Водопоглощение газобетона — на что влияет и как уменьшить
Газобетон является пористым материалом, который хорошо впитывает влагу, но также быстро он эту влагу отдает. Если дом построен из газоблока, причем без отделки, то под проливным длительным дождем стены намокнут максимум на 30 мм. Это связано с капилярным подсосом данного материала.
Другими словами, влага в газобетоне старается пройти, но на пути ее располагаются пузырьки воздуха, которые препятствуют дельнейшему капилярному проникновению воды.
Знать эту информацию нужно для того, чтобы здраво оценивать намокание блоков в реальных условиях, ведь противники газобетона заверяют, что мокрый газобетон намного хуже сохраняет тепло. Да, отчасти это так, но блок намокает далеко не полностью, а всего на три сантиметра, причем только с внешней стороны стены. В результате, на общую теплоэффективность это не сильно повлияет, тем более, что высыхает газоблок также быстро.
Вопрос водопоглощения и морозостойкости газобетона задают люди, которые планируют оставить свой дом на зиму без отделки, опасаясь того, что газоблоки начнут крошится.
В данном контексте отметим, что газоблоки принято класть на специальный клей, в состав которого входят специальные водоудерживающие добавки. Если укладку производить на обычный цементный раствор, то газобетон быстро впитает все влагу, не давая возможности раствору затвердеть.
Единственное место где газоблоки укладываются на цементный раствор – первый ряд на гидроизоляцию. Причем эти газоблоки желательно намочить водой, а сам растворный шов должен быть минимум 20мм.
На строительных сайтах, а также на каналах ютюба можно встретить множество тестов газобетонных блоков. Но далеко не все тесты дают объективную оценку водопоглощению газобетона. К примеру, берут небольшой кубик газобетона 10×10 см, кладут его в ведро с водой, и прижимают сверху камнем, чтобы блок не всплывал. Далее блок взвешивают и разрезают, показывая процент вобравшейся воды.
Но давайте разберемся в этих сомнительных тестах.
Во-первых, газоблоки в реальных условиях подвержены максимум проливному дождю, и никто не будет наполнять свой дом доверху водой. Таким образом, в реальных условиях намокание происходит капилярным способом, а в условиях погружения кубика в воду, влияет еще и давление воды в ведре.
Во-вторых, маленькие блоки, в процентном соотношении, напитываются водой намного сильнее, чем блоки большего размера.
В-третьих, в реальной жизни газоблоки намокают только с одной стороны, исключением является ситуация с недостроенным домом без крыши, когда дождь заливает со всех сторон.
Как итог данной статьи отметим, что газобетон является хорошим материалом, водопоглощение которого не является критичным, так как под дождем он намокает максимум на 30 мм, после чего быстро высыхает. На теплопроводность намокание влияет минимально, процентов на 10%.
Свойства газобетонных блоков: разбор плюсов и минусов
Имеют ли газобетонные блоки недостатки? В последнее время этот вопрос интересует многих. Материал становится все более популярным, а спрос на него растет в геометрической прогрессии. На современном строительном рынке изделия из газобетона все увереннее занимают лидирующие позиции. Какие именно плюсы и минусы имеют свойства газобетонных блоков, в каких конкретных технологических процессах по строительству их использование оптимально, а в каких существует альтернатива. Как не переплатить за материал и работу, и не раскаиваться о содеянном в последствии.
Свойства газобетонных блоков
Легкость и размер
Блок D500 размерами 30х25х60 см весит около 30 кг, для кладки того же объема потребуется 22 кирпича, вес которых в два раза больше, около 80 кг. Благодаря большим габаритам и легкому весу этапы строительства осуществляются быстрее, чем из других материалов. Такие монтажные работы может выполнить даже один человек. Эти характеристики снижают затраты на транспортировку и расходы на устройство фундамента. Высокая точность и большие размеры блоков позволяют возводить стены с минимальными отклонениями и высокой скоростью. Соответственно снижаются затраты на внешнюю отделку.
Теплопроводность
Ячеистая структура создает теплоизоляционный эффект. Также данный материал способен сохранять тепло, а в летний сезон – приятную прохладу. Здесь следует отметить, что теплопроводность газобетонного блока толщиной 375 мм равнозначен кладке из кирпича более чем в полметра. За счет наличия газовых (воздушных) пор изделия имеют высокое удельное тепловое сопротивление, что обеспечивает хорошие теплоизоляционные свойства газобетонных блоков. Это утверждение справедливо, когда полости действительно заполнены газом или воздухом, т.е. когда материал хорошо высушен. Картина резко изменяется при наличии повышенной влажности.
Теплопроводные свойства газобетонных блоковИсходя из величины удельного теплового сопротивления газобетона, для обеспечения нужной теплоизоляции нормируемая (рекомендуемая) толщина стены из газобетонных блоков составляет 375-380 мм, что считается преимуществом этого материала по сравнению с другими.
Однако в реальности даже под воздействием влаги при нормируемой строительными стандартами величине влагопоглощения (12%) тепловое сопротивление снижается на 30-32%.
Кроме того, при кладке стен из блоков используется, как правило, обычный цементный раствор, что уменьшает тепловое сопротивление еще на 25% (при применении специальных дорогостоящих клеевых составов – до 10%). Таким образом, для обеспечения равных условий тепловой защиты в реальных условиях необходимо увеличить толщину стены на 55-57%. В районах с повышенной влажностью водопоглощение может превысить 30%, что еще больше увеличивает требуемую толщину стены. Эти обстоятельства делают сомнительными преимущества газобетона в части тепловой защиты.
С приходом зимы выясняется, что стены из газобетона продуваются достаточно сильно. Недостатки можно устранить, используя специальный тонкослойный клеевой раствор (3-5 мм) для пенобетона. Но на практике он используется редко, так как работа с ним требует определенных навыков каменщика и стоит дороже.
Газосиликатные блоки стоят ненамного дешевле обычного кирпича, и привлечение к строительству высококвалифицированных специалистов ставит под сомнение целесообразность применения этого материала. К тому же экологическая чистота этого клея пока еще остается под вопросом. Газосиликатные блоки, уложенные с использованием цементно-песчаного раствора, ухудшают теплосопротивление кладки на 25%.
Не всегда положительно сказывается и свойства газобетонных блоков, связанные с малой инерцией нагрева. Отчасти проблему можно компенсировать применением внутренних перегородок, использованием панельных или монолитных перекрытий из бетона. Но из-за большой площади стен разница между кирпичным или бетонным домом (с эффективным утеплителем) все равно будет существенной.
Дома из газобетона обладают небольшой тепловой инерцией (камня в нем 5-15%). Вымерзшее в морозную погоду строение прогревается достаточно быстро – за 1,5-2 часа температуру воздуха можно поднять от 0 до +20°С. Конечно, это характеризует газобетон с положительной стороны, но проблема заключается в том, что дом так же быстро и остывает.
Использование специального клеящего состава вместо обычной цементной смеси минимизирует эффект от мостиков холода. Это снижает теплопотери с 25% до 8-10%. Количество используемого клея существенно меньше, до 5 раз, по сравнению с цементным раствором.
Морозостойкость
При соблюдении технологии на всех этапах строительства, данный материал способен выдержать более 25 циклов заморозки/оттаивания.
Высокая морозостойкость газобетонных блоков в фасадных стенах на практике не подтверждается. Это во многом объясняется водопоглощением и накоплением воды в порах материала. При этом вода при низких температурах в полостях замерзает, а, расширяясь, создает внутреннее напряжение в блоках. Морозостойкость конструкционно-теплоизоляционного газобетона марки D500 составляет всего лишь 25 циклов (норма – не менее 50 циклов). Это ограничивает применение газобетона для фасадных стен или требует дополнительной защиты. Рекомендован этот сорт для использования в строительстве в климатических условиях, не превышающих -18°С.
Характеристика морозостойкости говорит о том, сколько раз конструкция из газобетонных блоков может выдержать замерзание-оттаивание без значительных повреждений и деформаций. При достижении показателя в 25 циклов газобетон марки D500 начинает терять в показателях прочности и других характеристиках. Значительной морозостойкости можно достичь при использовании более плотных блоков. Но следует помнить, что они являются уже не теплоизоляционными, а конструкционными, и, следовательно, увеличивают толщину стен.
Паропроницаемость и газопроницаемость
Преимуществом материала считается высокая паро- и газопроницаемость, что дает возможность стенам «дышать». Но эти свойства газобетонных блоков имеет и отрицательную сторону. Высокая проницаемость воздуха хороша при теплой и нормальной температуре, но при холодной, а особенно при ветреной, погоде проникновение в дом холодного воздуха заметно снижает тепловую защиту газобетона. Холодный «сквозняк» проходит прямо через фасадную стену.
Отрицательная сторона паропроницаемости сказывается при использовании газобетона в строительстве бань, саун. В этом случае имеет место переувлажненный пар, который, проходя через пористый материал, вызывает абсорбцию воды в порах. Для предотвращения накопления воды в толще газобетона следует изготавливать парозащитный барьер в виде грунтовки, штукатурки или облицовки. Это, во-первых, приводит к удорожанию строительства; во-вторых, исключает реализацию одного из важнейших преимуществ газобетона – «выветривание» пара из помещений.
Звукоизоляция
Известное свойство материалов — при меньшей плотности и большом объеме, обладать высокими звукоизоляционными качествами. Газобетон имеет именно такую структуру. Полученная в результате химической реакции между пудрой алюминия и известью, легкая ячеистая масса газобетона наполняется воздушными пузырьками. Такой состав материала будет хорошим препятствием для звуковой волны.
Звукоизоляционные свойства газобетонных блоковИндекс шумопоглощения для газобетонных блоков в среднем 43- 44 дБ. Норма для жилых помещений, выведенная на основе свойств строительных материалов, равна 41 дБ.
Повысить звукоизоляционные свойства можно, если увеличить зазор между слоями блоков. Этой цели можно добиться, применяя соответствующие отделочные материалы. Оштукатуренные с обеих сторон стены способны обеспечить звукоизоляцию до 50 дБ! Устранить посторонние звуки поможет сочетание данного строительного материала с отделкой из пенопласта и других вспененных материалов.
Влагопроницаемость и водопоглощение газобетона
Недостатки блоков из газобетона особенно проявляются в холодное время года при повышенной влажности; и на то есть свои причины.
Один из главных недостатков газобетона – повышенные влагопроницаемость и водопоглощение. Этот недостаток определяется наличием пор в толще материала. Вода, проникая внутрь газобетона, абсорбируется в полостях и накапливается. Даже установленные строительные нормы допускают накопление влаги до 12% массы материала. Высыхание из-за изолированности пор происходит медленно. Высокое водопоглощение влияет на все основные свойства газобетонных блоков, заметно ухудшая их.
Газобетон – сильный абсорбент влаги и усиленно впитывает ее из окружающего пространства. Поэтому профессионально сделанный и качественный паровой барьер просто обязателен. Для этого стены необходимо обработать грунтовкой глубокого проникновения и только после этого приступать к шпатлеванию внутренних поверхностей.
Если проект дома не предусматривает отделку внешних стен декоративными отделочными материалами, поверхность фасада необходимо гидрофобизировать. Причем повторять эту манипуляцию необходимо раз в 2-3-летний период. Для этих целей производители рекомендуют использовать только гипсовую штукатурку, так как цементно-песчаные растворы имеют свойство растрескиваться и отслаиваться.
Механическая прочность и несущая способность газобетона
При использовании газобетонных блоков строители сталкиваются с дилеммой. Для обеспечения высокой механической прочности необходимо выбирать материал с высоким удельным весом; в то же время в газобетоне повышенной плотности заметно снижены теплоизоляционные свойства. Такая альтернатива приводит к тому, что обычно применяется газобетон с плотностью 400-500 кг/м³, что не может обеспечить высокой механической прочности.
При строительстве стен из газобетонных блоков проявляется ряд недостатков материала в части обеспечения механической прочности. Так, при возведении перекрытий их плиты или балки срезают и крошат газобетон, что требует дополнительных элементов: специального железобетонного армирующего пояса или опорной подушки. Это приводит к возникновению «мостиков холода» и заметно снижает тепловую защиту. Кроме того, необходимость сложных дополнительных элементов ведет к удорожанию строительства.
Использование газобетона плотностью менее 500 кг/м³ не может обеспечить необходимую механическую стойкость на сжатие.
Газобетонные блоки такой прочности обладают хрупкостью, к тому же следует добавить низкую стойкость к изгибу. Это практически ограничивает строительство вверх – возведение сооружений выше одноэтажных нежелательно.
Отрицательные механические свойства газобетонных блоков: недостаточная стойкость на изгиб, т.е. низкая эластичность. В процессе эксплуатации фундамент любого строения подвергается небольшим усадкам, которые спокойно переносят кирпичные или деревянные стены. Другое дело – газобетон. Уже через 1-2 года на блоках появляются микротрещины. Через 3 года такому растрескиванию подвергается до 25% всех газобетонных блоков.
Трещины газобетонных блоковПоявление микротрещин не ведет к быстрому разрушению стен, но заметно снижает их механическую прочность и может проявиться в будущем. Особенно опасно то, что со временем эти трещины расширяются, а их количество растет. Увеличение усадки фундамента приводит к серьезному растрескиванию газобетона.
Все это приводит к необходимости в качестве фундамента возводить массивные цокольные полуэтажи из обычного бетона. Для небольших жилых строений такой фундамент просто не выгоден экономически.
Опасно поведение и швов в стенах из газобетонных блоков. Со временем шовный раствор заметно растрескивается и отходит от поверхности блоков, даже без усадки фундамента. Через 7-10 лет блоки практически просто лежат друг на друге под своим весом. Существенное растрескивание газобетона замечено в местах прохождения металлической арматуры или колонны несущего каркаса без воздействия деформаций фундамента.
К большим недостаткам применения газобетона следует отнести и поведение штукатурки, выполненной по газобетонным блокам. На штукатурке уже через небольшое время появляются трещины, как правило, по швам между блоков. Такие трещины возникают как на цементной, так и на гипсовой штукатурке. Особенно активно они возникают при воздействии низких температур снаружи стены. Следует заметить, что чем больше мороз на улице, тем трещин больше внутри помещения. Производители рекомендуют использовать штукатурку на гипсовой основе, и она действительно имеет высокий уровень адгезии с газобетонной поверхностью. Но при резких термических перепадах у такой стены немедленно образуются трещины, повторяющие контуры кладки. Эти места необходимо укреплять монтажной сеткой, что дополнительно повышает стоимость отделочных работ.
Конструкционно-теплоизоляционная марка D500 предназначена для строительства домов высотой до 3-го этажа. Ее несущей способности хватает для выдерживания нагрузки всей конструкции дома и плит перекрытия. В этом моменте всплывает одно «но!». При этом в местах опоры плит перекрытия и иных нагружаемых элементов возникает необходимость возведения железобетонного армопояса или обычной кирпичной кладки, которые являются мостиками холода. Дома большей этажности из газосиликата не возводят, так как газобетон повышенной плотности (D900-D1200) не отличается хорошей теплоизоляцией и увеличивает стоимость строительства.
Легкость обрабатывания и технологичность газобетона
Придать ему любую форму можно при помощи ручных средств, например, ножовки или пилы. Блок легко режется, сверлится. Выполнить штробление, забить гвоздь или проделать рабочее отверстие под розетку не составит труда. Но в то же время сильно ограничено и такое преимущество газобетона, как технологичность. В блоки действительно легко вбиваются дюбеля и гвозди, но из-за хрупкости материала они так же легко вылетают после забивания. Особенно заметно проявляет себя этот недостаток газобетона при использовании анкеров или шурупов. Такие крепежи плохо держатся в блоках, что значительно осложняет облицовку или укрепление кладок. Эта проблема решается только применением специальных крепежных дюбелей и анкеров с пластиковыми капсулами, что тоже ведет к удорожанию конструкции.
Экологичность, биологическая стойкость и пожаробезопасность
Новые технологии дают возможность производить этот материал из сырья, не выделяющего токсичных веществ. Показатель радиоактивного фона 54 Бк/г при допустимой в жилищном строительстве норме в 370 Бк/г. Согласно ГОСТу 30108-94* «Материалы и изделия строительные. Определение удельной эффективной активности естественных радионуклидов»:
Класс | Удельная эффективность естественных радионуклеидов, Бк/г | Материал |
---|---|---|
1 | до 54 | дерево, гипс, газобетон, арболит |
2 | 54-120 | тяжелый бетон, керамзитбетон |
3 | 120-153 | глиняный кирпич |
4 | 153-370 | керамзит, керамическая плитка |
При этом не подвержен горению, гниению, воздействию насекомых. Сырье, используемое в производстве, имеет минеральное происхождение, по своим свойствам – не горючее. Поэтому блоки способны выдержать воздействие открытого пламени в течение 3 часов.
Газобетонные блоки стойкие к повреждениям различными микроорганизмами, грызунами и насекомыми. Хотя небольшой зеленый налет на нем все же может образовываться, но только в случае постоянного увлажнения.
Подведем итоги: разбор минусов газобетона
Основные недостатки газобетона заключаются в восприимчивости к влаге и завышенных показателях морозостойкости. Гигроскопичность бетона снижает теплотехнические свойства газобетонных блоков и приводит к деформациям, способствующим появлению дефектов отделки. Это ограничивает его применение в районах с повышенной влажностью, в сырых помещениях, а также при строительстве фасадов. Во избежание этого перед отделкой необходимо применение дорогостоящего комплекса мер по защите стройматериала от конденсата.
Реальная морозостойкость материала значительно ниже заявляемых значений, что делает нецелесообразным использование газобетона для жилых домов в районах с холодным климатом. Сильное снижение теплового сопротивления при увлажнении заставляет увеличивать толщину стен, что снижает преимущества газобетона по сравнению с другими стройматериалами.
Изъяны в механической прочности газобетона требуют строительства дорогостоящих видов фундамента и применения специальных крепежных элементов. Строительство домов с несколькими этажами не допускается или требует специальных упрочняющих операций. Наложение защитной или декоративной штукатурки вызывает осложнение из-за растрескивания.
Недостатки газобетона значительно ограничивают его применение при строительстве жилых домов и бань. В то же время преимущества позволяют широко применять его при возведении хозяйственных построек, ограждений и других строений.
При близком рассмотрении вопроса о заявленной низкой стоимости газобетона и гарантированной долговечности выходит, что эти характеристики оказываются значительно завышенными производителями.
При соблюдении норм в отношении показателей теплосопротивления заявленная производителями кладка толщиной в 380 мм является недостаточной. Игнорирование нормативов ведет к повышенному расходу энергии на отопление и кондиционирование. Для того чтобы здание соответствовало всем стандартам, толщину кладки необходимо увеличить как минимум до 640 мм. При этом максимальная толщина газоблока составляет 500 мм.
Еще одним недостатком газобетонной кладки является необходимость возведения монолитного ленточного фундамента, использование которого ведет к существенному удорожанию строительных работ. Без такого фундамента риск появления усадочных деформаций и возникновения массивных трещин в кладке значительно возрастает.
При изучении вышеописанных фактов напрашивается вывод, что такие достоинства свойства газобетонных блоков, как высокие показатели теплоизоляции и несущая способность перекрытий из газобетона, являются значительно преувеличенными и носят исключительно навязчивый рекламный характер. В защиту газосиликата хочется сказать, что на данный момент идеальных стройматериалов не существует, и каждый из них имеет как свои минусы, так и неоспоримые достоинства. Хотя, например, если сравнить свойства газобетонных блоков со свойствами арболита, то у последнего явное преимущество!
По материалам: http://ostroymaterialah.ru/smesi/gazobeton-nedostatki.html
http://o-cemente.info/vidi-betonnih-smesej/gazobetonnye-bloki-dostoinstva-i-ned.html
причины разрушения, защитные меры, цена блоков
Влагопоглощение пеноблоков почти вдвое ниже по сравнению с прочими видами легких бетонов. Но заявляемая производителями влагостойкость редко соответствует действительности. Она колеблется в промежутке 7-12 %, фактически же нередко превышает 18 %.
Оглавление:
- Технология изготовления
- Вред влаги
- Способы защиты
- Обработка своими руками
- Цены за м3
Процесс производства
При этом процессе образуется два вида крупных пор:
- «хорошие» или закрытые, непроницаемые для влаги;
- «плохие», связанные между собой и с наружной поверхностью.
За водопоглощение ответственны вторые, и даже незначительное нарушение технологии изготовления увеличивают их пропорцию. Если перемешивание составляющих продлится лишнюю минуту, влагостойкость упадет на 2-5 %.
На качество пор влияет пенообразователь. В себестоимости продукта его доля существенна, поэтому для снижения затрат производители стараются найти реактивы дешевле, свойства которых неустойчивы. При одинаковой пене получаем партии товара, где водопоглощение отличается в разы.
Насыщение влагой обеспечивают не только осадки или протечки водопровода, еще это вода, которую используют при производстве. Ее добавляют приблизительно 20 % от всего объема смеси, цементом же связывается едва ли треть. По этой причине только что изготовленные пеноблоки имеют влажность как минимум 14 %.
Чем плохо водопоглощение?
Обычная аш-два-о бетону не вредит, проблемы начинаются, когда добавляются другие факторы. Самых опасных три:
Лед распирает поры изнутри, ломая их тонкие стенки. При этом влагоизоляция падает, процесс разрушения ускоряется. Через время поверхность блоков начинает шелушиться, растрескиваться.
- Химическое воздействие растворенных веществ.
Бетон имеет щелочную химическую реакцию. Поэтому когда у попадающей влаги кислотность превышает определенное значение, она его разрушает. Еще хуже действуют на пеноблоки аммонийные соединения, сульфаты, соли магния. Эти вещества могут оказаться в воде, особенно когда речь идет о районах с высокой концентрацией промышленных производств.
- Биологическое воздействие.
Наличие влажной, пористой структуры способствует задержанию и развитию разных видов микробов, простейших одноклеточных, растений и грибов. Разрушают бетон процессы жизнедеятельности этих организмов, а также механические повреждения, вызванные их разрастанием в порах.
Методы решения проблемы
Какие защитные меры используют:
- Штукатурку.
- Облицовку водостойкими материалами, устройство вентилируемых фасадов.
- Гидроизоляцию.
- Гидрофобизацию, то есть обработку проблемных мест специальными водоотталкивающими составами.
Все эти меры дают максимальный эффект, применяясь комплексно. К примеру, цоколь здания защищаем керамической плиткой, стены снаружи закроем сайдингом, помещения с повышенной влажностью оштукатурим цементным раствором с добавлением жидкого стекла.
Сегодня помимо обычного строители научились делать влагостойкий пенобетон. Получают его тремя способами:
1. Добавляют специальный состав к пенообразователю. Поры оказываются покрытыми изнутри водостойкой полимерной смесью.
2. Добавляют в сам бетон.
3. Обрабатывают гидрофобизаторами готовые пенобетонные блоки и конструкции из них.
Самостоятельная защита
Сделать это можно, покрыв стены гидрофобными смесями: для этого приобретают готовые средства, которые на порядок повышают влагостойкость кладки. Производят их на основе силиконов и полиакриловых смол. У обоих видов эффективность защиты приблизительно одинакова. К акрилатам порой добавляют пигменты для придания желаемого цвета. Заплатить придется больше, но помимо влагоизоляции они делают поверхность прочнее.
Особняком стоят пенетрирующие составы. Они основаны на эффекте некоторых веществ реагировать с водой, образуя нерастворимые соединения. Эти реактивы не создают на материале влагостойкой пленки или чего-то подобного. Но как только вода проникает в микротрещину, она тут же закупоривается нерастворимой пробкой. Такие смеси оставляют возможность стене «дышать».
Обработка любым типом гидрофобизатора выполняется как обычная окраска. Нам потребуется малярный валик на длинной ручке с шубкой средней длины ворса, широкая кисть, стремянка, емкость под реактив, защитная одежда, очки и перчатки.
Стоимость
Способность впитывать зависит от плотности пеноблока, которая в свою очередь влияет на цену.
Стоимость простых блоков и с гидрофобизатором:
Наименование | Цена, руб/м3 | |
Обычные | Обработанные | |
D600 | 2550-2700 | 2720-2900 |
D700 | 2950-3340 | |
D800 | 3400-3650 | 3620-3820 |
D1000 | 3700-3870 | 3900-4080 |
Стоимость окрашенных блоков совпадает с ценой более прочных. Но если водопоглощение у них близко к нулевому, то у бетона с высокой плотностью выше лишь на 10-12 %. Для влагоизоляции дешевле потратиться на окраску, чем купить пенобетон на марку выше.
Защищаем газобетон от влаги
Распространенное мнение, что газобетон впитывает часть воды, как губка, связано с его пористой структурой, которая формируется в процессе производства. При этом накопленный объем воды газобетон держит в себе.
Незначительный уровень водопоглощения газобетона обусловлен тем, что поры в этом материале не только закрытые, но и открытые. Ячеистый газобетон впитывает влагу на 6-8%, так как обладает свойством гигроскопичности. Учитывая это свойство блоков, необходимо создавать дополнительную защиту от влаги. Защита материала предусматривается не только для построенных стен, но и при транспортировке и хранении.
По мнению специалистов, чтобы основательно разрушить газобетон, необходимо, чтобы газобетон длительно оставался при непосредственном контакте с водой, т. е. газобетон должен полежать в воде.
Готовый газобетонный блок состоит примерно на 75 % из пор. Причем наибольший объем приходится на макропоры, которые образуют округленные пустоты и межпоровые перегородки.
Эксплуатационная влажность газобетонных изделий – 4–5 %. При этом критическая для материала влажность, влекущая за собой его разрушение, для газобетона плотностью 400 кг/м³ составляет 45–50 %. Аналогичные показатели для газобетона плотностью 500 кг/м³ – 40 %.
Благодаря пористой структуре, материал «дышит» и, соответственно, обладает высокими свойствами теплоизоляции и звукоизоляции. Впитывание большого количества влаги приводит к изменению этих свойств в худшую сторону. Для того чтобы газобетон не впитывал влагу, проводится дополнительная обработка.
Он активно впитывает влагу из окружающей среды при дожде, мокром снеге, а также весной, когда снег тает. Если не создавать защиту, газобетон может впитывать до 35% влаги относительно своей массы. Такой процент влаги резко снижает теплосопротивление, и в помещениях становится сыро и холодно. Газобетон может потрескаться зимой, если осенью помещения не прогревались и материал впитал в себя большое количество влаги.
Влажность газобетона, применяемого для возведения стенки здания, зависит от количества сезонов эксплуатации дома, от того, какова конструкция стенки и сорбционность. К примеру, влажность газобетона стенки дачного домика, который не задействован в жилых целях в холодное время года, не играет какой-либо важной роли. Если же минеральный материал газобетон закрыт от осадков надежной кровлей, то в таком режиме пользования зданием он будет невредимым всегда.
Влага может попадать в помещение снизу из некачественного фундамента или из мест соединения стен с поверхностью земли; снаружи, при изменении времени года, осадки; изнутри при неправильной работе системы кондиционирования, затоплении.
По заверению производителей, какое-то количество воды может неглубоко проникать внутрь материала, однако именно капиллярно-пористая структура блока позволяет ему достаточно легко и быстро отдавать влагу назад, т. е. в структуре намоченного газобетона жидкость долго не задерживается.
Газобетон с легкостью отдает накопленную часть воды наружу, когда воздух в помещении становится излишне сухим, стена из этого материала обеспечит увлажнение.
Количество воды, проникшее в газобетон, в первую очередь ухудшает его теплоизоляционные свойства. Чем выше водопоглощение, тем ниже реальные теплоизоляционные свойства материала.
Стены из газобетона, напитываясь водой, создают дополнительные весовые нагрузки в конструкциях, в устройстве которых они используются. Соответственно, чем выше поглощение воды имеет газобетон, тем больше риск возникновения аварийной ситуации.
Сфера воды сама по себе является разрушительным фактором. Постоянное присутствие воды в газобетоне может привести, как минимум, к снижению прочности.
В настоящее время наибольшее практическое применение нашли два метода, как защитить газобетон от воды, – это гидроизоляция и гидрофобизация.
Гидрофобизаторы — составы, которые поставляются в виде концентратов или готовых к применению растворов, водных или на органических растворителях. Они не создают поверхностной пленки, а образуют водоотталкивающий (гидрофобный) слой глубиной до нескольких миллиметров. Паропроницаемость обработанной поверхности почти не снижается, т. е. часть воды испаряется, а внутрь не попадает. Обработанная гидрофобизатором поверхность, как правило, не изменяет цвета. Гидрофобное покрытие значительно увеличивает морозостойкость любого материала.
Данные свойства позволяют применять гидрофобизаторы по силикатному и керамическому кирпичу, бетону и газобетону, известнякам, травертину, ракушечнику, граниту, мрамору и даже по тротуарной плитке.
Водоотталкивающий эффект обусловлен проникновением гидрофобизатора в газобетон на глубину от 5 до 50 мм, в зависимости от его плотности и влажности. Закрепляется гидрофобизатор по истечении 12–24 часов. При этом в капиллярах материала образуются кристаллы, которые препятствуют проникновению воды в газобетон. Но это не препятствует проникновению воздуха.
Что касается гидроизоляции, то специалисты отмечают: во многом исключить негативное воздействие воды на газобетон помогает устройство стены. В идеале «пирог» стеновой конструкции должен быть таким, чтобы внешний слой был значительно более проницаем для паров, нежели внутренний. Это позволит не только эффективно удалять часть воды из помещений, но и препятствовать проникновению в дом воды с улицы.
Чтобы блоки не впитывали в себя влагу, используют различные способы защиты.
Обработка внутренней поверхности стен грунтовкой глубокого проникновения с последующей обработкой шпаклевкой для внутренних работ. Таким образом создается паровой барьер. Для создания такого барьера нельзя использовать традиционную штукатурку без обработки грунтовкой с приклеиванием на поверхность обоев. При использовании традиционной штукатурки происходит отсыревание газобетона от влаги изнутри помещения. Штукатурка трескается и отслаивается. Обработка внешней стороны стены проводится гипсовой штукатуркой, цементно-песчаная не подходит, так как отслаивается. Обработку гипсовой штукатуркой проводят один раз каждые 2-3 года.
Использование отделки внешней стороны стен декоративными материалами, например, плиткой, камнем и так далее. Декорирование будет защищать слой штукатурки на поверхности газобетона.
Внешняя сторона обкладывается кирпичом. Так как цементно-песчаный раствор хорошо пропускает пар между кирпичной кладкой и стеной из газобетона, оставляют воздушный зазор. Ширина зазора составляет примерно полкирпича. В строительстве таким способом возникает одна небольшая проблема: как зафиксировать фасадную стену, если она возводится с зазором. Проблема решается, используя анкерные элементы, которые устанавливаются через каждые 5 рядов выложенного кирпича. В качестве анкеров не рекомендуется использовать обычную арматуру или стальной уголок, так как эти элементы подвержены коррозии. Со временем жесткой связи между несущей стеной и фасадом не будет. Фасадная стена обвалится. В качестве анкеров используют популярный на рынке строительных материалов стеклопластик или нержавеющую сталь.
Отделка фасада сайдингом. Способ намного хуже, чем кирпичная кладка, применять его не рекомендуется, так как по окончании работ очень много скрытых проблем. Конечно, может, отделка и смотрится красиво и цена в несколько раз меньше, но долговечность строения из газобетона уменьшится.
Применение железобетонных сэндвич-панелей, в основе которого находится судостроительный бетон с величиной водного сопротивления W
Вместе с отделкой внутренней и наружной стен из газобетона проводятся работы по гидроизоляции фундамента, так как влага может проникать через неправильно сооруженный фундамент. Для этого при постройке стен блоки газобетона выкладываются над уровнем земли от 30 до 50 см.
При качественном оборудовании оконных проемов, декоративных выступов и крыш водоотводами, а также качественной гидроизоляции цоколя, дом, материалом которого является газобетон, может простоять не один десяток лет без возникновения каких-либо конструкционных дефектов.
При проведении строительных работ не оставляйте газобетон под открытым небом, так как при дожде очень быстро впитывается влага и ухудшаются его свойства. Не рекомендуется распаковывать газобетон полностью.
Не рекомендуется проводить застройку сооружений из газобетона с ноября по март. В этот же период нецелесообразно проводить оштукатуривание поверхностей стен. Излишняя влага ухудшит свойства блока, а штукатурка при высыхании в более жаркий, засушливый период будет отслаиваться и осыпаться. В этом случае все штукатурные работы надо повторять.
Пенобетон и газобетон в чем разница, компания градовой
Пенобетон и газобетон в чем разница?
VS
В современном домостроении успешно применяются газобетон и пенобетон. Оба материала иногда именуются газобетоном, хотя между ними есть существенные отличия. Объединяет эти виды бетона то, что они обладают малым весом и хорошими теплоизоляционными свойствами.
Специфика пеноблоков и газосиликатных блоков накладывает ряд ограничений на их использование при строительстве зданий и конструкций. При разработке проекта жилого дома обязательно нужно учитывать нюансы данных стройматериалов. При соблюдении технологии из блоков можно построить любой дом высотой 2-3 этажа, который с гораздо большими затратами мог быть возведен из обычного кирпича.
Рассмотрим основные технические показатели пенобетонных и газосиликатных блоков, поговорим об их отличиях и технологии производства.
Ячеистые бетоны получают почти из тех же компонентов, что и традиционный бетон, но придают материалу пористую структуру. Достигается это путем добавления алюминиевой пудры (газобетон) или пенообразователя (пенобетон), после чего в бетоне появляются пузырьки, равномерно распределяющиеся по всей массе.
Пенобетон обладает менее однородной структурой по сравнению с газобетоном. Но его легче изготавливать, себестоимость изделий получается ниже. Зато газосиликатные блоки (газобетонные) обладают более выраженными теплоизоляционными свойствами при равной прочности. Следовательно, пеноблоки необходимо приобретать с несколько большим запасом прочности, чем того требует проект. При возведении газобетонных построек можно использовать газоблоки с меньшей прочностью, чем у пеноблоков. Специалисты советуют применять при возведении двухэтажных строений газоблоки марки D400 или пеноблоки D500-D600.
Газоблоки получают путем разрезания монолитной массы на высокоточном оборудовании. Это позволяет изготавливать блоки с правильной геометрией и минимальными отклонениями от заданных размеров. За счет высокой точности исполнения блоков можно строить идеально ровные стены с клеевыми швами толщиной всего 3 мм. Минимальная толщина шва между блоками предотвращает появление «мостиков холода», что на 20% увеличивает теплотехнические показатели строения.
Так как пенобетонные блоки изготавливаются методом заливки раствора в формы, их размеры не столь точны, а это приводит к увеличению погрешностей при укладке. Соответственно, стены получаются с большими неровностями, которые необходимо нивелировать толстым слоем штукатурки.
Пенобетон тоже имеет выгодные отличия от газобетона. Его микроскопические поры имеют замкнутую оболочку и не связаны друг с другом капиллярами. В газобетонных блоках воздушные поры переходят одна в другую, поэтому вода просачивается внутрь достаточно быстро. Кусок пенобетона может месяцами находиться в воде и оставаться сухим внутри, а газосиликатный блок промокает насквозь за несколько часов. Высокое влагопоглощение газобетона делает невозможным его применение в местах с высокой влажностью. Например, при строительстве стен подвалов и цоколей газосиликатные блоки не используются. Из-за впитывания влаги повышается теплопроводность газобетона, поэтому конструкции из такого материала требуют качественной гидроизоляции.
Показатель паропроницаемости у пенобетона и газобетона существенно выше, чем у железобетона и кирпича.
Пеноблоки изготавливаются не только в заводских условиях, но и прямо на стройплощадке. Это упрощает процесс строительства и снижает стоимость возводимых объектов. Из газоблоков можно возводить более прочные конструкции, не требующие больших трудозатрат при отделке благодаря идеально ровной геометрии кладки.
Цены на пенобетонные блоки Цены на газобетонные блоки Цены на газосиликатные блоки
© «ГРАДОВОЙ», 2020
Что лучше — пеноблоки или газоблоки
Два основных представителя ячеистого бетона – пенобетон и газобетон. Эти материалы отличаются технологией производства, блоки из них одинаково успешно используются в строительстве. Что бы понять что лучше – пеноблоки или газоблоки – нужно узнать параметры каждого материала и сравнить их.
Показатель | Пеноблок | Газоблок |
Состав | песок, цемент, вода, пенообразователь | песок, цемент, вода, алюминиевая пудра |
Отвердевание бетона | в естественных условиях | автоклавное или в естественных условиях |
Плотность, кг/м3 | 300 — 1200 | 300 — 1200 |
Теплопроводность, Вт/(м*0К) | 0,08 — 0,38 | 0,08 — 0,38 |
Коэффициент паропроницаемости | 0,08 – 0,26 | 0,23 — 0,28 |
Класс прочности | В1-2 | B2-2,5 |
Экологичность | могут содержать химические добавки для пенообразования | экологичны |
Геометрия | возможны отклонения по всем параметрам до 5 мм | максимальные отклонения: по длине до 3 мм, по толщине до 1 мм, по ширине до 2 мм |
Влагопоглощение | до 14% | до 20% |
Морозостойкость | 50-100 циклов | 50-100 циклов |
Таким образом, отличия между газоблоками и пеноблоками не такие и существенные. Стоит обратить внимание на возможные различия в геометрии. Укладка газоблоков ведется на клей, а пеноблоков – и на клей, и на цементный раствор. Если пеноблоки значительно отличаются по размерам, то толстый слой цементно-песчаного раствора скроет эти погрешности.
Что касается влагопоглощения, то оно у газоблоков выше за счет того, что поры в газобетоне имеют и открытую и закрытую структуру, а у пеноблоков только закрытые поры. Газоблок быстрее и больше впитывает влагу.
Видео: сравнение пенобетона, газобетона и полистиролбетона
Оба типа блоков выпускаются разной плотности. Что же касается прочности, то при равной плотности газоблоки прочнее. В качестве конструкционных используются газоблоки плотностью от D500 и выше и пеноблоки от D900 и выше.
О значительных различиях между газоблоками и пеноблоками говорить не приходится. Это очень похожие строительные материалы. Они имеют одинаковый вес и могут быть одинаковых размеров. Они одинаково легко монтируются, режутся, гвоздятся. Газоблоки чуть меньше крошатся при обработке за счет автоклавного изготовления. Они почти одинаково хорошо впитывают и так же хорошо отдают влагу, поэтому необходима их отделка. И пеноблоки, и газоблоки по теплоизоляционным качествам превосходят кирпич.
Тот, кто еще задается вопросом, что лучше – газосиликат или пеноблок, нужно понять, что и газосиликатный и пенобетонный блок это хорошие современные материалы, самое главное отличие, которое я за 25 лет строительной практики для себя уяснил — это то, что найти качественный пеноблок очень трудно, а вот качественный газоблок — очень просто. Это обусловлено тем, что оборудование для производства пеноблоков стоит в разы меньше, чем оборудование для изготовления газоблоков, соответственно существует куча кустарных цехов по изготовлению пеноблоков, производящих сомнительные по качеству блоки.
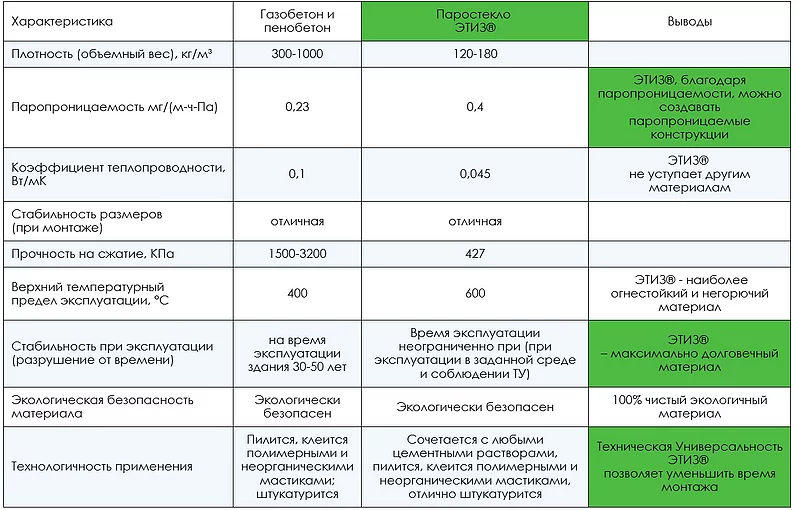
Подбирая материал для возведения стен, необходимо учитывать все качества, включая цену. Пеноблоки дешевле, зато по некоторым техническим характеристикам они проигрывают газоблокам.
Штукатурка и шпаклевка газоблока и пенобетона: выбор материалов, технология
Штукатурка и шпаклевка газобетона, пенобетона
Пористые строительные материалы, как газобетон и пенобетон требуют применения особой технологии оштукатуривания. Их невероятно высокая способность к водопоглощению усложняет процесс отделки. У каждого профессионального строителя существуют свои секреты. Используя их, с задачей по оштукатуриванию и шпатлеванию стен из ячеистого бетона сможет справиться даже новичок. Об основных особенностях выбора материалов для отделки газобетона, пенобетона и гипсокартона, а также их применении мы расскажем просто сейчас.
Сложности оштукатуривания ячеистых бетоновВысокое водопоглощение блоков из ячеистого бетона чревато негативными последствиями при несоблюдении технологии выполнения отделочных работ. Данные материалы, сравнимо с банной губкой, впитывают в себя влагу. При нанесении штукатурного раствора на такую стену, вся жидкость в течение нескольких минут будет поглощена стеновым материалом. В результате не произойдет полноценная гидратация цементного или гипсового вяжущего. Нанесенный слой приобретет рыхлую и сыпучую структуру. Для справки:
Гидратация цемента (гипса) представляет собой процесс, при котором основной компонент раствора в результате химических реакций насыщается достаточным количеством жидкости и после полного твердения образует плотную, твердую структуру (цементный или гипсовый камень).
Для нормальной гидратации цемента раствор должен сохранять достаточное количество жидкости (быть влажным) на протяжении 8-10 часов после нанесения. Только так можно гарантировать, что нанесенный слой получит нужные свойства и будет выполнять поставленную задачу длительное время.
Чтобы снизить влагопоглощение газобетонных или пенобетонных блоков и ГКЛ, важнейший этап подготовки стен – грунтование.
Независимо от способов последующей отделки, а также от того, выполняются работы внутри или снаружи помещения, грунтование газобетонных и пенобетонных блоков является необходимым этапом. Грунтовочные составы используют для получения следующих эффектов:
- Снижение и выравнивание водопоглощения основания. В любом грунтовочном составе имеются полимерные наполнители. Проникая в структуру блоков, они связываются с основанием и уплотняют его. Тем самым снижается свойство впитывания влаги и жидкостей.
- Усиление адгезивной способности стен. Пористые блоки и гипсокартон, за счет высокого водопоглощения, характеризуются невысокой способностью к адгезии. Грунтование стен перед оштукатуриванием позволяет немного улучшить силу сцепления с растворами.
- Обеспыливание поверхности. Наличие большого количества мелких фракций пили и песка на обрабатываемой поверхности негативно сказываются на сцеплении.
Это может привести даже к отслоению нанесенного отвердевшего слоя. Грунтование позволит связать частицы и придать поверхности клейкую структуру.
Для сильно впитывающих оснований рациональнее всего использовать или универсальные или грунтовки глубокого проникновения со свойством снижения влаговпитываемости материалов. Мы рекомендуем для подготовки стен из газосиликатного блока, пеноблока, прочих ячеистых бетонов использовать следующие виды грунтовок:
- Грунтовка Ceresit CT 17 глубокого проникновения. Применяется по всем типам сильно впитывающих оснований, укрепляет, выравнивает водопоглощение, усиливает силу сцепления. За счет пигментов в составе, при нанесении, оставляет легкий тон. Он позволяет визуально определять пробелы для максимально качественной и равномерной обработки поверхностей. Межслойная сушка – до 30-40 минут, полное высыхание за 2-4 часа (при комнатной температуре).
- Грунтовка Юнис для внутренних работ. Применяется для обработки и подготовки стен внутри помещений. Состав на основе акрилатов отлично выравнивает влаговпитываемость и связывает пыль (обеспыливает поверхность). Рекомендован для нанесения на стены из ячеисто-бетонных блоков и гипсокартона. Межслойная сушка – до 40 минут, полное высыхание – 3 часа.
- Грунтовка Ceresit фасадная СТ 16. Специализированный состав на полимерной основе с противоморозными добавками. Идеально подойдет для грунтования наружных стен перед нанесением декоративной штукатурки. Может применяться для внутренних работ перед последующим финишным шпатлеванием. Межслойная сушка – до 30-40 минут, полное высыхание – 3 часа (при температуре 18-25 градусов).
- Грунтовка Кнауф Миттельгрунд F. Концентрированный состав на основе полимерных вяжущих. Обладает высокой способностью к выравниванию влаговпитываемости. В составе имеется желтый пигмент для визуального определения качества нанесения на поверхность.
Рекомендуется разбавлять водой в соотношении 1к5 (пенобетон и газоблок) и 1к3 (гипсокартон). Грунтовка обладает свойством морозостойкости. Допускается ее применение при подготовке стен перед фасадной отделкой. Полное высыхание – до 6 часов.
Существует такой вид грунтовки, как бетоноконтакт. Использовать его на пористых сильно впитывающих основаниях, как пенобетон, газобетон не рекомендуется. Он образует в процессе высыхания пленку, которая не обладает достаточной адгезией к подобного рода материалам.
Технология нанесения грунтовок перед оштукатуриванием и шпатлеванием ГКЛ, газобетона, пенобетона
Наносить грунтовку на газобетон, пенобетон рекомендуется не менее, чем в 2-3 слоя. ГКЛ – не менее, чем в 1-2 слоя. Каждый слой должен быть обильным. Это важно для достижения лучшего эффекта.
Для нанесения можно использовать ручные и механизированные средства. Подойдут:
- кисть-макловица;
- валик;
- распылитель для вазонов;
- садовый распылитель.
Для обработки большой площади поверхности стен можно также использовать краскопульт, что существенно ускорит процесс подготовки.
Перед каждым последующим слоем необходимо выждать технологическую паузу – дать поверхности впитать раствор и высохнуть. Обращайте внимание на рекомендации производителя грунтовок, а именно – на время межслойной сушки и полного высыхания.
К дальнейшим работам нужно приступать только по истечению рекомендованного периода полного высыхания. Полностью высохший слой гарантирует качественную полимеризацию состава в структуре блоков и набор основанием требуемых качеств.
Выбор штукатурки для стен из газобетона, пенобетона
Даже качественно загрунтованная поверхность стены из пеноблоков и газоблоков характеризуется достаточно сильной впитываемостью. Поэтому многие строители перед нанесением штукатурного раствора дополнительно увлажняют стены обычной водой. Такой метод позволяет продлить время схватывания раствора, улучшить процесс гидратации и усилить сцепление.
Для оштукатуривания газобетонных и пенобетонных оснований рекомендуется выбирать штукатурки, которые включают в состав модифицирующие добавки. В частности, в таких сухих смесях должны содержаться вещества, снижающие быстрый вывод воды из готового раствора (обладают улучшенным влагоудержанием). На данное время существует много подобных штукатурных смесей на цементном и гипсовом вяжущем, для машинного и ручного нанесения, внутренних и наружных работ. Популярностью пользуются:
- Штукатурка цементная ЮНИС Силин универсальный армированный. Состав на цементом связующем с модификаторами, разработанный для отделки внутренних стен и фасадов. Включает армирующие волокна, повышающие прочность слоя. Допускается применение по загрунтованным газобетонным основаниям.
- Штукатурка гипсовая Кнауф Гольдбанд. Состав на гипсовой основе с модификаторами, которые увеличивают жизненность раствора.
Допускается применение по предварительно загрунтованным пористым бетонам. Рекомендована для отделки внутренних стен и перегородок, включая влажные помещения. При отделке ванных комнат необходимо обеспечить гидроизолирующий слой и отсутствие прямого контакта с водой.
- Штукатурка гипсовая белая ЮНИС Экослой. Состав для машинного или ручного нанесения. Обладает высокой пластичностью и повышенной жизненностью раствора. Допускается применение по пенобетону и другим недеформируемым сильновипитывающим основаниям с предварительным грунтованием.
При использовании цементных штукатурок рекомендуется в течении двух дней обрызгивать их водой. Процесс увлажнения положительно скажется на межкристаллических связях в структуре штукатурке, позволит улучшить гидратацию и повысит прочность полученного отвердевшего слоя.
Подготовка стен из газоблоков при помощи клея для плитки или клея для газоблоковНекоторые цементные и практически все гипсовые, штукатурные смеси рекомендованы для нанесения на базовую цементную штукатурку и другие слабовпитывающие основания. Применять их непосредственно на газоблоке и пенобетоне нужно с особой осторожностью. К числу таких составов относятся:
Существует технология подготовки газобетона и пенобетона для нанесения подобно рода штукатурных растворов. Суть ее заключается в предварительном изготовлении тонкого базового «слоя-моста» под последующее оштукатуривание. Для создания такого базового слоя отлично подойдет любой плиточный клей для газоблоков на цементной основе или штукатурно-клеевая смесь. В таких смесях содержатся модификаторы, которые снижают водоотдачу раствора. Соответственно, отвердевший слой пройдет полный цикл гидратации и образует прочное покрытие для последующих отделочных работ.
Для создания слоя-моста перед нанесением штукатурок допустимо использовать:
- Штукатурно-клеевая смесь Кнауф Севенер. В составе содержатся мелкофракционный песок и армирующие волокна, которые повышают прочность слоя. Также в состав включены водоотталкивающие модификаторы, за счет которых улучшается адгезия с последующими слоями гипсовых и цементных штукатурок.
- Клей универсальный Юнис Теплофасад. Основное назначение материала заключается в креплении утеплителей. Однако производитель допускает использование данной марки продукции для создания базового штукатурного слоя при условии применения армирующей сетки.
При нанесении базового слоя-моста обязательно должна использоваться укрепляющая фасадная армсетка. Ее устанавливают после того, как раствор нанесен на поверхность. Далее шпателем сетку придавливают к основанию.
Некоторые строители идут на небольшую хитрость. При создании базового штукатурного слоя на газоблоке используют гребенчатый шпатель с зубьями 6х6 мм. С помощью этого инструмента создаются бороздочки, которые придают слою рельефную структуру. При работе шпатель нужно проводить в горизонтальном направлении. Таким образом, образованная поверхность создаст дополнительный упор и не позволит штукатурке «сползать» при нанесении.
Шпатлевание стен из газобетона и пеноблока
Шпаклевка стен из газобетона при внутренней отделке помещения обычно выполняется с использованием полимерных и гипсовых смесей. При фасадной отделке предпочтение отдают цементным составам. Процесс шпатлевания можно выполнить двумя способами:
- по предварительно обустроенной штукатурке;
- непосредственно по стене из блоков.
Шпаклевочная сухая смесь выбирается, зависимо от способа отделки и условий эксплуатации. Чтобы стены служили качественно и долго, рекомендуем приобретать проверенные марки сухих смесей. Популярностью, к примеру, пользуются такие виды шпаклевок:
- Кнауф Фуген. Одна из самых популярных гипсовых шпаклевок, которая используется для внутренней отделки. Обладает хорошей пластичностью и трещиностойкостью, за счет чего подходит для нанесения на прочные основания из гипса, бетона, штукатурки, ГКЛ, ГВЛ и прочее.
- Кнауф Полимер Финиш. Продукт на основе полимерных вяжущих. Характеризуется повышенной жизненностью раствора (72 часа), что позволяет без проблем применять для работы на больших площадях. За счет тонкой фракции наполнителя и вяжущего образует очень гладкий слой с высокой прочностью и трещиностойкостью.
- Юнис Мастерслой. Данный материал допускается применять как для тонкослойного нанесения толщиной от 1 мм, так и для выравнивания стен толстослойным нанесением до 30 мм. Обладает хорошей жизненностью раствора и рекомендован производителем для нанесения непосредственно на основания из пенобетона, газобетона.
- Юнис Фасад. Шпаклевка на цементной основе, которая применяется для наружной отделки фасадов при подготовке их под последующие декоративные работы, к примеру, окрашивание. Эта продукция характеризуется высокой атмосферной устойчивостью и морозостойкостью. За счет модификаторов в составе обладает хорошей пластичностью, обеспечивая удобство проведения работ.
Шпаклевка газобетона с оштукатуренной поверхностью считается классическим способом финишной отделки. В данном случае, процесс ничем не отличается от шпатлевания на любых других стенах. Имеющуюся штукатурку качественно грунтуют. Если основание из гипса, то выполняют грунтование не менее двух раз. В качестве грунтовочных составов можно применять те же марки грунтовок (универсальные и глубокого проникновения), что и под штукатурку. Приступать к шпатлеванию можно после полного высыхания нанесенных грунтов.
Наносить шпаклевочный раствор нужно в два слоя небольшими порциями, тщательно разглаживая по поверхности широким шпателем. Каждое последующее нанесение должно разглаживаться с заходом на уже готовый слой, а не наоборот. Поэтому начинают шпатлевание не сверху, а со средины стены. Также рекомендуется начинать от углового примыкания стен, постепенно двигаясь к центру.
На первом слое допускаются мелкие неровности, риски или наплывы. После высыхания дефекты удаляются механическим способом (шпателем). Отвердевший слой шпаклевки еще раз грунтуется и процесс нанесения раствора повторяется.
Второй слой шпаклевки рекомендуется делать максимально ровным и бездефектным. Особенно, если речь идет о подготовке стен под покраску. Образованные дефекты после полного отверждения слоя затирают механическим путем. Для этого можно использовать шлифовальную бумагу с самой мелкой зернистостью, малярную сетку. Вручную проще это делать с использованием колодок. Также удобство и скорость работы повышают шлифовальные машинки.
После тщательной зачистки у вас должна получиться поверхность с отблеском и идеальной геометрией. Загрунтуйте ее грунтовочным составом глубокого проникновения. После высыхания грунта можно приступать к последующим декоративно-отделочным работам.
Шпаклевка по газобетону без штукатуркиШпаклевка по газобетону без штукатурки возможна при выполнении нескольких условий. К таким относятся идеальная ровность стен и отсутствие на них любых дефектов. При строительстве нового дома рекомендуется дать материалу пройти полную усадку в течении 3-6 месяцев. В ином случае нанесенный слой шпаклевки рискует растрескаться.
Перед нанесением шпаклевки, газобетон и пенобетон выравнивают механическим способом. Для этого применяется специальная терка по газобетону. Особое внимание уделяется местам состыковки блоков, где есть небольшие перепады. Затирать нужно до образования гладкой и ровной поверхности по всей площади стены.
Выравненную поверхность нужно обеспылить и прогурунтовать. Грунтовку лучше выбирать глубокого проникновения. Наносить ее рекомендуется в два слоя. Далее, по стандартной технологии шпаклюется стена в два слоя.
Уделить внимание нужно межслойной сушке раствора. Состав, нанесенный на поверхность блока, высыхает очень быстро. В месте швов процесс сушки занимает больше времени. Важно дождаться полного высыхания слоя по всей поверхности. Только после этого приступать к нанесению второго слоя шпаклевки.
После полного высыхания стен их очищают от мелких наплывов и дефектов путем затирки. Далее можно приступать к декоративной отделке – поклейке обоев или покраске.
Газобетон или пенобетон? Что лучше?
Часто, используя ячеистый бетон в строительстве, задаешься вопросом: пенобетон или пенобетон? Что лучше? Газобетон и пенобетон относятся к категории ячеистых бетонов, их свойства соответствуют ГОСТ 25485-89, а их существенное различие заключается в технологии изготовления. При производстве газобетона пористая структура бетона формируется с помощью пузырьков газа, являющихся результатом химической реакции между цементом и алюминиевым порошком, содержащимся в газообразующем агенте.Пористая структура материала сохраняется при затвердевании газобетона. Когда прочность набирается, получается легкий и прочный материал, который неплохо сохраняет тепло.
При изготовлении пенобетона пористая структура формируется с помощью пузырьков воздуха, равномерно распределенных по цементной смеси. Наличие пузырьков воздуха в пенобетоне обеспечивается подачей пены в цементную смесь или добавлением пенообразователя в цементную смесь при перемешивании.Когда материал затвердевает, пористая структура сохраняется. Пенобетон по сравнению с газобетоном имеет структуру с закрытыми ячейками, что обеспечивает меньшее влагопоглощение.
Однако стены из пенобетона или газобетона обычно не оставляют открытыми, а защищают от воздействия окружающей среды с помощью штукатурки, сайдинга, отделочной плитки и т. Д. На строительной площадке не только теплоизоляционные свойства, но и прочность на разрыв при сжатии. имеет значение. Пенообразователи (особенно синтетические), которые используются для изготовления пенобетона, отрицательно влияют на прочность цементного кирпича.Для изготовления несущей стены следует использовать кирпич не ниже класса В2 на разрыв при сжатии.
Для обеспечения такой прочности пенобетона плотность материала должна быть не менее 700-800 кг на куб. м. Такого же класса прочности (В2) у газобетона можно достичь при плотности 500-600 кг на куб. м. Так что газобетон можно считать более прочным материалом. По этой же причине пенобетон в производстве дороже газобетона.Для сравнения: расход цемента на изготовление 1 куб. м пенобетона плотностью 800 кг на куб. м составляет в среднем 380-400 кг, при изготовлении 1 куб. м газобетона плотностью 600 кг на куб. м потребуется всего 280-300 кг цемента. Также стоит отметить, что стена из газобетона плотностью 600 кг на куб. м может быть более тонким, имеющим такие же прочностные и теплотехнические свойства.
В любом случае, материал будет выбирать покупатель.Перед покупкой необходимо убедиться, что выбранный материал соответствует требованиям ГОСТа, а также изучить особенности использования материала и его дальнейшей эксплуатации.
% PDF-1.6 % 1 0 объект > эндобдж 5 0 obj > эндобдж 2 0 obj > транслировать 2011-09-05T07: 17: 41-07: 00easyPDF SDK 6.02012-07-05T14: 58: 20 + 08: 002012-07-05T14: 58: 20 + 08: 00BCL easyPDF 6.02 (0342) application / pdfuuid: 1502cd6b- 9ae1-429b-a39d-0b633b209f19uid: d176ea67-5571-4024-8c24-6b34c7cafa39 конечный поток эндобдж 3 0 obj > / Кодирование> >> >> эндобдж 4 0 obj > эндобдж 6 0 obj > эндобдж 7 0 объект > эндобдж 8 0 объект > эндобдж 9 0 объект > эндобдж 10 0 obj > эндобдж 11 0 объект > эндобдж 12 0 объект > эндобдж 13 0 объект > эндобдж 14 0 объект > эндобдж 15 0 объект > эндобдж 16 0 объект > / ProcSet [/ PDF / Text / ImageB / ImageC] / XObject> >> / Тип / Страница / Аннотации [67 0 R] >> эндобдж 17 0 объект > / ProcSet [/ PDF / Text / ImageB / ImageC] >> / Тип / Страница >> эндобдж 18 0 объект > / ProcSet [/ PDF / Text / ImageB / ImageC] >> / Тип / Страница >> эндобдж 19 0 объект > / ProcSet [/ PDF / Text / ImageB / ImageC] >> / Тип / Страница >> эндобдж 20 0 объект > / ProcSet [/ PDF / Text / ImageB / ImageC] >> / Тип / Страница >> эндобдж 21 0 объект > / ProcSet [/ PDF / Text / ImageB / ImageC] >> / Тип / Страница >> эндобдж 22 0 объект > / ProcSet [/ PDF / Text / ImageB / ImageC] >> / Тип / Страница >> эндобдж 23 0 объект > / ProcSet [/ PDF / Text / ImageB / ImageC] >> / Тип / Страница >> эндобдж 24 0 объект > / ProcSet [/ PDF / Text / ImageB / ImageC] >> / Тип / Страница >> эндобдж 25 0 объект > / ProcSet [/ PDF / Text / ImageB / ImageC] >> / Тип / Страница >> эндобдж 26 0 объект > / ProcSet [/ PDF / Text / ImageB / ImageC] >> / Тип / Страница >> эндобдж 27 0 объект > / ProcSet [/ PDF / Text / ImageB / ImageC] >> / Тип / Страница >> эндобдж 28 0 объект > / ProcSet [/ PDF / Text / ImageB / ImageC] >> / Тип / Страница >> эндобдж 29 0 объект > / ProcSet [/ PDF / Text / ImageB / ImageC] >> / Тип / Страница >> эндобдж 30 0 объект > / ProcSet [/ PDF / Text / ImageB / ImageC] >> / Тип / Страница >> эндобдж 31 0 объект > / ProcSet [/ PDF / Text / ImageB / ImageC] >> / Тип / Страница >> эндобдж 32 0 объект > / ProcSet [/ PDF / Text / ImageB / ImageC] >> / Тип / Страница >> эндобдж 33 0 объект > / ProcSet [/ PDF / Text / ImageB / ImageC] >> / Тип / Страница >> эндобдж 34 0 объект > / ProcSet [/ PDF / Text / ImageB / ImageC] >> / Тип / Страница >> эндобдж 35 0 объект > / ProcSet [/ PDF / Text / ImageB / ImageC] >> / Тип / Страница >> эндобдж 36 0 объект > / ProcSet [/ PDF / Text / ImageB / ImageC] >> / Тип / Страница >> эндобдж 37 0 объект > / ProcSet [/ PDF / Text / ImageB / ImageC] >> / Тип / Страница >> эндобдж 38 0 объект > / Тип / Страница >> эндобдж 39 0 объект > / Тип / Страница >> эндобдж 40 0 объект > / Тип / Страница >> эндобдж 41 0 объект > / Тип / Страница >> эндобдж 42 0 объект > / Тип / Страница >> эндобдж 43 0 объект > / Тип / Страница >> эндобдж 44 0 объект > / Тип / Страница >> эндобдж 45 0 объект > / Тип / Страница >> эндобдж 46 0 объект > / Тип / Страница >> эндобдж 47 0 объект > / Тип / Страница >> эндобдж 48 0 объект > / Тип / Страница >> эндобдж 49 0 объект > / Тип / Страница >> эндобдж 50 0 объект > / Тип / Страница >> эндобдж 51 0 объект > / Тип / Страница >> эндобдж 52 0 объект > / Тип / Страница >> эндобдж 53 0 объект > / Тип / Страница >> эндобдж 54 0 объект > / ProcSet [/ PDF / Text / ImageB / ImageC] >> / Тип / Страница >> эндобдж 55 0 объект > / ProcSet [/ PDF / Text / ImageB / ImageC] >> / Тип / Страница >> эндобдж 56 0 объект > / ProcSet [/ PDF / Text / ImageB / ImageC] >> / Тип / Страница >> эндобдж 57 0 объект > / ProcSet [/ PDF / Text / ImageB / ImageC] >> / Тип / Страница >> эндобдж 58 0 объект > / ProcSet [/ PDF / Text / ImageB / ImageC] >> / Тип / Страница >> эндобдж 59 0 объект > транслировать xmбn0q} dIV ݪ kMUV ^ ~ Y>] 3,2h @ P «= E = 4t! ܃ — {& EB
ء ĢLԟ = _82C7: V4qKiIOd, ox` {wq rm # *] ejhGOE (N # E ߩ` Jq? M,! = @ ~ J / $ XQJGbo ^ q конечный поток эндобдж 60 0 объект > транслировать xmN0Ew rlag۴ $$ DcwMS Կ ǴgckO2˛H_5: P * c * \ B1iF% xŴqXg == Pr-Q? PQ> 3 \ G @ f0 ] ~ zz = 0 / 0ѕBR # ~ fG3% 48Key7 ~ @ mlWpmc۵; `gw ~ a \? xf ^ OiVȺ» RvH8o ކ j = Fb конечный поток эндобдж 61 0 объект > транслировать xEM0D) fRMt
Пенобетон — обзор
1.
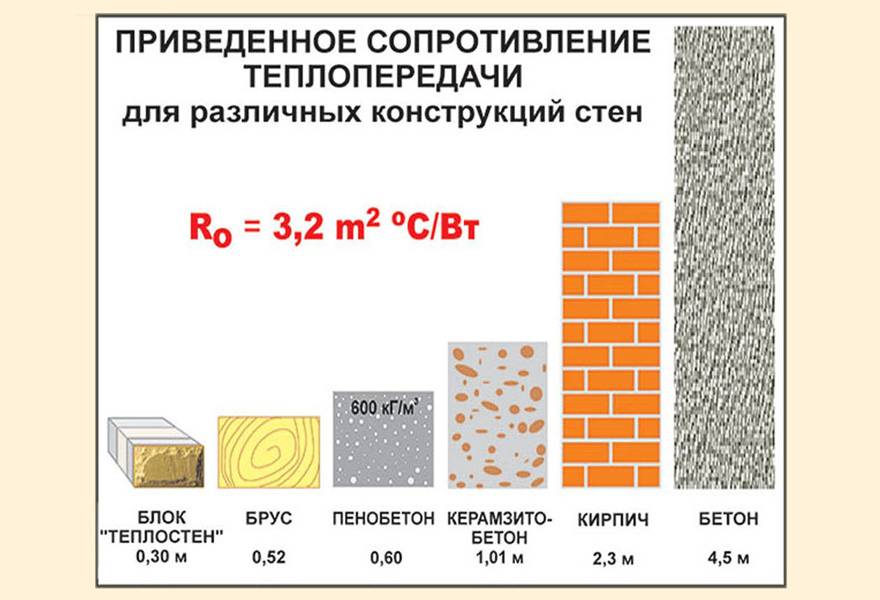
Пенобетон — это смесь цемента, песка, воды и вспененного пенобетона с подавляющим большинством пенобетона, не содержащего крупных заполнителей, а только мелкого песка (рис. 1.8) [4]. Чрезвычайно легкий пенобетон содержит только цемент, воду и пену. Сырьем для производства пенобетона являются вяжущее, заполнители, пенообразователь и вода. OPC используется с содержанием от 300 до 600 кг / м 3 . В дополнение к OPC, быстротвердеющему PC, высокоглиноземистые цементы могут использоваться для сокращения времени схватывания и улучшения начальной прочности.Возможна частичная замена цемента FA, GGBS и другими мелкими материалами. SF может быть добавлен для улучшения прочности бетона на сжатие. Однако следует убедиться в совместимости этих добавок с пенообразователями. GGBS придает пенобетону вязкую, почти липкую консистенцию. Использование FA делает смесь более текучей. Ключевым требованием здесь является наличие стабильной пены.
Рисунок 1. 8. Материалы, применяемые для пенобетона.
Используется только мелкий песок с размером частиц до 5 мм, так как крупный заполнитель имеет тенденцию оседать в легкой строительной смеси и вызывает схлопывание пены во время перемешивания.Предпочтительны песок очень низкой плотности с модулем крупности около 1,5, включая FA, известь, карбонат кальция, щебень, гранитную пыль, гранулы пенополистирола, мелкие частицы спеченного заполнителя FA, резиновые крошки, переработанное стекло и формовочный песок. Легкие заполнители, такие как спеченный заполнитель FA и вермикулит, также могут быть использованы для производства пенобетона.
Предварительно сформованная пена представляет собой смесь пенообразователя, воды и воздуха с плотностью 75 кг / м. 3 . Добавление предварительно сформованной пены снижает плотность смеси, увеличивая выход.Чем больше добавлено количество пены, тем легче получаемый материал. При производстве пенобетона используются два вида пены: мокрая пена и сухая пена. Влажную пену получают путем распыления раствора пенообразователя и воды на мелкую сетку. Пена, получаемая в этом случае, по внешнему виду похожа на пену для пены для ванн с размером пузырьков от 2 до 5 мм. Однако добавляемая пена должна оставаться стабильной, не разрушаясь во время перекачивания, укладки и отверждения. Этот фактор становится заметным, когда количество пены превышает 50% от базовой смеси (то есть при плотности приблизительно 1100 кг / м 3 ).Пенобетон ниже этой плотности необходимо производить и использовать с осторожностью. Водоцементное соотношение обычно составляет от 0,4 до 0,8, в зависимости от пропорций смеси и требований к консистенции. Когда очень мелкие материалы используются в больших количествах, потребность в воде увеличивается, что снижает прочность пенобетона. В пенобетон можно использовать химические добавки, такие как SP, VMA и ускорители, однако необходимо обеспечить их влияние на стабильность пены. Добавление волокон, таких как полипропиленовые и полиэфирные волокна, может использоваться для ограничения как пластической, так и усадочной деформации при высыхании.
Компоненты базовой смеси могут вступать в реакцию с некоторыми вспенивающими химикатами, что приводит к дестабилизации смеси.
Физико-микроструктурные свойства аэрированного цементного раствора для легких конструкций
Материалы (Базель). 2018 Apr; 11 (4): 597.
Areej T. Almalkawi
1 Департамент гражданской и экологической инженерии, Университет штата Мичиган, 3546 Engineering Building, E. Lansing, MI 48824, США
Talal Salem
1 Департамент гражданской и экологической инженерии, Университет штата Мичиган, 3546 Engineering Building, E.Lansing, MI 48824, USA
Sameer Hamadna
2 Metna Corporation, 1926 Turner Street, Lansing, MI 48906-4051, USA
AGND Darsanasiri
2 Metna Corporation, 1926 Turner Street, Lansing, MI 48906 -4051, USA
Parviz Soroushian
2 Metna Corporation, 1926 Turner Street, Lansing, MI 48906-4051, USA
Anagi Balchandra
2 Metna Corporation, 1926 Turner Street, Lansing, MI 48906-4051 , США
Гассан Аль-Чаар
3 Исследовательская лаборатория строительной инженерии (CERL), Центр исследований и разработок инженеров армии США, Шампейн, Иллинойс, 61822, США
1 Департамент гражданской и экологической инженерии, Университет штата Мичиган , 3546 Инженерный корпус, Е. Lansing, MI 48824, USA
2 Metna Corporation, 1926 Turner Street, Lansing, MI 48906-4051, USA
3 Исследовательская лаборатория строительной инженерии (CERL), Центр исследований и разработок инженеров армии США, Шампейн, Иллинойс 61822, США
Поступила 27 февраля 2018 г .; Принято 4 апреля 2018 г.
Лицензиат MDPI, Базель, Швейцария. Эта статья представляет собой статью в открытом доступе, распространяемую в соответствии с условиями лицензии Creative Commons Attribution (CC BY) (http: // creativecommons.org / licenses / by / 4.0 /). Эту статью цитировали в других статьях в PMC.Реферат
Цементные композиты, в том числе ферроцемент и цемент, армированный непрерывным волокном, все чаще используются для строительства и ремонта зданий. Одним из альтернативных вариантов обработки этих композитов является пропитывание арматуры (непрерывных волокон или куриной сетки) текучей цементной суспензией. Относительно высокая плотность цементных вяжущих по сравнению с полимерными вяжущими является неудачей в попытках представить вяжущие композиты как более дешевые, огнестойкие и долговечные альтернативы полимерным композитам. Аэрация раствора — эффективное средство снижения плотности цементных композитов. Однако такой подход ухудшает механические свойства цементирующих вяжущих. Была проведена экспериментальная программа для оценки потенциала производства аэрированной суспензии с желаемым балансом плотности, механических характеристик и барьерных свойств. Также была исследована возможность неразрушающего контроля развития прочности в пористом цементном растворе. В ходе этого исследования были получены аэрированные суспензии с плотностью до 0.9 г / см 3 с хорошими механическими и барьерными качествами для производства композитов. Также была исследована микроструктура этих композитов.
Ключевые слова: пористый цементный раствор , пенообразователь, микроструктура, теплопроводность, сорбционная способность, плотность, прочность на сжатие, легкие конструкции, композиты
1. Введение
Цементные композиты и ферроцемент, армированные непрерывным волокном, являются примерами композитов, используемых в строительстве приложения для строительства и ремонта [1,2,3,4]. По сравнению с полимерными композитами вяжущие композиты обладают улучшенной огнестойкостью и влагостойкостью, а также экономичностью. Однако плотность вяжущих матриц выше, чем у полимерных матриц.
Один из подходов к производству вяжущих композитов включает пропитку арматурной системы цементным раствором. Аэрация раствора дает возможность снизить плотность вяжущих матриц. Хотя аэрация имеет тенденцию снижать прочность вяжущих материалов, аэрированные матрицы все же могут соответствовать требованиям к их механическим характеристикам в контексте композитов с относительно большими объемными долями непрерывного армирования с высокой удельной площадью поверхности.Эти требования отличаются от требований, предъявляемых к бетону в обычных железобетонных конструкциях. Комбинация аэрации и армирования с высокой удельной площадью поверхности и близким расстоянием также может обеспечить желаемые характеристики удобоукладываемости (например, простоту наложения шурупов и нарезания), что сделало бы некоторые методы деревянного строительства применимыми к материалу.
В усилиях по снижению плотности суспензии необходимо учитывать (помимо механических характеристик и взаимодействия с различными системами армирования, такими как арматура из проволочной сетки) два аспекта поведения суспензии, которые имеют практическое значение в данном применении: (i) сорбционная способность для защиты изоляция и внутренняя часть здания от переноса влаги; и (ii) теплопроводность для добавления стоимости к повышению энергоэффективности здания.
Синергия между волокнами и органическими полимерами сыграла ключевую роль в превращении композитов в широко используемые конструкционные материалы. В этом синергетическом действии волокна обеспечивают отчетливо высокую прочность и модуль упругости композитов. Органические полимеры, с другой стороны, обеспечивают передачу напряжения волокнам и перераспределение напряжений между волокнами при раннем разрыве некоторых статистически более слабых [5]. Эти вклады полимерной матрицы в значительной степени зависят от их способности к деформации и желаемой адгезии к волокнам. Учитывая хрупкий характер полимерных матриц, таких как эпоксидная смола; их относительно низкий модуль упругости отвечает за их способность к удлинению. Полимерная матрица также придает композитам барьерные свойства. Обычно открытые молекулярные структуры как органических полимеров, так и волокон ответственны за относительно низкую плотность композитов, что способствует их «удельной» прочности и модулю. Снижение веса было жизненно важным соображением при переходе от металлов к композитам в аэрокосмической и других областях [5].
Работа, представленная в настоящем документе, сосредоточена на разработке неорганической матрицы с пониженной плотностью и модулем упругости, которая подходит для использования в качестве матрицы в композитах, армированных непрерывным волокном, которые имеют сходство с ферроцементными продуктами. Разработанная здесь матрица представляет собой аэрированную суспензию, которая обеспечивает желаемые реологические свойства для пропитки тканевых и сетчатых армирующих систем. Газобетонные цементные материалы (например, газобетон) были разработаны в основном для обеспечения теплоизоляционных качеств [6,7,8].Эта работа была сосредоточена на разработке аэрированных суспензий с относительно низкой плотностью и модулем упругости, а также жизнеспособной прочностью для использования в качестве матрицы в конструкционных композитах, как это было исследовано в наших предыдущих исследованиях [9,10,11,12,13]. Эта пористая сетка, пропитанная жидким навозом, разработана как строительный материал, обладающий промежуточными качествами между деревом и бетоном. Он предназначен для обеспечения желаемого баланса между относительно низкой плотностью, пластичностью, ударной вязкостью, прочностью, удобоукладываемостью, влаго- и огнестойкостью, а также долговечностью при атмосферных воздействиях.
2. Материалы и методы
Аэрированная суспензия была приготовлена путем смешивания пенообразователя (сапонина). Сапонины — это натуральные поверхностно-активные вещества, которые в изобилии содержатся в различных видах растений. Более конкретно, они представляют собой амфипатические гликозиды, содержащие один или несколько гидрофильных гликозидных фрагментов в сочетании с липофильным производным тритерпена [14]. показывает молекулу сапонина, полученную из остатков расщепления сизаля. Он был использован в составе моющих средств [15].
Молекула сапонина, выделенная из отходов сизаля [16].
Аэрация вяжущих материалов может быть достигнута путем стабилизации захваченного воздуха с помощью поверхностно-активных веществ [17,18,19] или путем добавления мелкодисперсного порошка, который выделяет газ в результате химических реакций с вяжущими материалами. Газобетон выпускается в широком диапазоне плотностей (от 300 до 1800 кг / м 3 ). Основное внимание в этой работе уделяется достижению плотности ниже 1000 кг / м 3 , которые обычно рассматриваются как изоляционные материалы [20,21]. Сапонин (гидролизованный белок, экстрагированный из растений) [22,23,24] был использован в этой работе в качестве поверхностно-активного вещества для производства аэрированной суспензии.Сапонин смешивали с водой для замешивания суспензии и перемешивали с образованием пены, которую затем смешивали с портландцементом типа 1 для получения аэрированной суспензии. Как поверхностно-активное вещество сапонин снижает поверхностное натяжение воды. Поверхностно-активные вещества — это молекулы с полярными и неполярными концами, которые присоединяются к воде и воздуху соответственно. Поверхностно-активные вещества — это молекулы с полярными и неполярными концами, которые присоединяются к воде и воздуху соответственно. Ориентация молекул ПАВ в объемном растворе случайна. Однако те, которые возникают на границах раздела воздух / жидкость или адсорбируются на частицах цемента, имеют предпочтительную ориентацию, которая стремится минимизировать неблагоприятные взаимодействия между жидкой фазой и различными молекулярными частями поверхностно-активного вещества.показывает выравнивание монослоя молекул поверхностно-активного вещества на границе раздела между воздухом и окружающей жидкой фазой. Гидрофобные хвосты молекул поверхностно-активного вещества выступают из раствора, чтобы уменьшить искажение молекул воды и, таким образом, снизить общую свободную энергию системы [25,26]. Взаимное отталкивание между гидрофильными головками молекул поверхностно-активного вещества снижает притяжение объемной жидкой фазы, создавая более низкое поверхностное натяжение. Из-за электростатической составляющей силы отталкивания ионных поверхностно-активных веществ их эффективность в снижении поверхностного натяжения более значительна, чем у неионных поверхностно-активных веществ [27].Природа и концентрация поверхностно-активных веществ определяют физические и химические свойства границ раздела воздух / жидкость, включая поверхностное натяжение (равное свободной поверхностной энергии) и стабильность. Электростатическое и стерическое отталкивание между поверхностно-активными веществами помогает стабилизировать пузырьки воздуха, которые образуются внутри жидкости [28,29]. Гидрофильные концы молекул поверхностно-активного вещества также электростатически притягиваются к частицам цемента, что также является фактором стабилизации пузырьков воздуха в цементном тесте ().
Молекулы ПАВ на границе раздела вода – воздух [25,30].
Взаимодействие пузырьков воздуха с частицами цемента [25].
Сапонин и воду смешивали при скорости вращения 1200 об / мин с использованием смесительной лопасти Craftsman ® , прикрепленной к сверлу (), для получения вспененной воды. Затем к цементу добавляли вспененную воду для смешивания при соотношении вода / цемент от 0,45 до 0,6. Перемешивание осуществляли в ступковой мешалке в течение 2 мин. Соотношение вода / цемент в различных аэрированных суспензиях регулировали для получения желаемой реологии свежей смеси для пропитки нескольких слоев куриной сетки.Требуемая реология свежей смеси может быть определена вязкостью около 1900 сП и пределом текучести около 70. Полученная аэрированная суспензия помещалась в кубические формы диаметром 50 мм и выдерживалась в герметизированном состоянии при комнатной температуре в течение 24 часов. Затем образцы кубиков были извлечены из формы и отверждены при относительной влажности 95 ± 5% и комнатной температуре в течение семи дней. Пропорции смеси аэрированной суспензии, рассматриваемые в этой экспериментальной программе, представлены в. Для неаэрированного раствора (с содержанием сапонина 0%) соотношение вода / цемент было между (0.45–0,55).
Образование пены в воде при высокоскоростном перемешивании.
Таблица 1
Аэрированная суспензия смешивает пропорции, рассмотренные в данном исследовании.
Mix | Дозировка сапонина (по весу цемента) | Отношение вода / цемент |
---|---|---|
1 | 0,005% | 0,45 | 0,02% |
4 | 0.005% | 0,50 |
5 | 0,01% | |
6 | 0,02% | |
7 | 0,005% | 0,55 | 0,015% |
10 | 0,02% | |
11 | 0,025% | |
12 | 0,03% | |
13 | 0,0240% | .025%
показывает примеры кубиков аэрированной суспензии, которые были испытаны на сжатие для измерения прочности на сжатие аэрированной суспензии (в возрасте семи дней). Плотность аэрированной суспензии измеряли путем деления высушенной на воздухе массы на объем этих образцов.
Образцы аэрированных суспензий.
Аэрированная суспензия будет основной защитой внутренней части здания, а также местной изоляцией, которая будет использоваться внутри структурных панелей от атмосферных воздействий.Влага будет транспортироваться через пену из аэрированной суспензии (с усилением куриной сетки) за счет капиллярной сорбции. Таким образом, было проведено экспериментальное исследование, чтобы измерить влияние аэрации на капиллярную сорбирующую способность суспензии. Испытания на сорбционную способность проводились согласно ASTM C1585; Образцы, использованные для этой цели, представляли собой цилиндры диаметром 100 мм и толщиной 50 мм. Схема испытательной установки показана на рисунке а, а изображение нескольких образцов во время тестирования сорбционной способности показано на рисунке b.Образцы извлекали из формы после 24 часов хранения в герметичном состоянии и выдерживали при комнатной температуре до испытательного возраста. Этот метод испытаний включает воздействие воды на одну плоскую поверхность образца, а остальные поверхности герметизируются от потери влаги. Прирост массы с течением времени регистрируется как мера сорбции влаги. Сорбционная способность выражается в показателях сорбции влаги аэрированной суспензией. Этот тест продолжался в течение двух дней, чтобы получить более полное представление о схематической временной истории капиллярной сорбции [31,32].
Установка для тестирования сорбционной способности. ( a ) Схемы; ( b ) фотография нескольких образцов во время испытания.
Скорость ультразвукового импульса (UPV) аэрированной суспензии была измерена неразрушающим методом с использованием портативного оборудования (тестер 58-E4800 UPV, CONTROLS S.p.A, Милан, Итлей). Схема тестирования UPV показана на. В этом тесте ультразвуковой импульс генерируется и передается на поверхность бетона через передающий преобразователь. Время, необходимое импульсу для прохождения через аэрированную суспензию, t us , измеряется приемным преобразователем на противоположной стороне.Преобразователи 54 кГц были расположены в центре каждой противоположной стороны. Время распространения ультразвуковых волн, прошедших через цилиндрические образцы длиной 150 мм, измерялось с точностью до 0,1 с. Тонкий связующий агент (твердая синяя каолин-глицериновая паста использовалась на границе раздела между преобразователями и поверхностями образца аэрированной суспензии для обеспечения хорошего контакта. Время прохождения импульса (t) от передней стороны к задней стороне регистрировалось автоматически. Ультразвуковой импульс Скорость была измерена примерно через 50 часов после перемешивания аэрированной суспензии [33,34,35].Образцы, используемые для измерения скорости ультразвукового импульса, были приготовлены из смесей аэрированной суспензии, пропорции которых аналогичны тем, которые использовались для других экспериментов; однако смеси, использованные для приготовления образцов со скоростью ультразвукового импульса, не были такими же, как смеси, использованные для подготовки образцов, используемых в других испытаниях. Все образцы были отверждены при комнатной температуре и относительной влажности 95 ± 5%.
Установка для измерения скорости ультразвукового импульса.
Теплопроводность аэрированной суспензии в тесте измеряли в возрасте семи дней в соответствии с ASTM C177 [36].Образцы аэрированного цементного раствора сушили в печи в течение 24 ч при температуре 105 ± 5 ° C. показывает конфигурацию тестирования теплопроводности и испытательную установку. Образец помещали между горячей и холодной пластинами с температурой 40 и 18 ° C, соответственно, для имитации наружной и внутренней температуры. Температуру горячей и холодной пластин, а также тепловой поток регистрировали в зависимости от времени в течение 24 часов. Результаты, после того как процесс достиг равновесия, были использованы для расчета теплопроводности аэрированной суспензии.
( a ) Диаграмма измерения теплопроводности и испытательная установка ( b ).
Кроме того, образцы аэрированной суспензии подвергали наблюдению с помощью сканирующих электронных измерений (SEM) для оценки микроструктурных особенностей. СЭМ-наблюдения проводились на JCM-5000 NeoScope ™ (JEOL Ltd., Токио, Япония) при ускоряющем напряжении 10–15 кВ с использованием детектора вторичных электронов (SE). Исследования проводились на поверхностях излома пасты образцов через 28 суток.Перед измерениями на сканирующем электронном микроскопе образцы были напылены золотом.
3. Результаты экспериментов и обсуждение
3.1. Прочность на сжатие
представляет измеренные значения прочности на сжатие и плотности в течение семи дней для конструкций аэрированной суспензии, представленных ранее в. Более низкие значения плотности, как правило, соответствуют более низким значениям прочности на сжатие. Это происходит как из-за увеличения содержания воздуха, так и из-за увеличения отношения вода / цемент для достижения жизнеспособной реологии свежей смеси.Смесь 13 с плотностью 0,9 г / см 3 и прочностью на сжатие 5,4 МПа в течение семи дней обеспечивает жизнеспособный баланс плотности и прочности для целевого применения ферроцемента. В этой статье особо подчеркивается плотность аэрированного раствора для повышения эффективности сейсмического проектирования [37,38], а также для обеспечения возможности ручной установки конструкции здания.
Таблица 2
Конструкции смесей и рабочие характеристики аэрированной суспензии.
Mix | Прочность на сжатие в течение семи дней, МПа | Плотность, г / см 3 | |||
---|---|---|---|---|---|
1 | 10.7 | 1,9 | |||
2 | 8,2 | 1,5 | |||
3 | 6,3 | 1,4 | |||
4 | 14,1 | 1,2 | 14,1 | 1,2 | |
6 | 9,2 | 1,3 | |||
7 | 13,3 | 1,6 | |||
8 | 11,1 | 1,7 | |||
9 | 41,3 | ||||
10 | 6,4 | 1,17 | |||
11 | 2,4 | 0,65 | |||
12 | 1,2 | 0,8 | 1,2 | 0,8 | 0,8 | 9015
14 | 7,1 | 1,12 |
3,2. Сорбционная способность
Результаты испытания сорбционной способности представлены в виде зависимости капиллярного подъема влаги от времени для аэрированных суспензий, приготовленных с различными дозировками пенообразователя (сапонина) при соотношении вода / цемент 0.55. Наблюдается, что две более высокие дозировки пенообразователя (0,015% и 0,02%) приводят к более низким скоростям и емкости сорбции. Это положительная тенденция, указывающая на то, что снижение плотности навозной жижи за счет аэрации фактически улучшило бы ее барьерные свойства для защиты внутренних помещений здания, а также естественную изоляцию от атмосферных воздействий.
Капиллярная сорбция аэрированных суспензий в зависимости от квадратного корня из времени.
Начальная скорость сорбции ( S i ) — это наклон кривой сорбции, показанный до 6 часов; скорость вторичной сорбции — это наклон кривой через сутки.Оба этих расчета выполнены с использованием линейного регрессионного анализа (ASTM C1585) [39]:
Полученные значения начальной и вторичной скорости сорбции представлены вместе с соответствующими значениями плотности аэрированной суспензии. Эти результаты подтверждают, что снижение плотности аэрированной суспензии с 1,7 до 1,17–1,3 г / см 3 приводит к значительному снижению начальной и вторичной скорости сорбции суспензии. Это можно объяснить тем, что аэрация вводит в суспензию изолированные пузырьки воздуха, которые нарушают непрерывность капиллярных пор, через которые происходит сорбция [40,41,42,43,44,45].Также представлено общее значение сорбционной способности, которое представляет собой наклон линии регрессии, подходящей для всех точек данных (с использованием приведенного выше уравнения). Общие значения сорбционной способности дополнительно подтверждают снижение скорости сорбции с уменьшением плотности аэрированной суспензии.
Таблица 3
Скорости сорбции и плотности суспензий, приготовленных с различными дозировками пенообразователя.
Дозировка пенообразователя% | 0,01% | 0,015% | 0.02% | ||
---|---|---|---|---|---|
Начальная скорость сорбции, мм / с | 0,0242 | 0,0188 | 0,0132 | ||
Скорость вторичной сорбции, мм / с | 0,0044 | 0,00134 | 2 (значение регрессии)0,951 | 0,950 | 0,958 |
Плотность, г / см 3 | 1,7 | 1,3 | 1,17 | ||
0, мм / мин5 | 0,75 | 0,5 | 0,34 |
Чтобы подтвердить вывод о том, что аэрация действительно снижает скорость и степень сорбции суспензии (т.е. улучшает ее барьерные качества), испытания были также выполнены на суспензии без любая аэрация. Представленные данные сорбционных испытаний подтверждают, что аэрация снижает скорость и степень сорбции влаги суспензией. Как схематически изображено на фиг.2, введение изолированного пузырька воздуха вызывает извилистые пути сорбции через капиллярные поры, что снижает скорость сорбции суспензии.Опыт с увлеченными пузырьками воздуха показывает, что отдельные пузырьки воздуха остаются в значительной степени свободными от воды даже при длительном воздействии влажных условий. Это явление, а также снижение скорости сорбции влаги, объясняют снижение степени сорбции влаги введением отдельных пузырьков воздуха за счет аэрации суспензии.
Сорбционная способность неаэрированных и аэрированных суспензий.
Пути сорбции в негазированные и аэрированные суспензии. ( a ) без вентиляции; ( b ) с газом.
Изображения под оптическим микроскопом были получены из срезов аэрированных суспензий, приготовленных с различными дозами пенообразователя, чтобы понять морфологию пузырьков воздуха и объяснить их влияние на прочность на сжатие. a, b показывают микроскопические изображения суспензий, приготовленных с концентрациями пенообразователя 0,005% и 0,02% соответственно. Наблюдается увеличение дозировки пенообразователя для увеличения размера (а также объемной доли) пузырьков воздуха. Следует отметить, что более мелкие и правильно сформированные воздушные пузырьки обеспечивают более высокую прочность на сжатие, чем более крупные и нерегулярно сформированные воздушные пузыри [46].На механические свойства сильно влияет распределение пор внутри затвердевшей аэрированной суспензии [47,48]. Сферический и распределенный характер пен в b с более высоким содержанием воздуха привел к приемлемому уровню прочности на сжатие, который был не ниже, чем у аэрированной суспензии, показанной на b, с более низким содержанием пузырьков воздуха неправильной формы. Это наблюдение подтверждает, что микроструктурные свойства являются основными факторами, влияющими на свойства материала аэрированной суспензии [38].Пример изображения с помощью оптического микроскопа внешней поверхности аэрированной суспензии с более высокой прочностью на сжатие показан на, где можно наблюдать более мелкие и более однородно диспергированные пузырьки воздуха.
Изображения с помощью оптического микроскопа срезов аэрированных суспензий с различными дозами пенообразователя (сапонина). ( a ) 0,005% пенообразователя; ( b ) 0,02% пенообразователя.
Типичное микроскопическое изображение внешней поверхности аэрированного раствора с более высокой прочностью на сжатие.
3.3. Наблюдения с помощью SEM
Сферическая геометрия воздушных пустот является важным фактором, влияющим на структурные и функциональные свойства аэрированных связующих [49,50]. Кроме того, пустоты должны быть равномерно распределены в массе для получения однородных связующих с улучшенными характеристиками. Более крупные пустоты (макропоры) снизят плотность аэрированной суспензии, но могут ухудшить ее механические характеристики. В зависимости от типа и дозировки пенообразователя аэрированные цементные растворы могут включать как микро-, так и макропоры [51].Макропоры могли образоваться в результате слияния микропор. Это связано с тем, что расширение матрицы при образовании микропор создает давление на границах раздела между микропорами [52]. а показывает изображение аэрированной суспензии после гидратации, полученное с помощью СЭМ.
СЭМ-изображения изломов поверхностей пеноцементов, изготовленных из суспензий после гидратации в течение 28 дней с плотностью ( a ) 1,0 г / см 3 ( b ) 0,75 г / см 3 ( c ) 1,3 г / см 3 .
Помимо пор геля (<10 нм) и капиллярных пор (от 10 нм до 10 мкм), полые поры оболочки были предложены в качестве третьей категории внутренних пор в массе продуктов гидратации [52]. Полые оболочки имеют размер от 1 до примерно 20 мкм, что примерно соответствует размеру более мелких цементных зерен, внедренных в цементный гель и выведенных наружу через капиллярные и гелевые поры.
Идеальная микроструктура пористого цемента сводит к минимуму степень переноса воды за счет равномерного распределения дискретных микропор, образованных пенообразователем, в цементном растворе.Однако слияние многих пор неправильной формы может создавать нарушенную микроструктуру, вызывая высокую степень подвижности воды. Чтобы проверить это, с помощью сканирующего электронного микроскопа исследовали два разрушенных образца аэрированных суспензий с объемной плотностью 0,75 и 1,3 г / см 3 (b, c, соответственно). Изображение справа для суспензии с насыпной плотностью 1,3 г / см 3 показывает микроструктуру из равномерно распределенных дизъюнктивных пор. Напротив, другая микроструктура наблюдалась для аэрированной суспензии с 0.75 г / см 3 насыпная плотность (слева), где развивалась аномальная коалесценция, приводящая к каналированной пористой структуре. Такая структура позволяет воде легко проникать через аэрированную суспензию. Возможным объяснением образования такой аномальной структуры пор является включение огромного количества ячеек с пузырьками воздуха с использованием избыточного количества пенообразователя, что способствует слиянию пузырьков воздуха в результате схлопывания стенок суспензии, разделяющих эти пузырьки. .
3.4. Скорость ультразвукового импульса
Скорость ультразвукового импульса (UPV) — это простой неразрушающий способ оценки бетона, который можно использовать для оценки качества аэрированного раствора и его изменения во времени. показывает изменение скорости ультразвукового импульса во времени (до 50 ч) после смешивания для трех аэратов суспензий с разной плотностью. УПВ выше для аэрированных суспензий с более высокой плотностью. В более раннем возрасте аэрированные суспензии с более низкой плотностью демонстрируют незначительное повышение UPV в течение более чем 10 часов, в то время как суспензии с более высокой плотностью демонстрируют четкую тенденцию к увеличению UPV уже через 1 час после смешивания.
Временная диаграмма UPV для аэрированных суспензий различной плотности.
Чтобы оценить вариабельность измерений UPV, были приготовлены три повторных образца аэрированной суспензии с одинаковым составом смеси (смесь 13) и плотностью (0,9 г / см 3 ). Эволюция UPV во времени представлена для трех повторных образцов. Вариации UPV для этих трех образцов для испытаний составляют менее 6%, что указывает на потенциальную ценность UPV как надежного метода мониторинга качества аэрированной суспензии (и его изменения со временем отверждения).
Проверка воспроизводимости трех тестов UPV для одной и той же смеси (смесь 13).
3.5. Теплопроводность
Ожидается, что легкий газированный раствор внесет определенный вклад в теплоизоляцию здания. Измеренные значения теплопроводности представлены в зависимости от плотности аэрированных суспензий. Как и ожидалось, суспензии с более низкой плотностью имеют более низкие значения теплопроводности [8,53,54]. Пузырьки воздуха действуют как барьеры против теплопроводности; изолированные пузырьки воздуха не вносят существенного вклада в теплопередачу за счет конвекции [7].
Зависимость теплопроводности аэрированных суспензий от их плотности.
4. Выводы
Аэрированная суспензия разработана как легкая матрица для производства вяжущих композитов, содержащих арматуру с высокой удельной площадью поверхности для структурных применений. Сверхтекучая суспензия необходима для тщательной инфильтрации структурного объема, который перегружен системами тонкого армирования. В этой работе был разработан и охарактеризован аэрированный раствор, содержащий вяжущий материал с относительно высоким соотношением вода / цемент, который включал пенообразователь (сапонин).При высокоскоростном перемешивании воды для замешивания, содержащей сапонин, образуется вспененная вода, которая затем используется для приготовления аэрированной суспензии путем смешивания с цементом. Следующие выводы были сделаны путем проведения экспериментальной программы на суспензиях различной плотности (скорректированной путем варьирования содержания сапонина).
Хотя снижение плотности аэрированной суспензии за счет увеличения дозировки пенообразователя имеет тенденцию к снижению ее прочности на сжатие, это соотношение несовместимо.Образование мелких, сферических и равномерно распределенных пузырьков воздуха в аэрированной суспензии способствует достижению более высокой прочности на сжатие.
Аэрация жидкого навоза улучшает его водонепроницаемые свойства, что увеличивает его долговечность. Изолированные пузырьки воздуха в аэрированной суспензии, по-видимому, действуют как барьеры против капиллярной сорбции влаги в суспензии, тем самым создавая извилистые пути диффузии. Степень абсорбции влаги суспензией также уменьшается с увеличением содержания воздуха.Это может быть связано с тенденцией изолированных пузырьков воздуха оставаться в значительной степени заполненными воздухом, когда аэрированная суспензия подвергается воздействию влаги.
Аэрация цементного раствора значительно снижает его теплопроводность, что способствует повышению энергоэффективности систем здания. Низкая теплопроводность воздуха в пузырьках, вводимых посредством аэрации, и отсутствие эффективной конвекции из-за изолированного характера пузырьков воздуха объясняют преимущества аэрации по сравнению с изоляционными характеристиками аэрированной суспензии.
Скорость ультразвукового импульса обеспечивает эффективные неразрушающие средства контроля качества аэрированной суспензии и ее изменения во времени. Этот метод может быть удобно реализован в полевых условиях для оценки качества аэрированного навоза и его изменения во времени.
Благодарности
Работа, представленная в настоящем документе, финансировалась армией США, грант № W9132T-16-C-0003-United States.
Вклад авторов
Все авторы внесли равный вклад в эту работу.
Конфликт интересов
Авторы заявляют об отсутствии конфликта интересов.
Ссылки
1. Прота А., Нанни А., Манфреди Г., Козенца Э. Выборочная модернизация недостаточно спроектированных соединений железобетонных балок и колонн с использованием полимеров, армированных углеродным волокном. ACI Struct. J. 2004; 101: 699–707. [Google Scholar] 2. Nelson MS, Fam AZ, Busel JP, Bakis CE, Nanni A., Bank LC, Henderson M., Hanus J. Армированные волокном полимерные несъемные структурные формы для бетонных настилов мостов: современный обзор .ACI Struct. J. 2014; 111: 1069–1079. DOI: 10.14359 / 51686810. [CrossRef] [Google Scholar] 3. Bianchi G., Arboleda D., Carozzi F.G., Poggi C., Nanni A. Армированные тканью материалы на цементной матрице (FRCM) для структурной реабилитации; Материалы 39-го Всемирного конгресса IAHS; Милан, Италия. 17–20 сентября 2013 г. [Google Scholar] 4. Donnini J., y Basalo F.D.C., Corinaldesi V., Lancioni G., Nanni A. Поведение армированной тканью цементной матрицы при высоких температурах: экспериментальные и численные результаты.Compos. Часть B англ. 2017; 108: 108–121. DOI: 10.1016 / j.compositesb.2016.10.004. [CrossRef] [Google Scholar] 5. Маллик П.К. Композиты, армированные волокном: материалы, производство, дизайн. CRC Press; Бока-Ратон, Флорида, США: 2007. [Google Scholar] 6. Аль-Джабри К.С., Хаго А.В., Аль-Нуайми А.С., Аль-Саиди А.Х. Бетонные блоки для теплоизоляции в жарком климате. Джем. Concr. Res. 2005; 35: 1472–1479. DOI: 10.1016 / j.cemconres.2004.08.018. [CrossRef] [Google Scholar] 7. Аленгарам У.Д., Аль Мухит Б.А., бин Джумаат М.Z., Jing M.L.Y. Сравнение теплопроводности пенобетона из скорлупы масличной пальмы с обычными материалами. Матер. Des. 2013; 51: 522–529. DOI: 10.1016 / j.matdes.2013.04.078. [CrossRef] [Google Scholar] 8. Ng S.-C., Low K.-S. Теплопроводность газобетонной сэндвич-панели из легкого бетона. Энергетика. 2010; 42: 2452–2456. DOI: 10.1016 / j.enbuild.2010.08.026. [CrossRef] [Google Scholar] 9. Алмалкави А.Т., Хамадна С., Сорушиан П. Однокомпонентная вулканическая пемза на основе цемента, активированного щелочью.Констр. Строить. Матер. 2017; 152: 367–374. DOI: 10.1016 / j.conbuildmat.2017.06.139. [CrossRef] [Google Scholar] 10. Almalkawi A.T., Hong W., Hamadna S., Soroushian P., Al-Chaar G. Поведение легкого каркаса, сделанного из куриной сетки, пропитанной аэрированной жидкой жидкостью, при циклической боковой нагрузке. Констр. Строить. Матер. 2018; 160: 679–686. DOI: 10.1016 / j.conbuildmat.2017.11.079. [CrossRef] [Google Scholar] 11. Алмалкави А., Хамадна С., Сорушиан П., Дарсана Н. Возможное использование местных материалов для синтеза однокомпонентного геополимерного цемента.Мировая Акад. Sci. Англ. Technol. Int. J. Civ. Environ. Англ. 2017; 4 DOI: 10.1999 / 1307-6892 / 65941. [CrossRef] [Google Scholar] 12. Алмалкави А.Т., Хонг В., Хамадна С., Сорушиан П., Дарсанасири А.Г.Н.Д., Балчандра А., Аль-Чаар Г. Механические свойства куриной сетки, пропитанной пеной из цементного раствора. Констр. Строить. Матер. 2018; 166: 966–973. DOI: 10.1016 / j.conbuildmat.2018.01.101. [CrossRef] [Google Scholar] 13. Маталка Ф., Бхарадвадж Х., Сорушиан П., Ву В., Алмалкави А., Балачандра А.М., Пейванди А.Разработка сэндвич-композитов для строительства зданий из местных материалов. Констр. Строить. Матер. 2017; 147: 380–387. DOI: 10.1016 / j.conbuildmat.2017.04.113. [CrossRef] [Google Scholar] 14. Хостеттманн К., Марстон А. Химия и фармакология натуральных продуктов, Сапонин. Издательство Кембриджского университета; Кембридж, Великобритания: 1995. [Google Scholar] 15. Рибейро Б., Баррето Д., Коэльо М. Применение пенопласта в качестве зеленой технологии для концентрирования сапонинов из сизаля ( Agave sisalana ) и Хуа ( Ziziphus joazeiro ) Braz.J. Chem. Англ. 2013; 30: 701–709. DOI: 10.1590 / S0104-66322013000400002. [CrossRef] [Google Scholar] 16. Рибейро Б.Д., Баррето Д.В., Коэльо М.А.З. Использование мицеллярной экстракции и концентрирования до точки помутнения для повышения ценности сапонинов из отходов сизаля ( Agave sisalana ). Пищевой Биопрод. Процесс. 2015; 94: 601–609. DOI: 10.1016 / j.fbp.2014.07.004. [CrossRef] [Google Scholar] 17. Намбиар Э.К., Рамамурти К. Определение характеристик воздухопроницаемости пенобетона. Джем. Concr. Res. 2007; 37: 221–230. DOI: 10.1016 / j.cemconres.2006.10.009. [CrossRef] [Google Scholar] 18. Рамамурти К., Намбияр Э.К., Ранджани Г.И.С. Классификация исследований свойств пенобетона. Джем. Concr. Compos. 2009. 31: 388–396. DOI: 10.1016 / j.cemconcomp.2009.04.006. [CrossRef] [Google Scholar] 19. Чжан З., Провис Дж. Л., Рид А., Ван Х. Геополимерный пенобетон: новый материал для устойчивого строительства. Констр. Строить. Матер. 2014; 56: 113–127. DOI: 10.1016 / j.conbuildmat.2014.01.081. [CrossRef] [Google Scholar] 20. Джонс М., Маккарти А.Предварительные взгляды на потенциал пенобетона как конструкционного материала. Mag. Concr. Res. 2005; 57: 21–32. DOI: 10.1680 / macr.2005.57.1.21. [CrossRef] [Google Scholar] 21. Уйсал Х., Демирбога Р., Шахин Р., Гюль Р. Влияние различных дозировок цемента, осадка и соотношения заполнителей пемзы на теплопроводность и плотность бетона. Джем. Concr. Res. 2004; 34: 845–848. DOI: 10.1016 / j.cemconres.2003.09.018. [CrossRef] [Google Scholar] 22. Фенвик Д.Э., Окенфул Д. Содержание сапонинов в пищевых растениях и некоторых готовых продуктах.J. Sci. Продовольственное сельское хозяйство. 1983; 34: 186–191. DOI: 10.1002 / jsfa.2740340212. [PubMed] [CrossRef] [Google Scholar] 23. Осборн А. Сапонины и защита растений — мыльная история. Trends Plant Sci. 1996; 1: 4–9. DOI: 10.1016 / S1360-1385 (96) 80016-1. [CrossRef] [Google Scholar] 24. Шимоямада М., Икедо С., Оотсубо Р., Ватанабе К. Влияние сапонинов сои на химотриптический гидролиз соевых белков. J. Agric. Food Chem. 1998; 46: 4793–4797. DOI: 10.1021 / jf980694j. [CrossRef] [Google Scholar] 25. Du L., Folliard K.J. Механизмы воздухововлечения в бетон.Джем. Concr. Res. 2005; 35: 1463–1471. DOI: 10.1016 / j.cemconres.2004.07.026. [CrossRef] [Google Scholar] 26. Мюррей Б.С. Стабилизация пузырей и пены. Curr. Opin. Коллоидный интерфейс Sci. 2007; 12: 232–241. DOI: 10.1016 / j.cocis.2007.07.009. [CrossRef] [Google Scholar] 27. Розен М.Дж., Кунджаппу Дж.Т. Поверхностно-активные вещества и межфазные явления. Джон Уайли и сыновья; Хобокен, Нью-Джерси, США: 2012. [Google Scholar] 28. Бинкс Б.П. Частицы как поверхностно-активные вещества — сходства и различия. Curr. Opin. Коллоидный интерфейс Sci.2002; 7: 21–41. DOI: 10.1016 / S1359-0294 (02) 00008-0. [CrossRef] [Google Scholar] 29. Мальдонадо-Вальдеррама Дж., Мартин-Молина А., Мартин-Родригес А., Кабреризо-Вилчес М.А., Гальвес-Руис М.Дж., Ланжевен Д. Свойства поверхности и стабильность пены смесей белок / поверхностно-активное вещество: теория и эксперимент. J. Phys. Chem. С. 2007. 111: 2715–2723. DOI: 10.1021 / jp067001j. [CrossRef] [Google Scholar] 30. Чаттерджи С. Замораживание воздухововлекающих материалов на основе цемента и особенности действия воздухововлекающих агентов. Джем. Concr.Compos. 2003. 25: 759–765. DOI: 10.1016 / S0958-9465 (02) 00099-9. [CrossRef] [Google Scholar] 31. Диас В. Показатели прочности OPC-бетонов при воздействии фитиля. Mag. Concr. Res. 1993. 45: 263–274. DOI: 10.1680 / macr.1993.45.165.263. [CrossRef] [Google Scholar] 32. Холл С., Яу М.Р. Движение воды в пористых строительных материалах — IX. Водопоглощение и сорбционная способность бетонов. Строить. Environ. 1987. 22: 77–82. DOI: 10.1016 / 0360-1323 (87) -8. [CrossRef] [Google Scholar] 33. Чжан Ю., Чжан В., Ше В., Ма Л., Чжу В. Ультразвуковой мониторинг процесса схватывания и твердения цементных материалов сверхвысоких характеристик. NDT E Int. 2012; 47: 177–184. DOI: 10.1016 / j.ndteint.2009.10.006. [CrossRef] [Google Scholar] 34. Лю З., Чжан Ю., Цзян К., Сунь Г., Чжан В. Непрерывный мониторинг на месте эволюции микроструктуры цементных материалов в раннем возрасте с помощью ультразвуковых измерений. Констр. Строить. Матер. 2011; 25: 3998–4005. DOI: 10.1016 / j.conbuildmat.2011.04.034. [CrossRef] [Google Scholar] 35. Она В., Чжан Ю., Джонс М. Использование метода передачи ультразвуковых волн для изучения поведения пенобетона при схватывании. Констр. Строить. Матер. 2014; 51: 62–74. [Google Scholar] 36. ASTM International; West Conshohocken, PA, USA: 2010. [(по состоянию на 12 апреля 2018 г.)]. Действующий стандарт ASTM C177-10. Стандартный метод испытаний для стационарных измерений теплового потока и свойств теплопередачи с помощью устройства с защищенной горячей пластиной. Доступно в Интернете: https://www.astm.org/Standards/C177.htm. [Google Scholar] 37.Го М., Хуан К., Ли П.Ф., Яо К.Ф. Экспериментальные исследования сейсмостойкости многореберной композитной стены, усиленной газобетонными блоками. J. Sichuan Univ. Англ. Sci. Эд. 2011; 43: 51–57. [Google Scholar] 38. Осаки М., Миямура Т., Кохияма М., Ямасита Т., Акиба Х. Высокопроизводительные вычисления для структурной механики и землетрясений / инженерии цунами. Springer; Чам, Швейцария: 2016. Моделирование сейсмических воздействий строительных конструкций; С. 105–139. [Google Scholar] 39. ASTM International; Вест Коншохокен, Пенсильвания, США: 2013.[(доступ 12 апреля 2018 г.)]. Действующий стандарт ASTM C1585-13. Стандартный метод испытаний для измерения скорости поглощения воды гидробетонами. Доступно в Интернете: http://www.astm.org/cgi-bin/resolver.cgi?C1585. [Google Scholar] 40. Прим П., Виттманн Ф. Автоклавный газобетон, влажность и свойства. Эльзевир; Амстердам, Нидерланды: 1983. Структура и водопоглощение ячеистого бетона; С. 55–69. [Google Scholar] 41. Тада С., Накано С. Труды Автоклавный газобетон, влажность и свойства.Эльзевир; Амстердам, Нидерланды: 1983. Микроструктурный подход к свойствам влажного ячеистого бетона; С. 71–89. [Google Scholar] 42. Гуаль М.С., Де Баркин Ф., Бенмалек М.Л., Бали А., Кенудек М. Оценка коэффициента капиллярного переноса глинистого газобетона с использованием гравиметрического метода. Джем. Concr. Res. 2000; 30: 1559–1563. DOI: 10.1016 / S0008-8846 (00) 00379-3. [CrossRef] [Google Scholar] 43. Маджудж Н., Дхейли Р.М., Квнедек М. Инновации и разработки в бетонных материалах и строительстве: материалы международной конференции, состоявшейся в Университете Данди, Шотландия, Великобритания, 9–11 сентября 2002 г.Томас Телфорд Паблишинг; Вестеркирк, Великобритания: 2002. Капиллярное водопоглощение ячеистого керамзитобетона, полученного путем белкового вспенивания. [Google Scholar] 44. Джаннаку А., Джонс М. Инновации и разработки в бетонных материалах и строительстве: материалы международной конференции, состоявшейся в Университете Данди, Шотландия, Великобритания, 9–11 сентября 2002 г. Thomas Telford Publishing; Лондон, Великобритания: 2002. Возможности пенобетона для улучшения тепловых характеристик малоэтажных жилых домов; С. 533–544.[Google Scholar] 45. Намбиар Э.К., Рамамурти К. Сорбционные характеристики пенобетона. Джем. Concr. Res. 2007; 37: 1341–1347. DOI: 10.1016 / j.cemconres.2007.05.010. [CrossRef] [Google Scholar] 46. Юст А., Миддендорф Б. Микроструктура высокопрочного пенобетона. Матер. Charact. 2009; 60: 741–748. DOI: 10.1016 / j.matchar.2008.12.011. [CrossRef] [Google Scholar] 47. Кирсли Э., Уэйнрайт П. Влияние пористости на прочность пенобетона. Джем. Concr. Res. 2002. 32: 233–239. DOI: 10.1016 / S0008-8846 (01) 00665-2.[CrossRef] [Google Scholar] 48. Олорунсого Ф.Т., Уэйнрайт П.Дж. Влияние гранулометрического состава GGBFS на прочность раствора на сжатие. J. Mater. Civ. Англ. 1998. 10: 180–187. DOI: 10.1061 / (ASCE) 0899-1561 (1998) 10: 3 (180). [CrossRef] [Google Scholar] 49. Дхир Р.К., Хендерсон Н.А., редакторы. Специальные методы и материалы для бетонных конструкций: материалы международной конференции, проходившей в Университете Данди, Шотландия, Великобритания, 8–10 сентября 1999 г. Томас Телфорд; Вестеркирк, Великобритания: 1999.[Google Scholar] 50. Valore R.C. Ячеистые бетоны Часть 1 Состав и способы приготовления. J. Proc. 1954. 50: 773–796. [Google Scholar] 51. Сугама Т., Братья Л., Ван де Путте Т. Вспененный на воздухе фосфатный цемент на основе алюмината кальция для геотермальных скважин. Джем. Concr. Compos. 2005. 27: 758–768. DOI: 10.1016 / j.cemconcomp.2004.11.003. [CrossRef] [Google Scholar] 52. Александерсон Дж. Связь между структурой и механическими свойствами автоклавного газобетона. Джем. Concr. Res. 1979; 9: 507–514. DOI: 10.1016 / 0008-8846 (79)-8. [CrossRef] [Google Scholar] 53. Сенгуль О., Азизи С., Караосманоглу Ф., Тасдемир М.А. Влияние вспученного перлита на механические свойства и теплопроводность легкого бетона. Энергетика. 2011. 43: 671–676. DOI: 10.1016 / j.enbuild.2010.11.008. [CrossRef] [Google Scholar] 54. Сайгылы А., Байкал Г. Новый метод улучшения теплоизоляционных свойств летучей золы. Энергетика. 2011; 43: 3236–3242. DOI: 10.1016 / j.enbuild.2011.08.024. [CrossRef] [Google Scholar]
Прикладных наук | Бесплатный полнотекстовый | Влияние добавок, типа цемента и количества пены на свойства пенобетона, полученного с отходами гражданского строительства
Рисунок 1. ( a ) Кумулятивное распределение нижнего продукта гранулометрии CCW и нормальные верхний и нижний пределы для производства бетона в соответствии с NBR 7211 [28]; ( b ) Против часовой стрелки. Рисунок 1. ( a ) Кумулятивное распределение нижнего продукта гранулометрии CCW и нормальные верхний и нижний пределы для производства бетона в соответствии с NBR 7211 [28]; ( b ) Против часовой стрелки.Рисунок 2. ( a ) Изображение экспериментальной установки, используемой для определения теплопроводности, и ( b ) схематическая конструкция прибора.
Рисунок 2. ( a ) Изображение экспериментальной установки, используемой для определения теплопроводности, и ( b ) схематическая конструкция прибора.
Рисунок 3. Прочность на сжатие, относящаяся к типу цемента ( a ), количеству пены ( b ) и типу добавки ( c ) для разного времени отверждения, где средняя точка — среднее значение, прямоугольник — доверительный интервал (95% ), а усы — стандартное отклонение.
Рисунок 3. Прочность на сжатие, относящаяся к типу цемента ( a ), количеству пены ( b ) и типу добавки ( c ) для разного времени отверждения, где средняя точка — среднее значение, прямоугольник — доверительный интервал (95% ), а усы — стандартное отклонение.
Рисунок 4. Плотность в сухом и влажном состоянии, относящаяся к типу цемента ( a ), количеству пены ( b ) и типу добавки ( c ) для разного времени отверждения, где средняя точка — среднее значение, прямоугольник — доверительный интервал. (95%), а усы показывают стандартное отклонение.
Рисунок 4. Плотность в сухом и влажном состоянии, относящаяся к типу цемента ( a ), количеству пены ( b ) и типу добавки ( c ) для разного времени отверждения, где средняя точка — среднее значение, прямоугольник — доверительный интервал. (95%), а усы показывают стандартное отклонение.
Рисунок 5. Водопоглощение, связанное с типом цемента ( a ), количеством пены ( b ) и типом добавки ( c ) для разного времени отверждения, где средняя точка — среднее значение, прямоугольник — доверительный интервал (95 %), а усы показывают стандартное отклонение.
Рисунок 5. Водопоглощение, связанное с типом цемента ( a ), количеством пены ( b ) и типом добавки ( c ) для разного времени отверждения, где средняя точка — среднее значение, прямоугольник — доверительный интервал (95 %), а усы показывают стандартное отклонение.
Рисунок 6. Воздушная пустота, связанная с типом цемента ( a ), количеством пены ( b ) и типом добавки ( c ) для разного времени отверждения, где средняя точка — среднее значение, прямоугольник — доверительный интервал (95 %), а усы показывают стандартное отклонение.
Рисунок 6. Воздушная пустота, связанная с типом цемента ( a ), количеством пены ( b ) и типом добавки ( c ) для разного времени отверждения, где средняя точка — среднее значение, прямоугольник — доверительный интервал (95 %), а усы показывают стандартное отклонение.
Рис. 7. Макрографические и типовые бинарные изображения для разных миксов.
Рис. 7. Макрографические и типовые бинарные изображения для разных миксов.
Рисунок 8. Средний диаметр воздушных пустот на основе D10, D50 и D90 для всех образцов.
Рисунок 8. Средний диаметр воздушных пустот на основе D10, D50 и D90 для всех образцов.
Рисунок 9. Теплопроводность, относящаяся к типу цемента ( a ), количеству пены ( b ) и типу добавки ( c ) для разного времени отверждения, где средняя точка — среднее значение, прямоугольник — доверительный интервал (95% ), а усы — стандартное отклонение.
Рисунок 9. Теплопроводность, относящаяся к типу цемента ( a ), количеству пены ( b ) и типу добавки ( c ) для разного времени отверждения, где средняя точка — среднее значение, прямоугольник — доверительный интервал (95% ), а усы — стандартное отклонение.
Рисунок 10. Прочность на сжатие в зависимости от ( a ) плотности в сухом состоянии и ( b ) воздушной пустоты.
Рисунок 10. Прочность на сжатие в зависимости от ( a ) плотности в сухом состоянии и ( b ) воздушной пустоты.
Рисунок 11. ( a ) Зависимость теплопроводности от плотности в сухом состоянии, ( b ) водопоглощение как функция воздушной пустоты и ( c ) воздушная пустота как функция от сухой плотности.
Рисунок 11. ( a ) Зависимость теплопроводности от плотности в сухом состоянии, ( b ) водопоглощение как функция воздушной пустоты и ( c ) воздушная пустота как функция сухой плотности.
Таблица 1. Свойства цементов.
Таблица 1. Свойства цементов.
Тип цемента | Физические свойства | |||||||||
Время схватывания | Blaine cm 2 / g | # 20021 9 Горячее расширение мм | Удельный вес г / см 3 | Прочность на сжатие | ||||||
Начальное время h: min | Последнее h: min | 3 мин. 7 дней МПа | 28 дней МПа | |||||||
CP II-F | 03:52 | 04:38 | 3.291 | 2,75 | 13,31 | 0,28 | 3,11 | 28,2 | 34,5 | 42,0 |
CP II-Z | 04:15 | 05:03 | 56 05:03 | 0,22 | 2,96 | 25,8 | 33,3 | 42,0 | ||
CP V-ARI | 03:19 | 04:01 | 4,448 | 0,08 | .05 | 38,4 | 44,9 | 53,6 | ||
Тип цемента | Химические свойства | |||||||||
Al 2 O 3 9 Fe 2 O 3 % | CaO% | MgO% | SO 3 % | LOI % | Свободный CaO% | I.R.% | AC% | |||
CP II-F | 4,17 | 18,46 | 2,93 | 60,60 | 3,78 | 2,78 | 4,85 | 4,85 | 2,78 | 4,85 |
CP II-Z | 6,01 | 20,14 | 3,10 | 54,60 | 3,45 | 2,69 | 5,51 | 0,57 | 10,96 | 0,84 |
0,84 | ||||||||||
18,80 | 2,95 | 60,27 | 3,91 | 3,14 | 3,33 | 0,68 | 0,75 | 0,69 |
Таблица 2. Расчетные значения потенциального состава для каждого цемента с использованием Bogue.
Таблица 2. Расчетные значения потенциального состава для каждого цемента с использованием Bogue.
Тип цемента | C 3 S (%) | C 2 S (%) | C 3 A (%) | C 4 AF (%) | C 4 AF + C 2 F |
---|---|---|---|---|---|
CP II-F | 66.3 | 2,9 | 6,1 | 8,9 | |
CP II-Z | 25,7 | 38,5 | — | — | 17,9 |
6,2 | 9,0 |
Таблица 3. Экспериментальная матрица.
Таблица 3. Экспериментальная матрица.
Заказ | Тип цемента | Цемент (кг) | Добавка | Пена (кг) | CCW (кг) | Вода (кг) | с соотношением | |||||||
---|---|---|---|---|---|---|---|---|---|---|---|---|---|---|
CP V-ARI | 1.8 | Без добавки | 0,25 | 1,8 | 0,57 | 0,45 | ||||||||
2 | CP V-ARI | 1,8 | Пластификатор | 0,25 | 1,8 | 3 | CP V-ARI | 1,8 | Суперпластификатор | 0,25 | 1,8 | 0,57 | 0,45 | |
4 | CP V-ARI | 1.8 | Воздухововлечение | 0,25 | 1,8 | 0,57 | 0,45 | |||||||
5 | CP V-ARI | 1,8 | Без добавки | 0,34 | 0,48||||||||||
6 | CP V-ARI | 1,8 | Пластификатор | 0,34 | 1,8 | 0,48 | 0,45 | |||||||
7 | CP V-ARI | 1.8 | Суперпластификатор | 0,34 | 1,8 | 0,48 | 0,45 | |||||||
8 | CP V-ARI | 1,8 | Воздухововлечение | 14 0,34 | 9015 901514 0,34 | 905 908 9CP V-ARI | 1,8 | Добавка не использовалась | 0,43 | 1,8 | 0,39 | 0,45 | ||
10 | CP V-ARI | 1.8 | Пластификатор | 0,43 | 1,8 | 0,39 | 0,45 | |||||||
11 | CP V-ARI | 1,8 | Суперпластификатор | 0,43 | 1,86 | 12 | CP II-F | 1,8 | Воздухововлечение | 0,43 | 1,8 | 0,39 | 0,45 | |
13 | CP II-F | 1.8 | Без добавок | 0,25 | 1,8 | 0,57 | 0,45 | |||||||
14 | CP II-F | 1,8 | Пластификатор | 0,25 | 1,8 | 15 | CP II-F | 1,8 | Суперпластификатор | 0,25 | 1,8 | 0,57 | 0,45 | |
16 | CP II-F | 1.8 | Воздухововлечение | 0,25 | 1,8 | 0,57 | 0,45 | |||||||
17 | CP II-F | 1,8 | Добавка не использовалась | 0,34 | 1,8 | |||||||||
18 | CP II-F | 1,8 | Пластификатор | 0,34 | 1,8 | 0,48 | 0,45 | |||||||
19 | CP II-F | 1.8 | Суперпластификатор | 0,34 | 1,8 | 0,48 | 0,45 | |||||||
20 | CP II-F | 1,8 | Воздухововлечение | 0,34 | 0,4 | 21 | CP II-F | 1,8 | Добавка не использовалась | 0,43 | 1,8 | 0,39 | 0,45 | |
22 | CP II-F | 1.8 | Пластификатор | 0,43 | 1,8 | 0,39 | 0,45 | |||||||
23 | CP II-F | 1,8 | Суперпластификатор | 0,43 | 1,8 | 24 | CP II-F | 1,8 | Воздухововлечение | 0,43 | 1,8 | 0,39 | 0,45 | |
25 | CP II-Z | 1.8 | Без добавок | 0,25 | 1,8 | 0,57 | 0,45 | |||||||
26 | CP II-Z | 1,8 | Пластификатор | 0,25 | 1,8 | 27 | CP II-Z | 1,8 | Суперпластификатор | 0,25 | 1,8 | 0,57 | 0,45 | |
28 | CP II-Z | 1.8 | Воздухововлечение | 0,25 | 1,8 | 0,57 | 0,45 | |||||||
29 | CP II-Z | 1,8 | Добавка не использовалась | 0,34 | 1,8 | |||||||||
30 | CP II-Z | 1,8 | Пластификатор | 0,34 | 1,8 | 0,48 | 0,45 | |||||||
31 | CP II-Z | 1.8 | Суперпластификатор | 0,34 | 1,8 | 0,48 | 0,45 | |||||||
32 | CP II-Z | 1,8 | Воздухововлечение | 0,34 | 0,4 9056 | 33 | CP II-Z | 1,8 | Добавка не использовалась | 0,43 | 1,8 | 0,39 | 0,45 | |
34 | CP II-Z | 1.8 | Пластификатор | 0,43 | 1,8 | 0,39 | 0,45 | |||||||
35 | CP II-Z | 1,8 | Суперпластификатор | 0,43 | 1,8 | 36 | CP II-Z | 1,8 | Воздухововлечение | 0,43 | 1,8 | 0,39 | 0,45 |
Таблица 4. Дисперсионный анализ прочности на сжатие после 28 дней отверждения.
Таблица 4. Дисперсионный анализ прочности на сжатие после 28 дней отверждения.
Фактор | Сумма квадратов | степеней свободы | Среднее значение квадратов | F-значение | p-значение | % вклад | |||
---|---|---|---|---|---|---|---|---|---|
6 Тип цемента 909 CT 2 | 33,848 | 34,159 | 0,0000 | 13,4 | |||||
Количество пены (FA) | 196.517 | 2 | 98,258 | 99,160 | 0,0000 | 39,0 | |||
Тип присадки (AT) | 5,425 | 3 | 1,808 | 9015 901567,534 | 4 | 16,883 | 17,038 | 0,0000 | 13,4 |
CT * AT | 18,880 | 6 | 3,147 | 3,147 | 3,10080 | 3,7 | |||
FA * AT | 49,273 | 6 | 8,212 | 8,288 | 0,0000 | 9,8 | |||
CT * FA * AT | 12159 | ||||||||
CT * FA * AT | 12159 | 2,3 | 0,0151 | 5,4 | |||||
Ошибка | 71,345 | 72 | 0,991 | 14,2 | |||||
Таблица 5. Дисперсионный анализ прочности на сжатие после 365 дней отверждения.
Таблица 5. Дисперсионный анализ прочности на сжатие после 365 дней отверждения.
Фактор | Сумма квадратов | степеней свободы | Среднее значение квадратов | F-значение | p-значение | % вклад | |||||||||||||||||||||||||||||||||||||||||||||||||||||||||||||||||||||||||||||||||||||||||||||||||||||||||||||||||||||||||||||||||||||||||||||||||||||||||||||||||||||||||||||||||||||||||||||||||||||||||||||||||||||||||||||||||||||||||||||||||||||||||||||||||||||||||||||||||||||||||||||||||||||||||||||||||||||||||||||||||||||||||||||||||||||||||||||||||||||||||||||||||||||||||||||||||||||||||||||||||||||||||||||||||||||||||||||||||||||||||||||||||||||||||||||||||||||||||||||||||||||||||||||||||||||||||||||||||||||||||||||||||||||||||||||||||||||||||||||||||||||||||||||||||||||||||||||||||||||||
---|---|---|---|---|---|---|---|---|---|---|---|---|---|---|---|---|---|---|---|---|---|---|---|---|---|---|---|---|---|---|---|---|---|---|---|---|---|---|---|---|---|---|---|---|---|---|---|---|---|---|---|---|---|---|---|---|---|---|---|---|---|---|---|---|---|---|---|---|---|---|---|---|---|---|---|---|---|---|---|---|---|---|---|---|---|---|---|---|---|---|---|---|---|---|---|---|---|---|---|---|---|---|---|---|---|---|---|---|---|---|---|---|---|---|---|---|---|---|---|---|---|---|---|---|---|---|---|---|---|---|---|---|---|---|---|---|---|---|---|---|---|---|---|---|---|---|---|---|---|---|---|---|---|---|---|---|---|---|---|---|---|---|---|---|---|---|---|---|---|---|---|---|---|---|---|---|---|---|---|---|---|---|---|---|---|---|---|---|---|---|---|---|---|---|---|---|---|---|---|---|---|---|---|---|---|---|---|---|---|---|---|---|---|---|---|---|---|---|---|---|---|---|---|---|---|---|---|---|---|---|---|---|---|---|---|---|---|---|---|---|---|---|---|---|---|---|---|---|---|---|---|---|---|---|---|---|---|---|---|---|---|---|---|---|---|---|---|---|---|---|---|---|---|---|---|---|---|---|---|---|---|---|---|---|---|---|---|---|---|---|---|---|---|---|---|---|---|---|---|---|---|---|---|---|---|---|---|---|---|---|---|---|---|---|---|---|---|---|---|---|---|---|---|---|---|---|---|---|---|---|---|---|---|---|---|---|---|---|---|---|---|---|---|---|---|---|---|---|---|---|---|---|---|---|---|---|---|---|---|---|---|---|---|---|---|---|---|---|---|---|---|---|---|---|---|---|---|---|---|---|---|---|---|---|---|---|---|---|---|---|---|---|---|---|---|---|---|---|---|---|---|---|---|---|---|---|---|---|---|---|---|---|---|---|---|---|---|---|---|---|---|---|---|---|---|---|---|---|---|---|---|---|---|---|---|---|---|---|---|---|---|---|---|---|---|---|---|---|---|---|---|---|---|---|---|---|---|---|---|---|---|---|---|---|---|---|---|---|---|---|---|---|---|---|---|---|---|---|---|---|---|---|---|---|---|---|---|---|---|---|---|---|---|---|---|---|---|---|---|---|---|---|---|---|---|---|---|---|---|---|---|---|---|---|---|---|---|---|---|---|---|---|---|---|---|---|---|---|---|---|---|---|---|---|---|---|---|---|---|---|---|---|---|---|---|---|---|---|---|---|---|---|---|---|---|---|---|---|---|---|---|---|---|---|---|---|---|---|---|---|---|---|---|---|---|---|---|---|---|---|---|---|---|---|---|---|---|---|---|---|---|---|---|---|---|---|---|---|---|---|---|---|---|---|---|
Тип цемента (CT)618 | 2 | 13,309 | 9,28 | 0,0002 | 2,8 | ||||||||||||||||||||||||||||||||||||||||||||||||||||||||||||||||||||||||||||||||||||||||||||||||||||||||||||||||||||||||||||||||||||||||||||||||||||||||||||||||||||||||||||||||||||||||||||||||||||||||||||||||||||||||||||||||||||||||||||||||||||||||||||||||||||||||||||||||||||||||||||||||||||||||||||||||||||||||||||||||||||||||||||||||||||||||||||||||||||||||||||||||||||||||||||||||||||||||||||||||||||||||||||||||||||||||||||||||||||||||||||||||||||||||||||||||||||||||||||||||||||||||||||||||||||||||||||||||||||||||||||||||||||||||||||||||||||||||||||||||||||||||||||||||||||||||||||||||||||||||
Количество пены (FA) | 362,858 | 2 | 181,429 | 86,817 | 3 | 28,939 | 20,17 | 0,0000 | 9,0 | ||||||||||||||||||||||||||||||||||||||||||||||||||||||||||||||||||||||||||||||||||||||||||||||||||||||||||||||||||||||||||||||||||||||||||||||||||||||||||||||||||||||||||||||||||||||||||||||||||||||||||||||||||||||||||||||||||||||||||||||||||||||||||||||||||||||||||||||||||||||||||||||||||||||||||||||||||||||||||||||||||||||||||||||||||||||||||||||||||||||||||||||||||||||||||||||||||||||||||||||||||||||||||||||||||||||||||||||||||||||||||||||||||||||||||||||||||||||||||||||||||||||||||||||||||||||||||||||||||||||||||||||||||||||||||||||||||||||||||||||||||||||||||||||||||||||||||||||||||||
CT * FA | 69,851 | 4 | 17,463 12.17 | 0,0000 | 7,3 | ||||||||||||||||||||||||||||||||||||||||||||||||||||||||||||||||||||||||||||||||||||||||||||||||||||||||||||||||||||||||||||||||||||||||||||||||||||||||||||||||||||||||||||||||||||||||||||||||||||||||||||||||||||||||||||||||||||||||||||||||||||||||||||||||||||||||||||||||||||||||||||||||||||||||||||||||||||||||||||||||||||||||||||||||||||||||||||||||||||||||||||||||||||||||||||||||||||||||||||||||||||||||||||||||||||||||||||||||||||||||||||||||||||||||||||||||||||||||||||||||||||||||||||||||||||||||||||||||||||||||||||||||||||||||||||||||||||||||||||||||||||||||||||||||||||||||||||||||||||||||
CT * AT | 114.476 | 6 | 19,079 | 13,30 | 0,0000 | 11,9 | |||||||||||||||||||||||||||||||||||||||||||||||||||||||||||||||||||||||||||||||||||||||||||||||||||||||||||||||||||||||||||||||||||||||||||||||||||||||||||||||||||||||||||||||||||||||||||||||||||||||||||||||||||||||||||||||||||||||||||||||||||||||||||||||||||||||||||||||||||||||||||||||||||||||||||||||||||||||||||||||||||||||||||||||||||||||||||||||||||||||||||||||||||||||||||||||||||||||||||||||||||||||||||||||||||||||||||||||||||||||||||||||||||||||||||||||||||||||||||||||||||||||||||||||||||||||||||||||||||||||||||||||||||||||||||||||||||||||||||||||||||||||||||||||||||||||||||||||||||||||
9056 9015 9015 9015 9015 9056 FA9 9015 9015 9056 8,01 | 0,0000 | 7,2 | |||||||||||||||||||||||||||||||||||||||||||||||||||||||||||||||||||||||||||||||||||||||||||||||||||||||||||||||||||||||||||||||||||||||||||||||||||||||||||||||||||||||||||||||||||||||||||||||||||||||||||||||||||||||||||||||||||||||||||||||||||||||||||||||||||||||||||||||||||||||||||||||||||||||||||||||||||||||||||||||||||||||||||||||||||||||||||||||||||||||||||||||||||||||||||||||||||||||||||||||||||||||||||||||||||||||||||||||||||||||||||||||||||||||||||||||||||||||||||||||||||||||||||||||||||||||||||||||||||||||||||||||||||||||||||||||||||||||||||||||||||||||||||||||||||||||||||||||||||||||||||
CT * FA * AT | 127,327 | 12 | 10,611 | 7,39 | 0,0000 | 13,3 103 | |||||||||||||||||||||||||||||||||||||||||||||||||||||||||||||||||||||||||||||||||||||||||||||||||||||||||||||||||||||||||||||||||||||||||||||||||||||||||||||||||||||||||||||||||||||||||||||||||||||||||||||||||||||||||||||||||||||||||||||||||||||||||||||||||||||||||||||||||||||||||||||||||||||||||||||||||||||||||||||||||||||||||||||||||||||||||||||||||||||||||||||||||||||||||||||||||||||||||||||||||||||||||||||||||||||||||||||||||||||||||||||||||||||||||||||||||||||||||||||||||||||||||||||||||||||||||||||||||||||||||||||||||||||||||||||||||||||||||||||||||||||||||||||||||||||||||||||||||||||||
Ошибка318 | 72 | 1,435 | 10,8 | ||||||||||||||||||||||||||||||||||||||||||||||||||||||||||||||||||||||||||||||||||||||||||||||||||||||||||||||||||||||||||||||||||||||||||||||||||||||||||||||||||||||||||||||||||||||||||||||||||||||||||||||||||||||||||||||||||||||||||||||||||||||||||||||||||||||||||||||||||||||||||||||||||||||||||||||||||||||||||||||||||||||||||||||||||||||||||||||||||||||||||||||||||||||||||||||||||||||||||||||||||||||||||||||||||||||||||||||||||||||||||||||||||||||||||||||||||||||||||||||||||||||||||||||||||||||||||||||||||||||||||||||||||||||||||||||||||||||||||||||||||||||||||||||||||||||||||||||||||||||||||
Всего | 960.263 | 107 | 100,0 |
Фактор | Сумма квадратов | степеней свободы | Среднее значение квадратов | F-значение | p-значение | % Вклад | |
---|---|---|---|---|---|---|---|
909 569 CT Тип цемента (CT) 2 | 329,896 | 275.9 | 0,0000 | 19,4 | |||
Количество пены (FA) | 1,696,582 | 2 | 848,291 | 709,6 | 0,0000 | 50,0 | 13,665 | 11,4 | 0,0000 | 1,2 |
CT * FA | 324,870 | 4 | 81,218 | 67,9 | 0,0000 | 4 9,68488 | 7.1 | 0,0000 | 1,5 |
FA * AT | 314,349 | 6 | 52,392 | 43,8 | 0,0000 | 9,3 | |
,69 9015 9015 9015 9015 6 | 15,3 | 0,0000 | 6,5 | ||||
Ошибка | 86,077 | 72 | 1196 | 2,5 | |||
9015 | 9015 | 9015 | 9056 .0 |
Таблица 7. Дисперсионный анализ плотности во влажном состоянии (28 дней отверждения).
Таблица 7. Дисперсионный анализ плотности во влажном состоянии (28 дней отверждения).
Фактор | Сумма квадратов | степеней свободы | Среднее квадратов | F-значение | p-значение | % вклад | |||||
---|---|---|---|---|---|---|---|---|---|---|---|
908 CT Тип цемента (CT) 2 | 271,392 | 344.4 | 0,0000 | 29,1 | |||||||
Количество пены (FA) | 526,782 | 2 | 263,391 | 334,3 | 0,0000 | 28,2 | 17,384 | 22,1 | 0,0000 | 2,8 | |
CT * FA | 165,006 | 4 | 41,251 | 52,4 | 0,0000 | 4 8,814 337 | 18.2 | 0,0000 | 4,6 | ||
FA * AT | 271,135 | 6 | 45,189 | 57,3 | 0,0000 | 14,5 | |||||
CT * FA | 17,4 | 0,0000 | 8,8 | ||||||||
Ошибка | 56,735 | 72 | 788 | 3,0 | |||||||
.0 |
Таблица 8. Дисперсионный анализ водопоглощения (28 дней отверждения).
Таблица 8. Дисперсионный анализ водопоглощения (28 дней отверждения).
Фактор | Сумма квадратов | степеней свободы | Среднее значение квадратов | F-значение | p-значение | % Вклад | ||||||||||||||||||||||||||||||||||||||||||||||||||||||||||||||||||||||||||||||||||||||||||||||||||||||||||||||||||||||||||||||||||||||||||||||||||||||||||||||||||||||||||||||||||||||||||||||||||||||||||||||||||||||||||||||||||||||||||||||||||||||||||||||||||||||||||||||||||||||||||||||||||||||||||||||||||||||||||||||||||||||||||||||||||||||||||||||||||||||||||||||||||||||||||||||||||||||||||||||||||||||||||||||||||||||||||||
---|---|---|---|---|---|---|---|---|---|---|---|---|---|---|---|---|---|---|---|---|---|---|---|---|---|---|---|---|---|---|---|---|---|---|---|---|---|---|---|---|---|---|---|---|---|---|---|---|---|---|---|---|---|---|---|---|---|---|---|---|---|---|---|---|---|---|---|---|---|---|---|---|---|---|---|---|---|---|---|---|---|---|---|---|---|---|---|---|---|---|---|---|---|---|---|---|---|---|---|---|---|---|---|---|---|---|---|---|---|---|---|---|---|---|---|---|---|---|---|---|---|---|---|---|---|---|---|---|---|---|---|---|---|---|---|---|---|---|---|---|---|---|---|---|---|---|---|---|---|---|---|---|---|---|---|---|---|---|---|---|---|---|---|---|---|---|---|---|---|---|---|---|---|---|---|---|---|---|---|---|---|---|---|---|---|---|---|---|---|---|---|---|---|---|---|---|---|---|---|---|---|---|---|---|---|---|---|---|---|---|---|---|---|---|---|---|---|---|---|---|---|---|---|---|---|---|---|---|---|---|---|---|---|---|---|---|---|---|---|---|---|---|---|---|---|---|---|---|---|---|---|---|---|---|---|---|---|---|---|---|---|---|---|---|---|---|---|---|---|---|---|---|---|---|---|---|---|---|---|---|---|---|---|---|---|---|---|---|---|---|---|---|---|---|---|---|---|---|---|---|---|---|---|---|---|---|---|---|---|---|---|---|---|---|---|---|---|---|---|---|---|---|---|---|---|---|---|---|---|---|---|---|---|---|---|---|---|---|---|---|---|---|---|---|---|---|---|---|---|---|---|---|---|---|---|---|---|---|---|---|---|---|---|---|---|---|---|---|---|---|---|---|---|---|---|---|---|---|---|---|---|---|---|---|---|---|---|---|---|---|---|---|---|---|---|---|---|---|---|---|---|---|---|---|---|---|---|---|---|---|---|---|---|---|---|---|---|---|---|---|---|---|---|---|---|---|---|---|---|---|---|---|---|---|
9 Тип цемента (CT)91 | 2 | 173,95 | 32,59 | 0,0000 | 3,3 | |||||||||||||||||||||||||||||||||||||||||||||||||||||||||||||||||||||||||||||||||||||||||||||||||||||||||||||||||||||||||||||||||||||||||||||||||||||||||||||||||||||||||||||||||||||||||||||||||||||||||||||||||||||||||||||||||||||||||||||||||||||||||||||||||||||||||||||||||||||||||||||||||||||||||||||||||||||||||||||||||||||||||||||||||||||||||||||||||||||||||||||||||||||||||||||||||||||||||||||||||||||||||||||||||||||||||||||
Количество пены (FA) | 5317,99 | 2 | 2659,00 | 56 498.208 9015 AT)120,47 | 3 | 40,16 | 7,52 | 0,0001 | 1,1 | |||||||||||||||||||||||||||||||||||||||||||||||||||||||||||||||||||||||||||||||||||||||||||||||||||||||||||||||||||||||||||||||||||||||||||||||||||||||||||||||||||||||||||||||||||||||||||||||||||||||||||||||||||||||||||||||||||||||||||||||||||||||||||||||||||||||||||||||||||||||||||||||||||||||||||||||||||||||||||||||||||||||||||||||||||||||||||||||||||||||||||||||||||||||||||||||||||||||||||||||||||||||||||||||||||||||||
CT * FA | 901,98 | 4 | 225,49 42159 | 0,0000 | 8,4 | |||||||||||||||||||||||||||||||||||||||||||||||||||||||||||||||||||||||||||||||||||||||||||||||||||||||||||||||||||||||||||||||||||||||||||||||||||||||||||||||||||||||||||||||||||||||||||||||||||||||||||||||||||||||||||||||||||||||||||||||||||||||||||||||||||||||||||||||||||||||||||||||||||||||||||||||||||||||||||||||||||||||||||||||||||||||||||||||||||||||||||||||||||||||||||||||||||||||||||||||||||||||||||||||||||||||||||||
CT * AT | 1314,68 | 6 | 219,11 | 41,05 | 0,0000 | 12,3 | ||||||||||||||||||||||||||||||||||||||||||||||||||||||||||||||||||||||||||||||||||||||||||||||||||||||||||||||||||||||||||||||||||||||||||||||||||||||||||||||||||||||||||||||||||||||||||||||||||||||||||||||||||||||||||||||||||||||||||||||||||||||||||||||||||||||||||||||||||||||||||||||||||||||||||||||||||||||||||||||||||||||||||||||||||||||||||||||||||||||||||||||||||||||||||||||||||||||||||||||||||||||||||||||||||||||||||||
9056 FA9 9015 9015 9056 9056 FA9 9015 9056 FA9 31,17 | 0,0000 | 9,3 | ||||||||||||||||||||||||||||||||||||||||||||||||||||||||||||||||||||||||||||||||||||||||||||||||||||||||||||||||||||||||||||||||||||||||||||||||||||||||||||||||||||||||||||||||||||||||||||||||||||||||||||||||||||||||||||||||||||||||||||||||||||||||||||||||||||||||||||||||||||||||||||||||||||||||||||||||||||||||||||||||||||||||||||||||||||||||||||||||||||||||||||||||||||||||||||||||||||||||||||||||||||||||||||||||||||||||||||||||
CT * FA * AT | 1310,15 | 12 | 109,18 | 20,46 | 0,0000 | 12,2 | ||||||||||||||||||||||||||||||||||||||||||||||||||||||||||||||||||||||||||||||||||||||||||||||||||||||||||||||||||||||||||||||||||||||||||||||||||||||||||||||||||||||||||||||||||||||||||||||||||||||||||||||||||||||||||||||||||||||||||||||||||||||||||||||||||||||||||||||||||||||||||||||||||||||||||||||||||||||||||||||||||||||||||||||||||||||||||||||||||||||||||||||||||||||||||||||||||||||||||||||||||||||||||||||||||||||||||||
72 | 5,34 | 3,6 | ||||||||||||||||||||||||||||||||||||||||||||||||||||||||||||||||||||||||||||||||||||||||||||||||||||||||||||||||||||||||||||||||||||||||||||||||||||||||||||||||||||||||||||||||||||||||||||||||||||||||||||||||||||||||||||||||||||||||||||||||||||||||||||||||||||||||||||||||||||||||||||||||||||||||||||||||||||||||||||||||||||||||||||||||||||||||||||||||||||||||||||||||||||||||||||||||||||||||||||||||||||||||||||||||||||||||||||||||
Всего | 10,695,54 | 107 | 100,0 |
Фактор | Сумма квадратов | степеней свободы | Среднее значение квадратов | F-значение | p-значение | % Вклад | ||||||||||||||||||||||||||||||||||||||||||||||||||||||||||||||||||||||||||||||||||||||||||||||||||||||||||||||||||||||||||||||||||||||||||||||||||||||||||||||||||||||||||||||||||||||||||||||||||||||||||||||||||||||||||||||||||||||||||||||||||||||||||||||||||||||||||||||||||||||||||||||||||||||||||||||||||||||||||||||||||||||||||||||||||||||||||||||||||||||||||||||||
---|---|---|---|---|---|---|---|---|---|---|---|---|---|---|---|---|---|---|---|---|---|---|---|---|---|---|---|---|---|---|---|---|---|---|---|---|---|---|---|---|---|---|---|---|---|---|---|---|---|---|---|---|---|---|---|---|---|---|---|---|---|---|---|---|---|---|---|---|---|---|---|---|---|---|---|---|---|---|---|---|---|---|---|---|---|---|---|---|---|---|---|---|---|---|---|---|---|---|---|---|---|---|---|---|---|---|---|---|---|---|---|---|---|---|---|---|---|---|---|---|---|---|---|---|---|---|---|---|---|---|---|---|---|---|---|---|---|---|---|---|---|---|---|---|---|---|---|---|---|---|---|---|---|---|---|---|---|---|---|---|---|---|---|---|---|---|---|---|---|---|---|---|---|---|---|---|---|---|---|---|---|---|---|---|---|---|---|---|---|---|---|---|---|---|---|---|---|---|---|---|---|---|---|---|---|---|---|---|---|---|---|---|---|---|---|---|---|---|---|---|---|---|---|---|---|---|---|---|---|---|---|---|---|---|---|---|---|---|---|---|---|---|---|---|---|---|---|---|---|---|---|---|---|---|---|---|---|---|---|---|---|---|---|---|---|---|---|---|---|---|---|---|---|---|---|---|---|---|---|---|---|---|---|---|---|---|---|---|---|---|---|---|---|---|---|---|---|---|---|---|---|---|---|---|---|---|---|---|---|---|---|---|---|---|---|---|---|---|---|---|---|---|---|---|---|---|---|---|---|---|---|---|---|---|---|---|---|---|---|---|---|---|---|---|---|---|---|---|---|---|---|---|---|---|---|---|---|---|---|---|---|---|---|---|---|---|---|---|---|---|---|---|---|---|
Тип цемента (CT) 5718 | 2 | 28,59 | 4,85 | 0,0105 | 0,6 | |||||||||||||||||||||||||||||||||||||||||||||||||||||||||||||||||||||||||||||||||||||||||||||||||||||||||||||||||||||||||||||||||||||||||||||||||||||||||||||||||||||||||||||||||||||||||||||||||||||||||||||||||||||||||||||||||||||||||||||||||||||||||||||||||||||||||||||||||||||||||||||||||||||||||||||||||||||||||||||||||||||||||||||||||||||||||||||||||||||||||||||||||
Количество пены (FA) | 3697,69 | 2 | 1848,84 | 9056 9056 903 AT) | 124,85 | 3 | 41,62 | 7,06 | 0,0003 | 1,4 | ||||||||||||||||||||||||||||||||||||||||||||||||||||||||||||||||||||||||||||||||||||||||||||||||||||||||||||||||||||||||||||||||||||||||||||||||||||||||||||||||||||||||||||||||||||||||||||||||||||||||||||||||||||||||||||||||||||||||||||||||||||||||||||||||||||||||||||||||||||||||||||||||||||||||||||||||||||||||||||||||||||||||||||||||||||||||||||||||||||||||||||
CT * FA | 987,53 | 4 | 246,88 | 900,0000 | 10,9 | |||||||||||||||||||||||||||||||||||||||||||||||||||||||||||||||||||||||||||||||||||||||||||||||||||||||||||||||||||||||||||||||||||||||||||||||||||||||||||||||||||||||||||||||||||||||||||||||||||||||||||||||||||||||||||||||||||||||||||||||||||||||||||||||||||||||||||||||||||||||||||||||||||||||||||||||||||||||||||||||||||||||||||||||||||||||||||||||||||||||||||||||||
CT * AT | 1578,10 | 6 | 263,02 | 44,64 | 0,0000 | 17,4 | 9056 FA8 27,20 | 0,0000 | 10,6 | |||||||||||||||||||||||||||||||||||||||||||||||||||||||||||||||||||||||||||||||||||||||||||||||||||||||||||||||||||||||||||||||||||||||||||||||||||||||||||||||||||||||||||||||||||||||||||||||||||||||||||||||||||||||||||||||||||||||||||||||||||||||||||||||||||||||||||||||||||||||||||||||||||||||||||||||||||||||||||||||||||||||||||||||||||||||||||||||||||||||||||||
CT * FA * AT | 1243,12 | 12 | 103,59 | 17,58 | 0,0000 | 13,7 | ||||||||||||||||||||||||||||||||||||||||||||||||||||||||||||||||||||||||||||||||||||||||||||||||||||||||||||||||||||||||||||||||||||||||||||||||||||||||||||||||||||||||||||||||||||||||||||||||||||||||||||||||||||||||||||||||||||||||||||||||||||||||||||||||||||||||||||||||||||||||||||||||||||||||||||||||||||||||||||||||||||||||||||||||||||||||||||||||||||||||||||||||
72 | 5,89 | 4,7 | ||||||||||||||||||||||||||||||||||||||||||||||||||||||||||||||||||||||||||||||||||||||||||||||||||||||||||||||||||||||||||||||||||||||||||||||||||||||||||||||||||||||||||||||||||||||||||||||||||||||||||||||||||||||||||||||||||||||||||||||||||||||||||||||||||||||||||||||||||||||||||||||||||||||||||||||||||||||||||||||||||||||||||||||||||||||||||||||||||||||||||||||||||||
Итого | 9074,343 | 107 | 100,0 | 0
Фактор | Сумма квадратов | степеней свободы | Среднее значение квадратов | F-значение | p-значение | % Вклад | ||||||||||||||||||||||||||||||||||||||||||||||||||||||||||||||||||||||||||||||||||||||||||||||||||||||||||||||||||||||||||||||||||||||||||||||||||||||||||||||||||||||||||||||||||||||||||||||||||||||||||||||||||||||||||||||||||||||||||||||||||||||||||||||||||||||||||||||||||||||||||||||||||||||||||||||||
---|---|---|---|---|---|---|---|---|---|---|---|---|---|---|---|---|---|---|---|---|---|---|---|---|---|---|---|---|---|---|---|---|---|---|---|---|---|---|---|---|---|---|---|---|---|---|---|---|---|---|---|---|---|---|---|---|---|---|---|---|---|---|---|---|---|---|---|---|---|---|---|---|---|---|---|---|---|---|---|---|---|---|---|---|---|---|---|---|---|---|---|---|---|---|---|---|---|---|---|---|---|---|---|---|---|---|---|---|---|---|---|---|---|---|---|---|---|---|---|---|---|---|---|---|---|---|---|---|---|---|---|---|---|---|---|---|---|---|---|---|---|---|---|---|---|---|---|---|---|---|---|---|---|---|---|---|---|---|---|---|---|---|---|---|---|---|---|---|---|---|---|---|---|---|---|---|---|---|---|---|---|---|---|---|---|---|---|---|---|---|---|---|---|---|---|---|---|---|---|---|---|---|---|---|---|---|---|---|---|---|---|---|---|---|---|---|---|---|---|---|---|---|---|---|---|---|---|---|---|---|---|---|---|---|---|---|---|---|---|---|---|---|---|---|---|---|---|---|---|---|---|---|---|---|---|---|---|---|---|---|---|---|---|---|---|---|---|---|---|---|---|---|---|---|---|---|---|---|---|---|---|---|---|---|---|---|---|---|---|---|---|---|---|---|---|---|---|---|---|---|---|---|---|---|---|---|---|---|---|---|
Тип цемента (CT)43250 | 2 | 0,21625 | 15,9986 | 0,0000 | 7,0 | |||||||||||||||||||||||||||||||||||||||||||||||||||||||||||||||||||||||||||||||||||||||||||||||||||||||||||||||||||||||||||||||||||||||||||||||||||||||||||||||||||||||||||||||||||||||||||||||||||||||||||||||||||||||||||||||||||||||||||||||||||||||||||||||||||||||||||||||||||||||||||||||||||||||||||||||||
Количество пены (FA) | 1,59326 | 2 | 0,79663 | |||||||||||||||||||||||||||||||||||||||||||||||||||||||||||||||||||||||||||||||||||||||||||||||||||||||||||||||||||||||||||||||||||||||||||||||||||||||||||||||||||||||||||||||||||||||||||||||||||||||||||||||||||||||||||||||||||||||||||||||||||||||||||||||||||||||||||||||||||||||||||||||||||||||||||||||||||
0,33054 | 3 | 0,11018 | 8,1513 | 0,0000 | 5,3 | |||||||||||||||||||||||||||||||||||||||||||||||||||||||||||||||||||||||||||||||||||||||||||||||||||||||||||||||||||||||||||||||||||||||||||||||||||||||||||||||||||||||||||||||||||||||||||||||||||||||||||||||||||||||||||||||||||||||||||||||||||||||||||||||||||||||||||||||||||||||||||||||||||||||||||||||||
CT * FA | 1, | 4 | 0.47986 | 35,5013 | 0,0000 | 31,0 | ||||||||||||||||||||||||||||||||||||||||||||||||||||||||||||||||||||||||||||||||||||||||||||||||||||||||||||||||||||||||||||||||||||||||||||||||||||||||||||||||||||||||||||||||||||||||||||||||||||||||||||||||||||||||||||||||||||||||||||||||||||||||||||||||||||||||||||||||||||||||||||||||||||||||||||||||
CT * AT | 0,21060 | 6 | 0,03510 | 2,5968 | 0,0246 | 60,04518 | 3,3423 | 0,0058 | 4,4 | |||||||||||||||||||||||||||||||||||||||||||||||||||||||||||||||||||||||||||||||||||||||||||||||||||||||||||||||||||||||||||||||||||||||||||||||||||||||||||||||||||||||||||||||||||||||||||||||||||||||||||||||||||||||||||||||||||||||||||||||||||||||||||||||||||||||||||||||||||||||||||||||||||||||||||||
CT * FA * AT | 0,46158 | 12 | 0,03846 | 2,8457 | 0,0029 | 7.5 | ||||||||||||||||||||||||||||||||||||||||||||||||||||||||||||||||||||||||||||||||||||||||||||||||||||||||||||||||||||||||||||||||||||||||||||||||||||||||||||||||||||||||||||||||||||||||||||||||||||||||||||||||||||||||||||||||||||||||||||||||||||||||||||||||||||||||||||||||||||||||||||||||||||||||||||||||
Ошибка | 0,97320 | 72 | 0,01352 | 15,7 | ||||||||||||||||||||||||||||||||||||||||||||||||||||||||||||||||||||||||||||||||||||||||||||||||||||||||||||||||||||||||||||||||||||||||||||||||||||||||||||||||||||||||||||||||||||||||||||||||||||||||||||||||||||||||||||||||||||||||||||||||||||||||||||||||||||||||||||||||||||||||||||||||||||||||||||||||||
Итого | 6,192 | 107 | 9015 |
Серия | AAC0 | AAC1 | AAC2 | AAC3 | AAC4 | 0 | 0.55 | 1,15 | 2,30 | 3,50 | |||||||||||||||||||||||||||||||||||||||||||||||||||||||||||||||||||||||||||||||||||||||||||||||||||||||||||||||||||||||||||||||||||||||||||||||||||||||||||||||||||||||||||||||||||||||||||||||||||||||||||||||||||||||||||||||||||||||||||||||||||||||||||||
---|---|---|---|---|---|---|---|---|---|---|---|---|---|---|---|---|---|---|---|---|---|---|---|---|---|---|---|---|---|---|---|---|---|---|---|---|---|---|---|---|---|---|---|---|---|---|---|---|---|---|---|---|---|---|---|---|---|---|---|---|---|---|---|---|---|---|---|---|---|---|---|---|---|---|---|---|---|---|---|---|---|---|---|---|---|---|---|---|---|---|---|---|---|---|---|---|---|---|---|---|---|---|---|---|---|---|---|---|---|---|---|---|---|---|---|---|---|---|---|---|---|---|---|---|---|---|---|---|---|---|---|---|---|---|---|---|---|---|---|---|---|---|---|---|---|---|---|---|---|---|---|---|---|---|---|---|---|---|---|---|---|---|---|---|---|---|---|---|---|---|---|---|---|---|---|---|---|---|---|---|---|---|---|---|---|---|---|---|---|---|---|---|---|---|---|---|---|---|---|---|---|---|---|---|---|---|---|---|---|---|---|---|---|---|---|---|---|---|---|---|---|---|---|---|---|---|---|---|---|---|---|---|---|---|---|---|---|---|---|---|---|---|---|---|---|---|---|---|---|---|---|---|---|---|---|---|---|---|---|---|---|---|---|
Цемент + известь [кг] | 143,0 | 145,0 | 141,0 | 136,0 | 133,0 | 347,0 | 345,0 | 340,0 | |||||||||||||||||||||||||||||||||||||||||||||||||||||||||||||||||||||||||||||||||||||||||||||||||||||||||||||||||||||||||||||||||||||||||||||||||||||||||||||||||||||||||||||||||||||||||||||||||||||||||||||||||||||||||||||||||||||||||||||||||||||||||||||||
Добавленный гипс [кг] | 0 | 2,7 | 5,6 | 11,1 | 16,6 | ||||||||||||||||||||||||||||||||||||||||||||||||||||||||||||||||||||||||||||||||||||||||||||||||||||||||||||||||||||||||||||||||||||||||||||||||||||||||||||||||||||||||||||||||||||||||||||||||||||||||||||||||||||||||||||||||||||||||||||||||||||||||||||||||||
кг / сек | Gy7 | 3,8 | 3,7 | 3,5 | 3,5 | ||||||||||||||||||||||||||||||||||||||||||||||||||||||||||||||||||||||||||||||||||||||||||||||||||||||||||||||||||||||||||||||||||||||||||||||||||||||||||||||||||||||||||||||||||||||||||||||||||||||||||||||||||||||||||||||||||||||||||||||||||||||||||||||||||
Общее содержание гипса [кг] | 3,7 | 6,5 | 9,3 | 14,6 | 20,1 | 0,42 | 0,42 | 0,42 | 0,42 | ||||||||||||||||||||||||||||||||||||||||||||||||||||||||||||||||||||||||||||||||||||||||||||||||||||||||||||||||||||||||||||||||||||||||||||||||||||||||||||||||||||||||||||||||||||||||||||||||||||||||||||||||||||||||||||||||||||||||||||||||||||||||||||||
Соотношение вода / сухие компоненты | 0,49 | 0,50 | 0,50 | 0,51 | 0,50 | 0,51 | 0,50 | 902 902 классическая обработка в вакууме первая фаза) использовалась в производственном процессе.Весь гидротермальный процесс длился 12 часов. Образцы для эксперимента отбирали сразу после автоклавирования.
Серия | AAC0 | AAC1 | AAC2 | AAC3 | AAC4 | ||||||||
---|---|---|---|---|---|---|---|---|---|---|---|---|---|
520 | 510 | 514 | 541 | ||||||||||
Прочность на сжатие в сухом состоянии [Н / мм 2 ] | 3.88 | 4,16 | 4,31 | 5,46 | 5,60 | ||||||||
Прочность на сжатие при стабилизированном содержании влаги [Н / мм 2 ] | 2,70 | 3,19 | 3,13 | 90143,19 Прочность на разрыв [Н / мм 2 ] | 1,1 | 1,1 | 1,3 | 1,4 | 1,6 | ||||
Стабилизированная влажность [%] | 5,1 | 4.4 | 4,8 | 5,4 | 4,9 | ||||||||
Время стабилизации влажности [ч] | 21,0 | 25,0 | 30,0 | 44,0 | 58,0 | %||||||||
59,7 | 61,8 | 56,4 | 60,1 | ||||||||||
после 10 ‘ | 185,4 | 148,1 | 151,4 | 91,6 | 1 | ||||||||
Водопоглощение [г / (м 2 с 0,5 )] | через 30 мин. | 150,8 | 113,5 | 120,3 | 77,9 | 94,3 | |||||||
125,0 | 91,3 | 95,1 | 65,9 | 74,7 | |||||||||
после 1 часа | 2,3 | 1,9 | 1,6 | 1,3 | 1,6 | 1,3 | 1 | 3,1 | 2,3 | 1,8 | 2,3 | ||
Капиллярный подъем [см] | через 24 часа | 6,2 | 4,7 | 3,8 | 2,7 | 3,8 | 2,7 | 9014 | после 24 часов 8,66,5 | 5,4 | 3,8 | 3,9 | |
через 72 часа | 7,4 | 10,0 | 7,3 | 4 .13444,4 | |||||||||
Изменение влажности в результате высыхания от влаги после производственного процесса [%] | через 0 ч | 29,6 | 28,2 | 29,8 | 29,6 | ||||||||
через 24 часа | 19,1 | 20,4 | 21,8 | 22,3 | 24,8 | ||||||||
через 48 часов | 12,0 | 12,8 | 16,0 | 18,4 | |||||||||
через 72 часа | 9,2 | 9,9 | 11,5 | 13,1 | 15,6 | ||||||||
через 96 часов | |||||||||||||
через 96 часов | 7,7139 8,33 14,0 | ||||||||||||
через 120 часов | 6,1 | 6,5 | 8,1 | 9,9 | 12,2 | ||||||||
через 144 часа | 5,2 | 5,2 | 6.8 | 8,5 | 10,8 | ||||||||
после 168 ч | 4,4 | 4,4 | 5,6 | 7,3 | 9,6 | ||||||||
после 184 ч | 3,813 | 3.8 8,7 | |||||||||||
через 200 ч | 3,6 | 3,4 | 4,4 | 6,0 | 8,2 | ||||||||
через 224 ч | 3,3 | 2,8 | 3,5 | 4.9 | 6,9 | ||||||||
после 264 ч | 3,1 | 2,4 | 2,9 | 4,1 | 6,1 | 6,1 | 6,1 | 59,7 | 61,8 | 56,4 | 60,1 | ||
через 6 часов | 59,2 | 54,4 | 57,7 | 52,4 51 | 55,5 | 934952,47 | 45,8 | 50,9 | 45,9 | 48,5 | |||
через 18 ч | 44,3 | 38,2 | 45,1 | 39,8 | 42,1 | 39,8 | 42,1 | через 24 часа36,6 | 31,0 | 38,8 | 34,4 | 36,3 | |
вне максимального содержания воды [%] | через 30 часов | 28,4 | 24.4 | 32,1 | 28,8 | 31,5 | |||||||
через 36 ч | 22,5 | 20,0 | 26,2 | 24,8 | 27,5 | ||||||||
27,5 | |||||||||||||
93,93 | 21,8 | 24,5 | |||||||||||
через 48 часов | 14,2 | 14,3 | 19,1 | 19,6 | 22,3 | ||||||||
через 54 часа через 54 часа | 3 | 12,8 | 17,1 | 17,9 | 20,5 | |
Прочность на сжатие, испытанная на высушенных и стабилизированных образцах влаги, увеличивается с увеличением содержания гипса, а также прочности на разрыв гипса. . Это увеличение является значительным, когда содержание гипса превышает 2% от сухого веса.
Не наблюдалось значительного влияния добавления сульфата на максимальное водопоглощение образцов AAC через 72 часа, хотя все образцы, содержащие гипс, имеют более низкое поглощение по сравнению с эталонным бетоном.
Эффект от добавления гипса проявляется в случае абсорбции через 10, 30 и 90 минут и капиллярного подъема. На рисунке 2 показаны экспериментальные результаты скорости поглощения w * (выраженной как совокупная поглощенная масса на единицу площади притока по сравнению с t 0,5 ). В течение 90 минут была протестирована только первая стадия водопоглощения — ранняя стадия, на которой скорость поглощения w * линейна в t 0,5 . Очевидно, что даже небольшое количество добавленного гипса снижает сорбционную способность ААЦ.Кривая, построенная для контрольных образцов, более крутая, а общее увеличение массы почти в два раза выше, чем для образцов с содержанием сульфата более 2% от сухой массы.
Рисунок 2
Капиллярное водопоглощение образцов AAC (кумулятивное поглощение w * по сравнению с t 0,5 ) в зависимости от содержания гипса
Существует сильная зависимость между капиллярным подъемом и дозировкой гипса (Рисунок 3). Как и в случае с механическими свойствами, эффект более значительный, когда гипс дозируется более 2% от сухой массы.Подъем капилляров после 72-часового теста снизился примерно на 40% по сравнению с контрольными образцами.
Рис. 3
Капиллярный подъем образцов AAC в зависимости от содержания гипса
Однако было замечено, что скорость высыхания от остатков влаги после производственного процесса бетонов, содержащих гидратированный сульфат кальция, была медленнее по сравнению с контрольными образцами (Рис. 4). Содержание влаги в образцах, содержащих 3,5% гипса, было примерно в два раза выше, чем в контрольном бетоне после 264 часов сушки при 22 ± 1 ° C.
Рисунок 4
Влияние дозировки гипса на процесс сушки AAC при 22 ° C от влажности, возникающей в процессе производства, до стабилизированного содержания влаги
Содержание влаги в образцах с 3,5% гипса было более чем на 60% выше чем в контрольной серии (20,5 против 12,3%) после 54 часов сушки в печи от максимального водопоглощения, хотя начальная точка была ниже (60,1 против 64,0%).
Известно, что кристалличность тоберморита в значительной степени влияет на физические свойства AAC.Различия в микроструктуре испытанных образцов ААС, приводящие к различным характеристикам, обусловлены составом связующего. Очевидно, добавление дигидрата сульфата кальция привело к изменению микроструктуры материала.
5 Выводы
AAC, который был предметом данного исследования, был произведен в промышленных масштабах, что минимизировало возможные ошибки в процессе дозирования, смешивания компонентов или гидротермальной обработки. Весь процесс контролировался автоматически.Изменяя состав вяжущих для бетона, мы можем изменять свойства ячеистого бетона и, следовательно, свойства элементов кладки, предназначенных для строительства перегородок.
Образцы AAC, в которых содержание дигидрата сульфата кальция превышает 2% от сухой массы, по сравнению с образцами без гипса имели:
- —
прочность на сжатие выше примерно на 40% в сухом состоянии и на 60% выше при стабилизированной влажности;
- —
прочность на разрыв выше примерно на 40%,
- —
- —
капиллярный подъем ниже примерно на 40%.
Однако было замечено, что когда содержание гипса было выше 2% от сухой массы, сушка от остатка влаги после производственного процесса происходила медленнее, и через 264 часа содержание влаги все еще оставалось выше 4%. Сульфат кальция влияет на процесс кристаллизации тобермита и фазы C-S-H, что подтверждается результатами испытаний на прочность. В результате образцы AAC3 и AAC4 характеризуются другой структурой пористости по сравнению с эталонным бетоном.
Исследование частично поддерживалось проектами № S / WBiIS / 1/2016, а финансовую поддержку — Министерством науки и высшего образования Польши.
Ссылки
[1] Zapotoczna-Sytek G., AAC летучей золы в стратегии устойчивого развития, Цемент-Известь-Бетон, 2006, 3, 193-201 Искать в Google Scholar
[2] PN-EN 771-4 Спецификация блоков для каменной кладки — Часть 4: Каменные блоки из автоклавного газобетона Поиск в Google Scholar
[3] Scheffler G.А., Плагге Р., Методы определения влагозапасных и транспортных свойств автоклавного газобетона. Цемент-известь-бетон, специальный выпуск, 2011 г., 70-77. Поиск в Google Scholar
[4] Унчик С., Стругарова А., Хлавинкова М., Сабова А., Балкович С., Влияние объемной плотности и влажности на свойства газобетона в автоклаве, Цемент-Известь-Бетон, 2013, 4, 189-196 Искать в Google Scholar
[5] Лоран Дж. П., Геррешали К., Влияние влажности и температуры на теплопроводность автоклавного бетона. газобетон, матер.Struct., 1995, 28, 464–72 Искать в Google Scholar
[6] Джерман М., Кепперт М., Выборный Дж., Черны Р., Гигрические, термические свойства и долговечность автоклавного газобетона, Констр. Строить. Матем., 2013, 41, 352–359 Искать в Google Scholar
[7] Шох Т., Крефт О., Влияние влаги на теплопроводность AAC, В: Материалы 5-й Международной конференции по креплению автоклавного пенобетона. устойчивое будущее (Быдгощ, Польша), Быдгощ, 2011, 361-369.Искать в Google Scholar
[8] PN EN ISO 10456: 2009 Строительные материалы и изделия — Гигротермические свойства — Табличные расчетные значения и процедуры для определения заявленных и расчетных тепловых значений Искать в Google Scholar
[9] Kurdowski W., Chemia Cementu i betonu, Wydawnictwo SPC и Wydawnictwo Naukowe PWN, 2010 Поиск в Google Scholar
[10] Кикума Дж., Цунашима М., Исикава Т., Мацуно С., Огава А., Мацуи К., In situ time- Решенная дифракция рентгеновских лучей процесса синтеза тоберморита в гидротермальных условиях, Матем.Sci. Eng., 2011, 18 (2), 022017, 10.1088 / 1757-899X / 18/2/022017 Искать в Google Scholar
[11] Кикума Дж., Цунасима М., Исикава Т., Мацуно С., Огава А. ., Мацуи К. и др., In situ Дифракция рентгеновских лучей с временным разрешением процесса образования тоберморита в условиях автоклава, J. Am. Ceram. Soc., 2010, 93 (9), 2667–2674. Поиск в Google Scholar
[12] Мацуи К., Огава А., Кикума Дж., Цунашима М., Исикава Т., Мацуно С., Влияние добавления соединения Al и гипс на образовании тоберморита в автоклавном ячеистом бетоне, изученном с помощью in situ рентгеновской дифракции, В: 5-я Международная конференция по автоклавному газобетону, обеспечивающая устойчивое будущее (Быдгощ, Польша), Быдгощ, 2011, 147-154 Поиск в Google Scholar
[13] Хеланова Е., Дрочитка Р. Черный В. Влияние гипсовой добавки на образование тоберморита в автоклавном ячеистом бетоне // Ключевые слова. Матем., 2016, 714, 116-121 Искать в Google Scholar
[14] Штумм А., Автоклавный газобетон без цемента и сульфатов, Цемент-известь-бетон, специальный выпуск 2011 г., 26-28 Искать в Google Scholar
[ 15] PN-EN 772-13: 2001 Методы испытаний каменных блоков. Часть 13: Определение чистой и брутто сухой плотности каменной кладки (кроме природного камня). Искать в Google Scholar
[16] PN-EN 772-1: 2011 Методы испытаний формовых блоков.Часть 7: Определение прочности на сжатие. Искать в Google Scholar
[17] PN-B-06258: 1989 Автоклавный газобетон. Искать в Google Scholar
[18] PN-EN 772-10: 2000 Методы испытаний каменных блоков. Часть 10: Определение влажности силиката кальция и блоков из автоклавного ячеистого бетона. Искать в Google Scholar
[19] PN-EN 772-11: 2011 Методы испытаний каменных блоков. Часть 11: Определение водопоглощения заполнителя бетона, автоклавного газобетона, искусственного камня и блоков каменной кладки из натурального камня за счет капиллярного действия и начальной скорости водопоглощения блоков глиняной кладки.Искать в Google Scholar
Получено: 2017-6-8
Принято: 2017-7-5
Опубликовано в Интернете: 2017-11-4
© 2017 D.Małaszkiewicz and J. Chojnowski
Это произведение находится под лицензией Creative Commons Attribution-NonCommercial-NoDerivatives 4.0 License.
Что это такое и в чем его преимущества.
Ячеистый бетон — один из наиболее широко используемых материалов в строительстве. Это связано с его универсальностью, так как его можно использовать в бесчисленных секторах.
Хотя это может быть визуально непривлекательным, его легко облицовывать многими материалами.
В этой статье мы собираемся немного больше узнать об одном из элементов в составе специальных бетонов .
Что такое ячеистый бетон?
Ячеистый бетон — белый материал, используемый в строительстве. Он получается из смеси воды, известняка, кварцевого песка и цемента, в которую добавлен вспенивающий агент на заключительной фазе смешивания .Он вступает в реакцию со смесью, образуя пузырьки воздуха внутри теста.
Он был изобретен и запатентован J.A. Эрикссон в 1924 году. Эрикссон был шведским архитектором, который искал материал, который обладал бы теми же конструктивными преимуществами, что и дерево (обрабатываемость, прочность и изоляция), и устранял бы его неудобства (необходимость в уходе, хрупкость и воспламеняемость).
В начале 60-х годов, как следствие роста в строительном секторе, возникла необходимость получить продукт для использования в потолках и перекрытиях, который был бы легким и действовал как теплоизолятор.
Ячеистый или пенобетон | Источник: es.wikipedia.org«В некоторых европейских странах, таких как Германия или Австрия, цементный раствор начали производить путем добавления пены. Это можно считать началом ячеистого бетона ».
С тех пор он был улучшен, и его использование стало широко распространенным во всем мире.
Сейчас это один из наиболее часто используемых материалов в мире, особенно в Европе. Его используют при строительстве тысяч домов.
Также известный как пенобетон , он изготавливается в виде бетонных блоков или панелей.
Преимущества ячеистого бетона
Ячеистый бетон обладает прекрасными физическими качествами, сочетающими изоляцию и сопротивление . Он имеет множество преимуществ, которые сделали его одной из лучших альтернатив в строительных материалах.
Это некоторые из преимуществ, которые он предлагает .
Быстрая сборка
Малая плотность и легкость позволяют увеличить скорость монтажа. С ним также легко работать, потому что это несложный для резки материал.
Прочность на сжатие
Она варьируется в зависимости от плотности материала. Очевидно, что его сопротивление будет тем выше, чем выше его плотность. С его помощью можно даже строить многоуровневые коллективные дома.
Источник: bigmatverger.comУстойчив к водопоглощению
Этот тип бетона имеет структуру, которая намного медленнее поглощает воду. Он действует как регулятор влажности, поглощая лишнюю влажность или смягчая сухой воздух. Таким образом создается приятная атмосфера в доме.
Теплоизоляция
Как мы упоминали ранее, она поддерживает приятную прохладу в помещении как зимой, так и летом.
Таким образом, в холодное время года внутри будет тепло, а летом — прохладно. Это приводит к значительной экономии затрат на кондиционирование и отопление.
Экономичный
Ячеистый бетон весит от 10% до 87% меньше, чем обычный бетон . Такое резкое снижение веса дает значительную экономию при строительстве фундаментов и конструкций.
Ячеистый бетон идеален для строительства домов | Источник: efinco.wordpress.comТранспорт
Это легкий материал, который весит вдвое меньше аналогичных материалов. Это позволяет значительно упростить транспортировку, а также работу с ней (резка, прибивание гвоздей, пиление и т. Д.).
Долговечность
Ячеистый бетон, который очень хорошо стареет с течением времени. Он прочен, как камень, и не разлагается.
Акустическое поглощение
Только очень небольшая часть поглощается бетоном, большая часть отскакивает обратно к месту происхождения.Шум, который действительно достигает внутреннего пространства, минимален.
Универсальность
Это очень универсальный материал, когда дело касается форм и форм. Из него можно легко изготовить что угодно: арки, пирамиды, углы и т. Д. Таким образом, он увеличивает эстетический эффект здания.
Огнестойкость
Благодаря низкой теплопроводности, обладает очень низким тепловым потоком ячеистого бетона. Это идеальный материал для использования в промышленных, сельскохозяйственных или административных зданиях.
Уменьшение дедвейта
Это важно в районах с высоким сейсмическим риском . Если произойдет землетрясение, сломанные стены упадут, но они не нанесут такого большого ущерба, как другие традиционные материалы.
Когда использовать ячеистый бетон?
Ячеистый бетон рекомендуется использовать в:
- 1. Холодный климат : Идеально подходит для мест, подверженных воздействию низких температур, где требуются теплоизоляционные материалы для предотвращения выхода тепла из здания.
- 2. Горячий климат : Он также предотвращает попадание тепла в здание.
- Умеренный климат или экстремальные условия , такие как зима или лето.
Элементы, изготовленные из ячеистого бетона
Вот некоторые из продуктов, которые производятся из ячеистого бетона :
- Плиты крыши
- Плиты
- Перемычки
- Перегородки
- Строительные блоки
- Террасы
- Засыпки
- Плиты основания для мощения
- Связующие
Также широко используется в качестве наполнителя между кирпичными стенами, как теплоизоляционный материал для крыш или полов, как акустический изолятор или как жесткий пол, например как теннисные корты.
Блоки из ячеистого бетона | Источник: albaniles.orgТипы ячеистого бетона
Сильфон объяснит некоторые из различных типов ячеистого бетона.
Чистый ячеистый бетон
Используются портландцемент, вода и подготовленная пена или газ. Не имеет твердых агрегатов. При производстве сначала смешивают воду и цемент, а затем добавляют химический агент или пену, которые необходимо правильно перемешать для достижения ячеистой консистенции.
Шлифованный ячеистый бетон
Содержит цемент, воду, выбранный пенящийся заполнитель и песок с максимальным диаметром 4 мм.
Бетон на легком заполнителе
Состоит из пемзы, тезонтла и т. Д., Который заменяет песок. Эти агрегаты должны быть очень прочными, чтобы повышать сопротивление сжатию.
В зависимости от композиционных материалов мы можем выделить различные типы ячеистого бетона | Источник: fi.pinterest.comЯчеистый бетон с расширяющимися заполнителями
Было показано, что добавление этих заполнителей помогает удерживать воду при отверждении бетона в жарком климате.
Это также элемент защиты металлических конструкций от огня.
Ячеистый бетон с диспергирующими добавками
Диспергирующее действие добавок способствует гидратации частиц цемента, улучшает сопротивление сжатию и увеличивает текучесть как следствие уменьшения отношения цемент / вода в смеси.
Производство ячеистого бетона
Наиболее важными этапами производства ячеистого бетона являются следующие:
- Сбор, подготовка, дозирование и смешивание сырья: воды, цемента, извести и песка.Соответствующие пропорции: 500 г оксида алюминия, 15 кг гипса, 40 кг извести и 90 кг цемента на каждые 200 кг песка.
- Подготовка форм.
- Режущие блоки или блоки особой геометрии.
- Отверждение бетона.
- Паллетирование и упаковка.
По крайней мере, 90% сокращенных отходов производства можно использовать повторно. Производство ячеистого бетона требует мало энергии, а воду также можно использовать повторно.
Выводы
Можно сказать, что использование ячеистого бетона ограничено человеческим воображением. Это такой универсальный материал, который позволяет создавать всевозможные элементы любой формы и размера.
«У него так много преимуществ, что производство этого материала стало новой и очень привлекательной альтернативой для любых предпринимателей в строительном секторе».
Исследования по его использованию в строительстве жилья показывают впечатляющие результаты.Он не горит, не гниет и противостоит термитам.
Дома из ячеистых бетонных блоков | Источник: projectpragmalia.blogspot.comЭтот бетон обладает особенностью дышать. То есть он пропускает водяной пар, выделяемый жильцами дома или повседневными задачами, такими как приготовление пищи. Это важно, чтобы избежать повреждений, вызванных конденсацией и влагой, например плесенью.