состав, арболит своими руками, пропорции смеси на 1 куб, из чего делают арболитобетон, рецепт из соломы и цемента
Арболитовые блоки – это популярный строительный материал, который применяют при строительстве домов, внутренних ограждений, гаражей и прочих построек. Такая востребованность арболитовых блоков связана с тем, что он имеет массу преимуществ, среди которых долговечность, простота укладки и отличные технические свойства.
Состав
При изготовлении арболитовых блоков применяют натуральные и химические компоненты. При их грамотном соединении с соблюдением пропорции можно получить изделие необходимой марочной прочности, которое в последующем можно будет использовать для возведения одноэтажных или двухэтажных построек.
Древесина
Дерево относится к органическим материалам, так что в его клетках содержится вода. Кроме воды, дерево содержит сахар, от которого необходимо избавиться. Процесс изготовления начинается с того, что щепку нужно нарубить.
Для этого используют сырую древесину. Затем она должна побыть рядом с химическими реагентами, чтобы весь сахар покинул ее. Как известно, дерево – это материал, имеющий низкие адгезивные свойства. Если не соблюдать технологии, то это станет причиной разрушения блока непосредственно в руках.
На фото-щепки в арболитовых блоках:
Размер щепки оказывает влияние на количество используемого цемента для получения 1 м3 арболита. Если задействовать щепки из сухой древесины, то фракция получится мелкой. Она будет иметь игольчатую структуру, а это потребует использование большего количества цемента. Щепка игольчатой формы должна присутствовать только в определенном количестве.
На 1 м3 арболита потребуется
Всего на 1м3 арболита необходимо:
- 8-10 кг химических составляющих;
- 250 кг цемента;
- 250 г щепы.
При замесе щепки ее нужно хорошенько смочить, чтобы вся свободная влага не выделялась, а сама щепка была укрыта слоем цемента. Именно он при трамбовки блока сможет соединить щепки между собой.
Сернокислый алюминий
Этот компонент используют при изготовлении арболита, а относится он к химическим составляющим. Его задача – это расщеплять сахара.
На фото – арболитовые блоки с алюминием
При добавлении сернокислого алюминия в смесь удается сократить время, которое требуется для набора прочности. При этом на схватываемость это не влияет.
Хлористый кальций
При использовании его в сочетании с сернокислым алюминием удается побороть всех микроорганизмов в дерево. Еще этот компонент оказывает противогнилостные свойства и не дает возникать очагам внешнего поражение готовых блоков.
На фото- арболитовые блоки с хлористым калием
Если хлористый кальций отсутствует, заменить его может хлористый алюминий.
Жидкое стекло
При помощи этого компонента можно закрыть поры в древесине и избежать проникновения влаги внутрь щепы. Применять жидкое стекло рекомендуется после того, как были устарнены все сахара и есть необходимость в защите от проникновения влаги.
А вот какой зимний клей для газосиликатных блоков самый популярный и чаще всего используемый, рассказывается в данной статье.
Какие блоки для внутренних перегородок самые подходящие, рассказывается в данной статье.
Какие плюсы и минусы дома из газоблока существуют и стоит ли использовать такой строительный материал, рассказывается в данной статье: https://resforbuild.ru/beton/bloki/gazobloki-plyusy-minusy.html
Возможно вам так же будет интересно узнать о том, какие технические характеристики газоблоков существуют.
Известь гашеная
Этот вариант станет отличной заменой первым двум химическим составляющим, если существуют сложность в их приобретении. Гашеная известь имеет уникальные способности выводить сахар и бороться с различными микроорганизмами, которые содержаться в древесине.
Как сделать своими руками
Изготовить арболитовые блоки совершенно несложно своими руками. Для этого не нужно использовать особое оборудование. Главное в этом деле, это четко придерживаться необходимых пропорций.
Рецепт смеси и пропорции
При изготовлении арболита важно строго придерживаться соотношениямежду всеми компонентами.
Расход каждого материала составит:
- соотношение наполнителей 80-90%;
- приблизительный объем цемента в общей смеси – 10-15%;
- объем воды – 60-70%;
- химические составляющие – 2-4%.
Чтобы получить 1 м3 материала, необходимо использовать следующие пропорции: 300 г наполнителей и 400 л воды. При обработке наполнителей применяют известковый раствор.
На видео – как сделать арболитовые блоки своими руками:
youtube.com/embed/jza6h8AeUME?feature=oembed» frameborder=»0″ allow=»accelerometer; autoplay; encrypted-media; gyroscope; picture-in-picture» allowfullscreen=»»/>
Для его приготовления необходимо воспользоваться следующей пропорцией:
- известь – 2,5 кг
- ,вода – 200-300 л на 1 м3 древесной щепы.
Для ускорения процесса затвердевания смеси и улучшения ее свойств применяют указанные выше химические компоненты. Для производства 1 м3 арболита уйдет до 10 кг химических компонентов. Если четко соблюдать пропорции, то состав смеси получается классическим. При смене пропорций вы рискуете получить некачественный строительный продукт.
Как залить блоки
Перед тем как переходить к заливке подготовленного материала, нужно позаботиться про оснащение:
- емкость для замешивания смеси или бетономешалку;
- формы съемного типа;
- лопату;
- сито;
- поддон из металла.
Что касается форм для заливки материала, то их можно сделать своими руками или купить готовый вариант в строительном магазине. Если вы решили выбрать первый способ, то тогда нужно взять доски толщиной до 2 с. Скрепить их по необходимым размерам. С наружной стороны оббить их пленкой.
На видео – дом из арболитовых блоков своими руками:
Процесс заливки сводится к соблюдению следующих действий:
- Очищенный наполнитель отправить в воду. Добавлять жидкое стекло и все перемешать. Для этих целей можно использовать бетономешалку или миксер.
- Для приготовления смеси необходимо взять наполнитель, песок и цемент в пропорции 6:2:1. Во время замешивания не стоит сразу вес компоненты помещать в бетономешалку.
Это приведет к образованию комочков, что в итоге снизит качество готового материала.
- Подготовить формы. Их внутреннюю сторону обработать известковым молоком. Чтобы смесь не прилипала к стенкам, можно отделать их линолеумом.
- Залить приготовленную смесь в форме. Чтобы отсутствовали пузырьки воздуха, стоит после заполнения всю массу взбалтывать, а стенки простукивать.
- Для уплотнения смеси применять трамбовку или вибропресс. Ждать 1 сутки.
На видео – станок для производства арболитовых блоков своими руками:
Формы установить в темное место, накрыть пленкой и ждать примерно 21 день.
А в данной статье можно прочесть про отрицательные отзывы о арболитовых блоках.
Так же будет интересно узнать о том, что лучше газоблок или пеноблок, поможет понять видео из статьи.
А вот что дешевле пеноблок или газоблок и что всё таки лучше использовать, очень подробно рассказывается в данной статье.
Так же будет важно узнать о том, какие размеры бетонных стеновых блоков существуют и как правильно их подобрать. Для этого стоит перейти по ссылке.
А вот какие существуют плюсы и минусы бани из шлакоблока, рассказывается в данном видео.
Арболитовые блоки – это широкоприменяемый строительный материал при взведении домов различного назначения. Изготовить блоки можно самостоятельно, если знать состав материала и пропорции всех компонентов. При четком соблюдении всех правил и рекомендаций можно получить качественные и прочнее арболитовые блоки, ни чем не хуже от тех, которые изготовлены промышленным путем.
Дом из соломы своими руками! | Инструкция по применению!
В последнее время сеть пестрит заголовками об экологическом и не дорогом строительстве. Предлагаются дешевые и экологические материалы – солома, глина, земля и т.д.
Строительство из прессованных соломенных блоков в российских широтах можно сразу отмести. Солома требует сухости и тепла. При таких перепадах температур как у нас – где-то в сердцевине блока будет проходить линия образования росы, а это — появление плесени, муравьев, мышей и всякой нечисти. Горючесть такого дома – 100%.
Делать ванну с антисептиком и противопожарной пропиткой – дело сложное, и трудоемкое. Вы однозначно не успеете построить дом до зимы и облицевать его.
Уже только потому – что солома становится доступной только в августе. Сроки не позволят вам провести все мероприятия, так что как ни расписывают все плюсы этого материала – минусы перевешивают. Одну солому применять нельзя.
А вот если ее измельчить, добавить известь, потом глину, песок и цемент – в общем то, что у нас под рукой — получаем хороший теплый и экологичный строительный материал – арболит или опилкобетон.
Можно формовать из него блоки, можно сделать опалубку и вылить стены. Опалубка при этом может быть не съемная и даже являться отделкой для стен как снаружи, так и внутри.
Например – внутренняя поверхность – ОСП или фанера толщиной 10 мм, а наружная – набираться вагонкой.
Кроме того – заливной арболит – еще и прекрасный пластический материал, если сделать опалубку криволинейную – то он хорошо воспринимает и держит форму. Что из прямоугольных блоков сделать затруднительно. Хорошо оштукатуривается.
Огромный плюс этого материала – его тепло- (0,08 Вт/(м·°C)) и шумоизоляционные качества. Относится к трудногорючим (0,75–1,5) материалам, хорошо режется подручным инструментом, морозоустойчив (от F25 до F50 циклов), но должен быть защищен снаружи от влаги (например, силикатным покрытием или штукатуркой, или вагонкой).
Минусы:
– может впитывать влагу (исправляется введением в раствор силиката), нельзя применять в помещениях без отопления и с постоянной повышенной влажностью.
— низковатые показатели прочности – материал для применения в малоэтажном строительстве. Максимальная высота – 3 этажа.
Но кроме арболита солому еще применяют в самане.
Это смесь из соломы, земли, извести, глины, а также можно добавлять цемент.
Это экологически чистый материал, дышит и создает особенный микроклимат внутри дома. Показатель влажности в таком доме практически постоянный, за счет впитывания саманом влаги. В жаркую погоду – влага отдается внутрь помещения, тем самым избегается высушивание воздуха летом.
Дешевый материал из подручных средств.
Тепло- и звукоизолирующий.
Не горючесть достигается специальными добавками в раствор. Можно добиться практически 100% негорючести.
Недостатки:
— из-за впитывающей влагу способности – материал требует улучшенной гидроизоляции, особенно с наружи.
— подвержен гниению, и порчей грызунами. Требует хорошей антисептической обработки на стадии размешивания раствора.
— после возведения стен и обустройства кровли – требует длительной выстойки и просушивания. Без этого материал не наберет прочность и возможно подгнивание органических наполнителей.
— из-за этого же строительство может вестись ограниченное время – жаркие летние дни.
— нужно следить за достаточным уплотнением материала, иначе линейная усадка может достигать 1/20 части стены.
— толщина стен намного больше чем у стен из арболита. Минимум 600, максимум – 800 мм. (у арболита 30 см толщины по теплоизоляции соответствует теплоизоляции кладки из кирпича толщиной 1,5 м)
— требуется завышенный фундамент, что бы влага с земли не попадала на стены.
— ограничение этажности – 1-2 этажа.
— сложность крепления к стенам.
Дома из самана очень приятны для проживания. Но сначала взвесьте все плюсы, минусы, и материальные возможности вашего кошелька)))
Дом из соломенных блоков имеет невысокую массу и нетребователен к фундаменту. Допустимо использовать небольшой поверхностный ленточный фундамент лежащий на дренированной подушке из гравия. Снаружи фундамент защищается ЭППС от промерзания. Этот способ неприменим на трофе — придется строить свайно-ростверковый фундамент. | Вначале для устройства фундамента дома из соломы в грунте отрывается траншея глубиной полметра и шириной достаточной для укладки соломенных блоков. | |
В траншею укладывается геотекстиль, засыпается небольшой слой щебня и укладывается перфорированная дренажная труба, которая выходит по траншее за пределы фундамента по спаду рельефа местности (в пруд, канаву и т.![]() |
Траншея заполняется щебнем. | |
Поверх траншеи выставлется деревянная опалубка, укладывается арматура (2+2 прута d12) выставляются закладные шпильки для крепления опорных столбов (d18-20) и деревнной обвязки (d12-14) под соломенные блоки. Фундамент заливается бетоном. Следует увлажнять заливку 3 раза в день в течении 3 х дней и накрывать ее полиэтиленом. | После того как фундамент залит, присупаем к устройству полов по грунту. Внутреннее пространство засывпается щебнем и трамбуется. Если вы планируете устройство теплых полов в доме из соломы, то поверх щебня нужно уложить 3-5 см ЭППС. | |
В данном случае пол будет холодным.![]() |
Такой раздел пола на плиты позволяет осуществалять заливку пола не одномоментно, а по этапам без опасений, что бетонный пол дома из соломы треснет в неожиданных местах. Перед домом бурятся скважины и заливаются две опорных сваи для столбов урыльца. Под крыльцо засыпается щебень и отливается тонкая (10 см) разделенная на две части плавающая армированная плита.![]() |
|
Затем плиты пола неравномерно прокрашиваются кислотным красителем 2-3 оттенков коричневой гаммы (Кислотные красители Increte Systems). | Швы между плитами затираются затиркой для плитки (например Mapei) При желании пол лакируется для придания плитам блеска. | |
На шпильки приваривются или привинчиваются U образные стальные опоры под брус стоек. Столбы будущего дома из соломы выставлются с помощью уровня или отвеса по вертикали и прихватываются раскосами. | Поверх опорных столбов дома из соломы монтируются деревянные балки. Монтаж осуществаляется при момощи специальных стальных уголков. | |
Собирается стропильная система, опирающаяся на коньковый брус и не требующая затяжек или раскосов.![]() |
На столбы крыльца устанавливается заранее собранная ферма, усиленная стальными накладками прошитая шпильками и стянутая гайками. | |
Поверх стропил дома из соломы нашивается OSB-3. | Кровля дома из соломы кроется листами профилированного оцинкованного железа. Также поверх ОСБ можно использовать простую наплавляемую кровлю или битумную мягую черепицу. | |
Основа для укладки соломенных блоков в стену: на фундамент кладется слой гидроизоляции, поверх укладывается лист ОСБ, к шпилькам крепится пропианный под давлением антисептиками брус (насечки на нем — это фабричная обработка против трещин — снижающая внутренние напряжения в брусе).![]() |
Столбы закрепляются раскосами из стальной ленты крест накрест. Эта лента и сами столбы снаружи обораживаются гидроизоляционной мембраной. Снаружи набивается (строительными скобами или стальной монтажной лентой с саморезами или гвоздями) стальная оцинкованная сетка, которая создаст опору для соломенных блоков и послужит основой для штукатурки. | |
Начинаем укладывать соломенные блоки. | Блоки из соломы укладываются как кирпичи — с перекрытием вертикальных швов. Соломенные блоки хорошо режутся обыкновенной цепной пилой. | |
Вид стальных раскосов и основы для наличников окон из ОСБ.![]() |
Заполняем соломенными блоками фронтон мансарды. | |
Края блоков у окон и дверей закругляются цепной пилой. Изнутри устанавливается оцинкованная сетка и… | приступаем к шитью стен: длинной иглой и толстой проволоки с отвертием на конце прошиваем блоки и стягиваем синтетической щелочестойкой (лавсановой) веревкой наружные и внутрение сетки. Это предупредит стену от разваливания. Придется сделать много сотен стежков через соломенные блоки. | |
Устанавливаем окна и двери и укрепляем мелок штукатурной сеткой откосы стены из соломенных блоков. | Основу для подоконника в соломенной стене отливаем из цементно-песчаной смеси.![]() |
|
Устанавливаем подоконник на место. | И готвим стену к нанесению цементной (а не глиняной) штукатурки. Затягиваем окна и двери пленкой и тщательно залееваем скотчем. Штукатурку мы будем наносить механическим способом с помощью компрессора и распылителя. | |
Механизирванное нанесение штукатурки. Рекомендуется смесь из песка и белого цемента (из лайм камня). | Вид ошуткатуренной и выровненной поверхности. Тщательного выравнивания штукатурки не требуется — у дома из соломы будет аутентичный деревенский вид. | |
Снаружи дом штукатурится смесью песка и белого цемента — он гораздо более прочен по сравнению с портланд цементом и имеет красивый белый цвет.![]() |
Штукатурка осуществляется в два слоя. Первый черновой слой штукатурки при застывании даст усадку и трещины. Время высыхания — несколько недель. После высахния все трещины и дефекты штукатурки заделываются. | |
Первый слой штукатурки не выравнивают — можно пройтись гребенкой для укладки плитки, чтобы создать рельеф для лучшего сцепления слоев. Каждый слой сушится под полиэтиленом, для предупреждения быстрого высыхания и образования изыточных трещин в штукатурке дома из соломы. | После высыхания первого чернового слоя штукатурки соломенных стен, наносят второй слой штукатурки. Впринципе прижелании после его высхания можно нанести и третий финишный — декоративный слой, например, из белой штукатурки «короед» Кнауф Диамант 260.![]() |
|
Вид стены дома из соломы после чистовой штукатурки. | Для равномерной просушки штукатурки весь дом из соломы оборачивают полиэтиленом. | |
Подшивка софитов вагонкой. | Подшивка софитов крыльца дома из соломы. | |
Пенополистирол фундамента защищают накладным кожухом из гнутого покрытого полимером металла. | Двери и окна дома из соломы обходят наличниками. | |
Потолки и кровлю в доме из соломы подшивают вагонкой.![]() |
Интресный и недорого способ создания напольного покрытия: пол из бумаги. Крафт бумагу разных цветов приклеивают полиуретановым лаком. Вместо бумаги можно использовать кусочки разноцветного шпона. | |
Бумага лакируется в несколько слоев. | И приобретает чудесный декоративный вид после высыхания лака. | |
Обустраиваем интерьер дома из соломы. | Задняя дверь дома из соломы. | |
Получился уютный дом из соломы. | Который радует и в зимнее время,так как прекрасно сохраняет тепло.![]() |
|
Теперь посмотрите как построить дом из земли и сделать аутентичную деревянную кровлю, как сделать летнюю постройку из дров или создать красивый и неприступный дом можно построить из морских контейнеров. | ||
Для дома из соломы можно сделать и соломенную крышу. |
Что такое соломенные блоки? — Дом из соломы своими руками, дневник стройки
Пока собственное строительство идет только в голове, будем разбираться с теорией. Итак, что же такое те самые соломенные блоки, из которых мы собираемся строить дом? Далее описание, схема, фото блоков, пресс-подборщиков и панелей из соломенных блоков…
Готовый соломенный блок имеет прямоугольную форму со стандартной шириной 450 мм, длиной от 900 до 1125 мм и высотой 350 мм. Вес одного прессованного соломенного блока составляет 16-30 кг.
Каждый соломенный блок обычно обвязан-прошит двумя-тремя полипропиленовыми шнурами. В колхозах могут использовать стальную проволоку и натуральное волокно, но в строительной практике их лучше не применять, т.к. проволка подвержена ржавчине, а волокна обладают невысоким пределом прочности и подвержены гниению.
- Солому для строительства лучше брать ржаную либо рисовую.
- Ржаную солому лучше брать озимую: она более высокая, плотная, у нее полный цикл и ее убирают немного раньше.
- Солома для строительства должна быть совершенно сухой, поэтому при сборе и хранении это надо обязательно учитывать.
Подходящие для строительства соломенные блоки следующие:
- Сухие — поэтому каждый блок довольно легкий, его можно поднять рукой.
Проверить на влажность легко: засовываем пальцы внутрь — влажность не должна ощущаться, не чувствуется запах гнили. Ствол и стебель у соломы крепкие и гибкие — просто согните и потяните отдельные стебли соломы, чтобы проверить это. - Хорошо спрессованные — блок мало деформируется, когда мы поднимаем его за шнур, при этом под шнур трудно просунуть больше 2-3 пальцев.
- Примерно одинаковые по размеру.
Схема соломенного блока:
Обновлено.
Решил проверить, сколько весит мой соломенный блок метровой длины. Оказалось, что около 15 кг. Те, что подмокли зимой и не просохли, весили около 20 кг. Так что просто подняв блок, уже можно сделать выводы о его каечстве (хотя бывает, что они тяжелее из-за более плотного прессования, но редко).
Фото соломенного блока:
Пресс-подборщик тюковый, он же киповальная машина, которая делает соломенные блоки:
Киповальщики, прессующие солому в блоки, в последне время в хозяйствах постепенно заменяют на другие, катающие солому в огромные ролы — это получается немного дешевле. Но в Беларуси, например, все еще можно легко найти дешевые готовые прямоугольные соломенные блоки.
Пресс-подборщик рулонный:
Как вариант, покупать можно и круглые ролы, а затем арендовать пресс, раскатать ролы и перекиповать. Но при этом солома обычно сильно мнется, соответственно ухудшаются ее теплоизоляционные свойства.
Панели из соломенных блоков:
Да, у нас таких панелей не найти, но в Европе и США компании, продающие такие готовые панели, уже появились и активно работают…
***
Какие лучше котлы отопления для соломенного дома? Говорят, что можно обойтись менее мощными, чем обычно. Осталось только понять, как сравнивать — уже задумался, ищу потихоньку:) А также локальная канализация интересует — как ее организовать вообще пока не знаю…
Поделиться «Что такое соломенные блоки?»
Код ТН ВЭД 6808000000. Панели, плиты, плитки, блоки и аналогичные изделия из растительных волокон, соломы или стружки, щепы, частиц, опилок или других древесных отходов, агломерированных с цементом, гипсом или прочими минеральными связующими веществами.

|
Позиция ОКПД 2
|
Базовая ставка таможенной пошлины | 14% реш.80 |
Акциз | Не облагается |
НДС | 20% |
Базовая ставка таможенной пошлины | Беспошлинно |
Акциз | Не облагается |
Рассчитать контракт
Особенности товараЗагрузить особенности ИМ Загрузить особенности ЭК
Делаем арболитовые блоки своими руками.
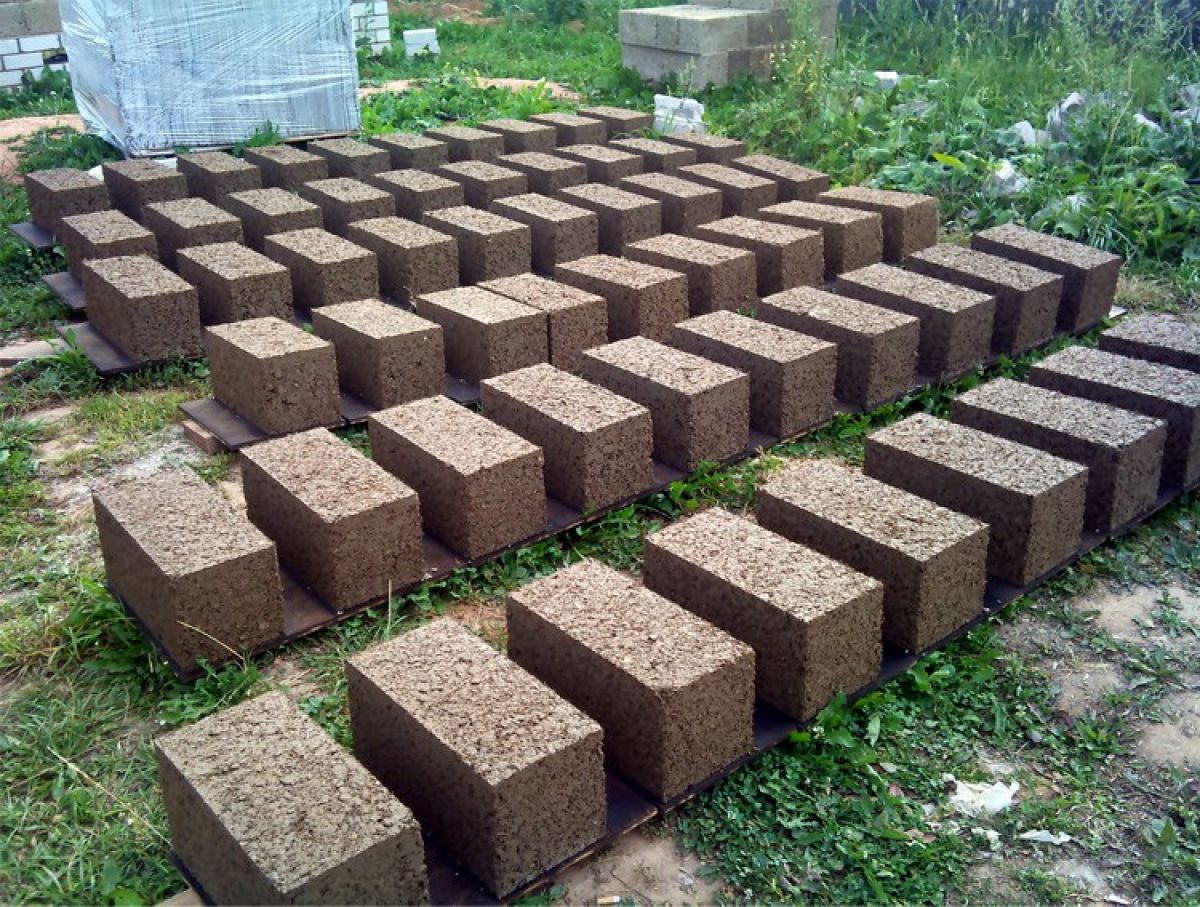
Арболит – это строительные блоки на основе цемента и древесной щепки. Он обладает хорошими характеристиками, которые существенно лучше, чем у опилкобетона. В статье речь пойдет о том, в каких сферах применяются арболитовые блоки, об их достоинствах и недостатках, а также о технологии изготовления.
Содержание:
- Что такое арболитовые блоки
- Преимущества и недостатки арболитовых блоков
- Виды арболитовых блоков
- Технология производства арболитовых блоков
- Производители арболитовых блоков
- Инструмент для арболитовых блоков
- Подготовка щепы для изготовления арболитовых блоков
- Раствор для арболитовых блоков и заливка в формы
- Советы для изготовления арболитовых блоков
Что такое арболитовые блоки
Бетон – это универсальный строительный материал. Его свойства напрямую зависят от наполнителя. Работать с ним легко, благодаря жидкой консистенции. Он заливается в опалубку или специальную форму и приобретает нужные размеры и проектную прочность. Арболит также изготавливается из бетона, но из-за опилок в составе имеет ряд отличий от привычных составов.
- В основе арболитовых блоков лежит древесная щепка. К ее размеру и количеству применяются строгие требования – эти два параметра влияют на качество материала и его марку. Кроме этого, есть производства арболита, которые используют стебли хлопчатника, рисовую солому или кору.
- Вяжущим компонентом выступает цемент марки не ниже М300. Его марка влияет на прочность готового изделия и, следовательно, на его маркировку.
- Для улучшения соединения компонентов смеси, в нее добавляют специальные добавки, обеспечивающие быстрое затвердение и т.д. В большинстве случаев это жидкое стекло, хлористые соли калия или алюминия.
- Изначально древесная щепка и цемент плохо сочетаются, чтобы доиться качественных и равномерных по прочности блоков требуется правильно поставить производство с четким технологическим процессом.
Во время которого важную роль играет продолжительное и тщательное перемешивание всех составляющих.
- Щепка, отбираемая для изготовления должна проходить жесткий контроль. Лучше всего подходят сосна, ель или бук. Немаловажен и характер древесины – поздняя или ранняя заготовка. Размер щепки не должен превышать 10 мм в ширину и 25 мм в длину. Соблюдая эти условия, материал получится с высокой паропроницаемостью, но прочный.
- Для достижения лучших теплоизоляционных показателей. Смесь делается из щепы, вяжущего (цемент с добавками) и воды в пропорции 1:1:1,5. Если нужен более прочный блок для стены с высокой несущей нагрузкой, то пропорции вяжущего соответственно меняются
Арболитовые блоки видео
Преимущества и недостатки арболитовых блоков
Самое главное – это высокие энергоэффективные показатели при строительстве внешних стен дома и невысокая стоимость материала. Но из-за невысокой прочности, допустим только для строительства малоэтажных домов.
Достоинства арболита
- По теплоизоляционным качествам он опережает обычный бетон или кирпич. Его теплопроводность составляет всего 0,08 Вт/(м*С).
- Он обладает лучшими качествами древесины, но в отличие от нее, является пожаробезопасным. Арболит трудновоспламеняемый материал, который во время пожара образует мало дыма.
- При нагревании дома и последующем отключении системы отопления, тепло в помещении будет сохраняться еще долгое время даже при отрицательной температуре снаружи.
- По своим паропроницаемым характеристикам он уступает только древесине. Поэтому внутри помещения будет всегда хороший микроклимат, даже при высокой влажности. Вот почему этот материал выбирают для строительства сауны или бани.
- Несмотря на невысокую прочность (допускается строительство зданий из арболитовых блоков не выше 3 этажей), он хорошо противостоит нагрузкам на растяжении.
Что особенно важно при сезонном пучении грунта, когда дом начинает «ходить». Это свойства материала убережет строение от появления трещин.
- Морозостойкость в зависимости от марки изделия может быть в пределах F25 – F50, Но если зимой чередуются влажность и отрицательная температура, срок годности арболита значительно снижается.
- Этот недорогой материал легко подгонять под нужные размеры, в нем достаточно прочно держится закрепленные предметы. Он станет лучшим вариантом для небольших хозяйственных построек или гаражей.
- Небольшой вес блоков позволяет экономить на фундаменте, так как на последний не будет оказываться высоких нагрузок.
Недостатки арболита
- Невысокая прочность ставит использование арболитовых блоков в узкие рамки. Разрешено только малоэтажное строительство, межкомнатные перегородки или в качестве дополнительной теплоизоляции.
- Долговечность материала зависит от его качества. Помимо специализирующихся крупных заводов, сегодня по стране очень много частных маленьких фирм, которые изготавливают блоки и продают их по более низким ценам.
Но, к несчастью, качество их продукции зачастую остается низким из-за желания максимально удешевить товар и сделать его привлекательным для покупателя.
- Изготовленный по ГОСТу материал имеет стоимость, практически равную пенобетону. Это связано с тем, что при его изготовлении не обойтись без человеческого труда.
- Из-за погрешностей в размерах блоков, во время кладки швы получаются неравномерными. Да и сам материал не отличается красивым внешним видом, поэтому требуется финишная декоративная облицовка фасадов дома.
Виды арболитовых блоков
Всего производят 2 основных вида:
- Конструкционный. Отличается наивысшей плотностью – 500-800 кг/куб.м. В нем пропорционально больше содержание цемента по отношению к щепе. По характеристикам он пригоден для кладки несущих стен и опор. Для большей прочности допускается его армирование стержнями или сеткой.
- Теплоизоляционный. Плотность в пределах 500 кг/куб.м. Предназначается для строительства межкомнатных перегородок, на которые не оказывается нагрузки и в качестве теплоизоляционного слоя.
Арболит может иметь 2 формы:
- В виде блоков. Это уже готовый к использованию материал определенных размеров. Но из-за особенностей материала и его изготовления в размерах могут быть существенные погрешности. Хотя они регламентированы ГОСТом, на деле чаще нестыковки превышают эти параметры. Это надо учитывать еще на стадии проектирования и подсчета требуемого количества материалов. Блоки имеют большой размер, поэтому темпы строительства высокие.
- Монолитный. Его изготавливают непосредственно перед использованием прямо на строительной площадке. После замеса сразу же используют полностью. Такой способ подойдет для создания тонкого теплоизоляционного слоя (когда арболит заливается в несъемную опалубку из пеноплэкса или пенопласта). После заливки придется остановить на работы на время схватывания состава. Это не менее 7 дней.
Технические характеристики арболитовых блоков
- Хоть в арболите и присутствует древесина на равне с бетоном, все же этот класс материала относится именно к строительному камню.
Поэтому его маркируют и дают класс прочности именно как любому другому изделию из бетона.
По форме арболитовые блоки могут быть:
- с U-образным углублением. Удобны для дверных или оконных поемов с перемычками;
- стеновые блоки могут быть крупными, средними или узкими;
- плоты. Но они обязательно имеют слой прочного и плотного бетона, так как характеристики арболита не могут отвечать необходимым, в данном случае, требованиям. Допустимая длина по ГОСТу не превышает 480 см.
Технология производства арболитовых блоков
Сам технологический процесс довольно прост, поэтому для небольших построек, например сарая или курятника, арболитовые блоки моно сделать своими руками. Но из-за медленного отвердения состава, изготовление займет очень много времени, особенно если форм для заливки немного. Особенно при условии, что арболит будет набирать необходимую прочность только при температуре от 12 градусов и выше. Конечно, можно добавить специальные химические компоненты, которые сделают возможным работы и при более низких температурах, но это приведет к удорожанию материала.
Этапы технологического процесса
- Получение деревянных щепок. Для этого подойдут отходы от деревообработки, которые имеются в большом количестве на любой лесопилке. Подходят практически все сорта древесины, кроме лиственницы и тополя. Нельзя забывать и про строгие ограничения в размере, которые являются основополагающими качества арболита. Поэтому изготовители изготавливают щепу самостоятельно при помощи различных дробилок (шредера, молотковой, дисковой или роторно-ножевой).
- Пропорции. Если профессионалы используют специализированные дозаторы, то при самостоятельном изготовлении придется руководствоваться весом или объемом.
- Соединение компонентов. Вначале соединяют щепку и цемент. Сделать это вручную лопатой не получится, допускается только длительный замес в бетономешалке.
- Заливка формы. Готовая смесь по желобу подается в специальные формы из металла или дерева.
- Трамбовка. Это очень ответственный этап, который нельзя упускать. Здесь используется ручной труд, так как сначала смесь надо проколоть, чтобы удалить пузырьки воздуха. Далее утрамбовка производится на вибростоле.
Совет: из-за плохой адгезии цемента с щепой, утрамбовка должна продолжаться не более 20 мин, иначе бетон начнет отделяться от щепы и утрамбовываться на дне.
- Отвердение. Происходит на проветриваемых складах, где нет прямых солнечных лучей. Формы снимаются через сутки. Дальнейшая транспортировка возможна через 2-3 недели.
Производители арболитовых блоков
В каждом городе есть не одно производство арболитовых блоков. Но чаще всего их производят в кустарных условиях и продают через объявления на местных ресурсах. Если поблизости нет крупного завода, то лучше обратиться в компании, которые занимаются строительством арболитовых домов. Как правило, у них всегда есть свое производство, на котором соблюдаются все технологии.
- Наиболее крупное предприятие в России, занимающееся арболитовыми блоками – «ЭкоДрев Продукт». Они поставляют свою продукцию на крупные рынки строительных материалов. В среднем стоимость конструкционного материала составляет 5500 – 6000 руб/м3, а теплоизоляционного 4500 руб/м3.
- Более низкие цены у производителя «Арболит Трейд» — 5300 руб/м3 с доставкой. Они производят не только полнотелый, но и пустотелый кирпич.
- Вологодский завод арболита также предлагает свою продукцию в большинстве регионов. Цена конструкционного блока от 4100 руб/м3.
Покупая большие объемы напрямую от изготовителя, всегда можно договориться о дополнительной скидке.
Инструмент для арболитовых блоков
Специального оборудования для арболитовых блоков не потребуется, достаточно подготовить стандартные инструменты:
- бетономешалка;
- большой металлический поддон;
- форма для заливки арболита;
- разделитель.
Он нужен, если в одной форме планируется залить несколько более маленьких блоков или сделать пустоты;
- большое сито с вибрацией;
- вибростол или молоток;
- вилы, лопата и ведро;
- мастерок.
Чертежи арболитовых блоков
Подготовка щепы для изготовления арболитовых блоков
Делается это двумя методами.
Выдержка на открытом воздухе
- Вначале на любой пилораме приобретается большой объем стружки или щепки подходящей породы древесины. Как правило, ее всегда отдают бесплатно, понадобится только оплатить доставку.
- Если такой возможности нет или материал там низкого качества, тогда при помощи рубильной машины (которую можно взять в аренду) материал подготавливается самостоятельно из пиломатериала.
- Перед использованием, щепу выдерживают на открытом воздухе 2-2,5 мес. За это время опил очищается от присутствующей в нем сахарозы, которая отрицательно влияет на качество готовых блоков (может начаться брожение).
На протяжении этого времени несколько раз щепу тормошат и обрабатывают оксидом кальция, переворачивают. Желается это для того, чтобы воздух попал и в нижний слой. Это предотвратит загнивание материала.
Обработка известняком
- Известняк смешивают с водой до получения 1,5% раствора. Для этого потребуется очень большая емкость. В полученный раствор засыпают щепку из расчета 200 л/1м3 щепы. Перемешивают 2 раза в день на протяжении 4 дней.
- Потом просеивают через крупное сито, чтобы отделить крупный мусор и оставляют просыхать.
Раствор для арболитовых блоков и заливка в формы
- Примерные пропорции для арболитовых блоков выглядят так: 25-30 кг цемента М400/25-30 кг щепы/1 кг жидкого стекла/35-40 л воды.
- Для замеса нужна электрическая бетономешалка. Вначале заливают нужный объем воды, добавляют жидкое стекло и начинают перемешивать в течение нескольких минут, для качественного смешивания.
- Затем засыпается щепа и перемешивается.
Она должна вся намокнуть, чтобы не оставалось сухих участков.
- Далее идет очереди цемента. Если засыпать сразу весь объем, неизбежно образуются комки. Поэтому засыпать надо постепенно в работающую бетономешалку.
- Не останавливая работы бетономешалки, добавляется весь цемент, пока он не образует со щепой однородной массы. Это возможно только в том случае, если щепа вся равномерно намокла.
- Готовую арболитовую смесь раскладывают в разъемные формы или опалубку. Если есть вибростол, то процесс очень упрощается. После заполнения форм только остается дождаться результата и извлечь готовые блоки.
- При самостоятельном изготовлении арболитовых блоков кустарным методом, чаще всего используется ручной труд при уплотнении. Для этого нужно подготовить трамбовалку в виде листа металла по размеру формы с ручкой.
- Форма представляет собой ящик из металла или досок без дна. Устанавливают его на абсолютно ровную поверхность, наливают слой смеси и утрамбовывают. Количество слоев зависит от высоты формы.
Чем их больше, тем более качественный и прочный получится блок. В среднем заливают примерно 5 слоев. Для удаления лишнего воздуха, смесь после каждой заливки протыкают вилами или металлическим прутом.
- Для наивысшей плотности, трамбовать нужно так, чтобы наименьше проявлялась распрессовка. Лучше всего поочередно чередовать сильные и более слабые нажимы.
- По окончанию излишки раствора счищаются мастерком.
- Наилучшей прочности добиваются посредством вибростола. В этом случае трамбовать вручную не надо. После заливки смеси в форму ее прижимают грузом и включают вибрацию на 15-20 мин.
- Дальше происходит момент сушки. Если прочность арболитового раствора высокая, форму допускается снимать сразу с сырых блоков и отправлять их на досушку. Но при более жидкой консистенции делать это нельзя. Так как блок потеряет свою геометрию.
- Технологический процесс подразумевает просушку блоков в течение 2 суток при температуре 60°C. Но в домашних условиях их сушат просто на улице в течение 2-3 недель, предварительно накрыв пленкой.
Производство арболитовых блоков видео
Советы для изготовления арболитовых блоков
- Готовую щепу можно купить у небольших производителей арболитовых блоков.
- Для более легкого извлечения блока из формы, ее внутреннюю часть отделывают гладким материалом, например, линолеумом.
- Для набора прочности блоки должны проходить гидратацию. Первые 10 дней они должны сохнуть под пленкой при температуре 13-15 °C.
- Если арболитовые блоки нужны только для утепления несущих стен, то технологический процесс можно незначительно упростить.
- Можно изготовить сразу отделочные блоки. Для этого на сырой блок прямо в форме наносят шпателем слой шпаклевки и разравнивают.
достоинства и недостатки — Реальное время
Достоинства и недостатки арболита, ГОСТы, секреты выбора
Еще один, доселе не упоминавшийся в проекте «Дом в фокусе», материал, из которых строят дома в нашей стране — арболит (его еще иногда называют древобетоном). Новинкой его назвать сложно — в СССР его делали еще в 1960-х, и ходит даже байка о том, что из него строили столовую на советской полярной станции. Так это было или нет — проверить трудно. Однако арболитовые блоки занимают свое не самое большое, но прочное место на рынке материалов для частного домостроения. Предлагаем познакомиться с ним поближе.
Строго говоря, он тоже считается легким бетоном, но на 80—90% состоит из древесной щепы и химических связующих. Остальные 20—10% — цементное связующее. Вместо измельченной древесины может быть использована и костра растений (льна, конопли), и даже рисовая солома. Словом, подходит любой плотный растительный материал, но арболит для строительства все-таки в основном делают на древесном наполнителе.
Технические условия изготовления этого материала регламентирует ГОСТ Р 54854-2011 В качестве вяжущего материала используются портландцемент (включая быстротвердеющую его разновидность), заполнителем чаще всего выступает деревянная щепа хвойных пород (сосновая, еловая, лиственничная).
В состав арболита обязательно вводятся химические добавки (хлористый кальций, жидкое стекло, известь, сернокислый глинозем). Во-первых, подобные добавки ускоряют твердение, улучшают защиту арматурной стали от коррозии. Во-вторых, они связывают сахара, содержащиеся в природной древесине, и исключают развитие гнилостных процессов внутри материала — минерализуют содержимое блока. Еще один тип добавок — порообразующие (чтобы обеспечить просыхание блоков и их вентилирование). Конструкции из арболита армируются. Для этого используется арматура классов A-I, A-II, A-III небольшого диаметра (до 16 мм).
Методы формирования блоков и плит из арболита могут быть разными: это происходит в металлических формах, материал в них либо послойно укатывается, либо спрессовывается, либо уплотняется на виброплощадках — словом, способов множество.
А еще бывает так называемый монолитный арболит, когда материал смешивается и заливается прямо на строительной площадке в несъемную опалубку. Эта технология относится к довольно экзотичным, зато полностью исключает образование мостиков холода и позволяет реализовывать самые фантастические архитектурные формы. А чтобы избежать формирования мостиков холода в случае использования обычных блоков и плит, строители используют теплоизоляционную кладочную смесь, которая имеет такую же теплопроводность, что и сам арболит.
Арболит, как и многие другие стеновые материалы для строительства дома, может быть разных классов по прочности на сжатие. Для конструкционного арболита он должен быть не ниже B1 (это соответствует плотности 650—750 кг/кв. м). Максимальный класс арболита по прочности на сжатие — В3,5 (800—850 кг/кв. м).
Согласно таблице, приведенной в ГОСТе, для несущих стен из арболита марка по средней плотности должна быть D750—D900, прочность на сжатие — B2. 5 и B3,5. Ненесущие стены могут быть ограничены показателями D500—В600, прочность на сжатие — от В0,75 до B1.5.
Марка арболита по морозостойкости для зданий с влажностью в помещениях от 60 до 75% должна быть не ниже F35 (а лучше — 50).
Влажность арболита, привезенного на площадку, не должна быть больше 25% по массе.
Арболитовые блоки и панели, в соответствии с СН 549-82, предназначены для строительства наружных и внутренних стен для зданий, относительная влажность воздуха в которых будет не выше 75%, без воздействия агрессивных сред. Диапазон систематического воздействия температур должен быть от 50 до -40 градусов по Цельсию.
Таким образом, можно заключить: арболитовые стены вполне подходят для строительства жилого дома в наших широтах. Для этого стены выкладывают в один ряд из блоков размером ориентировочно 500х300х200 мм. Поверхности стен, которые соприкасаются с атмосферной влагой, должны быть надежно защищены от увлажнения и от продувания отделочным слоем. Хорошо подходят для этого, к примеру, теплые штукатурные системы толщиной до 2 см с добавлением перлита.
Как и у любого другого строительного материала, у арболита есть и ряд достоинств, и список недостатков. Начнем с достоинств.
Во-первых, у него прекрасная теплоизоляция. Благодаря содержанию древесной стружки и большому количеству пор, арболит имеет низкую теплопроводность, он хорошо удерживает тепло. Правда, для этого надо, чтоб материал был произведен строго по ГОСТу (см. выше).
Во-вторых, он легкий. Кубометр арболита весит примерно 650 килограммов — примерно как газобетон или сосновый брус. И, как для любого другого легкого материала, это дает серьезную экономию на фундаменте.
Кубометр арболита весит примерно 650 килограммов — примерно как газобетон или сосновый брус, и это дает серьезную экономию на фундаменте.
В-третьих, объем арболитового блока довольно большой — аналогичный примерно 15 стандартным кирпичам. А это существенно ускоряет процесс возведения дома и позволяет сэкономить на рабочей силе. Кроме прочего, с арболитом работать не очень сложно, так что сбиваться с ног в поисках бригады, «заточенной» именно под этот материал, не придется (как, например, в случае газосиликатных блоков).
В-четвертых, геометрию арболитовых блоков можно менять как вам заблагорассудится — материал легко пилить обычной бензопилой. Поговаривают, что справляется с ним даже ножовка. А заселившись в дом из арболита, вы легко сможете забивать гвозди в такие стены.
В-пятых, у арболита довольно высокий коэффициент звукопоглощения. Акустика арболита, по результатам исследования, проведенного в СибГУ им. Решетнева, показала коэффициент звукопоглощения от 0,17 до 0,6 при частотах звука 125—2000 Гц. Например, кирпич при частоте 1000 Гц показывает коэффициент звукопоглощения на уровне 0,04.
В-шестых и в-седьмых, несмотря на то, что арболит почти полностью состоит из дерева, он лишен его главных недостатков — горючести и биоразлагаемости. Чтоб поджечь арболитовую стену, надо серьезно постараться, у нее низкий класс горючести — Г1. За час пожара арболит обугливается не более, чем на 30 мм. А благодаря содержанию в составе минерализующих добавок и цемента, арболитовая стена совершенно не привлекательна в качестве продукта питания ни для макрофауны (жучков или мышей), ни для микроорганизмов (гнили на блоках вы не увидите).
Геометрию арболитовых блоков можно менять как вам заблагорассудится — материал легко пилить обычной бензопилой. Фото: z500proekty.ruНедостатки арболитаКак часто бывает, недостатками часто обращаются явные достоинства материала.
Во-первых, вспомним легкое разрезание арболитовых блоков. Дом из такого материала будет не самым взломостойким. По форумам ходит страшилка о том, как однажды воры, не справившись с взломом двери, просто вырезали дверь из арболитовой стены и спокойно сделали свои злоумышленные дела. Правда, форумчане умалчивают о том, как же соседи не услышали звуков разделки стенового материала — все-таки абсолютно тихо это сделать не получится.
Во-вторых, стена из арболита может оказаться плохо оштукатуриваемой. Это может случиться из-за того, что железная форма для производства блоков обрабатывается машинным маслом, и его остатки могут остаться на поверхности. К такой поверхности штукатурный состав вы не прикрепите никакими уговорами. Придется воспользоваться штукатурной сеткой, а это повлечет за собой дополнительные расходы.
Совет: чтобы избежать такого казуса, при покупке блоков проверьте их на «измазанность» машинным маслом. Просто проведите пальцем по поверхности нескольких выборочных блоков. Если на пальце остается черный след — значит, вам грозит покупка километров штукатурной сетки.
В-третьих, у арболита низкая марка прочности. Поэтому несущие стены из него можно строить только на 2—3 этажа (правда, нам для нашего частного дома больше и не надо). А еще дому обязательно понадобится равномерное распределение нагрузки по всему периметру стен. Для этого специалисты советуют обустройство монолитного армирующего пояса по этому периметру.
В-четвертых, для защиты от влаги наружные поверхности арболитовых блоков надо обязательно штукатурить, причем выбирая паропроницаемые составы.
В-пятых, не стоит строить неутепленный дом из арболита там, где постоянно дует сильный ветер (в зонах турбулентности, на высоких берегах и обрывах). Дело в том, что в силу высокой воздухопроницаемости стены будут ощутимо сквозить. Штукатуркой можно отчасти нивелировать этот недостаток, но для более серьезной защиты от ветра придется дополнительно утеплять стену. Причем обязательно хорошо продумать паропроницаемость — иначе см. п. «в-четвертых». Вообще, все варианты отделки арболитовых стен должны быть «дышащими». Так что, например, с виниловыми обоями лучше не экспериментировать.
И в-шестых, найти качественное производство арболитовых блоков и плит, где выдерживаются все ГОСТы, не так легко. А вот нарваться на гаражное производство — проще простого. На рынке этого материала не очень много (и стоит он дороже, чем тот же газобетон) по одной простой причине: его производство во многом «завязано» на ручном труде, автоматизировать его сложно. Поэтому, если вы решили строить дом из арболита, нужно будет как следует прошерстить рынок и найти производство, которое действительно заслуживает доверия.
Людмила Губаева
Недвижимость ТатарстанLowimpact.org
Меня часто просят помочь с дизайном других людей, но один из моих принципов — никогда не проектировать из цемента. Не все знают это обо мне, и недавно меня спросили, каков мой общий опыт работы со стволовыми стенами из бетона (цемент плюс заполнитель), что нужно учитывать или возможные проблемы при строительстве на них соломенных тюков. Далее мой клиент сказал: «Большинство производителей соломенных тюков или компаний по строительству тюков соломы, которые я видел в Интернете, используют бетон для своих стволовых стен!? Значит, это работает?»
Хммм.То, что большинство людей что-то делают, не означает, что это работает или это хорошая идея. Тем не менее, это подчеркивает одну из основных проблем с цементом: проблемы, которые он вызывает, не видны или очевидны сразу, на самом деле они могут проявиться через много лет. Я сам был обучен использованию современных материалов и методов в рамках своего обучения в строительной отрасли, и я думал, как и большинство людей, что фундаменты должны быть сделаны из цемента, а кирпичи должны быть уложены с помощью цементного раствора.Так что я знаю, как класть цементные полы и строить кирпичные и каменные стены, и многое сделал в свое время — но все, к счастью, теперь уже давно.
Когда я начал узнавать о природных материалах в 1990-х годах, а также о строительстве из соломенных тюков, я изучал известковые и глиняные штукатурки, а также строительство из самана. У меня тоже был интерес к старым домам, и я понял, что все наши старые дома (построенные до 1900 года) построены полностью из натуральных материалов, да и все старые дома во всем мире тоже. Это показывает, насколько невероятно, что кто-то может думать, что натуральные материалы недолговечны, но мы все склонны думать, что то, что все делают сейчас, лучше, чем то, что люди делали в прошлом.Существует распространенное заблуждение, что цемент заменил известь и глину, потому что он лучше справляется со своей задачей, но я отвлекся…
Основная проблема с цементом и бетоном заключается в том, что они притягивают или «впитывают» воду. Если вы поместите бетонный блок в воду на дюйм и оставите его на пару дней, весь блок промокнет. Если вы поместите кусок дерева (или тюк соломы) в воду на дюйм, они оба станут мокрыми до уровня чуть выше дюйма, но не более. Они не впитывают воду. Таким образом, использование цемента для строительных растворов и штукатурок означает, что во время дождя цемент переносит влагу через себя к тому, что находится за ним. Обычно, когда дождь прекращается, большая часть этого снова высыхает, но не все, и не во влажных условиях или там, где большую часть времени присутствует влага. Вот почему цемент никогда не следует использовать в естественных постройках.
В цементных фундаментах цемент находится в контакте с влажной землей, поэтому стандартной практикой является защита здания выше от влажного цемента с помощью гидроизоляционного слоя. Что еще более важно, внешние стены всегда содержат определенное количество влаги из-за внешнего дождя и внутреннего присутствия (горячий душ, приготовление пищи и т. д.).В зданиях, построенных из цементных растворов, эта влажность увеличивается, так как дождь проникает через растворные швы. Эта влага всегда движется вниз из-за гравитации и заканчивается у основания стены. Опять же, стандартной практикой является использование влагонепроницаемого слоя полого поддона, чтобы направить внутреннюю влагу наружу здания. Основная причина, по которой люди не осознают, что цемент на самом деле увеличивает влажность здания, заключается в том, что движение влаги происходит очень медленно. Может пройти 30 или 40 лет, прежде чем начнут проявляться проблемы, которые примут форму влаги, скопившейся у основания стены, что в конечном итоге проявится как проблемы с влажностью внутри.
Когда эти проблемы из-за использования цемента впервые начали проявляться, в промышленности заявили, что это вызвано повышением влажности, и была изобретена химическая инъекция домов против сырости. На самом деле теперь мы знаем, что поднимающаяся влажность встречается очень редко, и большинство проблем с сыростью вызвано другими причинами. У Общества защиты древних зданий (SPAB) есть отличные исследования и информация по этому вопросу.См. http://www.spab.org.uk/advice/technical-qas/technical-qa-20-rising-damp/
. Еще одна начавшаяся тенденция заключалась в том, чтобы перекрашивать дома из цемента, которые были построены с использованием извести, и ремонтировать старые известковые штукатурки с помощью цементных штукатурок. Никто не знал, что это была грубая ошибка в течение многих лет, потому что проблемы, которые она вызвала, проявлялись очень долго. Только после впечатляющего обрушения нескольких глинобитных зданий, которые были заштукатурены цементом, мы начали понимать, что цемент повреждает наши здания, особенно старые, построенные из природных материалов.Опять же, печальный показатель того, почему цемент никогда не следует использовать в естественных постройках. Сегодня по этой причине организация English Heritage запретила использование цемента в зданиях наследия.
Многие современные здания страдают от проблем с конденсацией, и это является прямым результатом использования цементных блоков, растворов и гипсокартона, хотя это также связано с другим их свойством, а именно непроницаемостью, они препятствуют прохождению пара. Эта непроницаемость является еще одной причиной, по которой цемент никогда не следует использовать в естественных постройках.С другой стороны, известь и глина фактически регулируют влажность и могут удерживать избыточную влагу внутри себя, не становясь «мокрыми», и высвобождать ее при снижении уровня влажности — они гигроскопичны. Это также помогает поддерживать здоровое качество воздуха в помещении. Известь, используемая в качестве раствора или штукатурки снаружи, поглощает воду, когда идет дождь, и, когда она становится насыщенной, это фактически предотвращает проникновение влаги через нее и, таким образом, защищает здание позади нее. Когда дождь прекращается, эта влага выбрасывается в атмосферу.
Итак, я возвращаюсь к вопросу моего клиента. Тот факт, что так много людей используют цемент, не означает, что он «работает»! Это просто означает отсутствие осознания. Большинство людей не проектируют жизнь на 200 лет, как мы. Мы видим, что дома, построенные в 1970-х годах (из цемента), сносят и признают непригодными для проживания, в то время как дома, построенные в викторианскую эпоху или ранее (цемент стал широко использоваться в строительстве после Первой мировой войны), разрушаются. отремонтирован (о нет, часто с цементом) и продолжает служить хорошо… до тех пор, пока последствия новой гипсовой штукатурки или цемента не начнут вызывать проблемы с влажностью или конденсацией.
Наконец, есть много способов построить фундамент, не требующий цемента. Все наши старые дома имеют фундаменты без цемента — как же иначе? Я разработал несколько типов фундаментов, которые не требуют цемента, они доступны для использования на нашем сайте в разделе «Бесплатная информация». Все эти проекты являются законными, одобрены планировщиками и соответствуют действующим строительным нормам.
Всем рекомендую начать разбираться в чудесах извести и глины.Я ожидаю, что если вы, как и я, захотите стать Строителем Природы!
Если вам интересно узнать больше о цементе и причинах проблем, с которыми он сталкивается, вот три сообщения в блоге, которые я бы порекомендовал:
http://surveyingproperty.blogspot.co.uk/2014/11/concrete-part-1-understanding-basics.html#.VGyGQvmsWxI
http://surveyingproperty.blogspot.co.uk/2014/11/concrete-part-2-carbonation.html#.VGyGWfmsWxI
http://surveyingproperty.blogspot.co.uk/2014/11/cohttp://surveyingproperty. blogspot.co.uk/2014/11/concrete-part-3-understanding-basics.html#.VGyGb_msWxIncrete-part-3-understanding-basics.html#.VGyGb_msWxI
Спасибо Оливеру из Naturalhomes.org за изображение.
Хотите узнать больше о строительстве из соломенных тюков от Барбары Джонс?
Барбара Джонс — звезда нашего онлайн-курса по строительству из соломенных тюков. Курс содержит ряд документов и видео, охватывающих все аспекты строительства из соломенных тюков, от фундамента, стен и крыш до инструментов, внутренней отделки и штукатурки, с множеством советов и внутренней информации.Пожизненный доступ всего за 30 фунтов стерлингов. На сегодняшний день это наш самый популярный онлайн-курс.
%PDF-1.4 % 1 0 объект >поток 2022-01-07T12:02:08-08:002019-03-26T21:40:49+07:002022-01-07T12:02:08-08:00Acrobat PDFMaker 10.0 для Worduuid:f4653c70-3372-4548-a08a- 752405d417e2uuid:f0f6cb75-ab45-4816-96de-8c45e11a73cduuid:f4653c70-3372-4548-a08a-752405d417e2

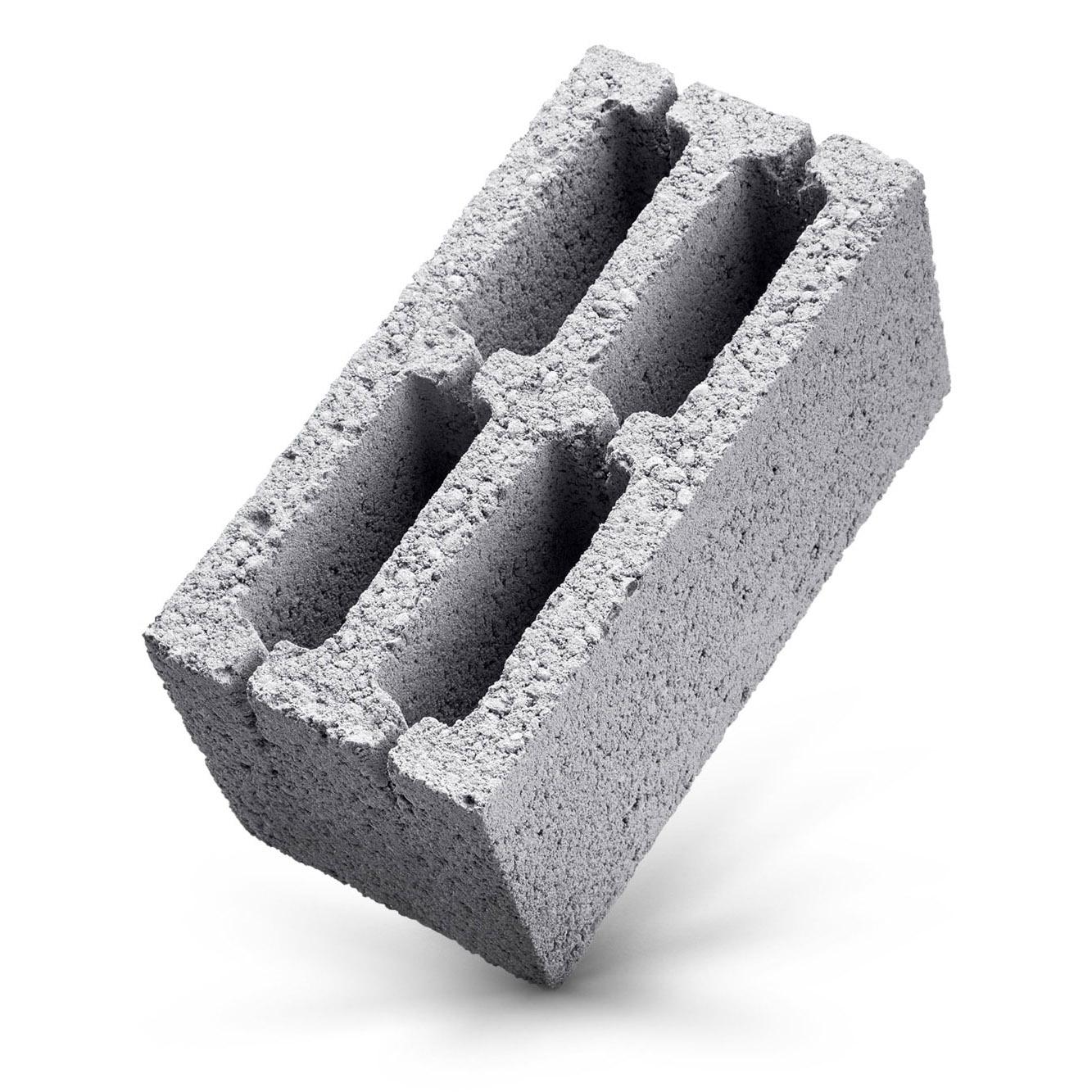
Механическая, огнестойкая и экономическая оценка.
Австралийский журнал фундаментальных и прикладных наук, 5(2): 27-33, 2011 г. Аллам, Гихан Л. Гарас, Хала Г. Эль Кади
Национальный исследовательский центр, Департамент гражданского строительства, Докки, Каир, Египет
Резюме: В Египте сжигание рисовой соломы приводит к выбросу большого количества загрязнителей воздуха, вызывая
серьезные экологические проблемы.В этой статье рассматривается переработка измельченной рисовой соломы для производства легких цементных кирпичей весом
. Были проведены различные тесты для оценки кирпича из рисовой соломы (R-кирпич) с
предложенными пропорциями смеси. Его вес на 25% легче, чем у традиционных. Испытания на косвенное воздействие огня
проводились в соответствии со стандартами ASTM 119-00A для сравнения поведения R-кирпичей при воздействии огня на
цементных кирпичей. Были проведены тесты на выдержку в течение одного и двух часов,
, при температуре от 300 до 800°C. Оба типа кирпичей не претерпели существенной потери прочности на сжатие при воздействии 300°C в течение 1 часа. Сообщалось о потере 70% прочности на сжатие
цементного кирпича из рисовой соломы при воздействии 800oC в течение 1 часа и 80% при воздействии огня в течение 2 часов
. Экономическое исследование показало, что стоимость исследуемых R-кирпичей на 25 % меньше, чем
стандартных цементных кирпичей. Был сделан вывод, что предлагаемые R-кирпичи представляют собой экономичный, легкий кирпич весом
с конкурирующими теплоизоляционными свойствами, при сохранении соответствующих механических свойств
и огнестойкости.
Ключевые слова: Композиты, Рубленая рисовая солома, Цементные кирпичи, Переработка, Испытания на огнестойкость около 4,0 млн тонн соломы в год. Способы утилизации остатков соломы и стерни
, остающихся на полях после сбора урожая, включают либо сжигание, либо прессование. Хотя некоторые ограниченные виды использования рисовой соломы
, такие как корм для животных или производство бумаги, сохраняются, тем не менее, сжигание, основной метод утилизации большинства остатков рисовой соломы
, является эффективным, действенным и дешевым, даже после того, как он был поэтапно прекращен в Египетский закон
Окружающая среда № 4 -1994 [8]. В результате большинство фермеров, как правило, сжигают солому на открытых полях, увеличивая загрязнение воздуха и вызывая серьезные проблемы со здоровьем человека из-за выбросов угарного газа. [2]
С 1950-х годов Египет принял несколько стратегий недорогого жилья, чтобы компенсировать
растущий спрос на жилье. В настоящее время подавляющее большинство жилых единиц представляют собой железобетонные конструкции с
заполнением либо кирпичом, либо цементными блоками, которые заимствованы из материалов из других климатических зон и стран с
различными видами природных ресурсов.Одним из наиболее заброшенных материалов в Египте являются целлюлозные недревесные
волокнистые материалы, такие как рисовая солома. Вместо того, чтобы сжигать солому, ее переработка со смесью цемента образует
устойчивый недорогой строительный материал, который также снижает загрязнение атмосферы. В дополнение к этим преимуществам,
полученный композитный кирпич из рисовой соломы может действовать как теплоизолятор, который можно использовать в строительстве для
неприятной египетской погоды. Использование теплоизоляции помогает снизить затраты на электроэнергию, одновременно повышая температуру в помещении.[2]
Akmal (2006) провел предварительное простое лабораторное исследование по подготовке и изучению цементных кирпичей из рисовой соломы
для использования в качестве наполнителя в традиционной технике каркасного строительства.[6]
2. Значение исследования и постановка проблемы:
Переработка рисовой соломы для использования в строительном процессе является одной из настоятельно рекомендуемых областей исследований, которые
могут привести к отличным решениям основных экологических проблем, возникающих в результате сжигания этого остатка.Доступна редкая информация
о влиянии добавления такого материала на различные элементы конструкции.
В этой статье исследуется влияние добавления рисовой соломы в цементные кирпичи, используемые в строительстве.
Целью данного исследования является оценка влияния добавления рубленой рисовой соломы на механические свойства
и огнестойкость цементных кирпичей. Было проведено исследование оптимизации между различными пропорциями смеси
и соответствующей прочностью на сжатие.Тепловые свойства предлагаемых кирпичей изучены. запрошенный не найден на нашем сайте
IRJET приглашает статьи из различных технических и научных дисциплин для Тома 9 Выпуск 1 (январь 2022 г.) …
Browse Papers
IRJET Получил «Импакт-фактор научного журнала: 7,529» за 2020 год.
Подтвердить здесь
IRJET приглашает статьи из различных технических и научных дисциплин для тома 9, выпуск 1 (январь 2022 г.)..
Browse Papers
IRJET Получил «Импакт-фактор научного журнала: 7,529» за 2020 год.
Подтвердить здесь
IRJET приглашает статьи из различных технических и научных дисциплин для тома 9, выпуск 1 (январь 2022 г.)..
Browse Papers
IRJET Получил «Импакт-фактор научного журнала: 7,529» за 2020 год.
Подтвердить здесь
IRJET приглашает статьи из различных технических и научных дисциплин для тома 9, выпуск 1 (январь 2022 г. )..
Browse Papers
IRJET Получил «Импакт-фактор научного журнала: 7,529» за 2020 год.
Подтвердить здесь
IRJET приглашает статьи из различных технических и научных дисциплин для тома 9, выпуск 1 (январь 2022 г.)..
Browse Papers
IRJET Получил «Импакт-фактор научного журнала: 7,529» за 2020 год.
Подтвердить здесь
IRJET приглашает статьи из различных технических и научных дисциплин для тома 9, выпуск 1 (январь 2022 г.)..
Browse Papers
IRJET Получил «Импакт-фактор научного журнала: 7,529» за 2020 год.
Подтвердить здесь
IRJET приглашает статьи из различных технических и научных дисциплин для тома 9, выпуск 1 (январь 2022 г.)..
Browse Papers
IRJET Получил «Импакт-фактор научного журнала: 7,529» за 2020 год.
Подтвердить здесь
IRJET приглашает статьи из различных технических и научных дисциплин для тома 9, выпуск 1 (январь 2022 г. )..
Browse Papers
IRJET Получил «Импакт-фактор научного журнала: 7,529» за 2020 год.
Подтвердить здесь
Гидроизоляция Альтернативное строительство Глыба, солома, щепа
Растительные материалы, такие как волокна из соломы, использовались в качестве строительных материалов на протяжении тысячелетий. Только после того, как были разработаны механические методы сбора, сжатия и прессования соломы (начиная с конца 1850-х годов, но запатентованные в 1910 году), стало возможным использовать солому в качестве основного строительного блока наружных стен.Джон Страубе, написавший в 2002 году статью «Влажностные свойства гипса и штукатурки для зданий из соломенных тюков», говорит, что было короткое время, когда дома из прессованных соломенных тюков были популярны в Небраске, но они вышли из моды почти на 50 лет. В последние десятилетия эти и другие альтернативные системы завоевали популярность.
Альтернативные «натуральные» конструкции стен, такие как тюки соломы или саман, аналогичны традиционным стенам с деревянным каркасом в том смысле, что они не должны располагаться ниже уровня земли. Для них требуется водонепроницаемый фундамент и водонепроницаемая крыша, отводящая влагу.Однако, в отличие от традиционных стен, эти альтернативные конструкции не являются водонепроницаемыми.
Соломенный тюк на конце прислоняется к внутренней части фанерной обшивки здания Махония. Вертикальная рама находится на 24-дюймовых центрах, что позволяло бригаде проталкивать полные трехрядные тюки (шириной около 23 дюймов) между стойками. Снаружи не скажешь, что здание Mahonia построено из тюков соломы.
Любые стены из любого строительного материала растительного происхождения, включая дерево, нуждаются в пароизоляции, чтобы избежать внутренней конденсации.Утепленные бетонные формы (блоки ICF) не пропускают воду через свои сборки. «Жидкая вода и водяной пар с трудом проходят через стены такого типа, поэтому их часто можно найти в приложениях ниже уровня земли, а когда они используются для всего дома, конструкция ОВиК обычно требует другого способа решения проблемы. с внутренним водяным паром», — объясняет Джим Рейланд, владелец компании Many Hands Builders в Джексонвилле, штат Орегон. Reiland является генеральным подрядчиком, специализирующимся на проектировании систем сбора дождевой воды, штукатурке из земли и извести, а также строительстве тюков соломы.Рейланд является членом Калифорнийской ассоциации строительства из соломы (CASBA), а также соавтором и главным редактором книги «Детали строительства из соломенных тюков: иллюстрированное руководство по проектированию и строительству». Он живет в доме с подвалом ICF и стенами первого этажа из тюков соломы. В своей работе он часто строил дома со стволовыми стенами ICF, которые поддерживают стены из соломенных тюков.
«Альтернативные стеновые системы, такие как глыба, тюки соломы и легкая солома-глина, по своей конструкции не являются водонепроницаемыми, как строители делают гидроизоляцией ICF или блоки из древесно-стружечных блоков или монолитные бетонные стены», — говорит он.Стеновые конструкции, изготовленные из натуральных материалов, таких как солома, должны быть паропроницаемыми. Отделка этих конструкций с обеих сторон какой-либо паропроницаемой штукатуркой обеспечивает защитное покрытие, обеспечивает паропроницаемость и повышает огнестойкость — в соответствии с Кодексом IRC 2018 г. стоимость указана на веб-сайте CASBA, www.strawbuilding.org, сборка стены из тюков соломы, оштукатуренных известью, имеет 2-часовую огнестойкость, а сборка, оштукатуренная глиной, имеет 1-часовой рейтинг, оба из которых выгодно отличаются от традиционного каркаса и изоляции. стеновые системы, хотя и не такие высокие, как здания с бетонными стенами.
«Я использую изоляцию из жесткого пенопласта ниже уровня земли», — говорит он. «Каждое здание, над которым я когда-либо работал, имеет бетонный фундамент. Почти все мы используем какую-либо мембрану, которую можно отслаивать и приклеивать, или краску для гидроизоляции фундамента или уязвимых мест вокруг окон и дверей. Просто есть некоторые вещи, в которых «натуральные» материалы не очень хороши — намокание и невозможность высохнуть — одна из них».
Любая влага в стенах из тюков соломы в то время, когда тюки складываются и оштукатуриваются, должна иметь возможность выйти или высохнуть из стен, объясняет Рейланд, и если содержание влаги в стене поднимается значительно выше 20%, она становится подходящей средой обитания для плесени.
Гидроизоляционный блок из щепы
Faswall представляет собой композитный цемент ICCF, состоящий из 85% минерализованной древесины и 15% цемента. Эти блоки сложены, как ICF, с размещенной арматурой, дверными и оконными проемами, а также добавленными инженерными и электрическими проводами. Затем в ядро заливают бетон. Хотя он похож на блок ICF, стратегия гидроизоляции больше похожа на альтернативную строительную конструкцию. На фундаменте Faswall рекомендует использовать дренажный мат с углублениями поверх вторичной дренажной плоскости поверх композита Faswall.Эта вторичная дренажная плоскость может представлять собой грунтовку с наносимой краской гидроизоляцией или MasterSeal, герметизирующий слой на основе битумной эмульсии с минеральным наполнителем. «Паржное покрытие похоже на штукатурку базового слоя, с гидроизоляционной краской сверху, а затем с двойным дублирующим трехмерным дренажным матом поверх», — говорит Джозеф Беккер, руководитель отдела продаж/техники ShelterWorks/Faswall и активный участник. Гильдии экостроительства Северо-Запада. «Это довольно надежный метод, и некоторые люди возражают, но для подвалов ниже уровня земли и влажной среды для нас важна система с двойным резервированием в такой критической ситуации.
Самоклеящиеся гидроизоляционные мембраны под плиты подоконника для стен из тюков соломы на фальшполе.
Для пользователей Faswall компания Becker рекомендует двойное резервирование, «вентилируемый экран от дождя» и сайдинг или штукатурку. «Вентилируемый экран от дождя» включает в себя вентилируемый воздушный зазор между WRB (атмосферостойким барьером) и сайдингом. Этот вентилируемый воздушный зазор продлевает срок службы сайдинга и связанной с ним морилки/краски, позволяя влаге, которая попадает за сайдинг, стекать или выходить наружу. Это может быть от 1/16 дюйма до 1/2 или 3/4 дюйма.Воздушный зазор и мембрана под сайдингом становятся все более распространенными, особенно во влажных, ненастных и дождливых условиях, таких как тихоокеанский северо-запад.
«Гидроизоляция высшего класса должна быть водонепроницаемой, воздухонепроницаемой и паропроницаемой», — говорит Беккер. «Воздушный зазор между герметичным WRB и сайдингом делает его более паропроницаемым, потому что сайдинг не прижимается к нему и не покрывается четырьмя слоями краски».
Штукатурка выше уровня грунта — очень распространенная отделка Faswall, но она обеспечивает только одну дренажную плоскость по сравнению с двойным дренажом сайдинга и WRB, объясняет Беккер.«Если это действительно важно, двойное резервирование — это хорошо», — говорит он. «Если это пустыня Айдахо или там, где действительно сухо, двойная избыточная гидроизоляция сайдинга не так важна, как одиночный гидроизоляционный слой, такой как штукатурка».
Хороший дизайн стены
Хороший дизайн стены этих альтернативных сборок включает в себя правильное размещение, соответствующие свесы крыши и внимание к деталям на окнах и дверях. «Внешние штукатурки чрезвычайно эффективны для защиты от воды, вызванной дождем, вызванным ветром», — говорит Рейланд. «Однако большинство штукатурок, наносимых непосредственно на стену из соломенных тюков, считаются резервуарными системами. По своей конструкции облицовка резервуара поглощает влагу от дождя или брызг, гонимых ветром, а затем отдает ее, когда погода становится сухой и солнечной».
В дождливом климате или на сильно открытых строительных площадках стены из соломенных тюков значительно выигрывают, если добавить сайдинг в качестве еще одного внешнего слоя защиты. Рейланд говорит, что система сайдинга с воздушным зазором, состоящая из облицовки, прикрепленной к воздушному зазору между штукатуркой и сайдингом, эффективно защищает стену, но позволяет водяному пару из стены выходить наружу.
Все это также верно для светло-соломенной глины (LSC), хотя плотная и огнестойкая природа LSC побуждает некоторых строителей избегать затрат на внутреннюю или внешнюю штукатурку и просто устанавливать наружный сайдинг от дождя и внутренний гипсокартон. Любая из рассматриваемых стеновых сборок требует такой же крыши и фундамента, что и здание ICF. Хотя крайне важно, чтобы эти материалы на основе целлюлозы оставались сухими, эти материалы могут иметь одну стенку, которая является паронепроницаемой.«Однако, как правило, почти все эти естественные строительные системы должны иметь обе стороны паропроницаемой, чтобы влага могла выйти из стенового узла», — объясняет Рейланд. «Это правда, если влага попала во время строительства или каким-то образом просочилась внутрь во время проживания или во время какого-то шторма».
Стены LSC представляют собой систему заполнения из рыхлой соломы, слегка покрытой глиной, которая упакована в формы для изоляции и ограждения здания. Под «светом» понимается легкий слой глины на волокнах соломинки — ровно столько, чтобы они склеились.Блоки не легкие, их вес составляет около 15 фунтов на кубический фут. LSC является хорошим выбором для добавления изоляции к существующим стенам, потому что стены могут быть обшиты любой толщиной путем добавления материала гвоздей до желаемой глубины стены, хотя большинство стен LSC не превышают 12 дюймов. Однако одним из недостатков здесь является то, что LSC требует нескольких месяцев высыхания между установкой и обшивкой. Если участок находится в несухом климате или не защищен должным образом, ранний или неожиданный дождь может привести к намоканию стен, которые не могут просохнуть.
Добавление слоев
В жилищном строительстве принято добавлять слои покрытия в виде краски. «Если вы нанесете несколько слоев латексной краски поверх внутренней стены из гипсокартона, она станет полупроницаемой при нанесении двух или трех слоев», — говорит Рейланд. «Затем домовладельцы съезжают, а кто-то въезжает и добавляет еще пару слоев краски — эти стены становятся все менее проницаемыми до такой степени, что становятся пароизоляцией».
Почти законченный участок стены здания Махония.Некоторые тюки еще нужно разместить. Они использовали вертикальные рейки и длинные винты, чтобы прикрепить внутренние вертикальные края тюков к внешней стойке. Внутренние стены были покрыты штукатуркой из глины, рубленой соломы и песка. Канавка на уровне талии предназначена для прокладки электропроводки.
Солома, соломенная глина или початок не могут подвергаться такой обработке внутри. Вместо этого им нужна штукатурка внутри и какая-то штукатурка, а также защита от дождя снаружи. «Для душа в ванной комнате, примыкающего к стене из соломенных тюков, другие строители нанесли два слоя внутренней штукатурки, добавили полоски обшивки, а затем уложили плитку и плитку.Это создает воздушный зазор, поэтому, если влага все же проникнет через эту плитку, она не попадет в тюк. Вместо этого он будет капать прямо вниз».
Рейланд помог построить трехэтажное здание Mahonia Building, в котором разместился оптовый дистрибьютор экологически чистых продуктов питания в Юджине, штат Орегон. Здание Mahonia является уникальным исключением из этого требования, поскольку у него нет внешней штукатурки. Только два верхних этажа покрыты соломенными тюками.
«Внутренняя часть отделана глиняной штукатуркой толщиной 1 1/2 дюйма», — говорит Рейланд. «Снаружи мы помещаем тюки вплотную к 1/2-дюймовой фанере, которая имеет самую минимальную паропроницаемость, позволяющую просто пропускать влагу». Снаружи также обшиты полосами обшивки и металлическим сайдингом поверх обшивки.
В 2022 году Reiland будет строить конструкцию из тюков соломы с использованием аналогичной детали обшивки, но вместо полос обшивки и сайдинга планируется использовать дренажный мат, подходящий для трехслойной штукатурки. «Эта конкретная комбинация может не сработать в более холодных и влажных регионах», — предупреждает Рейланд.
Штукатурка толщиной 1 1/2 дюйма является типичной толщиной для такого типа зданий, но она необычно толстая для обычного строительства, говорит Рейланд. «Вы найдете толщину штукатурки от полудюйма до двух дюймов и более», — говорит он. «При строительстве из тюков соломы обычно желательна более толстая штукатурка, потому что поверхность тюков неровная, в отличие от фанеры».
Различная проницаемость
В статье Штрауба сделан вывод о том, что штукатурка толщиной 1 1/2 дюйма, изготовленная из смеси цемента и песка, имеет проницаемость менее 1 US Perm. 3. По мере увеличения доли извести в штукатурной смеси проницаемость увеличивается. Проницаемость штукатурки из цемента и песка толщиной 1 1/2 дюйма может быть увеличена до 5 или 10 единиц проницаемости США путем замены половины цемента известью и до 15-30 единиц проницаемости США при использовании штукатурки из чистой извести и песка. Нанесение масляной краски на штукатурку из цемента: извести: песка 1: 1: 6 обеспечит проницаемость менее 60 метрических единиц (1 США) и, таким образом, удовлетворит требованиям кодов для пароизоляции.
Земляные штукатурки, такие как саман, которые представляют собой смеси глины, соломы и песка, легко выдерживают 24 часа постоянного увлажнения, говорит Штраубе, хотя самые верхние 1/8 дюйма поверхности становятся довольно «грязными».«Нанесение извести на земляную штукатурку увеличивает механическую прочность штукатурки после намокания, а это означает, что она повышает устойчивость штукатурки к эрозии под воздействием дождя. Прочтите статью Штраубе здесь: https://tallerconco. org/wp-content/uploads/2017/05/Straube_Moisture_Tests.pdf
Неисправности этих зданий
Дома в Небраске, на которые Штраубе ссылается в своей статье, были построены в конце 1800-х и начале 1900-х годов с обычными свесами крыш. «Некоторым из этих зданий более 100 лет, и они все еще используются», — говорит Рейланд.«Когда здание из тюков соломы было «возрождено» или заново открыто на юго-западе Америки в 1980-х годах, толстые стены напоминали те, которые можно найти в народных глинобитных постройках, которые люди знали и любили», — объясняет Рейланд. «Пока в проекте здания было достаточно свесов крыши для защиты стен от сезонных дождей, они работали очень хорошо. Конструкции, в которых использовались парапетные крыши в зданиях из соломенных тюков в стиле пуэбло, также не прижились».
Практически любая стеновая система, включая каркасную стену и обычную изоляцию, которая опирается не более чем на слой штукатурки для защиты от дождя сверху, будет иметь проблемы. Стены традиционных глинобитных домов ремонтировались каждый год, что, хотя и довольно легко исправить, не подходит для нашего современного образа жизни.
«Мы должны проектировать и строить из материалов, учитывая их сильные и слабые стороны, — говорит он. «Это уроки, которые подкрепляют часто слышимую мантру: зданиям нужны хорошая шляпа, хорошие ботинки и дышащее пальто».
Внешний вид здания Mahonia до установки сайдинга.
Влияние доли рисовой соломы на физические свойства добавляемых добавок Полый блок
В данном исследовании представлено влияние рисовой соломы как добавочного материала на физические свойства пустотелых блоков, такие как прочность на сжатие, прочность на изгиб и водопоглощение, коэффициент размягчения. Путем тестирования физических свойств полого блока была изучена добавка рисовой соломы. Когда доля количества рисовой соломы составляла 0 ~ 15%, с увеличением доли рисовой соломы, влияние на сжатие, прочность на изгиб и водостойкость при добавлении одного вида агента ранней прочности и смешивании полого блока агента ранней прочности Al2(SO4)3, CaCl2 уменьшалось. постепенно. Когда доля рисовой соломы составляла 10%, при добавлении агентов ранней прочности Al2(SO4)3, CaCl2 прочность на сжатие полого блока в течение 28 дней была минимальной, 3.5МПа; при смешивании агента ранней прочности CaCl2, Al2(SO4)3 коэффициент размягчения полого блока составил 0,76, коэффициент водопоглощения составил 3,9%, что соответствует требованиям национального стандарта для обычных бетонных пустотелых блоков. В результате эксперимента был сделан вывод о том, что смешивание добавок для ранней прочности Al2(SO4)3, CaCl2 явно превосходит добавление одного из видов добавок для ранней прочности — Al2(SO4)3 или CaCl2 по физическим свойствам полого блока.
Информация:
Цзяньцзюнь Чжэн, Сюли Ду, Веймин Янь, Юэ Ли и Цзяньвэй Чжан
[1]
М. З. Фан, Дж. М. Динвуди, П.В. Бонфилд, М.К. Бриз. Размерная нестабильность цементно-стружечной плиты: моделирование CBPB как композита из двух материалов. Wood Science Technology, 2004. 373-383.
DOI: 10.1007/s00226-003-0210-8
[2] Сяо Лигуан, Ли Хуишэн, Чжан Цичжи.Journal of Jilin Architecture and Civil Engineering Institute, vol. 22 (2005), p.1.
[3]
Zhao Jixin, Li Riqiang. Sci-Tech Information Development & Economy, vol. 20 (2010), p.189.
[4] Guo Xingkai.Перспективы развития искусственной соломенной доски в нашей стране. Искусственное общение на доске. (2010).
[5]
В. Ф. Рассказов, Г.Д. Ашмарин и А.Н. Ливада. Стекло и керамика. об. 66 (2009), стр.3.
[6] Йи Мин Вэй, Буничиро Томита.The Japan Wood Research Society. (2001), p.437.
[7]
Wen Junqiang, Chen Yimin, Zhang Hongtao. В нашей стране неорганические вяжущие материалы на основе соломенных материалов развиваются в настоящее время. Тезисы Десятой национальной конференции по химии и применению цемента и бетона (2007 г.).
[8] Шэн Ли.Журнал Аньхойской сельскохозяйственной науки. об. (2010), стр. 11335.
[9]
А. Мансур, Дж. Сребрик и Б. Дж. Берли. Журнал исследований прикладных наук, том. (2007), стр. 1571.
Stak Block экологически безопасно использует рисовую солому
Рис, в изобилии выращиваемый в Калифорнии, веками кормил миллионы людей в Индии, Китае и других странах Азии.Но рисовая солома, богатая кремнеземом, — отходы сельского хозяйства — обычно сжигается, потому что ее слишком дорого собирать для компостирования и она не подходит для кормления животных. Сейчас его значение изучают архитектор и изобретатель Бен Корман и его партнер Джей Раски в своей компании Oryzatech в Голете (округ Санта-Барбара).
Корман и Раски создали Stak Block, экспериментальный Lego-подобный строительный блок размером 12 на 12 на 24 дюйма, сделанный из высушенной рисовой соломы. Солома смешивается с бесформальдегидным клеем и плотно прессуется в металлических формах при температуре около 300 градусов.
«Рисовая солома обладает экологически чистыми энергосберегающими свойствами», — говорит Корман, бывший консультант НАСА, проектировавший жилые помещения для Марса.
«Вместо этого я решил сделать кое-что на Земле», — сказал он. Он сосредоточился на рисовой соломе, одном из крупнейших биоотходов на Земле, поскольку для его производства не требуются дополнительные ресурсы. Из тонны риса получается примерно 1 1/2 тонны соломы. Вот почему в сочетании с производством основных продуктов питания «солома является быстро возобновляемым строительным ресурсом», — говорит Корман.Каждый блок Stak весом 30 фунтов относительно прост в обращении. Блоки, врезанные вместе без цемента, скреплены сеткой из арматуры с резьбой, вставленной в их отверстия и прикрученной болтами к фундаменту и верхней деревянной плите. Плотно упакованная рисовая солома может использоваться для формирования толстых стен и удваивается как изоляция, которая более эффективна, чем стекловолокно или даже экологически чистые изоляционные материалы, такие как измельченная джинсовая ткань. Stak Block также поглощает шум и в случае пожара просто обуглится снаружи, в то время как его плотное внутреннее ядро останется невредимым, потому что не пропускает кислород.
Корман надеется, что финансирование его предприятия будет получено в течение следующего года. Тем временем он построил модельный сарай, который служит офисом в Голете.
Его цель состоит в том, чтобы низкотехнологичные фабрики, занимающиеся производством Stak Blocks, росли как грибы вокруг районов выращивания риса, чтобы расходы на транспортировку и углеродный след этого неиспользованного строительного материала были незначительными.
Краткий обзор
Мнение эксперта: Stak Блоковые стены должны дышать для предотвращения образования плесени, как и любой другой строительный материал. На внутренних поверхностях можно прикрутить гипсокартон. По словам изобретателя Бена Кормана, Tyvek или другой влагозащитный материал можно использовать снаружи, за исключением очень влажного климата, где барьеры могут замедлять быстрое испарение.
Плюсы: Stak Block может быть первой по-настоящему ресурсоэффективной конструкционной/изоляционной стеновой системой для строителей. С Stak Block может работать строитель со стандартными инструментами. Изготовленные из экологически чистых органических материалов, блоки Stak близки к нейтральному выбросу углерода и, скорее всего, будут соответствовать требованиям LEED.Блоки Stak, с которыми легче обращаться, чем с тяжелыми тюками соломы толщиной 18 дюймов, также образуют более тонкие стены.
Минусы: Блоки Stak так же устойчивы к плесени, как стандартные пиломатериалы, каменная кладка или бетон, но разрушатся, если вступят в контакт с чрезмерной влажностью. Блоки должны быть уложены на бетонный фундамент и требуют некоторого обрамления и защиты вокруг окон.