Размеры силикатного кирпича белого: характеристики, плюсы и минусы
Силикатный искусственный камень нашёл разное применение в строительстве из-за его невысокой стоимости и нетрудоёмкого процесса изготовления. В его состав входят компоненты, которые можно легко найти: песок, известь и вода.
Для того чтобы получить кирпич состав помещают в специальные автоклавы для обработки повышенной температурой и давлением.
В итоге получается ровный прочный блок, после сушки, который, можно сразу же использовать для стойки.
Сфера применения
Кирпич можно применять для строительства как жилых, так и производственных помещений. Он подходит для несущих стен и любых перегородок. Так как цена на него невысока, то часто его применяют для заборов, отделки и облицовки. Часто можно встретить дачи, веранды, хоз. постройки из силикатного кирпича. У таких зданий повышенная прочность и хорошая звукоизоляция.
Однако, из-за его специфических свойств, не стоит использовать этот искусственный камень для возведения фундамента и подвальных помещений. Это объясняется тем, что из-за близости расположения грунтовых вод повышена влажность, и силикатный кирпич может разрушиться.
Также не стоит его применять и для строительства труб и кладки печей, высокая температура действует разрушительно на кирпич.
Достоинства и недостатки
Прежде чем определиться с выбором материала для строительства стоит изучить все его достоинства:
- высокая шумоизоляция – в помещениях из силикатного материала не будут слышны посторонние звуки;
- на нём никогда не появляется высол: белый соляной налёт, выступающий на кирпичах из других материалов;
- устойчивость к низким температурам позволяет применять его в регионах с постоянными морозами;
- применяя пустотелые виды можно снизить давление на фундамент и облегчить вес всего здания;
- природные компоненты, входящие в состав, делают кирпич экологически безопасным;
- силикатный камень намного ниже по стоимости, в отличие от других аналогов.
Главный недостаток – это высокое влагопоглощение, в сырых помещениях этот материал начинает разрушаться. Эту проблему можно частично решить, обработав стены
Стоит отметить и повышенную теплопроводность, это значит, что этот искусственный камень легко отдаёт тепло, не сохраняя его, поэтому необходимо дополнительное утепление здания.
Разновидности силикатного кирпича
По назначению силикатный камень бывает рядовым: используется для обычной кладки, его поверхность может быть шероховатой, с мелкими трещинами и незначительными сколами. Облицовочный кирпич отличается отсутствием повреждений, может быть цветным, с декоративным покрытием или рельефной поверхностью.
В зависимости от того, какие нагрузки будет испытывать возводимая постройка, используют полнотелый или пустотелый кирпич.
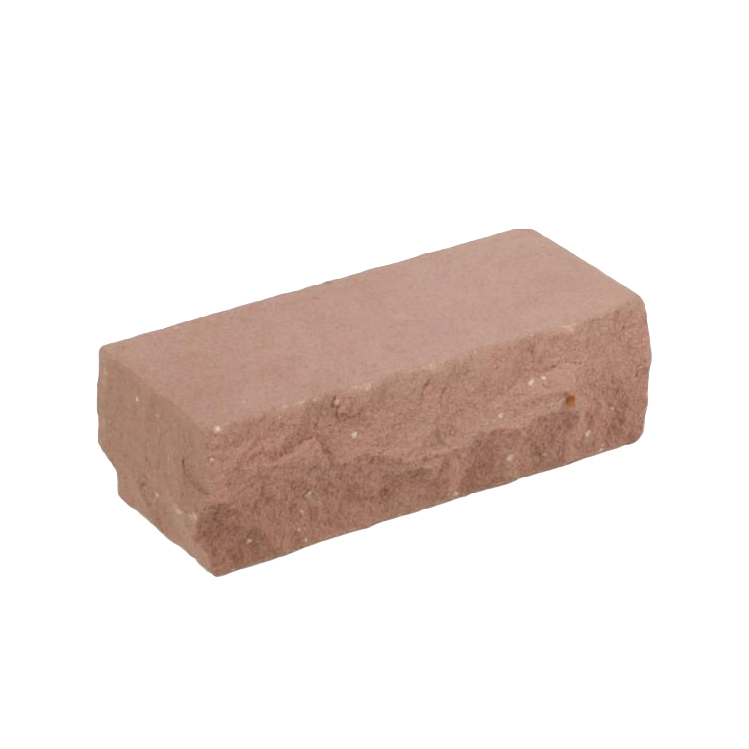
- Полнотелый используют для постройки несущих стен, где не имеет значения вес всего сооружения.
- Пустотелый же может различаться по количеству воздушных камер в нём. Минимум – это три отверстия, а максимум может достигать 14. Такое количество обеспечивает высокую звукоизоляцию и снижает теплопроводность. Но низкая прочность ограничивает его применение
Учтите, что наличие пустот в камне увеличивает расход раствора для кладки. Чем больше отверстий, тем больше раствора потребуется, разница может составлять примерно 30% .
Технические характеристики
Прочность – одна из основных характеристик кирпича, это способность к сопротивлению внешним воздействиям. Марки силикатного кирпича показывают, сколько килограммов приходится на 1 см2.
- Марки М-75 и М-100 используются только для перегородок;
- М-120, М-175 – для возведения одноэтажных зданий;
Устойчивость к морозам. Силикатный кирпич должен выдерживать от 15 до 50 циклов. Морозостойкость обозначается буквой F, число возле буквы показывает, сколько циклов заморозки и оттаивания он выдерживает, например, F25 или F30. Чем выше показатель морозостойкости, тем лучше.
Плотность. От неё зависит, какая теплопроводность будет у кирпича. Самая эффективная – у класса со значением 0,8. Класс 2 будет малоэффективным и требует дополнительного утепления. В основном используют класс 1 или 1,2.
Размеры силикатного кирпича белого могут быть совершенно разными, это надо учитывать при подсчёте необходимого количества материала.
- одинарный кирпич – это блок с размерами 25х12х6,5 см;
- утолщённый или полуторный имеет размеры 25х12х8,8 см;
- двойной имеет те же параметры, но высота будет 13 см.
Кирпичи с нестандартными размерами изготавливают для того, чтобы процесс строительства шёл быстрее и уменьшить расход раствора.
Вес кирпича силикатного одинарного:
- полнотелый камень весит 4 кг;
- пустотелый – 3,2 кг.
Вес силикатного кирпича 250х120х88 или полуторного тоже будет зависеть от плотности: с пустотами его масса составит примерно 3,9 кг, а плотного камня – 5 кг;
Обратите внимание на то, что у кирпичей с одинаковыми размерами, но разным весом теплоизоляционные свойства будут лучше у более лёгкого камня.
Как правильно выбрать
Для того чтобы здание из силикатного кирпича было прочным, долго не разрушалось и на поверхности камней не появлялось никаких дефектов, необходимо ещё при покупке обратить внимание на ряд моментов:
- если слегка ударить по кирпичу металлическим предметом, то звук должен получиться звонким, если же он получается глухим, то это говорит о плохой сушке изделия;
- условия хранения будут влиять и на качество кирпича, если он находится под открытым небом, то его эксплуатационные характеристики будут снижены;
- большое значение имеет правильная упаковка и доставка материала. Лучше всего, если используются поддоны, так меньше вероятность повреждения кирпичей и их разрушения;
- проверьте при покупке соответствие того, что хотите купить с тем, что вам отгружают, ошибка приведёт к дополнительным тратам.
Сделав правильный выбор, вы получите качественный материал, здания из которого, будут стоять долгое время. Кроме того, низкая стоимость и высокая декоративность силикатного кирпича позволяет применять его для самых разных построек.
вес и размеры- характеристики +Фото и Видео
Силикатный полуторный кирпич: вес и размеры. На сегодняшний день самым популярным строительным элементом является полуторный силикатный кирпич.
Его достаточно часто используют для строительства несущих поверхностей и перегородок в домах.
Популярность данного материала обусловлена тем, что работы с ним выполняются качественно, быстро и что немаловажно – экономно.
Общие сведения
Технические характеристики и свойства
Этот строительный материал получает благодаря прессованию в актоклаве особой смеси, которая включает в себя воду, кварцевый песок, модификаторы и известь. Кирпичи из силиката имеют достойные характеристики эксплуатации.
- Теплопроводность силикатного полуторного кирпича составляет 0,56Вт/мОс.
Этот показатель намного меньше, если сравнивать с красным керамическим материалом, поэтому для целесообразности возведение внешних стен лучше провести именно из этого кирпича.
- Плотность кирпича. Элементы, которые являются полнотелыми, намного крепче, чем пустотелые. При сравнении показателей плотность полнотелого элемента выше второго на 600 единиц.
- Поглощение влаги. Этот показатель весьма важен при строительстве. Кристаллическая структура материала дает возможность достаточно быстро и впитывать, и отдавать влагу. По этой причине вы можете не волноваться о том, что могут появиться трещины на стенах, которые выполнены из этого материала.
- Прочность на изгиб и сжатие. Самой популярной маркой является номер 150, так как у нее показатель прочности равен 50кг/см2.
- Оптимальный вариант для возведения перегородок между комнат, как именно силикатный полуторный кирпич обладает высокой звукоизоляцией.
- Размер полуторного силикатного кирпича равен 250*120*88 мм.
- Вес элемента составляет примерно 4 кг.
Обратите внимание, что специалисты настоятельно не рекомендуют возводить из силикатного кирпича фундамент и цокольные этажи, так как в подземных водах содержится больший процент серной кислоты, которая способна разлагать силикаты.
Достоинства силикатного кирпича
При строительстве перекрытий и стен обычно используют пустотелые кирпичи с утолщением. При этом пустоты бывают несквозные и сквозные. По форме они могут напоминать цилиндр, который расположен перпендикулярно основанию. За счет этих ячеек кирпич становится облегченным, что снижает нагрузку на фундамент. Еще одним плюсом в этой ситуации является то, что показатели и звукоизоляционные характеристики становятся лучше во много раз.
Если проанализировать все вышепреречисленное, становятся очевидны такие преимущества:
- Экономия времени при укладке. Перегородку, которая является несущей, укладывают в 2 ряда + 1 дополнительный ряд облицовки.
- Огромная экономия вяжущего раствора.
- Срок эксплуатации здания из силикатного кирпича увеличивается.
- Повышается показатель теплосохранности и морозоустойчивости стен.
Облицовочный полуторный кирпич может быть в нескольких цветах: красный, розовый, голубой и желтый. Такие оттенки стало возможным получать благодаря пигментам, которые добавляют в смесь и которые устойчивы к щелочи. Их добавляют еще на стадии производства. Помимо того, что стены можно сделать презентабельными, они позволяют стенам «дышать», а это тоже продлевает срок службы.
Особенности, размеры и вес полуторного силикатного кирпича
Габариты (вес и размер) одного силикатного кирпича превышают показатели керамического аналога в несколько раз. Это обусловлено тем, что известь и кварцевый песок, который являются основой, делает его достаточно тяжелым. Компоненты, которые берут при производстве этого строительного материала, имеют высокий уровень гигроскопичности, что тоже влияет на вес кирпича.
Если использовать силикатный кирпич для возведения стен, то его делят на такие 2 группы: рядовой и лицевой. Но размер кирпича никак не зависит от его вида. Стандартный размер, как мы уже говорили, 250*120*88 мм. Камень для облицовки отличается гладкостью и достаточно красивой поверхностью. Он имеет идеальный вид, что позволяет выполнять красивую укладку.
А вот рядовой полуторный силикатный кирпич используют для несколько иных целей. Обычно он выполняется только в белом цвете, и используется для стен и перегородок. В таких работах гладкость кирпича неважна, куда нужнее, чтобы кирпич был прочным и плотным по структуре. Показатель массы материала в этом случае зависит только от структуры. Полнотелые кирпичи представляют собой плотную, сплошную массу без отверстий и пустот. В этой случае максимальный вес полуторного силикатного кирпича будет 4,5 кг.
Пустотелые камни изнутри выглядят как соединение ячеек, отверстий и пустот. Вес будет зависеть от количества, но средний показатель не превышает 4 кг.
Популярные вопросы
Зачем знать массу кирпича?
Вес любого геометрического тела можно с легкостью рассчитать по формуле – плотность тела умножаем на объем (m=p*V). Эти показатели несложно найти самому. При вычислении берите во внимание показатель влажности, наличие и число пустот в кирпиче, а также присутствие декоративной отделки. Весовые показатели могут несколько отличаться друг от друга, но это зависит от концентрации влаги в кирпиче. Большое процент будет увеличивать вес изделия. Наличие пустот и ячеек, наоборот, уменьшит показатель массы кирпича.
На практике, удельная масса элемента бывают в рамках от 1300 до 1900 кг/м2. Зная формулу для расчета одного элемента, будет нетрудно рассчитать, какое давление будет на фундамент.
Если вы провели расчет, и он оказался верным, вы сможете сэкономить и не обустраивать цокольный этаж. Дом будет крепким, а стены не пойдут трещинами только из-за того, что при строительстве были совершены ошибки в расчетах. Производители силикатного полуторного кирпича и продавцы всегда указывают точные размеры и вес изделия, что облегчает процесс подсчета.
Где используется?
Этот материал стал популярным благодаря ассортименту: цвета поверхности граней разнообразны, кирпичи выпускают как полнотелые, так и пустотелые, а это дает возможность архитектору подойти к творению и созданию проекта творчески, чтобы в результате получить шедевр архитектуры.
Этот строительный материал активно используют для укладки внешних и внутренних стен. Если соединить между собой полуторный, одинарный, белый и разноцветные кирпичи, можно получить шикарную отделку здания.
Специалисты в этом деле определили некоторые факторы, при которых полуторный силикатный кирпич лучше не использовать в строительстве. На практике, это связано с климатическими условиями и эксплуатацией дома, а также особенностями конструкции технического характера.
Когда на силикатный кирпич оказывается воздействие температуры более 600-ти градусов, предел прочности становится в разы меньше, и начинают появляться трещины. Этот камень нельзя использовать для установки каминов, дымоходных труб и печей. Для этого вида работ следует использовать только огнеупорные материалы.
Внимание! Перевозка силикатного кирпича возможна только на поддонах. Это дает возможность сохранить материал, и правильно организовать процесс укладки стен.
Вывод
Итак, как показывает практика, силикатный полуторный кирпич представляет собой строительный материал, имеющий отличные эксплуатационные и технические характеристики. Его обычно используют для возведения перегородок, перекрытий и стен в доме. Важное преимущество использования этого материала – стоимость. Она небольшая, а это поможет уменьшить траты при строительстве.
Силикатный кирпич — характеристики и особенности
На сегодняшний день силикатный кирпича широко используются в строительстве разного рода зданий. Кирпич так назван из-за того, что состав смеси, из которой изготовлены эти кирпичи – это песок и известь, а саму смесь изначально назвали «силикатной». Так что, по сути, кирпичи получили название, производное от названия своего состава.
Размеры силикатного кирпича
В целом же, данный кирпич как стройматериал можно назвать одним из самых популярных материалов для строительства. Именно поэтому, при подсчете количества материала, необходимого для закупки, возникает вопрос про размеры силикатного кирпича.
При использовании полуторного – размеры будут, соответственно 250мм (дл.) Х 120мм (шир.) Х 88мм (толщ.). Двойной размер силикатного кирпича предполагает такие стандарты: 250мм (дл.) Х 120мм (шир.) Х 138мм (толщ.).
Все размеры стандартизированы для удобства подсчетов, а за основу брался самый тонкий кирпич силикатный размеры которого указаны выше. Такой размер является самым удобным для работы, поскольку удобен для удерживания одной рукой, а также, все стандартные расчеты схем кладки стен также ориентированы именно на такой тип кирпича.
Вес силикатного кирпича.
Несмотря на то, что размеры для кирпича установлены настолько разными, существует норматив, в котором максимальный вес единицы кирпича равняется 4,3 кг. Для работы используется чаще более легкий вариант, стандартного размера, с весом около 3,4 кг.
Если говорить именно о весе силикатного кирпича – то он находится в прямой зависимости от плотности. Следует помнить, что кирпич бывает полнотелый, или же пустотелый. Одинарный полнотелый по весу равен примерно 3,7 кг. Пустотелый же затянет около 3,2 килограмма. Учитывая вес поддона (30-40 кг) и количество кирпичей в упаковке (для полнотелых и пустотелых кирпичей это количество может быть разным) то получаем в результате вес от 800 до 1680 кг.
Характеристики силикатного кирпича
Уже неоднократно упоминалось, что благодаря своим свойствам, белый кирпич является очень востребованным материалом. Давайте рассмотрим, в чем заключается его привлекательность для потребителя.
- Прежде всего, следует упомянуть хорошую звуко- и тепло- изоляцию. Пожалуй, в этих показателях он стоит на втором месте после красного глиняного кирпича.
- Второе, он достаточно устойчив к воздействию холода. Для проверки морозостойкости такого материала его примерно 15 раз замораживают и дают оттаять. Если в результате всех этой процедуры кирпич не начал расслаиваться и крошиться – его признают морозостойким.
Конечно, у этого материала есть свои недостатки. Например, он отлично впитывает влагу, а при температуре 600 градусов по Цельсию, он становится более хрупким.
Насколько прочен силикатный кирпич?
Этот вопрос можно задать применительно к любым строительным материалам. Прежде всего, надо сказать, что под прочностью понимается способность материала сопротивляться внешнему воздействию. Предел прочности кирпича при изгибе и сжатии определяется лабораторными методами, и после соответствующим образом маркируется. Установленные маркировки силикатного кирпича:
- для полнотелого кирпича: М200, М150, М125,М100, М75;
- для пустотелого: М50, М25
Применение силикатного кирпича.
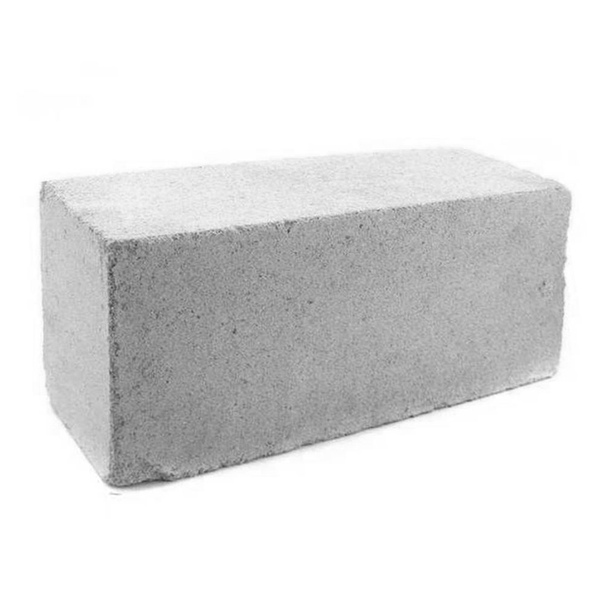
Поскольку это не только удобный и популярный вид кирпича, но еще и недорогой – его применение гораздо шире, чем у некоторых других его собратьев. Из-за хорошей звукоизоляции его часто используют при постройке перегородок и несущих стен жилых и офисных зданий. В последнее время часто используется цветной силикатный кирпич. В силу того, что в его состав добавлен краситель, такой кирпич может выполнять двойную функцию: как материал для стен, и как декоративный элемент отделки.
Недостатки этого материала делают нежелательным его применение при постройке фундаментов или облицовке водоемов, т.к. лучше всего минимизировать его контакт с водой. То же самое касается и применения его в помещениях с повышенной влажностью, если только не планируется облицовка керамической плиткой, к примеру. Также не стоит использовать его для постройки печей и каминов, а также дымоходов в непосредственной близости от огня, чтобы избежать его разрушения.
Прессы для силикатного кирпича — WKB Systems
В основе нашего завода по производству силикатного кирпича: прессы серии WKP
Прессы лежат в основе каждого завода по производству силикатного кирпича. Чтобы гарантировать производство высококачественного силикатного кирпича, мы разработали для наших клиентов прессы серии WKP.
Все прессы этой линейки — гидравлические и имеют особую конструкцию литого натяжного стержня. Эта устойчивая конструкция гарантирует долговечность и высочайшее качество продукции.Их конструкция и электрическая система управления современные. Техническое решение обеспечивает нашим клиентам индивидуальное и современное производство силикатного кирпича. Помимо прочего, наши заказчики могут производить как полнотелый, так и перфорированный кирпич, цветной силикатный кирпич и силикатный кирпич с подкладками. С помощью наших прессов вы получаете силикатный кирпич точных размеров и однородной прочности на сжатие. Последнего мы достигаем за счет автоматического и точно настроенного наполнения машины.Это важно для обеспечения того, чтобы при каждом такте давление было по большей части постоянным, так что достигается равномерная прочность кирпича на сжатие.
Благодаря особой конструкции наши прессы очень просты в обслуживании. Прессы серии WKP — это долговечность, богатый ассортимент продукции и силикатный кирпич высочайшего качества.
Для еще большей рентабельности и эффективности завода мы специально спроектировали эту зону завода: разбросанные отходы, которые накапливаются в зоне пресса, представляют собой ценное и пригодное для повторного использования сырье.Таким образом, отходы возвращаются в смеситель через обратную магистраль.
Краткий обзор наших прессов серии WKP:
WKP 750 — впечатляющие характеристики
Самый известный пресс для силикатного кирпича от WKB Systems — это WKP 750. Его производительность действительно впечатляет: можно прессовать до 10 000 кирпичей в час с максимальным усилием до 750 тонн. Еще одно преимущество — относительно компактный дизайн, а это значит, что он занимает мало места. Таким образом, в случае модернизации завода WKP 750 можно относительно легко интегрировать в существующие заводы, чтобы заменить машины с более низкими характеристиками.
WKP 750 S — для сверхбольшого кирпича
Вариантом WKP 750 является пресс для силикатного кирпича WKP 750S. Он был специально разработан для производства силикатного кирпича большого формата высочайшего качества. В отличие от WKP 750, он также оснащен фронтальным захватом для разгрузки, чтобы справиться с большим форматом.
WKP 750 DD — Обжатие с двух сторон
Верхний и нижний пуансоны двойного пресса WKP 750 DD с гидравлическим приводом сжимают сырье с двух сторон.В результате достигается очень высокая и равномерная прочность по всему поперечному сечению кирпича. Силикатный кирпич высотой до 250 мм, малогабаритная фасадная кладка и заготовки для системы раскалывания и тиснения могут быть произведены с высокой прочностью на сжатие.
WKP 600 — маленький, но мощный
Гидравлический пресс для силикатного кирпича WKP 600 — самый маленький пресс в линейке WKP. Он может производить до 5720 кирпичей в час.
Мы будем более чем счастливы настроить прессы серии WKP индивидуально в соответствии с вашими потребностями. Хотели бы вы иметь определенные модификации? Наши специалисты вместе с вами разработают прессы, подходящие для вашего предприятия.
|
|
EDS спектр традиционного силикатного кирпича.

Силикатные материалы подвергаются автоклавированию, что обуславливает их значительную огнестойкость (класс A). Этот вид материала иногда недооценивают, несмотря на его полезные качества (прочность на сжатие 15–20 МПа, насыпная плотность 1,73 кг / дм³, низкая водопоглощаемость), недавно вернувшиеся на рынок с более сильными позициями. Основное внимание в исследовании уделялось прочности на сжатие, насыпной плотности, пропитываемости и водопоглощаемости, а также микроструктурным характеристикам модифицированных силикатных материалов, подвергнутых автоклавированию.Для экспериментов были приготовлены лабораторные образцы традиционных и модифицированных продуктов. В лабораторных условиях были изготовлены образцы размером 40 × 40 × 160 мм. После лабораторных испытаний были изготовлены полнотелые силикатные кирпичи размерами 180 × 220 × 250 мм. Целью исследования было определение оптимальных ингредиентов силикатной массы с добавлением бариевого агрегата с зернистостью 0–2 мм и жидкого силиката лития в виде раствора. Отмечены физико-механические свойства силикатов по прочности образцов на сжатие.Для проведения экспериментов был установлен ортогональный композиционный план типа 3k (с k = 2), таким образом, полный эксперимент с двумя факторами. Для каждого соотношения факторов было проведено шесть параллельных экспериментов. Аналогичным образом проводились анализ и испытания объемной плотности. Модифицированная силикатная масса тщательно перемешивалась, затем прессовалась и на последнем этапе помещалась в автоклавы. Модификаторами служили: агрегат бария с зернистостью 0–2 мм в количестве до 20% (благоприятно 20%) и жидкий силикат лития в количестве до 5% (благоприятно 4%).В статье представлено влияние модификации автоклавных кальциево-песчаных материалов баритовым заполнителем (BaSO4) и силикатом лития на параметры их применения. Технологический процесс производства модифицированных силикатных изделий оставлен без изменений. Модификация доказывает положительное влияние на пористость силиката (ограничивает его свободное пространство) и значение прочности на сжатие, которое установлено на уровне 43,1 МПа при 5% силиката лития и 30% агрегата бария в силикатной массе (традиционные образцы имеют около 20 МПа).
Благоприятно улучшена фазовая микроструктура силикатных изделий. В микроструктуре модифицированных продуктов появляются крупные кластеры ксонотлита с C – S – H фазой и тоберморитом.
Masa Group — заводы по производству бетонных блоков, бетонных плит, пенобетона, силикатного кирпича
Это долгий путь от сырья и смеси до готового камня. В этом процессе задействованы многие компоненты растений. Только если компоненты системы согласованы, можно быть уверенным в бесперебойном процессе и экономичной работе завода по производству блоков.Узнайте о наших заводах по производству бетонных блоков.
Это долгий путь от сырья и смеси до готового (бордюрного) камня. Прессы Masa Kerbstone были разработаны с учетом, среди прочего, особых требований к бордюрам «Британского стандарта». Этот «британский стандарт» по-прежнему является условием в странах Ближнего Востока и Великобритании. Узнайте о наших заводах по производству Kerbstone.
Производство изделий из газобетона в автоклаве требует высоких стандартов для смешивания и дозирования заполнителей, контроля процесса ферментации и контроля каждого этапа производства. Газобетонные установки Masa — это проверенные передовые технологические процессы, разработанные в соответствии с конкретными требованиями клиентов. Такой подход позволяет комплексным решениям обеспечивать высокоэффективные, оптимизированные процессы, приводящие к стабильному качеству конечного продукта. Узнайте больше о наших заводах по производству AAC.
Это долгий путь от сырья и смеси до готовых силикатных кирпичей. В этом процессе задействованы многие компоненты растений.Только если компоненты системы подобраны, можно быть уверенным в бесперебойном процессе и экономичной работе завода по производству силикатного кирпича. Узнайте о наших заводах по производству силикатного кирпича.
Пресс для плит UNI 2000 — это сердце любого завода по производству бетонных плит. Кроме того, требуются дозирующие и смесительные установки, приемные устройства с установками прямой промывки и системы хранения, а также машины и оборудование для измельчения и упаковки слябов.Masa может предложить полное ноу-хау для производства бетонных плит. Это решающее преимущество для наших клиентов: планирование, проектирование, производство, сборка, ввод в эксплуатацию, обучение, техническое обслуживание и постоянная поддержка во время производства — все от одного поставщика. Узнайте о наших заводах по производству бетонных плит.
Masa LithoPore® — это минеральный строительный материал, который перерабатывается в паропроницаемую теплоизоляционную панель. Узнать больше о Masa-LithoPore®
IRJET-Запрошенная вами страница не найдена на нашем сайте
IRJET приглашает статьи из различных инженерных и технологических дисциплин, для выпуска 9 (сентябрь 2021 г.)
Отправить сейчас
IRJET Vol-8 Issue 9, Сентябрь 2021 г. Публикация продолжается…
Обзор статей
IRJET получил «Импакт-фактор научного журнала: 7,529» за 2020 год.
Проверить здесь
IRJET получил сертификат регистрации ISO 9001: 2008 для своей системы управления качеством.
IRJET приглашает специалистов по различным инженерным и технологическим дисциплинам, научным дисциплинам для Тома 8, выпуск 9 (сентябрь 2021 г. )
Отправить сейчас
IRJET Vol-8, выпуск 9, сентябрь 2021 г. Публикация продолжается…
Обзор статей
IRJET получил «Импакт-фактор научного журнала: 7,529» за 2020 год.
Проверить здесь
IRJET получил сертификат регистрации ISO 9001: 2008 для своей системы управления качеством.
IRJET приглашает специалистов по различным инженерным и технологическим дисциплинам, научным дисциплинам для Тома 8, выпуск 9 (сентябрь 2021 г.)
Отправить сейчас
IRJET Vol-8, выпуск 9, сентябрь 2021 г. Публикация продолжается…
Обзор статей
IRJET получил «Импакт-фактор научного журнала: 7,529» за 2020 год.
Проверить здесь
IRJET получил сертификат регистрации ISO 9001: 2008 для своей системы управления качеством.
IRJET приглашает специалистов по различным инженерным и технологическим дисциплинам, научным дисциплинам для Тома 8, выпуск 9 (сентябрь 2021 г. )
Отправить сейчас
IRJET Vol-8, выпуск 9, сентябрь 2021 г. Публикация продолжается…
Обзор статей
IRJET получил «Импакт-фактор научного журнала: 7,529» за 2020 год.
Проверить здесь
IRJET получил сертификат регистрации ISO 9001: 2008 для своей системы управления качеством.
IRJET приглашает специалистов по различным инженерным и технологическим дисциплинам, научным дисциплинам для Тома 8, выпуск 9 (сентябрь 2021 г.)
Отправить сейчас
IRJET Vol-8, выпуск 9, сентябрь 2021 г. Публикация продолжается…
Обзор статей
IRJET получил «Импакт-фактор научного журнала: 7,529» за 2020 год.
Проверить здесь
IRJET получил сертификат регистрации ISO 9001: 2008 для своей системы управления качеством.
IRJET приглашает специалистов по различным инженерным и технологическим дисциплинам, научным дисциплинам для Тома 8, выпуск 9 (сентябрь 2021 г. )
Отправить сейчас
IRJET Vol-8, выпуск 9, сентябрь 2021 г. Публикация продолжается…
Обзор статей
IRJET получил «Импакт-фактор научного журнала: 7,529» за 2020 год.
Проверить здесь
IRJET получил сертификат регистрации ISO 9001: 2008 для своей системы управления качеством.
IRJET приглашает специалистов по различным инженерным и технологическим дисциплинам, научным дисциплинам для Тома 8, выпуск 9 (сентябрь 2021 г.)
Отправить сейчас
IRJET Vol-8, выпуск 9, сентябрь 2021 г. Публикация продолжается…
Обзор статей
IRJET получил «Импакт-фактор научного журнала: 7,529» за 2020 год.
Проверить здесь
IRJET получил сертификат регистрации ISO 9001: 2008 для своей системы управления качеством.
IRJET приглашает специалистов по различным инженерным и технологическим дисциплинам, научным дисциплинам для Тома 8, выпуск 9 (сентябрь 2021 г. )
Отправить сейчас
IRJET Vol-8, выпуск 9, сентябрь 2021 г. Публикация продолжается…
Обзор статей
IRJET получил «Импакт-фактор научного журнала: 7,529» за 2020 год.
Проверить здесь
IRJET получил сертификат регистрации ISO 9001: 2008 для своей системы управления качеством.
Экспериментальные исследования кирпичей из золы-уноса с добавлением гипса
Ключевые слова: уголь летучая зола, конструкционный кирпич, песок, гипс, микроструктура, свойства
Американский журнал материаловедения и технологий , 2013 1 (3),
С. 35-40.
DOI: 10.12691 / материалы-1-3-2
Поступило 14.08.2013 г .; Отредактировано 26 августа 2013 г . ; Принята в печать 28 августа 2013 г.
1. Введение
Пылевидная зола, широко известная как летучая зола, является полезным побочным продуктом тепловых электростанций, использующих пылевидный уголь в качестве топлива.Высокая температура горения угля превращает глинистые минералы, присутствующие в угольном порошке, в плавленые мелкие частицы, в основном содержащие силикат алюминия. Полученная таким образом летучая зола обладает как керамическими, так и пуццолановыми свойствами. Летучая зола — опасные отходы. Проблема с летучей золой заключается не только в том, что для ее удаления требуется большое количество земли, воды и энергии, ее мелкие частицы, если с ними не справиться должным образом, в силу своей невесомости, могут попасть в воздух. Известно, что при неправильной утилизации летучая зола загрязняет воздух и воду и вызывает респираторные проблемы при вдыхании.
Во всем мире около 20% летучей золы используется в приложениях, связанных с бетоном. В основном CaO – SiO 2 –H 2 O и CaO – Al 2 O 3 — SiO 2 –H 2 O-фазы способствуют упрочнению [1, 2] . Летучая зола также используется во многих различных областях, таких как краски, пластмассы и в сельском хозяйстве [3, 4, 5, 6, 7] . В Бангладеш ежегодно производится около 0,6 миллиона тонн летучей золы, и ее производство, вероятно, значительно возрастет, поскольку будущие электростанции в Бангладеш, вероятно, будут работать на угле.С другой стороны, использование летучей золы пока не пользуется популярностью. Сообщается, что небольшое количество импортной летучей золы используется при производстве цемента в Бангладеш. Жизнеспособным вариантом массового использования летучей золы могло бы стать производство конструкционного кирпича, содержащего летучую золу в качестве основного ингредиента. Производство обычных глиняных кирпичей предполагает потребление большого количества глины. Это истощает верхний слой почвы и вызывает деградацию сельскохозяйственных земель. Если можно будет производить кирпичи из золы-уноса, не содержащие глины, это не только поможет сохранить верхний слой почвы, но и снизит экологические проблемы, вызванные сбросом летучей золы.
В этом исследовании была сделана попытка произвести легкие кирпичи для строительных конструкций с использованием летучей золы, образующейся на ТЭЦ Барапукурия.
2. Материалы и методы
Смеси летучей золы, песка и гашеной извести с гипсом в качестве связующего были использованы для изготовления кирпича. Были оптимизированы такие параметры процесса, как состав смеси, давление, условия отверждения и т. Д. Наконец, были определены свойства кирпичей, произведенных в оптимальных условиях.
Летучая зола, использованная в этом исследовании, была собрана на Барапукурийской ТЭС. Остальные ингредиенты — гашеная известь, песок и гипс — были собраны на местном рынке. Основные ингредиенты летучей золы представлены в таблице 1.
Таблица 1. Химический состав летучей золы Барапукурии ТЭЦ
Образцы кирпича были изготовлены в условиях, указанных в таблице 2. По крайней мере, пять кирпичей были изготовлены для каждого типа образца. Перед изготовлением кирпича каждый ингредиент сырья сушили в муфельной печи при 110 ℃ в течение 24 часов.Взвешивали необходимое количество каждого ингредиента, добавляли 14% влаги и тщательно перемешивали компоненты. Чтобы обеспечить одинаковый размер кирпичей, каждый раз для заполнения полости формы использовалась известная масса смеси. Размер отверстия полости формы составлял 6 х 3,5 см. Гидравлический пресс использовался для приложения давления в течение 15 секунд (Рисунок 1). Затем кирпичи (рис. 2) были извлечены и окончательно отверждены. Отверждение производилось на воздухе, с использованием водного спрея, путем помещения кирпичей под влажную ткань и выдерживания кирпичей в воде.Кирпичи, сформированные под различным давлением, также подвергались отверждению в течение разных периодов времени в оптимальных условиях отверждения.
Рисунок 1 . Гидравлический пресс
Рисунок 2 . Кирпич зольный, силикатно-известково-гипсовый
2.1. Методы испытаний2.1.1. Прочность на сжатие
Прочность на сжатие определяли путем приложения нагрузки к образцу с использованием универсальной испытательной машины.Нагрузка была приложена к площади размером 6 мм х 3,5 мм [размер одной стороны всего кирпича].
2.1.2. Микроструктура
Образцы наблюдали под оптическим микроскопом (ОМ), а микрофотографии записывали с помощью цифровой камеры (OPTIKA Microscope B-600 MET) для исследования пористости. Подготовка образцов не производилась.
2.1.3. Свойство усадки
Размеры кирпичей были измерены сразу после изготовления кирпичей, а также после отверждения, чтобы определить усадку кирпичей.
2.1.4. Объемный вес изделия
После 7 дней отверждения кирпичи сушили при 110 ℃ в течение 24 часов, а затем давали остыть до комнатной температуры. Затем измеряли сухой вес D (г). После этого кирпичи погружали на 24 часа в воду при комнатной температуре и измеряли взвешенный вес S (г). Затем кирпичи были удалены, поверхностная вода была вытерта влажной тканью и в течение 5 минут после извлечения кирпичей из водяной бани был измерен насыщенный вес W (г).Удельный объемный вес B, г / см 3 = D / V, где рассчитан объем V, см 3 = (W — S).
2.1.5. Начальная скорость абсорбции (IRA)
После измерения сухого веса D (г), как упоминалось ранее, поверхность слоя кирпича (поверхность размером 6 мм X 3,5 мм) заставляли абсорбировать воду в течение 1 мин. Вода была полностью удалена с поверхности кирпича в течение 10 с после удаления от контакта с водой, а вес D ’(г) был определен в течение 2 минут.Затем рассчитывали начальную скорость абсорбции IRA,% = D ’- D [Обозначение C 67-00 ASTM].
2.1.6. Абсорбционная способность
ASTM Обозначение C 67-00 использовалось для измерения абсорбционной способности A,% = [(W — D) / D].
2.1.7. Кажущаяся пористость, открытые поры и непроницаемые поры
Обозначение ASTM C 67-00 использовалось для определения кажущейся пористости P,% = [(W — D) / V], объем открытых пор, см 3 = W — D и непроницаемый объем пор, см 3 = D — S.
2.1.8. Тест на выцветание
Этот тест проводился в соответствии с ASTM C67-08. Для этого испытания один кирпич вертикально помещали в воду с одним погруженным концом, а другой кирпич хранили в условиях окружающей среды. Через 7 дней оба кирпича сушили в печи при 110 ℃ в течение 24 часов. Затем оба кирпича наблюдались с расстояния 10 футов под углом не менее 50 футов с нормальным зрением. Если наблюдается какое-либо различие из-за наличия солевых отложений, рейтинг отображается как «высохший».Если никакой разницы не наблюдается, рейтинг указывается как «не выцветший».
2.1.9. Тест на радиоактивность
Радиоактивность смеси оптимального состава была исследована Отделом физики здоровья Комиссии по атомной энергии Бангладеш.
2.1.10. Изменение процесса и времени отверждения
Было исследовано влияние четырех различных процессов отверждения, т. Е. На неподвижном воздухе, с разбрызгиванием воды дважды в день, выдерживанием образца под влажной тканью и выдерживанием образца в воде в течение семи дней.Наконец, был изучен эффект длительного отверждения. Для получения оптимального состава и разного давления уплотнения один комплект кирпичей выдерживали на воздухе в течение пяти недель. Другой набор сушили на воздухе в течение одной недели, а затем в течение четырех недель под водой. Затем сравнили их прочность на сжатие. Различие в прочности на сжатие исследовали с помощью инфракрасной спектроскопии с преобразованием Фурье (FTIR).
3. Результаты и обсуждение
3.1. Влияние песка на прочность на сжатиеОбразцы T1 — T4 (таблица 2) были подготовлены для определения влияния количества песка на прочность на сжатие.Прочность на сжатие может быть увеличена с 113,46 кг / см 2 до 165,57 кг / см 2 за счет увеличения количества песка с 10 до 40% (Рисунок 3). Максимальная прочность была обнаружена для 40% песка — 50% летучей золы — 10% известкового кирпича с 2% гипса. Поскольку основной целью данного исследования было массовое использование летучей золы, оптимальное количество песка было принято равным 30%, что дало прочность на сжатие 155,20 кг / см 2 . Повышение механической прочности с увеличением содержания песка в большей степени объясняется повышенным количеством свободного SiO 2 , который легче реагирует с известью, чем зола-унос [8] .
3.2. Определение оптимального содержания извести и летучей золыРезультаты испытаний на прочность при сжатии, проведенные на образцах Т5 — Т9, показали, что максимальная прочность может быть достигнута с 15% извести и 55% летучей золы (Рисунок 4). Предел прочности на сжатие для этой композиции составил 181,75 кг / см 2 .
Рисунок 3 . Влияние добавки песка на прочность на сжатие
Рисунок 4 . Влияние добавки извести на прочность на сжатие
3.3. Оптимальное количество добавленного гипсаИзменение прочности на сжатие образцов T10 — T13, содержащих различное количество гипса, показано на рисунке 5. Можно видеть, что прочность на сжатие увеличилась с 181,75 кг / см 2 для 2-процентного гипса до 287,78 кг / см 2 для оптимального содержания гипса 14%.
3.4. Влияние давления формования кирпича на прочность на сжатиеИспытания на прочность на сжатие образцов Т14 — Т16 показали, что прочность на сжатие увеличивается с увеличением давления формования кирпича (рис. 6).Образец T16 показал максимальную прочность на сжатие 417,96 кг / см 2 для давления формования кирпича 3000 фунтов на квадратный дюйм.
Рисунок 5 . Влияние добавки гипса на прочность на сжатие
Рисунок 6 . Влияние давления формования кирпича на прочность на сжатие
3,5. МикроструктураОбразцы Т14, Т15 и Т16 представляют собой образцы с оптимальным составом и различными давлениями формования кирпича.Микроструктура и другие свойства, помимо прочности на сжатие этих образцов, были исследованы для оптимизации давления формования кирпича. На рис. 7 показано, что как индивидуальный размер пор, так и общая пористость уменьшались с увеличением давления формования кирпича. Этого следовало ожидать.
Рисунок 7 . Микроструктура кирпичей, формованных под давлением (a) 1000 фунтов на квадратный дюйм (b) 2000 фунтов на квадратный дюйм (c) 3000 фунтов на квадратный дюйм [Все увеличение 500X]
3,6. Свойство усадкиЗаметной усадки не произошло, как это было измерено для образцов T14, T15 и T16.
3,7. Удельный весС увеличением давления формования кирпича объемный вес кирпича увеличивался (рисунок 8). Но выше 2000 фунтов на квадратный дюйм изменение плотности было незначительным. Максимальная плотность 1,81 г / куб.см была обнаружена для кирпичей, сформированных под давлением 3000 фунтов на квадратный дюйм, что намного ниже плотности кирпича на основе обожженной глины.
3.8. Начальная скорость абсорбции (IRA)Начальная скорость абсорбции кирпичей, изготовленных под давлением 1000 фунтов на квадратный дюйм, превышает 30 г, поэтому согласно ASTM C 67-00 эти кирпичи следует смачивать перед укладкой (Рисунок 9).С увеличением давления формования кирпича IRA упало ниже 30 г / м2. Самый низкий IRA 14,84 г был обнаружен для давления 3000 фунтов на квадратный дюйм. Так что эти кирпичи не нужно смачивать перед кладкой.
3.9. Впитывающая способностьКак показано на Рисунке 9 впитывающая способность составляла 14,63% для давления формования кирпича 1000 фунтов на квадратный дюйм. С увеличением давления это значение упало до 11,58% для давления 3000 фунтов на квадратный дюйм. Изменение абсорбционной способности при давлении выше 2000 фунтов на квадратный дюйм было незначительным.
Рисунок 8 . Влияние давления формования кирпича на удельную объемную массу
Рисунок 9 . Влияние давления формования кирпича на абсорбционную способность и IRA
3.10. Кажущаяся пористость, открытые поры и непроницаемые порыВлияние давления формования кирпича на кажущуюся пористость, открытые поры и объем закрытых пор показано на рисунке 10. Видимая пористость уменьшалась с увеличением давления. Выше 2000 фунтов на квадратный дюйм изменение было незначительным.Объем открытых пор также следовал той же тенденции. Как бы то ни было, на объем непроницаемых пор не повлияло давление формования кирпича. Этот результат указывает на то, что большее уплотнение при том же давлении возможно, если закрытые поры могут быть уменьшены посредством контроля размера частиц.
Рисунок 10 . Влияние давления формования кирпича на кажущуюся пористость, открытые поры и объем непроницаемых пор
3.11. ВыцветаниеБыло обнаружено, что кирпичи оптимального состава «не выцветают».Как видно на Фигуре 11, на поверхности испытанного кирпича не было обнаружено соли.
Рисунок 11 . Испытание высыхания кирпича оптимального состава
3.12. РадиоактивностьРадиоактивность цезия-137 была ниже предела обнаружения установки, т.е. ниже 1,54 Бк / кг. Так что эти кирпичи не представляют опасности как источник радиоактивности.
3,13. Влияние процесса отвержденияОбразец T17 был отвержден на неподвижном воздухе. Образцы Т18, Т19 и Т20 обрабатывали водным спреем два раза в день, держа образец под влажной тканью и погружая образец под воду соответственно.Максимальная прочность на сжатие 442,96 кг / см 2 была найдена для образца T18 (рисунок 12).
Рисунок 12 . Влияние процесса отверждения на прочность на сжатие
3,14. Эффект периода отвержденияОдин комплект кирпичей выдерживали в течение семи дней на воздухе; один подход — пять недель на воздухе, другой — первые четыре недели в воде, а затем одна неделя на воздухе. Максимальная прочность 877,36 кг / см 2 была обнаружена для кирпичей, сформированных под давлением 3000 фунтов на квадратный дюйм и отвержденных в воде в течение четырех недель, а затем одной недели на воздухе.FTIR-анализ показал (рис. 14), что, когда кирпичи выдерживались в воде в течение четырех недель, а затем одна неделя на воздухе вместо пяти недель на воздухе, более прочная межмолекулярная связь ОН-О стала преобладающей над более слабой внутримолекулярной связью ОН.
Рисунок 13 . Влияние процесса отверждения на прочность на сжатие
Рисунок 14 . FTIR-анализ кирпичей, отвержденных при различных условиях отверждения
4.Выводы
Из этого исследования можно сделать следующие основные выводы:
• Оптимальным составом необожженных кирпичей из золы-уноса, силиката, извести и гипса было 55 процентов летучей золы, 30 процентов песка, 15 процентов извести и 14 процентов гипса, а оптимальное давление формования кирпича составляло 3000 фунтов на квадратный дюйм.
• Повышенное давление формования кирпича показало увеличение прочности на сжатие и удельного объемного веса, а также снижение IRA, абсорбционной способности, кажущейся емкости и объема открытых пор. Было обнаружено, что объем непроницаемых пор практически не зависит от давления формования кирпича.
• Для оптимального состава и давления кирпич обладает следующими свойствами:
1 Без усадки.
2 Объемный вес устройства: 1,81 г / см 3 .
3 Начальная скорость абсорбции (IRA): 14,84 г. Так что эти кирпичи не нужно смачивать перед кладкой.
4 Поглощающая способность: 11,58%.
5 Видимая пористость: 20,99%.
6 Объем открытых пор: 9,23 см 3 .
7 Объем непроницаемых пор: 34,74 см 3 .
8 Для оптимального состава и давления кирпичи, отверждаемые под струей воды два раза в день, показали максимальную прочность на сжатие 442,96 г / см 2 .
Наконец, кирпичи, сформированные под давлением 3000 фунтов на квадратный дюйм, показали максимальную прочность 877,36 кг / см 2 при отверждении в воде в течение четырех недель с последующей неделей на воздухе, а прочность определялась степенью межмолекулярной связи ОН-О.
Несмотря на то, что до того, как будет сделан окончательный комментарий, потребуются дальнейшие исследования, кирпичи из золы-уноса, силиката, известняка и гипса, произведенные в этом исследовании, кажутся подходящими для использования в качестве строительного материала.Производство этого типа кирпича (если это технически и коммерчески жизнеспособно), безусловно, будет способствовать переработке летучей золы и, следовательно, минимизировать негативное воздействие на окружающую среду.
Список литературы
[1] | Goni, S. Guerrero, A. Luxan, M.P. и Macias, A. 2003. Активация пуццолоновой реакции летучей золы в гидротермальных условиях, Cem Concr Res , Vol. 33, стр 1399-405. | ||
В артикуле | CrossRef | ||
[2] | Klimesch, D.С. и Рэй, А. 1998. Влияние размера частиц кварца на образование гидрограната во время автоклавирования при 180 ℃ в системе CaO – Al 2 O 3 –SiO 2 –H 2 O, Cem Concr Res , Vol. 28, с. 1309-16. | ||
В статье | |||
[3] | Байкал и Довен, А.Г. 2000. Утилизация летучей золы в процессе гранулирования; теория, области применения и результаты исследований, Resour Conserv Recy, Vol.30, с. 59-77. | ||
В статье | CrossRef | ||
[4] | Iyer, R.S. и Скотт, Дж. 2001. Летучая зола электростанции — обзор использования добавленной стоимости вне ресурсов строительной индустрии, Conserv Recy , Vol. 31, стр. 217-28. | ||
В артикуле | CrossRef | ||
[5] | Пимракса, К.Вильгельм, М. Кохбергер, М. и Врусс, В. 2001. Новый подход к производству кирпичей из 100% летучей золы, Международный симпозиум по утилизации золы , Доступно по адресу: http://www.flyash.info/ повестка дня.html. | ||
В статье | |||
[6] | Poon, CS Kou, SC и Lam, L. 2002. Использование переработанных заполнителей в формованных бетонных кирпичах и блоках, Constr Build Mater , Vol.С. 281-9. | ||
В артикуле | |||
[7] | Токтай М.С. и Этин Б. 1991. Механическая прочность и водопоглощающие свойства автоклавных кирпичей из золы-уноса, ТММОБ, Публикация Палаты инженеров-строителей , Vol. 1. С. 385-394. | ||
В статье | |||
[8] | Cicek, T. akson-quick.ru © 2019
|