пропорции при производстве — Всё про бетон
Вот уже многие годы такой строительный материал, как опилкобетон используется в строительстве многих сооружений и зданий. Наряду с традиционным бетонным раствором, опилкобетон способен выполнять те же самые функции, что положены и бетону.
Принципиальной разницей в строительных характеристиках такого подтипа бетона не имеется. Отличие состоит лишь в том, что для приготовления раствора традиционного бетона используется щебень и цемент, а для приготовления раствора из опилкобетона — смесь древесных отходов (стружка, опилки).
Данная технология была придумана в советские годы, ближе к шестидесятым годам. Опилкобетон по определению — это одна из разновидностей бетонных смесей, в состав которого входят древесные опилки и стружки. В настоящий момент реализация и производство такого вида бетонного раствора совершенно забыта и не реализуется.
Дело в том, что в начале девяностых годов, во время перестройки, началась программа на блочное и панельное строение всех жилых зданий, а про традиционные виды приготовления строительных материалов было забыто вовсе и считалось издержками старого времени.
Что такое опилкобетон?
Опилкобетон — это строительная смесь, предназначенная для всякого рода производства или возведения стен, укреплений, заливки тех или иных объектов домовладения. Изготавливается опилкобетон как и обыкновенный цементный бетон с щебнем, за исключением того, что в опилкобетоне имеется ряд древесных частиц.
В состав опилкобетона входят:
- Цемент.
- Вода.
- Древесная стружка.
- Песок.
Стоит отметить тот факт, что смесь из опилкобетона, как показывает результат проверки, является натуральным веществом, который не влияет на санитарно-гигиенические условия местности и человека, а также наиболее лучшим строительным материалом для возведения несущих стен и конструкций.
Плотность данного раствора напрямую зависит от компонентов, входящих в его состав. К примеру, если в опилкобетоне содержится большое содержание песочных гранул, то такой песок является наиболее разрушимым и подверженым распаду, а также менее плотным раствором.
По этой причине, к выбору компонентов опилкобетона нужно подходить наиболее качественно и анализировано. К тому же, расчеты на пропорции элементов в опилкобетоне являются основными факторами прочности и качества будущих зданий и сооружений, где данный материал использовался как строительное средство.
Опилкобетон или по-другому арболит является отличным материалом для возведения стен в доме и имеет целый ряд преимуществ в своей эксплуатации:
- Первое, о чем стоит упомянуть — это состав смеси опилкобетона, который влияет на теплосохранение в доме. Опилки с древности считаются лучшим материалом для сохранения тепла, по этой причине и произошло их использование в строительных целях. Хорошая теплопроводность опилкобетона является большим фактором для конкурирования с иными блочными материалами, к примеру, газоликаты или пенобетон.
- За счет своего простейшего состава и грамотной пропорции каждой смеси арболита, его можно использовать как средство в борьбе за шумоизоляцию.
Наличие древесной смеси способствует также и тому, что опилкобетон является наиболее гибким и осадочным строительным средством. Но осадка такого материала относительно мала и варьируется в размерах ГОСТа.
- Многие факторы опилкобетона говорят о том, что данный строительный элемент является легковоспламеняемым, но это вовсе не так. В производстве опилкоблоков применяется определенный ряд химических элементов, которые могут позволить блоку устоять с гнилостными бактериями, также блокирующие и не допускающие процесс разрушения бетона во время его затвердевание.
- Более того, опилкобетон устойчив ко многим факторам влажности. Большой процент увлажнения совершенно не страшен данному типу строительного материала. Поэтому, установка пеноблочных стен разрешена только на уровне земли.
Стоит систематически выделить ряд основных характеристик арбалита (опилкоблока):
- Материал, из которого изготавливает опилкоблок, является абсолютно безвредны и экологически чистым.
- Замечательная теплопроводность и хорошая морозоустойчивостью.
- Не вступает в контакт с различного рода грибками, лишайниками, мхом. Не подвержен гниению за счет наличия химических реагентов, останавливающих результат гниения органических веществ в составе опилкоблока.
- Замечательно просверливается и бурится. Удерживает в своем каркасе шурупы и гвозди.
- Легкая фрезеровка материала, несмотря на его твердость и прочность.
- Состав опилкобетона таков, что его поверхность замечательно контактирует с любого вида штукатуркой и раствором цемента.
- Все грани опилкобетона легко подвергаются раскрашиванию его (каркаса всей стены) в декоративную краску или лак.
- Не имеет свойства возгораться.
- Опилкобетон имеет отличную шумоизоляцию и хорошо подходит для многоквартирных домов.
Область применения опилкобетона
Благодаря наличию таких качеств как, звукоизоляция и теплоудержание, опилкобетон используется в частных домовых строениях и отделке квартирных стен. Можно смело утверждать, что коэффициент теплопроводимости опилкобетона в разы выше, чем у кладки, выполненной из керамического камня. Кроме того, более полувековая история зданий, возведенных из опилкобетона, несомненно, подтверждают качество этого материала и его долговечность.
В начале шестидесятых годов прошлого столетия, опилкобетон широко применялся в строительстве жилых зданий и корпусов предприятий, так как являлся одним из дешевых строительных смесей, производимых на территории СССР.
Но с течением времени, производство опилкобетонного материала стало резко сокращаться в связи с появлением более удобных на тот момент, панельных плит.
Именно они пришли на смену опилкобетонным блокам. На сегодняшний день спрос на опилкобетон вновь возрастает. Связанно это с тем, что началось постепенное увеличение количества строящихся домов и коттеджей.
Как и каждый строительный материал, опилкобетон обладает теми или иными достоинствами или недостатками.
Плюсы:
- Пожалуй, самым большим плюсом данного строительного материала является его низкая себестоимость.
- Опилкобетон может быть использован как в блочной форме, так и в монолитной, заливаемой в обустроенную опалубку. Этот процесс выбора делает строительство дома удобнее.
- Хорошая пожароустойчивость.
- Санитарно-гигиеническая безопасность опилкобетона обусловлена использованием в составе лишь натуральных природных элементов.
- Возможность самостоятельно приготовить сырье и залить в форму блока.
- Высокий коэффициент теплоизоляции.
Минусов у пеноблочного материала не так уж и много:
- Маленькая прочность на сжимание блока.
- Хрупкий состав опилкобетона.
Благодаря таким характеристикам пеноблока, на сегодняшний момент его применяют в строительстве:
- Фундамента.
- Утеплителя стенных перегородок.
- Несущих каркасных стен.
- Забора и столбов.
В случае, если выбранным материалом для строительства дома стал опилкобетон, то не стоит делать более одного этажа.
Состав опилкобетона
В состав такого строительного материала, как опилкобетон входят все основные структурные компоненты бетонного раствора, а это:
- Цемент высшей марки.
- Песок, желательно очищенный от примесей.
- Щебень различной категории формации.
Помимо всего этого, отличительной особенностью опилкобетона является наличие в нем опилок или древесных стружек. Примечательно, что по истечении большого срока времени они вовсе не гниют. Происходит это по той причине, что в состав опилкобетона замешивается некоторое количество химических реагентов, способных остановить реакцию разложения.
Изготовление опилкобетона своими руками
Случается и так, что денежных средств на поставку строительного раствора, в частности опилкобетона, не имеется. В таком случае необходимо прибегать к самостоятельному приготовлению данной смеси. Стоит сказать заранее, что в этом процессе нет ничего сложного, и если приготовление традиционного бетонного раствора не вызывало никаких вопросов, то с приготовлением опилкобетона будет еще проще.
Нужно отметить, что на сегодняшний день сохранилось несколько способов приготовления данной смеси самостоятельно, причем, для каждого вида работы свой тип опилкобетона.
К примеру, для того, чтобы произвести опилкобетон, способный устоять шумовому воздействию, необходимо использовать известь в виде порошка, воду и древесные опилки. Отношение каждого элемента в растворе должно быть на два меньше, чем у первоначального элемента (извести).
Непосредственно процесс приготовления опилкобетона выглядит следующим образом:На заранее приготовленную поверхность нужно высыпать песок, цемент и известь. Все эти элементы нужно тщательно перемешать, пока сухой раствор не станет до конца однородным.
После размешивания сыпучих смесей, необходимо добавить соответствующее количество древесных опилок, а затем добавить воды.
Относительно пропорций каждого материала, входящего в состав опилкобетона, нужно отметить следующие цифры:
- Отношение стружки к извести должно быть в равных количествах, то есть 1:1.
- Отношение цемента и воды — 1:2.
- Песка должно быть столько же, сколько и извести.
Согласно подсчетам, на они кубический метр приготовленной смеси опилкобетона необходимо затратить около 250 — 300 литров воды. Примечательно, что вода должна находится непосредственно в растворе, а не выталкиваться из него на поверхность.
Опилкобетон с использованием марки цемент м-300 станет отличным теплоизолятором для дома. Смесь из цемента марки м-500 применяется как для строительства несущих конструкций стены дома, так и для балконных сооружений или мансард.
Что касается ведерного объема всех элементов опилкобетона, то для производства смеси понадобится:
- 2 ведра древесной стружки и порошковой извести.
- 1 ведро цемента и 2 ведра воды.
- 2 ведра песка.
Производство блоков из опилкобетона
Для того, чтобы самостоятельно производить опилкобетонные блоки необходимо знать как минимум 2 параметра:
- Размеры блоков.
- Состав смеси для опилкобетона.
Так как с составом смеси опилкобетона и его производством уже ознакомлено выше, стоит заострить внимание на форме и размерах будущих опилкобетонных блоков.
Стандартно, размеры блоков имеют величину 200*300*600 миллиметров. Изготовить формочки под такие размеры не составит большого труда. Проще всего соорудить их из деревянных дощечек. Для целесообразности лучше всего соорудить 10-15 таких формочек, чтобы бетонные блоки имелись в наличии каждый день по нескольку штук.
Застывание раствора в формах длится около четырех дней, после чего блок будет полностью готовым к реализации. Стоит сказать и то, что процесс высыхания опилкобетонных блоков должен происходить на открытом воздухе.
Состав и пропорции опилкобетона
Опилкобетон представляет собой разновидность облегченного бетона, состоящего из цемента и опилок. Как строительный материал он стал использоваться около 50 лет назад. В строительстве его применяли не так часто как крупноблочный бетон, а самой большой популярностью опилкобетон пользовался в 90-е годы прошлого века. В настоящее время популярность опилкобетона возрастает благодаря его экологичности.
Технология производства опилкобетона
Для приготовления опилкобетона понадобится вяжущий материал – цемент. В качестве заполнителя используются древесные опилки, смешанные с песком. Опилкобетон это не арболит, как принято считать. В составе арболита нет песка, а вместо опилок используется дробленая щепа.
Для получения все составляющие смешиваются с добавлением воды. Плотность готового блока составляет около 500 кг/м3. Это позволяет применять опилкобетон для строительства одно- или двухэтажных зданий.
Где применяется опилкобетон
Этот материал может использоваться для строительства жилых и нежилых малоэтажных объектов. В основном из него строят загородные дома, коттеджи, гаражи. Себестоимость опилкобетона достаточно низкая. Для его производства не требуются большие энергозатраты. А использование опилок помогает утилизации отходов деревообработки.
Плюсы опилкобетона
-
По санитарно-гигиеническим показателям опилкобетон практически идеальный строительный материал.
-
Опилкобетон обладает высокими теплозащитными качествами. Стена из опилкобетона толщиной в 30 см обладает теми же теплозащитными свойствами, что и кирпичная стена толщиной в 1 метр.
-
Опилкобетон имеет невысокий вес по сравнению с обычным бетоном. Благодаря этому снижается вес всего сооружения и уменьшается нагрузка на фундамент. Для дома из опилкобетона фундамент может быть сделан менее прочным, что уменьшает его стоимость.
-
Опилкобетон обладает хорошей устойчивостью к различным деформациям: удар, растяжение, сгиб.
-
Несмотря на содержание древесины, опликобетон огнестоек. Он способен выдержать в течение нескольких часов температуру в 1200 градусов.
-
Опилкобетон можно легко распилить, просверлить, забить в него гвоздь, в нем не заводится плесень и грибок, он не гниет.
Минус опилкобетона
Главный минус — опилкобетон поглощает влагу. Материал высокого качества впитывает меньше влаги. Показатель водопоглощения зависит от плотности блоков и составляет от 8 до 12%. Использование специальных водоотталкивающих составов способно снизить этот показатель до 2%.
Если сравнивать опилкобетон с другими строительными материалами по проценту поглощения влаги, то самые сухие материалы: глиняный кирпич и железобетон. Такими же водопоглощающими свойствами, как и опилкобетон обладают керамзитобетон, полистеролбетон, пенобетон, пеносиликат.
Водопоглощение можно считать несущественным недостатком опилкобетона, так как с ним можно справиться путем дополнительной обработки материала.
Какие опилки подойдут для опилкобетона
Преимущественно используются опилки деревьев хвойных пород, размер их может составлять от 1 до 5 мм. Хвойные опилки меньше всего подвержены биоразложению и обладают хорошей текучестью из-за однородного гранулированного строения. Лучшими характеристиками для создания опилкобетонной смеси обладают еловые опилки.
От породы дерева зависит время схватывания опилкобетона. Смесь из еловых опилок застывает за 10 часов, из сосновых за 15 часов, а из лиственничных за 4 дня.
Для уменьшения влияния водорастворимых органических элементов на связующее вещество цемент опилки необходимо обработать. Наиболее затратным по времени способом является их вымачивание в воде и последующее высушивание. Еще их можно оставить под лучами солнца, но опилки из хвойных пород будут окисляться около 3 месяцев.
Обработка опилок жидким стеклом или хлористым кальцием – наиболее быстрый и эффективный метод. Жидкое стекло позволяет опилкам быстрее затвердевать, а хлористый кальций делает их в 2 раза прочнее.
Также в опилки можно добавлять аммиачную селитру, хлористый алюминий, сернокислый натрий. Добавки вводятся в пропорции 1 часть химикатов к 40 частям опилок. Содержание химикатов не должно превышать 4% от общей массы опилок.
Технология начальной стадии приготовления опилкобетона
В качестве вяжущего вещества опилкобетона используется цемент с известью и глиной, такой состав обеспечивает хорошую эластичность и облегчает формирование блоков.
Песок в опилкобетоне гарантирует прочность и снижает усадку во время высушивания блоков. Добавляют его в пропорции 3 части песка на 1 часть вяжущих компонентов. Песок использует только чистый без каких-либо примесей. Речной песок лучше не использовать, так как он будет плохо сцепляться со всеми компонентами смеси.
По составу опилкобетон может быть разнообразным и отличается количественным и качественным составом всех компонентов. Цемент один из главных компонентов опилкобетона. При его недостатке снизится качество строительного материала: он станет менее морозоустойчивым, увеличится водопроницаемость и снизится плотность. Увеличение количества цемента приведет к удорожанию готовой смеси.
Марки опилкобетона и пропорции на 200 кг опилок
Марка опилкобетона |
Цемент, кг |
Песок, кг |
Известь (глина), кг |
Плотность, кг/м3 |
М5 |
50 |
50 |
200 |
500 |
М10 |
100 |
200 |
150 |
650 |
М15 |
150 |
350 |
100 |
800 |
М20 |
200 |
500 |
50 |
950 |
Данные марки опилкобетона используют для следующих работ:
- М5 и М10 обладают высокими теплоизоляционными свойствами и лучше всего подходят для строительства подвалов;
- М15 и М20 более прочные, водонепроницаемые и морозоустойчивые, поэтому из них возводят наружные стены.
Порядок изготовления опилкобетона своими руками
Благодаря своей доступности, простоте в изготовлении, хорошим характеристикам опилкобетон стал популярным материалом для индивидуального строительства. Для получения качественного опилкобетона необходимо строго соблюдать порядок проведения работ.
-
Взять необходимое количество вяжущих компонентов и песка в сухом виде и перемещать.
-
В полученную смесь добавить необходимое количество просеянных опилок и перемешать.
-
С помощью разбрызгивателя постепенно ввести вводу. Массу необходимо постоянно перемешивать до получения нужной консистенции.
Полученный состав используется сразу же, так как через час он начинает затвердевать. Облегчить процесс приготовления смеси поможет бетономешалка.
Использовать опилкобетон можно двумя способами:
- делать блоки;
- заливать монолитные стены.
Как рассчитать количество воды
Количество воды напрямую зависит от степени высушенности опилок и песка, поэтому сначала нужно сделать небольшое количество пробной смеси. Качественная смесь при сжимании не должна отдавать воду. Если получается отжать воду рукой, ее количество должно быть уменьшено. Если комок смеси в руке распадается на несколько частей – следует добавить воды. Получив эластичную массу пробной партии можно рассчитать необходимое количество воды.
В среднем для производства опилкобетона требуется от 250 до 350 л/м3. Для получения опилкобетона марок М5 и М10 требуется большее количество воды. Чем больше опилок в составе, тем выше водопоглощение. Для опилкобетона марок М15 и М2о и при использовании хорошо высушенных опилок потребуется воды не более 250 л/м3 .
Формирование блоков опилкобетона
Опилкобетон затвердевает достаточно долго и марочную прочность достигает спустя 3 месяца. По этой причине более рационально для строительства использовать высушенные блоки. При возведении стен в опалубке опилкобетон может деформироваться от надавливания.
Стандартами не установлены размеры блоков опилкобетона, поэтому их выбирают в зависимости от способа укладки, ширины стен, расстояний от углов и размеров проемов. Оптимальной считается толщина блока 140 мм. Такая толщина позволяет дополнительно использовать в кладке красный обожженный кирпич.
Форму для блоков можно изготовить из досок, внутри покрытых пластиком или листом стали. Это не позволит древесине впитать влагу из опилкобетона и тем самым пересушить его. Для ускорения сушки материала и улучшению его теплоизоляционных свойств можно предусмотреть 2-3 отверстия внутри блоков. Сделать их можно с помощью скрученных листов толи или обычных бутылок.
Смесь укладывают в форму, тщательно утрамбовывая, чтобы внутри не оставались воздушные пустоты. Для сушки необходима температура воздуха не менее 15 градусов. Через 3 дня блок проверяют, проведя по нему острым концом гвоздя. Если на поверхности не остается глубокая царапина, то блок можно вынуть из формы и сушить на открытом воздухе еще не менее трех дней.
Готовый высушенный блок не должен иметь трещин, пустот, сколов. При падении с высоты 1 м он остается целым.
youtube.com/embed/IHsniwvHKeU» frameborder=»0″/>
Как эффективно высушить блоки опилкобетона
Через 3 дня высушивания в деревянной форме блоки приобретают около 30% от марочной прочности. После их выемки и дальнейшего высушивания в течение 3-4 дней их прочность составляет около 70%.
Чтобы улучшить качество блоков необходимо учесть следующее:
- сквозняк улучшает сушку;
- при укладывании блоков для сушки, между ними должны оставаться зазоры;
- если блоки сушатся под открытым воздухом, их необходимо укрыть пленкой от дождя.
Завершающим этапом сушки является выкладывание из блоков столбов. Каждый ряд делают из двух блоков, уложенных попрек к предыдущему. Через месяц блоки приобретут плотность равную 90% от марочной, а полностью затвердеют спустя 3 месяца.
Правила получения качественного опилкобетона
- Опилки не должны содержать никаких посторонних включений. Для этого их просеивают сначала через сито с отверстиями в 1 см, затем через сито с отверстиями 0,5 см.
- Использовать лучше всего цемент марки 400.
- Для вымешивания смеси необходимо использовать бетономешалку. Вручную получить однородную смесь невозможно.
- Смесь в формах необходимо утрамбовывать ручным или механическим способом.
- Упростить извлечение готового блока из формы поможет набитый на внутренние стенки линолеум.
- После выемки из форм на открытом воздухе блоки сушатся минимум 10 дней.
пропорции, состав, как готовить раствор
Отличные характеристики и состав опилкобетона позволяют применять его в строительстве монолита и мелких стеновых блоков малоэтажных зданий. Опилки — продукт органических отходов, поэтому теплоотдача нового строительного материала больше, чем обычного бетона. Поскольку на строительном рынке такого материала нет, строители изготавливают его сами. Однако к опилкобетонным блокам применяют требования ГОСТа 6133–99, как и к другим бетонным камням. Поэтому нужно знать технологию изготовления и придерживаться указанных пропорций.
Посмотреть «ГОСТ 6133-99» или cкачать в PDF (2.4 MB)
Состав и марки
Компонентами этого строительного материала являются:
- Цемент, выполняющий роль вяжущего вещества, который должен в соответствии с ГОСТом 10178−85 не ниже М400.
- Крупный и средний песок, отвечающего ГОСТу 8736—93.
- Опилки всех пород деревьев, преимущественно хвойных, поддающихся меньшему гниению.
- Добавки: известь, глина, сульфат аммония, жидкое натриевое стекло. Но наиболее подходит требованиям ГОСТ присоединение кальция хлорида.
- Вода незагрязненная — ГОСТ 23732–79.
Посмотреть «ГОСТ 10178-85» или cкачать в PDF (181.6 KB)
Посмотреть «ГОСТ 8736-93» или cкачать в PDF (557.4 KB)
Посмотреть «ГОСТ 23732-79» или cкачать в PDF (117.1 KB)
Плотность опилкобетона зависит от количества, в первую очередь, песка, который вместе с другими добавками повышает качественные показатели материала.
Название | Плотность, т/м3 | Коэффициент теплопроводности |
М5 | 0,6 | 0,18 |
М10 | до 0,8 | 0,21 |
М15 | 0,8 | 0,24 |
М20 | 0,95 | 0,3 |
Плюсы и минусы
Бетон с опилками обладает уникальными качествами по сравнению с другими строительными материалами:
При своей простоте материал обладает завидными характеристиками.
- экологическая безопасность применения;
- легкий вес;
- необходимые показатели удержания тепла;
- простая обработка при строительстве;
- стойкость на прочность растяжения и изгиба;
- народный (доступный) состав.
Однако присутствуют и недостатки:
- Достаточная степень впитывания влаги, требующая проведения работ во избежание этого.
- Возрастание финансовых затрат в строительстве многоэтажных зданий из-за прибавления цемента. Дом из опилкобетона, который набрал природную прочность, будет качественнее, чем из бетона обычного.
- Большая вероятность усадки затрудняет работы по отделке.
Какой расход и пропорции?
Название | Опилки | Песок | Цемент | Известь или глина | Пропорции (цемент, песок, опилки, известь) |
М5 | 80 | 3 | 4,5 | 14 | 1:0:2:1 |
М10 | 80 | 12 | 9,5 | 10,5 | 1:2,2:6,5:1,5 |
М15 | 80 | 21 | 13,5 | 7 | 1,2:3:7,8:0,8 |
М25 | 80 | 30 | 18 | 35 | 1:2,8:6,4:0,8 |
Как готовить раствор?
Выбрав любой из двух методов изготовления, можно получить качественный материал.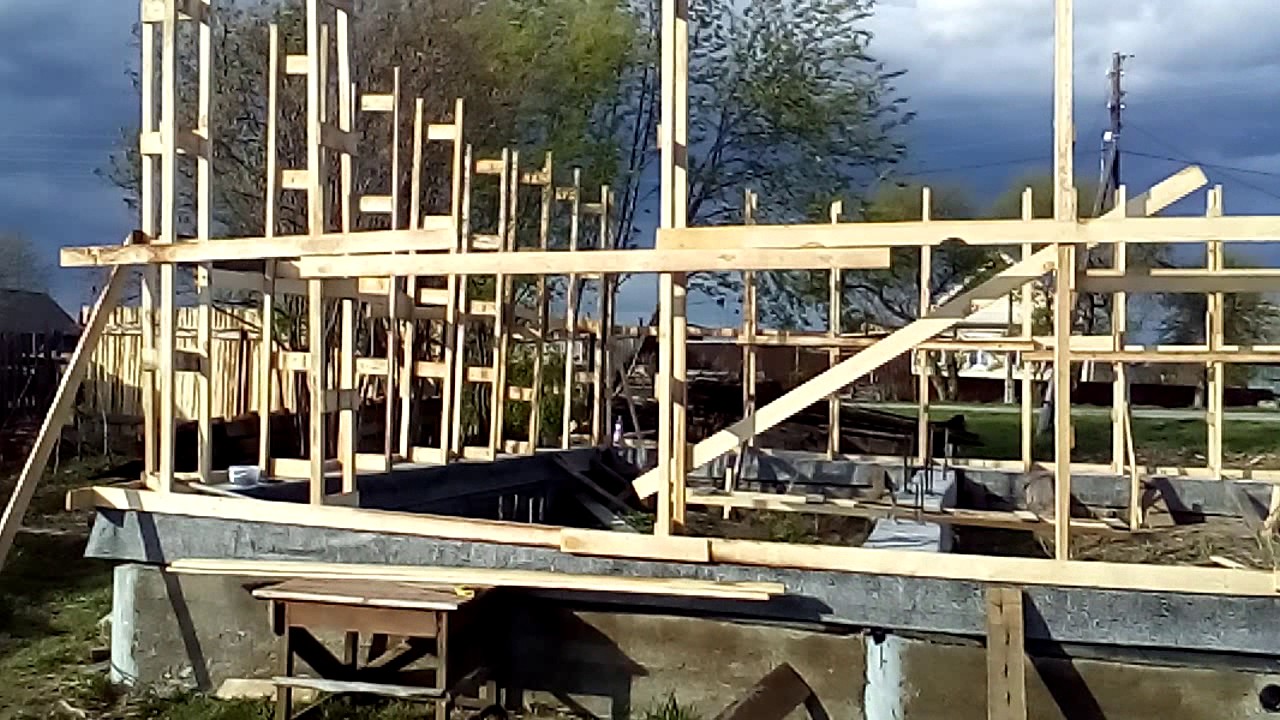
Для строительства жилых зданий и хозяйственных построек несложно изготовить опилкобетон своими руками. Используют 2 способа присоединения компонентов:
- Разводят в цемент в воде, а потом добавляют остальные ингредиенты.
- Смешивают сухие вещества и разбавляют водой.
Нет преимущества выбора варианта приготовления. Важно, чтобы образовалась однородная структура, в состав которой входят песок и цемент, образующие цементный камень. При самостоятельном изготовлении бетономешалка не понадобится, так как ручной способ — удобный, хотя и трудоемкий процесс. Сжатая в кулаке правильно приготовленная смесь не выделяет капель воды.
Опилкобетон: состав, пропорции, изготовление | Блоки
Разнообразие строительных материалов продиктовано поиском наиболее дешевых, простых в производстве и экологичных вариантов. Одной из интересных, но далеко не новых, технологий является производство опилкобетона. Он применяется в монолитном и блочном домостроении. Рассмотрим его основные характеристики и технологию изготовления.
Характеристика опилкобетона
В состав смеси входит вода, строительный песок, опилки и цемент; так же возможно применение дополнительных веществ. Благодаря натуральности компонентов материал получается экологически чистым. Процентное содержание опилок может достигать 70%. При этом материал не поддерживает горение, благодаря цементной оболочке. Сопротивление огню длится 3 часов при температуре 1200 °C.
Влагопоглощение материала составляет от 8 до 12%. Достигается показатель путем вымачивания опилок в жидком стекле. Низкая гигроскопичность увеличивает морозостойкость. При самых низких показателях влагопоглощения сопротивление минусовым температурам до 100 циклов.
Показатель теплопроводности экологичного бетона составляет 0,32 Вт/м°С. Для сравнения — 40 см стены из опилкобетона заменяют по 1 метр кирпичной кладки.
Конструкции, из рассматриваемого материала, имеют высокую сопротивляемость к механическим воздействиям. Опилки выступают, своего рода, арматурой, добавляя изделиям стойкость к растяжению.
Работать с опилкобетоном достаточно просто. Для обработки не нужны специальные приспособления. Материал можно, сверлить, забивать гвозди, резать фрезой или ножовкой. Опилкобетонные блоки применяются как для одноэтажного строительства, так и для домов до 4 этажей. В зависимости от конструктивных нагрузок используются различные маркировка, которая формируется исходя из соотношения компонентов
Таблица пропорций составляющих опилкобетона
Марка | Соотношение компонентов в указанном порядке (цемент, известь, песок, сухие опилки) |
5 | 1:1:0:2 |
10 | 1:2:8 |
15 | 1:1,2:5 |
25 | 1:1:1,2:4 |
При строительстве нужно помнить: чем меньше содержание опилок, тем прочнее изделие. При этом тепло- и шумоизоляционные свойства снижаются. Вес рассматриваемого бетона ниже многих строительных материалов, что позволяет уменьшить нагрузку на фундамент. Также отпадает необходимость в применении спецтехники.
Технология изготовления опилкобетона
Кратко рассмотрим производство блоков из опилкобетона своими руками. Для начала работ из доски сбивается опалубка размером 390*190*190 мм. Чтобы блок лучше извлекался, на внутреннюю сторону короба набивают линолеум. Готовить сырье желательно при помощи бетономешалки. В таком случае блоки будут более однородными, что понизит водопоглащение. Вначале перемешиваются сухие компоненты, массовая доля которых зависит от необходимого объема готового продукта. В качестве наполнителя применяются опилки деревьев хвойных пород. Перед добавлением они вымачиваются в известковом растворе или жидком стекле.
Пропорции для раствора извести
- Опилки — 1 м3;
- Вода — 150-200 литров, в зависимости от влажности опилок;
- Известь — 2,5 кг.
Лучше применять цемент марки 400. Добавки должны составлять не более 3% от массы цемента. После перемешивания сухих составляющих, добавляется вода. Она вливается небольшими дозами при помощи лейки. Готовая смесь, при сжатии в руке, не должна рассыпаться. Но и просачивание воды сквозь пальцы недопустимо. Бетон должен получиться однородным и пластичным.
В форме смесь уплотняется вибратором или вручную. Также для уплотнения массы применяются вибрационные столы. На вторые сутки блоки вынимаются из опалубки. Дальнейшая сушка происходит на улице в течение 10-14 дней при ясной погоде. Равномерность схватывания достигается периодическим смачиванием изделий.
Опилкобетон: состав, пропорции
Опилкобетон является экологически чистым материалом, и не оказывает вреда человеку. Такой материал имеет высокую звукоизоляцию, теплоизоляцию, а также паропроницаемость. В состав опилкобетона входят деревянные материалы, которые способствуют сохранению тепла в помещении.
Характеристика и преимущества опилкобетона
Опилкобетон может быть двух видов, теплоизоляционный, плотность которого может составлять 400-800 кг/м3, и конструкционный тип – 800-1200 кг/м3.
Материал становиться прочнее при плюсовой температуре, и повышенной влажности, при этом она медленно испаряется, и образуется цементный камень.
Опилкобетон отличается наличием положительных качеств
- Основные компоненты, из которых состоит материал, не имеют высокую цену, это помогает сэкономить.
- Для изготовления не требуется специальных знаний и навыков.
- Опилкобетон имеет повышенную устойчивость к морозам, влажности, и изменению температур.
- Материал экологически чистый, не выделяет токсические элементы, имеет повышенный уровень тепловой защиты, и является долговечным.
- Благодаря опилкам, входящим в состав материала, опилкобетон отличается повышенной прочностью.
Состав и производство опилкобетона
При производстве опилкобетона используют опилки таких деревьев, в которых показатель сахара является минимальным, это может быть сосна, береза, ель или тополь.
Деревья лиственные имеют самые высокие показатели сахара, поэтому их используют в последнюю очередь, при отсутствии других материалов. При использовании ели, материал начинает набирать прочность спустя две недели после застывания бетона. А лиственные деревья начинают набирать прочность спустя тридцать дней. То есть работу по укладке и заливке опилкобетона необходимо провести ещё в осенний период, чтобы до осени материал набрал прочность.
Перед приготовлением материала, опилки расстилают на открытом воздухе, и поливают водой, чтобы наибольшее количество сахара смылось. После двух раз такой промывки, опилки можно использовать для изготовления материал. Благодаря своей структуре, и всем остальным составляющим компонентам, опилки не подвергаются гниению, горению, и являются устойчивыми к влажности.
Опилкобетон состоит из таких компонентов, как опилки, гашеная известь, цемент и песок, от их пропорций изменяется марка материала. Для изготовления каждой марки опилкобетона потребуются определенные пропорции.
Пропорции компонентов в опилкобетоне
При производстве материала используют следующие пропорции компонентов:
- Для марки М10 используют опилки 3 части, песок 1 часть, цемент 0,5 части.
- Марка М15: опилки 4 части, песок 1,5 части, цемент 0,5 части.
- Для марки М25: опилки 3 части, песок 1,5 части, цемент 0,5 части.
Известь гашеного вида используется для удаления сахара в опилках, её добавляют в необходимом количестве. Все пропорции должны точно соблюдаться, чтобы материал получился качественным.
Как приготовить состав для опилкобетона?
Приготавливают смесь для опилкобетона вручную, обычную бетономешалку не используют, так как компоненты, входящие в состав материала, являются легкими, они будут оставаться на стенах или вовсе плавать сверху на воде.
Порядок добавления компонентов можно использовать любой, например, цемент разводят с водой, затем добавляют песок, известь и опилки. Можно опилки тщательно размешать с известью, добавить все остальные компоненты, и залить водой.
При смешивании нет разницы, в какой последовательности будут добавлены материалы, в результате должен получиться состав однородного вида. Благодаря песку и цементу, создается прочный цементный камень. Опилки являются наполнителем, а известь способствует уменьшению в них сахара. Опилкам не страшна влага, так как они проходят предварительную обработку известью.
Материал, в основе которого гипсовый вяжущий компонент
Также производят состав на основе гипса, его используют вместо цемента, несмотря на то, что он имеет способность быстро застывать.
Эту проблему можно разрешить, если в воду добавить моющее средство. Гипс, строительного вида, при соединении с водой, создает твердую структуру, которая является устойчивой к влажности.
Из такого материала можно сооружать стены внутри здания, так они будут защищены от агрессивных осадков, и перемены температуры. Также состав из гипсового материала будет иметь цену выше, чем из цемента.
Какими должны быть опилки для опилкобетона?
При обилии вяжущего компонента, размер наполнительного материала, то есть опилок, не играет роли. Опилки могут быть разного размера, стружка со станков оцилиндрованного вида не используется.
Смесь не будет однородной, если в одном замесе опилки будут иметь различную фракцию. Состав необходимо замесить так, чтобы после сжатия в кулаке, из него не вытекала жидкость, и не происходило рассыпание. Такой компонент, как известь способствует хорошему соединению всех компонентов, благодаря этому состав имеет однородность.
Где применяется опилкобетон?
Опилкобетон производить гораздо легче, чем остальные строительные материалы, он является экономичным, и изготавливается вручную, без дополнительной техники. Такой материал является экологически чистым, так как состоит из натуральных компонентов, отличается прочностью и практичностью.
С помощью опилкобетона можно сооружать здания до трех этажей, постройки хозяйственного и бытового характера, жилые помещения или гаражи. Строение из такого материала необходимо отделывать снаружи, обычно применяют штукатурку, для жилых зданий стены можно задекорировать. Несмотря на то, что блоки состоят из опилок, они не поглощают влагу, благодаря остальным компонентам. Материал не нуждается в утеплении, так как имеет высокий показатель теплоизоляции.
Опилки можно приобрести на специальных предприятиях, которые занимаются обработкой дерева, этот материал не является дорогостоящим.
Как изготовить блоки из опилкобетона?
Вначале необходимо приготовить состав, для этого опилки тщательно высушивают, пропускают через сито с ячейками 10 на 10 миллиметров. После этого производят смешивание всех компонентов в однородный состав.
Приготовленный состав однородного вида, укладывают в формы, и утрамбовывают так, чтобы внутри не скапливался воздух. Утрамбовку можно производить ручным или механическим методом, при этом состав должен тщательно уплотниться.
По размерам опилкобетон совпадает со шлакоблоком, поэтому формы и оборудование могут быть аналогичными.
Чтобы убрать пустоту из блоков, и выпустить весь скопившийся воздух, в смесь помещают два штыря. Стоимость одного блока является достаточно низкой по сравнению с остальными материалами, то есть шлакоблоком, газобетоном или пенобетоном. Состав необходимо раскладывать по формам сразу после приготовления, так как спустя 1,5 часа раствор начинает застывать.
Блоки из опилкобетона отличаются универсальностью, при строительстве не нужно возводить дополнительные опалубки, то есть сэкономить время и силы. Блоки сушат на протяжении трех месяцев, это дает возможность набрать им прочности, и соответствовать своей марки. После заливки форм опилкобетоном, блоки вынимают спустя пять дней, а затем оставляют для окончательного просушивания. Для того чтобы работа происходила быстрее, производят заливку сразу по несколько десятков блоков.
При изготовлении крупных блоков, используют формы разборного вида. Из деревянного материала сбивают специальные ящики, доски должны иметь толщину не меньше 20 миллиметров, чтобы под давлением раствора форма не развалилась.
Для блоков среднего или стандартного размера изготавливают формы в виде совместных ячеек, из досок толщиной от 20 миллиметров. В качестве крепления используют специальные стержни и гайки, а внутри выполняют пазы задвижного вида.
Выполнение монолитной заливки с помощью опилкобетона
Заливку производят при изготовлении крупных объемов материала. То есть если есть возможность залить сразу всю опалубку по периметру, с учетом её высоты. После заливки раствора, его тщательно утрамбовывают, для этого используют приборы из бруса, которые немного заостряются в нижней части.
Для того чтобы выполнить монолитную заливку, необходимо подготовить широкое корыто, которое имеет плоское дно, миксер ручного типа, и необходимые компоненты.
При этом не нужно изготавливать блоки, ожидать их высушивания, и выполнять работы по укладке. Монолитное строительство происходит быстрее.
состав и свойства, особенности технологии производства опилкоблоков, плюсы и недостатки
Опилкобетон представляет собой популярный строительный материал, который нашел широкое применение в разных направлениях монолитного строительства еще задолго до появления пенобетона. В настоящее время его используют при возведении стеновых блоков для построек, не превышающих высоту в 3 этажа. Технология производства опилкобетона несложная, поэтому его часто создают в домашних условиях.
Общая информация
Многие люди даже не догадываются, что представляет собой бетон с опилками, как называется материал в официальной терминологии и в чем кроются его сильные стороны. На самом деле, среди различных типов легкого строительного сырья опилкобетон является наиболее распространенным. Его создают на основе древесных опилок, что обеспечивает ему низкую плотность и ряд эксплуатационных преимуществ. История появления уходит своими корнями в 60-е года прошлого столетия, а родиной стал бывший Советский Союз.
После прохождения всех испытаний в лабораторных условиях материал получил сертификацию и начал поступать в продажу. При этом массовый спрос появился только в середине 90-х, когда строители оценили массу уникальных свойств и плюсов опилкобетона.
Среди ключевых преимуществ данного сырья выделяют:
- Экологическую безопасность.
- Устойчивость к воздействиям огня.
- Прочность.
- Паронепронецаемость.
- Морозостойкость.
- Дешевизну.
Сферы применения опилкобетона очень широкие, поэтому его активно внедряют при возведении частных домов, построек хозяйственного назначения и других помещений с небольшим количеством этажей.
Кроме этого, материал может использоваться для ремонтных работ и в качестве хорошего утеплителя. Реконструкция зданий с применением опилкобетона не требует дополнительного укрепления фундамента.
Если постройка создается на основе этого материала, можно применять практически любые проекты, разработанные для любого другого сырья. При этом строительные работы обойдутся гораздо дешевле, т. к. из-за небольшого веса необходимость возводить сложные фундаменты автоматически исчезнет.
Особенности и состав
Из названия становится понятно, что ключевой составляющей опилкобетона являются древесные опилки. Также в составе материала присутствуют и другие элементы, включая:
- Песок.
- Цемент.
- Глину или известь.
Экологическая безопасность и соответствие всем современным требованиям позволяют использовать опилкобетон для строительства стеновых конструкций жилых домов.
Что касается показателей плотности, то они определяются соотношением опилок и песка. В результате, чем больше в составе опилкобетона песка и других вяжущих элементов, тем выше показатели плотности.
Также этот параметр повышает прочность, но ухудшает теплотехнические свойства. Чем больше опилок входит в состав материала, тем хуже его морозостойкость и водонепронецаемость. В конечном итоге опилкобетон становится уязвимым ко всевозможным коррозийным процессам, что тоже является весомым недостатком. Создавать арматуру из некачественного материала нельзя, так как она не будет справляться со своими обязанностями и принимать внешние нагрузки.
Учитывая эти особенности, перед тем как приступить к строительству, следует тщательно разобраться с составом опилкобетона и изучить влияние конкретных элементов на эксплуатационные свойства.
При выборе тех или иных составов нужно учитывать толщину будущих стен, их назначение, а также количество этажей.
В зависимости от пропорций, которые используются при смешивании составляющих опилкобетона, конечный продукт может обладать разной маркой. В настоящее время выделяют такие наименования:
- М5. 100-килограммовый состав опилок разбавляется 25 кг цемента, 25 кг песка и 100 кг извести или глины. Показатели плотности равны 500 кг на кубический метр.
- М10. В 100 кг опилок находится 50 кг цемента, 100 кг песка и 75 известкового сырья. Показатели плотности составляют 650 кг на метр кубический.
- М15. На сто килограмм древесных опилок приходится около 75 кг цемента, 175 кг песка, 50 кг извести или глины. Плотность равна 800 кг на метр кубический.
Первые две марки задействуются при сооружении стеновых блоков для реконструкционных, утепляющих или строительных работ в подвалах, что объясняется их прекрасными теплоизоляционными свойствами. Третья марка незаменима при обустройстве стен внутреннего или наружного типа.
Заготовка материала
Технология производства опилкобетона отличается особой простотой, поэтому ее несложно освоить в домашних условиях. Главным преимуществом самодельной разработки является тот факт, что все составляющие не нуждаются в заготовке и продаются в готовом виде в любом гипермаркете или на рынке. Все, что требуется для будущей работы:
- Опилки.
- Песок.
- Цемент.
- Глина или известь.
Несмотря на простоту предстоящей процедуры, некоторые этапы нуждаются в особом подходе и требуют больших усилий.
Одним из наиболее сложных шагов является смешивание компонентов. Для упрощения задачи лучше применить качественную бетономешалку или растворосмеситель. В результате работа будет не только удобной, но и более быстрой. При этом конечный продукт получит высокое качество и эксплуатационные свойства.
Перед засыпанием древесных опилок в контейнер бетономешалки необходимо тщательно очистить их от крупных частиц с помощью сита с 1-сантиметровыми ячейками. Только после этого материал можно смешивать с цементом, глиной или известью. После размешивания компоненты разводятся водой, которая добавляется небольшими порциями.
В конечном итоге жижу еще раз размешивают до образования густой консистенции. Что касается пропорций, то они зависят от индивидуальных особенностей проекта и назначения будущей конструкции. Достаточно придерживаться простого алгоритма: чем больше нагрузка будет на блоки, тем плотнее и прочнее должен быть материал.
Качественный опилкобетон должен превращаться в пластичный комок при сжатии в руке. Именно это состояние является главным подтверждением высокого качества и правильной пропорции.
Формирование блоков
Готовую смесь нужно поместить в заранее подготовленные формы. Главное — не откладывать эту работу на будущее, так как через 1−2 часа консистенция станет слишком густой. В формах блоки могут оставаться не дольше 4−5 дней, после чего каркас нужно снять, а конструкцию переместить для просушивания в течение 30 суток. По окончании установленных сроков можно начинать работу с блоками, при этом полное высушивание произойдет только через 90 суток, поэтому с облицовочными мероприятиями лучше не спешить.
Как известно, стружкобетон широко применяется в разных направлениях монолитного строительства, в том числе и вместе с опалубками. Но в большинстве случаев специалисты отдают предпочтение не монолитному материалу, а блочному. Его создают с помощью заранее подготовленных форм, куда помещаются основные составляющие. Учитывая продолжительность процесса высыхания, лучше создать не меньше 10−20 заготовок.
При производстве крупноразмерных материалов берутся разборные двойные формы в виде деревянных ящиков с разъемной конструкцией. Для их изготовления можно брать доски толщиной два сантиметра, при этом отдельные составляющие конструкции лучше соединить Г-образными стальными стержнями с резьбой М8.
Небольшие блоки создаются в «остовых» каркасах из аналогичных досок диаметром 20 миллиметров. В большинстве случаев форма обладает девятью ячейками, при этом их можно менять в зависимости от индивидуальных предпочтений и особенностей проекта. Доски из внутренней части фиксируются посредством задвижных пазов, а в наружной — с помощью Г-образных стержней.
Чтобы предотвратить впитывание влаги, конструкцию нужно обработать пластиком или сталью. Также можно использовать обычный полиэтилен, что не просто предотвратит проникновение влаги, но и упростит вынимание готовых блоков.
Подсчет размеров
Точные показатели размеров опилкобетоновых блоков зависят от разных особенностей. В их числе:
- Толщина стен.
- Ширина проемов и простенков.
- Расстояние между проемами и углами.
- Способ укладки.
Чтобы сделать строительные работы максимально удобными и быстрыми, длину участков стеновых конструкций нужно установить таким образом, чтобы она соответствовала размерам блоков.
Многие строители используют классический способ унификации, который определяется по такому алгоритму: 140 мм — две толщины красного кирпича и раствор между ними. Чтобы ускорить процесс высыхания блоков и улучшить их теплоизоляционные свойства, в материале нужно сделать не меньше двух-трех отверстий.
Также важно помнить о том, что после высыхания блоки поддаются усушке, поэтому внутренние размеры заготовок должны на 10% превышать размер блоков. Например, для материала с габаритами 120х250х140 следует подготавливать ячейку размерами 132х275х154 миллиметра.
Перед заполнением форм смесью опилкобетона ее нужно поместить на ровный поддон из пластика или стали. После этого внутрь ячеек следует установить пробки, обернутые толем, что позволит проделать отверстия в блоках.
После помещения смеси в заготовку ее надо утрамбовать специальной трамбовкой. В течение следующих 3−5 суток опилкобетон будет приобретать требуемую форму, а показатели прочности будут соответствовать 30−40 процентам от заводской. По завершении этого времени форму можно разобрать, а также извлечь из блоков пробки. Готовые изделия оставляют на этом же месте еще на 3−4 дня. В конечном итоге они получат около 60−70 процентов заводской прочности.
Завершающий этап
Когда опилкобетон будет готов, остается тщательно его просушить. Чтобы завершить сушку, блоки помещаются под навес или укрываются пленкой из полиэтилена. Лучше перенести их в помещение со сквозняками, что ускорит процесс просушки. При укладывании блоков между ними оставляются небольшие вентиляционные зазоры. Укладочные работы осуществляются столбчатым методом.
Изначально на два кирпича нужно поместить два стеновых блока, а затем еще два поперек — и так далее.
Через 30 суток конструкция должна полностью затвердеть и высохнуть, достигнув 90% прочности. Чтобы добиться максимальной прочности, лучше выждать 90 дней и только после этого приступать к строительным работам.
Будет ли соблюден этот срок или нет — индивидуальное желание строителей. В этом случае следует учитывать тип и предназначение здания, для которого создаются блоки. Если говорить о банях из древесного бетона, то можно не дожидаться, пока материал получит 100% прочность. Главное — чтобы в конструкции не было трещин, сколов и прочих деформаций. Полностью готовые блоки должны обладать максимальной твердостью и не повреждаться при падении с высоты одного метра.
Если учесть отзывы профессиональных строителей и перечесть преимущества материала, то можно с уверенностью заявить, что он является достойной альтернативой для более дорогостоящих строительных продуктов. Без сомнений, главным достоинством опилкобетона является его экологическая безопасность и отличные теплоизоляционные свойства. За счет последнего плюса при сооружении стеновых конструкций нет необходимости дополнительно утеплять их, что обеспечивает максимальную экономию и избавляет владельца объекта от многих затрат.
Если рассматривать стружкобетон в качестве утеплителя, в этом плане у него практически нет конкурентов. Для примера, стена из опилкобетона толщиной 30 сантиметров способна сохранять тепло точно так же, как метровая кирпичная стена. Без сомнений, это превосходный показатель, который расширяет сферы применения материала и делает его более популярным.
К тому же, небольшой вес заметно снижает нагрузку на фундамент, поэтому возведение этой части дома требует меньших затрат и усилий.
Также опилкоблоки обладают большим сроком службы и надежностью, что, несомненно, высоко оценивается строителями. Помещения, изготовленные из этого сырья, всегда славятся надежностью, долговечностью и устойчивостью к любым воздействиям.
состав, характеристики, плюсы и минусы
1. Состав.
Представим базовый состав опилкобетонной смеси с удельным весом 1100 кг/м 3 в виде таблицы.
Наименование материала | Масса, кг | % от массы | Объём, л | % от объёма |
---|---|---|---|---|
Цемент М400 | 200 | 18,2 | 166 | 11,4 |
Песок | 590 | 54 | 393 | 26,7 |
Опилки | 200 | 18,2 | 800 | 54,8 |
Хлористый кальций и др. добавки | 5 | 0,5 | 4,5 | 0,3 |
Вода | 100 | 9,1 | 100 | 6,8 |
1.1. Цемент.
Рекомендуется применение цемента марки не ниже чем М-400 (ГОСТ 10178-85).
1.2. Песок.
В качестве основного наполнителя используется песок крупной или средней фракций (ГОСТ 8736-93), создающий прочный скелет блока, в который рекомендуется добавлять мелкий песок, доля которого не должна превышать 10%.
1.3. Опилки.
Возможно применение опилок практически всех пород деревьев. Предпочтительнее использование хвойных, поскольку они меньше подвержены гниению. Перед применением опилки желательно выдерживать под навесом в течение 2-3 месяцев. В случае использования опилок без предварительной выдержки необходима их обработка в смесителе защитными составами.
1.4. Основные добавки.
Для нейтрализации органических веществ, выделяемых опилками, и для сокращения времени затвердевания опилкобетона необходимо применение добавок: извести, сульфата аммония, жидкого натриевого стекла. Наиболее эффективным является добавление хлорида кальция (ГОСТ 450-77).
1.5. Вода.
Желательно применение воды, не загрязненной примесями (ГОСТ 23732-79). При умеренном содержании солей возможно использование морской воды.
2. Классификация.
Опилкобетонные блоки (как и любые стеновые бетонные камни) должны соответствовать ГОСТ 6133-99. Их можно классифицировать по следующим параметрам.
2.1. Применение.
- Стеновые блоки предназначены для кладки наружных и внутренних стен.
- Перегородочные блоки – для кладки перегородок.
2.2. Форма.
- Полнотелые – стеновые или перегородочные блоки без пустот.
- Пустотелые – блоки как со сквозными, так и глухими пустотами, формируемыми в процессе изготовления для придания блоку необходимых эксплуатационных характеристик.
2.3. Размеры.
- В соответствии с ГОСТ 6133-99 размеры блоков для кладки стен могут быть: 288х288х138мм, 288х138х138мм, 390х190х188мм, 290х190х188мм, 190х190х188мм, 90х190х188мм.
- Размеры блоков для перегородок: 590х90х188мм, 390х90х188мм, 190х90х188мм.
Допускается изготовление блоков других размеров.
3. Характеристики опилкобетона.
Характеристики обилкобетонного блока для базового состава смеси.
Наименование показателя | Значение | Комментарий |
---|---|---|
Прочность, кг/см2 | М 35 | Значительная прочность, учитывая низкий удельный вес и, как следствие, низкую нагрузку.![]() Опилки в блоке играют роль армировки. Благодаря этому достигается повышенная прочность на растяжение и изгиб. По этому показателю опилкобетонные блоки превосходят большинство строительных материалов. Её можно регулировать путём изменения соотношения вяжущего вещества и наполнителя. При высокоэтажном строительстве возможно использование цемента марки М-500, повышение его содержания в блоке и применение модифицирующих добавок. Это позволит достичь показателей прочности в 100 кг/см2. При возведении одноэтажных построек достаточно показателя в 20 кг/см2. При изготовлении блоков с такими характеристиками можно добиться значительной экономии дорогостоящего цемента. |
Объемный вес, кг/м3 | 1100 | При увеличении % содержания цемента в смеси увеличится объемный вес и прочность. |
Теплопроводность, Вт/м*К | 0,29 | Показатель лучше, чем у кирпича и бетона.![]() |
Морозостойкость, циклы | 50 | Материал выдерживает 50 циклов. Специальные меры позволяют увеличить ресурс. |
Усадка, мм/м | 0,5-1,5 | Достаточно высокое значение, затрудняющее отделочные работы. |
Водопоглощение, % | 8-12 | Высокое значение, отрицательно влияющее и на морозоустойчивость. Может быть снижено путём применения гидрофобизирующих добавок и обработке опилок водоотталкивающими и консервирующими составами. |
Паропроницаемость | 0,1-0,26 | Значение увеличивается с ростом % содержания опилок и степени пустотелости блоков. |
Огнестойкость, час | 2,5 | Трудногорючий материал группы Г1. |
Стоимость руб/м3 | 1800-3500 | Зависит от содержания цемента в смеси и степени пустотности.![]() |
Звукоизоляция | высокая | Растёт с повышением % содержания опилок. Легкие ячеистые бетоны, в том числе и газобетон, при значительном увеличении пористости могут обладать лучшей звукоизоляцией, но при этом они будут терять в прочности. |
Максимальная этажность строения, эт | 3 | Этажность может быть повышена при увеличении прочности блока путем повышения % содержания цемента и применения модифицирующих добавок. |
4. Уникальные качества. Преимущества блоков из опилкобетона в сравнении с альтернативными материалами.
- Экологическая безопасность. Опилкобетон производится из натуральных материалов (цемент, песок, древесные опилки), что обеспечивает его высокую экологичность. По показателям звукопоглощения и паропроницаемости этот материал близок к древесине. Он полностью соответствует современным санитарно-гигиеническим требованиям.
- Низкая теплопроводность опилкобетона в сочетании с применением в строительстве пустотелых блоков делает дома из этого материала теплыми.
- Низкий удельный вес опилкобетона снижает затраты на устройство фундамента и транспортировку.
- Простота обработки облегчает строительство. Опилкобетонные блоки можно пилить, они легко сверлятся, не составляет проблем забить гвоздь в стену.
- Высокая прочность на растяжение и изгиб.
5. Минусы применения опилкобетона.
- Относительно высокая степень влагопоглощения, требующая проведения влагозащитных мероприятий при строительстве.
- Необходимость увеличения содержания цемента в блоке при многоэтажном строительстве. Это влечет за собой удорожание, ухудшение теплоизоляционных качеств и повышение требований к фундаменту.
- Относительно высокая степень усадки, осложняющая проведение отделочных работ.
6. Область применения и способы транспортировки.
Возможность изготавливать блоки из опилкобетона с нужными свойствами позволяет использовать их при возведении любых зданий. Он применяется для утепления уже готовых домов и строительства оград и столбов.
Опилкобетонные блоки транспортируются на поддонах. Высота пакета с поддоном не должна превышать 1,3 м. Камни с глухими отверстиями укладывают пустотами вниз. Сформированные транспортные пакеты складируются в один ярус.
(PDF) РАЗРАБОТКА ОПИЛОВОГО БЕТОНА ДЛЯ БЛОКОВОГО ИЗГОТОВЛЕНИЯ
Труды конференции «Строительные технологии 2001»,
Кота-Кинабалу, Малайзия, 12–14 октября 2001 г.
РАЗРАБОТКА ОПЫЛОВОГО БЕТОНА ДЛЯ ИЗГОТОВЛЕНИЯ БЛОКОВ
р.
, C. Carroll2 & N. Appleyard2
1Центр исследований встроенной инфраструктуры, Технологический университет, Сидней, почтовый ящик
123, Бродвей, Новый Южный Уэльс, 2007, Австралия, электронная почта: R, Ravindra @ uts.edu.au
2 Бывшие студенты-строители Технологического университета, Сидней, PO Box
123, Бродвей, Новый Южный Уэльс 2007, Австралия.
РЕФЕРАТ
В данной статье представлены результаты исследования разработки бетона на опилках
, пригодного для производства легких несущих блоков. Ингредиенты
, использованные в смеси: цемент, известь, летучая зола, хлорид кальция, Radiata
сосновые опилки, песок и вода.Бетонная смесь из опилок плотностью 1540
кг / м3 (содержание опилок 12% по объему) имела 7-дневную прочность на сжатие
14 МПа. Хотя установлено, что использование 2% хлорида кальция обеспечивает оптимальную прочность
для всех возрастов, усадка значительно увеличивается. Установлено, что последовательность дозирования
влияет на эффективность перемешивания и характеристики бетонных опилок.
Ключевое слово: опилки, цемент, хлорид кальция, летучая зола, конструкция смеси, сжатие
Прочность, усадка, плотность, легкий бетон
1 ВВЕДЕНИЕ
Использование отходов в бетонных смесях теперь признано одним из
эффективные способы утилизации твердых отходов других производств.Летучая зола от сжигания угля
и гранулированный доменный шлак металлургических заводов
являются типичными успешными примерами замены дорогостоящего портландцемента в бетонных смесях
. Помимо снижения стоимости поставляемого бетона, они обеспечивают
ряд технических преимуществ, таких как пониженная теплота гидратации, улучшенная когезионная способность и химическая стойкость
, снижение просачивания и проницаемости и постоянное улучшение прочности
с возрастом.Сельскохозяйственные отходы, такие как рисовая шелуха
, могут быть использованы для производства отличного пуццоланового материала путем контролируемого сжигания. Этот материал
используется в производстве цемента из золы рисовой шелухи для строительства.
Во многих развивающихся и развитых странах лесная промышленность производит
значительного количества опилок в качестве побочного продукта обработки древесины. Хотя
в ограниченном количестве используется в качестве топлива в некоторых странах, большая часть образующихся опилок
тратится впустую.Из-за ограниченного количества свалок и полигонов захоронение опилок
стало серьезной проблемой, стоящей перед лесной промышленностью. Предыдущие исследования
показали, что опилки, являясь легким материалом, могут использоваться в качестве заполнителя
в бетонных смесях для производства легкого бетона. Еще в 1940 г. было опубликовано
исследований свойств бетонных опилок (Baver 1940).
Физико-механические свойства бетонных опилок
зависят не только от количества используемых опилок, но также от химических и физических характеристик
опилок.Из-за высоких характеристик водопоглощения
IRJET-Запрошенная вами страница не была найдена на нашем сайте
IRJET приглашает статьи из различных инженерных и технологических дисциплин для Тома 8, выпуск 8 (август 2021 г.)
Отправить сейчас
IRJET Vol-8, выпуск 8, август 2021 г. Публикация продолжается …
Обзор статей
Получено IRJET «Импакт-фактор научного журнала: 7,529» за 2020 год.
Проверить здесь
Получено IRJET Сертификат регистрации системы менеджмента качества ISO 9001: 2008.
IRJET приглашает специалистов по различным инженерным и технологическим дисциплинам, научным дисциплинам для Тома 8, выпуск 8 (август 2021 г.)
Отправить сейчас
IRJET Vol-8, выпуск 8, август 2021 г. Публикация продолжается …
Просмотр Статьи
IRJET получил «Импакт-фактор научного журнала: 7,529» за 2020 год.
Проверить здесь
IRJET получил сертификат регистрации ISO 9001: 2008 для своей системы менеджмента качества.
IRJET приглашает специалистов по различным инженерным и технологическим дисциплинам, научным дисциплинам для Тома 8, выпуск 8 (август 2021 г.)
Отправить сейчас
IRJET Vol-8, выпуск 8, август 2021 г. Публикация продолжается …
Просмотр Статьи
IRJET получил «Импакт-фактор научного журнала: 7,529» за 2020 год.
Проверить здесь
IRJET получил сертификат регистрации ISO 9001: 2008 для своей системы менеджмента качества.
IRJET приглашает специалистов по различным инженерным и технологическим дисциплинам, научным дисциплинам для Тома 8, выпуск 8 (август 2021 г.)
Отправить сейчас
IRJET Vol-8, выпуск 8, август 2021 г. Публикация продолжается …
Просмотр Статьи
IRJET получил «Импакт-фактор научного журнала: 7,529» за 2020 год.
Проверить здесь
IRJET получил сертификат регистрации ISO 9001: 2008 для своей системы менеджмента качества.
IRJET приглашает специалистов по различным инженерным и технологическим дисциплинам, научным дисциплинам для Тома 8, выпуск 8 (август 2021 г.)
Отправить сейчас
IRJET Vol-8, выпуск 8, август 2021 г. Публикация продолжается …
Просмотр Статьи
IRJET получил «Импакт-фактор научного журнала: 7,529» за 2020 год.
Проверить здесь
IRJET получил сертификат регистрации ISO 9001: 2008 для своей системы менеджмента качества.
IRJET приглашает специалистов по различным инженерным и технологическим дисциплинам, научным дисциплинам для Тома 8, выпуск 8 (август 2021 г.)
Отправить сейчас
IRJET Vol-8, выпуск 8, август 2021 г. Публикация продолжается …
Просмотр Статьи
IRJET получил «Импакт-фактор научного журнала: 7,529» за 2020 год.
Проверить здесь
IRJET получил сертификат регистрации ISO 9001: 2008 для своей системы менеджмента качества.
IRJET приглашает специалистов по различным инженерным и технологическим дисциплинам, научным дисциплинам для Тома 8, выпуск 8 (август 2021 г.)
Отправить сейчас
IRJET Vol-8, выпуск 8, август 2021 г. Публикация продолжается …
Просмотр Статьи
IRJET получил «Импакт-фактор научного журнала: 7,529» за 2020 год.
Проверить здесь
IRJET получил сертификат регистрации ISO 9001: 2008 для своей системы менеджмента качества.
IRJET приглашает специалистов по различным инженерным и технологическим дисциплинам, научным дисциплинам для Тома 8, выпуск 8 (август 2021 г.)
Отправить сейчас
IRJET Vol-8, выпуск 8, август 2021 г. Публикация продолжается …
Просмотр Статьи
IRJET получил «Импакт-фактор научного журнала: 7,529» за 2020 год.
Проверить здесь
IRJET получил сертификат регистрации ISO 9001: 2008 для своей системы менеджмента качества.
Утилизация опилок в цементном растворе и цементном бетоне
% PDF-1.3 % 2 0 obj >>>] / ON [337 0 R] / Order [] / RBGroups [] >> / OCGs [222 0 R 337 0 R] >> / Outlines 213 0 R / Pages 3 0 R / Type / Catalog / ViewerPreferences 208 0 R >> эндобдж 211 0 объект > / Шрифт >>> / Поля 332 0 R >> эндобдж 212 0 объект > поток application / pdf
Влияние летучей золы угля и мелких опилок на характеристики проницаемого бетона
Abstract
Проницаемый бетон (ПК) давно используется для управления поверхностными стоками.Но один из главных его недостатков — низкая прочность. Некоторые промышленные отходы, по-видимому, содержат свойства, которые могут способствовать увеличению прочности ПК, такие как угольная летучая зола и мелкие опилки. Таким образом, их использование — возможное решение, которое могло бы решить проблемы низкой прочности ПК наряду с управлением утилизацией промышленных отходов. Это исследование было проведено для изучения лабораторных и полевых характеристик ПК при включении угольной летучей золы (CFA) в качестве частичной замены цемента и мелкодисперсных опилок (FSD) в качестве внутреннего отвердителя и добавки наполнителя.Испытания проводились в соответствии со стандартами Американского общества испытаний и материалов (ASTM). В целом результаты испытаний показали, что ПК с CFA и FSD в качестве добавок к ПК приобрел достаточную прочность, чтобы его можно было использовать в полевых условиях. Результаты инфильтрации и прочности на месте показали, что дорожное покрытие соответствует типичным значениям для функционального покрытия из ПК.
Ключевые слова: Гражданское строительство, Пористый бетон, Угольная зола, Мелкие опилки, Промышленные отходы, Частичная замена цемента, Внутреннее отверждение
1.Введение
Затопление является обычным явлением, особенно в городских районах, где широко используется бетон. Бетон, используемый для тротуаров, обычно представляет собой непроницаемую поверхность, которая не позволяет дождевой воде проникать через почву. Это приводит к городским стокам и, в конечном итоге, к наводнениям. Эта ситуация ухудшится из-за изменения климата, растущей урбанизации и плохих систем управления ливневыми водами. Одной из лучших стратегий адаптации для решения этой проблемы является использование проницаемого бетонного покрытия для управления поверхностным стоком (Топличич-Дурчич и др., 2015). Проницаемый бетон можно определить как бетон с открытой фракцией или без мелкодисперсных материалов, позволяющий дождевой воде проникать в нижележащее основание из-за своей высокой проницаемости (ACI Committee 522 2006).
Проницаемый бетон (ПК) — это композитный материал, в основном состоящий из цемента, воды и крупных заполнителей, который имеет значительно более высокую проницаемость по сравнению с обычным бетоном и, как известно, обладает преимуществами уменьшения объема стока и возможного улучшения качества воды в пополнение подземных вод (Legret et al., 1996). К другим преимуществам ПК относятся более высокая безопасность дорожного движения из-за повышенного сопротивления скольжению (Schaefer et al., 2006), гашение шума дороги (Olek et al., 2003) и уменьшение эффекта «теплового острова» (Yang and Jiang, 2003; Шу и др., 2011). Существенным недостатком проницаемого бетона, который препятствует его использованию в больших масштабах, является его относительная слабость, низкая долговечность и необходимость обслуживания из-за засорения (Ghafoori and Dutta, 1995). Его использование ограничено автостоянками, проездами, тротуарами и дорогами с низкой проходимостью.
Прочность на сжатие и проницаемость типичного ПК с отношением цемента к крупному заполнителю 0,30 при размере заполнителя 9,5 мм обычно составляет около 10 МПа и 0,4 см / с, соответственно (Joung and Grasley, 2008). Чтобы устранить недостатки, связанные с его прочностью и долговечностью, в последние годы было проведено несколько исследований по созданию проницаемой бетонной конструкции с оптимальной проницаемостью и прочностью на сжатие / изгиб. К ним относятся использование соответствующего количества воды, цемента, типа и размера заполнителя, оптимальной пропорции смеси и типа органических интенсификаторов (Yang and Jiang, 2003; Wang et al., 2006; Kevern et al., 2010) и добавление полимера для улучшения обрабатываемости, прочности и сопротивления замораживанию-оттаиванию при сохранении его высокой пористости и проницаемости (Kevern, 2008; Huang et al., 2010). Более того, недавние исследования показали, что прочность на сжатие ПК может быть увеличена выше 20 МПа за счет добавления полимера, латекса, мелких заполнителей и различных типов добавок без ущерба для требований к его прочности и проницаемости (Shu et al., 2011).
Одной из областей, которые необходимо изучить, является повышение прочности и долговечности ПК путем добавления мелких опилок в качестве недорогого внутреннего отвердителя (Usman et al., 2018), наполнителя и / или в качестве добавки вместо мелкого песка (Belhadja et al., 2014). Вода, поглощаемая опилками (или древесными заполнителями в целом) при смешивании с другими компонентами бетона, способствует гидратации, особенно внутри помещений, где отверждение невозможно. Это может сократить время отверждения вдвое (Ganiron, 2014). Способность опилок впитывать воду и высвобождать ее позже предполагает, что они могут служить в качестве внутреннего отвердителя в самоуплотняющихся цементных системах при замене цемента на 2–7% (Usman et al., 2018) и при замене песка на 60% в обычном пескобетоне (Belhadja et al., 2014), но значительно снизилась прочность. Однако улучшенное сцепление между древесной стружкой и цементным тестом можно было наблюдать, когда древесную стружку перед использованием пропитывали раствором силиката натрия (Коатанлем и др., 2006). Более того, лучшие характеристики раствора наблюдали Corinaldesi et al. (2016) при использовании мелких опилок, а не крупных.
С другой стороны, добавление летучей золы угля в бетонную смесь, как сообщается, увеличивает прочность бетона на сжатие (Thomas, 2007; Bremseth, 2010; Mallisa and Turuallo, 2017).При добавлении к смеси летучая зола из угля снижает водопотребность бетона на 5–15 процентов. Он также имеет замедляющий эффект (Helmuth, 1987), который полезен при бетонировании в теплую погоду (Shi and Qian, 2003). Замена части цемента угольной золой приводит к низкой начальной прочности бетона, но в некоторых случаях превышает прочность портландцемента через 3–6 месяцев. Более высокая прочность является результатом пуццолановых реакций, благоприятствующих гидрату силиката кальция (C – S – H) при уменьшении Ca (OH) 2 (Shi and Qian, 2003; Opiso et al., 2017). Повышенное содержание Ca (OH) 2 ограничивает прочность бетона, поскольку Ca (OH) 2 имеет тенденцию к раскалыванию под действием напряжения сдвига (Mindess and Young, 1981).
Синергетический эффект комбинированного использования мелких опилок и летучей золы угля, обладающих свойствами, которые могут улучшить качество ПК, возможно, может помочь в разработке функционального и прочного покрытия из ПК. Однако исследования, касающиеся влияния их совместного использования на производительность ПК, еще не выяснены.В этом контексте целью данной работы является изучение вклада угольной летучей золы и мелких опилок в разработку дорожного покрытия из экологичного ПК без ущерба для его характеристик, основанных на прочности, проницаемости и способах обслуживания.
2. Материалы и методы
Переменными, измеряемыми для определения производительности ПК, являются прочность на сжатие, прочность на изгиб, проницаемость и скорость инфильтрации на месте. Также было проведено полевое применение разработанного ПК и измерены те же переменные.Кроме того, был также оценен режим обслуживания.
2.1. Материалы
Обычный портландцемент типа I (OPC), использованный в этом исследовании, соответствовал стандарту ASTM Standard C150. Размер используемого заполнителя составлял от 5 до 19 мм. Также использовалась питьевая водопроводная вода в соответствии с ASTM C1602. Опилки были собраны на местной лесопилке. Его сушили либо сушкой на солнце, либо сушкой в печи для удаления влаги, которая может повлиять на конечное соотношение воды и вяжущих материалов (в / ц). Затем его просеивали через сетку №8 (2,36 мм) для производства мелких опилок (FSD) с насыпным удельным весом 0,359, водопоглощающей способностью 89,82% и модулем крупности 3,69. Зола-унос класса C с индексом пуццолановой активности 75% (Sideris et al., 2018) была получена с угольной электростанции, расположенной на Минданао, и просеяна через сетку No. 200 (75 мкм) для обеспечения тонкости частиц. Химический состав вяжущих материалов кратко изложен в.
Таблица 1
Химический состав вяжущих материалов.
SiO 2 | TiO 2 | Al 2 O 3 | Fe 2 O 3 3 | 9029 MO3CaO3 | 9029 CaO3 9029 M 2 OSO 3 | LOI | |||||||||||||||||||||||||||||||||||||||||||||||||||||||||||
---|---|---|---|---|---|---|---|---|---|---|---|---|---|---|---|---|---|---|---|---|---|---|---|---|---|---|---|---|---|---|---|---|---|---|---|---|---|---|---|---|---|---|---|---|---|---|---|---|---|---|---|---|---|---|---|---|---|---|---|---|---|---|---|---|---|
OPC | 20,9 | — | 5,7 | 2,8 | — | 2,7 | 90302,9 | ||||||||||||||||||||||||||||||||||||||||||||||||||||||||||
CFA | 23,9 | 0,6 | 9,1 | 28,5 | 0,3 | 9,7 | 23,3 | 0,633 | 3,0 16,0 336 9038 903 Определение оптимального количества FSD Для определения оптимального количества FSD, которое будет добавлено в последующих экспериментах на бетонной смеси ПК, смешанного с угольной золой, бетонной смеси с соотношением цемента к крупному заполнителю 1: 3 и массой 0.50 было подготовлено. Соответствующее количество FSD было добавлено в диапазоне от 0 до 12% по массе цемента с интервалом 2%, а использованный крупнозернистый заполнитель имел диапазон 5–9 мм. Затем бетонная смесь выдерживалась в течение 28 дней и измерялась прочность на сжатие как функция процентного содержания FSD, добавленного к смеси. Процент FSD с наивысшей прочностью на сжатие — это оптимальное количество FSD, которое будет использоваться для разработки ПК с угольной летучей золой в качестве частичной замены цемента. С другой стороны, прочность на сжатие и проницаемость ПК в основном определяется размером заполнителя.Прочность на сжатие обратно пропорциональна размеру заполнителя, в то время как проницаемость напрямую связана с размером заполнителя. В связи с этим было также оценено влияние оптимального количества FSD на прочность на сжатие и проницаемость ПК с использованием заполнителей различных размеров, чтобы дать представление о выборе подходящего размера заполнителя, который будет соответствовать требованиям прочности конкретного типа. полевого применения. Используя ту же бетонную смесь, соотношение воды и цемента и оптимальный FSD, были изготовлены образцы с размерами заполнителей 5–9 мм, 10–14 мм и 15–19 мм.Образцы выдерживали в течение 28 дней, а затем испытывали на прочность на сжатие и проницаемость. 2.3. Приготовление образцов ПК с CFA и FSDОсновываясь на результатах влияния FSD на прочность на сжатие и проницаемость ПК, окончательная пропорция смеси, выбранная для производства ПК с CFA и FSD, состояла из 8% FSD по весу. размер цемента и заполнителя 10–14 мм. Десятипроцентная (10%) замена обычного портландцемента (OPC) угольной летучей золой (CFA) рассматривалась в этом исследовании, потому что относительная прочность бетона выше и меньше изменяется в раннем и позднем возрасте по сравнению с другими пропорциями (Невилл , 1981).Однако использованная в / ц составляла 0,35 вместо 0,50, и расчетное соотношение смеси также было изменено на 1: 3,5 для целей проницаемости и консистенции смеси. Следует отметить, что более высокое соотношение в / ц приведет к оседанию цементного теста на дне. показывает сводку пропорций смеси. Перемешивание производилось одноразовой бетономешалкой. Компонентам давали возможность смешаться до достижения гомогенности. Затем свежеприготовленный ПК был отлит в формы из стальных прямоугольных балок (152,4 мм × 152,4 мм × 533 мм).4 мм) и цилиндрических форм (диаметром 152,4 мм (Φ) × 304,8 мм и 101,6 мм Φ × 152,4 мм). Цилиндрические и прямоугольные образцы ПК были извлечены из форм через 24 и 48 ч соответственно. Они хранились в лаборатории в условиях окружающей среды и отверждались в течение 7, 14 и 28 дней путем опрыскивания. Во время отверждения образцы ПК не закрывали пластиковым листом, как это обычно применялось. Было изготовлено по пять образцов для каждого ПК с цилиндрической и прямоугольной балкой, из которых по три случайным образом были выбраны для испытания на прочность на сжатие и изгиб. Таблица 2Количество материалов на м 3 проницаемого бетона.
2.4. Экспериментальные методы2.4.1. Испытание на сжатиеИспытание на сжатие было выполнено в соответствии с ASTM C39 или «Стандартным методом испытания прочности на сжатие цилиндрических образцов бетона». Три цилиндрических образца ПК с размерами 152,4 мм Φ × 304,8 мм были испытаны на прочность при сжатии после назначенных дней отверждения. Перед испытанием образцов ПК каждый был измерен и взвешен. Среднее значение трех образцов было записано как конечная прочность на сжатие в МПа. 2.4.2. Испытание на изгибВ соответствии со стандартом ASTM C78 или «Стандартным методом испытания прочности бетона на изгиб (с использованием простой балки с нагрузкой в третьей точке)» три образца прямоугольной балки были испытаны и нагружены как простые балки с установкой нагрузки в третьей точке. для испытания прочности на изгиб. Испытание проводилось с использованием компрессионной машины с приспособлениями для испытания на изгиб. Перед тестированием каждый из образцов был измерен и взвешен. На обоих концах каждого образца был отмечен дюйм от края, чтобы легко определить точку, в которой опорные блоки машины будут выровнены.Оставшаяся длина каждого образца была разделена и размечена на три равные части. Средний результат прочности трех образцов был записан как конечная прочность на изгиб в МПа. 2.4.3. Испытание на проницаемостьИспытание на проницаемость проводилось на образцах ПК с размерами 101,6 мм Φ × 152,4 мм методом падающей головки. Каждый из образцов ПК был индивидуально помещен в ячейку устройства и имел три (3) синхронизированных испытания. Перед испытанием сначала смачивали внутреннюю поверхность устройства, включая трубки, чтобы не влиять на скорость и объем воды, протекающей через нее.Среднее значение 3 испытаний 3 различных образцов было принято в качестве окончательной гидравлической проводимости в см · с -1 . Гидравлическая проводимость рассчитывалась как в формуле. (1), , где a = площадь поперечного сечения трубки в см 2 , L = длина образца в см, A = площадь поперечного сечения образца в см 2 , t = время, прошедшее в s, h2 = начальный напор в см и h3 = конечный напор в см. 2.4.4. Морфологический тестСканирующая электронная микроскопия с полевой эмиссией (FESEM) Визуализация была проведена для получения микроструктурных деталей на затвердевшей массе цементной пасты структуры ПК после 28 дней отверждения.Анализ проводился на двухлучевом приборе Helios Nanolab 600i с ускоряющим напряжением 5,0 кВ в режиме обратного рассеяния электронов (BSE) и током пучка 0,17 нА. 2,5. Полевая заявкаПарковочный блок размером 6 м × 2,6 м × 101,6 мм был подготовлен к установке с помощью ПК (). Материалы для полевого применения получены из одних и тех же источников и подготовлены аналогично. Тем не менее, используемый размер заполнителя обычно составлял 15–19 мм из-за практичности и доступности.Кроме того, его лабораторная прочность 17,615 МПа может быть достаточной для применения на автостоянках, которые не требуют более высокой прочности по сравнению с дорогами. Нанесение газопроницаемого бетона на стоянке во время (а) заливки, (б) заливки и (в) окончательной укладки ПК-смеси. Образцы бетонных кернов были получены от дорожного покрытия из ПК в соответствии со стандартом ASTM C42 или «Стандартным методом испытаний для получения и испытания просверленных кернов и пиленых балок из бетона». Просверленные стержни имели неровные поверхности, особенно в нижней части, поэтому они были пропилены для создания гладкой поверхности.Затем были проведены испытания на сжатие полированных образцов керна. Поскольку отношение длины к диаметру образцов керна не является стандартным, были внесены необходимые поправки. Выполненная процедура тестирования соответствует ASTM C39. Пропитка проницаемого бетона в полевых условиях определялась с использованием ASTM C1701 или «Стандартного метода испытаний для инфильтрации проницаемого бетона на месте», который представляет собой установку одного кольца инфильтрации с использованием методологии постоянного напора. ASTM C1701 может использоваться для проверки желаемых скоростей инфильтрации для конкретных конструкций смесей, тестирования начальной проницаемости и тестирования снижения проницаемости с течением времени.Кольцо было прикреплено к мостовой с помощью герметика (замазки сантехника) для предотвращения утечки воды. Дорожное покрытие предварительно увлажнили путем заливки около 3,6 кг воды в кольцо со скоростью, достаточной для поддержания напора между размеченными линиями на расстоянии 10–15 мм от дна, до полного использования 3,6 кг воды. . Для фактического испытания было использовано 18 кг воды. Отсчет времени начинался, как только вода сталкивался с проницаемой бетонной поверхностью, и прекращался, когда на проницаемой поверхности больше не было свободной воды.Затем записывали соответствующую массу воды M и истекшее время t duration. Наконец, была рассчитана скорость инфильтрации. Результат был рассчитан по формуле , где I = скорость инфильтрации в см · с -1 , K = 4 583 666 см 3 кг -1 , M = масса инфильтрованной воды в кг, D = внутри диаметр инфильтрационного кольца в см и t = время, необходимое для инфильтрации измеренного количества воды, в с. 2.6. Оценка технического обслуживанияОценка технического обслуживания в отношении эксплуатационной пригодности проницаемого бетонного покрытия проводилась на основе скорости его инфильтрации, поскольку со временем накапливаются обломки и остатки.Первоначальная скорость инфильтрации дорожного покрытия была определена через 48 часов после строительства в соответствии со стандартами ASTM для скорости инфильтрации проницаемого бетона на месте. Оценка состояния парковки была проведена через два месяца после того, как она была открыта для публики. Тест скорости инфильтрации проводился в трех случайно выбранных точках расположения. Соответствующий тип методов очистки (пылесос, мощный обдув и промывка под давлением) был определен на основе разницы в скорости инфильтрации до и после технического обслуживания. Опилки бетонная смесьИзобретение относится к производству строительных материалов. Сущность: бетонная смесь на опилках, используемая предпочтительно в сельском хозяйстве, состоит, мас.%: Цемент 48-52, шишки хвойных деревьев 27-33, известь 10-14, гипс 1-3, хлористый кальций 4-6, указанные шишки были обработаны. предварительно подвергают термообработке при 120-170 ° ° C с целью подавления их биологической активности. Соотношение вода / цемент в смеси составляет 0,6-0,8. ДЕЙСТВИЕ: повышена прочность изделий и достигается экологичность смеси. 1 табл. Изобретение относится к промышленности строительных материалов, в основном используемых в сельском строительстве. Получение арболита известно с использованием цемента, шпатлевки, хлористого кальция [1]. Известна цементная древесная смесь, содержащая, мас.%: Цемент 47-52; щепа 30-33; гипс 1-3; лайм 9-15; хлорид кальция 2-6,5 [2]. Задачей изобретения является повышение прочности деревянных изделий из цементной смеси. Технический результат достигается тем, что в цементных древесных смесях, содержащих цемент, древесную стружку, известь, гипс, хлористый кальций, в качестве древесины используются измельченные шишки хвойных пород, при следующем соотношении компонентов, мас.%: цемент 48-52; лайм 10-14; гипс 1-3; хлорид кальция 4-6; шишки хвойных деревьев 27-33; кроме того, эти конусы предварительно подвергались термообработке, исключающей их биологическую активность (отжиг при 120-170 ° и водоцементном соотношении 0,6-0,8. Составы цементной древесной смеси и свойства производимых из нее изделий (плит) в таблице. Цементную древесную смесь готовят следующим образом: Проводят дозирование компонентов смеси, например, согласно таблице.В составе смеси используются измельченные спелые шишки хвойных пород, в основном кедра (после удаления и их семян), сосна, пихта, ель. Шишки предварительно подвергнуты для исключения их биологической активности (например, прорастания на удаленных остатках семян) термической обработки (отжиг при 120-170 ° С в течение 10-20 минут Смесь цемента, гипса, извести, хлорида кальция. В полученную массу добавляется подготовили измельченные шишки, все компоненты еще раз перемешиваем, добавляя воду для достижения необходимого водоцементного отношения.
Полученную смесь из цементного дерева помещают в форму, герметизируют и оставляют на суше. Извлечен из формы изделия (например, планшет выдерживают при комнатной температуре не менее 28 дней. Изделия из цементно-древесной смеси прочны, экологически безопасны. Источники информации 1. AS № 1516478 СССР, 1989. 2. Патент №2058967, Россия, 2005. Цементная древесная смесь, содержащая цемент, древесную стружку, известь, гипс, хлористый кальций, отличающаяся тем, что в качестве древесины используются измельченные шишки хвойных пород в следующее соотношение, мас.%:
кроме того, эти конусы предварительно подвергались термообработке без учета их биологической активности (отжиг при 120-170 ° и соотношении вода / цемент от 0,6 до 0,8. Обзор свойств, структурных характеристик и возможностей применения бетона, содержащего древесные отходы, в качестве частичной замены одного из составляющих его материалов[1] ICE.(1975) Институт инженеров-строителей — Королевская хартия, подзаконные акты, постановления и правила 1975 г .; https://www.ice.org.uk/ICEDevelopmentWebPortal/media/Documents/Royal-Charter-By-laws-Regulationsand-Rules-2015.pdf (оценка 19 — 02 — 2016). Поиск в Google Scholar [2 ] ЛЕД. Новый инженер-строитель 2017; http://www.newcivilengineer.com/confirmation?www.newcivilengineer.com%252fnew-definition-for-civil-engineering (оценка 17 — 02 — 2016) Поиск в Google Scholar [3] ASCE (2018) О Civil Инженерное дело.Американское общество инженеров-строителей 2018; http://www.asce.org/about_civil_engineering/ (оценка 12 — 01 — 2018) Поиск в Google Scholar [4] RAE. (2017) http://www.raeng.org.uk/education/vps/sustdev.htm 2017 (оценка 6-10-2017). Поиск в Google Scholar [5] MEHTA, P. K. (2002). Озеленение бетонной промышленности для устойчивого развития. Concrete International Vol. 24, No. 7, pp. 23–28. Поиск в Google Scholar [6] OCHSENDORF, J A. (2005) Устойчивое проектирование: будущее структурного проектирования, Structures.ASCE http://www.ascelibrary.org/Поиск в Google Scholar [7] СУХЕНДРО, Б. (2014). На пути к зеленому бетону для лучшей устойчивой окружающей среды. Инженерные процедуры, том. 95, стр. 305–320. Поиск в Google Scholar [8] ШАФИГ, П., МАХМУД, Х. Б., ДЖУМААТ, М. З., ЗАРГАР, М. (2014). Сельскохозяйственные отходы как агрегат в бетонных смесях — обзор. Строительные и строительные материалы. 53, pp. 110–117. Искать в Google Scholar [9] DEMIRBOGA, R., GÜL, R. (2006) Производство высокопрочного бетона с использованием промышленных побочных продуктов.Строительная среда, Vol. 41, стр. 1124-1127.Поиск в Google Scholar [10] DETWILER, RJ, FAPOHUNDA, C.A, NATALIE, J. (1994) Использование дополнительных цементных материалов для повышения устойчивости к проникновению хлорид-ионов в затвердевший бетон. при повышенных температурах. ACI Materials Journals, Vol. 91, No. 1, pp. 63–66. Поиск в Google Scholar [11] ZELJKOVIC, M. (2009). Метакаолин влияет на прочность бетона. Магистр. Диссертация, Университет Торонто, Канада. Поиск в Google Scholar [12] IBRAHIM, A.Г., ОКОЛИ, О. Г. ДАХИРУ, Д. (2016). Сравнительное исследование свойств обычного портландцементного бетона и бинарного бетона, содержащего метакаолин из каолина канкара в Нигерии. Журнал АТБУ по экологическим технологиям, Vol. 9, No. 2, pp. 53–59. Поиск в Google Scholar [13] THOMAS M. (2007). Оптимизация использования летучей золы в бетоне. Портлендская цементная ассоциация http://www.cement.org/docs/default-source/fc_concrete_technology/is548-optimizing-the-use-of-fly-ash-concrete.pdf, (оценка 1–1–2017 г.).Искать в Google Scholar [14] FOONG, K. Y., ALENGARAM, U. J., JUMAAT, M .. Z. MO, K.H. (2015) Улучшение механических свойств легкого бетона из скорлупы масличной пальмы с использованием золы рисовой шелухи и технологического песка. Журнал Чжэцзянского университета-НАУКА A (Прикладная физика и инженерия), Vol. 16, No. 1, pp. 59–69. Поиск в Google Scholar [15] FAPOHUNDA, C., AKINBILE, B, SHITTU A. (2017) Структура и свойства раствора и бетона, содержащих золу рисовой шелухи в качестве частичной замены обычного портландцемента — Обзор.Международный журнал устойчивой застроенной окружающей среды (в печати). http://dx.doi.org/10.1016/j.ijsbe.2017.07.00410.1016/j.ijsbe.2017.07.004Открыть DOISearch в Google Scholar [16] GHORPADE, V.G. (2012). Влияние золы древесных отходов на прочностные характеристики бетона. Природа, окружающая среда и технологии загрязнения, Vol. 11, No. 1, pp. 121–124. Поиск в Google Scholar [17] ЭЛИНВА, А. У. МАМУДА А. М. (2014). Зола опилок в качестве порошкового материала для самоуплотняющегося бетона, содержащего нафталинсульфонат.Hindawi Publishing Corporation: достижения в области гражданского строительства, стр. 1-8. Http://dx.doi.org/10.1155/2014/12927610.1155/2014/129276Open DOIearch in Google Scholar [18] MCNEIL, K. KANG, TH ( 2013). Переработанный бетонный заполнитель: обзор. Международный журнал бетонных конструкций и материалов. Vol. 7, No. 1, pp. 61-69, DOI 10.1007 / s40069-013-0032-5.10.1007 / s40069-013-0032-5Открыть DOISearch в Google Scholar [19] ALENGARAM. У. Дж., МУХИТ, Б. Дж., ДЖУМААТ, М. З. (2013). Использование легкого заполнителя из скорлупы ядра масличной пальмы в бетоне — обзор.Строительные и строительные материалы. 38, стр. 161–172. Поиск в Google Scholar [20] ФАПОУНДА, К. А., АКИНСАНЬЯ, А. Ю., АДЕРОДЖУ, С. О. и ШИТТУ, К. А. (2016). Пригодность измельченной коровьей кости в качестве частичной замены мелкого заполнителя при производстве бетона. Вест-индский инженерный журнал, Vol. 39, No. 1, pp. 25 — 31. Поиск в Google Scholar [21] FAPOHUNDA. C. A, SHITTU, K. A, ADEROJU., S. O. AKINSANYA AY. (2016). Прочностные характеристики бетона с дробленой костью как частичного замещения мелких заполнителей при различных водоцементных отношениях.Acta Technica Corniviensis — Технический бюллетень, Vol. 9, No. 1, pp. 162–169. Поиск в Google Scholar [22] GANIRON JR, T.U. (2014). Влияние опилок как мелкого заполнителя в бетонной смеси для строительства. Международный журнал передовых наук и технологий, Vol. 63, с. 73-82. http://dx.doi.org/10.14257/ijast.201 4.63.07Поиск в Google Scholar [23] РАХИМ, А.А., ОЛАСУНКАНМИ, Б.С. ФОЛОРУНСО, К.С. (2012). Зола опилок как частичная замена цемента в бетоне.Организация, технологии и менеджмент в строительстве, Vol. 4, No. 2, pp. 474–480. Поиск в Google Scholar [24] GARCIA, M., SOUSA-COUTINHO, J. (2013). Прочность и долговечность цемента с зольным остатком лесных отходов. Строительные и строительные материалы. 41, pp 897-910.Search in Google Scholar [25] ОГОРК, Э. Н., АЮБА, С. (2014). Влияние золы опилок (ЗДА) как добавки в цементном тесте и бетоне. IJISET — Международный журнал инновационной науки, техники и технологий, Vol.1, No. 10, pp. 736 — 743. Поиск в Google Scholar [26] SUBBARAMAIAH, G. (2016) Исследования прочности и долговечности бетона конструкционной марки из древесной золы. Докторская диссертация представлена в Технологический университет Джавахарлала Неру, Анантапур, Анантапураму, Индия. (http://shodhganga.inflibnet.ac.in/bitstream/.pdf, оценка 6–10 — 2017 г.). Поиск в Google Scholar [27] CHEAH, C. B., RAMLI, M. (2014). Применение золы древесных отходов в качестве материала для частичной замены цемента в производстве бетона и строительного раствора: обзор.Ресурс. Сохранить. Recycle, Vol. 55, No. 7, pp. 669-685. Поиск в Google Scholar [28] ЧОУДХУРИ С., МИШРА М., СУГАНЯ О. (2014). Использование золы древесных отходов в качестве частичного заменителя при изготовлении бетона конструкционного качества: обзор. Ain Shams Engineering Journal Vol. 6, стр. 429–437. Поиск в Google Scholar [29] ПРУСТИ, Дж. К., ПАТРО, С. К., БАСАРКАР, С. С. (2016). Бетон с использованием агроотходов в качестве мелкого заполнителя для устойчивой застроенной среды. T — Обзор.Международный журнал устойчивой искусственной среды Vol. 5, pp. 312–333.Поиск в Google Scholar [30] JAHANGIRI, N, KOSEOGLU, K, CENGIZLER, H. (2017). Бетон с побочными продуктами и отходами в виде заполнителя или цемента. Журнал Института естественных и прикладных наук Университета Дикле, Том 6, № 1, стр. 29–38. Поиск в Google Scholar [31] АБДУЛЛАХИ, М. (2006). Характеристики деревянного бетона ASH / OPC. Леонардо Электрон Дж. Практик. Техн. Том. 8, pp. 9–16. Поиск в Google Scholar [32] CHEAH, C.Б., РАМЛИ, М. (2012). Механическая прочность, долговечность и усадка при высыхании конструкционного раствора, содержащего HCWA в качестве частичной замены цемента. Строительные и строительные материалы. 30, pp. 320–329. Поиск в Google Scholar [33] БЕРРА, М., МАНДЖИАЛАРДИ, Т., ПАОЛИНИ, А. Э. (2015). Повторное использование летучей золы древесной биомассы в материалах на основе цемента. Строительные и строительные материалы. 76, стр. 286-296. Поиск в Google Scholar [34] ETIEGNI, L, CAMPBELL, A.G. (1991). Физико-химические характеристики древесной золы.Biresource Technol, Vol. 37, No. 2, pp. 173-178 Искать в Google Scholar [35] NAIK, T. R, KRAUS, R. N, SIDDIQUE, R. (2002) Демонстрация технологии производства бетона и использования древесной золы из Висконсина , Департамент природных ресурсов штата Висконсин (Мэдисон, Висконсин) для проекта № 1-06 Отчет UWM № CBU-2002-30, Центр утилизации побочных продуктов, Департамент гражданского строительства и механики, Университет Висконсин-Милуоки. Поиск в Google Scholar [36] NAIK, T.Р., КРАУС, Р. Н., СИДДИК, Р. (2003). CLSM, содержащий смесь угольной золы и нового пуццоланового материала. ACI Materials Journals, Vol. 100, No. 3, pp. 208-15. Поиск в Google Scholar [37] UDOEYO, F. F, INYANG, H, YOUNG, D. T, OPARADU, E. E. (2006). Возможности использования отходов древесной золы в качестве добавки в бетон. Журнал материалов в гражданском строительстве, Vol. 18, No. 4, pp. 605-11 Искать в Google Scholar [38] ETTU, L.O., MBAJIORGU, M. S. W, NJOKU, F. C, AJOKU, C. A, NWACHUKWU, K. C.(2013) Изменение прочности композитов из золы опилок и опилок с процентным содержанием золы опилок. Гражданские и экологические исследования, Vol. 3, No. 9, pp. 53–58. Поиск в Google Scholar [39] ЧОУДХУРИ, С., МАНИАР, А., СУГАНЯ, О. М. (2015). Развитие прочности в бетоне с использованием цемента с добавлением древесной золы и использование моделей мягких вычислений для прогнозирования параметров прочности ». Журнал перспективных исследований, Vol. 6, стр. 907-913. Поиск в Google Scholar [40] НАИК, Т. Р., Краус, Р. Н. (2003). Новый источник пуццолановых материалов.Concrete International, 55–62. Поиск в Google Scholar [41] АБХИШЕК Д.С., КУМБАР П.К. (2017). Экспериментальное исследование аспектов прочности бетона с частичной заменой цемента золой из опилок. Международный журнал научно-исследовательской организации Vol. 1, No. 5, pp. 36–41. Поиск в Google Scholar [42] CHEAH, C. B, PART, W. K, RAMLI, M. (2015). Гибридизация угольной летучей золы и древесной золы для изготовления несущего блока из геополимера с низкой щелочностью, отверждаемого при температуре окружающей среды, Construction Building Material, Vol.88, стр. 41-55. Поиск в Google Scholar [43] ADAMU, M, TIFASE, A.S, UCHE, O.A.U. (2017). Технические свойства древесных отходов производства ясеня-бетона. Международный журнал достижений в строительной инженерии, Vol. 1, No. 1, pp. 1–10. Поиск в Google Scholar [44] AWOLUSI, T. M, SOJOBI, A. O, AFOLAYAN, J. O. S. D. A (2017). и применение латерита в бетоне: перспективы и последствия повышенной температуры. Cogent Engineering. https://doi.org/10.1080/23311916.2017.1387954.10.1080 / 23311916.2017.1387954Открыть DOISearch в Google Scholar [45] РАХИМ, А.А., АДЕДОКУН, С.И., АДЖАИ, Б.Р., АДЕДОЙН, О., АДЕГБОЙГА, Б.О. (2017). Применение золы опилок в качестве частичной замены цемента при производстве брусчатки. Международный журнал устойчивого строительства и технологий, Vol. 8, No. 1, pp. 1–11. Поиск в Google Scholar [46] КУМАР, Т. Р. П, СУДХИШ, К., САСИ, К. С. (2015). Прочностные характеристики геополимерного бетона на основе золы из опилок.Международный журнал исследований ChemTech, Vol. 8, No. 2, pp. 738-745. Поиск в Google Scholar [47] MARTHONG, C. (2012). Зола опилочная (ПЗД) как частичная замена цемента ». Международный журнал инженерных исследований и приложений, Vol. 2, No. 4, pp. 1980-1985. Поиск в Google Scholar [48] TYAGHER, S, UTSEV, J, ADAGBA, T. (2011). Пригодность зольно-известковой смеси опилок для производства пустотелых блоков из песчаного бетона. Нигерийский технологический журнал, Vol. 30, No. 1, с.79-84Поиск в Google Scholar [49] МАГЕСВАРИ, М., ВИДИВЕЛЛИ, Б. (2009). Использование золы из опилок в качестве замены мелкого заполнителя в бетоне. Журнал экологических исследований и разработок, Vol. 3, No. 3, pp. 720-726. Поиск в Google Scholar [50] UDOEYO, F.F, DASHIBIL, P.U. (2002). Опилки золы как бетонный материал. Журнал материалов в гражданском строительстве, Vol. 14, No. 2, pp. 173-176. Поиск в Google Scholar [51] ASTM C618-05 (2005). Стандартные спецификации для угольной золы-уноса и сырого или кальцинированного природного пуццолана для использования в качестве минеральной добавки в бетон.Американское общество по испытаниям и материалам International West Conshohocken Philadelphia. Поиск в Google Scholar [52] ВАСИЛЕВ, С. В., БАКСТЕР, Д., АНДЕРСЕН, Л. К., ВАСИЛЕВА, К. Г. (2010). Обзор химического состава биомассы. Топливо, об. 89, стр. 913-33. Поиск в Google Scholar [53] ЭЛИНВА А. У, МАХМУД А. М. (2002). Зола из древесных отходов как заменитель цемента. Цементно-бетонные композиты. 24, 219-22. Искать в Google Scholar [54] ELINWA, A.U, EJEH, S. P. (2004). Эффекты включения летучей золы от сжигания опилок в цементные пасты и растворы. Журнал азиатской архитектуры, строительства, Vol. 3, No. 1, pp. 1-7. Искать в Google Scholar [55] BS12. (1996). Британский институт стандартов — Спецификация портландцемента. Британский институт стандартов, Лондон Поиск в Google Scholar [56] RAJAMMA, R, BALL, R.J, TARELHO, L.A.C, ALLEN, G.C, LABRINCHA, J.A, FERREIRA, V.M. (2009). Характеристики и использование летучей золы биомассы в материалах на основе цемента.J Hazard Mater, Vol. 172, стр. 1049-60. Поиск в Google Scholar [57] ДЕМИС, С., ТАПАЛИ, Т.Г., ПАПАДАКИС, В.Г. (2014). Исследование эффективности использования золы биомассы в качестве пуццолановых материалов. Строительные и строительные материалы. 68, стр. 291-300 Поиск в Google Scholar [58] ПАПАДАКИС, В. Г., АНТИОХОС, С., ЦИМАС, С. (2002). Дополнительные цементирующие материалы в бетоне — Часть II: фундаментальная оценка КПД. Цемент, бетон и исследования, Vol.32, No. 10, pp. 1533–1538. Поиск в Google Scholar [59] АНТИОХОС, С. К., ПАПАДАКИС, В. Г., ЧАНИОТАКИС, Э, ЦИМАС, С. (2007). Повышение эффективности трехкомпонентных цементов за счет смешивания различных типов летучей золы. Cem Concr Res. Vol. 37, No. 6, pp. 877-85. Поиск в Google Scholar [60] RAMOS, T, MATOS, A.M, SOUSA-COUTINHO, J. (2013). Раствор с золой древесных отходов: Механическая прочность, стойкость к карбонизации и расширению ASR. Строительные и строительные материалы. 49, стр.343-351Поиск в Google Scholar [61] MEHTA, P. K, MONTEIRO, P. J. M. (2006). Конкретный. микроструктура, свойства и материалы McGraw-Hill, 3-е издание. Поиск в Google Scholar [62] NEVILLE, A. M. (2011). Свойства бетона. Pearson Education Limited, Эдинбург, Англия, 5-е издание. http://www.pearsoned.co.uk. Поиск в Google Scholar [63] MASSAZZA, F. (1998). LEA’S химия цемента и бетона. Питер К. Хьюлетт Арнольд, 4-е издание. Поиск в Google Scholar [64] BS EN 196-1.(1995). Методы испытания цемента. Физические испытания. Прочностные испытания. Британский институт стандартов, Лондон. Поиск в Google Scholar [65] SHETTY, M. S. (2009). Бетонные технологии. S. Chand and Company Ltd, Нью-Дели, MultiColour Edition. Поиск в Google Scholar [66] ГАМБХИР, М. Л. (2013). Бетонные технологии — теория и практика. McGraw Hill Education Private Limited, Нью-Дели, 5-е издание. Поиск в Google Scholar [67] FALADE, F, IKPONMWOSA, E, AROGUNDADE, A.(2011). Исследование некоторых структурных свойств пенобетона. Журнал инженерных исследований, Vol. 16, стр. 67–80. Поиск в Google Scholar [68] ЭЛЛИНВА, А. У, ЭДЖЕ, С. П., АКАПАБИО, И. О. (2005). Использование метакаолина для улучшения бетона на основе золы из опилок. Concrete International. Поиск в Google Scholar [69] BS 811 0 (1997). Конструктивное использование бетона. Британский институт стандартов, Лондон. Поиск в Google Scholar [70] MARTHONG, C. (2013). Исследование размерного эффекта опилок золобетона при сжимающей нагрузке.Журнал IOSR по машиностроению и гражданскому строительству, Vol. 1, No. 5, pp. 27–32. Поиск в Google Scholar [71] ETTU, L. O, EZEH, J. C, ANYA, U. C, NWACHUKWU, K. C, NJOKU, KO (2013 ). Прочность трехкомпонентного цементного бетона, содержащего золу рисовой шелухи афикпо и золу опилок. Международный журнал технических наук: изобретения, Vol. 2, No. 4, pp. 38–42. Поиск в Google Scholar [72] ACI 318M-08 (2008). Требования строительных норм для конструкционного бетона (ACI 318M-08) и комментарии.Американский институт бетона. Поиск в Google Scholar [73] ASTM-C330 (2009). Стандартные технические условия на легкие заполнители для конструкционного бетона. Американское общество испытаний и материалов, Филадельфия. Поиск в Google Scholar [74] ДЕНЬ, Р. Л. (1990). Пуццоланы для использования в недорогом жилье — современный отчет, подготовленный для международного исследовательского центра развития Оттава, Канадский центр исследований международного развития, Оттава. Поиск в Google Scholar [75] MHAISKAR, Y, NAIK, D.Д. (2012). Исследования корреляции между прочностью на изгиб и прочностью бетона на сжатие, Индийский журнал по бетону, стр. 1–6. Поищите в Google Scholar [76] ОЛУОКУН, Ф.А. (1991). Прогноз прочности бетона на растяжение на основе его прочности на сжатие: оценка существующих отношений для бетона с нормальным весом. ACI Materials Journal, Vol. 88, No. 3, pp. 302–309. Поиск в Google Scholar [77] ATIS, C. D. (2005). Прочностные свойства крупногабаритного роликового уплотненного и работоспособного бетона из золы-уноса и влияние условий отверждения.Исследование цемента и бетона, Vol. 35, стр. 1112 — 1121. Поиск в Google Scholar [78] JSCE (2007). Стандартные технические условия на бетонные конструкции, материалы и конструкции. Японское общество инженеров-строителей, Vol. 7, pp. 10–11. Поиск в Google Scholar [79] Комитет ACI (2011). Строительные нормы и правила для конструкционного бетона. Американский институт бетона, Фармингтон-Хиллз, Мичиган. Поиск в Google Scholar [80] JACKSON, N, DHIR, R.K (1990). Материалы гражданского строительства, Macmillan London, 4-е издание.Искать в Google Scholar [81] Патель, В. Н. (209). Испытание сорбционной способности для оценки устойчивости бетона к циклическому замерзанию-оттаиванию. Департамент гражданского строительства и прикладной механики, Университет Макгилла, Монреаль, Канада. Поиск в Google Scholar [82] SIDDIQUE, R. (2013). Прочность на сжатие, водопоглощение, сорбционная способность, сопротивление истиранию и проницаемость самоуплотняющегося бетона, содержащего угольный шлак. Констр. Строить. Матер. Vol. 47, стр. 1444-1450. Поиск в Google Scholar [83] ASTM C1567-11 (2011).Стандартный метод испытаний для определения потенциальной реакционной способности щелочного кремнезема для комбинаций вяжущих материалов и заполнителя (метод ускоренного строительного раствора). Американское общество испытаний и материалов, Филадельфия. Поиск в Google Scholar [84] WANG, S, BAXTER, L. (2007). Комплексное исследование золы уноса биомассы в бетоне: прочность, микроскопия, кинетика и долговечность. Технология топливных процессов. 88, pp. 1165-70. Поиск в Google Scholar [85] CHANG, C.F, CHEN, J. W. (2006). Экспериментальное исследование глубины карбонизации бетона. Исследование цемента и бетона, Vol. 36, стр. 1760-1767. Поиск в Google Scholar [86] WANG, S, LLAMAZOS, E, BAXTER, L, FONSECA, F. (2008). Прочность бетона из золы-уноса из биомассы: замерзание и оттаивание, а также быстрые тесты на проницаемость для хлоридов. Топливо, об. 87, стр. 359-64. Поиск в Google Scholar [87] ASTM C 1202-97 (1997). Стандартный метод испытаний для электрического определения способности хлоридов сопротивляться хлоридам ».Американское общество испытаний и материалов, Филадельфия. Поиск в Google Scholar [88] АМРУТА, Г., НАЯК, М., НАРАСИМХАН, К., РАДЖЕЕВА, С. В. (2089). Хлорид-ионная непроницаемость самоуплотняющихся бетонных смесей с большим объемом летучей золы. Int. J. Civil Environ. Англ. Vol. 11, No. 4, pp.29–35. Поиск в Google Scholar [89] ACI 515.1 (1985). Руководство по использованию систем гидроизоляции, гидроизоляции, защитных и декоративных барьеров для бетона, ACI Manual of Concrete Practice Masonry, Precast Concrete, Special Processes.Искать в Google Scholar [90] БДЭИР, Л. М. Х. (2012). Изучите некоторые механические свойства раствора с опилками как частичную замену песка. Анбарский журнал технических наук, Vol. 5, No. 1, pp. 22–30. Поиск в Google Scholar [91] KUMAR, D, SINGH, S, KUMAR, N, GUPTA, A. (2014). Недорогой строительный материал для бетона в виде опилок. Глобальный журнал исследований в области инженерии, Vol. 14, No. 4, pp. 1–5. Искать в Google Scholar [92] OLUTOGE, F. A.(2010) Исследования опилок и скорлупы пальмовых ядер в качестве агрегатной замены. ARPN Journal of Engineering and Applied Sciences, Vol. 5, No. 4, pp. 7–13 Искать в Google Scholar [93] BOOB, T. N. (2014). Выполнение опилок в недорогих пескоблоках. Американский журнал инженерных исследований (AJER), Vol. 3, No. 4, pp. 197-206. Поиск в Google Scholar [94] OSEI, D. Y, JACKSON, E. N. (2016). Прочность на сжатие бетона с использованием опилок в качестве заполнителя. Международный журнал научных и инженерных исследований, Vol.7, No. 4, pp. 1349–1353. Поиск в Google Scholar [95] НАРАЯНАН, А., ХЕМНАТ, Г., САМПАУЛ, К., МЭРИ, А. (2017). Замена мелкого заполнителя опилками. Международный журнал перспективных исследований в области фундаментальных инженерных наук и технологий, Vol. 3, No. 35, pp. 206 — 210. Поиск в Google Scholar [96] OKOROAFOR, S.U, IBEARUGBULAM, O.M, ONUKWUGHA, E.R, ANYAOGU, L, ADAH, E.I. Структурные характеристики опилочно-песчано-цементного композита. Международный журнал достижений в области исследований и технологий, Vol.6, No. 1, pp. 173–180. Поиск в Google Scholar [97] OYEDEPO, O.J, OLUWAJANA, S.D, AKANDE, S.P. (2014). Исследование свойств бетона с использованием опилок как частичной замены песка. Гражданские и экологические исследования, Том 6, № 2, стр. 35–42. Поиск в Google Scholar [98] АЛЬБЕРТ, М. Дж., ААЙЕНА, К. Дж., АНДЖУ, М. Р., БОБИНА, Э.Дж. ( 2016). Частичная замена мелкого заполнителя опилками для бетона. Международный журнал технологических исследований в машиностроении Vo.3, No. 9, pp. 2439–2443. Поиск в Google Scholar [99] THANDAVAMOORTHY, T. S. (2015). Древесные отходы как крупнозернистый заполнитель при производстве бетона. Европейский журнал экологического и гражданского строительства. Http://dx.doi.org/10.1080/19648189.2015.101663110.1080/19648189.2015.1016631Open DOISearch in Google Scholar [100] BUTT, W. A, GUPTA, K, JHA JN (2016 ) Прочностные характеристики глинистого грунта, стабилизированного золой опилок. Международный журнал геоинженерии, Vol. 7, вып.18, стр. 2–9. Поиск в Google Scholar [101] НИМЯТ, П.С., ТО К., Ю. (2013). Влияние золы из опилочной пыли (SDA) Pozzolana на характеристики бетона с добавлением цементной пасты при высоких температурах. Гражданские и экологические исследования, Vo. 3, No. 11, pp. 22 — 28. Искать в Google Scholar Деревянные блоки — виды, состав, особенности изготовления | Своими рукамиБезопасные недорогие материалы, существенно сокращающие сроки строительства, на рынке малоэтажного домостроения всегда актуальны. Что ожидать дачнику, не имея большой суммы на строительство дома? Доступная по цене и удовлетворяющая всем требованиям безопасности (пожарной, физической, химической и биологической) группа материалов, получившая условное название «арболит ». Древесная щепа разного размера (щепа, опилки, щепа) служит в этих материалах наполнителем, связующим. В качестве связующего используется бетон. Изначально сырье измельчается в крошку и обрабатывается минерализующим составом (сульфат кальция, хлорид кальция, сульфат алюминия, жидкое стекло и др.)), который действует как антисептик и усиливает адгезию связующего вещества к дереву. Затем «глазированные» минерализующие добавки, древесная стружка и цемент замешиваются в массу, из которой формируются материалы в виде пластин или блоков.
Масса достоинствБлагодаря объемной минерализации изделия из щебеночного бетона не гниют, геометрически устойчивы, устойчивы к влаге, не поддерживают горение, не выделяют вредных летучих веществ. Материалы обладают высокими теплоизоляционными свойствами, способны поддерживать тепловой комфорт в помещениях на уровне современных требований к теплоизоляции, поглощают шум. Биологическая стабильность материалов этой группы также заслуживает похвалы: они не подвержены воздействию насекомых, древоточцев или грызунов. Опилки + бетонСамый известный материал этой группы — цементно-стружечные плиты (ЦСП). Материалом для их производства служат опилки мелкой и средней фракций и цемент. В процессе производства все компоненты укладываются послойно (с мелкими опилками во внешнем слое и более крупными внутри) и запрессовываются в плиты плотностью 1100/1400 кг / м3. Толщина пластин варьируется от 8 до 36 мм. В зависимости от толщины и плотности такие изделия используются в самых разных местах: в качестве наружной обшивки каркасных конструкций, для устройства перегородок внутри сухих и влажных помещений, для устройства оснований под перекрытиями и мансардными перекрытиями, в помещениях. украшение подоконников и т. д.Находят свое применение плиты ДСП при опалубке, как съемной, так и несъемной. Чтобы закрепить цементно-стружечные плиты гвоздями, необходимо предварительно просверлить отверстия. Арболит: щепа + бетонДругая группа арболитов состоит из материалов, образованных из крупной крошки хвойных деревьев и портландцемента. Небольшие воздушные полости между крупными стружками обеспечивают этим материалам высокие тепло- и звукоизоляционные характеристики. Пористая структура позволяет им «дышать». Один из материалов этой группы — арболит — известен на отечественном рынке еще с советских времен.Фактически, это разновидность легкого бетона, и стружка имеет длину 2–20 мм, ширину 2–5 мм и толщину 5 мм. В качестве вяжущего используется обыкновенный портландцемент марки не ниже М400. Арболит делится на теплоизоляционный (плотность — до 450 кг / м 3 ), конструкционный и теплоизоляционный (450-600 кг / м 3 ) и конструкционный (600-800 кг / м 3 ). Последний используется в виде крупноформатных блоков, из которых возводятся малоэтажные малоэтажные дома. Смотрите также: Блоки из арболита своими руками (+ видео)
Технология «Велокс»Основным элементом строительной системы «Велокс» являются стружечно-цементные плиты размером 2000 х 500 мм и толщиной 25, 35, 50 и 75 мм, используемые в качестве несъемной опалубки.При комплектации опалубочной системы изнутри плит, из которых будет собираться внешняя стена, приклеивается теплоизоляционная вставка из пенополистирола. Таким образом, обеспечиваются высокие тепловые характеристики ограждающих конструкций. Монтаж первого ряда опалубки Velox производится по разметке на фундаменте. Монтаж плит начинается с углов. В местах стыковки стен опалубку фиксируют саморезами. Одновременно со сборкой первого ряда монтируют арматурный каркас и прокладывают скрытые инженерные коммуникации. Второй и последующие ряды опалубки собирают с зачисткой швов. Для заливки нераздельных секций плиты разрезают стационарной дисковой пилой или «болгаркой». Блоки «Дюрисол»Упростить и ускорить процесс возведения несъемной опалубки позволяет технология Durisol. При этом используются стружкоцементные блоки длиной 500 мм и высотой 250 мм, их толщина в зависимости от назначения составляет 150, 220, 250, 300 и 375 мм. Типовые серии включают стандартные, рядные, универсальные и дополнительные блоки для возведения внешних и внутренних несущих стен и межкомнатных перегородок. Из универсальных блоков выкладываем углы, перемычки, торцы, обрамление оконных и дверных проемов. В комплект поставки также входят утеплители из пенополистирола или минеральной ваты (по желанию клиента) толщиной 70-175 мм. После каждых четырех рядов кладки внутренняя полость опалубки заполняется бетонной смесью (вручную или с помощью бетононасоса). Как только бетон застынет, продолжайте сборку блоков. Чтобы уменьшить технологические перерывы, используйте подпорную конструкцию, которая позволяет возводить и бетонировать стену до высоты одного этажа.
См. Также: Арболит и другие строительные материалы на его основе (арболит, опилки, фибробетон и др.) ФибролитПри производстве фибролита (еще называемого фибробетоном) используют специальную стружку — длинную и тонкую (длиной 250-500 мм и шириной 1-4 мм).Это древесное волокно обрабатывают жидким стеклом и смешивают с бетоном, и из полученной смеси методом прессования формуют плиты толщиной 30-150 мм. Плиты обладают недостаточной прочностью на изгиб, но являются хорошими тепло- и звукоизоляторами. В зависимости от плотности материал делится на тепло- и звукоизоляционный (плотность 250-300 кг / м 3 ) и конструкционный (более 450 кг / м 3 ). Последняя используется в качестве несъемной опалубки и обшивки каркасных стен. akson-quick.ru © 2019
|