Газобетон — Википедия
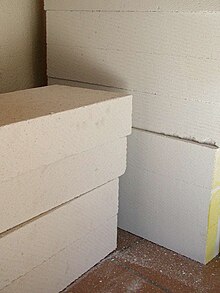
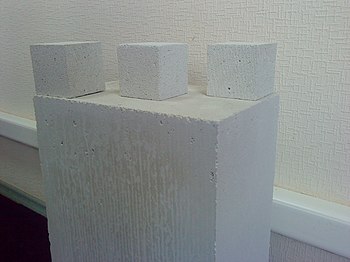
Газобето́н — разновидность ячеистого бетона; строительный материал, искусственный камень с равномерно распределёнными по всему объёму приблизительно сферическими, замкнутыми, но сообщающимися друг с другом порами диаметром 1—3 мм. По технологии окончательной обработки газобетон подразделяют на автоклавный газобетон и «неавтоклавный».
При производстве этого материала используются цемент, кварцевый песок и специализированные газообразователи, также, в состав смеси при его изготовлении иногда добавляют гипс, известь, промышленные отходы, такие, как, например, зола и шлаки металлургических производств.
Газообразование в замешенной на воде смеси обусловлено взаимодействием газообразователя, обычно мелкодисперсного металлического алюминия со сильнощелочным цементным или известковым раствором, в результате химической реакции образуются газообразный водород, вспенивающий цементный раствор, и алюминаты кальция.
Пылевидный алюминий неудобен для применения при замешивании раствора, так как сильно пылит. Поэтому в качестве специализированных газообразователей используются алюминиевые пасты и суспензии.
Типичный цикл производства газобетона: Перемешанные сухие ингредиенты смешиваются с водой, раствор заливается в форму. Происходит реакция щелочного водного раствора гидроксида кальция и газообразователя, приводящая к выделению водорода, который и «вспучивает» смесь. Смесь увеличивает объём и вспучивается как тесто. После предварительного схватывания цементного раствора, монолит извлекают из формы и разрезают на заготовки блоков, плит, панелей. После этого разрезанные заготовки подвергают обработке водяным паром в автоклаве для придания им окончательной прочности, либо высушиваются в электроподогреваемых сушильных камерах.
Газобетон легко обрабатывается: пилится, сверлится, строгается обычными стальными инструментами, даже без твердосплавных напаек. В него легко забиваются гвозди, скобы, установочные изделия. Со временем газобетон ещё более твердеет. Не горюч, так как состоит только из минеральных компонентов.
Имеет меньшую естественную радиоактивность по сравнению с обычным бетоном, так как в его состав не входит гранитный щебень, слюды, — составная часть природных гранитов, которые имеют повышенную естественную радиоактивность из-за концентрации в этих минералах тория и урана.
Разнообразие строительных материалов на рынке приумножается с каждым десятилетием. Если в Средние Века основными материалами были искусственный камень, древесина и кирпич, то сейчас появилось множество новых стройматериалов с улучшенными эксплуатационными характеристиками. В их число вошел газобетон, промышленное производство которого началось только в 1929 году. Газобетон является разновидностью ячеистого бетона (к этой группе также относятся пенобетон и газопенобетон). Впервые изготовлен в 1889 году, а спустя 40 лет поступил в производство.
Газобетон применяется в жилищном, коммерческом и промышленном строительстве. Основной объем потребления занимают строительные (стеновые и перегородочные блоки), также применяются армированные изделия (перемычки и плиты перекрытия).
Классификация газобетонов
- По назначению:
- конструкционные.
- конструкционно-теплоизоляционные.
- теплоизоляционные.
- По условиям твердения:
- автоклавные (синтезного твердения) — твердеющие в среде насыщенного пара при давлении выше атмосферного;
- неавтоклавные (гидратационного твердения) — твердеющие в естественных условиях, при электропрогреве или в среде насыщенного пара при атмосферном давлении.
- По виду вяжущих и кремнеземистых компонентов подразделяют:
- по виду основного вяжущего:
- на известковых вяжущих, состоящих из извести-кипелки более 50 % по массе, шлака и гипса или добавки цемента до 15 % по массе;
- на цементных вяжущих, в которых содержание портландцемента 50 % и более по массе;
- на смешанных вяжущих, состоящих из портландцемента от 15 до 50 % по массе, извести или шлака, или шлако-известковой смеси;
- на шлаковых вяжущих, состоящих из шлака более 50 % по массе в сочетании с известью, гипсом или щелочью;
- на зольных вяжущих, в которых содержание высокоосновных зол 50 % и более по массе;
- по виду кремнеземистого компонента:
- на природных материалах — тонкомолотом кварцевом и других песках;
- на вторичных продуктах промышленности — золе-унос ТЭС, золе гидроудаления, вторичных продуктах обогащения различных руд, отходах ферросплавов и других.
- по виду основного вяжущего:
История появления технологии производства автоклавного газобетона
Для придания бетону пористой структуры чех Гоффман добавил в цементные и гипсовые растворы кислоты, углекислые и хлористые соли. Соли, взаимодействуя с растворами, выделяли газ, который и делал бетон пористым. За изобретённый газобетон Гоффман в 1889 году получил патент, но дальше этого у него дело не пошло.
Замысел Гоффмана развили американцы Аулсворт и Дайер. В качестве газообразователя в 1914 году они использовали порошки алюминия и цинка. В процессе химической реакции этих порошков с гашеной известью выделялся водород, который и способствовал образованию в бетоне пористой структуры. Это изобретение оказалось столь значимым, что его и поныне считают отправной точкой технологии изготовления газобетона.
Свой вклад в дело совершенствования газобетона (газосиликата) внёс шведский архитектор и ученый Юхан Аксель Эрикссон. В своих исследованиях он пытался вспучивать раствор извести, кремнезёмистых компонентов и цемента за счёт взаимодействия этого раствора с алюминиевым порошком. Этот подход увенчался успехом. В 1929 году в местечке Иксхульт фирмой «Итонг» (Ytong) был начат промышленный выпуск газобетона. Инженерами этой фирмы за основу была взята технология тепловлажностного воздействия в автоклавах на известково-кремнезёмистые компоненты, запатентованная в 1880 году немецким профессором В. Михаэлисом. Только за первый год работы этим предприятием было произведено 14 тысяч м³ газобетона (газосиликата). Следует заметить, что фирмой «Итонг» цемент не применялся вообще.
Несколько иной метод производства газобетона внедрила в жизнь в 1934 году шведская фирма «Сипорекс» (Siporex). Он основывается на применении смеси из портландцемента и кремнезёмистого компонента. Известь в данном случае не применялась. Авторы этого метода — инженеры финн Леннарт Форсэн и швед Ивар Эклунд. Научные и практические достижения вышеперечисленных инженеров и стали впоследствии основой промышленного производства как газосиликатов, так и газобетонов во многих странах мира.
История производства ячеистых бетонов в СССР
Производство ячеистых бетонов в СССР стало активно развиваться в 1930-е годы. Автоклавные ячеистые бетоны (АЯБ) с газовой поризацией появились в промышленных масштабах к 1950-м годам. К 1960-м годам производство АЯБ стало самостоятельным развивающимся научным направлением, во многом опережающим европейские наработки в этой области.
К концу 1980-х годов в СССР из ячеистых бетонов было построено более 250 млн м² зданий различного назначения (жилых, общественных, производственных, животноводческих). При этом, несмотря на высокий уровень отечественных научных разработок, ориентиром для советской промышленности служили западно-европейские достижения (понижение плотности панелей и блоков вплоть до 300 кг/м³), основанные, в первую очередь, на стабильном сырье и оборудовании, обеспечивающем высокую однородность материала.
В 1987 г. с принятием очередной жилищной программы СССР основным средством её реализации стала научно-производственно-техническая программа «Система эффективного строительства жилых и общественных зданий из ячеистых бетонов», которая предполагала строительство около 250 новых заводов по производству АЯБ с доведением общего его выпуска к 1995 г. до 40-45 млн м³/год.
Планы по этой программе предусматривали не только механическое наращивание объёмов выпуска автоклавных бетонов. Важной задачей было также и снижение средней плотности выпускаемой продукции (для блоков она составляла 600—700 кг/м³). В программе говорилось: «Таким образом, семикратное увеличение производства ячеистых бетонов в нашей стране следует сопровождать двукратным снижением их объёмной массы».
К 2011 году производство ячеистого бетона в России составило более 3,2 млн м³/год, количество заводов-производителей АЯБ — более 80, до 2015 года планируется к запуску 10.
Наиболее крупные и современные предприятия по выпуску газобетона в РФ, в основном, построены в 1990-е годы.
ГОСТы и СНиПы
- ГОСТ 25485-89 «Бетоны ячеистые»
- ГОСТ 21520-89 «Блоки из ячеистых бетонов стеновые мелкие»
- СН 277-80 «Инструкция по изготовлению изделий из ячеистого бетона»
- ГОСТ 31359-2007 «Бетоны ячеистые автоклавного твердения. Технические условия»
- ГОСТ 31360-2007 «Изделия стеновые неармированные из ячеистого бетона автоклавного твердения»
См. также
Примечания
Ссылки
Газобетон — Википедия. Что такое Газобетон
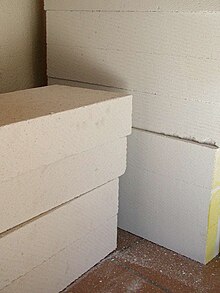
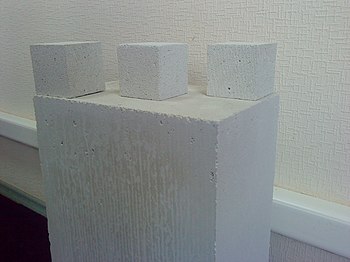
При производстве этого материала используются цемент, кварцевый песок и специализированные газообразователи, также, в состав смеси при его изготовлении иногда добавляют гипс, известь, промышленные отходы, такие, как, например, зола и шлаки металлургических производств.
Газообразование в замешенной на воде смеси обусловлено взаимодействием газообразователя, обычно мелкодисперсного металлического алюминия со сильнощелочным цементным или известковым раствором, в результате химической реакции образуются газообразный водород, вспенивающий цементный раствор, и алюминаты кальция.
Пылевидный алюминий неудобен для применения при замешивании раствора, так как сильно пылит. Поэтому в качестве специализированных газообразователей используются алюминиевые пасты и суспензии.
Типичный цикл производства газобетона: Перемешанные сухие ингредиенты смешиваются с водой, раствор заливается в форму. Происходит реакция щелочного водного раствора гидроксида кальция и газообразователя, приводящая к выделению водорода, который и «вспучивает» смесь. Смесь увеличивает объём и вспучивается как тесто. После предварительного схватывания цементного раствора, монолит извлекают из формы и разрезают на заготовки блоков, плит, панелей. После этого разрезанные заготовки подвергают обработке водяным паром в автоклаве для придания им окончательной прочности, либо высушиваются в электроподогреваемых сушильных камерах.
Газобетон легко обрабатывается: пилится, сверлится, строгается обычными стальными инструментами, даже без твердосплавных напаек. В него легко забиваются гвозди, скобы, установочные изделия. Со временем газобетон ещё более твердеет. Не горюч, так как состоит только из минеральных компонентов.
Имеет меньшую естественную радиоактивность по сравнению с обычным бетоном, так как в его состав не входит гранитный щебень, слюды, — составная часть природных гранитов, которые имеют повышенную естественную радиоактивность из-за концентрации в этих минералах тория и урана.
Разнообразие строительных материалов на рынке приумножается с каждым десятилетием. Если в Средние Века основными материалами были искусственный камень, древесина и кирпич, то сейчас появилось множество новых стройматериалов с улучшенными эксплуатационными характеристиками. В их число вошел газобетон, промышленное производство которого началось только в 1929 году. Газобетон является разновидностью ячеистого бетона (к этой группе также относятся пенобетон и газопенобетон). Впервые изготовлен в 1889 году, а спустя 40 лет поступил в производство.
Физико-механические свойства
- На производство газобетонного изделия требуется меньше цемента.
- Газобетон по простоте обработки сравним с деревом: он легко пилится, сверлится.
Применение
Газобетон применяется в жилищном, коммерческом и промышленном строительстве. Основной объем потребления занимают строительные (стеновые и перегородочные блоки), также применяются армированные изделия (перемычки и плиты перекрытия).
В малоэтажном индивидуальном строительстве самонесущая способность газобетонных блоков позволяет использовать их в качестве материала для наружных стен домов небольшой этажности (до пяти этажей). При строительстве многоэтажных каркасно-монолитных домов, когда блоки играют роль ограждающих конструкций (фасады и перегородки), этажность практически не ограничена.
Недостатки
К основным недостаткам газобетона относится быстрое разрушение материала под воздействием влаги[источник не указан 115 дней].
Строения после постройки необходимо обязательно закрывать от внешней среды, в противном случае, газобетон начинает разрушаться.
Согласно действующим ГОСТам долговечность газобетона определена на отметке в 50 лет.
Также среди недостатков газобетона стоит отметить:
- Низкая прочность монтажа крепёжных материалов(дюбель-саморезов, анкеров). Они не держатся, так как газобетон имеет пористую структуру. Особенно данный недостаток выражен в автоклавном газобетоне[источник не указан 115 дней].
- Низкая плотность газобетона влияет на кaчество установки окон и дверей, они со временем расшатываются. Особенно заметно в строениях, возведенных из автоклавного газобетона[источник не указан 115 дней].
- Свойства материала в значительной степени определяются бетонной составляющей.
- Стена из автоклавного газобетона имеет низкие показатели сцепления со штукатурной смесью[источник не указан 115 дней], а значит, требует дополнительной подготовки перед оштукатуриванием.
- Усадка газобетона в три раза больше, чем у полистиролбетона и пенобетона –2 мм/метр[источник не указан 115 дней].
- Блоки из газобетона относятся к группе горючести НГ, то есть они не горючи и огнестойки. Тем не менее, под воздействием высокой температуры, вблизи источника огня, газобетонные блоки начинают взрываться и хотя остающийся бетонный каркас не позволяет разрушится блокам до конца, их прочность и сопротивление теплопередаче при этом снижается в несколько раз. Использование газобетонных блоков без огнестойкой защиты запрещено действующим СНИП[источник не указан 115 дней].
Классификация газобетонов
- По назначению:
- конструкционные.
- конструкционно-теплоизоляционные.
- теплоизоляционные.
- По условиям твердения:
- автоклавные (синтезного твердения) — твердеющие в среде насыщенного пара при давлении выше атмосферного;
- неавтоклавные (гидратационного твердения) — твердеющие в естественных условиях, при электропрогреве или в среде насыщенного пара при атмосферном давлении.
- По виду вяжущих и кремнеземистых компонентов подразделяют:
- по виду основного вяжущего:
- на известковых вяжущих, состоящих из извести-кипелки более 50 % по массе, шлака и гипса или добавки цемента до 15 % по массе;
- на цементных вяжущих, в которых содержание портландцемента 50 % и более по массе;
- на смешанных вяжущих, состоящих из портландцемента от 15 до 50 % по массе, извести или шлака, или шлако-известковой смеси;
- на шлаковых вяжущих, состоящих из шлака более 50 % по массе в сочетании с известью, гипсом или щелочью;
- на зольных вяжущих, в которых содержание высокоосновных зол 50 % и более по массе;
- по виду кремнеземистого компонента:
- на природных материалах — тонкомолотом кварцевом и других песках;
- на вторичных продуктах промышленности — золе-унос ТЭС, золе гидроудаления, вторичных продуктах обогащения различных руд, отходах ферросплавов и других.
- по виду основного вяжущего:
История появления технологии производства автоклавного газобетона
Для придания бетону пористой структуры чех Гоффман добавил в цементные и гипсовые растворы кислоты, углекислые и хлористые соли. Соли, взаимодействуя с растворами, выделяли газ, который и делал бетон пористым. За изобретённый газобетон Гоффман в 1889 году получил патент, но дальше этого у него дело не пошло.
Замысел Гоффмана развили американцы Аулсворт и Дайер. В качестве газообразователя в 1914 году они использовали порошки алюминия и цинка. В процессе химической реакции этих порошков с гашеной известью выделялся водород, который и способствовал образованию в бетоне пористой структуры. Это изобретение оказалось столь значимым, что его и поныне считают отправной точкой технологии изготовления газобетона.
Свой вклад в дело совершенствования газобетона (газосиликата) внёс шведский архитектор и ученый Юхан Аксель Эрикссон. В своих исследованиях он пытался вспучивать раствор извести, кремнезёмистых компонентов и цемента за счёт взаимодействия этого раствора с алюминиевым порошком. Этот подход увенчался успехом. В 1929 году в местечке Иксхульт фирмой «Итонг» (Ytong) был начат промышленный выпуск газобетона. Инженерами этой фирмы за основу была взята технология тепловлажностного воздействия в автоклавах на известково-кремнезёмистые компоненты, запатентованная в 1880 году немецким профессором В. Михаэлисом. Только за первый год работы этим предприятием было произведено 14 тысяч м³ газобетона (газосиликата). Следует заметить, что фирмой «Итонг» цемент не применялся вообще.
Несколько иной метод производства газобетона внедрила в жизнь в 1934 году шведская фирма «Сипорекс» (Siporex). Он основывается на применении смеси из портландцемента и кремнезёмистого компонента. Известь в данном случае не применялась. Авторы этого метода — инженеры финн Леннарт Форсэн и швед Ивар Эклунд. Научные и практические достижения вышеперечисленных инженеров и стали впоследствии основой промышленного производства как газосиликатов, так и газобетонов во многих странах мира.
История производства ячеистых бетонов в СССР
Производство ячеистых бетонов в СССР стало активно развиваться в 1930-е годы. Автоклавные ячеистые бетоны (АЯБ) с газовой поризацией появились в промышленных масштабах к 1950-м годам. К 1960-м годам производство АЯБ стало самостоятельным развивающимся научным направлением, во многом опережающим европейские наработки в этой области.
К концу 1980-х годов в СССР из ячеистых бетонов было построено более 250 млн м² зданий различного назначения (жилых, общественных, производственных, животноводческих). При этом, несмотря на высокий уровень отечественных научных разработок, ориентиром для советской промышленности служили западно-европейские достижения (понижение плотности панелей и блоков вплоть до 300 кг/м³), основанные, в первую очередь, на стабильном сырье и оборудовании, обеспечивающем высокую однородность материала.
В 1987 г. с принятием очередной жилищной программы СССР основным средством её реализации стала научно-производственно-техническая программа «Система эффективного строительства жилых и общественных зданий из ячеистых бетонов», которая предполагала строительство около 250 новых заводов по производству АЯБ с доведением общего его выпуска к 1995 г. до 40-45 млн м³/год.
Планы по этой программе предусматривали не только механическое наращивание объёмов выпуска автоклавных бетонов. Важной задачей было также и снижение средней плотности выпускаемой продукции (для блоков она составляла 600—700 кг/м³). В программе говорилось: «Таким образом, семикратное увеличение производства ячеистых бетонов в нашей стране следует сопровождать двукратным снижением их объёмной массы».
К 2011 году производство ячеистого бетона в России составило более 3,2 млн м³/год, количество заводов-производителей АЯБ — более 80, до 2015 года планируется к запуску 10.
Наиболее крупные и современные предприятия по выпуску газобетона в РФ, в основном, построены в 1990-е годы.
ГОСТы и СНиПы
- ГОСТ 25485-89 «Бетоны ячеистые»
- ГОСТ 21520-89 «Блоки из ячеистых бетонов стеновые мелкие»
- СН 277-80 «Инструкция по изготовлению изделий из ячеистого бетона»
- ГОСТ 31359-2007 «Бетоны ячеистые автоклавного твердения. Технические условия»
- ГОСТ 31360-2007 «Изделия стеновые неармированные из ячеистого бетона автоклавного твердения»
Выводы
Можно сделать несколько выводов про газобетон:
- Газобетон – разновидность ячеистого бетона.
- Состоит из нескольких элементов: очищенный кварцевый песок, вода, цемент, известь, алюминиевый преобразователь.
- Газоблок хорошо подходит для изготовления: элементов теплоизоляции, огнестойких изделий, стеновых блоков различных габаритов, панелей перекрытия.
- Обладает множеством преимуществ, среди которых экологичность, малый удельный вес, прекрасные тепло- и звукоизоляционные характеристики, наличие системы «паз-гребень», устойчивость к негативным факторам окружающей среды, простой монтаж и удобная транспортировка и т.д.
- В строительстве используется для возведения несущих и каркасных стен, внутренних перегородок, заполнения монолитно-каркасных конструкций, ремонта стен.
См. также
Примечания
Ссылки
История газобетона
Газобетон был изобретён в XIX веке в Чехии. Инженер Гоффман долгое время экспериментировал с составом бетона, чтобы сделать его более лёгким и хорошо сохраняющим тепло. В итоге в растворы цемента и гипса он добавил кислоты и соли, получив пористый бетон. Это изобретение запатентовали в 1889 году, и оно получило развитие уже в Америке.
Здесь в качестве газообразователя американцы Аулсворт и Дайер применили порошки алюминия и цинка, при взаимодействии с которыми из гашёной извести выделялся водород и формировал ячеистую структуру изделий. Именно этот поворотный момент принято считать отправной точкой в изготовлении газобетона.
В 20-х годах XX века шведский архитектор Юхан Аксель Эрикссон сделал ещё один большой шаг вперёд, создав газосиликат — газобетон с известковым компонентом и автоклавной обработкой. В 1929 году в городке Иксухльт началось промышленное изготовление газобетона, который впоследствии даже носил название «Итонг», как у фирмы—производителя.
Шведами Эклундом и Форсэном из компании «Сипорекс» в 30-х годах была разработана новая формула газобетона без использования извести, которая стала применяться на многих производствах.
В Советском Союзе первый автоклавный газобетон произвели на рижском заводе по лицензии той самой компании «Сипорекс» в 1937 году. Здания, возведённые из этих блоков, стоят до сих пор.
Газобетон стал широко применяться после Великой Отечественной Войны, когда нужно было быстрыми темпами и без огромных затрат восстанавливать архитектуру и промышленность городов.
В 50-х годах ячеистый автоклавнй бетон производился уже в промышленных масштабах на заводах по всей стране: Новосибирске, Набережных Челнах, Луганске, Ленинграде и в других городах. В 60-70 годах советские инженеры уже разрабатывали собственное оборудование и технологии производства, которыми впоследствии также использовались и в других государствах.
В 80-х годах была принята новая жилищная программа, которая включала большие объёмы строительства из газоблоков, а значит, и увеличение числа заводов-изготовителей этого стройматериала. В 90-х годах он стал широко использоваться для строительства именно жилых помещений.
По данным Национальной ассоциации производителей автоклавного газобетона, в России на 2012 год насчитывалось 62 работающих предприятия по выпуску газоблоков. Суммарно они производили 14,5 млн куб.м стройматериала. Естественно, это продукт более совершенный, нежели десятки лет назад. В 2014 году на фоне неблагоприятной экономической ситуации объёмы снизились до 12,9 млн куб.м в год.
Основная тенденция в развитии технологий — снижение плотности газобетона. Установлено, что этот показатель во многом зависит от территории производства и местных строительных стандартов. Так, наиболее лёгкий материал получают на северо-западе страны, самый тяжёлый — в Сибири.
История изобретения и использования газобетона
К современным строительным материалам предъявляются очень серьезные требовании в нынешних реалиях, которые можно выразить формулой «трёх Э» — это экономичность, энергоэффективность и конечно же экологичность. Вдобавок стройматериал должен быть высокопрочным и легким в применении. Конечно же, Вы наверняка узнали, прочитав все выше перечисленные свойства, газобетон.
История изобретения газобетонных блоков
Газобетон или газобетонный блок, как его сегодня называют, «родился» в Чехии в 1889 году. «Отцом-создателем» этого материала считается ученый и изобретатель Гофман, который соединив соли, углекислые и хлорные кислоты с цементным раствором заметил, что в бетоне стали формироваться поры. Так появился этот уникальный строительный материал, который мы привыкли называть газоблок.
Спустя 25 лет, в 1914 году, два американских инженера Дайер и Аулсворт, проведя опыты с добавлением цинка и алюминия для лучшего газообразования смеси, получили технологию, которая положила начало широкому применению ячеистых бетонов при строительстве домов. Пористая структура, которая сформировалась при применении этих компонентов, «дала» возможность газобетону «дышать», что в свою очередь делает более комфортным проживание в домах возведенных из этого материал.
А еще через 15 лет, в 1929 году, архитектор и ученый из Швеции Аксель Эрикссон усовершенствовал производство газосиликатов, использовав технологию с применением высокой температуры и пара на основе соединения с кремнезистыми компонентами. Так к газобетону добавилось слово «автоклавный».
Спустя 5 лет, в это был уже 1934 год, специалисты компании «Сипорекс»Леннард Форсени и Ивар Эвклунд усовершенствовали метод Акселя Ерикссона, добавив в газосиликаты портландцемент. Данная технология оказалась очень успешной и стала широко использоваться в производстве газобетонов во многих странах мира.
Газобетон в Совестском Союзе
После войны Советскому Союзу нужно было восстанавливать страну после масштабных разрушений, поэтому понадобился недорогой и легкий в производстве строительный материал. Так в 50-е годы прошлого века газобетоны попали в СССР, где было налажено его производство более чем на 80-ти заводах, количество которых к конце 80-х увеличилось до 120.
Главными достоинствами ячеистых газобетонов, из-за которых они получили популярность в СССР и во многих странах мира, стали звукоизоляция, теплозащита и, конечно же, быстровозводимость зданий. Если сравнивать газобетон с пеноблоком, то окажется, что газобетон гораздо прочнее и легок в обработке (пилится простой ножовкой).
Немаловажную роль имеет еще такое качество газобетона, как вес. Не большие нагрузки на фундаменты возводимых строений позволяют сэкономить на их формировании, увеличив срок эксплуатации домов. Исследовав значения экологических показателей с учетом последствий аварии на Чернобыльской АЭС, надо сказать, что газобетон экологически безопасный строительный материал, обычный радиационный фон которого всего 12 мкр./ч.
Состав газобетонов довольно прост и состоит из: порлендцемент и извесь – вяжущее вещество, алюминиевая пудра – газообразователь, и вода.
Существует два способа производства ячеистого бетона – это автоклавный и неавтоклавный. Материал, полученный в автоклаве еще называют газосиликатом. Все эти материала сегодня широко применяются при возведении различных зданий и заняли достойное место среди лидеров строительного рынка.
Некоторые особенности производства газобетона
Первый выпуск газобетонов датирован 30-ми годами прошлого века. Создателем метода промышленного изготовления ячеистых автоклавных бетонов стал ученый-инженер из Швеции Эрикссон. Первый газобетонный блок появился в 1929 году под маркой Ytong(Итонг), а в 1939 году стал продаваться газобетон фирмы Siporex (Сипорекс), который использовал другую технологию, описанную нами выше. Оба способа изготовления были в принципе идентичными, первые применяли в производстве известь, а другие – цемент. Отсюда пошло различие в названиях этого ячеистого бетона: марку Итонг стали называть газосиликатом, а продукцию фирмы Сипорекс – газобетоном. В настоящее время производится газобетон по обеим технологиям.
Пройдя обработку в автоклаве, газобетон приобретает хороший показатели прочности. Хотя пенобетон схож по своей визуальной идентичности с газоблоками, но не обладает такой прочностью. Газобетон конечно подороже пеноблоков, но при возведении несущих стен не поднимаются вопросы связанные с прочностью конструкции дома.
Из чего же производится газобетон (газоблок)
Производство газобетонов осуществляется из экологически чистых материалов:
-
Цемент;
-
Известь;
-
Вода;
-
Алюминиевая пудра;
-
Кварцевый песок.
Кварцевый песок перерабатывают в песочный шлам и перемешивают с другими компонентами. Сформированную смесь переливают в специальные емкости, где после химических процессов создается пористый состав ячеистого бетона, после чего осуществляется нарезание по необходимым размерам будущих блоков. Дальше идет процесс обработки нарезанных по размеру блоков в автоклаве при температуре 180-200 градусов водяного пара под высоким давлением. После завершения всех этих манипуляций на свет появляется совершенно новый минерал, который химики называют доберморитом, благодаря которому газобетон приобретает просто отличные свойства по прочности и усадке материала. И для справки: доберморит в своем составе уже не имеет компонентов, из которых он создавался, то есть в результате химической реакции получается совершенно другой материал по составу и своей структуре
Особенности применения газобетона
В наше время газобетон или как его называют многие газоблок является одним из наиболее популярных среди стеновых строительных материалов при строительстве домов, коттеджей а также зданий хозяйственного, жилого или технического предназначения.Даже новичок может правильно положить кладку газобетона, хотя в таком деле как строительство собственного дома, работу по возведению, лучше отдать профессионалам.
На современном строительном рынке газобетонные блоки это один из самых популярных строительных материалов, применяемых для возведения домов, как индивидуального строительства, так и хозяйственнного и промышленного назначения. Любой неподготовленный в строительстве человек может в принципе без особых сложностей произвести кладку газобетонных блоков, но так как строительство жилого дома дело серьезное, то мы все-таки рекомендуем доверить это профессионалам.
Наиглавнейшим и неоспоримым фактом является теплозащита газобетонных блоков. Если сравнивать эти показатели газоблоков с керамическим кирпичом, то разница будет видна не вооруженным глазом. Показываем, газобетонный блок: влажность 12%, коэффициент теплопроводности 0,145 Вт/м °С, в сухом состоянии 0,12 Вт/м °С; керамический кирпич: коэффициент теплопроводности0,55-0,64 Вт/м °С, эффективный — 0,25-0,5 Вт/м °С при марке М75-125. Отсюда становится понятным, что теплозащита в доме из газобетонных блоков будет в 5-6 раз больше, чем в кирпичном.
Окупаемость газосиликатов складывается в основном из экономии на отопление дома, при растущих ценах на энергоносители (газ, электричество, дрова и т.д).и это становится заметно уже после первой холодной зимы.
Еще один момент, по объему 1 газбетонный блок=16 керамических кирпичей, а разница в массе порядка 60 кг, что существенно уменьшает давление на фундамент и сокращает время строительства.
Каждый строительный материал имеет свои особенности применения. Безусловно, они есть и у газобетона. Расскажем о них. Для того чтобы ваш дом был теплее мы рекомендуем при кладке газобетонных блоков использовать специальную клеевую массу, которая гарантирует минимальные теплопотери из-за своего небольшого слоя между блоками в кладке. Избегая создания так называемых мостков холода. При использовании песочно-цементного раствора толщина раствора в кладке будет на уровне 15-22 мм, а применяя клеевую массу, толщина будет 2-3 мм. Клеевую смесь рекомендуется использовать только с блоками из ячеистого бетона, с другими материалами применять ее запрещено.
Надо еще помнить о том, что теплоизоляция газобетонных блоков с большой пористостью больше, большая пористость это меньше прочность, поэтому при проведении проектных расчетов нужно учитывать все моменты возведения стен. Несущие стены естественно необходимо поднимать из газобетона большей прочности, а для внутренних перегородок применять блоки с большей пористостью.
Газобетон это достойный внимания строительный материал, построив из которого свой дом вы проживете в нем долго и счастливо!
31.07.2017
Газобетон — Вікіпедія
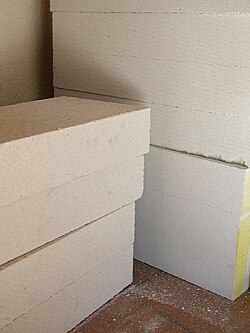
Газобетон — різновид пористого бетону; будівельний матеріал, штучний камінь з рівномірно розподіленими по всьому об’єму приблизно сферичними, замкнутими один з одним порами діаметром 1-3 мм. При виробництві цього матеріалу використовуються цемент, кварцовий пісок і спеціалізований газоутворювач, також, до складу суміші при його виготовленні іноді додають гіпс, вапно, промислові відходи, такі, як, наприклад, зола і шлаки металургійних виробництв.
Газоутворення в замішаній на воді суміші обумовлено взаємодією газоутворювача, зазвичай дрібнодисперсного металевого алюмінію з сильнолужним цементним або вапняним розчином. У результаті хімічної реакції утворюються газоподібний водень, який спінює цементний розчин, і алюмінати кальцію.
Пилоподібний алюміній незручний для застосування при замішуванні розчину, бо створює багато пилу. Тому як спеціалізовані газоутворювачі використовують алюмінієві пасти та суспензії.
Типовий цикл виробництва газобетону[ред. | ред. код]
Перемішані сухі інгредієнти змішують з водою, розчин заливають у форму. Відбувається реакція лужного водного розчину гідроксиду кальцію й газоутворювача, що приводить до виділення водню, який і «спучує» суміш. Суміш збільшує обсяг і спучується як тісто. Після попереднього схоплювання цементного розчину, моноліт виймають з форми і розрізають на заготовки блоків, плит, панелей. Після цього розрізані заготовки піддають обробці водяною парою в автоклаві для додання їм остаточної міцності, або висушуються в електронагріваючих сушильних камерах. За технологією остаточної обробки газобетон підрозділяють на «автоклавний» і «неавтоклавний».
Фізико-механічні властивості[ред. | ред. код]
Газобетон легко обробляється: пиляється, свердлиться, стружиться звичайними сталевими інструментами, навіть без твердосплавних напайок. У нього легко забиваються цвяхи, скоби, настановні вироби. З часом газобетон ще більш твердне. Не горючий, тому що складається тільки з мінеральних компонентів.
Має меншу природну радіоактивність у порівнянні зі звичайним бетоном, так як в його склад не входить гранітний щебінь, слюди, — складова частина природних гранітів, мають підвищену природну радіоактивність через концентрацію в цих мінералах торію та урану.
Газобетон широко використовується як будівельний матеріал у всьому світі. В даний час (2014) його виробляють більше 240 заводів у 50 країнах з сумарною потужністю близько 60 млн м³ будівельних виробів з газобетону.
Газобетон застосовують у житловому, комерційному та промисловому будівництві. Основний обсяг споживання займають будівельні (стінові й перегородкові блоки), також застосовуються армовані вироби (перемички та плити перекриття).
У малоповерховому індивідуальному будівництві самонесуча здатність газобетонних блоків дозволяє використовувати їх як матеріал для зовнішніх стін будинків невеликої поверховості (в середньому до трьох поверхів). При будівництві багатоповерхових каркасно-монолітних будинків, коли блоки відіграють роль огороджувальних конструкцій (фасади і перегородки), поверховість практично не обмежена.
Класифікація газобетонів[ред. | ред. код]
За призначенням:
- конструкційні.
- конструкційно-теплоізоляційні.
- теплоізоляційні.
За умовами твердіння:
- автоклавні (синтезного твердіння) — тверднуть в середовищі насиченої пари при тиску вище атмосферного;
- неавтоклавні (гідратаційного твердіння) — тверднуть в природних умовах, при електропрогріванні або в середовищі насиченої пари при атмосферному тиску.
За видом в’яжучих і кремнеземистих компонентів підрозділяють:
1. За видом основного в’яжучого:
- на вапняних в’яжучих, які складаються з вапна-кипілки більше 50 % за масою, шлаку і гіпсу або добавки цементу до 15 % за масою;
- на цементних в’яжучих, в яких вміст портландцементу 50 % і більше по масі;
- на змішаних в’яжучих, які складаються з портландцементу від 15 до 50 % за масою, вапна або шлаку, або шлако-вапняної суміші;
- на шлакових в’яжучих, які складаються з шлаку більше 50 % за масою в поєднанні з вапном, гіпсом або лугом;
д) на зольних в’яжучих, в яких вміст високолужних зол 50 % і більше по масі;
2. За видом кремнеземистого компонента:
- а) на природних матеріалах -тонкомолотому кварцовому та інших пісках;
- б) на вторинних продуктах промисловості — золі-виносу ТЕС, золі гідровидалення, вторинних продуктах збагачення різних руд, відходах феросплавів та інших.
Історія появи технології виробництва автоклавного газобетону[ред. | ред. код]
Для того, щоб зробити структуру бетону пористою, чех Гоффман додав в цементні і гіпсові розчини кислоти, вуглекислі й хлористі солі. Солі, взаємодіючи з розчинами, виділяли газ, який і робив бетон пористим. За винайдений газобетон Гоффман в 1889 році отримав патент, але далі цього у нього справа не пішла.
Задум Гоффмана розвинули американці Аулсворт і Дайер. Як газоутворювач у 1914 році вони використовували порошки алюмінію і цинку. У процесі хімічної реакції цих порошків з гашеним вапном виділявся водень, який і сприяв утворенню в бетоні пористої структури. Це винахід виявився настільки значущим, що його і понині вважають відправною точкою технології виготовлення газобетону.
Свій внесок у справу вдосконалення газобетону (газосилікату) додав шведський архітектор і вчений Юхан Аксель Ерікссон. У своїх дослідженнях він намагався спучувати розчин вапна, кремнеземистих компонентів і цементу за рахунок взаємодії цього розчину з алюмінієвим порошком. Цей підхід увінчався успіхом. У 1929 році в містечку Іксхульт фірмою «Ітонг» (Ytong) був початий промисловий випуск газобетону. Інженерами цієї фірми за основу була взята технологія тепловологістного впливу в автоклавах на вапняно-кремнеземисті компоненти, запатентована в 1880 році німецьким професором В. Міхаелісом. Тільки за перший рік роботи цим підприємством було вироблено 14000 м³ газобетону (газосилікату). Слід зауважити, що фірмою «Ітонг» цемент не застосовувався взагалі.
Дещо інший метод виробництва газобетону впровадила в життя в 1934 році шведська фірма «Сипорекс» (Siporex). Він ґрунтується на застосуванні суміші з портландцементу і кремнеземистого компонента. Вапно в даному випадку не застосовувалася. Автори цього методу — інженери фін Леннарт Форсен і швед Івар Еклунд. Наукові та практичні досягнення вищеперелічених інженерів і стали згодом основою промислового виробництва як газосилікату, так і газобетонів в багатьох країнах світу.
Переваги та недоліки газобетону[ред. | ред. код]
Переваги[ред. | ред. код]
- На виробництво газобетонного виробу потрібно менше цементу, ніж звичайного бетону.
- Газобетон за простотою обробки порівняний із деревом: він легко пиляється, свердлиться.
Недоліки[ред. | ред. код]
- Крихкість. Стіни з газобетону не бояться механічних пошкоджень, але окремі блоки вимагають до себе дбайливого ставлення. Вони просто можуть розкришитися або надломитися.
- Гігроскопічність. Пориста структура є одночасно перевагою і недоліком газоблоків, адже вони забезпечують циркуляцію повітря, але дуже швидко вбирають вологу. Впоратися з проблемою допоможе тільки правильна внутрішня і зовнішня обробка.
- Особлива система кріплень. Через технологічні особливості даного будівельного матеріалу до нього не підходять традиційні елементи кріплення. Додаткові компоненти не входять в комплект для продажу. Тому є досить відчутні додаткові витрати, про які рекламщики замовчують.
Порівняльна таблиця цегли і газобетону[ред. | ред. код]
Порівняння параметрів цегли та газобетону | ||
---|---|---|
Параметр | Керамічна цегла | Газобетон |
Межа міцності на стиск, кг/см² | 110÷220 | 25÷50 |
Маса стіни (1 м³) | 1200÷2000 | 700÷900 |
Теплопровідність, Вт/мК | 0,32÷0,46 | 0,10÷0,12 |
Морозотривкість, циклів | 50÷100 | 50 |
Вологопоглинання (% до маси) | 5÷12 | 20 |
Вогнетривкість (клас) | 1 | 1 |
Газобетон — это… Что такое Газобетон?
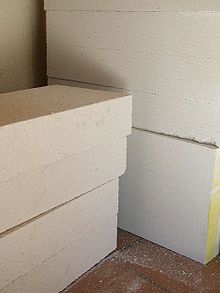
Газобетон — это разновидность ячеистого бетона, являющийся, по своей сути, искусственным камнем, на всей поверхности которого «расположились» отверстия-поры, представляющий собой искусственный камень с равномерно распределёнными по всему объёму сферическими порами диаметром 1-3 мм. Качество газобетона определяет равномерность распределения, равность объёма и закрытость пор.
Основными компонентами этого материала являются цемент, кварцевый песок и специализированные газообразователи[1], также возможно добавление гипса и извести. Сюда могут входить и промышленные отходы, такие как, например, зола и шлаки. В качестве специализированных газообразователей используются алюминиевые пасты и пудры. Сырьё смешивается с водой заливается в форму и происходит реакция воды и газообразователя, приводящая к выделению водорода, который и образует поры, смесь поднимается как тесто. После первичного затвердевания разрезается на блоки, плиты и панели. После этого изделия подвергаются закалке паром в автоклаве, где они приобретают необходимую жёсткость, либо высушиваются в условиях электроподогрева. В зависимости от условий твердения газобетон подразделяется на автоклавный газобетон и неавтоклавный газобетон.
Газобетон хорошо подлежит обработке простейшими инструментами: пилится, сверлится, строгается. В него легко забиваются гвозди, скобы. Со временем газобетон становится твёрже и твёрже. Не горит, так как состоит только из минеральных компонентов. Относительно экологически безопасен, по естественной радиоактивности благополучнее железобетона и тяжёлого бетона[источник не указан 1186 дней], так как плотность материала меньше.
Газобетон популярен во всем мире. В настоящее время работают более 240 заводов в 50 странах, которые ежегодно производят порядка 60 млн м³ строительных изделий из газобетона.[источник не указан 1119 дней]
Физико-механические свойства
- Лучшая, по сравнению с обычным пенобетоном, теплоизоляция и прочность.
- На производство газобетонного изделия требуется меньше цемента.
- Газобетон по простоте обработки сравним с деревом: он легко пилится, сверлится, гвоздится.
Недостатки:
- Неавтоклавный газобетон имеет сквозные поры, и из-за этого обладает плохой гидроизоляцией.
Классификация газобетонов
- По назначению:
- конструкционные.
- конструкционно-теплоизоляционные.
- теплоизоляционные.
- По условиям твердения:
- автоклавные (синтезного твердения) — твердеющие в среде насыщенного пара при давлении выше атмосферного;
- неавтоклавные (гидратационного твердения) — твердеющие в естественных условиях, при электропрогреве или в среде насыщенного пара при атмосферном давлении.
- По виду вяжущих и кремнеземистых компонентов подразделяют:
- по виду основного вяжущего:
- на известковых вяжущих, состоящих из извести-кипелки более 50 % по массе, шлака и гипса или добавки цемента до 15 % по массе;
- на цементных вяжущих, в которых содержание портландцемента 50 % и более по массе;
- на смешанных вяжущих, состоящих из портландцемента от 15 до 50 % по массе, извести или шлака, или шлако-известковой смеси;
- на шлаковых вяжущих, состоящих из шлака более 50 % по массе в сочетании с известью, гипсом или щелочью;
- на зольных вяжущих, в которых содержание высокоосновных зол 50 % и более по массе;
- по виду кремнеземистого компонента:
- на природных материалах — тонкомолотом кварцевом и других песках;
- на вторичных продуктах промышленности — золе-унос ТЭС, золе гидроудаления, вторичных продуктах обогащения различных руд, отходах ферросплавов и других.
- по виду основного вяжущего:
История появления технологии производства автоклавного газобетона
Для придания бетону пористой структуры чех Гоффман добавил в цементные и гипсовые растворы кислоты, углекислые и хлористые соли. Соли, взаимодействуя с растворами, выделяли газ, который и делал бетон пористым. За изобретенный газобетон Гоффман в 1889 году получил патент, но дальше этого у него дело не пошло.
Замысел Гоффмана развили американцы Аулсворт и Дайер. В качестве газообразователя в 1914 году они использовали порошки алюминия и цинка. В процессе химической реакции этих порошков с гашеной известью выделялся водород, который и способствовал образованию в бетоне пористой структуры. Это изобретение оказалось столь значимым, что его и поныне считают отправной точкой технологии изготовления газобетона.
Свой вклад в дело совершенствования газобетона (газосиликата) внес шведский архитектор и ученый А.Эрикссон. В своих исследованиях он пытался вспучивать раствор извести, кремнеземистых компонентов и цемента за счет взаимодействия этого раствора с алюминиевым порошком. Этот подход увенчался успехом. В 1929 году в местечке Иксхульт фирмой «Итонг» (Ytong) был начат промышленный выпуск газобетона. Инженерами этой фирмы за основу была взята технология тепловлажностного воздействия в автоклавах на известково-кремнеземистые компоненты, запатентованная в 1880 году немецким профессором В.Михаэлисом. Только за первый год работы этим предприятием было произведено 14 тысяч м3 газобетона (газосиликата). Следует заметить, что фирмой «Итонг» цемент не применялся вообще.
Несколько иной метод производства газобетона внедрила в жизнь в 1934 году шведская фирма «Сипорекс» (Siporex). Он основывается на применении смеси из портландцемента и кремнеземистого компонента. Известь в данном случае не применялась. Авторы этого метода инженеры финн Леннарт Форсэн и швед Ивар Эклунд. Научные и практические достижения вышеперечисленных инженеров и стали впоследствии основой промышленного производства как газосиликатов, так и газобетонов во многих странах мира.[2]
История производства ячеистых бетонов в В СССР
Производство ячеистых бетонов в СССР стало активно развиваться в 30-е годы. Автоклавные ячеистые бетоны (АЯБ) с газовой поризацией появились в промышленных масштабах к 50-м годам. К 60-м годам производство АЯБ стало самостоятельным развивающимся научным направлением, во многом опережающим европейские наработки в этой области.
К концу 80-х годов в СССР из ячеистых бетонов было построено более 250 млн м2 зданий различного назначения (жилых, общественных, производственных, животноводческих). При этом, несмотря на высокий уровень отечественных научных разработок ориентиром для советской промышленности служили западно-европейские достижения (понижение плотности панелей и блоков вплоть до 300 кг/м3), основанные в первую очередь на стабильном сырье и оборудовании, обеспечивающем высокую однородность материала. В 1987 г. с принятием очередной жилищной программы СССР основным средством ее реализации стала научно-производственно-техническая программа «Система эффективного строительства жилых и общественных зданий из ячеистых бетонов», которая предполагала строительство около 250 новых заводов по производству АЯБ с доведением общего его выпуска к 1995 г. до 40-45 млн м3/год.
Планы по этой программе предусматривали не только механическое наращивание объемов выпуска автоклавных бетонов. Важной задачей было также и снижение средней плотности выпускаемой продукции (для блоков она составляла 600—700 кг/м3). В программе говорилось: «Таким образом, семикратное увеличение производства ячеистых бетонов в нашей стране следует сопровождать двукратным снижением их объемной массы».[3]
К 2011 году производство ячеистого бетона в России составило более 3,2 млн м3/год, количество заводов-производителей АЯБ — более 80, до 2015 года планируется к запуску 10.
ГОСТы и СНиПы
- ГОСТ 25485-89 «Бетоны ячеистые»
- ГОСТ 21520-89 «Блоки из ячеистых бетонов стеновые мелкие»
- СН 277-80 «Инструкция по изготовлению изделий из ячеистого бетона»
См. также
Примечания
Что такое газоблок? — АЗАГ
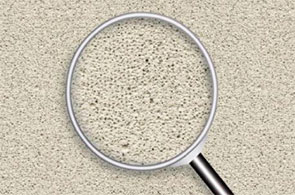
Газоблок – универсальный современный строительный материал, применение которого позволяет успешно решить целый комплекс строительных задач. Газобетонные блоки могут использоваться при возведении зданий различного размера и назначения – от небольших безкаркасных загородных домов до небоскребов, торговых и развлекательных комплексов, устроенных на каркасной основе.
Газоблок долговечен, огнестоек, экологически безопасен, обладает отличными теплоизоляционными характеристиками, имеет небольшой удельный вес, легко поддается обработке. Расходы на возведение коттеджа из газобетонных блоков по карману большинству представителей среднего класса.
Технология строительства из этого материала не отличается особой сложностью, поэтому малоэтажный дом из газоблока своими руками или с небольшой посторонней помощью может построить человек, не имеющий специального образования. Параметры этого строительного материала обуславливают значительное уменьшение количества операций по возведению стен и перегородок, позволяя сократить время строительства и расходы по оплате строительных работ.
1. Общие сведения о газоблоке
Технология изготовления газоблока
Газоблок – представитель семейства ячеистых бетонов, в которое входят также пенобетон и аэрированные легкие бетоны. Характерная черта представителей этой группы бетонов – ячеистая структура. Пузырьки газа занимают до 85% объема материала, поэтому ячеистые бетоны имеют малый объемный вес. Изготавливается газоблок из извести, воды, цемента и кварцевого песка. Все составляющие дозирует компьютер. В газобетоносмесителе в течение 4 – 5 минут готовится «тесто» — тщательно перемешанная смесь рецептурных компонентов. Затем в готовую смесь добавляют в небольшом количестве водную суспензию алюминиевой пудры, которая вступает в реакцию с известью. Продукт реакции — водород образует в сырьевой массе огромное количество пор размером от 0,5 до 2 мм, равномерно пронизывающих материал.
Сразу после добавления алюминиевой пасты смесь помещают в специальные металлические емкости, в которых и проходит вспучивание. Для ускорения химических реакций, схватывания и твердения полуфабрикат подвергают вибрационным нагрузкам. Когда газоблок достигает стадии предварительного твердения, с застывшей смеси проволочными струнами срезают неровную верхушку, а оставшуюся массу разрезают на блоки равного размера. Полученные элементы проходят тепловую обработку в автоклаве. Затем блоки калибруют при помощи специальной фрезерной машины. На заключительном этапе рабочие выполняют отделку фасадных поверхностей.
Применение современных технологий, позволяющее управлять процессом окончательного твердения газоблока, обеспечивает абсолютную однородность готового материала, поэтому свойства газобетонных блоков одинаковы в горизонтальном и вертикальном направлении.
Автоклавная обработка газоблока
Автоклавирование материала – важный этап, улучшающий свойства газобетонных блоков. Сформированный и разрезанный на блоки газоблок помещают в специальные автоклавные камеры, где они в течение двенадцати часов в условиях повышенного давления (12 кг/см?) обрабатываются насыщенным водяным паром при температуре 190°С.
Газоблок автоклавного твердения более прочен, дает меньшую усадку, имеет более однородную структуру, может применяться в различных областях строительства в качестве основного строительного, теплоизолирующего и звукоизолирующего материала. Коэффициент теплопроводности газоблока автоклавного твердения – 0,09-0,18 Вт/(м·°С). Такая теплопроводность газоблочнных изделий позволяет в российских климатических условиях (за исключением северных районов) возводить однорядные наружные стены из газобетонных блоков толщиной 375 – 400мм, не требующие дополнительного утепления.
Газоблок может изготавливаться неавтоклавным методом. В этом случае твердение происходит в естественных условиях. Для производства неавтоклавного газоблока не требуется современное высокотехнологичное оборудование. Газоблок неавтоклавного твердения менее прочен. Усадка неавтоклавных газобетонных блоков в процессе эксплуатации составляет 3 – 5 мм/м, автоклавных – 0,3 – 0,5 мм/м. Прочность автоклавного газоблока — 28-40 кгс/ м?, неавтоклавного — 10-12 кгс/ м?.
Неавтоклавный газоблок производится значительно реже, чем автоклавный. Газоблок, выпускаемый заводом «АЗАГ» проходит автоклавную обработку, которая является обязательной частью технологического процесса.
2. Свойства газоблока
Прочность и долговечность газоблока
Несмотря на небольшую объемную массу, составляющую для газоблока, обычно используемого в коттеджном строительстве, всего 400-500 кг/м?, материал обладает высокой прочностью на сжатие — 28-40 кгс/ м?. Газоблок может применяться в малоэтажном строительстве для возведения безкаркасных строений высотой не более 14 метров, создания внутренних стен и перегородок. Срок службы газобетонных блоков примерно равен сроку службы традиционных кирпичей. Производители обычно дают гарантию на 80 лет, но уже сейчас понятно, что этот материал может служить дольше – стены зданий, построенных из газобетонных блоков более восьмидесяти лет назад, не обнаруживают никаких признаков разрушения или изменения основных характеристик материала.
Качественная теплоизоляция
Воздух, заключенный в многочисленных порах, обеспечивает отличные теплосберегающие свойства газоблока. Стены дома из газобетонных блоков соответствуют строительным нормам, предусмотренным для жилых и общественных зданий. Сухой газоблок имеет коэффициент теплопроводности 0,12 Вт/м·°С. Чем ниже объемный вес газоблока, тем выше его теплоизоляционные характеристики, однако с уменьшением плотности прочность газобетонных блоков уменьшается. В настоящее время для возведения частных домов и коттеджей используется конструктивно-теплоизоляционный газоблок с объемным весом от 400 до 600 кг/м?, в котором прочность сочетается с достаточной легкостью и хорошими теплоизоляционными свойствами.
Гладкая поверхность и точные геометрические размеры газобетонных блоков позволяют применять технологию тонкошовной кладки. Свойства стен в домах, сложенных по этой технологии приближаются к свойствам монолитных стен. Зазор между блоками составляет всего 1 – 3 мм, что предотвращает образование «мостиков холода» и значительно уменьшает тепловые потери. Следствием низкой теплопроводности является меньшая тепловая инерция газоблока. Дома, сложенные из газобетонных блоков, в отличие от кирпичных, прогреваются всего за несколько часов.
Экономичность газоблока
Использование газоблока в строительстве позволяет снизить нагрузку на фундамент. Кладка методом тонких швов, по сравнению с традиционной кладкой, снижает расход кладочного раствора в шесть раз. Значительно снижается и трудоемкость строительных работ. 1 газобетонный блок заменяет 15 – 20 кирпичей, следовательно, во время выкладки стены из газоблока рабочие должны будут произвести в 15 – 20 раз меньше операций, чем при кладке кирпичной стены такого же размера. Газобетонные блоки при большом размере имеют малый объемный вес. Для работы с ними не нужны специальные подъемные механизмы. Все это сокращает трудозатраты. При использовании газобетонных блоков скорость возведения здания увеличивается примерно в четыре раза, а стоимость строительства снижается.
Экологическая безопасность и комфорт проживания в домах из газоблока
При изготовлении газоблока используются только натуральные, экологически чистые компоненты. Готовый строительный материал инертен, не выделяет в окружающую среду никаких соединений, абсолютно безопасен для здоровья людей. По своей способности «дышать», возникающей, благодаря пористой структуре, газоблок сходен с одним из наиболее натуральных материалов – деревом, от которого выгодно отличается долговечностью, легкостью монтажа и стабильностью размеров, практически не изменяющихся под воздействием влажности и перепадов температуры. Через поры в газоблоке постоянно осуществляется паро- и газообмен. Пар и вредные вещества выделяются наружу, а в помещение поступает свежий воздух с улицы, поэтому в домах из газоблока дышится легко и свободно.
Стены из газоблока на ощупь всегда теплые. Это связано с низкой теплопроводностью материала, который не забирает тепло от человеческой кожи, создавая ощущение тепла. Газобетонные стены «дышат», эффективно выводя лишнюю влагу из помещения и внутренней структуры материала, поэтому на стенах, сложенных из газобетонных блоков не развивается гниение, не появляется плесень и грибок.
Огнестойкость газоблока
Газоблок изготавливается из негорючего природного минерального сырья, не горит и не поддерживает горение. Он может в течение 3-7 часов выдерживать одностороннее воздействие огня. Также газоблок способен защитить от огня металлические конструкции.
Морозостойкость газоблока
Под морозостойкостью материала понимают его способность выдерживать полное замораживание и оттаивание в состоянии максимального насыщения водой. При проведении испытаний газоблок погружают на 8 часов в воду, а затем на 8 часов помещают в морозильную камеру. Такое действие считается одним циклом. Испытания повторяют до тех пор, пока газоблок не начнет терять прочность и массу. Газобетонные блоки пронизаны тысячами мелких пор, в которые при замерзании вытесняется лед и вода. Это обеспечивает сохранность газоблока при замерзании в течение 100 и более циклов. Для сравнения: нормы морозостойкости кирпича, пригодного для использования в Центральном регионе – строительный – 15-25 циклов, лицевой – 50 циклов. Пенобетон выдерживает до 35 циклов заморозки.
Высокая технологичность
Производители газоблока выпускают блоки шириной от 50 до 500 мм и дополнительные конструктивные элементы. Оптимальная толщина стен из газоблока в климатических условиях средней полосы России составляет 350 – 400 мм, поэтому дома из газобетонных блоков строятся в один слой. При возведении зданий из газоблока не нужно использовать дополнительные утеплители. Это упрощает строительство и снижает стоимость конструкции.
Удобство обработки газоблока
Газоблок легко обрабатывается обычным ручным и электрическим инструментом. Его можно сверлить, колоть и резать. Газобетонные блоки разрезают, используя обычную ручную или электрическую пилу. Штробы под арматуру и проводку прокладывают электродрелью со специальной насадкой. Отверстия под розетки и выключатели также высверливают дрелью. Округлые формы создают при помощи ленточной шлиф-машины. Газобетонные изделия могут использоваться в качестве отделочного и декоративного материала, из которого изготавливают колонны, подставки, тумбы, декоративные украшения, имитирующие лепнину.
Немного цифр
Объемный вес газоблоков различных марок колеблется от 300 до 1200 кг/ м?. В малоэтажном строительстве обычно используют газоблок с объемным весом 400 до 600 кг/м?. Прочность газоблока — 10-50 кг/см?, коэффициент теплопроводности — 0,09-0,14 Вт·м°ree;С. Допустимые отклонения геометрических параметров граней +/- 1 мм.
3. Сравнение газоблока с пенобетоном
Газоблок нередко путают с другим пористым строительным материалом – пенобетоном. Между тем, эти два материала различаются по способу производства, компонентам и конечным характеристикам. Основные компоненты сырьевой массы пенобетона сходны с составляющими газобетонной смеси. При производстве пенобетона также используется вода, известь и цемент. Чтобы снизить себестоимость пенобетонных изделий, вместо кварцевого песка производители нередко используют производственные отходы — нефелиновый шлам, золу и доменные шлаки. Пенообразователи зачастую также являются побочными продуктами производства. Для образования пены применяют сульфитный и подмыльный щелок, дубильные экстракты кожевенной промышленности и т.д.
Для производства пенобетона не нужно сложное современное оборудование. Автоклавную обработку материал, как правило, не проходит, «дозревая» естественным путем – на воздухе. Простота производства пенобетона приводит к большому количеству некачественных подделок, изготовленных кустарным способом. Производственный цикл изготовления пенобетона может включать автоклавирование. На практике автоклавный пенобетон изготавливают редко. Автоклавная обработка улучшает эксплуатационные характеристики материала и повышает его стоимость. Цена автоклавного пенобетона сравнима с ценой газоблока.
Пенобетон, даже изготовленный с соблюдением технологии и состава рецептуры, менее прочен и не так долговечен. Его сложнее обрабатывать. Непостоянство сырья и использование отходов производства приводит к ухудшению технических характеристик и может снижать экологическую безопасность материала. Блоки из пенобетона и газоблока одинаковой прочности различаются по коэффициенту теплопередачи. Газоблок обеспечивает более высокий уровень теплоизоляции. Достаточная для сохранения тепла толщина стен из газоблока – около 400 мм. Толщина стен из пенобетона, обеспечивающих аналогичный уровень сохранения тепла – не менее 600 мм.
В отличие от пенобетона, который в процессе эксплуатации дает усадку, вызывающую появление трещин, газоблок с течением времени практически не изменяет объем и конфигурацию. Усадка газоблока в процессе эксплуатации составляет всего 0,3 мм/м. Усадка пенобетона примерно в десять раз больше – 2-3 мм/м. При этом отпускная влажность пенобетонных изделий превышает отпускную влажность газоблока. В процессе производства пенобетона технически невозможно добиться идеальной геометрической формы и гладкой поверхности блоков. Поэтому при кладке из пенобетона нельзя использовать технологию тонких швов. Увеличение пространства между блоками, заполненного раствором, приводит к появлению «мостиков холода» и снижению теплоизоляционных свойств пенобетонных стен.
Крупные производители газоблока (такие, как Ytong) изготавливают не только газобетонные блоки стандартных типоразмеров, но и дополнительные элементы, облегчающие процесс возведения здания. Типоразмеры пенобетонных блоков ограничены. Дополнительные конструктивные элементы для пенобетона не выпускаются. Нередко производители пенобетона подчеркивают, что пенобетон имеет более низкие показатели водопоглощения, приводя пример с пенобетонным блоком, не тонущим в воде. Более длительная плавучесть пенобетона объясняется особенностями материала. Пузырьки газа в пенобетоне не сообщаются друг с другом и с внешней средой, тогда как газоблок пронизан сообщающимися порами. Поэтому вода быстрее проникает в газоблок, который тонет первым.
При нахождении во влажной среде реальные показатели различаются не столь существенно, а опыт с плавающим пенобетоном – просто эффектная демонстрация, не отражающая разницу водопоглощения в реальных условиях. В процессе эксплуатации влажных помещений пенобетон более интенсивно насыщается влагой из-за большей величины пор и их неравномерного распределения.
Пенобетон дешевле газоблока на 20 – 25%, так как в процессе его производства используются дешевые ингредиенты. При покупке пенобетона возрастает риск приобретения некачественного материала, изготовленного с нарушением рецептуры кустарным способом. Газоблок обеспечивает лучшую звукоизоляцию. Показатели морозостойкости у газоблока (100 циклов) почти в три раза превышают соответствующие показатели у пенобетона (не более 35 циклов).
Газоблок и пенобетон легко можно отличить по внешнему виду. Газобетонные блоки белого цвета, они примерно в полтора раза легче блоков из пенобетона, имеют правильную геометрию. Допускается отклонение граней до 1 мм. На распиле видны равномерно распределенные поры практически одинакового размера и формы. Блоки из пенобетона темно-серые, более тяжелые. Отклонения в параллельности сторон могут достигать 10 мм. На распиле видны ячейки разного размера и формы.
4. Область применения газоблока
Первоначально газоблок предназначался для утепления зданий, а не для их возведения, но после того, как строители и проектировщики оценили этот удобный в монтаже и обработке, прочный материал, область применения газоблока существенно расширилась. В настоящее время газобетонные изделия применяются в малоэтажном строительстве для возведения наружных и внутренних несущих стен, перегородок, перемычек, перекрытий и даже ступеней. В отдельных случаях газоблок используют в качестве утеплителя для малоэтажных домов. В высотном строительстве газобетонные изделия применяются для заполнения стен зданий на каркасной основе. Из газобетонных блоков строят торговые, развлекательные и общественные здания. Газоблок используется при наращивании этажности, реконструкции старых зданий, возведении мансард, обеспечении звукоизоляции и утеплении строений без изменения конструктивных особенностей и несущей способности фундамента.
90000 aerated concrete Wikipedia 90001 90002 Lightweight, precast building material 90003 Aerated autoclaved concrete — close-up view Autoclaved aerated concrete tiles of various shapes and sizes Uncured «green» AAC blocks (on the right) ready to be fed into an autoclave to be rapidly cured into a finished product under heat and pressure 90002 90005 Autoclaved aerated concrete 90006 (90005 AAC 90006) is a lightweight, precast, foam concrete building material suitable for producing concrete masonry unit (CMU) like blocks.Composed of quartz sand, calcined gypsum, lime, cement, water and aluminum powder, AAC products are cured under heat and pressure in an autoclave. Invented in the mid-1920s, AAC simultaneously provides structure, insulation, and fire- and mold-resistance. Forms include blocks, wall panels, floor and roof panels, cladding (façade) panels and lintels. 90009 [1] 90010 90009 [2] 90010 90003 90002 AAC products may be used for both interior and exterior construction, and may be painted or coated with a stucco or plaster compound to guard against the elements, or covered with siding materials such as veneer brick or vinyl siding.In addition to their quick and easy installation, ACC materials can be routed, sanded, or cut to size on site using standard power tools with carbon steel cutters. 90009 [3] 90010 90009 [4] 90010 90003 90020 Etymology [] 90021 90002 Other names for the product include 90005 autoclaved cellular concrete 90006 (ACC), 90005 autoclaved lightweight concrete 90006 (ALC), 90005 autoclaved concrete 90006, 90005 cellular concrete 90006, 90005 porous concrete 90006, 90005 Aircrete 90006, 90005 Thermalite 90006, 90005 Hebel Block 90006, 90005 Starken 90006, and 90005 Ytong 90006.90009 [90044 citation needed 90045] 90010 90003 90020 History [] 90021 90002 AAC was perfected in the mid-1920s by the Swedish architect and inventor Dr. Johan Axel Eriksson, 90009 [5] 90010 90009 [6] 90010 working with Professor Henrik Kreüger at the Royal Institute of Technology. 90009 [5] 90010 90009 [6] 90010 The process was patented in 1924. In 1929 року, production started in Sweden at the city of Yxhult. From «Yxhults Ånghärdade Gasbetong» later became the first registered building materials brand in the world: Ytong.Another brand «Siporex» was established in Sweden in тисяча дев’ятсот тридцять дев’ять and presently licences and owns plants in 35 locations around the world. The second major international cellular concrete Hebel brand goes back to company founder and technicians Josef Hebel from Memmingen. In 1943 року, the first Hebel-plant was opened in Germany. 90003 90002 Originally Ytong autoclaved aerated concrete in Sweden was produced with alum shale, whose combustible carbon content was beneficial in the production process. Unfortunately, the slate deposits used for Ytong in Sweden also contain a very low level of natural uranium, which makes the material give off radioactive radon gas in the building.In 1972, the Swedish Radiation Safety Authority pointed out the unsuitability of a radon-emitting construction material, and the use of alum slate in the production of Ytong ceased in 1975. By using new formulations, containing only quartz sand, calcined gypsum, lime ( mineral), cement, water and aluminum powder, Ytong produced a new type of aerated concrete which no longer contains alum slate and thus has eliminated the problem of radon exposure from this raw material. The production of this white autoclaved aerated concrete is now state of the art and similar formulations are used by all producers around the world.90003 90002 In 1978 The Swedish team of Siporex Sweden opened the Siporex Factory in the Kingdom of Saudi Arabia — the «Lightweight Construction Company — Siporex — LCC SIPOREX» which have supplied the Middle-East and Africa and Japan by most of its need. The LCC SIPOREX FACTORY has operated for more than 40 years. Today aerated concrete is produced by many companies, particularly in Europe and Asia. There is some production in the Americas and in Africa, there is one plant in Egypt. AAC production in Europe has slowed down considerably, but the industry is growing rapidly in Asia due to strong demand in housing and commercial space.China is now the largest aircrete market in the world with several hundred factories. China, Central Asia, India, and the Middle-East are the biggest in terms of AAC manufacturing and consumption. 90009 [7] 90010 90003 90002 The product aircrete is sold, like other masonry materials, under many different brand names. Ytong and Hebel are brands of the international operating company Xella headquartered in Duisburg. Other more internationally renowned brand names in Europe are H + H Celcon (Denmark), or Solbet (Poland).90003 90020 Uses [] 90021 90002 AAC is a highly thermally insulating concrete-based material used for both interior and exterior construction. Besides AAC’s insulating capability, one of its advantages is quick and easy installation, because the material can be routed, sanded, or cut to size on site using standard power tools with carbon steel cutters. 90009 [90044 citation needed 90045] 90010 90003 90002 AAC is well suited for high-rise buildings and those with high temperature variations.Due to its lower density, high-rise buildings constructed using AAC require less steel and concrete for structural members. The mortar needed for laying of AAC blocks is reduced due to the lower number of joints. Similarly, the material required for rendering is also lower due to the dimensional accuracy of AAC. The increased thermal efficiency of AAC makes it suitable for use in areas with extreme temperatures, as it eliminates the need for separate materials for construction and insulation, leading to faster construction and cost savings.90003 90002 Even though regular cement mortar can be used, most of the buildings erected with AAC materials use thin bed mortar in thicknesses around ⅛ inch, depending on the national building codes. AAC materials can be coated with a stucco or plaster compound to guard against the elements, or covered with siding materials such as brick or vinyl. 90003 90020 Manufacturing [] 90021 90002 Unlike most other concrete applications, AAC is produced using no aggregate larger than sand. Quartz sand, calcined gypsum, lime (mineral) and / or cement and water are used as a binding agent.Aluminum powder is used at a rate of 0.05% -0.08% by volume (depending on the pre-specified density). In some countries, like India and China, fly ash generated from coal fire power plants and having 50-65% silica content is used as an aggregate. 90003 90002 When AAC is mixed and cast in forms, several chemical reactions take place that gives AAC its light weight (20% of the weight of concrete) and thermal properties. Aluminum powder reacts with calcium hydroxide and water to form hydrogen. The hydrogen gas foams and doubles the volume of the raw mix creating gas bubbles up to 3mm (⅛ inch) in diameter.At the end of the foaming process, the hydrogen escapes into the atmosphere and is replaced by air. 90003 90002 When the forms are removed from the material, it is solid but still soft. It is then cut into either blocks or panels, and placed in an autoclave chamber for 12 hours. During this steam pressure hardening process, when the temperature reaches 190 ° Celsius (374 ° Fahrenheit) and the pressure reaches 8 to 12 bar, quartz sand reacts with calcium hydroxide to form calcium silicate hydrate, which gives AAC its high strength and other unique properties .Because of the relatively low temperature used AAC blocks are not considered fired brick but a lightweight concrete masonry unit. After the autoclaving process, the material is ready for immediate use on the construction site. Depending on its density, up to 80% of the volume of an AAC block is air. AAC’s low density also accounts for its low structural compression strength. It can carry loads of up to 8 MPa (1,160 PSI), approximately 50% of the compressive strength of regular concrete. 90003 90002 In 1978, the first AAC material was opened in the Persian Gulf state of the Kingdom of Saudi Arabia — LCC SIPOREX- Lightweight Construction Company supplying the GCC countries with the Aerated products of blocks and panels.90003 90002 Since 1980, there has been a worldwide increase in the use of AAC materials. New production plants are being built in Australia, Bahrain, China, Eastern Europe, India, and the United States. AAC is increasingly used by developers, architects, and home builders worldwide. 90003 90020 Advantages [] 90021 90002 AAC has been produced for more than 70 years, and it offers several advantages over other cement construction materials, one of the most important being its lower environmental impact.90003 90096 90097 Improved thermal efficiency reduces the heating and cooling load in buildings. 90098 90097 Porous structure gives superior fire resistance. 90098 90097 Workability allows accurate cutting, which minimizes the generation of solid waste during use. 90098 90097 Resource efficiency gives it lower environmental impact in all phases of its life cycle, from the processing of raw materials to the disposal of waste. 90098 90097 Lightweight saves cost and energy in transportation, labour expenses, and increases chances of survival during seismic activity.90009 [8] 90010 90098 90097 Larger size blocks leads to faster masonry work. 90098 90097 Reduces project cost for large constructions. 90098 90097 Environmentally friendly: It produces at least 30% less solid waste than traditional concrete. There is a decrease of 50% of greenhouse gas emissions. 90098 90097 Fire resistant: As with regular concrete, AAC is fire resistant. 90098 90097 Great ventilation: This material is very airy and allows diffusion of water. This reduces the humidity inside the building.AAC will absorb moisture and release humidity. This helps to prevent condensation and other problems that are related to mildew. 90098 90097 Non-toxic: There are no toxic gases or other toxic substances in autoclaved aerated concrete. It neither attracts rodents or other pests nor can it be damaged by such. 90098 90097 Accuracy: The panels and blocks made of autoclaved aerated concrete are produced to the exact sizes needed before leaving the factory. There is less need for on-site trimming.Since the blocks and panels fit so well together, there is less use of finishing materials such as mortar. 90098 90097 Long lasting: The life of this material is extended because it is not affected by harsh climates or extreme weather changes. It will not degrade under normal climate changes. 90098 90125 90020 Disadvantages [] 90021 90002 AAC has been produced for more than 70 years, however, some disadvantages were found when it was introduced in the UK (where cavity wall with clay brick two-skin construction has been the norm).90003 90096 90097 Installation during rainy weather: AAC is known to crack after installation, which can be avoided by reducing the strength of the mortar and ensuring the blocks are dry during and after installation. 90098 90097 Brittle nature: they need to be handled more carefully than clay bricks to avoid breakage. 90098 90097 Attachments: the brittle nature of the blocks requires longer, thinner screws when fitting cabinets and wall hangings and wood-suitable drill bits or hammering in.Special, large diameter wall plugs (90044 anchors 90045) are available at a higher cost than common wall plugs. 90009 [9] 90010 90098 90097 Insulation requirements in newer building codes of northern European countries would require very thick walls when using AAC alone. Thus many builders choose to use traditional building methods installing an extra layer of insulation around the entire building. 90098 90125 90020 References [] 90021 90020 External links [] 90021 .90000 Aerated Autoclaved Concrete Blocks | 90001 90002 AAC Blocks: Aerated Autoclaved Concrete Blocks 90003 90004 Krishna 90004 April 26 2017 90004 TECHNOLOGY 90002 AAC blocks are light weight 90008 Aerated Autoclave Concrete Blocks 90009. It is manufactured through a reaction of aluminium and a proportionate blend of lime, cement and fly ash. During this process, the hydrogen gas that escapes creates millions of tiny air cells, rendering AAC with a strong cellular structure. AAC blocks are further strengthened by high pressure steam curing in autoclaves.The product thus formed is not only light weight but also has higher Compressive strength. 90003 90002 Density of these AAC lightweight blocks usually ranges between 90008 550 — 650 kg / m³ 90009. Which is superior to most types of light weight blocks. AAC blocks are 25% stronger than other products of the same density. 90003 90002 Auto-claved Aerated concrete blocks are new to civil industry. It is replacing the current usage of red bricks. As it has a many features when compared with the traditional red bricks.You can learn some of them from below. 90003 [NO_TOC] 90017 90018 90019 Benefits of AAC Blocks: 90020 90021 90022 The nominal size of AAC block is 90008 9 «X 8» X 4 «-12» 90009 90025 90022 When compared with the volume of normal redbrick with the AAC bricks 90027 90028 90002 90008 Volume of 1 AAC Brick = Volume of 7 red bricks for (9 «X 8» X 4 «) 90009 90003 90033 90025 90022 AAC block has a weight of 9-12 kg depending on moisture conditions. When compared with redbricks 60% of dead load on structure is decreased.90025 90022 It not only decreases the 90008 dead load 90009 on the structure. It also depreciate the use of Steel and 90008 concrete 90009 in structure. 90025 90022 Jointing AAC bricks are economical. As mentioned 1 AAC brick = 7 bricks. For Jointing 7 red bricks with each other it requires more jointing mortar when compared with jointing one AAC block to other. 90025 90022 Compressive strength of AAC block is higher 5-6N / Sq.m whereas the redbrick has a Compressive strength of 3.50 N / Sq.mm 90025 90022 90008 Fire resistance: 90009 They offer good fire 90025 90051.90000 AAC Blocks — Autoclaved Aerated Concrete Blocks Manufacturer from Rajkot 90001 Our AAC Blocks come in a size of 600 x 200 x (100 to 300) mm and hence are almost 8 times bigger than a normal burnt brick. Though these blocks are big, they weigh a lot lesser and hence, the labor expense will come down too. As we are equipped and well aware of the latest trend in the building construction industry, a visit to our office and our official website will take you ahead in your construction venture.90002 We, at Aercon India, work towards manufacturing the latest building blocks for modern day edifices- Aerated Autoclaved Concrete Blocks, popularly known as AAC Blocks. In India, this is relatively a novel concept as compared to the rest of the world. In terms of usage of the AAC Blocks, we can say that our blocks are increasingly being used for constructing buildings in the most environmental-friendly manner. Yet, these blocks are very light in weight as they contain air to almost 80% of its actual weight.90003 90002 When you think of a city, the next thing that comes to your mind is buildings. Over the years, we have come up with buildings of varying shapes and sizes and we have just got better at it. On one side, we are adapting architectural techniques and tools to construct marvelous buildings, we are also ensuring that the materials we use are of the topmost quality. Now with technology, even the most fundamental bricks and cement have undergone a sea change. The reason is that we have pioneers in this field with vast engineering knowledge and matchless experience to help us make the most marvelous building blocks and other materials.Aercon India is a group with a stronghold in Western India and in the construction and realty industry today. 90003 90002 When we say that we are adapting the styles of building homes and sky scrapers that are the most in use in developed and developing countries abroad, can we stay behind in adapting their materials and tools too? Our founders themselves are experts in the field and have plenty of rich experience in manufacturing AAC Blocks or Aerated Autoclaved Concrete Blocks, and supply them to the companies across the country.90003.90000 Aerated Concrete Block Factory, Custom Aerated Concrete Block OEM / ODM Manufacturing Company 90001 Total 142 aerated concrete block factories & companies found with 426 products. Source high quality aerated concrete block from our great selection of reliable aerated concrete block manufacturing factories. Diamond Member 90002 90003 90004 90005 Business Type: 90006 90005 Manufacturer / Factory , Trading Company , Other 90006 90009 90004 90005 Main Products: 90006 90005 Wall Panel, AAC Panel, Alc Panel, Exterior Wall, AAC Floor Panel 90006 90009 90004 90005 Mgmt.Certification: 90006 90005 90020 ISO 9001, ISO 9000, ISO 14001, ISO 14000, ISO 20000 90021 90006 90009 90004 90005 R & D Capacity: 90006 90005 OEM, ODM 90006 90009 90004 90005 Location: 90006 90005 Nanjing, Jiangsu 90006 90009 90036 90037 Gold Member 90002 90003 90004 90005 Business Type: 90006 90005 Trading Company 90006 90009 90004 90005 Main Products: 90006 90005 AAC Panel, Fiber Cement Board 90006 90009 90004 90005 Mgmt.Certification: 90006 90005 90020 ISO 9001, ISO 14001 90021 90006 90009 90004 90005 Factory ownership: 90006 90005 Limited Company 90006 90009 90004 90005 R & D Capacity: 90006 90005 OEM, ODM 90006 90009 90004 90005 Location: 90006 90005 Hangzhou, Zhejiang 90006 90009 90036 90037 Diamond Member 90002 90003 90004 90005 Business Type: 90006 90005 Manufacturer / Factory 90006 90009 90004 90005 Main Products: 90006 90005 AAC Panel, Steel Structure Building, Alc Panel House, Prefabricated Houses, Modular Homes 90006 90009 90004 90005 Mgmt.Certification: 90006 90005 90020 ISO 9001 90021 90006 90009 90004 90005 Factory ownership: 90006 90005 Limited Company 90006 90009 90004 90005 R & D Capacity: 90006 90005 OEM, Own Brand 90006 90009 90004 90005 Location: 90006 90005 Qingdao, Shandong 90006 90009 90036 90037 Diamond Member 90002 90003 90004 90005 Business Type: 90006 90005 Manufacturer / Factory , Trading Company 90006 90009 90004 90005 Main Products: 90006 90005 90134 Concrete 90135 90134 Block 90135 Making Machine, 90134 Concrete 90135 Brick Machine, Road Machines, Stone Crusher, 90134 Concrete 90135 Pump 90006 90009 90004 90005 Mgmt.Certification: 90006 90005 90020 ISO 9001, ISO 20000 90021 90006 90009 90004 90005 Factory ownership: 90006 90005 Limited Company 90006 90009 90004 90005 R & D Capacity: 90006 90005 OEM, Own Brand 90006 90009 90004 90005 Location: 90006 90005 Linyi, Shandong 90006 90009 90036 90037 Gold Member 90002 90003 90004 90005 Business Type: 90006 90005 Manufacturer / Factory 90006 90009 90004 90005 Main Products: 90006 90005 Aluminum Powder Paste 90006 90009 90004 90005 Factory ownership: 90006 90005 Limited Company 90006 90009 90004 90005 R & D Capacity: 90006 90005 Own Brand, ODM, OEM 90006 90009 90004 90005 Location: 90006 90005 Binzhou, Shandong 90006 90009 90004 90005 Production Lines: 90006 90005 Above 10 90006 90009 90036 90037 Diamond Member 90002 90003 90004 90005 Business Type: 90006 90005 Manufacturer / Factory 90006 90009 90004 90005 Main Products: 90006 90005 90134 Block 90135 Machine, AAC 90134 Block 90135 Machine, Mixer, Brick Machine, 90134 Aerated 90135 90134 Block 90135 Machine 90006 90009 90004 90005 Mgmt.Certification: 90006 90005 90020 ISO9001: 2008 90021 90006 90009 90004 90005 Factory ownership: 90006 90005 Limited Company 90006 90009 90004 90005 R & D Capacity: 90006 90005 Own Brand 90006 90009 90004 90005 Location: 90006 90005 Linyi, Shandong 90006 90009 90036 90037 Diamond Member 90002 90003 90004 90005 Business Type: 90006 90005 Manufacturer / Factory , Trading Company 90006 90009 90004 90005 Main Products: 90006 90005 Stone Crusher, Ball Mill, Rotary Dryer, Ore Dressing Machine, Rotary Kiln 90006 90009 90004 90005 Mgmt.Certification: 90006 90005 90020 ISO9001: 2008 90021 90006 90009 90004 90005 Factory ownership: 90006 90005 Limited Company 90006 90009 90004 90005 R & D Capacity: 90006 90005 ODM, OEM 90006 90009 90004 90005 Location: 90006 90005 Zhengzhou, Henan 90006 90009 90036 90037 .