Завод ДСП с ламинацией (15000 м3 в год)
1. Участок I подготовки сырья
2. Участок II сушки сырья
3. Участок III клееподготовки и осмоления
4. Участок IV формирования и подпрессовки плит
5. Участок V горячего прессования плит
6. Участок VI форматирования готовой продукции
Схема производства ДСП 10 000 — 15 000 м3/год
Древесно-стружечная плита (ДСП, ДСтП) — листовой композиционный материал, изготовленный путем горячего прессования древесных частиц, преимущественно стружки, смешанных со связующим неминерального происхождения с введением при необходимости специальных добавок на одно- и многоэтажных прессах. Типы смол могут использоваться разные, основное их назначение — выступить в роли связующего вещества. Плотность таких плит составляет 660-750 кг/м3 в зависимости от толщины. Класс эмиссии Е1 делает их крайне безвредными и позволяет использовать данную продукцию внутри помещений в непосредственной близости от людей.
Внешне сорт ДСП можно опознать по качеству обработки поверхности плиты. Более качественный первый сорт — это шлифованная ДСП, поверхность второго сорта не столь безупречна и имеет некоторые дефекты. Кроме того, существует еще ряд различий в сортах древесностружечной плиты: поверхность мелкоструктурная или обычная, по виду марки П-А, П-Б (зависит от механических показателей), по водостойкости (обычная или повышенная), по содержанию формальдегидной смолы (Е1, Е2). Плиты ДСП, в основном, зависят от плотности, формы и размера древесных частиц, а также от количества и качества связующего материала. Различают плиты одно-, трех- и пятислойные. Не рекомендуется применять в помещениях с повышенной влажностью, в таких помещениях следует применять только гидрофобизованные или защищенные покрытиями плиты.
Ламинированное ДСП, это обыкновенное шлифованное ДСП, покрытое посредством физико-химического процесса бумажно-смоляными пленками. Процесс изготовления ЛДСП осуществляется под действием температуры (140-210 С) и давления (25-28 МПа). В результате этого процесса декоративно-защитный слой на плите ламинированного ДСП образуется за счет растекания смолы по поверхности плиты с последующим затвердеванием и образованием прочного покрытия.
Одним из основных достоинств ДСП является прочность, которая у ДСП ни чуть не хуже прочности натуральной древесины. Ещё одним достоинством шлифованного ДСП является легкость обработки, несмотря на большую плотность.
Сферы применения ДСП:
— обшивка стен и крыш;
— изготовление стеновых панелей;
— изготовление полов, оснований под ковровые и линолеумные покрытия, перегородок;
— изготовление съемной опалубки;
— изготовление мебели, стеллажей, полок, упаковки;
— строительство ограждений и разборных конструкций;
— использование для декорирования и отделки, благодаря оригинальной текстуре поверхности.
Шлифованная ДСП Ламинированная ДСП (ЛДСП)
Плотность: по плотности ДСП делится на плиту малой плотности (менее 550 кг/м³), средней (550—750 кг/м³) и высокой (более 750 кг/м³).
Номинальные размеры плит:
Параметр | Значение, мм | Предельное отклонение, мм |
Толщина | От 8 до 38 | ±0,3* (для шлифованных плит) −0,3/ +1,7 (для нешлифованных плит) |
Длина | 1830, 2040, 2440, 2500, 2600, 2700, 2750, 2840, 3220 3500, 3600, 3660, 3690, 3750, 4100, 5200, 5500, 5680 | ± 5,0 |
Ширина | 1220, 1250, 1500, 1750, 1800, 1830, 2135, 2440, 2500 | ± 5,0 |
Технологический поток производства ДСП
рис.1
Ведущим производителем и потребителем ДСП является Западная Европа, за которой следуют Северная Америка и Восточная Европа. В России объемы потребления на ДСП составляют около 4,0 млн. м3/год, а текущий объем производства — 3,6 млн. м3/год, импорт — 0,4 млн. м3/год. Крупным потребителем ДСП является Китай, но лишь небольшая часть китайского спроса (7-8%) удовлетворяется за счет международной торговли. ДСП – относительно дешевая продукция и потому практически не является объектом международной и трансконтинентальной торговли. Так, российские производители экспортируют лишь около 5% своей продукции в страны СНГ (см. рис. 2).
рис.2
В Западной Европе ожидается незначительный рост спроса на ДСП; в период до 2015 г. темпы прироста составят 1,1%/год. В России годовые темпы прироста спроса прогнозируются на уровне 5,2%, что означает около 270 000 м3/год в объемном выражении. Значительный рост спроса (3,7%/год) ожидается также в др. странах Восточной Европы. По расчетам, прирост потребления ДСП в Японии не превысит 0,9%/год. В Северной Америке в период 2004-2015 гг. ожидается сокращение спроса на уровне -1,2% /год. Наиболее динамичный рост будет происходить в Китае; здесь темпы прироста составят 8,3%/год, т.е. около 870 000 м3/год.
Баланс спроса и предложения на ДСП в России
Размеры плит должны соответствовать указанным в табл. 1. ГОСТ 10632-89
Параметр | Значение, мм | Предельное отклонение, мм |
Толщина | От 8 до 38 | ±0,3 |
Длина | 1830, 2040, 2440, 2500, 2600, 2700, 2750, 2840, 3220 3500, 3600, 3660, 3690, 3750, 4100, 5200, 5500, 5680 | ± 5,0 |
Ширина | 1220, 1250, 1500, 1750, 1800, 1830, 2135, 2440, 2500 | ± 5,0 |
Примечания:
1. Толщина нешлифованных плит устанавливается как сумма номинального значения толщины шлифованной плиты и припуска на шлифование, который не должен быть более 1,5 мм.
3. По согласованию с потребителем допускается выпускать плиты форматов, не установленных в табл. 1.
4. Отклонение от прямолинейности кромок не должно быть более 2 мм.
5. Отклонение от перпендикулярности кромок плит не должно быть более 2 мм на 1000 мм длины кромки.
6. Перпендикулярность кромок может определяться разностью длин диагоналей пластин, которая не должна быть более 0,2% длины плиты.
7. Плиты должны изготовляться с применением синтетических смол, разрешенных Минздравом.
8. Содержание вредных химических веществ, выделяемых плитами в производственных помещениях, не должно превышать предельно допустимых концентраций, утвержденных Минздравом для воздуха рабочей зоны производственных помещений.

9. В условиях эксплуатации количество химических веществ, выделяемых плитками, не должно превышать в окружающей среде предельно допустимых концентраций, утвержденных Минздравом для атмосферного воздуха.
Физико-механические показатели плит плотностью от 550 кг/м2 до 820 кг/м2 должны соответствовать нормам, указанным в табл. 2. ГОСТ 10632-89
Наименование показателя | Норма для плит марок | |
П-А | П-Б | |
Влажность, % Тн* Тв* Разбухание по толщине: за 24 ч (размер образцов 100Х100 мм), %, (Тв) за 2 ч (размер образцов 25Х25 мм), % (Тв)** Предел прочности при изгибе, МПа, для толщин,мм (Тн): от 8 до 12 » 13 » 19 » 20 » 30 Предел прочности при растяжении перпендикулярно пласти плиты, МПа, для толщин, мм (Тн): от 8 до 12 » 13 » 19 » 20 » 30 Удельное сопротивление выдергиванию шурупов, Н/мм (Тн)***: из пласти » кромки Покоробленность, мм (Тв) Шероховатость поверхности пласти Rm, мкм (Тв), для образцов а) с сухой поверхностью: от для шлифованных плит с обычной поверхностью от для шлифованных плит с мелкоструктурной поверхностью от для нешлифованных плит б) после 2 ч вымачивания***: для шлифованных плит с обычной поверхностью для шлифованных плит с мелкоструктурной поверхностью для нешлифованных плит | 5 22 18 0. 60 50 150 | 5 33 16 0.30 55 63 180 |
** Для плит повышенной водостойкости.
*** Определяется по согласованию изготовителя с потребителем.
Качество поверхности плит должно соответствовать нормам, указанным в табл. 3. ГОСТ 10632-89
Дефекты по ГОСТ 27935 | Норма для плит | |||
шлифованных, сортов: | не шлифованных, сортов: | |||
I | II | I | II | |
Углубления (выступы) или царапины на пласти | Не допускаются | Допускаются на 1 м поверхности плиты не более двух углублений диаметром до 20 мм и глубиной до 0,3 мм или двух царапин длиной до 200 мм | Допускаются на площади не более 5% поверхности плиты, глубиной (высотой), мм, не более: 0,5 | 0,8 | |
Парафиновые и масляные пятна, а также пятна от связующего | То же | Допускаются на 1 м поверхности плиты пятна площадью не более 1 см в количестве 2 шт.![]() | Допускаются на площади не более 2% поверхности плиты | |
Пылесмоляные пятна | » | Допускаются на площади не более 2% поверхности плиты | Допускаются | |
Сколы кромок | Не допускаются (единичные глубиной по пласти 3 мм и менее протяженностью покромке15 мм и менее не учитываются) | Допускаются в пределах отклонений по длине (ширине) плиты | ||
Выкрашивание углов | Не допускается (длиной по кромке 3 мм и менее не учитываются) | Допускается в пределах отклонений по длине (ширине) плиты | ||
Дефекты шлифования(недошлифовка, прошлифовка, линейные следы от шлифования, волнистость поверхности) | Не допускаются | Допускаются площадью не более 10% площади каждой пласти | Не определяют | |
Отдельные включения частиц коры на пласти плиты размером, мм, не более | 3 | 10 | 3 | 10 |
Отдельные включения крупной стружки: для плит с мелкоструктурной поверхностью | Допускаются в количестве 5 шт. | |||
для плит с обычной поверхностью | Не определяют |
Допускается для плит с обычной поверхностью не более 5 шт. отдельных включений частиц коры на 1 м пласти плиты размером, мм: для I сорта более 3 до 10; для II сорта — более 10 до 15.
В зависимости от содержания формальдегида плиты изготовляют двух классов эмиссии, указанных в табл. 4. ГОСТ 10632-89
Класс эмиссии формальдегида | Содержание формальдегида, мг на 100 г абсолютно сухой плиты |
Е1 | До 10 включ. |
Е2 | Св. 10 до 30 включ. |
Е3 | Св. 30 до 60 включ. |
Допускается изготовлять плиты класса эмиссия формальдегида Е3 до 01.01.1991г.
ЛИНИЯ ПО ПРОИЗВОДСТВУ ПЛИТ ДСП ПРОИЗВОДИТЕЛЬНОСТЬЮ 10000 — 15000 М3/ГОД
№ |
Артикул |
Наименование |
Технические характеристики |
Кол-во |
Мощность (кВт) |
||
1 |
Секция подготовки сырья |
||||||
101 |
Zh2110/12 |
Конвейер ленточный |
Ширина=1 м; Длина=12 м |
1 |
4,0 |
||
102 |
Bh3110 |
Барабанная дробилка |
Диаметр барабана Ø=1000 мм |
1 |
200 |
||
103 |
BZ1110/26 |
Конвейер ленточный |
Ширина=1 м; Длина=26 м |
1 |
5,5 |
||
104 |
BP1110/7 |
Конвейер ленточный передвижной |
Ширина=1 м; Длина=7 м |
1 |
3,0 |
||
105 |
B2750 |
Бункер сырья (щепы) |
Объем=50 м3 |
3 |
3×15,0 |
||
106 |
BZ1160/6 |
Ленточный конвейер |
Ширина=0,6 м; Длина=6 м |
3 |
3×2,2 |
||
107 |
P-468 |
2-х барабанная дробилка для получения стружки |
Диаметр барабана Ø=800 мм |
3 |
3×200,0 |
||
108 |
MS5-54 |
Пневмотранспортер |
Циклон с роторным клапаном для регулировки скорости потока |
1 |
37,0 |
||
109 |
M32/22 |
Скребковый конвейер |
Ширина=0,8 м; Длина=22 м |
1 |
11,0 |
||
110 |
BL2650 |
Бункер для полученной стружки |
Объем=50 м3 |
3 |
3×15,0 |
||
2 |
Секция сушки и сортировки | ||||||
201 |
BW1160/16 |
Конвейер ленточный |
Ширина=0,6 м; Длина=16 м |
3 |
3×3,0 |
||
202 |
B233 |
Роторная сушка |
Диаметр корпуса внешний Ø=2,9 м |
3 |
2×70,9 |
||
203 |
BW1160/6 |
Конвейер ленточный |
Ширина=0,6 м; Длина=6 м |
3 |
3×2,2 |
||
204 |
BM1110/9 |
Конвейер ленточный |
Ширина=1 м; длина=9 м, с магнитным сепаратором |
1 |
4,0 |
||
205 |
B1437 |
3-х уровневое вибросито |
6×30 мм, 3×15 мм |
1 |
4,0 |
||
206 |
MS5-54 No. |
Пневмотранспортер |
Циклон с роторным клапаном для регулировки скорости потока |
1 |
37,0 |
||
207 |
MS5-54 No.8 |
Пневмотранспортер |
Циклон с роторным клапаном для регулировки скорости потока |
1 |
45,0 |
||
208 |
BR1160/6 |
Конвейер ленточный |
Ширина=0,6 м; Длина=6 м |
1 |
2,2 |
||
209 |
B5612 |
Дробилка для получения сырья тонкой фракции |
Диаметр барабана Ø=1200 мм |
1 |
200,0 |
||
210 |
MS5-54 No. |
Пневмотранспортер |
Циклон с роторным клапаном для регулировки скорости потока |
1 |
17,2 |
||
211 |
BC2750 |
Бункер для внутреннего слоя |
Объем=30 м3 |
1 |
8,5 |
||
212 |
BC2450 |
Бункер для внешних слоев |
Объем=15 м3 |
1 |
8,5 |
||
213 |
XC-12 | Система пылеудаления | — | 1 | — | ||
3 |
Секция клееподготовки и осмоления |
||||||
301 |
GS-1 |
Емкость для хранения клея |
Объем=20 м3 |
1 |
— | ||
302 |
GS-2 |
Насосная установка для клея |
Расход=250 л/мин |
1 |
2,2 |
||
303 |
GS-3 |
Помпа для подачи клея для внешних слоев |
Расход=0~60 л/мин |
1 |
1,5 |
||
304 |
GS-4 |
Помпа для подачи клея для внутреннего слоя |
Расход=0~60 л/мин |
1 |
1,5 |
||
305 |
GH-1 |
Клеевой миксер |
Объем=1,5 м3 |
1 |
2,2 |
||
306 |
GY-2 |
Бункер с клеем для внешних слоев плиты |
Объем=1,5 м3 |
1 |
1,5 |
||
307 |
GP-5 |
Бункер с клеем для внутреннего слоя плиты |
Объем=1,5 м3 |
1 |
1,5 |
||
308 |
BX1160/3 |
Конвейер ленточный |
Ширина=0,6 м; Длина=16 м |
2 |
2×3,3 |
||
309 |
BZ1250 |
Бункер осмоления стружки |
Ø=510 мм |
2 |
2х30,0 |
||
310 |
BR1160/22 |
Конвейер ленточный |
Ширина=0,6 м, Длина=22 м; с магнитным сепаратором |
2 |
2×4,0 |
||
311 |
BL12342/4 |
Виброконвейер |
Ширина=0,42 м; Длина=4 м |
2 |
2×4,0 |
||
4 |
Секция формирования и предварительного прессования |
||||||
401 |
B4313 |
Воздушнопоточный формовщик |
Рабочая ширина=1,83 м |
1 |
85,0 |
||
402 |
B8314/2 |
Роликовый предпресс |
Диаметр ролика Ø=0,96 м; Длина=2 м |
1 |
33,0 |
||
403 |
BJ1113 |
Форматно-раскроечный станок |
Пильный диск Ø=0,4 м; Рабочая ширина=1,3 м |
1 |
1,5+2,2 |
||
404 |
BB1250 |
Кромкообрезной станок |
Пильный диск Ø=0,3 м |
2 |
2х1,1 |
||
405 |
BY1232/3 |
Рециркуляционный шнековый конвейер |
Ширина=0,3 м; Длина=3 м |
1 |
3,0 |
||
406 |
BY1160/19 |
Рециркуляционный шнековый конвейер |
Ширина=0,6 м; Длина=19 м |
1 |
4,0 |
||
407 |
BY1015 |
Синхронный конвейер 1 |
Ширина=2 м |
1 |
2,2 |
||
408 |
BY1315 |
Конвейер ускоритель 1 |
Рабочая ширина=2 м; Длина=4 м |
1 |
2,2 |
||
409 |
BZY1315 |
Конвейер ускоритель 2 |
Рабочая ширина=2 м; Длина=4 м |
1 |
2,2 |
||
410 |
Bh2399 |
Система взвешивания |
— |
1 |
0,2 |
||
411 |
BY1315 |
Конвейер ускоритель 1 |
Рабочая ширина=2м; Длина=4м |
1 |
2,2 |
||
412 |
BY1315 |
Конвейер ускоритель 2 |
Рабочая ширина=2м; Длина=4м |
1 |
2,2 |
||
413 |
BZ1115/4 |
Бункер предварительной загрузки |
Рабочая ширина=2м; Длина=4,5м |
1 |
2,2+1,1 |
||
5 |
Секция горячего прессования |
||||||
501 |
B124×8/22 |
Загрузочный станок |
13 пролетов; |
1 |
3,0 |
||
502 |
B124×8/22 |
Горячий пресс |
13 пролетов; Расстояние между плитами =120 мм; Время прессования 15 сек. ![]() |
1 |
223,0 |
||
503 |
B114X8/15 |
Разгрузочный станок |
13 пролетов |
1 |
28,6 |
||
504 |
B114/V |
Система удаления горячего пара и паров клея из зоны прессования |
— |
2 |
2х4,0 |
||
505 |
DX-2 | Корпус системы удаления пара | — |
1 |
— | ||
506 |
BY354 |
Конвейер |
Ширина=0,4м; Длина=3,6м |
1 |
0,75 |
||
6 | Секция охлаждения и форматирования плит | ||||||
601 |
BJ422 |
Подающий конвейер |
— |
1 |
1,1 |
||
602 |
B4230 |
Система охлаждения плит |
— |
1 |
2,2 |
||
603 |
BC423 |
Конвейер на выходе |
— |
1 |
1,1 |
||
604 |
BY3715 |
Подающий конвейер |
— |
1 |
1,1 |
||
605 |
B1112 |
Пильный станок продольного форматирования |
Рабочая ширина=1,83 м |
1 |
2х4+1,5 |
||
606 |
BY1122 |
Ленточный конвейер |
— |
1 |
1,1 |
||
607 |
BY3215 |
Конвейер реверсивный |
— |
1 |
1,1+3,0 |
||
608 |
B2124 |
Пильный станок поперечного форматирования |
Рабочая ширина=2,44 м или 2,75 м |
1 |
2х4+1,1 |
||
609 |
BY3920 |
Разгрузочный роликовый конвейер |
— |
1 |
0,75 |
||
610 |
BJ114X8/2 |
Гидравлический стол |
Грузоподъемность ≤2 тонн; с роликами |
1 |
3,0 |
||
611 |
B-14 |
Укладчик |
— |
1 |
1,5 |
||
612 |
BY114 |
Подъемник с роликами |
— |
1 |
2,2 |
||
613 | ZX-3 | Система пылеудаления | — | 1 | 7,5 | ||
7 | Секция калибрования и шлифования | ||||||
701 |
BY114 |
Подъемник с роликами |
— |
2 |
2×1,5 |
||
702 |
BJ116X8/2 |
Гидравлический стол |
Грузоподъемность≤2 тонн |
2 |
2X1,5 |
||
703 |
BY |
Подающий роликовый конвейер |
— |
1 |
1,5 |
||
704 |
BG2719 |
4-х агрегатный калибровальный станок |
Калибрование плиты в размер |
1 |
110х2+90х2+11 |
||
705 |
BY |
Конвейер |
— |
1 |
1,5 |
||
706 |
BG2719A |
4-х агрегатный калибровально-шлифовальный станок |
Шлифование плиты |
1 |
75×2+55×2+15 |
||
707 |
BY-12 |
Ленточный конвейер |
— |
1 |
1,5 |
||
708 |
BY-14 |
Ленточный конвейер |
— |
1 |
1,5 |
||
709 |
CV-2 |
Разгрузочный укладчик плит |
— |
1 |
3 |
||
710 | BG-21 | Система удаления | — | 1 | 11 | ||
711 | SC-7 | Панель контроля управления | — | 1 | — |
линий ламинирования ДСП лист формата 8/4 (1220*2440 мм) без упаковки товара |
формат 9/6 (1875*2750 мм) |
линий ламинирования лист формата 4/8 (1220*2440 мм) без упаковки товара |
формата 6/9 (1875*2750 мм) |
ИСКЛЮЧЕНИЯ ИЗ КОМПЛЕКТНОСТИ ПОСТАВКИ И ЛОКАЛЬНО ПРИОБРЕТАЕМЫЕ МАТЕРИАЛЫ ДЛЯ МИНИ ЗАВОДА ДСП
Здания/фундаменты/доставка/транспорт
- Полное производственное здание с отоплением, освещением и т.
п.
- Все фундаменты, кладки, проведение коммуникаций в фундаментах и другие связанные с установкой строительные работы, крепежные элементы и приспособления, кабельные короба, крышки и проходы и т.п.
- Доставка, разгрузка и требующееся хранение оборудования, а также перевозка машин к месту установки.
- Кран, автокран/ специальные краны, грузоподъемники, подъемное снаряжение, инструменты для выгрузки, перемещение по заводу и сборки линии.
- Санитарно-гигиенические нормы для персонала.
- Защитные панели для пакетов исходных и готовых изделий.
- Сырьевой материал, необходимый для тестовых испытаний в достаточном количестве.
- Крановые системы, автопогрузчики, инструменты для работы на линии.
- Лабораторное оборудование.
- Все переходы и платформы, монтажные леса, включая поручни безопасности, лестницы, защитные ограждения, необходимые для предотвращения несчастных случаев на работе.
- Масляное наполнение гидропривода пресса.
Сжатый воздух/удаляемый воздух/вода
- Воздушный компрессор со всеми линиями подачи к индивидуальным секциям линии сухого, сжатого воздуха.
- Выводящий агрегат, включая трубы подачи и возврата от индивидуальных секций прессовой линии.
- Вытяжной короб над прессом и другими компонентами линии.
Электрика/передача данных
- Распределительная панель и главная энергоподача к отдельным коммутаторным шкафам всей линии, а также электроуправление всеми компонентами линии локальной поставки.
- Заземление всей линии.
- Кабельные связи/кабельные шкафы и их установка/подготовка для подсоединения кабелей между главными шкафами выключателей и панелей управления линией и т.п.
- Программный модуль.
- Модем для онлайн-контроля программного потока в ЧПУ.
- Одна линия связи.
Устройства безопасности
- Все специальные системы безопасности, такие как запорные цепи т.п., требуемые местными властями.
- Все меры, требуемые местными властями, правилами по экологической безопасности, а также все требования по шуму, загрязнениям земли, воды, воздуха.
- Оборудование по пожарной безопасности.
- Возможно необходимые шумоизоляционные кабины для разделительных пил, обрезных агрегатов и т.п.
Технология производства ДСП (древесностружечных плит)
Древесностружечные плиты за последние 10—15 лет стали, очевидно, одним из самых известных и распространенных древесных материалов. Они являются основным конструкционным материалом в производстве мебели, а в последнее время получают все большее признание и в строительстве, в частности в производстве малоэтажных домов.
Сырье для древесностружечных плит — различного вида отходы лесопиления, лесозаготовок, деревообработки (горбыли, рейки, откомлевки, сучья, срезки, стружка, опилки), а также низкокачественные круглые лесоматериалы. Становится понятным значимость этого производства: из отходов и низкокачественной древесины получается материал, из которого изготовляют высококачественные, долговечные изделия.
Все кусковые отходы измельчаются в щепу на рубительных машинах. Из щепы, а также из стружки, отходов и опилок на специальных роторных станках приготовляется стружка. Из круглых лесоматериалов стружка изготовляется или непосредственно из бревна на станках с ножевым валом, или по схеме щепа — стружка, когда сначала изготовляется щепа, а затем из щепы стружка. Перед подачей бревен на струженный станок их разрезают на мерные заготовки (обычно длиной 1 м).
Стружка должна иметь определенные, наперед заданные размеры (толщина 0,2—0,5 мм, ширина 1 — 10 мм, длина 5—40 мм). В наружные слои плиты направляется стружка наименьших размеров. Кроме соблюдения размеров необходимо также следить, чтобы стружка была плоской, равномерной толщины, с ровной поверхностью. Стружка для наружных слоев после стружечных станков проходит дополнительное измельчение на дробилках (здесь уменьшается ширина) или в мельницах, где изменяется толщина. Последняя операция имеет особое значение для плит, которые отделываются методом ламинирования, так как в этом случае предъявляются высокие требования к качеству их поверхности.
Изготовленная сырая стружка хранится в бункерах, куда подается системой пневмотранспорта или механическими транспортерами. Из бункеров сырая стружка подается в сушилки. Сушить стружку необходимо до влажности 4—6%, а для внутреннего слоя — до 2—4%. Поэтому стружку разных слоев сушат в отдельных сушилках. В производстве древесностружечных плит используются, как правило, конвективные сушилки, в большинстве случаев барабанного типа. В топке сушилки сжигается газ или мазут, температура в ней 900— 1000° С. На входе в барабан Температура сушильного агента достигает 450—550° С, на выходе она от 90 до 120° С. Барабан имеет диаметр 2,2 м и длину 10 м, устанавливается он с наклоном в 2—3° в сторону входа сырой стружки.
После сушки стружка сортируется или на механических (ситовых) агрегатах, или пневматически. На этих машинах происходит разделение стружки на фракции для наружных и внутренних слоев. На этом заканчивается изготовление стружки. Автор должен заметить, что эта часть технологического процесса во многом предопределяет успешное выполнение последующих операций, производительность процесса и особенно качество плит. Поэтому приготовлению стружки (работе оборудования на этом участке, квалификации операторов) уделяется большое внимание.
Стружка смешивается со связующим в специальных агрегатах, Называемых смесителями. Операция эта сложная, поскольку технология производства требует покрытия связующим каждой стружки. Неосмоленные стружки не склеиваются, а излишняя смола на стружке приводит к перерасходу связующего и плохому качеству плит. Связующее в смеситель подается в виде растворов. Их концентрация в потоке наружного слоя 53— 55%, внутреннего слоя несколько больше (60—61%). В настоящее время наиболее распространены смесители, в которых распыленное связующее (размеры частиц 30—100 мкм) факелом направляется на поток взвешенных в воздухе стружек. Эти два потока перемешиваются, связующее осаждается на поверхности стружек. Смесители, как правило, нуждаются в тонком регулировании, при котором соблюдаются строгие количественные соотношения между стружкой, смолой и отвердителем. После осмоления стружка ленточными или скребковыми транспортерами направляется в формирующие машины.
Формирующие машины принимают осмоленную стружку и высыпают ее ровным слоем (ковром) на проходящие под ними поддоны или ленточные транспортеры. Стружечный ковер — это непрерывная лента определенной ширины и толщины. Он разделяется на пакеты, из которых и образуются в последующем при горячем прессовании плиты. Естественно, что равномерность насыпки ковра прямым образом влияет на качество плит (равноплотность, равнотолщинность). Кроме того, формирующие машины должны насыпать во внешние слои мелкие стружки.
Конвейер перемещает пакеты, которые после прохождения пресса для подпрессовки становятся плотными, обладающими транспортной прочностью брикетами. В настоящее время в промышленности древесностружечных плит известно два принципиально различных типа главных конвейеров. Они различаются тем, что в одном случае пакеты (а затем брикеты) перемещаются на металлических поддонах, в другом типе главного конвейера — на ленточных транспортерах, когда прессование бесподдонное. Каждая схема главного конвейера имеет преимущества и недостатки. Поддонный способ более простой и надежный, но плиты получаются с большей разнотолщинностью, расход тепловой энергии больше. Бесподдонный способ обеспечивает некоторую экономию энергии, повышенное качество плит. Конструкции главных конвейеров достаточно подробно описаны в специальной литературе, и при необходимости читатель может с -ее помощью более детально изучить эту основную технологическую линию заводов древесностружечных плит.
Автор уже упоминал, что в состав главного конвейера входит пресс для подпрессовки. Подпрессовка необходима для уменьшения толщины пакета и повышения его транспортабельности. Толщина пакета уменьшается в 2,5—4 раза (больше при бесподдонном прессовании). Давление при этом составляет 1—1,5 МПа при прессовании на поддонах и 3—4 МПа при бесподдонном прессовании. Подпрессовка производится обычно в одноэтажных прессах, иногда это бывает подвижный пресс, чаще — стационарный.
После подпрессовки брикеты на поддонах поступают в многоэтажный гидравлический пресс для горячего прессования. При бесподдонном прессовании брикеты выкладываются лентой непосредственно на горячие плиты пресса; При прессовании на брикет воздействуют тепло и давление. Читателю, очевидно, понятно, что продолжительность горячего прессования предопределяет продолжительность цикла работы пресса и тем самым производительность всего завода. Поэтому уделяется большое внимание уменьшению цикла прессования. Стоимость пресса для горячего прессования, как и в производстве древесноволокнистых плит, составляет 20— 25% стоимости всего оборудования завода, и поэтому проблема его лучшего использования — постоянная забота работников заводов, а профессия оператора пресса — самая почитаемая.
Прессование производится при 180°С и удельном давлении 2,5—3,5 МПа. Продолжительность прессования 0,3—0,35 мин на 1 мм толщины плиты. Современные прессы имеют размеры горячих плит, достигающие 6×3 м, до 22 рабочих промежутков (одновременно прессуются 22 древесностружечные плиты). Высота пресса достигает 8 м.
Сокращение цикла прессования (увеличение производительности пресса) достигается за счет повышения температуры прессования, применения смол с меньшей продолжительностью отверждения, увеличения количества рабочих промежутков. Эти мероприятия реализованы на большинстве заводов, что позволило поднять производительность прессов с 35 до 80—85 тыс. м3 плит в год.
Автор считает необходимым информировать читателя о том, что имеются и одноэтажные прессы. У них длина горячих плит достигает 20 м, а общая длина главного конвейера —60—70 м. При его обслуживании оператор для перемещения вынужден использовать велосипед.
Готовые плиты пресса выгружаются на приемную (разгрузочную) этажерку, а с нее на линию, где они обрезаются с четырех сторон (линию форматной обрезки). В состав этой линии часто входит агрегат для охлаждения плит. Затем они укладываются в стопы, где выдерживаются не менее 5 суток. Далее плиты шлифуются на оборудований и инструментом, которые были описаны выше. В соответствии с требованиями стандарта плиты сортируются, а затем или раскраиваются на заготовки для мебельных щитов, или отправляются потребителям полноформатными.
В заключение укажем, что на 1 м3 древесностружечных плит расходуется 1,75—1,85 м3 древесины, 70— 80 кг смолы (в пересчете на сухое вещество), 1,4— 1,5 т пара, 160—170 кВт-ч электроэнергии. Затраты труда составляют 2,5—4 чел.-ч на 1 м3.
Необходимо отметить, что производство древесностружечных плит непрерывно совершенствуется: появляются новые виды плит, принципиально новые машины, более эффективные связующие. Представляют, в частности, интерес плиты из стружки, размеры которых по длине и ширине составляют десятки миллиметров; стружка располагается в плоскости плиты. Это обеспечивает высокую прочность плит на статический изгиб,
что важно при их применении в строительстве. Такие плиты (из ориентированной крупноформатной стружки) с успехом заменяют фанеру, которая становится все более дефицитной.
В последние годы стали использовать нетоксичные быстроотверждающиеся смолы, что увеличивает производительность прессов, а значит, и заводов, ликвидирует загазованность в цехах, позволяет использовать плиты внутри жилых помещений. Объем производства древесностружечных плит непрерывно растет, эта тенденция сохранится и в будущем. Для отрасли, оснащенной современным оборудованием, нужны высококвалифицированные рабочие, инженеры и техники, хорошо знающие технологию и механической и химической переработки древесины, электронику, гидравлику, теплотехнику.
Изготовление шкафов из ДСП: инструкция как сделать
MesterulManole6623 1 0
Минимум инструмента, плюс начальные навыки столяра — это то, что нужно для сборки шкафа из ДСП
Решили самостоятельно сделать небольшой гардероб и не знаете, какие материалы для этого применить? В качестве лучшего материала для самостоятельного изготовления мебели рекомендую ДСП. Также расскажу о том, чем хорош этот материал и как из него самому сделать шкаф.
Самый популярный материал для изготовления мебели
Распиливать лист ДСП несложно, если использовать стационарную дисковую пилу
Можно ли самостоятельно собрать мебель из ДСП в домашней мастерской? Конечно же можно, ведь древесностружечная плита (ДСП) — это популярный, простой в обработке и доступный по цене материал. Работать с таким материалом, можно даже не имея большого столярного опыта. Закажите раскрой деталей на фабрике и вам останется ограничиться сборкой конструкции.
Помимо мебели для обычной комнаты, из ДСП можно собрать кухонный или ванный гарнитур, а также одностворчатый шкаф на балкон
Что можно собрать из ДСП? Из древесностружечной плиты можно сделать любую модификацию шкафов, относящихся к категории корпусной мебели. На рынке представлен такой выбор ДСП, которого будет достаточно и для сборки корпуса двухсекционного шкафа, и для изготовления фасада, и для изготовления внутреннего наполнения.
Плюсы мебели из ДСП, сделанной своими руками
Преимуществ немало и среди них:
- Доступная цена мебели. Ламинированная древесностружечная плита стоит вдвое меньше качественной фанеры той же толщины и конечно же меньше мебельных фасадов. Поэтому выбор такого материала позволяет снизить стоимость готовой мебели.
- Возможность сборки мебели, которая впишется в интерьер. В продаже представлен широкий ассортимент цветовых и фактурных исполнений стружечных плит, а потому можно будет выбрать материал под обои и прочие элементы антуража в помещении.
- Широкий ассортимент типоразмеров. Стружечная плита в продаже представлена материалами с толщиной от 10 до 28 мм. Из этих материалов можно выбрать вариант для сборки любых узлов в конструкции шкафа. То есть, мебель можно целиком собрать из ДСП.
- Долговечность. При условии правильной сборки и правильной эксплуатации мебель, изготовленную из стружечной плиты, долго не придется чинить и красить.
Под правильной эксплуатацией подразумевается поддержание оптимальной влажности и температуры воздуха в помещении.
Есть ли недостатки на которые нужно обратить внимание? Бытует мнение, что стружечная плита экологически небезопасна из-за содержания формальдегидов в связующем компоненте. Такая проблема есть, но, если ламинированная пленка не имеет повреждений и по торцу приклеена кромка, эмиссия летучих веществ не превысит допустимой нормы и собранный вами шкаф будет опасен не более, чем цельнодеревянный гарнитур.
Мебель своими руками: работы с ДСП в домашних условиях
Лучше приступать к сборочным работам в специально оборудованной мастерской, но за неимением мастерской заняться этим можно и дома
Как самостоятельно собирать мебель из ДСП? Для начала нужно определиться с тем, что вы хотите сделать. То есть, нужно понимание дизайна, функциональности и габаритов будущего шкафа.
На этом этапе можно использовать типовые чертежи или самостоятельно набросать на бумаге эскиз шкафа своей мечты. Далее придётся подготовить материалы, выполнить распиловку в соответствии с чертежами, закупить необходимую фурнитуру и собрать заготовленные детали воедино.
Чертеж
Для вдохновения предлагаю подборку стандартных чертежей, из которых вы сможете выбрать неплохой вариант для самостоятельной сборки шкафа.
Книжный стеллаж отличается простотой конструкции за счёт отсутствия створок. Поперечная жесткость корпуса достигается за счет крепления полок разбежку.
Чертеж небольшого гардероба со створками для установки в прихожей
Чертеж углового шкафа со створками в центральной части
Чертеж гардероба во всю стену – боковая секция для длинных вещей предусматривает установку створок, остальные секции можно оставить открытыми
Чертеж шкафа купе с открытой боковой секцией
Как изготовить кухонную мебель своими руками из ДСП
Чертеж прямого кухонного гарнитура
Теперь вы знаете, как самому сделать шкаф из ДСП для эксплуатации в жилом помещении. Можно ли сделать такую же мебель для использования на кухне?
Проект углового кухонного гарнитура
Разумеется, можно, так как отличия обычной корпусной мебели от кухонных аналогов минимальны и заключаются только в размерах и в элементах наполнения. Если для сборки обычных корпусов используется ДСП с толщиной 16 мм, то для изготовления столешницы потребуется плита с толщиной не менее 30 мм.
Подготовка материала
Инструменты
Выбор инструментов зависит от того, кто будет выполнять раскрой. Если раскрой деталей будете выполнять сами, понадобится стационарная дисковая пила и электролобзик. Кроме этого, потребуется шуруповерт, измерительный инструмент, струбцины, утюг для поклейки кромки.
Корпус шкафа будет собираться на полу, а потому освободите достаточное пространство, сдвинув мебель к стенкам. Застелите пол упаковочным картоном или аналогичными материалами, чтобы не повредить его в ходе сборки.
Сборка
Образец сборки шкафа в помещении, где он будет эксплуатироваться
Процесс сборки мебели из готового комплекта начинается с изготовления корпуса – каркаса, состоящего из боковых верхней и нижней части. После того как корпус собран, с изнанки набивается ДВП.
Корпус собранной мебели подымается и устанавливается вплотную к стене, где будет впоследствии эксплуатироваться. Внутри собранного корпуса устанавливается наполнение, выбранное в соответствии с функциональным назначением шкафа. в соответствии с чертежом устанавливаются дверные створки.
Как обработать кромку ДСП
Чтобы не окрашивать торцы стружечных плит, кромку закрываем специальной лентой.
Иллюстрации | Виды кромочных лент |
На меламиновой основе. Это плоская лента толщиной 0,5-0,8 мм без поперечного профиля. В продаже представлены клеевые и безклеевые модификации. Клеевая лента прикладывается к торцу плиты и разогревается утюгом в итоге термоклей размягчается и приклеиваются. Оклейка ленты без термоклея выполняется с предварительным нанесением отдельно купленного клея. | |
Из ПВХ.![]() |
Как крепить ПВХ ленту
Иллюстрации | Монтаж мебельной торцевой ленты |
Т-образная. По торцу вырезается паз глубиной 8 мм и шириной 2 мм. Кромка шипом прикладывается к вырезу и киянкой вбивается по всей длине. | |
П-образная. Ленту прикладываем так, чтобы ее края обхватили торец плиты. Проходим киянкой по всей длине плиты, так чтобы лента легла одинаково ровно. |
Правильная разметка и отцентровка отверстий на ДСП
Делать отверстия под разметку карандашом можно, только если на поверхности ЛДСП краска, с винилового покрытия отметка быстро сотрется
Как правильно разметить ЛДСП? При сборке корпусной мебели часто приходится в нескольких точках отмечать расстояние с одинаковым отступом от края мебели. Сделать это можно, используя угольник. Угольник поочерёдно прикладываем к краю и по отверстиям отмечаем отступ на необходимое расстояние.
Правильный вариант – разметку продавливаем шилом
Но есть более простой и удобный способ. На алюминиевом уголке сверлим отверстие на необходимом расстоянии от края и по этому шаблону наносим разметку. Ламинированный ДСП — это материал с гладкой поверхностью, а потому при нанесении разметки отверстия накерниваем шилом или пробойником. Такая разметка не сотрется и, кроме того, сверло не будет соскальзывать.
Форма сверла должна утолщаться к основанию, чтобы отверстие получалось с потаем под винт
Как сверлить? Чтобы вкрутить саморез или конфирмат в ДСП сверлится отверстие с диаметром на 2 мм меньше диаметра используемых метизов. Сверло устанавливаем по накрененной разметке и сверлим на малых оборотах с нажимом. Разумеется, используем заточенные сверла.
Установка выдвижных ящиков при помощи направляющих
Иллюстрации | Виды телескопических направляющих |
Роликовые.![]() Недостаток таких направляющих в том, что пластик на роликах крошится и уже через год их придется ремонтировать. | |
Шариковые. В таких конструкциях основные полозья и их ответная часть собраны воедино с применением подшипников. Ящики на таких направляющих выезжают плавно, и такая фурнитура служит дольше, чем роликовая. |
Монтаж направляющих полозьев
Как установить? Одна часть направляющих крепится на внутреннюю стенку корпуса, тогда как ответная часть устанавливается на боковине ящика. Крепление выполняется на саморезы длиной 20 мм. Перед тем как крепить направляющие выполняются замеры так, чтобы ящик впоследствии встал ровно без перекосов.
Фасад
Какие фасады предпочтительно использовать для сборки мебели из ДСП? Лучший вариант — это фасады из такой же стружечной плиты.
Офисный шкаф купе с фасадом из ДСП с покрытием из винилового шпона
Коричневый гардероб с фасадом из стружечной плиты с глянцевым виниловым покрытием
Комбинированный дизайн, где шпонированная часть фасада сочетается массивными вставками, отделанными под стекло
Дополнительные элементы
Наполнение стандартного вещевого шкафа
К дополнительным элементам шкафа относится декор и наполнение. Элементы наполнения — это полки, ящики, направляющие для вешалок и т.п. Большая часть этих элементов может быть изготовлена из той же древесностружечной плиты. Поэтому, выбирая для изготовления шкафчика ЛДСП, вы сможете справиться со сборкой, используя только этот материал.
Вывод
Теперь вызнаете, как из ДСП собирается корпусная мебель. Если по технологии сборки остались вопросы, задайте их в комментариях к этой статье.
Понравилась статья? Подписывайтесь на наш канал Яндекс.
Если вы хотите выразить благодарность, добавить уточнение или возражение, что-то спросить у автора — добавьте комментарий или скажите спасибо!
Технология изготовления ДСП
Изготовление ДСП
Начнем с того, что это один из самых экологичных процессов, связанных с обработкой древесины. Само изготовление древесно-стружечной плиты или ДСП это сложный и длительный процесс, который начинается с распилки дерева на ровные круглые бревна, далее расщепление древесины в специальных машинах.Всю технологию, можно разделить на несколько этапов, которые идут следующим образом:
- Измельчение чистой древесины либо отходов, в процессе этого процесса появляется продукт-щепа.
- В процессе переработки, всю щепу перемалывают до однородного состояния и перерабатывают роторные станки в результате чего появляется следующий продукт-стружка
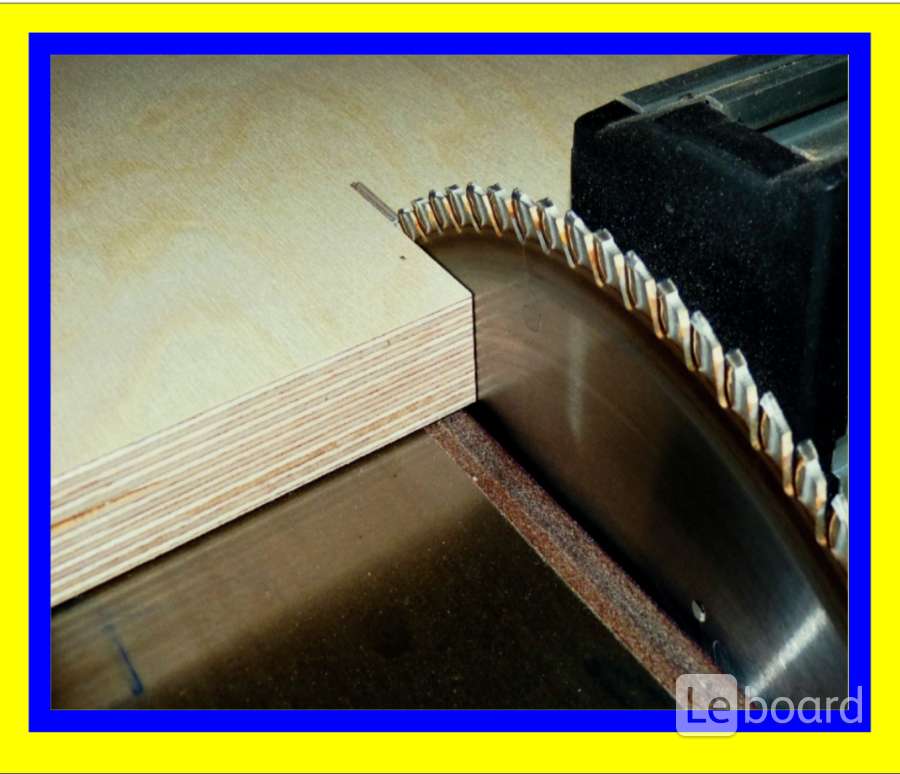
Согласно технологическим регламентам по производству ДСП обязательным является соблюдение толщины стружки которая составляет 0,5 мм, ширина 8 мм, длина от 5 до 40 мм. Регламент является обязательным и имеет некие погрешности в несколько миллиметров, что позволяет незначительные колебания и отклонения от нормы.
Также есть требования, которые есть к форме и структуре стружки. Форма должна быть плоской и ровной по толщине с гладкой поверхностью. Для измерения толщины стружки используются специальные устройства. Ее отвозят в специализированные бункеры, где хранится все время предшествующие сушке.
В в такой бункер, ее завозят при помощи специализированного пневматического транспорта, далее ее передают на сушку. Высушивание стружки происходит только до 5% влажности, а вот внутренние слои не более 25%. Из-за этого стружку сушат в разных сушильных установках, чтобы добиться именно стандартного готового продукта.
Если смотреть на отличия внутренней сушки от внешней, то оно очень простое. Внешний слой нагревают и остужают быстро, а вот внутренний слой медленнее и дольше держат сушилке, что все процессы шли постепенно. Говоря про пневматические агрегаты сортирующие стружку для разных слоев, то пневматика из различает их по влажности.
Следующий процесс это смешивание готовой стружки со связующими веществами, а именно со смолами, как натурального происхождения, так и синтетического, которые находятся в жидком состоянии. Этот процесс преобразует стружки в однородную массу.
После получения единой массы, стружку отправляют в формовочные, где она подвергается горячей прессовке. После этого паллеты из стружки становятся твердыми и готовыми к шлифовке и покрытию закрепителями и смолами.
Купить ДСП для изготовления мебели
Последний этап этого длительного процесса, заключается в продаже готового ДСП для потребителя. Купить панели ДСП, любых видов можно напрямую с нашего склада.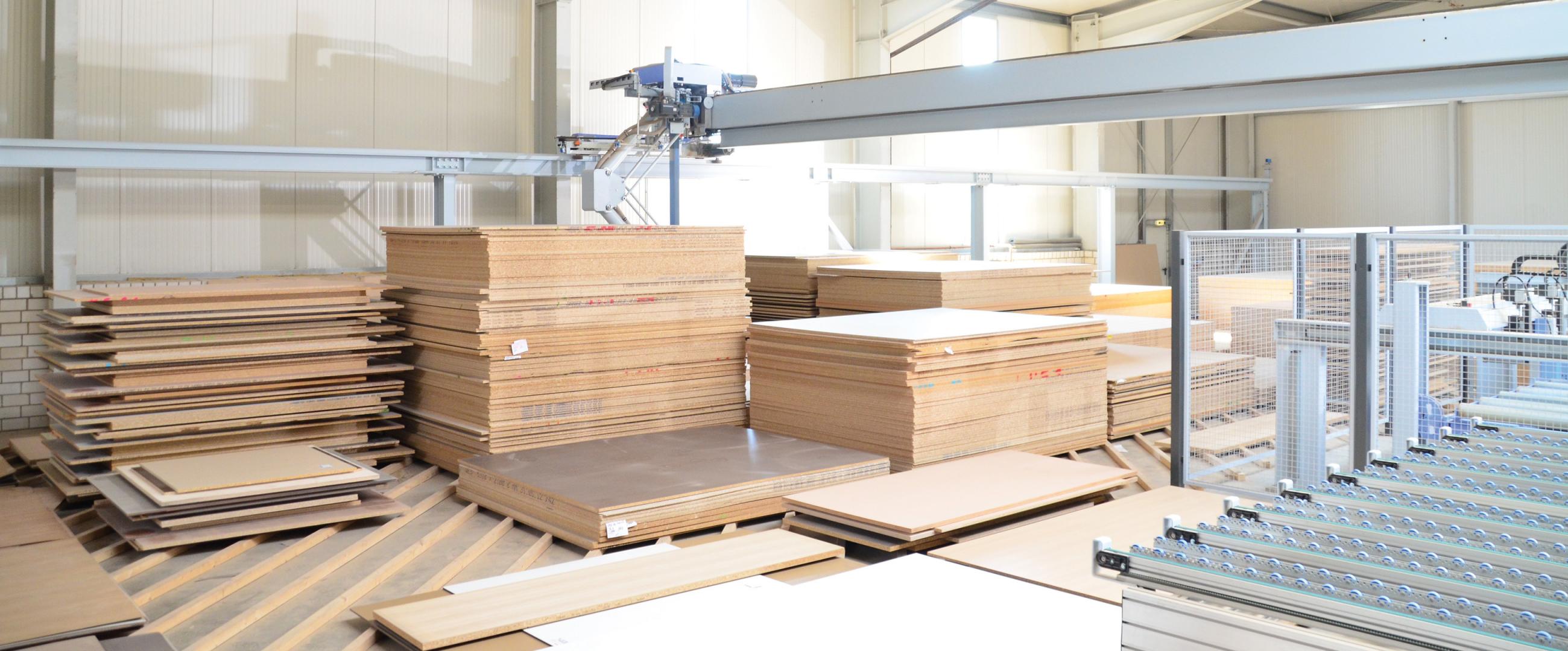
Бизнес на производстве ДСП. Запускаем цех с нуля.
Древесно-стружечная плита, или как ее в народе называют ДСП, является одним из наиболее востребованных строительных материалов.
Этот материал используется в различных сферах строительства и производства:
- при сооружении напольных покрытий;
- при конструировании панелей для стен;
- для изготовления мебели, для этого в основном используется ламинированное ДСП;
- для обшивки крыши и прочее.
Отчасти такое производство можно отнести к перерабатывающему, поскольку основным сырьем для изготовления таких плит являются отходы от древесных предприятий.
Технология изготовления ДСП
Процесс производства можно разделить на несколько основных этапов:
— подготовка сырья. Сюда входит процесс дробления древесины, и получение из нее стружки необходимых размеров. Этот этап можно пропустить, если сразу покупать готовое сырье;
— на втором этапе стружка смешивается со связующим веществом (клеем). Тут важно придерживаться необходимых пропорций, поскольку излишнее количество клея может привести к ухудшению технических свойств плиты и соответственно, такой материал будет считаться браком.
— полученную смесь помещают в специальные формы, и запрессовывают их. Под силой давления и достаточно большой температуры материал схватывается и образует единое целое;
— на следующем этапе его помещают в сушильную камеру;
— следующий этап обрезка краев плиты;
— и в самом конце плита проходит процесс шлифования.
Для организации такого производства вам понадобиться помещение, скорее всего в виде склада, где вы сможете установить саму линию по изготовлению и стенды для хранения продукции.
Организуйте свой бизнес по производству полиэтиленовых пакетов. Пошаговый алгоритм запуска своего дела с нуля.
Оборудование для производства ДСП
Для подготовки сырья:
1.) Оборудование для переработки бревен дерева в щепки;
2. ) Камеры для сушки щепок;
3.) Строгальный станок;
4.) Вибросито.
Производство материала:
1.) Аппарат для смешивания стружки со связующим веществом;
2.) Формы для будущей плиты;
3.) Термопресс;
4.) Охладитель или сушка для готовой продукции.
Завершающий этап:
1.) Станок для распила, чтобы придать листу определенных размеров;
2.) Станок для шлифования торцов;
3.) Станки для грубой и тонкой шлифовки.
В случае изготовления ДСП для изготовления мебели:
1.) Пресс для нанесения двусторонней ламинации.
Также на производстве возможно нужны будут аппараты для транспортировки, например роликовые или ленточные.
Средние затраты на открытие бизнеса:
Приведем несколько примеров стоимости различных линий по производству ДСП.
1.) Линия (производитель SMS Харьков) производительностью 100 листов в сутки и более, с возможностью выбора любого формата листа будет стоять в пределах 209 000 евро.
2.) Мини линия производительностью 50 листов в сутки $50 000.
Как видите стоимость такого оборудования очень большая.
В итоге, перед тем, как вложить такую серьезную сумму в этот бизнес изучите для начала спрос на этот материал, и посчитайте, сможете ли вы конкурировать по ценовой политике с более крупными производителями. Идеальной схемой, является заключение договора с мебельными заводами, тогда стабильный сбыт продукции вам гарантирован.
АО «Казанский Гипронииавиапром» им. Б.И.Тихомирова»
АО «Казанский Гипронииавиапром» им. Б.И.Тихомирова» > Деятельность > Проектирование > Промышленность > Деревообрабатывающая и целлюлозно-бумажная промышленность > Завод по производству МДФ, ДСП, ОСБ плит в ОЭЗ «Алабуга»Завод по производству МДФ, ДСП, ОСБ плит в ОЭЗ «Алабуга»
Завод по производству МДФ, ДСП , ОСБ плит расположен на территории Особой экономической зоны промышленно-производственного типа «Алабуга» (ОЭЗ ППТ «Алабуга»).
На заводе предусмотрено производство плит МДФ, ДСП, ОСБ производственной мощностью 475 000 м3/год (МДФ), в том числе с финишной обработкой (шлифовка, ламинирование, производство ламинированного паркета). Исходным сырьем для производства является нестроевой лес в т.ч. образующийся при санитарной вырубке, отходы предприятий деревообработки.
Большим плюсом данного проекта является отсутствие технологических твердых отходов производства, так как древесные отходы в виде коры, древесной пыли и брака плит используется как топливо в технологических энергетических установках завода.
На территории завода запроектированы с учетом функционального зонирования следующие здания и сооружения:
-производственная зона: производственный корпус с внекорпусными производственными участками и погрузочными рампами, с которых осуществляется погрузка готовых изделий на железнодорожный состав и автомобильный транспорт, а так же бытовой корпус со столовой, соединенный надземным переходом с производственным корпусом.
-складская зона: склады леса с разгрузочными железнодорожными платформами, склад метанола со сливной эстакадой.
-зона технического сервиса: корпус технического обслуживания, стоянки технологического транспорта и грузовых автомобилей;
-зона вспомогательных объектов: инженерная инфраструктура, энергетические объекты, контрольно-пропускной пункт с автовесовой; административный корпус со столовой, служебной стоянкой транспорта.
Производственная годовая программа составляет:
– МДФ плита (шлифованная и ламинированная) 475 тыс.м3 в год
– ДСП плита (шлифованная и ламинированная) 725 тыс.м3 в год
– ОСБ плита 575 тыс.м3 в год
Сырье для производства ДСП
Для производства древесно-стружечных плит может быть использовано неделовое (дровяное) сырье различных пород, а также отходы, получаемые на лесопильно-деревообрабатывающих предприятиях в виде горбылей, реек и обрезков от пиломатериалов. Все круглое сырье, предназначаемое для производства, должно быть окорено, разрезано на чураки длиной в 1 м, которые поступают на специальный теплый бассейн для гидротермической обработки. После этого чураки расторцовывают на отрезки длиной 0,5 м и подают на специальные стружечные станки, срезающие стружку параллельно волокнам древесины.
При изготовлении трехслойных плит выработка стружки для наружных слоёв и среднего слоя производится отдельными потоками, так как для среднего слоя допускается более крупная стружка (расход ее на плиту составляет от 50 до 66%). Далее стружка проходит через молотковые мельницы, где она размельчается в основном по ширине, становится более гладкой и более мелкой и поступает в бункера. Туда же идет и стружка от деревообрабатывающих цехов, если она не нуждается в дополнительном измельчении на молотковых мельницах. Из бункера стружка подается пневматическим транспортером на двуступенчатую газовую сушильную установку. Лопатки метального механизма первой ступени сушилки, так называемой «вихревой», распределяют сырую стружку равномерно по всей поверхности сетчатого дна сушилки. Горячий воздух, поступающий в сушилку снизу, выносит подсушенные частицы стружки в циклон, откуда стружка переходит на вторую ступень сушки. Работа сушилки контролируется автоматическими приборами. Из сушилки стружка попадает в сортировку, где отделяется крупная (некондиционная) стружка, которая возвращается в молотковую мельницу для дополнительного измельчения, а кондиционная стружка подается в бункер сухой стружки. Стружка сушится до 5%-ной влажности. Бункер для хранения сухой стружки связан с дозирующей установкой и питателем перед смесительной камерой.
Из питателя через дозирующую установку стружка подается в смесительную камеру непрерывного действия, где она перемешивается с синтетическим связующим клеем, подаваемым из отделения приготовления клея.
Приготовление синтетического клея и смешение его со стружкой. Для изготовления древесно-стружечных плит применяется клей на основе водорастворимых мочевино-формальдегидных синтетических смол. Процентное отношение веса смолы в перерасчете на ее сухой остаток к весу сухой стружки составляет примерно 6—12%. Раствор клея подается в непрерывный смеситель из отделения подготовки смолы (клея). Распыление смолы при подаче в смесительную камеру для лучшего смачивания стружки осуществляется с помощью сжатого воздуха.
Образование ковра плит, прессование и обрезка. Подготовленная древесная стружка подается из смесителя через воронку на вибратор пресса, посредством которого на стальной ленте формируется ковер плиты. Первый вибратор образует нижний слой из более мелкой щепы, второй и третий вибраторы образуют средний слой, а четвертый — верхний слой плиты. Подготовленный и неуплотненный ковер плиты проходит через пресс предварительного уплотнения, где толщина ковра уменьшается в 2—3 раза. Перед поступлением в горячий пресс ковер проходит через высоко-частотный нагреватель, где стружка ковра предварительно нагревается до 75°, после чего ковер поступает в горячий гидравлический пресс с температурой 120—150° и давлением от 18 до 25 кг/см2.
Режим прессования изменяется в зависимости от вида применяемого клея, толщины и назначения плит. После прессования плита охлаждается, обрезается и шлифуется. Производительность подобной установки составляет 15—20 тыс. т плит в год.
Технология производства древесно-стружечных плит по способу «Бартрев» отличается тем, что плиты прессуются в установке непрерывного действия и этим создается определенный ритм в работе цеха. Однако устройство пресса непрерывного действия весьма сложно. Так, пресс имеет длину 40,2 м, ширину 2,3 м, высоту 6 м, вес 200 т Пресс вырабатывает плиты толщиной 5—19 мм, шириной 1200 мм.
Основной частью пресса, осуществляющей прессование стружек, являются две движущиеся бесконечные стальные ленты, расположенные одна над другой. Ковер из стружек, смешанных с синтетическим клеем, проносится нижней лентой через высокочастотную установку, в которой получает предварительный нагрев до 75°, затем он проходит между указанными двумя лентами, движущимися со скоростью 1,5—9 м/мин; ленты, соприкасаясь с одной стороны е ковром стружек, другой стороной находятся в контакте с обогревательными прессовыми плитами, нагреваемыми до 140° и создающими удельное давление 18—25 кг/см2. Таким образом, здесь ковер стружек получает свой конечный размер по толщине и превращается в спрессованную непрерывную плиту. Движущаяся на конвейере плита охлаждается и автоматически разрезается на необходимые размеры по ширине и длине. Производительность подобной установки при работе в три смены 300 дней в год составляет 22—25 тыс. т.
Имеется также способ непрерывного прессования с применением пресса типа «Крайбаум», который по устройству значительно проще, чем «Бартрев». Здесь стружки прессуются непрерывно, проходя через канал прямоугольного сечения со скоростью 0,1—1 м/мин при температуре 160°. Производительность одного пресса 4 тыс. т плит в год. Последняя установка по своим показателям считается наиболее экономичной из всех рассмотренных способов, однако плиты, получаемые этим методом, имеют невысокую прочность и поэтому непременно должны подвергаться фанерованию.
На небольших предприятиях применяются более упрощенные схемы производства однослойных древесно-стружечных плит из сухой стружки и сухих мелких кусковых отходов. Как правило, такие производства менее механизированы, но достаточно эффективны. В настоящее время разработан типовой проект установки для производства древесно-стружечных плит из сухих стружек для мебельных предприятий. Проектная производительность установки составляет 5 м3 плит в смену. Установка обслуживается семью рабочими и занимает площадь в 250— 300 м2. Еще более упрощенные установки выпускают 2,5 м3 плит (210 м2) на площади 30 м2. Древесно-стружечные плиты, изготовляемые на мебельных фабриках, обходятся на 20—30% дешевле столярных плит.
Ниже даются основные технико-экономические показатели по производству древесно-стружечных плит (применительно к механизированному производству с прессом периодического действия.
Производитель коробчатых перегородок из ДСП и гофрированного картона, коробчатых перегородок и прокладок
С момента открытия в 1987 году компания Multicell стала крупнейшим независимым производителем коробчатых перегородок в Северной Америке. Как Независимый производитель коробчатых перегородок , мы не связаны никакими корпоративными контрактами или обязательствами по закупке сырья у дочерней компании. Multicell имеет возможность окружить себя сырьевыми партнерами, предлагая лучший сервис и качество по конкурентоспособным ценам, чтобы помочь удовлетворить потребности наших клиентов.
Наша дочерняя компания Box Partition Technologies анализирует потребности клиентов и рынка, чтобы настроить и создать наиболее эффективное производственное оборудование для современного рынка упаковки. Это оборудование позволяет нам стабильно обеспечивать лучшие сроки выполнения заказов по конкурентоспособным ценам.
Кроме того, группа инженеров Multicell Innovative гордится тем, что разрабатывает наиболее экономичную внутреннюю упаковку для обеспечения надлежащей защиты продуктов клиентов.Дизайн упаковки и отбор проб выполняются своевременно, чтобы удовлетворить потребности наших клиентов в срочном порядке.
Multicell гордится своим Agility . Мы применяем наш гибкий подход к дизайну, расценкам и образцам и, в конечном итоге, к производству продуктов премиум-класса на самом передовом и эффективном оборудовании в мире. Строгая рабочая этика Multicell и стремление удовлетворить потребности клиентов — вот почему мы стали ведущим поставщиком на рынке.
Непрерывное стремление и внедрение инноваций в дизайне оборудования и продуктов, привлечение Гибкость к нашему персоналу и процессам, а также опора на нашу Независимость от крупных поставщиков позволяет Multicell уверенно и последовательно удовлетворять потребности наших клиентов. потребности.
АРАУКО | Изделия из дерева, композитные панели, фанера
АРАУКО | Изделия из дерева, Композитные панели, Фанера — ARAUCO ВНИМАНИЕ! Браузер не поддерживается . Похоже, вы используете Internet Explorer (IE) в качестве веб-браузера.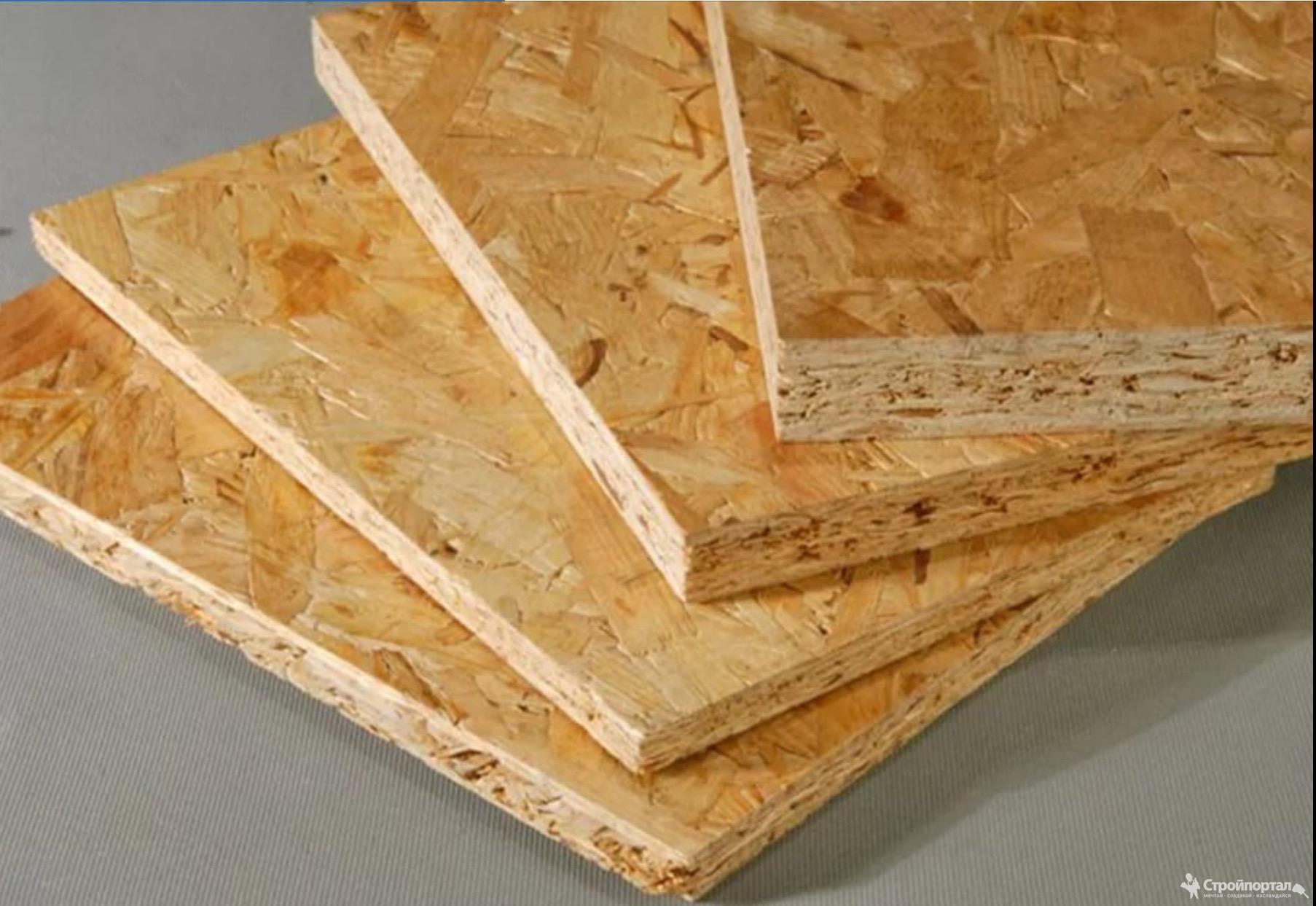
Готовы отслеживать ваши заказы?
Зарегистрируйтесь на нашем клиентском веб-портале.
Лукбук Prism TFL 2021
Откройте для себя коллекцию подсказок Prism TFL 2021 для ярких пространств.
Зарегистрированный курс TFL
Новый кредитный курс для A&D! Занятия под руководством инструктора предлагаются квалифицированным группам.
ARAUCO является мировым производителем лесоматериалов, обслуживающим Северную Америку с превосходным качеством производства и дистрибуции изделий из дерева.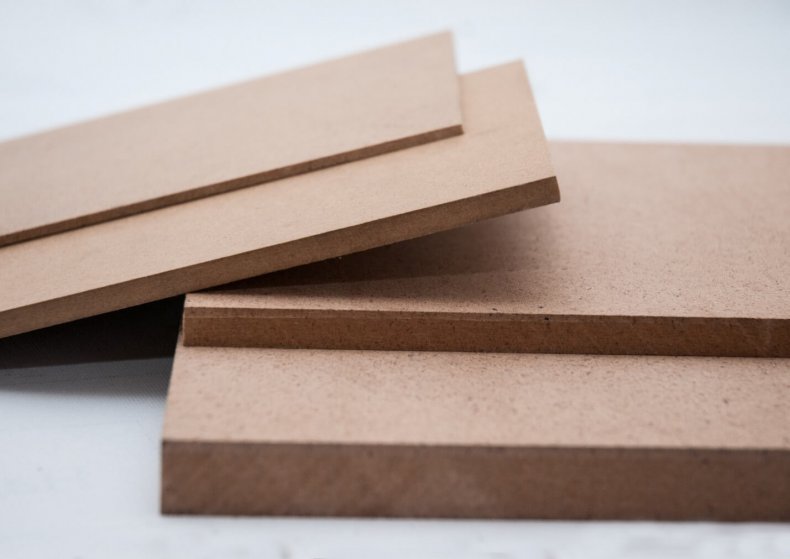
Известная передовыми автоматизированными производственными платформами, ARAUCO предлагает безопасную и продуктивную карьеру тысячам сотрудников в США и Канаде.
Основные характеристики промышленных, OEM и специальных продуктов
Строительство сарая
ARAUCO предлагает широкий выбор деревянных панелей для строительства ангаров. От фанерного сайдинга до обработанных столярных изделий, напольных покрытий, стеллажей и прилавков — для этого есть деревянные панели.От ящиков к дверям
Fibrex HDF — это универсальная промышленная панель для компонентов выдвижных ящиков, мебели и приспособлений, игровых и поперечных лент для архитектурных дверей.
Мебель для полов
Благодаря своим превосходным характеристикам механической обработки и физико-механическим свойствам Trupan MDF идеально подходит для изготовления мебели, а также в качестве основы для паркетных полов.Композитный материал кабинетного класса
Ультра ДСП представляет собой гладкую, плотную и стабильную панель, хорошо поддающуюся механической обработке.Это идеальная подложка для отделки шкафов и ламинирования с низким уровнем эмиссии и влагостойкостью.Курорты Калахари Choses Prism TFL WF397 Стромболи
Prism TFL был выбран в качестве основного элемента декора курорта Kalahari Resorts & Conventions в Раунд-Роке, штат Техас, аутентичного места отдыха в африканском стиле с местным техасским духом.Вдохновитесь проектом Kalahari Resorts и другими проектами в нашей галерее.
Tubula Процесс производства ДСП и правила классификации – Фанера
Процесс производства ДСП Tubula и правила классификации
Проверки сортировки и контроля качества проводятся на каждом этапе производственного процесса. Случайные образцы проверяются на соответствие установленным стандартам в нашей хорошо оборудованной заводской лаборатории.
- СЫРЬЕ
Волокнистые материалы представляют собой бревна, ветки и древесные отходы RubberWood. Каучуковое дерево представляет собой однородный материал средней плотности светлого цвета, пригодный для производства высококачественных древесно-стружечных плит. - ИЗМЕЛЬЧЕНИЕ И ОТШЛУПЛЕНИЕ
Материалы из каучукового дерева измельчаются перед измельчением до мелких чешуек желаемой толщины и длины.Это способствует оптимальной прочности и гладкости поверхности плит. - СУШКА И ПРОСЕТИВАНИЕ
Влажные хлопья сушат в сушилке с горячим газом до требуемого уровня влажности. Затем высушенные хлопья просеивают, чтобы отделить мелкие и сердцевинные частицы, и хранят в поверхностном бункере и силосе сердцевины. - СМЕШИВАНИЕ КЛЕЯ И СМЕШИВАНИЕ
Поверхностные и сердцевинные частицы отдельно смешиваются с клеем, восковой эмульсией и другими добавками, точно дозируемыми для достижения качества высокого стандарта. - ФОРМОВАНИЕ МАТОВ
Смоляные частицы распределяются с помощью воздушного и механического формования, включенного в компьютеризированную программируемую систему управления, что обеспечивает постоянную плотность мата и равномерное распределение веса. - ГОРЯЧЕЕ ПРЕССОВАНИЕ
Горячее прессование, работающее автоматически на основе программируемого логического управления, сжимает мат под высоким давлением и контролируемой температурой для формирования плит точной толщины. - ОХЛАЖДЕНИЕ
Готовые плиты, выходящие из горячего пресса, автоматически взвешиваются, чтобы убедиться, что получена определенная плотность, а затем помещаются в охладитель Star Cooler для схватывания клея. - ШЛИФОВАНИЕ
Необработанные плиты хранятся для окончательного отверждения для стабилизации свойств плит. Позже эти плиты будут откалиброваны до точной толщины, отшлифованы до идеальной поверхности и откалиброваны. - РАЗМЕР
Основные панели проверяются на соответствие склеивания и допуски по толщине перед обрезкой боковых сторон и обрезкой до точного размера. Панели штабелируются для промежуточного хранения. - ЛАМИНИРОВАНИЕ
Сортированные гладкие плиты могут быть ламинированы декоративной бумагой, пропитанной меламином, методом прессования короткого цикла или натуральным шпоном.Платы пересортированы и упакованы для окончательной отправки
Производители трубчатых древесностружечных плит, производимых по современным передовым технологиям, выделяются своей ценой и моделями. Мебельный сектор является наиболее часто используемой областью, хотя есть разные области применения. Все изделия, используемые в гостиной, гостиной, спальне, прихожей, кухне и ванной комнате, могут быть изготовлены из трубчатой мебели из ДСП. Причем, с большим разнообразием рисунков и расцветок. Для тех, кто любит простоту, доступны различные цвета и дизайны для тех, кто любит простую, стильную и яркую жизнь.Мебель из ДСП можно приобрести во всех мебельных магазинах, а также в интернет-магазинах. В последние годы область применения пустотелых древесностружечных плит получает все большее распространение. В зависимости от постоянного развития технологий мебель из трубчатого ДСП каждый день предлагается в разных ценовых диапазонах.
如无特殊说明,文章均为本站原创,转载请注明出处。Если нет специальных указаний, статьи являются оригинальными, если вы хотите использовать или воспроизвести, пожалуйста, укажите первоисточник www.plywoodinspection.com, если вы обнаружите, что наши статьи нарушают ваши авторские права и интересы, своевременно напишите нам по адресу info@plywoodinspection.
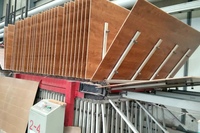
Руководство по упаковке всего ДСП
Мы все видим влияние дерева на нашу повседневную жизнь, ведь все, от наших домов и мебели до бумаги и книг, изготавливается из дерева. Но знаете ли вы, что даже оставшуюся древесину можно использовать для изготовления широкого спектра упаковочных изделий? ДСП, также известная как картон, представляет собой надежный и прочный материал, изготовленный из скромных материалов, таких как опилки.В сегодняшней статье The Packaging Company объяснит все, что вам нужно знать о ДСП, от того, как он производится, до того, как он может использоваться предприятиями в США и Канаде в качестве формы упаковки.
Использование для ДСП
Существует множество применений ДСП, и большинство из них можно найти в типичном североамериканском доме или офисе.
Назначение ДСП существенно зависит от его плотности. Вы можете использовать очень тонкий ДСП для:
Более толстая ДСП имеет совершенно другой набор применений. Вы можете использовать более толстую ДСП как:
Производство ДСП
ДСП изготавливается из древесных отходов, таких как необработанная щепа или опилки, что делает его более экологичным выбором, чем другие формы упаковки, в которых иногда используется свежая древесина или пластик. После сбора древесные частицы измельчаются, измельчаются и высушиваются для создания однородной смеси с заданным уровнем влажности, необходимым для производства.Эта смесь щепы затем делится на более мелкие и более крупные древесные частицы.
После разделения древесная стружка наслаивается и склеивается, при этом меньшая древесная щепа образует слои вокруг более крупных частей внутри. Затем его спрессовывают вместе с помощью пресса для горячей древесины, чтобы создать конечный продукт из ДСП. Плотность пресса во многом зависит от желаемой толщины и назначения ДСП. После завершения древесно-стружечная плита подвергается некоторым завершающим штрихам, таким как шлифовка или добавление декоративных элементов, прежде чем она будет готова к использованию.
В чем разница между ДСП и гофрокартоном?
Другой популярный материал для упаковки коробок и картонных коробок, гофрокартон отличается от ДСП. Хотя оба изготавливаются из древесной массы, они изготавливаются с использованием разных процессов. ДСП — это прочный однослойный слой древесины определенной плотности, в то время как гофрированный картон состоит из нескольких тонких слоев, неплотно соединенных друг с другом. Внутри этих слоев находится лист картона, который скомкан и сложен в виде треугольника, что придает ему дополнительную поддержку при нагрузке.Цель этого состоит в том, чтобы укрепить картон и придать ему долговечность, поэтому многие картонные упаковочные изделия могут удерживать значительно более тяжелые предметы, такие как мебель.
ДСП или гофрированный картон: что лучше?
Как гофрокартон, так и ДСП очень эффективны для упаковки товаров, хотя могут использоваться в разных условиях. В то время как гофрированный картон является лучшим выбором для транспортной упаковки, ДСП идеально подходит для упаковки самого продукта. Нередко гофрированный картон используется в качестве транспортной упаковки для изделий из ДСП, например, подарочных коробок.
Что касается окружающей среды, ДСП является более экологичным из-за использования меньшего количества материалов и процессов в процессе производства. Он также прочнее и может использоваться в большем количестве случаев, чем гофрированный картон, из-за его различной плотности, например, в качестве мебели. Гофрокартон по-прежнему является отличным выбором для упаковки и зарекомендовал себя как прочный материал, учитывая его легкий вес и доступную стоимость.
В то время как гофрокартон лучше подходит для транспортировки и промышленных нужд, упаковка из ДСП предлагает то преимущество, что на нее легко наносить печать, что делает ее идеальной для фирменных продуктов.
Оба типа материалов могут быть переработаны, хотя всегда рекомендуется заранее проконсультироваться с местным предприятием по переработке. Особенно это касается изделий из ДСП, которые лучше подходят для компостирования.
Упаковочные изделия из ДСП
От коробок до картонных коробок изделия из ДСП служат надежным упаковочным материалом.В The Packaging Company мы имеем большой опыт работы с ДСП для изготовления разнообразной упаковочной продукции. В нашем каталоге представлены такие позиции, как:
Ознакомьтесь с нашим полным ассортиментом упаковки из ДСП здесь.
Приобретите упаковку из ДСП в The Packaging Company
Если вы хотите приобрести коробки и картонные коробки из ДСП для своего бизнеса, рассмотрите возможность приобретения упаковки из ДСП в The Packaging Company.

Производство древесно-стружечных плит — WOOD TEC PEDIA
Древесно-стружечные плиты относятся к категории материалов на основе древесины.Они используются в мебельном и интерьерном строительстве, а также в деревянном строительстве, т.е. для обшивки стен.
Маркировка ДСП
1. Производитель/торговая марка/обозначение
2. Европейский стандарт DIN EN 312
3. Панель/тип — класс
4. Номинальная толщина
5. Формальдегидная группа
6. Партия/номер неделя изготовления
Классификация
ДСП делятся на семь групп по назначению и несущей способности.
- P1 — Сухая зона — Ненесущая (общего назначения)
- P2 — Сухая зона — Ненесущая (Мебель и внутренняя конструкция)
- P3 — Диапазон влажности — Ненесущий (оборудование для ванной и кухни)
- P4 — Сухая зона — Несущие (полы, сборные дома)
- P5 — Влажная зона — Несущие (полы, сборные дома)
- P6 — Сухая зона — Тяжелые условия эксплуатации (полы, сборные дома)
- P7 — Диапазон влажности — Тяжелая нагрузка (полы, сборные дома)
Чтобы можно было различать ДСП, панели для влажного диапазона окрашены в зеленый цвет, а панели с антипиреном окрашены в красный цвет.
Формальдегид класса
Формальдегид – это химический компонент синтетической смолы, которой склеены чипсы. Как в процессе прессования, так и при «дозревании» ДСП формальдегид ДСП происходит в виде газа. Он вызывает раздражение глаз и затрудняет дыхание. Формальдегид классифицируется как канцероген для человека. По этой причине были введены пороговые значения выбросов, которые могут варьироваться от страны к стране. Значение выбросов дается в мг/м³ или ppm.
- Германия: E1 (класс выбросов 1 с 0,1 ppm), E2 (0,2 ppm), E3 (0,3 ppm)
НОВИНКА с января 2020 г.: E0,5 (0,05 ppm)
- США: CARB I и CARB II (Калифорнийский совет по воздушным ресурсам с пороговым значением 0,9 частей на миллион)
- Япония: JIS F**** (японский промышленный стандарт)
Завод ДСП (округ) | Сообщество PV
Если вы не получили электронное письмо с регистрацией для подтверждения своей учетной записи, отправьте нам электронное письмо с вашим именем пользователя. Убедитесь, что вы отправили электронное письмо с адреса электронной почты, который вы использовали при регистрации, чтобы мы могли вручную подтвердить вашу учетную запись. Отправьте электронное письмо на адрес [email protected]. Альтернативой является отправка вашего имени пользователя и электронной почты FloydN в разногласиях. Наш дискорд-сервер находится внизу страницы. Извините за неприятности.
JavaScript отключен. Для лучшего опыта, пожалуйста, включите JavaScript в вашем браузере, прежде чем продолжить.
Вы используете устаревший браузер.Он может некорректно отображать этот или другие веб-сайты.Вам следует обновить или использовать альтернативный браузер.
ПЕРЕЙДИТЕ В АДМИНИСТРАТИВНУЮ ПАНЕЛЬ > ДОПОЛНЕНИЯ И УСТАНОВИТЕ БОКОВУЮ ПАНЕЛЬ VERTIFORO, ЧТОБЫ ПРОСМОТРЕТЬ ФОРУМЫ И БОКОВУЮ ПАНЕЛЬ
B uil даблТребуются другие заводские продукты
Дополнительные заводские продукты: щепа для лесопилки/щепа для измельчения досок, клей 3M Adhesive’s Glue
Построен в округе Плезант-Вэлли
.

Этот цвет означает, что он применим только к версии карты округа Плезант-Вэлли.
входов | , полученные от | |
Пиление / Лесное хозяйство / Доска Чипов / Отправляются 3м. | ДСП |
Теперь на земле есть значки, чтобы вы знали, что там есть подсказка глобальной компании:
- Автор
- Раппрам
- просмотров
- 1 011
- Последнее обновление
Производство ДСП в Гермерсхайме, Германия с 1973 года – Rheinspan
Мы производим ДСП в Гермерсхайме (Пфальц, Германия) с 1973 года, однако уже в 1951 году мы производили ДСП. Таким образом, Rheinspan является старейшим действующим производителем ДСП в мире. В семейной компании работает около 200 сотрудников. Современные линии по производству ДСП ежедневно производят более 1500 м³ ДСП. Самые большие доски имеют максимальные размеры 2,62 м x 7,20 м, и после завершения они обрезаются на заказ по размерам, указанным заказчиком.
Мощность производственной площадки
- 550 000 м³/год необработанной ДСП толщиной Ø 17 мм
- 9 000 000 м²/год из меламиновой ламинированной плиты
- Резка в размер: 380 000 м³/год
Основание для сравнения: С таким количеством необработанной ДСП можно было бы покрыть автобан от Зальцбурга, Австрия, до Фленсбурга, Германия, а меламиновой ламинированной плитой можно было бы покрыть более 900 футбольных полей.Кроме того, расположение в Гермерсхайме дает нам ценную возможность с точки зрения логистики: контейнерный терминал на реке Рейн расположен всего в восьми километрах от завода и, таким образом, обеспечивает прямое сообщение с портами Атлантического океана.
Вы можете узнать больше о прессах для ДСП и делительных пилах, используемых на заводе в Гермерсхайме, по ссылке:
Пресс для ДСП Dieffenbacher CPS
- Длина: 38.00 м / 41,34 дюйма
- Ширина: 2,62 м / 41,34 дюйма
- Толщина: от 8 мм до 49 мм
- Производительность в день: ок. 1500 м³
Пресс короткого цикла Wemhöner
- Крупнейший в Европе пресс для ламинирования меламина из рулона
- Длина: от 5,20 м до 6,70 м, вкл. косой разрез
- Ширина: от 2,07 м до 2,55 м
- Толщина: от 8 мм до 49 мм
- Производительность в день: ок.30 000 м²
Делительная пила Holzma HQP 66/27/75 (Holzma 2)
- Длина: от 3,75 м до 7,52 м
- Ширина: от 2,00 м до 2,62 м
- Толщина: от 8 мм до 49 мм
- Производительность в час: ок.