Технология производства газобетона
Благодаря автоклавированию, непосредственно после его окончания газобетон имеет соответствующую прочность, долговечность и морозостойкость. Автоклавирование исключает возможность усадки, а также обеспечивает долговечность газобетона.
Газобетон хорошо подлежит обработке простейшими инструментами: пилится, сверлится, строгается. В него легко забиваются гвозди, скобы. Со временем газобетон становится твёрже. Дома из газобетона сегодня очень популярны в России. К тому же, проекты домов из газобетона и цена на него, доступны всем.
Автоклавная обработка газобетона производится не только для того, чтобы ускорить процесс твердения смеси. Основной смысл состоит в том, что в автоклаве при температуре +180 °С и давлении до 14 бар в газобетоне образуется новый минерал — доберморит. Благодаря этому повышается прочность материала и, что особенно важно, в несколько раз уменьшается усадка. За счет своих характеристик автоклавный бетон имеет гораздо больше способов применения. Он может использоваться, например, в армированных конструкциях — перемычках, панелях, и др. Ячеистый бетон автоклавного твердения имеет пониженную трещиностойкость и морозостойкость. Автоклавная обработка позволяет в более короткие сроки получать изделия с достаточно высокой прочностью при пониженном расходе вяжущего. У автоклавной обработки имеются и недостатки: дорогостоящее оборудование, специфика его эксплуатации, требующая высококвалифицированного обслуживающего персонала, высокая металлоемкость автоклавов, низкий коэффициент использования внутреннего объема автоклава. Мелкосерийное производство при автоклавном способе оказывается экономически невыгодным.
Автоклавный газобетон производится на крупных заводах и на стройплощадку попадает в виде готовых блоков. Изготовление этого материала на малом производстве или изготовление газобетона автоклавного своими руками — невозможны.
Основными компонентами этого материала являются цемент, кварцевый песок (либо зола унос), газообразователи, также возможно добавление гипса и извести. В качестве специализированных газообразователей используются алюминиевые пасты и пудры. Сырьё смешивается с водой заливается в форму и происходит реакция воды и газообразователя, приводящая к выделению водорода, который и образует поры, смесь поднимается как тесто. После набора пластической прочности, массив разрезается на блоки, плиты и панели. Ипользование высокотехнологичного резательного оборудования позволяет разрезать полученный массив с высокой точностью на блоки и плиты.
После этого изделия подвергаются закалке паром в автоклаве, где они приобретают необходимую жёсткость, либо высушиваются в условиях электроподогрева.
Процесс производства ячеистого бетона напоминает выпекание хлеба: в смесителе замешивается вода, цемент, молотый кварцевый песок, тщательно размельченная известь и гипс (не на всех производствах), добавляется газообразователь. В теплой влажной камере смесь поднимается.
Процесс газообразования происходит вследствие химической реакции между гидратом окиси кальция и алюминием; выделяющийся при этом водород вызывает вспучивание раствора, который, затвердевая, сохраняет пористую структуру.
При определении состава газобетона необходимо обеспечить заданную объемную массу и его наибольшую прочность при минимальных расходах порообразователя и вяжущего вещества. При этом структура газобетона должна характеризоваться равномерно распределенными мелкими порами правильной шаровидной формы.
Объемная масса газобетона и его пористость зависят главным образом от расхода порообразователя и степени использования его порообразующей способности. Некоторое влияние на них оказывают температура смеси и количество воды, принятое для затворения смеси, т.е. водотвердое отношение В/Т. Увеличение В/Т повышает текучесть смеси, а следовательно улучшает условия образования пористой структуры, если обеспечивается достаточная пластичная прочность смеси к концу процесса газообразования.
Прочность газобетона зависит также от характера его пористости, размеров и структуры пор и прочности межпоровых оболочек. С увеличением В/Т до оптимального значения, обеспечивающего наилучшие условия формирования структуры смеси, прочность газобетона повышается. Прочность оболочек, в свою очередь, зависит от оптимального соотношения основного вяжущего и кремнеземистого компонента, В/Т, а также условий тепловлажностной обработки. Из этого следует, что применение смесей с минимальным значением В/Т при условии образования высококачественной структуры (например виброспучиванием) позволяет получить газобетон более высокой прочности.
Для изготовления газобетона применяют портландцемент марок 300, 400, 500, удовлетворяющий требованиям ГОСТ 970-61. Производство газобетона предъявляет специальные требования к портландцементу в отношении щелочности цементного теста – рН теста не должна быть ниже 12. Щелочность цемента определяется количеством свободной СаО и суммой Na2О и K2О. По данным работы газобетонных заводов, содержание щелочей (Nа2О, К20) в 1 л раствора цемента не должно быть менее 75 мг. В случае недостаточной щелочности раствора в газобетонную массу следует дополнительно вводить известь или щелочь в виде каустической соды (NаОН).
При применении в качестве основного вяжущего извести особое внимание уделяют значительному количеству активных окиси кальция (СаО) и магния (МgО). Общая активность извести не должна быть менее 75%, количество МgО — не более 1,5%. В производстве можно применять известь. Известь должна быть равномерно обожженной.
Введение извести как добавки к цементу сокращает расход цемента и одновременно увеличивает щелочность раствора, обеспечивая энергичное протекание реакции газообразования:
3 Са(ОН)2 + 2 Аl + 6 Н2О 3 СаО·Аl2О3·6Н2О + 3 Н2
В качестве кремнеземистого компонента в производстве газобетона применяют речной или горный кварцевый песок, золу-унос тепловых электростанций, маршалит и другие материалы. Кварцевый песок для изготовления газобетона и газосиликата должен быть чистым, без примесей глины и органических веществ, с содержанием SiO2 не менее 80%. Присутствие глины замедляет твердение газобетона и уменьшает его прочность. Органические примеси вредно сказываются на протекании реакции газовыделения; вспучивание газобетона при наличии органических примесей ухудшается. Зола-унос может применяться в производстве газозолобетона при содержании SiО2 более 55%. Зола-унос должна иметь незначительное количество сернистых соединений, несгоревших частиц угля и карбонатов кальция.
Важнейшей технологической особенностью получения высококачественных газобетонных изделий максимальной пористости и достаточной прочности является создание оптимальных условий для двух одновременно протекающих процессов газовыделения и газоудержания. Необходимо обеспечить соответствие между скоростью реакции газовыделения и скоростью нарастания структурной вязкости цементного теста или раствора. При этом выделение газа должно как можно полнее закончиться к началу схватывания системы цемент — вода. Протекание процесса газообразования определяется большим количеством различных факторов. Наибольшее влияние на скорость этого процесса оказывают вид, количество и свойства газообразователя, щелочность и температура среды и т. д.
Изготовление газобетона осуществляется мокрым или сухим способом. Экономически более целесообразным является мокрый способ, при котором помол кремнеземистого компонента или его смеси с известью производится в присутствии воды с получением шлама. При сухом способе помол и смешение компонентов осуществляются в шаровых мельницах в сухом виде. Песок размалывают в шаровых мельницах. Для осуществления мокрого помола в мельницу вводят подогретую воду. При применении в производстве извести, последнюю вводят в мельницу для совместного помола с песком. Из мельницы шлам пропускают через сито для отделения от крупных включений. Далее шлам собирают в сборнике и с помощью мембранного насоса или путем передавливания сжатым воздухом подают в шламовый бассейн или шламовый силос. Для предотвращения разделения шлама, т. е. осаждения частиц песка, шлам в бассейнах и силосах подвергают непрерывному перемешиванию. Одновременно производят барботаж шлама.
Дозировка шлама, подогрев и предварительное смешение осуществляются в ванне-дозаторе. Для подогрева шлама до 40-45° применяют острый пар. Дозировка цемента – весовая. Газообразователь взвешивают и подают в бачок с клееканифольной эмульсией, снабженный пропеллерной мешалкой.
Окончательное интенсивное смешение всех компонентов газобетонной массы происходит в передвижной самоходной пропеллерной газобетономешалке. Материалы в газобетономешалку загружают в определенной последовательности. Сначала заливают песчаный шлам, затем немолотый песок (в случае необходимости) и в последнюю очередь – цемент. После этого в течение 2-3 мин перемешивают всю массу. Введение алюминиевой суспензии определяет начало перемешивания газобетонной массы. Одновременно с этим газобетономешалка начинает передвигаться. Перемешивание газобетонной массы должно продолжаться 2-3 мин. Тщательное перемешивание массы обеспечивает однородность смеси и равномерность вспучивания. Излишняя продолжительность перемешивания вредна, так как возможно начало интенсивного газообразования в газобетономешалке. При этом теряется часть выделившегося газа и три заливке в формы газобетонная масса не даст нужного вспучивания. Разливают массу в формы через отверстия в нижней части мешалки при помощи гибких резинотканевых рукавов. Формы до заливки газобетона смазывают минеральным маслом или специальными эмульсиями для предотвращения сцепления газобетона с металлом форм. Газобетонную массу заливают с учетом вспучивания на 2/3 или 3/4 высоты формы.
После заливки газобетонной массы начинается вспучивание. процесс вспучивания продолжается 30-40 мин. После вспучивания происходит схватывание и твердение газобетона. Для ускорения схватывания и твердения газобетона, а также для ускорения процесса газовыделения в цехе по производству газобетонных тонных изделий температура воздуха должна поддерживаться не ниже +25°. Формы, в которых вспучивается и твердеет газобетон, нельзя передвигать, подвергать сотрясениям и ударам, так как вспученная, но не затвердевшая масса может при этом осесть. При вспучивании газобетонная масса образует так называемую горбушку, которую после затвердевания срезают ручными или механическими ножами. Затем застывшую массу разрезают на изделия нужного размера, формы устанавливают на автоклавные вагонетки в 2-3 яруса по высоте и загоняют в автоклав для ускоренного твердения.
На сайте Вы можете найти информацию: видео о газобетоне, возведение стен, стоимость газобетона, производители газобетона, что лучше — газобетон или пенобетон, отзывы, а также купить газобетон.
litebeton.ru
Технология производства газобетона
В данной статье мы поговорим о технологии производства газобетона. Если вы собираетесь строить дом из газобетона, то необходимо понимать не только процесс постройки дома, но и иметь основные представления о газобетоне с возможными трудностями, которые могут возникнуть при строительстве дома.
В первую очередь, что такое автоклавный газобетон? Автоклавный газобетон (АГБ) сильно отличается от обычно нами представляемого бетона. АГБ – композитный материал, в котором прочность при сжатии обеспечивается прочностью входящих в его состав заполнителей, а прочность при растяжении и изгибе, постоянства форм обеспечивается характеристиками вяжущего. Знаем цементный бетон, асфальтный бетон, полимерный бетон и в этом ряду слово газобетон выбивается. Газобетон, строго говоря, не бетон, а искусственно синтезированный минерал, причем достаточно однородный. По постоянству прочности он почти совпадает со сталью. Коэффициент вариации прочности порядка 5%, примерно также как у стальных сплавов.
Различия газобетона и газосиликата
В современном разговорном языке понятия газобетона и газосиликата перемешаны. Есть области в России, где распространен термин газосиликат. На северо-западе и центральной России чаще используется газобетон. По большинству описывается один и тот же материал – ячеистый бетон автоклавного твердения.
Смешение понятий возникло еще с 1960-1980 годов, когда производство автоклавных бетонов развивалось стремительно, параллельно существовали несколько способов производства. В частности были автоклавные бетоны на цементном, известковым и смешанном вяжущем.
В современной промышленности остались более долговечные на цементном и смешанном вяжущем, а чисто силикатные ячеистые бетоны вымерли как класс. Чистых газосиликатов современная промышленность не выпускает.
Поэтому сейчас, говоря «газосиликат», как правило, имеют в виду автоклавный газобетон.
Свойства газобетона определяется двумя технологическими переделами:
- Помол песка смалывается до тонины цемента (2000 – 3000 см²/г)
- Автоклавная обработка. Автоклав по сути большая скороварка, в которой поддерживается (нагнетается) давление 12 атм. при температуре 188°С и в течении 12 часов газобетонные массивы находятся в автоклаве
Кварцевый песок расходуется в синтезе гидросиликатов
SiO2 + h3O = h3SiO3
Синтезируется тоберморит – основной минерал, обеспечивающий прочность и долговечность газобетона. По сути силикатный кирпич, но только с ячеистой структурой.
Технология производства газобетона
Алюминиевая пудра, или любой другой металл, стоящий в электрохимическом ряду до водорода вводится в виде суспензии. Одновременно всё подается в бетономешалку известь, цемент, песчаный шлам (суспензия молотого песка) и просто вода. Компоненты проходят взвешивание, дозируются и затем отправляются на смешение в скоростную мешалку. Смешение происходит за 30 секунд в полном объеме, и за один массив выходит порядка 4,5 м³ газобетона. Заливается в формы разогретые до 40 °С, приблизительно половина от этого объема.
В результате реакции происходят газовыделения, когда алюминий вытесняет h3. Алюминий превращается в гидроксид, а затем участвует в гидросиликатах, где получаются алюминаты кальция и силикаты алюминия и т.д. Алюминий в окисленном состоянии, как в земной коре.
После заливания смесь отправляется в камеру созревания. Там происходит процесс парообразования. Образуется большое количество пор, массив возрастает до требуемого объема, набирая прочность, называемую транспортной. Затем массив при помощи тележки выезжает из камеры и отправляется на линию резки. Массив достаточно большой 4,5 метра по объему. Здесь происходит нарезка на блоки.
Далее из отдельных массивов формируются автоклавные поезда, которые поступают на автоклав. Здесь в течение 12 часов обрабатываются при высоком давлении в среде насыщенного водяного пара.
После автоклавной обработки блоки поступают на разделительную машину, т.к. в автоклаве могли слипнуться. На некоторых заводах разделение происходит до автоклавирования.
После разделения блоки упаковываются сверху в термоусадочную пленку или полиэтилен, это помогает сохранить влажность газобетона до начала строительства. Газобетон на заводах хранится на открытых площадках до 2-3 лет.
Далее со склада материал отправляется на строящийся объект.
mainstro.ru
особенности блоков, технические характеристики, фото
Как производится газобетон? Каким образом технические характеристики газобетонных блоков соотносятся с практическими качествами этого строительного материала? Какие особенности материала нужно учитывать при строительстве? Давайте разбираться.
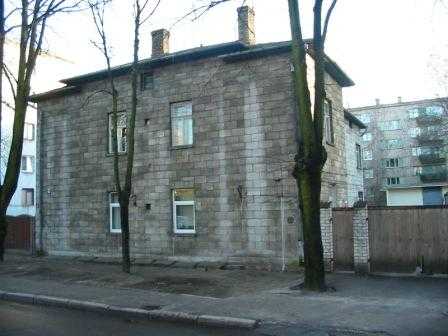
Один из старейших домов из автоклавного газобетона. Постройка — 1939 год, г. Рига.
История
Она начинается с получения чешским промышленником Гоффманом патента на технологию вспенивания цементных и гипсовых растворов. Патент был выдан в 1889 году; изобретение сводилось к добавке в раствор кислоты и реагирующих с ней солей.
Цель — получение материала с уступающей бетону плотностью и улучшенными теплоизоляционными характеристиками — была достигнута; однако метод был дорогим и крайне неудобным в применении.
Идея получила развитие четвертью века позже: американцы Дайер и Аусворт использовали в качестве газообразующей добавки порошки металлов — цинка и алюминия. Собственно, современная технология производства газобетона не слишком отличается от разработанной тогда. Именно 1914 год считается годом рождения материала.
Однако: первый автоклавный газобетон начал массово производиться в Швеции еще на 15 лет позже.
В 1929 году компания Ytong наладила промышленный выпуск блоков из смеси извести и кремнезема, проходивших пропарку при повышенной температуре.
Ytong по сей день считается одним из ведущих производителей материала.
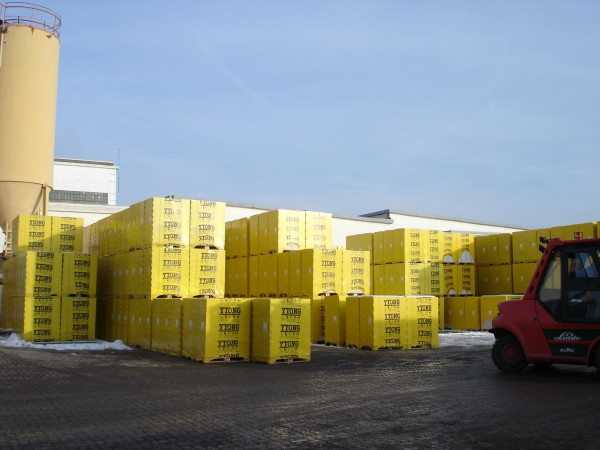
Продукция компании завоевала популярность на российском рынке.
В 1934 году в Швеции был налажен выпуск блоков по несколько иной технологии: в качестве связующего использовалась не известь, а цемент.
В СССР производство автоклавных ячеистых бетонов стало массовым к середине 20 века. К нашему времени объем производства блоков достиг примерно 3,5 миллионов кубометров в год.
Описание
В чем причина популярности материала? Какие технические характеристики газобетона сделали его настолько востребованным?
Достоинства
- Теплоизоляционные качества газобетонных стен примерно соответствуют соответствующим характеристикам сухой древесины, в разы превосходя тяжелый бетон, силикатный и керамический кирпич. Схожий материал — пенобетон — тоже отстает по этому параметру.
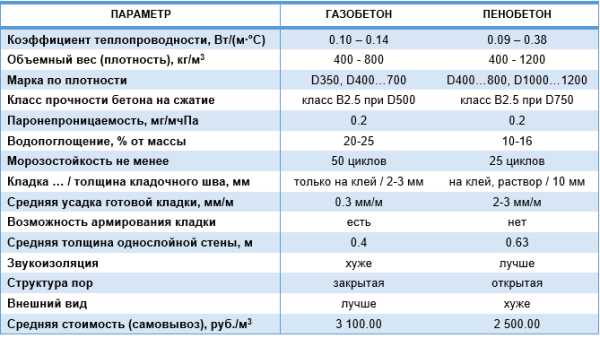
Сравнение характеристик газо- и пенобетона.
- Механическая прочность превосходит пенобетон, хоть и заметно уступает более плотным материалам.
Уточним: в зависимости от марки по плотности различают конструкционные, конструкционно-теплоизоляционные и строго теплоизоляционные блоки.
Прочность первых изделий позволяет использовать их для сооружения несущих стен и перекрытий; последние применяются в каркасно-монолитном строительстве в качестве заполнения стен.
- Благодаря все той же пористой структуре, производство оказывается довольно экономичным: на фиксированный объем строительного материала уходит меньше сырья.
- Структура с открытыми порами способствует естественной вентиляции стен. Эта особенность напоминает деревянные дома: часть воздухообмена с улицей и до трети парообмена осуществляется непосредственно через ограждающие конструкции.
- Простота обработки тоже напоминает о древесине: газобетон легко пилится ручной пилой, его можно сверлить и вбивать в его толщу гвозди.
Характеристики
Стоит сделать небольшое лирическое отступление и рассказать о методах классификации газобетона.
Основные характеристики, описывающие материал, выглядят так:
Характеристика | Описание |
Марка по плотности | Соответствует плотности в кг/м3 |
Класс прочности | Соответствует максимально допустимой нагрузке на сжатие в мегапаскалях (МПа) |
Морозостойкость | Количество циклов заморозки и оттаивания, которые блок может перенести без падения прочности более чем на 5% |
А теперь давайте посмотрим, какие значения эти и некоторые другие важные для строителя параметры принимают у газобетонных блоков наиболее востребованных типов.
Марка по плотности | D400 | D500 | D600 | |
Класс прочности | В 2 | В 2,5 | В 3,5 | В 3,5 |
Коэффициент теплопроводности, Вт/м*С | 0,096 | 0,12 | 0,14 | |
Морозостойкость, циклы | F75 | F75 | F100 | F100 |
Усадка при высыхании, мм/м | 0,3 и менее | |||
Паропроницаемость, мг/м*ч*Па | 0,24 | 0,28 | 0,24 | 0,23 |
Обратите внимание: марке по плотности D500 соответствуют два класса прочности.
Разница между ними заключается в соотношении количества связующего и заполнителя при производстве блоков.
Что этот набор характеристик означает в практическом плане?
- Газобетон обеспечивает примерно втрое — впятеро более эффективное утепление по сравнению с керамическим кирпичом. Так, для того, чтобы обеспечить сопротивление теплопереносу в 2,5 м2*С/Вт, необходима газобетонная кладка толщиной 375 мм или кирпичная толщиной 1100 мм.
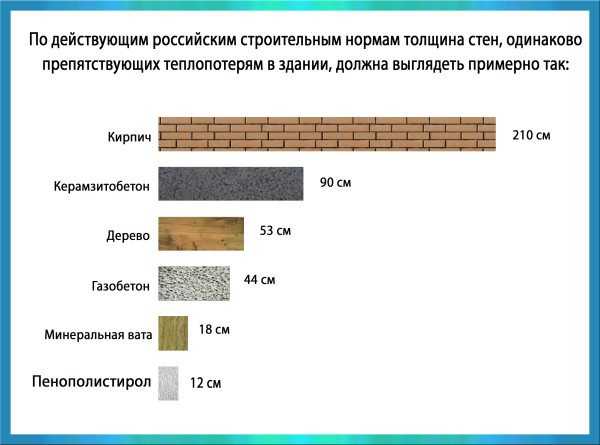
Сравнение теплоизолирующих качеств разных материалов.
- При упомянутом соотношении толщины нагрузка на фундамент, соответствующая квадратному метру кладки, в первом случае равна 205 килограммам, а во втором — 2000 кг.
- Минимальная ширина ленточного фундамента в первом случае равна 400 мм, во втором — 1200.
Производство
Из чего делают газобетон?
Сырье
В состав материала входит два основных компонента — наполнитель и связующее. Что может использоваться в этом качестве?
Наполнитель
- Тонкомолотый кварцевый песок.
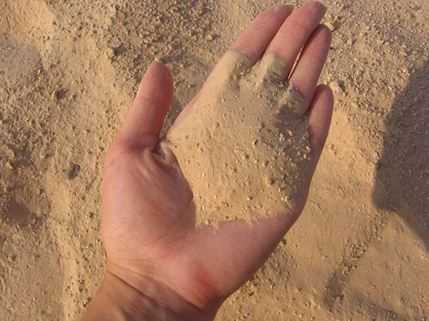
Речной песок — наиболее востребованный наполнитель.
- Измельченные отходы горно-добывающей промышленности (скальные и осадочные породы).
- Зола, образующаяся при сжигании угля.
- Вторичные продукты обогащения руд.
- Металлургический шлак.
Связующее
- Известь.
- Портландцементы.
- Смешанное связующее (цемент + известь, известь + гипс и т.д.).
Технология
Технология изготовления газобетона в промышленных масштабах включает следующие основные операции:
- Наполнитель смешивается со связующим, после чего в полученную массу добавляется суспензия газообразователя — алюминиевого порошка. В чистом виде порошок не используется: он слишком легко разносится любым сквозняком.
- Смесь разливается в формы, где выделяющийся при реакции алюминия с щелочной средой водород вспучивает ее.
- После схватывания пористая масса нарезается на блоки. Для резки используются прочные струны толщиной до миллиметра; карманы для захвата и переноски блоков вырезаются фрезой.
- Последний этап — сушка в камерах с подогревом или пропаривание в автоклаве. Второй сценарий требует более дорогостоящего оборудования, зато способствует скорейшему набору газобетоном прочности. Среднее время выдержки блоков в автоклаве — 12 часов; рабочее давление — около 12 бар при температуре 190 С.
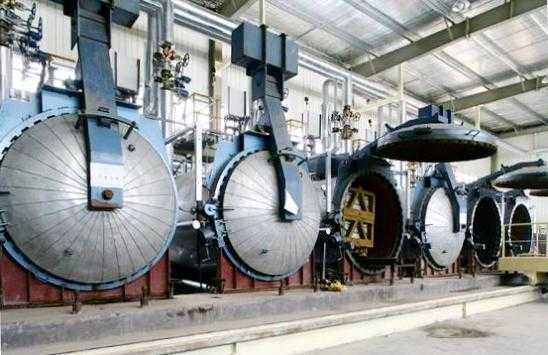
Загрузка автоклавов.
Любопытно: выход на рабочий режим и подготовка к разгрузке автоклава постепенны и занимают 1,5 — 2 часа.
- Последний этап — упаковка продукции в водонепроницаемую упаковку и укладка на поддоны.
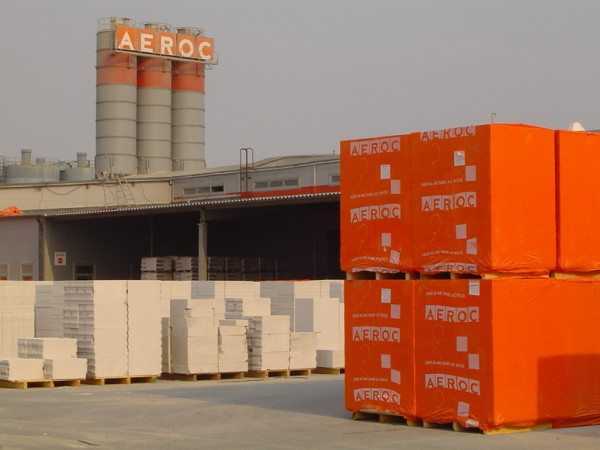
Водонепроницаемая упаковка обеспечивает стабильно низкую влажность.
Когда вместо пропарки используется сушка блоков? Прежде всего, при производстве газобетона своими руками, в домашних условиях либо при полукустарном изготовлении небольших партий на продажу.
Как уже упоминалось, цена необходимого оборудования в этом случае гораздо ниже; однако качество продукции несколько ухудшится:
- Усадка в процессе сушки достигнет 3-5 мм/метр.
- Прочность бетонных изделий на сжатие не превысит 10 — 12 кгс/см2. Впрочем, постепенный набор прочности при поглощении атмосферной влаги связующим будет продолжаться несколько лет.
Особенности строительства
Какие ограничения использование газобетонных блоков накладывает на строительство?
Фундамент
Основное требование к нему — максимальная жесткость, исключающая любую деформацию несущих стен. Несмотря на относительно высокую прочность, газобетон полностью лишен эластичности и при изгибающих нагрузках дает трещины.
Какие виды фундаментов применяются при газобетонном строительстве?
- На скальных и сухих супесчаных грунтах используются мелкозаглубленные ленточные основания.
- На пучинистых грунтах (глины, суглинки) оптимальное решение — свайный фундамент на буронабивных сваях с монолитным железобетонным ростверком.
- На болотистых почвах и других нестабильных грунтах заливается бетонный плитный фундамент. Он равномерно распределяет нагрузку по значительной площади и исключает любые неравномерные просадки стен.
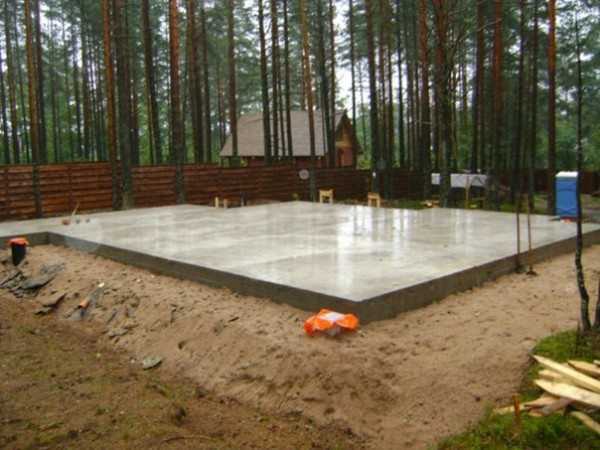
На фото — плитный фундамент.
Стены
Ключевое требование к стенам — высокое сопротивление теплопереносу. Оно нормируется действующими СНиП и для центра страны равно 3 — 3,2 м2 * С/Вт.
Обеспечить соответствующие тепловые характеристики, согласно заверениям производителей, могут:
- Блоки марки по плотности D500 при толщине стен в 500 мм.
- Блоки D600 — при толщине стен в 600 мм.
Для несущих стен из газобетона действуют ограничения по этажности строения.
Количество этажей | Класс прочности блоков |
1 — 2 | В 2 |
3 | В 2,5 |
4 — 5 | В 3,5 |
Более 5 | Строительство несущих газобетонных стен не допускается. Строение должно быть каркасным. |
Кроме того: в сейсмоопасных районах армирующий железобетонный каркас предназначен для повышения сейсмостойкости конструкции здания.
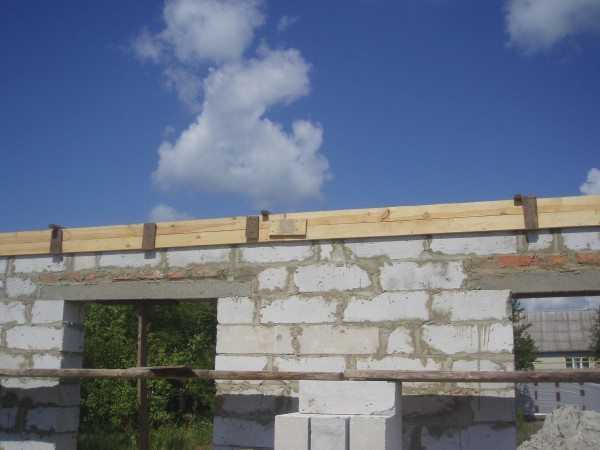
В опалубке — армопояс, способствующий повышению сейсмостойкости строения.
Какие правила действуют для внутренних несущих стен и ненагруженных перегородок?
- Если на стену опирается одна плита перекрытия, она возводится из блоков прочностью В 2,5 с толщиной 240 мм или из блоков прочностью В 3,5 толщиной 200 мм.
- Стена, на которую опираются две плиты, должна быть толще — 300 и 400 мм соответственно.
- Ненагруженные межквартирные перегородки выполняются из блоков ненормируемой прочности толщиной не менее 240 мм. Инструкция связана с необходимостью обеспечить качественную звукоизоляцию.
- Межкомнатные перегородки имеют толщину 100 — 150 мм. Прочность, разумеется, не нормируется и в этом случае.
Перемычки
Они могут выполняться из монолитного железобетона (в этом случае перемычка заливается на месте; кладка стен используется как часть опалубки) или из специальных U-образных блоков. В последнем случае перемычка может быть сборной.
Как обеспечивается достаточная несущая способность конструкции?
- U-образные блоки выставляются на временную подпорку полостью вверх. Они должны заходить за края проема как минимум на 10 см с каждой стороны.
- В полость блоков закладывается арматурный каркас.
- Полость бетонируется. Подпорка убирается после надежного схватывания бетона.
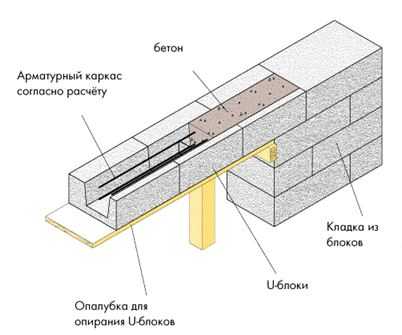
Устройство сборной перемычки.
Кладочный раствор
На обычный цементно-песчаный раствор, приготовленный в пропорции 1:3, выкладывается только первый ряд блоков. Следующие ряды кладутся только и исключительно на специальный клей для ячеистых бетонов, обеспечивающий толщину шва не более 3 мм.
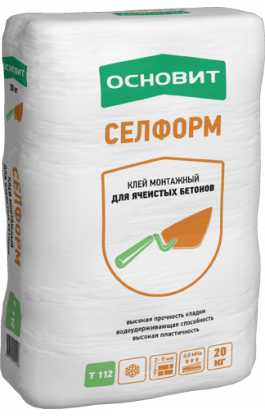
Клей для газобетона.
Почему обычный раствор не стоит использовать для кладки?
- Толстый шов — это мостик холода, ведущий в помещение с качественной теплоизоляцией. Как вырастут потери тепла — думается, можно не объяснять.
- Кроме того, блоки обладают точными размерами и идеальной геометрией. Тонкие швы позволяют использовать это преимущество, делая внешний вид кладки безупречным.
Наружная и внутренняя отделка
Главное требование к ней вполне стандартно: паропроницаемость стен должна увеличиваться изнутри наружу. Нарушение этого несложного правила приводит к отсыреванию стен, а в перспективе — и к их ускоренному разрушению.
Поскольку паропроницаемость газобетона исключительно высока, для стен из него обычно используются специальные штукатурные смеси с повышенной паро- и воздухопроницаемостью. Не менее популярное решение — вентфасады, обеспечивающие дополнительное утепление, и не препятствующие естественной вентиляции стен.
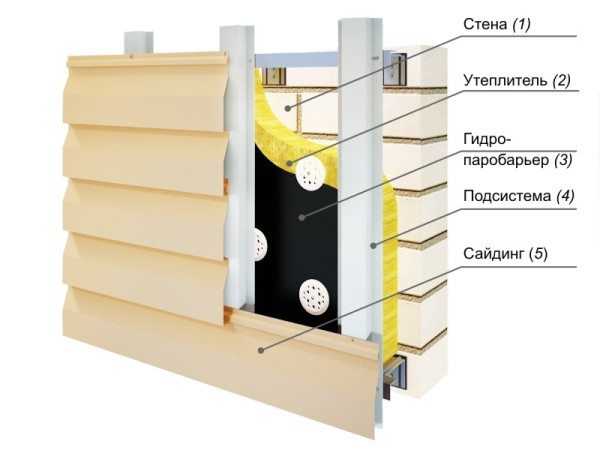
Утепленный вентфасад с облицовкой виниловым сайдингом.
Заключение
Надеемся, что предложенная информация будет полезной как начинающим строителям, так и потенциальным производителям недорогого и практичного строительного материала. Как всегда, видео в этой статье содержит дополнительные материалы. Успехов!
masterabetona.ru
Технология изготовления автоклавного газобетона | gazobeton.org
Газобетон – это легкий искусственный материал, полученный в результате твердения поризованной смеси, состоящей из гидравлических вяжущих веществ, тонкомолотого кремнеземистого компонента, воды и добавки газообразователя.
Для изготовления изделий из ячеистого бетона можно применять различные сырьевые материалы, но наибольшее распространение получили следующие:
— портландцемент ПЦ 400 – ПЦ 500, без активных минеральных добавок;
— известь негашеная кальциевая с содержанием CaO не менее 70%;
— кварцевый песок с содержанием кварца SiO2 не менее 85%, а глинистых примесей не более 3%;
— газообразователь алюминиевая пудра (паста) с содержанием активного алюминия не менее 80%.
Технологический процесс изготовления автоклавного газобетона включает в себя:
— прием и подготовку сырьевых материалов;
— приготовление газобетонной смеси;
— формование массивов газобетона;
— разрезку массивов на изделия;
— автоклавную обработку;
— упаковку изделий.
Сырьевые материалы могут поступать на завод различными видами транспорта (чаще всего автомобильным и железнодорожным). Хранение вяжущих предусматривается в специальных силосах. Количество и объем силосов выбирается в зависимости от мощности завода, удаленности от поставщиков материалов и вида транспорта.
Кварцевый песок выгружаются в приемный бункер, откуда по ленточному конвейеру поступает на помол для приготовления шлама. Помол производится в шаровых мельницах. Далее песчаный шлам транспортируется в шламбассейны, где гомогенизируется с помощью постоянного механического перемешивания.
Негашеная известь на предприятие поступает в тонкомолотом или комовом виде.
В первом случае, тонкомолотая негашеная известь хранится, по аналогии с портландцементом, в силосах и уже готова к употреблению. Во втором случае, если поступает комовая негашеная известь, на предприятии используется технология приготовления известково-песчаного вяжущего путем совместного сухого помола в шаровых мельницах извести и кварцевого песка.
Приготовление газобетонной смеси производится в дозаторно-смесительном отделении. Портландцемент, известь (известково-песчаное вяжущее), песчаный шлам, шлам из отходов резки, вода и алюминиевая суспензия дозируются в соответствии с установленной рецептурой в специальный смеситель, обеспечивающий высокую гомогенность смеси.
Процесс формования включает разгрузку (заливку) смеси из смесителя в форму и вспучивание смеси. Окончание процесса формования наступает после достижения максимальной высоты вспучивания смеси и прекращения активного газовыделения.
После вспучивания формы с газобетонной смесью выдерживаются на постах, желательно при температуре воздуха не менее +15-20oС до приобретения требуемой пластической прочности сырца. Для ускорения процесса набора первоначальной прочности формы со смесью могут выдерживаться в специальных термокамерах при температуре до +70-80oС. Время выдержки при использовании термокамер уменьшается.
После достижения сырцом пластической прочности 0,04-0,12 МПа (в зависимости от технологии) формы подаются на резательный комплекс. Газобетонный массив калибруется со всех сторон и разрезается проволочными струнами в продольном и поперечном направлениях на изделия требуемых размеров. Метод резки газобетонных массивов в полупластическом состоянии с помощью тонких проволочных струн хорошо зарекомендовал себя и на современных резательных машинах позволяет получать изделия точных размеров с отклонениями от номинальных до ±1,0-1,5 мм. Такая точность позволяет осуществлять кладку блоков на тонкослойную клеевую смесь вместо традиционного цементно-песчаного раствора.
Разрезанные на изделия массивы устанавливаются на автоклавные тележки и загружаются в автоклав. После полной загрузки автоклава начинается тепловлажностная обработка по определенному режиму, включающему плавный набор температуры и давления, изотермическую выдержку при температуре около 190°С и давлении 12 атм, плавный спуск давления и подготовка изделий к выгрузке.
Из компонентов CaO и SiO2, вяжущих материалов и кварцевого песка, а также воды, в условиях автоклавной обработки (высокое давление и температура) происходит образование новых минералов – низкоосновных гидросиликатов кальция, что предопределяет более высокие физико-механические характеристики автоклавного газобетона в сравнении с неавтоклавными ячеистыми бетонами (пенобетон, газобетон).
После завершения цикла тепловлажностной обработки изделия подаются на участок деления и упаковки, а затем на склад готовой продукции.
Основные моменты технологии производства блоков из автоклавного газобетона показаны на видео одного из участников ассоциации ВААГ:
gazobeton.org
Способы и оборудование для производства газобетона. Технические характеристики и свойства газобетона
Современные технологии строительства диктуют свои правила и условия. Новые методики предполагают использование новых строительных материалов. Относительно недавно на строительном рынке появился такой материал, как газобетон или его модификация пенобетон.
Оба варианта относятся к категории ячеистых бетонов, которые относятся к классу искусственных материалов. Характерной особенностью между пено- и газобетоном является технология образования внутренних пор.
Газобетонные блоки используются для всех видов строительства. Малогабаритные сооружения – загородные дома, дачи. Возведение крупномасштабных объектов из газобетона требует наличия дополнительного металлического каркаса для усиления прочности конструкции.
Популярность материалу принесли его многочисленные положительные качества, одно из которых способы его производства и цена.
Посмотрите видео о производстве газобетона
Технические характеристики и свойства газобетона
— прочность – уникальный материал, сочетающий в себе два противоположных качества – легкость и прочность;
— технологичность и простота обработки – газобетонные блоки легко обработать любым подручным инструментом, что позволяет значительно расширить возможности архитектурного дизайна;
— теплоизоляция – сооружения из газобетона принято называть «теплый дом»; материал отлично удерживает тепло в холодный период года, и одновременно не позволяет перегреваться летом, создавая, таким образом, микроклимат внутри здания;
— огнестойкость – газобетон не горит, поскольку в своем составе не имеет горючих компонентов;
— устойчивость к грибкам и паразитам – благодаря высокой степени влагоустойчивости, нет среды для появления плесени или грибка;
— долговечность – строения из газобетона имеют довольно солидный срок эксплуатации – специалисты отмечаю срок от 50 до 100 лет.
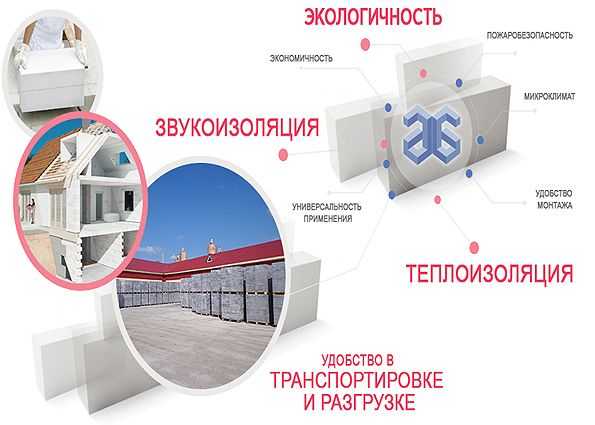
Для организации небольшого предприятия достаточно иметь технологию, сырье, и, конечно, необходимо специальное оборудование для производства газобетона. Особо надо отметить, что качество производимого газобетона в домашних условиях, абсолютно не отличается от материала, выпущенного на промышленных предприятиях, где работают целые комплексы, а вернее сказать линии для производства газобетона.
Способы производства газобетона
1. Автоклавный способ. При изготовлении газобетонные блоки проходят специальную обработку в автоклавах, с высокой температурой и давлением. Материал отличается высокой прочностью и долговечностью. Метод используется исключительно в промышленных условиях, так как требует наличия специального и довольно дорогостоящего оборудования.
2. Неавтоклавный способ. Данный способ имеет два этапа. Первый – производство бетонной смеси, включающей специальные добавки, второй – заливка смеси в формы до полного ее отвердения в естественных условиях. Такой газобетон имеет гораздо меньшую прочность и соответственно срок эксплуатации. Вместе с тем этот способ вполне подходит для домашнего изготовления и не требует больших затрат на оборудование для производства газобетона.
Компонентный состав материала практически не меняется от способа производства, могут иметь место только отдельные нюансы.
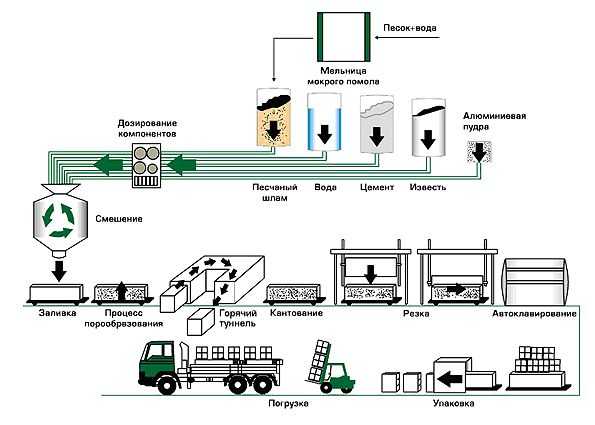
Технологии и оборудование для производства газобетонных блоков
Технология производства газобетона известна с незапамятных времен, в производство газобетонных блоков в промышленных масштабах началось в начале XX века в Швеции. В состав смеси для производства газобетонных блоков входит цемент. Марка цемента имеет значение, поскольку это один факторов, влияющих на прочность готового материала. По технологии необходим цемент марок М400 и М500. Помимо цемента для производства автоклавного газобетона применяется кварцевый песок, негашенная известь, алюминиевые газообразователи и вода. Возможно использование каких-либо дополнительных компонентов, например, гипсового камня.
Что включает оборудование для производства газобетонных блоков? В условиях масштабных предприятий процесс изготовления выглядит таким образом. После формирования газобетонной смеси масса выкладывается в крупногабаритную емкость. Далее следует этап нарезки, который выполняют специальные машины. Резка производится с помощью струн, что позволяет получать блоки точных размеров. Такая точность габаритных размеров важна в силу того, что материал укладывают на клеевую основу.
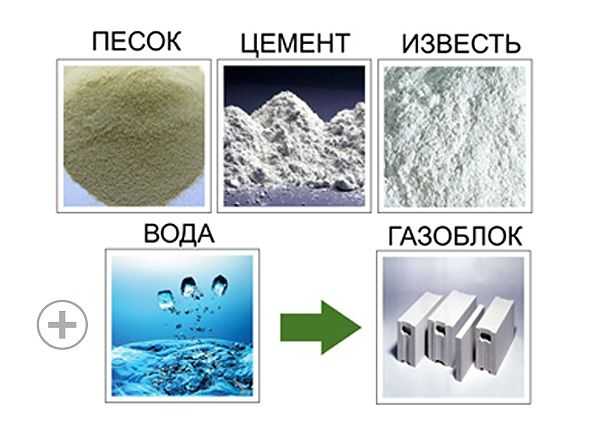
Промышленные линии для производства газобетона
Масштабы современного строительства требуют наличие материалов в необходимом количестве и самого высокого качества. Такие условия может обеспечить только предприятие с необходимым и современным оборудованием. Линии для производства газобетона позволяют увеличить производительность и сократить время производства. Практически все процессы производства полностью автоматизированы. Это полностью исключает погрешность в технологии и так называемый человеческий фактор.
Еще один момент — производительность линии. В зависимости от масштабов производства можно выбрать линию определенной производительности. Главной ее составляющей является газобетоносмеситель, объем которого считается главным показателем общей производительности линии.
Итак, согласно с выбранным способом производства, необходимо приобрести оборудование. Как отмечалось ранее, оборудование для производства автоклавного газобетона предполагает масштабное производство. Для этого необходимы соответствующие площади, где будет располагаться линии производства газобетона.
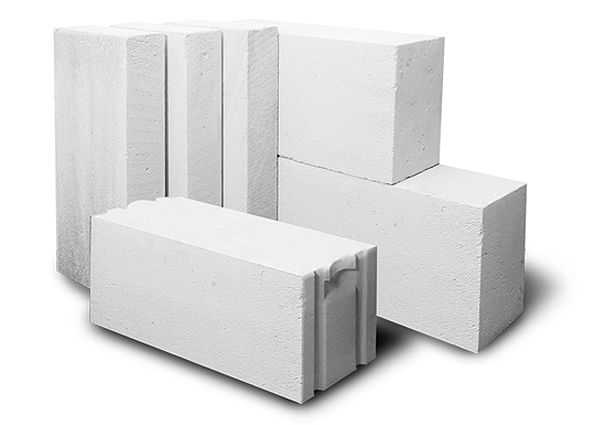
Технология и оборудование для производства автоклавного газобетона
— дозировка и смешивание компонентов;
— формирование массы;
— закладка массива в форму;
— выдерживание и опрокидывание бетонной смеси;
— формирование газобетонного блока или резка заготовки;
— подготовка блоков к закладке в автоклав;
— загрузка в автоклав;
— время выдержки в автоклаве;
— выгрузка из автоклава;
— упаковка и загрузка на поддон.
Более простой и менее затратный способ производства газобетонных блоков – неавтоклавный. Таким методом можно изготавливать строительный материал в домашних условиях. Он не требует больших помещений или специального оборудования. Тогда возникает вопрос – какое необходимо оборудование для производства неавтоклавного газобетона?

Технология и оборудование для производства неавтоклавного газобетона
— дозировка и смешивание компонентов – принципиальной разницы в компонентном составе между автоклавным и неавтоклавным методами производства не существует;
— подготовка форм для выкладки готовой смеси;
— выкладка массы;
— время на застывание газобетона;
— формирование газобетонного блока — для распила можно использовать любые подручные инструменты, как механические, так и электрические.
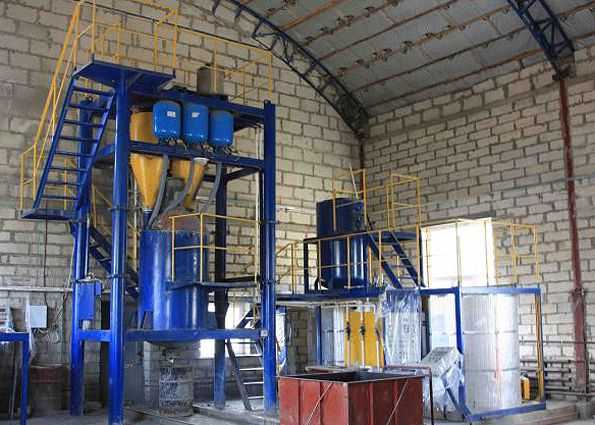
Производители оборудования для газобетона
Родиной газобетона считается Швеция. Именно там была впервые применена технология вспенивания цементно-известковой смеси с помощью алюминиевого газообразователя. Технология постоянно совершенствовалась. Параллельно улучшалось качество и технические характеристики материала. Некоторые производители работают над качеством и свойствами строительного материала, другие постоянно модернизируют оборудование для производства газобетона.
Среди европейских заводов-производителей оборудования для производства строительных материалов обязательно надо сказать о предприятиях Германии. Немецкое оборудование для производства газобетона по праву считается одним из самых качественных не только в Европе, но и в странах Азии и Америки. Лидер среди немецких концернов оборудования для производства строительных материалов – фирма «Masa». Предприятие имеет внушительный опыт работы, и значительный авторитет на рынке.
Еще одна величина – концерн Hess AAC. Это предприятие выпускает готовые заводы для производства газобетона и других материалов и конструкций.
Строительство из газобетонных блоков считается приоритетным направлением среди строительных технологий.
Поделиться:nastroike.com
Технология производства газобетона — АлтайСтройМаш
С изобретения технологии начал свою работу весь завод. А сейчас её легко приобретают все заказчики в комплекте со своим оборудованием. Для начала расскажем о преимуществах нашей технологии перед аналогами:
- быстро окупает производство – от пары недель до нескольких месяцев;
- производит газобетон высшего качества — по ГОСТ;
- даёт отличный результат с минимальными ресурсами — даже без ускорителей твердения и фиброволокна.
Технология как план действий
Для каждой линии описан свой порядок работы. Его соблюдение – одна их составляющих наивысшего качества. Соблюдать технологию просто, потому что она похожа на план:
- подготовить формы – монтаж и смазка;
- приготовить смеси из компонентов;
- заполнить формы смесью;
- нарезать застывший массив;
- прогреть блоки;
- разобрать массив и упаковать блоки – обернуть полиэтиленом.
При покупке линии вы получаете массу подробностей по каждому этапу и приступаете к практике — она важнее любых советов.
Об особенностях работы с каждой линией читайте в разделах:
- мини-линии;
- стационарное оборудование;
- конвейерное производство.
Линии отличаются по производительности и степени автоматизации, поэтому для каждой линии — своя технология. Мы также делаем линии на заказ, по индивидуальным пожеланиям клиента. Таких примеров на сайте нет, но знайте, что заказы на оборудование по вашей задумке мы тоже принимаем. В таких случаях технологию пишем специально под изготовленную линию.
Главное преимущество технологии «АлтайСтройМаш»
Это простота.
Технология считается совершенной, когда её можно объяснить даже ребёнку. И сейчас вы уже понимаете, что производство газобетона на оборудовании «АлтайСтройМаш» — действительно простой процесс.
Заказчики оборудования сами справляются и со сборкой линии, и с запуском производства. Кроме иллюстраций и видео-инструкций, у каждого клиента есть свой технолог. Он контролирует запуск, отвечает на все вопросы, а при необходимости – лично налаживает производство.
Прочитайте, какие минимальные требования нужно соблюсти для производства. Может у вас уже всё готово к производству?
Читать о Требованиях к производству
asm.ru
Неавтоклавный газобетон: технологии производства, фото
Газобетон в последнее время является очень популярным строительным материалом, благодаря ряду своих достоинств. Зачастую застройщики отдают предпочтение более дешевому его варианту – неавтоклавному газобетону. Но что представляет собой этот материал, чем отличается автоклавный и неавтоклавный газобетон и стоит ли на нем экономить?
Далее мы постараемся ответить на все эти вопросы и дать исчерпывающую информацию по данному типу ячеистого бетона.
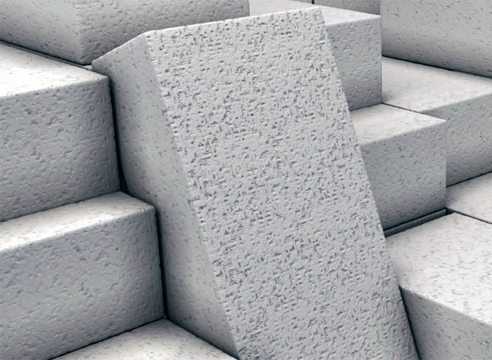
Полученные неавтоклавным способом газобетонные блоки
Общие сведения
Многие люди считают, что газобетон – это современный материал. Однако,на самом деле он был запатентован впервые еще в 1889 г. в Праге неким изобретателем Гофманом. Он придумал изготавливать материал на основе газа, получаемого в результате химической реакции между бикарбонатом натрия и соляной кислотой.
В Голландии в начале прошлого века была запатентована технология приготовления газобетона с использованием дрожжей. Немного позже в Германии предложили применять в качестве газообразующего вещества металлическую пудру.
Практически современная технология изготовления пористого бетона была разработана в Швейцарии изобретателем Эриксоном в 1923 г. Уже в 1925 году было налажено промышленное производство неавтоклавного газобетона как строительного материала. Очень скоро его производство появилось и во многих других странах.
В то время материал приготавливали на основе портландцемента, а немного позже стали использовать и вяжущие на основе зол и шлаков. Изначально материал был придуман как утепляющий, однако уже в 30-х годах удалось получить и конструкционный газобетон. Его применяли для ограждающих конструкций в малоэтажных зданиях.
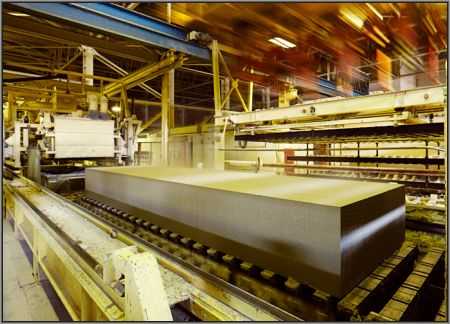
Современная линия производства неавтоклавного газобетона
Таким образом, материал сложно назвать совсем новым, так как он прошел уже достаточную и вполне успешную проверку временем.Конечно, на сегодняшний день используют современное технологическое оборудование для производства неавтоклавного газобетона, с новыми видами тепловлажностной обработки. Кроме того, подобраны самые оптимальные составы, что значительно повысило качество изделия.
Технология производства
Состав
В составе данного типа ячеистого бетона используют следующие основные компоненты:
- Портландцемент – является вяжущим элементом;
- Наполнители – песок в чистом виде, либо с добавлением золы-уноса ТЭЦ, мела, гипса и пр.
- Алюминиевая пудра – используется при формировании материала в качестве парообразующего вещества.
Кроме того, для улучшения характеристик, в состав неавтоклавного газобетона добавляют различные модифицированные добавки, к примеру, полуводный микрокремнезем или гипс. Для ускорения процесса твердения используют хлорид кальция.
На фото — структура изделия
На сегодняшний день ведутся работы по увеличению прочностных характеристик изделия выполненного неавтоклавным методом. Самым перспективным считается использование различных армирующих добавок, представляющих собой волокна разного происхождения.
Это могут быть:
- Стекловолокна;
- Полимерные волокна;
- Базальтовые;
- Асбестовые и пр.
Кроме того, положительный результат дает и увеличение на 5-10 процентов содержания наполнителя в составе, к примеру, золы-уноса или микрокремнезема. Причем, это позволяет не только повысить прочность ячеистого бетона, но и уменьшить его стоимость.
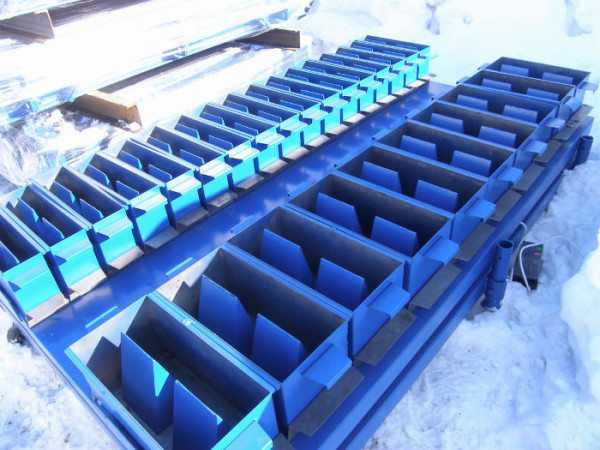
Формы для изготовления блоков
Изготовление
Технология производства неавтоклавного газобетона основана на том, что в результате химической реакции алюминиевой пудры и щелочи в составе смеси, внутри нее образуются поры, которые заполняются воздухом. Получившуюся пористую смесь оставляют застывать в естественных условиях, т.е. без применения автоклавов (специальных печей).
Иногда оборудование для неавтоклавного газобетона содержит пропарочные печи. Благодаря качественному пропарочному режиму, тоже улучшаются прочностные характеристики изделия.
Надо сказать, что неавтоклавному ячеистому бетону свойственны сквозные поры, в результате чего он обладает плохими гидроизоляционными свойствами. Однако, благодаря внедрению современных технологий, этим параметром материал стал приближаться к автоклавному газобетону.
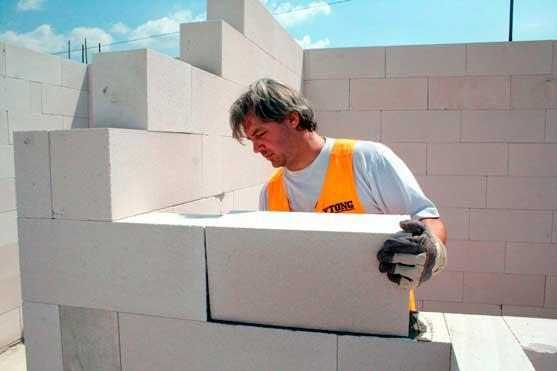
Легкий блок удобно укладывать своими руками
Особенности материала
Достоинства
Характеристики неавтоклавного газобетона во многом схожи с автоклавным материалом.
В частности, можно выделить следующие моменты:
- Низкая плотность при высокой прочности. Благодаря пористости материала снижается его цена, за счет уменьшения расхода компонентов.
- Небольшой вес, в результате чего с материалом легко работать. Кроме того, снижается нагрузка на фундамент здания.Это обеспечивает не только долговечность строения, но и экономию при его возведении, так как можно использовать менее мощную основу.
- Отличные теплоизоляционные свойства благодаря пористости. Данное свойство обеспечивает энергосбережение при отоплении помещений.
- Легко обрабатывается.Если обычно выполняется резка железобетона алмазными кругами, то для газобетона можно использовать обычную ножовку.
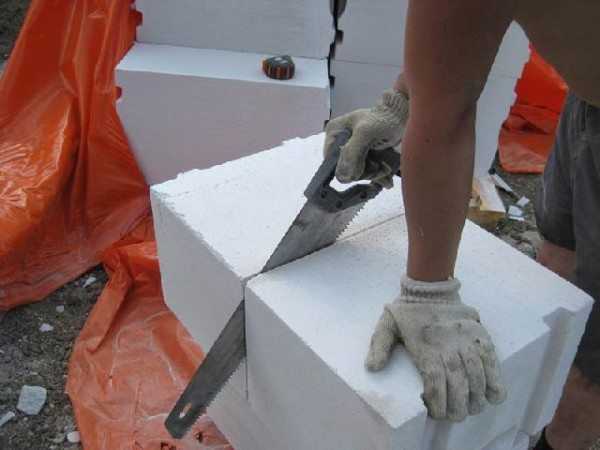
Разрезка блока ножовкой
Соответственно, чтобы подвести коммуникации в помещении не понадобится алмазное бурение отверстий в бетоне, так как можно воспользоваться обычными сверлами.
- Пожаростойкость. Материал является абсолютно не горючим. Поэтому его можно использовать для обшивки стен, когда необходимо обеспечить надежную пассивную пожаробезопасность. (См. также статью Облицовка газобетона: как сделать.)
- Экологичность. Материал не только выполнен из экологически чистых компонентов, но еще и обладает отличной паропропускной способностью, что обеспечивает благоприятный микроклимат внутри зданий, построенных из газобетона.
- Инструкция по укладке, такая же, как и при работе с более традиционным материалом, к примеру, кирпичом.
Совет!
Газобетон является отличным материалом для межкомнатных перегородок, так как обладает хорошими шумоизоляционными свойствами.
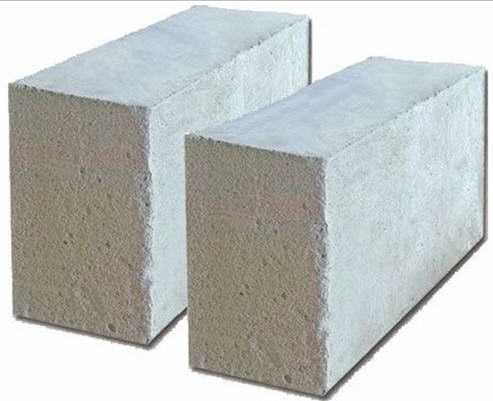
Автоклавные блоки
Отличия между материалами, выполненными по разным технологиям
Теперь рассмотрим в чем отличие автоклавного газобетона от неавтоклавного.
А заключаются они всего в нескольких моментах:
- Неавтоклавный материал обладает большей усадкой, которая составляет примерно 2-3 мм/м, в то время как автоклавный имеет усадку не более 0,3 мм/м. Если при заливке монолитных изделий данный недостаток практически незаметен, то при возведении сборных конструкций он проявляется гораздо больше. (См. также статью Шпаклевка по бетону: особенности.)
- Время твердения – как не сложно догадаться, у материала изготовленного неавтоклавным методом время твердения значительно больше. Однако,этот недостаток имеет значение только при производстве изделия.
- Выполненный автоклавным методом газобетон более прочный, так как в его составе образуется минералтоберморит. При изготовлении неавтоклавного ячеистого бетона, образование тоберморита невозможно. Поэтому изделие используют в тех случаях, когда на него не предполагаются большие нагрузки.
- Теплоизоляционные свойства неавтоклавного газобетона немного лучше, что связано с большей его пористостью.
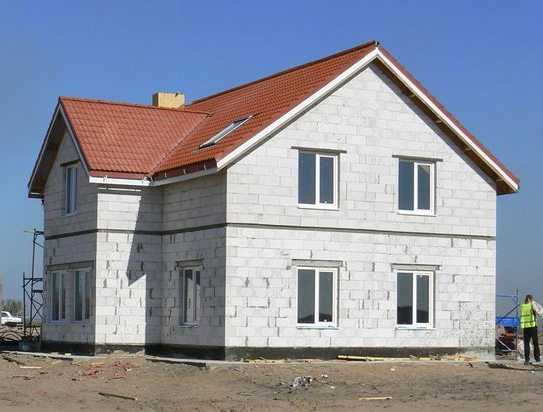
Дом из газобетонного блока
В остальном же характеристики изделий очень схожи.
Обратите внимание!
В продаже зачастую можно встретить газобетон низкого качества, изготовленный «кустарным» способом.
Определить его не сложно, так как он сильно крошится.
Вывод
Не смотря на то, что полученный неавтоклавным методом газобетон появился достаточно давно, благодаря постоянному совершенствованию технологии его изготовления, он может считаться вполне современным материалом. В ряде случаев его использование является более целесообразным, чем применение автоклавного газобетона. Однако, если важна высокая прочность материала, то автоклавный более предпочтителен.
Из видео в этой статье вы можете получить дополнительную информацию по данной теме.
masterabetona.ru