы снег и дождь не попадали на стеновые поверхности.
- При возведении стен летом в качестве связующего раствора используют глинопесчаную смесь с добавлением опилок или мелкорубленой соломы (пшеничной, ржаной и т. д.). Если строительство проходит весной или осенью, то лучше применить известково-цементный раствор.
Дом из глины видео
- Минимизировать усадку дома из глиняных блоков поможет тонкий слой связующей смеси в горизонтальных швах (до 1 см).
- Оконные и дверные проемы армируют толстыми стеблями тростника или тонкими досками. Этот же материал укладывают и в угловых сопряжениях. Проемы не следует располагать слишком близко к углам дома, минимальное расстояние 1,5 м.
- Для саманных стен используют только деревянные перекрытия. Крыша должна быть простых форм, а кровельные материалы – легкими. Для этих целей подойдет профильный лист, шифер, ондулин. Чтобы экстерьер строения выглядел современно, внешние стены можно обшить сайдингом или облицевать кирпичом.
- Оштукатуривание осуществляют спустя год после строительства. За данный период дом полностью усядется.
Штукатурка глиняных стен
- Оштукатуривание проводится в 2 слоя – черновое и финишное. Для 1-го слоя понадобится:
- глина;
- чистый песок средней фракции;
- опилки, которые должны быть просушенными и не иметь грибковых заболеваний.
- Сначала перемешиваются опилки с песком, затем добавляется глина и вода. Наличие опилок в растворе позволяет наносить смесь без применения специальной штукатурной сетки.
- Пропорция составляющих производится экспериментальным путем. В небольшой емкости перемешиваются 3 части песка и по 1 части глины и опилок, постепенно добавляется воды. Так как глина бывает разной жирности, то именно от этого компонента зависит эластичность массы.
- Из готовой смеси необходимо скрутить жгутик диаметром примерно 20 мм. Наличие трещин при сгибании жгута говорит о плохом качестве полученной массы. Если трещин нет, то в таких пропорциях замешивается раствор больших объемов.
- Саманная масса накидывается на стены небольшими порциями и разглаживается шпателем. Если смесь слегка подсохла, в нее добавляется вода. Толщина штукатурного слоя в зависимости от неровностей может составлять до 2-3 см.
- Для финишной отделки замешивается раствор из песка, цемента, глины и воды (3:1:1). Смесь должна быть немного жидкой, что значительно облегчит выравнивание поверхностей.
- Стоит отметить, что сушка слоев должна проходить в естественных условиях, и этот процесс может занять до 2-3 недель. Категорически запрещается использовать строительные фены для ускорения сушки. Подобные манипуляции приведут к растрескиванию слоев, тогда необходимо будет заделать все трещины и провести повторное финишное выравнивание.
И в заключение
Экологическая и экономическая составляющая жилого дома из глины очевидна. При соблюдении всех правил изготовления блоков и возведения стен, строение прослужит долгие десятилетия.
Как вариант можно рассмотреть довольно интересную идею, которую предложили итальянские разработчики – делать дома из глины на 3D-принтере для малоимущих граждан. Привести оборудование в рабочее состояние можно буквально за пару часов. Для обслуживания принтера необходимо всего 2 человека.
Конечно, эксплуатация такого жилья довольно коротка – около 5 лет, но как утверждают «строители» к этому времени можно напечатать и новый дом.
Строительство дома из опилок — Зеленые дома
Статья о строительстве дома из опилок и о том, как этот дом сохранился тридцать лет спустя.
Тридцать лет назад — сразу после Второй мировой войны, когда так много интересных вещей человеческого масштаба еще делалось на стольких полях — парень из Айдахо построил дом из опилок и бетона. И Popular Mechanics , среди других публикаций, сообщил о строительстве этого дома. Подходит для Popular Mechanics .
Беда только в том. . . С тех пор мы ждали следующего отчета, который расскажет нам, насколько хорошо это необычное здание выдержало испытание временем. И — поскольку не похоже, что кто-то еще заинтересован в этом продолжении, МАТЬ взялась за проект.
Итак, вот оригинальная история Popular Mechanics , написанная 30 лет назад. . . и новости MOTHER о доме Уэйт Фриберг из опилок / бетона, как он выглядит и работает сегодня.
Перепечатано с разрешения Popular Mechanics , авторское право © 1948, H.Х. Виндзор.
Любой, кто переживает возрождение давнего желания использовать опилки и стружку вместо песка и гравия, чтобы получить более легкий и дешевый бетон, должен познакомиться с крошечной диатомовой водорослью — чудо-природным растением — и с тем, как Уолт Фриберг использовал ее для сокращения затрат. в своем новом доме в Москве, штат Айдахо.
Стены, полы и крыша дома выполнены из этого опилочного бетона. Объединив древесные отходы и диатомовую землю, каждый кубический дюйм которой содержит миллионы микроскопических чудесных растений, Фриберг вдвое сократил стоимость этих частей своего дома и получил превосходную изоляцию.
Когда он вернулся на факультет сельскохозяйственной инженерии Университета Айдахо, Фриберг, ветеран армейских инженеров, стал искать дом.
Он видел опилки и стружку, сжигаемые как отходы на мельницах в его местности. Он понял, что построить дом из древесных отходов было давней мечтой. Большинство инженеров давно оставили надежды получить удовлетворительный древесный бетон. Когда смесь была бедной, чтобы использовать дешевые древесные отходы, полученный бетон не был прочным и горел почти так же быстро, как дерево.Когда смесь была достаточно густой, чтобы быть огнестойкой, дополнительный использованный цемент уничтожил большую часть экономии на песке и гравии, а также разрушил большую часть изоляционных свойств древесины.
Но во время войны Фриберг узнал кое-что о диатомовых водорослях, что придало ему смелости снова открыть старый вопрос. Кизельгур использовался в промышленности как изолятор и огнезащитный состав. Он видел, как волшебный материал, добавленный к бетонной смеси при строительстве гигантских мелиоративных дамб в Калифорнии, значительно повысил ее работоспособность.Возможно, диатомовая земля решит проблему опилок и бетона. Эта догадка оправдалась, и сегодня диатомовые водоросли находятся в центре внимания зданий.
Отложения диатомовых водорослей широко распространены в США. Некоторые из крупнейших месторождений находятся в Орегоне, Калифорнии, Неваде и Вашингтоне. Из-за его стратегического значения во время войны велись интенсивные поиски новых месторождений. Были найдены многие. Хотя большинство новых слишком малы или недостаточно чисты для промышленного использования, они подходят для бетона из опилок и стружки.
Во времена дедов диатомовая водоросль была просто интересным маленьким растением, на которое можно было смотреть в микроскоп. Школьные учителя поразили своих учеников чудесами природы, подняв небольшую щепотку диатомовой земли и сказав им, что она содержит тысячи и тысячи крошечных раковин.
Однако за последнее десятилетие диатомовая водоросль заняла ведущее место в промышленности. Он используется в зубной пасте, лаке для серебра и лаке для ногтей, в фильтрах очистки на сахарных заводах, в качестве изоляторов в высоковольтных двигателях и электрическом оборудовании, а также в качестве наполнителей в красках.Кизельгур имеет более сотни промышленных применений, в основном в химической, пищевой и фармацевтической областях.
Фриберг обнаружил, что когда небольшая часть цемента была заменена некоторым количеством диатомовой земли и добавлена небольшая часть обычной глины, в результате получился недорогой, обладающий высокими изоляционными свойствами, огнестойкий и легкий бетон. Стоимость, примерно половина стоимости обычного бетона, варьируется в зависимости от местности, в зависимости от наличия древесных отходов и расстояния от месторождения диатомитовой земли.
Бетон Фриберга не выдерживает больших нагрузок.Но поскольку один дюйм этого материала имеет изоляционную ценность от 12 до 14 дюймов обычного бетона, он отлично подходит для полов и стен, где требуется высокая изоляция и нагрузка может нести облицовка из кирпича или досок. Опилки-бетон можно распиливать, сверлить и забивать гвоздями, как и по дереву, и они обладают удивительной огнестойкостью. Вот смесь, которую он использовал: одна часть цемента, одна часть диатомитовой земли, три части опилок, три части стружки и одна часть глины. . . все измерения объема. Поскольку бетон из опилок имеет более высокую степень абсорбции, чем прямой бетон, Фриберг добавил в смесь одну часть глины.
Сначала в бетономешалку загружается глина. Если глина комковатая, перед использованием ее следует замочить на ночь. Затем засыпается диатомит, затем цемент. После тщательного перемешивания добавляют опилки и стружку.
В своем доме Фриберг использовал опилки заводской обработки, выдержанные около года. В ходе экспериментов он обнаружил, что новые опилки нежелательны. Также нет опилок, которые стояли так долго, что они белые. По его словам, годичный срок старения — это правильно.При стружке возраст не важен. Он использовал их зеленые, возрастом от года и старше. Все они работали хорошо.
В доме использовалась смесь опилок и стружки сосны, лиственницы и пихты. В отходах осталась кора. Фриберг не нашел возражений против этого, но он обнаружил, что кедровые и твердые древесные отходы не подходят.
Для использования диатомовых водорослей в домашних условиях не требуется специального оборудования. Литые блоки и кирпич Friberg в промышленном оборудовании для производства сборного железобетона.Он также отливал маленькие и большие плиты, используя простые формы, подобные тем, которые используются при строительстве домов из сырца. Поскольку бетон такой легкий, он вылил пол и крышу своего дома одной плитой.
Для испытания бетонных опилок компания Friberg отлила плиты размером 32 на 48 дюймов и толщиной один дюйм. Ближе к краю этих плит он забивал гвозди за восемь пенсов и просверливал ряды отверстий с помощью дрели. Расщепления не было. Потом пил пилой порезал полосы шириной в дюйм. С помощью шлифовальной машины он создал гладкую поверхность, которую можно было красить.Он проверил плиту на изоляционные свойства и обнаружил, что она равна футу или более бетону.
Фриберг считает, что плита размером 3-5 / 8 на 32 на 48 дюймов, которую можно собирать и отверждать в свободное время, будет полезна в хозяйственных постройках. Этот размер будет охватывать две стойки или балки пола или может быть распилен, чтобы поместиться между стойками. Фермеры Северо-Запада уже проявляют интерес к его использованию для молочных коровников и птичников, где существует большая потребность в недорогом материале, обладающем высокой изоляционной способностью.
Когда-нибудь будет найден способ гидроизоляции бетона.До тех пор Фриберг рекомендует использовать его только в помещении. Есть еще одно ограничение. Обладая прочностью нагрузки от одной четверти до одной трети, чем у обычного бетона, он не может использоваться на тротуарах или проездах, а также для полов и стен, которые несут большие нагрузки.
Но даже если эти ограничения никогда не будут полностью преодолены, Фриберг видит огромное поле для крошечной диатомовой водоросли, кучи опилок и стружки. Пол в его гостиной, например, представляет собой сплошной блок из недорогого материала.Прямо на него крепятся ковролин и линолеум. Крыша также представляет собой цельный блок, покрытый рубероидом и измельченной пемзой. В стенах его дома основную нагрузку несет слой обычных бетонных кирпичей. Утеплитель обеспечивают опилочно-бетонные кирпичи двойной толщины.
Поскольку месторождения диатомита были исследованы во время войны, государственные департаменты геологии и шахтные школы имеют информацию об их местонахождении. Итак, если потенциальный строитель может найти удобную кучу опилок и стружки сосны, лиственницы или пихты и недалеко от месторождения диатомовой земли, Фриберг нашел способ собрать их вместе, чтобы произвести новый вид недорогого стройматериала.
Дом Фрибергов 30 лет спустя
Недавно сотрудники MOTHER Мартин Фокс и Трэвис Брок отправились в Москву, штат Айдахо, чтобы найти дом из древесного волокна / диатомита / бетона, о котором 30 лет назад сообщал Popular Mechanics (см. Предыдущий рассказ). Наши бесстрашные сотрудники хотели узнать: сохранилось ли первоначальное здание? Бетонная смесь осела, потрескалась или распалась? Как сооружение выдержало тридцать лет холодных зим в Айдахо?
Ответы на эти вопросы — Мартин и Трэвис быстро усвоили — были «да», «нет» и «очень хорошо, спасибо».
Оказывается, пара по имени Рэй и Барбара Харрисон 23 года назад купила необычный дом из опилок у строителя-новатора дома — Уэйта Фриберга. Рэй и его жена, которые вырастили семерых детей в особенном доме, утверждают, что дом на протяжении многих лет служил им хорошей службой. Основная структура по-прежнему в хорошем состоянии и не имеет признаков разрушения.
Что касается тех «холодных зим в Айдахо», Рэй Харрисон говорит, что — отчасти благодаря отличным изоляционным свойствам опилок — бетонных стен — счета за отопление его семьи обычно составляют на 30-40 долларов в месяц меньше, чем у их соседей, которые живут в однотипные дома обычной постройки.Рэй, однако, быстро добавляет, что по крайней мере часть этой экономии тепла может быть отнесена на счет «пассивных» конструктивных особенностей солнечного тепла, которые Уолт Фриберг внедрил в дом.
Например, северная сторона дома выстроена на склоне, а большие окна закрывают большую часть южной стороны дома. Более того, прямо над окнами, выходящими на южную сторону, находится серия алюминиевых отражателей, которые направляют в жилище даже больше энергии зимнего солнца, чем обычно проникает внутрь.(Те же самые отражатели несколько затемняют окна и помогают защищать от нежелательной жары летом). Ночью, семья Харрисонов; «закрыть» солнечное тепло в здании, натянув прочно изолированные шторы за окнами, выходящими на юг.
Если вы до сих пор следили за этой историей, вам может быть интересно [1], были ли когда-либо построены какие-либо другие конструкции с использованием «древесно-волокнистого и диатомитового» бетона, разработанного Вальтером Фрибергом, и [2] что с этим случилось? во всяком случае, умный парень Фриберг.Что ж, Уолт — за эти годы — построил или помог построить около 30-40 зданий из опилок в северном Айдахо / восточном районе Вашингтона. . . и он все еще работает с материалом. Уолт говорит, что он считает, что с точки зрения стоимости материалов и энергии его необычная бетонная смесь сегодня даже более привлекательна, чем 30 лет назад.
Первоначально опубликовано: январь / февраль 1978 г.
% PDF-1.3 % 66 0 объект > эндобдж xref 66 1596 0000000016 00000 н. 0000032271 00000 п. 0000034115 00000 п. 0000034330 00000 п. 0000053395 00000 п. 0000053445 00000 п. 0000053495 00000 п. 0000053545 00000 п. 0000053595 00000 п. 0000053645 00000 п. 0000053695 00000 п. 0000053745 00000 п. 0000053795 00000 п. 0000053845 00000 п. 0000053895 00000 п. 0000053945 00000 п. 0000053995 00000 п. 0000054045 00000 п. 0000054095 00000 п. 0000054145 00000 п. 0000054195 00000 п. 0000054245 00000 п. 0000054295 00000 п. 0000054345 00000 п. 0000054395 00000 п. 0000054445 00000 п. 0000054495 00000 п. 0000054545 00000 п. 0000054595 00000 п. 0000054645 00000 п. 0000054695 00000 п. 0000054745 00000 п. 0000054795 00000 п. 0000054845 00000 п. 0000054895 00000 п. 0000054946 00000 п. 0000054997 00000 п. 0000055048 00000 п. 0000055099 00000 п. 0000055150 00000 п. 0000055201 00000 п. 0000055252 00000 п. 0000055303 00000 п. 0000055354 00000 п. 0000055405 00000 п. 0000055456 00000 п. 0000055507 00000 п. 0000055558 00000 п. 0000055609 00000 п. 0000055660 00000 п. 0000055711 00000 п. 0000055762 00000 п. 0000055813 00000 п. 0000055864 00000 п. 0000055915 00000 п. 0000055966 00000 п. 0000056017 00000 п. 0000056068 00000 п. 0000056119 00000 п. 0000056170 00000 п. 0000056221 00000 п. 0000056272 00000 п. 0000056323 00000 п. 0000056374 00000 п. 0000056425 00000 п. 0000056476 00000 п. 0000056527 00000 п. 0000056578 00000 п. 0000056629 00000 п. 0000056680 00000 п. 0000056731 00000 п. 0000056782 00000 п. 0000056833 00000 п. 0000056884 00000 п. 0000056935 00000 п. 0000056986 00000 п. 0000057037 00000 п. 0000057088 00000 п. 0000057139 00000 п. 0000057190 00000 п. 0000057241 00000 п. 0000057292 00000 п. 0000057343 00000 п. 0000057394 00000 п. 0000057445 00000 п. 0000057496 00000 п. 0000057547 00000 п. 0000057598 00000 п. 0000057649 00000 п. 0000057700 00000 п. 0000057751 00000 п. 0000057802 00000 п. 0000057853 00000 п. 0000057904 00000 п. 0000057955 00000 п. 0000058006 00000 п. 0000058057 00000 п. 0000058108 00000 п. 0000058159 00000 п. 0000058210 00000 п. 0000058261 00000 п. 0000058312 00000 п. 0000058363 00000 п. 0000058414 00000 п. 0000058465 00000 п. 0000058516 00000 п. 0000058567 00000 п. 0000058618 00000 п. 0000058669 00000 п. 0000058720 00000 н. 0000058771 00000 п. 0000058822 00000 п. 0000058873 00000 п. 0000058924 00000 п. 0000058975 00000 п. 0000059026 00000 п. 0000059077 00000 п. 0000059128 00000 п. 0000059179 00000 п. 0000059230 00000 п. 0000059281 00000 п. 0000059332 00000 п. 0000059383 00000 п. 0000059434 00000 п. 0000059485 00000 п. 0000059536 00000 п. 0000059587 00000 п. 0000059638 00000 п. 0000059689 00000 п. 0000059740 00000 п. 0000059791 00000 п. 0000059842 00000 п. 0000059893 00000 п. 0000059944 00000 н. 0000059995 00000 н. 0000060046 00000 п. 0000060097 00000 п. 0000060148 00000 п. 0000060199 00000 п. 0000060250 00000 п. 0000060301 00000 п. 0000060352 00000 п. 0000060403 00000 п. 0000060454 00000 п. 0000060505 00000 п. 0000060556 00000 п. 0000060607 00000 п. 0000060658 00000 п. 0000060709 00000 п. 0000060760 00000 п. 0000060811 00000 п. 0000060862 00000 п. 0000060913 00000 п. 0000060964 00000 п. 0000061015 00000 п. 0000061066 00000 п. 0000061117 00000 п. 0000061168 00000 п. 0000061219 00000 п. 0000061270 00000 п. 0000061321 00000 п. 0000061372 00000 п. 0000061423 00000 п. 0000061474 00000 п. 0000061525 00000 п. 0000061576 00000 п. 0000061627 00000 п. 0000061678 00000 п. 0000061729 00000 п. 0000061780 00000 п. 0000061831 00000 п. 0000061882 00000 п. 0000061933 00000 п. 0000061984 00000 п. 0000062035 00000 п. 0000062086 00000 п. 0000062137 00000 п. 0000062188 00000 п. 0000062239 00000 п. 0000062290 00000 н. 0000062341 00000 п. 0000062392 00000 п. 0000062443 00000 п. 0000062494 00000 п. 0000062545 00000 п. 0000062596 00000 п. 0000062647 00000 н. 0000062698 00000 п. 0000062749 00000 п. 0000062800 00000 п. 0000062851 00000 п. 0000062902 00000 п. 0000062953 00000 п. 0000063004 00000 п. 0000063055 00000 п. 0000063106 00000 п. 0000063157 00000 п. 0000063208 00000 п. 0000063259 00000 п. 0000063310 00000 п. 0000063361 00000 п. 0000063412 00000 п. 0000063463 00000 п. 0000063514 00000 п. 0000063565 00000 п. 0000063616 00000 п. 0000063667 00000 п. 0000063718 00000 п. 0000063769 00000 п. 0000063820 00000 п. 0000063871 00000 п. 0000063922 00000 п. 0000063973 00000 п. 0000064024 00000 п. 0000064075 00000 п. 0000064126 00000 п. 0000064177 00000 п. 0000064228 00000 п. 0000064279 00000 н. 0000064330 00000 н. 0000064381 00000 п. 0000064432 00000 п. 0000064483 00000 п. 0000064534 00000 п. 0000064585 00000 п. 0000064636 00000 н. 0000064687 00000 п. 0000064738 00000 п. 0000064789 00000 п. 0000064840 00000 п. 0000064891 00000 п. 0000064942 00000 п. 0000064993 00000 п. 0000065044 00000 п. 0000065095 00000 п. 0000065146 00000 п. 0000065197 00000 п. 0000065248 00000 п. 0000065299 00000 п. 0000065350 00000 п. 0000065401 00000 п. 0000065452 00000 п. 0000065503 00000 п. 0000065554 00000 п. 0000065605 00000 п. 0000065656 00000 п. 0000065707 00000 п. 0000065758 00000 п. 0000065809 00000 п. 0000065860 00000 п. 0000065911 00000 п. 0000065962 00000 п. 0000066013 00000 п. 0000066064 00000 п. 0000066115 00000 п. 0000066166 00000 п. 0000066217 00000 п. 0000066268 00000 п. 0000066319 00000 п. 0000066370 00000 п. 0000066421 00000 п. 0000066472 00000 н. 0000066523 00000 п. 0000066574 00000 п. 0000066625 00000 п. 0000066676 00000 п. 0000066727 00000 п. 0000066778 00000 п. 0000066829 00000 п. 0000066880 00000 п. 0000066931 00000 п. 0000066982 00000 п. 0000067033 00000 п. 0000067084 00000 п. 0000067135 00000 п. 0000067186 00000 п. 0000067237 00000 п. 0000067288 00000 п. 0000067339 00000 п. 0000067390 00000 п. 0000067441 00000 п. 0000067492 00000 п. 0000067543 00000 п. 0000067594 00000 п. 0000067645 00000 п. 0000067696 00000 п. 0000067747 00000 п. 0000067798 00000 п. 0000067849 00000 п. 0000067900 00000 н. 0000067951 00000 п. 0000068002 00000 п. 0000068053 00000 п. 0000068104 00000 п. 0000068155 00000 п. 0000068206 00000 п. 0000068257 00000 п. 0000068308 00000 п. 0000068359 00000 п. 0000068410 00000 п. 0000068461 00000 п. 0000068512 00000 п. 0000068563 00000 п. 0000068614 00000 п. 0000068665 00000 п. 0000068716 00000 п. 0000068767 00000 п. 0000068818 00000 п. 0000068869 00000 п. 0000068920 00000 н. 0000068971 00000 п. 0000069022 00000 н. 0000069073 00000 п. 0000069124 00000 п. 0000069175 00000 п. 0000069226 00000 п. 0000069277 00000 п. 0000069328 00000 п. 0000069379 00000 п. 0000069430 00000 п. 0000069481 00000 п. 0000069532 00000 п. 0000069583 00000 п. 0000069634 00000 п. 0000069685 00000 п. 0000069736 00000 п. 0000069787 00000 п. 0000069838 00000 п. 0000069889 00000 п. 0000069940 00000 н. 0000069991 00000 н. 0000070042 00000 п. 0000070093 00000 п. 0000070144 00000 п. 0000070195 00000 п. 0000070246 00000 п. 0000070297 00000 п. 0000070348 00000 п. 0000070399 00000 п. 0000070450 00000 п. 0000070501 00000 п. 0000070552 00000 п. 0000070603 00000 п. 0000070654 00000 п. 0000070705 00000 п. 0000070756 00000 п. 0000070807 00000 п. 0000070858 00000 п. 0000070909 00000 п. 0000070960 00000 п. 0000071011 00000 п. 0000071062 00000 п. 0000071113 00000 п. 0000071164 00000 п. 0000071215 00000 п. 0000071266 00000 п. 0000071317 00000 п. 0000071368 00000 п. 0000071391 00000 п. 0000072478 00000 п. 0000072500 00000 н. 0000073465 00000 п. 0000073487 00000 п. 0000074485 00000 п. 0000074508 00000 п. 0000075609 00000 п. 0000075632 00000 п. 0000076847 00000 п. 0000077077 00000 п. 0000077301 00000 п. 0000077863 00000 п. 0000077904 00000 п. 0000078480 00000 п. 0000078502 00000 п. 0000079511 00000 п. 0000079534 00000 п. 0000081420 00000 н. 0000081443 00000 п. 0000083978 00000 п. 0000084218 00000 п. 0000084500 00000 п. 0000084867 00000 н. 0000085104 00000 п. 0000085385 00000 п. 0000085625 00000 п. 0000085928 00000 п. 0000086165 00000 п. 0000086405 00000 п. 0000086642 00000 п. 0000086934 00000 п. 0000087232 00000 п. 0000087472 00000 п. 0000087764 00000 п. 0000087986 00000 п. 0000088272 00000 н. 0000088640 00000 п. 0000088871 00000 п. 0000089186 00000 п. 0000089393 00000 п. 0000089684 00000 п. 0000089894 00000 н. 00000 00000 п. 00000
00000 н. 00000 00000 п. 00000 00000 п. 0000091169 00000 п. 0000091462 00000 п. 0000091702 00000 п. 0000091944 00000 п. 0000092172 00000 п. 0000092461 00000 п. 0000092745 00000 п. 0000092978 00000 п. 0000093221 00000 п. 0000093458 00000 п. 0000093719 00000 п. 0000093929 00000 п. 0000094166 00000 п. 0000094462 00000 п. 0000094696 00000 п. 0000094943 00000 п. 0000095174 00000 п. 0000095411 00000 п. 0000095686 00000 п. 0000095902 00000 п. 0000096279 00000 н. 0000096510 00000 п. 0000096719 00000 п. 0000096947 00000 п. 0000097274 00000 п. 0000097599 00000 п. 0000097919 00000 п. 0000098132 00000 п. 0000098366 00000 п. 0000098570 00000 п. 0000098830 00000 н. 0000099160 00000 п. 0000099389 00000 н. 0000099708 00000 п. 0000100020 00000 н. 0000100257 00000 н. 0000100575 00000 н. 0000100886 00000 н. 0000101120 00000 н. 0000101357 00000 н. 0000101660 00000 н. 0000102030 00000 н. 0000102258 00000 н. 0000102633 00000 п. 0000102870 00000 п. 0000103110 00000 н. 0000103338 00000 н. 0000103583 00000 п. 0000103848 00000 н. 0000104140 00000 н. 0000104374 00000 п. 0000104611 00000 п. 0000104845 00000 н. 0000105173 00000 п. 0000105467 00000 н. 0000105804 00000 п. 0000105992 00000 н. 0000106170 00000 п. 0000106389 00000 п. 0000106576 00000 н. 0000106759 00000 н. 0000106978 00000 п. 0000107326 00000 н. 0000107551 00000 п. 0000107736 00000 п. 0000107922 00000 п. 0000108281 00000 п. 0000108470 00000 п. 0000108665 00000 п. 0000108926 00000 н. 0000109112 00000 н. 0000109297 00000 н. 0000109537 00000 п. 0000109875 00000 п. 0000110127 00000 н. 0000110314 00000 п. 0000110506 00000 н. 0000110855 00000 н. 0000111047 00000 н. 0000111227 00000 н. 0000111410 00000 н. 0000111602 00000 н. 0000149461 00000 н. 0000178046 00000 н. 0000180724 00000 н. 0000180803 00000 н. 0000180992 00000 н. 0000181346 00000 н. 0000181524 00000 н. 0000181702 00000 н. 0000181915 00000 н. 0000182252 00000 н. 0000182431 00000 н. 0000182635 00000 н. 0000182830 00000 н. 0000183019 00000 н. 0000183203 00000 н. 0000183375 00000 н. 0000183713 00000 н. 0000184051 00000 н. 0000184383 00000 н. 0000184573 00000 н. 0000184764 00000 н. 0000185059 00000 н. 0000185249 00000 н. 0000185436 00000 н. 0000185731 00000 н. 0000186096 00000 н. 0000186389 00000 п. 0000186577 00000 н. 0000186778 00000 н. 0000186947 00000 н. 0000187307 00000 н. 0000187595 00000 н. 0000187921 00000 н. 0000188097 00000 н. 0000188272 00000 н. 0000188456 00000 н. 0000188747 00000 н. 0000189076 00000 н. 0000189270 00000 н. 0000189457 00000 н. 0000189642 00000 н. 0000189980 00000 н. 00001 00000 н. 00001 00000 н. 00001 00000 н. 00001 00000 н. 0000191109 00000 н. 0000191301 00000 н. 0000191493 00000 н. 0000191769 00000 н. 0000191960 00000 н. 0000192310 00000 н. 0000192502 00000 н. 0000192694 00000 н. 0000192982 00000 н. 0000193312 00000 н. 0000193498 00000 н. 0000193800 00000 н. 0000194081 00000 н. 0000194276 00000 н. 0000194468 00000 н. 0000194657 00000 н. 0000194987 00000 н. 0000195194 00000 н. 0000195518 00000 н. 0000195881 00000 н. 0000196232 00000 н. 0000196542 00000 н. 0000196895 00000 н. 0000197249 00000 н. 0000197449 00000 н. 0000197779 00000 п. 0000198110 00000 н. 0000198385 00000 н. 0000198707 00000 н. 0000198976 00000 н. 0000199294 00000 н. 0000199612 00000 н. 0000199933 00000 н. 0000200297 00000 н. 0000200662 00000 н. 0000200979 00000 н. 0000201257 00000 н. 0000201616 00000 н. 0000201937 00000 н. 0000202264 00000 н. 0000202478 00000 н. 0000202828 00000 н. 0000203045 00000 н. 0000203402 00000 н. 0000203597 00000 н. 0000203796 00000 н. 0000203994 00000 н. 0000204371 00000 н. 0000204734 00000 н. 0000205009 00000 н. 0000205225 00000 н. 0000205444 00000 н. 0000205663 00000 н. 0000206016 00000 н. 0000206294 00000 н. 0000206650 00000 н. 0000206845 00000 н. 0000207035 00000 н. 0000207229 00000 н. 0000207507 00000 н. 0000207862 00000 н. 0000208228 00000 н. 0000208444 00000 н. 0000208809 00000 н. 0000209109 00000 н. 0000209452 00000 н. 0000209740 00000 н. 0000210032 00000 н. 0000210392 00000 п. 0000210673 00000 н. 0000210966 00000 н. 0000211266 00000 н. 0000211564 00000 н. 0000211907 00000 н. 0000212202 00000 н. 0000212565 00000 н. 0000212845 00000 н. 0000213130 00000 н. 0000213419 00000 п. 0000213777 00000 н. 0000214054 00000 н. 0000214338 00000 н. 0000214685 00000 н. 0000214960 00000 н. 0000215241 00000 н. 0000215582 00000 н. 0000215889 00000 н. 0000216204 00000 н. 0000216519 00000 н. 0000216843 00000 н. 0000217129 00000 н. 0000217445 00000 н. 0000217785 00000 н. 0000218128 00000 н. 0000218455 00000 н. 0000218776 00000 п. 0000219097 00000 н. 0000219371 00000 п. 0000219692 00000 н. 0000219978 00000 н. 0000220251 00000 н. 0000220570 00000 н. 0000220858 00000 н. 0000221128 00000 н. 0000221422 00000 н. 0000221734 00000 н. 0000222049 00000 н. 0000222409 00000 н. 0000222712 00000 н. 0000223018 00000 н. 0000223237 00000 н. 0000223500 00000 н. 0000223688 00000 н. 0000223894 00000 н. 0000224229 00000 н. 0000224434 00000 н. 0000224765 00000 н. 0000224945 00000 н. 0000225151 00000 н. 0000225477 00000 н. 0000225676 00000 н. 0000226039 00000 н. 0000226252 00000 н. 0000226480 00000 н. 0000226815 00000 н. 0000227077 00000 н. 0000227299 00000 н. 0000227637 00000 н. 0000227969 00000 н. 0000228151 00000 п. 0000228376 00000 п. 0000228566 00000 н. 0000228830 00000 н. 0000229088 00000 н. 0000229316 00000 н. 0000229580 00000 н. 0000229902 00000 н. 0000230115 00000 н. 0000230445 00000 н. 0000230770 00000 н. 0000230975 00000 п. 0000231209 00000 н. 0000231469 00000 н. 0000231833 00000 н. 0000232054 00000 н. 0000232425 00000 н. 0000232619 00000 н. 0000232815 00000 н. 0000233001 00000 н. 0000233338 00000 п. 0000233668 00000 н. 0000233991 00000 н. 0000234204 00000 н. 0000234406 00000 п. 0000234616 00000 н. 0000234870 00000 н. 0000235080 00000 н. 0000235440 00000 н. 0000235665 00000 н. 0000235869 00000 н. 0000236246 00000 н. 0000236444 00000 н. 0000236645 00000 н. 0000236870 00000 н. 0000237229 00000 н. 0000237503 00000 н. 0000237718 00000 н. 0000238083 00000 н. 0000238305 00000 н. 0000238666 00000 н. 0000238939 00000 н. 0000239301 00000 н. 0000239496 00000 н. 0000239700 00000 н. 0000239968 00000 н. 0000240187 00000 н. 0000240388 00000 н. 0000240610 00000 н. 0000240966 00000 н. 0000241328 00000 н. 0000241538 00000 н. 0000241805 00000 н. 0000242153 00000 н. 0000242360 00000 н. 0000242588 00000 н. 0000242816 00000 н. 0000243042 00000 н. 0000243377 00000 н. 0000243752 00000 н. 0000244097 00000 н. 0000244307 00000 н. 0000244665 00000 н. 0000245023 00000 н. 0000245227 00000 н. 0000245449 00000 н. 0000245650 00000 н. 0000245923 00000 н. 0000246298 00000 н. 0000246564 00000 н. 0000246789 00000 н. 0000246990 00000 н. 0000247209 00000 н. 0000247566 00000 н. 0000247746 00000 н. 0000247929 00000 н. 0000248112 00000 н. 0000248298 00000 н. 0000248484 00000 н. 0000248670 00000 н. 0000248859 00000 н. 0000249048 00000 н. 0000249238 00000 п. 0000249428 00000 н. 0000249618 00000 н. 0000249798 00000 н. 0000249991 00000 н. 0000250171 00000 н. 0000250364 00000 н. 0000250543 00000 н. 0000250739 00000 н. 0000250921 00000 н. 0000251117 00000 н. 0000251299 00000 н. 0000251494 00000 н. 0000251676 00000 н. 0000251876 00000 н. 0000252061 00000 н. 0000252261 00000 н. 0000252446 00000 н. 0000252647 00000 н. 0000252832 00000 н. 0000253035 00000 н. 0000253220 00000 н. 0000253423 00000 н. 0000253611 00000 н. 0000253818 00000 н. 0000254006 00000 н. 0000254213 00000 н. 0000254403 00000 н. 0000254613 00000 н. 0000254803 00000 н. 0000255013 00000 н. 0000255203 00000 н. 0000255416 00000 н. 0000255606 00000 н. 0000255819 00000 н. 0000256012 00000 н. 0000256228 00000 н. 0000256421 00000 н. 0000256637 00000 н. 0000256830 00000 н. 0000257046 00000 н. 0000257242 00000 н. 0000257461 00000 н. 0000257657 00000 н. 0000257876 00000 н. 0000258072 00000 н. 0000258291 00000 н. 0000258490 00000 н. 0000258712 00000 н. 0000258911 00000 н. 0000259133 00000 н. 0000259332 00000 н. 0000259553 00000 н. 0000259755 00000 н. 0000259981 00000 н. 0000260183 00000 п. 0000260363 00000 п. 0000260588 00000 н. 0000260790 00000 н. 0000260970 00000 н. 0000261196 00000 н. 0000261398 00000 н. 0000261581 00000 н. 0000261810 00000 н. 0000261990 00000 н. 0000262196 00000 п. 0000262379 00000 п. 0000262608 00000 н. 0000262812 00000 н. 0000262994 00000 н. 0000263226 00000 н. 0000263435 00000 н. 0000263621 00000 н. 0000263851 00000 н. 0000264060 00000 н. 0000264246 00000 н. 0000264479 00000 н. 0000264688 00000 н. 0000264873 00000 н. 0000265108 00000 п. 0000265320 00000 н. 0000265505 00000 н. 0000265741 00000 н. 0000265954 00000 н. 0000266143 00000 п. 0000266380 00000 н. 0000266593 00000 н. 0000266782 00000 н. 0000267020 00000 н. 0000267233 00000 н. 0000267423 00000 н. 0000267651 00000 н. 0000267831 00000 н. 0000268043 00000 н. 0000268233 00000 н. 0000268473 00000 н. 0000268686 00000 н. 0000268876 00000 н. 0000269117 00000 н. 0000269335 00000 н. 0000269515 00000 н. 0000269705 00000 н. 0000269917 00000 н. 0000270097 00000 н. 0000270290 00000 н. 0000270502 00000 н. 0000270682 00000 н. 0000270876 00000 н. 0000271089 00000 н. 0000271272 00000 н. 0000271465 00000 н. 0000271678 00000 н. 0000271861 00000 н. 0000272054 00000 н. 0000272267 00000 н. 0000272449 00000 н. 0000272645 00000 н. 0000272857 00000 н. 0000273039 00000 н. 0000273238 00000 н. 0000273450 00000 н. 0000273632 00000 н. 0000273831 00000 н. 0000274043 00000 н. 0000274225 00000 н. 0000274423 00000 н. 0000274635 00000 н. 0000274817 00000 н. 0000275016 00000 н. 0000275229 00000 н. 0000275415 00000 н. 0000275618 00000 н. 0000275831 00000 н. 0000276017 00000 н. 0000276220 00000 н. 0000276433 00000 н. 0000276622 00000 н. 0000276825 00000 н. 0000277037 00000 н. 0000277226 00000 н. 0000277429 00000 н. 0000277641 00000 н. 0000277830 00000 н. 0000278037 00000 н. 0000278250 00000 н. 0000278439 00000 н. 0000278619 00000 н. 0000278826 00000 н. 0000279039 00000 н. 0000279228 00000 н. 0000279438 00000 н. 0000279651 00000 н. 0000279840 00000 н. 0000280050 00000 н. 0000280263 00000 н. 0000280452 00000 н. 0000280662 00000 н. 0000280875 00000 н. 0000281064 00000 н. 0000281277 00000 н. 0000281490 00000 н. 0000281680 00000 н. 0000281893 00000 н. 0000282106 00000 н. 0000282296 00000 н. 0000282511 00000 н. 0000282724 00000 н. 0000282917 00000 н. 0000283130 00000 н. 0000283344 00000 п. 0000283537 00000 н. 0000283753 00000 н. 0000283967 00000 н. 0000284160 00000 н. 0000284376 00000 п. 0000284590 00000 н. 0000284783 00000 н. 0000284999 00000 н. 0000285213 00000 н. 0000285406 00000 н. 0000285625 00000 н. 0000285839 00000 н. 0000286032 00000 н. 0000286253 00000 н. 0000286467 00000 н. 0000286663 00000 н. 0000286885 00000 н. 0000287099 00000 н. 0000287295 00000 н. 0000287518 00000 п. 0000287732 00000 н. 0000287929 00000 п. 0000288153 00000 н. 0000288368 00000 н. 0000288565 00000 н. 0000288787 00000 н. 0000289002 00000 н. 0000289203 00000 н. 0000289428 00000 н. 0000289643 00000 н. 0000289844 00000 н. 0000200000 н. 00002
00000 н. 00002
00000 н. 00002
00000 н. 00002
00000 н. 0000291131 00000 н. 0000291361 00000 н. 0000291576 00000 н. 0000291777 00000 н. 0000292007 00000 н. 0000292222 00000 н. 0000292426 00000 н. 0000292656 00000 н. 0000292872 00000 н. 0000293076 00000 н. 0000293309 00000 н. 0000293525 00000 н. 0000293729 00000 н. 0000293962 00000 н. 0000294178 00000 п. 0000294386 00000 п. 0000294620 00000 н. 0000294836 00000 н. 0000295106 00000 н. 0000295322 00000 н. 0000295592 00000 н. 0000295808 00000 н. 0000296078 00000 н. 0000296294 00000 н. 0000296558 00000 н. 0000296774 00000 н. 0000297037 00000 н. 0000297253 00000 н. 0000297512 00000 н. 0000297693 00000 н. 0000297911 00000 п. 0000298172 00000 н. 0000298392 00000 н. 0000298657 00000 н. 0000298877 00000 н. 0000299147 00000 н. 0000299371 00000 н. 0000299637 00000 н. 0000299818 00000 н. 0000300042 00000 н. 0000300306 00000 н. 0000300532 00000 н. 0000300795 00000 н. 0000301022 00000 н. 0000301288 00000 н. 0000301469 00000 н. 0000301698 00000 н. 0000301959 00000 н. 0000302189 00000 п. 0000302453 00000 н. 0000302685 00000 н. 0000302947 00000 н. 0000303179 00000 н. 0000303442 00000 н. 0000303674 00000 н. 0000303939 00000 н. 0000304170 00000 н. 0000304436 00000 н. 0000304667 00000 н. 0000304933 00000 н. 0000305164 00000 п. 0000305430 00000 н. 0000305661 00000 н. 0000305931 00000 н. 0000306162 00000 н. 0000306427 00000 н. 0000306658 00000 п. 0000306921 00000 н. 0000307151 00000 н. 0000307411 00000 н. 0000307641 00000 н. 0000307902 00000 н. 0000308132 00000 н. 0000308397 00000 н. 0000308626 00000 н. 0000308891 00000 н. 0000309121 00000 н. 0000309392 00000 н. 0000309621 00000 н. 0000309890 00000 н. 0000310119 00000 п. 0000310383 00000 п. 0000310612 00000 н. 0000310881 00000 н. 0000311062 00000 н. 0000311291 00000 н. 0000311557 00000 н. 0000311738 00000 н. 0000311967 00000 н. 0000312231 00000 п. 0000312412 00000 н. 0000312596 00000 н. 0000312825 00000 н. 0000313087 00000 н. 0000313277 00000 н. 0000313506 00000 н. 0000313771 00000 п. 0000313955 00000 н. 0000314146 00000 н. 0000314375 00000 н. 0000314644 00000 н. 0000314845 00000 н. 0000315073 00000 н. 0000315344 00000 н. 0000315525 00000 н. 0000315729 00000 н. 0000315957 00000 н. 0000316225 00000 н. 0000316439 00000 н. 0000316667 00000 н. 0000316888 00000 н. 0000317116 00000 н. 0000317337 00000 н. 0000317565 00000 н. 0000317786 00000 н. 0000318014 00000 н. 0000318234 00000 н. 0000318461 00000 п. 0000318682 00000 н. 0000318909 00000 н. 0000319129 00000 н. 0000319356 00000 н. 0000319576 00000 н. 0000319803 00000 н. 0000320023 00000 н. 0000320250 00000 н. 0000320470 00000 н. 0000320696 00000 н. 0000320916 00000 н. 0000321142 00000 н. 0000321362 00000 н. 0000321588 00000 н. 0000321808 00000 н. 0000322034 00000 н. 0000322254 00000 н. 0000322480 00000 н. 0000322700 00000 н. 0000322926 00000 н. 0000323146 00000 н. 0000323372 00000 н. 0000323592 00000 н. 0000323817 00000 н. 0000324037 00000 н. 0000324262 00000 н. 0000324481 00000 н. 0000324706 00000 н. 0000324925 00000 н. 0000325150 00000 н. 0000325369 00000 н. 0000325594 00000 н. 0000325814 00000 н. 0000326039 00000 н. 0000326258 00000 н. 0000326483 00000 н. 0000326702 00000 н. 0000326926 00000 н. 0000327144 00000 н. 0000327367 00000 н. 0000327585 00000 н. 0000327809 00000 н. 0000328027 00000 н. 0000328251 00000 н. 0000328470 00000 н. 0000328694 00000 н. 0000328912 00000 н. 0000329135 00000 н. 0000329354 00000 н. 0000329578 00000 н. 0000329795 00000 н. 0000330019 00000 н. 0000330237 00000 н. 0000330460 00000 н. 0000330678 00000 н. 0000330901 00000 н. 0000331119 00000 п. 0000331342 00000 н. 0000331560 00000 н. 0000331781 00000 н. 0000331998 00000 н. 0000332219 00000 н. 0000332436 00000 н. 0000332657 00000 н. 0000332874 00000 н. 0000333135 00000 н. 0000333396 00000 н. 0000333656 00000 н. 0000333916 00000 н. 0000334175 00000 н. 0000334434 00000 п. 0000334693 00000 п. 0000334951 00000 п. 0000335209 00000 н. 0000335467 00000 н. 0000335724 00000 н. 0000335981 00000 п. 0000336237 00000 н. 0000336493 00000 н. 0000336749 00000 н. 0000337004 00000 н. 0000337259 00000 н. 0000337514 00000 н. 0000337768 00000 н. 0000338022 00000 н. 0000338203 00000 н. 0000338456 00000 н. 0000338640 00000 н. 0000338821 00000 н. 0000339075 00000 н. 0000339262 00000 н. 0000339515 00000 н. 0000339702 00000 н. 0000339956 00000 н. 0000340143 00000 н. 0000340396 00000 н. 0000340586 00000 н. 0000340839 00000 н. 0000341029 00000 н. 0000341281 00000 н. 0000341472 00000 н. 0000341724 00000 н. 0000341918 00000 н. 0000342170 00000 н. 0000342363 00000 н. 0000342615 00000 н. 0000342812 00000 н. 0000343063 00000 н. 0000343260 00000 н. 0000343510 00000 н. 0000343707 00000 н. 0000343957 00000 н. 0000344158 00000 п. 0000344408 00000 п. 0000344612 00000 н. 0000344862 00000 н. 0000345070 00000 н. 0000345320 00000 н. 0000345526 00000 н. 0000345707 00000 н. 0000345956 00000 н. 0000346167 00000 н. 0000346416 00000 н. 0000346627 00000 н. 0000346875 00000 н. 0000347086 00000 п. 0000347334 00000 н. 0000347546 00000 н. 0000347794 00000 н. 0000348011 00000 н. 0000348258 00000 н. 0000348475 00000 п. 0000348721 00000 н. 0000348938 00000 н. 0000349184 00000 п. 0000349404 00000 н. 0000349650 00000 н. 0000349872 00000 н. 0000350118 00000 н. 0000350340 00000 н. 0000350585 00000 н. 0000350810 00000 н. 0000351055 00000 н. 0000351281 00000 н. 0000351525 00000 н. 0000351754 00000 н. 0000351998 00000 н. 0000352229 00000 н. 0000352473 00000 н. 0000352654 00000 н. 0000352885 00000 н. 0000353128 00000 н. 0000353361 00000 н. 0000353603 00000 н. 0000353842 00000 н. 0000354084 00000 н. 0000354323 00000 н. 0000354565 00000 н. 0000354802 00000 н. 0000355044 00000 н. 0000355286 00000 н. 0000355527 00000 н. 0000355769 00000 н. 0000356010 00000 н. 0000356252 00000 н. 0000356492 00000 н. 0000356740 00000 н. 0000356980 00000 н. 0000357228 00000 н. 0000357468 00000 н. 0000357716 00000 н. 0000357956 00000 н. 0000358208 00000 н. 0000358448 00000 н. 0000358711 00000 н. 0000358974 00000 н. 0000359237 00000 н. 0000359501 00000 н. 0000359765 00000 н. 0000359946 00000 н. 0000360210 00000 н. 0000360391 00000 п. 0000360655 00000 н. 0000360921 00000 н. 0000361187 00000 н. 0000361368 00000 н. 0000361634 00000 н. 0000361902 00000 н. 0000362083 00000 н. 0000362352 00000 п. 0000362533 00000 н. 0000362802 00000 н. 0000362983 00000 н. 0000363254 00000 н. 0000363435 00000 н. 0000363706 00000 н. 0000363886 00000 н. 0000364158 00000 н. 0000364431 00000 н. 0000364703 00000 н. 0000364884 00000 н. 0000365157 00000 н. 0000365430 00000 н. 0000365705 00000 н. 0000365982 00000 п 0000366257 00000 н. 0000366438 00000 н. 0000366715 00000 н. 0000366993 00000 н. 0000367271 00000 н. 0000367551 00000 н. 0000367832 00000 н. 0000368113 00000 п. 0000368294 00000 н. 0000368575 00000 н. 0000368858 00000 н. 0000369141 00000 п. 0000369424 00000 н. 0000369707 00000 н. 0000369990 00000 н. 0000370272 00000 н. 0000370554 00000 н. 0000370835 00000 н. 0000371116 00000 н. 0000371396 00000 н. 0000371674 00000 н. 0000371952 00000 н. 0000372229 00000 н. 0000372505 00000 н. 0000372781 00000 н. 0000373056 00000 н. 0000373331 00000 н. 0000373512 00000 н. 0000373787 00000 н. 0000374062 00000 н. 0000374336 00000 н. 0000374611 00000 н. 0000374886 00000 н. 0000375162 00000 н. 0000375437 00000 н. 0000375713 00000 н. 0000375988 00000 н. 0000376264 00000 н. 0000376540 00000 н. 0000376816 00000 н. 0000377092 00000 н. 0000377368 00000 н. 0000377645 00000 н. 0000377922 00000 н. 0000378199 00000 н. 0000378476 00000 н. 0000378753 00000 н. 0000379030 00000 н. 0000379308 00000 н. 0000379585 00000 н. 0000379863 00000 н. 0000380141 00000 н. 0000380419 00000 п. 0000380699 00000 н. 0000380977 00000 н. 0000381255 00000 н. 0000381533 00000 н. 0000381810 00000 н. 0000382087 00000 н. 0000382361 00000 н. 0000382542 00000 н. 0000382815 00000 н. 0000383087 00000 н. 0000383358 00000 п. 0000383628 00000 н. 0000383897 00000 н. 0000384165 00000 н. 0000384346 00000 п. 0000384612 00000 н. 0000384793 00000 н. 0000385058 00000 н. 0000385323 00000 н. 0000385587 00000 н. 0000385850 00000 н. 0000386113 00000 п. 0000386375 00000 н. 0000386556 00000 н. 0000386818 00000 н. 0000387079 00000 п. 0000387339 00000 н. 0000387599 00000 н. 0000387859 00000 н. 0000388118 00000 н. 0000388376 00000 п. 0000388631 00000 н. 0000388888 00000 н. 0000389144 00000 н. 0000389399 00000 н. 0000389654 00000 н. 0000389909 00000 н. 00003
00000 н. 00003 00000 н. 0000300000 н. 00003 00000 н. 0000391173 00000 н. 0000391424 00000 н. 0000391605 00000 н. 0000391856 00000 н. 0000392106 00000 н. 0000392355 00000 н. 0000392536 00000 н. 0000392785 00000 н. 0000393034 00000 н. 0000393283 00000 н. 0000393532 00000 н. 0000393782 00000 н. 0000394032 00000 н. 0000394282 00000 н. 0000394533 00000 н. 0000394784 00000 н. 0000395030 00000 н. 0000395221 00000 н. 0000395466 00000 н. 0000395657 00000 н. 0000395900 00000 н. 0000396091 00000 н. 0000396272 00000 н. 0000396512 00000 н. 0000396703 00000 н. 0000396887 00000 н. 0000397123 00000 н. 0000397314 00000 н. 0000397495 00000 н. 0000397679 00000 н. 0000397912 00000 п. 0000398103 00000 н. 0000398284 00000 н. 0000398465 00000 н. 0000398696 00000 н. 0000398887 00000 н. 0000399078 00000 н. 0000399306 00000 н. 0000399497 00000 н. 0000399722 00000 н. 0000399903 00000 н. 0000400126 00000 н. 0000400317 00000 н. 0000400508 00000 н. 0000400729 00000 н. 0000400947 00000 н. 0000401138 00000 н. 0000401353 00000 н. 0000401544 00000 н. 0000401754 00000 н. 0000401945 00000 н. 0000402215 00000 н. 0000402406 00000 п. 0000402669 00000 н. 0000402860 00000 н. 0000403041 00000 н. 0000403293 00000 н. 0000403484 00000 н. 0000403665 00000 н. 0000403846 00000 н. 0000404085 00000 н. 0000404276 00000 н. 0000404509 00000 н. 0000404700 00000 н. 0000404933 00000 н. 0000405124 00000 н. 0000405355 00000 н. 0000405546 00000 н. 0000405774 00000 н. 0000405965 00000 н. 0000406195 00000 н. 0000406386 00000 п. 0000406615 00000 н. 0000406806 00000 н. 0000407033 00000 п. 0000407224 00000 н. 0000407449 00000 н. 0000407640 00000 н. 0000407865 00000 н. 0000408056 00000 н. 0000408283 00000 н. 0000408474 00000 н. 0000408701 00000 п. 0000408892 00000 н. 0000409115 00000 н. 0000409306 00000 н. 0000409529 00000 н. 0000409720 00000 н. 0000409940 00000 н. 0000410131 00000 п. 0000410351 00000 п. 0000410542 00000 п. 0000410762 00000 н. 0000410953 00000 п. 0000411173 00000 н. 0000411367 00000 н. 0000411582 00000 н. 0000411773 00000 п. 0000411990 00000 н. 0000412184 00000 н. 0000412400 00000 н. 0000412594 00000 н. 0000412811 00000 н. 0000413002 00000 н. 0000413219 00000 н. 0000413413 00000 н. 0000413624 00000 н. 0000413818 00000 н. 0000414030 00000 н. 0000414224 00000 н. 0000414435 00000 п. 0000414629 00000 н. 0000414840 00000 н. 0000415034 00000 н. 0000415245 00000 н. 0000415439 00000 н. 0000415650 00000 н. 0000415844 00000 н. 0000416052 00000 н. 0000416244 00000 н. 0000416452 00000 н. 0000416646 00000 н. 0000416854 00000 н. 0000417048 00000 н. 0000417256 00000 н. 0000417450 00000 н. 0000417658 00000 н. 0000417852 00000 н. 0000418056 00000 н. 0000418250 00000 н. 0000418454 00000 п. 0000418648 00000 н. 0000418849 00000 н. 0000419043 00000 н. 0000419244 00000 н. 0000419438 00000 н. 0000419639 00000 п. 0000419833 00000 н. 0000420030 00000 н. 0000420224 00000 н. 0000420425 00000 н. 0000420619 00000 п. 0000420816 00000 н. 0000421010 00000 н. 0000421204 00000 н. 0000421398 00000 н. 0000421592 00000 н. 0000421786 00000 н. 0000421980 00000 н. 0000422174 00000 н. 0000422368 00000 н. 0000422562 00000 н. 0000422755 00000 н. 0000422946 00000 н. 0000423140 00000 п. 0000423334 00000 н. 0000423525 00000 н. 0000423718 00000 н. 0000423909 00000 н. 0000424103 00000 п. 0000424294 00000 н. 0000424488 00000 н. 0000424678 00000 н. 0000424871 00000 н. 0000425061 00000 н. 0000425255 00000 н. 0000425442 00000 н. 0000425637 00000 н. 0000425824 00000 н. 0000426018 00000 н. 0000426205 00000 н. 0000426399 00000 н. 0000426586 00000 н. 0000426780 00000 н. 0000426967 00000 н. 0000427164 00000 н. 0000427347 00000 н. 0000427528 00000 н. 0000427722 00000 н. 0000427905 00000 н. 0000428102 00000 п. 0000428286 00000 п. 0000428480 00000 н. 0000428661 00000 н. 0000428858 00000 н. 0000429055 00000 н. 0000429252 00000 н. 0000429449 00000 н. 0000429646 00000 н. 0000429843 00000 н. 0000430040 00000 н. 0000430237 00000 н. 0000430434 00000 п. 0000430631 00000 н. 0000430828 00000 н. 0000431025 00000 н. 0000431222 00000 н. 0000431419 00000 п. 0000431616 00000 н. 0000431813 00000 н. 0000432010 00000 н. 0000432206 00000 н. 0000432403 00000 н. 0000432600 00000 н. 0000432797 00000 н. 0000432994 00000 н. 0000433191 00000 п. 0000433388 00000 п. 0000433585 00000 н. 0000433782 00000 н. 0000433979 00000 н. 0000434176 00000 п. 0000434373 00000 п. 0000434570 00000 н. 0000434767 00000 н. 0000434964 00000 н. 0000435161 00000 п. 0000435357 00000 п. 0000435551 00000 п. 0000435745 00000 н. 0000435936 00000 п. 0000436127 00000 н. 0000436317 00000 п. 0000436507 00000 н. 0000436694 00000 н. 0000436877 00000 н. 0000437061 00000 н. 0000032364 00000 п. 0000034091 00000 п. трейлер ] >> startxref 0 %% EOF 67 0 объект > эндобдж 1660 0 объект > транслировать Hmpg
Инженерные характеристики и потенциальное более широкое использование композитов из опилок в строительстве — обзор
Технические характеристики и возможность увеличения использования композитов из опилок в строительстве — обзор
Реферат : Многие страны-производители древесины производят более 2 миллионов м3 древесины. опилки ежегодно.В развивающихся странах опилки часто утилизируют путем открытого захоронения, открытого сжигания или вывоза на свалки. Это создает огромные экологические проблемы, связанные с загрязнением воздуха, выбросами парниковых газов и уничтожением растений и водных организмов. Результаты этой обзорной статьи показывают, что опилки можно использовать для изготовления строительных композитов из опилок с хорошим модулем упругости, водопоглощением и прочностными характеристиками, которые соответствуют международным спецификациям. Эти композиты включают в себя древесно-стружечные плиты, бетонные блоки или кирпичи из опилок и бетон из опилок.В статье сделан вывод о том, что частичная замена от 5% до 17% песка на опилки или замена цемента золой опилок в пропорциях от 5% до 15% в бетонных смесях позволяет получить конструкционный бетон с прочностью на сжатие более 20 МПа. Частичная замена от 10% до 30% песка, используемого при производстве блоков и кирпичей, опилками также позволяет производить кирпичи и блоки из опилок с прочностью на сжатие более 3 МПа. Композиты на опилках также привлекательны своей низкой теплопроводностью, высоким звукопоглощением и хорошими звукоизоляционными характеристиками.Эти результаты показывают, что более широкое использование композитных опилок в строительстве снизит потенциальное загрязнение окружающей среды опилками, сэкономит энергию и снизит затраты на утилизацию.
1. Введение
Опилки — это отходы или побочный продукт целого ряда процессов производства древесины, включая пиление, планирование, фрезерование, сверление, шлифование, производство мебели и столярные изделия. Этот поток отходов включает мелкую прерывистую стружку или просто мелкие частицы древесины [1] [2].
Удаление опилок часто осуществляется путем открытого захоронения, открытого сжигания или захоронения на свалках [3] [4]. Опилки, сбрасываемые на свалки, увеличивают нагрузку на свалки, а их сжигание способствует выбросам парниковых газов [5]. Несмотря на загрязнение воздуха и проблемы общественного здравоохранения, связанные с открытым сжиганием, лесопилки обычно практикуют его как самый простой способ избавиться от опилок [6] [7]. При сбросе на берег ручьев и рек опилки переносятся дождевой водой или ветром в поверхностные воды и могут серьезно повлиять на водную флору и фауну.Более того, опилки, без разбора выбрасываемые на землю, убивают жизнь растений и вызывают образование древесной пыли при попадании в атмосферу [8].
Создание ценности из этого потока отходов снизит затраты на утилизацию и создаст рабочие места [5]. Кроме того, использование в строительстве изделий из древесины, таких как композитные опилки, способствует смягчению последствий изменения климата [9] [10]. Замена стали, бетона и других изделий, производимых с высоким энергопотреблением, композитными опилками может снизить потребление большого количества ископаемого топлива.Учитывая, что продукты на основе древесины накапливают углерод на протяжении всего своего жизненного цикла, использование композитных опилок, соответственно, приводит к снижению выбросов CO 2 [10] [11] и, следовательно, снижает глобальное потепление.
Мотивация для этой обзорной статьи заключается в том, что опилки, представляющие опасность для окружающей среды, имеют большой потенциал для использования в качестве сырья для производства строительных композитов, соответствующих международным стандартам. Это потенциальное использование еще предстоит полностью изучить, особенно в развивающихся странах, где широко распространены неизбирательные захоронения опилок.В статье кратко освещаются некоторые экологические проблемы, которые создают опилки, и рассматриваются технические характеристики строительных композитов из опилок, а именно, ДСП, бетонных блоков из опилок, кирпичей и легких опилок бетона. Предполагается, что рассмотренная литература послужит катализатором для дальнейших исследований композитов из опилок и для содействия более широкому использованию этих композитов в строительстве. Это внесет дополнительный вклад в развитие экологически чистых строительных материалов и снизит угрозу загрязнения окружающей среды опилками.Данные, представленные и обсуждаемые в этой статье, также полезны для исследователей, изучающих альтернативные строительные материалы, направленные на сохранение невозобновляемых природных ресурсов и энергии.
Производство, совместное использование и удаление опилок вне строительства
1) Количество опилок, произведенных на лесопилках
Лесопилка — один из основных источников опилок. Количество опилок, получаемых при лесопилении, зависит от эффективности лесопильного производства, которую можно измерить по качеству и количеству восстановленных пиленых досок по сравнению с образовавшимися древесными отходами.Эти древесные отходы представляют собой комбинацию коры, опилок, обрезков, колотого дерева, строгальных стружек и шлифовальной пыли [12]. Тип используемого оборудования также влияет на количество образующихся опилок. Камбугу и др. [13] отметили, что отсутствие надлежащего оборудования для распиловки древесины приводит к высокому образованию опилок в процессе распиловки древесины.
В таблице 1 показано количество древесных отходов и опилок, образующихся на лесопилках, а также некоторые годовые объемы производства опилок в отдельных регионах мира.Из Таблицы 1 видно, что во многих странах-производителях древесины в результате лесопильных операций ежегодно образуется более 2 миллионов м 3 3 опилок. В провинции Коппербелт Замбии, как и во многих развивающихся странах, большие груды опилок, плит, обрезков и коры характерны для рабочих зон 13 зарегистрированных в провинции лесопильных предприятий. Это указывает на огромную экологическую проблему, если этот материал просто оставить как отходы.
2) Обычное использование и удаление опилок, не связанных со строительством
Обычное использование опилок не для строительства включает подстилку для домашней птицы и домашнего скота, компостирование почвы и мульчирование [21].До появления холодильников его использовали для хранения льда в ледниках летом. При смешивании с водой и последующем замораживании он образует медленно тающий и более прочный лед. Иногда он используется для впитывания пролитой жидкости, что позволяет легко собрать или смести пролитую жидкость [1]. Опилки также считаются очень хорошим сырьем для производства древесных гранул и брикетов из биомассы, используемых в качестве твердого топлива [20] [22] [23].
Таблица 1. Приблизительное количество опилок, ежегодно образующихся на лесопилках.
* Данные основаны на данных 9 из 10 исследованных лесопильных предприятий; ** Данные по лесопилкам в 1 из 10 провинций Замбии; -Данные недоступны; † Количество рассчитано из объемов с использованием приблизительной плотности опилок 210 кг / м 3 ; †† Средние значения по данным о производстве опилок за четыре года.
Обычная утилизация большей части этих отходов включает открытые захоронения, открытое сжигание и иногда захоронение на свалках. На Рисунке 1 показаны беспорядочные сбросы и сжигание опилок, типичные для развивающихся стран.
2. Текущее использование композитных опилок в строительстве
Композиты на опилках применяются в строительстве давно. Например, он использовался для производства бетона на опилках более 40 лет [1]. Помимо использования в бетоне, в литературе указывается, что другие композиты из опилок, используемые в строительной отрасли, включают ДСП, панели пола, перегородки, облицовку, потолок, опалубку, бетонные блоки и кирпичи.
2.1. ДСП и сопутствующие товары
Значительное количество опилок и древесной стружки в Соединенных Штатах Америки используется для производства древесностружечных плит [24].В период с 2000 по 2017 год мировое производство древесных плит, включая ДСП, фанеру, ориентированно-стружечные плиты (OSB) и ДВП, увеличилось на 125% [25]. В период с 2012 по 2016 год наибольшая доля (62%) этой продукции была произведена в Азиатско-Тихоокеанском регионе, за которым следовали Европа (21%), Северная Америка (11%), Латинская Америка и Карибский бассейн (5%) и Африка ( 1%) [26]. Низкий производственный показатель в Африке и других развивающихся континентах по сравнению с большим объемом производимых опилок (Таблица 1) предполагает наличие большого потенциала
.(а) (б) (в) (г)
Рисунок 1.Открытый сброс опилок: (а) сжигание опилок вблизи жилых районов; (б) и (в) сжигание опилок на лесопилке; (d) Сброс опилок на берегу ручья.
для увеличения производства строительных композитов из опилок из этих отходов в развивающихся странах.
В Замбии постоянно растет спрос на ДСП и сопутствующие товары, такие как фанера и пиломатериалы. Прогнозируется увеличение спроса на эту продукцию на 39% с 501 100 м 3 в 2010 г. до 698 700 м 3 в 2025 г. [27].Предполагается, что использование опилок при производстве этих древесно-стружечных плит уменьшит загрязнение окружающей среды, которое эти отходы создают в Замбии.
ДСП и соответствующие изделия из древесины, такие как древесноволокнистые плиты низкой плотности (ЛДФ) и ДСП, производятся путем смешивания различных пропорций древесной щепы, стружек лесопилок или опилок с синтетической смолой или любым подходящим связующим [9] [28]. Например, Абдулкарим и др. [28] установили, что древесностружечные плиты, изготовленные из древесных опилок и смолы на основе пластика (PBR), синтезированные из отходов пенополистирола в качестве связующего, обладают свойствами, соответствующими требованиям Американского национального института стандартов (ANSI) A208.1 требования. Этот стандарт определяет требуемые размеры, а также физико-механические свойства для различных марок древесностружечных плит. Исследование показало, что древесно-стружечные плиты из древесных опилок и PBR демонстрируют лучшую стойкость к проникновению воды, стабильность размеров, механические свойства и сопротивление деформации по сравнению с древесностружечными плитами на основе карбамида и формальдегида (UF). Таким образом, они были более прочными, жесткими и лучше подходили для применения в большинстве сред, чем УФ-древесно-стружечные плиты.
Исследование Dotun, A.O. и другие. [29] отметили, что древесно-стружечные плиты, полученные из комбинации древесных опилок и полиэтилентерефталатных пластиковых отходов, подходят для использования внутри помещений. Однако исследование также показало, что эти продукты имеют ограниченное применение в конструкции и несущей способности. Аналогичным образом Akinyemi et al. [30] рекомендовали, чтобы панели, произведенные в виде композитов из кукурузных початков и опилок, с использованием формальдегида мочевины в качестве связующего, подходили для внутреннего использования в зданиях, но не для несущих целей.
Erakhrumen et al. [31] доказали, что для смесей древесных опилок сосны (Pinus caribaea M.) и кокосовой шелухи или кокосового волокна (Cocos nucifera L.) с использованием цемента в качестве связующего, такие параметры, как водостойкость, прочностные свойства и плотность древесностружечных плит были улучшены за счет высокого содержания цемента. содержание. Однако эти свойства были снижены при увеличении количества кокосового волокна в смеси.
Композитные опилки, полученные путем склеивания опилок или древесной стружки вместе с пенополистиролом, обладают хорошими характеристиками теплопроводности.Эти продукты считаются подходящими для использования в перегородках и подвесных потолках [32].
2.2. Панели пола
Исследование Chanhoun et al. [33] исследовали комбинацию древесных отходов, отходов полистирола и композитных отходов пластмассы. Исследование показало, что эти композиты могут использоваться не только для внутренних и наружных полов, но также в качестве самоклеящихся сэндвич-панелей или досок для дверных проемов, подвесных потолков и сэндвич-панелей для опалубки.
Инновационная бетонная сэндвич-панель, исследованная в Ираке, была изготовлена с использованием слоя легкого бетона (LWC), зажатого между двумя внешними слоями железобетона.Эти элементы были соединены между собой арматурой фермы как соединители, работающие на сдвиг. Прочность сэндвич-панели с опилками, которая использовалась в качестве заполнителя во внутренней обмотке, была выше прочности сэндвич-панели с полистиролом (стиропором) или порциленитом [34].
Chung et al. [35] продемонстрировали потенциал гашения вибрации слоя песчаных опилок в легких деревянных каркасных системах пола / потолка (LTFS). Исследуемый LTFS включал верхний этаж из смеси опилок и песка, полость, заполненную волокнистым заполнителем для звукоизоляции, и потолок.Теоретическая модель и экспериментальные измерения показали, что слой песчано-опилок гасит вибрацию в диапазоне частот от 10 до 200 Гц.
2.3. Перегородка и облицовка
Композиты из древесных опилок и цемента могут быть использованы для облицовки и стен. Однако важным соображением для этого применения является необходимость тщательного выбора древесины с подходящими компонентами для совместимости с цементом [36].
2.4. Бетонные блоки или кирпичи и строительный раствор из опилок
Различные исследования были проведены в поисках зеленых и менее дорогих строительных блоков, которые содержат опилки в необработанном виде или в виде золы из опилок.Mangi et al. [37] дает хороший обзор 17 исследований, проведенных на бетонных кладочных блоках в период с 2012 по 2016 год в 11 разных странах. В этом обзоре подчеркивается потенциал более широкого использования бетонных блоков из опилок в качестве легких каменных блоков в зданиях.
Gil et al. [38] отметили, что отходы древесных опилок положительно влияют на последующее растрескивание строительного раствора. Это, в свою очередь, улучшает пластичность раствора. Клаудиу [8] изучал использование опилок в штукатурных растворах.Исследование выявило важные характеристики исследованных штукатурных растворов, в том числе их хорошую звуко- и теплоизоляцию, а также невосприимчивость к возгоранию от открытого пламени. Таким образом, эти растворы были рекомендованы для использования во внутренних стенах зданий.
2,5. Бетон из легких опилок
Легкий бетон — это бетон с плотностью от 300 до 1850 кг / м 3 . Конструкционный легкий бетон имеет плотность от 1120 до 1920 кг / м 3 и имеет минимальную прочность на сжатие 17 МПа [39] [40].Низкая плотность и высокие показатели теплоизоляции древесных отходов, таких как опилки [24], делают их хорошей альтернативой для производства легкого бетона и теплоизоляционных строительных композитов. Ахмед и др. [41] отметили, что смесь крупного заполнителя, песка и цемента с различными дозировками опилок в качестве частичной замены песка позволила получить экологически чистый и термоэффективный нормальный и легкий бетон.
3. Технические характеристики и эксплуатационные характеристики композитных древесных опилок, используемых в строительстве
3.1. ДСП
Бадеджо [42] заметил, что цементно-стружечные плиты толщиной 12 мм, изготовленные из опилок четырех тропических лиственных пород древесины (Mitragyna ciliata, Triplochiton scleroxylon, Terminalia superba и Ceiba pentandra), оказали сильное влияние на свойства испытанных плит. Расчетный модуль упругости (MOR) варьировался от 4,72 до 8,20 МПа, от 5,00 до 8,00 МПа, от 4,35 до 6,05 МПа и от 3,75 до 6,20 МПа соответственно для четырех пород древесины. Модуль упругости (MOE) варьировался от 2750 до 4000 МПа, от 2500 до 3500 МПа, от 2500 до 3400 МПа и от 2100 до 3350 МПа соответственно для четырех пород древесины.После выдержки в холодной воде в течение 72 часов процент набухания по толщине варьировался от 2,80% до 4,5%, от 2,9% до 5,5%, от 2,2% до 3,55% и от 4,50% до 5,70% для четырех видов древесины. Соответствующие приблизительные плотности этих пород древесины составляют от 450 до 560, 320 и 400, 450 и 580 и 230 и 260 кг / м 3 [43] [44]. MOE-свойства экспериментальных плит зависят от плотности используемой древесины. Виды Mitragyna ciliata и Terminalia superba имеют более высокую плотность и дают более высокие значения MOE, чем два других вида.Также следует отметить, что результаты MOE этого исследования удовлетворяют требованиям ANSI 208.1 [45] для древесностружечных плит высокого и среднего класса. Однако результаты MOR не соответствовали требованиям ANSI 208.1. Исследуемые древесно-стружечные плиты показали приемлемое набухание, учитывая, что BS EN 312: 2010 [46] и BS EN 317: 1993 [47] предусматривают, что древесностружечные плиты должны иметь максимальное значение набухания (TS) по толщине (TS) 8% при 2-часовом погружении в воду. , или максимальное TS 15%, если используется процедура погружения в воду на 24 часа.
Древесные опилки Okhuen и переработанный полиэтилен (RLDPE) были смешаны и затем подвергнуты горячему прессованию для производства композитных плит из древесных опилок и переработанного полиэтилена компанией Atuanya и Obele [48]. Исследованная средняя прочность на растяжение оптимизированной композитной плиты составила 13,991 МПа, значение, которое соответствовало спецификациям для общего применения.
Абу-Зарифа и др. [49] исследовали древесностружечные плиты, которые были изготовлены из опилок и сельскохозяйственных отходов (стебли банана, пшеничные отруби и апельсиновые корки).Все сельскохозяйственные отходы смешивались с опилками в двух пропорциях: 25% и 75%, в то время как количество полипропиленового пластика оставалось постоянным на уровне 40%. Смеси прессовали под нагрузкой 24 тонны при температуре 170 ° C в течение 2,5 часов. Результаты испытаний показали максимальное значение модуля упругости (MOE) 2160,78 МПа для смеси с 75% -ным составом пшеницы, максимальное значение модуля упругости (MOR) 11,07 МПа для смеси со 100% -ным составом опилок и максимальное значение: значение напряжения 7,8 МПа для смеси с содержанием банана 25%.Диапазон значений водопоглощения составлял от 8,19% до 19,3%. Эти результаты были лучше, чем у древесностружечных плит коммерческого типа (древесно-волокнистые плиты средней плотности, волокнистые и прессованные древесные плиты). Смесь ДСП с 75% банановой композиции показала наименьшую водопоглощающую способность и способность к набуханию. Тот, у которого 75% апельсинового состава, показал самый высокий процент водопоглощения и набухания.
3.2. Опилки в бетонных блоках или кирпичах и строительном растворе
Куполати и др. [50] исследовали использование опилок как частичную замену песка для дробления при производстве кирпича как способ повышения уровня озеленения окружающей среды.Опилки использовались в качестве частичной замены песка для дробилки в количестве 1%, 3% и 5% по объему. Исследованные значения прочности на сжатие опилочно-песчаных кирпичей, произведенных на месте, были ниже минимальных значений 4,0 МПа, установленных для массивных блоков каменной кладки стен [51]. Средняя прочность на сжатие кирпичей (290 мм × 150 мм 90 мм) на стройплощадке в течение 28 дней составила 0,67 МПа, 0,23 МПа и 0,21 МПа для соответствующих процентов замены опилок. Однако кубики кирпичей размером 100 мм × 100 мм × 100 мм, изготовленные в лаборатории, показали среднюю прочность на сжатие 6.10 МПа, 5,73 МПа и 3,7 МПа для вышеуказанных соответствующих процентов замены опилок. Это было связано с улучшением практики контроля качества в лаборатории. В этом исследовании подчеркивается важность контроля качества при массовом производстве кирпичей из опилок. Исследование также показало возможность использования опилок в качестве частичного заменителя дробильного песка при производстве кирпича.
Чтобы исследовать потенциальное использование опилок в блоках, Ravindrarajah et al. [52] оценивали блоки, изготовленные с использованием цемента, извести, летучей золы, хлорида кальция, опилок сосны Radiata, песка и воды.Смесь бетонных блоков из опилок с содержанием опилок 12% по объему имела плотность 1540 кг / м 3 и 28-дневную прочность на сжатие 14 МПа. Использование 2% хлорида кальция привело к достижению оптимальной прочности в любом возрасте, но также привело к значительному увеличению усадки. Исследование показало, что опилки являются хорошим наполнителем для производства легких бетонных блоков.
Замена песка опилками в смеси из песчано-цементных блоков, пропорции замены опилок 10%, 20%, 30% и 40%, с водоцементным соотношением 0.5 был исследован Dadzie et al. [53]. Прочность на сжатие исследуемых композитных блоков из опилок превышала минимальное требование BS 6073 в 2,8 МПа для замены опилок не более 10%. Далее было отмечено, что содержание заменяемых опилок не должно превышать 10%, если блоки из опилок должны соответствовать стандартным спецификациям.
Boob [54] установил, что блоки из песчаника, полученные путем частичной замены песка опилками, дают оптимальные и желаемые результаты при соотношении смеси 1: 6 (цемент: песок + опилки) (85% песок + 15% опилки).Прочность на сжатие, полученная для блоков размером 100 мм × 100 мм × 100 мм для этой пропорции смеси, составляла 4,5 МПа. Это хороший результат для блоков, изготовленных с заменой опилок не более 10%, при оценке относительно минимального требования BS 6073 в 2,8 МПа [55].
Ettu et al. [56] исследовали использование обычного портландцемента (OPC), золы из опилок (SDA) и золы из листовой стали (PPLA) для возможного производства песчаных блоков (где песок был основным компонентом) и грунтбетонных блоков, где латерит является основным компонентом. основная составляющая.Были оценены бинарные вяжущие смеси OPC-SDA и OPC-PPLA и тройные вяжущие смеси OPC-SDA-PPLA для производства блоков. Исследование показало, что произведенные блоки из этих смешанных цементных материалов обладают достаточной прочностью для их использования, особенно в строительных работах, где потребность в высокой начальной прочности не является критическим фактором. Значения прочности за 150 дней для трехкомпонентного цемента с добавкой OPC-SDA-PPLA для пескобетона и грунтбетонных блоков составили, соответственно, 6,00 МПа и 5 МПа.20 МПа для замены 5%, 5,90 МПа и 5,10 МПа для замены 10%, 5,75 МПа и 5,00 МПа для замены 15% OPC и 5,70 МПа и 4,90 МПа для замены 20% OPC. Эти результаты были немного лучше, чем соответствующие контрольные значения 5,20 МПа и 4,80 МПа.
В исследованиях Тургута и Альгина [57] для получения кирпичей WSW-LPW использовались отходы известнякового порошка (LPW) от работ в карьерах и отходы древесных опилок (WSW), полученные в процессе распиловки необработанной древесины. Эти композитные кирпичи с различными комбинациями WSW-LPW показали прочность на сжатие, прочность на изгиб, удельный вес, скорость ультразвуковых импульсов (UPV) и значения водопоглощения, которые соответствовали международным стандартам, а именно ASTM C67-03a, BS 6073 и BS 1881.Замена 30% WSW в кирпичной композитной смеси позволила получить кирпичи с прочностью на сжатие 7,2 МПа и прочностью на изгиб 3,1 МПа. Эти результаты соответствуют требованиям BS6073 для строительных материалов, используемых в конструкциях. Этот композит из опилок был оценен как потенциальный элемент для строительства стен, заменитель деревянной доски, а также как экономичная альтернатива бетонным блокам, потолочным панелям и панелям звукоизоляции.
Moreira et al. [58] изучали характеристики строительных блоков, изготовленных с частичной заменой мелких заполнителей опилками древесных пород Dinizia Excelsa Ducke.Блоки были изготовлены путем замены мелких заполнителей опилками в количестве 5% по весу. Были использованы два процесса обработки опилок, один из которых включает промывку опилок в щелочном растворе (известь), а другой — погружение опилок в сульфат алюминия. Результаты прочности на сжатие на 28 -й день составили 1,39 и 3,98 МПа для двух методов обработки соответственно. Результаты водопоглощения составили 13,13% и 10,40% соответственно. Результаты показали хорошие характеристики блоков, изготовленных из опилок, обработанных сульфатом алюминия, по сравнению с блоками, изготовленными из опилок, обработанных щелочным раствором.Результаты прочности на сжатие в течение 28 дней, составляющие 3,98 МПа для блоков с опилками, обработанными сульфатом алюминия, удовлетворяли бразильскому стандарту NBR7173, который определяет минимальную среднюю прочность на сжатие 2,5 МПа для строительных блоков. Исследование показало возможность производства кирпичных блоков с заменой 5% мелких заполнителей на опилки Dinizia Excelsa Ducke, обработанные сульфатом алюминия.
Adebakin et al. [59] исследовали использование опилок в качестве частичной замены песка при производстве пустотелых блоков из песчаника.Исследование было направлено на снижение стоимости строительных материалов и снижение собственных нагрузок на высотные здания и здания, построенные на грунтах с низкой несущей способностью. Исследование показало, что замена песка на 10% опилок привела к получению блоков со значениями прочности на сжатие, которые почти соответствовали требуемой нигерийской стандартной спецификации 3,5 — 10 МПа для блоков из песчаника. Это 10% заменителя опилок также позволило получить блоки с уменьшением веса на 10% и снижением себестоимости продукции на 3%.
Легкие кирпичи, изготовленные из смеси опилок и цемента с соотношением 3: 2 и 2: 1, исследовали Zziwa et al. [60]. Кирпичи размером 100 × 100 × 100 мм испытывали в виде высушенных на воздухе образцов и в виде замоченных образцов после замачивания в воде при комнатной температуре в течение 24 часов. Наивысший результат по прочности на сжатие 2,21 МПа был получен для сухих образцов с соотношением опилок к цементу 3: 2. Соответствующий результат прочности на сжатие для замоченных образцов составил в среднем 1,38 МПа. Низкая прочность на сжатие в сухом состоянии и еще более низкая прочность на сжатие в мокром состоянии указывали на то, что эти кирпичи не соответствовали требованиям для использования в несущих стенах и стенах, подверженных воздействию влажных сред.Однако их можно было использовать для внутренней обшивки стен там, где были минимальные условия смачивания и небольшая нагрузка или ее отсутствие.
Сводка результатов прочности на сжатие выбранных кирпичей и блоков из опилок представлена в Таблице 2. Эти результаты указывают на хорошие характеристики композитных блоков кирпич / блок из опилок, что должно вселять уверенность в их более широкое использование в строительстве.
3.3. Опилки в легком бетоне
3.3.1. Частичная замена песка опилками в бетонной смеси
Осей и Джексон [61] изучали использование опилок, гранитного щебня и быстротвердеющего цемента для производства бетонных опилок.Используя бетонную смесь 1: 2: 4, опилки использовали для замены 25%, 50%, 75% и 100% песка по объему. Прочность за 28 дней для соответствующих пропорций замены опилок составляла 12,13 МПа, 9,15 МПа, 4,66 МПа и 3,37 МПа. Исследование показало, что опилки потенциально могут быть использованы в качестве заполнителя при производстве неструктурного легкого бетона для использования в ситуациях, когда прочность на сжатие не является основным требованием. Дальнейший анализ прочности на сжатие показал, что замена опилок менее 14% может дать бетон с 28-дневной прочностью на сжатие 20 МПа.Это минимальная прочность бетона для использования в конструкции. Ранее Бдейр [62] заметил, что замена 10% песка опилками показала увеличение прочности на сжатие с 23,24 до 27,31 МПа в период от 7 до 28 дней, что указывает на то, что частичная замена песка опилками в бетоне может достигать того же порядка прочности, что и обычные бетон при более длительных периодах отверждения.
Suliman et al. [63] использовали опилки, песок, щебень и цемент для производства опилок бетона. Замена песка на опилки в размере 5%,
Таблица 2.Прочность на сжатие блоков опилок или кирпича на 28 суток.
10% и 15% от общего объема песка. Полученные значения прочности на сжатие через 28 дней составили 50,06 МПа, 41,48 МПа и 34,7 МПа соответственно. Оптимальная конструкция для производства бетонных опилок была установлена при 10% замещении опилок. Исследование также показало, что бетонные опилки не содержат каких-либо вредных для здоровья веществ.
Исследование Oyedepo et al. [64] показали, что значения прочности на сжатие, полученные при содержании опилок, равном или превышающем 25%, не соответствуют минимальным требованиям Нигерии в 17 МПа для легкого бетона.Соотношение бетонной смеси 1: 2: 4 было приготовлено с использованием воды / цемента 0,65, с 0%, 25%, 50%, 75% и 100% опилками в качестве частичной замены мелкого песка. Значения прочности на сжатие для процентов замены опилок 25%, 75% и 100% составили 14,15 МПа, 12,96 МПа и 11,93 МПа соответственно. Следовательно, это исследование показало, что использование опилок в количестве более 25% отрицательно сказывается на прочностных и плотностных свойствах бетона. Еще одно предположение заключалось в том, что использование от 0% до 25% опилок в качестве частичной замены в бетоне не повлияет отрицательно на прочность бетона.
Натан [65] показал, что опилки являются потенциальным материалом для приготовления легкого бетона. Используя цемент, мелкий заполнитель, крупный заполнитель, воду и опилки, была приготовлена стандартная контрольная смесь с пропорциями смеси 1: 1,5: 3. Замена мелкого заполнителя опилками производилась на 0%, 5%, 10%, 15% и 20%. Средние значения прочности на сжатие, зарегистрированные через 28 дней, составили 29,33 МПа, 27,7 МПа, 26,37 МПа, 24,15 МПа и 22,67 МПа соответственно. Соответствующие значения прочности на разрыв равнялись 2.08 МПа, 1,82 МПа, 1,69 МПа, 1,49 МПа и 1,41 МПа. Используя аналогичный дизайн смеси, исследование Tilak et al. [2] показали более низкую прочность на сжатие 24,13 МПа, 15,55 МПа, 11,11 МПа и 8,13 МПа, когда мелкий заполнитель был заменен опилками в пропорциях 10%, 20%, 50% и 100% соответственно. Эти два исследования указывают на возможное использование опилок в конструкционном бетоне, когда доля опилок, заменяющих песок, не превышает 10%.
Читра и Хемаприя [66] использовали пропорцию смеси 1: 1.60: 2.78, чтобы подтвердить возможность использования опилок в качестве альтернативы песку с оптимальной прочностью, полученной при 15% замене песка опилками. Значения прочности на сжатие, полученные через 28 дней, составили 25,1 МПа, 24,2 МПа, 23,75 МПа и 17,54 МПа, когда мелкий заполнитель был заменен опилками при 0%, 5%, 10%, 15% соответственно.
Sawant et al. [67] исследовали бетон на опилках, изготовленный из смеси в пропорции 1: 1,62: 2,83, которая включала в себя вяжущий метакаолин в качестве добавки, предназначенной для обеспечения хорошего сцепления между опилками и другими ингредиентами бетона.В ходе исследования производилась частичная замена песка опилками в размерах 0%, 5%, 10%, 15%, 20% и 25%. Полученные значения прочности на сжатие составили 24,4 МПа, 21,11 МПа, 12,45 МПа, 10,07 МПа, 7,25 МПа и 5,12 МПа соответственно, что указывает на хорошую прочность при содержании опилок менее 10%.
Исследование Awal et al. [68] исследовали образцы бетона из опилок, изготовленные с соотношением цемента к опилкам 1: 1, 1: 2 и 1: 3 по объему. Соответствующие результаты по прочности на сжатие в возрасте 28 дней для вышеупомянутого соотношения цемента и опилок составили 18.65 МПа, 17,20 МПа и 12,80 МПа. Прочность бетонных опилок увеличивалась с увеличением возраста выдержки. Однако прочность и зарегистрированный модуль упругости уменьшались с увеличением количества опилок в смеси.
Опилки бетона из смесей 1: 1: 2 и 1: 1,5: 3 с опилками, заменяющими крупный заполнитель, исследовали Огундипе и Джимох [3]. Результаты по прочности на сжатие за 28 дней составили 18,33 и 8,78 МПа соответственно, а их прочность на изгиб за 28 дней — 1.71 и 1,33 МПа соответственно. Водопоглощение смесей за 28 дней составило 5,69%, 8,97%, 8,29%, 7,83% и 11,11%, соответственно, за 28 дней линейная усадка составила 0,67%, 0,50%, 1,83%, 1,83% и 1,95%.
Соджоби [69] заметил, что отходы опилок и латерит в качестве альтернативного мелкозернистого заполнителя и вяжущего материала, соответственно, могут быть использованы для производства экологически чистых легких блоков для бетонных дорожных покрытий (ICPU). Следовательно, Sojobi et al. [70] из тех же материалов изготовили сверхлегкие зеленые блоки для дорожной одежды.При оптимальном содержании опилок 10% и после 90 дней отверждения в воде блоки для мощения достигли прочности на сжатие 16,6 МПа и продемонстрировали сопротивление скольжению 64,5 значения маятникового испытания (PVT). Результаты по прочности превысили минимальные требования от 3,45 до 15 МПа для пешеходов и ненесущих бетонных конструкций.
Возможность использования арматуры в опилках бетона была изучена Олутоге [71]. Это исследование показало, что замена менее 25% песка опилками в железобетоне дала результаты, которые удовлетворяли характерным требованиям прочности для конструкционного использования бетона, как указано в BS 8110, 1997.
На рис. 2 показан обзор результатов прочности на сжатие опилок бетона за 28 дней в связи с частичной заменой песка опилками в различных бетонных смесях. Данные на Рисунке 2 показывают, что бетонные смеси с содержанием опилок от 5% до 15% в качестве замены песка, как правило, могут давать бетон со значениями прочности на сжатие, превышающими 15 МПа, что подходит для легких конструкций, как рекомендовано Невиллом [72].
Рисунок 2 также показывает, что смеси с содержанием опилок от 5% до 10% в качестве замены песка могут производить бетон со значениями прочности на сжатие выше 20 МПа.Таким образом, эти смеси могут быть использованы в конструкциях в соответствии с рекомендациями ASTM C330 / C330M-09 [73]. Кроме того, следует отметить, что прочность на сжатие значительно снижается с увеличением содержания опилок выше 15% содержания песка.
Диаграмма разброса, показывающая влияние замены песка опилками на прочность на сжатие опилок бетона, представлена на рисунке 3. Средние результаты прочности на сжатие дают экспоненциальную зависимость с хорошим значением корреляции, т.е.е. R 2 = 0,8017. Это отношение может быть выражено как
ж c знак равно 25,944 е — 0,015 λ (1)
Рисунок 2. Прочность на сжатие опилок бетона по отношению к компоненту, заменяющему опилки.
Рис. 3. График зависимости замены песка опилками от прочности на сжатие опилок бетона.
где:
ж c прочность на сжатие в течение 28 дней, МПа.
λ — процент замещения песка опилками.
Из уравнения (1) следует, что оптимальное содержание замены песка опилками, необходимое для производства конструкционного бетона с прочностью на сжатие 20 МПа, составляет 17%. Содержание опилок выше этой пропорции приводит к получению бетона из опилок с прочностью на сжатие ниже 20 МПа.
На рис. 4 показано снижение прочности на изгиб с увеличением содержания опилок. Это особенно очевидно из исследований Sawant et al.[67] и [74].
3.3.2. Опилки бетона с опилками как один из основных компонентов
Помимо частичной замены песка опилками, были проведены и другие исследования, в которых опилки являются одним из основных компонентов бетонной смеси. Сравнения результатов прочности на сжатие, разрывное растяжение и изгиб опилок бетона из выбранной литературы показаны в таблице 3. Табличные результаты показывают снижение прочности на сжатие, изгиб и разделение прочности при увеличении количества опилок в бетонной смеси.Из таблицы 3 также следует, что смеси 1: 1: 2 и 1: 1: 1 дают легкий бетон с хорошими показателями прочности на сжатие.
3.3.3. Частичная замена цемента золой опилок (SDA) в бетонной смеси
Удойо и Дашибил [78] и Мартонг [79] исследовали бетон из золы опилок (SDA), заменив обычный портландцемент (OPC) на SDA. Исследования показали, что при замене 10% SDA можно было достичь расчетной прочности 20 МПа за 28 дней, что сопоставимо с прочностью, достигнутой обычным бетоном при более длительных периодах отверждения.Marthong [79], однако, отметил, что включение SDA в качестве частичной замены цемента имеет тенденцию к снижению долговечности бетона при воздействии сульфатной среды. Позже Обилад [80]
Рис. 4. Испытание прочности на изгиб опилок бетона в зависимости от содержания опилок.
Таблица 3. Прочность на сжатие, изгиб и разрыв при растяжении, полученная при использовании различных композитных смесей из опилок.
* Соотношение смеси цемента и опилок; -Данные недоступны.
показал, что SDA привел к достижению 28-дневной прочности на сжатие от 21,02 до 19,05 МПа при замене золы опилок от 5% до 15% соответственно. Таким образом, содержание SDA от 5% до 15% было сочтено оптимальной заменой SDA для цемента, поскольку содержание SDA выше 15% значительно снижает прочность бетона на сжатие. Это исследование рекомендовало оценку долговечности бетона, изготовленного из SDA, в качестве частичной замены цемента.
Dhull [81] частично заменил массу цемента на 5%, 10%, 15% и 20% в соотношении бетонной смеси 1: 1: 2.Прочность в течение 28 дней с содержанием замены 5% и 10% привела к результатам прочности на сжатие 32,44 и 30,24 МПа соответственно. Замена цемента с более высоким содержанием SDA, превышающим 10%, позволила получить бетон с прочностью на сжатие ниже прочности контрольной смеси.
Используя расчетное соотношение компонентов Simpexfive от Scheffe, равное 0,5: 0,95: 0,05: 2,25: 4, то есть вода: цемент: опилки, зола: песок: граниты, исследование Onwuka et al. [82] произвел бетон SDA с оптимальным результатом по прочности на сжатие через 28 дней из 20.44 МПа. Исследование пришло к выводу, что бетон из опилок может быть подходящим образом использован в качестве строительного материала в строительной индустрии.
Fapohunda et al. [83] показали, что древесные отходы либо в форме ПДД, либо в виде древесного заполнителя, либо в виде опилок; могут быть включены в соответствующую конструкцию бетонной смеси, из которой можно получить конструкционный бетон, удовлетворяющий требованиям здания. Однако содержание SDA не должно превышать 20%. Бетон с добавлением SDA, как известно, демонстрирует хорошие свойства долговечности в отношении большей части процессов, приводящих к ухудшению качества бетона в течение его срока службы.Однако его долговечность ухудшается, когда он подвергается воздействию углекислого газа и сульфатов. Mangi et al. [84] также отметили необходимость исследования долговечности высокопрочного бетона, разработанного с использованием SDA, и его характеристик в агрессивных щелочных и кислых средах.
Исследование Raheem et al. [85] далее отмечает, что бетон SDA становится менее работоспособным по мере увеличения содержания SDA. Это указывает на то, что SDA требует больше воды по сравнению с обычным портландцементом.Исследование показало, что 5% SDA было оптимальным содержанием замещения, которое привело к увеличению прочности бетона SDA, сравнимому с контрольной смесью, в которой не было содержания SDA.
Значения прочности на сжатие бетона SDA на Рисунке 5 демонстрируют тенденцию, аналогичную показанной на Рисунке 2, с точки зрения уменьшения прочности с увеличением SDA. Рисунок 5 также показывает, что бетон с содержанием SDA от 5% до 15% в качестве замены цемента можно использовать для производства бетона со значениями прочности на сжатие более 20 МПа.Этот бетон можно использовать для строительных конструкций.
3.4. Влияние композитов из опилок на тепловые свойства строительных конструкций
Теплоизоляционные материалы и системы используются для уменьшения передачи теплового потока. Теплопроводность и коэффициент теплопередачи указывают на термический
Рисунок 5. Прочность на сжатие бетона SDA.
изоляционные характеристики таких материалов. Строительные материалы с теплопроводностью менее 0.07 Вт / мК считаются теплоизоляторами [86].
У древесины более высокая теплопроводность по сравнению с другими материалами, используемыми в строительстве. Они незначительно различаются в зависимости от плотности, содержания влаги и разновидностей, более низкие плотности имеют более низкую проводимость. Мейер [24] утверждает, что одним из основных преимуществ заполнителей древесных отходов, таких как опилки и стружка, является небольшой вес и высокая теплоизоляционная способность материала.
Бетонные опилки, изготовленные из цемента, опилок и песка, смешанных в соотношении 1: 1: 1, 1: 2: 1 и 1: 3: 1 соответственно, показали, что соотношение смеси 1: 3: 1 показало более низкую теплопроводность по сравнению с два других микса.Это снижение теплопередачи через смесь 1: 3: 1 было связано с повышенным содержанием опилок в этой смеси по сравнению с двумя другими [76] [87].
Салих и Кзар [88] использовали комбинацию предварительно обработанного тростника и опилок в качестве частичной замены природного песка в смеси 1: 2,5 (цемент: песок). Тростник и опилки были предварительно обработаны путем замачивания их в кипящей воде, в которую была добавлена известь в количестве 20% от веса тростника или опилок. Обработка замачиванием была проведена для уменьшения вредных растворимых углеводов, дубильных веществ, восков и изюма.Содержимое замены представляло собой равные комбинации опилок и тростника в пропорциях 10%, 20%, 30% и 40%. Например, замена 10% включала 5% опилок и 5% тростника. Водоцементное соотношение для всех смесей сохранялось равным 0,4. Значения плотности сушки в печи за 28 дней находились в диапазоне от 2060 до 1693 кг / м 3 — высокие значения, относящиеся к плотности контрольной смеси. Более низкие значения плотности были получены для 40% -ного содержания песка (т.е. 20% опилок и 20% тростника). Теплопроводность значительно снизилась с 0.От 745 до 0,222 Вт / мК для контрольной смеси и смеси, замещающей 40% песка, соответственно.
Исследование Sindanne et al. [89], включающие земляные блоки, стабилизированные цементом, опилками и известью, показали увеличение теплопроводности с увеличением количества цемента и извести в качестве стабилизаторов. Однако стабилизация опилками снизила теплопроводность блоков. Таким образом, было обнаружено, что блоки, стабилизированные опилками, демонстрируют повышенное термическое сопротивление по сравнению с блоками, стабилизированными цементом или известью.Результаты этого исследования представлены в Таблице 4.
Огундипе и Джимо [75] заменили крупный заполнитель опилками в четырех смесях, а именно 1: 1: 2, 1: 1,5: 3, 1: 2: 4, 1: 3: 6 и 1: 4: 8. Соответствующие результаты проводимости, измеренные после 28-дневного периода отверждения, составили 0,229, 0,232, 0,229, 0,223 и 0,176 Вт / мК. Результаты указывают на постепенное снижение теплопроводности с увеличением содержания опилок. Эта тенденция была также замечена в исследованиях, проведенных Абдул Амиром [90], Салихом и Кзаром [88] и Ченгом и др.[91], представленный на рисунке 6.
Рисунок 6 также показывает, что бетон из опилок имеет более низкую теплопроводность по сравнению с обычным бетоном (в данном случае содержание опилок 0%). Снижение теплопроводности с увеличением опилок, облегченный
Таблица 4. Теплопроводность стабилизированных земляных блоков (Вт / мК) — после Sindanne et al. [89].
Рисунок 6. Коэффициент теплопроводности опилок бетона в зависимости от количества опилок.
, согласуется с выводами Asadi et al. [92]. Легкие заполнители не только снижают плотность, но и теплопроводность бетона. Обычный бетон с плотностью от 2100 до 2400 кг / м 3 имеет теплопроводность от 1,40 до 1,75 Вт / мК [93] [94]. Таким образом, добавление опилок в бетонную смесь значительно снижает теплопроводность получаемого легкого бетона.
Значения теплопроводности, показанные на рисунке 6, также удовлетворяют требованиям стандарта ASTM C332-09 [95], который устанавливает, что максимальная средняя теплопроводность для бетона, сделанного из легких заполнителей, должна быть равна 0.43 Вт / мК для сухого бетона с плотностью 1440 кг / м 3 на 28 дней.
3.5. Влияние композитов из опилок на акустические свойства строительных единиц
3.5.1. Звукопоглощение
Шумовое загрязнение считается одной из четырех основных экологических опасностей, включая загрязнение воздуха, воды и твердых отходов. Поэтому звукопоглощающие материалы играют важную роль в снижении воздействия шумового загрязнения на здоровье человека, например, потери слуха и стресса [96].Низкочастотный шум, особенно в диапазоне частот от 10 Гц до 100 Гц, создает особый шум окружающей среды, который может вызывать повышенное беспокойство у людей, чувствительных к его воздействию [97]. Звукопоглощающие материалы уменьшают акустическую энергию звуковой волны, когда волна проходит через нее. Одним из способов оценки характеристик звукопоглощающих материалов является измерение коэффициента звукопоглощения, который определяется как мера акустической энергии, поглощаемой материалом при падении энергетической волны [98] [99].
Коэффициент звукопоглощения 0,00 означает, что звук не поглощается, тогда как коэффициент звукопоглощения, близкий к 1,00 для диапазона звуковых частот от 125 до 4000 Гц, означает хорошее звукопоглощение [98] [100].
Древесина — наиболее часто используемый материал для звукопоглощения в зрительных залах. При использовании в различных формах в сочетании с дополнительными звукопоглощающими материалами он может обеспечить оптимальные звукопоглощающие свойства. В связи с этим было обнаружено, что древесина в виде опилок, включенных в бетон или строительный раствор, и другие связанные строительные элементы эффективно поглощают звук.
Kang et al. [101] исследовали композитные плиты из рисовой шелухи и опилок на предмет звукопоглощения в строительстве. Заданные плотности плит составляли 400, 500, 600 и 700 кг / м 3 . Процентное соотношение по массе смесей рисовой шелухи / опилок / фенола и смолы составляло 10/80/10, 20/70/10, 30/60/10 и 40/50/10 соответственно. Характеристики звукопоглощения этих плит сравнивали с характеристиками коммерческих гипсокартонных и древесноволокнистых плит. Коэффициенты звукопоглощения композитной плиты были около 0.20 при 500 Гц, 0,40 при 1000 Гц и 0,40 — 0,55 при более 1000 Гц. Коэффициент звукопоглощения композитной плиты оказался в два раза выше, чем у гипсокартона толщиной 11 мм, особенно на частоте 1000 Гц. Композитные плиты также показали более высокие коэффициенты звукопоглощения, чем коммерческие гипсовые плиты, в диапазоне частот от 500 до 4000 Гц. Общие результаты показали, что композитные плиты из рисовой шелухи и опилок можно использовать в качестве заменяющего материала для звукопоглощающих целей в неструктурных конструкциях, таких как потолки, обшивка стен и внутренние поверхности стен.
Tiuc et al. [100] исследовали звукопоглощение двух продуктов, сделанных из двух отходов, а именно переработанной резины и опилок. Один продукт состоит из переработанных резиновых частиц и 15% полиуретанового связующего. Другой составлен из опилок и 30% полиуретана. Оба продукта были толщиной 15 мм. Для диапазона частот от 100 до 1000 Гц оба продукта показали одинаковые характеристики коэффициента звукопоглощения. Однако для более высокого диапазона частот от 1000 до 3150 Гц образец с частицами каучука имел лучшие звукопоглощающие свойства.
Материалы, изготовленные из опилок и переработанных резиновых гранул, были протестированы на акустические характеристики и сопоставлены с существующими акустическими продуктами на рынке, а именно стекловатой и гибким пенополиуретаном. Коэффициент звукопоглощения был экспериментально оценен в диапазоне частот от 100 до 3200 Гц. Результаты показали, что композитные материалы из опилок и резиновых гранул обладают лучшими акустическими свойствами, чем существующие продукты, особенно на частотах ниже 1600 Гц.Коэффициент звукопоглощения, измеренный для материала, изготовленного из опилок и 30% полиуретанового связующего, имел минимальное значение 0,65 в диапазоне частот от 300 до 3150 Гц. Максимальный коэффициент звукопоглощения 0,979 был зарегистрирован на частоте 2000 Гц [99].
Tiuc et al. [102] далее сравнили звукопоглощение изделий, изготовленных из 100% гибкого пенополиуретана (100-FPF), и изделий, изготовленных из 50% еловых опилок и 50% гибкого пенополиуретана (50-FPF). Продукт 100-FPF продемонстрировал эффективные характеристики звукопоглощения в диапазоне частот от 100 до 1700 Гц.Этот продукт зарегистрировал максимальное значение коэффициента звукопоглощения 0,86 на частоте 1700 Гц. Продукт 50-FPF продемонстрировал эффективные характеристики звукопоглощения в диапазоне частот от 100 до 700 Гц, при этом максимальное значение коэффициента звукопоглощения составляло 0,89 на частоте 700 Гц. Это исследование также показало, что композиционные пористые материалы демонстрируют сложные характеристики звукопоглощения.
В таблице 5 представлены характеристики звукопоглощения различных материалов.Из этой таблицы ясно видно, что композитные опилки имеют лучшую звукопоглощающую способность по сравнению с такими материалами, как обычная древесина, обычный бетон и кирпич.
Таблица 5. Звукопоглощающие свойства некоторых распространенных строительных материалов и материалов, содержащих опилки.
3.5.2. Звукоизоляция
Звукопоглощающие изделия поглощают эхо внутри комнаты, тем самым предотвращая распространение звука по комнате. С другой стороны, звукоизоляционные материалы блокируют или останавливают распространение звуковых волн в соседние помещения.
Деревянные перегородки для офисов могут быть спроектированы таким образом, чтобы обеспечить любую требуемую степень звукоизоляции, начиная с минимума. Грамотный дизайн и внимание к деталям могут привести к очень высокой звукоизоляции при минимальной общей толщине [106].
Chung et al. [107] установили, что легкие системы пола / потолка на основе древесины (LTFS) могут иметь лучшую изоляцию от ударного шума по сравнению с системами на основе бетонных плит. Примеры таких систем включают элементы виброизоляции / демпфирования, такие как резиновые зажимы для потолочных реек, стекловолокно и слой смеси песка и опилок.Было обнаружено, что включение слоя песчано-опилок обеспечивает эффективное гашение вибрации и, следовательно, звукоизоляцию всей композитной конструкции в широком диапазоне частот. Позже Chung et al. [35] использовали математическую модель для прогнозирования вибрации легких деревянных каркасных систем пола / потолка (LTFS), вызванной механическим возбуждением. В этом исследовании были обобщены ранее полученные данные о хороших звукоизолирующих свойствах слоя песчано-опилок в LTFS. Теоретическая модель и экспериментальные измерения показали, что слой песчано-опилок эффективно гасит вибрацию в диапазоне частот от 10 до 200 Гц.
Emms et al. [108] исследовали несколько проблем, связанных с легкими полами, одной из которых является недостаточная ударопрочность в области низких частот от 16 до 250 Гц. Использование смеси песка и опилок в качестве заполнения в полостях этих легких полов обеспечивает хорошие результаты ударной изоляции, что объясняется сочетанием добавленной массы, большей демпфирующей способности и жесткости пола.
Chathurangani et al. [109] исследовали комбинацию опилок и волокна кокосовой койры для использования в качестве материалов для снижения шума стен.Исследование подтвердило возможность использования этих материалов для эффективного снижения шума. Из этого исследования коэффициент снижения шума, отношение между уровнями снижения шума к интенсивности падающего звука, значения, полученные для опилок и плиток из кокосового волокна, варьировались от 0,1 до 0,5. Позже исследование, проведенное в Индонезии, показало, что панели, изготовленные из аналогичных материалов, обладают хорошими акустическими характеристиками и могут использоваться для облицовки стен в шумных городских домах [110].
4. Будущие тенденции
Опилки — это перерабатываемые отходы и сырье, легкодоступное и легко доступное во многих странах-производителях древесины.Его можно собирать и транспортировать с минимальными затратами и энергией по сравнению с затратами и энергией, необходимыми для эксплуатации природных ресурсов. Повышение ценности этих отходов за счет их включения в производство строительных композитов будет направлено на поиск экологически чистых и энергоэффективных материалов в строительстве, внесет вклад в экологически чистую окружающую среду и создаст рабочие места.
Таким образом, в ближайшем будущем, вероятно, увеличатся исследования и разработки строительных композитов из опилок.Возможные направления будущих исследований и разработок включают производство универсальных строительных композитных материалов из опилок, которые будут более прочными, долговечными, легкими, энергоэффективными, рентабельными и безопасными для инфраструктуры гражданского строительства, чем это делается в настоящее время. Новые экологически чистые и энергоэффективные строительные композиты, которые, как ожидается, будут привлекать исследовательский и строительный интерес, включают те, которые сделаны из добавок цементных опилок, битумно-опилок и добавок полимеров и опилок.Разработка этих новых композитных материалов из опилок внесет огромный вклад в науку об альтернативных строительных материалах и сильно повлияет на пересмотр спецификаций и стандартов строительных материалов.
Другие потенциальные возможности будущего использования композитных опилок в строительстве включают их использование в качестве строительной опалубки и легкой кровельной черепицы. Эти композиты также могут заменить традиционные системы кондиционирования воздуха в условиях городской жары и теплового дискомфорта с дополнительными преимуществами энергосбережения и смягчения последствий изменения климата.
5. Выводы
Литература показывает, что во многих странах-производителях древесины ежегодно производится более 2 млн. М 3 3 опилок. В развивающихся странах этот материал часто утилизируется без разбора путем открытого захоронения и открытого сжигания, что создает огромную экологическую проблему. В этой статье были рассмотрены различные исследования по использованию опилок в строительстве, направленные на смягчение этой экологической проблемы, связанной с опилками. Рассмотренные исследования включают использование и возможное использование опилок и золы из опилок в строительных композитах из опилок, таких как ДСП, кирпичи, блоки и легкий бетон.
Древесно-стружечные плиты, содержащие опилки, могут иметь значения модуля упругости более 2100 МПа, разбухание по толщине не более 15% и приемлемые характеристики водопоглощения, соответствующие международным требованиям. Опилки и зола из опилок могут быть включены в состав сырья для производства кирпичей и блоков, которые удовлетворяют строительным требованиям для кирпичной кладки стеновых блоков и тротуарной плитки. Легкий бетон как для строительных, так и для неструктурных работ может производиться из опилок или золы из опилок, являющихся частью или одним из основных ингредиентов бетона.Строительные композиты из опилок также привлекательны своей низкой теплопроводностью, высоким звукопоглощением и хорошими звукоизоляционными характеристиками.
Однако из литературы отмечается, что повышенная доля опилок в строительных композитах из опилок отрицательно влияет на механические и физические характеристики производимых композитов. Замена части обычного песка в бетонной смеси с долей опилок от 5% до 15% может дать хороший легкий конструкционный бетон со значениями прочности на сжатие более 20 МПа.Анализ собранных данных дает зависимость между прочностью на сжатие опилок бетона ( ж c ) и замену песка содержанием опилок (λ) как ж c знак равно 25,944 е — 0,015 λ . Это соотношение дает оптимальное значение λ 17% для производства конструкционного бетона с ж c 20 МПа.
Замена цемента золой из опилок (SDA) в пропорции от 5% до 15% также дает бетон с прочностью на сжатие более 20 МПа.Более высокие пропорции опилок и SDA, чем эти, значительно снижают прочность опилок бетона. Замена от 10% до 30% песка, используемого при производстве блоков и кирпичей, опилками также может дать кирпичи и блоки из опилок с характеристиками сжатия и водопоглощения, которые соответствуют международным требованиям.
Более широкое использование опилок в строительстве будет в значительной степени способствовать устойчивости строительства, связанной с разработкой и использованием экологически чистых строительных материалов.Кроме того, использование композитных опилок в строительстве будет способствовать сохранению невозобновляемых строительных ресурсов, снижению потребления энергии, а также выбросов CO 2 в результате эксплуатации природных строительных материалов. Все это в конечном итоге внесет большой вклад в смягчение последствий изменения климата. Таким образом, композиты из опилок имеют не только рыночную, но и экологическую ценность. Таким образом, развивающиеся страны должны рассматривать опилки не как отходы, а как ценный побочный продукт, который может быть широко использован в строительной отрасли.
Благодарности
Авторы выражают благодарность за поддержку Университета Коппербелт, Китве, Замбия.
Ссылки[1] Кумар Д., Сингх С., Кумар Н. и Гупта А. (2014) Недорогой строительный материал для бетона в виде опилок. Глобальный журнал исследований в области инженерии, 14, 33-36.
[2] Тилак, Л.Н., Сантош Кумар, М.Б., Манвендра, С. и Ниранджан (2018) Использование древесной пыли в качестве мелкозернистого заполнителя в бетонной смеси.Международный научно-исследовательский журнал техники и технологий (IRJET), 5, 1249-1253.
[3] Огундипе, О. и Джимох, Ю. (2012) Соответствие бетонных опилок для жестких покрытий на основе прочности. Перспективные исследования материалов, 367, 13-18.
https://doi.org/10.4028/www.scientific.net/AMR.62-64.11
[4] Аду, С., Аду, Г., Фримпонг-Менса, К., Антви-Боасиако, К., Эффах, Б. и Аджеи, С. (2014) Максимальное использование древесных остатков и снижение производительности до Борьба с изменением климата.Международный журнал наук о растениеводстве и лесоводстве, 1, 1-12.
[5] Кларк, Дж. М. (2018) Создание рабочих мест в сельском хозяйстве, лесном хозяйстве и рыболовстве в Южной Африке: анализ тенденций, возможностей и ограничений занятости в лесном хозяйстве и деревообрабатывающей промышленности. Рабочий документ 52, Институт бедности, земельных и аграрных исследований (PLAAS), Университет Западного Кейпа, Беллвилл.
[6] Okedere, O.B., Fakinle, B.S., Sonibare, J.A., Elehinafe, F.Б., Адесина О.А. (2017) Загрязнение твердыми частицами от открытого сжигания опилок на юго-западе Нигерии. Cogent Environmental Science, 3, ID статьи: 1367112.
https://doi.org/10.1080/23311843.2017.1367112
[7] Schmidt, G.B.S. (2014) Китайский лес: пример из лесного сектора Западной Замбии. 8-я Международная конференция по качеству, Крагуевац, 23 мая 2014 г., стр. 37-49.
[8] Клаудиу А. (2014) Использование опилок в составе штукатурных растворов.ProEnvironment Promediu, 7, 30-34.
[9] Мамза П.А., Эзех Э.С., Гимба Э. и Артур Д.Э. (2014) Сравнительное исследование древесностружечных плит фенолформальдегида и карбамида формальдегида из древесных отходов для устойчивого развития окружающей среды. Международный журнал научных и технологических исследований, 3, 53-61.
[10] Хурмекоски, Э. (2017) Как деревянное строительство может снизить экологическую деградацию? Европейский лесной институт, Йоэнсуу.
[11] Оливер, К.Д., Нассар, Н.Т., Липпке, Б.Р. и Маккартер, Дж. Б. (2014) Углерод, ископаемое топливо и уменьшение биоразнообразия с помощью древесины и лесов. Журнал устойчивого лесного хозяйства, 33, 248-275.
https://doi.org/10.1080/10549811.2013.839386
[12] Эхуемело, Д. и Атондо, Т. (2015) Оценка восстановления пиломатериалов и образования отходов на отдельных лесопильных предприятиях в трех муниципальных районах штата Бенуэ, Нигерия. Прикладное тропическое сельское хозяйство, 20, 62-68.
[13] Камбугу, Р.К., Банана, А.Ю., Ззива, А., Агея, Дж. и Кабоггоза, Дж. Р. (2005) Относительная эффективность лесопильных заводов, работающих на плантациях хвойных пород Уганды. Угандийский журнал сельскохозяйственных наук, 11, 14-19.
[14] Ахатор П., Обанор А. и Угеге А. (2017) Древесные отходы Нигерии: потенциальный ресурс для экономического развития. Журнал прикладных наук и экологического менеджмента, 21, 246-251.
https://doi.org/10.4314/jasem.v21i2.4
[15] Олуфеми, Б., Акиндени, Дж. и Оланиран, С. (2012) Эффективность восстановления древесины на выбранных лесопилках в Акуре, Нигерия. Drvna Industrija, 63, 15-18.
https://doi.org/10.5552/drind.2012.1111
[16] Нкубе, Э. и Фири, Б. (2015) Концентрации тяжелых металлов в древесных опилках и дыме эвкалипта и сосны, провинция Коппербелт, Замбия. Мадерас. Ciencia y Tecnología, 17, 585-596.
https://doi.org/10.4067/S0718-221X2015005000052
[17] Департамент по вопросам окружающей среды (DEA), Отчет о состоянии отходов в Южной Африке (2018) Отчет о состоянии окружающей среды, во втором проекте отчета.DEA, Претория, 1-105.
[18] Guzman, A.D.M. и Манно, M.G.T. (2015) Дизайн кирпича со звукопоглощающими свойствами на основе пластиковых отходов и опилок. IEEE Access, 3, 1260-1271.
https://doi.org/10.1109/ACCESS.2015.2461536
[19] Garay, R.M. (2012) Лабораторные испытания влагостойких древесно-стружечных плит P3, изготовленных из остатков древесины. BioResources, 7, 3093-3103.
[20] Европейская организация лесопильной промышленности (EOS) (2018) Годовой отчет европейской лесопильной промышленности за 2017/2018 гг.EOS, Брюссель.
[21] Роминии, О., Адарамола, Б., Икумапайи, О., Огинни, О. и Акинола, С. (2017) Возможное использование опилок в энергетике, обрабатывающей промышленности и сельском хозяйстве; От расточительства к богатству. Всемирный журнал инженерии и технологий, 5, 526-539.
https://doi.org/10.4236/wjet.2017.53045
[22] Петри Б. (2014) Южная Африка: аргументы в пользу биомассы? Международный институт окружающей среды и развития, Лондон.
[23] Дик, Т., Фешете-Тутунару, Л. и Гаспар, Ф. (2016) Экспериментальный подход к воздействию брикетов из древесных опилок на окружающую среду. Энергетические процедуры, 85, 178-183.
https://doi.org/10.1016/j.egypro.2015.12.324
[24] Мейер, К. (2002) Бетон и устойчивое развитие. Специальные публикации ACI, 206, 501-512.
[25] Продовольственная и сельскохозяйственная организация Объединенных Наций (ФАО) (2019) Статистика лесных товаров.
http://www.fao.org/forestry/statistics/80938/en
[26] Продовольственная и сельскохозяйственная организация (ФАО) (2017 г.) Глобальные лесные товары: факты и цифры, 2016 г.Продовольственная и сельскохозяйственная организация Объединенных Наций, Рома.
[27] Нгандве, П., Чунгу, Д., Ратнасингам, Дж., Раманантоандро, Т., Донфак, П. и Мвитва, Дж. (2017) Развитие лесной промышленности в Замбии: возможность для государственно-частного партнерства для малых и средних предприятий. Международный обзор лесного хозяйства, 19, 467-477.
https://doi.org/10.1505/1465548822272374
[28] Абдулкарим, С., Раджи, С. и Адении, А. (2017) Разработка древесностружечных плит из отходов пенополистирола и опилок.Нигерийский журнал технологического развития, 14, 18-22.
https://doi.org/10.4314/njtd.v14i1.3
[29] Дотун, А.О., Адедиран, А.А. и Олуватимилехин, A.C. (2018) Оценка физических и механических свойств древесностружечных плит, полученных из древесной пыли и пластиковых отходов. Международный журнал инженерных исследований в Африке, 40, 1-8.
https://doi.org/10.4028/www.scientific.net/JERA.40.1
[30] Акинеми, А.Б., Афолаян, Дж.и Олуватоби, Э. (2016) Некоторые свойства композитных плит из кукурузного початка и древесных опилок. Строительные и строительные материалы, 127, 436-441.
https://doi.org/10.1016/j.conbuildmat.2016.10.040
[31] Эрахрумен, А., Ареган, С., Огунлей, М., Ларинде, С. и Одеяле, О. (2008) Отдельные физико-механические свойства цементно-стружечных плит, изготовленных из сосны (Pinus caribaea M.) Смесь кокосовых опилок (Cocos nucifera L.). Научные исследования и эссе, 3, 197-203.
[32] Агуа, Э., Аллогнон-Хуэсу, Э., Аджови, Э. и Тогбеджи, Б. (2013) Теплопроводность композитов из отходов древесины и пенополистирола. Строительные и строительные материалы, 41, 557-562.
https://doi.org/10.1016/j.conbuildmat.2012.12.016
[33] Чанхун, М., Падону, С., Аджови, Э.С., Олодо, Э. и Доко, В. (2018) Исследование использования древесных отходов, пластиков и полистиролов для различных применений в строительной индустрии.Строительные и строительные материалы, 167, 936-941.
https://doi.org/10.1016/j.conbuildmat.2018.02.080
[34] Давуд, М.Х.А., Абтан, Ю.Г. и Варёш, В.А. (2013) Структурное поведение композитных многослойных панелей. Журнал инженерии и устойчивого развития, 17, 220-232.
[35] Чанг, Х., Эммс, Г. и Фокс, К. (2014) Снижение вибрации в легких напольных / потолочных системах с демпфирующим слоем из песчано-опилок. Acta Acustica United with Acustica, 100, 628-639.
https://doi.org/10.3813/AAA.918742
[36] Antwi-Boasiako, C., Ofosuhene, L. и Boadu, K.B. (2018) Пригодность опилок трех тропических пород древесины для древесно-цементных композитов. Журнал устойчивого лесного хозяйства, 37, 414-428.
https://doi.org/10.1080/10549811.2018.1427112
[37] Манги, С.А., Джамалуддин, Н.Б., Сиддики, З., Мемон, С.А. и Ибрагим, М.Х.Б.В. (2019) Использование опилок в бетонных блоках: обзор.Научно-исследовательский журнал инженерии и технологий Мехранского университета, 38, 487.
[38] Гил, Х., Ортега, А. и Перес, Дж. (2017) Механическое поведение строительного раствора, армированного отходами опилок. Разработка процедур, 200, 325-332.
https://doi.org/10.1016/j.proeng.2017.07.046
[39] Акерс, Д.Дж., Грубер, Р.Д., Рамм, Б.В., Бойл, М.Дж., Григар, Дж. Г., Роу, С.К., Бремнер, Т.В., Клуцковски, Е.С., Шитц, С.Р. и Бург, Р. (2003) Руководство для конструкционного легкого заполнителя, в ACI 213R-03.Американский институт бетона (ACI), Мичиган.
[40] Mohammed, J.H. и Хамад, А.Дж. (2014) Обзор материалов, свойств и применения легкого бетона. Технический обзор инженерного факультета Сулийского университета, 37, 10-15.
[41] Ахмед В., Хушнуд Р.А., Мемон С.А., Ахмад С., Белудж В.Л. и Усман М. (2018) Эффективное использование опилок для производства экологически чистых и теплосберегающих бетонов нормального веса и легких бетонов с заданными характеристиками разрушения.Журнал чистого производства, 184, 1016-1027.
https://doi.org/10.1016/j.jclepro.2018.03.009
[42] Badejo, S.O.O. (1987) Исследование влияния содержания цементного вяжущего на свойства цементно-стружечных плит из четырех тропических пород древесины. Малазийский лесник (Малайзия).
[43] Олуфеми Б. и Малами А. (2011) Плотность и характеристики прочности на изгиб выращенного в северо-западной части Нигерии эвкалипта камалдуансис в отношении использования в качестве древесины.Исследовательский журнал лесного хозяйства, 5, 107-114.
https://doi.org/10.3923/rjf.2011.107.114
[44] Рейес, Г., Браун, С., Чепмен, Дж. И Луго, А.Е. (1992) Плотность древесины тропических пород деревьев. Общий технический отчет SO-88. Департамент сельского хозяйства США, Лесная служба, Южная лесная экспериментальная станция, Новый Орлеан, 1-15.
[45] ANSI (Американский национальный институт стандартов) (2009) Американский национальный стандарт на ДСП. ANSI / A208.1. Ассоциация композитных панелей, Гейтерсбург.
[46] BS EN 312 (2010) ДСП. Характеристики. Европейский комитет по стандартизации, Брюссель.
[47] BS EN 317 (1993) ДСП и древесноволокнистые плиты. Определение набухания по толщине после погружения в воду. Британский институт стандартов, Лондон.
[48] Атуанья, C.U. и Обеле, К. (2016) Оптимизация технологических параметров композитов из опилок / переработанного полиэтилена.Journal of Minerals and Materials Characterization and Engineering, 4, 270.
https://doi.org/10.4236/jmmce.2016.44024
[49] Абу-Зарифа, А., Абу-Шаммала, М. и Аль-Шейх, А. (2018) Устойчивое производство ДСП из опилок и сельскохозяйственных отходов, смешанных с переработанными пластиками. Американский журнал экологической инженерии, 8, 174-180.
[50] Куполати, В.К., Грасси, С. и Фраттари, А. (2012) Экологическое озеленение за счет использования опилок для производства кирпича.OIDA International Journal of Sustainable Development, 4, 63-78.
[51] SANS 10400 (2011) Применение национальных строительных норм. Часть K: Стены. Отдел стандартов SABS, Претория.
[52] Равиндрараджа, Р.С., Кэрролл, К. и Апплярд, Н. (2001) Разработка бетонных опилок для изготовления блоков. Материалы конференции строительных технологий, Кота-Кинабалу, 12-14 октября 2001 г.
[53] Дадзие, Д.К., Доки, Г.О., Ниакох, Н. (2018) Сравнительное исследование свойств песчаных блоков, изготовленных с использованием опилок в качестве частичной замены песка. Международный журнал научных и инженерных исследований, 9, 1357-1362.
[54] Буб, Т. (2014) Характеристики опилок в недорогих блоках из песчаника. Американский журнал инженерных исследований, 3, 197-206.
[55] BS 6073 (1981) Часть 1: Сборные железобетонные блоки, часть 1. Спецификация для сборных бетонных блоков.Британский институт стандартов, Лондон.
[56] Этту, Л.О., Ариманва, Дж. И., Нджоку, Ф. К., Аманзе, А. П.С. и Эзиефула, У.Г. (2013) Прочность бетонных блоков из цементного песка и бетонных блоков, содержащих золу из опилок и золу из папилломы. Международный журнал технических изобретений, 2, 35-40.
[57] Тургут П. и Альгин Х.М. (2007) Известняковая пыль и древесные опилки как кирпич. Строительство и окружающая среда, 42, 3399-3403.
https: // doi.org / 10.1016 / j.buildenv.2006.08.012
[58] Moreira, A.B.S., Macêdo, A.N. и Соуза, П.С.Л. (2012) Состав для прочности бетонных блоков с опилками в зависимости от обработки остатков. Acta Scientiarum. Технологии, 34, 269-276.
https://doi.org/10.4025/actascitechnol.v34i3.14372
[59] Adebakin, I.H., Adeyemi, A.A., Adu, J.T., Ajayi, F.A., Lawal, A.A. и Огунринола, О. (2012) Использование опилок в качестве добавки при производстве недорогих и легких пустотелых блоков из песчаника.Американский журнал научных и промышленных исследований, 3, 458-463.
https://doi.org/10.5251/ajsir.2012.3.6.458.463
[60] Зива, А., Кизито, С., Банана, А., Кабоггоза, Дж., Камбугу, Р. и Ссеремба, О. (2006) Производство композитных кирпичей из опилок с использованием портландцемента в качестве связующего. Угандийский журнал сельскохозяйственных наук, 12, 38-44.
[61] Осей, Д.Ю. и Джексон, Э. (2016) Прочность бетона на сжатие с использованием опилок в качестве заполнителя.Международный журнал научных и инженерных исследований, 7, 1349-1353.
[62] Bdeir, L.M.H. (2012) Исследование некоторых механических свойств строительного раствора с опилками как частичная замена песка. Анбарский журнал технических наук, 5, 22-30.
[63] Сулиман, Н.Х., Разак, А.А.А., Мансор, Х., Алисибрамулиси, А. и Амин, Н.М. (2019) Бетон с использованием опилок в качестве частичной замены песка: прочен ли он и не угрожает здоровью? Сеть конференций MATEC, 258, идентификатор статьи: 01015.
[64] Ойедепо, О.Дж., Олуваджана, С.Д. и Аканде, С.П. (2014) Исследование свойств бетона с использованием опилок в качестве частичной замены песка. Гражданские и экологические исследования, 6, 35-42.
[65] Натан, М.В. (2018) Влияние опилок как мелкого заполнителя в бетонной смеси. Международный инженерно-технический журнал, 4, 1-12.
[66] Читра, Р. и Хемаприя (2018) Экспериментальное исследование прочности бетона путем частичной замены мелкозернистого заполнителя на опилочную пыль.Международный журнал чистой и прикладной математики, 119, 9473-9479.
[67] Савант, А., Шарма, А., Рахат, Р., Майекар, Н. и Гаддж, М.Д. (2018) Частичная замена песка опилками в бетоне. Международный научно-исследовательский журнал техники и технологий, 5, 3098-3101.
[68] Аваль А.А., Марьяна А. и Хоссейн М. (2016) Некоторые аспекты физико-механических свойств опилок бетона. Международный журнал GEOMATE, 10, 1918-1923.
[69] Соджоби, А.О. (2016) Оценка эффективности экологически чистых легких блокировочных бетонных блоков для мощения, включающих отходы опилок и латерит. Cogent Engineering, 3, идентификатор статьи: 1133480.
https://doi.org/10.1080/23311916.2016.1255168
[70] Соджоби, А.О., Аладегбойе, О.Дж. и Аволуси Т.Ф. (2018) Зеленые блокирующие брусчатки. Строительные и строительные материалы, 173, 600-614.
https://doi.org/10.1016/j.conbuildmat.2018.04.061
[71] Олутоге, Ф.А. (2010) Исследования опилок и оболочки пальмовых ядер как совокупного замещения. ARPN Journal of Engineering and Applied Sciences, 5, 7-13.
[72] Невилл, А. (2011) Свойства бетона. 5-е издание, Pearson Education Limited, Эссекс.
[73] ASTM C330 / C330M-09 (2009) Стандартные технические условия для легких заполнителей для конструкционного бетона. ASTM International, Западный Коншохокен.
[74] Сасах Дж. И Канкам К. (2017) Исследование кирпичного раствора с использованием опилок в качестве частичной замены песка. Lambert Academic Publishing, Маврикий, 1-66.
[75] Огундипе, О. и Джимох, Ю. (2009) Соответствие бетонных опилок для жестких покрытий, основанное на долговечности. Перспективные исследования материалов, 62-64, 11-16.
https://doi.org/10.4028/www.scientific.net/AMR.62-64.11
[76] Хусейн, Г.Ф., Мемон, Р.П., Кубба, З., Сэм, A.R.M., Асаад, М.А., Мирза, Дж. И Мемон, У. (2019) Механические, термические и долговечные характеристики отходов опилок в качестве замены грубых заполнителей в обычном бетоне. Jurnal Teknologi, 81, 151-161.
https://doi.org/10.11113/jt.v81.12774
[77] Окороафор, С.Ю., Ибеаругбулам, О.М., Онуквуга, Э.Р., Аняогу, Л. и Ада, Э.И. (2017) Структурные характеристики композита опилки-песок-цемент. Международный журнал достижений в области исследований и технологий, 6, 173-180.
[78] Удоео, Ф.Ф. и Дашибил П. (2002) Опилки золы как бетонный материал. Журнал материалов в гражданском строительстве, 14, 173-176.
https://doi.org/10.1061/(ASCE)0899-1561(2002)14:2(173)
[79] Мартонг, К. (2012) Зола из опилок (SDA) как частичная замена цемента. Международный журнал инженерных исследований и приложений, 2, 1980–1985.
[80] Обиладе, И. (2014) Использование золы от опилок в качестве частичной замены цемента в бетоне.Международный журнал инженерии и научных изобретений, 2319, 36-40.
[81] Дхалл, Х. (2017) Влияние на свойства бетона при использовании золы от опилок в качестве частичной замены цемента. Международный журнал инновационных исследований в области науки, техники и технологий, 6, 18603-18610.
[82] Онвука, Д., Аняогу, Л., Чидзиоке, К. и Окой, П. (2013) Прогноз и оптимизация прочности на сжатие золоцементного бетона на основе древесных опилок с использованием симплекс-конструкции Шеффе.Международный журнал научных и исследовательских публикаций, 3, 1-9.
[83] Фапохунда, К., Акинбиле, Б. и Ойеладе, А. (2018) Обзор свойств, структурных характеристик и возможностей применения бетона, содержащего древесные отходы, в качестве частичной замены одного из составляющих его материалов. Журнал YBL по искусственной среде, 6, 63-85.
https://doi.org/10.2478/jbe-2018-0005
[84] Манги, С.А., Джамалуддин, Н., Ван Ибрагим, М., Норидах, М. и Соху, С. (2017) Использование золы из опилок в качестве замены цемента при производстве бетона: обзор. Международный научно-исследовательский журнал технических наук и технологий, 1, 11-15.
[85] Рахим А., Оласунканми Б. и Фолорунсо К. (2012) Пыльная зола как частичная замена цементу в бетоне. Организация, технологии и менеджмент в строительстве: Международный журнал, 4, 474-480.
https://doi.org/10.5592/otmcj.2012.2.3
[86] Асдрубали, Ф., Д’Алессандро, Ф. и Скьявони, С. (2015) Обзор нетрадиционных устойчивых строительных изоляционных материалов. Устойчивые материалы и технологии, 4, 1-17.
https://doi.org/10.1016/j.susmat.2015.05.002
[87] Мемон, Р.П., Сэм, А.Р.М., Авал, А.А. и Ачекзай, Л. (2017) Механические и термические свойства опилок бетона. Jurnal Teknologi (наука и техника), 79, 23-27.
https://doi.org/10.11113/jt.v79.9341
[88] Салих, С.А., Кзарь А. (2015) Изучение полезности использования камыша и опилок в качестве отходов для производства цементных строительных блоков. Инженерный журнал, 21, 36-54.
[89] Sindanne, SA, Ntamack, GE, Sanga, RPL, Moubeke, CA, Sallaboui, ESK, Bouabid, H., Mansouri, K. и D’ouazzane, SC (2014) Теплофизические характеристики земных блоков, стабилизированных цементом , Опилки и известь. Журнал строительных материалов и конструкций, 1, 58-64.
[90] Абдул Амир, О.(2018) Оценка тепловых свойств легкого бетона, полученного с использованием местных промышленных отходов. Сеть конференций MATEC, 162, идентификатор статьи: 02027.
https://doi.org/10.1051/matecconf/201816202027
[91] Ченг, Ю., Ю, В., Чжан, К., Ли, Х. и Ху, Дж. (2013) Использование отходов опилок в бетоне. Инженерная, 5, 943.
https://doi.org/10.4236/rus.2013.512115
[92] Асади, И., Шафиг, П., Хассан, З.F.B.A. и Махьюддин, Н. (2018) Теплопроводность бетона — обзор. Журнал Строительной техники, 20, 81-93.
https://doi.org/10.1016/j.jobe.2018.07.002
[93] Тармак, Л. (2015) Бетон с низкой теплопроводностью, в руководстве по решениям. Лафарж Тармак Лимитед, Солихалл.
[94] Баден-Пауэлл, К. (2008) Карманный справочник архитектора. 3-е издание, Architectural Press, Elsevier, Oxford.
https://doi.org/10.4324/97800804
[95] ASTM C332-09 (2009) Стандартные технические условия для легких заполнителей для изоляционного бетона.ASTM International, Западный Коншохокен.
[96] Куи, Х. и Энхуи, Ю. (2018) Влияние толщины, плотности и глубины полости на звукопоглощающие свойства шерстяных плит. Autex Research Journal, 18, 203-208.
https://doi.org/10.1515/aut-2017-0020
[97] Левентхолл, Х. (2004) Низкочастотный шум и раздражение. Шум и здоровье, 6, 59.
[98] Seddeq, H.S. (2009) Факторы, влияющие на акустические характеристики звукопоглощающих материалов.Австралийский журнал фундаментальных и прикладных наук, 3, 4610-4617.
[99] Тиук, А.-Э., Вермешан, Х., Габор, Т. и Василе, О. (2016) Улучшенные звукопоглощающие свойства пенополиуретана, смешанного с текстильными отходами. Энергетические процедуры, 85, 559-565.
https://doi.org/10.1016/j.egypro.2015.12.245
[100] Тиук, А.Е., Василе, О. и Габор, Т. (2014) Определение антивибрационных и акустических свойств некоторых материалов, изготовленных из переработанных резиновых частиц и опилок.Румынский журнал акустики и вибрации, 11, 47-52.
[101] Канг, К.-В., О, С.-В., Ли, Т.-Б., Кан, В., Мацумура, Дж. (2012) Способность звукопоглощения и механические свойства композитного риса Доска корпуса и опилок. Journal of Wood Science, 58, 273-278.
https://doi.org/10.1007/s10086-011-1243-5
[102] Тиук, А.Е., Немеш, О., Вермешан, Х. и Тома, А.С. (2019) Новые звукопоглощающие композитные материалы на основе опилок и пенополиуретана.Композиты Часть B: Инженерия, 165, 120-130.
https://doi.org/10.1016/j.compositesb.2018.11.103
[103] Дэнс, С. и Шилд, Б. (2000) Коэффициенты поглощения обычных строительных материалов для использования в компьютерном моделировании замкнутых пространств. Строительная Акустика, 7, 217-224.
https://doi.org/10.1260/1351010001501615
[104] Ворлендер М. (2007) Аурализация: основы акустики, моделирования, моделирования, алгоритмов и акустической виртуальной реальности.Springer Science & Business Media, Берлин.
[105] Тиук, А.-Э., Дан, В., Вермешан, Х., Габор, Т. и Проороку, М. (2016) Восстановление опилок и гранул вторичного каучука в качестве звукопоглощающих материалов. Журнал экологической инженерии и менеджмента, 15, 1093-1101.
https://doi.org/10.30638/eemj.2016.122
[106] Чадли Р. и Грино Р. (2013) Справочник по строительству зданий. 9-е издание, Рутледж, Абингдон-он-Темз.
https://doi.org/10.4324/9780080970622
[107] Чанг, Х., Фокс, К., Додд, Г. и Эммс, Г. (2010) Легкие напольные / потолочные системы с улучшенной изоляцией от ударного шума. Строительная акустика, 17, 129-141.
https://doi.org/10.1260/1351-010X.17.2.129
[108] Эммс, Г., Чанг, Х., Макганнигл, К. и Додд, Г. (2006) Улучшение ударной изоляции полов из легкой древесины. in Proceedings of Acoustics 2006, Крайстчерч, 20-22 ноября 2006 г., стр. 147-153.
[109] Чатурангани, О., Перера, В., Кумари, Х., Субаши, Г. и Де Силва, Г. (2013) Использование опилок и кокосового кокосового волокна в качестве шумопоглощающих материалов поверхности стен. Симпозиум по обмену исследованиями в области гражданского строительства, Матара, 16-19.
[110] Сетйовати, Э., Хардиман, Г. и Атмаджа, С.Т. (2015) Сравнение экологически чистых материалов для акустических вафельных панелей из опилок и кокосового волокна. Прикладная механика и материалы, 747, 221-225.
https: // doi.org / 10.4028 / www.scientific.net / AMM.747.221
Прочностные характеристики глинистого грунта, стабилизированного золой опилок
Пределы консистенции
Изменение пределов консистенции в зависимости от содержания SDA (%) показано на рис. 4. Как видно из рисунка, предел текучести и предел пластичности возрастают с увеличением Содержание SDA. Это можно рассматривать как результат добавления SDA, который имеет более высокое сродство к водопоглощению.
Фиг.4Изменение пределов консистенции в зависимости от зольности опилок (%)
Характеристики уплотнения
Изменение максимальной плотности в сухом состоянии и оптимального содержания влаги в зависимости от содержания SDA (%) показано на рис.5 и 6 соответственно. Максимальная сухая плотность уменьшается с увеличением содержания SDA. Однако оптимальная влажность увеличивается с увеличением содержания SDA до 8% и уменьшается. Уменьшение веса сухой единицы может быть связано с более низким удельным весом SDA, в то время как увеличение оптимального содержания влаги может быть связано с необходимостью гидратации воды.
Фиг.5Изменение максимальной плотности в сухом состоянии в зависимости от зольности опилок (%)
Фиг.6Изменение оптимальной влажности в зависимости от зольности опилок (%)
Калифорния передаточное число подшипников
Метод CBR был признан наиболее надежным практическим средством определения прочности грунтового основания (несущей способности грунта) и оценки необходимой толщины дорожного покрытия для удовлетворения заданной нагрузки. CBR — это мера сопротивления прямому проникновению (несущая способность) любого грунта, которая выражается в процентах от несущей способности стандартных образцов щебня (которая принимается за 100% -ное значение), определяемой испытанием на проникновение.В настоящем исследовании была предпринята попытка провести испытания CBR на грунте, стабилизированном различными пропорциями SDA. На рисунке 7 показаны результаты испытаний CBR для стабилизированного грунта. Как видно, показатели CBR стабилизированного грунта были значительно улучшены, что положительно сказалось на строительстве дорожных покрытий. Институт асфальта [16] рекомендовал значение CBR 7–20% для основания шоссе и 0–7% для материалов основания. На основании этого грунт, стабилизированный SDA, может быть использован в качестве материала основания для строительства дорожных покрытий.На рис. 8 показано изменение CBR в зависимости от содержания SDA. Увеличение CBR может быть связано с пуццолановым эффектом SDA, а снижение после достижения оптимального значения связано с низкой силой, демонстрируемой SDA.
Рис. 7Кривые пенетрации для испытаний CBR для глинистых грунтов, стабилизированных золой опилок (SDA)
Рис. 8Вариация CBR с добавлением разного процентного содержания золы опилок
Прочность на сжатие без ограничений
Испытания на прочность на сжатие без ограничений — это наиболее распространенный, популярный и применяемый метод оценки прочности связных и стабилизированных грунтов.Это испытание можно рассматривать как частный случай испытания на трехосное сжатие, когда боковое ограничивающее давление равно нулю. Это основной тест, рекомендуемый для определения необходимого количества добавки, используемой для стабилизации грунта. Как правило, для данного типа стабилизации, чем выше прочность на сжатие, тем лучше качество стабилизированного материала. Кривая напряжения-деформации для всех образцов показана на рис. 9. Изменение прочности на неограниченное сжатие в зависимости от содержания SDA показано на рис.10. Прочность на сжатие без ограничения увеличивается с 248 до 313,14 кН / м 2 при добавлении 4% SDA, который считается оптимальным. Увеличение прочности может быть связано с пуццолановыми реакциями SDA с образованием цементных продуктов между CaOH, присутствующим в почве, и пуццоланом, присутствующим в SDA. Тогда как прочность снижается до 184,428 и 182 кН / м 2 при добавлении 8 и 12% SDA соответственно. Это происходит из-за низкой прочности SDA, который, следовательно, занимает в образце.Когда избыток SDA вносится в почву, он образует слабые связи между почвой и образовавшимися цементными соединениями. Согласно Дасу [17], консистенция глинистого грунта может быть определена следующим образом: 0–25 кН / м 2 — очень мягкий, 25–50 кН / м 2 — мягкий, 50–100 кН / м 2 — средне-мягкий, 100–200 кН / м 2 — жесткий, 200–400 кН / м 2 — очень жесткий и более 400 кН / м. 2 указывает на твердую глину. Из района исследования: однородная глинистая почва и глинистая почва с содержанием SDA 4% очень жесткая, тогда как глинистая почва с 8 и 12% SDA является жесткой.Если целевая почва изменится, свойства и прочность могут измениться в зависимости от состава почвы.
Рис. 9Кривые напряжение-деформация для глинистого грунта, стабилизированного разным процентным содержанием SDA
Рис. 10Вариант UCS с добавлением разного процентного содержания золы опилок
поделок из глины для детей | HowStuffWorks
Детские поделки из глины непременно запачкают руки, но результат того стоит.Вы можете использовать глину для создания причудливых творений или использовать ее для трансформации принтов из газет. На самом деле способов использования глины слишком много, чтобы их рассматривать.
Одна из лучших особенностей поделок из глины — это то, что у вас в доме есть все необходимые ингредиенты. Вам не нужно будет специально ехать в магазин, чтобы что-нибудь забрать — так вы сможете сразу же приступить к работе.
Продолжайте читать, чтобы узнать, как создавать поделки из глины:
Crazy Putty Dough
Это сумасшедшее глиняное тесто позволяет делать точные копии комиксов, которые вы найдете в газете.Узнайте больше здесь.
Глиняное тесто на опилках
Вместо того, чтобы выбрасывать опилки, смешайте их с несколькими другими ингредиентами, чтобы создать удивительные аксессуары.
Глиняное тесто для лепки
Смешивая это базовое тесто, вы можете создавать множество типов маленьких существ. Узнать больше.
Coiled Bowl
Добавьте глину в скрученные спирали, чтобы создать уникальную чашу.
Глиняное тесто для лепки
Зажигайте лепешку из глиняного теста своим любимым пищевым красителем и получайте удовольствие от лепки своих творений.
Тесто из соленой глины
Для приготовления обычного глиняного теста добавьте немного соли и вылепите себе несколько шедевров.
Аксессуары из глины
Украсьте свою одежду носимыми глиняными заколками и глиняными пуговицами.
Глиняный принтер
Создайте свои собственные канцелярские принадлежности или настенное искусство с помощью глиняного блока для печати.
Глиняные статуи
Используя проволоку и украсив ее глиной, вы можете создавать свои собственные трехмерные творения.Узнайте больше здесь.
Глиняные лодки
Плавайте, создавая веселье, с этими удивительными глиняными лодками.
Глина и свечи
Если вы хотите подсвечник, который выражает тепло и любовь, обратите внимание на этот забавный проект.
Shell Print Clay Craft
Окаменелости являются свидетельством древней жизни на Земле. Сделайте свои «древние» окаменелости с помощью этой глиняной поделки.
Сюжетные персонажи Clay Craft
Создайте персонажей для историй, которые вам нравятся, с помощью этого изящного глиняного проекта.
Картина Эта поделка из глины
Эта рамка для картины, украшенная глиной, станет отличным подарком на праздники. Узнайте больше об этой поделке из глины.
You are a Star Clay Craft
Сделайте эти звезды, а затем устройте свою собственную церемонию награждения с помощью этого забавного глиняного проекта.
Продолжайте читать, чтобы узнать, как волшебным образом поднять комикс прямо с газеты с помощью какой-нибудь сумасшедшей замазки.
Чтобы узнать больше о творческих поделках для детей, посетите:
Выращивание грибов на опилках
Многие виды грибов, особенно устрицы, отлично подходят и сильно плодоносят на соломенных бревнах, как было объяснено в этом посте .
Тем не менее, большинство грибов для гурманов на самом деле будут лучше расти, если их выращивать на опилках лиственных пород с добавлением какой-либо добавки, богатой азотом.
Выращивание изысканных грибов на блоках из опилок потребует немного больше первоначальной работы, чем соломенные бревна, и больше оборудования — в основном потому, что блоки из опилок необходимо стерилизовать под давлением — в отличие от бревен из соломы, которые нужно только пастеризовать.
Тем не менее, этот процесс быстрый, менее беспорядочный, имеет меньшую вероятность заражения и обеспечивает идеальную среду для грибов для выращивания крупных здоровых плодов.
В основном рецепте, который мы используем для выращивания всех наших изысканных грибов, используются гранулы из древесных опилок, пшеничные отруби и вода. Пеллеты из твердой древесины используются, потому что они легко доступны в местных розничных магазинах или в Интернете и легко хранятся.
Убедитесь, что вы покупаете гранулы из твердой древесины, а не из древесины хвойных пород. На древесине хвойных пород грибы вообще плохо растут.
Гранулы маленькие и расширяются только при замачивании в воде. Пшеничные отруби используются в качестве добавки, богатой азотом. Его можно найти в небольших количествах в местном бакалейном магазине, но это может быть довольно дорого.
Лучше купить немного в кормовом или фермерском магазине. Также можно использовать овсяные отруби, но мы обнаружили, что пшеничные отруби являются наиболее эффективными. Что касается воды, хитрость заключается в том, чтобы добавить ровно столько, сколько нужно, чтобы добиться нужного содержания влаги.
Вы не хотите, чтобы ваш блок был слишком влажным или слишком сухим. Следующий рецепт отлично подходит для использования, но вам, возможно, придется немного изменить его, чтобы он соответствовал определенному содержанию влаги в гранулах.
Рецепт блока для плодоношения:
На каждые 5 фунтов плодового блока :
- 5 чашек гранул из твердой древесины
- 1.4 литра воды
- 1-1 / 4 стакана пшеничных отрубей
Как выращивать грибы на блоках для плодоношения из опилок
Шаг 1: Измерьте компоненты
По приведенному выше рецепту получится блок весом приблизительно 4 фунта 4 унции. Ваш последний бок должен весить 5 фунтов после того, как вы добавите 12 унций зерновой порции . Лучше всего использовать несколько блоков одновременно, столько, сколько может поместиться внутри вашего стерилизатора высокого давления.
Этот консервный автомат presto pressure относительно дешев и может вместить 4 больших блока, изготовленных из гранул на 20 чашек, 22.5 стаканов воды и 5 стаканов пшеничных отрубей
Шаг 2: Добавьте воды к гранулам опилок
Поместите гранулы из опилок твердых пород в большую емкость или подходящий контейнер для смешивания. Добавьте необходимое количество воды и перемешивайте, пока гранулы не распадутся на рыхлые опилки. Добавление теплой воды заставляет опилки распадаться намного быстрее, но в этом нет необходимости, так как холодная вода отлично подойдет. Чтобы перемешать все гранулы, может потребоваться некоторое время, но вы должны быть уверены, что все они разбиты, потому что грибам будет намного сложнее разрушить затвердевшие гранулы.
Шаг 3: Добавьте пшеничные отруби
После того, как опилки смешаны и все гранулы распались, добавьте необходимое количество отрубей. Вы можете увеличить количество отрубей, чтобы добавить больше питательных веществ в блок, но большее количество отрубей увеличит вероятность заражения, а добавление большего количества в конечном итоге приведет к снижению отдачи. Обязательно тщательно и равномерно перемешайте отруби с опилками.
Шаг 4: Добавление смеси в мешки для выращивания
Взвесьте необходимое количество смеси опилок / отрубей и добавьте ее в мешок для выращивания .Я добавляю 4 фунта 4 унции в каждый мешок для выращивания, что делает блок 5 фунтов после добавления порождения.
Пакеты специально созданы для выращивания грибов. Они изготовлены из полипропилена, который выдерживает процесс стерилизации. Пластырь фильтра позволяет грибам дышать, пока они заселяют субстрат.
Шаг 5: Сложите пакеты вниз
Верхние части пакетов для выращивания имеют складки и должны быть сложены определенным образом, с фильтром, установленным между вставками. Это предотвращает загрязнение во время охлаждения после стерилизации.Когда пакеты остынут, в них будет втягиваться воздух.
Если между косынками нет фильтра, грязный воздух может проникнуть сквозь него и испортить ваш проект. Поместив фильтр между косынками, вы можете решить эту проблему.
После того, как фильтр вставлен, сложите верхнюю часть пакетов пару раз. В качестве фильтра вы можете использовать отрезок тайвека или квадратный вырез костюма маляра.
Шаг 6: Стерилизация под давлением
Загрузите стерилизатор под давлением, сложив пакеты друг на друга.
Обязательно используйте крышки для банок или что-нибудь такое, что предотвратит прямой контакт пакетов для выращивания со дном стерилизатора, так как это может привести к возгоранию пакетов. Заполните водой до уровня чуть ниже верха нижнего мешка.
Вам понадобится больше воды, чем при изготовлении зерновых банок, потому что стерилизация будет длиться намного дольше. Кроме того, не забудьте добавить тарелку или что-нибудь тяжелое на верх пакетов. Если вы не сделаете этого важного шага, вы рискуете, что мешок забьет груз и предохранительный клапан на скороварке.
Это может привести к тому, что давление внутри скороварки достигнет опасного уровня. Стерилизуйте пакеты под давлением в течение 2,5 часов.
Это кажется долгим, но необходимо, чтобы тепло полностью проникло внутрь блока и полностью уничтожило все загрязнения.
Блок плодоношения после стерилизации, готовый к инокулированию зерновой икрой. Обратите внимание, как накладка с фильтром вставляется между косынками, а верхняя часть складывается вдвое.
Шаг 7: Охлаждение и инокуляция
Дайте вашим плодовым блокам остыть не менее 8 часов.Я люблю стерилизовать под давлением на ночь и позволять скороварке полностью остыть за ночь. Все, что превышает 38 ° C, потенциально может убить ваш мицелий.
Плодовые блоки лучше всего инокулировать перед вытяжкой с ламинарным потоком . Вы можете сделать это в перчаточном ящике или подобном, но это повысит ваши шансы на заражение. После того, как вы добавили зерновую породу к опилкам, закрепите верхнюю часть пакета проволокой или стяжкой-молнией и поставьте на полку.
Встряхните пакет для равномерного распределения отдельных зерен по всему пакету.Это ускорит заселение блока.
Влияние опилок на поведение глинистых почв
Реферат
Обработка почвы различными материалами, такими как известь, летучая зола, цемент с бентонитом и химические инъекции, использовалась для обработки хорошей почвы. Характеристики почвы позволили выбрать лучший добавочный материал, улучшающий его поведение. В этой статье отходы опилок были добавлены к набухающей почве, чтобы улучшить стабилизированные характеристики. При строительстве традиционных домов в некоторых районах египетской сельской местности в качестве цементируемого материала используется глина, смешанная с опилками.В этой бумаге использовались опилки с различным процентным содержанием глинистой почвы 0, 1, 3 и 5% от веса. Для изучения поведения смесей глиняных опилок использовались многие тесты, такие как определение индекса, прочности и набухания. Результат показал, что непрямая прочность на разрыв для образцов, высушенных на воздухе, увеличилась за счет увеличения доли опилок примерно на 1,75%, а потенциал набухания также снизился примерно до 32%.
1. Введение
Обширные почвы были обнаружены во многих разных местах мира.Термин «экспансивная почва» используется для обозначения почв, которые обладают способностью к усадке и набуханию при изменении содержания воды. Набухающая и расширяющаяся почва была обнаружена во многих провинциях Египта, таких как Сохаг, Асьют и Сина и т. Д. Что касается решения проблемы набухания, теоретический анализ был проведен. Многие научные исследования применяли различные материалы для стабилизации экспансивной почвы в различных условиях. Thomas et al. Использовали известь для определения эффективности гашеной извести и портландцемента на трех техасских глинах.Они изучали множество переменных, чтобы оценить удвоение обработки, измельчения, усилий по уплотнению, условий влажности и диапазона времени отверждения. Обработка известью доказала лучшую устойчивость к повреждениям от влаги после того, как почва очень хорошо уплотнена. Использование цементной обработки дало более высокую прочность на сжатие, чем обработка известью 1 . Hesham, 2013, исследовал это использование одной только цементной пыли (CKD) и добавления цемента к цементной пыли, чтобы уменьшить набухание и улучшить их геотехнические свойства.Было исследовано множество образцов обширных почв из квартала Эль-Каусер в провинции Сохге. Сделан вывод, что добавление цементной пыли и цементной пыли с известью привело к снижению максимальной сухой плотности и увеличению оптимального содержания воды. Кроме того, были увеличены значения прочности на неограниченное сжатие при использовании цементной пыли и цементной пыли с известью при времени выдержки 7 дней. Значения дополнительных ультразвуковых продольных (Vp) и сдвиговых (Vs) скоростей также были увеличены за счет добавления цементной пыли и цементной пыли с известью при времени отверждения 7 дней.Увеличение времени отверждения с 7 до 28 дней привело к увеличению как прочности на неограниченное сжатие, так и значений скорости ультразвука. Процент свободного набухания исследуемой почвы после обработки снизился с 80,0% до 0,0% 2 . Bayat et al., Добавили два типа стабилизированного материала для набухания почвы (цемент / известь) для исследования механических свойств. Они пришли к выводу, что при добавлении извести или цемента улучшилось положительное действие некоторых свойств, таких как индекс пластичности, содержание влаги и максимальный сухой удельный вес.Кроме того, добавление цемента к образцу привело к увеличению прочности на неограниченное сжатие (UCS) для этих образцов. Они определили взаимосвязь между модулем (E 50 ) и прочностью на одноосное сжатие, временем обработки и содержанием добавки (цемента или извести) 3 . Hussein et al., 2018 изучили и исследовали глинистые почвы в Ираке, и они обнаружили, что около 35% мягкой глины вызывает множество проблем для инженеров-строителей и геологов во время выполнения строительных работ.На протяжении всего исследования основное внимание уделялось почве, стабилизированной с помощью золы из опилок с разным процентным содержанием; 0, 2,4,6,8 и 10% от веса сухих образцов. Они установили, что смесь опилок улучшает характеристики почвы; снижение удельного веса, максимальной плотности в сухом состоянии и коэффициента сжатия, 4 . Ali et al., 2017 изучили поведение почвы в зависимости от добавления вяжущих веществ, таких как известь, цемент и других побочных продуктов, таких как летучая зола и шлак. Обработка набухающей почвы является проблемой для проектировщика, строящего планы инфраструктуры на глинистых месторождениях, которые улучшают геотехнические свойства.Это исследование касалось некоторых фундаментальных и успешных улучшений почвы, используемых в области гражданского строительства 5 . Бангладеш страдает от большой проблемы золы, образующейся при сгорании, которая поступает из байпаса при производстве электроэнергии. Зола остатков сгорания использовалась в качестве стабилизатора для улучшения механических свойств набухающих грунтов. Они добавляли различное процентное содержание древесной золы (0, 5, 7,5, 10 и 12,5)% по весу образцов, которые содержат 30% CaO, для улучшения механических свойств, таких как прочность на неограниченное сжатие (UCS), параметры прочности на сдвиг, удобоукладываемость, характеристики уплотнения и сжимаемости.результат теста, означающий, что почву можно сделать легче с увеличением содержания влаги, прочности и снижения сжимаемости за счет добавления зольности 6 . Sun et. al. В 2018 году расширяющийся грунт был улучшен путем добавления опилок, были изучены многие механические свойства прочности на неограниченное сжатие, характеристики прочности на сдвиг и циклическое смачивание стабилизированного грунта. Они упомянули, что оптимальное количество опилок составляет 7 штук.5%. Они рекомендовали улучшить почву путем добавления опилок, чтобы как потенциал набухания, так и давление набухания уменьшались с увеличением количества опилок. Кроме того, некоторые механические свойства, улучшенные в соответствии с увеличением опилок плитки, достигают 7,5%, такие как UCS, прочность на сдвиг, когезия и трение. Добавление опилок может эффективно снизить влияние циклов сушки и смачивания на изменение объема и параметры прочности почвы на сдвиг 7 .Abdullah et al., 2017, они использовали цементную пыль в качестве побочного продукта для улучшения почвы сабхи. Улучшение почв производилось не только механическими, но и химическими методами. x Обработка почвы путем добавления химической стабилизации для улучшения инженерных свойств обработанной почвы x. Они пытаются найти процент цементной пыли для улучшения почвы сабха, образцы были предоставлены с 2% цемента и 10%, 20% или 30% CKD и испытаны для определения их прочности на неограниченное сжатие (UCS), пропитанного Калифорнийского коэффициента несущей способности. (CBR) и долговечность.Они использовали передовые методы, такие как сканирующий электронный микроскоп (SEM), энергодисперсионный рентгеновский анализ (EDX), изображение в отраженных электронах (BEI) и рентгеноструктурный анализ (XRD). Следует отметить, что грунт сабха, смешанный с 2% цемента и 30% ЦП, может использоваться в качестве материала основания в жестких покрытиях. Внедрение CKD приводит к техническим и экономическим преимуществам 8 .
Одним из наиболее важных материалов, используемых в цементной промышленности, является цементная пыль (CKD), которая увеличивалась на диаграмме, авторы дают обзор, чтобы выяснить экономичные и эффективные способы использования цементной пыли (CKD) в различных областях, таких как почва. стабилизация, тротуары, дороги, стабилизация отходов, сельское хозяйство и т. д.Они сосредоточились на химической реакции между почвой и цементом. Они изучили химические соединения, обнаруженные в почве; кварц, полевой шпат, доломит, кальцит, монтмориллонит, каолинит и т. д. вступают в реакцию с химическими составляющими, содержащимися в различных идентифицированных химических стабилизаторах. Это помогает улучшить и улучшить текстуру, повысить прочность и снизить характеристики набухания различных грунтов. Путем изучения полученных значений были получены идеальные значения при 50% -ном соотношении CKD в общем процентном соотношении 9 .Hussein et al, 2018, согласно геологическим исследованиям и исследованиям в Ираке, особенно в южной части, они обнаружили мягкую глинистую почву около 35%. Таким образом, они изучают слабый грунт, чтобы улучшить его механические свойства, чтобы его можно было использовать в строительстве и инфраструктуре с использованием различных стабилизаторов, таких как зола опилок. Образцы были собраны из мягкой глины для улучшения с использованием опилок (SDA) с различным процентным содержанием; 0, 2, 4, 6, 8 и 10% от сухой массы образца почвы. Стабилизированные почвы с зольностью 4 и 10% дали низкие значения CBR 1.6-1,2%, которые можно использовать как подоснову. SDA можно рассматривать как дешевый и приемлемый стабилизирующий агент в дорожном строительстве для улучшения большинства геотехнических свойств мягкого глинистого грунта 10 . Zhuhai et al, 2017 пытались изменить химические свойства мягких грунтов, используя стабилизаторы или вяжущие вещества, чтобы повысить прочность и жесткость изначально слабых грунтов. Они исследовали механические свойства, набухающие в почве после добавления золы из опилок, измеряли свойства, такие как индексные свойства материнской почвы, пределы Аттерберга, характеристики уплотнения и UCC как материнской почвы, так и почвы, обработанной золой из опилок и известью.X Все пробы были собраны в соответствии с Индийским Кодексом X. Это исследование показало, что известь с опилками в качестве корректирующего материала больше всего обнадеживает. По результатам легко понять, что при небольшом процентном содержании активаторов SDA и промышленные отходы могут быть эффективно использованы для стабилизации грунта. Это может снизить стоимость строительства дорог, особенно в сельских районах развивающихся стран, таких как Индия 11, 12, 13, 14, 15 .
.