Бетон всех марок. Производитель бетона Бетон Строй
Бетон применяется во время строительства большинства зданий и сооружения. Подобные смеси — это один из самых дешевых материалов для строительства, которые отличаются высокими прочностными показателями, устойчивостью к температурным перепадам, способные выдержать большие нагрузки не только на земле, но и под ней и даже в водной среде. Производство и доставка бетона осуществляется в вязком состоянии, а итоговую форму изделиями из бетона производят строители непосредственно на стройплощадке. Подобные свойства дают возможность строителям и архитекторам применять бетон для создания инновационных форм и решений.
На основе смеси из бетона можно изготовить каркас строения, элементы сборных конструкций, фундамент, стены, пролеты ступеней, плиты и перекрытия, дорожные покрытия и мостовые сооружения. Марки бетона с указанием параметров прочности, поглощения воды и устойчивости к низким температурам четко указаны в ГОСТ
Состав бетонных смесей
В составе бетона имеется цемент, песок мелких фракций, наполняющий материал и вода. Наполняющие материалы — это, известный всем, щебень, разновидности доменных шлаков повышенной твердости, пористые составы, перлит, керамзит. Песок может использоваться самый разнообразный это зависит от особенностей состава – заводского производства, шамотный, карьерный и речной песок. Если используется стеклобетон, то в качестве добавки применяется жидкое стекло. Для усиления свойств бетонной смеси применяются пластификаторы и гидрофобизаторы.
Составов бетона достаточно много среди них есть такие как — облегченный, пористый, конструкционный – вид его подбирается индивидуально это зависит от особенностей применения. К бетонным смесям также относятся песко-цементные смеси, смеси для кладки и отделки швов, растворы для штукатурки.
Виды смесей бетона и специфика их применения
Технология смешивания, а также особенности состава бетонных растворов можно найти в соответствующих ГОСТах. Марка бетона подбирается отталкиваясь от используемого состава и физико-механических параметров. Маркируется бетон цифрами и буквами от В3.5 до В30.
Существующие марки бетона:
В3.5-В10 — тощий бетон, который применяется для фундаментных блоков;
В10-В12.5 — используется при строительстве дорог и городских постройках;
В15-В25 — это основа для строительства стен, фундаментов и перегородок;
В22.5 и более высокие находят применение для строительства особо ответственных конструкций;
Характеристики смеси бетона
Любая марка бетона имеет свои технические параметры, к которым относятся:
- Плотность;
- Прочность на сжатие;
- Прочность на изгиб;
- Теплопроводность;
- Устойчивость к низким температурам;
- Процент водопоглощения;
Эти характеристики устанавливаются экспериментальным путем в специальных лабораториях заводов-производителей.
Как контролируется качество бетона
Каждая бетонная смесь имеет свой паспорт, который составляется в процессе производства. Согласно действующих СНиП при строительстве особо ответственных запрещено применение смесей без соответствующей документации, которая подтверждается результатами испытаний и печатями завода-производителя. Наличие таких документов является обязательным для того, чтобы объект строительства был сдан соответствующей комиссии.
Паспорт бетонной смеси содержит данные о производителе, дата и время, когда бетон замешан отправляется с завода, печати производителя. В таблицах с параметрами смеси указываются параметры, описанные выше.
Как выбрать необходимую бетонную смесь
Компанией «Бетон Строй» производится реализация смесей на основе бетона и цемента по приемлемым ценам, с возможностью расчета необходимого количества и квалифицированными консультациями. Для того чтобы доставить бетон в минимальные сроки, специалистами компании подбирается ближайший филиал компании.
Состав бетона для отмостки дома
Выбираем бетон для фундамента
Марочная прочность материала, используемого для заливки основания, определяется параметрами нагрузки, глубиной залегания грунтовых вод, архитектурными особенностями строения.
Специалисты приводят некоторые рекомендации СНиП:
- при проведении работ на слабопучинистых грунтах и обустройстве мелкозаглубленного или среднезаглубленного фундамента допустимо использование
железобетона М150, но в том случае, если планируется строительство лёгких деревянных и каркасных строений; - марки М200/М250 целесообразно применять при заливке буронабивных свай, заглубленных ленточных фундаментов, плитных подошв или оснований под столбы с пучинистым характером грунтов.
Такое основание способно выдержать блочный или кирпичный дом;
- марки М300/М400 – необходимы для возведения заглубленных лент, свайных буронабивных конструкций. Материал используется, если предполагается возведение многоэтажного загородного дома из кирпича, железобетона или цементных блоков.
Например, бетон М300, пропорции которого составляют 1.00/1.90/3.70, требует использования цемента марки М400. Объём воды зависит от характеристик песка. Для отмостки подойдёт меньшая марочная прочность – М200
Состав, пропорции
Состав любой бетонной смеси является стандартным – это цемент, песок, щебень (гравий), либо ПГС и вода. Пропорциональное соотношение компонентов в зависимости от марки материала указано в табличных данных.
Железобетон, марка М | Пропорции компонентов, Ц/П/Щ |
100 | 1.00/4.60/7.00 |
150 | 1.00/3.50/5.70 |
200 | 1.![]() |
250 | 1.00/2.10/3.90 |
300 | 1.00/1.90/3.70 |
400 | 1.00/1.20/2.70 |
450 | 1.00/1.10/2.50 |
Базовым параметром, характеризующим качество смеси, является прочность на сжатие. Это помогает отнести рабочий раствор к определенной категории. Правильный подбор материала, необходимого для обустройства конструктивного элемента, позволяет получить оптимальные характеристики готового покрытия, подходящие к реальным условиям эксплуатации.
Состав для отмостки
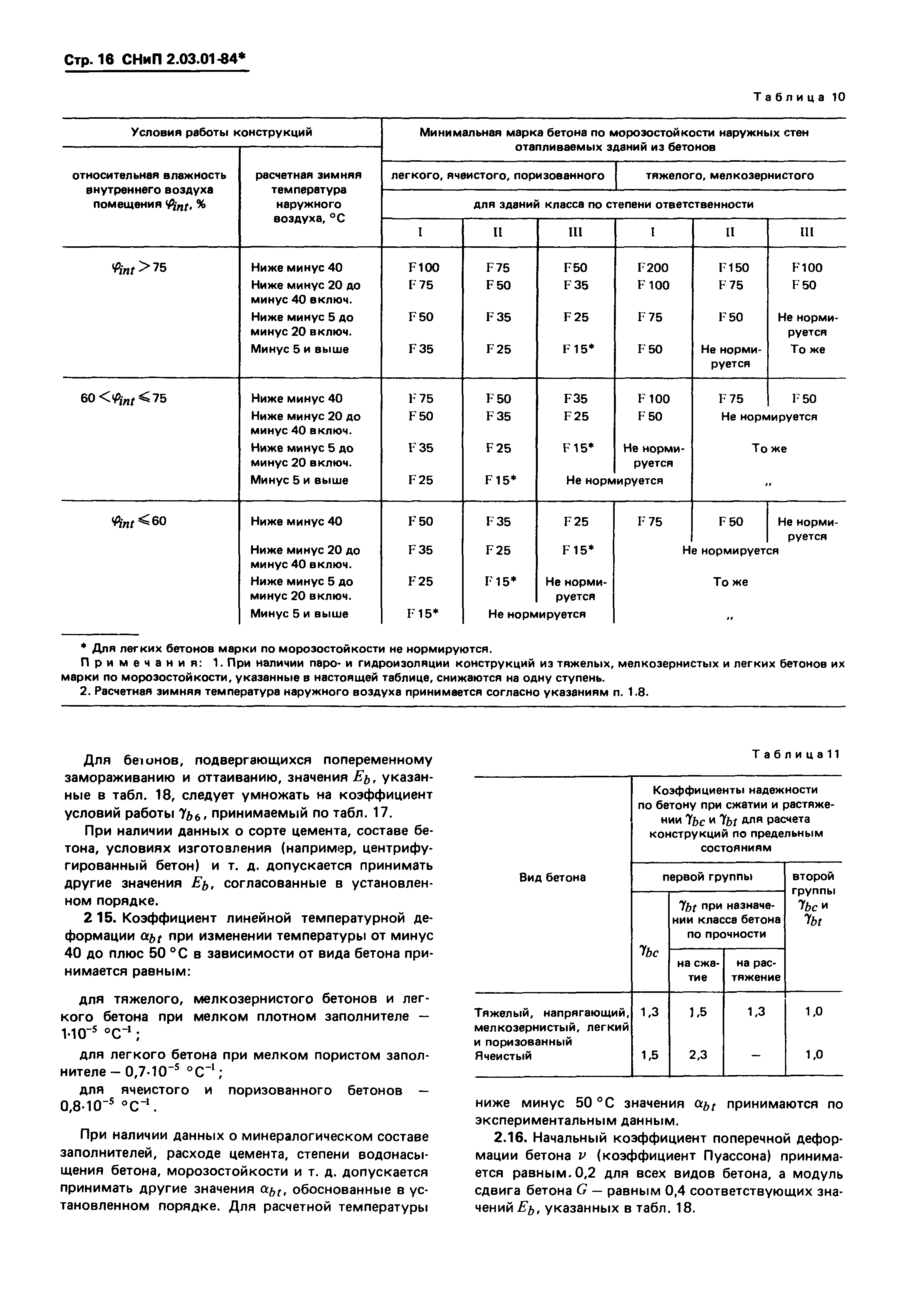
Подбираем состав бетона для отмостки своими руками:
- цемент М400 — 287 кг;
- щебень гранитный фракции 5-20 мм – 1135 кг;
- ПГС – 751 кг;
- вода очищенная – 185 л.
- цемент М400 – 287 кг;
- песок – 803.6 кг;
- щебень – 1377.6 кг;
- вода – 186 л.
Последовательность действий:
- в бетономешалку наливают воду;
- вводят цемент;
- ингредиенты смешиваются до образования цементного молока;
- вводится щебень;
- вводится песок.
Если при замесе используется крупнозернистый щебень содержание жидкости можно уменьшить, тогда марка бетона для отмостки частного дома не уменьшится
Пропорции бетона под отмостку соответствуют действующим нормам и правилам.
Функции конструктивного элемента
Назначение конструктивного элемента раскрывается следующим образом
- декоративные свойства, создание архитектурной завершенности;
- защита основания от любой влаги, водоотведение;
- уменьшение уровня промерзания грунтов, теплосбережение.
- защита основания от повреждений корневой системой растений.
Требования к производству работ
Определив, какая марка бетона нужна для отмостки, следует ознакомиться с тем, какие требования предъявляются к ее обустройству:
- ширина полосы рассчитывается так – выступ карниза (см) + 20 см;
- полоса покрытия должна составлять непрерывный слой;
- должен быть предусмотрен небольшой уклон от стены.
Марка по СНиП
Современные норма и правила, действующие в строительстве, рекомендуют придерживаться всех пропорций ингредиентов, используя указанную марку цемента, иначе слабый бетон не сможет обеспечить полную защиту основания.
Все ингредиенты, необходимые для получения смеси марки М200 должны быть высококачественными и чистыми, лишенными примесей и посторонних включений.
В завершение стоит отметить, что строительство проводится при температурах не ниже -5°С. Если необходимо провести все работы в более холодный период года, обязателен прогрев рабочего раствора.
Стоимость
Средняя цена за 1 м³ материала марки М200 составляет 2400 р. Окончательные издержки зависят от площади дома, ширины полосы, привлечения услуг команды профессиональных строителей.
Как делается отмостка и состав бетона для отмостки своими руками показано в видео:
Книги по теме:
Норма расхода бетона для различных сооружений и конструкций. Справочная информация
Бетон, стоимость которого напрямую зависит от его состава, в свою очередь определяющего характеристики изделий из него, ввиду значительных объемов применения на строительных площадках и промышленных производства зачастую требует от покупателя внушительных расходов на свое приобретение. Чтобы не переплачивать за лишние объемы или испытывать дефицит в этом стройматериале в ходе производственного процесса, заказчику необходимо правильно рассчитать свои потребности в бетоне и осуществлять многоэтапный контроль за его расходом. Для этого и существуют норма расхода бетона.
Норма расхода бетона: что это такое
Для учета расхода бетонной смеси в ходе работ существуют особая нормативная документация, включающая СНиП 5.01.23-83, СНиП 4.02-91, СНиП 4.05-91, а также сборником 2007 года, выпущенном Минстроем РФ.
Норма расхода бетона, определяемые документами:
- содержат обязательный и при этом единый для всех субъектов хозяйствования порядок расчета расходов бетона;
- отражают максимальный объем бетона, который можно использовать для создания единицы продукции или осуществления работы при данном уровне технической вооруженности и используемых технологиях изготовления. При этом учитывается потери бетона, технологические отходы и его полезный расход.
Норма бетона не учитывают потери и отходы, возникающие при отступления от стандартов, технических условий и утвержденных технологических процессов при выполнении конкретных работ или выпуске продукции.
Очевидно, что различные виды работ требуют различных норм расхода бетона. Для каждой из них установлено, бетон в каком объеме может максимально использоваться для производства единицы продукции или выполнения работы. Для каждой из этих работ присвоен собственный функциональный ход, составлено описание и определен измеритель.
Соответственно, норма расхода бетона представляют собой регламентированную меру его затрат, основанную на передовых производственных технологиях. Норма расхода бетонов для сооружений и конструкций конкретного типа (панельных перегородок, стеновых панелей, колонн с заданными сечениями, бетонных оснований) прилагаются к действующим строительным нормативам в виде специальных таблиц. Данные этих показатели могут служить определенным ориентиром для возможных усовершенствований технологий, оборудования, методов работы и спектра выпускаемой продукции.
Если Вам в Нижегородской области для любых строительных нужд необходим бетон, цена которого будет выгодно отличаться от предложений конкурентов, «Первый Бетонный Завод» ждет Ваших заявок. Мы предлагаем широкий спектр марок бетона, которые в полной мере соответствуют требованиям покупателя, на самых выгодных условиях с возможностью доставки непосредственно на строительный объект в удобное для заказчика время.
Более подробную консультацию по характеристикам бетона и способах его оптимального применения вы можете получить, позвонив нашему специалисту по тел.: 8 953 415-95-41. Для вашего объекта будет подобрана оптимальная смесь бетона, доставка до места в Нижнем Новгороде и области, способ заливки.
Качество бетона и стандартизация правил контроля его прочности
С.А. ПОДМАЗОВА, канд. техн. наук; Н.Н. КУПРИЯНОВ, канд. техн. наук; Б.А. КРЫЛОВ, доктор техн. наук; А.И. САГАЙДАК, канд. техн. наук Научно-исследовательский, проектно-конструкторский и технологический институт бетона и железобетона (НИИЖБ).
Рассматривается фактор комплексного подхода к изготовлению бетона. Только при соблюдении всех составляющих процесса, начиная с процедур контроля прочности бетона и заканчивая соблюдением правил ухода за ним в готовой конструкции, можно рассчитывать на обеспечение надлежащего качества железобетонных изделий.
В течение последних 10–15 лет в Москве и других регионах России бурно развивается монолитное строительство. Проверка поставляемых на строительный объекты бетонных смесей, контроль прочности бетона в монолитных конструкциях, анализ имеющихся дефектов в них указывают на серьезные проблемы с обеспечением качества в монолитном строительстве. Нередко строительным организациям приходится тратить время и средства на усиление и/или ремонт возведенных конструкций.
Для строительства жилых, общественных зданий и объектов транспортной инфраструктуры из монолитного бетона изготавливаются и поставляются на строительные площадки готовые бетонные смеси. По оценке специалистов, ежегодный объем таких поставок в масштабе страны составляет порядка 40 млн м3.
В строительной практике бетонные смеси, в зависимости от требований проекта или условий договора, поставляются с заданной проектной прочностью (обычно назначаемой как класс бетона по прочности на сжатие) и дополнительно, в зависимости от назначения объекта, заданной маркой бетона по водонепроницаемости и маркой по морозостойкости. Все эти показатели должны контролироваться согласно процедурам, указанным в соответствующих стандартах.
В настоящей статье речь будет идти о влиянии систем контроля прочности на качество бетона монолитных и сборных железобетонных конструкций.
Соответствующая идеология контроля прочности, как и любого другого показателя качества, направлена на обеспечение стабильности заданного показателя в рамках допустимого статистического разброса. Так, показатель прочности бетона должен соответствовать средней прочности для заданного класса бетона.
В период централизованного управления экономикой одним из концептуальных требований государственной политики в области строительства была экономия материалов. Практически все научные результаты в строительных НИИ, включая диссертационные работы, должны были заканчиваться показателями достигаемой экономии при применении этого результата на практике — «внедрении», как тогда было принято говорить.
Одним из важнейших фондируемых, т. е. распределяемых централизованно, материалов был цемент. Экономия цемента была одной из главных целей при разработке новых и пересмотре старых стандартов. Поскольку прочность бетона зависит, главным образом, от водоцементного отношения и зависимого от этого показателя расхода цемента на единицу объема, то одной из задач стандартизации была разработка процедур, которые вели бы к снижению расхода цемента. Иными словами, стандарт должен был разрешать легально снижение прочности бетона в конструкции. А иногда не просто разрешать, но и обязывать снизить прочность бетона. Этого подхода не избежали и СНиП «Типовые нормы расхода цемента» и, естественно, стандарты, определяющие правила контроля прочности.
Во всех строительных нормах, вплоть до ГОСТ 26633, регламентировалась минимальная типовая норма расхода цемента, например для армированных железобетонных изделий — 220 кг/м3в нормальных условиях.
Следующий и действующий в настоящее время СНиП 82-02-95 «Федеральные (типовые) элементные нормы расхода цемента при изготовлении бетонных и железобетонных конструкций» был разработан с позиции упрощения назначения теоретического расхода цемента на 1 м³ бетона. Нормы расхода цемента были разработаны из условия приготовления бетонов на портландцементе марки 400 и его разновидностей с определёнными фракцией щебня и модулем крупности песка. При применении других составляющих бетонной смеси следует пользоваться различными поправочными коэффициентами.
Применение химических добавок рекомендуется этим СНиП не для всех бетонов, а только для бетонов, к которым предъявляются требования по морозостойкости и водонепроницаемости. Ограничения по минимальным классам бетона по прочности на сжатие для обеспечения морозостойкости и водонепроницаемости в этом документе отсутствуют. Однако следует отметить, что отсутствие требований по назначению минимальной прочности бетонов, эксплуатирующихся в средах с агрессивным воздействием на конструкции, например дорожные и гидротехнические сооружения (ГОСТ 26633 «Бетоны тяжёлые и мелкозернистые. Технические условия»), частично компенсировались требованиями по обязательному воздухововлечению и ограничению максимального значения водоцементного отношения.
Сравнивая нормы расхода цемента, можно сказать, что за 30 лет рекомендуемые расходы цемента снизились в среднем на 1 7–20% для бетонов всех классов по прочности, морозостойкости и водонепроницаемости при фактически таком же качестве самого цемента.
Стандарт «Бетоны. Правила контроля прочности» насчитывает уже несколько десятилетий своей истории. Так, разработанный в 1972 г. стандарт устанавливал методы контроля прочности и однородности на заводах по производству готовых бетонных смесей и комбинатах по изготовлению сборных железобетонных конструкций. В этом документе указывалось, что контроль и оценка прочности и однородности бетона должны быть направлены на достижение постоянства показателей, принятых для данной марки бетона.
Оценка прочности бетона должна выполняться сопоставлением фактической средней прочности контрольных образцов бетона в партии с требуемой средней прочностью. Прочность бетона в партии признается отвечающей требуемой, если фактическая средняя прочность бетона в партии не менее требуемой средней партионной прочности. Требуемая прочность бетона определялась как величина, устанавливаемая лабораторией БСУ в процентах от нормируемой прочности с учетом фактической однородности бетона.
В ГОСТе 1980 г. в разделе «Правила приемки бетона по прочности» был сохранен такой же подход к контролю прочности бетона. Но при высокой однородности показателей прочности бетона уже требовалось назначать более низкую прочность, которая была равна или несколько выше требуемой прочности. Например, если за анализируемый предшествующий период на заводе был получен коэффициент вариации прочности Vn=7%, то было достаточно при проектной марке бетона М400, выпускаемой в данный момент (контролируемый период), обеспечить прочность, равную 340 кгс/см2.
В 1980-х годах нормирование бетона по прочности перешло от марок к классам.
В редакции ГОСТ 18105 1986 г. уже указаны классы бетона по прочности и принято, что показатели, которые близки к значению класса, считаются принадлежащими к этому классу. Так, марка бетона М400 примерно соответствует классу бетона В30 (средняя прочность класса 393 кгс/см2 при Vn=13,5%).
В соответствии с требованиями ГОСТ 18105–86, при получении коэффициента вариации прочности за анализируемый (т. е. предшествующий) период производства бетона, например 7%, требуемая средняя прочность класса бетона ВЗО в контролируемый (т. е. текущий) период должна быть равна 32,4 МПа.
Для того чтобы в следующий контролируемый период выпускать бетон с пониженной требуемой прочностью 32,4 МПа, следует разработать состав бетона с обеспечением среднего уровня его прочности, который должен быть выше требуемой всего на 4%. При этом результат по прочности подобранного состава бетона станет известен разработчику лишь через 28 суток.
Указанные 4% — это разрешённая поправка на предполагаемый разброс прочности бетона в серии и/или на возможную ошибку при дозировании составляющих бетонной смеси. Иными словами, стандарт разрешал разрабатывать составы бетона практически на минимально допустимое значение прочности.
Требуемая прочность, согласно этому стандарту, равна минимально допустимому значению фактической прочности бетона в партии, которая вычисляется на основании показателей однородности, полученных на предыдущем этапе процесса производства. Чем выше однородность показателей прочности бетона, тем ближе может быть средняя фактическая (т. е. требуемая) прочность к значению класса. И с такими значениями прочности поставку бетона на объекты строительства стандарт разрешает.
В 2008 г. была подготовлена новая редакция стандарта ГОСТ 18105, где требования к назначению фактической прочности класса не изменились.
Как может влиять на качество бетона монолитных конструкций разрешаемое прежним и только что утверждённым стандартом «вылизывание» всех возможных прочностных запасов бетона на стадии его приготовления? Основное положение ГОСТ 1972 г. говорит о том, что контроль и оценка однородности с применением статистических методов необходимы для достижения постоянства производственного процесса и принятых при расчете величин нормативных сопротивлений. В редакции ГОСТа 2008 г. о постоянстве производственного процесса уже не упоминается, основная цель — обеспечить значения заданного класса бетона по прочности. Например, класс бетона по прочности ВЗО, в зависимости от величины коэффициента вариации, полученного в предшествующий период производства, может быть обеспечен в диапазонах изменения прочности от 32,1 МПа до 42,9 МПа. Оба эти показателя прочности соответствуют значению класса бетона по прочности на сжатие ВЗО, только первый при коэффициенте вариации 7%, второй — 16%.
На предприятии с недостаточно налаженной технологией производства всегда присутствует соблазн указать пониженный коэффициент вариации по результатам заводского контроля прочности, с тем, чтобы подогнать полученную прочность под необходимый класс, согласно требованию заказчика на поставку бетона, при его пониженной фактической и средней прочности. Различные бетоносмесительные узлы могут поставлять на один и тот же объект бетонную смесь, спроектированную на получение прочности в готовой конструкции от 32,1 до 42,9 МПа, и этот бетон будет одного и того же класса по прочности.
Иными словами, при поставке бетонной смеси от нескольких заводов-изготовителей на объект (а это широко распространённая ситуация), величина средней прочности бетона одного и того же класса может существенно различаться. Укладка бетона одного заказанного класса, но с различной средней прочностью приведёт к увеличению разброса прочности бетона в готовой конструкции. Может даже получиться, что проектный класс бетона будет не обеспечен. В реальной практике ощутимые разбросы по прочности в пределах готовой конструкции являются массовым явлением.
Представим, что на объект поставили бетон с одинаковой заводской прочностью 31,2 МПа, что соответствует классу ВЗО при коэффициенте вариации 7%. Бетон уложен в опалубку, укрыт, выдержан в соответствии с правилами производства работ и через 28 суток, будучи проверен не-разрушающими методами, показывает прочность- как раз те самые 31,2 МПа, что были заданы на заводе. Согласно п. 7.4 того же ГОСТ 18105, для того чтобы определить условный класс, эту величину необходимо умножить на 0,8, следовательно, в конструкции условный класс бетона по прочности на сжатие будет равен не ВЗО, а В25, т. е. ниже проектного. Таким образом, минимизация требований по прочности приводит при определённых условиях к необеспечению проектного класса бетона в конструкции.
Выход видится в изменении требований ГОСТ 53231, а именно в том, чтобы изложить требования в стандарте в следующей редакции: состав бетона следует производить с обеспечением средней прочности класса, принятой из предположения, что коэффициент вариации равен 13,5% плюс запас в 10%. Этот подход позволяет быть уверенным в том, что требования к бетону по прочности будут обеспечены после доставки бетонной смеси на стройплощадку. Имеется в виду, что укладка, уплотнение и уход за бетоном в процессе набора прочности даёт дополнительный разброс по прочности бетона в конструкции. Зарубежный опыт монолитного строительства, существующая нормативная база подтверждает целесообразность такого подхода.
Есть ряд бетонно-смесительных узлов, которые уже сегодня выпускают бетон с обеспечением средней прочности класса, исходя из предположения, что коэффициент вариации Vn=13,5%. На объект строительства поставляется бетон с несколько завышенными показателями относительно требуемой прочности, но с большей вероятностью обеспечения проектных характеристик. По этому пути идут БСУ, поставляющие бетон на объекты транспортного строительства. По распоряжению Мостовой инспекции и центральной лаборатории «Мостотреста» номинальный состав бетона разрабатывается на среднюю прочность класса при Vn=13,5% и еще дополнительно 10%. При таком подходе обеспечивается средняя прочность в пределах средней прочности класса при Vn=13,5% и более высокая однородность бетона при всех равных условиях.
Теперь рассмотрим контроль качества бетона сборных конструкций. На ныне действующих предприятиях ЖБИ и ДСК при приемке партии готовых изделий ведется контроль прочности двух видов: при передаче напряжения с упоров форм или стендов на бетон (передаточная прочность) и отпуске продукции потребителю (отпускная прочность). Предприятие при всех условиях должно гарантировать достижение бетоном проектной прочности в возрасте 28 суток.
ГОСТ 1972 г. содержит таблицу 3, где указано, что следует снижать отпускную проектную прочность на 1 5%, если коэффициент вариации не превышает 5%, при испытании одной серии из 6 опытных образцов.
В аналогичном ГОСТе 1980 г. указано, что снижение отпускной или передаточной прочности ниже проектной допустимо, если ведется проверка выполнения технологических требований. В правилах приемки готовой продукции сказано, что если фактическая средняя прочность не ниже требуемой, т. е. если коэффициент вариации в партии равен 5% и ниже, то разрешается, в зависимости от количества испытанных образцов, снижение отпускной и передаточной прочности, соответственно, на 8–18%.
ГОСТ 1986 г. повторяет версию предыдущих стандартов, но дана таблица (приложение 4, справочное), согласно которой в зависимости от нормируемой величины отпускной прочности, от группы цементов по эффективности пропаривания, продолжительности тепловой обработки необходимо назначить отпускную прочность, увеличенную до 45%. В примечании к этой таблице указано, что следует применять следующие технологические приемы: удлинить цикл тепловой обработки, применять добавки-ускорители твердения или применять цементы только I группы эффективности при пропаривании. Все эти предложения практически невыполнимые. И в этом же стандарте, с другой стороны, предлагается при высокой однородности по прочности снижать отпускную или передаточную прочность.
Наконец, в упоминаемом выше ГОСТ 2008 г. «Бетоны. Правила контроля прочности» указаны такие же подходы к назначению отпускной или передаточной прочности. Все эти приёмы, направленные на экономию цемента, ведут к тому, что в конструкции на стадии строительства закладывается пониженный эксплуатационный ресурс. И не случайно обследование и разработка рекомендаций по усилению железобетонных конструкций как монолитных, так и сборных составляют сегодня весомую долю в объеме работ различных проектных и исследовательских организаций.
На основании вышеизложенного для повышения качества бетона конструкций, в первую очередь — показателей качества по прочности, необходимо пересмотреть уровень требований обеспечения прочности как отпускной и передаточной, так и проектной (соответственно классу бетона по прочности).
Анализ методов по определению прочности и назначению рабочего (номинального) состава в зависимости от уровня по лученной однородности по ГОСТ 18105 выпуска 1972, 1980, 1986 и 2008 гг. показывает, что следует разработать другие подходы по назначению рабочего (номинального) состава, а также уровня прочности при назначении отпускной, передаточной и проектной прочности в сборном железобетоне и бетоне, изготовленном из готовых бетонных смесей.
В сборном железобетоне отпускную, передаточную и проектную прочность следует обеспечивать на уровне проектных требований или выше вне зависимости от показателей однородности бетона по прочности, полученной за анализируемый период.
При производстве готовых бетонных смесей (товарного бетона) для монолитных конструкций необходимо в стандарте установить уровень средней прочности и поддерживать ее вне зависимости от показателя однородности бетона по прочности, полученного в анализируемом периоде. Кроме того, следует строго выдерживать правила ухода за бетоном после его укладки.
На заводах сборного железобетона и на бетонно-смесительных узлах контроль прочности с определением однородности бетона по прочности следует проводить с целью оценки стабильности показателей выпускаемой продукции.
Только при комплексном подходе к изготовлению бетона, начиная с процедур контроля его прочности и заканчивая соблюдением правил ухода за бетоном в готовой конструкции, можно рассчитывать на обеспечение надлежащего качества железобетонных конструкций.
Журнал «Технологии бетонов», №5, 2009.
Все публикации
Архив по годам: 2006; 2008; 2013; 2015; 2016; 2018; 2019; 2020; 2021;
MK Diamond — Понимание бетона
Для правильного выбора алмазного диска необходимо знать четыре важных момента о бетоне.
1. Прочность на сжатие
Твердость бетона определяется его прочностью на сжатие, измеряемой в фунтах на квадратный дюйм (PSI). Затвердевшие бетонные плиты сильно различаются по прочности на сжатие; с влажностью, температурой, составом смесей, добавками, вяжущими материалами и процессами отверждения, часто определяющими их измеренный уровень прочности. Чем выше прочность на сжатие, тем тверже материал.
Твердость бетона | фунтов на квадратный дюйм | Типичное применение |
Очень твердый | 8000 или более | Атомные станции |
Жесткий | 6 000 — 8 000 | Мосты, Пирсы |
Средний | 4 000 — 6 000 | Дороги |
Мягкий | 3000 или менее | Тротуары, патио, автостоянки |
2. Возраст бетона
«Возраст» или продолжительность отверждения сильно влияет на то, как алмазный диск взаимодействует с бетоном. Несмотря на то, что существуют методы ускорения процесса отверждения, «состояние» бетона от начальной заливки до периода в 72 часа и более можно определить по трем различным приращениям, и на него влияют температура, погода, влажность, заполнитель, время года, примеси и состав.
Состояние 1 – от 0 до 8 часов
Бетон считается в «зеленом» состоянии от 0 до 8 часов после заливки, что означает, что он схватился, но не полностью затвердел.В сыром бетоне песок в смеси не прочно связан с растворной смесью и вызовет сильное абразивное воздействие, как только начнется физика пиления. Кроме того, шлам, образованный сырым бетоном, в равной степени абразивен и требует специальной защиты от подрезания стального сердечника алмазного диска. Как правило, в этом состоянии выполняется распиловка контрольных стыков автомобильных дорог, промышленных полов, проездов, взлетно-посадочных полос и подобных объектов.
Состояние 2 – от 8 до 24 часов
Бетон считается затвердевшим через 8-24 часа после заливки.Песок удерживается прочно прилипшим к общей смеси. Как правило, регулирующие шарниры, установленные в состоянии 1, в это время расширяются.
Состояние 3 – от 24 до 72
Бетон считается затвердевшим через 24–72 часа после заливки. Песок прочно удерживается в растворной смеси, а общее абразивное действие и свойства бетона значительно уменьшаются. Теперь рассмотрение заполнителей, прочности на сжатие и содержание стали в бетоне становятся важными факторами при выборе правильного алмазного диска.
3. Заполнители и песок
Заполнители представляют собой гранулированные наполнители в цементе, которые могут занимать от 60 до 75% общего объема. Они влияют на характеристики как свежего, так и затвердевшего бетона. Заполнителями могут быть природные минералы, песок и гравий, щебень или искусственный песок. Наиболее желательные заполнители, используемые в бетоне, имеют треугольную или квадратную форму и обладают твердыми, плотными, хорошо гранулированными и прочными свойствами. Средний размер и состав агрегатов сильно влияют на режущие характеристики и выбор алмазного диска.Большие заполнители, как правило, заставляют лезвия резать медленнее; меньшие заполнители позволяют лезвиям резать быстрее.
Сложность | Средний размер агрегата |
Труднее резать (лезвие изнашивается медленнее) | 1-1/2 дюйма или более 1-1/2 дюйма до 3/4 дюйма 3/4 дюйма до 3/8 дюйма |
Легче резать (лезвие изнашивается быстрее) | Мелкий гравий (менее 3/8 дюйма) |
Общая твердость измеряется по шкале Мооса.Эта шкала присваивает произвольные количественные единицы от 1 до 10, по которым определяется твердость минерала при царапании. Каждая единица твердости представлена минералом, который может поцарапать любой другой минерал, имеющий более низкий ранг. Минералы ранжируются от талька или 1 (самый мягкий), вверх через алмаз или 10 (самый твердый). Твердые заполнители сокращают срок службы полотна и снижают скорость резания.
Состав песка является еще одним фактором, определяющим характеристики твердости цемента и абразивные свойства раствора.Обычно в смеси используются три вида песка:
- Речной песок (круглый, неабразивный)
- Песок речного берега (острый абразив)
- Промышленный песок (острый абразив)
Песок речного берега и искусственный песок более абразивны, чем речной песок. Чем абразивнее песок, тем жестче требования к связующей матрице. Более острые, более геометрически очерченные пески также требуют более прочных связей.
Шкала твердости Мооса
4. Стальная арматура
Дальнейшее укрепление и структурная целостность бетона достигается за счет введения в бетон армирующих стальных стержней (арматурных стержней), стальных прядей проволочной сетки. Резка бетона, содержащего арматурную сталь, обходится дороже, потому что скорость резания ниже, а срок службы диска сокращается. Если площадь поперечного сечения бетона составляет 1% стали, срок службы лезвия будет примерно на 25% короче, чем если бы сталь отсутствовала. Бетон с 3% стали может сократить срок службы лезвия на 75%.
Метрический размер (мм) | Диаметр | Имперский размер (дюймы) | Диаметр |
10 | 9,5 | #3 | .![]() |
13 | 12,7 | #4 | .500 |
16 | 15.9 | #5 | .625 |
19 | 19,1 | #6 | .750 |
22 | 22,2 | #7 | .875 |
25 | 25,4 | #8 | 1.![]() |
29 | 28,7 | #9 | 1.128 |
32 | 32,3 | #10 | 1,270 |
Тяжелая арматура: | Арматурный стержень №6 через каждые 12 дюймов в центре или 2 мата из арматурного стержня №4 через каждые 12 дюймов в центре |
Средняя арматура: | Арматурный стержень №4 через каждые 12 дюймов в центре |
Легкая арматура: | Проволочная сетка, одинарный мат |
Эта история бетона | Динамический бетононасос
С его использованием в прочных современных конструкциях вы можете не думать о бетоне как об историческом строительном материале. Однако это вещество имеет богатое прошлое. То, что во времена Древнего Рима не было грузовиков с цементом, не означает, что тогдашние культуры не могли строить из бетона. У них были свои способы адаптации и использования материалов.
Изучая историю бетона, мы можем понять, как мы используем его сегодня. Мы собрали некоторые ключевые годы на протяжении всей истории, а также известные и исторические бетонные сооружения, чтобы дать вам лучшее понимание сути.
Для этих целей мы будем рассматривать бетон как смесь крупных и мелких частиц в сочетании с пастой. Паста схватывает и скрепляет частицы, которые затем можно использовать в качестве строительного материала. Мы также рассмотрим некоторые похожие материалы, которые имеют общие различия. На протяжении всей истории культуры строили из:
- Цемент: Этот мелкодисперсный порошок позволяет создавать другие материалы, такие как раствор, бетон, штукатурку и цементный раствор. Цемент действует как связующее вещество в этих строительных продуктах.
Его часто делают из известняка, но другие возможные ингредиенты включают глину, кварцевый песок и ракушки. Какие бы разные культуры ни использовали на протяжении всей истории, зависело от того, какой у них был доступ к тому месту, где они жили. Независимо от ингредиента, люди измельчают и объединяют его с такими материалами, как железная руда, а затем нагревают до высоких температур. Полученный продукт, называемый клинкером, перемалывается в цемент.
- Раствор: Раствор связывает кирпичи, камни и другие строительные материалы. Он сделан из цемента, песка и извести.Когда строители добавляют в смесь воду, цемент активируется, а затем затвердевает по мере высыхания. Затирка представляет собой аналогичный продукт, но в ней больше воды, которая течет между трещинами и щелями. Любое вещество может выступать в качестве клея для других строительных материалов от плитки до камня.
- Adobe: Высушенная на солнце грязь создает сырцовые кирпичи.
Песок, грязь и другие частицы почвы попадают в эти кирпичи, в которые люди могут также добавлять палки или солому вместе с водой. После высыхания кирпич сжимается и растет в зависимости от погоды.Поскольку его не обжигают в печи для отверждения, а вместо этого сушат на воздухе, он не подходит для влажного климата. Многие из первых применений строительных материалов, таких как бетон, на самом деле были глинобитными.
Вышеуказанные материалы относятся к одному семейству, но бетон является более прочным материалом. Он был с нами на протяжении всего времени в бесчисленных строительных проектах в самых разных формах. Читайте дальше, чтобы узнать больше об истории бетона и о том, как материал изменился за эти годы.
Самые ранние способы использования бетона
То, что мы сегодня считаем бетоном, несколько отличается от первого использования бетона.Тем не менее, подобные материалы имели свое значение на протяжении всей истории. Среди некоторых целей этих материалов было создание:
- Здания
- Этажи
- Мосты
- Дороги
- Скульптурные сооружения
Культуры по всему миру построили эти и другие здания из бетона и бетоноподобных материалов. Поскольку материал менялся с годами, трудно сказать, как долго существует бетон. Через приблизительную временную шкалу мы знаем, что она существовала за тысячи лет до нашей эры.Культуры использовали бетон на протяжении многих лет:
- 6500 г. до н.э.: Примерно в этом году были построены первые бетонные здания. Бедуины создали эти исторические бетонные сооружения на территории современной Сирии и Иордании. Ранние начинания подготовили почву для улучшения методов с течением времени.
- 3000 г. до н.э.: В это время египтяне использовали глину, смешанную с соломой, для создания глиноподобного строительного материала. Они также разработали и использовали гипсовые и известковые растворы для соединения сырцовых кирпичей.Примерно в то же время строители в Китае использовали форму цемента, созданную из липкого риса.
- 700 г. до н.э.: Бедуины обнаружили цемент, который затвердевает под водой, и примерно в это же время построили печи для обжига раствора.
Они использовали этот раствор для строительства полов, домов и других сооружений. За это время они также начали трамбовать бетонный материал и поняли, что вещество не будет работать так же хорошо, если оно будет слишком насыщенным.
- 600 Б.C.: Греки открыли натуральное вещество, которое может создавать бетон, если смешать его с известью. Хотя они использовали это вещество, они не были так продвинуты в конкретных методах, как другие культуры.
- 200 г. до н.э.: К этому времени римляне усовершенствовали строительство из бетона, хотя и не так, как мы используем его сегодня. Римляне создавали большую часть конструкции из рыхлых камней и материалов, цементируя их вместе раствором. Они даже использовали косметический кирпич в сочетании со своей версией цемента.Использование неструктурных блоков установило бетон как целевое и эстетическое изделие.
- 1414: Крах Римской империи заставил интерес к бетону угаснуть до тех пор, пока в этом году не появились рукописи, объясняющие это вещество.
С этим пришло новое понимание строительного материала. Этот год стал одним из многих поворотных моментов в истории бетона. Это запустило цепную реакцию открытия новых способов изготовления и использования бетона на века вперед.
- 1793: Джон Смитон разработал более эффективный метод производства гидравлической извести в 1793 году. Этот продукт использовался для ускорения схватывания цемента, а модернизированное производство упростило изготовление бетона и обеспечило его быстрое схватывание.
- 1824: Этот год был очень важным в истории бетона, потому что именно тогда каменщик Джозеф Аспдин создал портландцемент. Названный так, потому что он был похож на строительные камни в Портленде, Англия, портландцемент был прочной формой строительного материала.Аспдин произвел цемент, обжигая мел и глину в печи. Позже он решил добавить в глину известняк для создания клинкера.
Аспдин способствовал использованию цемента и бетона в современных конструкциях. Стремясь создать лучшую альтернативу строительному материалу римлян, он вдохновил конкуренцию на создание еще лучших версий своего портландцемента.
С первым использованием цемента и бетона произошла эволюция продуктов. Мы разработали множество способов изменить вещества, чтобы они работали лучше для нас, что со временем повлияло на историю бетонного строительства.
Контактный динамический бетононасос
Как бетон изменился за эти годы?
С годами бетон превратился в более эффективный материал. Мы перешли от использования натуральных веществ, напоминающих цемент, к обогащению природных материалов искусственными процессами. По мере развития технологий совершенствовались и наши методы производства бетона и цемента.
В конце 1800-х годов люди в Германии, Франции и США одновременно разрабатывали железобетон.В то время он использовался для промышленных построек, но впоследствии он стал использоваться в жилых домах и других сооружениях.
Портландцемент, созданный Джозефом Аспдином, отличается от того, что мы производим сегодня. Хотя Аспдин не указал конкретных соотношений или температур для изготовления своего портландцемента, мы знаем, что он не смог бы достичь высоких температур, которые мы используем сегодня для нагревания веществ.
Сегодня у нас есть стандартная формула портландцемента. Он был создан еще в 1917 году Американским обществом испытаний и материалов совместно с Национальным бюро стандартов.Стандартная формула создавала постоянное качество независимо от того, когда и где кто-то производил вещество.
Еще до того, как мы разработали формулу портландцемента, строители снова использовали бетон в проектах по всему миру. В начале 1900-х годов бетон снова получил общественное признание в качестве строительного материала, и появились следующие типы конструкций:
- Многоквартирный дом в Париже в 1902 году
- Первое бетонное высотное здание в Огайо в 1904 году
- 328-футовый мост в Риме в 1911 году
После этих и других зданий был разработан товарный бетон. В 1913 году материал был доставлен в Балтимор, штат Мэриленд. Это помогло сделать рабочие места более эффективными, поскольку рабочим больше не нужно было смешивать бетон на месте. Вместо этого он поступал предварительно смешанным с завода в ранних версиях того, что мы сегодня называем цементовозами.
Несколько десятилетий спустя мы обнаружили, что образование мелких пузырьков воздуха, известное как вовлечение воздуха, улучшает качество бетона. После введения в состав бетона воздухововлекающих веществ в 1930 году строительный материал стал легче работать и менее подвержен замерзанию.Теперь архитекторы в более холодном климате могли выбирать материал, не беспокоясь о трещинах или поломках.
Примерно в то же время строители разработали тонкостенный бетон. Крыши, купола, арки и другие подобные конструкции были сделаны из тонкой оболочки из бетона. Из-за прочной округлой формы этих конструкций не требовалось толстых слоев материала. Легкий вес тонкостенного бетона делает остальную часть здания более защищенной от обрушения, поскольку ему не нужно поддерживать тяжелый материал.
Работая с бетоном, мы сделали его более прочным и стойким строительным материалом. Мы нашли более простые способы его изготовления, транспортировки и использования. Наряду с этими открытиями строители и архитекторы возводили здания в разных стилях. Бруталистские, современные и другие бетонные конструкции включают подвиги и художественные творения, такие как:
- Зал Пола Рудольфа Йельского университета
- Музей Science Hills в Японии
- Юбилейная церковь за пределами Рима
- Исследовательский центр Института Солка в Калифорнии
- Жилой комплекс Villa Saitan в Японии
- Национальный музей Бразилии
Эти здания демонстрируют универсальность бетона как строительного материала.По мере развития технологий строители и архитекторы смогли создавать кривые, вырезы и другие привлекательные элементы дизайна из бетона. Гибкость стиля вещества позволила ему строить церкви, музеи, жилые дома и многое другое, а также некоторые исторические бетонные сооружения.
Знаменитые сооружения стали возможными благодаря бетону
За многие исторические и узнаваемые здания мы обязаны бетону. Были ли они построены тысячелетия назад или в этом столетии, некоторые бетонные конструкции, о которых вы, вероятно, слышали, включают:
- Пантеон: Пантеон в Риме — это самый большой неармированный бетонный купол.Несмотря на то, что Пантеон был завершен в 125 году, он до сих пор стоит в Риме. Он имеет диаметр 142 фута с 27-футовым глазком или отверстием в центре.
- Великая Китайская стена: Знаменитая достопримечательность из бетона строилась на протяжении многих веков. В зависимости от того, как вы определяете начало обширного проекта, творение началось в третьем веке до нашей эры. или несколько веков назад. Династии и королевства на протяжении всей истории Китая укрепляли эту структуру, добавляя к ней столетия после ее основания.
- Маяк Эддистоун: Расположенный у побережья южной Англии, этот третий вариант маяка был построен в 1700-х годах с использованием гидравлической извести Джона Смитона.
Единственная причина, по которой историческое бетонное сооружение рухнуло, заключалась в том, что скалы под ним со временем подверглись эрозии.
- Бетонная улица: В 1891 году в штате Огайо появилась первая бетонная улица. Известная как Корт-стрит, она стоит и сегодня. Несмотря на то, что Джордж Варфоломей создал улицу более 100 лет назад, она в два раза прочнее бетона, используемого в современных жилых проектах.Прочность делает его идеальным для противостояния трафику.
- Панамский канал: После неудачных попыток создать жизненно важное развитие путешествий и транспорта в 1904 году началось строительство Панамского канала. Через 10 лет проект был завершен. Бетон играл роль в шлюзах, которые помогают поднимать корабли, когда они движутся по каналу. По его завершении многие страны и порты были окончательно соединены.
- Плотина Гувера: Сама плотина, построенная в 1935 году, потребовала более 3 миллионов ярдов бетона.
На строительство электростанции и других сооружений плотины ушло еще 1 миллион ярдов. Однако строители не заливали бетон в одну массу, потому что он растрескался бы и затвердел слишком долго. Вместо этого они заполнили блоки бетоном, чтобы построить колонны. Испытания, проведенные двадцать лет спустя, показали, что бетон со временем стал прочнее.
- Плотина Гранд-Кули: Менее чем через 10 лет после завершения строительства плотины Гувера строители создали самое массивное бетонное сооружение из когда-либо построенных.Для завершения строительства плотины Гранд-Кули в Вашингтоне в 1942 году потребовалось 12 миллионов ярдов бетона. Поскольку для ее завершения требовалось в четыре раза больше бетона, чем для плотины Гувера, строители использовали конвейерную ленту длиной 2 мили для транспортировки материала на строительную площадку. Строители использовали тот же метод, что и при строительстве плотины Гувера для плотины Гранд-Кули, только в гораздо большем масштабе.
- Сиднейский оперный театр: Это бетонное сооружение получило титул крупнейшего бетонного сооружения в южном полушарии.Строительство началось в 1959 году и завершилось в 1973 году. Проект столкнулся с некоторыми трудностями, но его завершение привело к созданию великолепной бетонной конструкции. Сиднейский оперный театр в настоящее время служит местом для культурных мероприятий и туристов со всего мира.
- Burj Khalifa: Расположенный в Дубае, Burj Khalifa был построен из железобетона. Оно будет удерживать титул самого высокого здания в мире до завершения строительства башни Джидда в 2020 году. В Бурдж-Халифе было использовано более 400 000 кубических ярдов бетона, а также более 60 000 тонн арматуры или арматуры.
Эти современные и исторические сооружения были бы невозможны, если бы не бетон. Их высота, прочность, размер и многое другое демонстрируют способности бетона. Полезность вещества не угасла после того, как до н. э. лет тоже. Сегодня и в далеком будущем мы продолжим использовать бетон для строительства инновационных зданий, домов, квартир, отелей, скульптур и многого другого.
Получите бетонное оборудование и услуги с помощью динамического бетононасоса
Примите участие в истории бетона сегодня, воспользовавшись услугами и оборудованием Dynamic Concrete Pumping.У нас есть 40-летний опыт, помогающий подрядчикам воплощать в жизнь архитектурные замыслы, дополняя наследие исторических бетонных сооружений. Если вам нужны бетонные услуги или оборудование, свяжитесь с нами в Dynamic Concrete Pumping.
Когда снимать опалубку после заливки бетона? Когда можно снимать летом и зимой при бетонировании? Через сколько дней снять его с ленточного фундамента по СНиП?
Фундамент и опалубка являются одним из важнейших этапов строительства дома, так как выступают в роли фундамента и каркаса для формирования будущего строения.Опалубочная конструкция должна оставаться в собранном виде до полного застывания бетона. Поэтому очень важно иметь информацию, через какой промежуток времени его можно безопасно разобрать .
Влияющие факторы
Для формирования фундамента используется бетон, представляющий собой полужидкий состав. Но необходимо, чтобы вещество сохраняло требуемую форму . Для этого используется деревянная опалубка. Это временная съемная конструкция, внутренний объем которой соответствует всем необходимым параметрам и конфигурации. Опалубка формируется непосредственно на строительной площадке, закрепляется деревянным или арматурным каркасом, затем производится непосредственно заливка бетоном .
Изображение В зависимости от типа фундамента деревянная опалубка формируется по-разному … Снятие ее с ленточного фундамента или со столбчатого фундамента может немного отличаться по срокам. Для достижения равномерного распределения нагрузки на здание используется армопояс. Демонтировать опалубку с армопояса требуется только после того, как будет установлена арматура и затвердеет бетонный раствор.
Бетон формируется в несколько этапов
- Схватывающий раствор из бетона.
- Процесс усиления.
При бетонировании важными факторами, влияющими на прочность бетонной композиции, являются следующие
- Наличие воды (постоянное насыщение бетона водой позволяет избежать появления трещин на формируемой поверхности, при недостатке влаги состав становится хрупким и рыхлым).
- Температурный режим (любые реакции протекают тем быстрее, чем выше температура).
В процессе работы можно влиять только на влажность бетонного состава. Нельзя влиять на температурный режим. Поэтому время застывания в разных регионах и в разных климатических условиях будет отличаться.
Опалубка может быть с пленкой или без нее
ИзображениеПленка предназначена для защиты платы от повышенной влажности. Целесообразность его использования спорна, решение должно приниматься в каждом конкретном случае.
Стандарты
Согласно СНиП 3.03-87 снятие опалубки должно производиться только при достижении бетоном необходимой степени прочности и в зависимости от конфигурации конкретной конструкции .
- Вертикальное исполнение — производить отвод, если показатель достигает 0,2 МПа.
- Фундамент ленточный или армированный монолитный — возможен демонтаж деревянной опалубки при показателе 3.5 МПа или 50% марки бетона.
- Наклонные конструкции (лестницы) , различные плиты длиной более 6 метров — период распалубки начинается при достижении 80% показателей прочности бетона.
- Наклонные конструкции (лестницы), плиты длиной менее 6 метров — период разбора начинается при достижении 70% прочности марки используемого бетона.
Настоящий СНиП 3.03-87 в настоящее время официально считается нерасширенным . …Однако указанные в нем требования сегодня абсолютно актуальны. Это подтверждает многолетняя строительная практика. Согласно американскому стандарту ACI318-08 деревянная опалубка должна быть снята через 7 дней, если температура и влажность воздуха соответствуют всем принятым стандартам .
В Европе есть собственный стандарт ENV13670-1: 20000 . По этому стандарту демонтаж деревянной опалубки можно проводить в том случае, когда происходит 50% прочности бетонного состава, если среднесуточная температура воздуха была не ниже нуля градусов.
При строгом соблюдении сроков, указанных в требованиях СНиП, может быть достигнута прочность монолитной конструкции . Накопление прочности осуществляется впоследствии, но минимально необходимая прочность должна быть достигнута до того момента, когда будет производиться демонтаж деревянной опалубки.
Image При осуществлении частного строительства далеко не всегда удается установить точный процент прочности бетонного материала, чаще всего из-за отсутствия необходимых приборов. Поэтому требуется принимать решение о демонтаже опалубки, начиная со времени твердения бетона.
Опытным путем доказано, что бетон общеупотребительных марок М200-М300 при среднесуточной температуре воздуха 0 градусов за 14 суток может набрать прочность около 50% . Если температура около 30%, то те же марки бетона получают 50% гораздо быстрее, а именно за трое суток.
ИзображениеСнятие деревянной опалубки производится на следующий день или через сутки после окончания периода схватывания бетонной композиции.Однако специалисты рекомендуют не торопиться с демонтажем деревянной опалубки, так как каждые несколько часов раствор становится только прочнее и надежнее.
ИзображениеВ любом случае необходимо убедиться, что бетон достиг необходимого уровня прочности состава.
Через сколько дней снимать с учетом температуры воздуха?
При принятии решения о снятии деревянной опалубки необходимо учитывать один важный фактор, а именно температуру окружающей среды . Соответственно, период закладки будет отличаться в разное время года. В результате в основном все строительные работы, связанные с заливкой фундамента, проводятся летом.
При расчете температуры учитывается не максимальное или минимальное значение в течение суток, а среднесуточное значение. В зависимости от конкретных погодных условий производится расчет времени снятия созданной опалубки с бетонного пола. С распалубкой точно не стоит торопиться, так как некоторые неучтенные факторы могут несколько замедлить процесс кристаллизации бетонного раствора .
ImageImageНа практике при проведении работ по организации фундамента деревянную опалубку предпочитают не снимать минимум две недели. Бетон наиболее интенсивно набирает прочность в первую неделю. Впоследствии основа твердеет еще два года.
По возможности рекомендуется подождать 28 дней .Именно это время требуется для того, чтобы фундамент имел примерно 70% прочности.
Можно ли ускорить настройку?
Для того, чтобы строительные работы шли быстрее, может потребоваться ускорение процесса твердения бетонного раствора. Для этого используются три основных метода .
- Нагрев бетонной смеси.
- Использование специальных видов цемента.
- Применение специализированных добавок, ускоряющих процесс твердения бетонного раствора.
На заводе используются высокие температуры для ускорения твердения бетонной композиции . Процесс пропарки различных железобетонных конструкций значительно сокращает сроки схватывания. Но этот метод обычно не используется в частном строительстве. Повышение температуры на каждые 10 градусов увеличивает скорость схватывания в 2-4 раза.
Достаточно эффективным методом ускорения процесса схватывания является использование мелкомолотого цемента
ИзображениеНесмотря на то, что цемент крупного помола имеет длительный срок хранения, именно смесь мелкого помола твердеет значительно быстрее.
Еще одним способом ускорить процесс твердения бетонной композиции является применение специальных добавок .В качестве добавок могут быть использованы хлористый кальций, сульфат натрия, железо, калий, сода и другие. Эти добавки смешивают при приготовлении раствора. Такие ускорители повышают степень растворимости компонентов цемента, быстрее происходит насыщение водой, в результате чего кристаллизация протекает активнее. В соответствии с требованиями ГОСТ ускорители повышают скорость твердения в первые сутки не менее чем на 30% .
ИзображениеЧто произойдет, если опалубку демонтировать слишком рано?
В теплое время года расформовку можно произвести достаточно быстро, не нужно ждать 28 дней. После завершения первой недели бетон уже имеет способность сохранять требуемую форму.
ImageImageНо на таком фундаменте сразу вести строительство нельзя. Необходимо дождаться момента, когда монолит достигнет необходимого уровня прочности.
Слишком ранний демонтаж опалубки может привести к разрушению созданной бетонной конструкции .Фундамент – это основа конструкции, а не одна технологическая деталь. На этом монолите будет держаться вся конструкция, поэтому очень важно соблюдать все необходимые стандартные требования и стандарты.
Что делает бетон твердым, средним или мягким? И как я могу сказать?
Любой бетон является ТВЕРДЫМ, если вы упадете и ударитесь о него затылком, будь то 2500 фунтов на квадратный дюйм в вашем доме или 8000 фунтов на квадратный дюйм на мосту или военном объекте! Но в строительном мире, где живут многие из нас, часто бывает важно иметь и знать свойства бетона, чтобы мы могли выбрать правильный инструмент.Одно важное свойство, которое нужно знать, — это твердость бетона. Это называется его PSI или прочностью на сжатие в фунтах на квадратный дюйм, эта информация имеет решающее значение, помогая вам понять, приемлемо ли это для проекта, в котором он будет использоваться. Или, если вы режете или шлифуете бетон, вам нужно знать PSI, чтобы вы могли выбрать правильную алмазную матрицу для использования.
НАЖМИТЕ ЗДЕСЬ ДЛЯ ЛУЧШЕГО ПОНИМАНИЯ ДЛЯ ВЫБОРА ПРАВИЛЬНОГО АЛМАЗА.
К сведению, мы в США используем PSI при определении твердости бетона, это британская единица измерения, фунты на квадратный дюйм.Но большая часть остального мира использует метрическую оценку, известную как МПа или мегапаскаль (чем бы ни был, черт возьми, мегапаскаль, я посмотрел на него, и мои глаза просто остекленели, что-то связанное с Ньютоном, являющимся мерой силы и толкающей грамм материи с определенной скоростью и все в таком духе… Я придерживаюсь PSI!)
Вот общее сравнение между двумя способами измерения твердости бетона, а также того, что считается твердым и мягким бетоном.
2500 psi = 18 МПа, мягкий бетон
3000 psi = 20 МПа, мягкий бетон
3500 psi = 25 МПа, средний бетон
4000 psi = 30 МПа, средний бетон
5000 psi = 35 МПа, среднетвердый бетон
МПа = твердый бетон
Это сравнение не является точным, но если вам нужно точное сравнение, используйте 0. 00698915 для преобразования PSI в МПа
БЕТОН, УЧАСТВУЮЩИЕ ФАКТОРЫ
Так что же делает бетон твердым или мягким? Ну, есть ряд вещей, влияющих на твердость бетона. Сначала это,
АГРЕГАТ (камни в бетоне)
На эту часть приходится около 70% бетонной смеси. Таким образом, это очень важно и сильно различается по стране, где заполнитель состоит из очень твердой породы, такой как гранит, кремень, кварцит, вы, как правило, получаете более твердый бетон, а в местах с заполнителем, таким как сланец, песчаник и известняк, вы получаете более мягкий .Следующая диаграмма дает вам общее представление о твердости и мягкости по всей стране в зависимости от состава заполнителя, но, как мы увидим, существуют и другие факторы, которые также определяют твердость бетона.
КОНСТРУКЦИЯ СМЕСИ — В конце концов, вы не просто добавляете воду!
Разработка бетонной смеси — это процесс разработки правильных пропорций цемента, воды, диапазона заполнителя от песка до более крупного заполнителя, обычно до 1. 5 дюймов для достижения желаемой твердости как для производительности, так и для долговечности, существует также широкий спектр как химических, так и минеральных добавок, их использование будет зависеть от того, чего хочет достичь подрядчик, от понизителей атмосферной усадки до ускорителей, помогающих в процессе отверждения. и множество других. В колдовское зелье часто включают такие материалы, как летучая зола, которая первоначально использовалась в качестве наполнителя в бетоне, чтобы сократить все миллионы фунтов летучей золы, остатков угольной энергетики, которые ежегодно выбрасываются на свалки, но теперь их обнаруживают. фактически помочь в твердости бетона.
ПРОЦЕСС ОТВЕРЖДЕНИЯ
В детстве я просто предполагал, как, наверное, и все остальные, что бетон отверждается сушкой, и все мы были совершенно неправы. Бетон затвердевает в результате химического процесса, называемого «гидратация», когда компоненты цемента образуют химическую связь с молекулами воды и становятся гидратами, отсюда и название.
Важно не дать бетону «высохнуть» до того, как произойдет процесс гидратации, так как это делает плиту более слабой и склонной к растрескиванию.поэтому, когда бетон затвердевает, иногда необходимо опрыскивать поверхность, поддерживая ее влажной, чтобы дать необходимое время для гидратации. На самом деле, бетон будет затвердевать так же хорошо, если не лучше, под водой, если вы не будете «вымывать» бетонную смесь.
Личный пример: однажды я приложил камень к стене под прямыми летними солнечными лучами. на следующий день я вышел посмотреть на свою качественную установку и обнаружил 95% камня на земле. После обвинения моего поставщика в продаже мне некачественного раствора, продавец любезно объяснил мне важность процесса гидратации, я позволил раствору высохнуть слишком быстро!
ДРУГИЕ ВЕЩИ, КОТОРЫЕ ИЗМЕНЯЮТ
Время года, плита, залитая в холодных, влажных условиях, будет более твердой, и наоборот, если ее уложить в жаркую и сухую погоду. Затирочная машина может дать очень твердую поверхность, даже если бетон под ней мягкий.
КАК УЗНАТЬ, ЧТО У МЕНЯ ТВЕРДЫЙ ИЛИ МЯГКИЙ БЕТОН?
Для определения твердости бетона обычно используются два инструмента: молоток с отскоком и тест на царапанье Мооса.
Отбойный молоток
Молот с отскоком имеет поршень, который «выстреливает» пользователем и дает рейтинг PSI для плиты.Мне нравится этот, потому что он рассказывает вам о всей плите, а не только о самой поверхности.
Тест Мооса является наиболее часто используемым инструментом для определения твердости. Тест имеет рейтинг от № 1 до № 10, но для тестирования бетона обычно используется № 2– № 9, поскольку № 1 — твердость детской присыпки, а № 10 — алмаз. В наборе будет 8-9 «карандашных наконечников», эти наконечники постепенно становятся все более и более твердыми, поэтому вы должны начать, возможно, с № 4 и сделать 2-дюймовую царапину, затем, если бетонные царапины вы перейдете к № 5 и так далее. до тех пор, пока ваш штифт не поцарапает поверхность, поэтому, если он царапает в № 6, но не в № 7, вы смотрите на диаграмму, и это дает вам вашу конкретную твердость CSP, это хороший тест и менее затратный, чем молоток отскока, который может варьируется до 600 долларов.00 долларов по сравнению с комплектом Mohs около 120 долларов. Единственное, что мне не нравится в наборе Мооса, это то, что он говорит вам только о самой поверхности плиты, где молоток говорит вам о плите глубже.
К СУММЕ
Итак, мы можем начать понимать, что вы можете получить представление о твердости бетона, взглянув на используемый заполнитель, а также на географическое положение, но приготовление твердого или мягкого бетона требует гораздо большего. Я живу на северо-западе штата Вашингтон в Пьюджет-Саунд, и у нас одни из самых твердых бетонов на континенте, но иногда я нахожу здесь очень мягкий бетон, и это из-за всех других факторов, которые влияют на изготовление твердых и средних материалов. мягкий бетон.
У НАС есть несколько блогов по связанным темам, поэтому НАЖМИТЕ ЗДЕСЬ, чтобы перейти в центр контента Bartell Global и просмотреть их.
В настоящее время у вас недостаточно прав для чтения этого закона
В настоящее время у вас недостаточно прав для чтения этого закона Логотип Public.Resource.OrgЛоготип представляет собой черно-белый рисунок улыбающегося тюленя с усами. Вокруг печати находится красная круглая полоса с белым шрифтом, на которой в верхней половине написано «The Creat Seal of the Seal of Approval», а в нижней половине «Public».Resource.Org» На внешней стороне красной круглой марки находится круглая серебряная круглая полоса с зубчатыми краями, призванная вызвать печать из серебряной фольги.Public.Resource.Org
Хилдсбург, Калифорния, 95448
США
Этот документ в настоящее время недоступен для вас!
Дорогой земляк:
В настоящее время вам временно отказано в доступе к этому документу.
Public Resource судится за ваше право читать и высказываться в соответствии с законом.Для получения дополнительной информации см. досье этого незавершенного судебного дела:
Американское общество испытаний и материалов (ASTM), Национальная ассоциация противопожарной защиты (NFPA), и Американское общество инженеров по отоплению, охлаждению и кондиционированию воздуха (ASHRAE) против Public.Resource.Org (Общественный ресурс), DCD 1:13-cv-01215, Объединенный окружной суд округа Колумбия [1]
Ваш доступ к этому документу, который является законом Соединенных Штатов Америки, был временно отключен, пока мы боремся за ваше право читать и говорить о законах, по которым мы хотим управлять собой как демократическим обществом.
Чтобы подать заявку на получение лицензии на чтение этого закона, ознакомьтесь со Сводом федеральных правил или применимыми законами и правилами штата.
для имени и адреса поставщика. Для получения дополнительной информации о указах правительства и ваших правах гражданина в соответствии с законом , пожалуйста, прочтите мое свидетельство перед Конгрессом Соединенных Штатов. Более подробную информацию о нашей деятельности вы можете найти на сайте Public Resource.
в нашем реестре деятельности 2015 года. [2][3]
Благодарим вас за интерес к чтению закона.Информированные граждане являются фундаментальным требованием для того, чтобы наша демократия работала. Я ценю ваши усилия и приношу извинения за неудобства.
С уважением,
Карл Маламуд
Public.Resource.Org
7 ноября 2015 г.
Примечания
[1] http://www.archive.org/download/gov.uscourts.dcd.161410/gov.uscourts.dcd.161410.docket.html
[2] https://public.resource.org/edicts/
[3] https://public.resource.org/pro.docket.2015.html
Контрольные швы в бетоне — когда резать и расстояние
Правильно расположенные стыки. Примечание. Внутренние углы, где обычно возникают трещины, имеют правильно расположенные швы.
Важно принимать активное участие в принятии решения о размещении управляющих соединений. Часто к расшивке не относятся достаточно серьезно, и «пилорез» приходит к вам на работу и делает разрезы там, где он считает нужным или там, где ему удобно. Кроме того, на большинстве планов не указано расстояние между швами.Так что не оставляйте эту важную часть бетонной конструкции на волю случая.
Найдите местных подрядчиков по бетону, которые помогут с вашим проектом.
ЧТО ТАКОЕ КОНТРОЛЬНЫЕ СОЕДИНЕНИЯ?
Контрольные швы представляют собой запланированные трещины, допускающие деформации, вызванные изменениями температуры и усадкой при высыхании. Другими словами, если бетон трескается, вы должны играть активную роль в принятии решения о том, где он трескается, и что он будет трескаться по прямой линии, а не случайным образом.
КОГДА РЕЗАТЬ КОНТРОЛЬНЫЕ СОЕДИНЕНИЯ
Убедитесь, что вы разрезаете стыки достаточно быстро.В жаркую погоду бетон может треснуть, если швы не будут вырезаны в течение 6-12 часов после отделки бетона. В этом случае, если вы не хотите использовать инструмент для нарезки канавок для резки швов, есть легкие пилы для сухой резки с ранним входом, которые можно использовать почти сразу после отделки. Эти пилы режут на глубину от 1 до 3 дюймов, в зависимости от модели.
РАССТОЯНИЕ РЕГУЛЯЦИОННОГО СОЕДИНЕНИЯ
Пространственные швы (в футах) не более чем в 2-3 раза больше толщины плиты (в дюймах). 4-дюймовая плита должна иметь стыки на расстоянии 8-12 футов друг от друга.
При выполнении швов опытные подрядчики часто используют их для создания привлекательного ромбовидного узора. Если ваш бетон будет штамповаться, спросите о лучших способах избежать прерывания рисунка контрольными швами. Посмотрите это видео, чтобы узнать о хорошем решении: Заливка бетона с помощью Zip Strips.
Видео о желобовании бетона (размещение контрольных швов в свежем бетоне)
Время: 03:11
ДОПОЛНИТЕЛЬНЫЕ СОВЕТЫ ПО СОЕДИНЕНИЮ
- Вырезать швы достаточно глубоко
Вырезать швы на 25% глубины плиты.Плита толщиной 4 дюйма должна иметь швы глубиной 1 дюйм. - Как резать швы
Инструменты для нарезки швов в свежем бетоне.Резка пилой прорезает швы, как только бетон становится достаточно твердым, чтобы края, примыкающие к разрезу, не откалывались от пильного диска.
- Проложите стыки под стенами или под коврами
Под стенами их не будет видно. Под ковром у стыков не будет возможности телеграфировать через виниловые области. - Избегайте повторных углов
Планирование схемы соединения иногда может устранить повторные углы.
Дополнительные советы по созданию деформационных швов в бетонных плитах.
КОНТРОЛЬНОЕ СОЕДИНЕНИЕ VS. КОМПЕНСАТОР
Регулирующие швы предназначены для предотвращения растрескивания, а компенсационные швы предназначены для обеспечения движения. Компенсационные швы или изоляционные швы используются между двумя разными заливками бетона или там, где бетон соединяется с другим материалом или даже конструкцией. Деформационные швы чаще используются в крупных коммерческих проектах и часто не требуются при заливке жилых перекрытий. Эти швы обычно требуют заполнения, особенно если бетон будет полироваться или покрываться защитным покрытием (см. Герметизация швов в бетонной плите).
На голову выше обычного
Износ стыков стал новой проблемой для бетонных покрытий в северном климате.
В последнее время на ряде относительно молодых дорожных покрытий произошел преждевременный износ швов, что привело к большим затратам на техническое обслуживание. Строительная отрасль только в Висконсине оценивает ежегодные расходы примерно в 60 миллионов долларов на ремонт бетонного покрытия, из которых около 15-30 миллионов долларов предназначены для ремонта бетонных швов из-за проблем с долговечностью.Как правило, старые покрытия менее подвержены повреждению швов, даже в районах с высокой концентрацией противогололедных реагентов, используемых во время зимних работ по техническому обслуживанию, что побудило провести недавние исследования, посвященные изменениям в методах строительства и технического обслуживания.
Осенью 2015 года Департамент транспорта штата Висконсин (WisDOT) инициировал исследование влияния методов распиловки швов на долговечность бетонных швов. Исследование, проведенное исследователями из Университета Маркетт и Университета Миссури-Канзас-Сити, включало строительство двух испытательных участков бетонного покрытия и проверку ряда находящихся в эксплуатации покрытий с разрушением стыков и без них.В этой статье обсуждаются результаты, полученные на тестовых участках бетонного покрытия, спроектированных и построенных таким образом, чтобы можно было создать широкий диапазон распиленных соединений, включая условия для типа пилы, типа и качества пильного диска, глубины пропила и пропила. сроки.
В обе стороны
WisDOT в настоящее время позволяет использовать как обычную мокрую распиловку, так и распиловку с предварительным входом в сухую для формирования поперечных деформационных швов. В то время как конкретный тип распила обычно остается на усмотрение подрядчика, глубина распила обычно указывается на уровне одной трети толщины плиты (D/3). Время распиловки швов также имеет решающее значение, и WisDOT указывает, что распиловка должна начинаться, как только бетон достаточно затвердеет, чтобы предотвратить чрезмерное растрескивание вдоль распила и отделки до того, как условия вызовут неконтролируемое растрескивание.
Осенью 2015 года WisDOT инициировала исследование, завершенное учеными из Университета Маркетт и Университета Миссури-Канзас-Сити, для изучения влияния методов распиловки швов на долговечность бетонных швов.Исследование включало строительство двух испытательных участков бетонного покрытия и проверку ряда находящихся в эксплуатации покрытий с разрушением швов и без них.
Проверка
Первоначальный участок для испытаний бетона, построенный в октябре 2015 года, был спроектирован таким образом, чтобы обеспечить установку многочисленных распиловочных соединений D/3 с использованием различных типов пилы, типа пильного диска, времени пропила и типа бетонной смеси. Эта секция была построена на территории завода по производству готовых смесей Zignego в Вокеше, штат Висконсин., что устранило необходимость в средствах управления дорожным движением во время операций по укладке и последующих операциях по распиловке/отбору проб. Эта секция включала два разных состава смеси, заливаемой вручную, одна из которых включала более мягкий известняк южного Висконсина в качестве преобладающего крупного заполнителя, а другая — более твердый изверженный гравий северного Висконсина.
Каждая смесь использовалась для создания сплошной бетонной плиты толщиной 10 дюймов, шириной 10 футов и длиной 50 футов. Смеси были уложены рядом друг с другом, в результате чего общая длина асфальта составила 100 футов.В каждой смеси использовалась оптимальная градация заполнителя, расчетное соотношение воды и вяжущих материалов (в/см) 0,42, расчетное содержание воздуха 6% и значения осадки в пределах 2-4 дюйма.
Общий факторный фактор исследования распиловки включал основной фактор типа состава смеси (известняк или гравий, крупный заполнитель) и четыре дополнительных фактора, а именно:
- Фактор 1: Тип пилы — ранний вход или обычный;
- Фактор 2: время пилы — раннее, оптимальное или позднее в допустимом окне;
- Фактор 3: Тип отвала — твердый или мягкий заполнитель; и
- Фактор 4: Износ лезвия — новое или старое.
Поперечные распилы были сделаны на продольном расстоянии 2-3 фута, при этом соседние распилы были рассчитаны соответствующим образом для смягчения воздействия температуры. Для начальных входных пропилов стареющее состояние лезвия было смоделировано с использованием изношенной башмачной плиты с расширенным порталом пильного полотна.
Второй испытательный участок бетонного покрытия был построен в июле 2017 года в рамках проекта модернизации автомагистрали и включал в себя соединенное шпонками гладкое бетонное покрытие (JPCP), уложенное поверх регенерированного асфальтового основания.Эта секция, построенная в качестве замены одного из въездов, включала тротуар толщиной 8 дюймов с шириной покрытия 15 футов. Участок рампы длиной 900 футов, включающий 60 последовательных поперечных стыков, был создан в качестве исследовательского участка, чтобы учесть изменения глубины распила и операции по герметизации после разреза.
Состав смеси подходил для укладки со скользящими опалубками, в нем использовалась оптимальная градация заполнителя, расчетное отношение массы к см 0,37, целевые показатели содержания воздуха и осадки составляли 6% и 1. 5 дюймов соответственно. В состав крупного заполнителя входят как известняк, так и гравий.
Секция была спроектирована таким образом, чтобы обеспечить возможность установки многочисленных распилов неполной глубины, используя различные типы распила с ранним входом и глубину распила. Были сделаны распилы глубиной 2,67 дюйма (D/3), 2 дюйма (D/4) и 1,25 +/- 0,25 дюйма. Весь испытательный участок длиной 900 футов был разделен на три участка по 300 футов, каждый состоит из 20 последовательных поперечных швов, вырезанных на одну из выбранных глубин пропила.В каждом из трех подразделов 10 швов оставались незагерметизированными, а остальные 10 швов были загерметизированы с помощью силанового проникающего герметика.
Все распилы с ранним входом были произведены переносными пилами, управляемыми членами бригады подрядчика по укладке дорожного покрытия. Для разрезов глубиной 1,25 дюйма использовалась легкая пила. Срезы, которые должны были быть заделаны силановым проникающим герметиком, применявшимся в полевых условиях, были промыты под давлением через три дня после укладки. Проникающий в силан герметик был нанесен на следующий день после промывки с использованием оборудования, материалов и персонала, предоставленного местным подрядчиком.
В лаборатории
Репрезентативные образцы были взяты из каждого построенного соединения, чтобы получить достаточно материалов для сравнительного анализа. Для начального испытательного участка четыре образца блоков размером 12 дюймов в ширину (вдоль поверхности стыка) и 24 дюйма в длину (перпендикулярно к стыку) были получены из каждого стыка путем распила на всю глубину, завершенного через месяц после укладки. Для второй тестовой секции диаметром 6 дюймов. керны на всю глубину были получены из шести случайно выбранных швов (три герметизированных и три негерметизированных) и одного места центральной плиты в каждом подразделе через неделю после укладки.Все полевые образцы были доставлены в лабораторию для документации и тестирования производительности.
Поглощение измеряли в соответствии со стандартом ASTM C1585, при этом распиленная поверхность оставалась открытой, а все остальные поверхности были заклеены лентой из алюминиевой фольги толщиной 2 мил. Устойчивость к замораживанию-оттаиванию была испытана в соответствии с ASTM C666A. Относительный динамический модуль и массу измеряли каждые 30 циклов в соответствии с ASTM C215. После того, как стало очевидно, что морозостойкость бетона, распиленного в полевых условиях, была превосходной и не позволяла отличить какие-либо перестановки распиловки, было применено модифицированное испытание на замораживание-оттаивание, чтобы лучше дифференцировать характеристики.Испытания проводились с использованием стандартного оборудования ASTM C666A и времени цикла, за исключением того, что противогололедная жидкость вводилась посредством одномерной капиллярной абсорбции снизу. Относительный динамический модуль и весовые испытания измерялись каждые 30 циклов вплоть до 300 циклов. Масштабирование антиобледенителя было протестировано с использованием версии ASTM C672, адаптированной к специфике тестирования рабочих характеристик соединений. Для каждой перестановки тестировали один образец в состоянии поставки и один образец, покрытый 40% силаном.
Образцам с силановым покрытием давали высохнуть не менее 24 часов перед погружением в раствор антиобледенителя.Поскольку это исследование было предназначено для изучения влияния пиления на физические свойства, вместо CaCl2 использовали 3% раствор NaCl, чтобы предотвратить дополнительное повреждение суставов, вызванное образованием оксихлорида кальция.
Один из испытательных участков бетонного покрытия был спроектирован таким образом, чтобы обеспечить установку многочисленных швов с распилом на неполную глубину с использованием различных типов пилы с ранним входом и глубины распила. Полный испытательный участок длиной 900 футов был разделен на три участка по 300 футов, каждый из которых состоял из 20 последовательных поперечных швов, вырезанных на одну из выбранных глубин распиловки.В каждом из трех подразделов 10 швов оставались незагерметизированными, а остальные 10 швов были загерметизированы с помощью силанового проникающего герметика.
Просмотр образцов
Образцы известняковой смеси из начального тестового участка, распиленные очень рано в окне распила с помощью оборудования для раннего входа, все имели отметки, где башмачная плита полностью удаляла покрытие и где круг сдавливал поверхность. Состояние поверхности суставов раннего входа улучшилось с прогрессированием в временном окне.Что касается известняковой смеси, то заполнитель действительно выглядел нарушенным и вытягивался к поверхности, где заполнитель разбивался о башмак. Нарушение известняковой смеси произошло непосредственно под башмаком. Раннее старение также наблюдалось для гравийной смеси, где движение крупного заполнителя вызвало трещину, непосредственно прилегающую к башмаку.
Испытания на абсорбцию показали типичное поведение: вода сначала абсорбировалась очень быстро, а затем впитывалась гораздо медленнее (от одного до 15 дней).Одномерное поглощение позволяло различать условия оборудования: образцы, распиленные новыми лезвиями, давали гораздо более низкое и менее изменчивое поглощение, чем образцы, распиленные старым лезвием.
Все протестированные образцы показали хорошую морозостойкость в течение 300 циклов. Испытания, проведенные до 600 циклов, показали износ, сгруппированный по выскакиванию заполнителя и износу/эрозии пасты. Как правило, потеря массы образцов известняка была связана с выпадением заполнителя, в то время как потеря массы образцов гравия была ограничена разрушением пасты.Ни один образец не нарушил критерии массы или относительного динамического модуля ни при 300, ни при 600 циклах.
Результаты образования отложений и проникновения хлоридов в известняковую смесь показали, что обработка силаном значительно улучшила характеристики антиобледенителя, при этом большинство образцов с покрытием не имели визуальных различий после испытаний, а проникновение с поверхности уменьшилось с 0,50 дюйма (без обработки) до 0,38 дюйма ( обрабатывали). Результаты антиобледенителя для смеси гравия показали лучшие характеристики, чем для смеси известняка, с улучшением характеристик как для необработанных, так и для обработанных силаном образцов.Среднее проникновение вдоль поверхности соединения уменьшилось с 0,50 дюйма (без обработки) до 0,26 дюйма (с обработкой).
Образцы керна из второго испытательного участка показали, что стык на всех образцах активировался, при этом трещина на всю глубину начиналась возле вершины пилы и распространялась вокруг большинства соседних кусков крупного заполнителя. Как правило, извилистость активированной трещины уменьшалась по мере увеличения глубины пропила. Испытания на поглощение показали заметное снижение начальной скорости поглощения для всех кернов, запечатанных в полевых условиях и в лаборатории.Однако для всех образцов наблюдалось незначительное влияние на скорость вторичного поглощения. Модифицированные результаты испытаний на устойчивость к замораживанию-оттаиванию показали, что общая потеря массы имела тенденцию к увеличению с возрастом испытаний, что было ожидаемо, поскольку микротрещины обеспечивали больше места для удержания антиобледенительного раствора до того, как материал отслаивался. Хотя в распиленном стыке наблюдалась значительная эрозия, потери массы было недостаточно для большинства образцов стыков. Однако сердечники, полученные из одного герметичного соединения в пределах 1.5-дюймовый и секции D / 3 имели гораздо более низкие характеристики динамического модуля, чем любой из образцов. После испытаний на замораживание-оттаивание в антиобледенительном растворе была проведена визуальная оценка распиленных поверхностей с использованием тех же критериев, что и шкала ASTM C672.
Производительность с использованием визуальных критериев была напрямую связана с глубиной пропила, при этом самые глубокие пропилы имели наилучшие характеристики. Во всех случаях образцы, обработанные силаном, имели худшие характеристики, чем необработанные образцы. Оказалось, что паста, обработанная силаном, разъела, оставив несколько миллиметров обнаженного заполнителя.
Что все это значит
Распиловка в самом начале временного окна с использованием оборудования для раннего входа действительно вызвала физическое повреждение заполнителя и бетона на первом участке испытаний. В случае известнякового заполнителя повреждение произошло непосредственно под пильным башмаком, в то время как в случае гравийного заполнителя сразу снаружи и параллельно башмаку образовалась трещина. Результаты абсорбции не указывали на больший потенциал снижения долговечности; однако стойкость к замораживанию и оттаиванию образцов известняка раннего возраста указывала на то, что повреждение отрицательно сказалось на производительности.Никакой разницы в характеристиках замораживания-оттаивания не наблюдалось для перестановок гравия.
На образцах, полученных из первого тестового участка, наблюдались различия в поглощении, вызванные временем распиловки, техникой и оборудованием. Гравийная смесь поглощала меньше, чем известняковая смесь. Пиление в начале временного окна давало наименьшее поглощение только в том случае, если пиление проводилось новым диском, подходящим для заполнителя. Старое/изношенное лезвие обеспечивает более высокое поглощение и большую изменчивость во всех случаях, чем соответствующий шов, распиливаемый одновременно с новым лезвием.Если смесь известнякового заполнителя была распилена в конце временного окна, диск, предназначенный для более твердых заполнителей, давал меньшее поглощение. Силановая обработка швов обеспечила значительное снижение поглощения и смогла свести к минимуму поглощение в самых неблагоприятных условиях пиления.
Обе бетонные смеси на первом испытательном участке были устойчивы к замораживанию-оттаиванию до 300 циклов без перестановок распиловки, демонстрирующих значительное ухудшение свойств при замораживании-оттаивании после 300 циклов. Образцы со значительно высокой или низкой абсорбцией были испытаны до 600 циклов, и все образцы, кроме одного, имели приемлемые характеристики, что указывало на то, что бетон был высокого качества, считался очень морозоустойчивым и не мог отличить эффекты от распиливания.
Как и ожидалось, факторы распиловки не повлияли на образование отложений антиобледенителя на поверхности. Известняковая смесь имела худшие характеристики, чем гравийная смесь, причем обе они значительно улучшились при применении местного силанового герметика. Проникновение хлоридов в известняковую смесь не уменьшилось при применении силана, скорее всего, из-за сложности определения четкой границы с известняковым заполнителем. Проникновение хлоридов в гравийную смесь было снижено на 50% за счет применения силана.
Применение силанаобычно снижало абсорбцию на втором тестовом участке; тем не менее, изменчивость была намного больше, чем для образцов с лабораторным покрытием из первого тестового участка, вероятно, из-за уже низкой скорости впитывания бетона.
Морозостойкость сердечников из второго испытательного участка была превосходной при оценке по массе или относительному динамическому модулю. Однако через 300 циклов произошло значительное ухудшение зрения. Эффективность замораживания-оттаивания была наилучшей для более глубоких надрезов, сделанных позже в окне.
Исследователи дали следующие рекомендации по внесению изменений в текущую спецификацию и руководящие документы WisDOT:
- Подрядчик должен предоставить график для всех используемых дисков, показывающий совокупную длину пропила и глубину пропила, в дополнение к проверке соответствующего выбора диска для преобладающего крупного заполнителя, содержащегося в бетонной смеси. Для пил с ранним входом установочные башмаки необходимо заменять через те же промежутки времени, что и диски;
- Оборудование для пиления с ранним входом должно быть разрешено только для смесей, содержащих преимущественно крупные заполнители изверженного гравия.Убедитесь, что пилы оснащены алмазными дисками с функционирующими защитными кожухами и оборудованы для контроля выравнивания и глубины пропила. Не рекомендуется пиление в самом начале окна пиления. Минимальное время начала пиления не должно приводить к повреждению текстуры поверхности;
- Изношенные лезвия оказывают измеримое воздействие на бетон, и подрядчик должен поддерживать бревно лезвия с указанием глубины, расстояния и времени; и
- Использование силана привело к улучшению антиобледенительного отложения на образцах начального тестового участка, но к худшим характеристикам образцов после замораживания-оттаивания из второго тестового участка.Перед определением эффективности силана в полевых условиях рекомендуется провести дополнительную работу.
В этой статье представлены результаты исследования, финансируемого Департаментом транспорта штата Висконсин (WisDOT) и Министерством транспорта США в интересах обмена информацией. Представленная информация является результатом исследования, проведенного под эгидой WisDOT. Содержание данной публикации отражает точку зрения авторов, которые несут ответственность за правильное использование названий торговых марок, а также за точность, анализ и любые выводы, сделанные на основе опубликованной информации или материалов.WisDOT и FHWA (U.S. DOT) не несут ответственности за его содержание или его использование. Эта публикация не поддерживает и не одобряет какой-либо коммерческий продукт, даже если могут быть указаны торговые названия, и не отражает официальную точку зрения или политику WisDOT или FHWA (US DOT), а также не является стандартной спецификацией или регламентом WisDOT или ФХВА.
—————
Об авторе:
Кроветти — почетный адъюнкт-профессор Университета Маркетт.Кеверн — адъюнкт-профессор и заведующий кафедрой Университета Миссури-Канзас-Сити. Канг — инженер по дорожному покрытию и инженер-проектировщик в WisDOT-BTS. Макмаллен является президентом Ассоциации бетонных покрытий штата Висконсин.
.